SSANGYONG MUSSO 1998 Workshop Repair Manual
MUSSO 1998
SSANGYONG
SSANGYONG
https://www.carmanualsonline.info/img/67/57510/w960_57510-0.png
SSANGYONG MUSSO 1998 Workshop Repair Manual
Page 409 of 1463
OM600 ENGINE MECHANICAL 1B3-107
Removal & Installation Procedure
1. Remove the nuts (8) uniformly and then remove the washer
(7), exhaust manifold (9) and gasket.
Installation Notice
Check the stud bolt (6) for damage and replace if necessary.
Tighten Torque 12 Nm
Tighten Torque 25 Nm
Tools Required
102 589 03 40 00 Magnetic Bar
116 589 06 63 00 Magnetic Finger
601 589 01 59 00 Assembling Board
601 589 02 59 00 Supporting Bridge
667 589 00 31 00 Press Lever
Replace the gasket and tighten the nuts (8).
2. Install the assembling board (11) to the cylinder head with 4
cylinder head blots (10).
Assembling Board 601 589 01 59 00
3. Pull out the valve tappet (1) with magnetic bar (12).
Notice
Place the valve tappets upside down (open end upward).
Magnetic Bar 102 589 03 40 00
4. Install the supporting bridge (13) on the cylinder head (5).
Supporting Bridge 601 589 02 59 00
Page 440 of 1463
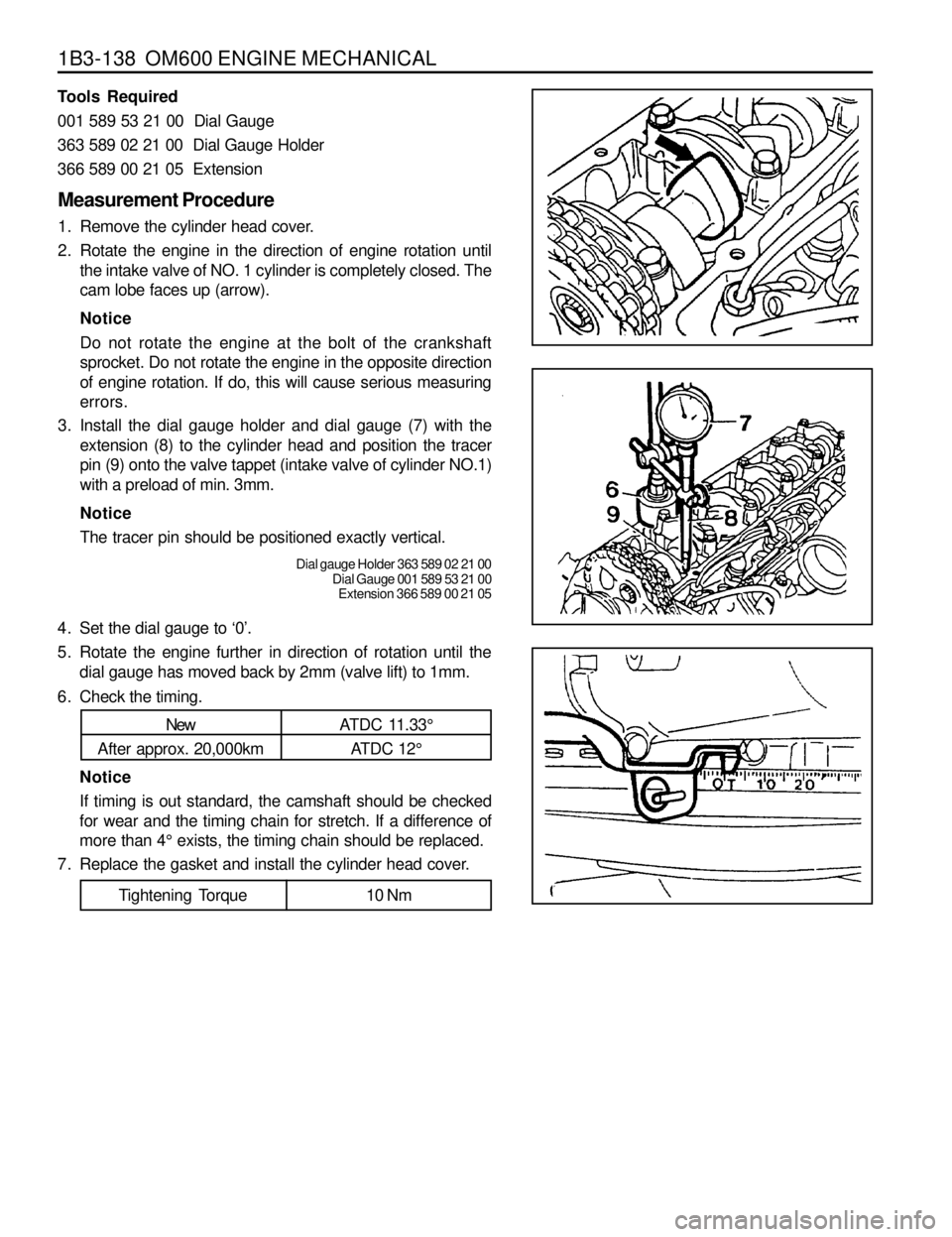
1B3-138 OM600 ENGINE MECHANICAL
6. Check the timing.
New
After approx. 20,000kmATDC 11.33°
ATDC 12°
Notice
If timing is out standard, the camshaft should be checked
for wear and the timing chain for stretch. If a difference of
more than 4° exists, the timing chain should be replaced.
7. Replace the gasket and install the cylinder head cover.
Tightening Torque 10 Nm
Measurement Procedure
1. Remove the cylinder head cover.
2. Rotate the engine in the direction of engine rotation until
the intake valve of NO. 1 cylinder is completely closed. The
cam lobe faces up (arrow).
Notice
Do not rotate the engine at the bolt of the crankshaft
sprocket. Do not rotate the engine in the opposite direction
of engine rotation. If do, this will cause serious measuring
errors.
3. Install the dial gauge holder and dial gauge (7) with the
extension (8) to the cylinder head and position the tracer
pin (9) onto the valve tappet (intake valve of cylinder NO.1)
with a preload of min. 3mm.
Notice
The tracer pin should be positioned exactly vertical.
Dial gauge Holder 363 589 02 21 00
Dial Gauge 001 589 53 21 00
Extension 366 589 00 21 05
4. Set the dial gauge to ‘0’.
5. Rotate the engine further in direction of rotation until the
dial gauge has moved back by 2mm (valve lift) to 1mm.
Tools Required
001 589 53 21 00 Dial Gauge
363 589 02 21 00 Dial Gauge Holder
366 589 00 21 05 Extension
Page 445 of 1463
OM600 ENGINE MECHANICAL 1B3-143
5. Tighten the camshaft bearing cap bolts acccording to
installation order.
6. Install the camshaft sprocket to be aligned the markings of
the camshaft / camshaft bearing cap (arrow).
Notice
Align the alignment marks on the timing chain and sprocket.
Tightening Torque 25 Nm
Notice
Tighten the No. 1 bolts (light arrow) by one revolution in
stages first and then tighten the No.2 bolts (dark arrow).
OM 661LA OM 662LA
7. Tighten the camshaft sprocket bolt.
Tightening Torque 25Nm + 90°
Page 446 of 1463
1B3-144 OM600 ENGINE MECHANICAL
10. Check the TDC marking of OT on the crankshaft.8. Install the chain tensioner.
Tightening Torque 80 Nm
Notice
Replace the seal.
Before installation, by pumping in the oil approx. 10 times,
fill the oil.
9. Remove the engine lock.
Notice
If max. length ‘L’ of the 12-sided bolt exceeds 53.6mm,
replace it.
Page 452 of 1463
1B3-150 OM600 ENGINE MECHANICAL
In this position, the marking on camshaft / camshaft bearing
cap (arrow) must also be aligned. If the markings are not
aligned, the timing chain must be re-set and the injection
pump timing has to be set.
14. Position the no.1 cylinder at TDC.
11. Place the fitting tool (8) onto the chain link and rivet the
chain pins one by one.
12. Check the riveting of chain pins and re-rivet if necessary.
13. Remove the wire.
Tightening Torque 35 - 40 Nm
Page 456 of 1463
1B3-154 OM600 ENGINE MECHANICAL
4. Position the no. 1 cylinder at the TDC of OT.
6. Pull out the bearing pins (9, 11) with sliding hammer and
remove the guide rail 10.
Sliding Hammer 116 589 20 33 00
Threaded Pin 116 589 02 34 00
Installation Procedure
1. Apply collar of both bearing pins with sealing compound.
2. Position the guide rail and insert the bearing pins.
3. Install the camshaft sprocket.
Tightening Torque 10 Nm
Notice
If the max. length ‘L’ of the 12-sided bolt exceeds 53.6mm,
replace it.
Page 457 of 1463
OM600 ENGINE MECHANICAL 1B3-155
In this position, the marking on the camshaft / camshaft
bearing cap (arrow) must also be aligned.
5. Install the guide pulley (12).
Tightening Torque 23 Nm
6. Attach the tensioning lever (7) to the spring (15) and install.
7. Replace the gasket and install the cylinder head cover.
Tightening Torque 10 Nm
Page 463 of 1463
OM600 ENGINE MECHANICAL 1B3-161
Installation Procedure
1. Put the same alignment mark on the new crankshaft
sprocket as in the old sprocket.
Notice
Check the timing chain, camshaft sprocket, injection pump
timing sprocket, oil pump chain and oil pump sprocket for
wear and replace if necessary.
2. Install the new crankshaft sprocket (12) by using a drift (21).
Notice
Align the groove of sprocket and woodruff key (arrow)
exactly.
Drift 116 589 07 15 00
3. Fit the timing chain (4) on the crankshaft sprocket (12).
Notice
Align the alignment marks (arrow) on the chain and sprocket.
4. Install the camshaft sprocket (3).
Tightening Torque 25 Nm + 90°
Notice
Pay attention on the alignment marks and dowel pin (arrow).
Page 470 of 1463
1B3-168 OM600 ENGINE MECHANICAL
12. Coat the bolts (12) with oil and then tighten the bolts.
Tightening Torque 40Nm + 90°
13. Rotate the crankshaft and check axial clearance between
the connecting rod and crankshaft.
14. Measure clearance between the piston crown and cylinder
StandardMax. 0.12mm
15. Position the piston at TDC and measure the distance
between the piston crown and the crankcase surface.
Notice
Measure at points marked.
Dial Gauge 001 589 00 53 21
Dial Gauge Holder 363 589 02 21 00
Standard Max. 0.965 mm
Page 478 of 1463
1B3-176 OM600 ENGINE MECHANICAL
Tightening Torque 10 Nm
3. Unscrew the oil strainer bracket bolt.
4. Remove the oil pump.
5. Unscrew the screw plug and remove the relief valve.
6. Installation should follow the removal procedure in the
reverse order.