clock SSANGYONG MUSSO 1998 Workshop User Guide
[x] Cancel search | Manufacturer: SSANGYONG, Model Year: 1998, Model line: MUSSO, Model: SSANGYONG MUSSO 1998Pages: 1463, PDF Size: 19.88 MB
Page 746 of 1463
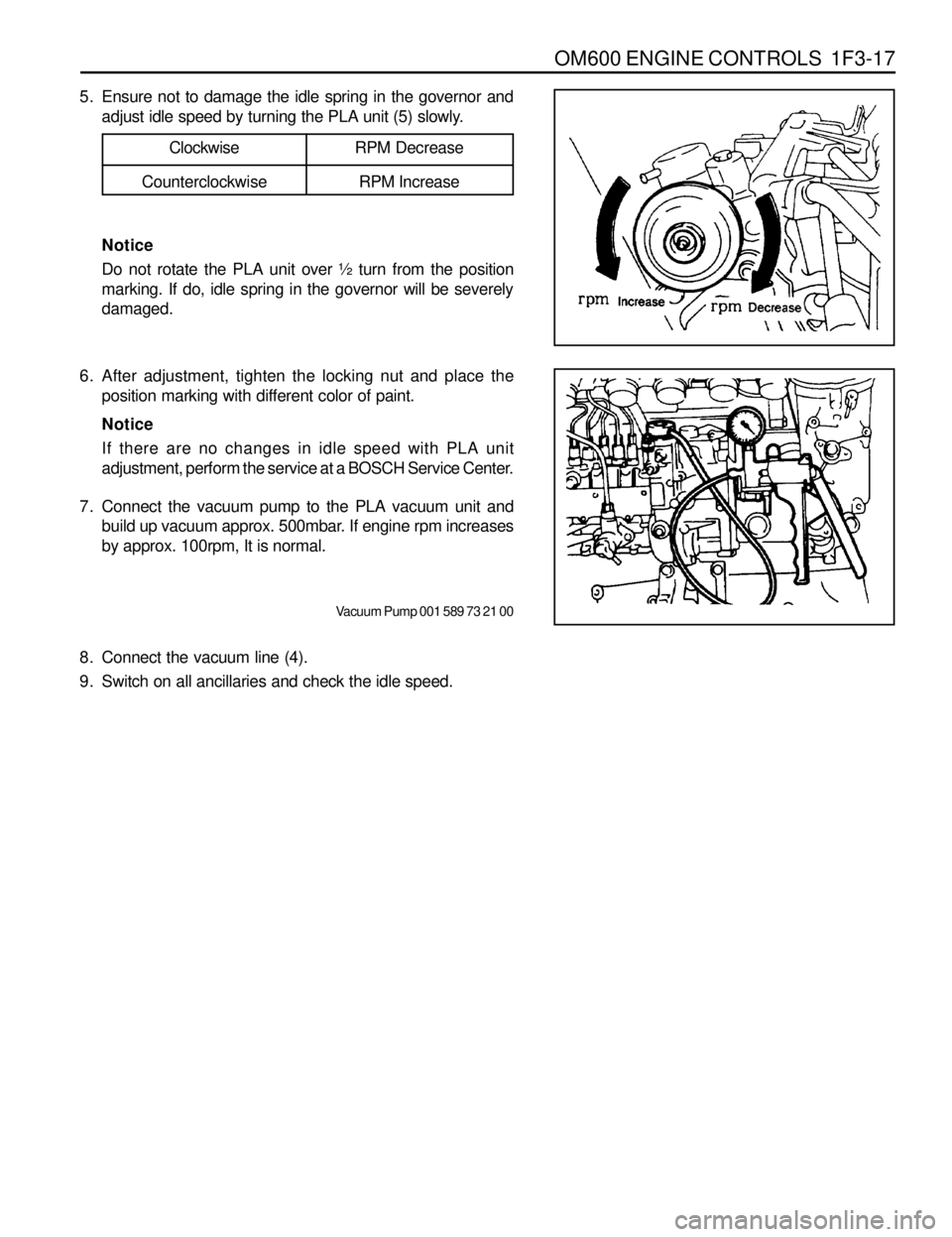
OM600 ENGINE CONTROLS 1F3-17
6. After adjustment, tighten the locking nut and place the
position marking with different color of paint.
Notice
If there are no changes in idle speed with PLA unit
adjustment, perform the service at a BOSCH Service Center.
7. Connect the vacuum pump to the PLA vacuum unit and
build up vacuum approx. 500mbar. If engine rpm increases
by approx. 100rpm, It is normal.
Vacuum Pump 001 589 73 21 00
8. Connect the vacuum line (4).
9. Switch on all ancillaries and check the idle speed.
5. Ensure not to damage the idle spring in the governor and
adjust idle speed by turning the PLA unit (5) slowly.
Notice
Do not rotate the PLA unit over ½ turn from the position
marking. If do, idle spring in the governor will be severely
damaged.Clockwise
Counterclockwise
RPM Decrease
RPM Increase
Page 915 of 1463
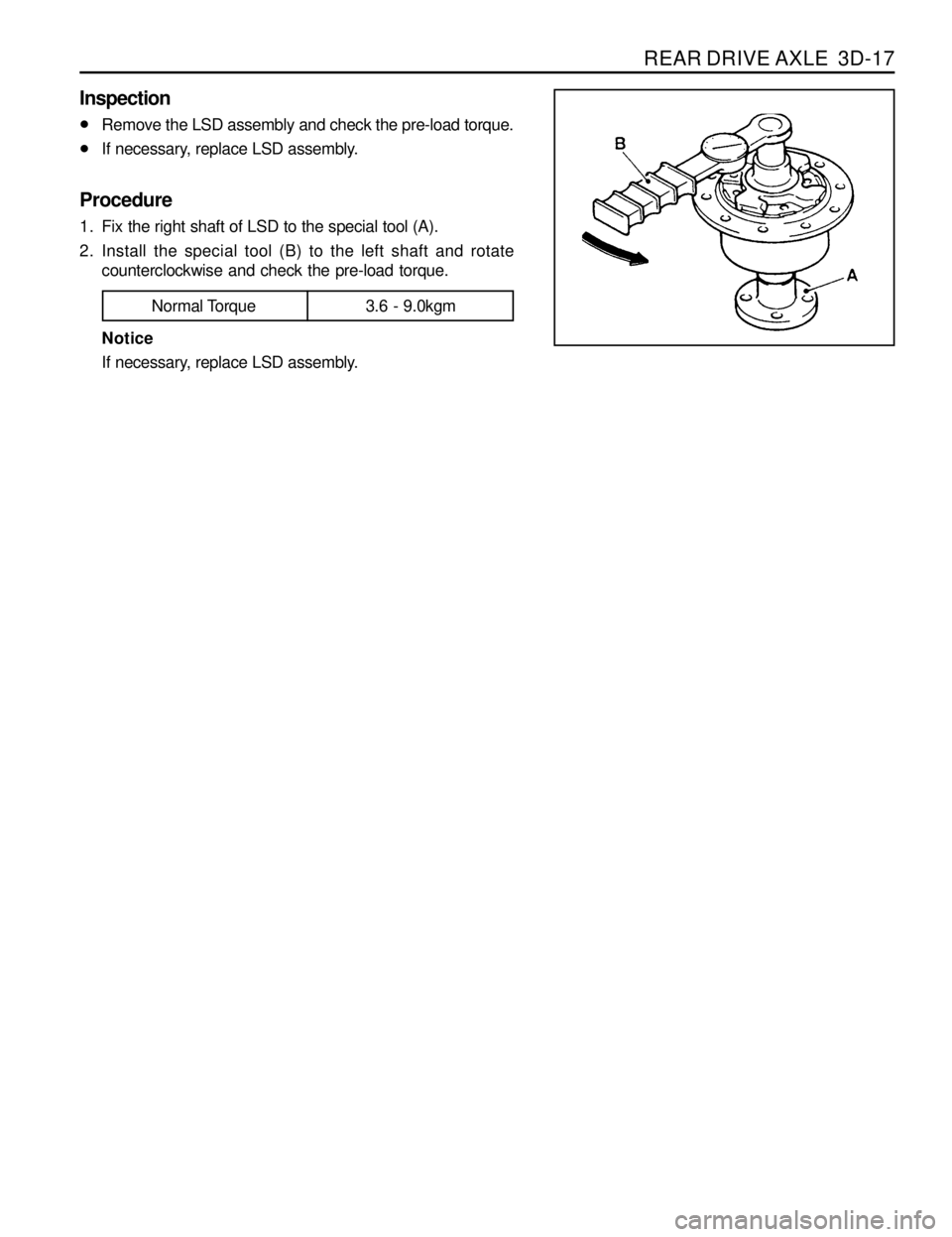
REAR DRIVE AXLE 3D-17
Inspection
lRemove the LSD assembly and check the pre-load torque.
lIf necessary, replace LSD assembly.
Procedure
1. Fix the right shaft of LSD to the special tool (A).
2. Install the special tool (B) to the left shaft and rotate
counterclockwise and check the pre-load torque.
Normal Torque 3.6 - 9.0kgm
Notice
If necessary, replace LSD assembly.
Page 1026 of 1463
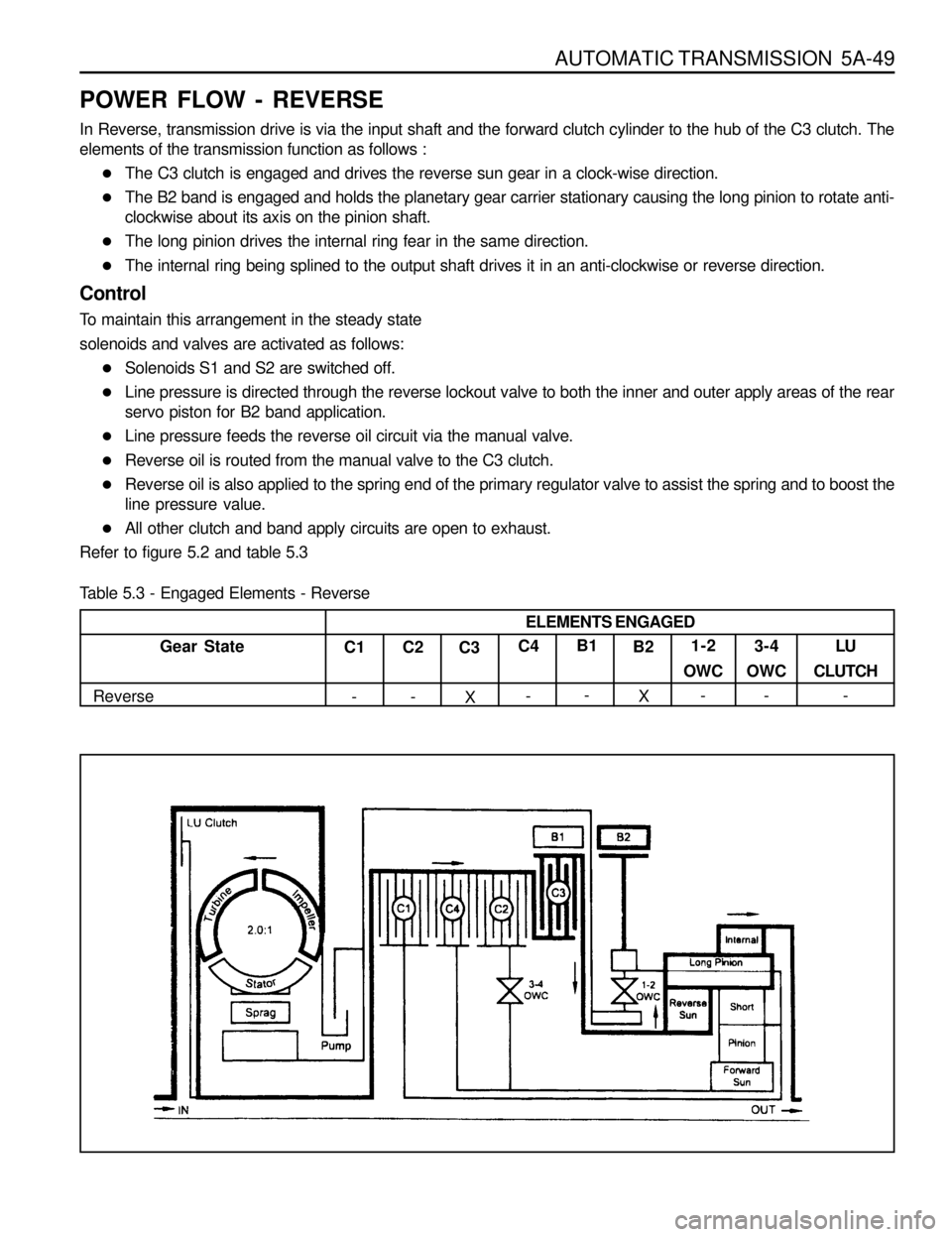
AUTOMATIC TRANSMISSION 5A-49
POWER FLOW - REVERSE
In Reverse, transmission drive is via the input shaft and the forward clutch cylinder to the hub of the C3 clutch. The
elements of the transmission function as follows :
lThe C3 clutch is engaged and drives the reverse sun gear in a clock-wise direction.
lThe B2 band is engaged and holds the planetary gear carrier stationary causing the long pinion to rotate anti-
clockwise about its axis on the pinion shaft.
lThe long pinion drives the internal ring fear in the same direction.
lThe internal ring being splined to the output shaft drives it in an anti-clockwise or reverse direction.
Control
To maintain this arrangement in the steady state
solenoids and valves are activated as follows:
lSolenoids S1 and S2 are switched off.
lLine pressure is directed through the reverse lockout valve to both the inner and outer apply areas of the rear
servo piston for B2 band application.
lLine pressure feeds the reverse oil circuit via the manual valve.
lReverse oil is routed from the manual valve to the C3 clutch.
lReverse oil is also applied to the spring end of the primary regulator valve to assist the spring and to boost the
line pressure value.
lAll other clutch and band apply circuits are open to exhaust.
Refer to figure 5.2 and table 5.3
Table 5.3 - Engaged Elements - Reverse
Gear State
ReverseC1
-C2
-C3
XC4
-B1
-B2
X1-2
OWC
-3-4
OWC
-LU
CLUTCH
- ELEMENTS ENGAGED
Page 1027 of 1463
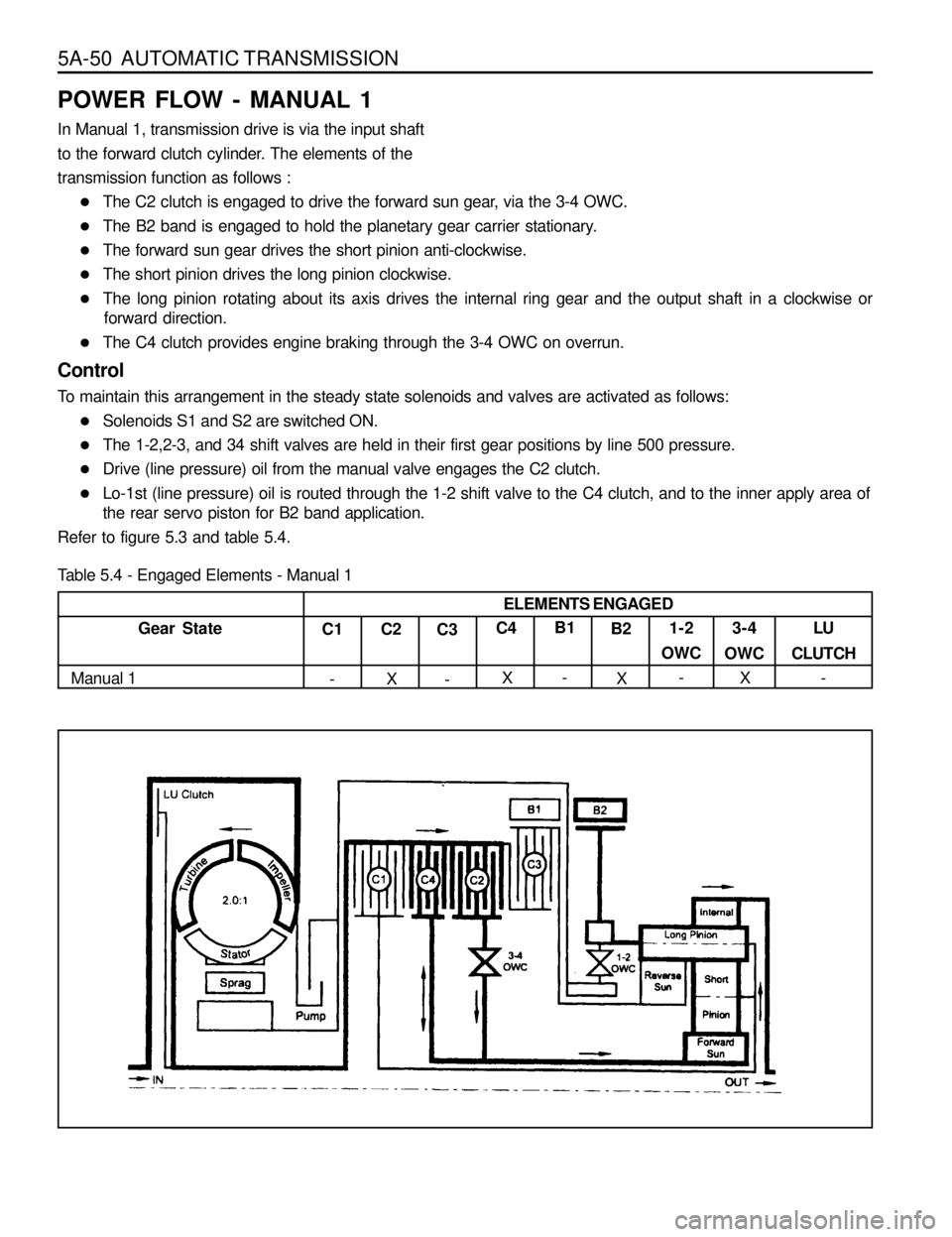
5A-50 AUTOMATIC TRANSMISSION
POWER FLOW - MANUAL 1
In Manual 1, transmission drive is via the input shaft
to the forward clutch cylinder. The elements of the
transmission function as follows :
lThe C2 clutch is engaged to drive the forward sun gear, via the 3-4 OWC.
lThe B2 band is engaged to hold the planetary gear carrier stationary.
lThe forward sun gear drives the short pinion anti-clockwise.
lThe short pinion drives the long pinion clockwise.
lThe long pinion rotating about its axis drives the internal ring gear and the output shaft in a clockwise or
forward direction.
lThe C4 clutch provides engine braking through the 3-4 OWC on overrun.
Control
To maintain this arrangement in the steady state solenoids and valves are activated as follows:
lSolenoids S1 and S2 are switched ON.
lThe 1-2,2-3, and 34 shift valves are held in their first gear positions by line 500 pressure.
lDrive (line pressure) oil from the manual valve engages the C2 clutch.
lLo-1st (line pressure) oil is routed through the 1-2 shift valve to the C4 clutch, and to the inner apply area of
the rear servo piston for B2 band application.
Refer to figure 5.3 and table 5.4.
Table 5.4 - Engaged Elements - Manual 1
Gear State
Manual 1C1
-C2
XC3
-C4
XB1
-B2
X1-2
OWC
-3-4
OWC
XLU
CLUTCH
- ELEMENTS ENGAGED
Page 1028 of 1463
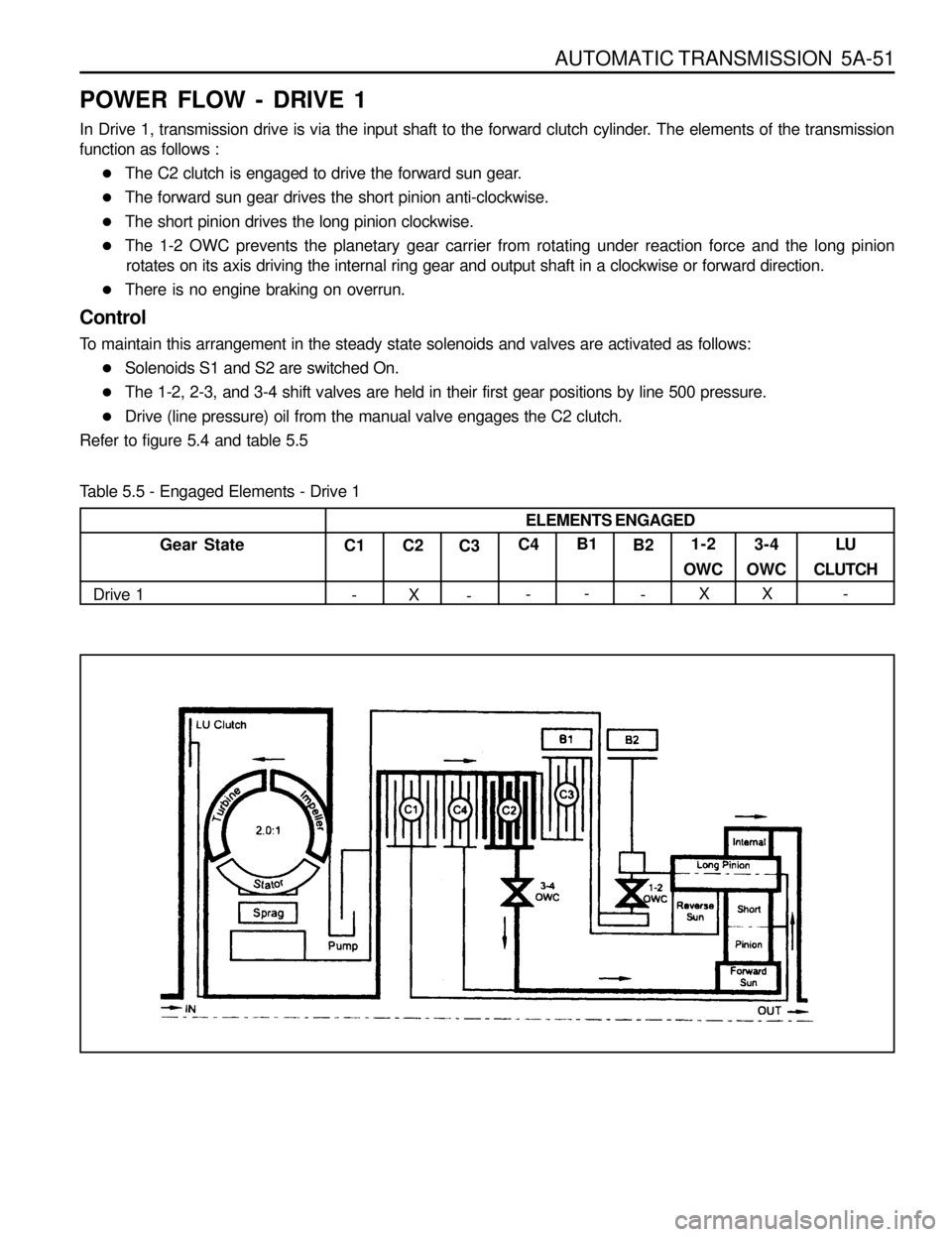
AUTOMATIC TRANSMISSION 5A-51
POWER FLOW - DRIVE 1
In Drive 1, transmission drive is via the input shaft to the forward clutch cylinder. The elements of the transmission
function as follows :
lThe C2 clutch is engaged to drive the forward sun gear.
lThe forward sun gear drives the short pinion anti-clockwise.
lThe short pinion drives the long pinion clockwise.
lThe 1-2 OWC prevents the planetary gear carrier from rotating under reaction force and the long pinion
rotates on its axis driving the internal ring gear and output shaft in a clockwise or forward direction.
lThere is no engine braking on overrun.
Control
To maintain this arrangement in the steady state solenoids and valves are activated as follows:
lSolenoids S1 and S2 are switched On.
lThe 1-2, 2-3, and 3-4 shift valves are held in their first gear positions by line 500 pressure.
lDrive (line pressure) oil from the manual valve engages the C2 clutch.
Refer to figure 5.4 and table 5.5
Table 5.5 - Engaged Elements - Drive 1
Gear State
Drive 1C1
-C2
XC3
-C4
-B1
-B2
-1-2
OWC
X3-4
OWC
XLU
CLUTCH
- ELEMENTS ENGAGED
Page 1029 of 1463
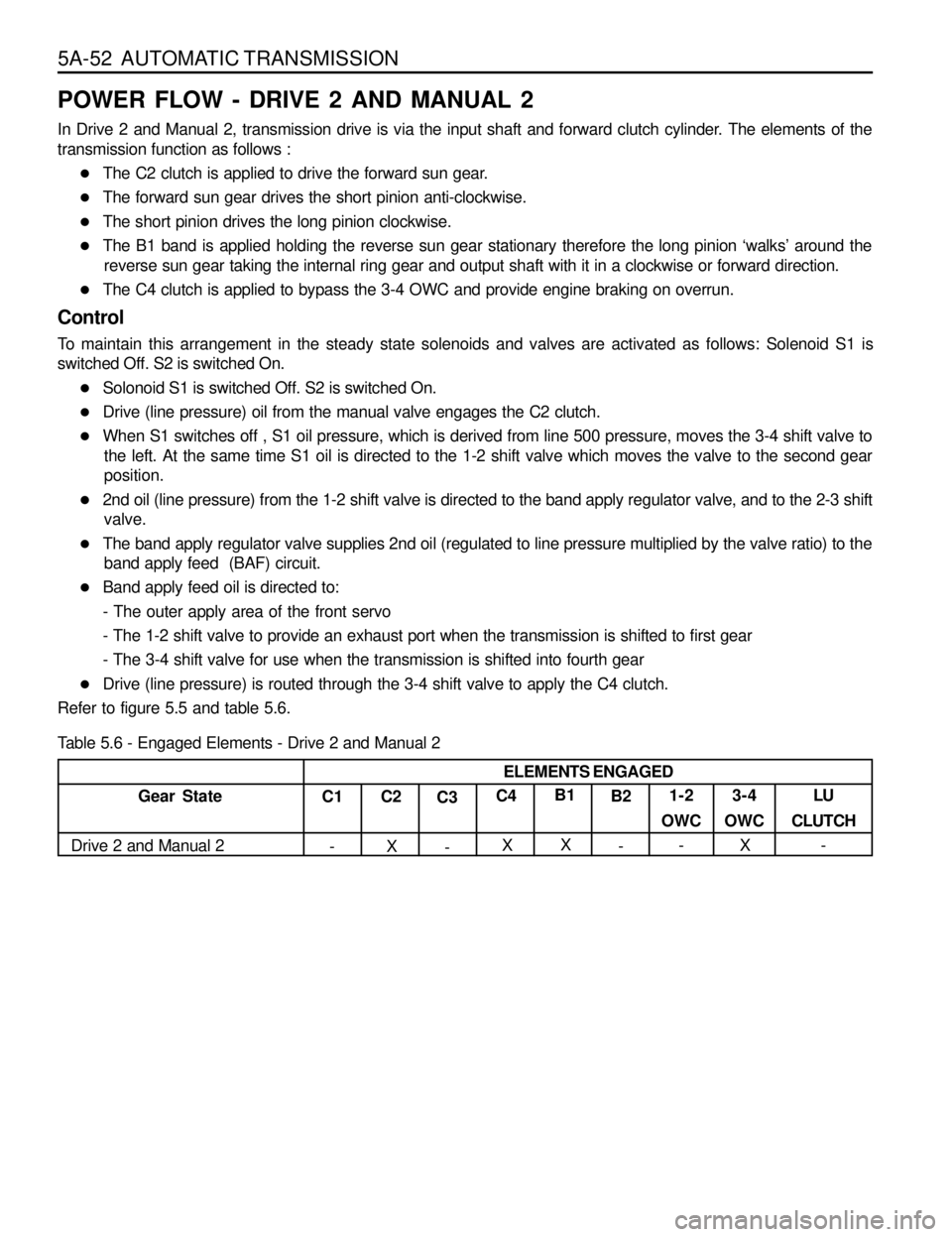
5A-52 AUTOMATIC TRANSMISSION
POWER FLOW - DRIVE 2 AND MANUAL 2
In Drive 2 and Manual 2, transmission drive is via the input shaft and forward clutch cylinder. The elements of the
transmission function as follows :
lThe C2 clutch is applied to drive the forward sun gear.
lThe forward sun gear drives the short pinion anti-clockwise.
lThe short pinion drives the long pinion clockwise.
lThe B1 band is applied holding the reverse sun gear stationary therefore the long pinion ‘walks’ around the
reverse sun gear taking the internal ring gear and output shaft with it in a clockwise or forward direction.
lThe C4 clutch is applied to bypass the 3-4 OWC and provide engine braking on overrun.
Control
To maintain this arrangement in the steady state solenoids and valves are activated as follows: Solenoid S1 is
switched Off. S2 is switched On.
lSolonoid S1 is switched Off. S2 is switched On.
lDrive (line pressure) oil from the manual valve engages the C2 clutch.
lWhen S1 switches off , S1 oil pressure, which is derived from line 500 pressure, moves the 3-4 shift valve to
the left. At the same time S1 oil is directed to the 1-2 shift valve which moves the valve to the second gear
position.
l2nd oil (line pressure) from the 1-2 shift valve is directed to the band apply regulator valve, and to the 2-3 shift
valve.
lThe band apply regulator valve supplies 2nd oil (regulated to line pressure multiplied by the valve ratio) to the
band apply feed (BAF) circuit.
lBand apply feed oil is directed to:
- The outer apply area of the front servo
- The 1-2 shift valve to provide an exhaust port when the transmission is shifted to first gear
- The 3-4 shift valve for use when the transmission is shifted into fourth gear
lDrive (line pressure) is routed through the 3-4 shift valve to apply the C4 clutch.
Refer to figure 5.5 and table 5.6.
Table 5.6 - Engaged Elements - Drive 2 and Manual 2
Gear State
Drive 2 and Manual 2C1
-C2
XC3
-C4
XB1
XB2
-1-2
OWC
-3-4
OWC
XLU
CLUTCH
- ELEMENTS ENGAGED
Page 1031 of 1463
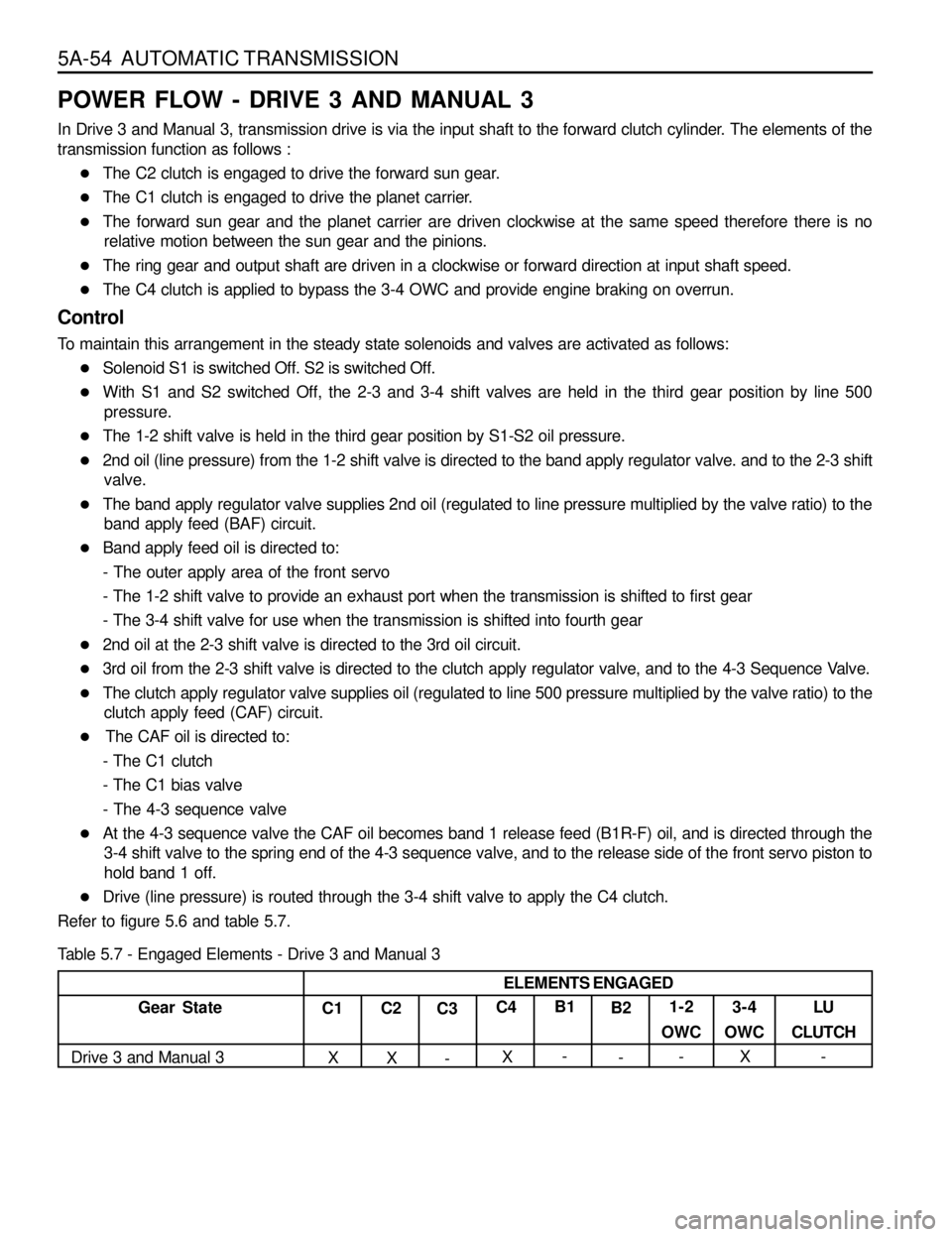
5A-54 AUTOMATIC TRANSMISSION
POWER FLOW - DRIVE 3 AND MANUAL 3
In Drive 3 and Manual 3, transmission drive is via the input shaft to the forward clutch cylinder. The elements of the
transmission function as follows :
lThe C2 clutch is engaged to drive the forward sun gear.
lThe C1 clutch is engaged to drive the planet carrier.
lThe forward sun gear and the planet carrier are driven clockwise at the same speed therefore there is no
relative motion between the sun gear and the pinions.
lThe ring gear and output shaft are driven in a clockwise or forward direction at input shaft speed.
lThe C4 clutch is applied to bypass the 3-4 OWC and provide engine braking on overrun.
Control
To maintain this arrangement in the steady state solenoids and valves are activated as follows:
lSolenoid S1 is switched Off. S2 is switched Off.
lWith S1 and S2 switched Off, the 2-3 and 3-4 shift valves are held in the third gear position by line 500
pressure.
lThe 1-2 shift valve is held in the third gear position by S1-S2 oil pressure.
l2nd oil (line pressure) from the 1-2 shift valve is directed to the band apply regulator valve. and to the 2-3 shift
valve.
lThe band apply regulator valve supplies 2nd oil (regulated to line pressure multiplied by the valve ratio) to the
band apply feed (BAF) circuit.
lBand apply feed oil is directed to:
- The outer apply area of the front servo
- The 1-2 shift valve to provide an exhaust port when the transmission is shifted to first gear
- The 3-4 shift valve for use when the transmission is shifted into fourth gear
l2nd oil at the 2-3 shift valve is directed to the 3rd oil circuit.
l3rd oil from the 2-3 shift valve is directed to the clutch apply regulator valve, and to the 4-3 Sequence Valve.
lThe clutch apply regulator valve supplies oil (regulated to line 500 pressure multiplied by the valve ratio) to the
clutch apply feed (CAF) circuit.
l The CAF oil is directed to:
- The C1 clutch
- The C1 bias valve
- The 4-3 sequence valve
lAt the 4-3 sequence valve the CAF oil becomes band 1 release feed (B1R-F) oil, and is directed through the
3-4 shift valve to the spring end of the 4-3 sequence valve, and to the release side of the front servo piston to
hold band 1 off.
lDrive (line pressure) is routed through the 3-4 shift valve to apply the C4 clutch.
Refer to figure 5.6 and table 5.7.
Table 5.7 - Engaged Elements - Drive 3 and Manual 3
Gear State
Drive 3 and Manual 3C1
XC2
XC3
-C4
XB1
-B2
-1-2
OWC
-3-4
OWC
XLU
CLUTCH
- ELEMENTS ENGAGED
Page 1034 of 1463
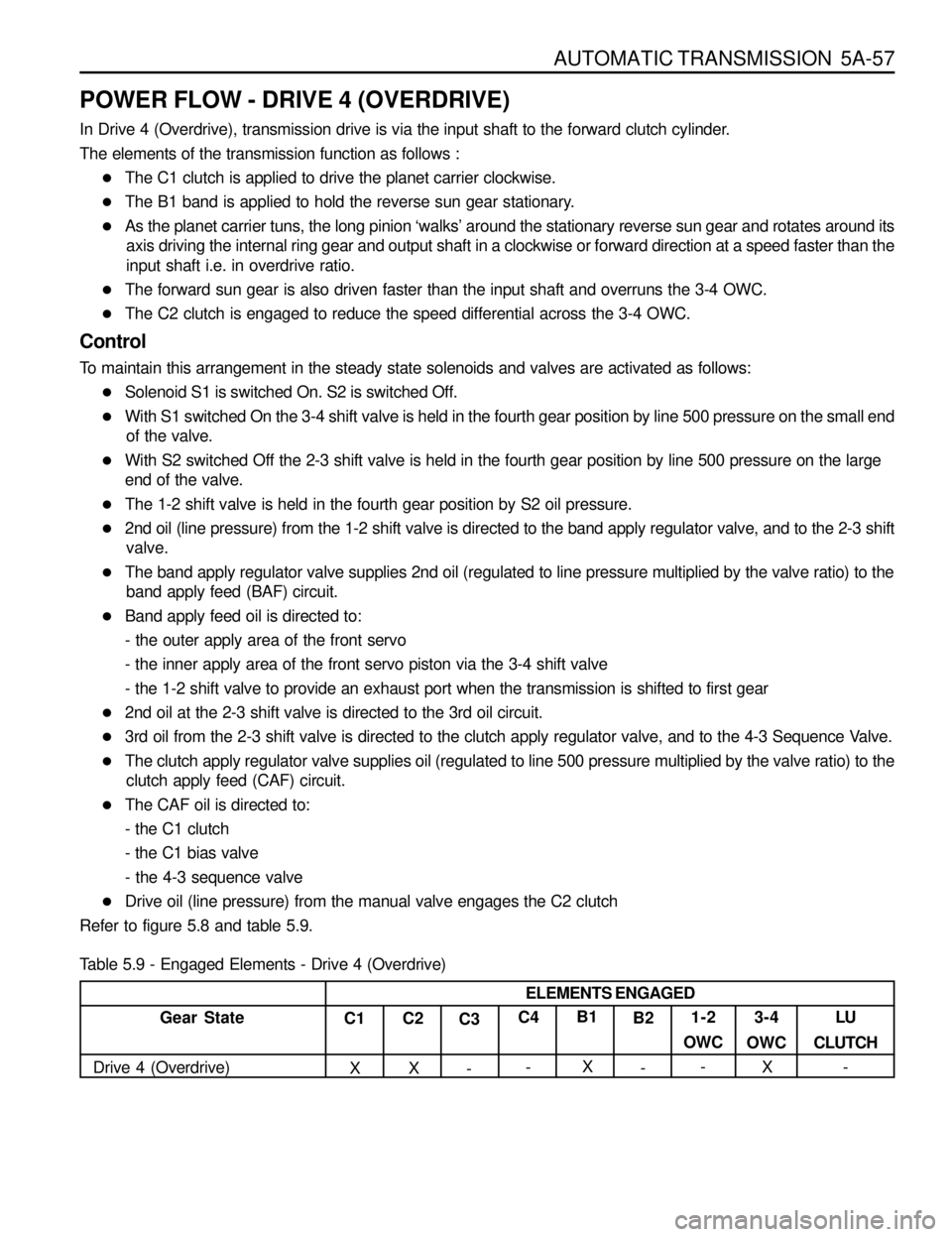
AUTOMATIC TRANSMISSION 5A-57
POWER FLOW - DRIVE 4 (OVERDRIVE)
In Drive 4 (Overdrive), transmission drive is via the input shaft to the forward clutch cylinder.
The elements of the transmission function as follows :
lThe C1 clutch is applied to drive the planet carrier clockwise.
lThe B1 band is applied to hold the reverse sun gear stationary.
lAs the planet carrier tuns, the long pinion ‘walks’ around the stationary reverse sun gear and rotates around its
axis driving the internal ring gear and output shaft in a clockwise or forward direction at a speed faster than the
input shaft i.e. in overdrive ratio.
lThe forward sun gear is also driven faster than the input shaft and overruns the 3-4 OWC.
lThe C2 clutch is engaged to reduce the speed differential across the 3-4 OWC.
Control
To maintain this arrangement in the steady state solenoids and valves are activated as follows:
lSolenoid S1 is switched On. S2 is switched Off.
lWith S1 switched On the 3-4 shift valve is held in the fourth gear position by line 500 pressure on the small end
of the valve.
lWith S2 switched Off the 2-3 shift valve is held in the fourth gear position by line 500 pressure on the large
end of the valve.
lThe 1-2 shift valve is held in the fourth gear position by S2 oil pressure.
l2nd oil (line pressure) from the 1-2 shift valve is directed to the band apply regulator valve, and to the 2-3 shift
valve.
lThe band apply regulator valve supplies 2nd oil (regulated to line pressure multiplied by the valve ratio) to the
band apply feed (BAF) circuit.
lBand apply feed oil is directed to:
- the outer apply area of the front servo
- the inner apply area of the front servo piston via the 3-4 shift valve
- the 1-2 shift valve to provide an exhaust port when the transmission is shifted to first gear
l2nd oil at the 2-3 shift valve is directed to the 3rd oil circuit.
l3rd oil from the 2-3 shift valve is directed to the clutch apply regulator valve, and to the 4-3 Sequence Valve.
lThe clutch apply regulator valve supplies oil (regulated to line 500 pressure multiplied by the valve ratio) to the
clutch apply feed (CAF) circuit.
lThe CAF oil is directed to:
- the C1 clutch
- the C1 bias valve
- the 4-3 sequence valve
lDrive oil (line pressure) from the manual valve engages the C2 clutch
Refer to figure 5.8 and table 5.9.
Table 5.9 - Engaged Elements - Drive 4 (Overdrive)
Gear State
Drive 4 (Overdrive)C1
XC2
XC3
-C4
-B1
XB2
-1-2
OWC
-3-4
OWC
XLU
CLUTCH
- ELEMENTS ENGAGED
Page 1066 of 1463
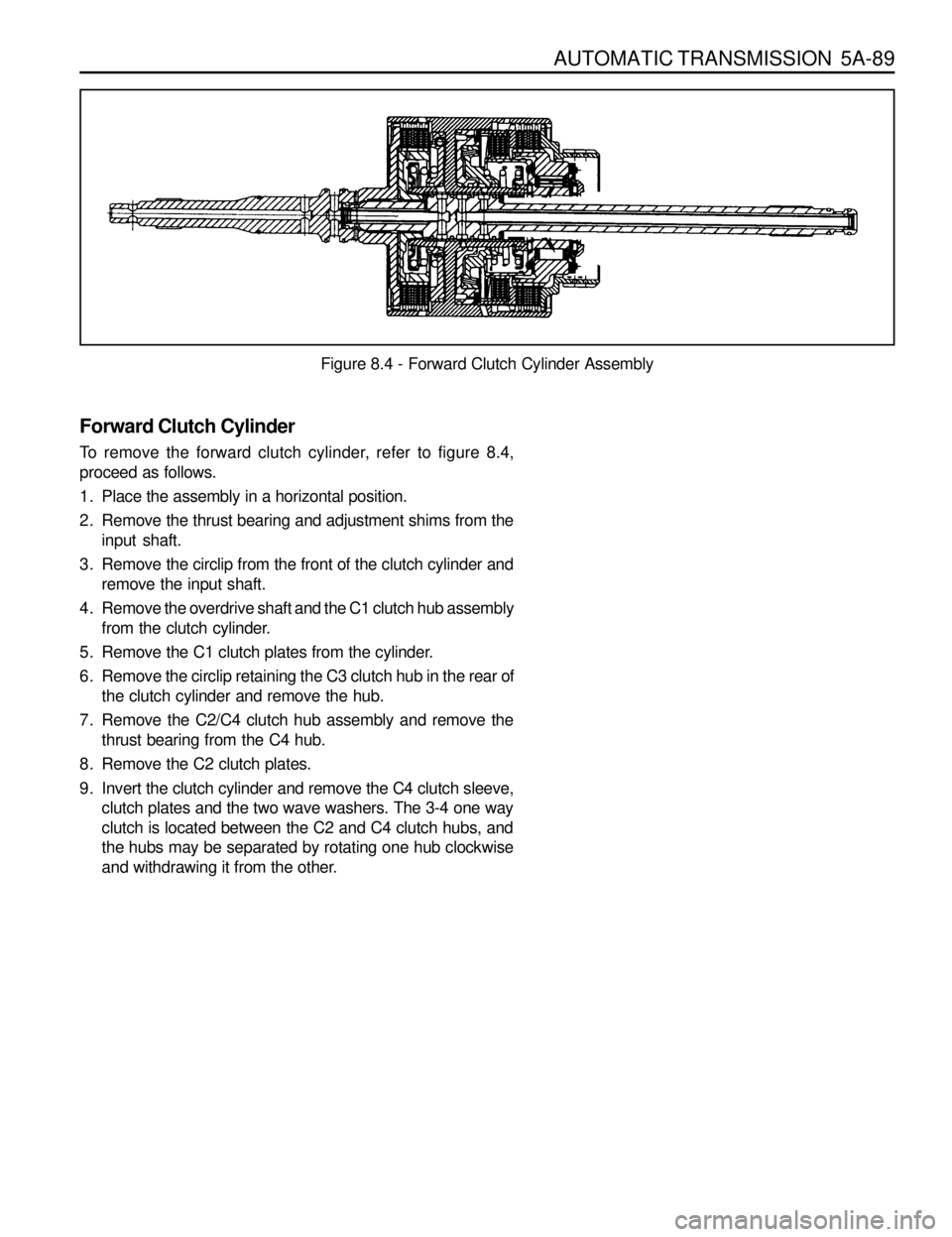
AUTOMATIC TRANSMISSION 5A-89
Forward Clutch Cylinder
To remove the forward clutch cylinder, refer to figure 8.4,
proceed as follows.
1. Place the assembly in a horizontal position.
2. Remove the thrust bearing and adjustment shims from the
input shaft.
3. Remove the circlip from the front of the clutch cylinder and
remove the input shaft.
4. Remove the overdrive shaft and the C1 clutch hub assembly
from the clutch cylinder.
5. Remove the C1 clutch plates from the cylinder.
6. Remove the circlip retaining the C3 clutch hub in the rear of
the clutch cylinder and remove the hub.
7. Remove the C2/C4 clutch hub assembly and remove the
thrust bearing from the C4 hub.
8. Remove the C2 clutch plates.
9. Invert the clutch cylinder and remove the C4 clutch sleeve,
clutch plates and the two wave washers. The 3-4 one way
clutch is located between the C2 and C4 clutch hubs, and
the hubs may be separated by rotating one hub clockwise
and withdrawing it from the other.
Figure 8.4 - Forward Clutch Cylinder Assembly
Page 1069 of 1463
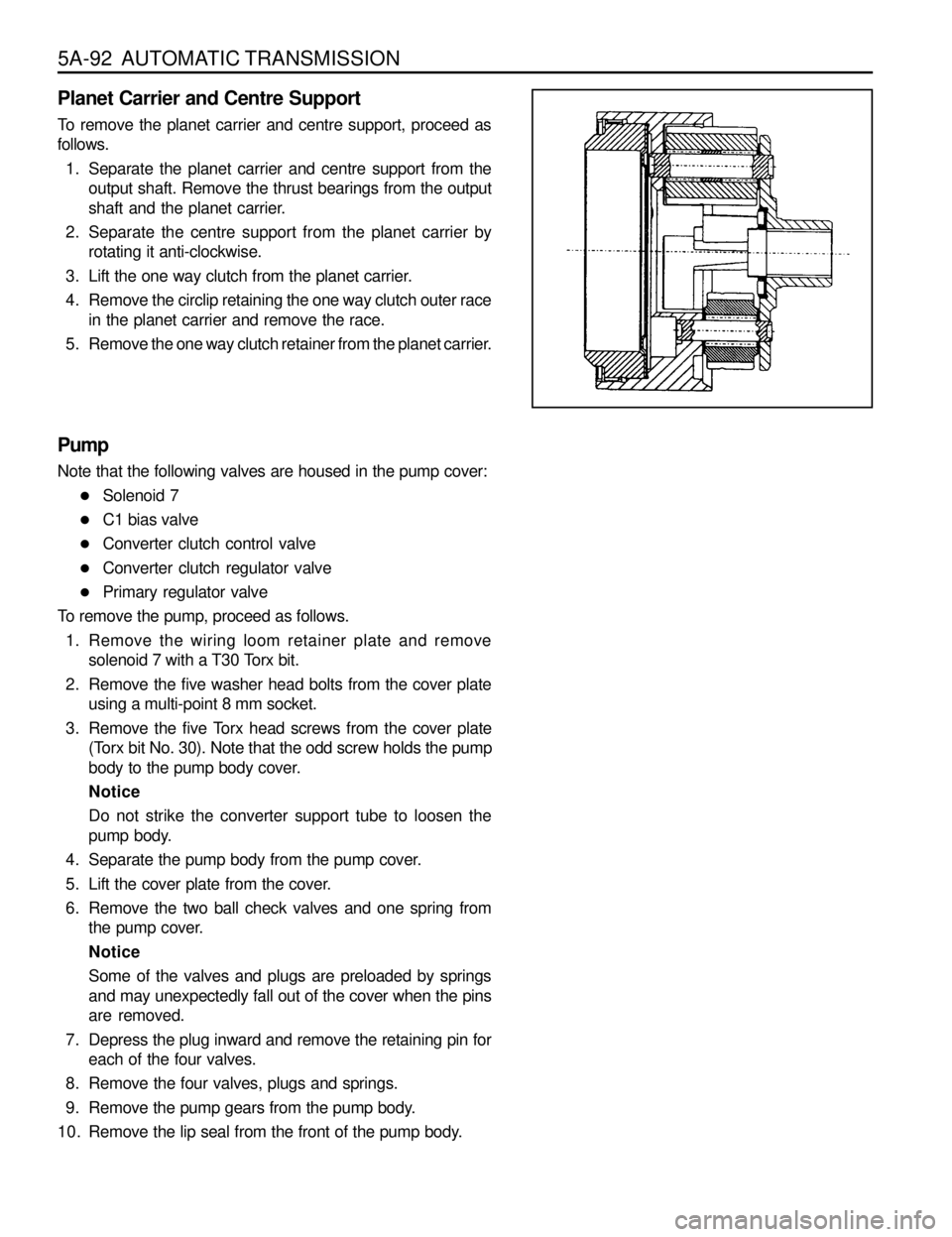
5A-92 AUTOMATIC TRANSMISSION
Planet Carrier and Centre Support
To remove the planet carrier and centre support, proceed as
follows.
1. Separate the planet carrier and centre support from the
output shaft. Remove the thrust bearings from the output
shaft and the planet carrier.
2. Separate the centre support from the planet carrier by
rotating it anti-clockwise.
3. Lift the one way clutch from the planet carrier.
4. Remove the circlip retaining the one way clutch outer race
in the planet carrier and remove the race.
5. Remove the one way clutch retainer from the planet carrier.
Pump
Note that the following valves are housed in the pump cover:
lSolenoid 7
lC1 bias valve
lConverter clutch control valve
lConverter clutch regulator valve
lPrimary regulator valve
To remove the pump, proceed as follows.
1. Remove the wiring loom retainer plate and remove
solenoid 7 with a T30 Torx bit.
2. Remove the five washer head bolts from the cover plate
using a multi-point 8 mm socket.
3. Remove the five Torx head screws from the cover plate
(Torx bit No. 30). Note that the odd screw holds the pump
body to the pump body cover.
Notice
Do not strike the converter support tube to loosen the
pump body.
4. Separate the pump body from the pump cover.
5. Lift the cover plate from the cover.
6. Remove the two ball check valves and one spring from
the pump cover.
Notice
Some of the valves and plugs are preloaded by springs
and may unexpectedly fall out of the cover when the pins
are removed.
7. Depress the plug inward and remove the retaining pin for
each of the four valves.
8. Remove the four valves, plugs and springs.
9. Remove the pump gears from the pump body.
10. Remove the lip seal from the front of the pump body.