battery SUZUKI SWIFT 2000 1.G RG413 Service Manual Online
[x] Cancel search | Manufacturer: SUZUKI, Model Year: 2000, Model line: SWIFT, Model: SUZUKI SWIFT 2000 1.GPages: 698, PDF Size: 16.01 MB
Page 594 of 698
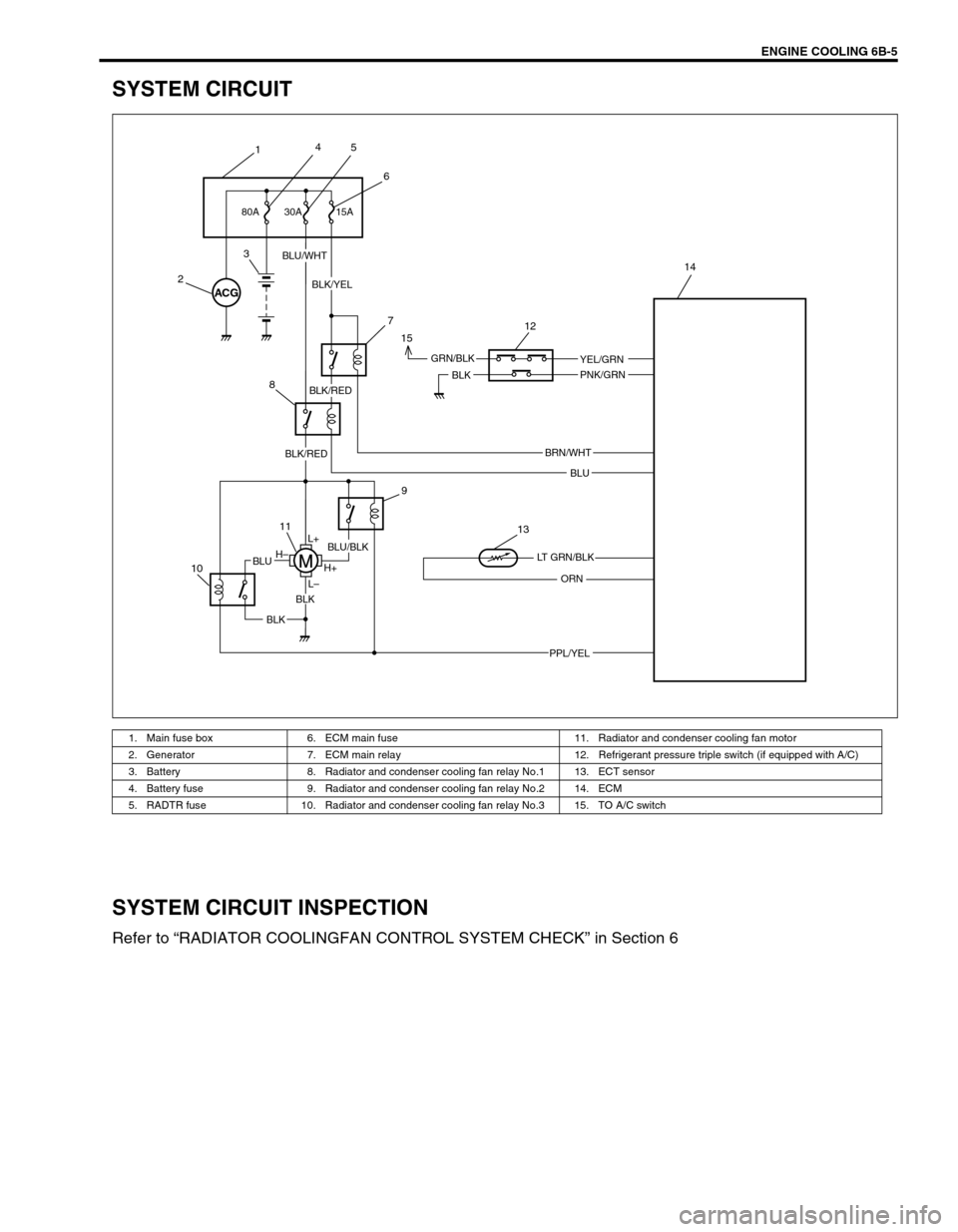
ENGINE COOLING 6B-5
SYSTEM CIRCUIT
SYSTEM CIRCUIT INSPECTION
Refer to “RADIATOR COOLINGFAN CONTROL SYSTEM CHECK” in Section 6
1. Main fuse box 6. ECM main fuse 11. Radiator and condenser cooling fan motor
2. Generator 7. ECM main relay 12. Refrigerant pressure triple switch (if equipped with A/C)
3. Battery 8. Radiator and condenser cooling fan relay No.1 13. ECT sensor
4. Battery fuse 9. Radiator and condenser cooling fan relay No.2 14. ECM
5. RADTR fuse 10. Radiator and condenser cooling fan relay No.3 15. TO A/C switch
ACG
15A 30A
BLU/WHT
BLK/YEL
BLK
BLU
ORN
BLK
BLK
BLUH–
H+
L– L+
GRN/BLK
BLU/BLK
BRN/WHT
YEL/GRN
PNK/GRN
PPL/YEL
LT GRN/BLK
BLK/RED
BLK/RED 80A
145
6
2
3
7
8
9
11
10
13 15
12
14
Page 598 of 698

ENGINE COOLING 6B-9
WATER PUMP/GENERATOR DRIVE BELT TENSION INSPECTION AND
ADJUSTMENT
1) Inspect belt for cracks, cuts, deformation, wear and cleanli-
ness. If it is necessary to replace belt, refer to “WATER
PUMP/GENERATOR DRIVE BELT” in this section.
2) Check belt for tension. Belt is in proper tension when it
deflects 4.5 to 5.5 mm (0.18 – 0.22 in.) under thumb pres-
sure (about 10 kg or 22 lb.).
Water pump / generator drive belt tension “a”
4.5 – 5.5 mm (0.18 – 0.22 in.) as deflection/10 kg (22 lbs)
3) If belt is too tight or too loose, adjust it to proper tension by
displacing generator position.
4) Tighten generator adjusting bolt and pivot bolts as specified
torque.
Tightening torque
Generator adjusting bolt (a) : 23 N·m (2.3 kg-m, 17.0 lb-ft)
Generator pivot bolt (b) : 50 N·m (5.0 kg-m, 36.0 lb-ft)
5) Connect negative cable at battery. WARNING:
Disconnect negative cable at battery before checking and adjusting belt tension.
To help avoid danger of being burned, do not remove radiator cap while engine and radiator are still
hot. Scalding fluid and steam can be blown out under pressure if cap is taken off too soon.
NOTE:
When replacing belt with a new one, adjust belt tension
to 3 – 4 mm (0.12 – 0.16 in.).
“a”
Page 599 of 698
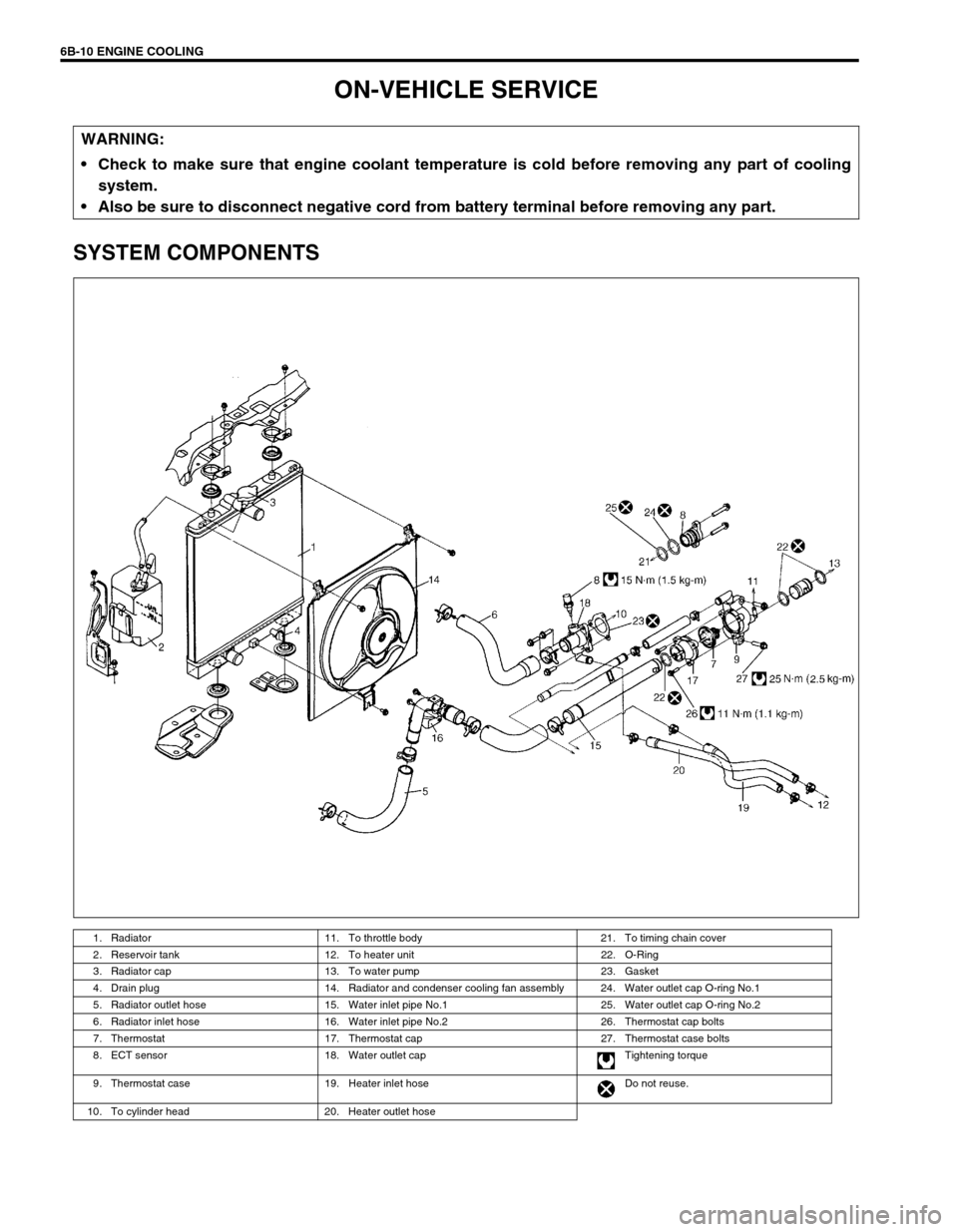
6B-10 ENGINE COOLING
ON-VEHICLE SERVICE
SYSTEM COMPONENTS
WARNING:
Check to make sure that engine coolant temperature is cold before removing any part of cooling
system.
Also be sure to disconnect negative cord from battery terminal before removing any part.
1. Radiator 11. To throttle body 21. To timing chain cover
2. Reservoir tank 12. To heater unit 22. O-Ring
3. Radiator cap 13. To water pump 23. Gasket
4. Drain plug 14. Radiator and condenser cooling fan assembly 24. Water outlet cap O-ring No.1
5. Radiator outlet hose 15. Water inlet pipe No.1 25. Water outlet cap O-ring No.2
6. Radiator inlet hose 16. Water inlet pipe No.2 26. Thermostat cap bolts
7. Thermostat 17. Thermostat cap 27. Thermostat case bolts
8. ECT sensor 18. Water outlet cap Tightening torque
9. Thermostat case 19. Heater inlet hose Do not reuse.
10. To cylinder head 20. Heater outlet hose
Page 603 of 698
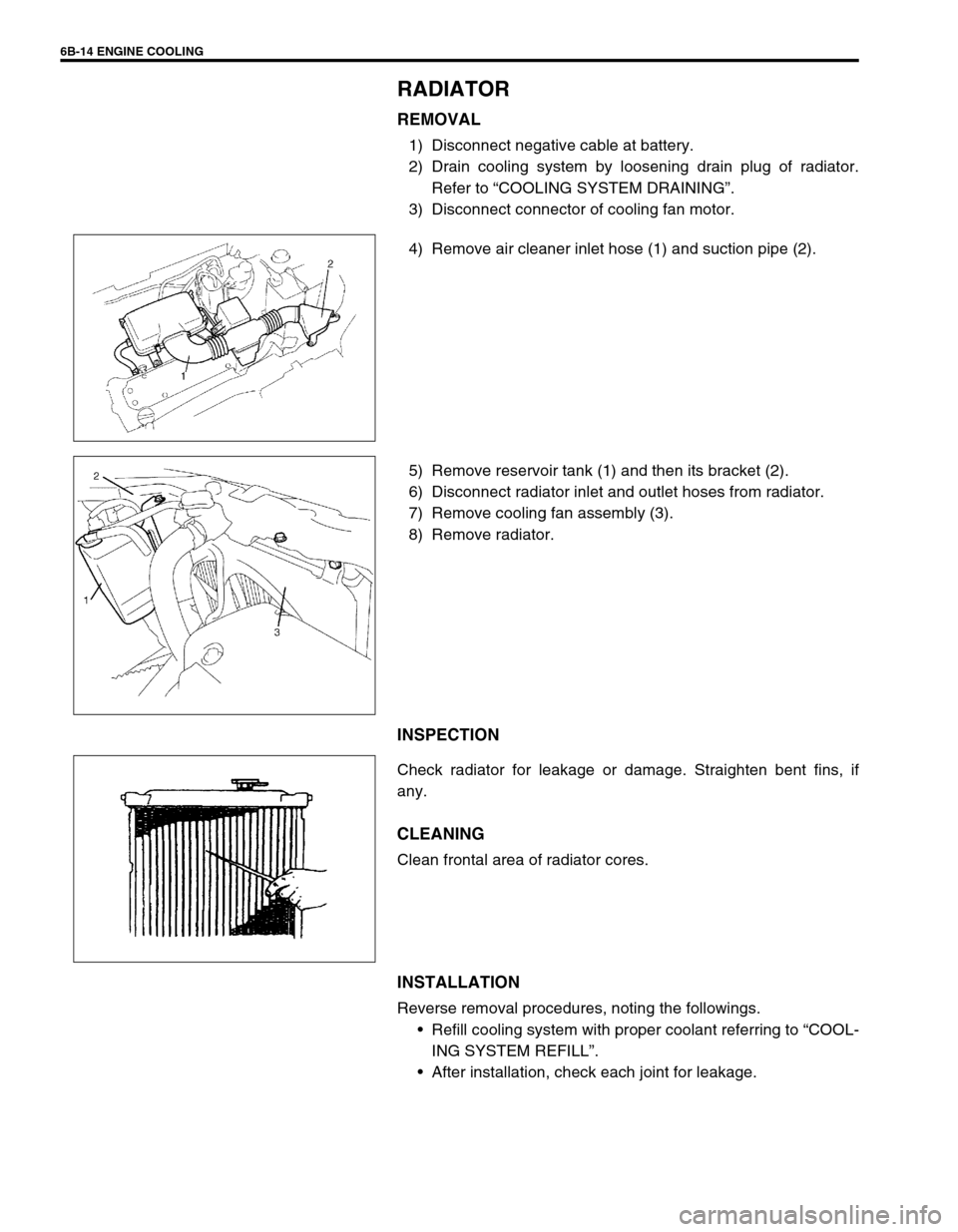
6B-14 ENGINE COOLING
RADIATOR
REMOVAL
1) Disconnect negative cable at battery.
2) Drain cooling system by loosening drain plug of radiator.
Refer to “COOLING SYSTEM DRAINING”.
3) Disconnect connector of cooling fan motor.
4) Remove air cleaner inlet hose (1) and suction pipe (2).
5) Remove reservoir tank (1) and then its bracket (2).
6) Disconnect radiator inlet and outlet hoses from radiator.
7) Remove cooling fan assembly (3).
8) Remove radiator.
INSPECTION
Check radiator for leakage or damage. Straighten bent fins, if
any.
CLEANING
Clean frontal area of radiator cores.
INSTALLATION
Reverse removal procedures, noting the followings.
Refill cooling system with proper coolant referring to “COOL-
ING SYSTEM REFILL”.
After installation, check each joint for leakage.
Page 604 of 698
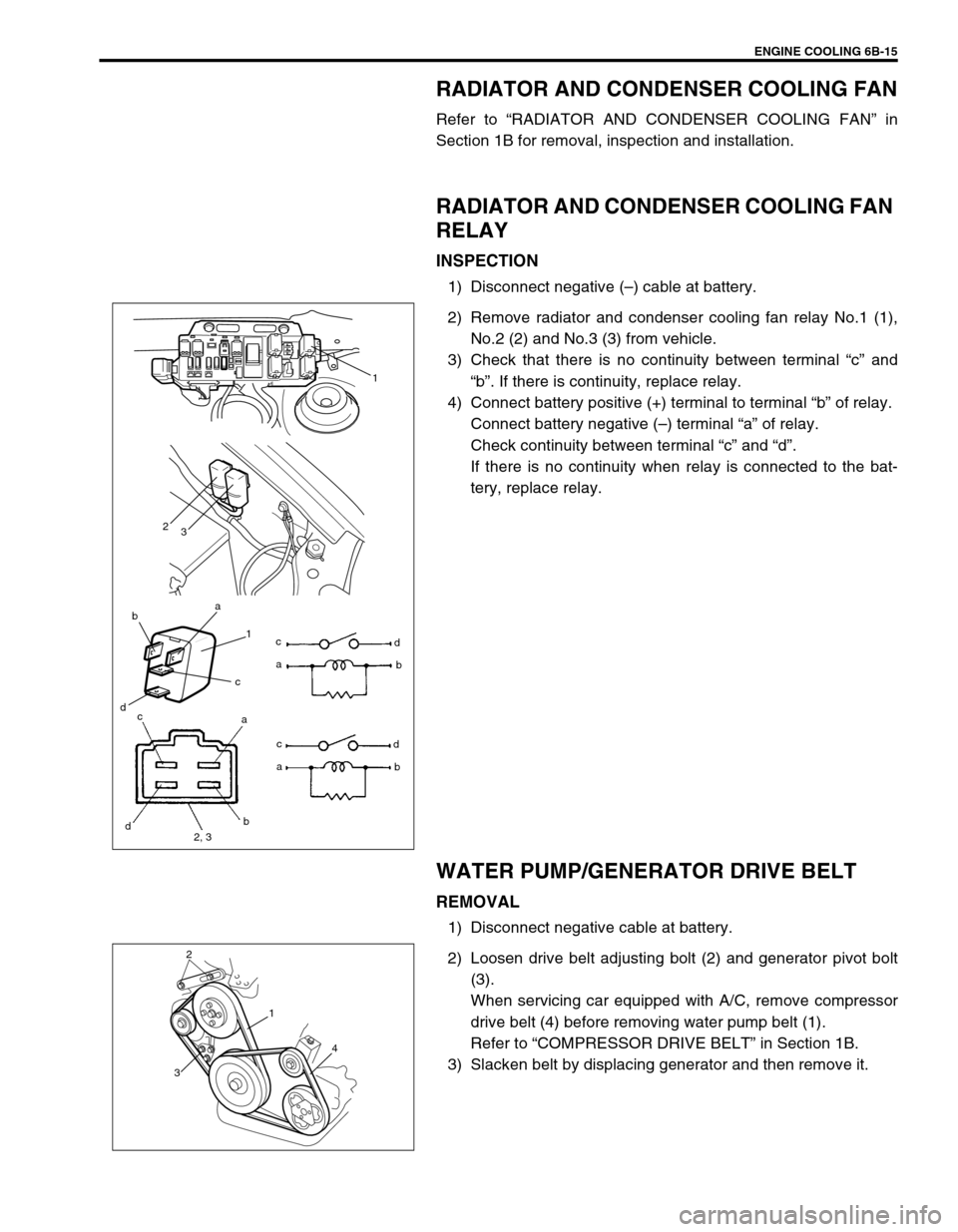
ENGINE COOLING 6B-15
RADIATOR AND CONDENSER COOLING FAN
Refer to “RADIATOR AND CONDENSER COOLING FAN” in
Section 1B for removal, inspection and installation.
RADIATOR AND CONDENSER COOLING FAN
RELAY
INSPECTION
1) Disconnect negative (–) cable at battery.
2) Remove radiator and condenser cooling fan relay No.1 (1),
No.2 (2) and No.3 (3) from vehicle.
3) Check that there is no continuity between terminal “c” and
“b”. If there is continuity, replace relay.
4) Connect battery positive (+) terminal to terminal “b” of relay.
Connect battery negative (–) terminal “a” of relay.
Check continuity between terminal “c” and “d”.
If there is no continuity when relay is connected to the bat-
tery, replace relay.
WATER PUMP/GENERATOR DRIVE BELT
REMOVAL
1) Disconnect negative cable at battery.
2) Loosen drive belt adjusting bolt (2) and generator pivot bolt
(3).
When servicing car equipped with A/C, remove compressor
drive belt (4) before removing water pump belt (1).
Refer to “COMPRESSOR DRIVE BELT” in Section 1B.
3) Slacken belt by displacing generator and then remove it.
ba
1
c
dc
ad
b
2
3
1
c
d
2, 3b a
ac
d
b
2
3
1
4
Page 605 of 698

6B-16 ENGINE COOLING
INSTALLATION
1) Install belt (1) to water pump pulley (2), crankshaft pulley (3)
and generator pulley (4).
When servicing car equipped with A/C, install compressor
drive belt, too.
2) Adjust belt tension by referring to “WATER PUMP/GENERA-
TOR DRIVE BELT TENSION INSPECTION AND ADJUST-
MENT” in this section.
For adjustment of compressor drive belt tension, refer to
COMPRESSOR DRIVE BELT in Section 1B.
3) Tighten water pump belt adjusting bolt and pivot bolt to spec-
ified torque.
Tightening torque
Generator adjusting bolt (a) : 23 N·m (2.3 kg-m, 17.0 lb-ft)
Generator pivot bolt (b) : 50 N·m (5.0 kg-m, 36.0 lb-ft)
4) Connect negative cable at battery.
WATER PUMP BELT TENSION INSPECTION AND
ADJUSTMENT
For this inspection or adjustment, refer to “WATER PUMP GEN-
ERATOR DRIVE BELT TENSION INSPECTION AND ADJUST-
MENT”.
WATER PUMP
REMOVAL
1) Disconnect negative cable at battery.
2) Drain coolant. Refer to “COOLING SYSTEM DRAINING”.
3) Remove A/C compressor belt (4) by referring to “COM-
PRESSOR DRIVE BELT” in Section 1B. (if equipped).
4) Loosen water pump/generator drive belt adjusting bolt (1)
and generator pivot bolt (2). Then remove water pump/gen-
erator drive belt (3) and water pump pulley.
Refer to “WATER PUMP BELT” in this section.
2
1
3
4
1
2
43
Page 606 of 698
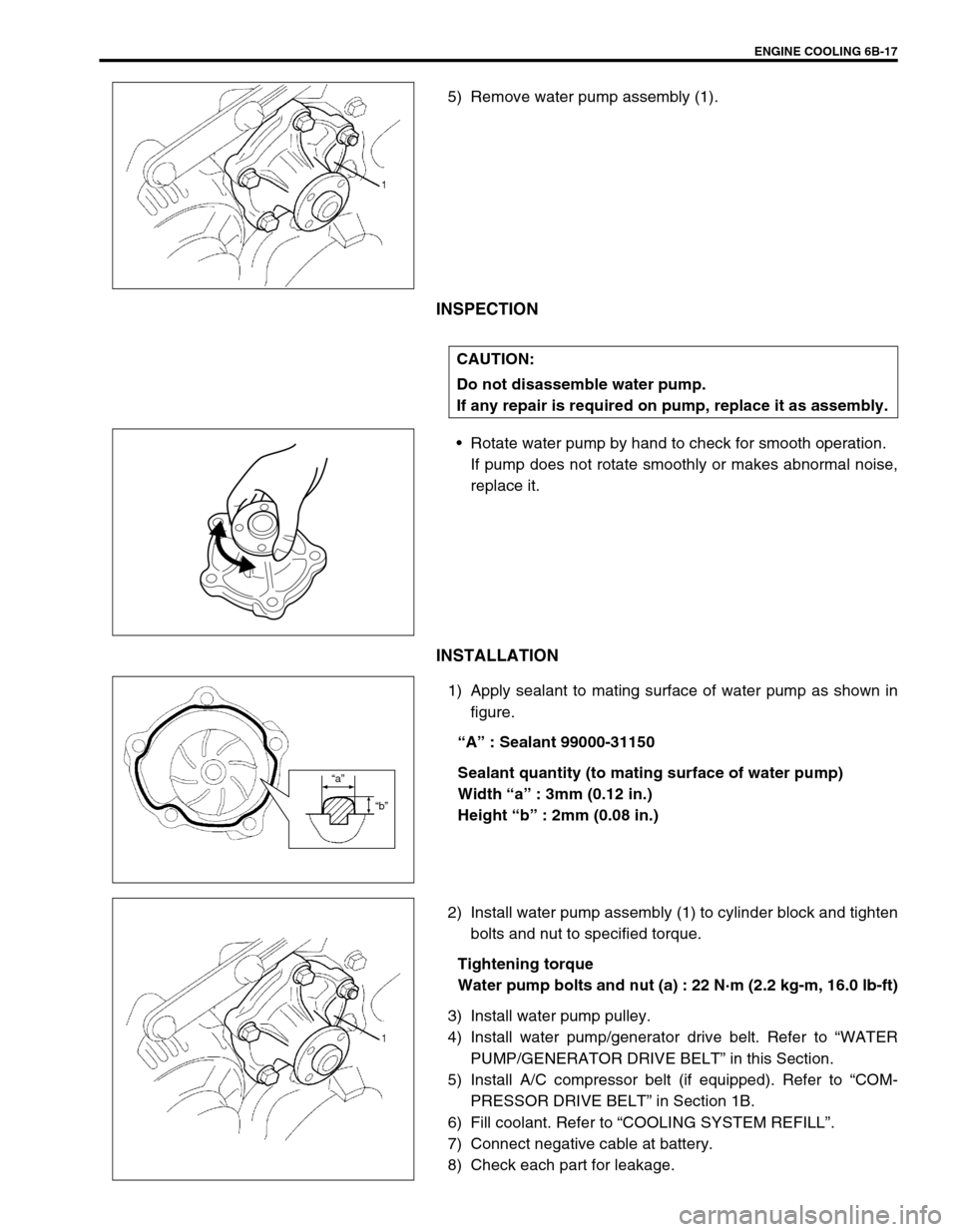
ENGINE COOLING 6B-17
5) Remove water pump assembly (1).
INSPECTION
Rotate water pump by hand to check for smooth operation.
If pump does not rotate smoothly or makes abnormal noise,
replace it.
INSTALLATION
1) Apply sealant to mating surface of water pump as shown in
figure.
“A” : Sealant 99000-31150
Sealant quantity (to mating surface of water pump)
Width “a” : 3mm (0.12 in.)
Height “b” : 2mm (0.08 in.)
2) Install water pump assembly (1) to cylinder block and tighten
bolts and nut to specified torque.
Tightening torque
Water pump bolts and nut (a) : 22 N·m (2.2 kg-m, 16.0 lb-ft)
3) Install water pump pulley.
4) Install water pump/generator drive belt. Refer to “WATER
PUMP/GENERATOR DRIVE BELT” in this Section.
5) Install A/C compressor belt (if equipped). Refer to “COM-
PRESSOR DRIVE BELT” in Section 1B.
6) Fill coolant. Refer to “COOLING SYSTEM REFILL”.
7) Connect negative cable at battery.
8) Check each part for leakage.
CAUTION:
Do not disassemble water pump.
If any repair is required on pump, replace it as assembly.
“a”
“b”
Page 608 of 698
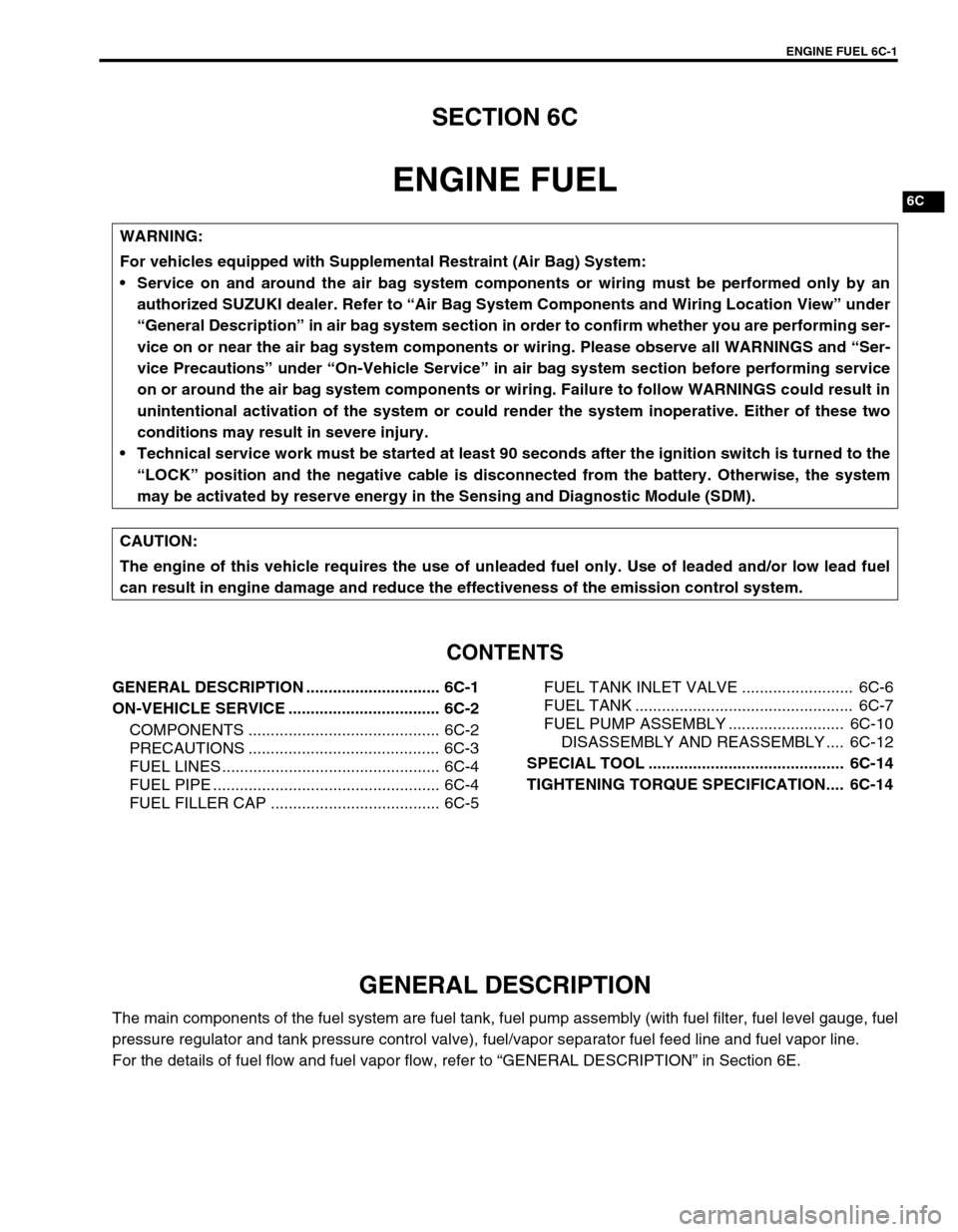
ENGINE FUEL 6C-1
6F1
6F2
6G
6C
6K
7A
7A1
7B1
7C1
7D
7E
7F
8A
8B
8C
8D
8E
9
10
10A
10B
SECTION 6C
ENGINE FUEL
CONTENTS
GENERAL DESCRIPTION .............................. 6C-1
ON-VEHICLE SERVICE .................................. 6C-2
COMPONENTS ........................................... 6C-2
PRECAUTIONS ........................................... 6C-3
FUEL LINES ................................................. 6C-4
FUEL PIPE ................................................... 6C-4
FUEL FILLER CAP ...................................... 6C-5FUEL TANK INLET VALVE ......................... 6C-6
FUEL TANK ................................................. 6C-7
FUEL PUMP ASSEMBLY .......................... 6C-10
DISASSEMBLY AND REASSEMBLY .... 6C-12
SPECIAL TOOL ............................................ 6C-14
TIGHTENING TORQUE SPECIFICATION.... 6C-14
GENERAL DESCRIPTION
The main components of the fuel system are fuel tank, fuel pump assembly (with fuel filter, fuel level gauge, fuel
pressure regulator and tank pressure control valve), fuel/vapor separator fuel feed line and fuel vapor line.
For the details of fuel flow and fuel vapor flow, refer to “GENERAL DESCRIPTION” in Section 6E. WARNING:
For vehicles equipped with Supplemental Restraint (Air Bag) System:
Service on and around the air bag system components or wiring must be performed only by an
authorized SUZUKI dealer. Refer to “Air Bag System Components and Wiring Location View” under
“General Description” in air bag system section in order to confirm whether you are performing ser-
vice on or near the air bag system components or wiring. Please observe all WARNINGS and “Ser-
vice Precautions” under “On-Vehicle Service” in air bag system section before performing service
on or around the air bag system components or wiring. Failure to follow WARNINGS could result in
unintentional activation of the system or could render the system inoperative. Either of these two
conditions may result in severe injury.
Technical service work must be started at least 90 seconds after the ignition switch is turned to the
“LOCK” position and the negative cable is disconnected from the battery. Otherwise, the system
may be activated by reserve energy in the Sensing and Diagnostic Module (SDM).
CAUTION:
The engine of this vehicle requires the use of unleaded fuel only. Use of leaded and/or low lead fuel
can result in engine damage and reduce the effectiveness of the emission control system.
Page 610 of 698
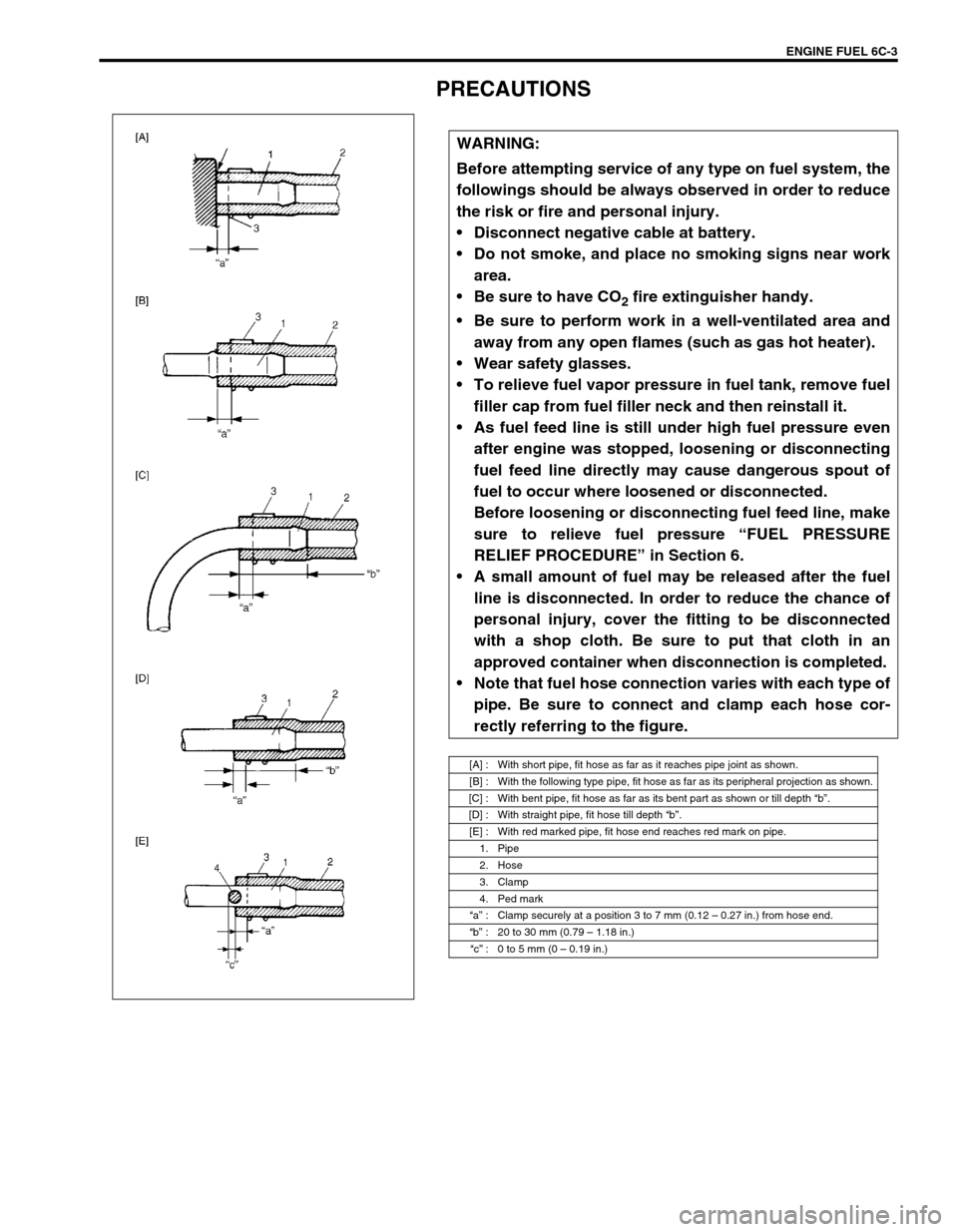
ENGINE FUEL 6C-3
PRECAUTIONS
WARNING:
Before attempting service of any type on fuel system, the
followings should be always observed in order to reduce
the risk or fire and personal injury.
Disconnect negative cable at battery.
Do not smoke, and place no smoking signs near work
area.
Be sure to have CO
2 fire extinguisher handy.
Be sure to perform work in a well-ventilated area and
away from any open flames (such as gas hot heater).
Wear safety glasses.
To relieve fuel vapor pressure in fuel tank, remove fuel
filler cap from fuel filler neck and then reinstall it.
As fuel feed line is still under high fuel pressure even
after engine was stopped, loosening or disconnecting
fuel feed line directly may cause dangerous spout of
fuel to occur where loosened or disconnected.
Before loosening or disconnecting fuel feed line, make
sure to relieve fuel pressure “FUEL PRESSURE
RELIEF PROCEDURE” in Section 6.
A small amount of fuel may be released after the fuel
line is disconnected. In order to reduce the chance of
personal injury, cover the fitting to be disconnected
with a shop cloth. Be sure to put that cloth in an
approved container when disconnection is completed.
Note that fuel hose connection varies with each type of
pipe. Be sure to connect and clamp each hose cor-
rectly referring to the figure.
[A] : With short pipe, fit hose as far as it reaches pipe joint as shown.
[B] : With the following type pipe, fit hose as far as its peripheral projection as shown.
[C] : With bent pipe, fit hose as far as its bent part as shown or till depth “b”.
[D] : With straight pipe, fit hose till depth “b”.
[E] : With red marked pipe, fit hose end reaches red mark on pipe.
1. Pipe
2. Hose
3. Clamp
4. Ped mark
“a” : Clamp securely at a position 3 to 7 mm (0.12 – 0.27 in.) from hose end.
“b” : 20 to 30 mm (0.79 – 1.18 in.)
“c” : 0 to 5 mm (0 – 0.19 in.)
Page 611 of 698
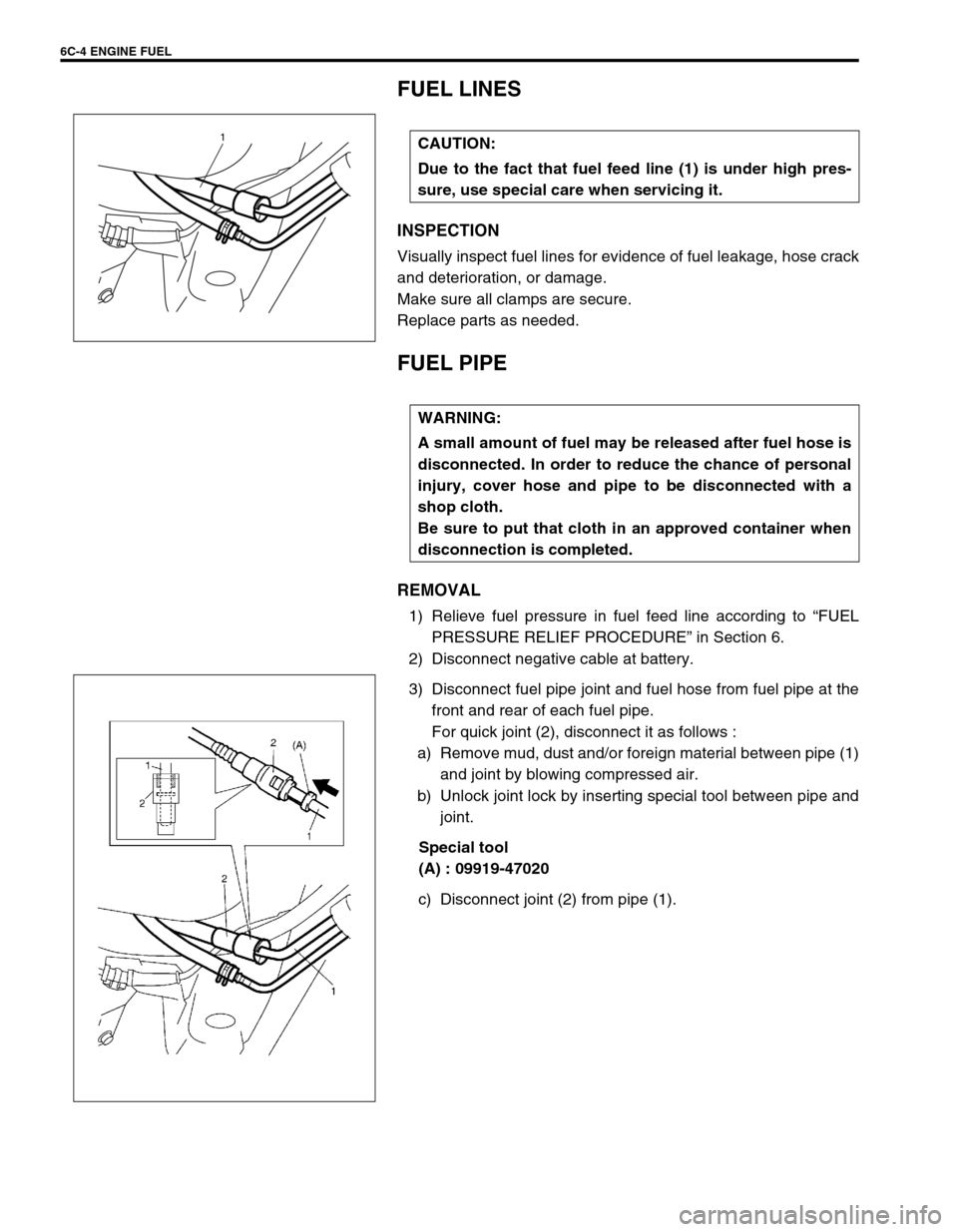
6C-4 ENGINE FUEL
FUEL LINES
INSPECTION
Visually inspect fuel lines for evidence of fuel leakage, hose crack
and deterioration, or damage.
Make sure all clamps are secure.
Replace parts as needed.
FUEL PIPE
REMOVAL
1) Relieve fuel pressure in fuel feed line according to “FUEL
PRESSURE RELIEF PROCEDURE” in Section 6.
2) Disconnect negative cable at battery.
3) Disconnect fuel pipe joint and fuel hose from fuel pipe at the
front and rear of each fuel pipe.
For quick joint (2), disconnect it as follows :
a) Remove mud, dust and/or foreign material between pipe (1)
and joint by blowing compressed air.
b) Unlock joint lock by inserting special tool between pipe and
joint.
Special tool
(A) : 09919-47020
c) Disconnect joint (2) from pipe (1). CAUTION:
Due to the fact that fuel feed line (1) is under high pres-
sure, use special care when servicing it.
1
WARNING:
A small amount of fuel may be released after fuel hose is
disconnected. In order to reduce the chance of personal
injury, cover hose and pipe to be disconnected with a
shop cloth.
Be sure to put that cloth in an approved container when
disconnection is completed.