Reverse back up SSANGYONG MUSSO 2003 Service Manual
[x] Cancel search | Manufacturer: SSANGYONG, Model Year: 2003, Model line: MUSSO, Model: SSANGYONG MUSSO 2003Pages: 1574, PDF Size: 26.41 MB
Page 644 of 1574
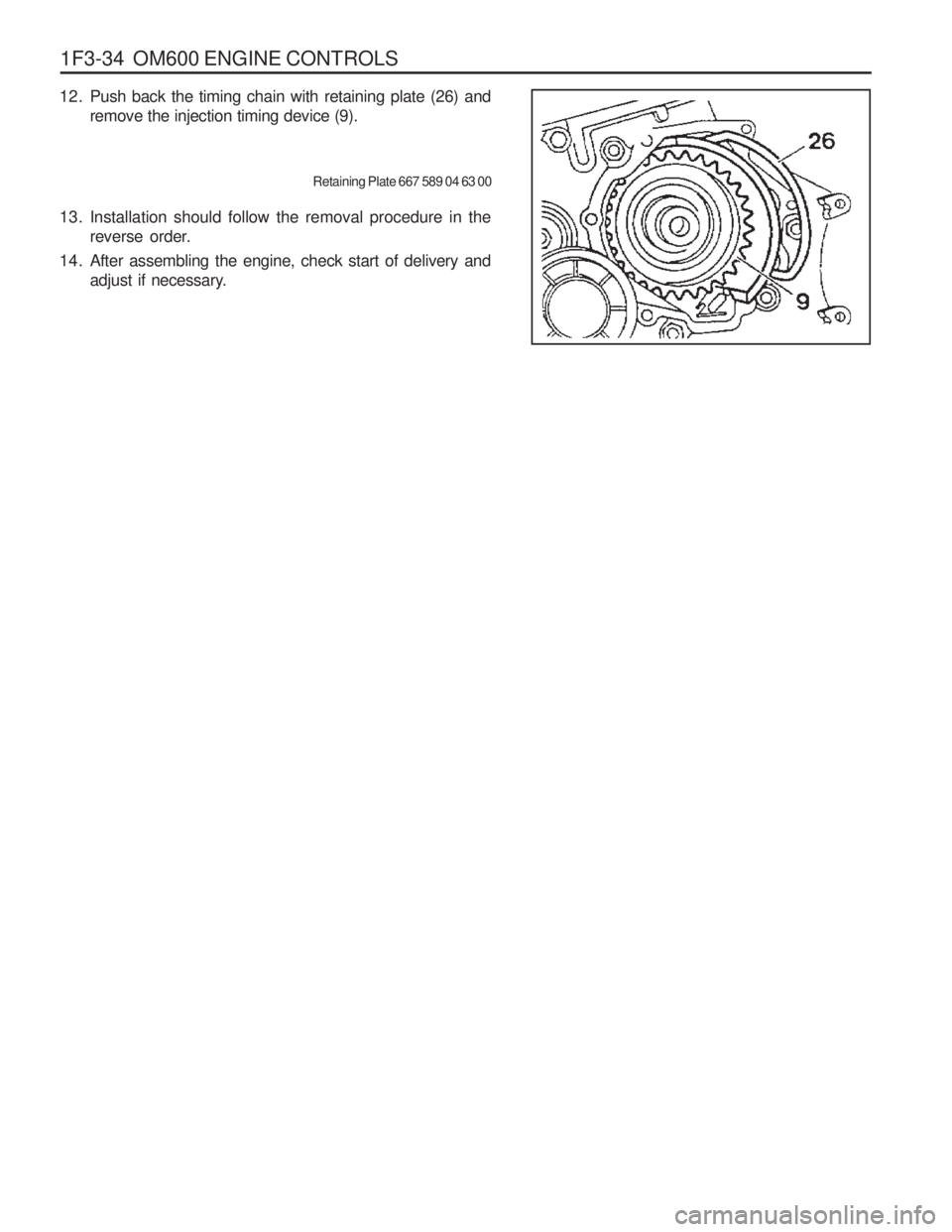
1F3-34 OM600 ENGINE CONTROLS
12. Push back the timing chain with retaining plate (26) and remove the injection timing device (9).
Retaining Plate 667 589 04 63 00
13. Installation should follow the removal procedure in the reverse order.
14. After assembling the engine, check start of delivery and adjust if necessary.
Page 788 of 1574
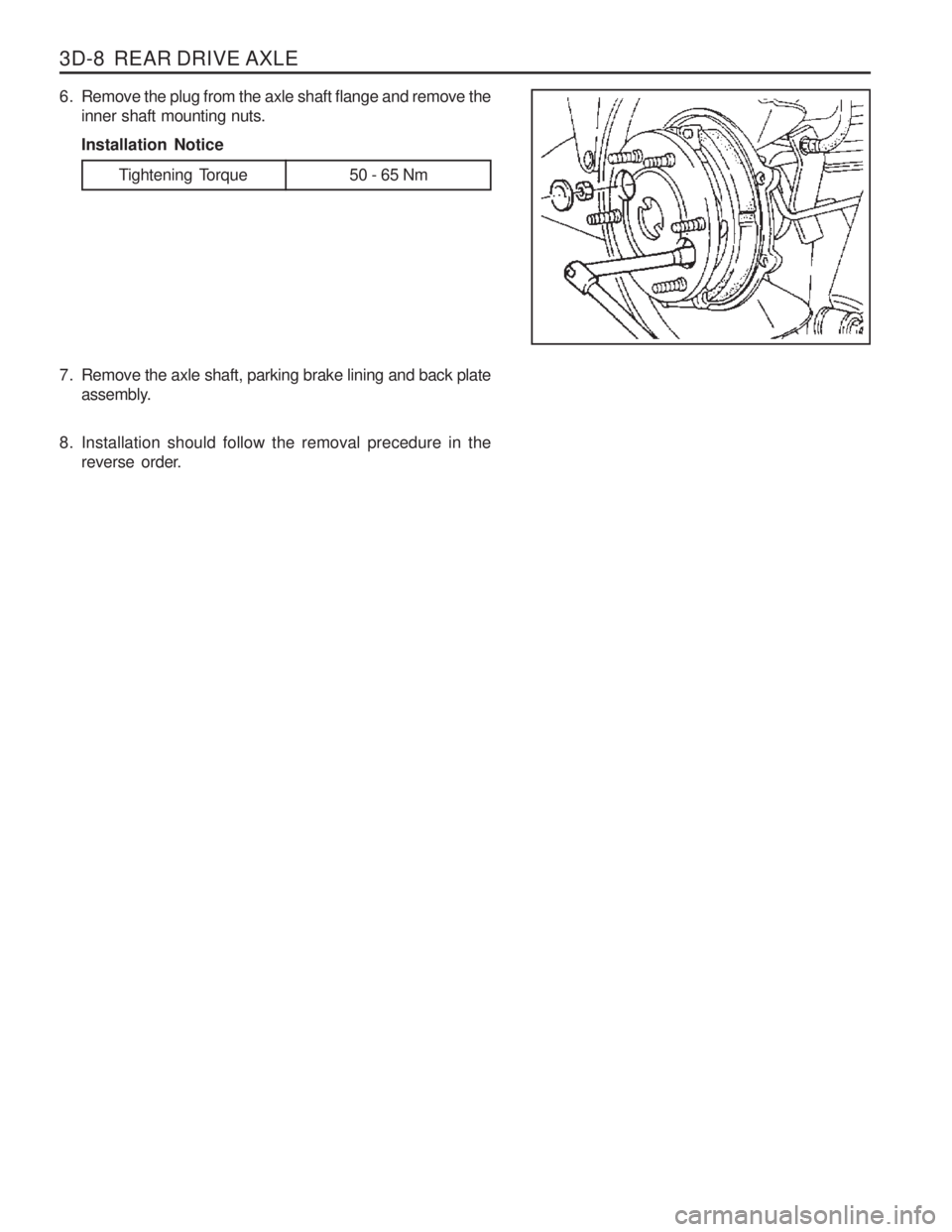
3D-8 REAR DRIVE AXLE
Tightening Torque 50 - 65 Nm
6. Remove the plug from the axle shaft flange and remove theinner shaft mounting nuts. Installation Notice
7. Remove the axle shaft, parking brake lining and back plate assembly.
8. Installation should follow the removal precedure in the reverse order.
Page 883 of 1574
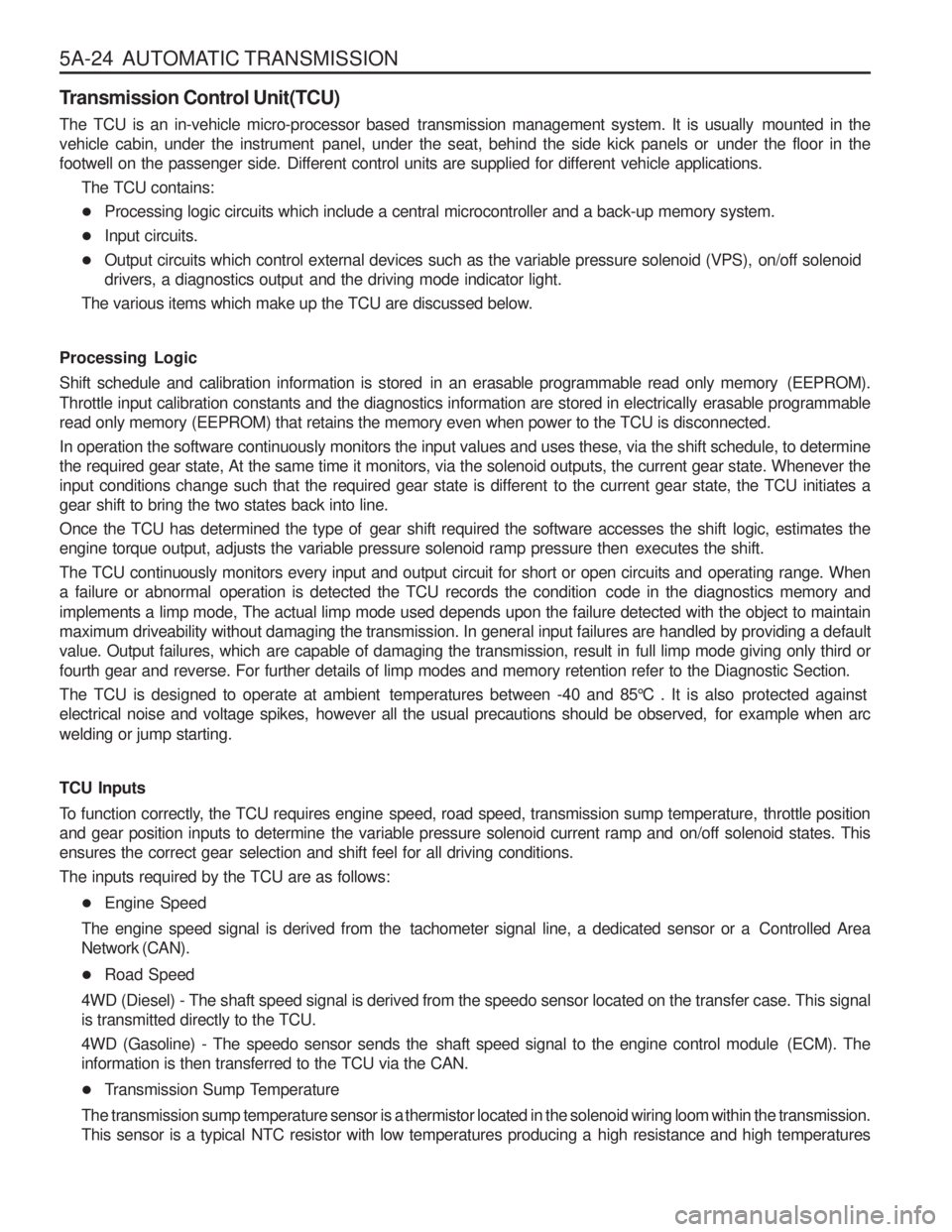
5A-24 AUTOMATIC TRANSMISSION
Transmission Control Unit(TCU)
The TCU is an in-vehicle micro-processor based transmission management system. It is usually mounted in the
vehicle cabin, under the instrument panel, under the seat, behind the side kick panels or under the floor in the
footwell on the passenger side. Different control units are supplied for different vehicle applications.The TCU contains:
Processing logic circuits which include a central microcontroller and a back-up memory system.
Input circuits.
Output circuits which control external devices such as the variable pressure solenoid (VPS), on/off solenoid
drivers, a diagnostics output and the driving mode indicator light.
The various items which make up the TCU are discussed below.
Processing Logic
Shift schedule and calibration information is stored in an erasable programmable read only memory (EEPROM).
Throttle input calibration constants and the diagnostics information are stored in electrically erasable programmable
read only memory (EEPROM) that retains the memory even when power to the TCU is disconnected. In operation the software continuously monitors the input values and uses these, via the shift schedule, to determine the required gear state, At the same time it monitors, via the solenoid outputs, the current gear state. Whenever the
input conditions change such that the required gear state is different to the current gear state, the TCU initiates a
gear shift to bring the two states back into line.
Once the TCU has determined the type of gear shift required the software accesses the shift logic, estimates the
engine torque output, adjusts the variable pressure solenoid ramp pressure then executes the shift.
The TCU continuously monitors every input and output circuit for short or open circuits and operating range. When
a failure or abnormal operation is detected the TCU records the condition code in the diagnostics memory and
implements a limp mode, The actual limp mode used depends upon the failure detected with the object to maintain
maximum driveability without damaging the transmission. In general input failures are handled by providing a default
value. Output failures, which are capable of damaging the transmission, result in full limp mode giving only third or
fourth gear and reverse. For further details of limp modes and memory retention refer to the Diagnostic Section.
The TCU is designed to operate at ambient temperatures between -40 and 85°C . It is also protected against
electrical noise and voltage spikes, however all the usual precautions should be observed, for example when arc welding or jump starting. TCU Inputs
To function correctly, the TCU requires engine speed, road speed, transmission sump temperature, throttle position
and gear position inputs to determine the variable pressure solenoid current ramp and on/off solenoid states. This
ensures the correct gear selection and shift feel for all driving conditions. The inputs required by the TCU are as follows: Engine Speed
The engine speed signal is derived from the tachometer signal line, a dedicated sensor or a Controlled Area Network (CAN).
Road Speed
4WD (Diesel) - The shaft speed signal is derived from the speedo sensor located on the transfer case. This signal is transmitted directly to the TCU.
4WD (Gasoline) - The speedo sensor sends the shaft speed signal to the engine control module (ECM). The
information is then transferred to the TCU via the CAN.
Transmission Sump Temperature
The transmission sump temperature sensor is a thermistor located in the solenoid wiring loom within the transmission.
This sensor is a typical NTC resistor with low temperatures producing a high resistance and high temperatures
Page 898 of 1574
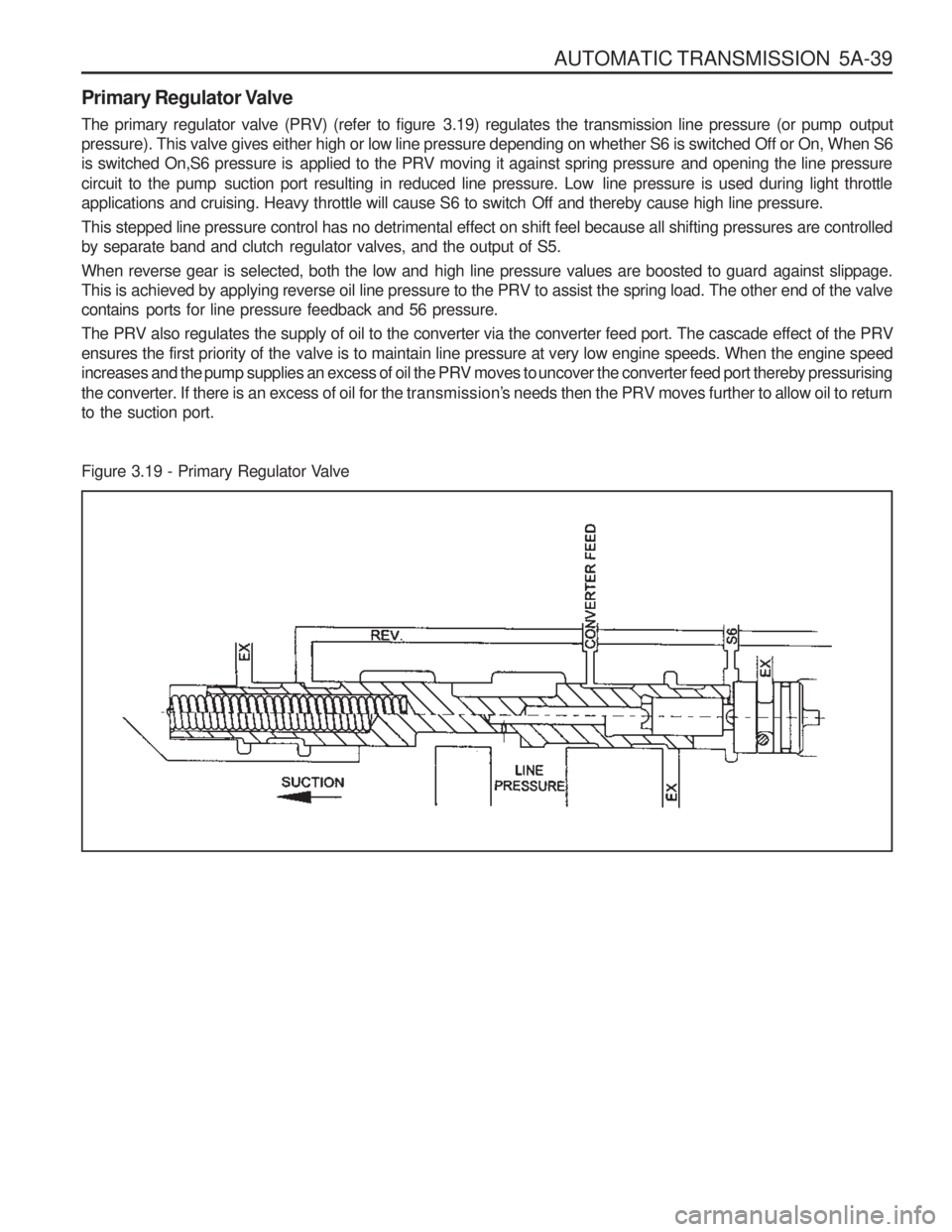
AUTOMATIC TRANSMISSION 5A-39
Primary Regulator Valve
The primary regulator valve (PRV) (refer to figure 3.19) regulates the transmission line pressure (or pump output
pressure). This valve gives either high or low line pressure depending on whether S6 is switched Off or On, When S6
is switched On,S6 pressure is applied to the PRV moving it against spring pressure and opening the line pressure
circuit to the pump suction port resulting in reduced line pressure. Low line pressure is used during light throttle
applications and cruising. Heavy throttle will cause S6 to switch Off and thereby cause high line pressure.
This stepped line pressure control has no detrimental effect on shift feel because all shifting pressures are controlled
by separate band and clutch regulator valves, and the output of S5.
When reverse gear is selected, both the low and high line pressure values are boosted to guard against slippage.
This is achieved by applying reverse oil line pressure to the PRV to assist the spring load. The other end of the valvecontains ports for line pressure feedback and 56 pressure.
The PRV also regulates the supply of oil to the converter via the converter feed port. The cascade effect of the PRV
ensures the first priority of the valve is to maintain line pressure at very low engine speeds. When the engine speed
increases and the pump supplies an excess of oil the PRV moves to uncover the converter feed port thereby pressurising
the converter. If there is an excess of oil for the transmission’s needs then the PRV moves further to allow oil to return
to the suction port.
Figure 3.19 - Primary Regulator Valve