change time SSANGYONG MUSSO 1998 Workshop Owner's Manual
[x] Cancel search | Manufacturer: SSANGYONG, Model Year: 1998, Model line: MUSSO, Model: SSANGYONG MUSSO 1998Pages: 1463, PDF Size: 19.88 MB
Page 1045 of 1463
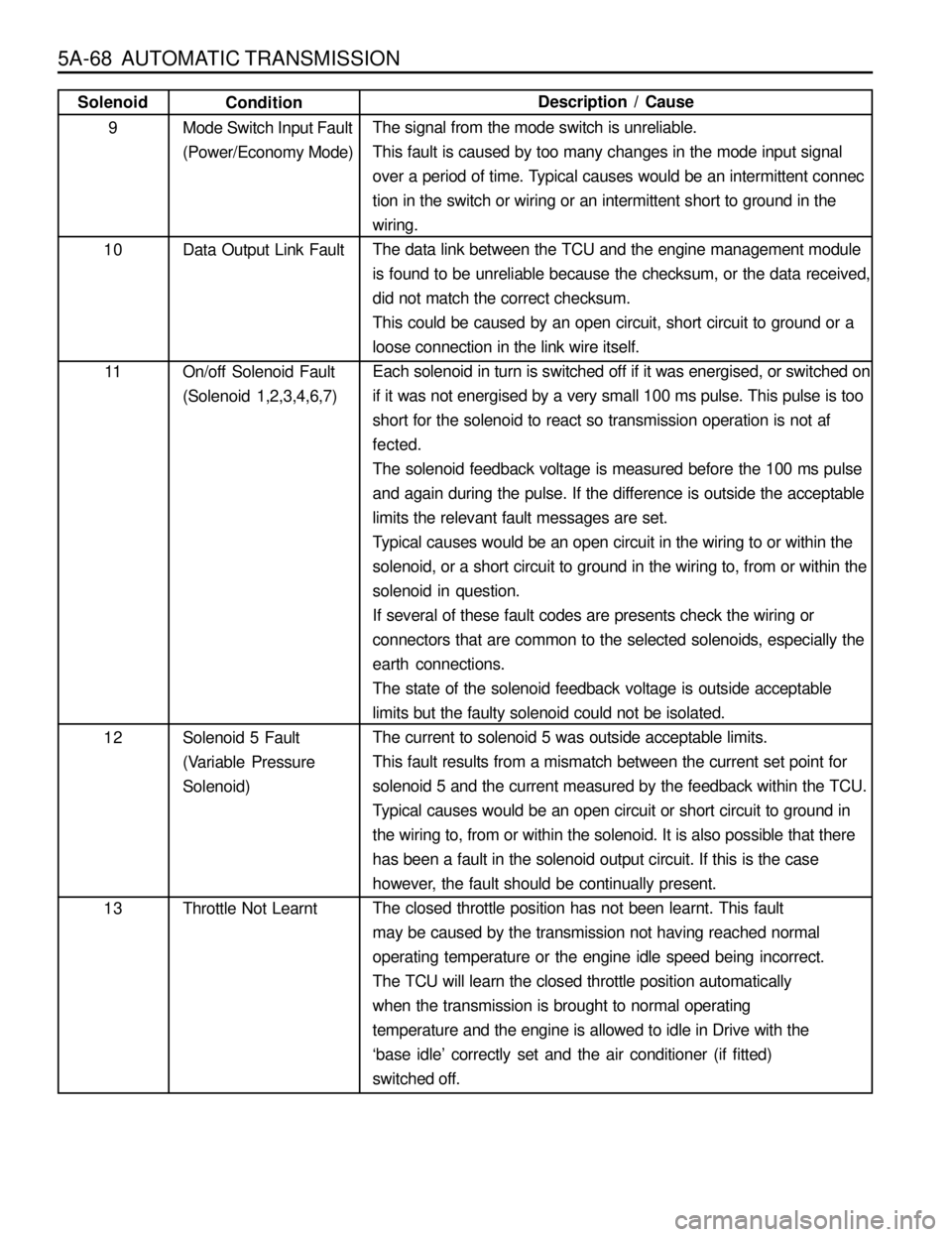
5A-68 AUTOMATIC TRANSMISSION
Description / Cause
The signal from the mode switch is unreliable.
This fault is caused by too many changes in the mode input signal
over a period of time. Typical causes would be an intermittent connec
tion in the switch or wiring or an intermittent short to ground in the
wiring.
The data link between the TCU and the engine management module
is found to be unreliable because the checksum, or the data received,
did not match the correct checksum.
This could be caused by an open circuit, short circuit to ground or a
loose connection in the link wire itself.
Each solenoid in turn is switched off if it was energised, or switched on
if it was not energised by a very small 100 ms pulse. This pulse is too
short for the solenoid to react so transmission operation is not af
fected.
The solenoid feedback voltage is measured before the 100 ms pulse
and again during the pulse. If the difference is outside the acceptable
limits the relevant fault messages are set.
Typical causes would be an open circuit in the wiring to or within the
solenoid, or a short circuit to ground in the wiring to, from or within the
solenoid in question.
If several of these fault codes are presents check the wiring or
connectors that are common to the selected solenoids, especially the
earth connections.
The state of the solenoid feedback voltage is outside acceptable
limits but the faulty solenoid could not be isolated.
The current to solenoid 5 was outside acceptable limits.
This fault results from a mismatch between the current set point for
solenoid 5 and the current measured by the feedback within the TCU.
Typical causes would be an open circuit or short circuit to ground in
the wiring to, from or within the solenoid. It is also possible that there
has been a fault in the solenoid output circuit. If this is the case
however, the fault should be continually present.
The closed throttle position has not been learnt. This fault
may be caused by the transmission not having reached normal
operating temperature or the engine idle speed being incorrect.
The TCU will learn the closed throttle position automatically
when the transmission is brought to normal operating
temperature and the engine is allowed to idle in Drive with the
‘base idle’ correctly set and the air conditioner (if fitted)
switched off. Condition
Mode Switch Input Fault
(Power/Economy Mode)
Data Output Link Fault
On/off Solenoid Fault
(Solenoid 1,2,3,4,6,7)
Solenoid 5 Fault
(Variable Pressure
Solenoid)
Throttle Not LearntSolenoid
9
10
11
12
13
Page 1180 of 1463
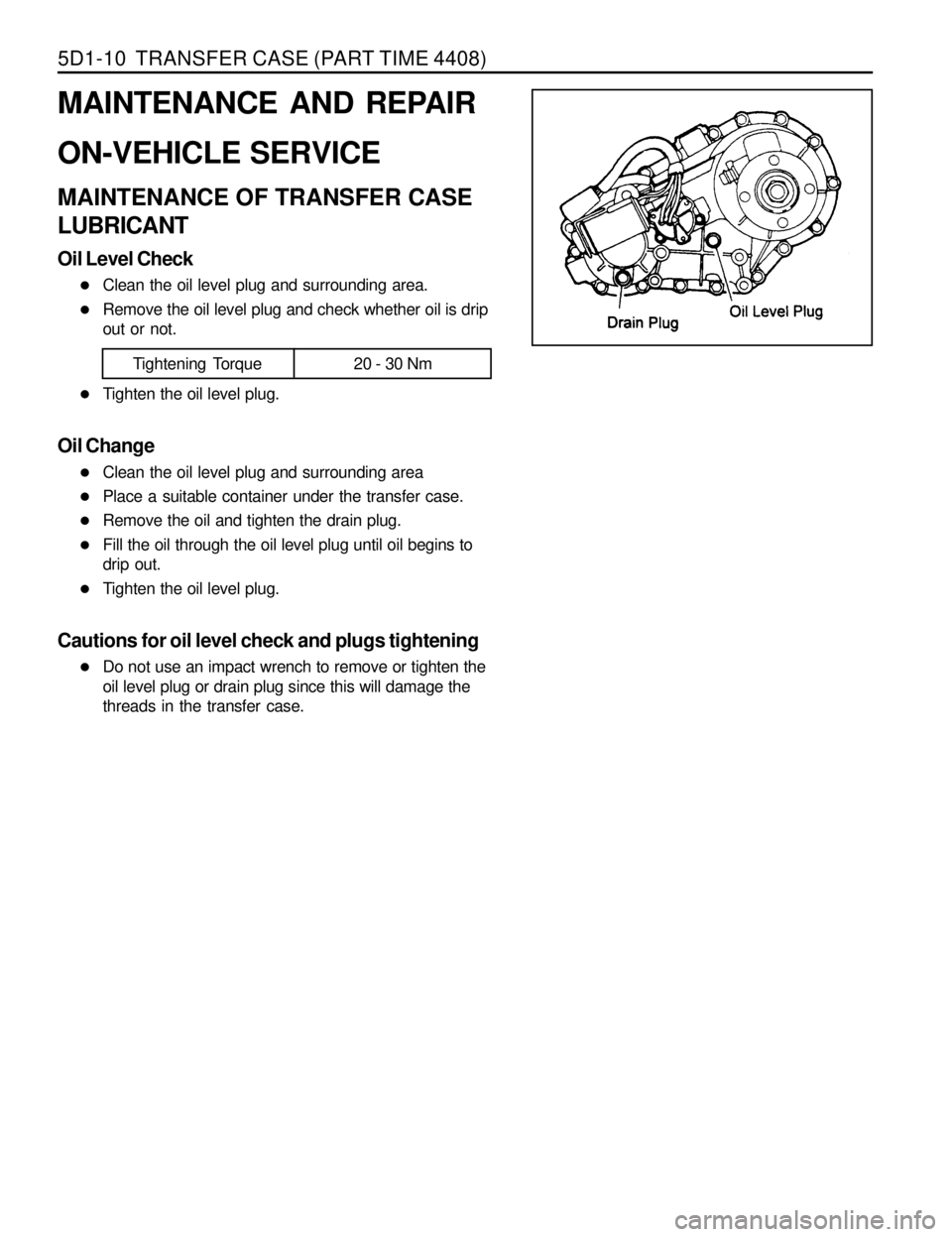
5D1-10 TRANSFER CASE (PART TIME 4408)
MAINTENANCE AND REPAIR
ON-VEHICLE SERVICE
MAINTENANCE OF TRANSFER CASE
LUBRICANT
Oil Level Check
lClean the oil level plug and surrounding area.
lRemove the oil level plug and check whether oil is drip
out or not.
lTighten the oil level plug.
Oil Change
lClean the oil level plug and surrounding area
lPlace a suitable container under the transfer case.
lRemove the oil and tighten the drain plug.
lFill the oil through the oil level plug until oil begins to
drip out.
lTighten the oil level plug.
Cautions for oil level check and plugs tightening
lDo not use an impact wrench to remove or tighten the
oil level plug or drain plug since this will damage the
threads in the transfer case.
Tightening Torque 20 - 30 Nm
Page 1212 of 1463
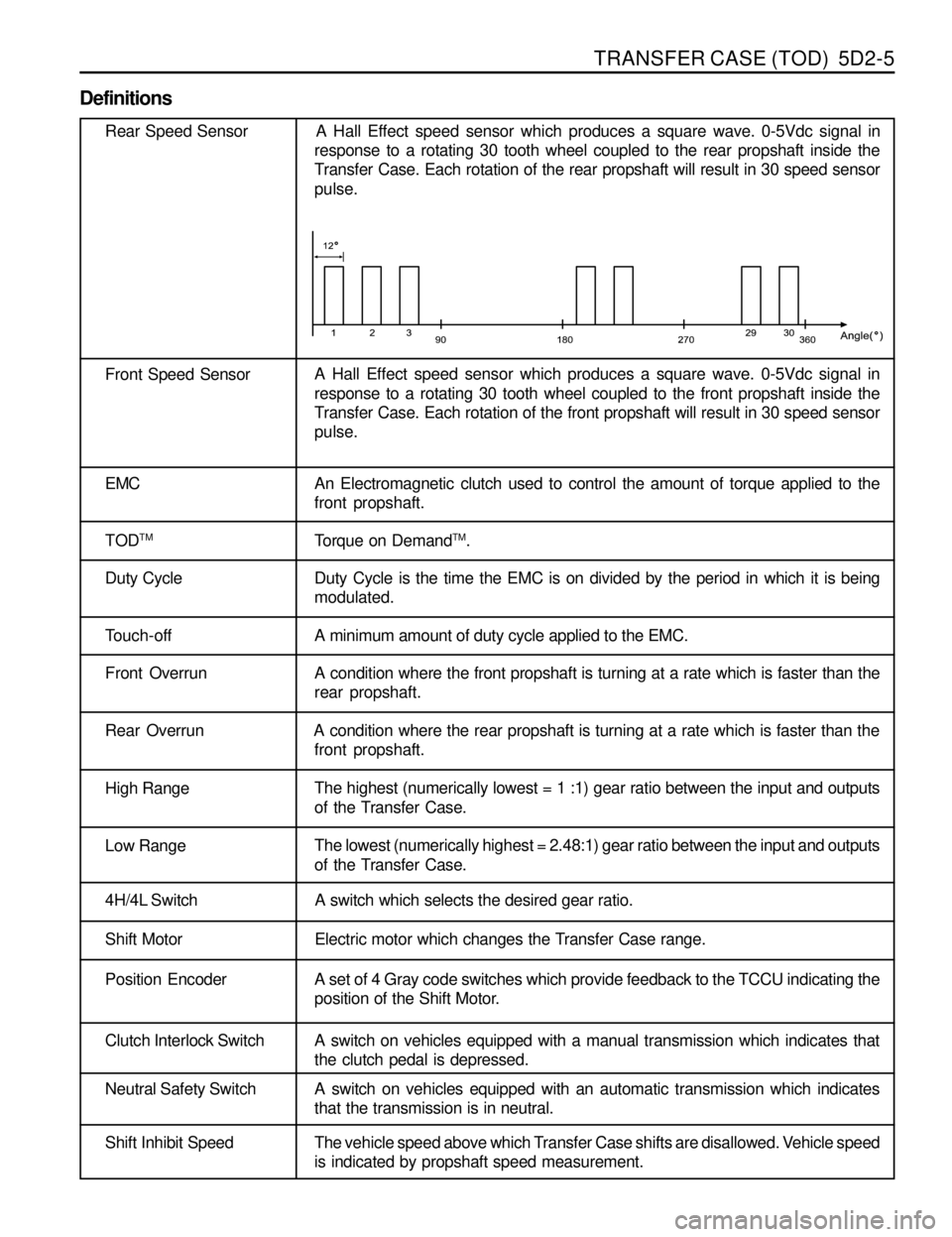
TRANSFER CASE (TOD) 5D2-5
Definitions
Rear Speed Sensor A Hall Effect speed sensor which produces a square wave. 0-5Vdc signal in
response to a rotating 30 tooth wheel coupled to the rear propshaft inside the
Transfer Case. Each rotation of the rear propshaft will result in 30 speed sensor
pulse.
Front Speed SensorA Hall Effect speed sensor which produces a square wave. 0-5Vdc signal in
response to a rotating 30 tooth wheel coupled to the front propshaft inside the
Transfer Case. Each rotation of the front propshaft will result in 30 speed sensor
pulse.
EMC An Electromagnetic clutch used to control the amount of torque applied to the
front propshaft.
TOD
TMTorque on DemandTM.
Duty Cycle Duty Cycle is the time the EMC is on divided by the period in which it is being
modulated.
Touch-off A minimum amount of duty cycle applied to the EMC.
Front OverrunA condition where the front propshaft is turning at a rate which is faster than the
rear propshaft.
Rear Overrun A condition where the rear propshaft is turning at a rate which is faster than the
front propshaft.
High RangeThe highest (numerically lowest = 1 :1) gear ratio between the input and outputs
of the Transfer Case.
Low RangeThe lowest (numerically highest = 2.48:1) gear ratio between the input and outputs
of the Transfer Case.
4H/4L Switch A switch which selects the desired gear ratio.
Shift Motor Electric motor which changes the Transfer Case range.
Position Encoder A set of 4 Gray code switches which provide feedback to the TCCU indicating the
position of the Shift Motor.
Clutch Interlock Switch A switch on vehicles equipped with a manual transmission which indicates that
the clutch pedal is depressed.
Neutral Safety Switch A switch on vehicles equipped with an automatic transmission which indicates
that the transmission is in neutral.
Shift Inhibit Speed The vehicle speed above which Transfer Case shifts are disallowed. Vehicle speed
is indicated by propshaft speed measurement.
Page 1236 of 1463
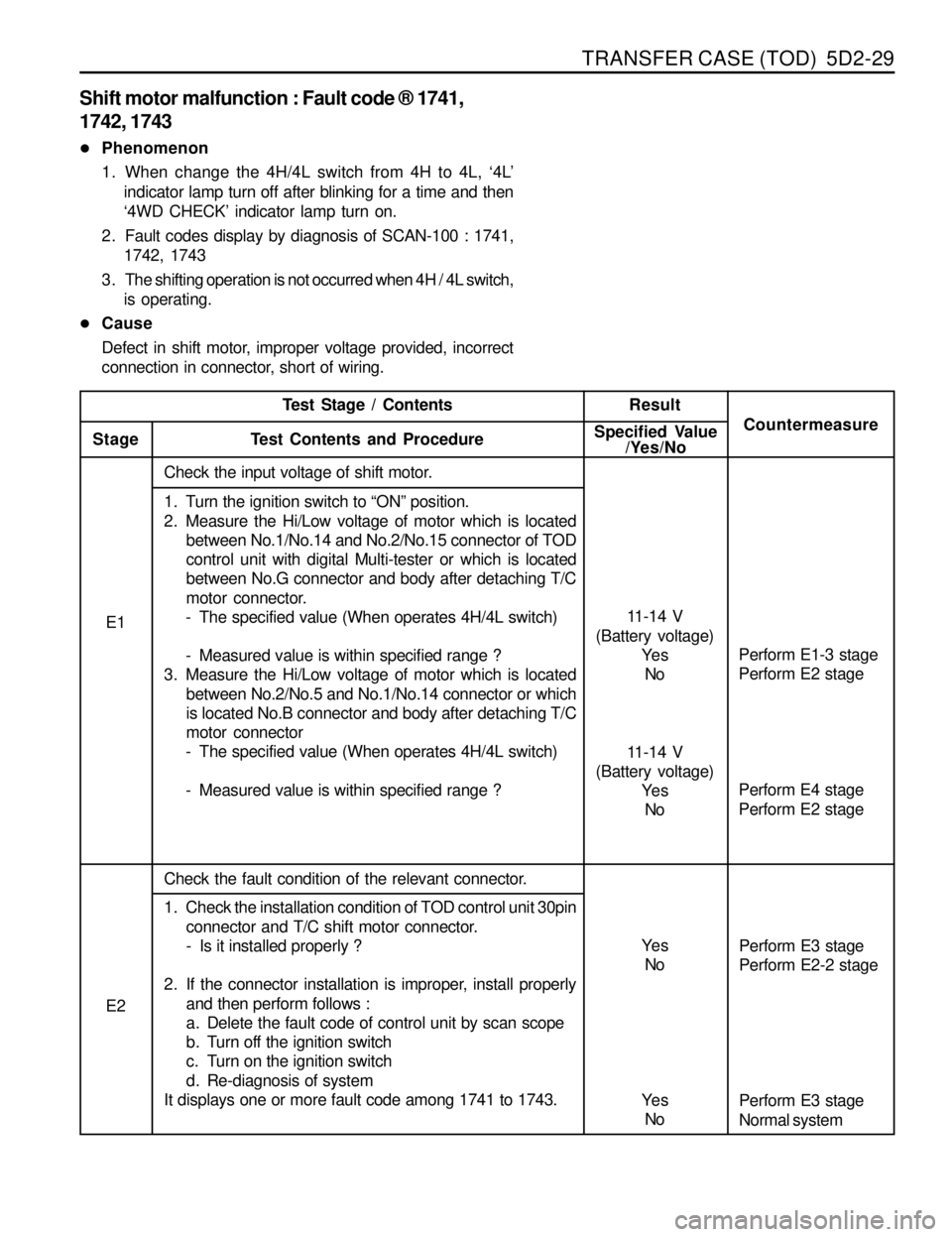
TRANSFER CASE (TOD) 5D2-29
Shift motor malfunction : Fault code ® 1741,
1742, 1743
lPhenomenon
1. When change the 4H/4L switch from 4H to 4L, ‘4L’
indicator lamp turn off after blinking for a time and then
‘4WD CHECK’ indicator lamp turn on.
2. Fault codes display by diagnosis of SCAN-100 : 1741,
1742, 1743
3. The shifting operation is not occurred when 4H / 4L switch,
is operating.
lCause
Defect in shift motor, improper voltage provided, incorrect
connection in connector, short of wiring.
11-14 V
(Battery voltage)
Ye s
No E1
11-14 V
(Battery voltage)
Ye s
No
Ye s
No
E2
Ye s
No Test Stage / Contents
Result
Stage Test Contents and ProcedureSpecified Value
/Yes/NoCountermeasure
Check the input voltage of shift motor.
1. Turn the ignition switch to “ON” position.
2. Measure the Hi/Low voltage of motor which is located
between No.1/No.14 and No.2/No.15 connector of TOD
control unit with digital Multi-tester or which is located
between No.G connector and body after detaching T/C
motor connector.
- The specified value (When operates 4H/4L switch)
- Measured value is within specified range ?
3. Measure the Hi/Low voltage of motor which is located
between No.2/No.5 and No.1/No.14 connector or which
is located No.B connector and body after detaching T/C
motor connector
- The specified value (When operates 4H/4L switch)
- Measured value is within specified range ?
Check the fault condition of the relevant connector.
1. Check the installation condition of TOD control unit 30pin
connector and T/C shift motor connector.
- Is it installed properly ?
2. If the connector installation is improper, install properly
and then perform follows :
a. Delete the fault code of control unit by scan scope
b. Turn off the ignition switch
c. Turn on the ignition switch
d. Re-diagnosis of system
It displays one or more fault code among 1741 to 1743.Perform E1-3 stage
Perform E2 stage
Perform E4 stage
Perform E2 stage
Perform E3 stage
Perform E2-2 stage
Perform E3 stage
Normal system
Page 1266 of 1463
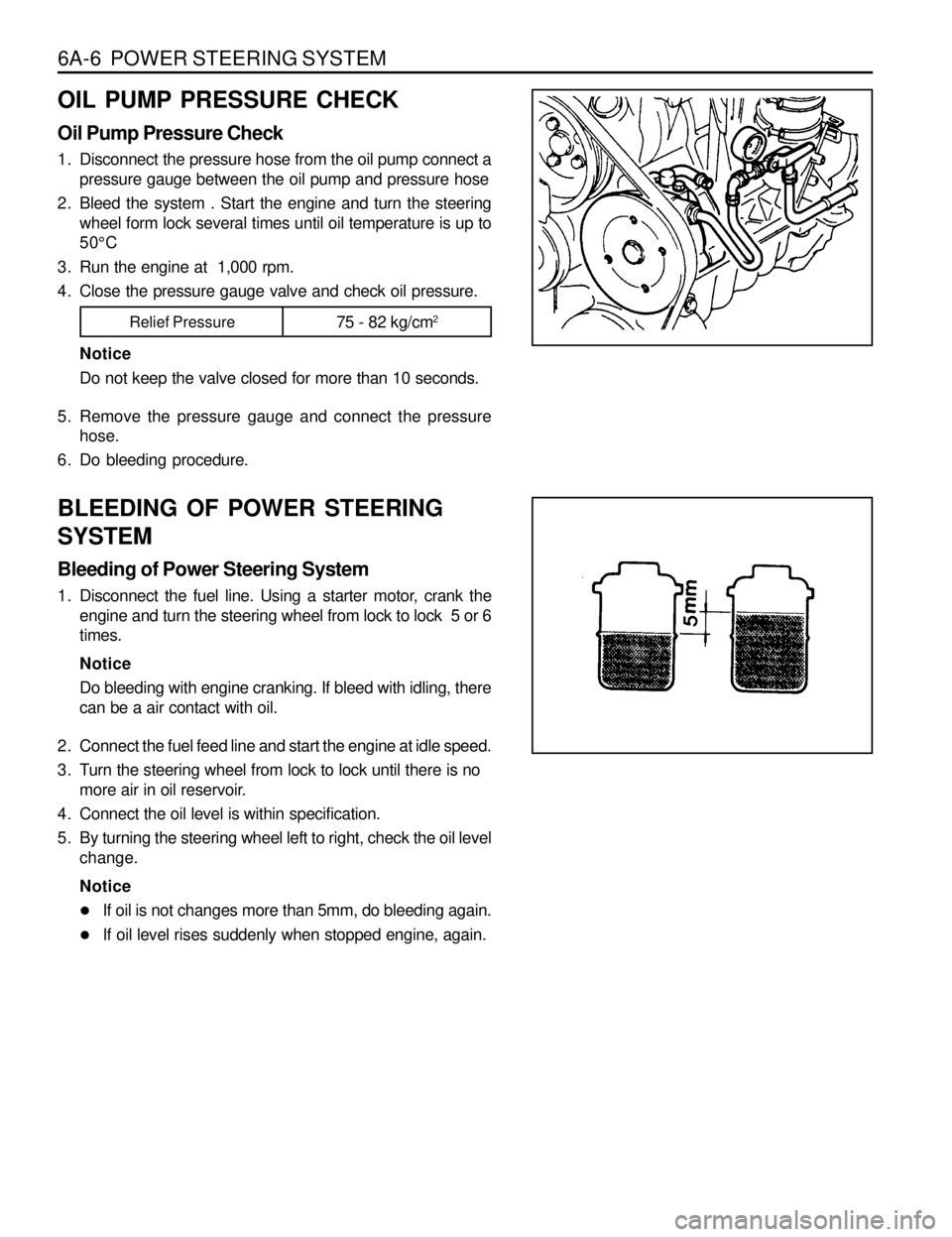
6A-6 POWER STEERING SYSTEM
OIL PUMP PRESSURE CHECK
Oil Pump Pressure Check
1. Disconnect the pressure hose from the oil pump connect a
pressure gauge between the oil pump and pressure hose
2. Bleed the system . Start the engine and turn the steering
wheel form lock several times until oil temperature is up to
50°C
3. Run the engine at 1,000 rpm.
4. Close the pressure gauge valve and check oil pressure.
Notice
Do not keep the valve closed for more than 10 seconds.
5. Remove the pressure gauge and connect the pressure
hose.
6. Do bleeding procedure.
BLEEDING OF POWER STEERING
SYSTEM
Bleeding of Power Steering System
1. Disconnect the fuel line. Using a starter motor, crank the
engine and turn the steering wheel from lock to lock 5 or 6
times.
Notice
Do bleeding with engine cranking. If bleed with idling, there
can be a air contact with oil.
2. Connect the fuel feed line and start the engine at idle speed.
3. Turn the steering wheel from lock to lock until there is no
more air in oil reservoir.
4. Connect the oil level is within specification.
5. By turning the steering wheel left to right, check the oil level
change.
Notice
lIf oil is not changes more than 5mm, do bleeding again.
lIf oil level rises suddenly when stopped engine, again.
Relief Pressure75 - 82 kg/cm2
Page 1325 of 1463
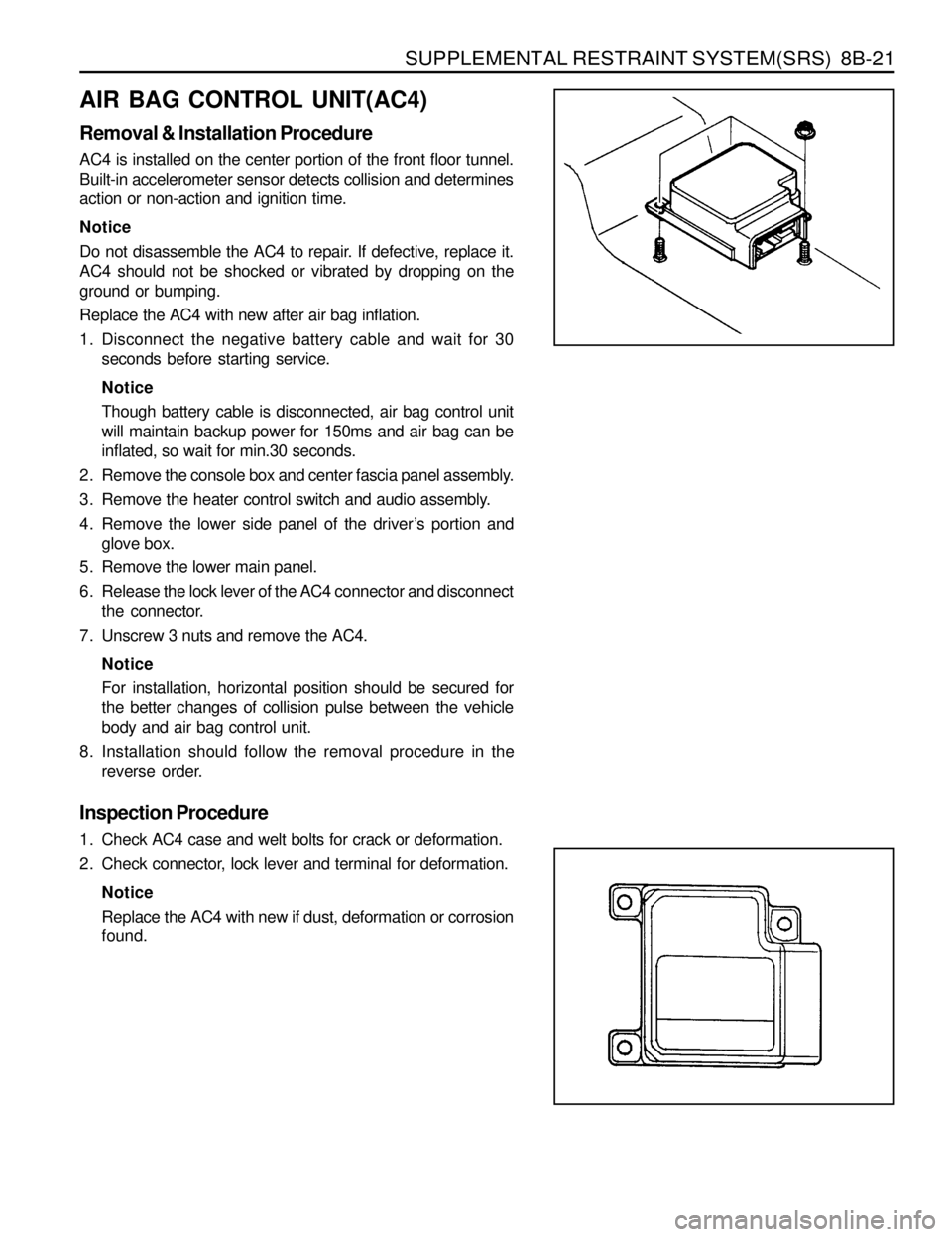
SUPPLEMENTAL RESTRAINT SYSTEM(SRS) 8B-21
AIR BAG CONTROL UNIT(AC4)
Removal & Installation Procedure
AC4 is installed on the center portion of the front floor tunnel.
Built-in accelerometer sensor detects collision and determines
action or non-action and ignition time.
Notice
Do not disassemble the AC4 to repair. If defective, replace it.
AC4 should not be shocked or vibrated by dropping on the
ground or bumping.
Replace the AC4 with new after air bag inflation.
1. Disconnect the negative battery cable and wait for 30
seconds before starting service.
Notice
Though battery cable is disconnected, air bag control unit
will maintain backup power for 150ms and air bag can be
inflated, so wait for min.30 seconds.
2. Remove the console box and center fascia panel assembly.
3. Remove the heater control switch and audio assembly.
4. Remove the lower side panel of the driver’s portion and
glove box.
5. Remove the lower main panel.
6. Release the lock lever of the AC4 connector and disconnect
the connector.
7. Unscrew 3 nuts and remove the AC4.
Notice
For installation, horizontal position should be secured for
the better changes of collision pulse between the vehicle
body and air bag control unit.
8. Installation should follow the removal procedure in the
reverse order.
Inspection Procedure
1. Check AC4 case and welt bolts for crack or deformation.
2. Check connector, lock lever and terminal for deformation.
Notice
Replace the AC4 with new if dust, deformation or corrosion
found.
Page 1431 of 1463
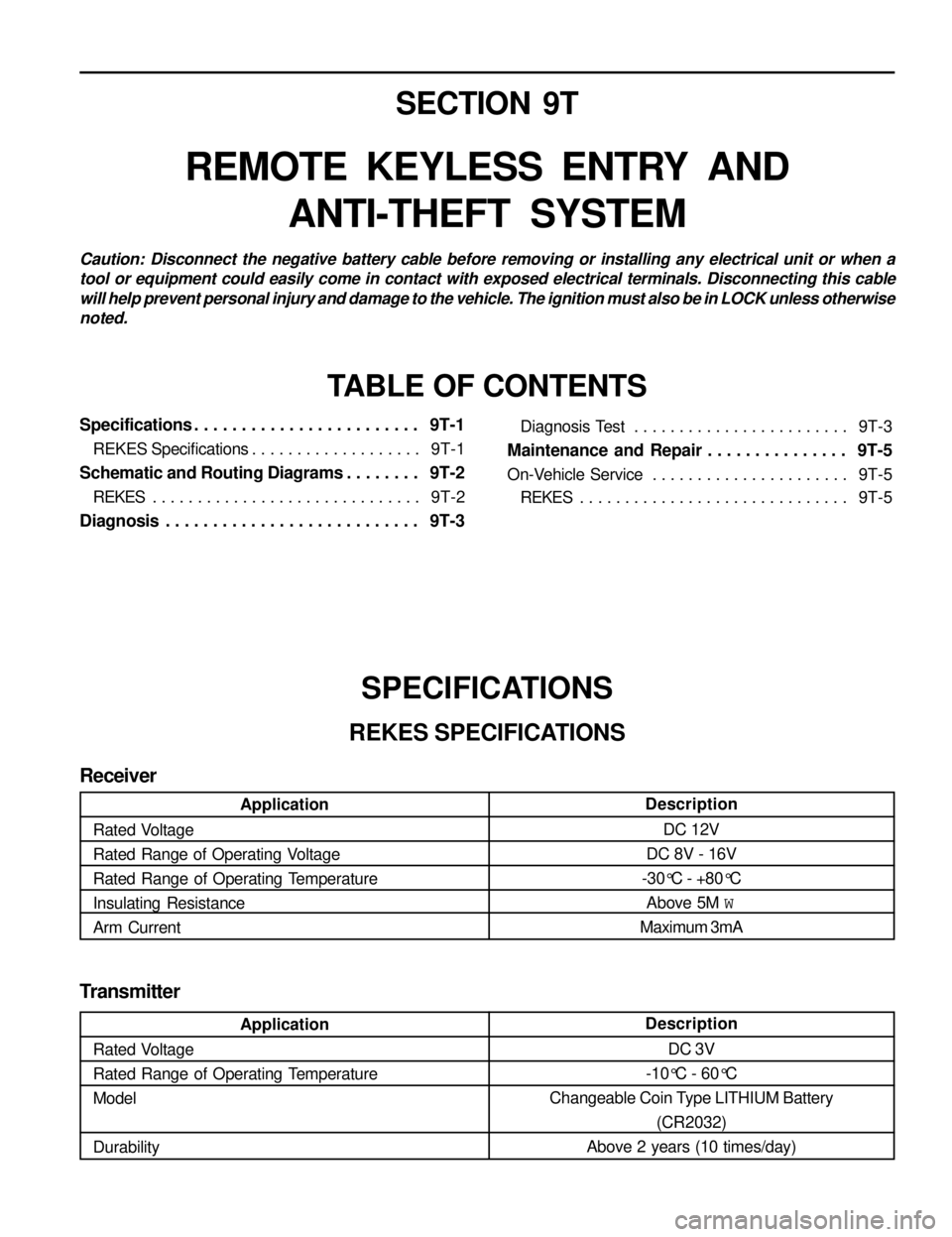
SECTION 9T
REMOTE KEYLESS ENTRY AND
ANTI-THEFT SYSTEM
Caution: Disconnect the negative battery cable before removing or installing any electrical unit or when a
tool or equipment could easily come in contact with exposed electrical terminals. Disconnecting this cable
will help prevent personal injury and damage to the vehicle. The ignition must also be in LOCK unless otherwise
noted.
TABLE OF CONTENTS
Specifications . . . . . . . . . . . . . . . . . . . . . . . . 9T-1
REKES Specifications . . . . . . . . . . . . . . . . . . . 9T-1
Schematic and Routing Diagrams . . . . . . . . 9T-2
REKES . . . . . . . . . . . . . . . . . . . . . . . . . . . . . . 9T-2
Diagnosis . . . . . . . . . . . . . . . . . . . . . . . . . . . 9T-3
SPECIFICATIONS
REKES SPECIFICATIONS
Diagnosis Test . . . . . . . . . . . . . . . . . . . . . . . . 9T-3
Maintenance and Repair . . . . . . . . . . . . . . . 9T-5
On-Vehicle Service . . . . . . . . . . . . . . . . . . . . . . 9T-5
REKES . . . . . . . . . . . . . . . . . . . . . . . . . . . . . . 9T-5
Transmitter
Description
DC 3V
-10°C - 60°C
Changeable Coin Type LITHIUM Battery
(CR2032)
Above 2 years (10 times/day) Application
Rated Voltage
Rated Range of Operating Temperature
Model
Durability
Description
DC 12V
DC 8V - 16V
-30°C - +80°C
Above 5M W
Maximum 3mA Application
Rated Voltage
Rated Range of Operating Voltage
Rated Range of Operating Temperature
Insulating Resistance
Arm Current
Receiver
Page 1440 of 1463
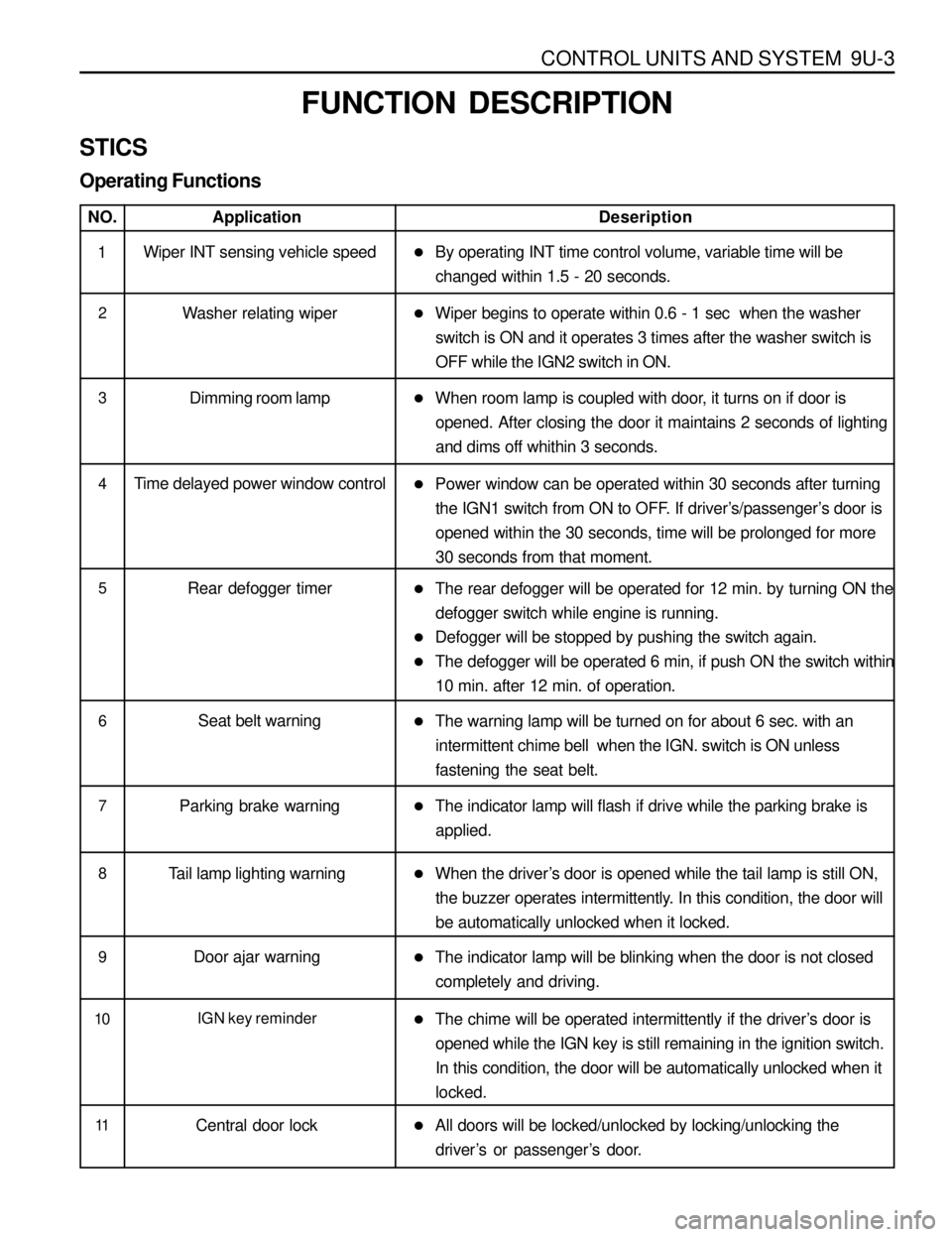
CONTROL UNITS AND SYSTEM 9U-3
FUNCTION DESCRIPTION
STICS
Operating Functions
NO.ApplicationDeseription
1Wiper INT sensing vehicle speed
lBy operating INT time control volume, variable time will be
changed within 1.5 - 20 seconds.
2Washer relating wiperlWiper begins to operate within 0.6 - 1 sec when the washer
switch is ON and it operates 3 times after the washer switch is
OFF while the IGN2 switch in ON.
3Dimming room lamplWhen room lamp is coupled with door, it turns on if door is
opened. After closing the door it maintains 2 seconds of lighting
and dims off whithin 3 seconds.
4Time delayed power window controllPower window can be operated within 30 seconds after turning
the IGN1 switch from ON to OFF. If driver’s/passenger’s door is
opened within the 30 seconds, time will be prolonged for more
30 seconds from that moment.
5Rear defogger timerlThe rear defogger will be operated for 12 min. by turning ON the
defogger switch while engine is running.
lDefogger will be stopped by pushing the switch again.
lThe defogger will be operated 6 min, if push ON the switch within
10 min. after 12 min. of operation.
6Seat belt warninglThe warning lamp will be turned on for about 6 sec. with an
intermittent chime bell when the IGN. switch is ON unless
fastening the seat belt.
7Parking brake warninglThe indicator lamp will flash if drive while the parking brake is
applied.
8Tail lamp lighting warninglWhen the driver’s door is opened while the tail lamp is still ON,
the buzzer operates intermittently. In this condition, the door will
be automatically unlocked when it locked.
9Door ajar warninglThe indicator lamp will be blinking when the door is not closed
completely and driving.
10IGN key reminderlThe chime will be operated intermittently if the driver’s door is
opened while the IGN key is still remaining in the ignition switch.
In this condition, the door will be automatically unlocked when it
locked.
11Central door locklAll doors will be locked/unlocked by locking/unlocking the
driver’s or passenger’s door.