turn signal SUZUKI SWIFT 2000 1.G RG413 Service Workshop Manual
[x] Cancel search | Manufacturer: SUZUKI, Model Year: 2000, Model line: SWIFT, Model: SUZUKI SWIFT 2000 1.GPages: 698, PDF Size: 16.01 MB
Page 142 of 698
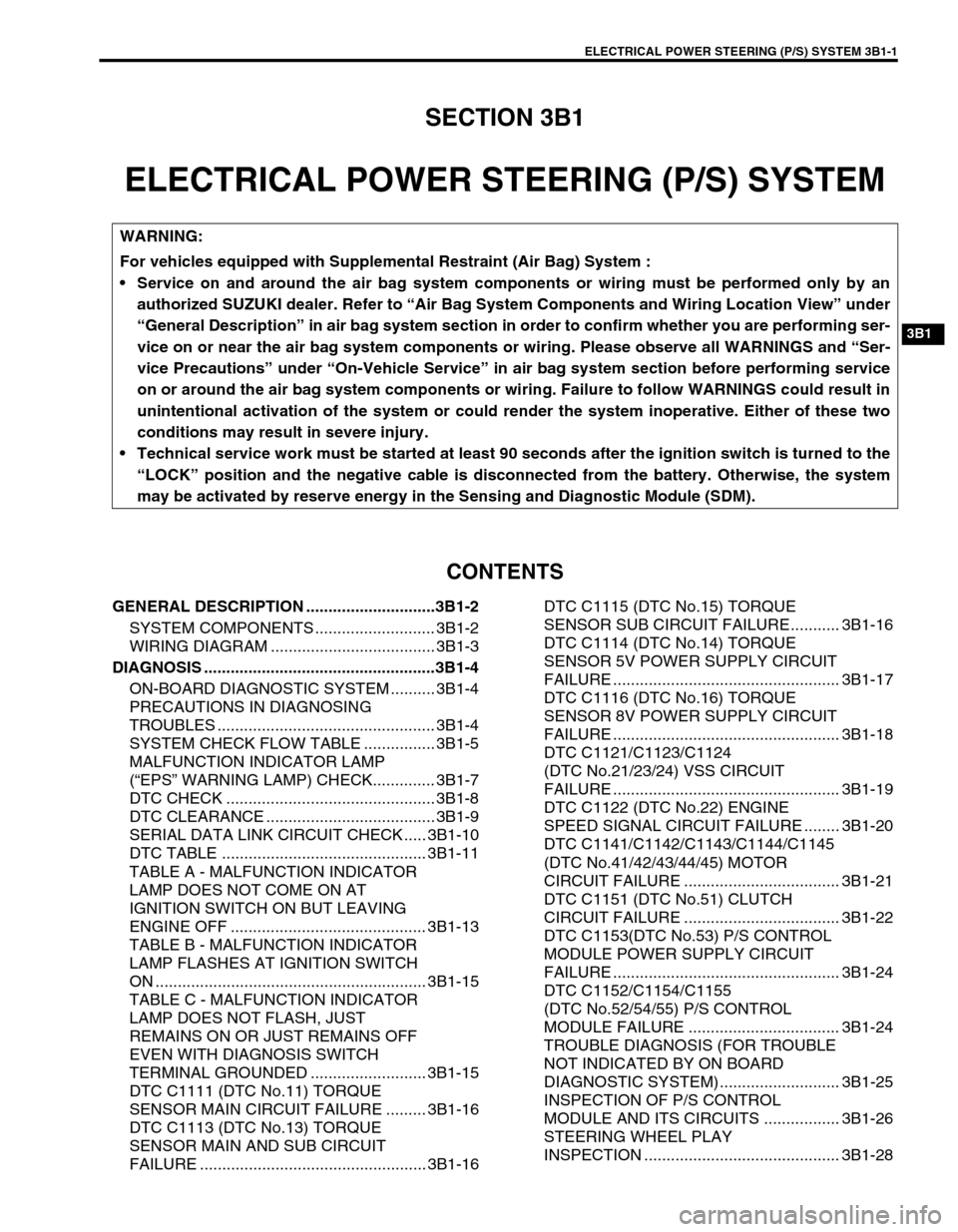
ELECTRICAL POWER STEERING (P/S) SYSTEM 3B1-1
6F1
6F2
6G
6H
6K
7A
7A1
3B1
7D
7E
7F
8A
8B
8C
8D
8E
9
10
10A
10B
SECTION 3B1
ELECTRICAL POWER STEERING (P/S) SYSTEM
CONTENTS
GENERAL DESCRIPTION .............................3B1-2
SYSTEM COMPONENTS ........................... 3B1-2
WIRING DIAGRAM ..................................... 3B1-3
DIAGNOSIS ....................................................3B1-4
ON-BOARD DIAGNOSTIC SYSTEM .......... 3B1-4
PRECAUTIONS IN DIAGNOSING
TROUBLES ................................................. 3B1-4
SYSTEM CHECK FLOW TABLE ................ 3B1-5
MALFUNCTION INDICATOR LAMP
(“EPS” WARNING LAMP) CHECK.............. 3B1-7
DTC CHECK ............................................... 3B1-8
DTC CLEARANCE ...................................... 3B1-9
SERIAL DATA LINK CIRCUIT CHECK ..... 3B1-10
DTC TABLE .............................................. 3B1-11
TABLE A - MALFUNCTION INDICATOR
LAMP DOES NOT COME ON AT
IGNITION SWITCH ON BUT LEAVING
ENGINE OFF ............................................ 3B1-13
TABLE B - MALFUNCTION INDICATOR
LAMP FLASHES AT IGNITION SWITCH
ON ............................................................. 3B1-15
TABLE C - MALFUNCTION INDICATOR
LAMP DOES NOT FLASH, JUST
REMAINS ON OR JUST REMAINS OFF
EVEN WITH DIAGNOSIS SWITCH
TERMINAL GROUNDED .......................... 3B1-15
DTC C1111 (DTC No.11) TORQUE
SENSOR MAIN CIRCUIT FAILURE ......... 3B1-16
DTC C1113 (DTC No.13) TORQUE
SENSOR MAIN AND SUB CIRCUIT
FAILURE ................................................... 3B1-16DTC C1115 (DTC No.15) TORQUE
SENSOR SUB CIRCUIT FAILURE........... 3B1-16
DTC C1114 (DTC No.14) TORQUE
SENSOR 5V POWER SUPPLY CIRCUIT
FAILURE ................................................... 3B1-17
DTC C1116 (DTC No.16) TORQUE
SENSOR 8V POWER SUPPLY CIRCUIT
FAILURE ................................................... 3B1-18
DTC C1121/C1123/C1124
(DTC No.21/23/24) VSS CIRCUIT
FAILURE ................................................... 3B1-19
DTC C1122 (DTC No.22) ENGINE
SPEED SIGNAL CIRCUIT FAILURE ........ 3B1-20
DTC C1141/C1142/C1143/C1144/C1145
(DTC No.41/42/43/44/45) MOTOR
CIRCUIT FAILURE ................................... 3B1-21
DTC C1151 (DTC No.51) CLUTCH
CIRCUIT FAILURE ................................... 3B1-22
DTC C1153(DTC No.53) P/S CONTROL
MODULE POWER SUPPLY CIRCUIT
FAILURE ................................................... 3B1-24
DTC C1152/C1154/C1155
(DTC No.52/54/55) P/S CONTROL
MODULE FAILURE .................................. 3B1-24
TROUBLE DIAGNOSIS (FOR TROUBLE
NOT INDICATED BY ON BOARD
DIAGNOSTIC SYSTEM)........................... 3B1-25
INSPECTION OF P/S CONTROL
MODULE AND ITS CIRCUITS ................. 3B1-26
STEERING WHEEL PLAY
INSPECTION ............................................ 3B1-28 WARNING:
For vehicles equipped with Supplemental Restraint (Air Bag) System :
Service on and around the air bag system components or wiring must be performed only by an
authorized SUZUKI dealer. Refer to “Air Bag System Components and Wiring Location View” under
“General Description” in air bag system section in order to confirm whether you are performing ser-
vice on or near the air bag system components or wiring. Please observe all WARNINGS and “Ser-
vice Precautions” under “On-Vehicle Service” in air bag system section before performing service
on or around the air bag system components or wiring. Failure to follow WARNINGS could result in
unintentional activation of the system or could render the system inoperative. Either of these two
conditions may result in severe injury.
Technical service work must be started at least 90 seconds after the ignition switch is turned to the
“LOCK” position and the negative cable is disconnected from the battery. Otherwise, the system
may be activated by reserve energy in the Sensing and Diagnostic Module (SDM).
Page 145 of 698
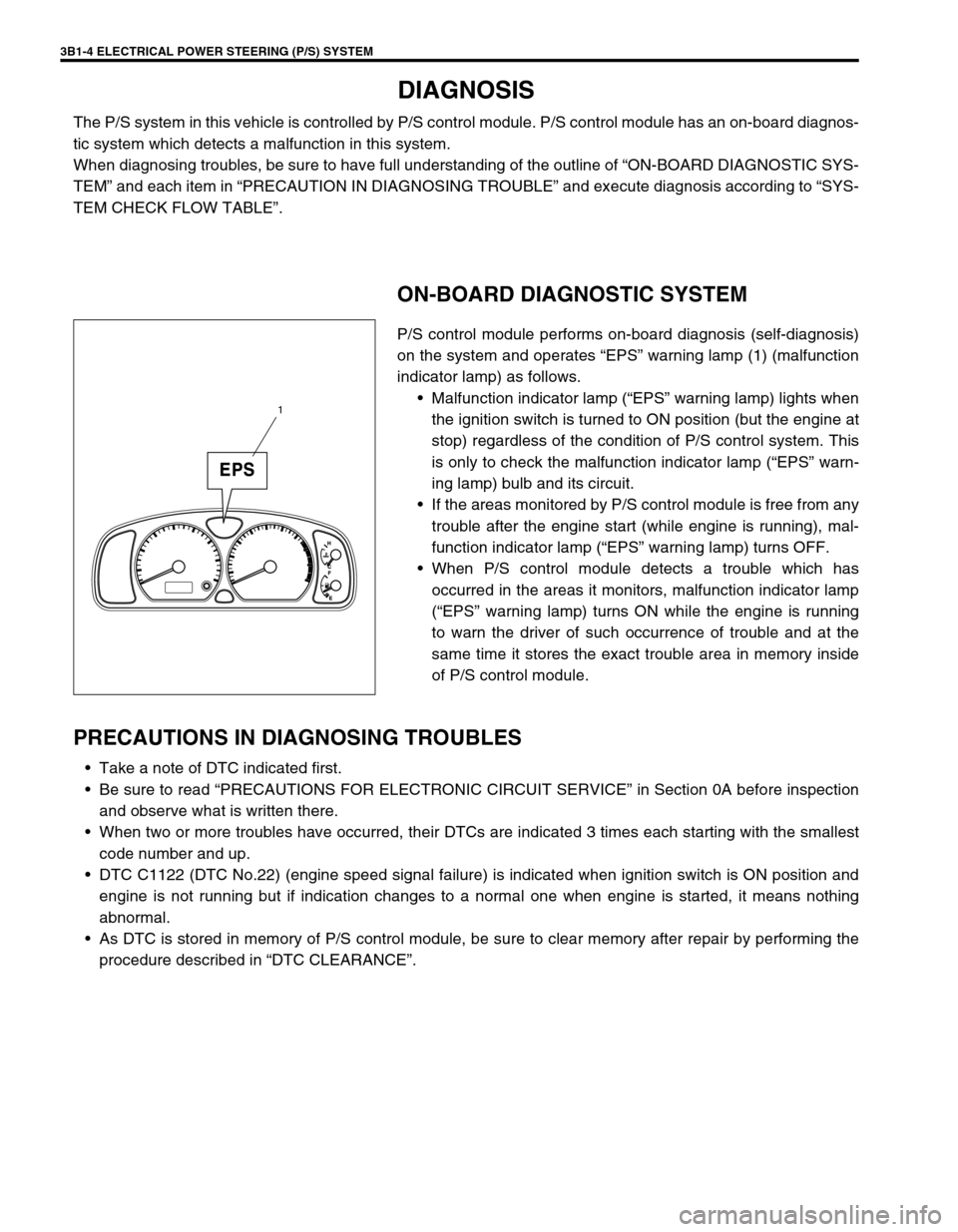
3B1-4 ELECTRICAL POWER STEERING (P/S) SYSTEM
DIAGNOSIS
The P/S system in this vehicle is controlled by P/S control module. P/S control module has an on-board diagnos-
tic system which detects a malfunction in this system.
When diagnosing troubles, be sure to have full understanding of the outline of “ON-BOARD DIAGNOSTIC SYS-
TEM” and each item in “PRECAUTION IN DIAGNOSING TROUBLE” and execute diagnosis according to “SYS-
TEM CHECK FLOW TABLE”.
ON-BOARD DIAGNOSTIC SYSTEM
P/S control module performs on-board diagnosis (self-diagnosis)
on the system and operates “EPS” warning lamp (1) (malfunction
indicator lamp) as follows.
Malfunction indicator lamp (“EPS” warning lamp) lights when
the ignition switch is turned to ON position (but the engine at
stop) regardless of the condition of P/S control system. This
is only to check the malfunction indicator lamp (“EPS” warn-
ing lamp) bulb and its circuit.
If the areas monitored by P/S control module is free from any
trouble after the engine start (while engine is running), mal-
function indicator lamp (“EPS” warning lamp) turns OFF.
When P/S control module detects a trouble which has
occurred in the areas it monitors, malfunction indicator lamp
(“EPS” warning lamp) turns ON while the engine is running
to warn the driver of such occurrence of trouble and at the
same time it stores the exact trouble area in memory inside
of P/S control module.
PRECAUTIONS IN DIAGNOSING TROUBLES
Take a note of DTC indicated first.
Be sure to read “PRECAUTIONS FOR ELECTRONIC CIRCUIT SERVICE” in Section 0A before inspection
and observe what is written there.
When two or more troubles have occurred, their DTCs are indicated 3 times each starting with the smallest
code number and up.
DTC C1122 (DTC No.22) (engine speed signal failure) is indicated when ignition switch is ON position and
engine is not running but if indication changes to a normal one when engine is started, it means nothing
abnormal.
As DTC is stored in memory of P/S control module, be sure to clear memory after repair by performing the
procedure described in “DTC CLEARANCE”.
1
Page 168 of 698
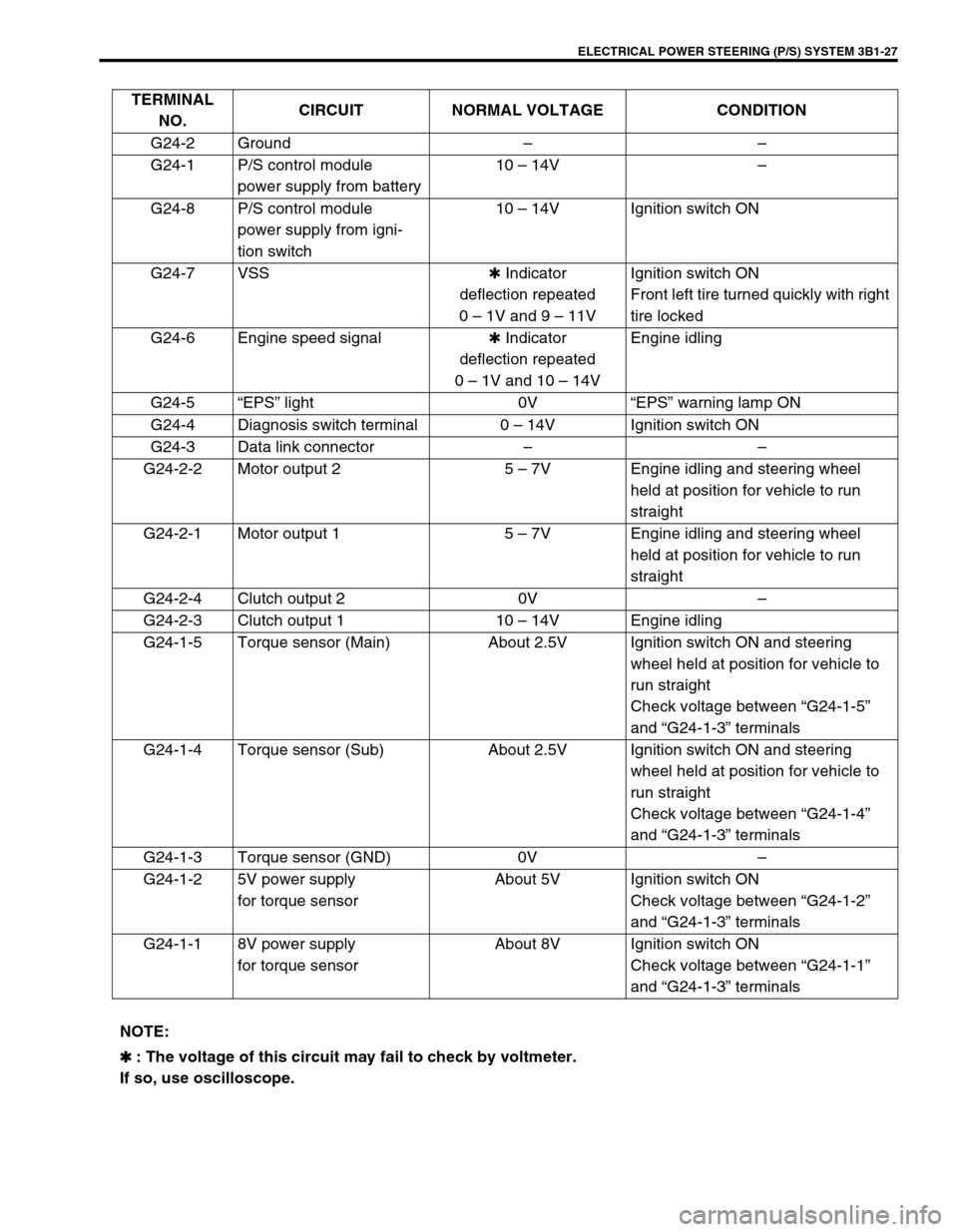
ELECTRICAL POWER STEERING (P/S) SYSTEM 3B1-27
TERMINAL
NO.CIRCUIT NORMAL VOLTAGE CONDITION
G24-2 Ground––
G24-1 P/S control module
power supply from battery10 – 14V–
G24-8 P/S control module
power supply from igni-
tion switch10 – 14V Ignition switch ON
G24-7 VSS✱ Indicator
deflection repeated
0 – 1V and 9 – 11VIgnition switch ON
Front left tire turned quickly with right
tire locked
G24-6 Engine speed signal✱ Indicator
deflection repeated
0 – 1V and 10 – 14VEngine idling
G24-5“EPS” light 0V“EPS” warning lamp ON
G24-4 Diagnosis switch terminal 0 – 14V Ignition switch ON
G24-3 Data link connector––
G24-2-2 Motor output 2 5 – 7V Engine idling and steering wheel
held at position for vehicle to run
straight
G24-2-1 Motor output 1 5 – 7V Engine idling and steering wheel
held at position for vehicle to run
straight
G24-2-4 Clutch output 2 0V–
G24-2-3 Clutch output 1 10 – 14V Engine idling
G24-1-5 Torque sensor (Main) About 2.5V Ignition switch ON and steering
wheel held at position for vehicle to
run straight
Check voltage between “G24-1-5”
and “G24-1-3” terminals
G24-1-4 Torque sensor (Sub) About 2.5V Ignition switch ON and steering
wheel held at position for vehicle to
run straight
Check voltage between “G24-1-4”
and “G24-1-3” terminals
G24-1-3 Torque sensor (GND) 0V–
G24-1-2 5V power supply
for torque sensorAbout 5V Ignition switch ON
Check voltage between “G24-1-2”
and “G24-1-3” terminals
G24-1-1 8V power supply
for torque sensorAbout 8V Ignition switch ON
Check voltage between “G24-1-1”
and “G24-1-3” terminals
NOTE:
✱
✱✱ ✱ : The voltage of this circuit may fail to check by voltmeter.
If so, use oscilloscope.
Page 180 of 698
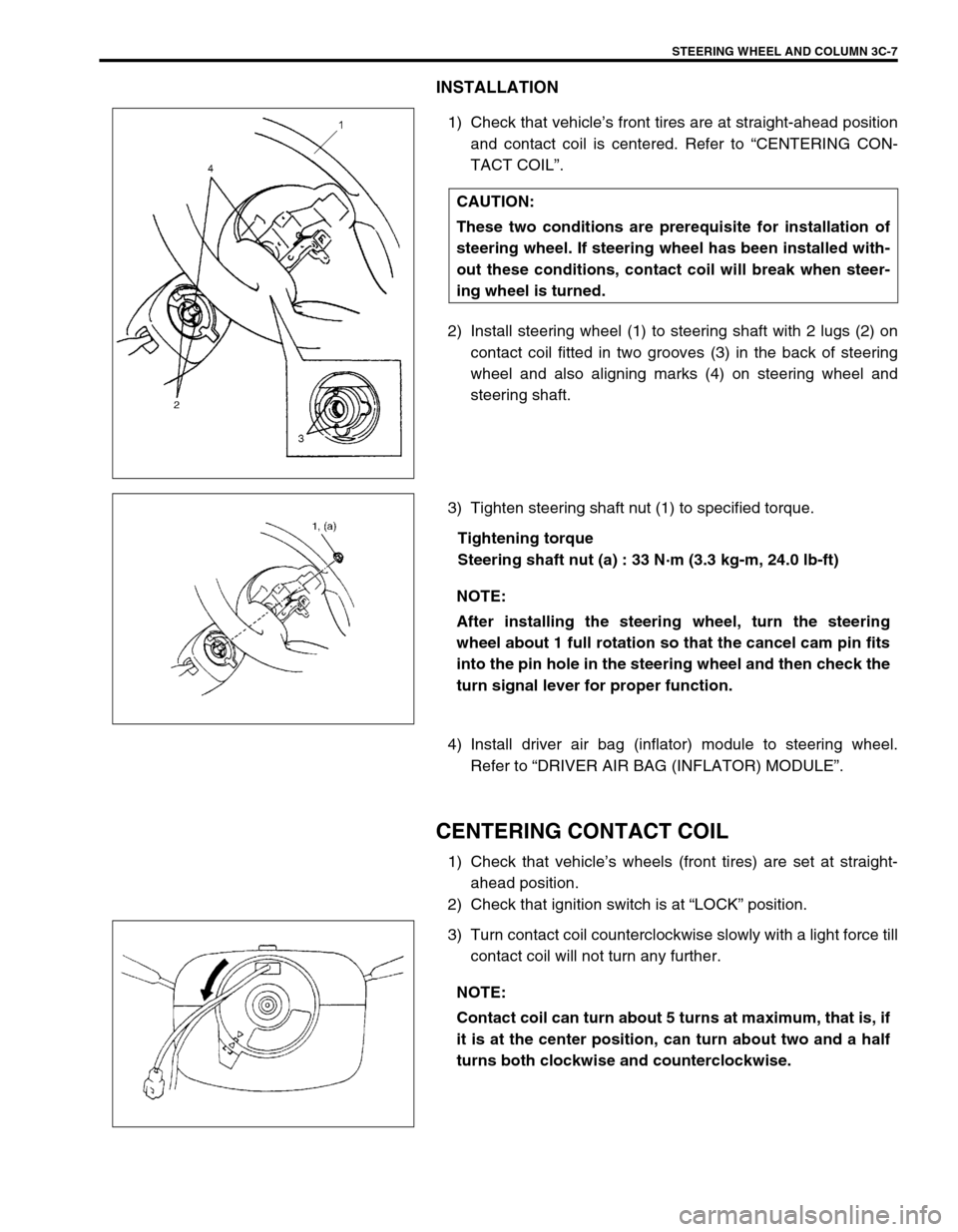
STEERING WHEEL AND COLUMN 3C-7
INSTALLATION
1) Check that vehicle’s front tires are at straight-ahead position
and contact coil is centered. Refer to “CENTERING CON-
TACT COIL”.
2) Install steering wheel (1) to steering shaft with 2 lugs (2) on
contact coil fitted in two grooves (3) in the back of steering
wheel and also aligning marks (4) on steering wheel and
steering shaft.
3) Tighten steering shaft nut (1) to specified torque.
Tightening torque
Steering shaft nut (a) : 33 N·m (3.3 kg-m, 24.0 lb-ft)
4) Install driver air bag (inflator) module to steering wheel.
Refer to “DRIVER AIR BAG (INFLATOR) MODULE”.
CENTERING CONTACT COIL
1) Check that vehicle’s wheels (front tires) are set at straight-
ahead position.
2) Check that ignition switch is at “LOCK” position.
3) Turn contact coil counterclockwise slowly with a light force till
contact coil will not turn any further. CAUTION:
These two conditions are prerequisite for installation of
steering wheel. If steering wheel has been installed with-
out these conditions, contact coil will break when steer-
ing wheel is turned.
NOTE:
After installing the steering wheel, turn the steering
wheel about 1 full rotation so that the cancel cam pin fits
into the pin hole in the steering wheel and then check the
turn signal lever for proper function.
NOTE:
Contact coil can turn about 5 turns at maximum, that is, if
it is at the center position, can turn about two and a half
turns both clockwise and counterclockwise.
Page 347 of 698
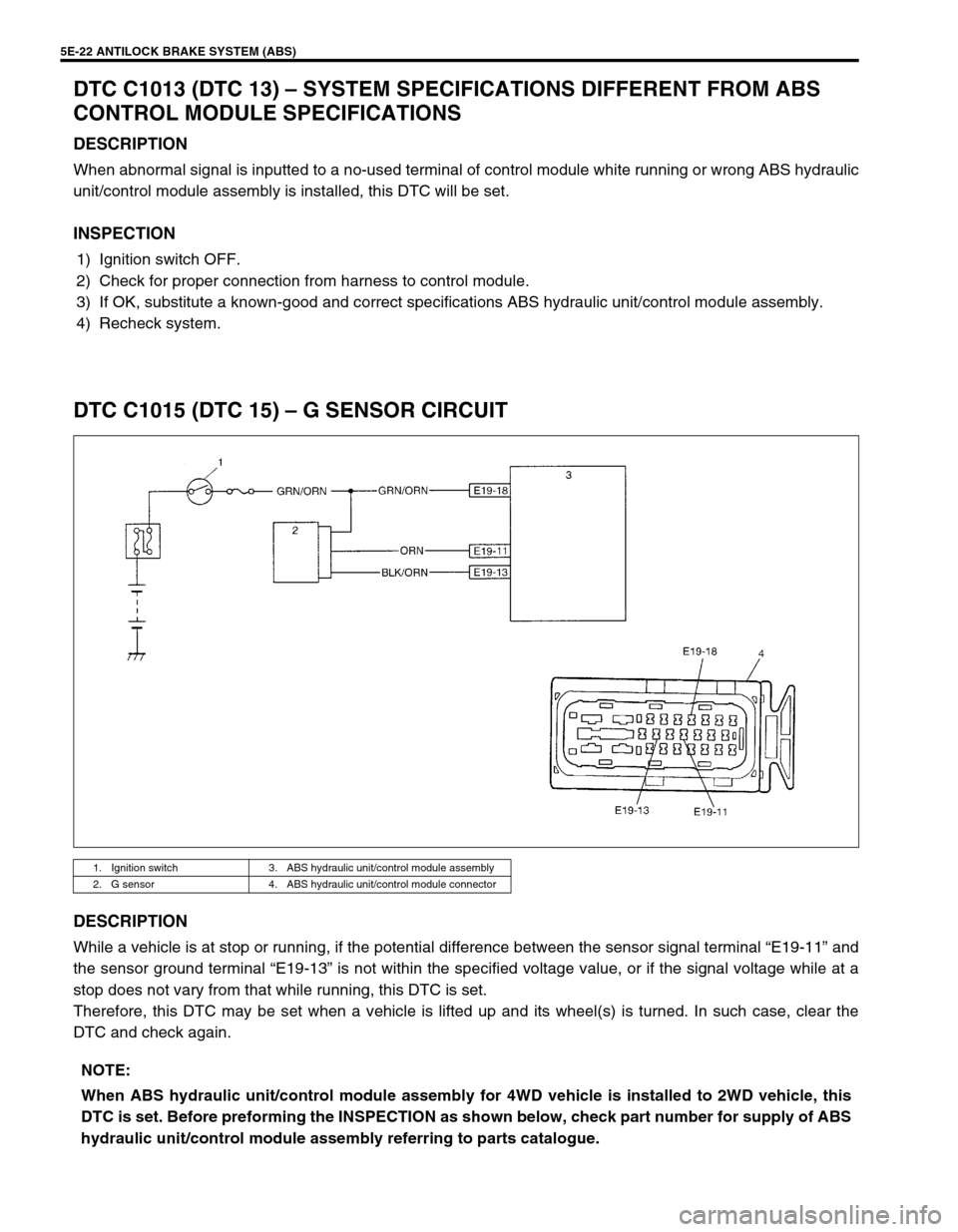
5E-22 ANTILOCK BRAKE SYSTEM (ABS)
DTC C1013 (DTC 13) – SYSTEM SPECIFICATIONS DIFFERENT FROM ABS
CONTROL MODULE SPECIFICATIONS
DESCRIPTION
When abnormal signal is inputted to a no-used terminal of control module white running or wrong ABS hydraulic
unit/control module assembly is installed, this DTC will be set.
INSPECTION
1) Ignition switch OFF.
2) Check for proper connection from harness to control module.
3) If OK, substitute a known-good and correct specifications ABS hydraulic unit/control module assembly.
4) Recheck system.
DTC C1015 (DTC 15) – G SENSOR CIRCUIT
DESCRIPTION
While a vehicle is at stop or running, if the potential difference between the sensor signal terminal “E19-11” and
the sensor ground terminal “E19-13” is not within the specified voltage value, or if the signal voltage while at a
stop does not vary from that while running, this DTC is set.
Therefore, this DTC may be set when a vehicle is lifted up and its wheel(s) is turned. In such case, clear the
DTC and check again.
1. Ignition switch 3. ABS hydraulic unit/control module assembly
2. G sensor 4. ABS hydraulic unit/control module connector
NOTE:
When ABS hydraulic unit/control module assembly for 4WD vehicle is installed to 2WD vehicle, this
DTC is set. Before preforming the INSPECTION as shown below, check part number for supply of ABS
hydraulic unit/control module assembly referring to parts catalogue.
Page 349 of 698
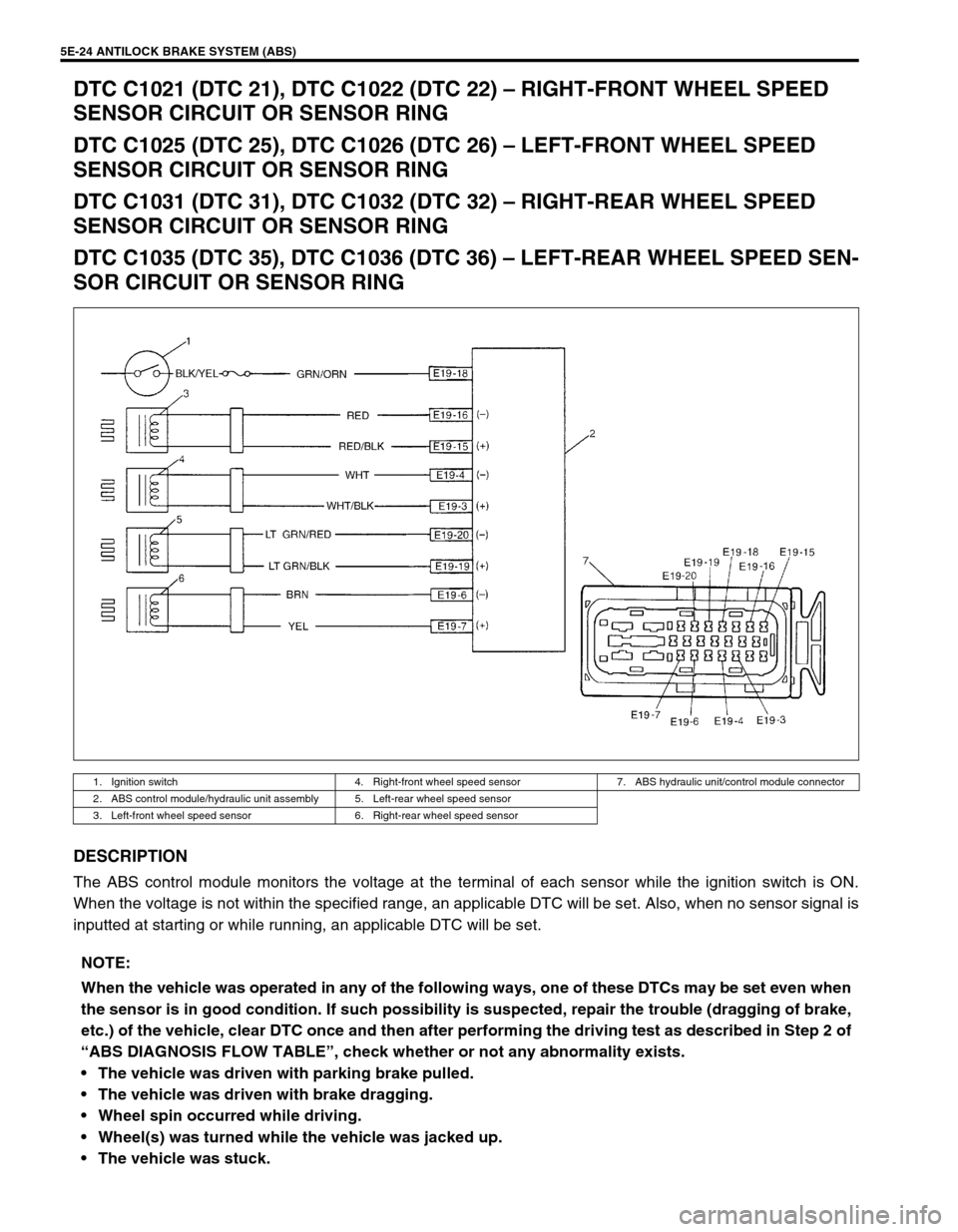
5E-24 ANTILOCK BRAKE SYSTEM (ABS)
DTC C1021 (DTC 21), DTC C1022 (DTC 22) – RIGHT-FRONT WHEEL SPEED
SENSOR CIRCUIT OR SENSOR RING
DTC C1025 (DTC 25), DTC C1026 (DTC 26) – LEFT-FRONT WHEEL SPEED
SENSOR CIRCUIT OR SENSOR RING
DTC C1031 (DTC 31), DTC C1032 (DTC 32) – RIGHT-REAR WHEEL SPEED
SENSOR CIRCUIT OR SENSOR RING
DTC C1035 (DTC 35), DTC C1036 (DTC 36) – LEFT-REAR WHEEL SPEED SEN-
SOR CIRCUIT OR SENSOR RING
DESCRIPTION
The ABS control module monitors the voltage at the terminal of each sensor while the ignition switch is ON.
When the voltage is not within the specified range, an applicable DTC will be set. Also, when no sensor signal is
inputted at starting or while running, an applicable DTC will be set.
1. Ignition switch 4. Right-front wheel speed sensor 7. ABS hydraulic unit/control module connector
2. ABS control module/hydraulic unit assembly 5. Left-rear wheel speed sensor
3. Left-front wheel speed sensor 6. Right-rear wheel speed sensor
NOTE:
When the vehicle was operated in any of the following ways, one of these DTCs may be set even when
the sensor is in good condition. If such possibility is suspected, repair the trouble (dragging of brake,
etc.) of the vehicle, clear DTC once and then after performing the driving test as described in Step 2 of
“ABS DIAGNOSIS FLOW TABLE”, check whether or not any abnormality exists.
The vehicle was driven with parking brake pulled.
The vehicle was driven with brake dragging.
Wheel spin occurred while driving.
Wheel(s) was turned while the vehicle was jacked up.
The vehicle was stuck.
Page 404 of 698
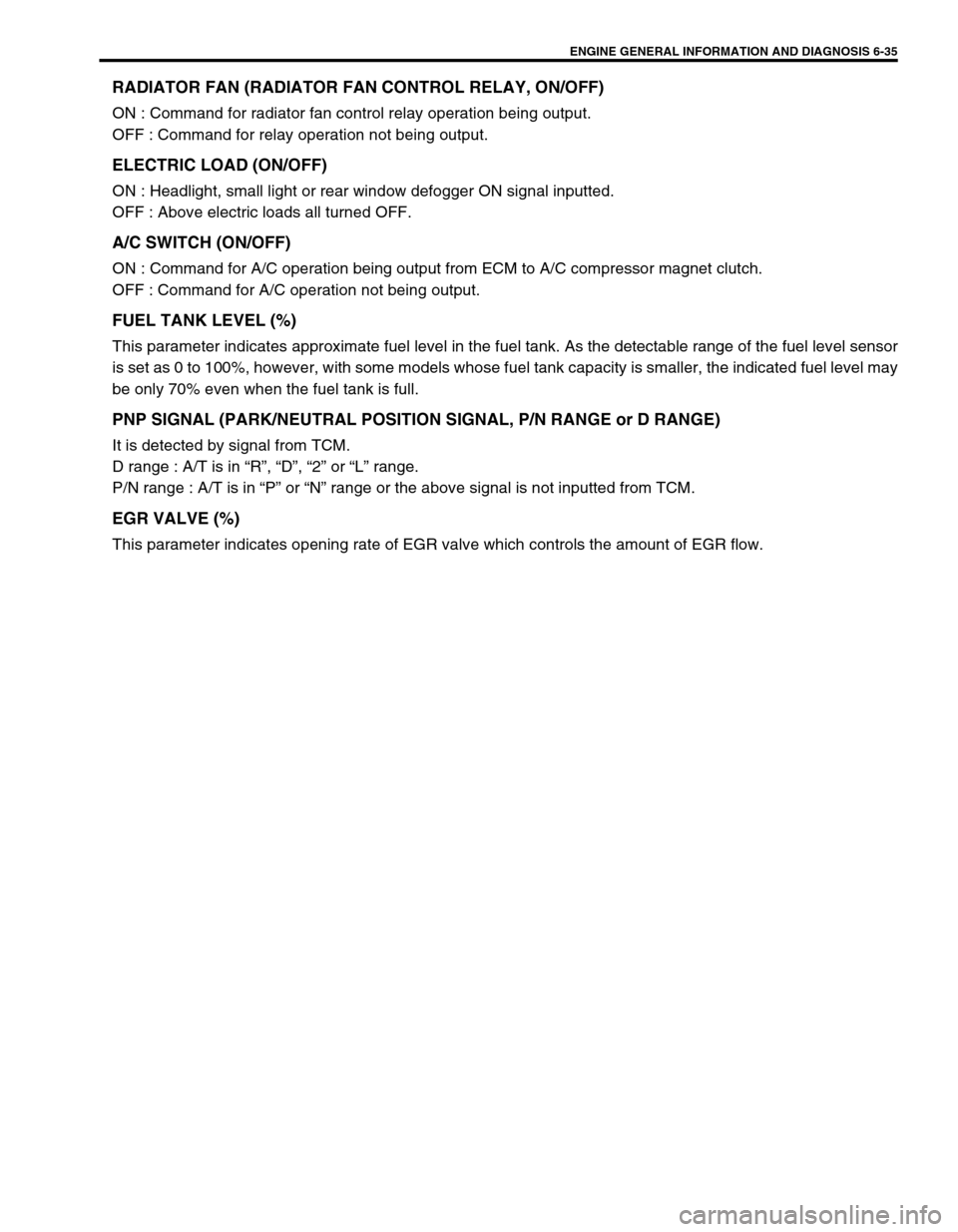
ENGINE GENERAL INFORMATION AND DIAGNOSIS 6-35
RADIATOR FAN (RADIATOR FAN CONTROL RELAY, ON/OFF)
ON : Command for radiator fan control relay operation being output.
OFF : Command for relay operation not being output.
ELECTRIC LOAD (ON/OFF)
ON : Headlight, small light or rear window defogger ON signal inputted.
OFF : Above electric loads all turned OFF.
A/C SWITCH (ON/OFF)
ON : Command for A/C operation being output from ECM to A/C compressor magnet clutch.
OFF : Command for A/C operation not being output.
FUEL TANK LEVEL (%)
This parameter indicates approximate fuel level in the fuel tank. As the detectable range of the fuel level sensor
is set as 0 to 100%, however, with some models whose fuel tank capacity is smaller, the indicated fuel level may
be only 70% even when the fuel tank is full.
PNP SIGNAL (PARK/NEUTRAL POSITION SIGNAL, P/N RANGE or D RANGE)
It is detected by signal from TCM.
D range : A/T is in “R”, “D”, “2” or “L” range.
P/N range : A/T is in “P” or “N” range or the above signal is not inputted from TCM.
EGR VALVE (%)
This parameter indicates opening rate of EGR valve which controls the amount of EGR flow.
Page 408 of 698
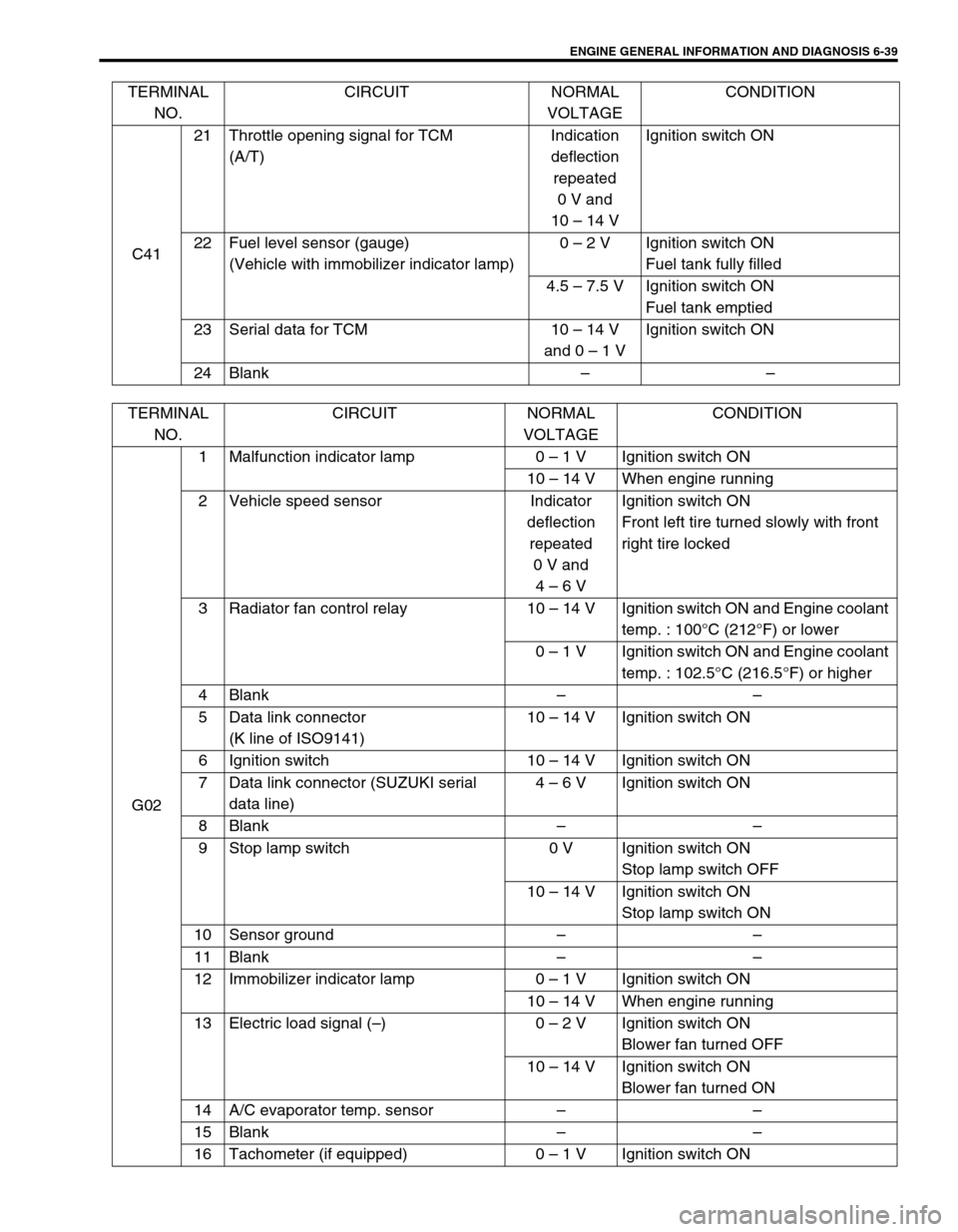
ENGINE GENERAL INFORMATION AND DIAGNOSIS 6-39
C4121 Throttle opening signal for TCM
(A/T)Indication
deflection
repeated
0 V and
10 – 14 VIgnition switch ON
22 Fuel level sensor (gauge)
(Vehicle with immobilizer indicator lamp)0 – 2 V Ignition switch ON
Fuel tank fully filled
4.5 – 7.5 V Ignition switch ON
Fuel tank emptied
23 Serial data for TCM 10 – 14 V
and 0 – 1 VIgnition switch ON
24 Blank–– TERMINAL
NO.CIRCUIT NORMAL
VOLTAGECONDITION
TERMINAL
NO.CIRCUIT NORMAL
VOLTAGECONDITION
G021 Malfunction indicator lamp 0 – 1 V Ignition switch ON
10 – 14 V When engine running
2 Vehicle speed sensor Indicator
deflection
repeated
0 V and
4 – 6 VIgnition switch ON
Front left tire turned slowly with front
right tire locked
3 Radiator fan control relay 10 – 14 V Ignition switch ON and Engine coolant
temp. : 100°C (212°F) or lower
0 – 1 V Ignition switch ON and Engine coolant
temp. : 102.5°C (216.5°F) or higher
4 Blank––
5 Data link connector
(K line of ISO9141)10 – 14 V Ignition switch ON
6 Ignition switch 10 – 14 V Ignition switch ON
7 Data link connector (SUZUKI serial
data line)4 – 6 V Ignition switch ON
8 Blank––
9 Stop lamp switch 0 V Ignition switch ON
Stop lamp switch OFF
10 – 14 V Ignition switch ON
Stop lamp switch ON
10 Sensor ground––
11 Blank––
12 Immobilizer indicator lamp 0 – 1 V Ignition switch ON
10 – 14 V When engine running
13 Electric load signal (–)0 – 2 V Ignition switch ON
Blower fan turned OFF
10 – 14 V Ignition switch ON
Blower fan turned ON
14 A/C evaporator temp. sensor––
15 Blank––
16 Tachometer (if equipped) 0 – 1 V Ignition switch ON
Page 411 of 698
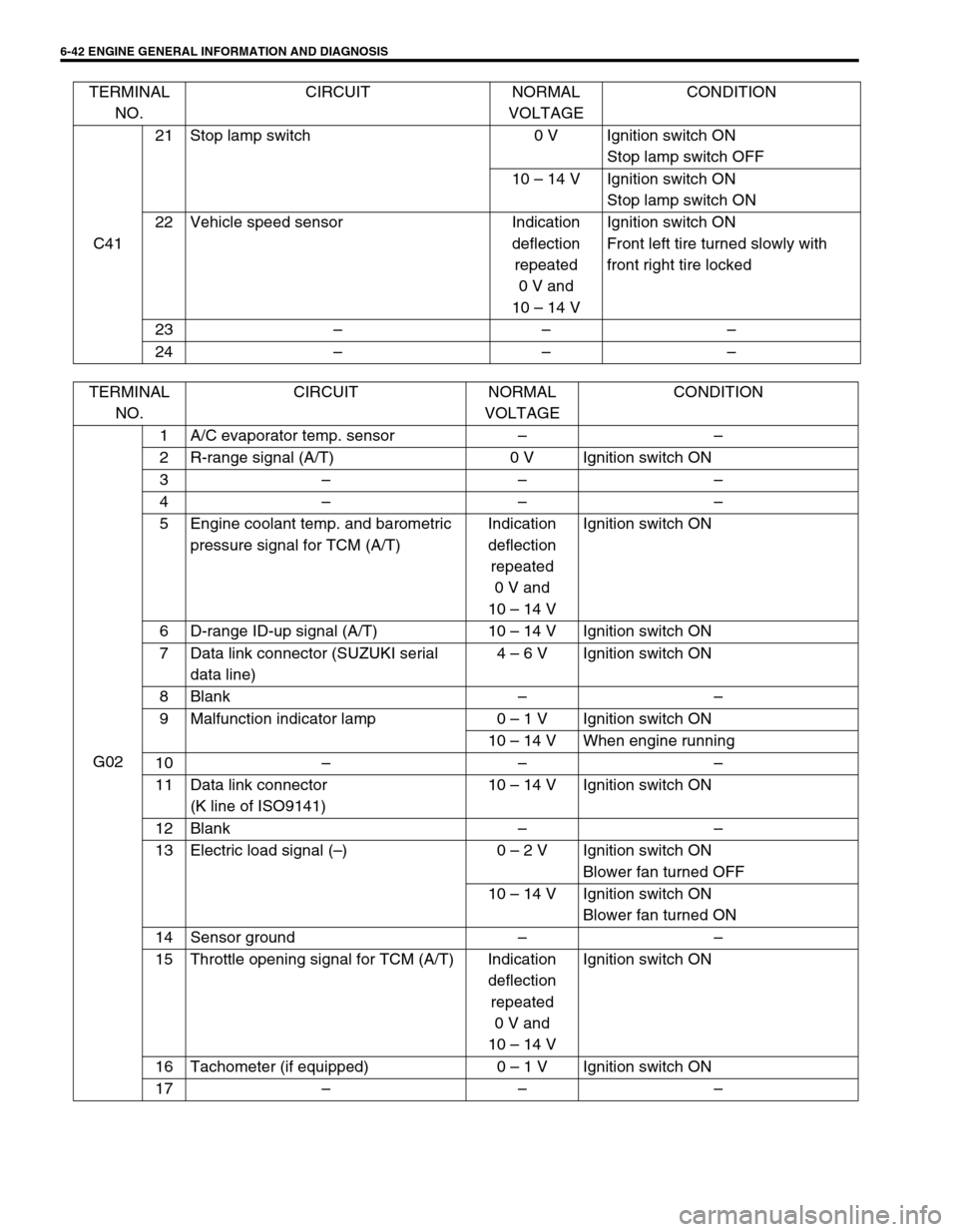
6-42 ENGINE GENERAL INFORMATION AND DIAGNOSIS
C4121 Stop lamp switch 0 V Ignition switch ON
Stop lamp switch OFF
10 – 14 V Ignition switch ON
Stop lamp switch ON
22 Vehicle speed sensor Indication
deflection
repeated
0 V and
10 – 14 VIgnition switch ON
Front left tire turned slowly with
front right tire locked
23–––
24––– TERMINAL
NO.CIRCUIT NORMAL
VOLTAGECONDITION
TERMINAL
NO.CIRCUIT NORMAL
VOLTAGECONDITION
G021 A/C evaporator temp. sensor––
2 R-range signal (A/T) 0 V Ignition switch ON
3–––
4–––
5 Engine coolant temp. and barometric
pressure signal for TCM (A/T)Indication
deflection
repeated
0 V and
10 – 14 VIgnition switch ON
6 D-range ID-up signal (A/T) 10 – 14 V Ignition switch ON
7 Data link connector (SUZUKI serial
data line)4 – 6 V Ignition switch ON
8Blank––
9 Malfunction indicator lamp 0 – 1 V Ignition switch ON
10 – 14 V When engine running
10–––
11 Data link connector
(K line of ISO9141)10 – 14 V Ignition switch ON
12 Blank––
13 Electric load signal (–)0 – 2 V Ignition switch ON
Blower fan turned OFF
10 – 14 V Ignition switch ON
Blower fan turned ON
14 Sensor ground––
15 Throttle opening signal for TCM (A/T) Indication
deflection
repeated
0 V and
10 – 14 VIgnition switch ON
16 Tachometer (if equipped) 0 – 1 V Ignition switch ON
17–––
Page 442 of 698
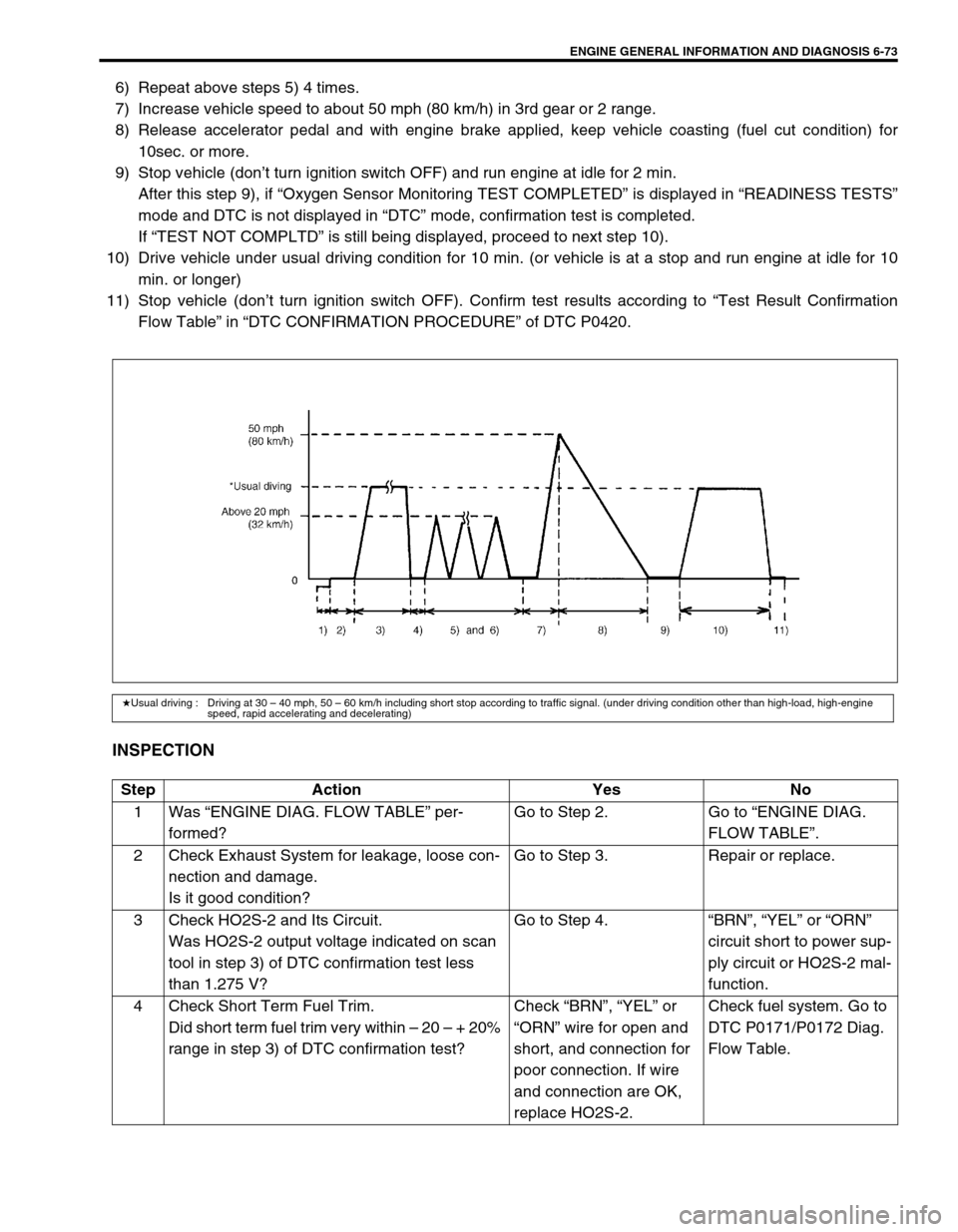
ENGINE GENERAL INFORMATION AND DIAGNOSIS 6-73
6) Repeat above steps 5) 4 times.
7) Increase vehicle speed to about 50 mph (80 km/h) in 3rd gear or 2 range.
8) Release accelerator pedal and with engine brake applied, keep vehicle coasting (fuel cut condition) for
10sec. or more.
9) Stop vehicle (don’t turn ignition switch OFF) and run engine at idle for 2 min.
After this step 9), if “Oxygen Sensor Monitoring TEST COMPLETED” is displayed in “READINESS TESTS”
mode and DTC is not displayed in “DTC” mode, confirmation test is completed.
If “TEST NOT COMPLTD” is still being displayed, proceed to next step 10).
10) Drive vehicle under usual driving condition for 10 min. (or vehicle is at a stop and run engine at idle for 10
min. or longer)
11) Stop vehicle (don’t turn ignition switch OFF). Confirm test results according to “Test Result Confirmation
Flow Table” in “DTC CONFIRMATION PROCEDURE” of DTC P0420.
INSPECTION
Usual driving : Driving at 30 – 40 mph, 50 – 60 km/h including short stop according to traffic signal. (under driving condition other than high-load, high-engine
speed, rapid accelerating and decelerating)
Step Action Yes No
1Was “ENGINE DIAG. FLOW TABLE” per-
formed?Go to Step 2. Go to “ENGINE DIAG.
FLOW TABLE”.
2 Check Exhaust System for leakage, loose con-
nection and damage.
Is it good condition?Go to Step 3. Repair or replace.
3 Check HO2S-2 and Its Circuit.
Was HO2S-2 output voltage indicated on scan
tool in step 3) of DTC confirmation test less
than 1.275 V?Go to Step 4.“BRN”, “YEL” or “ORN”
circuit short to power sup-
ply circuit or HO2S-2 mal-
function.
4 Check Short Term Fuel Trim.
Did short term fuel trim very within – 20 – + 20%
range in step 3) of DTC confirmation test?Check “BRN”, “YEL” or
“ORN” wire for open and
short, and connection for
poor connection. If wire
and connection are OK,
replace HO2S-2.Check fuel system. Go to
DTC P0171/P0172 Diag.
Flow Table.