clock SSANGYONG MUSSO 1998 Workshop Owner's Manual
[x] Cancel search | Manufacturer: SSANGYONG, Model Year: 1998, Model line: MUSSO, Model: SSANGYONG MUSSO 1998Pages: 1463, PDF Size: 19.88 MB
Page 1077 of 1463
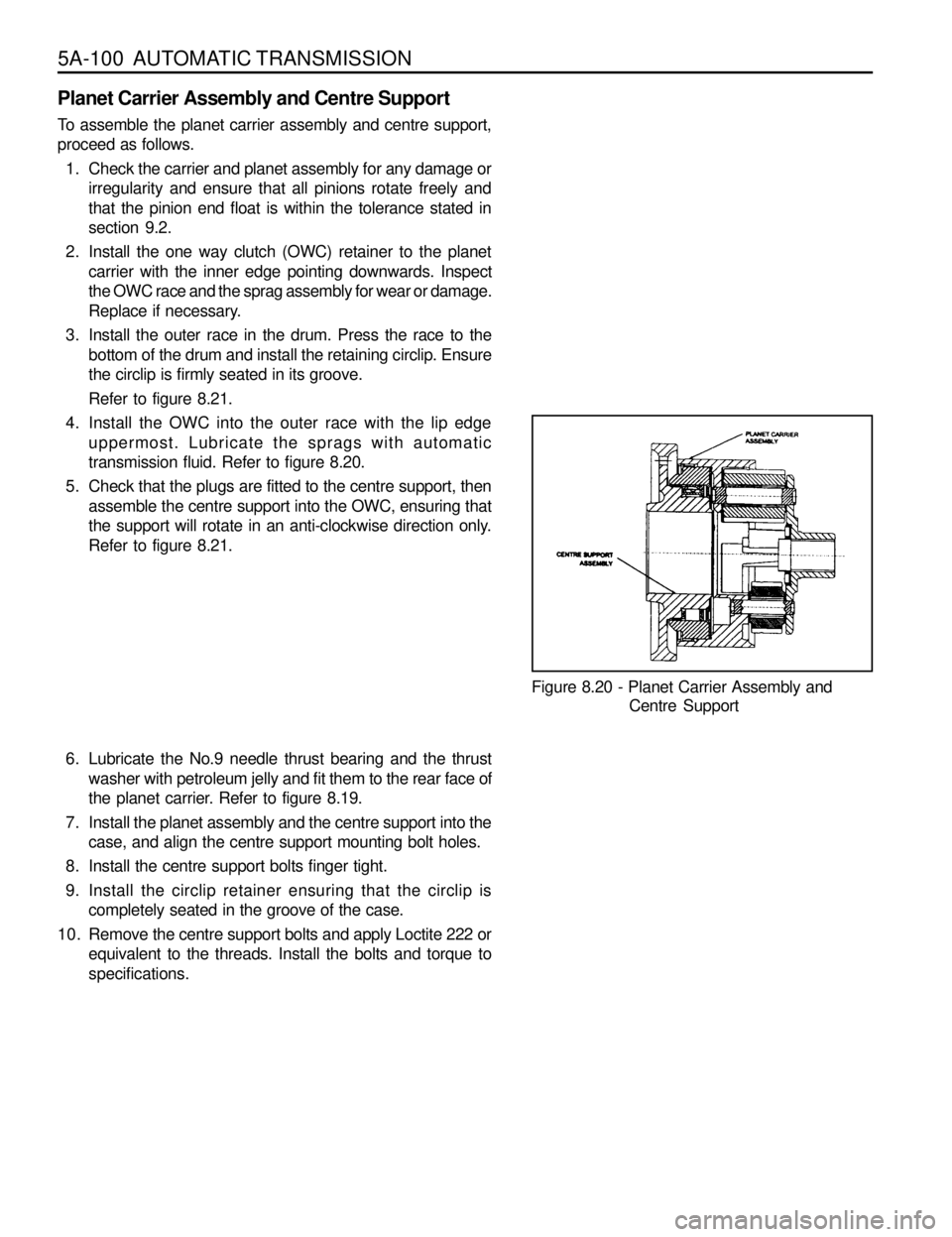
5A-100 AUTOMATIC TRANSMISSION
Planet Carrier Assembly and Centre Support
To assemble the planet carrier assembly and centre support,
proceed as follows.
1. Check the carrier and planet assembly for any damage or
irregularity and ensure that all pinions rotate freely and
that the pinion end float is within the tolerance stated in
section 9.2.
2. Install the one way clutch (OWC) retainer to the planet
carrier with the inner edge pointing downwards. Inspect
the OWC race and the sprag assembly for wear or damage.
Replace if necessary.
3. Install the outer race in the drum. Press the race to the
bottom of the drum and install the retaining circlip. Ensure
the circlip is firmly seated in its groove.
Refer to figure 8.21.
4. Install the OWC into the outer race with the lip edge
uppermost. Lubricate the sprags with automatic
transmission fluid. Refer to figure 8.20.
5. Check that the plugs are fitted to the centre support, then
assemble the centre support into the OWC, ensuring that
the support will rotate in an anti-clockwise direction only.
Refer to figure 8.21.
Figure 8.20 - Planet Carrier Assembly and
Centre Support
6. Lubricate the No.9 needle thrust bearing and the thrust
washer with petroleum jelly and fit them to the rear face of
the planet carrier. Refer to figure 8.19.
7. Install the planet assembly and the centre support into the
case, and align the centre support mounting bolt holes.
8. Install the centre support bolts finger tight.
9. Install the circlip retainer ensuring that the circlip is
completely seated in the groove of the case.
10. Remove the centre support bolts and apply Loctite 222 or
equivalent to the threads. Install the bolts and torque to
specifications.
Page 1083 of 1463
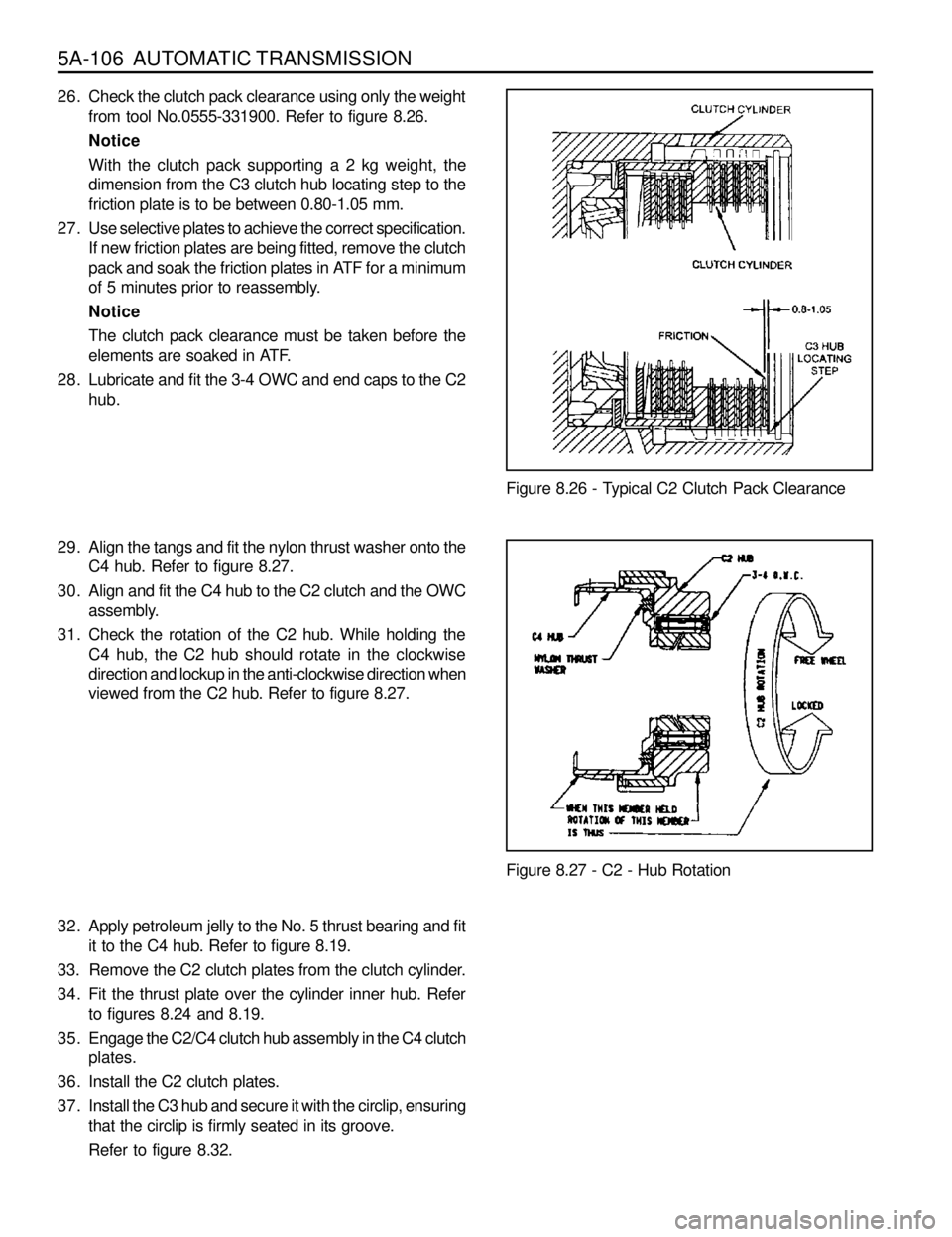
5A-106 AUTOMATIC TRANSMISSION
29. Align the tangs and fit the nylon thrust washer onto the
C4 hub. Refer to figure 8.27.
30. Align and fit the C4 hub to the C2 clutch and the OWC
assembly.
31. Check the rotation of the C2 hub. While holding the
C4 hub, the C2 hub should rotate in the clockwise
direction and lockup in the anti-clockwise direction when
viewed from the C2 hub. Refer to figure 8.27.
Figure 8.27 - C2 - Hub Rotation
32. Apply petroleum jelly to the No. 5 thrust bearing and fit
it to the C4 hub. Refer to figure 8.19.
33. Remove the C2 clutch plates from the clutch cylinder.
34. Fit the thrust plate over the cylinder inner hub. Refer
to figures 8.24 and 8.19.
35. Engage the C2/C4 clutch hub assembly in the C4 clutch
plates.
36. Install the C2 clutch plates.
37. Install the C3 hub and secure it with the circlip, ensuring
that the circlip is firmly seated in its groove.
Refer to figure 8.32.Figure 8.26 - Typical C2 Clutch Pack Clearance 26. Check the clutch pack clearance using only the weight
from tool No.0555-331900. Refer to figure 8.26.
Notice
With the clutch pack supporting a 2 kg weight, the
dimension from the C3 clutch hub locating step to the
friction plate is to be between 0.80-1.05 mm.
27. Use selective plates to achieve the correct specification.
If new friction plates are being fitted, remove the clutch
pack and soak the friction plates in ATF for a minimum
of 5 minutes prior to reassembly.
Notice
The clutch pack clearance must be taken before the
elements are soaked in ATF.
28. Lubricate and fit the 3-4 OWC and end caps to the C2
hub.
Page 1204 of 1463
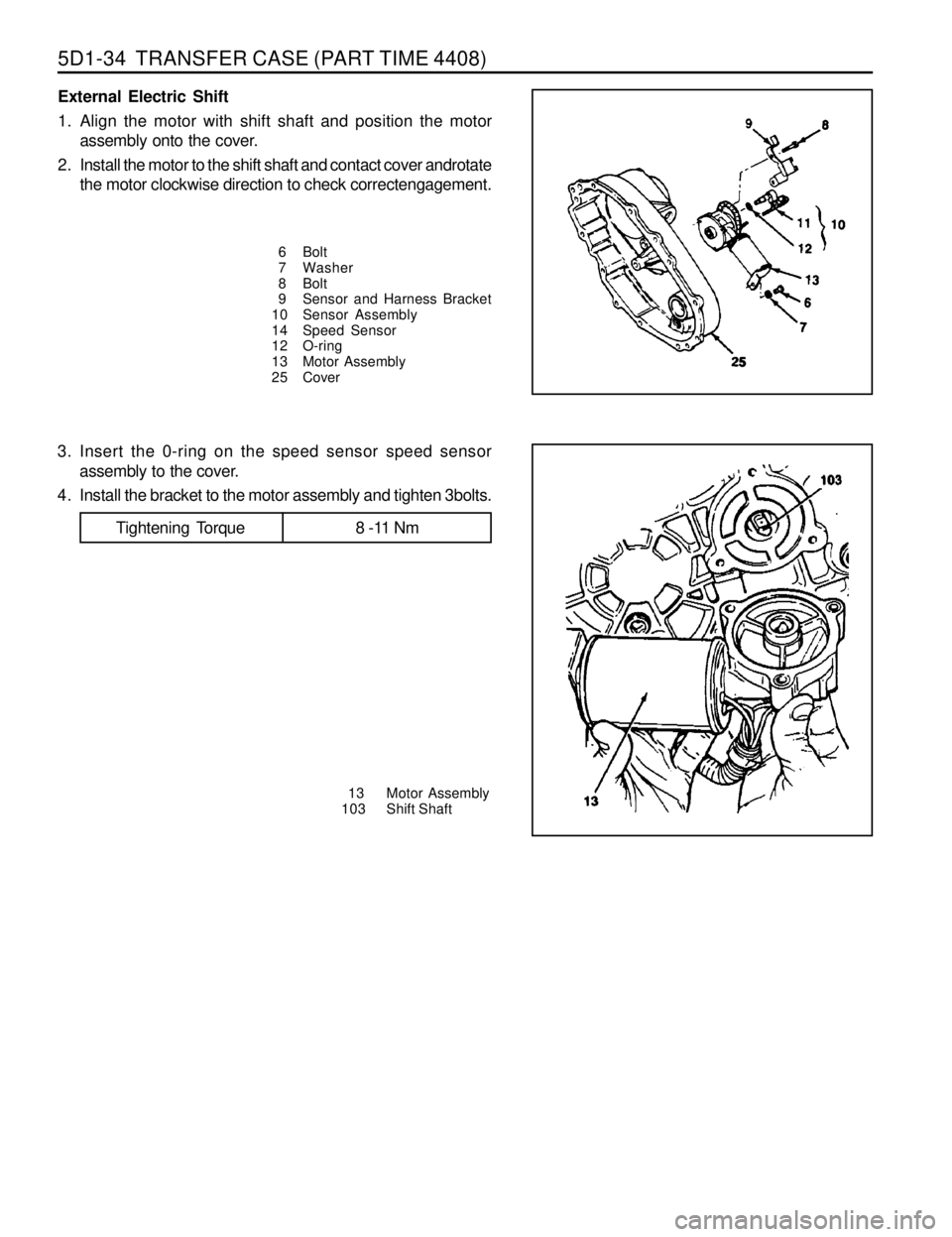
5D1-34 TRANSFER CASE (PART TIME 4408)
External Electric Shift
1. Align the motor with shift shaft and position the motor
assembly onto the cover.
2. Install the motor to the shift shaft and contact cover androtate
the motor clockwise direction to check correctengagement.
6 Bolt
7 Washer
8 Bolt
9 Sensor and Harness Bracket
10 Sensor Assembly
14 Speed Sensor
12 O-ring
13 Motor Assembly
25 Cover
13 Motor Assembly
103 Shift Shaft
3. Insert the 0-ring on the speed sensor speed sensor
assembly to the cover.
4. Install the bracket to the motor assembly and tighten 3bolts.
Tightening Torque 8 -11 Nm
Page 1220 of 1463
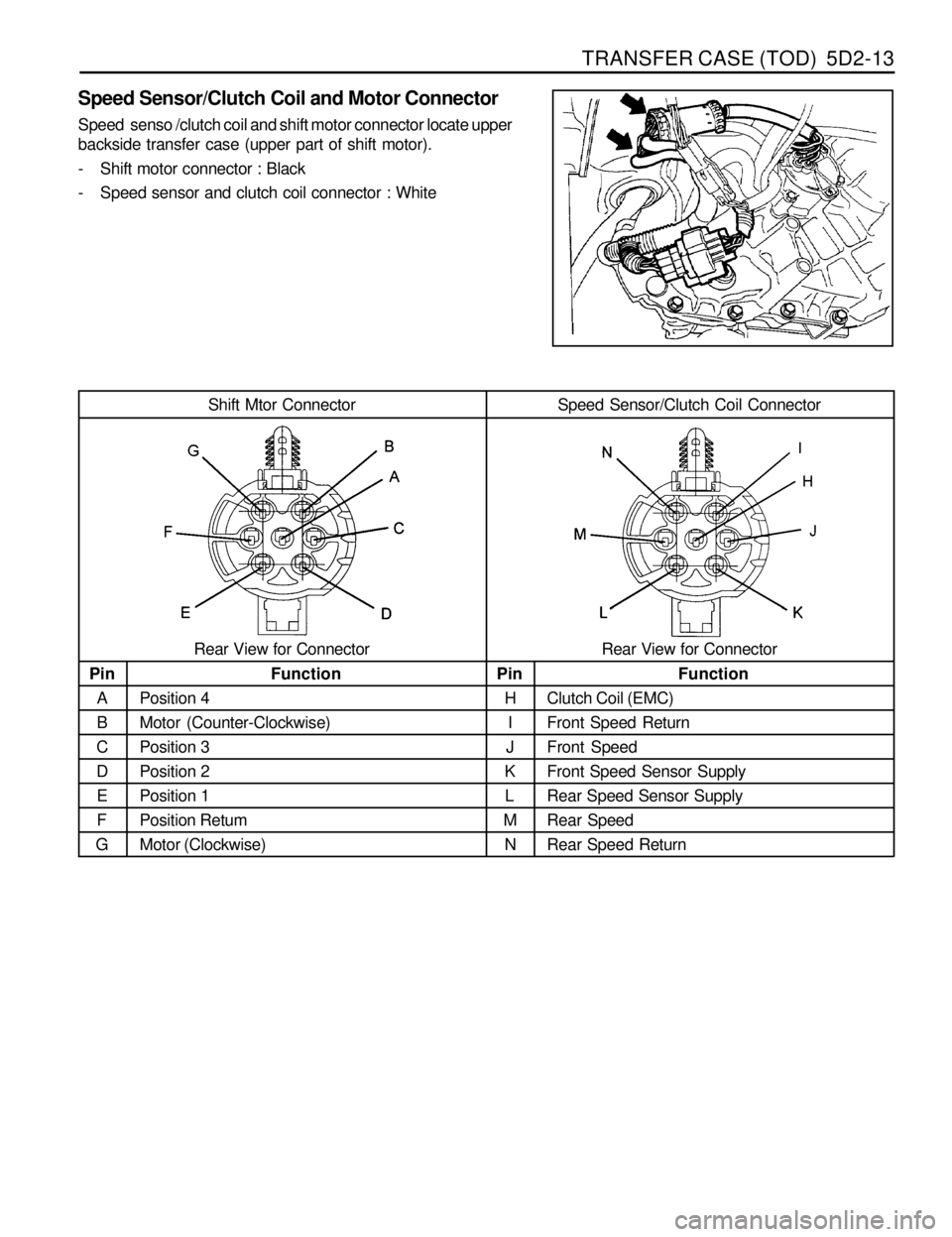
TRANSFER CASE (TOD) 5D2-13
Speed Sensor/Clutch Coil and Motor Connector
Speed senso /clutch coil and shift motor connector locate upper
backside transfer case (upper part of shift motor).
- Shift motor connector : Black
- Speed sensor and clutch coil connector : White
Shift Mtor Connector Speed Sensor/Clutch Coil Connector
Rear View for Connector
Pin
A
B
C
D
E
F
GFunction
Position 4
Motor (Counter-Clockwise)
Position 3
Position 2
Position 1
Position Retum
Motor (Clockwise)Pin
H
I
J
K
L
M
NFunction
Clutch Coil (EMC)
Front Speed Return
Front Speed
Front Speed Sensor Supply
Rear Speed Sensor Supply
Rear Speed
Rear Speed Return Rear View for Connector
Page 1221 of 1463
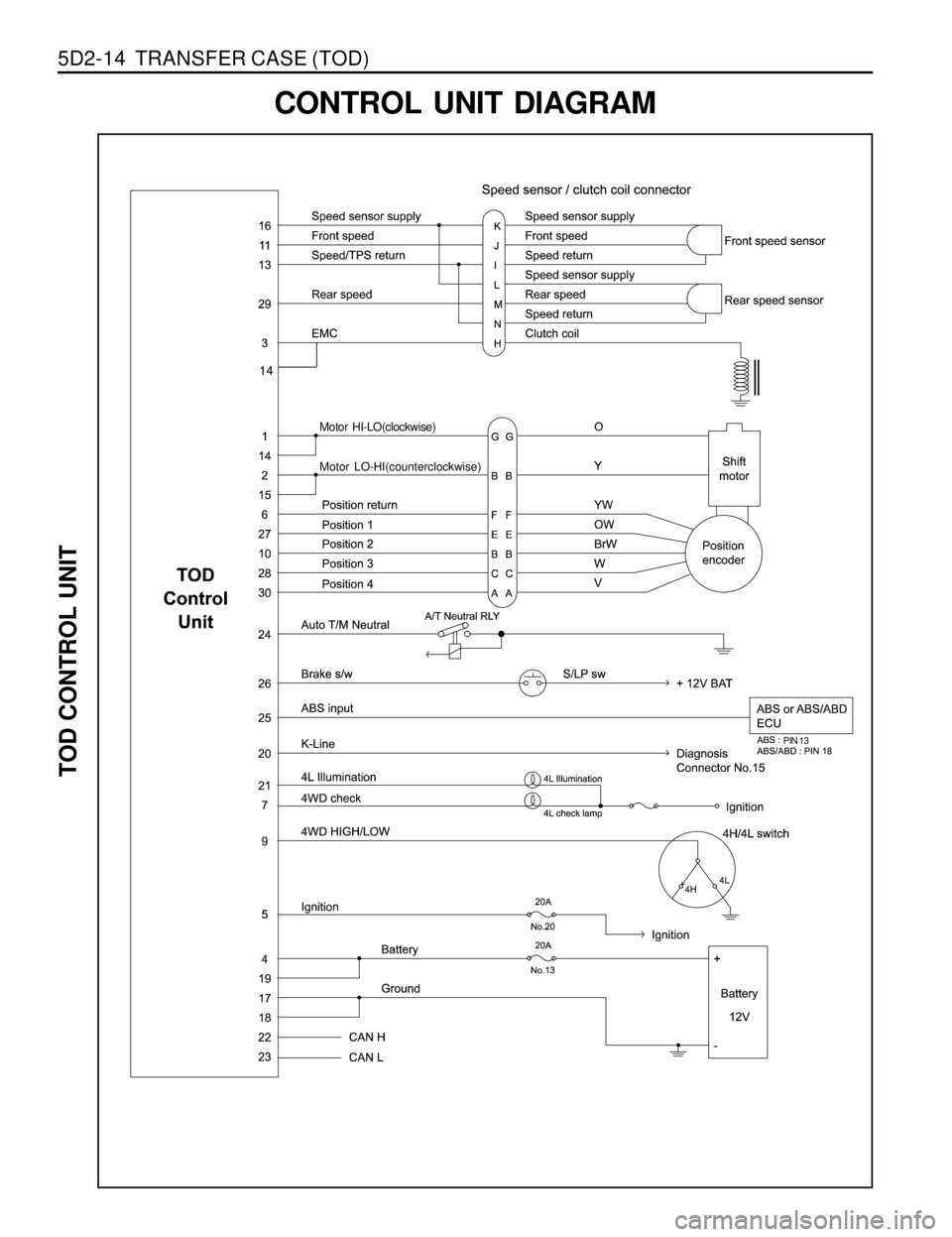
5D2-14 TRANSFER CASE (TOD)
Motor HI-LO(clockwise)
Motor LO-HI(counterclockwise)
PIN 13
CONTROL UNIT DIAGRAM
TOD CONTROL UNIT
14
Page 1257 of 1463
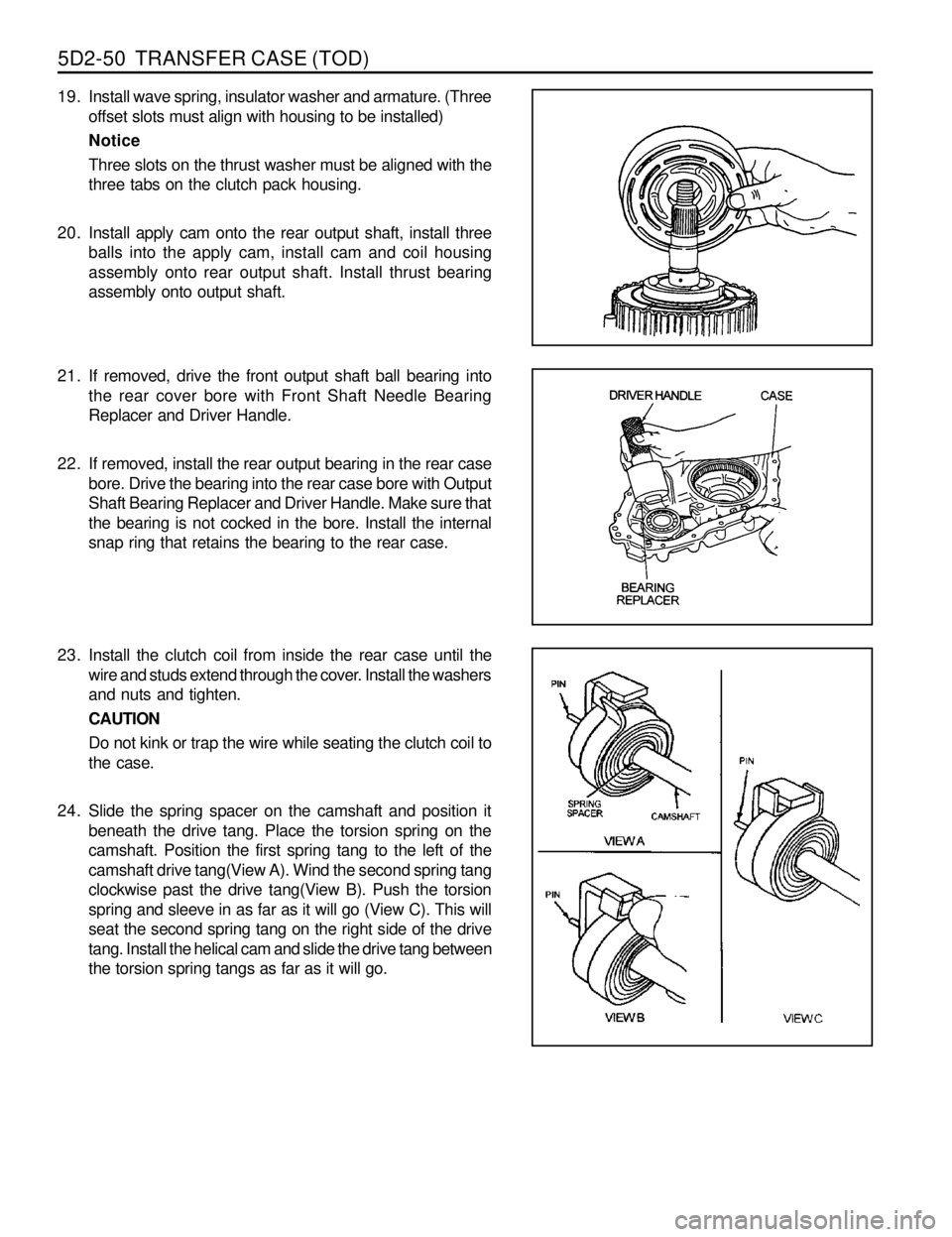
5D2-50 TRANSFER CASE (TOD)
19. Install wave spring, insulator washer and armature. (Three
offset slots must align with housing to be installed)
Notice
Three slots on the thrust washer must be aligned with the
three tabs on the clutch pack housing.
20. Install apply cam onto the rear output shaft, install three
balls into the apply cam, install cam and coil housing
assembly onto rear output shaft. Install thrust bearing
assembly onto output shaft.
21. If removed, drive the front output shaft ball bearing into
the rear cover bore with Front Shaft Needle Bearing
Replacer and Driver Handle.
22. If removed, install the rear output bearing in the rear case
bore. Drive the bearing into the rear case bore with Output
Shaft Bearing Replacer and Driver Handle. Make sure that
the bearing is not cocked in the bore. Install the internal
snap ring that retains the bearing to the rear case.
23. Install the clutch coil from inside the rear case until the
wire and studs extend through the cover. Install the washers
and nuts and tighten.
CAUTION
Do not kink or trap the wire while seating the clutch coil to
the case.
24. Slide the spring spacer on the camshaft and position it
beneath the drive tang. Place the torsion spring on the
camshaft. Position the first spring tang to the left of the
camshaft drive tang(View A). Wind the second spring tang
clockwise past the drive tang(View B). Push the torsion
spring and sleeve in as far as it will go (View C). This will
seat the second spring tang on the right side of the drive
tang. Install the helical cam and slide the drive tang between
the torsion spring tangs as far as it will go.
Page 1269 of 1463
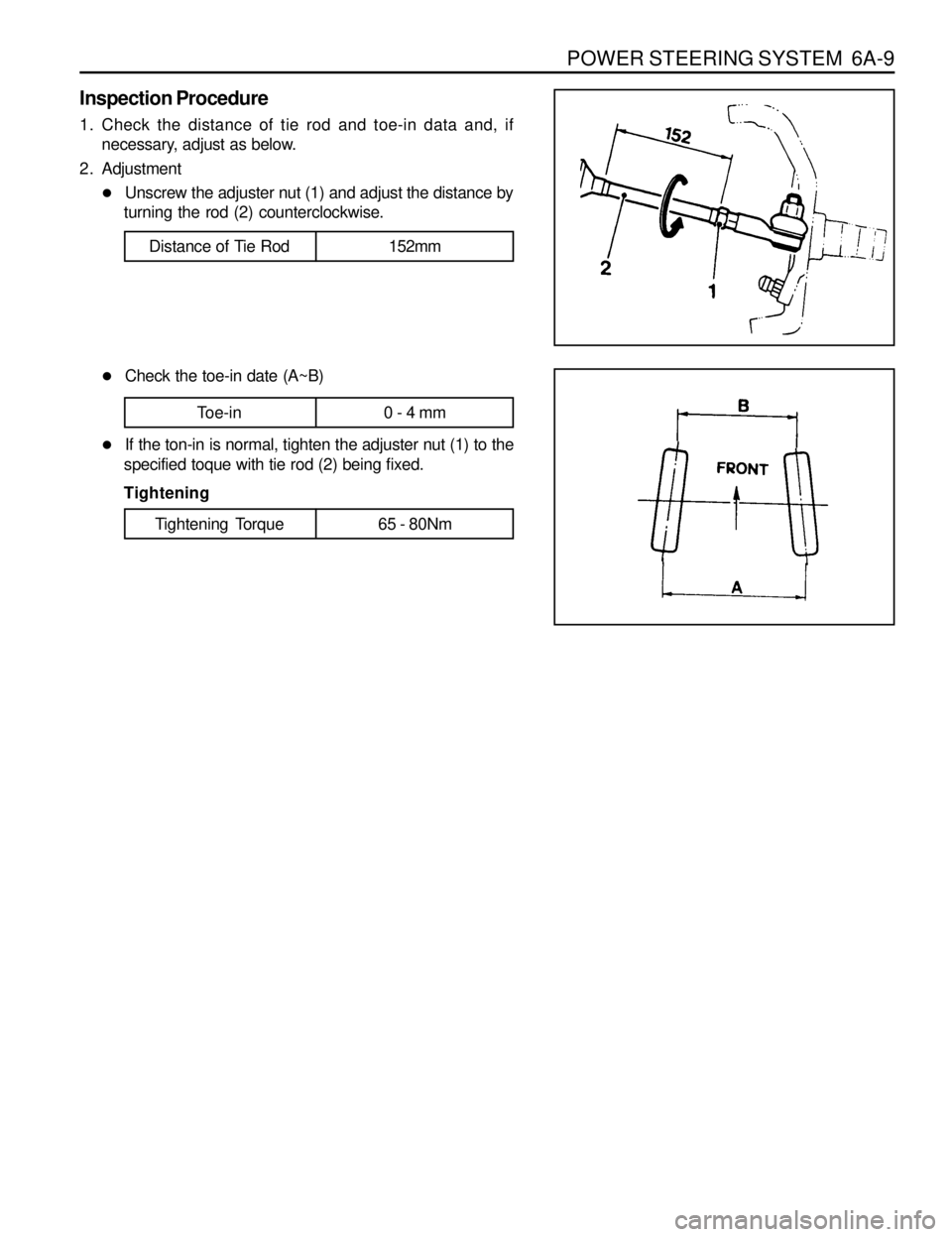
POWER STEERING SYSTEM 6A-9
Inspection Procedure
1. Check the distance of tie rod and toe-in data and, if
necessary, adjust as below.
2. Adjustment
lUnscrew the adjuster nut (1) and adjust the distance by
turning the rod (2) counterclockwise.
Distance of Tie Rod152mm
Toe-in 0 - 4 mm
Tightening Torque 65 - 80Nm
lCheck the toe-in date (A~B)
lIf the ton-in is normal, tighten the adjuster nut (1) to the
specified toque with tie rod (2) being fixed.
Tightening
Page 1305 of 1463
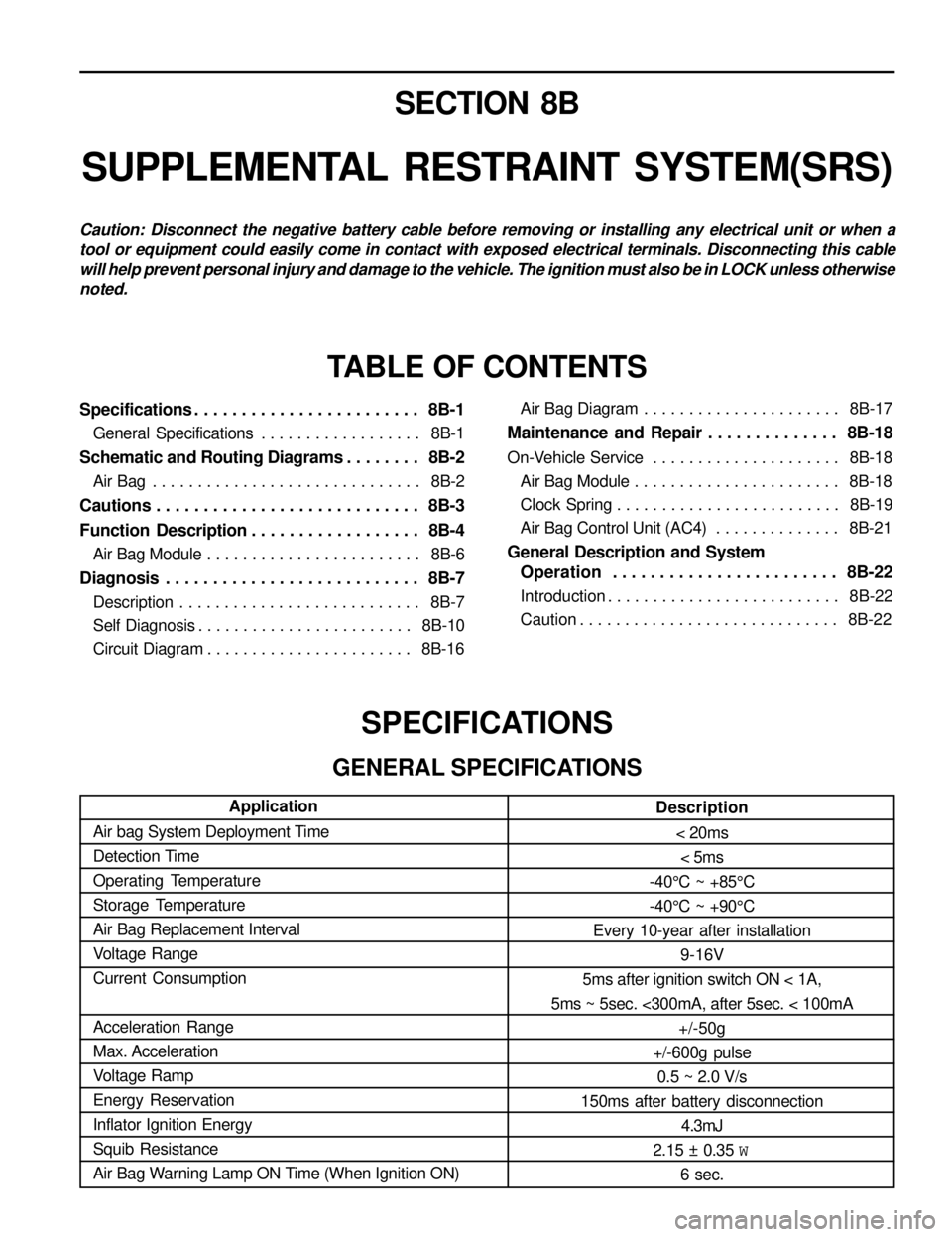
SECTION 8B
SUPPLEMENTAL RESTRAINT SYSTEM(SRS)
Specifications . . . . . . . . . . . . . . . . . . . . . . . . 8B-1
General Specifications . . . . . . . . . . . . . . . . . . 8B-1
Schematic and Routing Diagrams . . . . . . . . 8B-2
Air Bag . . . . . . . . . . . . . . . . . . . . . . . . . . . . . . 8B-2
Cautions . . . . . . . . . . . . . . . . . . . . . . . . . . . . 8B-3
Function Description . . . . . . . . . . . . . . . . . . 8B-4
Air Bag Module . . . . . . . . . . . . . . . . . . . . . . . . 8B-6
Diagnosis . . . . . . . . . . . . . . . . . . . . . . . . . . . 8B-7
Description . . . . . . . . . . . . . . . . . . . . . . . . . . . 8B-7
Self Diagnosis . . . . . . . . . . . . . . . . . . . . . . . . 8B-10
Circuit Diagram . . . . . . . . . . . . . . . . . . . . . . . 8B-16
TABLE OF CONTENTS
Caution: Disconnect the negative battery cable before removing or installing any electrical unit or when a
tool or equipment could easily come in contact with exposed electrical terminals. Disconnecting this cable
will help prevent personal injury and damage to the vehicle. The ignition must also be in LOCK unless otherwise
noted.
SPECIFICATIONS
GENERAL SPECIFICATIONS
Application
Air bag System Deployment Time
Detection Time
Operating Temperature
Storage Temperature
Air Bag Replacement Interval
Voltage Range
Current Consumption
Acceleration Range
Max. Acceleration
Voltage Ramp
Energy Reservation
Inflator Ignition Energy
Squib Resistance
Air Bag Warning Lamp ON Time (When Ignition ON)Description
< 20ms
< 5ms
-40°C ~ +85°C
-40°C ~ +90°C
Every 10-year after installation
9-16V
5ms after ignition switch ON < 1A,
5ms ~ 5sec. <300mA, after 5sec. < 100mA
+/-50g
+/-600g pulse
0.5 ~ 2.0 V/s
150ms after battery disconnection
4.3mJ
2.15 ± 0.35 W
6 sec.
Air Bag Diagram . . . . . . . . . . . . . . . . . . . . . . 8B-17
Maintenance and Repair . . . . . . . . . . . . . . 8B-18
On-Vehicle Service . . . . . . . . . . . . . . . . . . . . . 8B-18
Air Bag Module . . . . . . . . . . . . . . . . . . . . . . . 8B-18
Clock Spring . . . . . . . . . . . . . . . . . . . . . . . . . 8B-19
Air Bag Control Unit (AC4) . . . . . . . . . . . . . . 8B-21
General Description and System
Operation . . . . . . . . . . . . . . . . . . . . . . . . 8B-22
Introduction . . . . . . . . . . . . . . . . . . . . . . . . . . 8B-22
Caution . . . . . . . . . . . . . . . . . . . . . . . . . . . . . 8B-22
Page 1307 of 1463
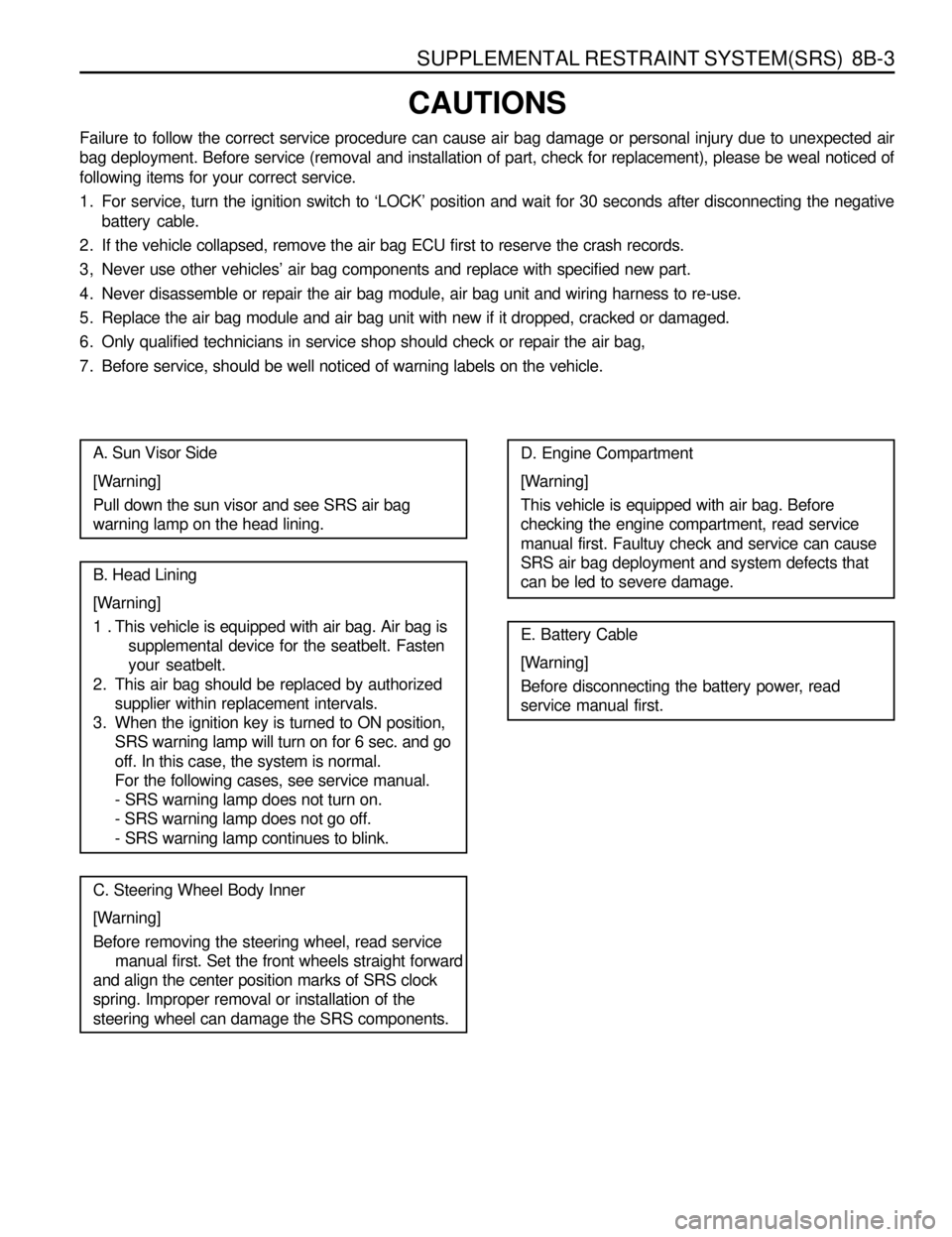
SUPPLEMENTAL RESTRAINT SYSTEM(SRS) 8B-3
CAUTIONS
Failure to follow the correct service procedure can cause air bag damage or personal injury due to unexpected air
bag deployment. Before service (removal and installation of part, check for replacement), please be weal noticed of
following items for your correct service.
1. For service, turn the ignition switch to ‘LOCK’ position and wait for 30 seconds after disconnecting the negative
battery cable.
2. If the vehicle collapsed, remove the air bag ECU first to reserve the crash records.
3, Never use other vehicles’ air bag components and replace with specified new part.
4. Never disassemble or repair the air bag module, air bag unit and wiring harness to re-use.
5. Replace the air bag module and air bag unit with new if it dropped, cracked or damaged.
6. Only qualified technicians in service shop should check or repair the air bag,
7. Before service, should be well noticed of warning labels on the vehicle.
A. Sun Visor Side
[Warning]
Pull down the sun visor and see SRS air bag
warning lamp on the head lining.
B. Head Lining
[Warning]
1 . This vehicle is equipped with air bag. Air bag is
supplemental device for the seatbelt. Fasten
your seatbelt.
2. This air bag should be replaced by authorized
supplier within replacement intervals.
3. When the ignition key is turned to ON position,
SRS warning lamp will turn on for 6 sec. and go
off. In this case, the system is normal.
For the following cases, see service manual.
- SRS warning lamp does not turn on.
- SRS warning lamp does not go off.
- SRS warning lamp continues to blink.
C. Steering Wheel Body Inner
[Warning]
Before removing the steering wheel, read service
manual first. Set the front wheels straight forward
and align the center position marks of SRS clock
spring. Improper removal or installation of the
steering wheel can damage the SRS components.D. Engine Compartment
[Warning]
This vehicle is equipped with air bag. Before
checking the engine compartment, read service
manual first. Faultuy check and service can cause
SRS air bag deployment and system defects that
can be led to severe damage.
E. Battery Cable
[Warning]
Before disconnecting the battery power, read
service manual first.
Page 1323 of 1463
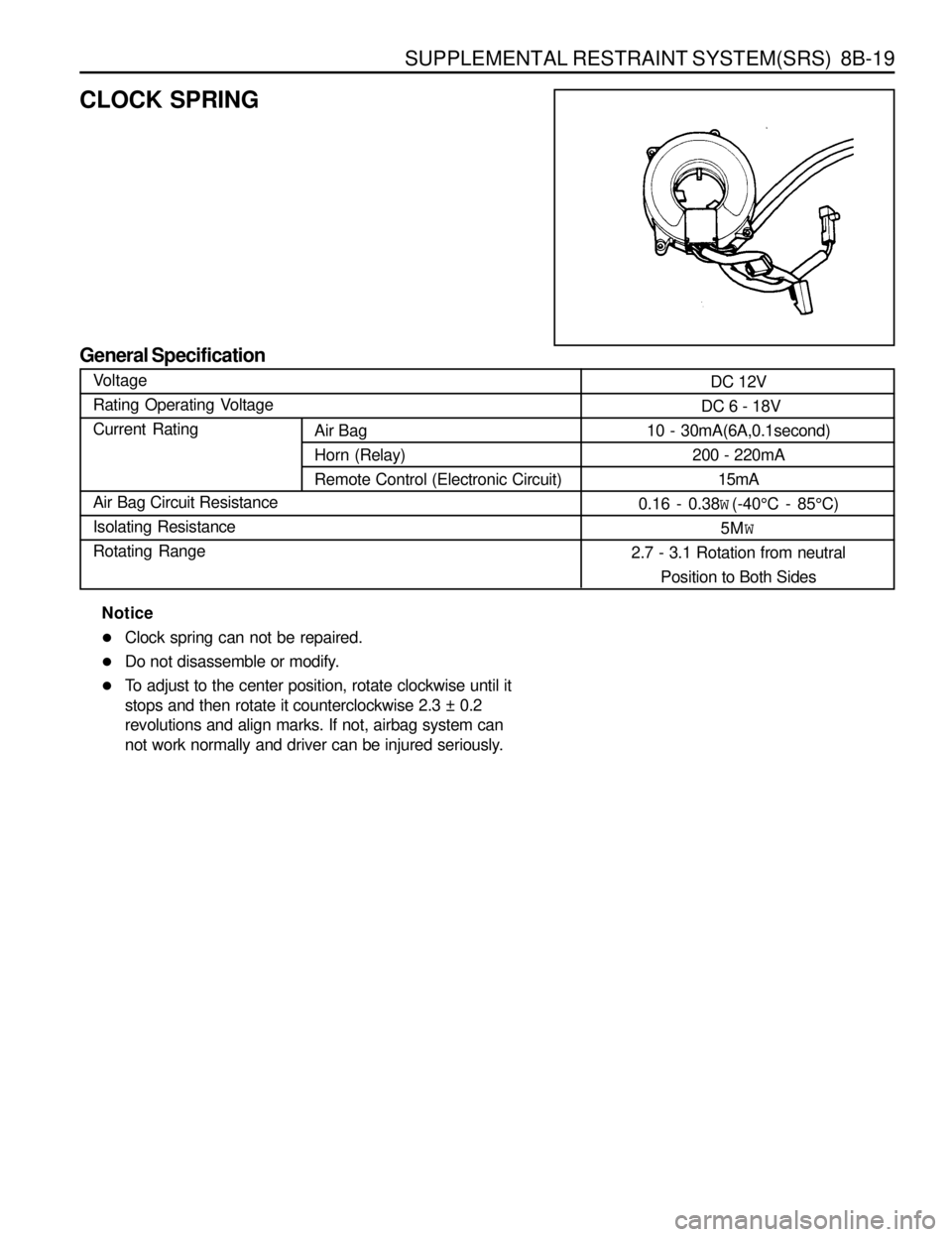
SUPPLEMENTAL RESTRAINT SYSTEM(SRS) 8B-19
Air Bag
Horn (Relay)
Remote Control (Electronic Circuit)
CLOCK SPRING
General Specification
Voltage
Rating Operating Voltage
Current Rating
Air Bag Circuit Resistance
Isolating Resistance
Rotating RangeDC 12V
DC 6 - 18V
10 - 30mA(6A,0.1second)
200 - 220mA
15mA
0.16 - 0.38W(-40°C - 85°C)
5MW
2.7 - 3.1 Rotation from neutral
Position to Both Sides
Notice
lClock spring can not be repaired.
lDo not disassemble or modify.
lTo adjust to the center position, rotate clockwise until it
stops and then rotate it counterclockwise 2.3 ± 0.2
revolutions and align marks. If not, airbag system can
not work normally and driver can be injured seriously.