SUZUKI GRAND VITARA 1999 2.G Owners Manual
Manufacturer: SUZUKI, Model Year: 1999, Model line: GRAND VITARA, Model: SUZUKI GRAND VITARA 1999 2.GPages: 656, PDF Size: 14.31 MB
Page 401 of 656
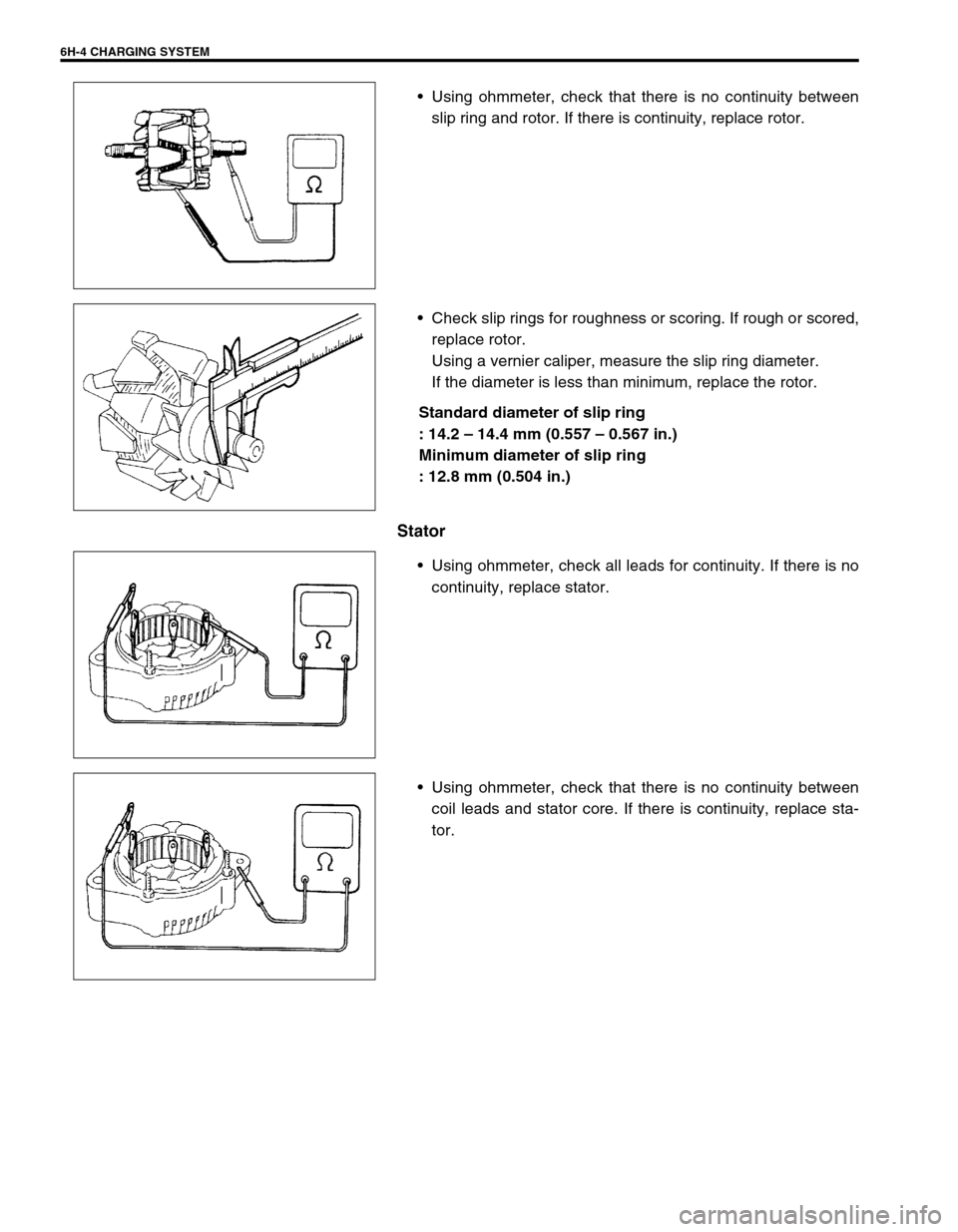
6H-4 CHARGING SYSTEM
•Using ohmmeter, check that there is no continuity between
slip ring and rotor. If there is continuity, replace rotor.
•Check slip rings for roughness or scoring. If rough or scored,
replace rotor.
Using a vernier caliper, measure the slip ring diameter.
If the diameter is less than minimum, replace the rotor.
Standard diameter of slip ring
: 14.2 – 14.4 mm (0.557 – 0.567 in.)
Minimum diameter of slip ring
: 12.8 mm (0.504 in.)
Stator
•Using ohmmeter, check all leads for continuity. If there is no
continuity, replace stator.
•Using ohmmeter, check that there is no continuity between
coil leads and stator core. If there is continuity, replace sta-
tor.
Page 402 of 656
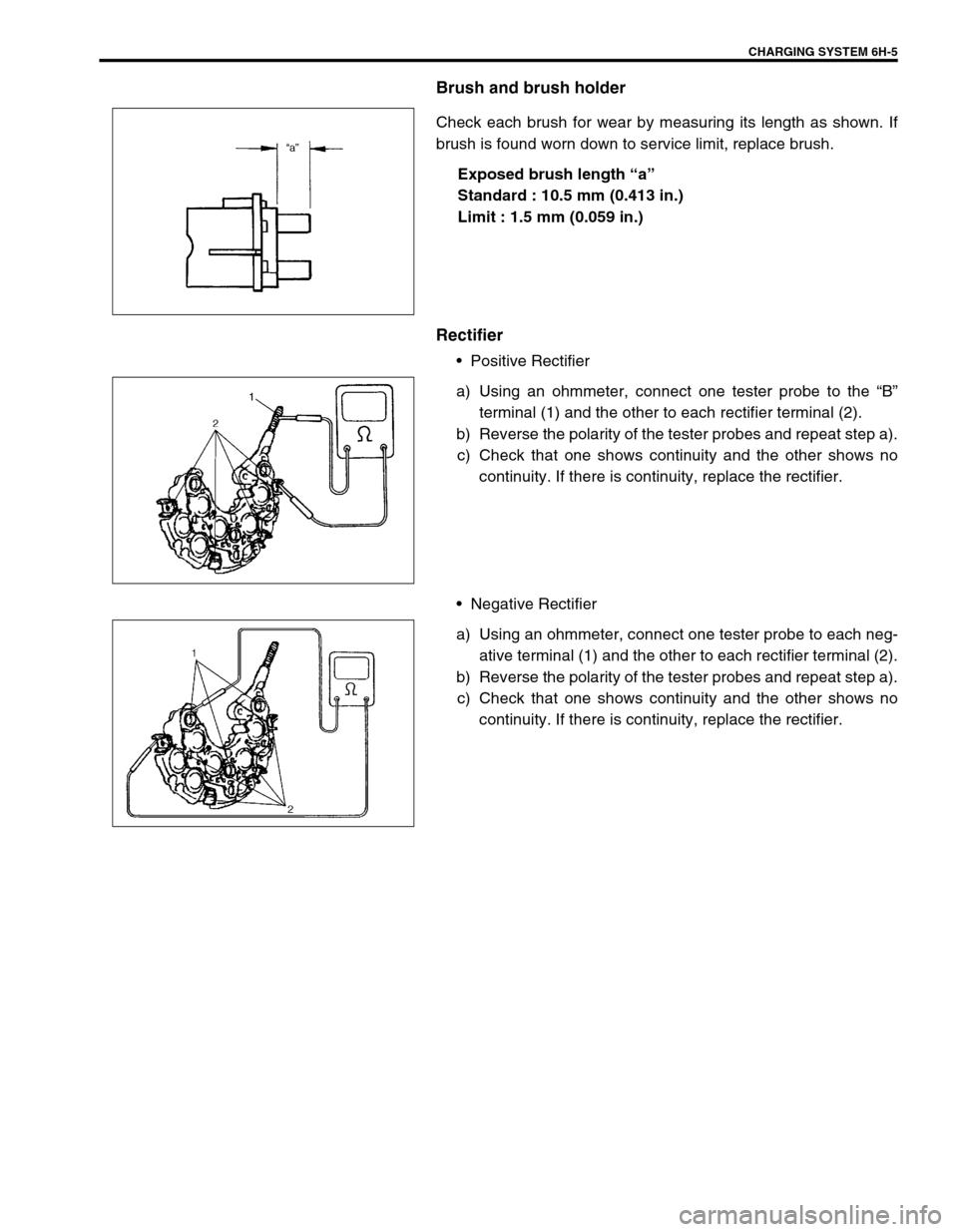
CHARGING SYSTEM 6H-5
Brush and brush holder
Check each brush for wear by measuring its length as shown. If
brush is found worn down to service limit, replace brush.
Exposed brush length “a”
Standard : 10.5 mm (0.413 in.)
Limit : 1.5 mm (0.059 in.)
Rectifier
•Positive Rectifier
a) Using an ohmmeter, connect one tester probe to the “B”
terminal (1) and the other to each rectifier terminal (2).
b) Reverse the polarity of the tester probes and repeat step a).
c) Check that one shows continuity and the other shows no
continuity. If there is continuity, replace the rectifier.
•Negative Rectifier
a) Using an ohmmeter, connect one tester probe to each neg-
ative terminal (1) and the other to each rectifier terminal (2).
b) Reverse the polarity of the tester probes and repeat step a).
c) Check that one shows continuity and the other shows no
continuity. If there is continuity, replace the rectifier.
Page 403 of 656
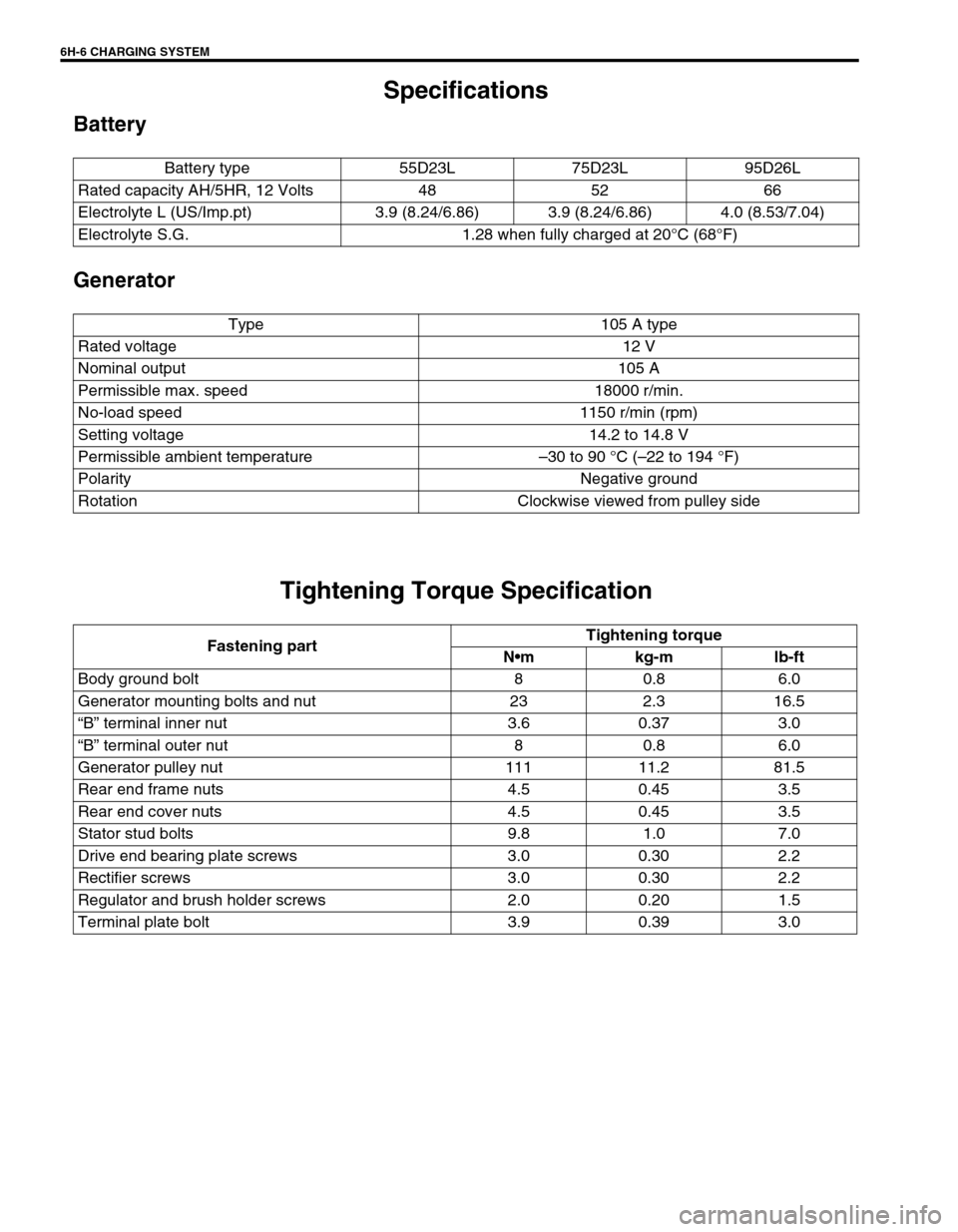
6H-6 CHARGING SYSTEM
Specifications
Battery
Generator
Tightening Torque Specification
Battery type 55D23L 75D23L 95D26L
Rated capacity AH/5HR, 12 Volts 48 52 66
Electrolyte L (US/Imp.pt) 3.9 (8.24/6.86) 3.9 (8.24/6.86) 4.0 (8.53/7.04)
Electrolyte S.G. 1.28 when fully charged at 20°C (68°F)
Type 105 A type
Rated voltage 12 V
Nominal output 105 A
Permissible max. speed 18000 r/min.
No-load speed 1150 r/min (rpm)
Setting voltage 14.2 to 14.8 V
Permissible ambient temperature–30 to 90 °C (–22 to 194 °F)
Polarity Negative ground
Rotation Clockwise viewed from pulley side
Fastening partTightening torque
Nm kg-m lb-ft
Body ground bolt 8 0.8 6.0
Generator mounting bolts and nut 23 2.3 16.5
“B” terminal inner nut 3.6 0.37 3.0
“B” terminal outer nut 8 0.8 6.0
Generator pulley nut 111 11.2 81.5
Rear end frame nuts 4.5 0.45 3.5
Rear end cover nuts 4.5 0.45 3.5
Stator stud bolts 9.8 1.0 7.0
Drive end bearing plate screws 3.0 0.30 2.2
Rectifier screws 3.0 0.30 2.2
Regulator and brush holder screws 2.0 0.20 1.5
Terminal plate bolt 3.9 0.39 3.0
Page 404 of 656
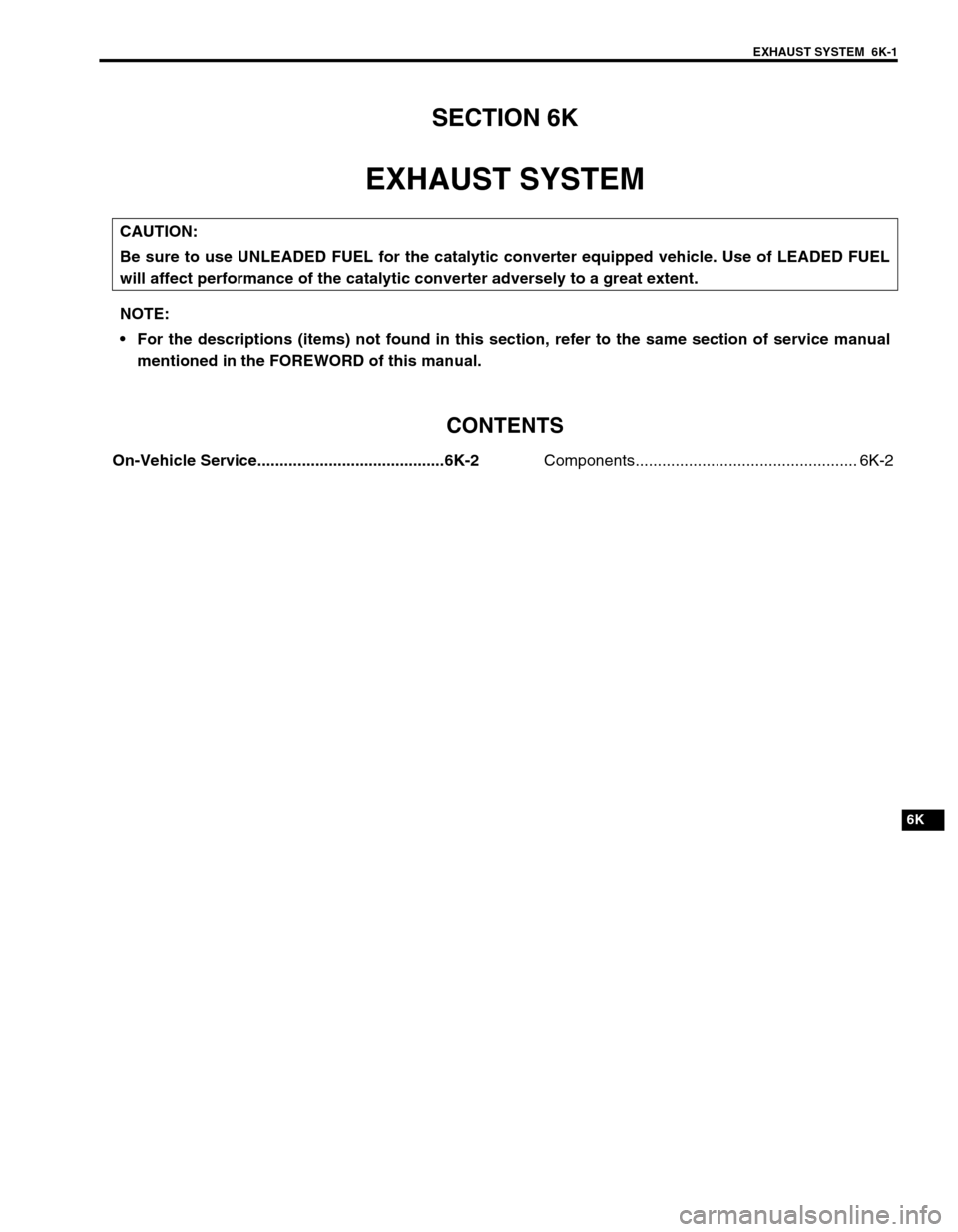
EXHAUST SYSTEM 6K-1
6K
SECTION 6K
EXHAUST SYSTEM
CONTENTS
On-Vehicle Service..........................................6K-2Components.................................................. 6K-2
CAUTION:
Be sure to use UNLEADED FUEL for the catalytic converter equipped vehicle. Use of LEADED FUEL
will affect performance of the catalytic converter adversely to a great extent.
NOTE:
For the descriptions (items) not found in this section, refer to the same section of service manual
mentioned in the FOREWORD of this manual.
Page 405 of 656
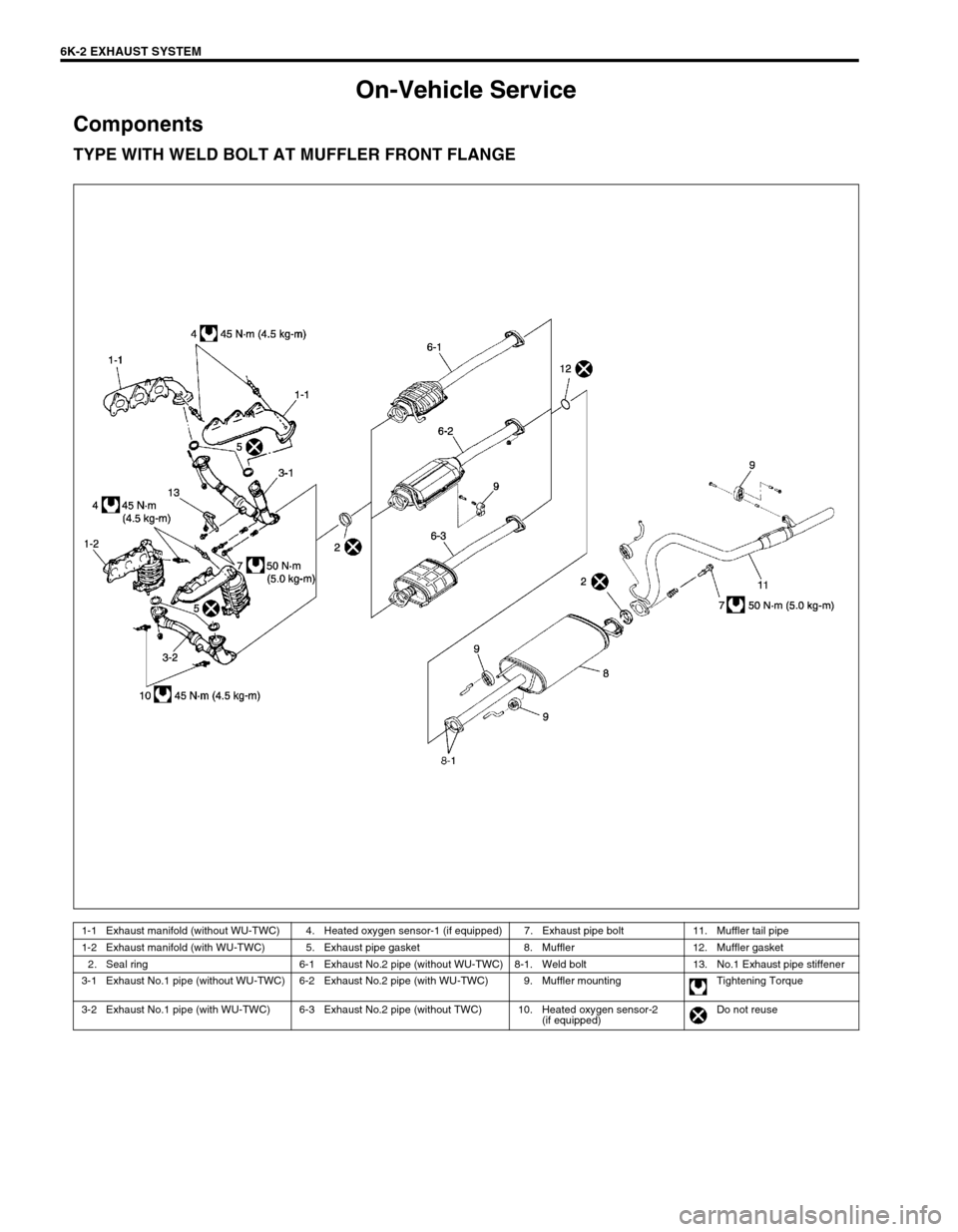
6K-2 EXHAUST SYSTEM
On-Vehicle Service
Components
TYPE WITH WELD BOLT AT MUFFLER FRONT FLANGE
1-1 Exhaust manifold (without WU-TWC) 4. Heated oxygen sensor-1 (if equipped) 7. Exhaust pipe bolt 11. Muffler tail pipe
1-2 Exhaust manifold (with WU-TWC) 5. Exhaust pipe gasket 8. Muffler 12. Muffler gasket
2. Seal ring 6-1 Exhaust No.2 pipe (without WU-TWC) 8-1. Weld bolt 13. No.1 Exhaust pipe stiffener
3-1 Exhaust No.1 pipe (without WU-TWC) 6-2 Exhaust No.2 pipe (with WU-TWC) 9. Muffler mounting Tightening Torque
3-2 Exhaust No.1 pipe (with WU-TWC) 6-3 Exhaust No.2 pipe (without TWC) 10. Heated oxygen sensor-2
(if equipped)Do not reuse
Page 406 of 656
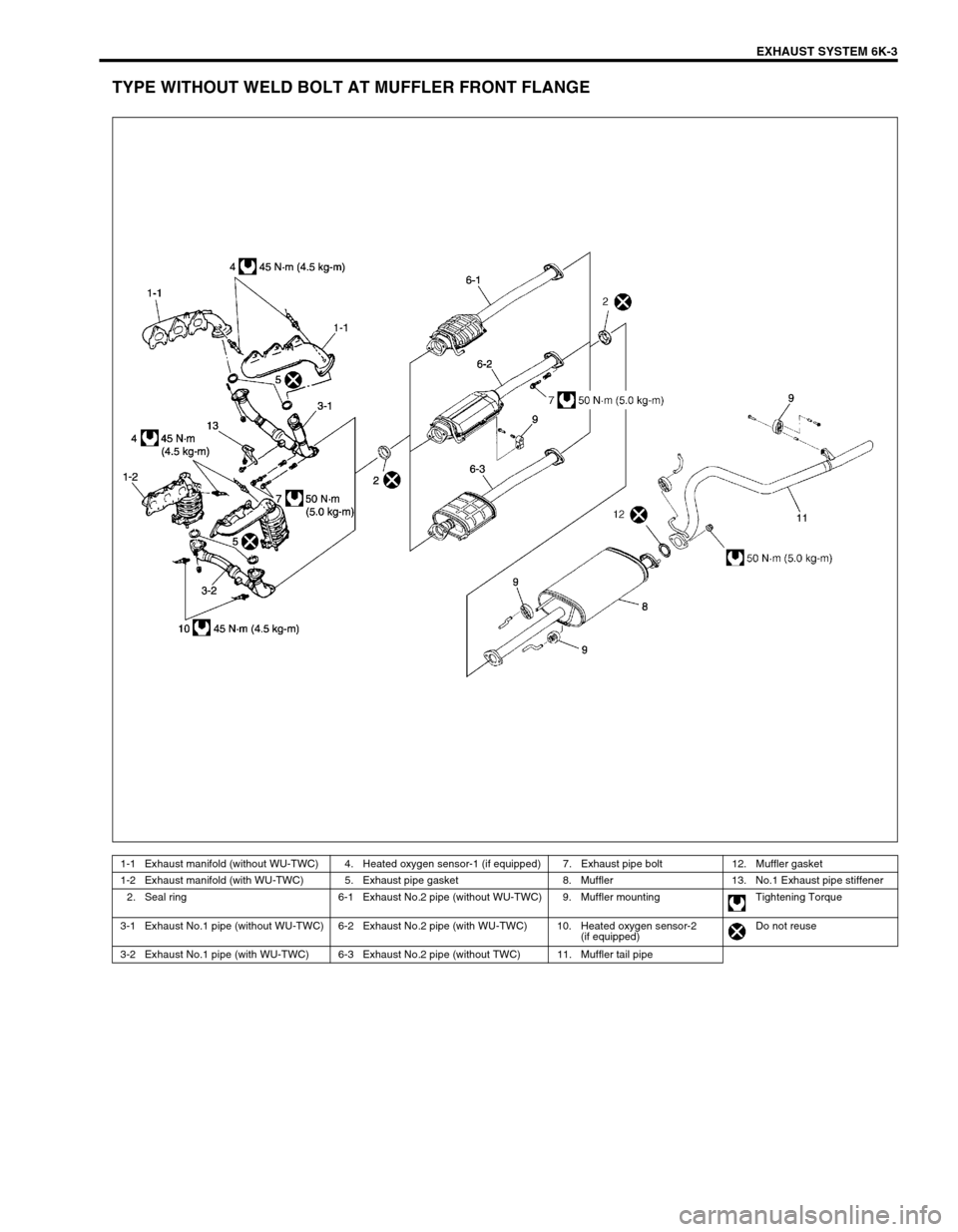
EXHAUST SYSTEM 6K-3
TYPE WITHOUT WELD BOLT AT MUFFLER FRONT FLANGE
1-1 Exhaust manifold (without WU-TWC) 4. Heated oxygen sensor-1 (if equipped) 7. Exhaust pipe bolt 12. Muffler gasket
1-2 Exhaust manifold (with WU-TWC) 5. Exhaust pipe gasket 8. Muffler 13. No.1 Exhaust pipe stiffener
2. Seal ring 6-1 Exhaust No.2 pipe (without WU-TWC) 9. Muffler mounting Tightening Torque
3-1 Exhaust No.1 pipe (without WU-TWC) 6-2 Exhaust No.2 pipe (with WU-TWC) 10. Heated oxygen sensor-2
(if equipped)Do not reuse
3-2 Exhaust No.1 pipe (with WU-TWC) 6-3 Exhaust No.2 pipe (without TWC) 11. Muffler tail pipe
Page 407 of 656
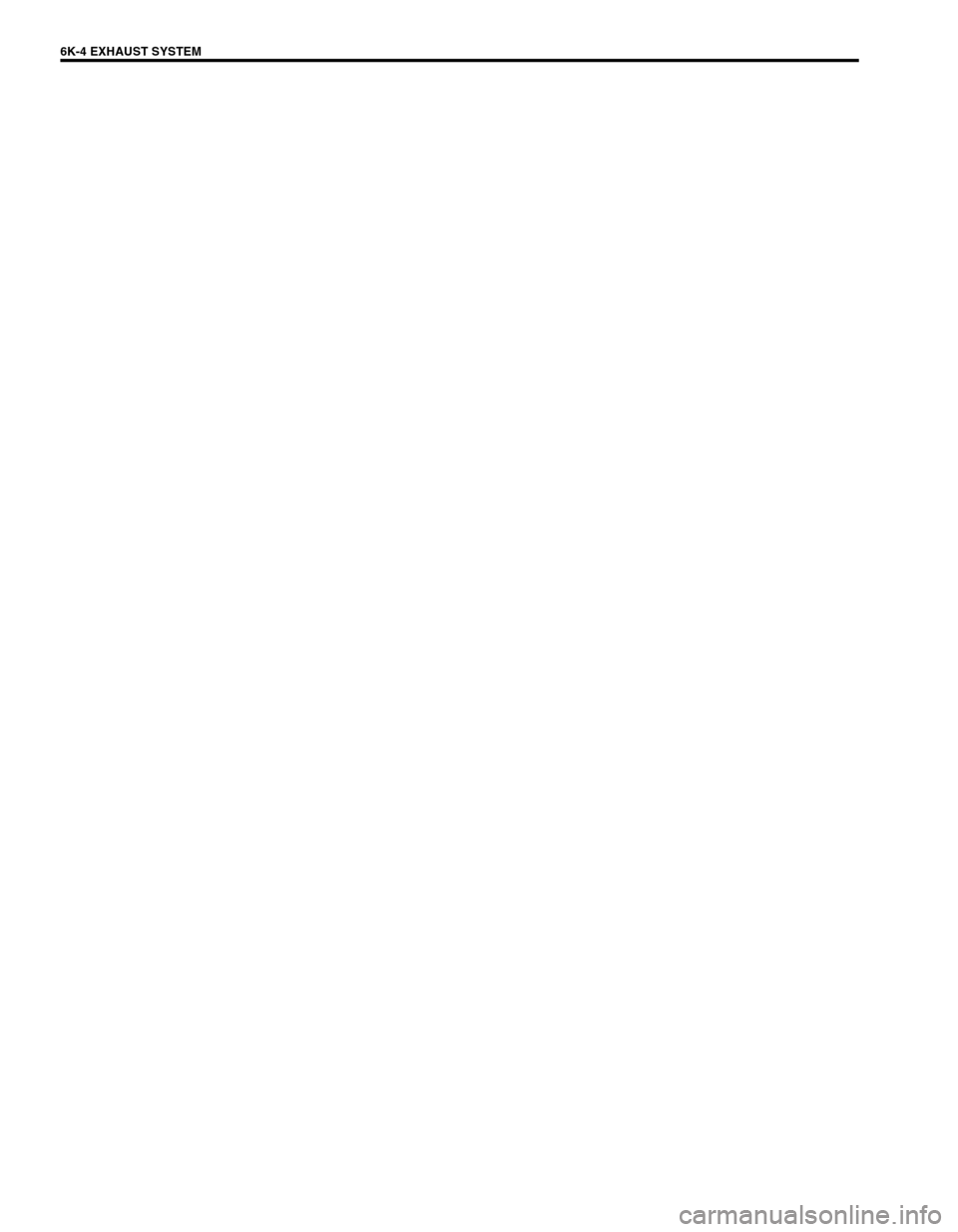
6K-4 EXHAUST SYSTEM
Page 408 of 656
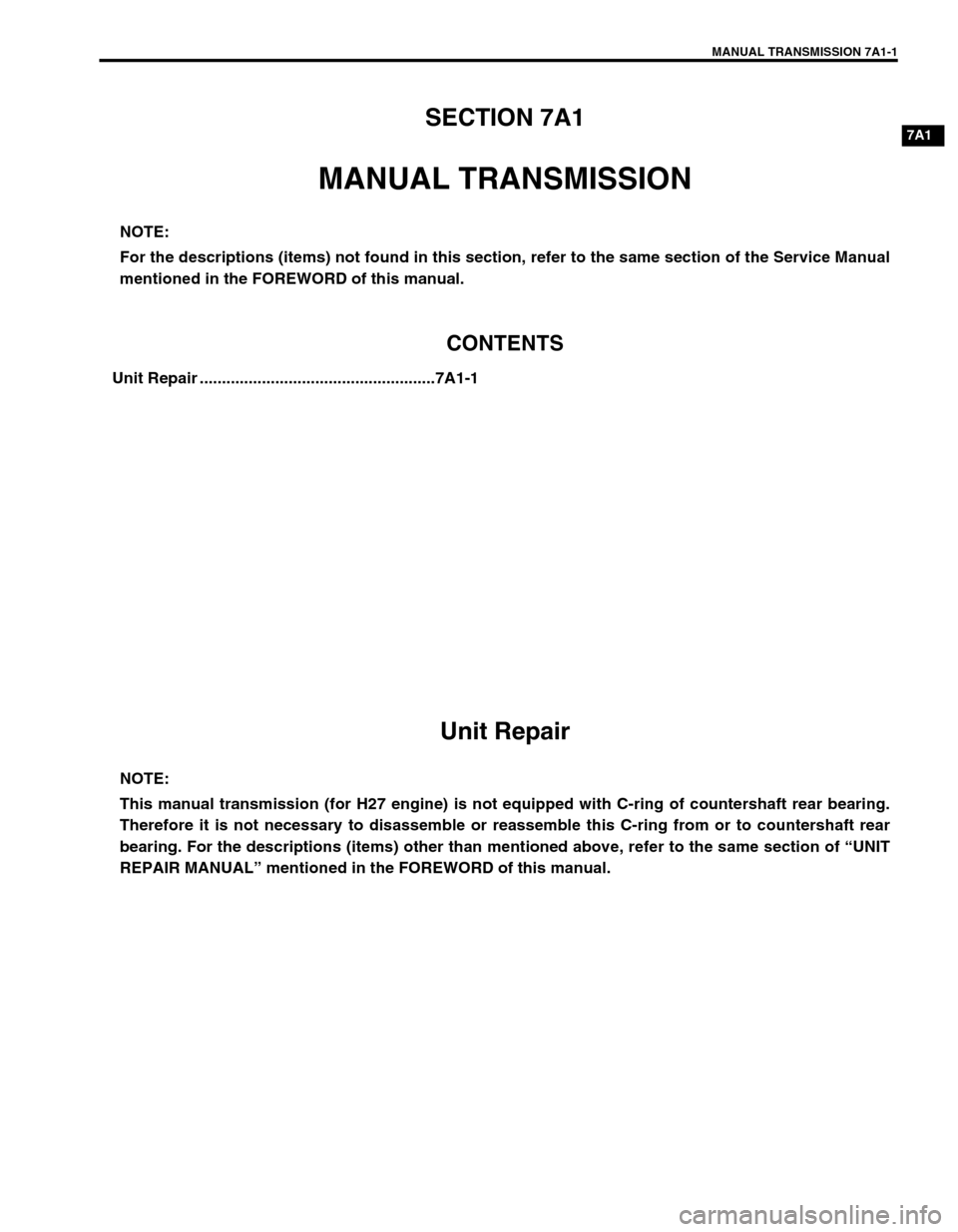
MANUAL TRANSMISSION 7A1-1
7A1SECTION 7A1
MANUAL TRANSMISSION
CONTENTS
Unit Repair .....................................................7A1-1
Unit Repair
NOTE:
For the descriptions (items) not found in this section, refer to the same section of the Service Manual
mentioned in the FOREWORD of this manual.
NOTE:
This manual transmission (for H27 engine) is not equipped with C-ring of countershaft rear bearing.
Therefore it is not necessary to disassemble or reassemble this C-ring from or to countershaft rear
bearing. For the descriptions (items) other than mentioned above, refer to the same section of “UNIT
REPAIR MANUAL” mentioned in the FOREWORD of this manual.
Page 409 of 656
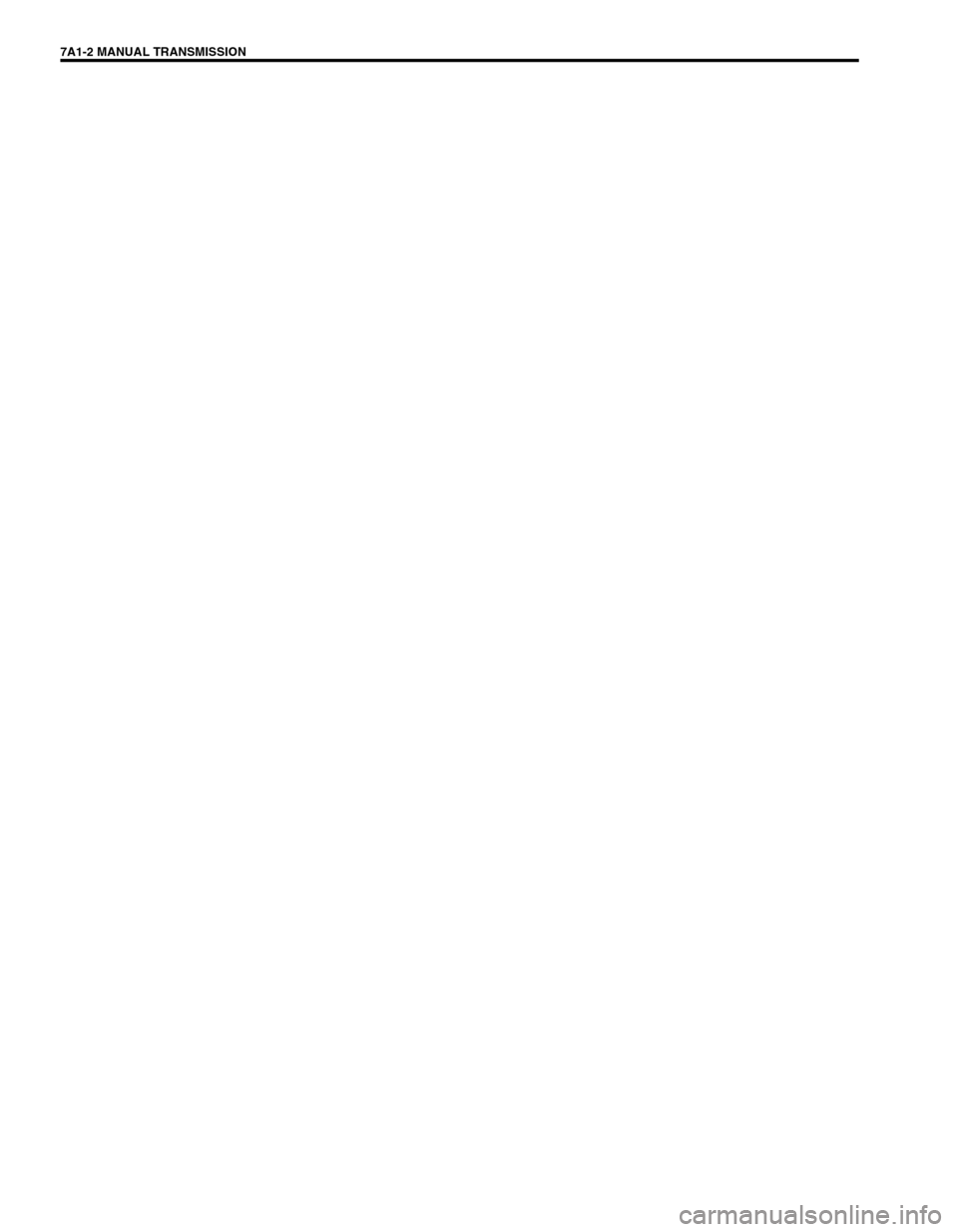
7A1-2 MANUAL TRANSMISSION
Page 410 of 656
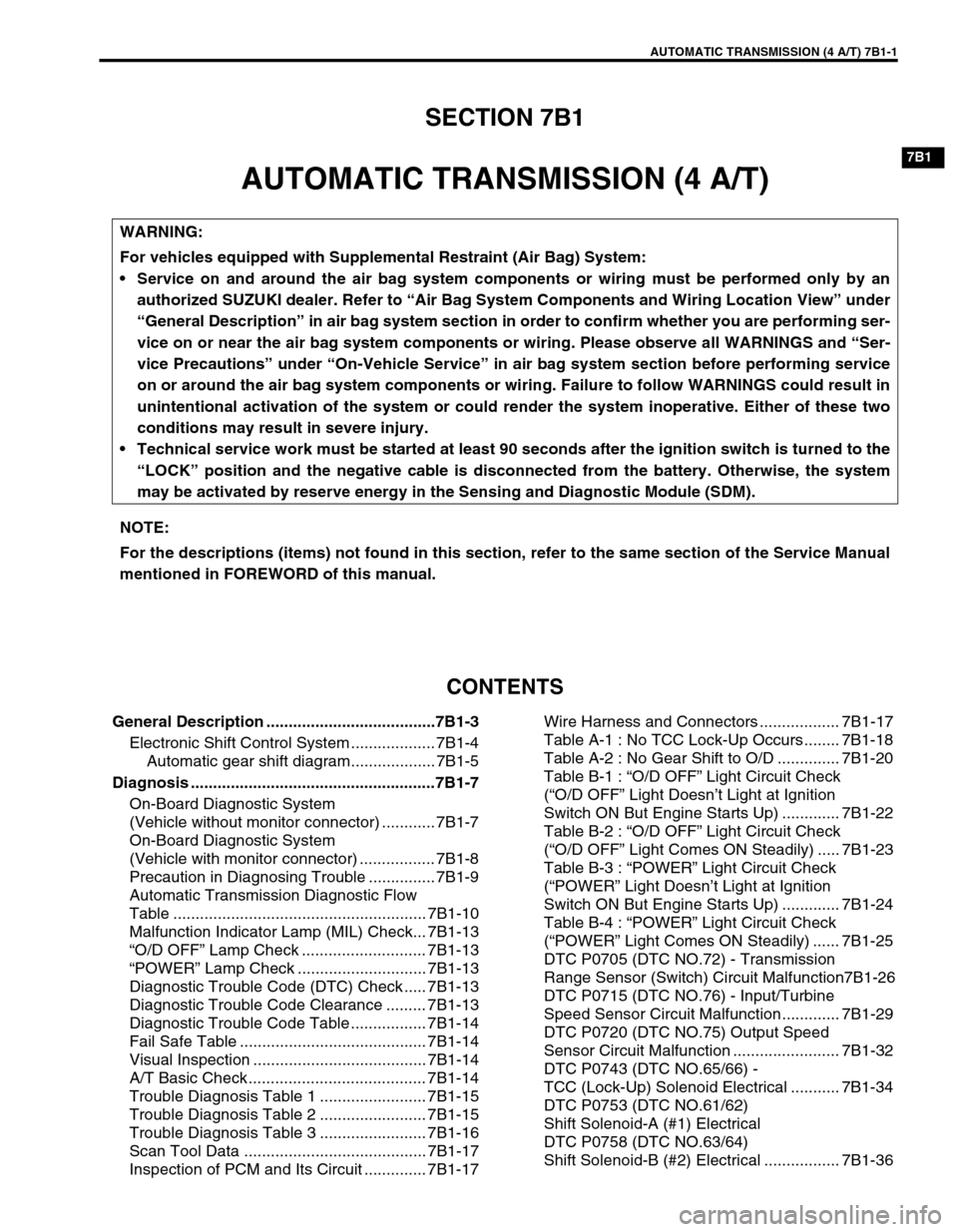
AUTOMATIC TRANSMISSION (4 A/T) 7B1-1
7B1
SECTION 7B1
AUTOMATIC TRANSMISSION (4 A/T)
CONTENTS
General Description ......................................7B1-3
Electronic Shift Control System ................... 7B1-4
Automatic gear shift diagram................... 7B1-5
Diagnosis .......................................................7B1-7
On-Board Diagnostic System
(Vehicle without monitor connector) ............ 7B1-7
On-Board Diagnostic System
(Vehicle with monitor connector) ................. 7B1-8
Precaution in Diagnosing Trouble ............... 7B1-9
Automatic Transmission Diagnostic Flow
Table ......................................................... 7B1-10
Malfunction Indicator Lamp (MIL) Check... 7B1-13
“O/D OFF” Lamp Check ............................ 7B1-13
“POWER” Lamp Check ............................. 7B1-13
Diagnostic Trouble Code (DTC) Check ..... 7B1-13
Diagnostic Trouble Code Clearance ......... 7B1-13
Diagnostic Trouble Code Table ................. 7B1-14
Fail Safe Table .......................................... 7B1-14
Visual Inspection ....................................... 7B1-14
A/T Basic Check ........................................ 7B1-14
Trouble Diagnosis Table 1 ........................ 7B1-15
Trouble Diagnosis Table 2 ........................ 7B1-15
Trouble Diagnosis Table 3 ........................ 7B1-16
Scan Tool Data ......................................... 7B1-17
Inspection of PCM and Its Circuit .............. 7B1-17Wire Harness and Connectors .................. 7B1-17
Table A-1 : No TCC Lock-Up Occurs ........ 7B1-18
Table A-2 : No Gear Shift to O/D .............. 7B1-20
Table B-1 : “O/D OFF” Light Circuit Check
(“O/D OFF” Light Doesn’t Light at Ignition
Switch ON But Engine Starts Up) ............. 7B1-22
Table B-2 : “O/D OFF” Light Circuit Check
(“O/D OFF” Light Comes ON Steadily) ..... 7B1-23
Table B-3 : “POWER” Light Circuit Check
(“POWER” Light Doesn’t Light at Ignition
Switch ON But Engine Starts Up) ............. 7B1-24
Table B-4 : “POWER” Light Circuit Check
(“POWER” Light Comes ON Steadily) ...... 7B1-25
DTC P0705 (DTC NO.72) - Transmission
Range Sensor (Switch) Circuit Malfunction7B1-26
DTC P0715 (DTC NO.76) - Input/Turbine
Speed Sensor Circuit Malfunction............. 7B1-29
DTC P0720 (DTC NO.75) Output Speed
Sensor Circuit Malfunction ........................ 7B1-32
DTC P0743 (DTC NO.65/66) -
TCC (Lock-Up) Solenoid Electrical ........... 7B1-34
DTC P0753 (DTC NO.61/62)
Shift Solenoid-A (#1) Electrical
DTC P0758 (DTC NO.63/64)
Shift Solenoid-B (#2) Electrical ................. 7B1-36 WARNING:
For vehicles equipped with Supplemental Restraint (Air Bag) System:
Service on and around the air bag system components or wiring must be performed only by an
authorized SUZUKI dealer. Refer to “Air Bag System Components and Wiring Location View” under
“General Description” in air bag system section in order to confirm whether you are performing ser-
vice on or near the air bag system components or wiring. Please observe all WARNINGS and “Ser-
vice Precautions” under “On-Vehicle Service” in air bag system section before performing service
on or around the air bag system components or wiring. Failure to follow WARNINGS could result in
unintentional activation of the system or could render the system inoperative. Either of these two
conditions may result in severe injury.
Technical service work must be started at least 90 seconds after the ignition switch is turned to the
“LOCK” position and the negative cable is disconnected from the battery. Otherwise, the system
may be activated by reserve energy in the Sensing and Diagnostic Module (SDM).
NOTE:
For the descriptions (items) not found in this section, refer to the same section of the Service Manual
mentioned in FOREWORD of this manual.