engine SUZUKI SWIFT 2000 1.G SF310 Service Workshop Manual
[x] Cancel search | Manufacturer: SUZUKI, Model Year: 2000, Model line: SWIFT, Model: SUZUKI SWIFT 2000 1.GPages: 557, PDF Size: 14.35 MB
Page 399 of 557
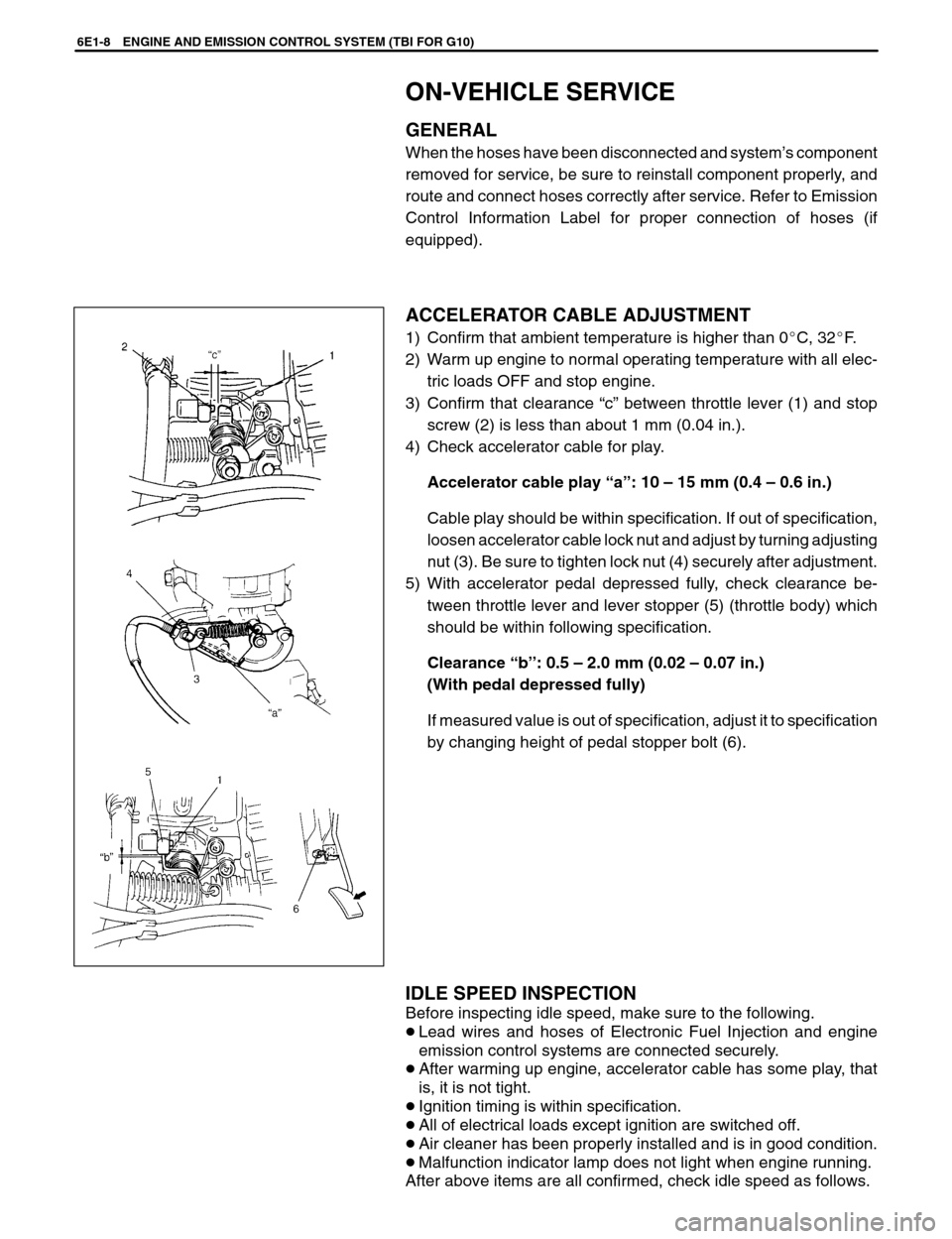
6E1-8 ENGINE AND EMISSION CONTROL SYSTEM (TBI FOR G10)
ON-VEHICLE SERVICE
GENERAL
When the hoses have been disconnected and system’s component
removed for service, be sure to reinstall component properly, and
route and connect hoses correctly after service. Refer to Emission
Control Information Label for proper connection of hoses (if
equipped).
ACCELERATOR CABLE ADJUSTMENT
1) Confirm that ambient temperature is higher than 0C, 32F.
2) Warm up engine to normal operating temperature with all elec-
tric loads OFF and stop engine.
3) Confirm that clearance “c” between throttle lever (1) and stop
screw (2) is less than about 1 mm (0.04 in.).
4) Check accelerator cable for play.
Accelerator cable play “a”: 10 – 15 mm (0.4 – 0.6 in.)
Cable play should be within specification. If out of specification,
loosen accelerator cable lock nut and adjust by turning adjusting
nut (3). Be sure to tighten lock nut (4) securely after adjustment.
5) With accelerator pedal depressed fully, check clearance be-
tween throttle lever and lever stopper (5) (throttle body) which
should be within following specification.
Clearance “b”: 0.5 – 2.0 mm (0.02 – 0.07 in.)
(With pedal depressed fully)
If measured value is out of specification, adjust it to specification
by changing height of pedal stopper bolt (6).
IDLE SPEED INSPECTION
Before inspecting idle speed, make sure to the following.
Lead wires and hoses of Electronic Fuel Injection and engine
emission control systems are connected securely.
After warming up engine, accelerator cable has some play, that
is, it is not tight.
Ignition timing is within specification.
All of electrical loads except ignition are switched off.
Air cleaner has been properly installed and is in good condition.
Malfunction indicator lamp does not light when engine running.
After above items are all confirmed, check idle speed as follows.
Page 400 of 557
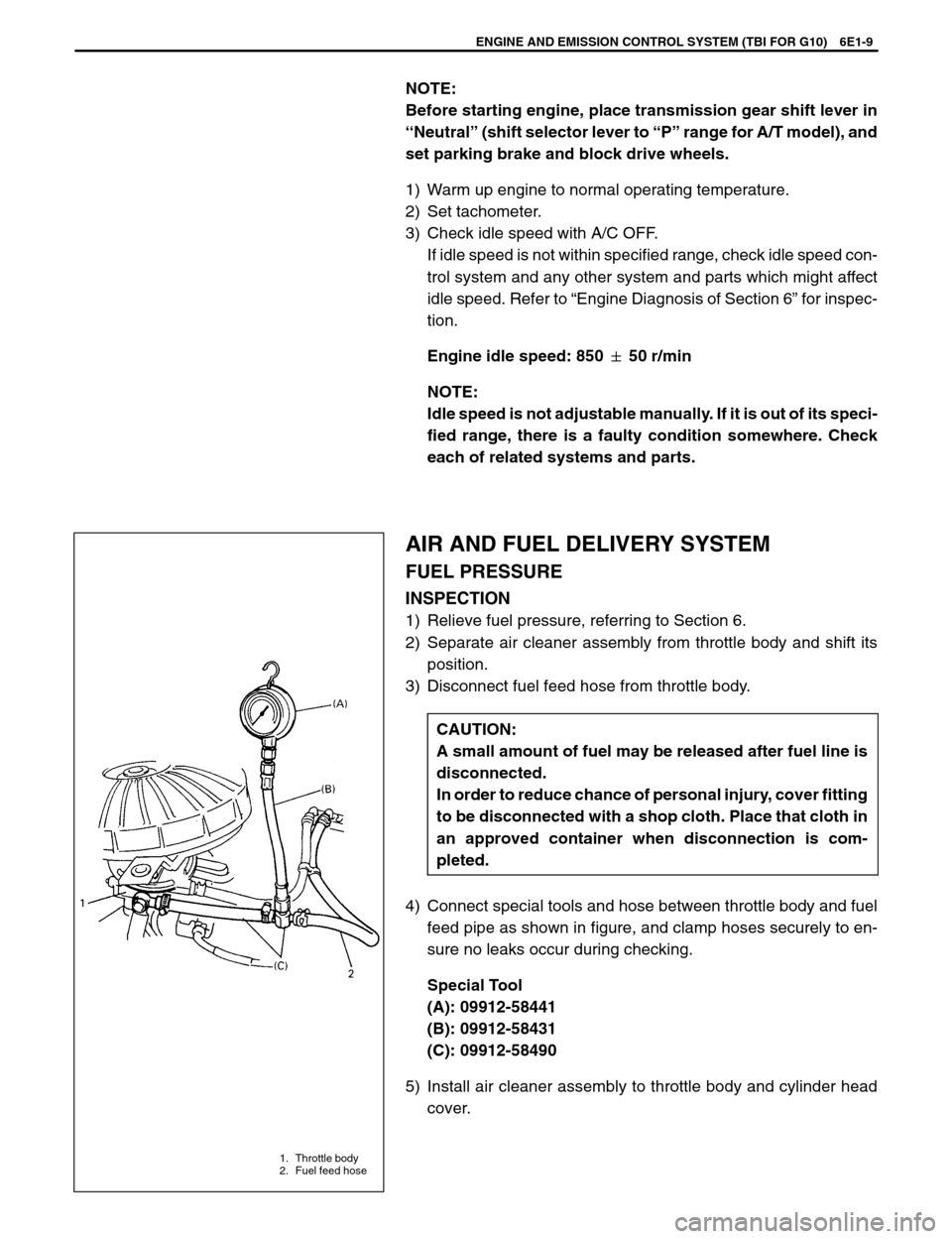
ENGINE AND EMISSION CONTROL SYSTEM (TBI FOR G10) 6E1-9
1. Throttle body
2. Fuel feed hose
NOTE:
Before starting engine, place transmission gear shift lever in
“Neutral” (shift selector lever to “P” range for A/T model), and
set parking brake and block drive wheels.
1) Warm up engine to normal operating temperature.
2) Set tachometer.
3) Check idle speed with A/C OFF.
If idle speed is not within specified range, check idle speed con-
trol system and any other system and parts which might affect
idle speed. Refer to “Engine Diagnosis of Section 6” for inspec-
tion.
Engine idle speed: 850 50 r/min
NOTE:
Idle speed is not adjustable manually. If it is out of its speci-
fied range, there is a faulty condition somewhere. Check
each of related systems and parts.
AIR AND FUEL DELIVERY SYSTEM
FUEL PRESSURE
INSPECTION
1) Relieve fuel pressure, referring to Section 6.
2) Separate air cleaner assembly from throttle body and shift its
position.
3) Disconnect fuel feed hose from throttle body.
CAUTION:
A small amount of fuel may be released after fuel line is
disconnected.
In order to reduce chance of personal injury, cover fitting
to be disconnected with a shop cloth. Place that cloth in
an approved container when disconnection is com-
pleted.
4) Connect special tools and hose between throttle body and fuel
feed pipe as shown in figure, and clamp hoses securely to en-
sure no leaks occur during checking.
Special Tool
(A): 09912-58441
(B): 09912-58431
(C): 09912-58490
5) Install air cleaner assembly to throttle body and cylinder head
cover.
Page 401 of 557
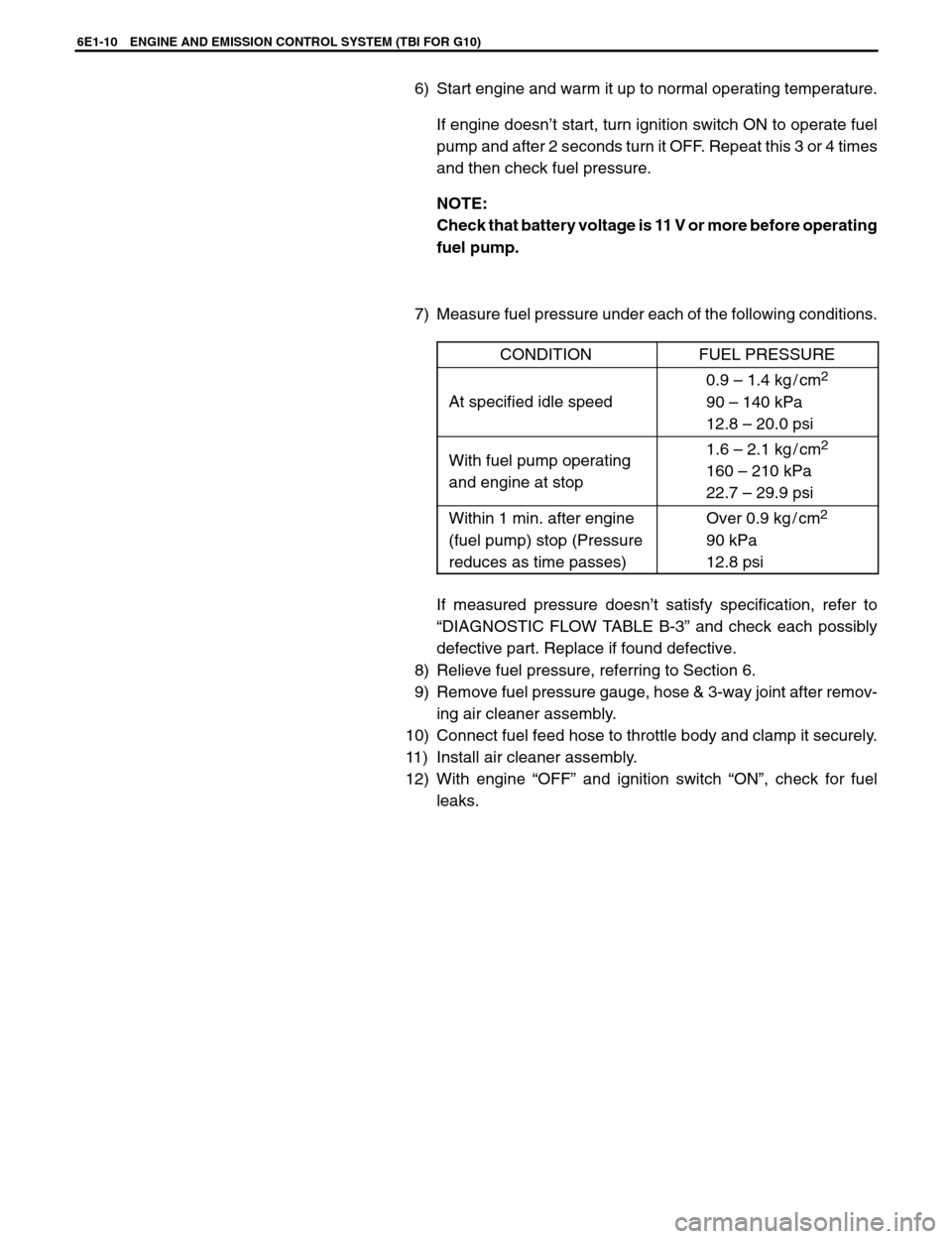
6E1-10 ENGINE AND EMISSION CONTROL SYSTEM (TBI FOR G10)
6) Start engine and warm it up to normal operating temperature.
If engine doesn’t start, turn ignition switch ON to operate fuel
pump and after 2 seconds turn it OFF. Repeat this 3 or 4 times
and then check fuel pressure.
NOTE:
Check that battery voltage is 11 V or more before operating
fuel pump.
7) Measure fuel pressure under each of the following conditions.
CONDITION
FUEL PRESSURE
At specified idle speed
0.9 – 1.4 kg / cm2
90 – 140 kPa
12.8 – 20.0 psi
With fuel pump operating
and engine at stop1.6 – 2.1 kg / cm2
160 – 210 kPa
22.7 – 29.9 psi
Within 1 min. after engine
(fuel pump) stop (Pressure
reduces as time passes)Over 0.9 kg / cm2
90 kPa
12.8 psi
If measured pressure doesn’t satisfy specification, refer to
“DIAGNOSTIC FLOW TABLE B-3” and check each possibly
defective part. Replace if found defective.
8) Relieve fuel pressure, referring to Section 6.
9) Remove fuel pressure gauge, hose & 3-way joint after remov-
ing air cleaner assembly.
10) Connect fuel feed hose to throttle body and clamp it securely.
11) Install air cleaner assembly.
12) With engine “OFF” and ignition switch “ON”, check for fuel
leaks.
Page 402 of 557
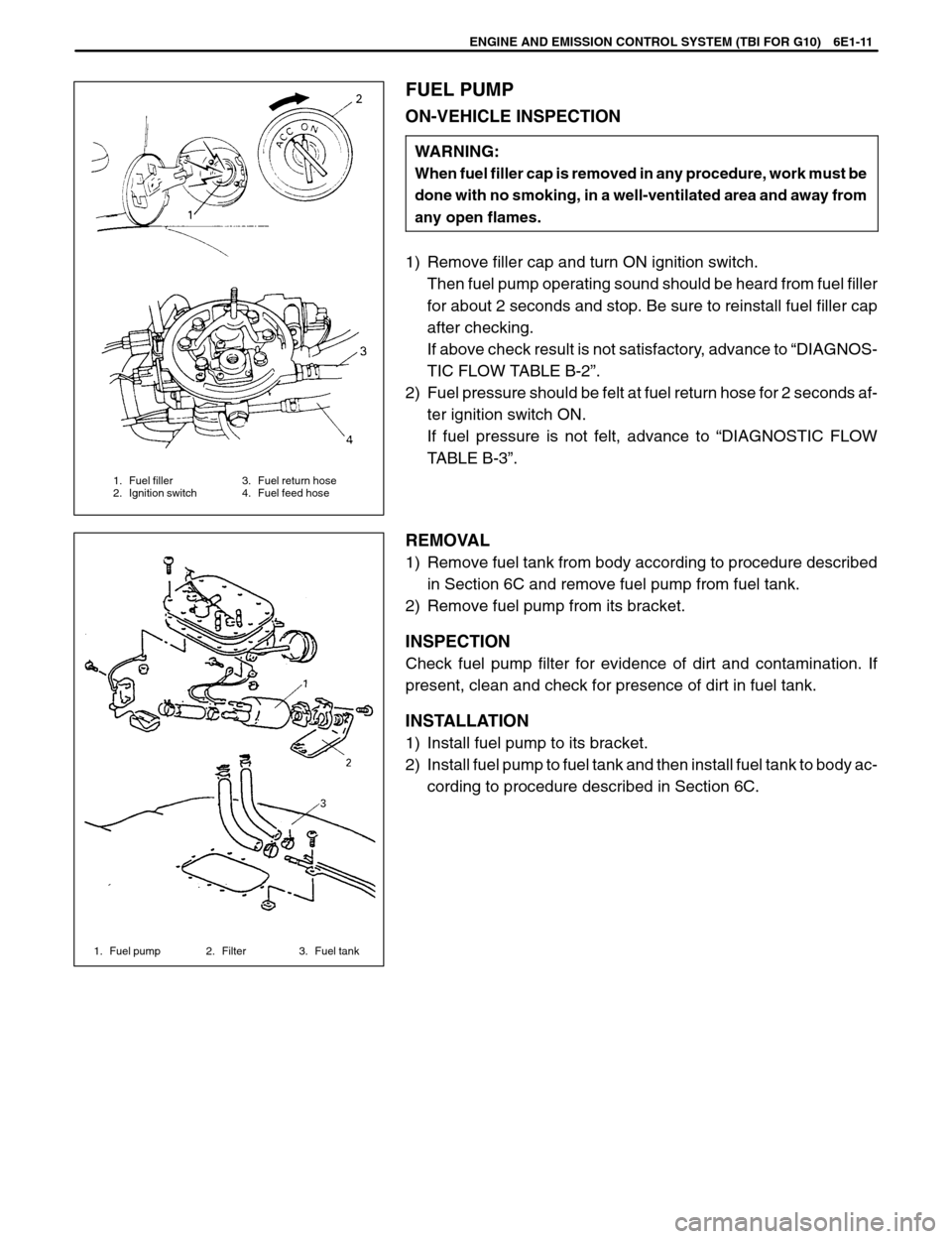
ENGINE AND EMISSION CONTROL SYSTEM (TBI FOR G10) 6E1-11
1. Fuel filler
2. Ignition switch3. Fuel return hose
4. Fuel feed hose
1. Fuel pump 2. Filter 3. Fuel tank
FUEL PUMP
ON-VEHICLE INSPECTION
WARNING:
When fuel filler cap is removed in any procedure, work must be
done with no smoking, in a well-ventilated area and away from
any open flames.
1) Remove filler cap and turn ON ignition switch.
Then fuel pump operating sound should be heard from fuel filler
for about 2 seconds and stop. Be sure to reinstall fuel filler cap
after checking.
If above check result is not satisfactory, advance to “DIAGNOS-
TIC FLOW TABLE B-2”.
2) Fuel pressure should be felt at fuel return hose for 2 seconds af-
ter ignition switch ON.
If fuel pressure is not felt, advance to “DIAGNOSTIC FLOW
TABLE B-3”.
REMOVAL
1) Remove fuel tank from body according to procedure described
in Section 6C and remove fuel pump from fuel tank.
2) Remove fuel pump from its bracket.
INSPECTION
Check fuel pump filter for evidence of dirt and contamination. If
present, clean and check for presence of dirt in fuel tank.
INSTALLATION
1) Install fuel pump to its bracket.
2) Install fuel pump to fuel tank and then install fuel tank to body ac-
cording to procedure described in Section 6C.
Page 403 of 557
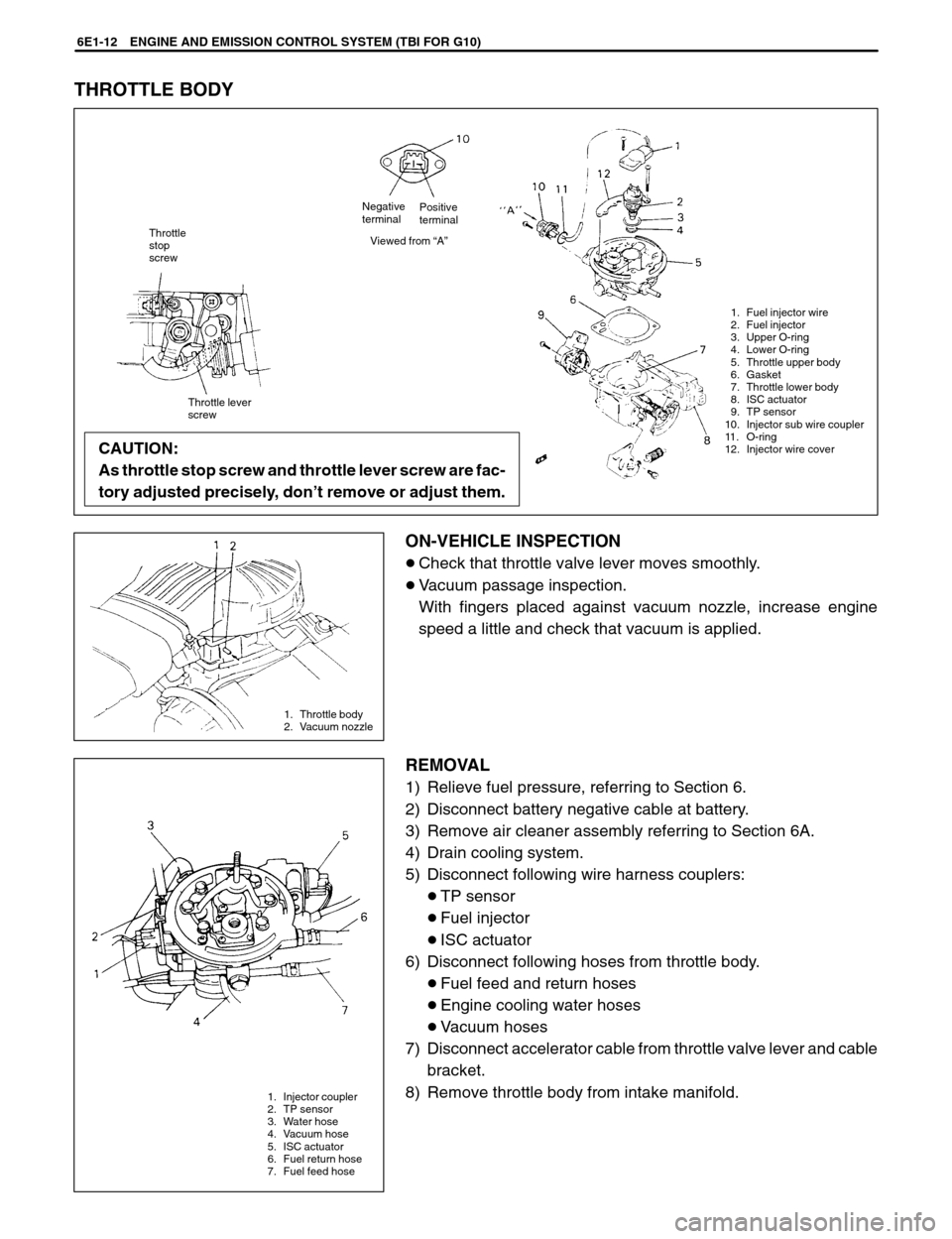
6E1-12 ENGINE AND EMISSION CONTROL SYSTEM (TBI FOR G10)
1. Fuel injector wire
2. Fuel injector
3. Upper O-ring
4. Lower O-ring
5. Throttle upper body
6. Gasket
7. Throttle lower body
8. ISC actuator
9. TP sensor
10. Injector sub wire coupler
11. O-ring
12. Injector wire cover
CAUTION:
As throttle stop screw and throttle lever screw are fac-
tory adjusted precisely, don’t remove or adjust them.
Throttle
stop
screw
Throttle lever
screwPositive
terminal Negative
terminal
Viewed from “A”
1. Throttle body
2. Vacuum nozzle
1. Injector coupler
2. TP sensor
3. Water hose
4. Vacuum hose
5. ISC actuator
6. Fuel return hose
7. Fuel feed hose
THROTTLE BODY
ON-VEHICLE INSPECTION
Check that throttle valve lever moves smoothly.
Vacuum passage inspection.
With fingers placed against vacuum nozzle, increase engine
speed a little and check that vacuum is applied.
REMOVAL
1) Relieve fuel pressure, referring to Section 6.
2) Disconnect battery negative cable at battery.
3) Remove air cleaner assembly referring to Section 6A.
4) Drain cooling system.
5) Disconnect following wire harness couplers:
TP sensor
Fuel injector
ISC actuator
6) Disconnect following hoses from throttle body.
Fuel feed and return hoses
Engine cooling water hoses
Vacuum hoses
7) Disconnect accelerator cable from throttle valve lever and cable
bracket.
8) Remove throttle body from intake manifold.
Page 404 of 557
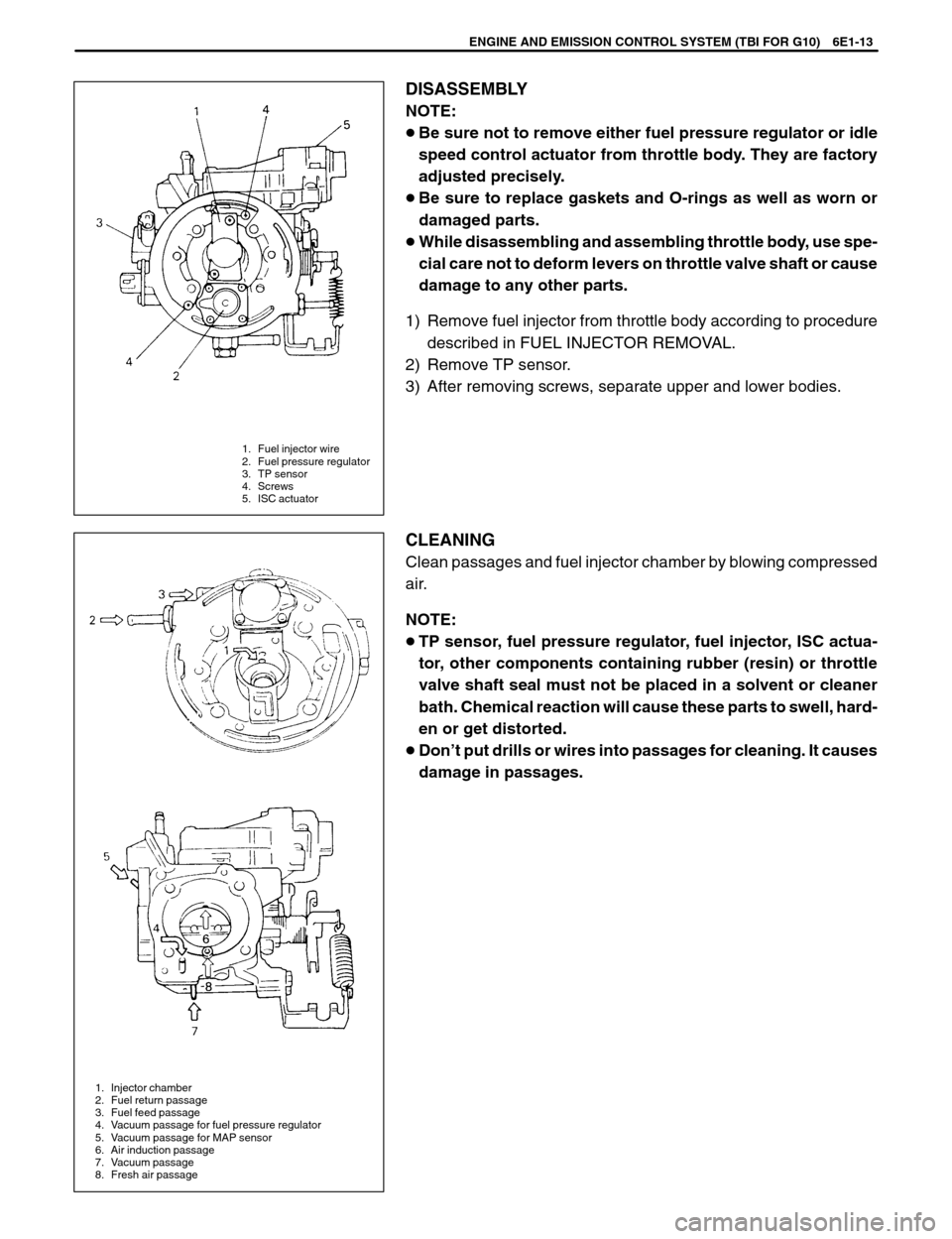
ENGINE AND EMISSION CONTROL SYSTEM (TBI FOR G10) 6E1-13
1. Fuel injector wire
2. Fuel pressure regulator
3. TP sensor
4. Screws
5. ISC actuator
1. Injector chamber
2. Fuel return passage
3. Fuel feed passage
4. Vacuum passage for fuel pressure regulator
5. Vacuum passage for MAP sensor
6. Air induction passage
7. Vacuum passage
8. Fresh air passage
DISASSEMBLY
NOTE:
Be sure not to remove either fuel pressure regulator or idle
speed control actuator from throttle body. They are factory
adjusted precisely.
Be sure to replace gaskets and O-rings as well as worn or
damaged parts.
While disassembling and assembling throttle body, use spe-
cial care not to deform levers on throttle valve shaft or cause
damage to any other parts.
1) Remove fuel injector from throttle body according to procedure
described in FUEL INJECTOR REMOVAL.
2) Remove TP sensor.
3) After removing screws, separate upper and lower bodies.
CLEANING
Clean passages and fuel injector chamber by blowing compressed
air.
NOTE:
TP sensor, fuel pressure regulator, fuel injector, ISC actua-
tor, other components containing rubber (resin) or throttle
valve shaft seal must not be placed in a solvent or cleaner
bath. Chemical reaction will cause these parts to swell, hard-
en or get distorted.
Don’t put drills or wires into passages for cleaning. It causes
damage in passages.
Page 405 of 557
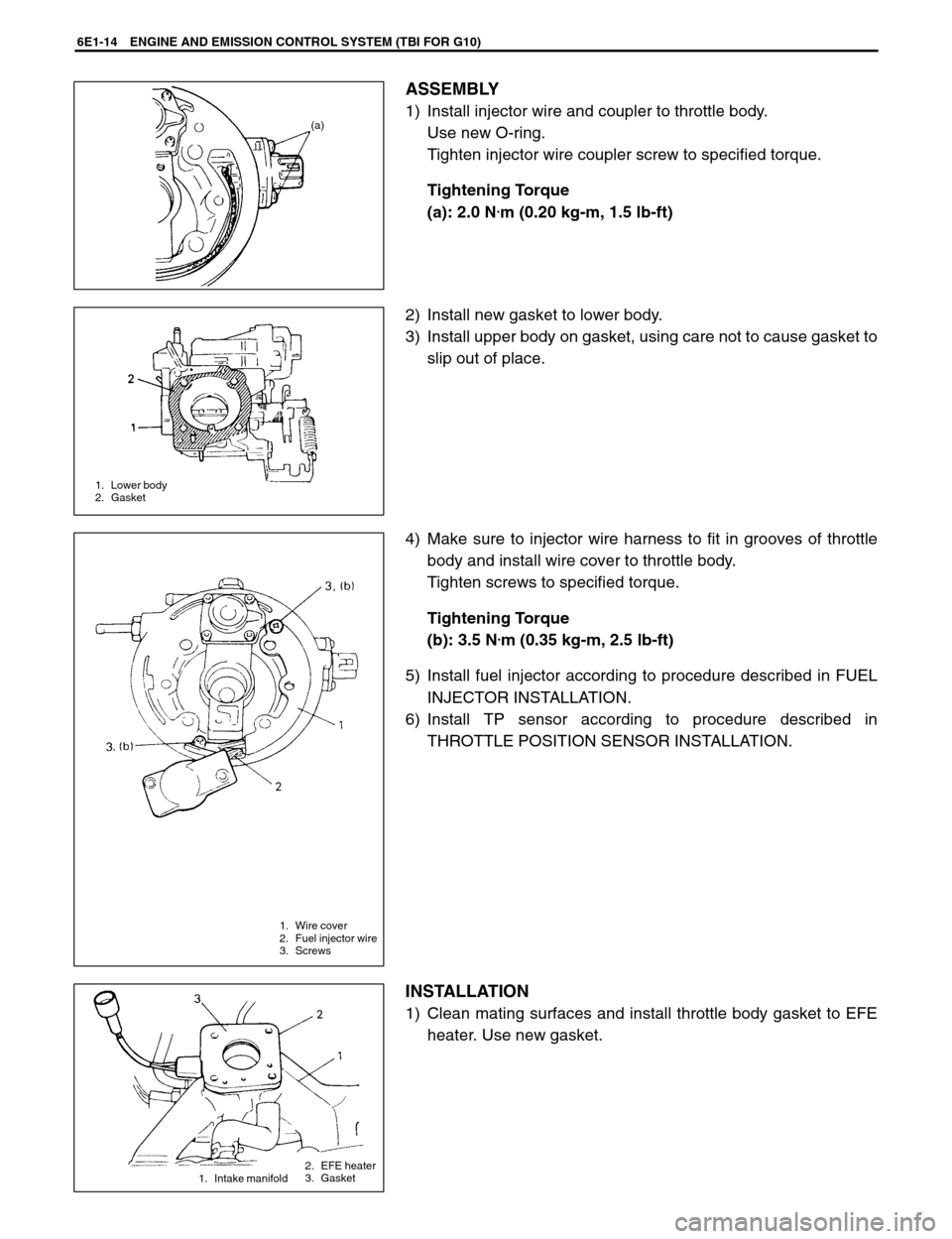
6E1-14 ENGINE AND EMISSION CONTROL SYSTEM (TBI FOR G10)
(a)
1. Lower body
2. Gasket
1. Wire cover
2. Fuel injector wire
3. Screws
2. EFE heater
3. Gasket
1. Intake manifold
ASSEMBLY
1) Install injector wire and coupler to throttle body.
Use new O-ring.
Tighten injector wire coupler screw to specified torque.
Tightening Torque
(a): 2.0 N
.m (0.20 kg-m, 1.5 lb-ft)
2) Install new gasket to lower body.
3) Install upper body on gasket, using care not to cause gasket to
slip out of place.
4) Make sure to injector wire harness to fit in grooves of throttle
body and install wire cover to throttle body.
Tighten screws to specified torque.
Tightening Torque
(b): 3.5 N
.m (0.35 kg-m, 2.5 lb-ft)
5) Install fuel injector according to procedure described in FUEL
INJECTOR INSTALLATION.
6) Install TP sensor according to procedure described in
THROTTLE POSITION SENSOR INSTALLATION.
INSTALLATION
1) Clean mating surfaces and install throttle body gasket to EFE
heater. Use new gasket.
Page 406 of 557
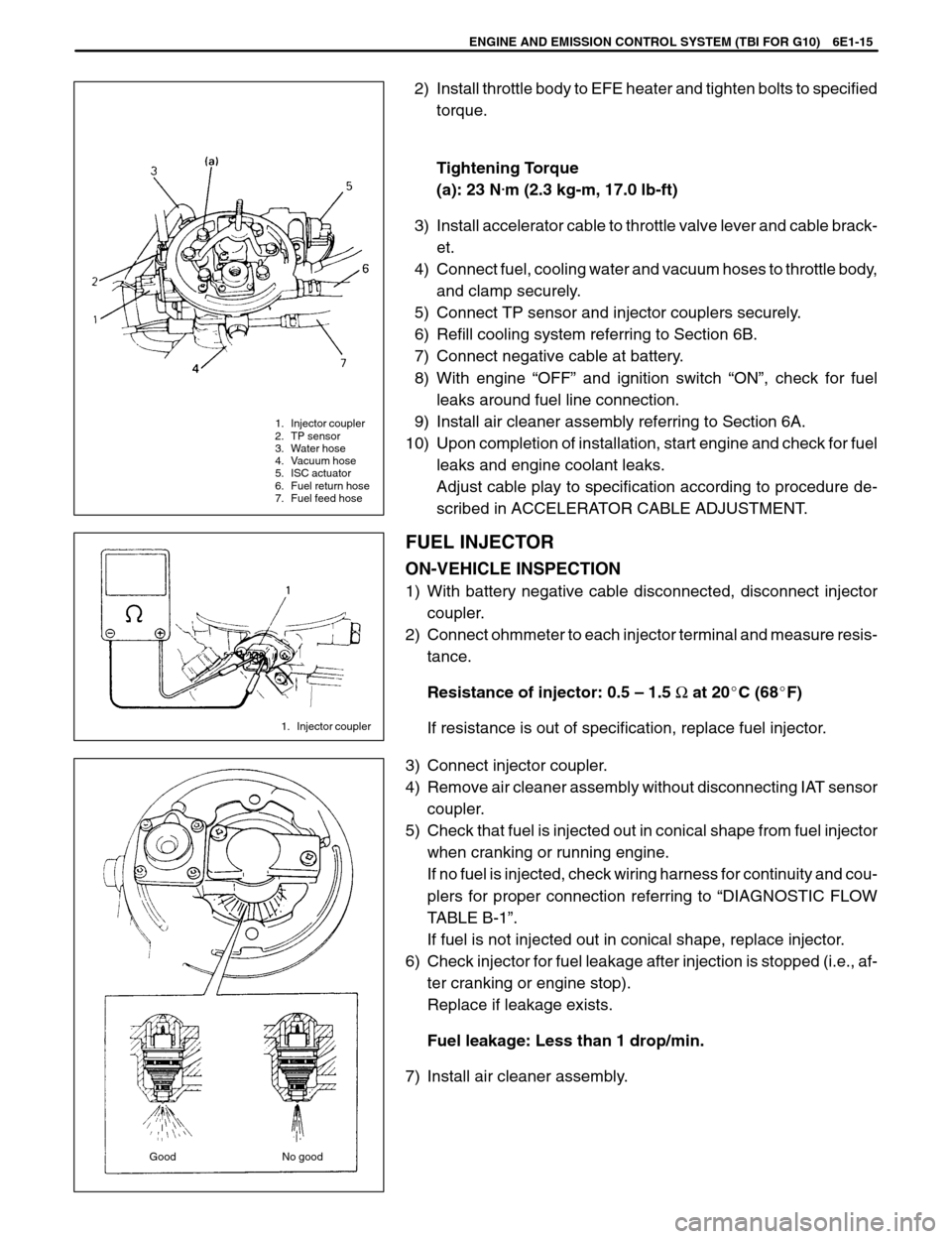
ENGINE AND EMISSION CONTROL SYSTEM (TBI FOR G10) 6E1-15
1. Injector coupler
2. TP sensor
3. Water hose
4. Vacuum hose
5. ISC actuator
6. Fuel return hose
7. Fuel feed hose
1. Injector coupler
Good No good
2) Install throttle body to EFE heater and tighten bolts to specified
torque.
Tightening Torque
(a): 23 N
.m (2.3 kg-m, 17.0 lb-ft)
3) Install accelerator cable to throttle valve lever and cable brack-
et.
4) Connect fuel, cooling water and vacuum hoses to throttle body,
and clamp securely.
5) Connect TP sensor and injector couplers securely.
6) Refill cooling system referring to Section 6B.
7) Connect negative cable at battery.
8) With engine “OFF” and ignition switch “ON”, check for fuel
leaks around fuel line connection.
9) Install air cleaner assembly referring to Section 6A.
10) Upon completion of installation, start engine and check for fuel
leaks and engine coolant leaks.
Adjust cable play to specification according to procedure de-
scribed in ACCELERATOR CABLE ADJUSTMENT.
FUEL INJECTOR
ON-VEHICLE INSPECTION
1) With battery negative cable disconnected, disconnect injector
coupler.
2) Connect ohmmeter to each injector terminal and measure resis-
tance.
Resistance of injector: 0.5 – 1.5 Ω at 20C (68F)
If resistance is out of specification, replace fuel injector.
3) Connect injector coupler.
4) Remove air cleaner assembly without disconnecting IAT sensor
coupler.
5) Check that fuel is injected out in conical shape from fuel injector
when cranking or running engine.
If no fuel is injected, check wiring harness for continuity and cou-
plers for proper connection referring to “DIAGNOSTIC FLOW
TABLE B-1”.
If fuel is not injected out in conical shape, replace injector.
6) Check injector for fuel leakage after injection is stopped (i.e., af-
ter cranking or engine stop).
Replace if leakage exists.
Fuel leakage: Less than 1 drop/min.
7) Install air cleaner assembly.
Page 407 of 557
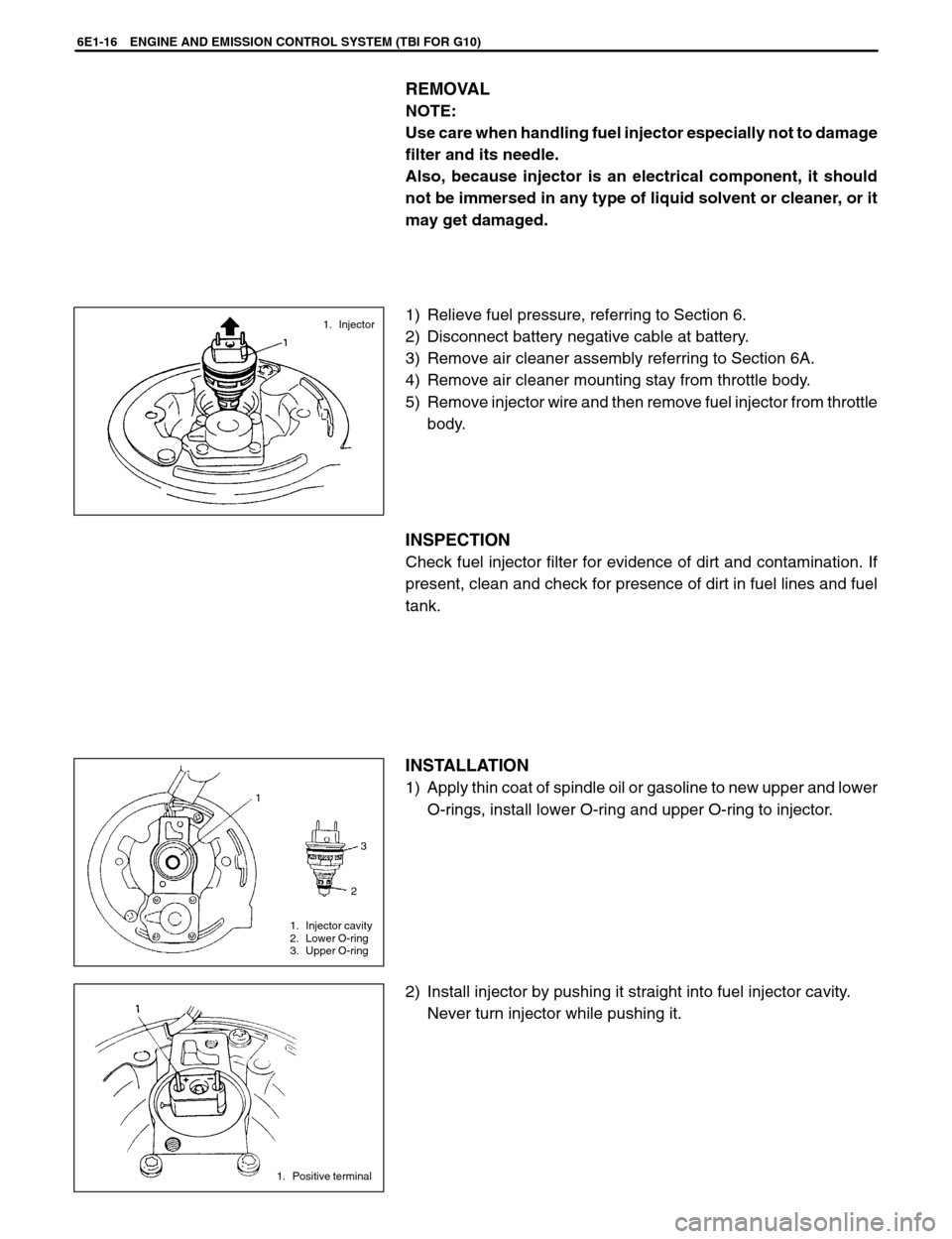
6E1-16 ENGINE AND EMISSION CONTROL SYSTEM (TBI FOR G10)
1. Injector
1
3
2
1. Injector cavity
2. Lower O-ring
3. Upper O-ring
1. Positive terminal
REMOVAL
NOTE:
Use care when handling fuel injector especially not to damage
filter and its needle.
Also, because injector is an electrical component, it should
not be immersed in any type of liquid solvent or cleaner, or it
may get damaged.
1) Relieve fuel pressure, referring to Section 6.
2) Disconnect battery negative cable at battery.
3) Remove air cleaner assembly referring to Section 6A.
4) Remove air cleaner mounting stay from throttle body.
5) Remove injector wire and then remove fuel injector from throttle
body.
INSPECTION
Check fuel injector filter for evidence of dirt and contamination. If
present, clean and check for presence of dirt in fuel lines and fuel
tank.
INSTALLATION
1) Apply thin coat of spindle oil or gasoline to new upper and lower
O-rings, install lower O-ring and upper O-ring to injector.
2) Install injector by pushing it straight into fuel injector cavity.
Never turn injector while pushing it.
Page 408 of 557
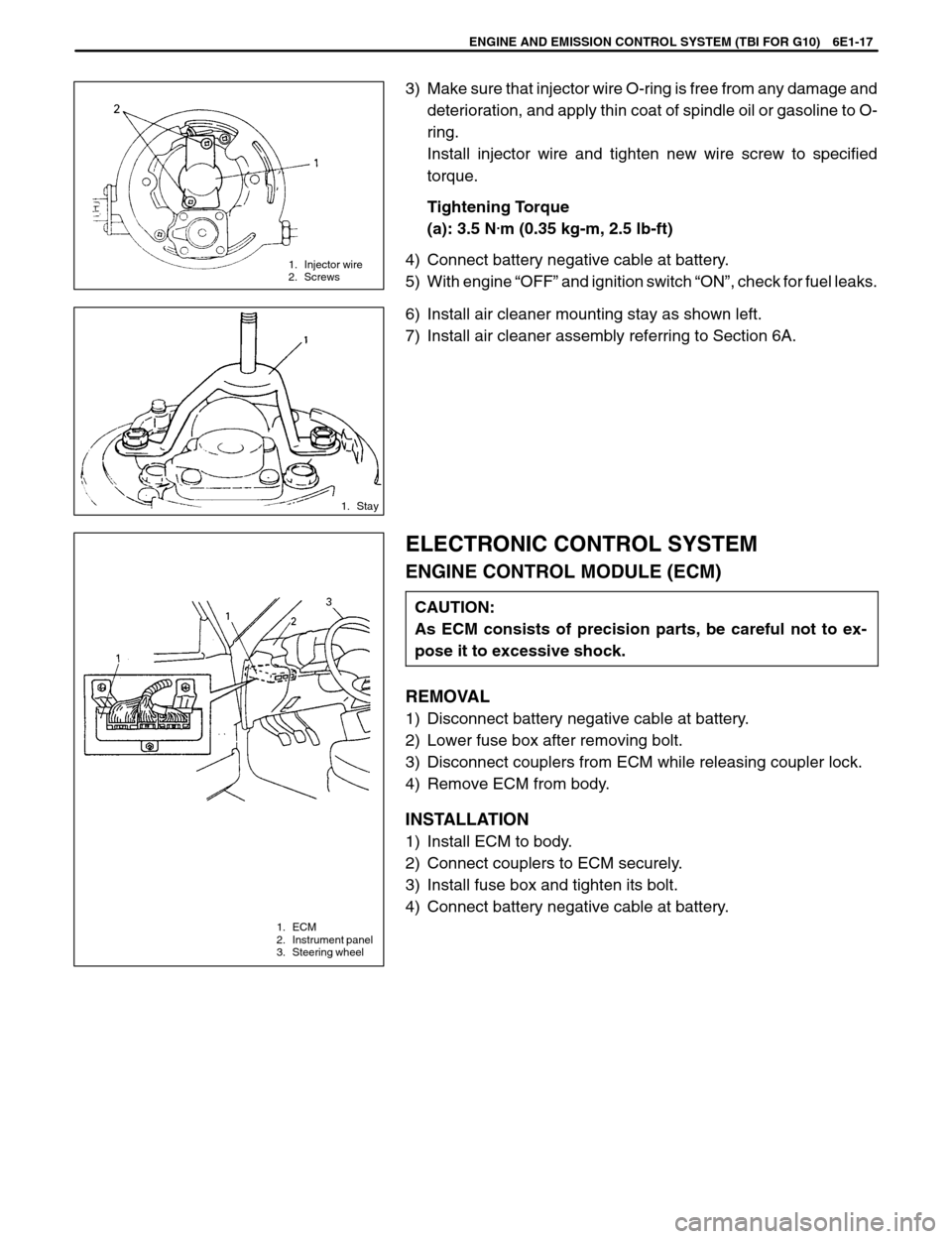
ENGINE AND EMISSION CONTROL SYSTEM (TBI FOR G10) 6E1-17
1. ECM
2. Instrument panel
3. Steering wheel
1. Injector wire
2. Screws
1. Stay
3) Make sure that injector wire O-ring is free from any damage and
deterioration, and apply thin coat of spindle oil or gasoline to O-
ring.
Install injector wire and tighten new wire screw to specified
torque.
Tightening Torque
(a): 3.5 N
.m (0.35 kg-m, 2.5 lb-ft)
4) Connect battery negative cable at battery.
5) With engine “OFF” and ignition switch “ON”, check for fuel leaks.
6) Install air cleaner mounting stay as shown left.
7) Install air cleaner assembly referring to Section 6A.
ELECTRONIC CONTROL SYSTEM
ENGINE CONTROL MODULE (ECM)
CAUTION:
As ECM consists of precision parts, be careful not to ex-
pose it to excessive shock.
REMOVAL
1) Disconnect battery negative cable at battery.
2) Lower fuse box after removing bolt.
3) Disconnect couplers from ECM while releasing coupler lock.
4) Remove ECM from body.
INSTALLATION
1) Install ECM to body.
2) Connect couplers to ECM securely.
3) Install fuse box and tighten its bolt.
4) Connect battery negative cable at battery.