coolant temperature SSANGYONG KORANDO 2012 Owner's Manual
[x] Cancel search | Manufacturer: SSANGYONG, Model Year: 2012, Model line: KORANDO, Model: SSANGYONG KORANDO 2012Pages: 1082, PDF Size: 96.1 MB
Page 290 of 1082
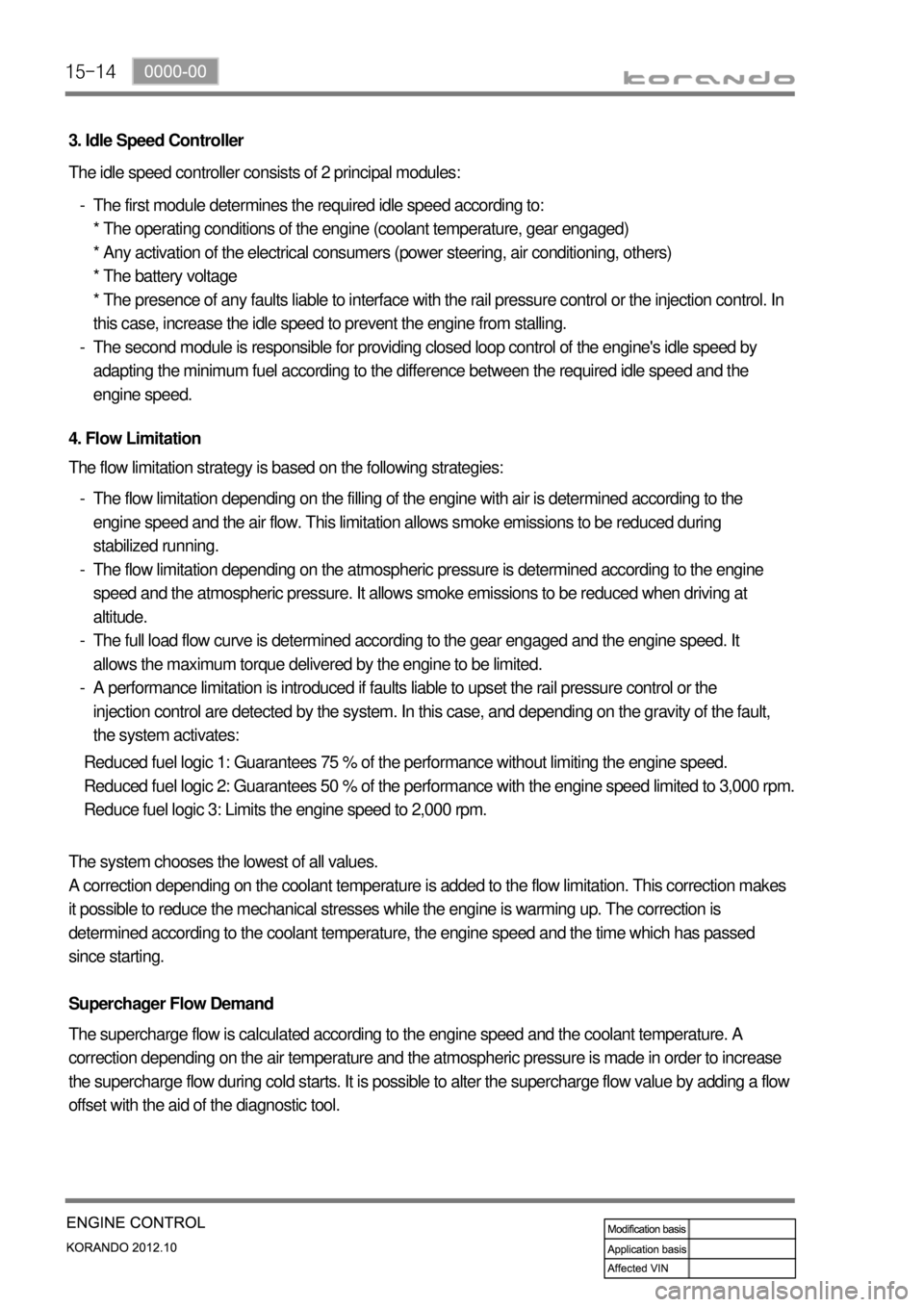
15-14
3. Idle Speed Controller
The idle speed controller consists of 2 principal modules:
The first module determines the required idle speed according to:
* The operating conditions of the engine (coolant temperature, gear engaged)
* Any activation of the electrical consumers (power steering, air conditioning, others)
* The battery voltage
* The presence of any faults liable to interface with the rail pressure control or the injection control. In
this case, increase the idle speed to prevent the engine from stalling.
The second module is responsible for providing closed loop control of the engine's idle speed by
adapting the minimum fuel according to the difference between the required idle speed and the
engine speed. -
-
4. Flow Limitation
The flow limitation strategy is based on the following strategies:
The flow limitation depending on the filling of the engine with air is determined according to the
engine speed and the air flow. This limitation allows smoke emissions to be reduced during
stabilized running.
The flow limitation depending on the atmospheric pressure is determined according to the engine
speed and the atmospheric pressure. It allows smoke emissions to be reduced when driving at
altitude.
The full load flow curve is determined according to the gear engaged and the engine speed. It
allows the maximum torque delivered by the engine to be limited.
A performance limitation is introduced if faults liable to upset the rail pressure control or the
injection control are detected by the system. In this case, and depending on the gravity of the fault,
the system activates: -
-
-
-
Reduced fuel logic 1: Guarantees 75 % of the performance without limiting the engine speed.
Reduced fuel logic 2: Guarantees 50 % of the performance with the engine speed limited to 3,000 rpm.
Reduce fuel logic 3: Limits the engine speed to 2,000 rpm.
The system chooses the lowest of all values.
A correction depending on the coolant temperature is added to the flow limitation. This correction makes
it possible to reduce the mechanical stresses while the engine is warming up. The correction is
determined according to the coolant temperature, the engine speed and the time which has passed
since starting.
Superchager Flow Demand
The supercharge flow is calculated according to the engine speed and the coolant temperature. A
correction depending on the air temperature and the atmospheric pressure is made in order to increase
the supercharge flow during cold starts. It is possible to alter the supercharge flow value by adding a flow
offset with the aid of the diagnostic tool.
Page 291 of 1082
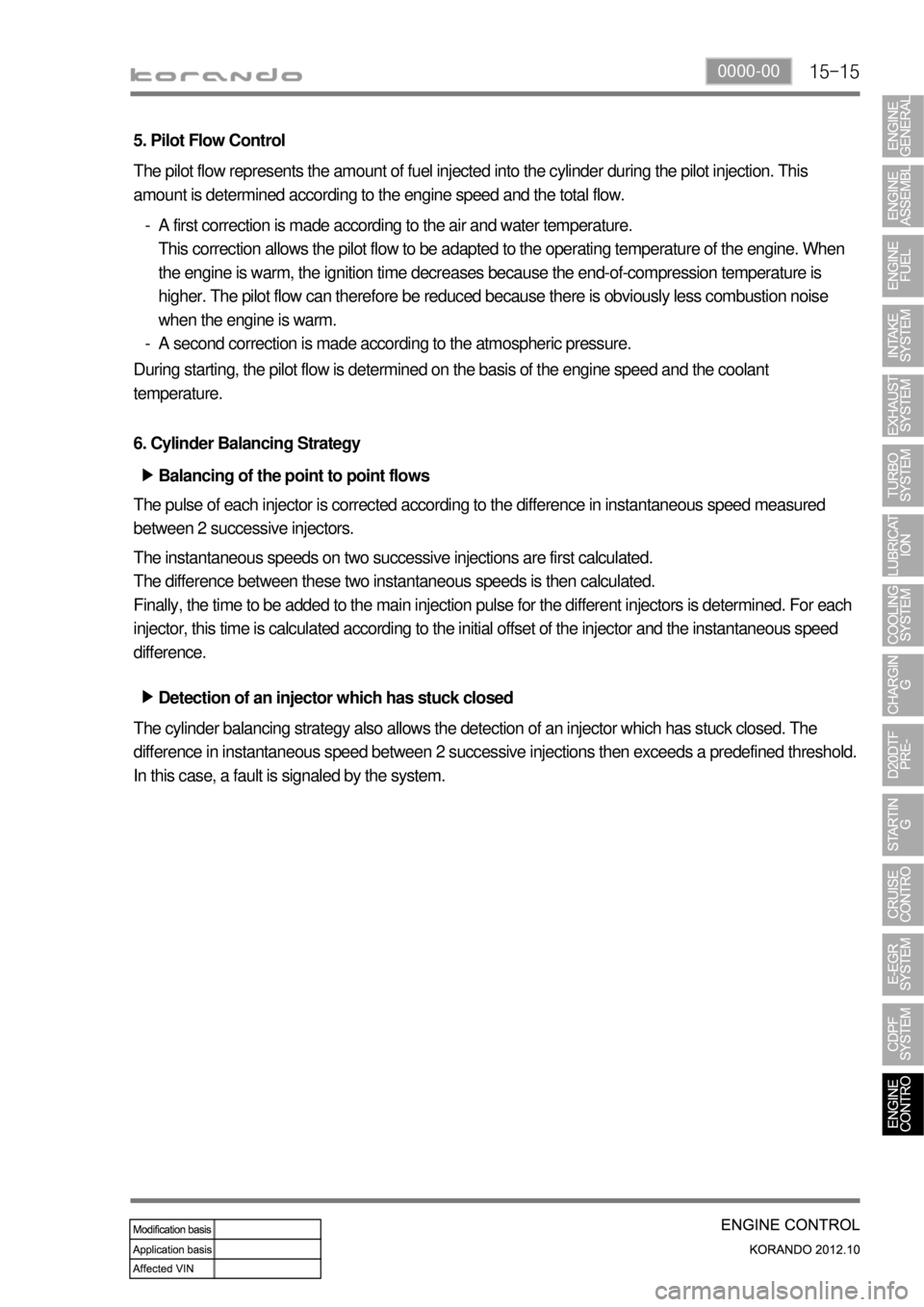
15-150000-00
5. Pilot Flow Control
The pilot flow represents the amount of fuel injected into the cylinder during the pilot injection. This
amount is determined according to the engine speed and the total flow.
A first correction is made according to the air and water temperature.
This correction allows the pilot flow to be adapted to the operating temperature of the engine. When
the engine is warm, the ignition time decreases because the end-of-compression temperature is
higher. The pilot flow can therefore be reduced because there is obviously less combustion noise
when the engine is warm.
A second correction is made according to the atmospheric pressure. -
-
During starting, the pilot flow is determined on the basis of the engine speed and the coolant
temperature.
6. Cylinder Balancing Strategy
Balancing of the point to point flows â–¶
The pulse of each injector is corrected according to the difference in instantaneous speed measured
between 2 successive injectors.
The instantaneous speeds on two successive injections are first calculated.
The difference between these two instantaneous speeds is then calculated.
Finally, the time to be added to the main injection pulse for the different injectors is determined. For each
injector, this time is calculated according to the initial offset of the injector and the instantaneous speed
difference.
Detection of an injector which has stuck closed â–¶
The cylinder balancing strategy also allows the detection of an injector which has stuck closed. The
difference in instantaneous speed between 2 successive injections then exceeds a predefined threshold.
In this case, a fault is signaled by the system.
Page 295 of 1082
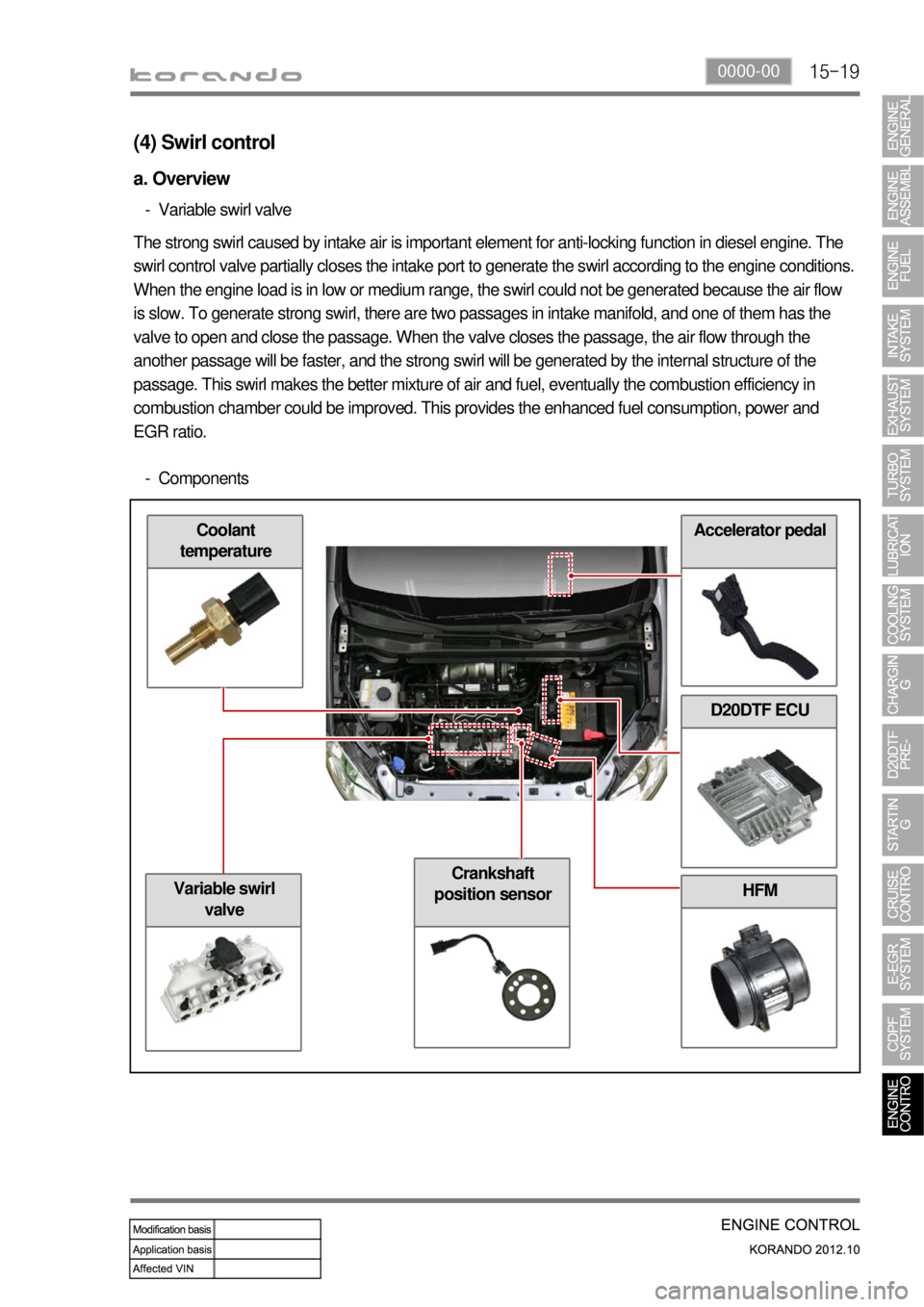
15-190000-00
HFM
Accelerator pedalCoolant
temperature
(4) Swirl control
a. Overview
Variable swirl valve -
The strong swirl caused by intake air is important element for anti-locking function in diesel engine. The
swirl control valve partially closes the intake port to generate the swirl according to the engine conditions.
When the engine load is in low or medium range, the swirl could not be generated because the air flow
is slow. To generate strong swirl, there are two passages in intake manifold, and one of them has the
valve to open and close the passage. When the valve closes the passage, the air flow through the
another passage will be faster, and the strong swirl will be generated by the internal structure of the
passage. This swirl makes the better mixture of air and fuel, eventually the combustion efficiency in
combustion chamber could be improved. This provides the enhanced fuel consumption, power and
EGR ratio.
Components -
D20DTF ECU
Crankshaft
position sensor
Variable swirl
valve
Page 302 of 1082
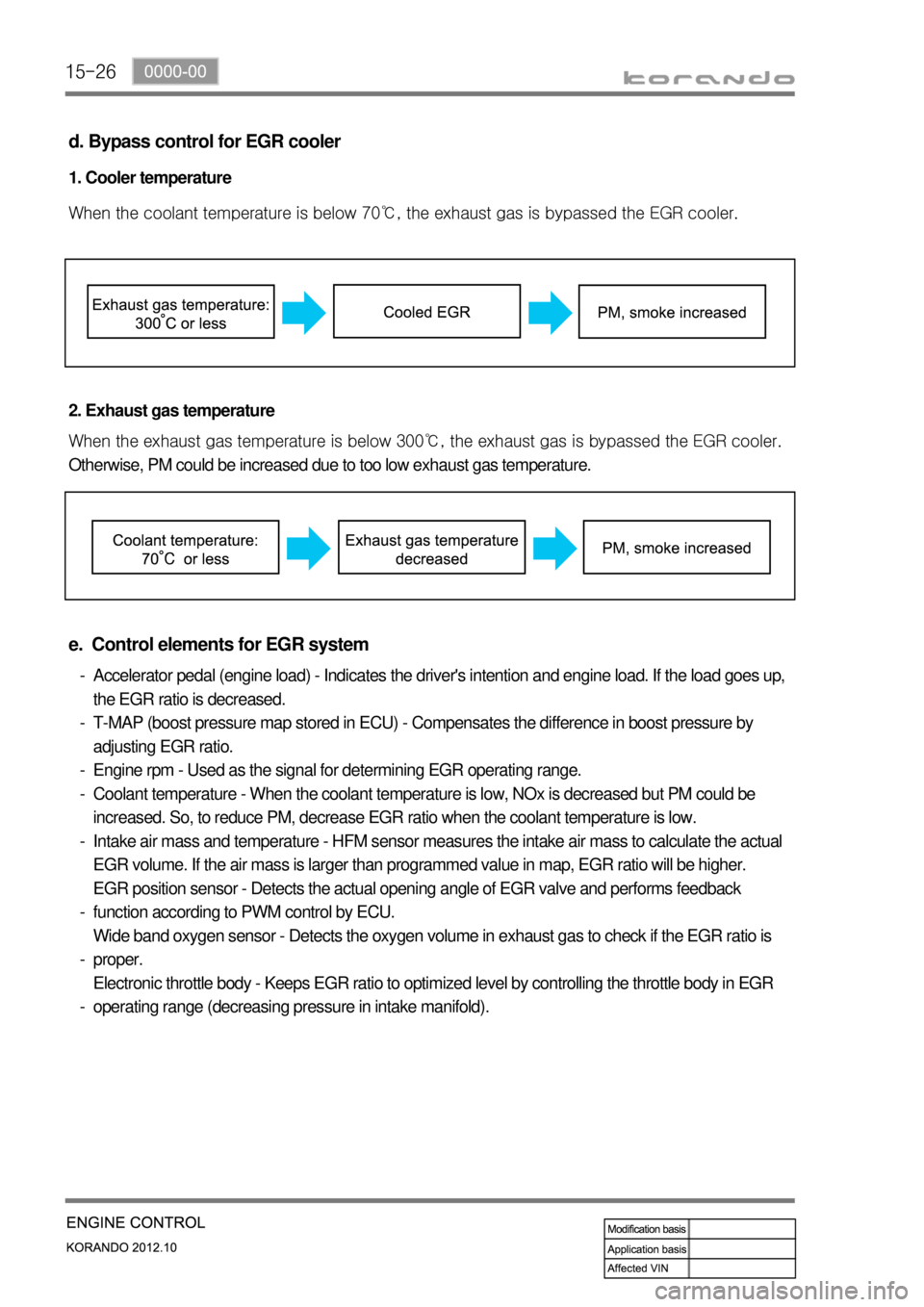
15-26
d. Bypass control for EGR cooler
1. Cooler temperature
<007e008f008c00950047009b008f008c0047008a00960096009300880095009b0047009b008c00940097008c00990088009b009c0099008c00470090009a00470089008c00930096009e0047005e00570b4500530047009b008f008c0047008c009f008f00
88009c009a009b0047008e0088009a00470090009a00470089>ypassed the EGR cooler.
2. Exhaust gas temperature
<007e008f008c00950047009b008f008c0047008c009f008f0088009c009a009b0047008e0088009a0047009b008c00940097008c00990088009b009c0099008c00470090009a00470089008c00930096009e0047005a005700570b4500530047009b008f00
8c0047008c009f008f0088009c009a009b0047008e0088009a> is bypassed the EGR cooler.
Otherwise, PM could be increased due to too low exhaust gas temperature.
e. Control elements for EGR system
Accelerator pedal (engine load) - Indicates the driver's intention and engine load. If the load goes up,
the EGR ratio is decreased.
T-MAP (boost pressure map stored in ECU) - Compensates the difference in boost pressure by
adjusting EGR ratio.
Engine rpm - Used as the signal for determining EGR operating range.
Coolant temperature - When the coolant temperature is low, NOx is decreased but PM could be
increased. So, to reduce PM, decrease EGR ratio when the coolant temperature is low.
Intake air mass and temperature - HFM sensor measures the intake air mass to calculate the actual
EGR volume. If the air mass is larger than programmed value in map, EGR ratio will be higher.
EGR position sensor - Detects the actual opening angle of EGR valve and performs feedback
function according to PWM control by ECU.
Wide band oxygen sensor - Detects the oxygen volume in exhaust gas to check if the EGR ratio is
proper.
Electronic throttle body - Keeps EGR ratio to optimized level by controlling the throttle body in EGR
operating range (decreasing pressure in intake manifold). -
-
-
-
-
-
-
-
Page 304 of 1082
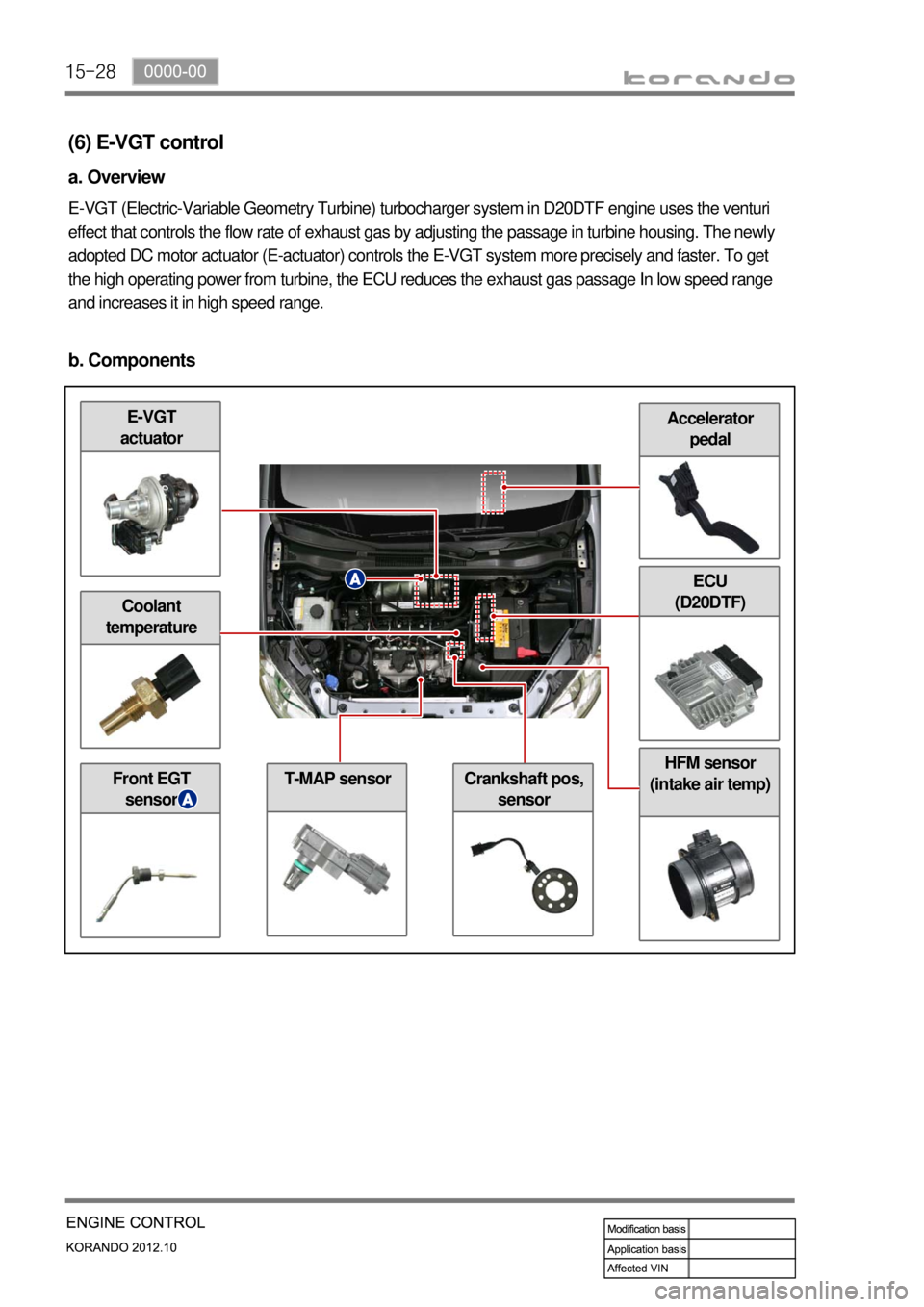
15-28
Accelerator
pedal
(6) E-VGT control
a. Overview
E-VGT (Electric-Variable Geometry Turbine) turbocharger system in D20DTF engine uses the venturi
effect that controls the flow rate of exhaust gas by adjusting the passage in turbine housing. The newly
adopted DC motor actuator (E-actuator) controls the E-VGT system more precisely and faster. To get
the high operating power from turbine, the ECU reduces the exhaust gas passage In low speed range
and increases it in high speed range.
b. Components
E-VGT
actuator
Coolant
temperature
Front EGT
sensorT-MAP sensorCrankshaft pos,
sensor
HFM sensor
(intake air temp)
ECU
(D20DTF)
Page 306 of 1082
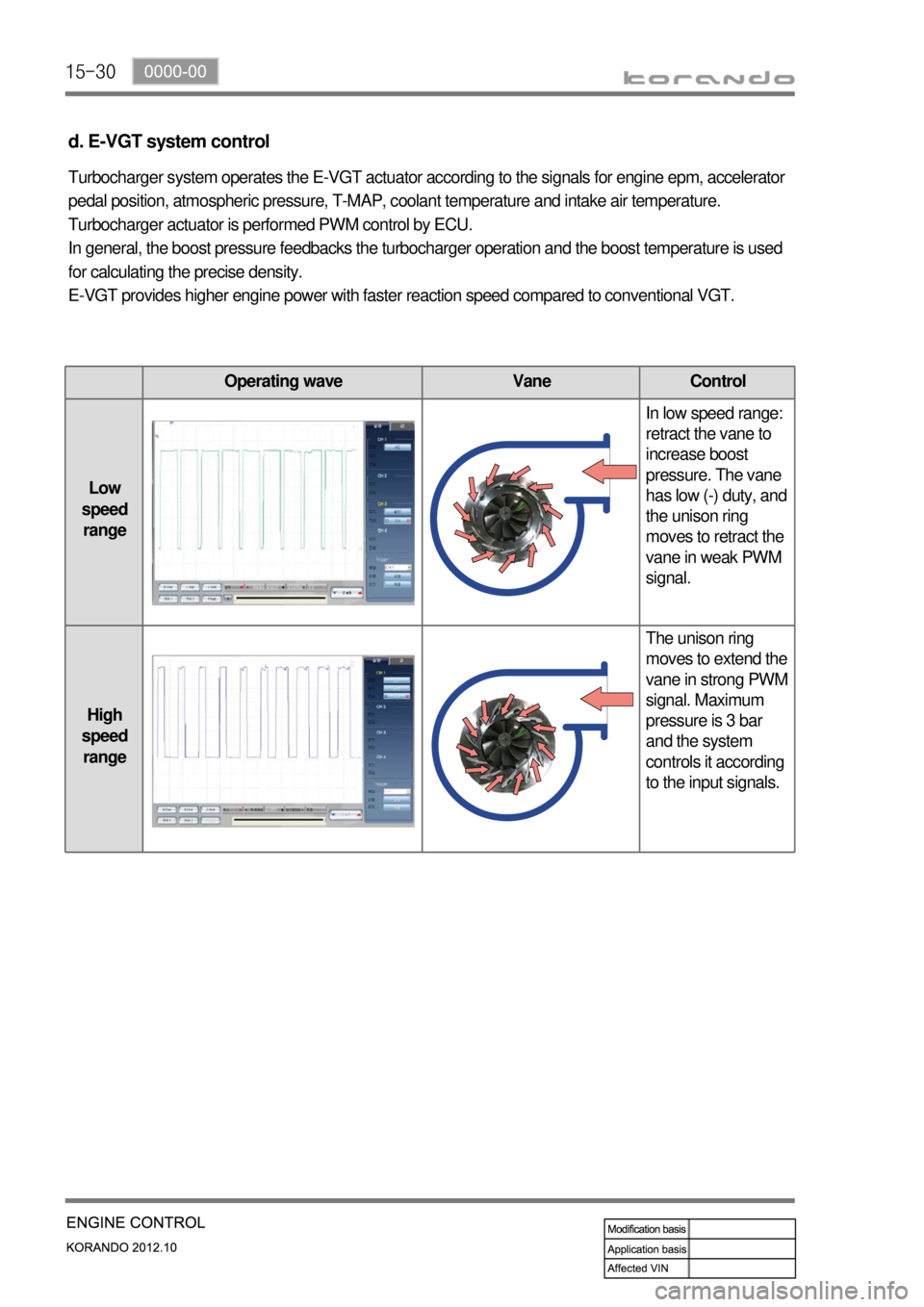
15-30
d. E-VGT system control
Turbocharger system operates the E-VGT actuator according to the signals for engine epm, accelerator
pedal position, atmospheric pressure, T-MAP, coolant temperature and intake air temperature.
Turbocharger actuator is performed PWM control by ECU.
In general, the boost pressure feedbacks the turbocharger operation and the boost temperature is used
for calculating the precise density.
E-VGT provides higher engine power with faster reaction speed compared to conventional VGT.
Operating wave Vane Control
Low
speed
rangeIn low speed range:
retract the vane to
increase boost
pressure. The vane
has low (-) duty, and
the unison ring
moves to retract the
vane in weak PWM
signal.
High
speed
rangeThe unison ring
moves to extend the
vane in strong PWM
signal. Maximum
pressure is 3 bar
and the system
controls it according
to the input signals.
Page 310 of 1082
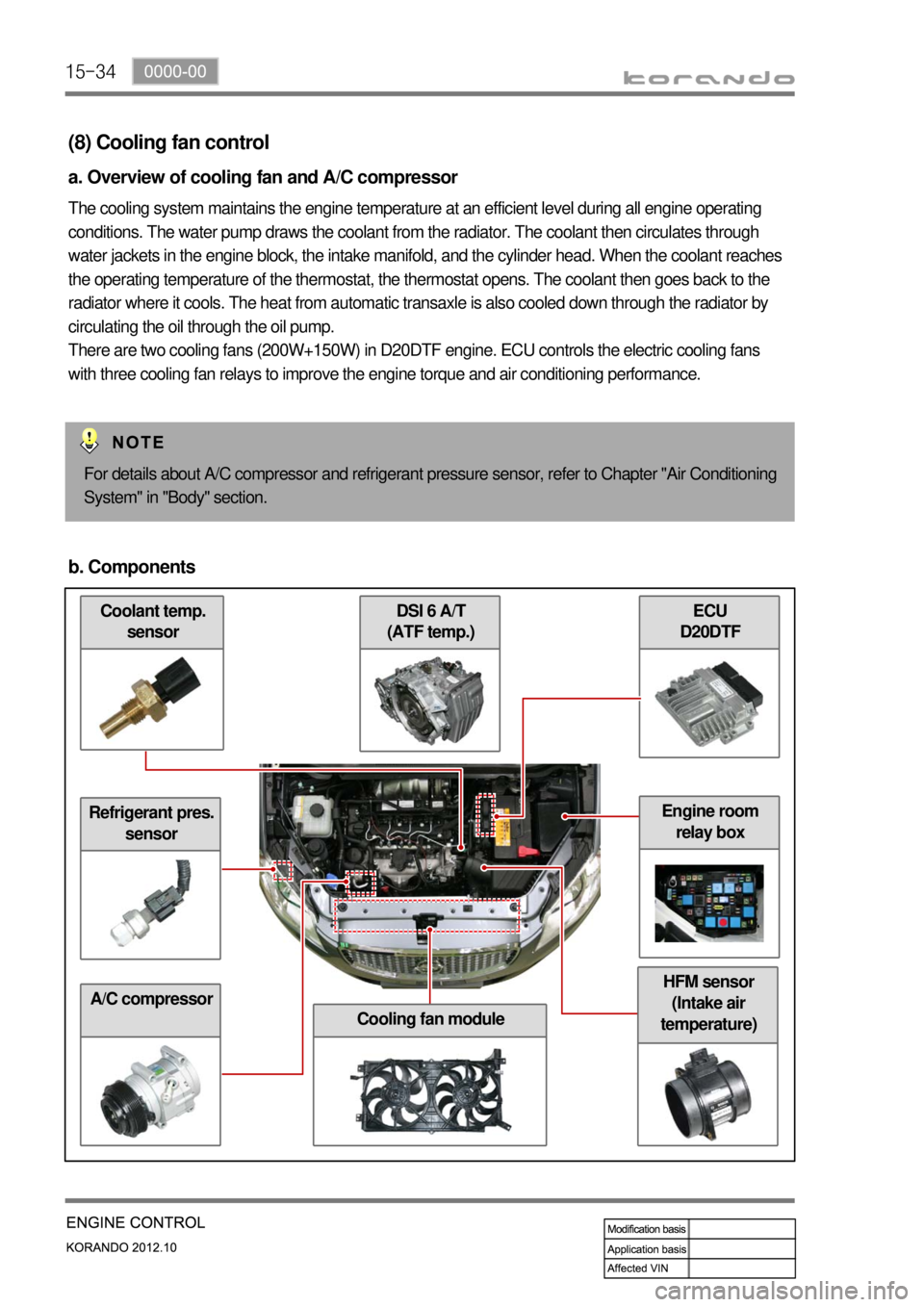
15-34
Coolant temp.
sensor
(8) Cooling fan control
a. Overview of cooling fan and A/C compressor
The cooling system maintains the engine temperature at an efficient level during all engine operating
conditions. The water pump draws the coolant from the radiator. The coolant then circulates through
water jackets in the engine block, the intake manifold, and the cylinder head. When the coolant reaches
the operating temperature of the thermostat, the thermostat opens. The coolant then goes back to the
radiator where it cools. The heat from automatic transaxle is also cooled down through the radiator by
circulating the oil through the oil pump.
There are two cooling fans (200W+150W) in D20DTF engine. ECU controls the electric cooling fans
with three cooling fan relays to improve the engine torque and air conditioning performance.
For details about A/C compressor and refrigerant pressure sensor, refer to Chapter "Air Conditioning
System" in "Body" section.
b. Components
Refrigerant pres.
sensor
A/C compressor
ECU
D20DTF DSI 6 A/T
(ATF temp.)
Cooling fan module
HFM sensor
(Intake air
temperature)
Engine room
relay box
Page 312 of 1082
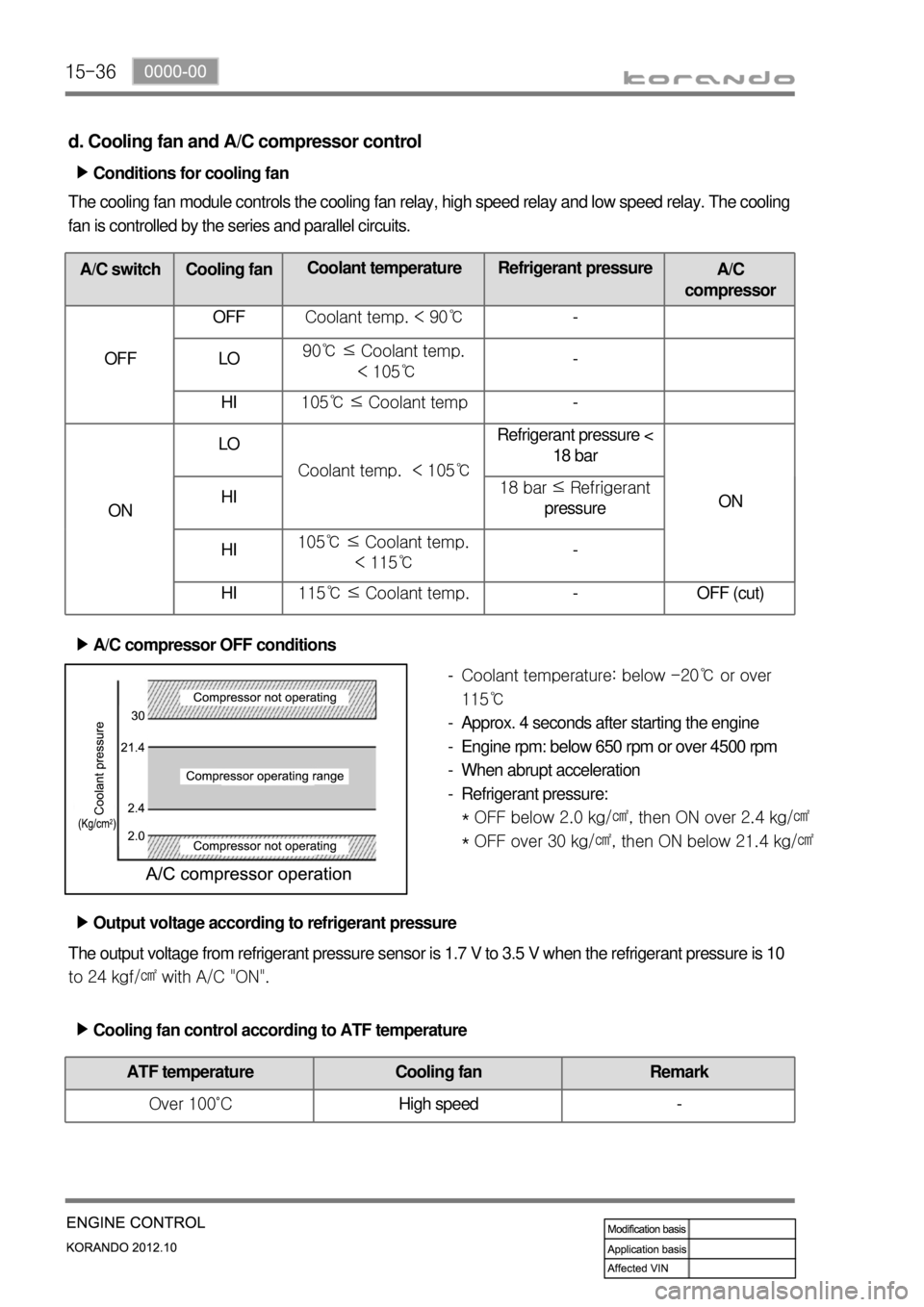
15-36
d. Cooling fan and A/C compressor control
Conditions for cooling fan â–¶
The cooling fan module controls the cooling fan relay, high speed relay and low speed relay. The cooling
fan is controlled by the series and parallel circuits.
A/C switch Cooling fanCoolant temperature Refrigerant pressure
A/C
compressor
OFF OFF Coolant temp. < 90℃-
LO 90℃ ≤ Coolant temp.
< 105℃-
HI105℃ ≤ Coolant temp-
ONLO
Coolant temp. < 105℃Refrigerant pressure <
18 bar
ON HI18 bar ≤ Refrigerant
pressure
HI105℃ ≤ Coolant temp.
< 115℃-
HI115℃ ≤ Coolant temp. - OFF (cut)
A/C compressor OFF conditions â–¶
Coolant temperature: below -20℃ or over
115℃
Approx. 4 seconds after starting the engine
Engine rpm: below 650 rpm or over 4500 rpm
When abrupt acceleration
Refrigerant pressure:
* OFF below 2.0 kg/㎠, then ON over 2.4 kg/ãŽ
* OFF over 30 kg/㎠, then ON below 21.4 kg/㎠-
-
-
-
-
The output voltage from refrigerant pressure sensor is 1.7 V to 3.5 V when the refrigerant pressure is 10
to 24 kgf/㎠with A/C "ON".Output voltage according to refrigerant pressure ▶
Cooling fan control according to ATF temperature â–¶
ATF temperature Cooling fan Remark
Over 100ËšCHigh speed -
Page 313 of 1082
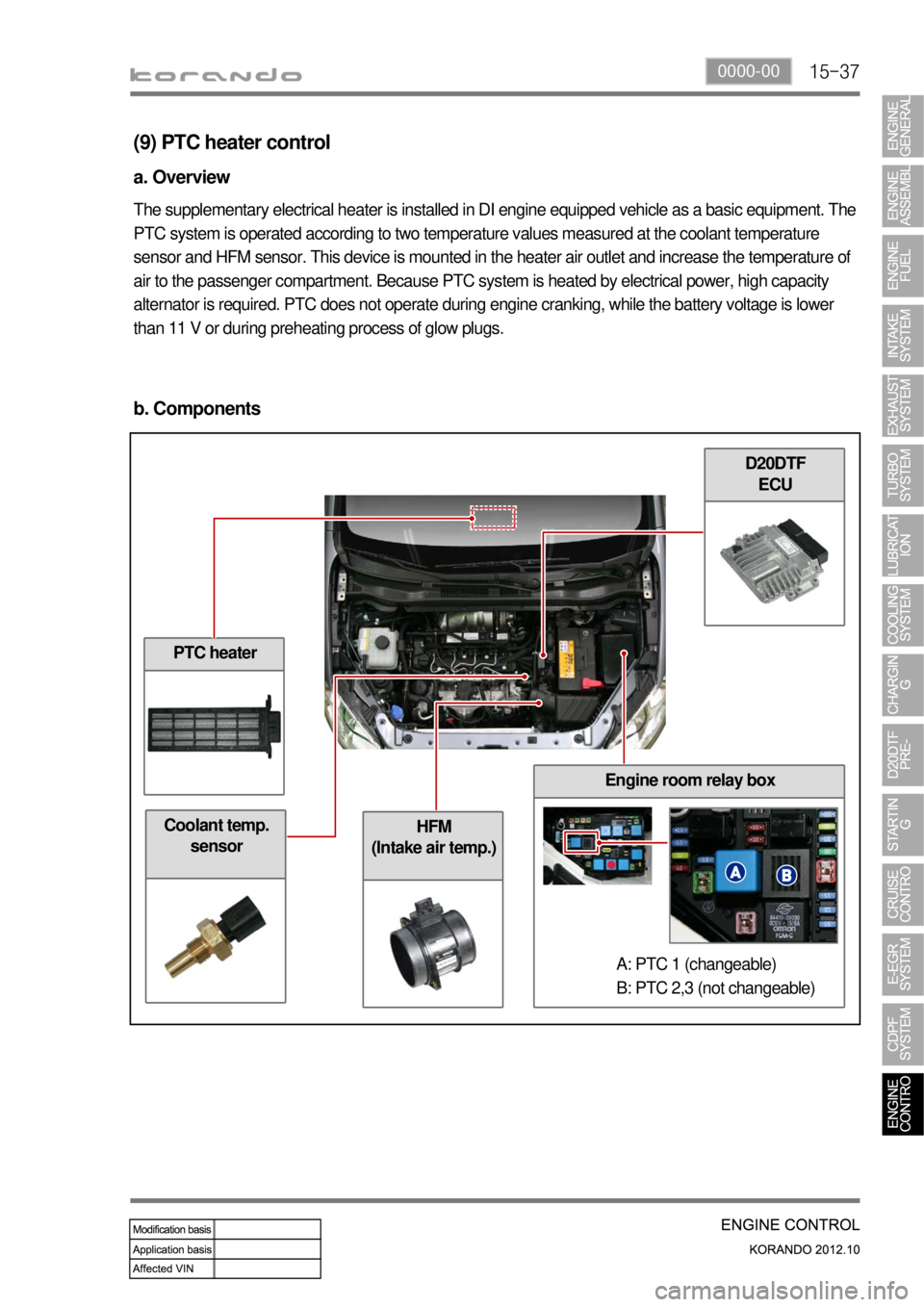
15-370000-00
HFM
(Intake air temp.)Coolant temp.
sensor
(9) PTC heater control
a. Overview
The supplementary electrical heater is installed in DI engine equipped vehicle as a basic equipment. The
PTC system is operated according to two temperature values measured at the coolant temperature
sensor and HFM sensor. This device is mounted in the heater air outlet and increase the temperature of
air to the passenger compartment. Because PTC system is heated by electrical power, high capacity
alternator is required. PTC does not operate during engine cranking, while the battery voltage is lower
than 11 V or during preheating process of glow plugs.
b. Components
PTC heater
D20DTF
ECU
Engine room relay box
A: PTC 1 (changeable)
B: PTC 2,3 (not changeable)
Page 315 of 1082
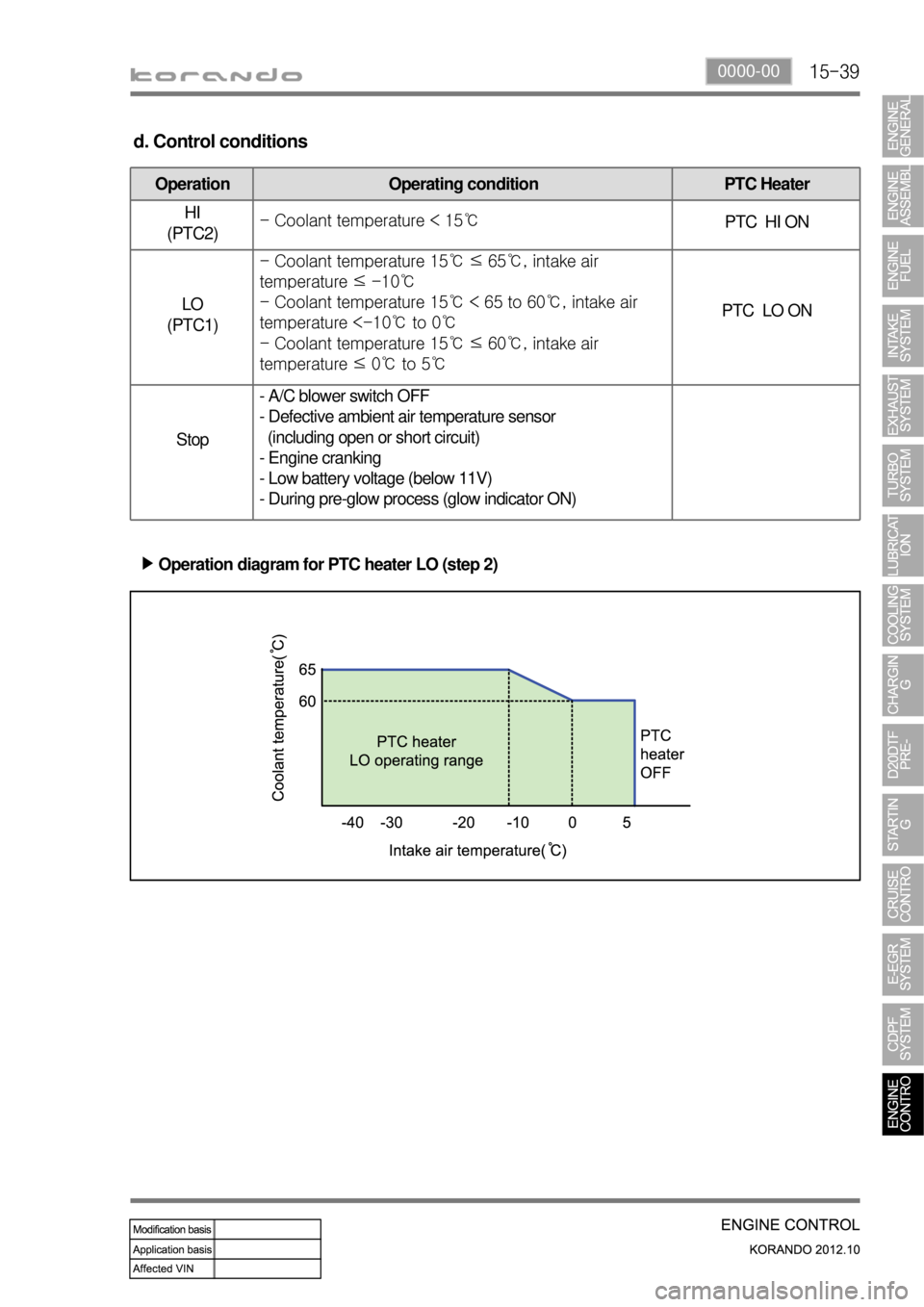
15-390000-00
d. Control conditions
Operation Operating condition PTC Heater
HI
(PTC2)- Coolant temperature < 15℃
PTC HI ON
LO
(PTC1)- Coolant temperature 15℃ ≤ 65℃, intake air
temperature ≤ -10℃
- Coolant temperature 15℃ < 65 to 60℃, intake air
temperature <-10℃ to 0℃
- Coolant temperature 15℃ ≤ 60℃, intake air
temperature ≤ 0℃ to 5℃PTC LO ON
Stop- A/C blower switch OFF
- Defective ambient air temperature sensor
(including open or short circuit)
- Engine cranking
- Low battery voltage (below 11V)
- During pre-glow process (glow indicator ON)
Operation diagram for PTC heater LO (step 2) â–¶