differential SSANGYONG MUSSO 1998 Workshop User Guide
[x] Cancel search | Manufacturer: SSANGYONG, Model Year: 1998, Model line: MUSSO, Model: SSANGYONG MUSSO 1998Pages: 1463, PDF Size: 19.88 MB
Page 909 of 1463
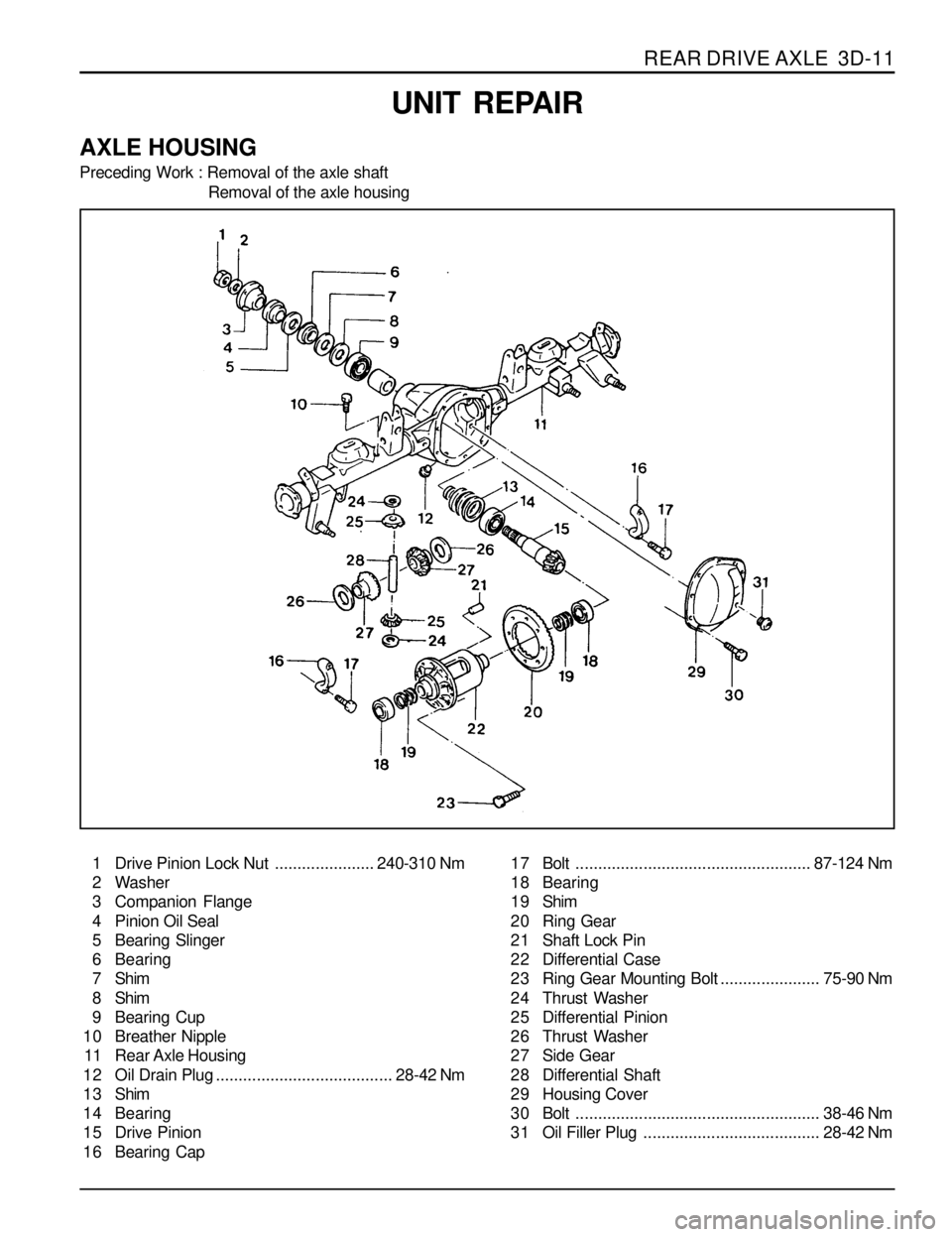
REAR DRIVE AXLE 3D-11
UNIT REPAIR
AXLE HOUSING
Preceding Work : Removal of the axle shaft
Removal of the axle housing
1 Drive Pinion Lock Nut......................240-310 Nm
2 Washer
3 Companion Flange
4 Pinion Oil Seal
5 Bearing Slinger
6 Bearing
7 Shim
8 Shim
9 Bearing Cup
10 Breather Nipple
11 Rear Axle Housing
12 Oil Drain Plug.......................................28-42 Nm
1 3 Shim
14 Bearing
15 Drive Pinion
16 Bearing Cap1 7 Bolt....................................................87-124 Nm
18 Bearing
1 9 Shim
20 Ring Gear
21 Shaft Lock Pin
22 Differential Case
23 Ring Gear Mounting Bolt......................75-90 Nm
24 Thrust Washer
25 Differential Pinion
26 Thrust Washer
27 Side Gear
28 Differential Shaft
29 Housing Cover
3 0 Bolt......................................................38-46 Nm
31 Oil Filler Plug.......................................28-42 Nm
Page 910 of 1463
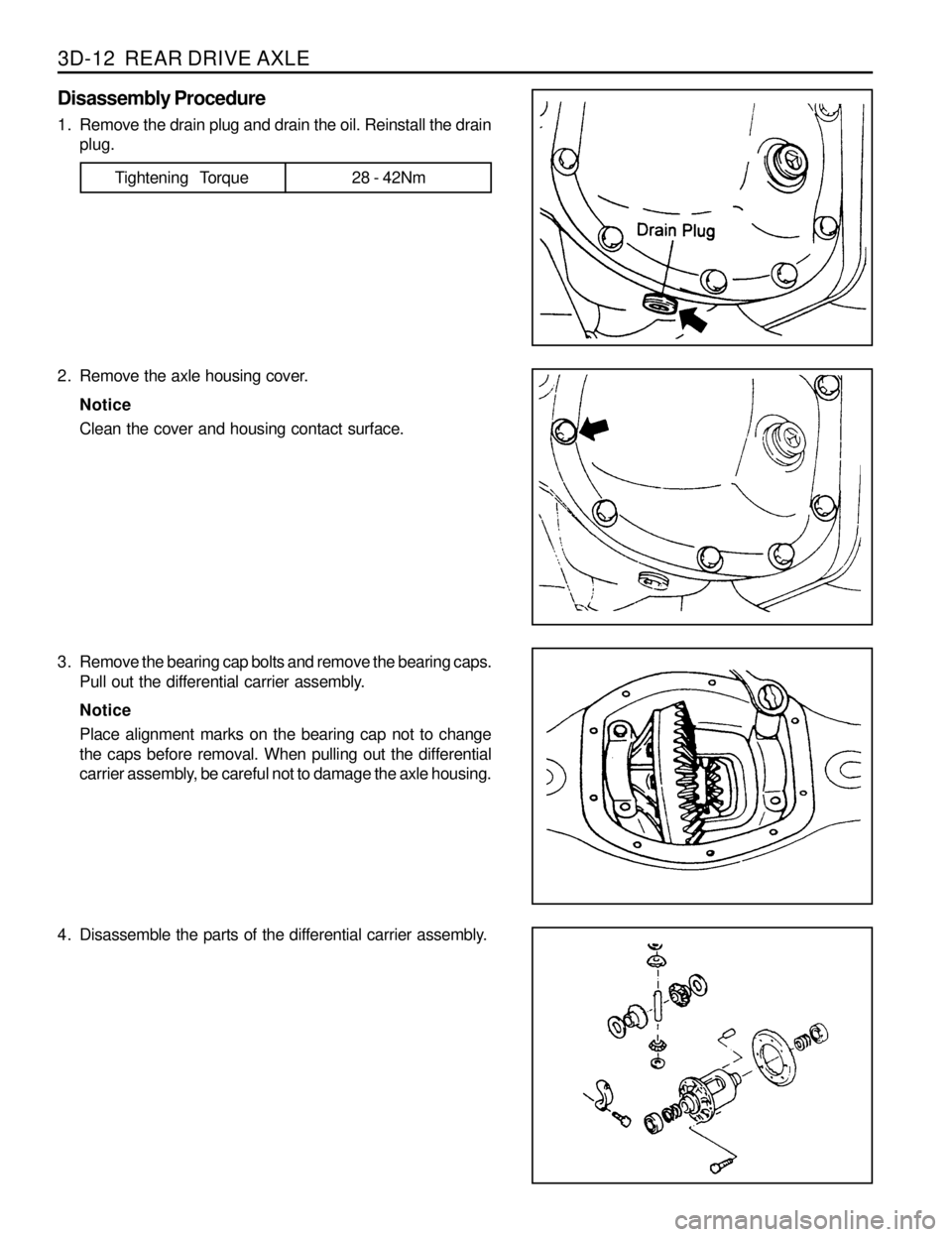
3D-12 REAR DRIVE AXLE
Disassembly Procedure
1. Remove the drain plug and drain the oil. Reinstall the drain
plug.
2. Remove the axle housing cover.
Notice
Clean the cover and housing contact surface.
3. Remove the bearing cap bolts and remove the bearing caps.
Pull out the differential carrier assembly.
Notice
Place alignment marks on the bearing cap not to change
the caps before removal. When pulling out the differential
carrier assembly, be careful not to damage the axle housing.
4. Disassemble the parts of the differential carrier assembly.
Tightening Torque 28 - 42Nm
Page 911 of 1463
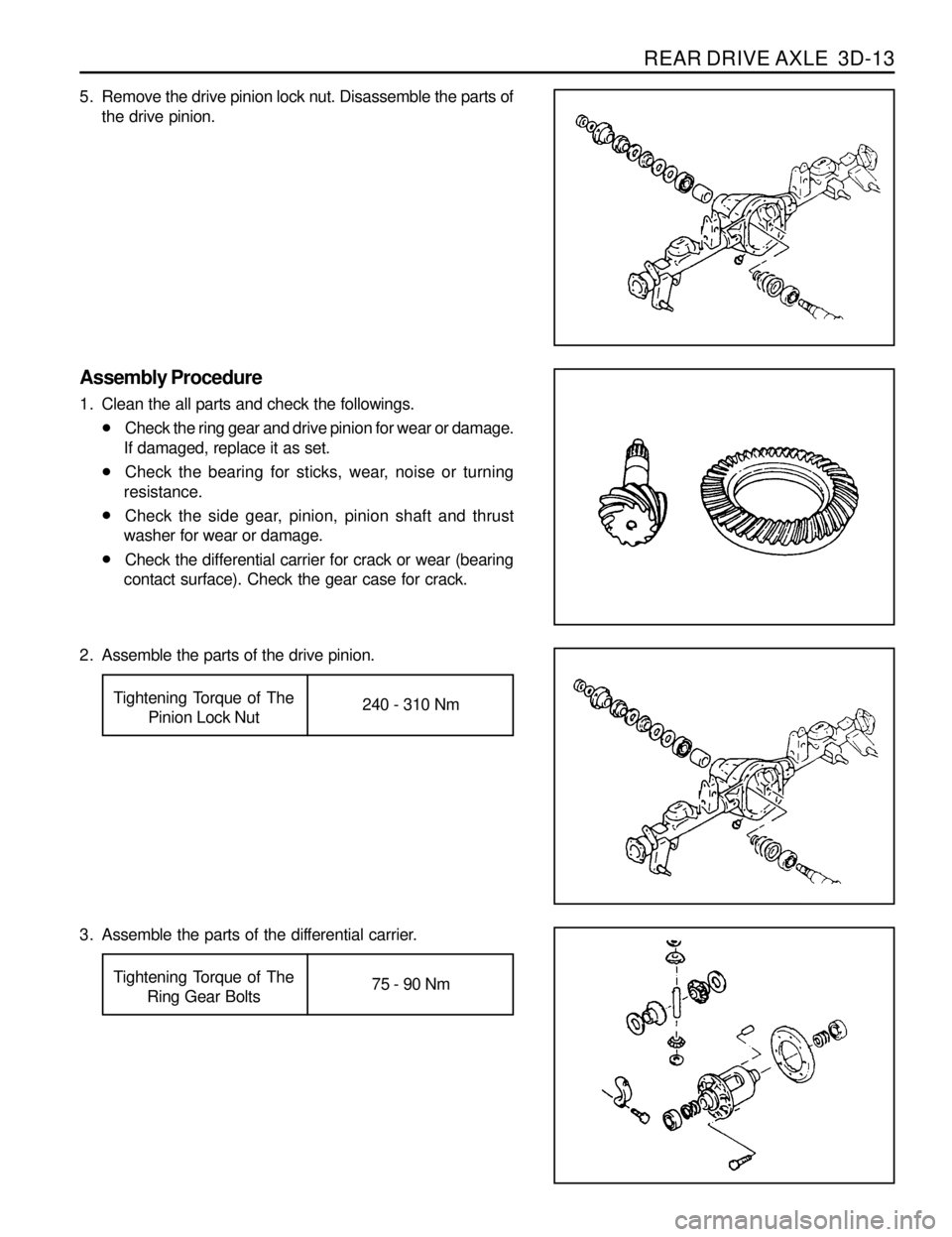
REAR DRIVE AXLE 3D-13
5. Remove the drive pinion lock nut. Disassemble the parts of
the drive pinion.
Assembly Procedure
1. Clean the all parts and check the followings.
lCheck the ring gear and drive pinion for wear or damage.
If damaged, replace it as set.
lCheck the bearing for sticks, wear, noise or turning
resistance.
lCheck the side gear, pinion, pinion shaft and thrust
washer for wear or damage.
lCheck the differential carrier for crack or wear (bearing
contact surface). Check the gear case for crack.
2. Assemble the parts of the drive pinion.
3. Assemble the parts of the differential carrier.
Tightening Torque of The
Pinion Lock Nut240 - 310 Nm
Tightening Torque of The
Ring Gear Bolts75 - 90 Nm
Page 912 of 1463
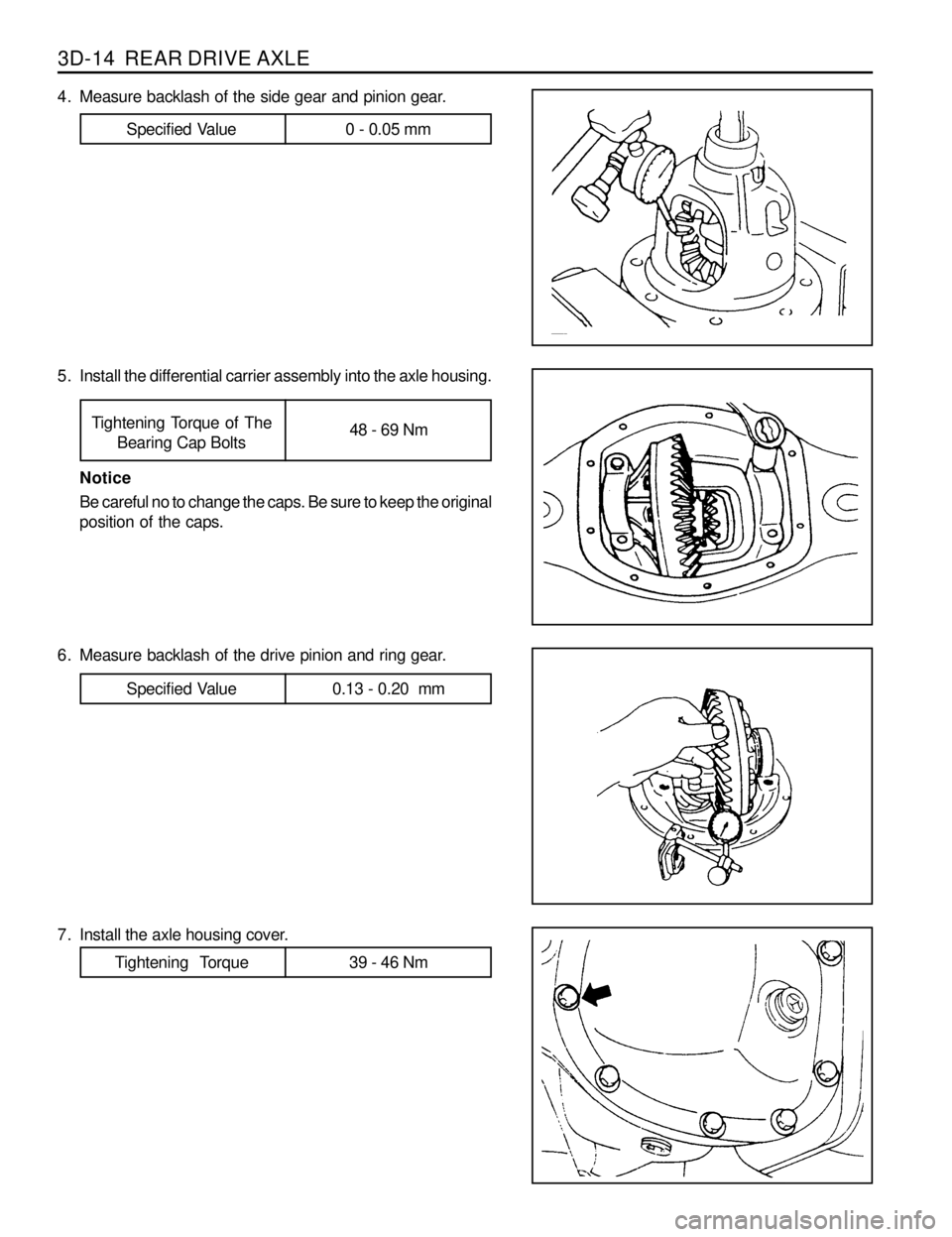
3D-14 REAR DRIVE AXLE
4. Measure backlash of the side gear and pinion gear.
Specified Value 0 - 0.05 mm
5. Install the differential carrier assembly into the axle housing.
Tightening Torque of The
Bearing Cap Bolts48 - 69 Nm
Notice
Be careful no to change the caps. Be sure to keep the original
position of the caps.
6. Measure backlash of the drive pinion and ring gear.
7. Install the axle housing cover.
Specified Value 0.13 - 0.20 mm
Tightening Torque 39 - 46 Nm
Page 914 of 1463
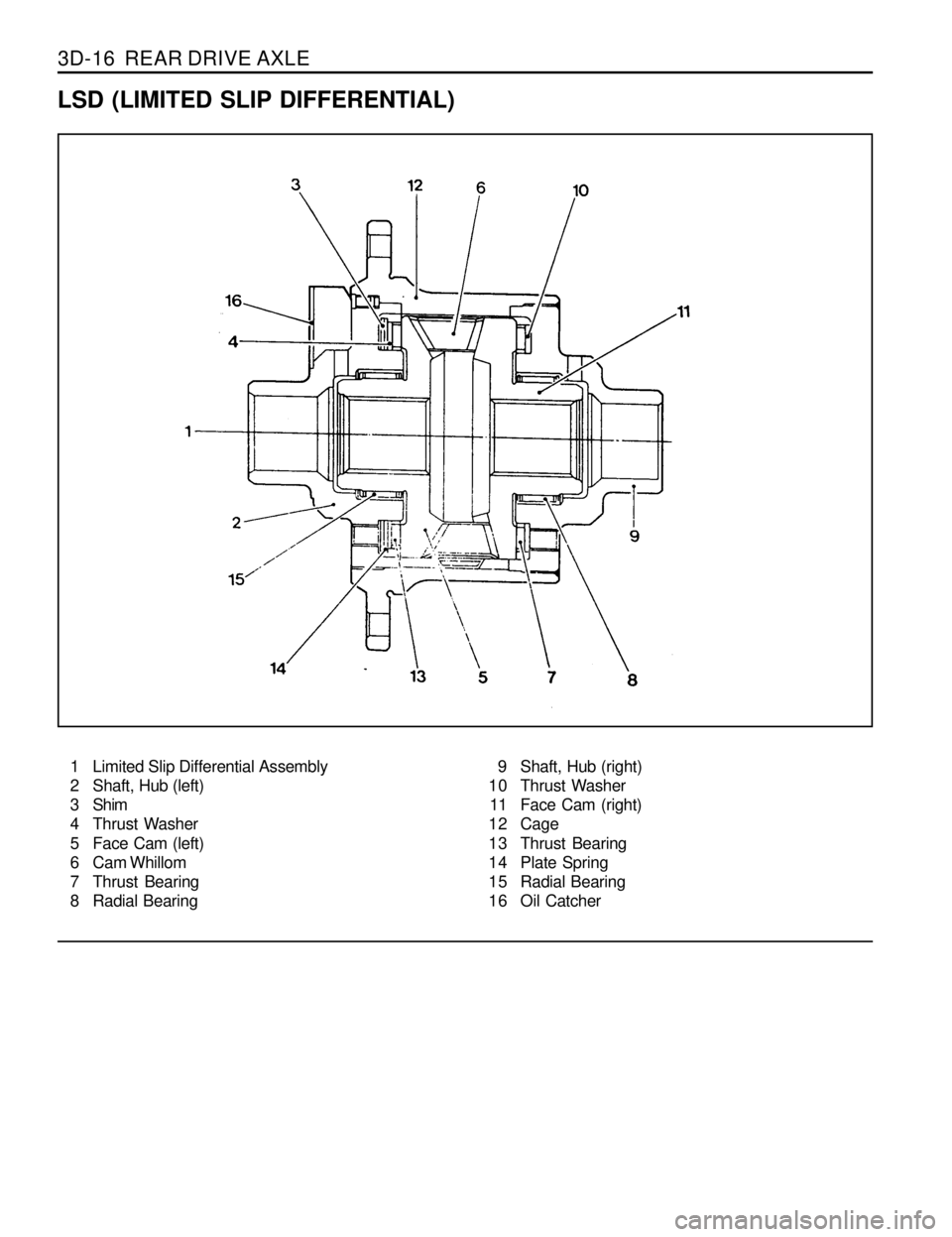
3D-16 REAR DRIVE AXLE
LSD (LIMITED SLIP DIFFERENTIAL)
1 Limited Slip Differential Assembly
2 Shaft, Hub (left)
3 Shim
4 Thrust Washer
5 Face Cam (left)
6 Cam Whillom
7 Thrust Bearing
8 Radial Bearing9 Shaft, Hub (right)
10 Thrust Washer
11 Face Cam (right)
12 Cage
13 Thrust Bearing
14 Plate Spring
15 Radial Bearing
16 Oil Catcher
Page 954 of 1463
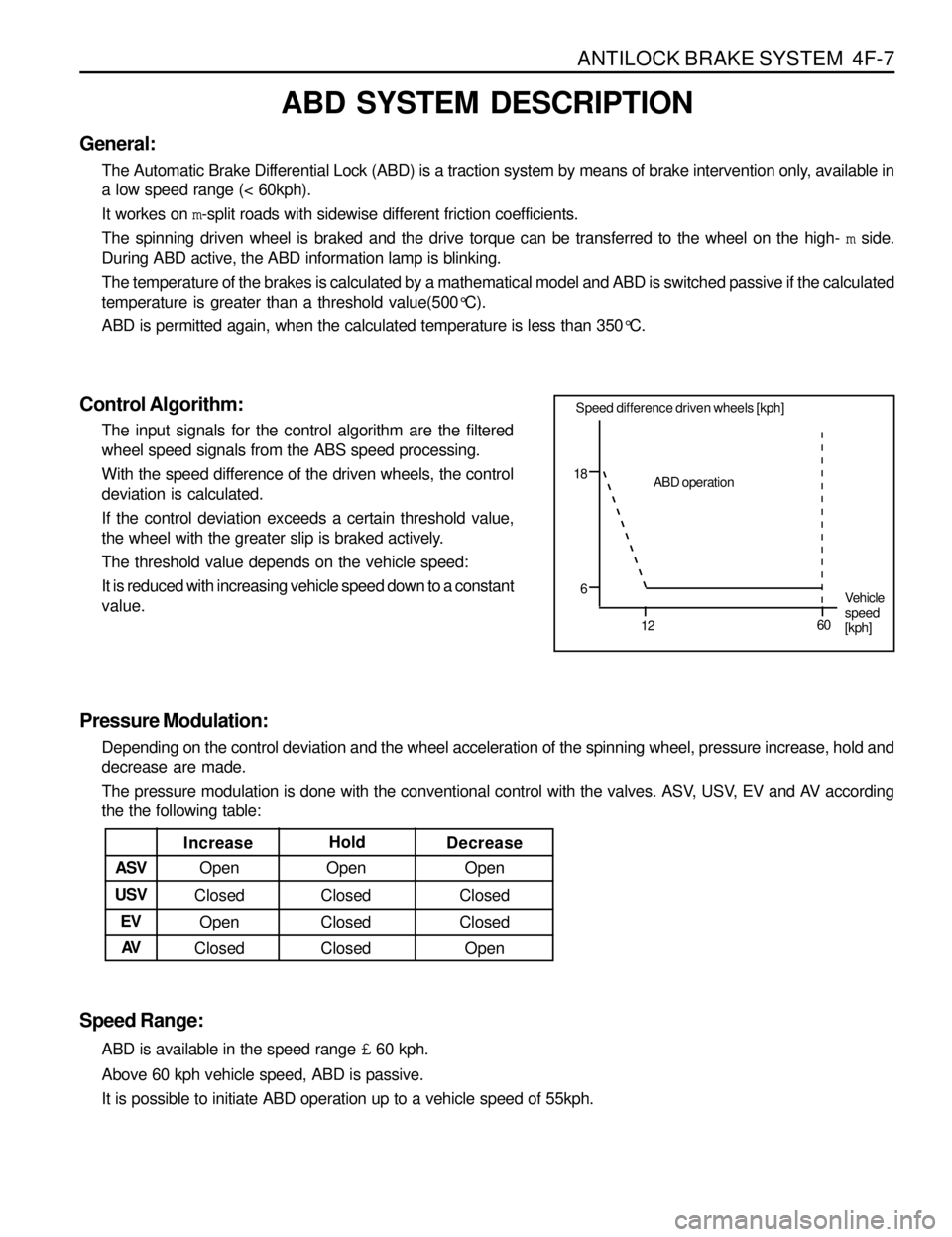
ANTILOCK BRAKE SYSTEM 4F-7
ABD SYSTEM DESCRIPTION
General:
The Automatic Brake Differential Lock (ABD) is a traction system by means of brake intervention only, available in
a low speed range (< 60kph).
It workes on m-split roads with sidewise different friction coefficients.
The spinning driven wheel is braked and the drive torque can be transferred to the wheel on the high- m side.
During ABD active, the ABD information lamp is blinking.
The temperature of the brakes is calculated by a mathematical model and ABD is switched passive if the calculated
temperature is greater than a threshold value(500°C).
ABD is permitted again, when the calculated temperature is less than 350°C.
Control Algorithm:
The input signals for the control algorithm are the filtered
wheel speed signals from the ABS speed processing.
With the speed difference of the driven wheels, the control
deviation is calculated.
If the control deviation exceeds a certain threshold value,
the wheel with the greater slip is braked actively.
The threshold value depends on the vehicle speed:
It is reduced with increasing vehicle speed down to a constant
value.
Pressure Modulation:
Depending on the control deviation and the wheel acceleration of the spinning wheel, pressure increase, hold and
decrease are made.
The pressure modulation is done with the conventional control with the valves. ASV, USV, EV and AV according
the the following table:
Speed Range:
ABD is available in the speed range £ 60 kph.
Above 60 kph vehicle speed, ABD is passive.
It is possible to initiate ABD operation up to a vehicle speed of 55kph.
Increase
Open Open Open ASVDecrease Hold
Closed Closed Closed
Closed Closed Open
Open Closed Closed USV
EV
AV
Speed difference driven wheels [kph]
18
6
1260ABD operation
Vehicle
speed
[kph]
Page 1034 of 1463
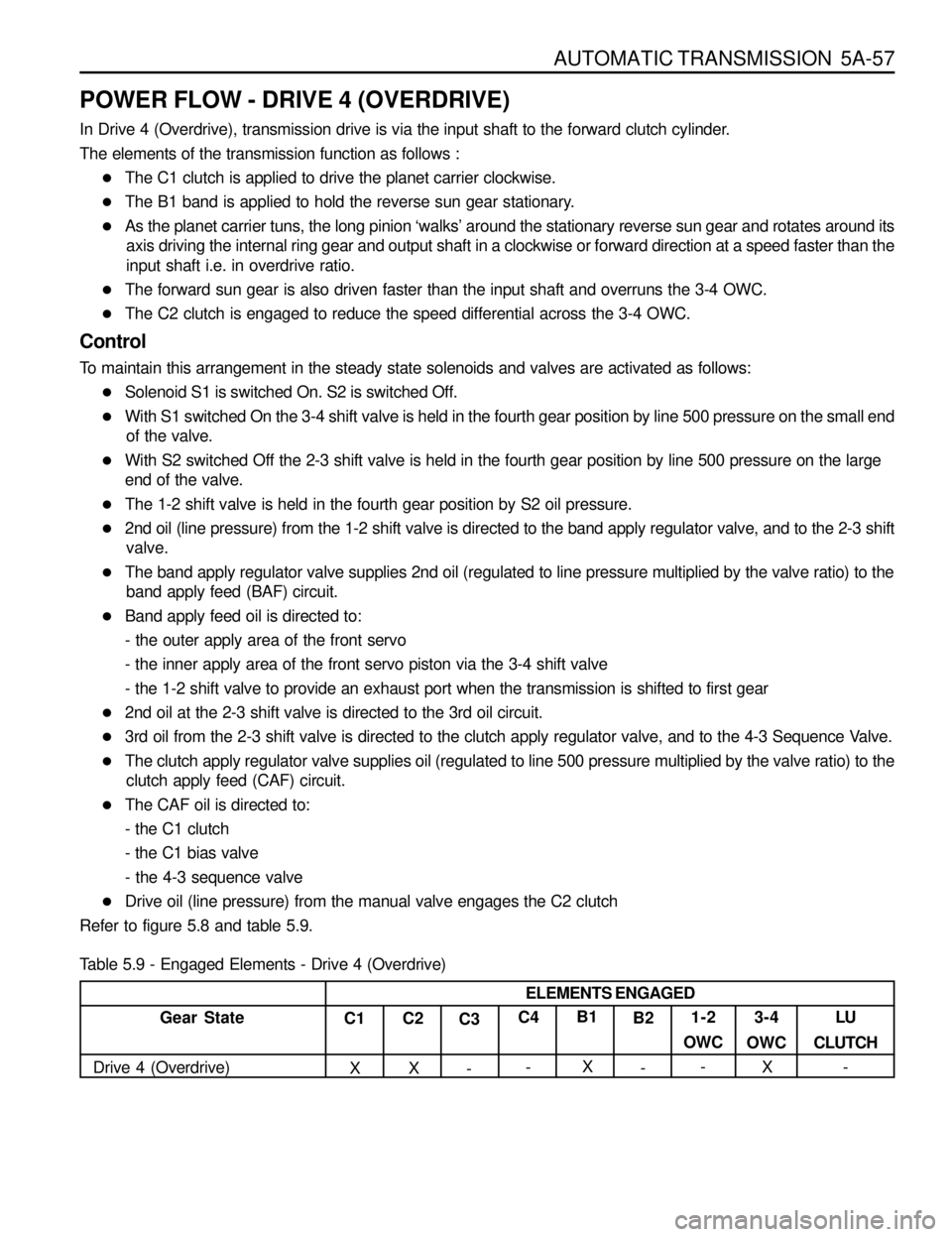
AUTOMATIC TRANSMISSION 5A-57
POWER FLOW - DRIVE 4 (OVERDRIVE)
In Drive 4 (Overdrive), transmission drive is via the input shaft to the forward clutch cylinder.
The elements of the transmission function as follows :
lThe C1 clutch is applied to drive the planet carrier clockwise.
lThe B1 band is applied to hold the reverse sun gear stationary.
lAs the planet carrier tuns, the long pinion ‘walks’ around the stationary reverse sun gear and rotates around its
axis driving the internal ring gear and output shaft in a clockwise or forward direction at a speed faster than the
input shaft i.e. in overdrive ratio.
lThe forward sun gear is also driven faster than the input shaft and overruns the 3-4 OWC.
lThe C2 clutch is engaged to reduce the speed differential across the 3-4 OWC.
Control
To maintain this arrangement in the steady state solenoids and valves are activated as follows:
lSolenoid S1 is switched On. S2 is switched Off.
lWith S1 switched On the 3-4 shift valve is held in the fourth gear position by line 500 pressure on the small end
of the valve.
lWith S2 switched Off the 2-3 shift valve is held in the fourth gear position by line 500 pressure on the large
end of the valve.
lThe 1-2 shift valve is held in the fourth gear position by S2 oil pressure.
l2nd oil (line pressure) from the 1-2 shift valve is directed to the band apply regulator valve, and to the 2-3 shift
valve.
lThe band apply regulator valve supplies 2nd oil (regulated to line pressure multiplied by the valve ratio) to the
band apply feed (BAF) circuit.
lBand apply feed oil is directed to:
- the outer apply area of the front servo
- the inner apply area of the front servo piston via the 3-4 shift valve
- the 1-2 shift valve to provide an exhaust port when the transmission is shifted to first gear
l2nd oil at the 2-3 shift valve is directed to the 3rd oil circuit.
l3rd oil from the 2-3 shift valve is directed to the clutch apply regulator valve, and to the 4-3 Sequence Valve.
lThe clutch apply regulator valve supplies oil (regulated to line 500 pressure multiplied by the valve ratio) to the
clutch apply feed (CAF) circuit.
lThe CAF oil is directed to:
- the C1 clutch
- the C1 bias valve
- the 4-3 sequence valve
lDrive oil (line pressure) from the manual valve engages the C2 clutch
Refer to figure 5.8 and table 5.9.
Table 5.9 - Engaged Elements - Drive 4 (Overdrive)
Gear State
Drive 4 (Overdrive)C1
XC2
XC3
-C4
-B1
XB2
-1-2
OWC
-3-4
OWC
XLU
CLUTCH
- ELEMENTS ENGAGED