engine SSANGYONG TURISMO 2013 Service Manual
[x] Cancel search | Manufacturer: SSANGYONG, Model Year: 2013, Model line: TURISMO, Model: SSANGYONG TURISMO 2013Pages: 796, PDF Size: 78.99 MB
Page 640 of 796
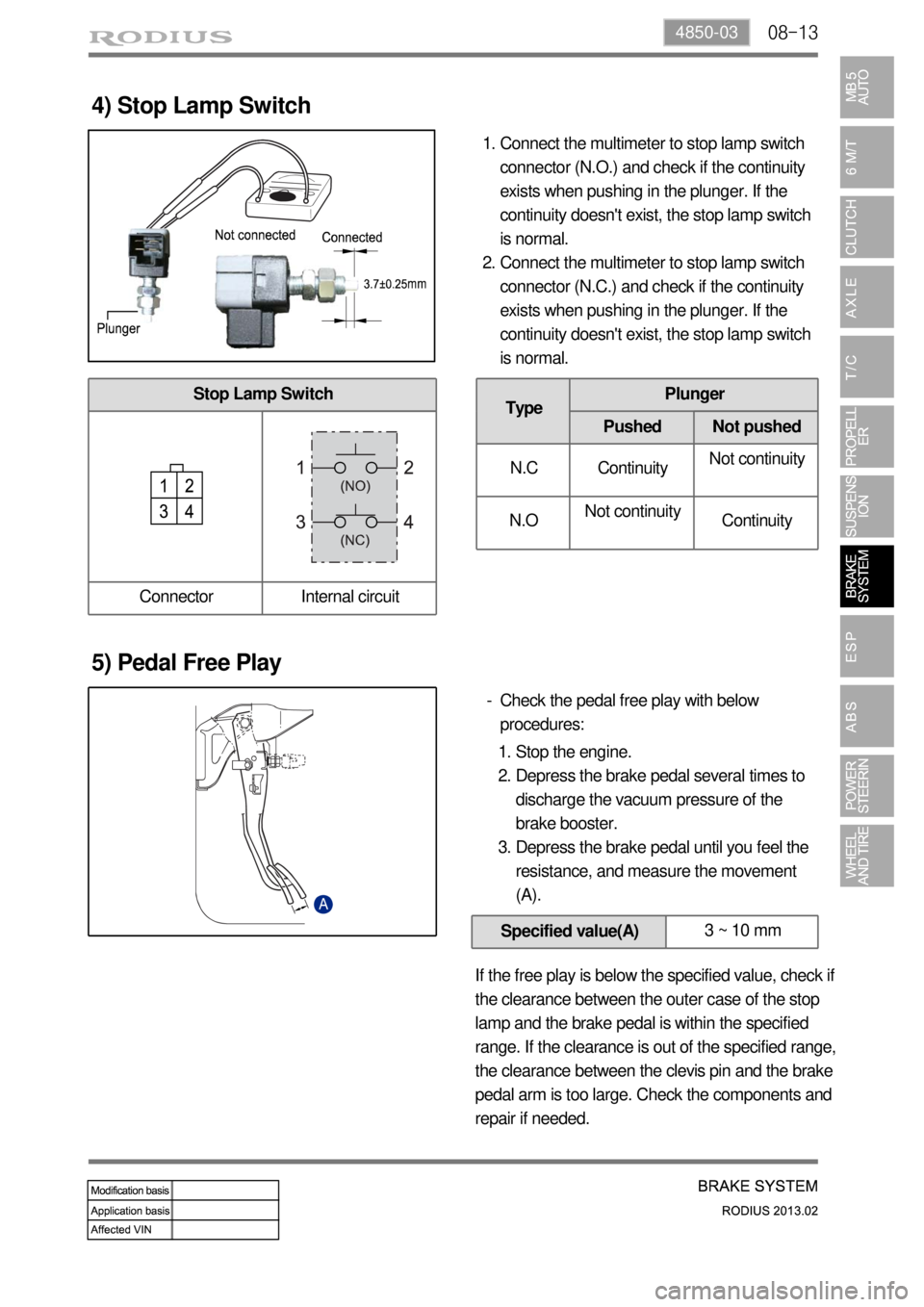
08-134850-03
Stop Lamp Switch
Connector Internal circuit
4) Stop Lamp Switch
Connect the multimeter to stop lamp switch
connector (N.O.) and check if the continuity
exists when pushing in the plunger. If the
continuity doesn't exist, the stop lamp switch
is normal.
Connect the multimeter to stop lamp switch
connector (N.C.) and check if the continuity
exists when pushing in the plunger. If the
continuity doesn't exist, the stop lamp switch
is normal. 1.
2.
TypePlunger
Pushed Not pushed
N.C ContinuityNot continuity
N.O Not continuity
Continuity
5) Pedal Free Play
Check the pedal free play with below
procedures: -
Stop the engine.
Depress the brake pedal several times to
discharge the vacuum pressure of the
brake booster.
Depress the brake pedal until you feel the
resistance, and measure the movement
(A). 1.
2.
3.
Specified value(A)3 ~ 10 mm
If the free play is below the specified value, check if
the clearance between the outer case of the stop
lamp and the brake pedal is within the specified
range. If the clearance is out of the specified range,
the clearance between the clevis pin and the brake
pedal arm is too large. Check the components and
repair if needed.
Page 651 of 796
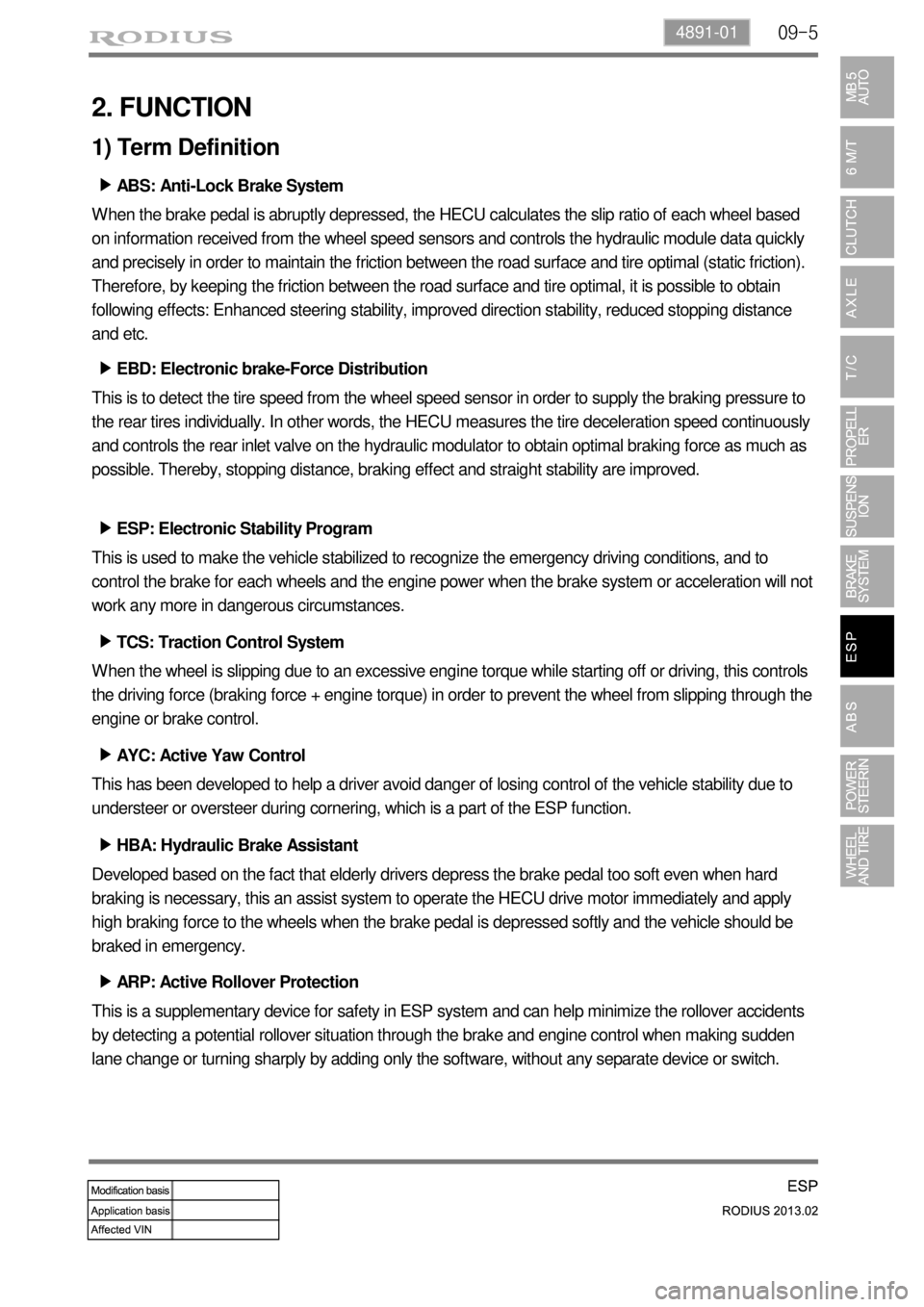
09-54891-01
2. FUNCTION
1) Term Definition
ABS: Anti-Lock Brake System ▶
When the brake pedal is abruptly depressed, the HECU calculates the slip ratio of each wheel based
on information received from the wheel speed sensors and controls the hydraulic module data quickly
and precisely in order to maintain the friction between the road surface and tire optimal (static friction).
Therefore, by keeping the friction between the road surface and tire optimal, it is possible to obtain
following effects: Enhanced steering stability, improved direction stability, reduced stopping distance
and etc.
EBD: Electronic brake-Force Distribution ▶
This is to detect the tire speed from the wheel speed sensor in order to supply the braking pressure to
the rear tires individually. In other words, the HECU measures the tire deceleration speed continuously
and controls the rear inlet valve on the hydraulic modulator to obtain optimal braking force as much as
possible. Thereby, stopping distance, braking effect and straight stability are improved.
ESP: Electronic Stability Program ▶
This is used to make the vehicle stabilized to recognize the emergency driving conditions, and to
control the brake for each wheels and the engine power when the brake system or acceleration will not
work any more in dangerous circumstances.
TCS: Traction Control System ▶
When the wheel is slipping due to an excessive engine torque while starting off or driving, this controls
the driving force (braking force + engine torque) in order to prevent the wheel from slipping through the
engine or brake control.
AYC: Active Yaw Control ▶
This has been developed to help a driver avoid danger of losing control of the vehicle stability due to
understeer or oversteer during cornering, which is a part of the ESP function.
HBA: Hydraulic Brake Assistant ▶
Developed based on the fact that elderly drivers depress the brake pedal too soft even when hard
braking is necessary, this an assist system to operate the HECU drive motor immediately and apply
high braking force to the wheels when the brake pedal is depressed softly and the vehicle should be
braked in emergency.
ARP: Active Rollover Protection ▶
This is a supplementary device for safety in ESP system and can help minimize the rollover accidents
by detecting a potential rollover situation through the brake and engine control when making sudden
lane change or turning sharply by adding only the software, without any separate device or switch.
Page 653 of 796
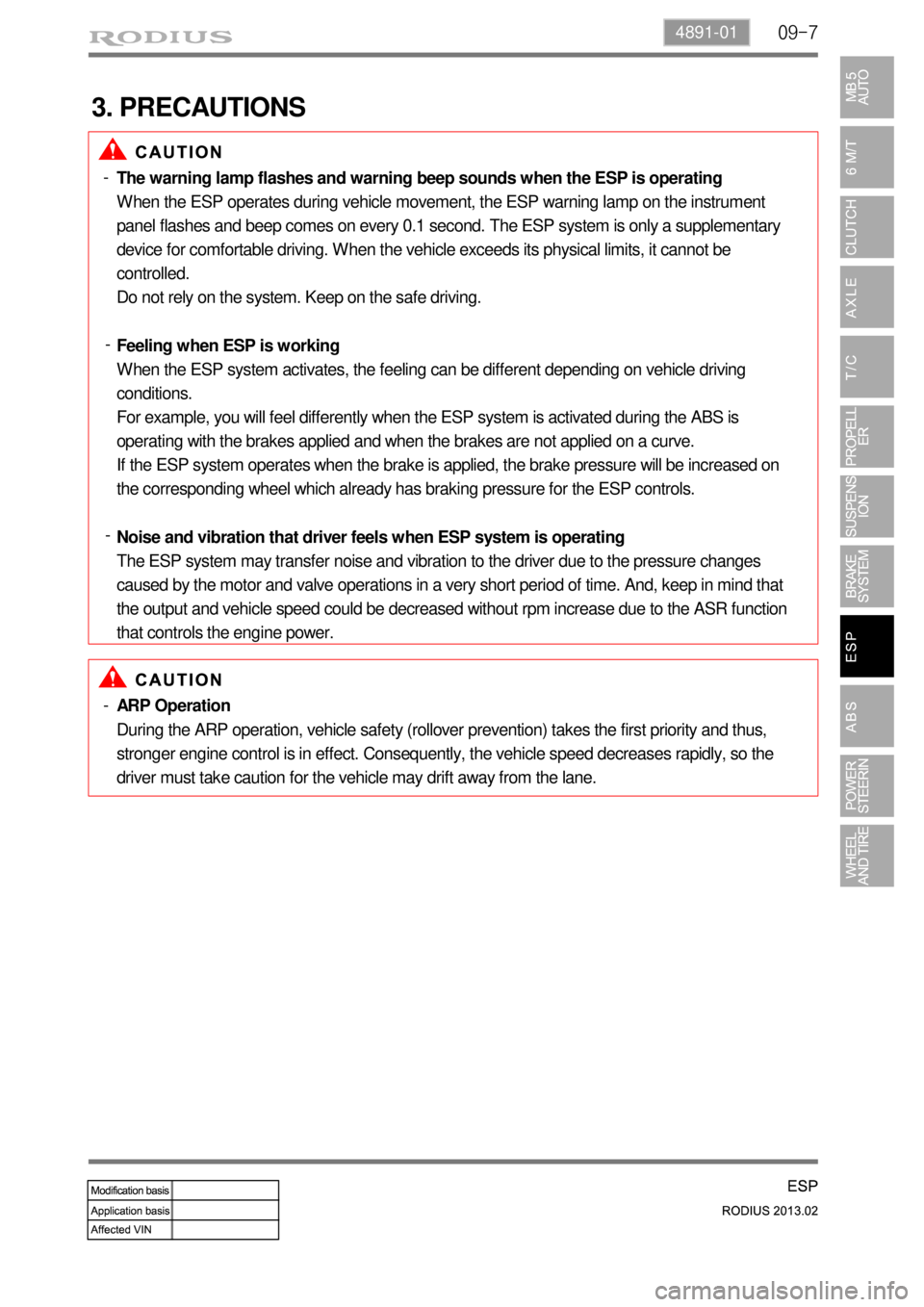
09-74891-01
3. PRECAUTIONS
The warning lamp flashes and warning beep sounds when the ESP is operating
When the ESP operates during vehicle movement, the ESP warning lamp on the instrument
panel flashes and beep comes on every 0.1 second. The ESP system is only a supplementary
device for comfortable driving. When the vehicle exceeds its physical limits, it cannot be
controlled.
Do not rely on the system. Keep on the safe driving.
Feeling when ESP is working
When the ESP system activates, the feeling can be different depending on vehicle driving
conditions.
For example, you will feel differently when the ESP system is activated during the ABS is
operating with the brakes applied and when the brakes are not applied on a curve.
If the ESP system operates when the brake is applied, the brake pressure will be increased on
the corresponding wheel which already has braking pressure for the ESP controls.
Noise and vibration that driver feels when ESP system is operating
The ESP system may transfer noise and vibration to the driver due to the pressure changes
caused by the motor and valve operations in a very short period of time. And, keep in mind that
the output and vehicle speed could be decreased without rpm increase due to the ASR function
that controls the engine power. -
-
-
ARP Operation
During the ARP operation, vehicle safety (rollover prevention) takes the first priority and thus,
stronger engine control is in effect. Consequently, the vehicle speed decreases rapidly, so the
driver must take caution for the vehicle may drift away from the lane. -
Page 661 of 796
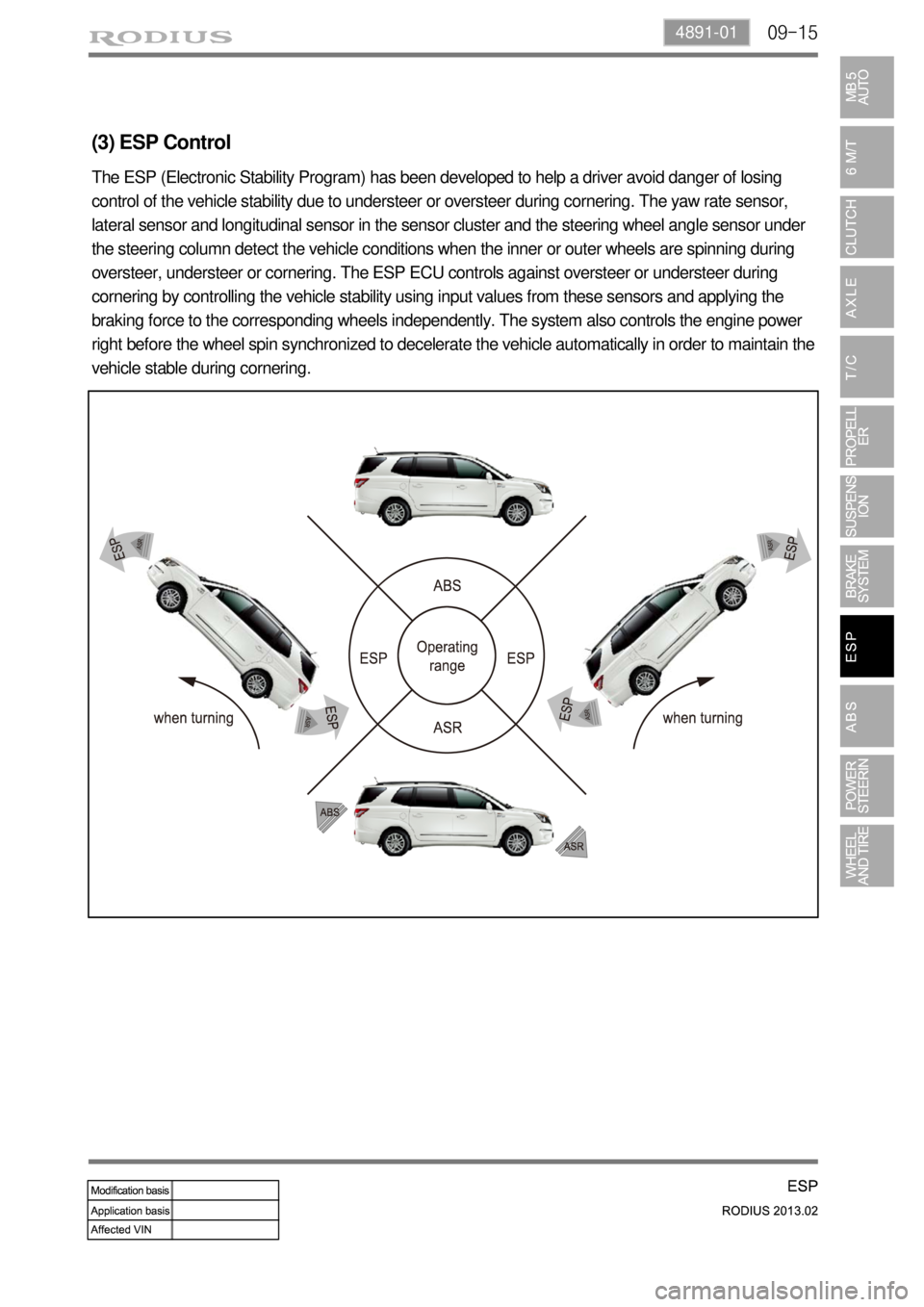
09-154891-01
(3) ESP Control
The ESP (Electronic Stability Program) has been developed to help a driver avoid danger of losing
control of the vehicle stability due to understeer or oversteer during cornering. The yaw rate sensor,
lateral sensor and longitudinal sensor in the sensor cluster and the steering wheel angle sensor under
the steering column detect the vehicle conditions when the inner or outer wheels are spinning during
oversteer, understeer or cornering. The ESP ECU controls against oversteer or understeer during
cornering by controlling the vehicle stability using input values from these sensors and applying the
braking force to the corresponding wheels independently. The system also controls the engine power
right before the wheel spin synchronized to decelerate the vehicle automatically in order to maintain the
vehicle stable during cornering.
Page 665 of 796
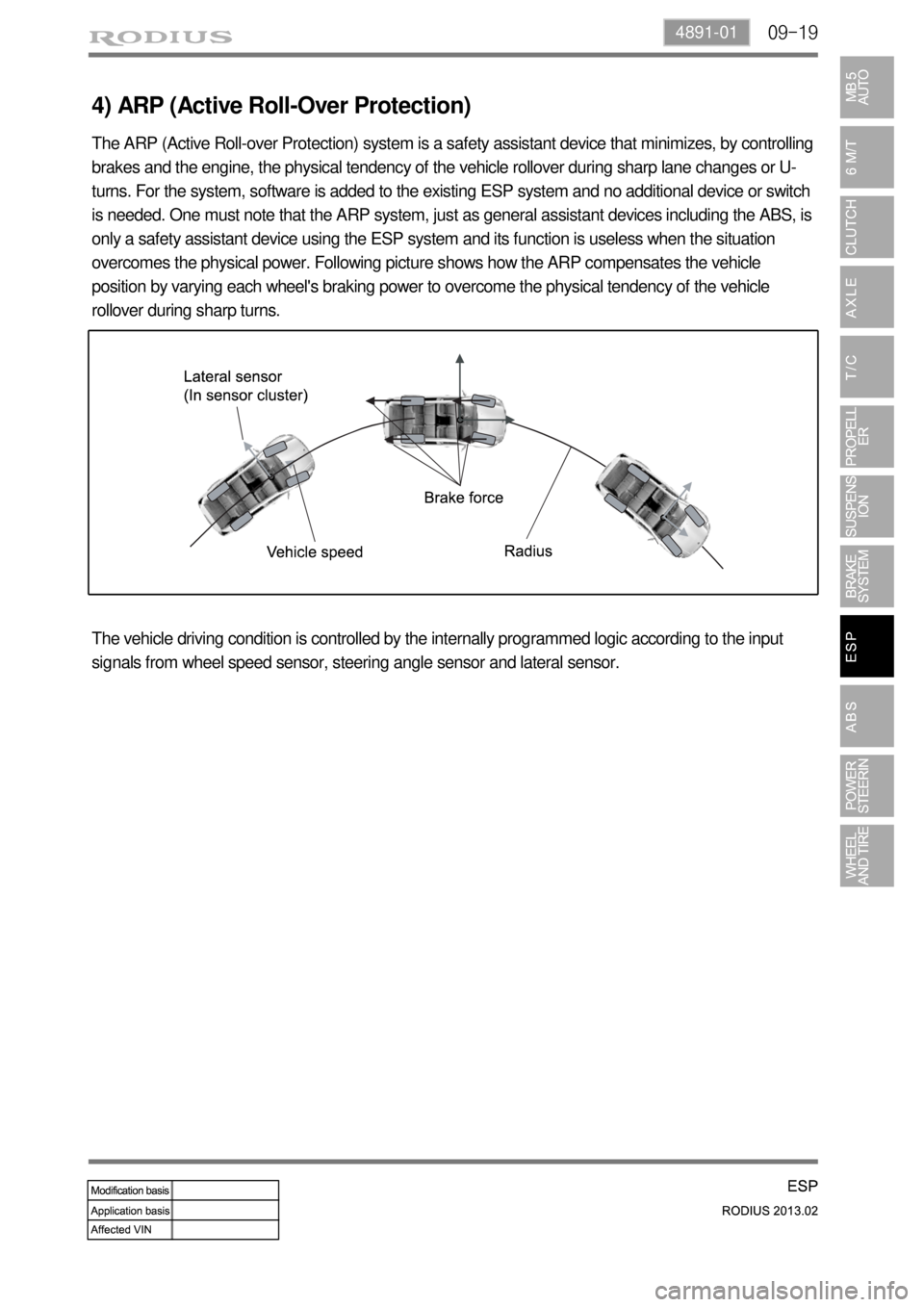
09-194891-01
4) ARP (Active Roll-Over Protection)
The ARP (Active Roll-over Protection) system is a safety assistant device that minimizes, by controlling
brakes and the engine, the physical tendency of the vehicle rollover during sharp lane changes or U-
turns. For the system, software is added to the existing ESP system and no additional device or switch
is needed. One must note that the ARP system, just as general assistant devices including the ABS, is
only a safety assistant device using the ESP system and its function is useless when the situation
overcomes the physical power. Following picture shows how the ARP compensates the vehicle
position by varying each wheel's braking power to overcome the physical tendency of the vehicle
rollover during sharp turns.
The vehicle driving condition is controlled by the internally programmed logic according to the input
signals from wheel speed sensor, steering angle sensor and lateral sensor.
Page 666 of 796
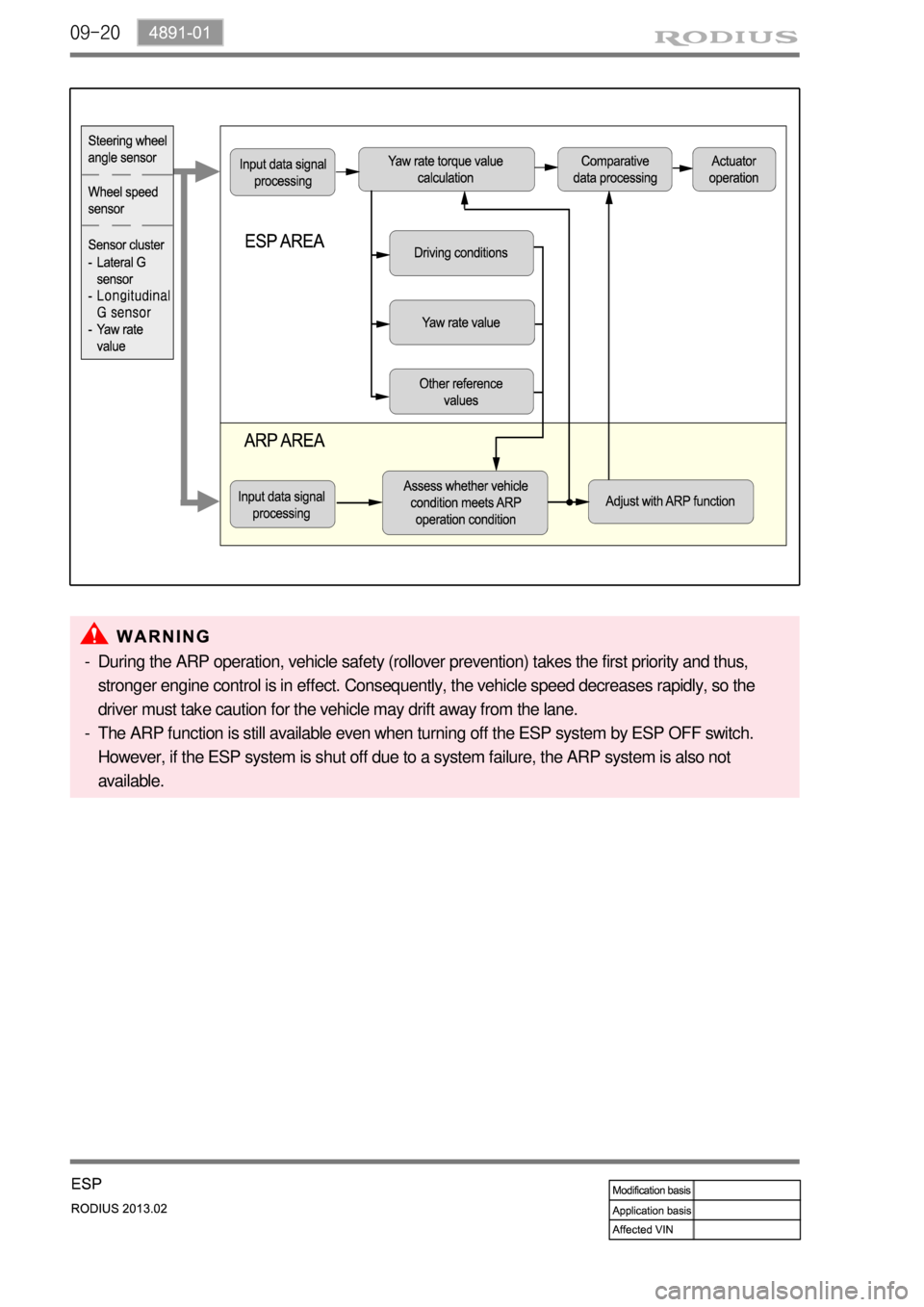
09-20
During the ARP operation, vehicle safety (rollover prevention) takes the first priority and thus,
stronger engine control is in effect. Consequently, the vehicle speed decreases rapidly, so the
driver must take caution for the vehicle may drift away from the lane.
The ARP function is still available even when turning off the ESP system by ESP OFF switch.
However, if the ESP system is shut off due to a system failure, the ARP system is also not
available. -
-
Page 667 of 796
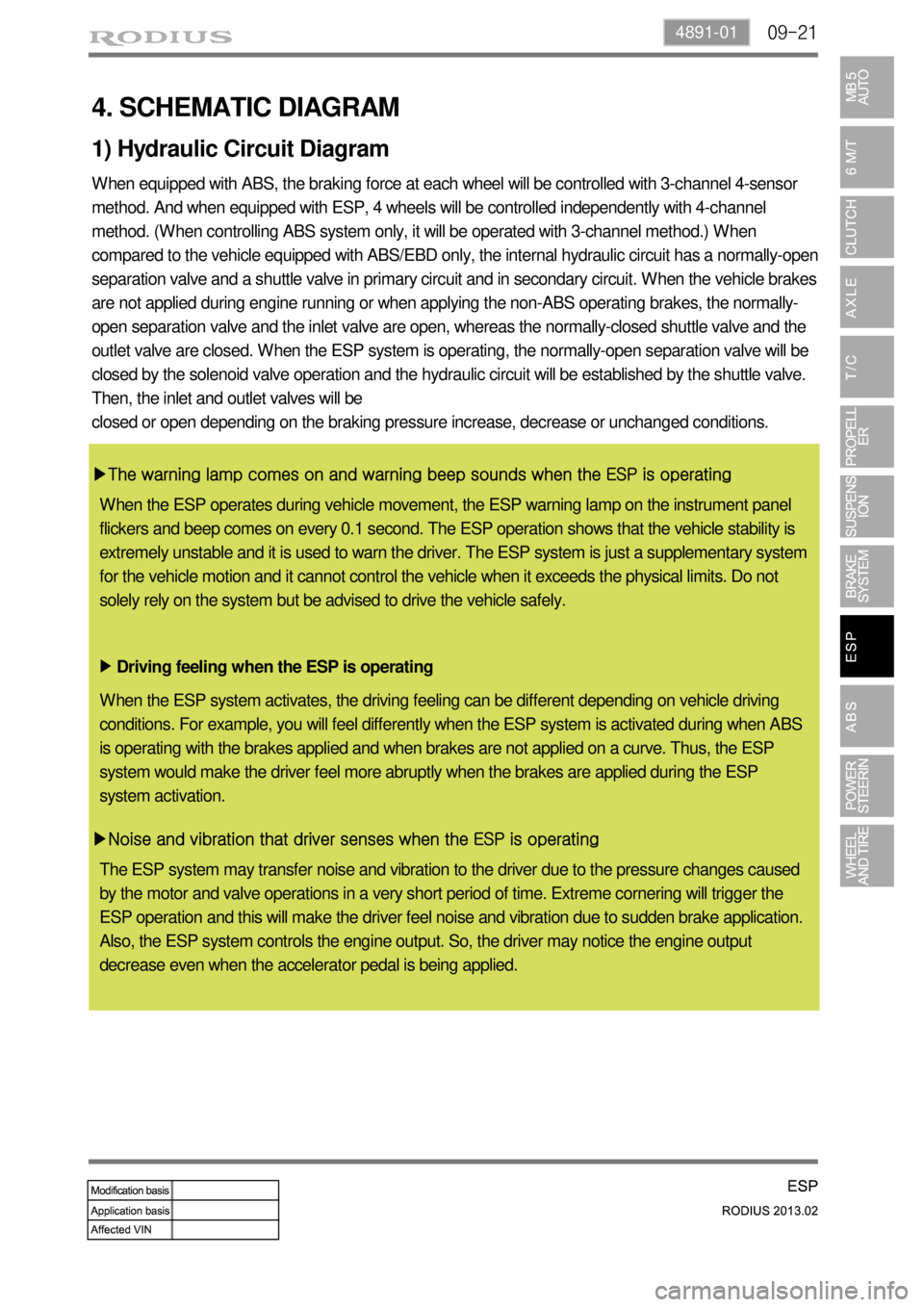
09-214891-01
4. SCHEMATIC DIAGRAM
When equipped with ABS, the braking force at each wheel will be controlled with 3-channel 4-sensor
method. And when equipped with ESP, 4 wheels will be controlled independently with 4-channel
method. (When controlling ABS system only, it will be operated with 3-channel method.) When
compared to the vehicle equipped with ABS/EBD only, the internal hydraulic circuit has a normally-open
separation valve and a shuttle valve in primary circuit and in secondary circuit. When the vehicle brakes
are not applied during engine running or when applying the non-ABS operating brakes, the normally-
open separation valve and the inlet valve are open, whereas the normally-closed shuttle valve and the
outlet valve are closed. When the ESP system is operating, the normally-open separation valve will be
closed by the solenoid valve operation and the hydraulic circuit will be established by the shuttle valve.
Then, the inlet and outlet valves will be
closed or open depending on the braking pressure increase, decrease or unchanged conditions.
▶The warning lamp comes on and warning beep sounds when the ESP is operating
Driving feeling when the ESP is operating ▶
▶Noise and vibration that driver senses when the ESP is operating
1) Hydraulic Circuit Diagram
When the ESP operates during vehicle movement, the ESP warning lamp on the instrument panel
flickers and beep comes on every 0.1 second. The ESP operation shows that the vehicle stability is
extremely unstable and it is used to warn the driver. The ESP system is just a supplementary system
for the vehicle motion and it cannot control the vehicle when it exceeds the physical limits. Do not
solely rely on the system but be advised to drive the vehicle safely.
When the ESP system activates, the driving feeling can be different depending on vehicle driving
conditions. For example, you will feel differently when the ESP system is activated during when ABS
is operating with the brakes applied and when brakes are not applied on a curve. Thus, the ESP
system would make the driver feel more abruptly when the brakes are applied during the ESP
system activation.
The ESP system may transfer noise and vibration to the driver due to the pressure changes caused
by the motor and valve operations in a very short period of time. Extreme cornering will trigger the
ESP operation and this will make the driver feel noise and vibration due to sudden brake application.
Also, the ESP system controls the engine output. So, the driver may notice the engine output
decrease even when the accelerator pedal is being applied.
Page 668 of 796
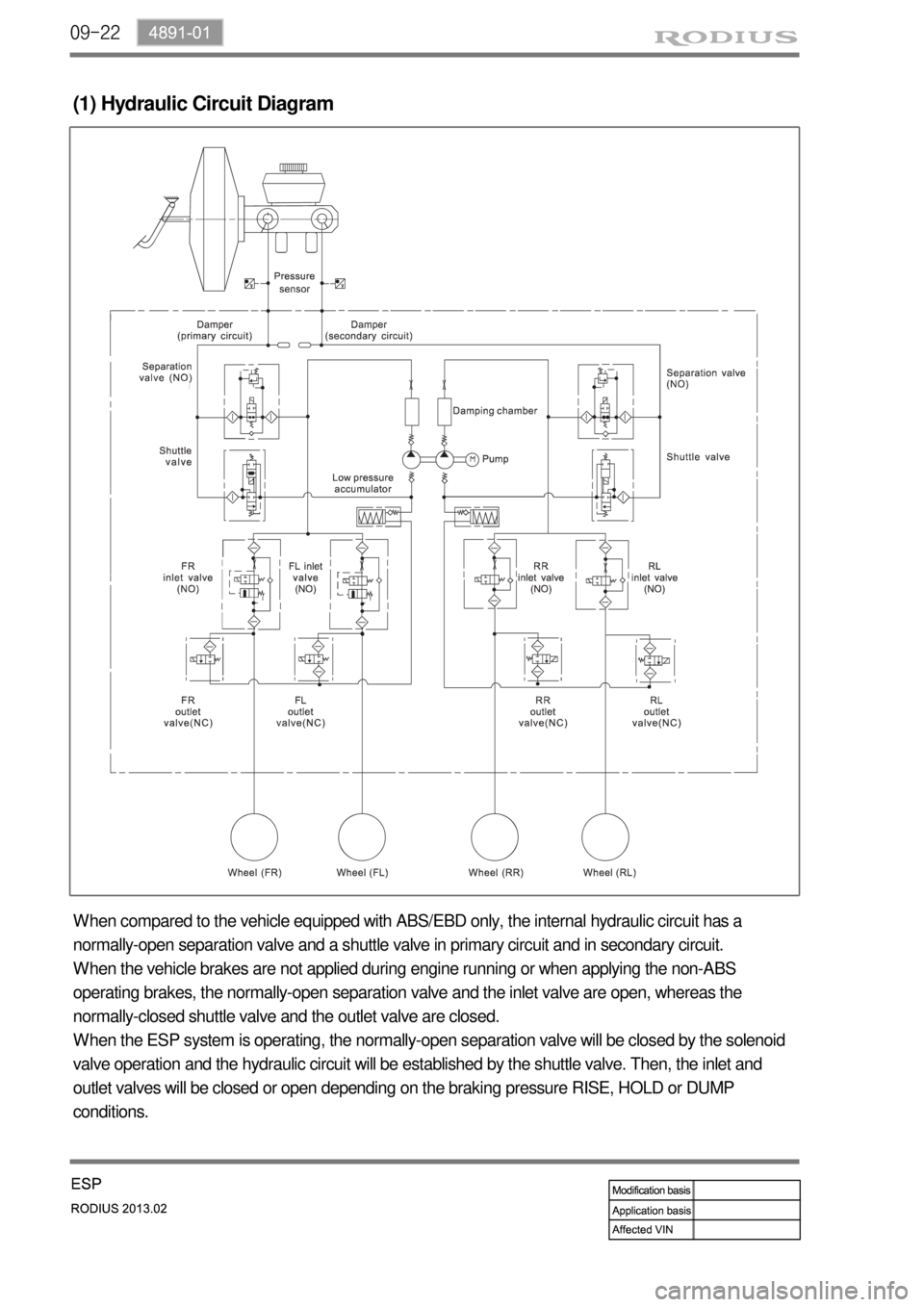
09-22
(1) Hydraulic Circuit Diagram
When compared to the vehicle equipped with ABS/EBD only, the internal hydraulic circuit has a
normally-open separation valve and a shuttle valve in primary circuit and in secondary circuit.
When the vehicle brakes are not applied during engine running or when applying the non-ABS
operating brakes, the normally-open separation valve and the inlet valve are open, whereas the
normally-closed shuttle valve and the outlet valve are closed.
When the ESP system is operating, the normally-open separation valve will be closed by the solenoid
valve operation and the hydraulic circuit will be established by the shuttle valve. Then, the inlet and
outlet valves will be closed or open depending on the braking pressure RISE, HOLD or DUMP
conditions.
Page 690 of 796
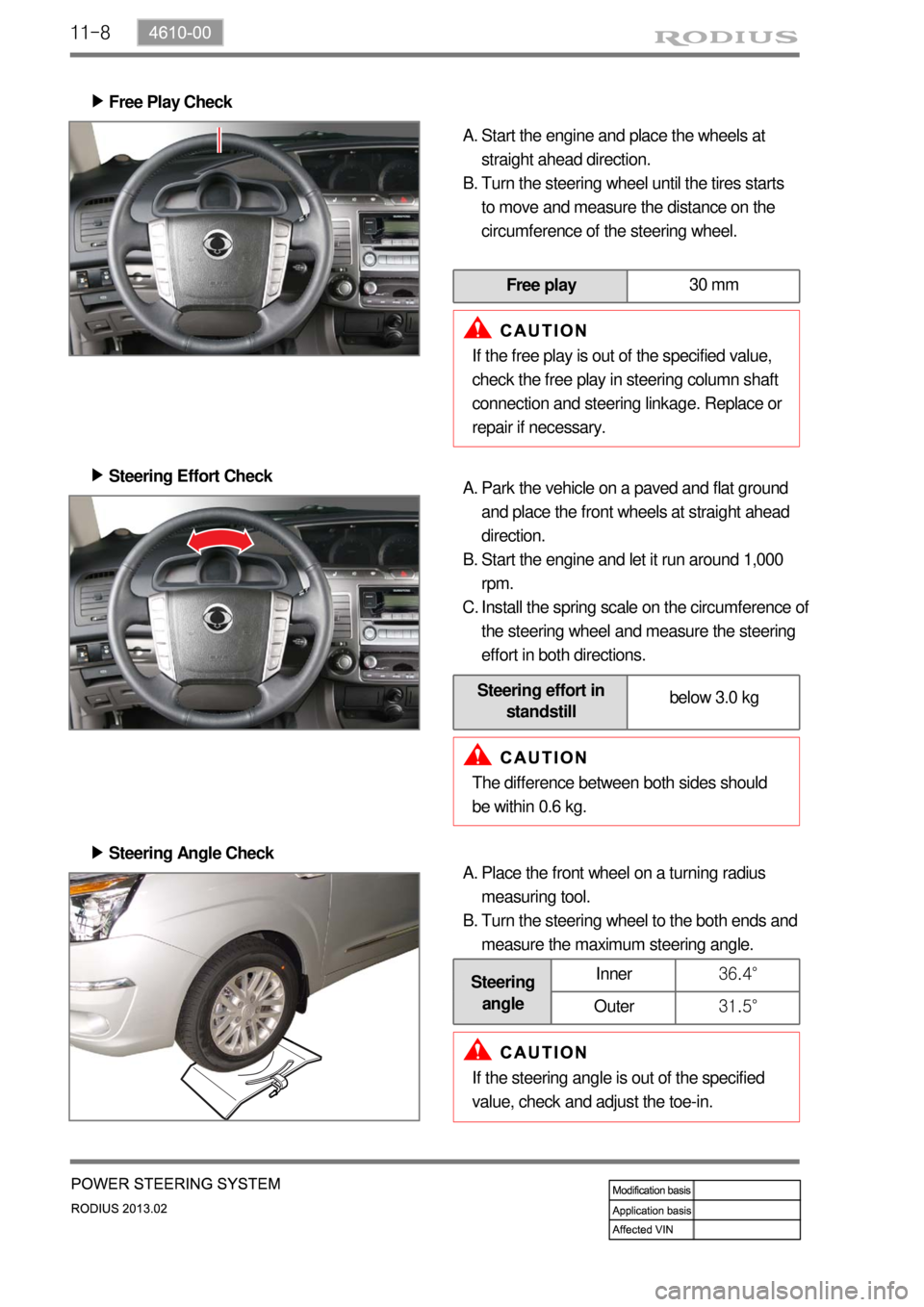
11-8
Free Play Check ▶
Start the engine and place the wheels at
straight ahead direction.
Turn the steering wheel until the tires starts
to move and measure the distance on the
circumference of the steering wheel. A.
B.
Free play30 mm
If the free play is out of the specified value,
check the free play in steering column shaft
connection and steering linkage. Replace or
repair if necessary.
Steering Effort Check ▶
Park the vehicle on a paved and flat ground
and place the front wheels at straight ahead
direction.
Start the engine and let it run around 1,000
rpm.
Install the spring scale on the circumference of
the steering wheel and measure the steering
effort in both directions. A.
B.
C.
Steering effort in
standstillbelow 3.0 kg
The difference between both sides should
be within 0.6 kg.
Steering Angle Check ▶
Place the front wheel on a turning radius
measuring tool.
Turn the steering wheel to the both ends and
measure the maximum steering angle. A.
B.
Steering
angleInner36.4°
Outer31.5°
If the steering angle is out of the specified
value, check and adjust the toe-in.
Page 691 of 796
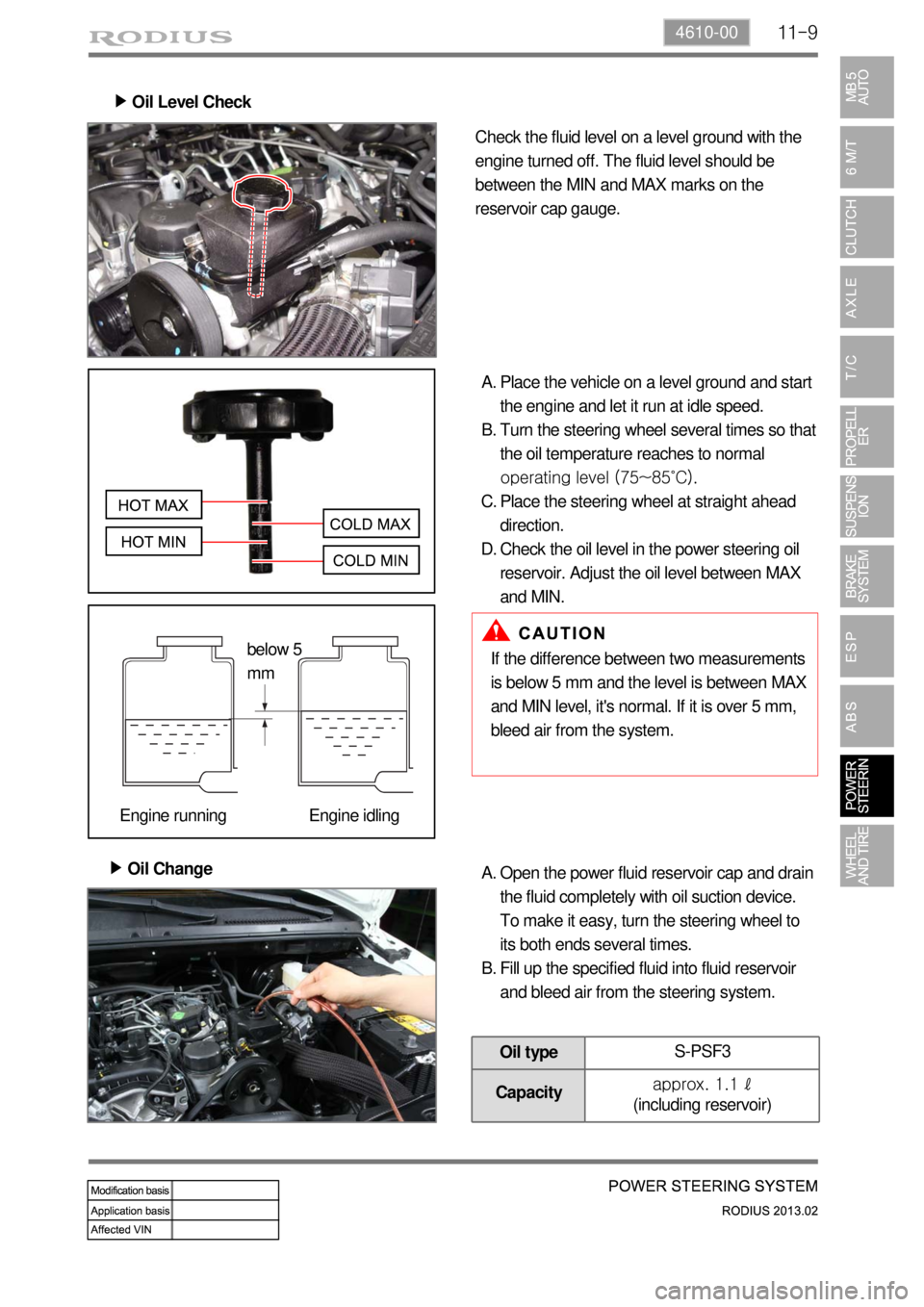
11-94610-00
Oil Level Check ▶
Check the fluid level on a level ground with the
engine turned off. The fluid level should be
between the MIN and MAX marks on the
reservoir cap gauge.
Place the vehicle on a level ground and start
the engine and let it run at idle speed.
Turn the steering wheel several times so that
the oil temperature reaches to normal
operating level (75~85˚C).
Place the steering wheel at straight ahead
direction.
Check the oil level in the power steering oil
reservoir. Adjust the oil level between MAX
and MIN. A.
B.
C.
D.
Oil Change ▶
If the difference between two measurements
is below 5 mm and the level is between MAX
and MIN level, it's normal. If it is over 5 mm,
bleed air from the system.
Open the power fluid reservoir cap and drain
the fluid completely with oil suction device.
To make it easy, turn the steering wheel to
its both ends several times.
Fill up the specified fluid into fluid reservoir
and bleed air from the steering system. A.
B.
Oil typeS-PSF3
Capacityapprox. 1.1 ℓ
(including reservoir)
below 5
mm
Engine running Engine idling