change time SSANGYONG MUSSO 1998 Workshop User Guide
[x] Cancel search | Manufacturer: SSANGYONG, Model Year: 1998, Model line: MUSSO, Model: SSANGYONG MUSSO 1998Pages: 1463, PDF Size: 19.88 MB
Page 696 of 1463
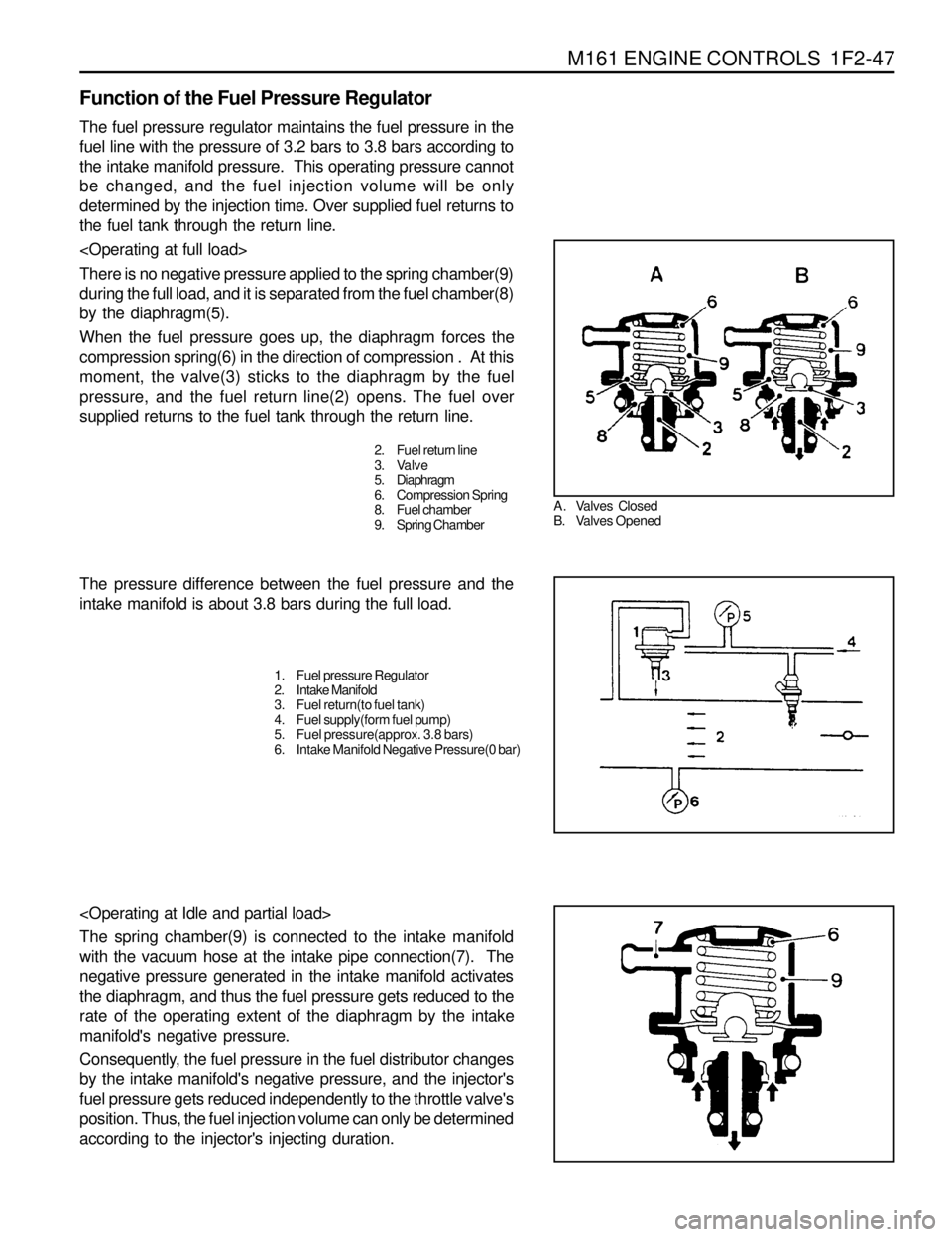
M161 ENGINE CONTROLS 1F2-47
A . Valves Closed
B. Valves Opened
The pressure difference between the fuel pressure and the
intake manifold is about 3.8 bars during the full load.
The spring chamber(9) is connected to the intake manifold
with the vacuum hose at the intake pipe connection(7). The
negative pressure generated in the intake manifold activates
the diaphragm, and thus the fuel pressure gets reduced to the
rate of the operating extent of the diaphragm by the intake
manifold's negative pressure.
Consequently, the fuel pressure in the fuel distributor changes
by the intake manifold's negative pressure, and the injector's
fuel pressure gets reduced independently to the throttle valve's
position. Thus, the fuel injection volume can only be determined
according to the injector's injecting duration.
2. Fuel return line
3. Valve
5. Diaphragm
6. Compression Spring
8. Fuel chamber
9. Spring Chamber
1. Fuel pressure Regulator
2. Intake Manifold
3. Fuel return(to fuel tank)
4. Fuel supply(form fuel pump)
5. Fuel pressure(approx. 3.8 bars)
6. Intake Manifold Negative Pressure(0 bar)
Function of the Fuel Pressure Regulator
The fuel pressure regulator maintains the fuel pressure in the
fuel line with the pressure of 3.2 bars to 3.8 bars according to
the intake manifold pressure. This operating pressure cannot
be changed, and the fuel injection volume will be only
determined by the injection time. Over supplied fuel returns to
the fuel tank through the return line.
There is no negative pressure applied to the spring chamber(9)
during the full load, and it is separated from the fuel chamber(8)
by the diaphragm(5).
When the fuel pressure goes up, the diaphragm forces the
compression spring(6) in the direction of compression . At this
moment, the valve(3) sticks to the diaphragm by the fuel
pressure, and the fuel return line(2) opens. The fuel over
supplied returns to the fuel tank through the return line.
Page 938 of 1463
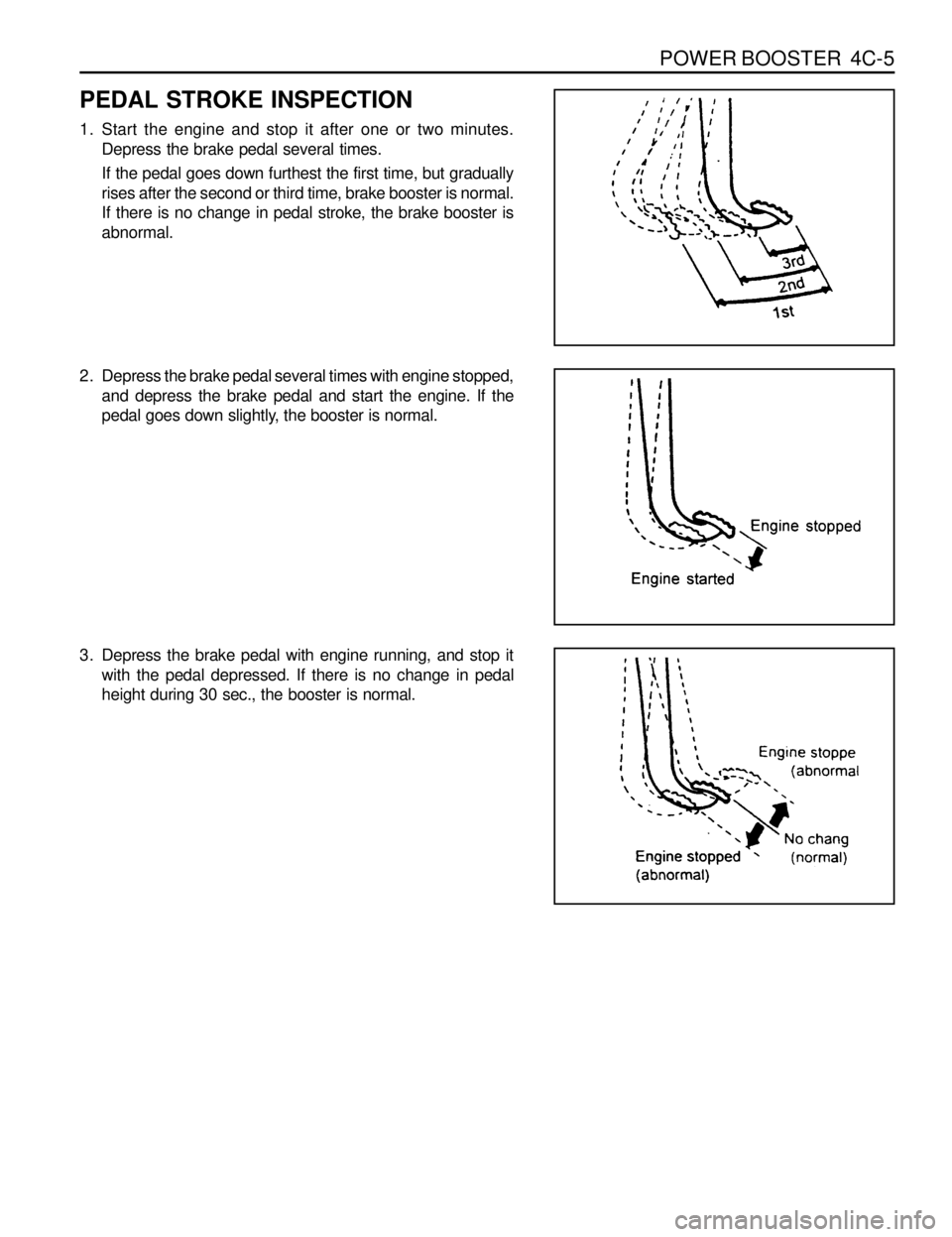
POWER BOOSTER 4C-5
PEDAL STROKE INSPECTION
1. Start the engine and stop it after one or two minutes.
Depress the brake pedal several times.
If the pedal goes down furthest the first time, but gradually
rises after the second or third time, brake booster is normal.
If there is no change in pedal stroke, the brake booster is
abnormal.
2. Depress the brake pedal several times with engine stopped,
and depress the brake pedal and start the engine. If the
pedal goes down slightly, the booster is normal.
3. Depress the brake pedal with engine running, and stop it
with the pedal depressed. If there is no change in pedal
height during 30 sec., the booster is normal.
Page 942 of 1463
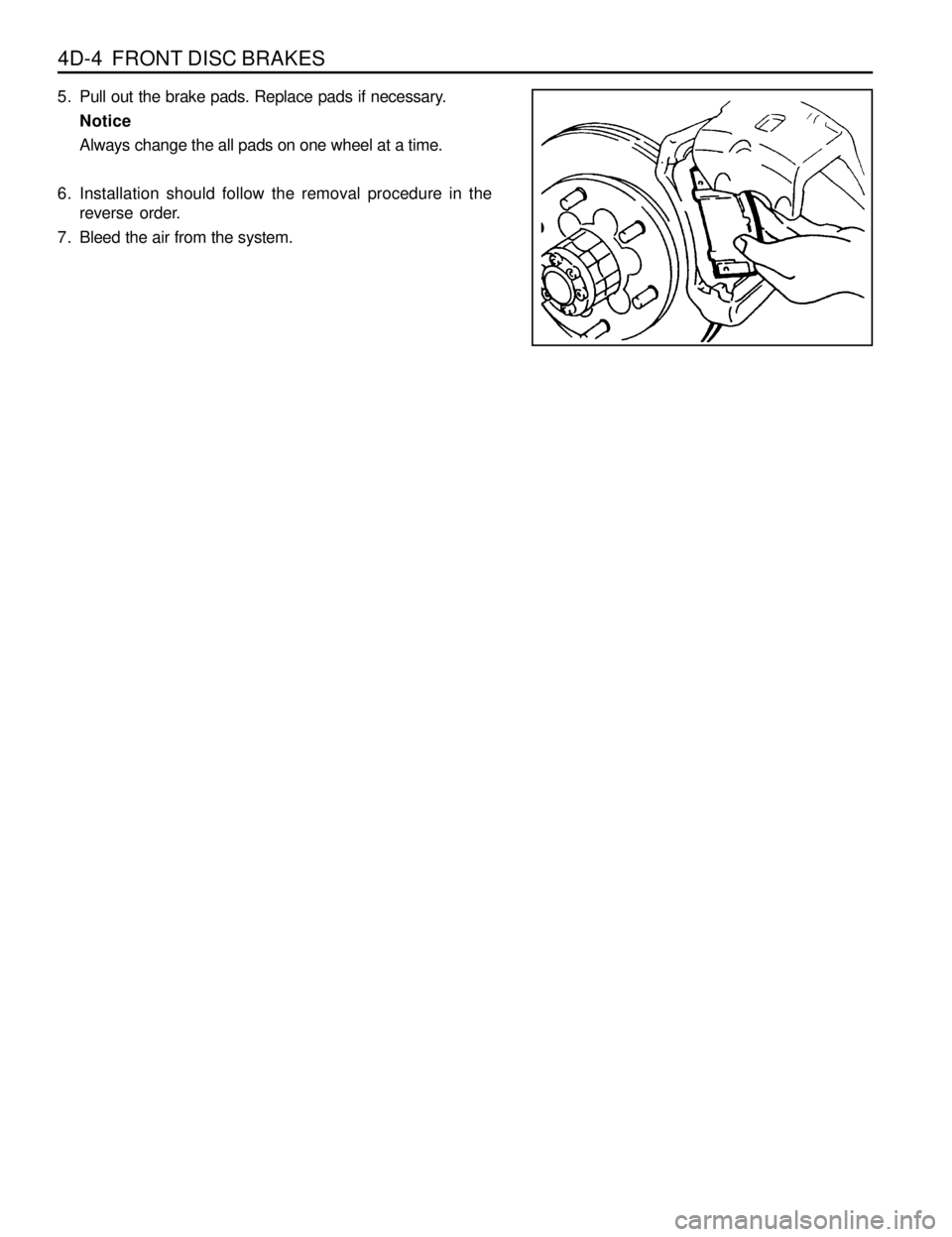
4D-4 FRONT DISC BRAKES
5. Pull out the brake pads. Replace pads if necessary.
Notice
Always change the all pads on one wheel at a time.
6. Installation should follow the removal procedure in the
reverse order.
7. Bleed the air from the system.
Page 943 of 1463
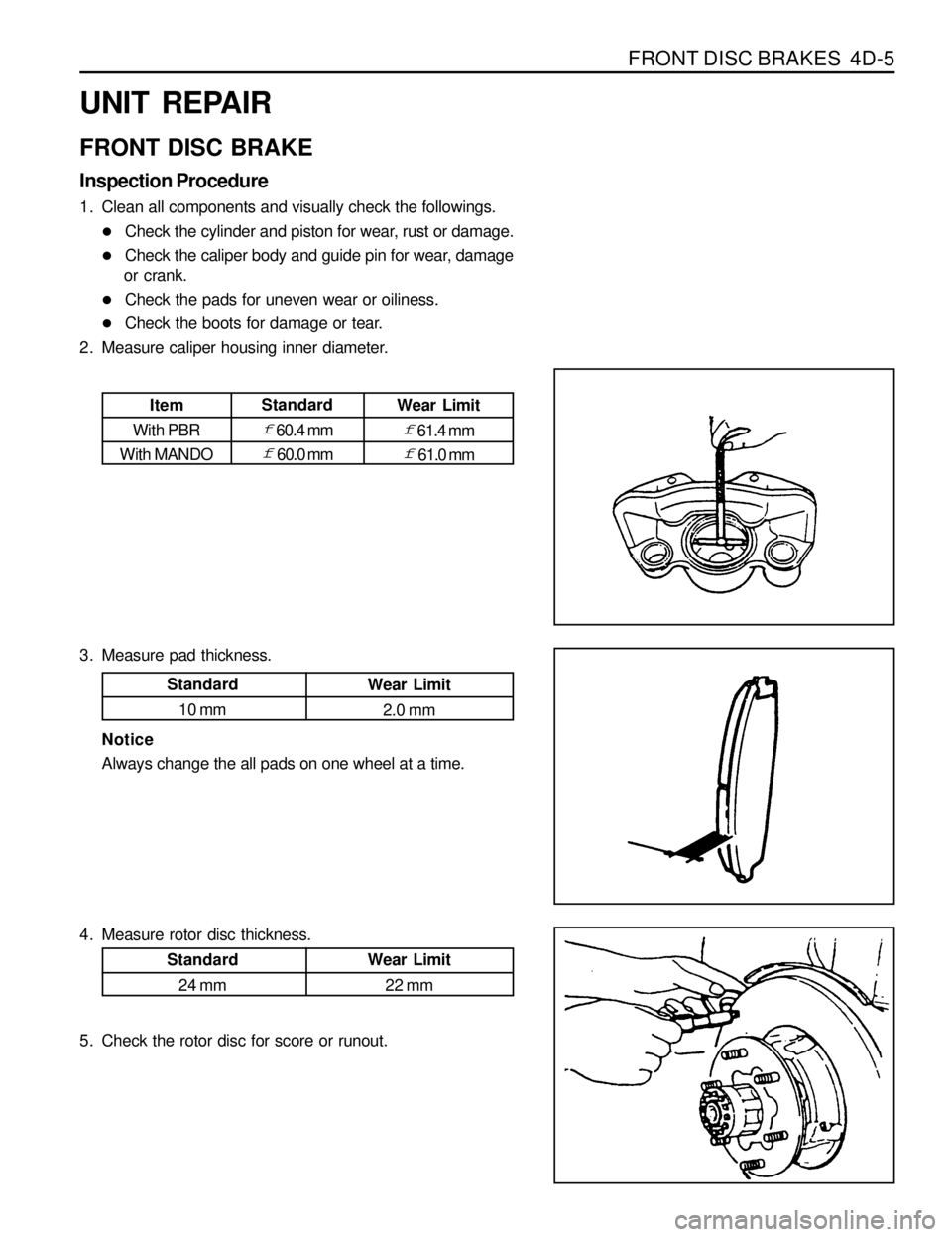
FRONT DISC BRAKES 4D-5
4. Measure rotor disc thickness.
UNIT REPAIR
FRONT DISC BRAKE
Inspection Procedure
1. Clean all components and visually check the followings.
lCheck the cylinder and piston for wear, rust or damage.
lCheck the caliper body and guide pin for wear, damage
or crank.
lCheck the pads for uneven wear or oiliness.
lCheck the boots for damage or tear.
2. Measure caliper housing inner diameter.
Item
With PBR
With MANDOWear Limit
f 61.4 mm
f 61.0 mm
Standard
10 mmWear Limit
2.0 mm
Standard
f 60.4 mm
f 60.0 mm
3. Measure pad thickness.
Notice
Always change the all pads on one wheel at a time.
5. Check the rotor disc for score or runout.
Standard
24 mmWear Limit
22 mm
Page 946 of 1463
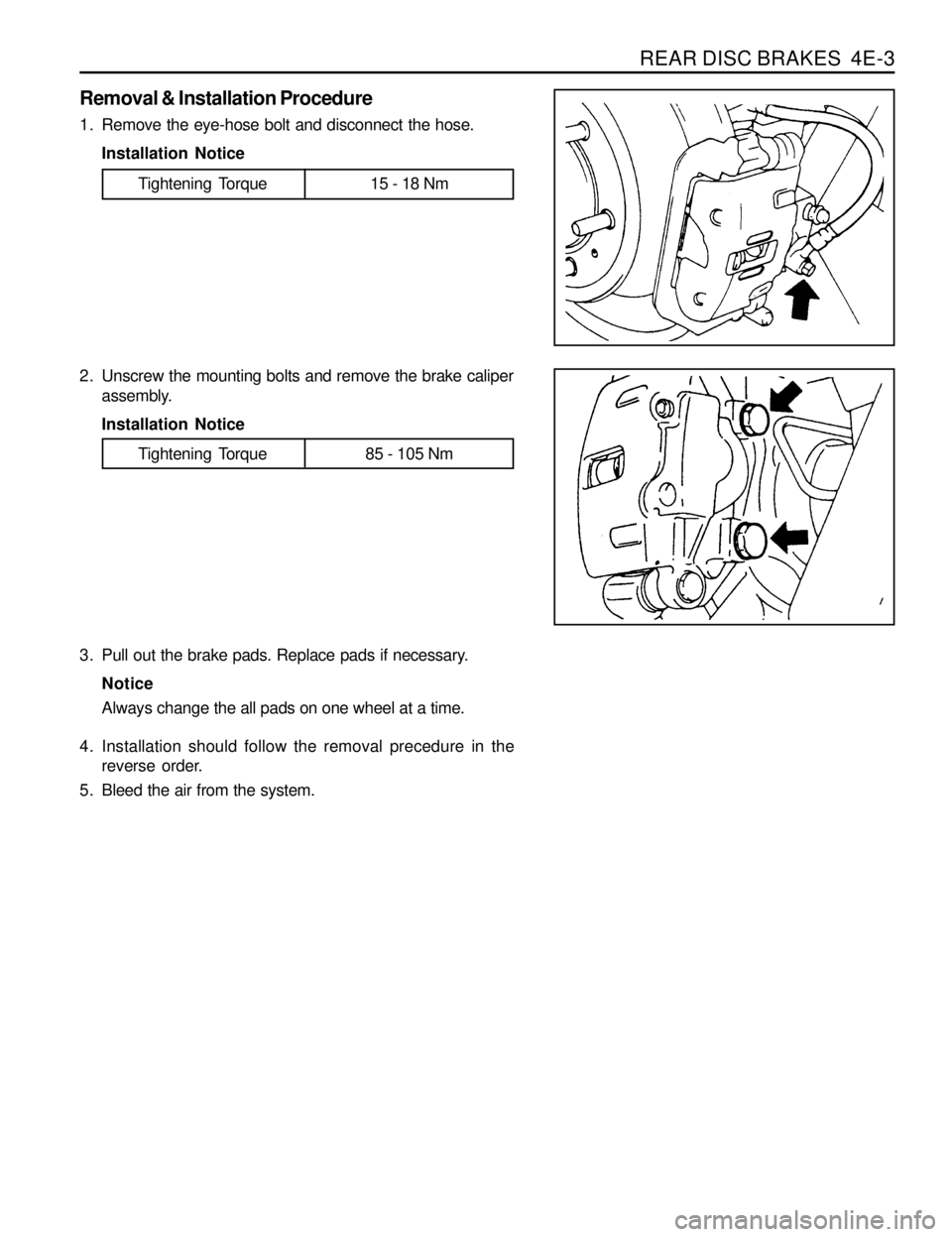
REAR DISC BRAKES 4E-3
Tightening Torque 15 - 18 Nm
Tightening Torque 85 - 105 Nm
Removal & Installation Procedure
1. Remove the eye-hose bolt and disconnect the hose.
Installation Notice
2. Unscrew the mounting bolts and remove the brake caliper
assembly.
Installation Notice
3. Pull out the brake pads. Replace pads if necessary.
Notice
Always change the all pads on one wheel at a time.
4. Installation should follow the removal precedure in the
reverse order.
5. Bleed the air from the system.
Page 947 of 1463
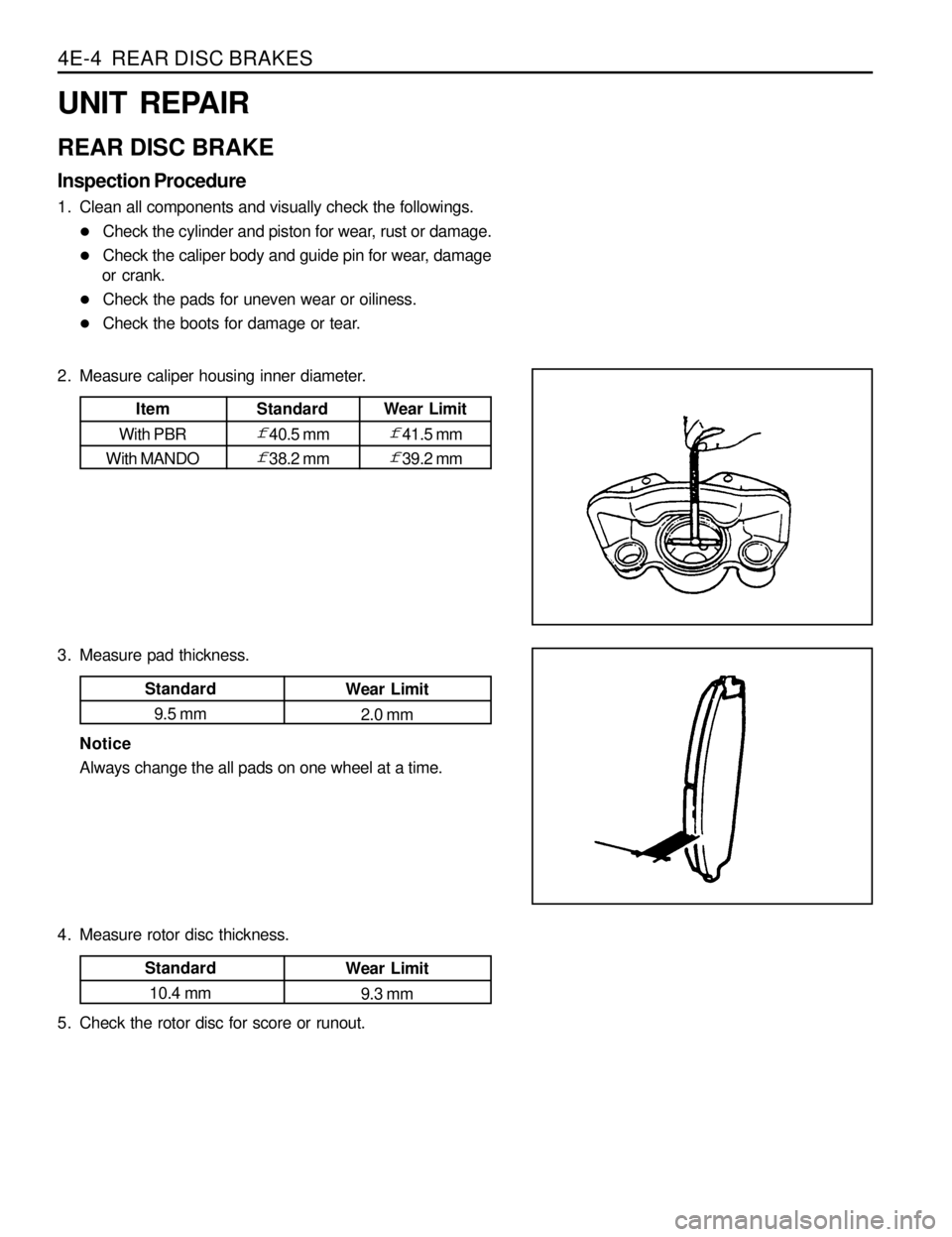
4E-4 REAR DISC BRAKES
Standard
10.4 mmWear Limit
9.3 mm
UNIT REPAIR
REAR DISC BRAKE
Inspection Procedure
1. Clean all components and visually check the followings.
lCheck the cylinder and piston for wear, rust or damage.
lCheck the caliper body and guide pin for wear, damage
or crank.
lCheck the pads for uneven wear or oiliness.
lCheck the boots for damage or tear.
Standard
f40.5 mm
f38.2 mmWear Limit
f41.5 mm
f39.2 mm
2. Measure caliper housing inner diameter.
3. Measure pad thickness.
Standard
9.5 mmWear Limit
2.0 mm
Notice
Always change the all pads on one wheel at a time.
4. Measure rotor disc thickness.
5. Check the rotor disc for score or runout.
Item
With PBR
With MANDO
Page 998 of 1463
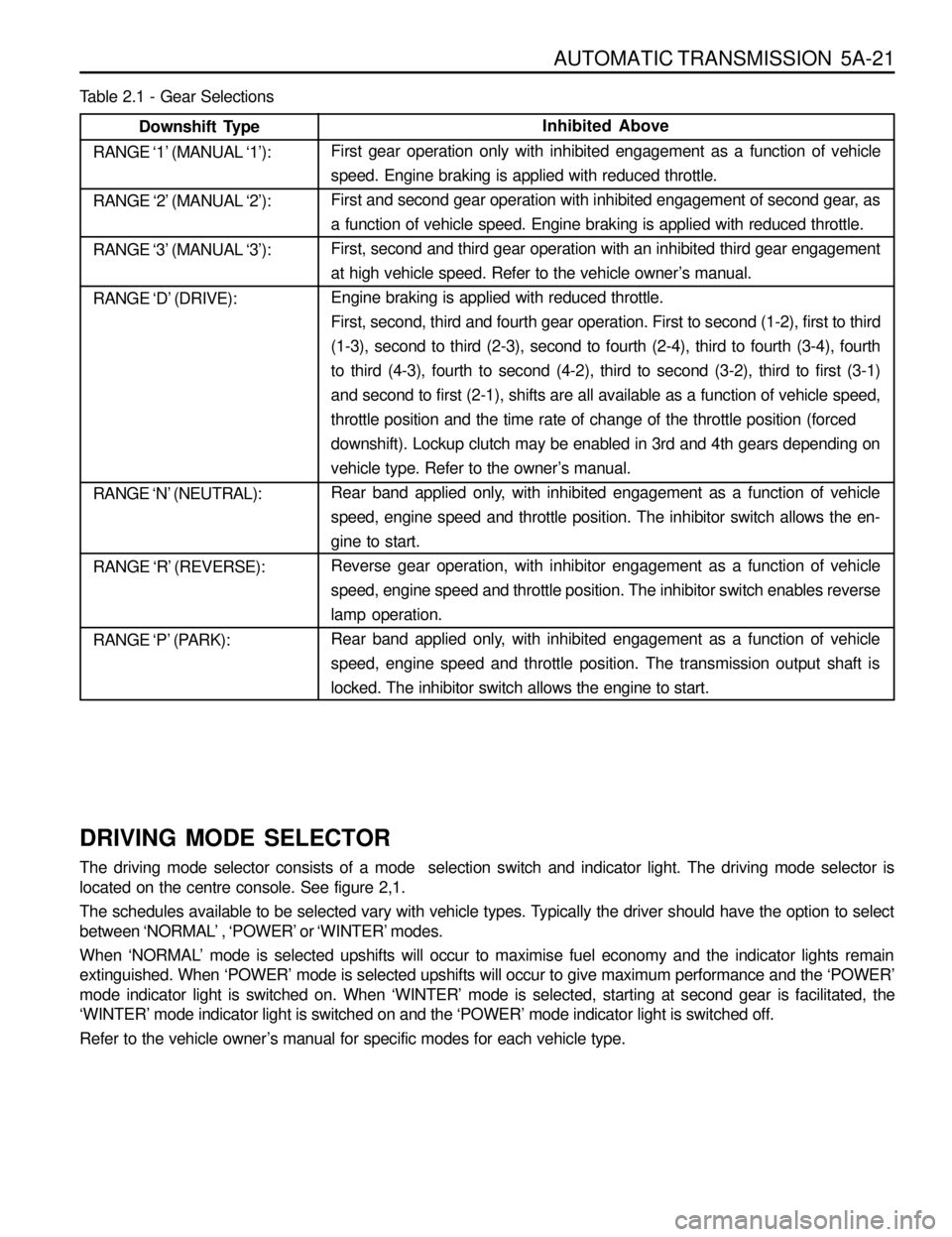
AUTOMATIC TRANSMISSION 5A-21
Downshift Type
RANGE ‘1’ (MANUAL ‘1’):
RANGE ‘2’ (MANUAL ‘2’):
RANGE ‘3’ (MANUAL ‘3’):
RANGE ‘D’ (DRIVE):
RANGE ‘N’ (NEUTRAL):
RANGE ‘R’ (REVERSE):
RANGE ‘P’ (PARK):Inhibited Above
First gear operation only with inhibited engagement as a function of vehicle
speed. Engine braking is applied with reduced throttle.
First and second gear operation with inhibited engagement of second gear, as
a function of vehicle speed. Engine braking is applied with reduced throttle.
First, second and third gear operation with an inhibited third gear engagement
at high vehicle speed. Refer to the vehicle owner’s manual.
Engine braking is applied with reduced throttle.
First, second, third and fourth gear operation. First to second (1-2), first to third
(1-3), second to third (2-3), second to fourth (2-4), third to fourth (3-4), fourth
to third (4-3), fourth to second (4-2), third to second (3-2), third to first (3-1)
and second to first (2-1), shifts are all available as a function of vehicle speed,
throttle position and the time rate of change of the throttle position (forced
downshift). Lockup clutch may be enabled in 3rd and 4th gears depending on
vehicle type. Refer to the owner’s manual.
Rear band applied only, with inhibited engagement as a function of vehicle
speed, engine speed and throttle position. The inhibitor switch allows the en-
gine to start.
Reverse gear operation, with inhibitor engagement as a function of vehicle
speed, engine speed and throttle position. The inhibitor switch enables reverse
lamp operation.
Rear band applied only, with inhibited engagement as a function of vehicle
speed, engine speed and throttle position. The transmission output shaft is
locked. The inhibitor switch allows the engine to start.
Table 2.1 - Gear Selections
DRIVING MODE SELECTOR
The driving mode selector consists of a mode selection switch and indicator light. The driving mode selector is
located on the centre console. See figure 2,1.
The schedules available to be selected vary with vehicle types. Typically the driver should have the option to select
between ‘NORMAL’ , ‘POWER’ or ‘WINTER’ modes.
When ‘NORMAL’ mode is selected upshifts will occur to maximise fuel economy and the indicator lights remain
extinguished. When ‘POWER’ mode is selected upshifts will occur to give maximum performance and the ‘POWER’
mode indicator light is switched on. When ‘WINTER’ mode is selected, starting at second gear is facilitated, the
‘WINTER’ mode indicator light is switched on and the ‘POWER’ mode indicator light is switched off.
Refer to the vehicle owner’s manual for specific modes for each vehicle type.
Page 1001 of 1463
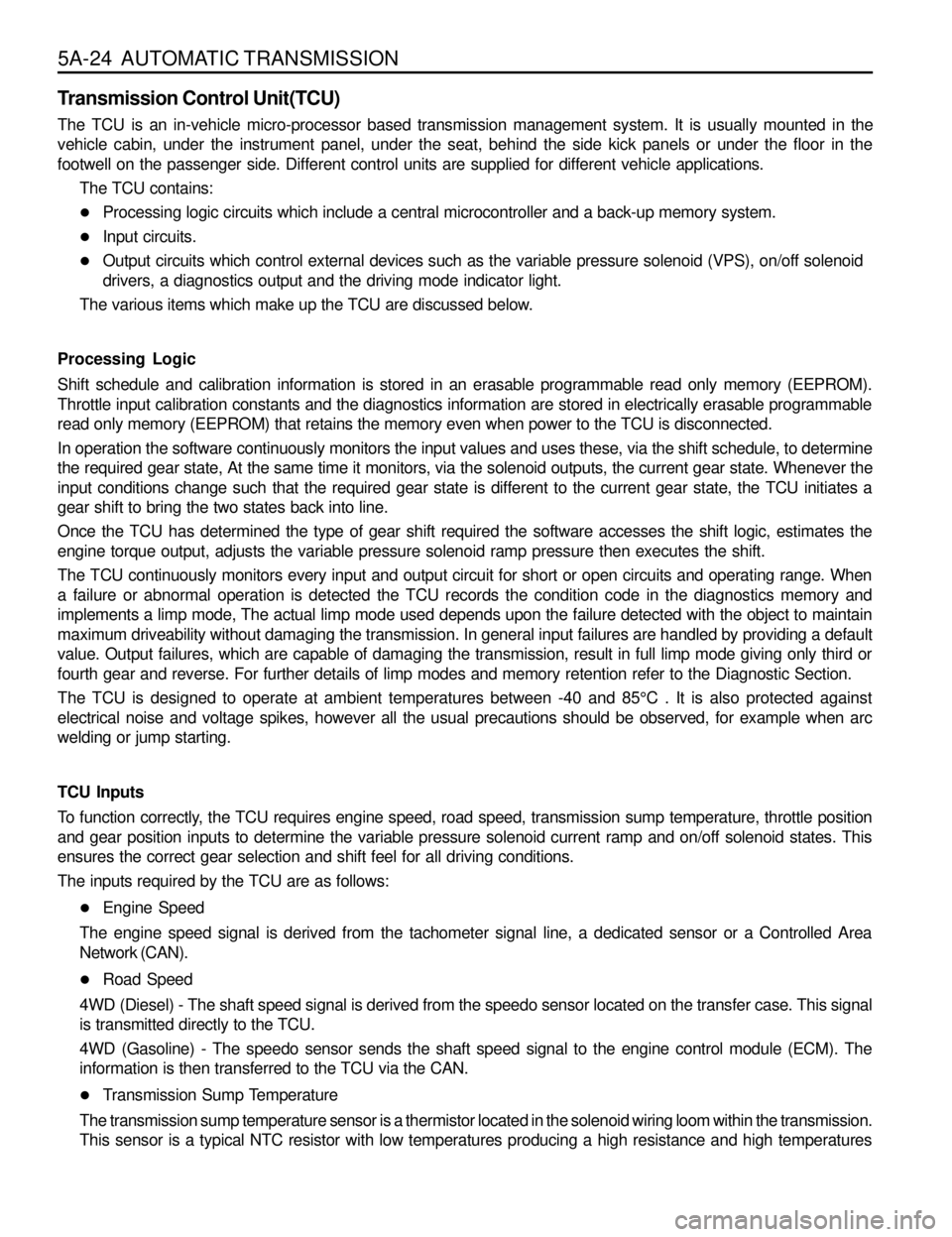
5A-24 AUTOMATIC TRANSMISSION
Transmission Control Unit(TCU)
The TCU is an in-vehicle micro-processor based transmission management system. It is usually mounted in the
vehicle cabin, under the instrument panel, under the seat, behind the side kick panels or under the floor in the
footwell on the passenger side. Different control units are supplied for different vehicle applications.
The TCU contains:
lProcessing logic circuits which include a central microcontroller and a back-up memory system.
lInput circuits.
lOutput circuits which control external devices such as the variable pressure solenoid (VPS), on/off solenoid
drivers, a diagnostics output and the driving mode indicator light.
The various items which make up the TCU are discussed below.
Processing Logic
Shift schedule and calibration information is stored in an erasable programmable read only memory (EEPROM).
Throttle input calibration constants and the diagnostics information are stored in electrically erasable programmable
read only memory (EEPROM) that retains the memory even when power to the TCU is disconnected.
In operation the software continuously monitors the input values and uses these, via the shift schedule, to determine
the required gear state, At the same time it monitors, via the solenoid outputs, the current gear state. Whenever the
input conditions change such that the required gear state is different to the current gear state, the TCU initiates a
gear shift to bring the two states back into line.
Once the TCU has determined the type of gear shift required the software accesses the shift logic, estimates the
engine torque output, adjusts the variable pressure solenoid ramp pressure then executes the shift.
The TCU continuously monitors every input and output circuit for short or open circuits and operating range. When
a failure or abnormal operation is detected the TCU records the condition code in the diagnostics memory and
implements a limp mode, The actual limp mode used depends upon the failure detected with the object to maintain
maximum driveability without damaging the transmission. In general input failures are handled by providing a default
value. Output failures, which are capable of damaging the transmission, result in full limp mode giving only third or
fourth gear and reverse. For further details of limp modes and memory retention refer to the Diagnostic Section.
The TCU is designed to operate at ambient temperatures between -40 and 85°C . It is also protected against
electrical noise and voltage spikes, however all the usual precautions should be observed, for example when arc
welding or jump starting.
TCU Inputs
To function correctly, the TCU requires engine speed, road speed, transmission sump temperature, throttle position
and gear position inputs to determine the variable pressure solenoid current ramp and on/off solenoid states. This
ensures the correct gear selection and shift feel for all driving conditions.
The inputs required by the TCU are as follows:
lEngine Speed
The engine speed signal is derived from the tachometer signal line, a dedicated sensor or a Controlled Area
Network (CAN).
lRoad Speed
4WD (Diesel) - The shaft speed signal is derived from the speedo sensor located on the transfer case. This signal
is transmitted directly to the TCU.
4WD (Gasoline) - The speedo sensor sends the shaft speed signal to the engine control module (ECM). The
information is then transferred to the TCU via the CAN.
lTransmission Sump Temperature
The transmission sump temperature sensor is a thermistor located in the solenoid wiring loom within the transmission.
This sensor is a typical NTC resistor with low temperatures producing a high resistance and high temperatures
Page 1014 of 1463
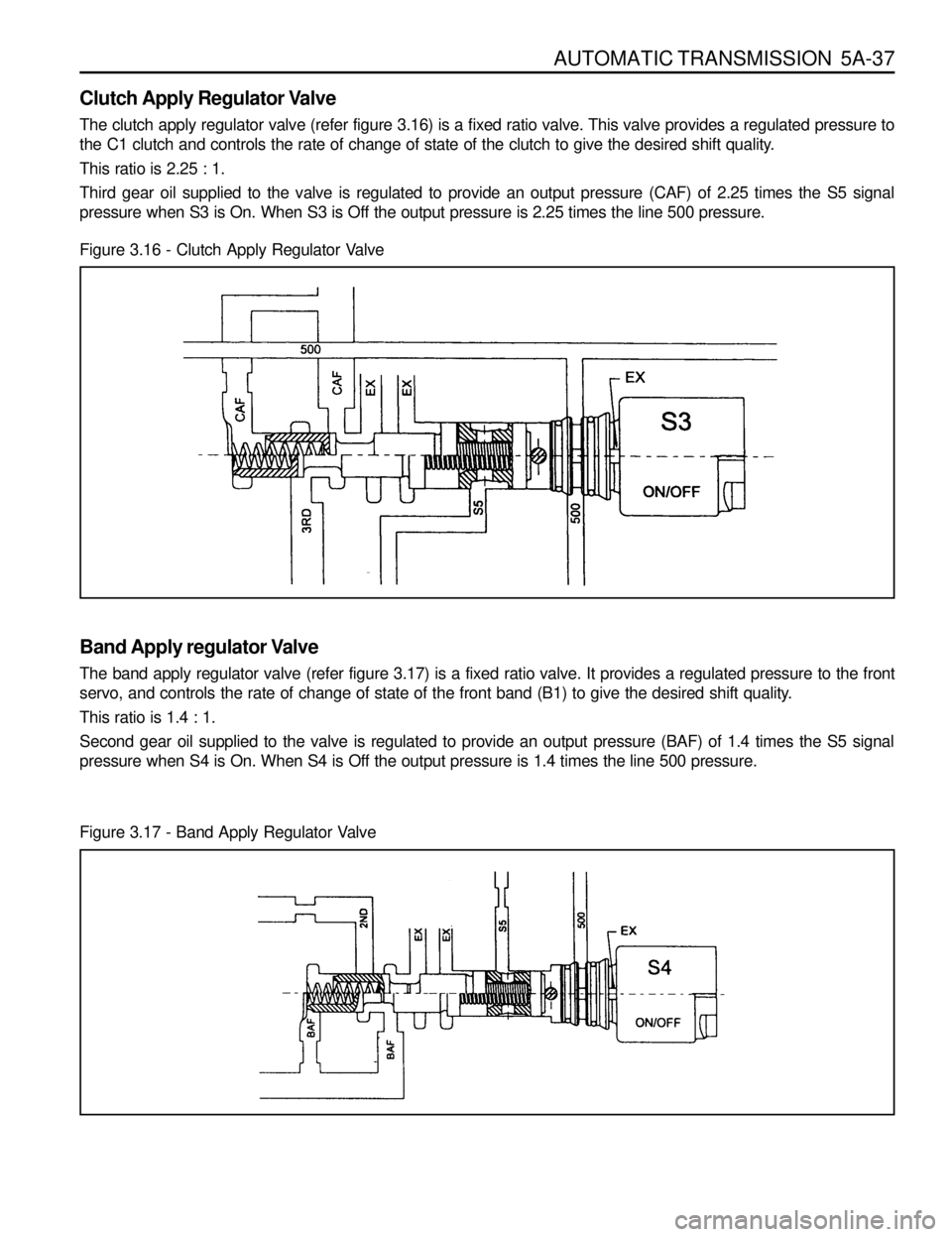
AUTOMATIC TRANSMISSION 5A-37
Figure 3.16 - Clutch Apply Regulator Valve
Clutch Apply Regulator Valve
The clutch apply regulator valve (refer figure 3.16) is a fixed ratio valve. This valve provides a regulated pressure to
the C1 clutch and controls the rate of change of state of the clutch to give the desired shift quality.
This ratio is 2.25 : 1.
Third gear oil supplied to the valve is regulated to provide an output pressure (CAF) of 2.25 times the S5 signal
pressure when S3 is On. When S3 is Off the output pressure is 2.25 times the line 500 pressure.
Band Apply regulator Valve
The band apply regulator valve (refer figure 3.17) is a fixed ratio valve. It provides a regulated pressure to the front
servo, and controls the rate of change of state of the front band (B1) to give the desired shift quality.
This ratio is 1.4 : 1.
Second gear oil supplied to the valve is regulated to provide an output pressure (BAF) of 1.4 times the S5 signal
pressure when S4 is On. When S4 is Off the output pressure is 1.4 times the line 500 pressure.
Figure 3.17 - Band Apply Regulator Valve
Page 1042 of 1463
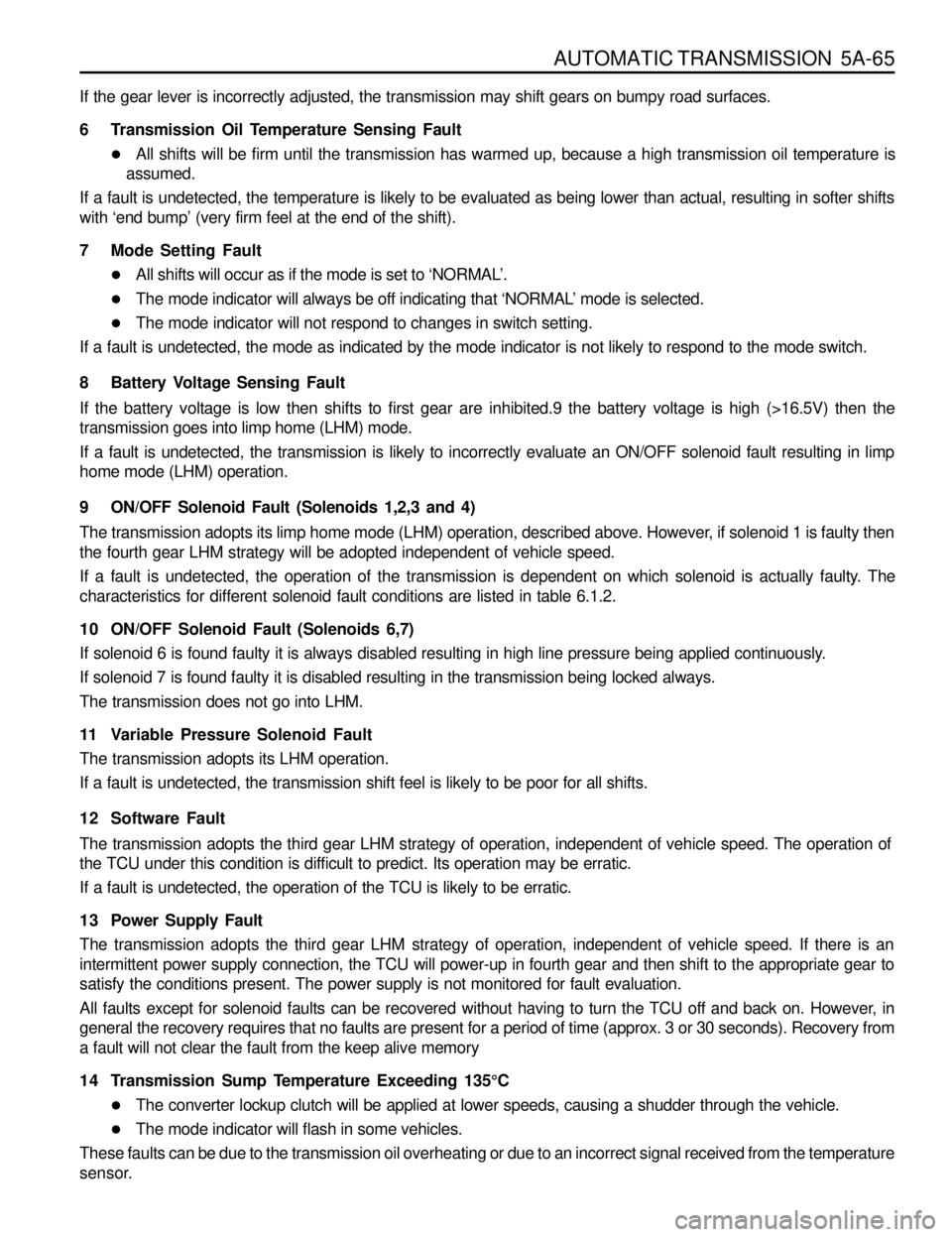
AUTOMATIC TRANSMISSION 5A-65
If the gear lever is incorrectly adjusted, the transmission may shift gears on bumpy road surfaces.
6 Transmission Oil Temperature Sensing Fault
lAll shifts will be firm until the transmission has warmed up, because a high transmission oil temperature is
assumed.
If a fault is undetected, the temperature is likely to be evaluated as being lower than actual, resulting in softer shifts
with ‘end bump’ (very firm feel at the end of the shift).
7 Mode Setting Fault
lAll shifts will occur as if the mode is set to ‘NORMAL’.
lThe mode indicator will always be off indicating that ‘NORMAL’ mode is selected.
lThe mode indicator will not respond to changes in switch setting.
If a fault is undetected, the mode as indicated by the mode indicator is not likely to respond to the mode switch.
8 Battery Voltage Sensing Fault
If the battery voltage is low then shifts to first gear are inhibited.9 the battery voltage is high (>16.5V) then the
transmission goes into limp home (LHM) mode.
If a fault is undetected, the transmission is likely to incorrectly evaluate an ON/OFF solenoid fault resulting in limp
home mode (LHM) operation.
9 ON/OFF Solenoid Fault (Solenoids 1,2,3 and 4)
The transmission adopts its limp home mode (LHM) operation, described above. However, if solenoid 1 is faulty then
the fourth gear LHM strategy will be adopted independent of vehicle speed.
If a fault is undetected, the operation of the transmission is dependent on which solenoid is actually faulty. The
characteristics for different solenoid fault conditions are listed in table 6.1.2.
10 ON/OFF Solenoid Fault (Solenoids 6,7)
If solenoid 6 is found faulty it is always disabled resulting in high line pressure being applied continuously.
If solenoid 7 is found faulty it is disabled resulting in the transmission being locked always.
The transmission does not go into LHM.
11 Variable Pressure Solenoid Fault
The transmission adopts its LHM operation.
If a fault is undetected, the transmission shift feel is likely to be poor for all shifts.
12 Software Fault
The transmission adopts the third gear LHM strategy of operation, independent of vehicle speed. The operation of
the TCU under this condition is difficult to predict. Its operation may be erratic.
If a fault is undetected, the operation of the TCU is likely to be erratic.
13 Power Supply Fault
The transmission adopts the third gear LHM strategy of operation, independent of vehicle speed. If there is an
intermittent power supply connection, the TCU will power-up in fourth gear and then shift to the appropriate gear to
satisfy the conditions present. The power supply is not monitored for fault evaluation.
All faults except for solenoid faults can be recovered without having to turn the TCU off and back on. However, in
general the recovery requires that no faults are present for a period of time (approx. 3 or 30 seconds). Recovery from
a fault will not clear the fault from the keep alive memory
14 Transmission Sump Temperature Exceeding 135°C
lThe converter lockup clutch will be applied at lower speeds, causing a shudder through the vehicle.
lThe mode indicator will flash in some vehicles.
These faults can be due to the transmission oil overheating or due to an incorrect signal received from the temperature
sensor.