turn signal SSANGYONG MUSSO 1998 Workshop Repair Manual
[x] Cancel search | Manufacturer: SSANGYONG, Model Year: 1998, Model line: MUSSO, Model: SSANGYONG MUSSO 1998Pages: 1463, PDF Size: 19.88 MB
Page 24 of 1463
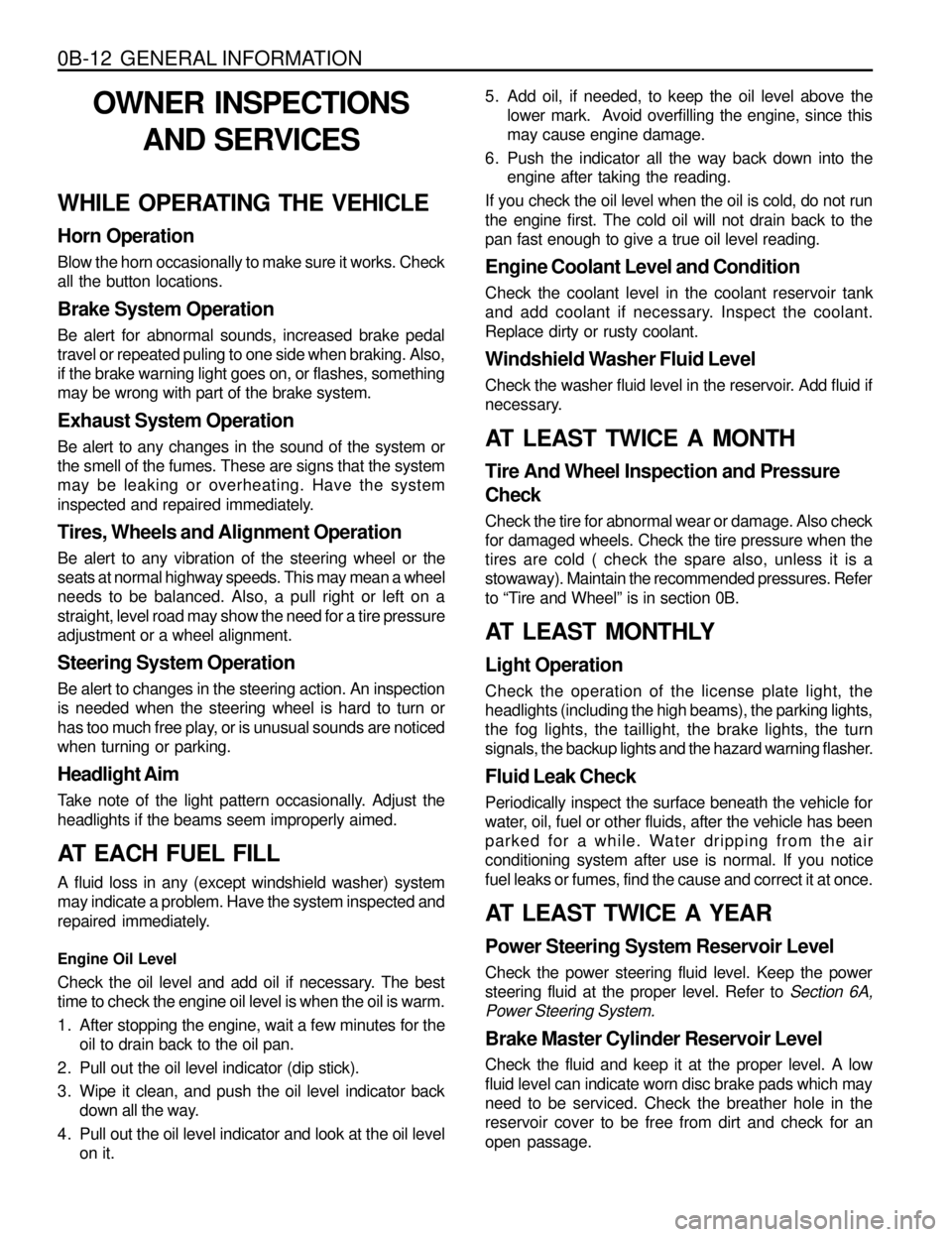
0B-12 GENERAL INFORMATION
OWNER INSPECTIONS
AND SERVICES
WHILE OPERATING THE VEHICLE
Horn Operation
Blow the horn occasionally to make sure it works. Check
all the button locations.
Brake System Operation
Be alert for abnormal sounds, increased brake pedal
travel or repeated puling to one side when braking. Also,
if the brake warning light goes on, or flashes, something
may be wrong with part of the brake system.
Exhaust System Operation
Be alert to any changes in the sound of the system or
the smell of the fumes. These are signs that the system
may be leaking or overheating. Have the system
inspected and repaired immediately.
Tires, Wheels and Alignment Operation
Be alert to any vibration of the steering wheel or the
seats at normal highway speeds. This may mean a wheel
needs to be balanced. Also, a pull right or left on a
straight, level road may show the need for a tire pressure
adjustment or a wheel alignment.
Steering System Operation
Be alert to changes in the steering action. An inspection
is needed when the steering wheel is hard to turn or
has too much free play, or is unusual sounds are noticed
when turning or parking.
Headlight Aim
Take note of the light pattern occasionally. Adjust the
headlights if the beams seem improperly aimed.
AT EACH FUEL FILL
A fluid loss in any (except windshield washer) system
may indicate a problem. Have the system inspected and
repaired immediately.
Engine Oil Level
Check the oil level and add oil if necessary. The best
time to check the engine oil level is when the oil is warm.
1. After stopping the engine, wait a few minutes for the
oil to drain back to the oil pan.
2. Pull out the oil level indicator (dip stick).
3. Wipe it clean, and push the oil level indicator back
down all the way.
4. Pull out the oil level indicator and look at the oil level
on it.5. Add oil, if needed, to keep the oil level above the
lower mark. Avoid overfilling the engine, since this
may cause engine damage.
6. Push the indicator all the way back down into the
engine after taking the reading.
If you check the oil level when the oil is cold, do not run
the engine first. The cold oil will not drain back to the
pan fast enough to give a true oil level reading.
Engine Coolant Level and Condition
Check the coolant level in the coolant reservoir tank
and add coolant if necessary. Inspect the coolant.
Replace dirty or rusty coolant.
Windshield Washer Fluid Level
Check the washer fluid level in the reservoir. Add fluid if
necessary.
AT LEAST TWICE A MONTH
Tire And Wheel Inspection and Pressure
Check
Check the tire for abnormal wear or damage. Also check
for damaged wheels. Check the tire pressure when the
tires are cold ( check the spare also, unless it is a
stowaway). Maintain the recommended pressures. Refer
to “Tire and Wheel” is in section 0B.
AT LEAST MONTHLY
Light Operation
Check the operation of the license plate light, the
headlights (including the high beams), the parking lights,
the fog lights, the taillight, the brake lights, the turn
signals, the backup lights and the hazard warning flasher.
Fluid Leak Check
Periodically inspect the surface beneath the vehicle for
water, oil, fuel or other fluids, after the vehicle has been
parked for a while. Water dripping from the air
conditioning system after use is normal. If you notice
fuel leaks or fumes, find the cause and correct it at once.
AT LEAST TWICE A YEAR
Power Steering System Reservoir Level
Check the power steering fluid level. Keep the power
steering fluid at the proper level. Refer to
Section 6A,
Power Steering System.
Brake Master Cylinder Reservoir Level
Check the fluid and keep it at the proper level. A low
fluid level can indicate worn disc brake pads which may
need to be serviced. Check the breather hole in the
reservoir cover to be free from dirt and check for an
open passage.
Page 578 of 1463
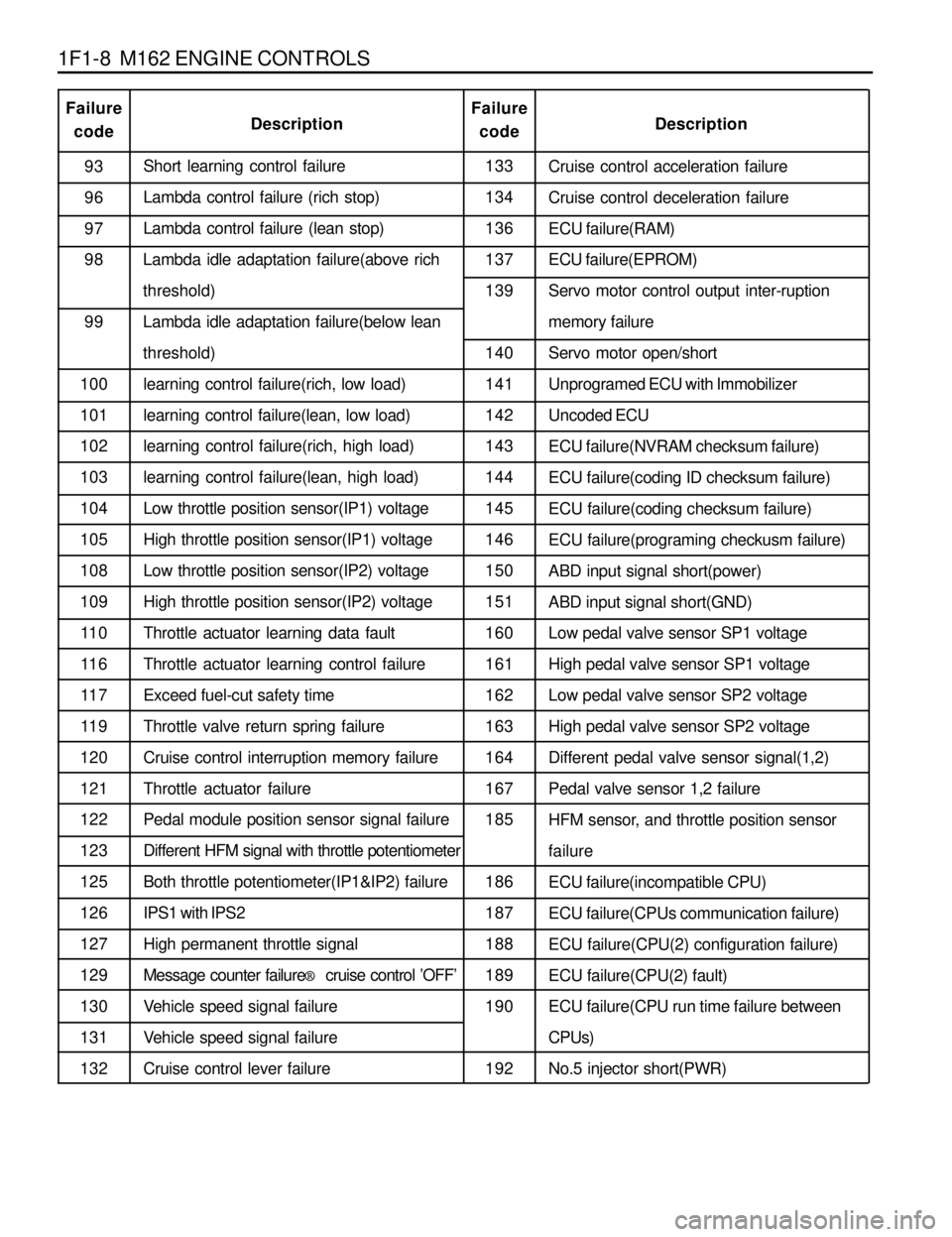
1F1-8 M162 ENGINE CONTROLS
Cruise control acceleration failure
Cruise control deceleration failure
ECU failure(RAM)
ECU failure(EPROM)
Servo motor control output inter-ruption
memory failure
Servo motor open/short
Unprogramed ECU with Immobilizer
Uncoded ECU
ECU failure(NVRAM checksum failure)
ECU failure(coding ID checksum failure)
ECU failure(coding checksum failure)
ECU failure(programing checkusm failure)
ABD input signal short(power)
ABD input signal short(GND)
Low pedal valve sensor SP1 voltage
High pedal valve sensor SP1 voltage
Low pedal valve sensor SP2 voltage
High pedal valve sensor SP2 voltage
Different pedal valve sensor signal(1,2)
Pedal valve sensor 1,2 failure
HFM sensor, and throttle position sensor
failure
ECU failure(incompatible CPU)
ECU failure(CPUs communication failure)
ECU failure(CPU(2) configuration failure)
ECU failure(CPU(2) fault)
ECU failure(CPU run time failure between
CPUs)
No.5 injector short(PWR) 93
96
97
98
99
100
101
102
103
104
105
108
109
11 0
11 6
11 7
11 9
120
121
122
123
125
126
127
129
130
131
132Short learning control failure
Lambda control failure (rich stop)
Lambda control failure (lean stop)
Lambda idle adaptation failure(above rich
threshold)
Lambda idle adaptation failure(below lean
threshold)
learning control failure(rich, low load)
learning control failure(lean, low load)
learning control failure(rich, high load)
learning control failure(lean, high load)
Low throttle position sensor(IP1) voltage
High throttle position sensor(IP1) voltage
Low throttle position sensor(IP2) voltage
High throttle position sensor(IP2) voltage
Throttle actuator learning data fault
Throttle actuator learning control failure
Exceed fuel-cut safety time
Throttle valve return spring failure
Cruise control interruption memory failure
Throttle actuator failure
Pedal module position sensor signal failure
Different HFM signal with throttle potentiometer
Both throttle potentiometer(IP1&IP2) failure
IPS1 with IPS2
High permanent throttle signal
Message counter failure® cruise control ’OFF’
Vehicle speed signal failure
Vehicle speed signal failure
Cruise control lever failure133
134
136
137
139
140
141
142
143
144
145
146
150
151
160
161
162
163
164
167
185
186
187
188
189
190
192
Failure
codeDescriptionFailure
codeDescription
Page 638 of 1463
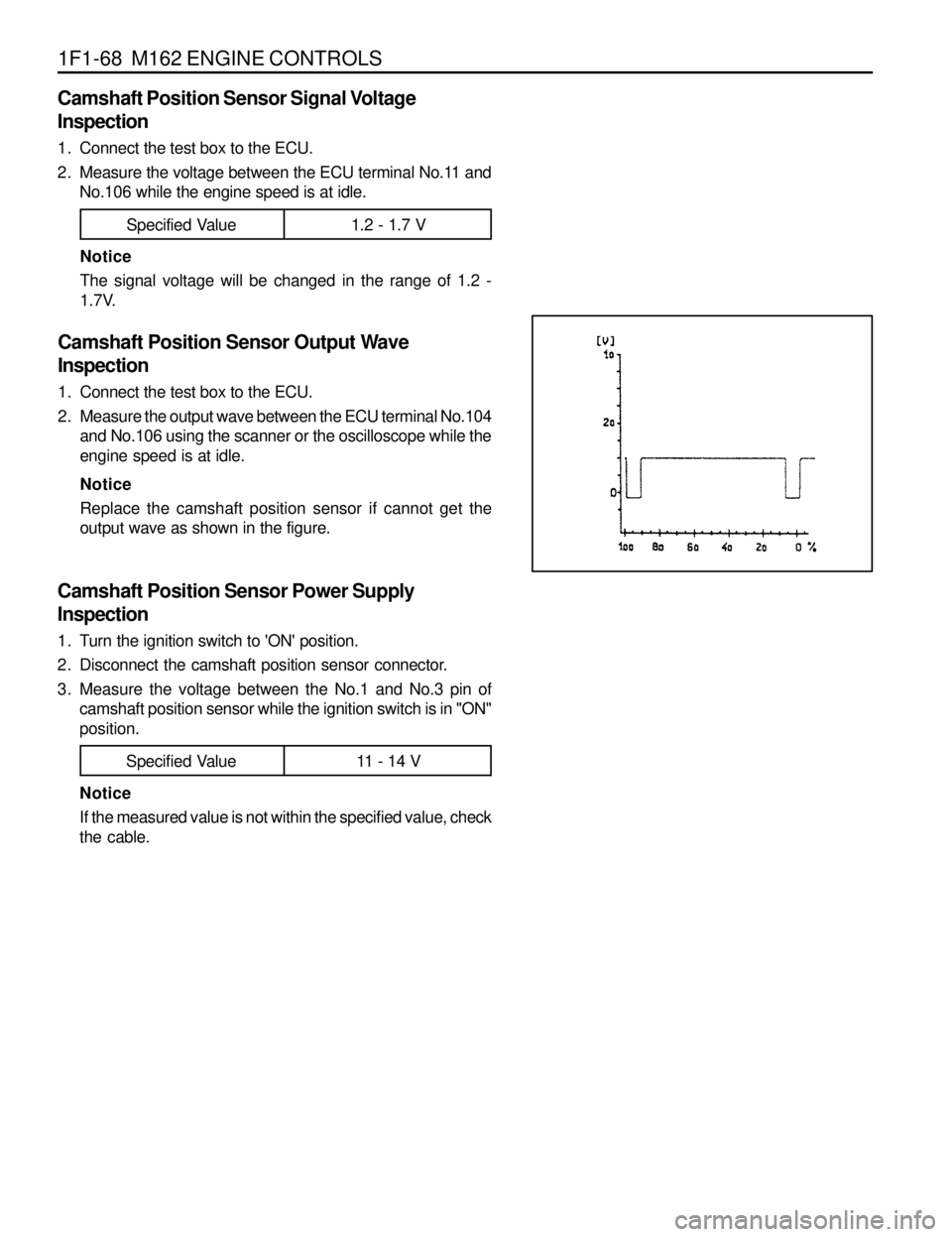
1F1-68 M162 ENGINE CONTROLS
Camshaft Position Sensor Power Supply
Inspection
1. Turn the ignition switch to 'ON' position.
2. Disconnect the camshaft position sensor connector.
3. Measure the voltage between the No.1 and No.3 pin of
camshaft position sensor while the ignition switch is in "ON"
position.
Notice
If the measured value is not within the specified value, check
the cable.Notice
The signal voltage will be changed in the range of 1.2 -
1.7V.
Camshaft Position Sensor Output Wave
Inspection
1. Connect the test box to the ECU.
2. Measure the output wave between the ECU terminal No.104
and No.106 using the scanner or the oscilloscope while the
engine speed is at idle.
Notice
Replace the camshaft position sensor if cannot get the
output wave as shown in the figure.
Specified Value 11 - 14 V
Specified Value 1.2 - 1.7 V
Camshaft Position Sensor Signal Voltage
Inspection
1. Connect the test box to the ECU.
2. Measure the voltage between the ECU terminal No.11 and
No.106 while the engine speed is at idle.
Page 657 of 1463
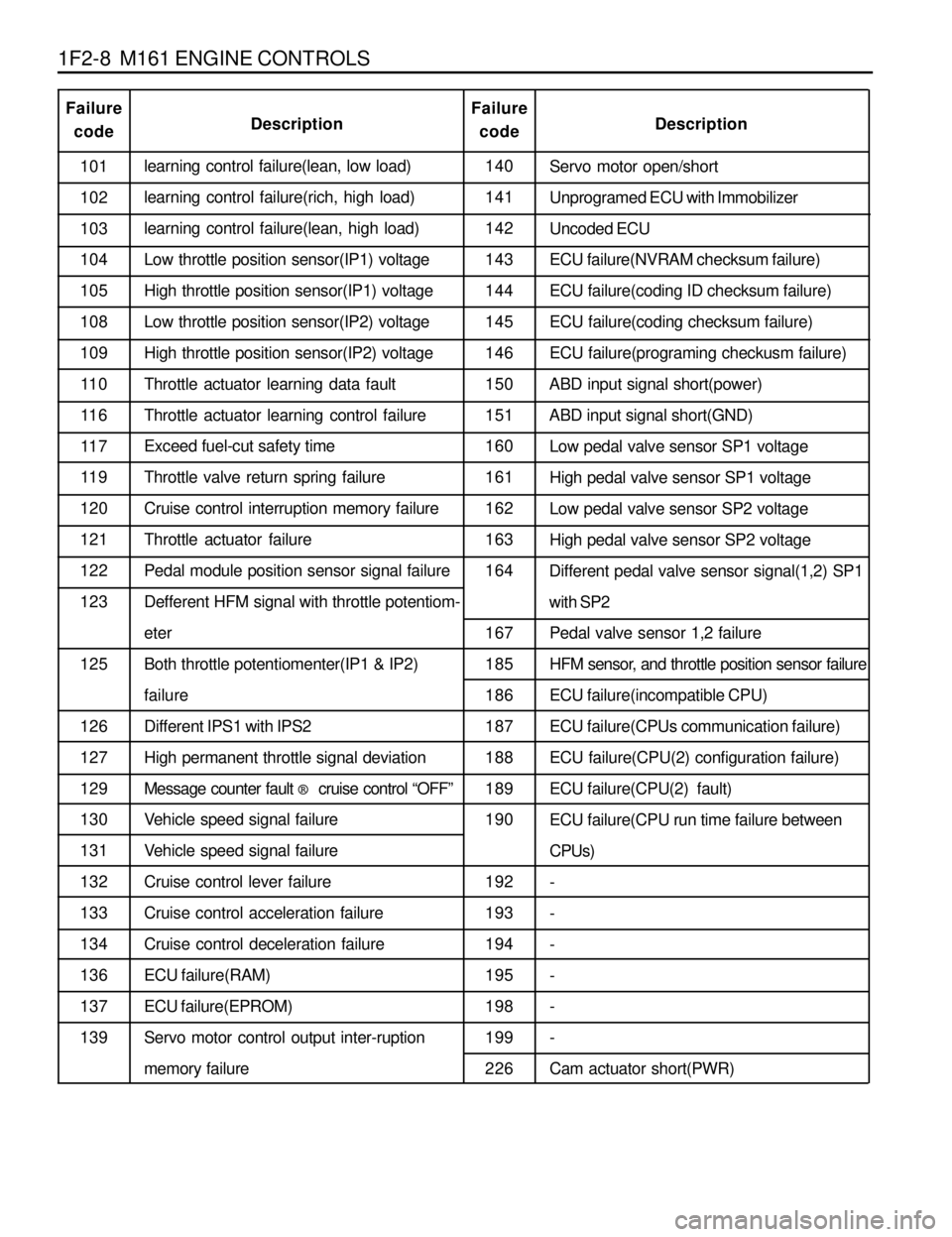
1F2-8 M161 ENGINE CONTROLS
Servo motor open/short
Unprogramed ECU with Immobilizer
Uncoded ECU
ECU failure(NVRAM checksum failure)
ECU failure(coding ID checksum failure)
ECU failure(coding checksum failure)
ECU failure(programing checkusm failure)
ABD input signal short(power)
ABD input signal short(GND)
Low pedal valve sensor SP1 voltage
High pedal valve sensor SP1 voltage
Low pedal valve sensor SP2 voltage
High pedal valve sensor SP2 voltage
Different pedal valve sensor signal(1,2) SP1
with SP2
Pedal valve sensor 1,2 failure
HFM sensor, and throttle position sensor failure
ECU failure(incompatible CPU)
ECU failure(CPUs communication failure)
ECU failure(CPU(2) configuration failure)
ECU failure(CPU(2) fault)
ECU failure(CPU run time failure between
CPUs)
-
-
-
-
-
-
Cam actuator short(PWR) 101
102
103
104
105
108
109
11 0
11 6
11 7
11 9
120
121
122
123
125
126
127
129
130
131
132
133
134
136
137
139140
141
142
143
144
145
146
150
151
160
161
162
163
164
167
185
186
187
188
189
190
192
193
194
195
198
199
226 learning control failure(lean, low load)
learning control failure(rich, high load)
learning control failure(lean, high load)
Low throttle position sensor(IP1) voltage
High throttle position sensor(IP1) voltage
Low throttle position sensor(IP2) voltage
High throttle position sensor(IP2) voltage
Throttle actuator learning data fault
Throttle actuator learning control failure
Exceed fuel-cut safety time
Throttle valve return spring failure
Cruise control interruption memory failure
Throttle actuator failure
Pedal module position sensor signal failure
Defferent HFM signal with throttle potentiom-
eter
Both throttle potentiomenter(IP1 & IP2)
failure
Different IPS1 with IPS2
High permanent throttle signal deviation
Message counter fault ® cruise control “OFF”
Vehicle speed signal failure
Vehicle speed signal failure
Cruise control lever failure
Cruise control acceleration failure
Cruise control deceleration failure
ECU failure(RAM)
ECU failure(EPROM)
Servo motor control output inter-ruption
memory failure
Failure
codeDescriptionFailure
codeDescription
Page 718 of 1463
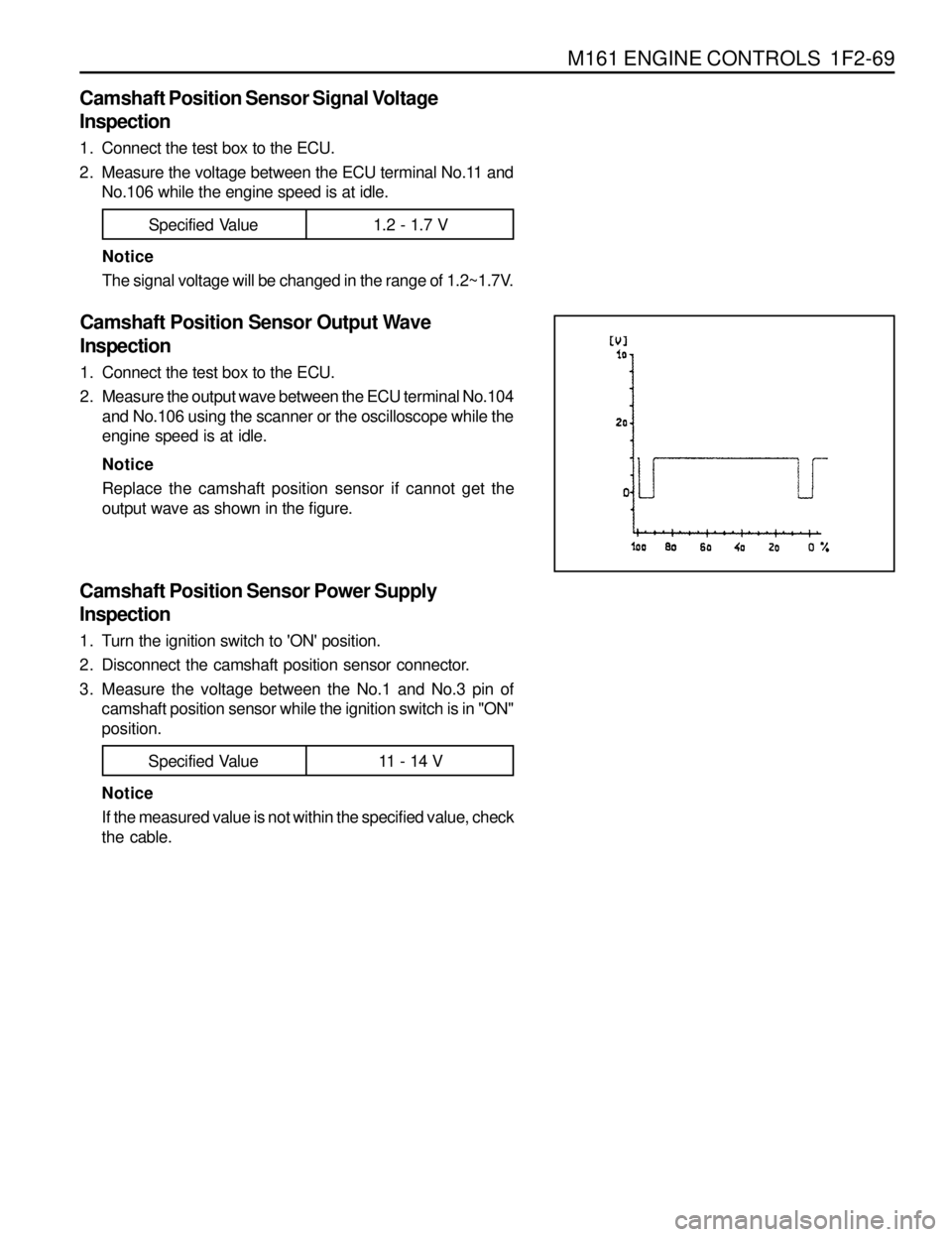
M161 ENGINE CONTROLS 1F2-69
Camshaft Position Sensor Power Supply
Inspection
1. Turn the ignition switch to 'ON' position.
2. Disconnect the camshaft position sensor connector.
3. Measure the voltage between the No.1 and No.3 pin of
camshaft position sensor while the ignition switch is in "ON"
position.
Notice
If the measured value is not within the specified value, check
the cable.Notice
The signal voltage will be changed in the range of 1.2~1.7V.
Camshaft Position Sensor Output Wave
Inspection
1. Connect the test box to the ECU.
2. Measure the output wave between the ECU terminal No.104
and No.106 using the scanner or the oscilloscope while the
engine speed is at idle.
Notice
Replace the camshaft position sensor if cannot get the
output wave as shown in the figure.
Specified Value 11 - 14 V
Specified Value 1.2 - 1.7 V
Camshaft Position Sensor Signal Voltage
Inspection
1. Connect the test box to the ECU.
2. Measure the voltage between the ECU terminal No.11 and
No.106 while the engine speed is at idle.
Page 964 of 1463
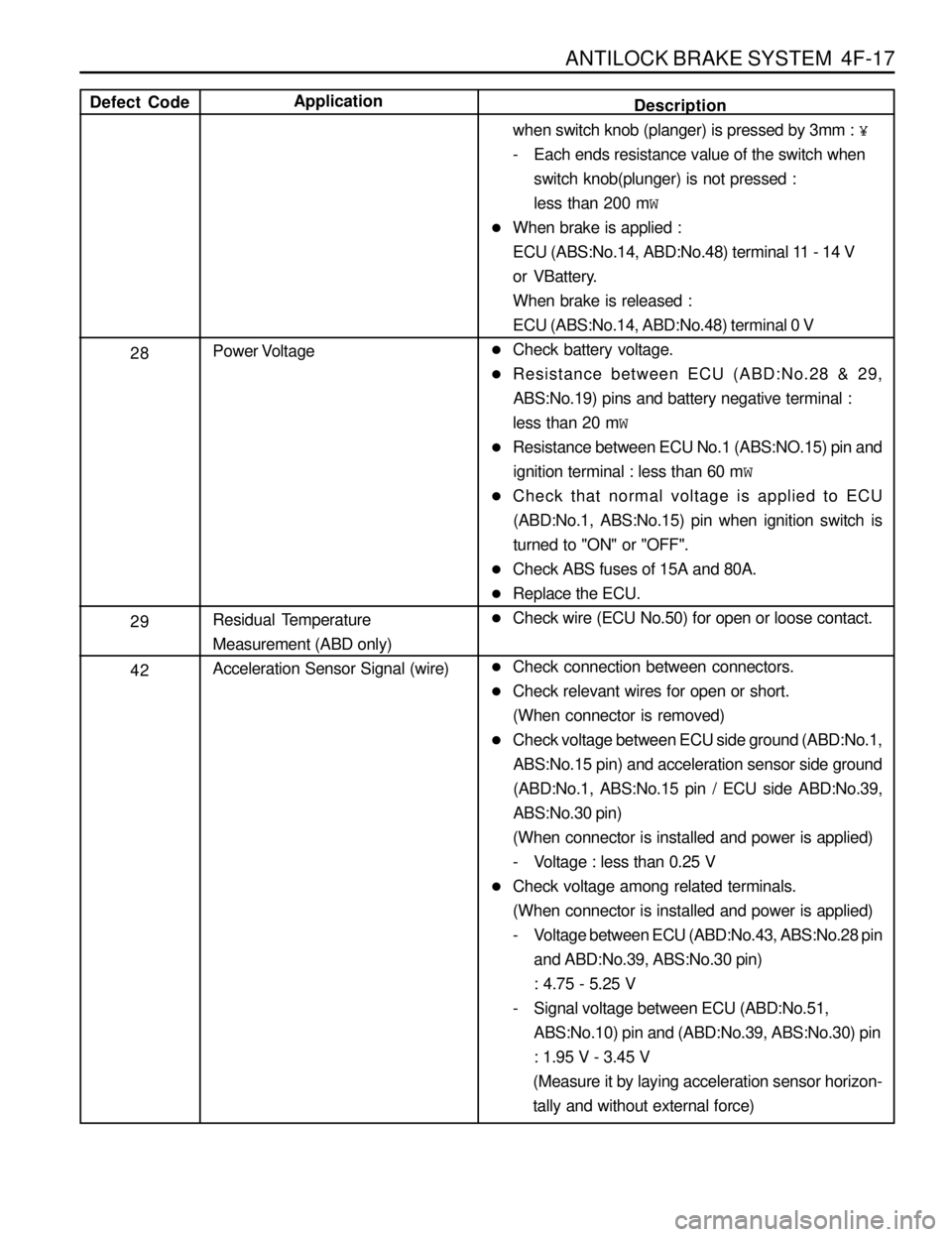
ANTILOCK BRAKE SYSTEM 4F-17
Application
Power Voltage
Residual Temperature
Measurement (ABD only)
Acceleration Sensor Signal (wire)Defect Code
28
29
42Description
when switch knob (planger) is pressed by 3mm : ¥
- Each ends resistance value of the switch when
switch knob(plunger) is not pressed :
less than 200 mW
lWhen brake is applied :
ECU (ABS:No.14, ABD:No.48) terminal 11 - 14 V
or VBattery.
When brake is released :
ECU (ABS:No.14, ABD:No.48) terminal 0 V
lCheck battery voltage.
lResistance between ECU (ABD:No.28 & 29,
ABS:No.19) pins and battery negative terminal :
less than 20 mW
lResistance between ECU No.1 (ABS:NO.15) pin and
ignition terminal : less than 60 mW
lCheck that normal voltage is applied to ECU
(ABD:No.1, ABS:No.15) pin when ignition switch is
turned to "ON" or "OFF".
lCheck ABS fuses of 15A and 80A.
lReplace the ECU.
lCheck wire (ECU No.50) for open or loose contact.
lCheck connection between connectors.
lCheck relevant wires for open or short.
(When connector is removed)
lCheck voltage between ECU side ground (ABD:No.1,
ABS:No.15 pin) and acceleration sensor side ground
(ABD:No.1, ABS:No.15 pin / ECU side ABD:No.39,
ABS:No.30 pin)
(When connector is installed and power is applied)
- Voltage : less than 0.25 V
lCheck voltage among related terminals.
(When connector is installed and power is applied)
- Voltage between ECU (ABD:No.43, ABS:No.28 pin
and ABD:No.39, ABS:No.30 pin)
: 4.75 - 5.25 V
- Signal voltage between ECU (ABD:No.51,
ABS:No.10) pin and (ABD:No.39, ABS:No.30) pin
: 1.95 V - 3.45 V
(Measure it by laying acceleration sensor horizon-
tally and without external force)
Page 1007 of 1463
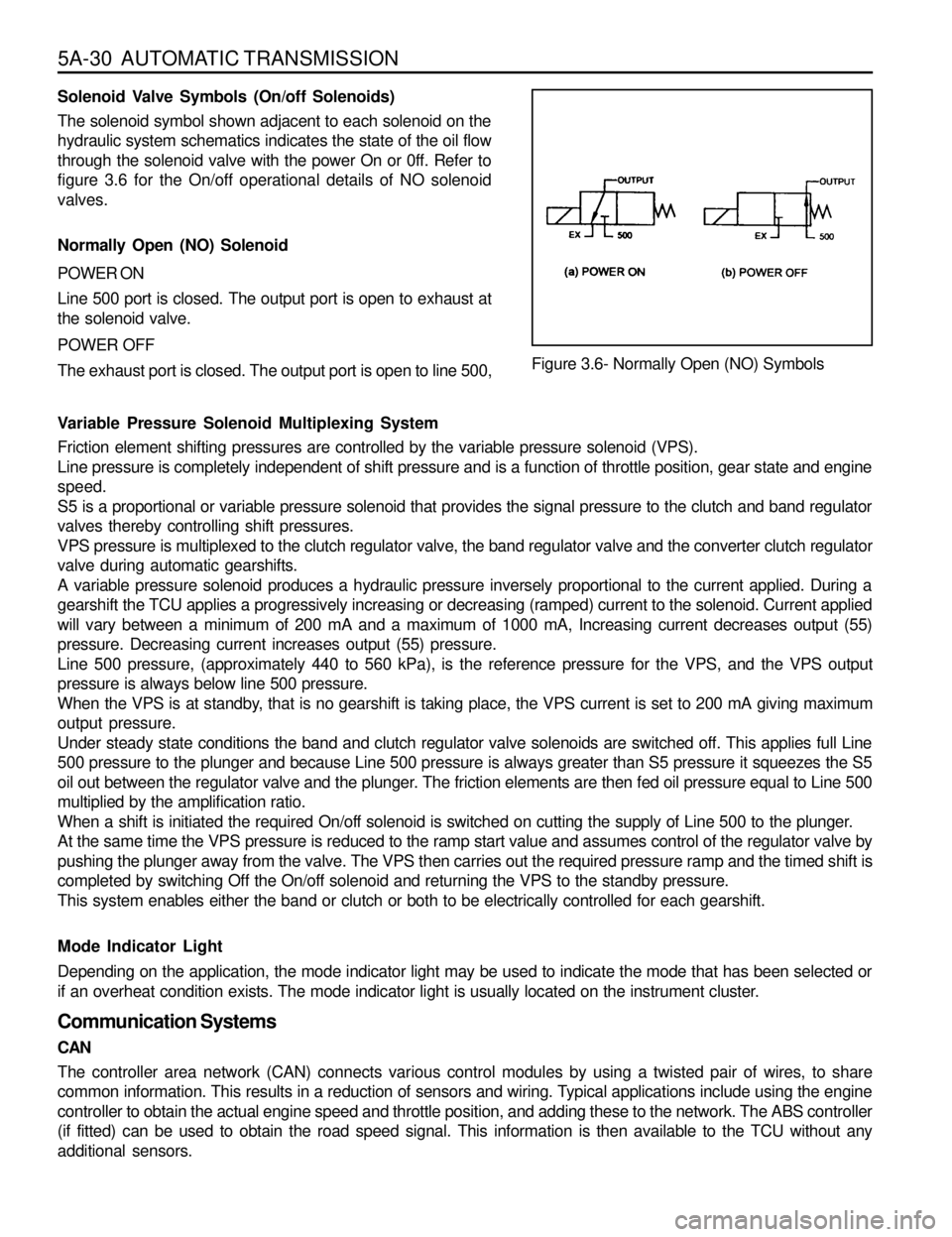
5A-30 AUTOMATIC TRANSMISSION
Solenoid Valve Symbols (On/off Solenoids)
The solenoid symbol shown adjacent to each solenoid on the
hydraulic system schematics indicates the state of the oil flow
through the solenoid valve with the power On or 0ff. Refer to
figure 3.6 for the On/off operational details of NO solenoid
valves.
Normally Open (NO) Solenoid
POWER ON
Line 500 port is closed. The output port is open to exhaust at
the solenoid valve.
POWER OFF
The exhaust port is closed. The output port is open to line 500,Figure 3.6- Normally Open (NO) Symbols
Variable Pressure Solenoid Multiplexing System
Friction element shifting pressures are controlled by the variable pressure solenoid (VPS).
Line pressure is completely independent of shift pressure and is a function of throttle position, gear state and engine
speed.
S5 is a proportional or variable pressure solenoid that provides the signal pressure to the clutch and band regulator
valves thereby controlling shift pressures.
VPS pressure is multiplexed to the clutch regulator valve, the band regulator valve and the converter clutch regulator
valve during automatic gearshifts.
A variable pressure solenoid produces a hydraulic pressure inversely proportional to the current applied. During a
gearshift the TCU applies a progressively increasing or decreasing (ramped) current to the solenoid. Current applied
will vary between a minimum of 200 mA and a maximum of 1000 mA, Increasing current decreases output (55)
pressure. Decreasing current increases output (55) pressure.
Line 500 pressure, (approximately 440 to 560 kPa), is the reference pressure for the VPS, and the VPS output
pressure is always below line 500 pressure.
When the VPS is at standby, that is no gearshift is taking place, the VPS current is set to 200 mA giving maximum
output pressure.
Under steady state conditions the band and clutch regulator valve solenoids are switched off. This applies full Line
500 pressure to the plunger and because Line 500 pressure is always greater than S5 pressure it squeezes the S5
oil out between the regulator valve and the plunger. The friction elements are then fed oil pressure equal to Line 500
multiplied by the amplification ratio.
When a shift is initiated the required On/off solenoid is switched on cutting the supply of Line 500 to the plunger.
At the same time the VPS pressure is reduced to the ramp start value and assumes control of the regulator valve by
pushing the plunger away from the valve. The VPS then carries out the required pressure ramp and the timed shift is
completed by switching Off the On/off solenoid and returning the VPS to the standby pressure.
This system enables either the band or clutch or both to be electrically controlled for each gearshift.
Mode Indicator Light
Depending on the application, the mode indicator light may be used to indicate the mode that has been selected or
if an overheat condition exists. The mode indicator light is usually located on the instrument cluster.
Communication Systems
CAN
The controller area network (CAN) connects various control modules by using a twisted pair of wires, to share
common information. This results in a reduction of sensors and wiring. Typical applications include using the engine
controller to obtain the actual engine speed and throttle position, and adding these to the network. The ABS controller
(if fitted) can be used to obtain the road speed signal. This information is then available to the TCU without any
additional sensors.
Page 1017 of 1463

5A-40 AUTOMATIC TRANSMISSION
Converter Clutch Regulator Valve
The converter clutch regulator valve (refer figure 3.20) regulates
the pressure of the oil which applies the converter clutch. Input
oil from the line 500 circuit is regulated within the valve, with
the output pressure being variable according to the signal
pressure from the S5 circuit. Converter clutch apply and release
application is smoothed by electronically varying the S5 circuit
pressure.
Converter Clutch Control Valve
The converter clutch control valve (refer figure 3.21) is a two position valve which applies or releases the converter
clutch.
The switching of this valve is governed by the signal pressure from S7.
When the valve is in the off or released position, converter feed oil from the PRV is directed to the release side of the
converter clutch. After flowing through the converter, oil returns to the converter clutch control valve and is then
directed to the oil cooler.
When the valve is in the on or applied position, regulated oil from the converter clutch regulator valve is directed to
the apply side of the converter clutch. This oil remains within the converter because the converter clutch piston is
sealed against the flat friction surface of the converter cover. To provide oil flow to the cooler the converter clutch
control valve directs converter feed oil from the PRV directly to the cooler circuit.
Figure 3.21- Converter Clutch Control ValveFigure 3.20 - Converter Clutch Regulator Valve
Page 1042 of 1463
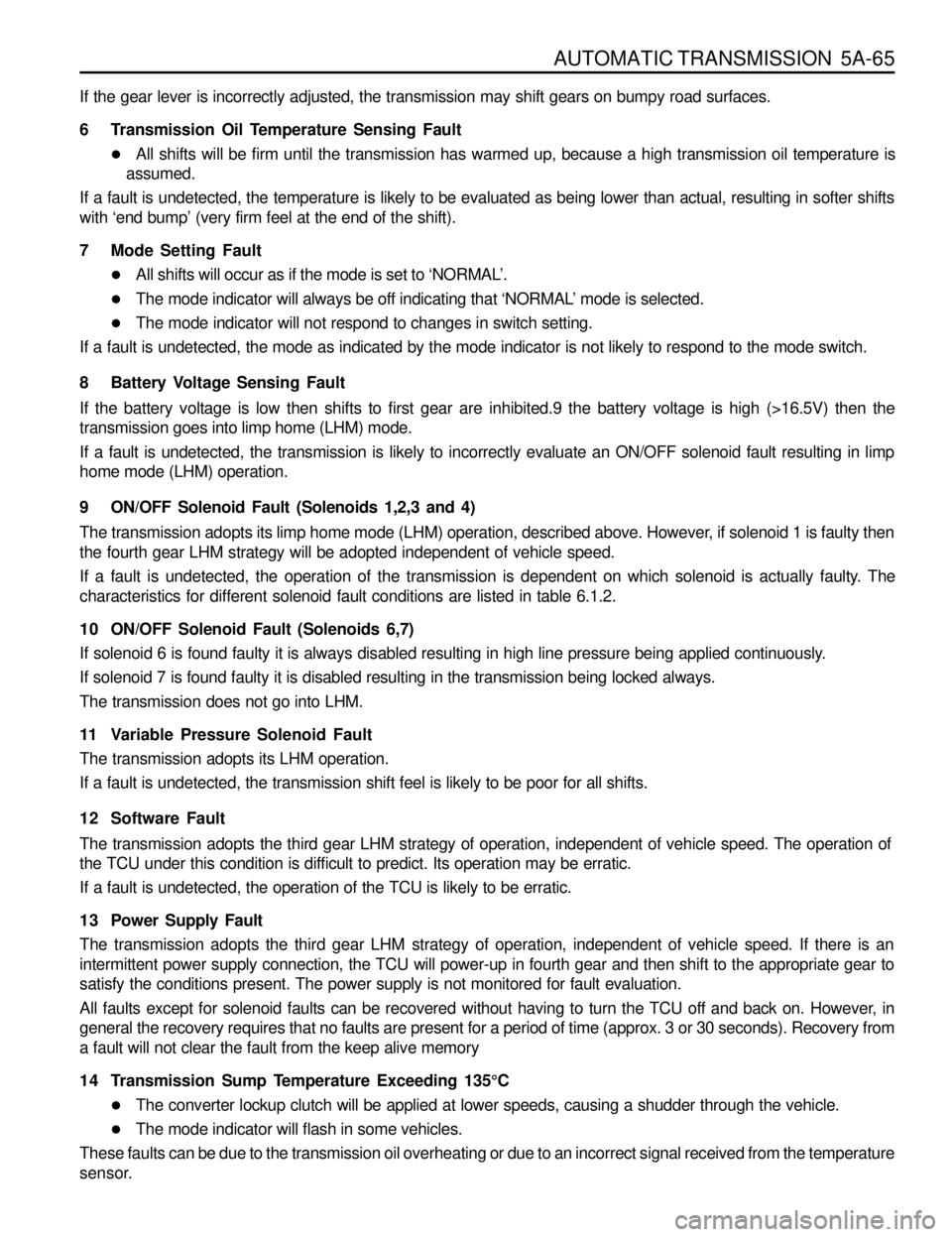
AUTOMATIC TRANSMISSION 5A-65
If the gear lever is incorrectly adjusted, the transmission may shift gears on bumpy road surfaces.
6 Transmission Oil Temperature Sensing Fault
lAll shifts will be firm until the transmission has warmed up, because a high transmission oil temperature is
assumed.
If a fault is undetected, the temperature is likely to be evaluated as being lower than actual, resulting in softer shifts
with ‘end bump’ (very firm feel at the end of the shift).
7 Mode Setting Fault
lAll shifts will occur as if the mode is set to ‘NORMAL’.
lThe mode indicator will always be off indicating that ‘NORMAL’ mode is selected.
lThe mode indicator will not respond to changes in switch setting.
If a fault is undetected, the mode as indicated by the mode indicator is not likely to respond to the mode switch.
8 Battery Voltage Sensing Fault
If the battery voltage is low then shifts to first gear are inhibited.9 the battery voltage is high (>16.5V) then the
transmission goes into limp home (LHM) mode.
If a fault is undetected, the transmission is likely to incorrectly evaluate an ON/OFF solenoid fault resulting in limp
home mode (LHM) operation.
9 ON/OFF Solenoid Fault (Solenoids 1,2,3 and 4)
The transmission adopts its limp home mode (LHM) operation, described above. However, if solenoid 1 is faulty then
the fourth gear LHM strategy will be adopted independent of vehicle speed.
If a fault is undetected, the operation of the transmission is dependent on which solenoid is actually faulty. The
characteristics for different solenoid fault conditions are listed in table 6.1.2.
10 ON/OFF Solenoid Fault (Solenoids 6,7)
If solenoid 6 is found faulty it is always disabled resulting in high line pressure being applied continuously.
If solenoid 7 is found faulty it is disabled resulting in the transmission being locked always.
The transmission does not go into LHM.
11 Variable Pressure Solenoid Fault
The transmission adopts its LHM operation.
If a fault is undetected, the transmission shift feel is likely to be poor for all shifts.
12 Software Fault
The transmission adopts the third gear LHM strategy of operation, independent of vehicle speed. The operation of
the TCU under this condition is difficult to predict. Its operation may be erratic.
If a fault is undetected, the operation of the TCU is likely to be erratic.
13 Power Supply Fault
The transmission adopts the third gear LHM strategy of operation, independent of vehicle speed. If there is an
intermittent power supply connection, the TCU will power-up in fourth gear and then shift to the appropriate gear to
satisfy the conditions present. The power supply is not monitored for fault evaluation.
All faults except for solenoid faults can be recovered without having to turn the TCU off and back on. However, in
general the recovery requires that no faults are present for a period of time (approx. 3 or 30 seconds). Recovery from
a fault will not clear the fault from the keep alive memory
14 Transmission Sump Temperature Exceeding 135°C
lThe converter lockup clutch will be applied at lower speeds, causing a shudder through the vehicle.
lThe mode indicator will flash in some vehicles.
These faults can be due to the transmission oil overheating or due to an incorrect signal received from the temperature
sensor.
Page 1045 of 1463
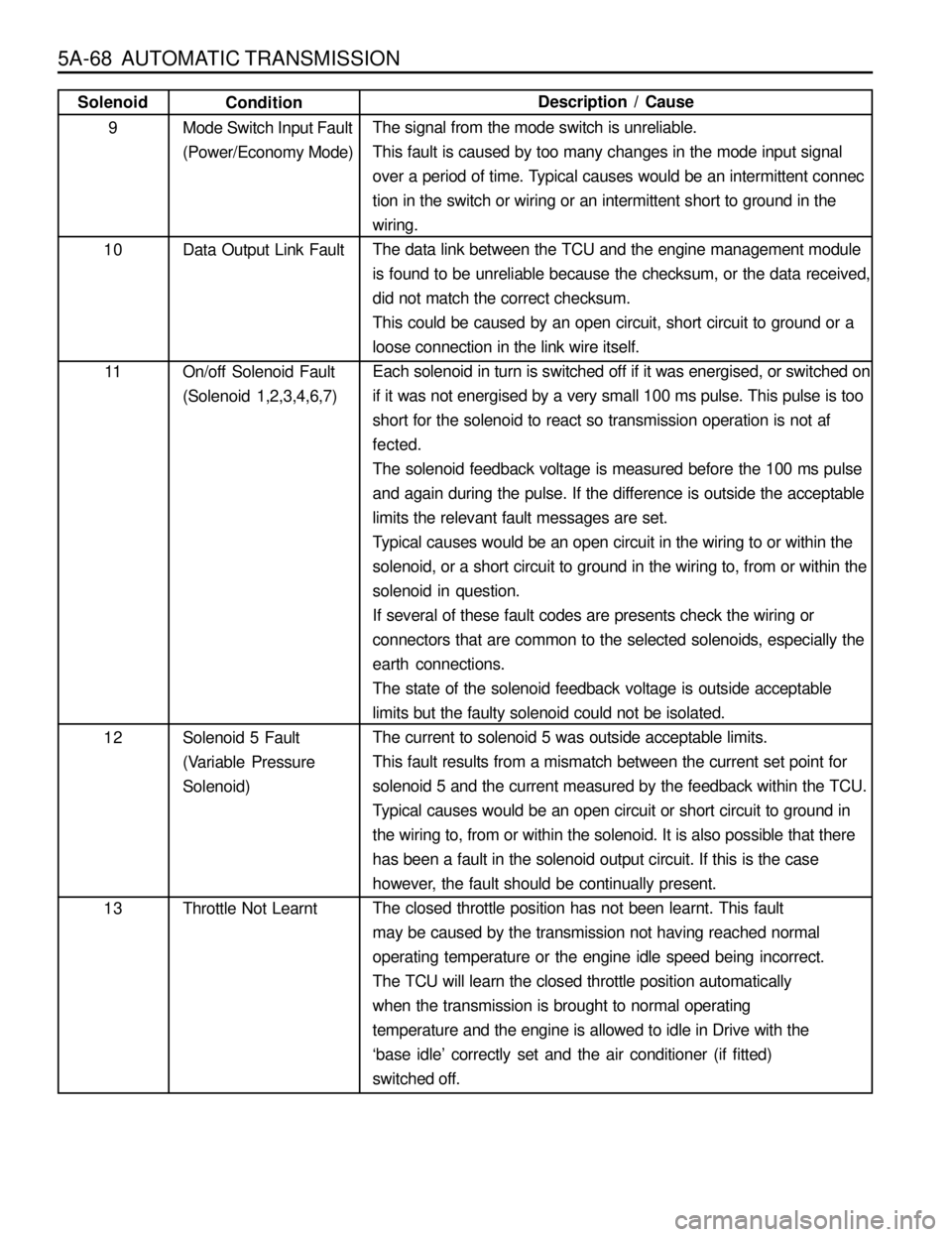
5A-68 AUTOMATIC TRANSMISSION
Description / Cause
The signal from the mode switch is unreliable.
This fault is caused by too many changes in the mode input signal
over a period of time. Typical causes would be an intermittent connec
tion in the switch or wiring or an intermittent short to ground in the
wiring.
The data link between the TCU and the engine management module
is found to be unreliable because the checksum, or the data received,
did not match the correct checksum.
This could be caused by an open circuit, short circuit to ground or a
loose connection in the link wire itself.
Each solenoid in turn is switched off if it was energised, or switched on
if it was not energised by a very small 100 ms pulse. This pulse is too
short for the solenoid to react so transmission operation is not af
fected.
The solenoid feedback voltage is measured before the 100 ms pulse
and again during the pulse. If the difference is outside the acceptable
limits the relevant fault messages are set.
Typical causes would be an open circuit in the wiring to or within the
solenoid, or a short circuit to ground in the wiring to, from or within the
solenoid in question.
If several of these fault codes are presents check the wiring or
connectors that are common to the selected solenoids, especially the
earth connections.
The state of the solenoid feedback voltage is outside acceptable
limits but the faulty solenoid could not be isolated.
The current to solenoid 5 was outside acceptable limits.
This fault results from a mismatch between the current set point for
solenoid 5 and the current measured by the feedback within the TCU.
Typical causes would be an open circuit or short circuit to ground in
the wiring to, from or within the solenoid. It is also possible that there
has been a fault in the solenoid output circuit. If this is the case
however, the fault should be continually present.
The closed throttle position has not been learnt. This fault
may be caused by the transmission not having reached normal
operating temperature or the engine idle speed being incorrect.
The TCU will learn the closed throttle position automatically
when the transmission is brought to normal operating
temperature and the engine is allowed to idle in Drive with the
‘base idle’ correctly set and the air conditioner (if fitted)
switched off. Condition
Mode Switch Input Fault
(Power/Economy Mode)
Data Output Link Fault
On/off Solenoid Fault
(Solenoid 1,2,3,4,6,7)
Solenoid 5 Fault
(Variable Pressure
Solenoid)
Throttle Not LearntSolenoid
9
10
11
12
13