ECU SSANGYONG RODIUS 2012 Owner's Manual
[x] Cancel search | Manufacturer: SSANGYONG, Model Year: 2012, Model line: RODIUS, Model: SSANGYONG RODIUS 2012Pages: 715, PDF Size: 79.36 MB
Page 320 of 715
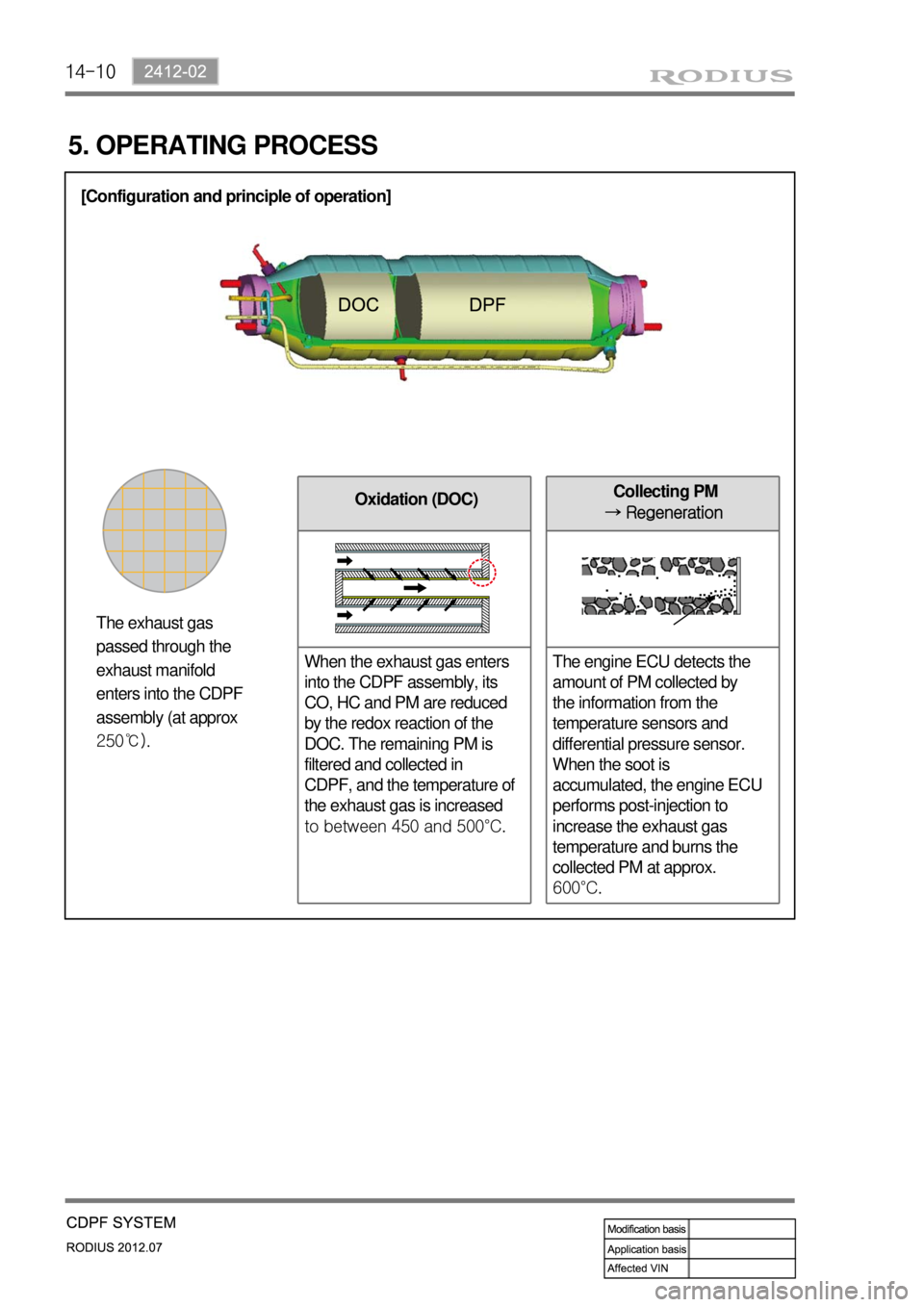
14-10
Collecting PM
→ Regeneration
The engine ECU detects the
amount of PM collected by
the information from the
temperature sensors and
differential pressure sensor.
When the soot is
accumulated, the engine ECU
performs post-injection to
increase the exhaust gas
temperature and burns the
collected PM at approx.
600°C.Oxidation (DOC)
When the exhaust gas enters
into the CDPF assembly, its
CO, HC and PM are reduced
by the redox reaction of the
DOC. The remaining PM is
filtered and collected in
CDPF, and the temperature of
the exhaust gas is increased
to between 450 and 500°C.
5. OPERATING PROCESS
[Configuration and principle of operation]
The exhaust gas
passed through the
exhaust manifold
enters into the CDPF
assembly (at approx
250℃).
Page 322 of 715
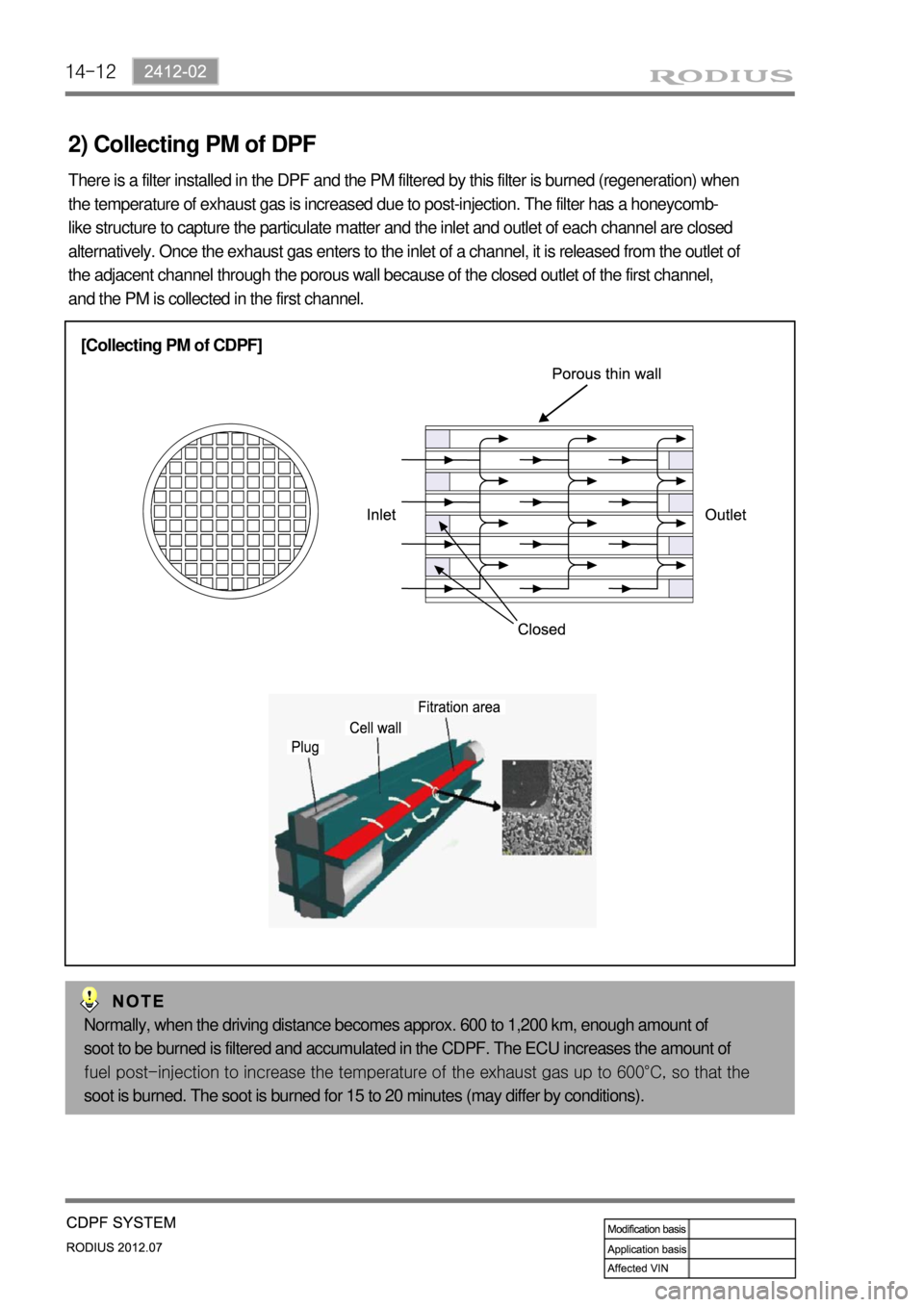
14-12
2) Collecting PM of DPF
There is a filter installed in the DPF and the PM filtered by this filter is burned (regeneration) when
the temperature of exhaust gas is increased due to post-injection. The filter has a honeycomb-
like structure to capture the particulate matter and the inlet and outlet of each channel are closed
alternatively. Once the exhaust gas enters to the inlet of a channel, it is released from the outlet of
the adjacent channel through the porous wall because of the closed outlet of the first channel,
and the PM is collected in the first channel.
[Collecting PM of CDPF]
Normally, when the driving distance becomes approx. 600 to 1,200 km, enough amount of
soot to be burned is filtered and accumulated in the CDPF. The ECU increases the amount of
fuel post-injection to increase the temperature of the exhaust gas up to 600°C, so that the
soot is burned. The soot is burned for 15 to 20 minutes (may differ by conditions).
Page 323 of 715
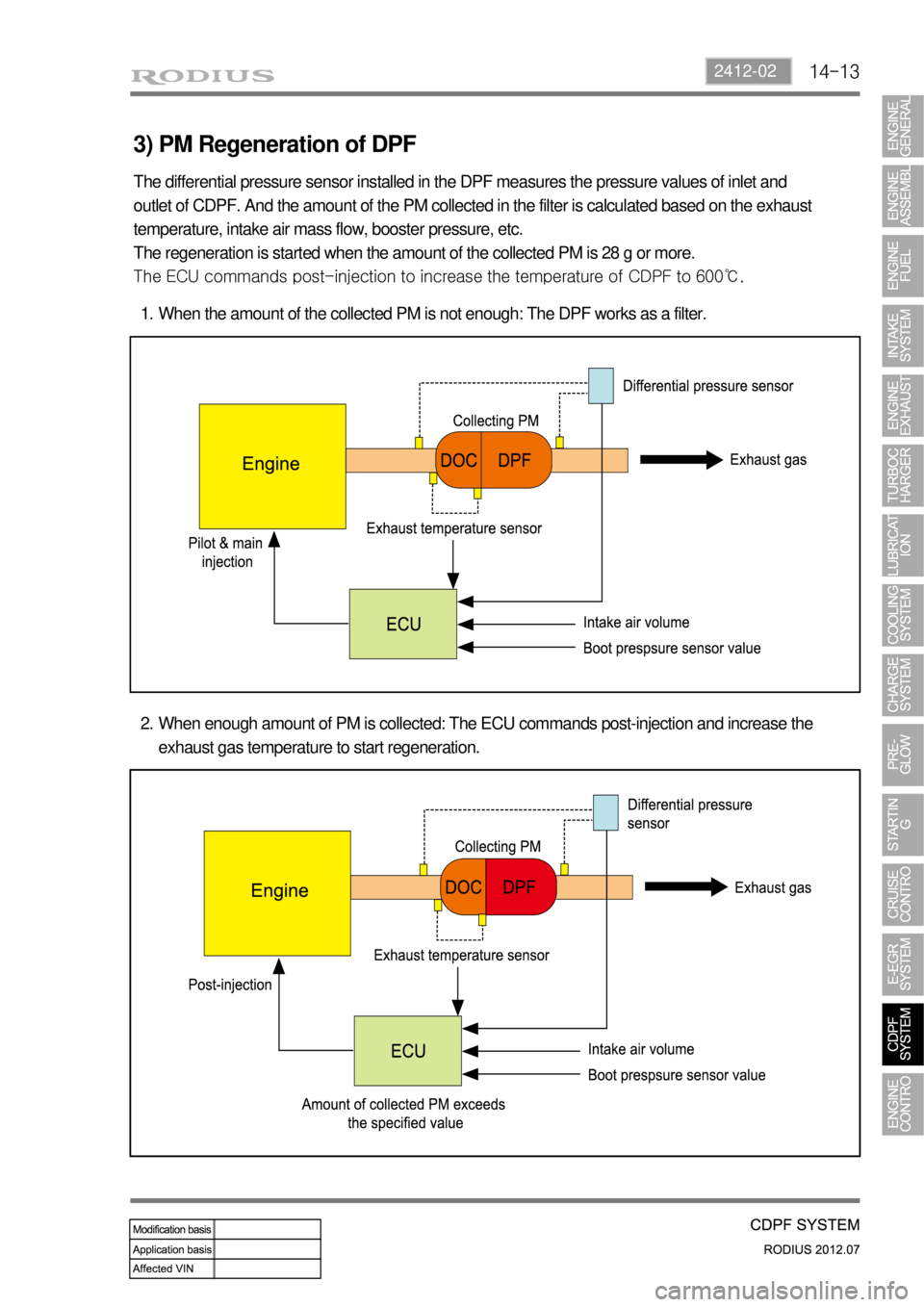
14-132412-02
3) PM Regeneration of DPF
The differential pressure sensor installed in the DPF measures the pressure values of inlet and
outlet of CDPF. And the amount of the PM collected in the filter is calculated based on the exhaust
temperature, intake air mass flow, booster pressure, etc.
The regeneration is started when the amount of the collected PM is 28 g or more.
<007b008f008c0047006c006a007c0047008a00960094009400880095008b009a004700970096009a009b0054009000950091008c008a009b0090009600950047009b0096004700900095008a0099008c0088009a008c0047009b008f008c0047009b008c00
940097008c00990088009b009c0099008c00470096008d0047>CDPF to 600℃.
When the amount of the collected PM is not enough: The DPF works as a filter. 1.
When enough amount of PM is collected: The ECU commands post-injection and increase the
exhaust gas temperature to start regeneration. 2.
Page 332 of 715
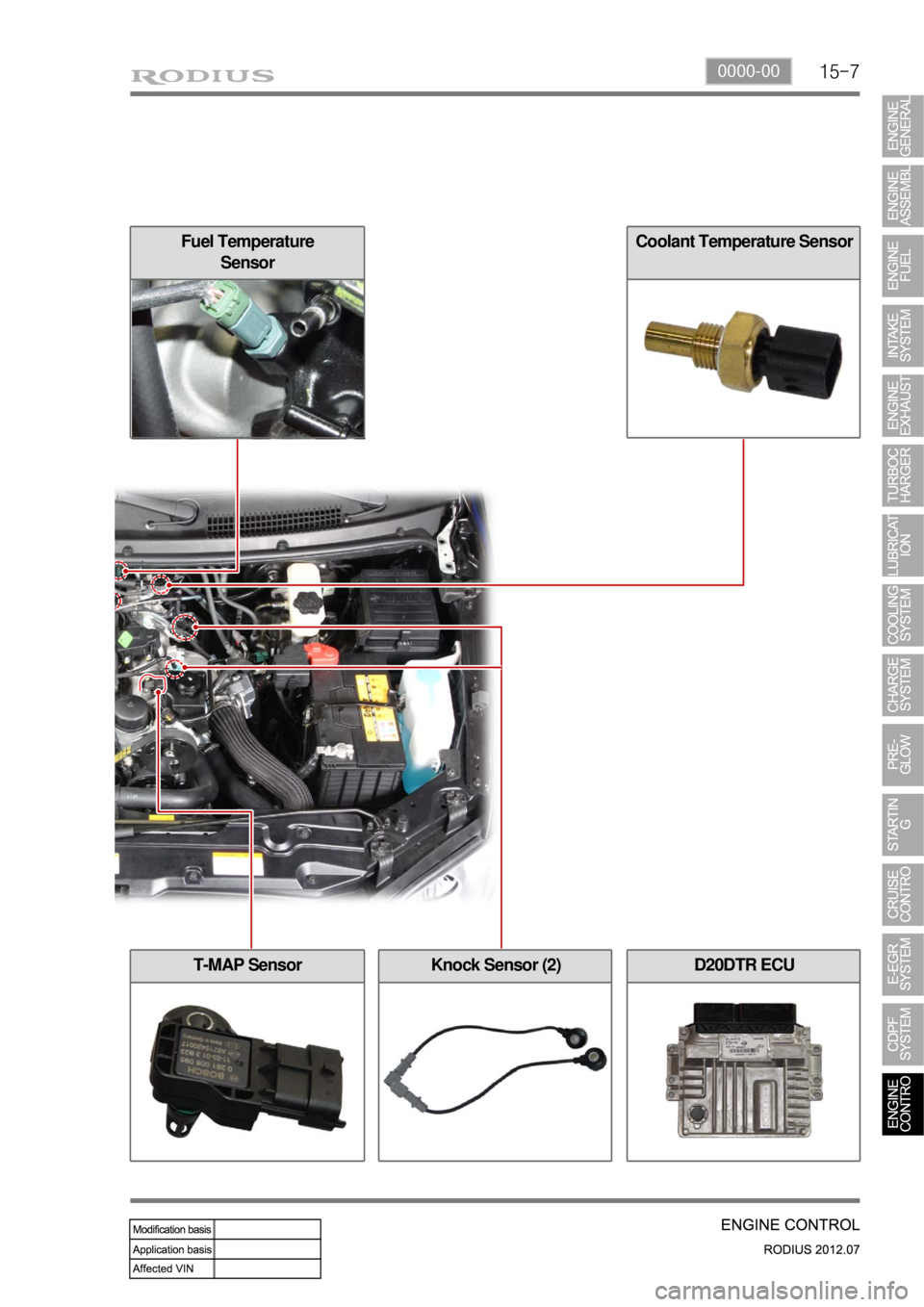
15-70000-00
Fuel Temperature
SensorCoolant Temperature Sensor
Knock Sensor (2)T-MAP SensorD20DTR ECU
Page 333 of 715
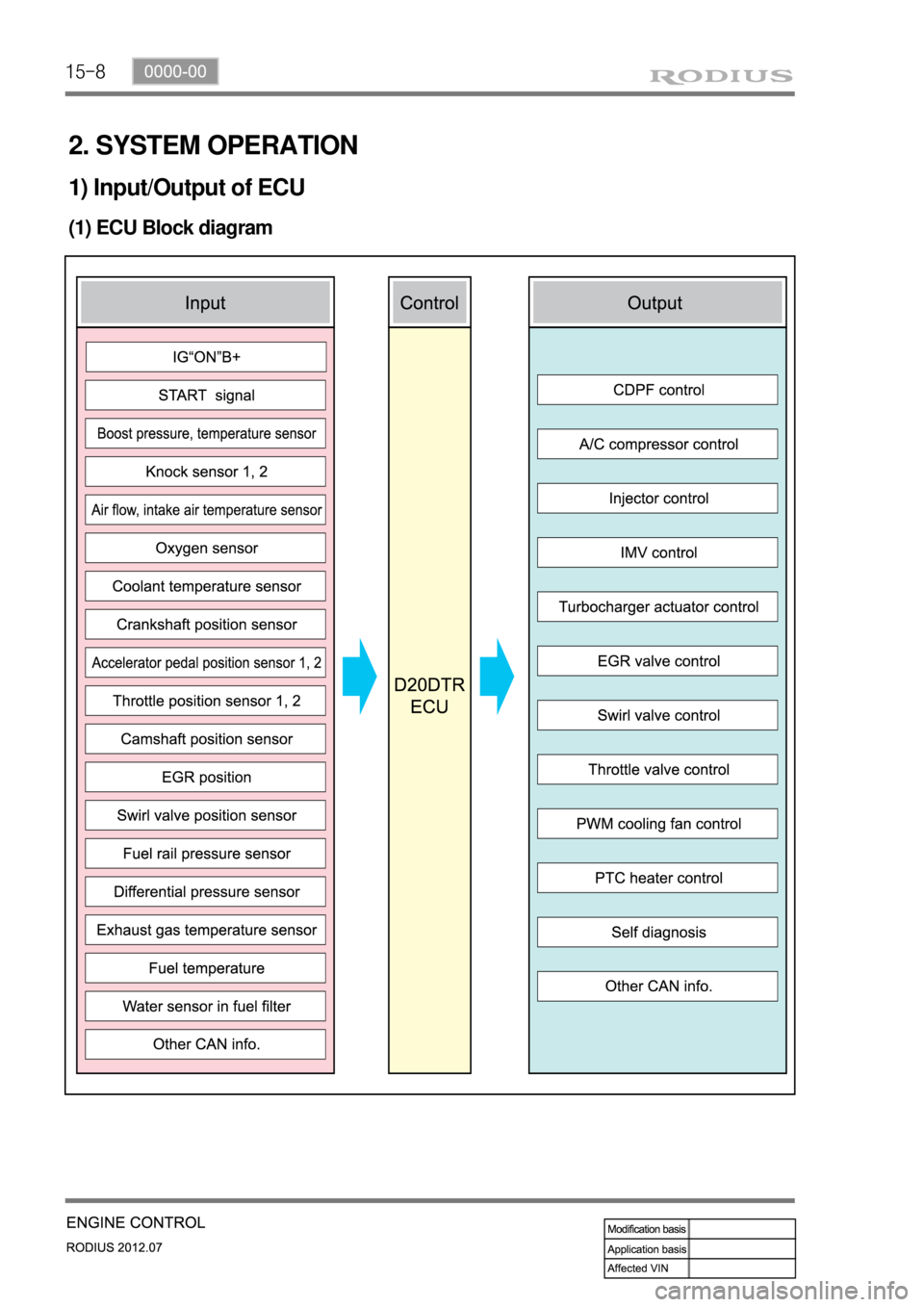
15-8
2. SYSTEM OPERATION
1) Input/Output of ECU
(1) ECU Block diagram
Page 334 of 715
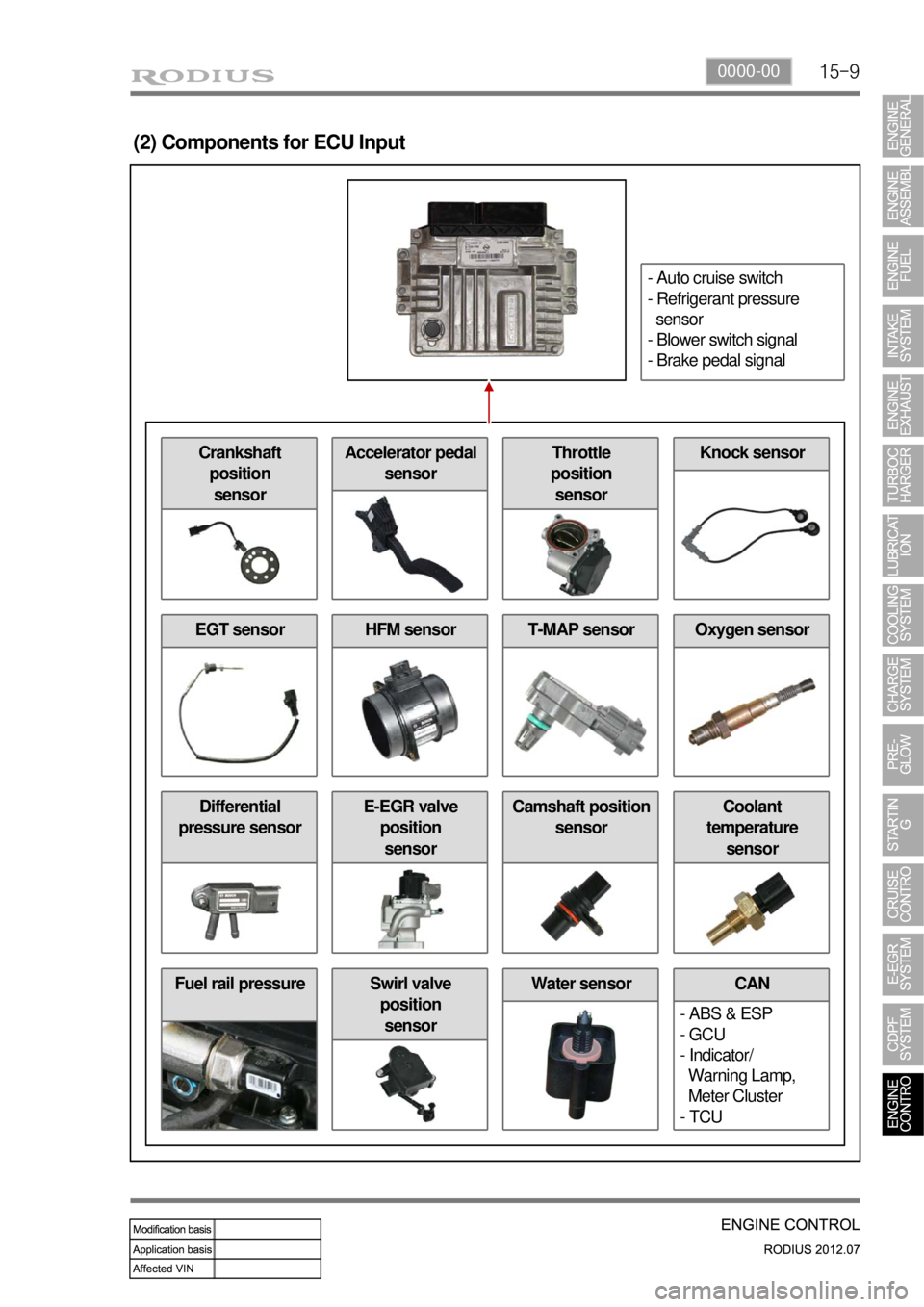
15-90000-00
Fuel rail pressure Water sensor
(2) Components for ECU Input
CAN
- ABS & ESP
- GCU
- Indicator/
Warning Lamp,
Meter Cluster
- TCUSwirl valve
position
sensor
Differential
pressure sensorE-EGR valve
position
sensorCamshaft position
sensorCoolant
temperature
sensor
EGT sensorHFM sensorOxygen sensorT-MAP sensor
Crankshaft
position
sensorAccelerator pedal
sensorThrottle
position
sensorKnock sensor
- Auto cruise switch
- Refrigerant pressure
sensor
- Blower switch signal
- Brake pedal signal
Page 335 of 715
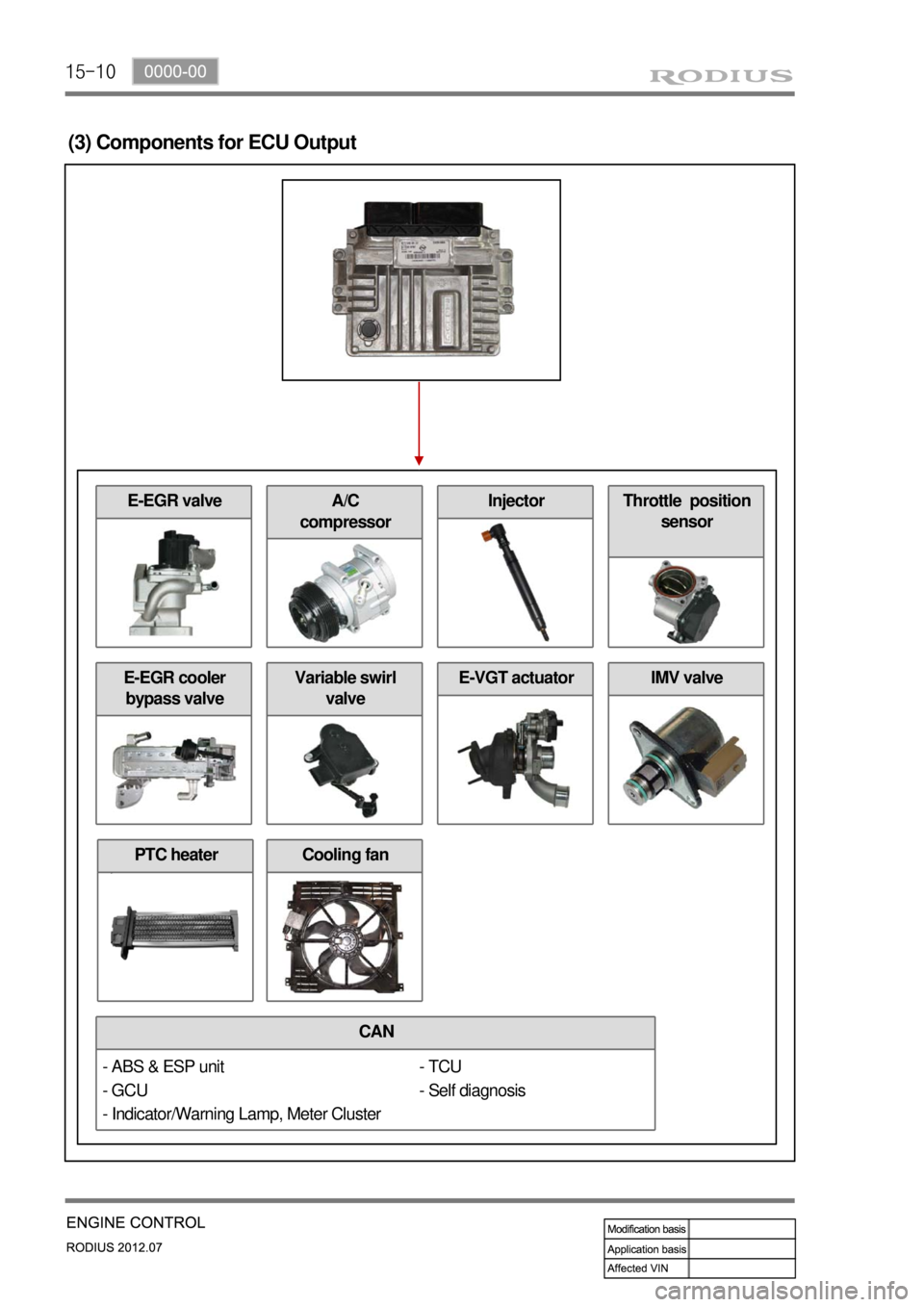
15-10
(3) Components for ECU Output
CAN
E-EGR cooler
bypass valve
- TCU
- Self diagnosis
Cooling fan
E-EGR valve
Variable swirl
valveE-VGT actuatorIMV valve
A/C
compressorInjectorThrottle position
sensor
- ABS & ESP unit
- GCU
- Indicator/Warning Lamp, Meter Cluster
PTC heater
Page 336 of 715
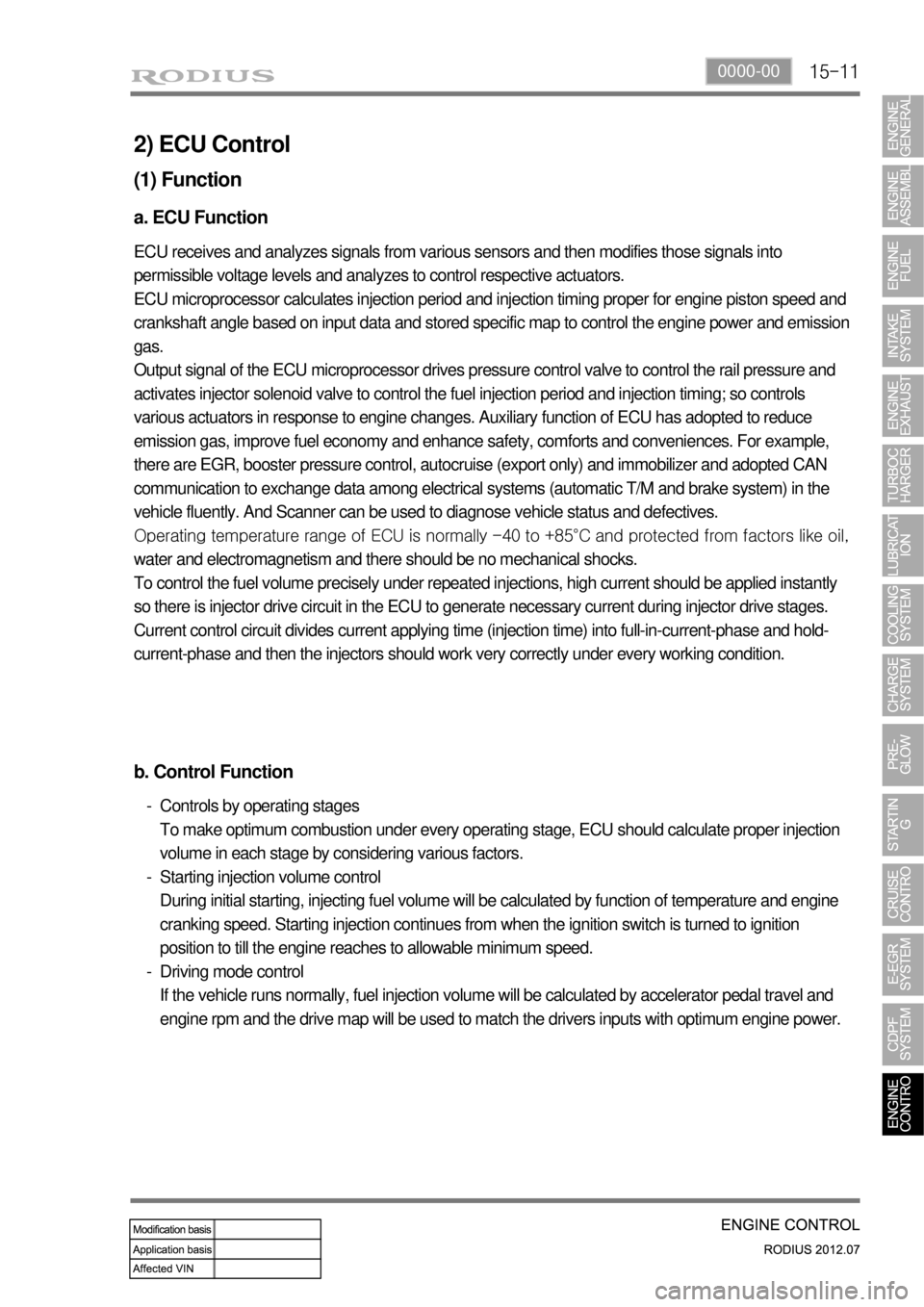
15-110000-00
2) ECU Control
(1) Function
a. ECU Function
ECU receives and analyzes signals from various sensors and then modifies those signals into
permissible voltage levels and analyzes to control respective actuators.
ECU microprocessor calculates injection period and injection timing proper for engine piston speed and
crankshaft angle based on input data and stored specific map to control the engine power and emission
gas.
Output signal of the ECU microprocessor drives pressure control valve to control the rail pressure and
activates injector solenoid valve to control the fuel injection period and injection timing; so controls
various actuators in response to engine changes. Auxiliary function of ECU has adopted to reduce
emission gas, improve fuel economy and enhance safety, comforts and conveniences. For example,
there are EGR, booster pressure control, autocruise (export only) and immobilizer and adopted CAN
communication to exchange data among electrical systems (automatic T/M and brake system) in the
vehicle fluently. And Scanner can be used to diagnose vehicle status and defectives.
<00760097008c00990088009b00900095008e0047009b008c00940097008c00990088009b009c0099008c0047009900880095008e008c00470096008d0047006c006a007c00470090009a0047009500960099009400880093009300a000470054005b005700
47009b009600470052005f005c00b6006a004700880095008b> protected from factors like oil,
water and electromagnetism and there should be no mechanical shocks.
To control the fuel volume precisely under repeated injections, high current should be applied instantly
so there is injector drive circuit in the ECU to generate necessary current during injector drive stages.
Current control circuit divides current applying time (injection time) into full-in-current-phase and hold-
current-phase and then the injectors should work very correctly under every working condition.
b. Control Function
Controls by operating stages
To make optimum combustion under every operating stage, ECU should calculate proper injection
volume in each stage by considering various factors.
Starting injection volume control
During initial starting, injecting fuel volume will be calculated by function of temperature and engine
cranking speed. Starting injection continues from when the ignition switch is turned to ignition
position to till the engine reaches to allowable minimum speed.
Driving mode control
If the vehicle runs normally, fuel injection volume will be calculated by accelerator pedal travel and
engine rpm and the drive map will be used to match the drivers inputs with optimum engine power. -
-
-
Page 340 of 715
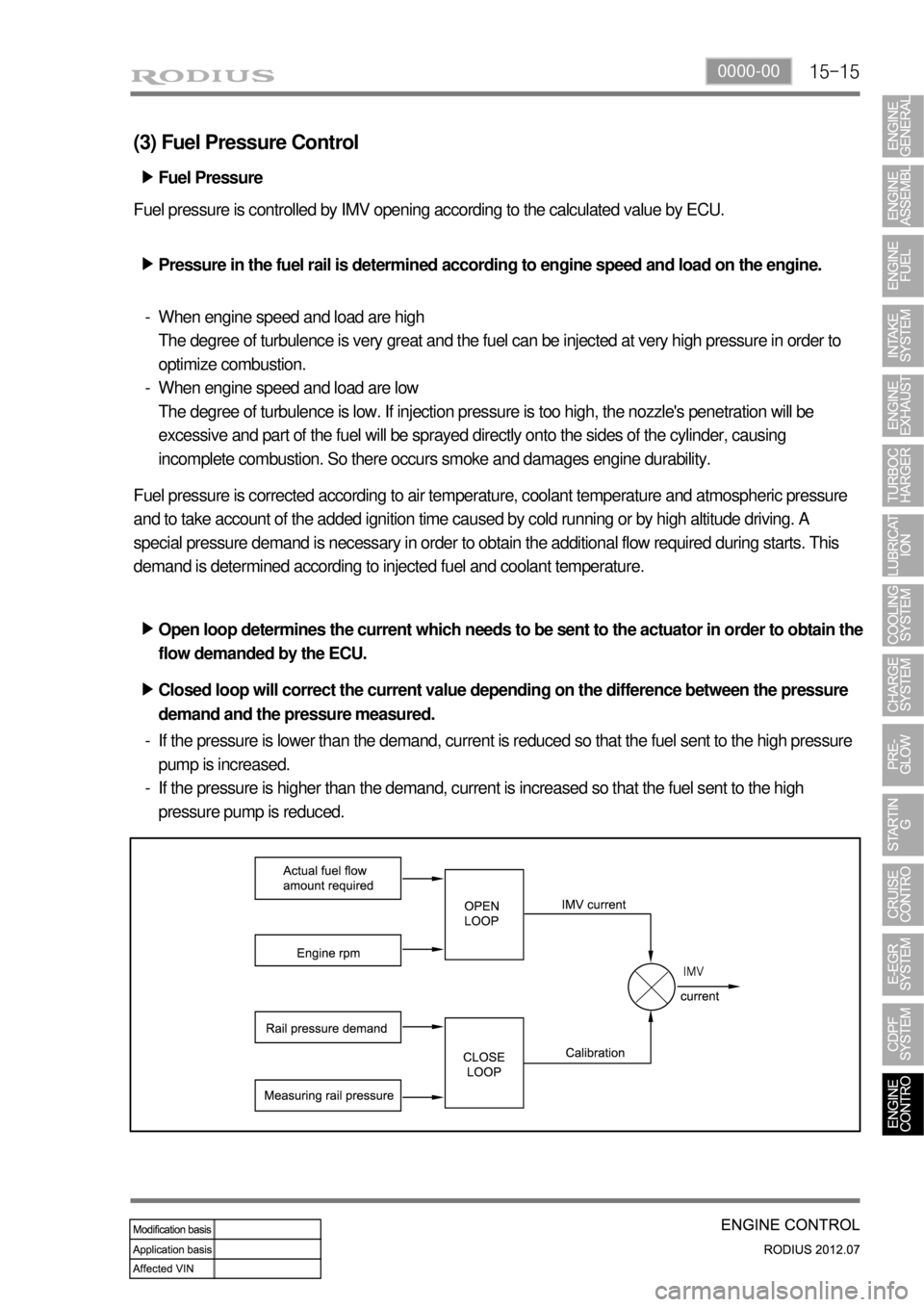
15-150000-00
(3) Fuel Pressure Control
Fuel pressure is controlled by IMV opening according to the calculated value by ECU.
Pressure in the fuel rail is determined according to engine speed and load on the engine. â–¶
When engine speed and load are high
The degree of turbulence is very great and the fuel can be injected at very high pressure in order to
optimize combustion.
When engine speed and load are low
The degree of turbulence is low. If injection pressure is too high, the nozzle's penetration will be
excessive and part of the fuel will be sprayed directly onto the sides of the cylinder, causing
incomplete combustion. So there occurs smoke and damages engine durability. -
-
Fuel pressure is corrected according to air temperature, coolant temperature and atmospheric pressure
and to take account of the added ignition time caused by cold running or by high altitude driving. A
special pressure demand is necessary in order to obtain the additional flow required during starts. This
demand is determined according to injected fuel and coolant temperature.
Open loop determines the current which needs to be sent to the actuator in order to obtain the
flow demanded by the ECU. â–¶
Closed loop will correct the current value depending on the difference between the pressure
demand and the pressure measured. â–¶
If the pressure is lower than the demand, current is reduced so that the fuel sent to the high pressure
pump is increased.
If the pressure is higher than the demand, current is increased so that the fuel sent to the high
pressure pump is reduced. -
-Fuel Pressure â–¶
Page 345 of 715
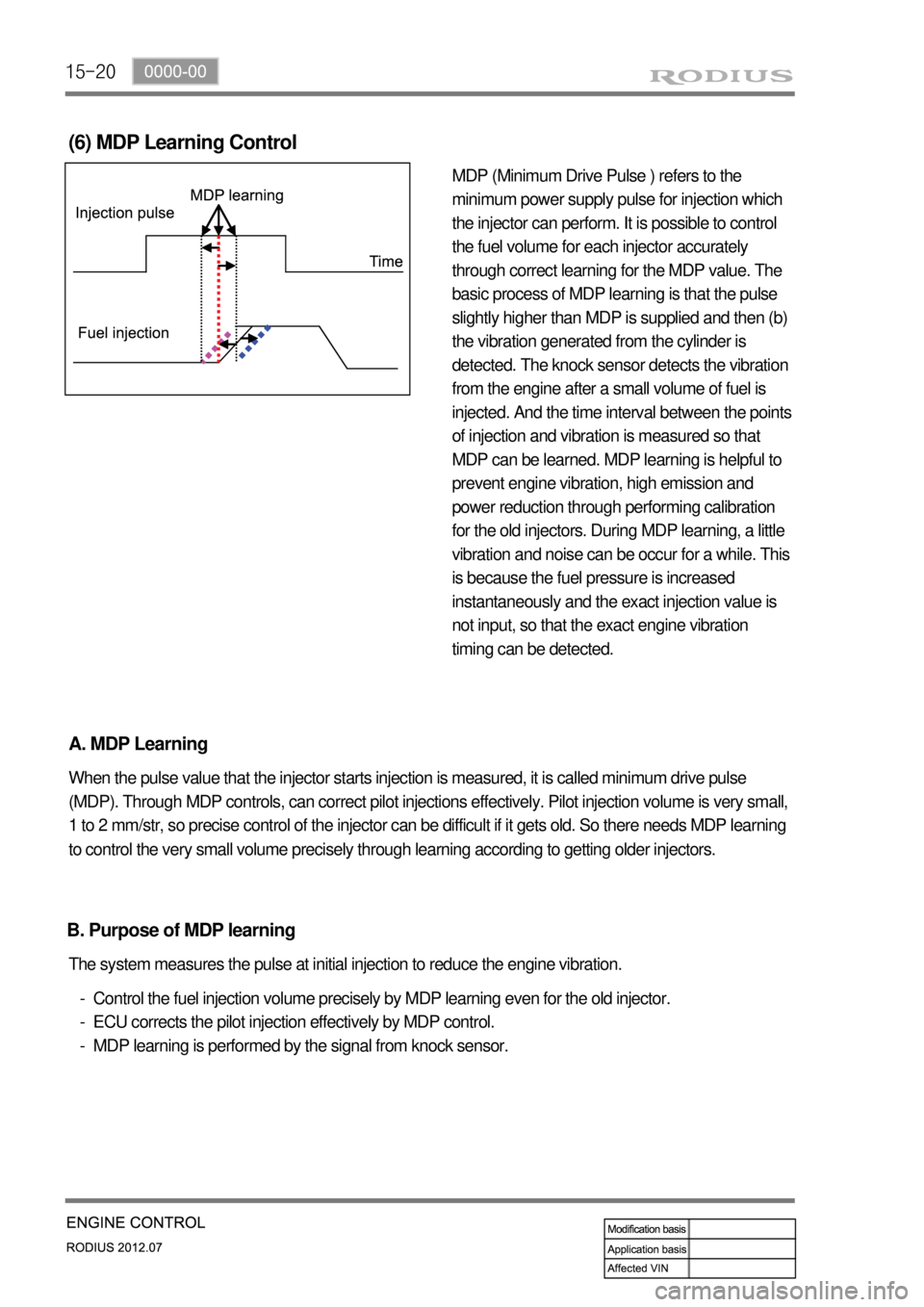
15-20
MDP (Minimum Drive Pulse ) refers to the
minimum power supply pulse for injection which
the injector can perform. It is possible to control
the fuel volume for each injector accurately
through correct learning for the MDP value. The
basic process of MDP learning is that the pulse
slightly higher than MDP is supplied and then (b)
the vibration generated from the cylinder is
detected. The knock sensor detects the vibration
from the engine after a small volume of fuel is
injected. And the time interval between the points
of injection and vibration is measured so that
MDP can be learned. MDP learning is helpful to
prevent engine vibration, high emission and
power reduction through performing calibration
for the old injectors. During MDP learning, a little
vibration and noise can be occur for a while. This
is because the fuel pressure is increased
instantaneously and the exact injection value is
not input, so that the exact engine vibration
timing can be detected.
(6) MDP Learning Control
A. MDP Learning
When the pulse value that the injector starts injection is measured, it is called minimum drive pulse
(MDP). Through MDP controls, can correct pilot injections effectively. Pilot injection volume is very small,
1 to 2 mm/str, so precise control of the injector can be difficult if it gets old. So there needs MDP learning
to control the very small volume precisely through learning according to getting older injectors.
Control the fuel injection volume precisely by MDP learning even for the old injector.
ECU corrects the pilot injection effectively by MDP control.
MDP learning is performed by the signal from knock sensor. -
-
- The system measures the pulse at initial injection to reduce the engine vibration.
B. Purpose of MDP learning