Head SUZUKI SWIFT 2000 1.G SF310 Service Manual PDF
[x] Cancel search | Manufacturer: SUZUKI, Model Year: 2000, Model line: SWIFT, Model: SUZUKI SWIFT 2000 1.GPages: 557, PDF Size: 14.35 MB
Page 356 of 557
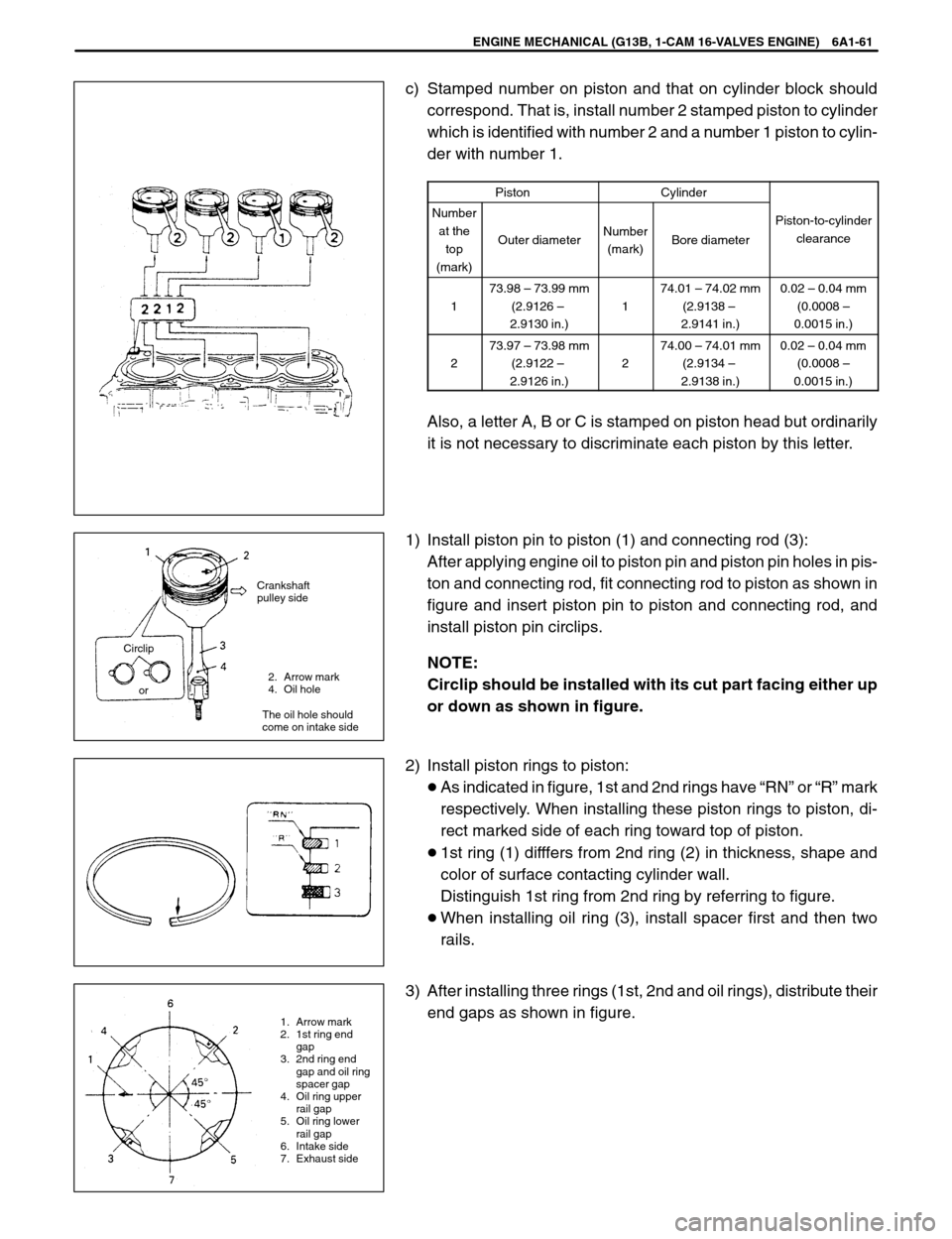
2. Arrow mark
4. Oil hole
The oil hole should
come on intake side
1. Arrow mark
2. 1st ring end
gap
3. 2nd ring end
gap and oil ring
spacer gap
4. Oil ring upper
rail gap
5. Oil ring lower
rail gap
6. Intake side
7. Exhaust side Crankshaft
pulley side
Circlip
or
ENGINE MECHANICAL (G13B, 1-CAM 16-VALVES ENGINE) 6A1-61
c) Stamped number on piston and that on cylinder block should
correspond. That is, install number 2 stamped piston to cylinder
which is identified with number 2 and a number 1 piston to cylin-
der with number 1.
PistonCylinder
Number
at the
top
(mark)
Outer diameterNumber
(mark)Bore diameter
Piston-to-cylinder
clearance
1
73.98 – 73.99 mm
(2.9126 –
2.9130 in.)
1
74.01 – 74.02 mm
(2.9138 –
2.9141 in.)0.02 – 0.04 mm
(0.0008 –
0.0015 in.)
2
73.97 – 73.98 mm
(2.9122 –
2.9126 in.)
2
74.00 – 74.01 mm
(2.9134 –
2.9138 in.)0.02 – 0.04 mm
(0.0008 –
0.0015 in.)
Also, a letter A, B or C is stamped on piston head but ordinarily
it is not necessary to discriminate each piston by this letter.
1) Install piston pin to piston (1) and connecting rod (3):
After applying engine oil to piston pin and piston pin holes in pis-
ton and connecting rod, fit connecting rod to piston as shown in
figure and insert piston pin to piston and connecting rod, and
install piston pin circlips.
NOTE:
Circlip should be installed with its cut part facing either up
or down as shown in figure.
2) Install piston rings to piston:
As indicated in figure, 1st and 2nd rings have “RN” or “R” mark
respectively. When installing these piston rings to piston, di-
rect marked side of each ring toward top of piston.
1st ring (1) difffers from 2nd ring (2) in thickness, shape and
color of surface contacting cylinder wall.
Distinguish 1st ring from 2nd ring by referring to figure.
When installing oil ring (3), install spacer first and then two
rails.
3) After installing three rings (1st, 2nd and oil rings), distribute their
end gaps as shown in figure.
Page 357 of 557
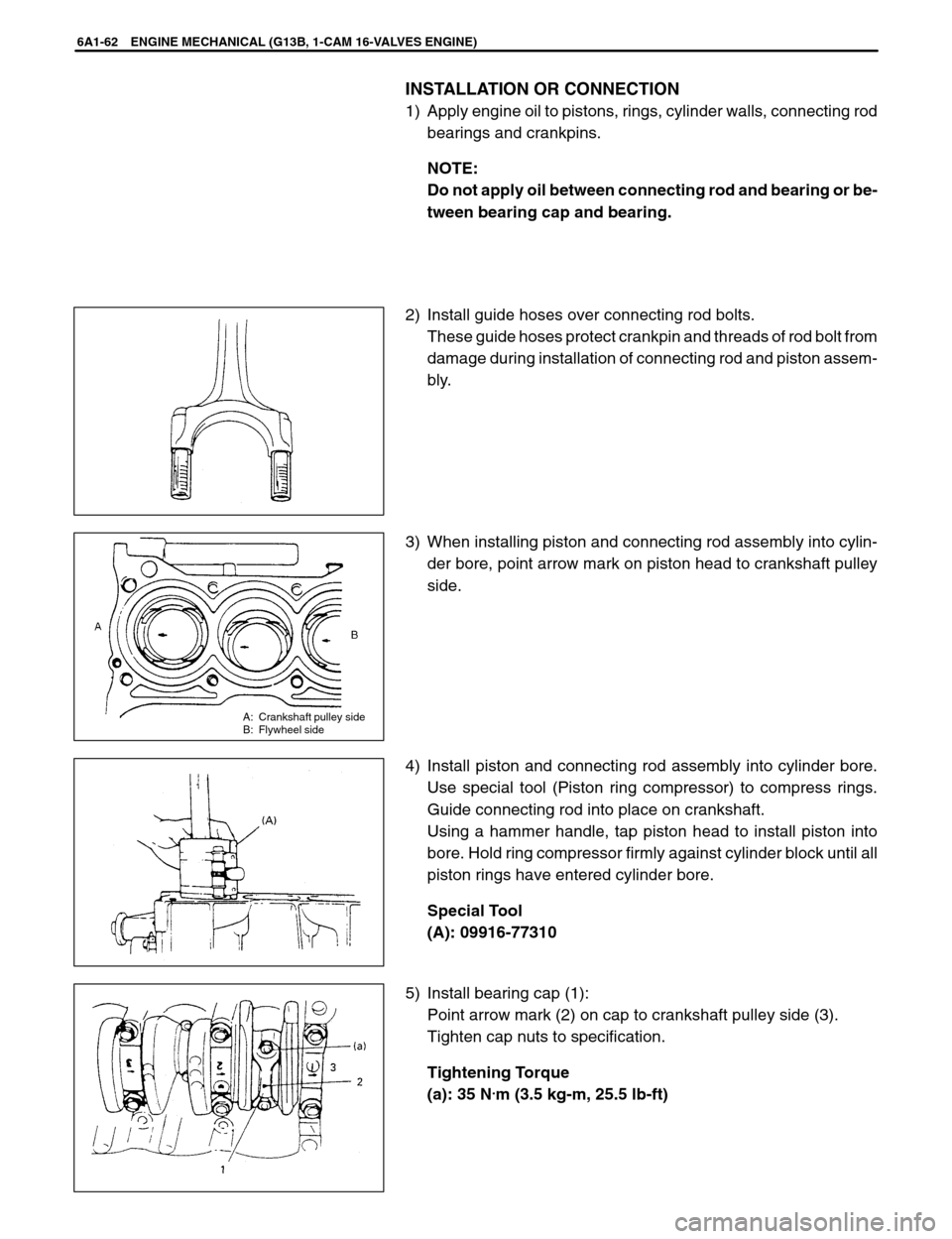
A: Crankshaft pulley side
B: Flywheel side
6A1-62 ENGINE MECHANICAL (G13B, 1-CAM 16-VALVES ENGINE)
INSTALLATION OR CONNECTION
1) Apply engine oil to pistons, rings, cylinder walls, connecting rod
bearings and crankpins.
NOTE:
Do not apply oil between connecting rod and bearing or be-
tween bearing cap and bearing.
2) Install guide hoses over connecting rod bolts.
These guide hoses protect crankpin and threads of rod bolt from
damage during installation of connecting rod and piston assem-
bly.
3) When installing piston and connecting rod assembly into cylin-
der bore, point arrow mark on piston head to crankshaft pulley
side.
4) Install piston and connecting rod assembly into cylinder bore.
Use special tool (Piston ring compressor) to compress rings.
Guide connecting rod into place on crankshaft.
Using a hammer handle, tap piston head to install piston into
bore. Hold ring compressor firmly against cylinder block until all
piston rings have entered cylinder bore.
Special Tool
(A): 09916-77310
5) Install bearing cap (1):
Point arrow mark (2) on cap to crankshaft pulley side (3).
Tighten cap nuts to specification.
Tightening Torque
(a): 35 N
.m (3.5 kg-m, 25.5 lb-ft)
Page 364 of 557
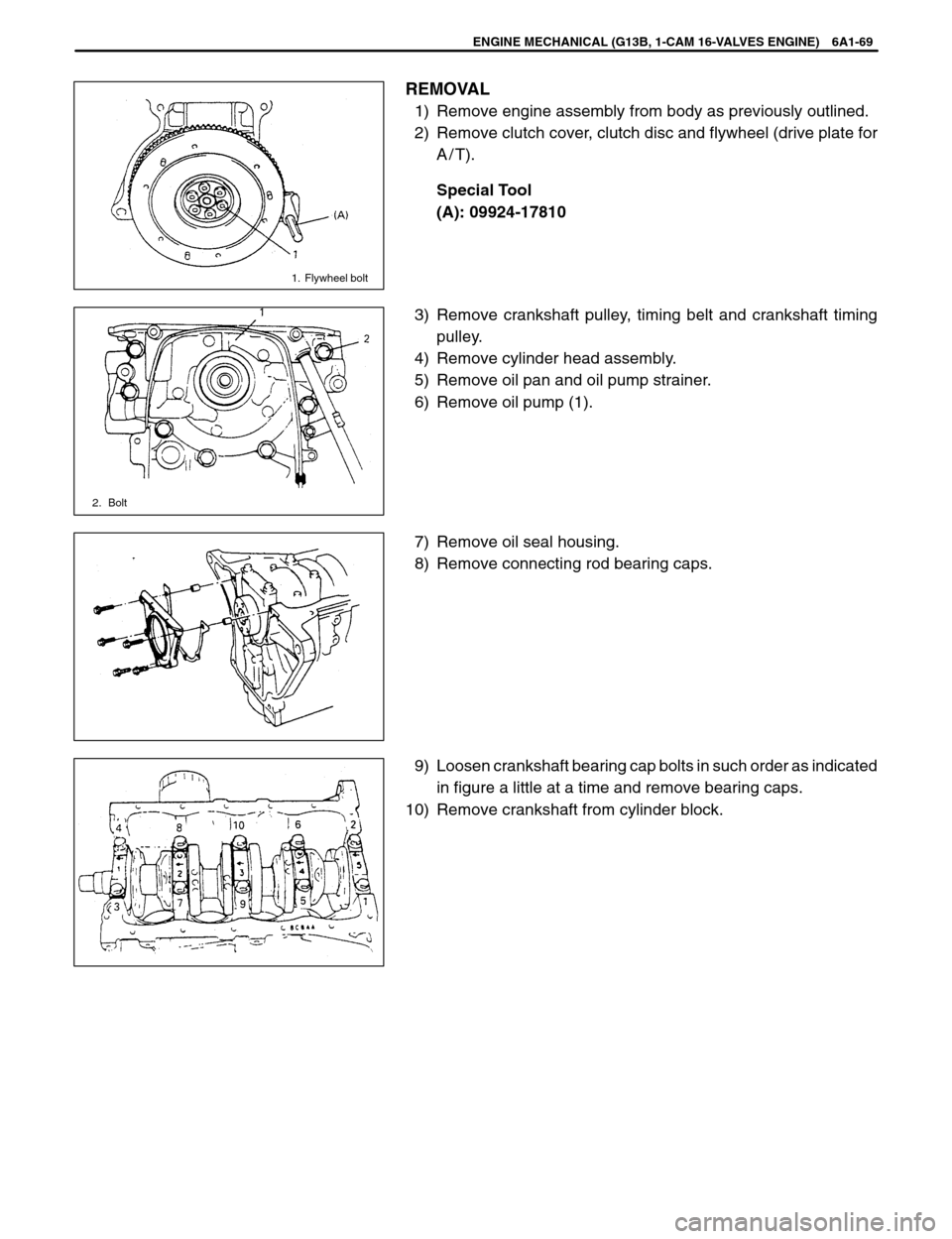
1. Flywheel bolt
2. Bolt
ENGINE MECHANICAL (G13B, 1-CAM 16-VALVES ENGINE) 6A1-69
REMOVAL
1) Remove engine assembly from body as previously outlined.
2) Remove clutch cover, clutch disc and flywheel (drive plate for
A / T).
Special Tool
(A): 09924-17810
3) Remove crankshaft pulley, timing belt and crankshaft timing
pulley.
4) Remove cylinder head assembly.
5) Remove oil pan and oil pump strainer.
6) Remove oil pump (1).
7) Remove oil seal housing.
8) Remove connecting rod bearing caps.
9) Loosen crankshaft bearing cap bolts in such order as indicated
in figure a little at a time and remove bearing caps.
10) Remove crankshaft from cylinder block.
Page 374 of 557
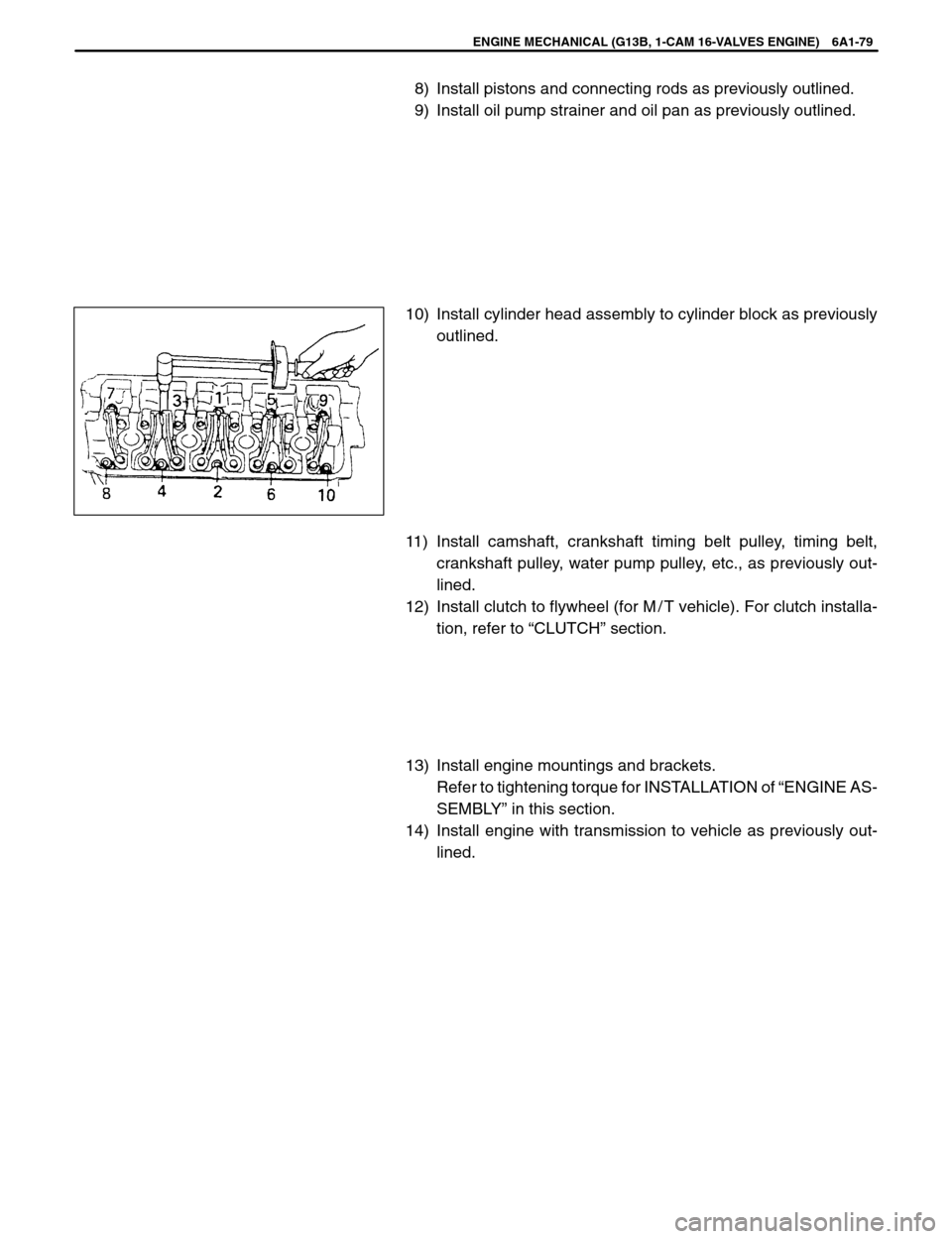
ENGINE MECHANICAL (G13B, 1-CAM 16-VALVES ENGINE) 6A1-79
8) Install pistons and connecting rods as previously outlined.
9) Install oil pump strainer and oil pan as previously outlined.
10) Install cylinder head assembly to cylinder block as previously
outlined.
11) Install camshaft, crankshaft timing belt pulley, timing belt,
crankshaft pulley, water pump pulley, etc., as previously out-
lined.
12) Install clutch to flywheel (for M / T vehicle). For clutch installa-
tion, refer to “CLUTCH” section.
13) Install engine mountings and brackets.
Refer to tightening torque for INSTALLATION of “ENGINE AS-
SEMBLY” in this section.
14) Install engine with transmission to vehicle as previously out-
lined.
Page 377 of 557
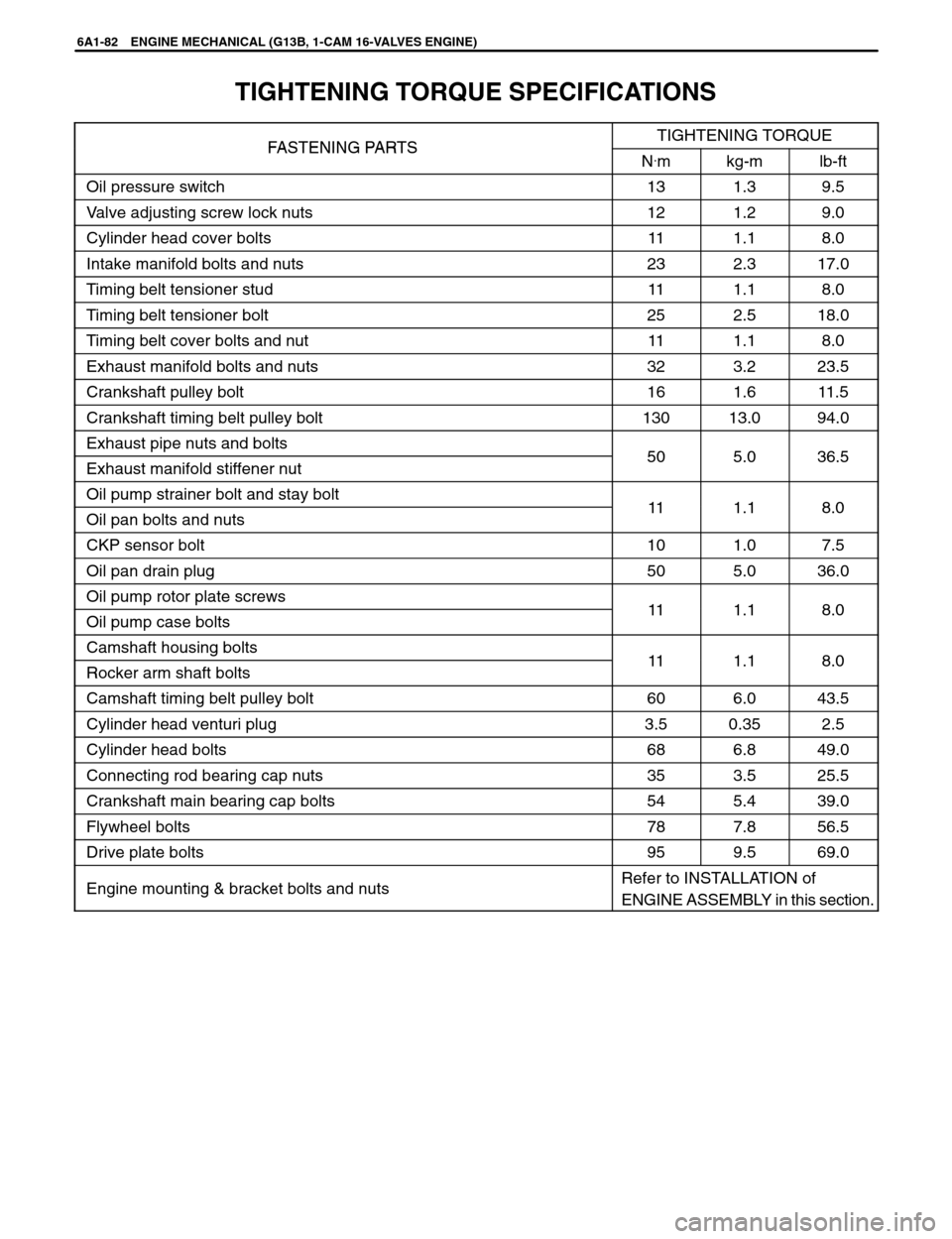
6A1-82 ENGINE MECHANICAL (G13B, 1-CAM 16-VALVES ENGINE)
TIGHTENING TORQUE SPECIFICATIONS
FASTENING PARTSTIGHTENING TORQUEFASTENING PA R T SN.mkg-mlb-ft
Oil pressure switch131.39.5
Valve adjusting screw lock nuts121.29.0
Cylinder head cover bolts111.18.0
Intake manifold bolts and nuts232.317.0
Timing belt tensioner stud111.18.0
Timing belt tensioner bolt252.518.0
Timing belt cover bolts and nut111.18.0
Exhaust manifold bolts and nuts323.223.5
Crankshaft pulley bolt161.611.5
Crankshaft timing belt pulley bolt13013.094.0
Exhaust pipe nuts and bolts505036 5Exhaust manifold stiffener nut505.036.5
Oil pump strainer bolt and stay bolt111180Oil pan bolts and nuts111.18.0
CKP sensor bolt101.07.5
Oil pan drain plug505.036.0
Oil pump rotor plate screws111180Oil pump case bolts111.18.0
Camshaft housing bolts111180Rocker arm shaft bolts111.18.0
Camshaft timing belt pulley bolt606.043.5
Cylinder head venturi plug3.50.352.5
Cylinder head bolts686.849.0
Connecting rod bearing cap nuts353.525.5
Crankshaft main bearing cap bolts545.439.0
Flywheel bolts787.856.5
Drive plate bolts959.569.0
Engine mounting & bracket bolts and nutsRefer to INSTALLATION of
ENGINE ASSEMBLY in this section.
Page 386 of 557
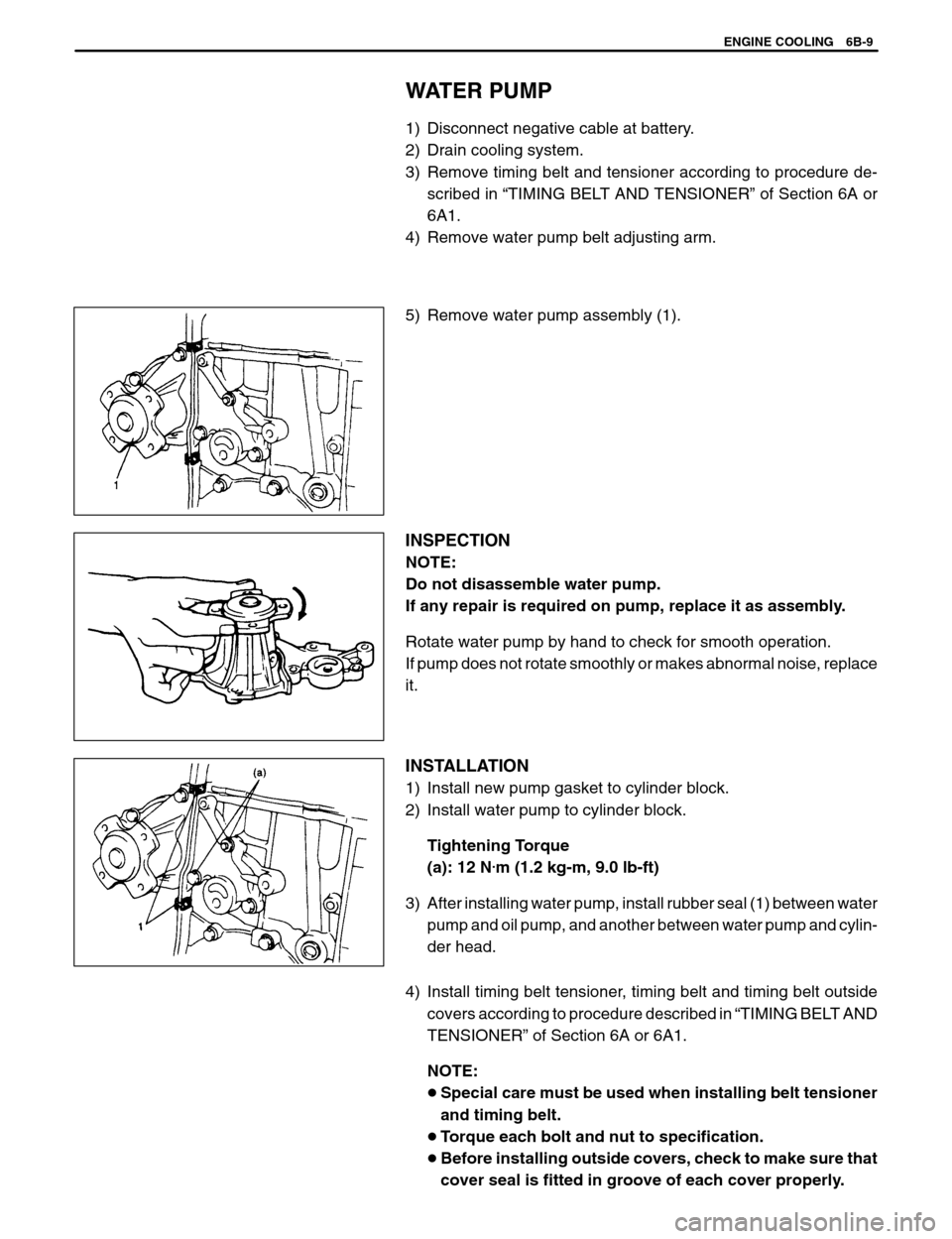
ENGINE COOLING 6B-9
WATER PUMP
1) Disconnect negative cable at battery.
2) Drain cooling system.
3) Remove timing belt and tensioner according to procedure de-
scribed in “TIMING BELT AND TENSIONER” of Section 6A or
6A1.
4) Remove water pump belt adjusting arm.
5) Remove water pump assembly (1).
INSPECTION
NOTE:
Do not disassemble water pump.
If any repair is required on pump, replace it as assembly.
Rotate water pump by hand to check for smooth operation.
If pump does not rotate smoothly or makes abnormal noise, replace
it.
INSTALLATION
1) Install new pump gasket to cylinder block.
2) Install water pump to cylinder block.
Tightening Torque
(a): 12 N
.m (1.2 kg-m, 9.0 lb-ft)
3) After installing water pump, install rubber seal (1) between water
pump and oil pump, and another between water pump and cylin-
der head.
4) Install timing belt tensioner, timing belt and timing belt outside
covers according to procedure described in “TIMING BELT AND
TENSIONER” of Section 6A or 6A1.
NOTE:
Special care must be used when installing belt tensioner
and timing belt.
Torque each bolt and nut to specification.
Before installing outside covers, check to make sure that
cover seal is fitted in groove of each cover properly.
Page 400 of 557
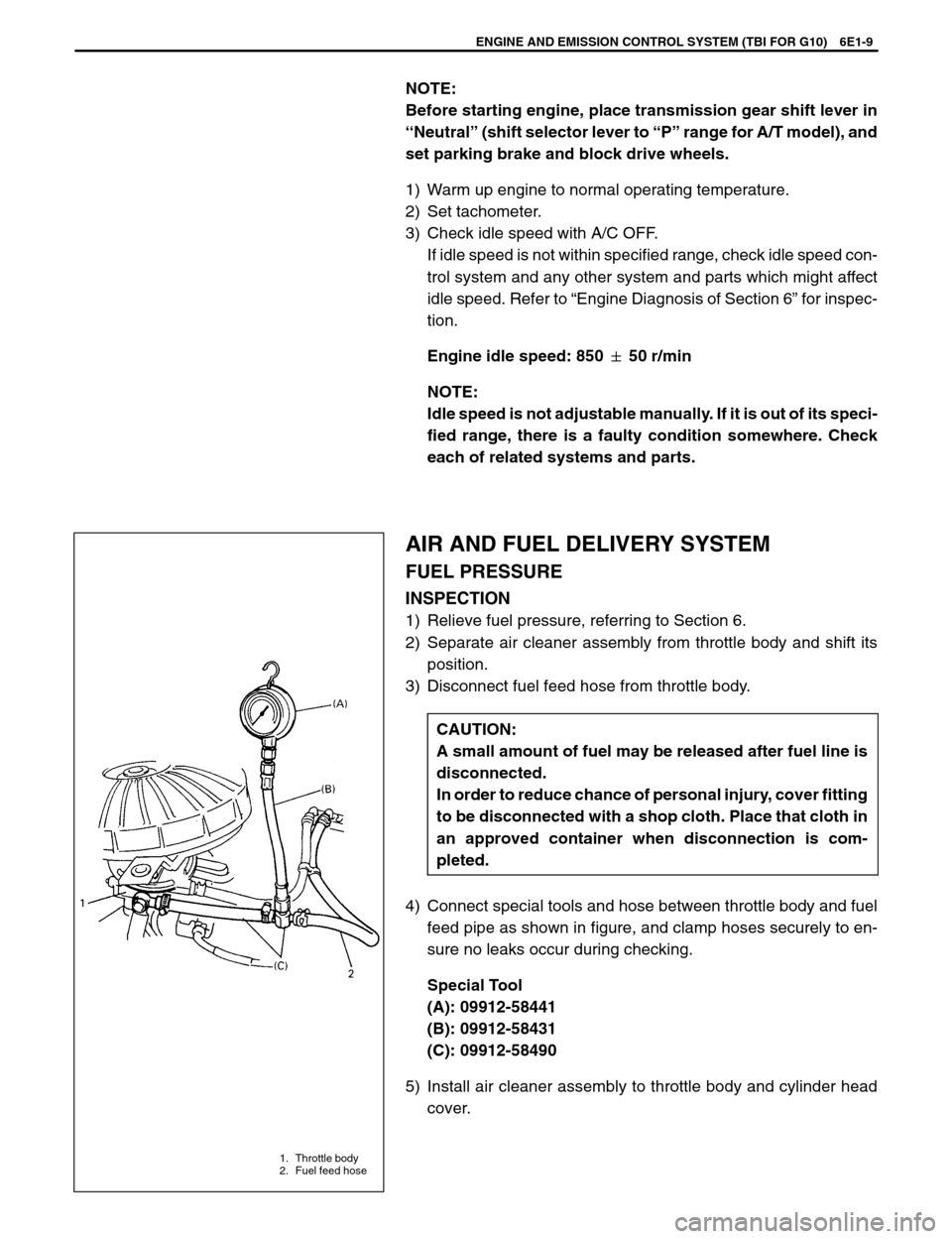
ENGINE AND EMISSION CONTROL SYSTEM (TBI FOR G10) 6E1-9
1. Throttle body
2. Fuel feed hose
NOTE:
Before starting engine, place transmission gear shift lever in
“Neutral” (shift selector lever to “P” range for A/T model), and
set parking brake and block drive wheels.
1) Warm up engine to normal operating temperature.
2) Set tachometer.
3) Check idle speed with A/C OFF.
If idle speed is not within specified range, check idle speed con-
trol system and any other system and parts which might affect
idle speed. Refer to “Engine Diagnosis of Section 6” for inspec-
tion.
Engine idle speed: 850 50 r/min
NOTE:
Idle speed is not adjustable manually. If it is out of its speci-
fied range, there is a faulty condition somewhere. Check
each of related systems and parts.
AIR AND FUEL DELIVERY SYSTEM
FUEL PRESSURE
INSPECTION
1) Relieve fuel pressure, referring to Section 6.
2) Separate air cleaner assembly from throttle body and shift its
position.
3) Disconnect fuel feed hose from throttle body.
CAUTION:
A small amount of fuel may be released after fuel line is
disconnected.
In order to reduce chance of personal injury, cover fitting
to be disconnected with a shop cloth. Place that cloth in
an approved container when disconnection is com-
pleted.
4) Connect special tools and hose between throttle body and fuel
feed pipe as shown in figure, and clamp hoses securely to en-
sure no leaks occur during checking.
Special Tool
(A): 09912-58441
(B): 09912-58431
(C): 09912-58490
5) Install air cleaner assembly to throttle body and cylinder head
cover.
Page 418 of 557
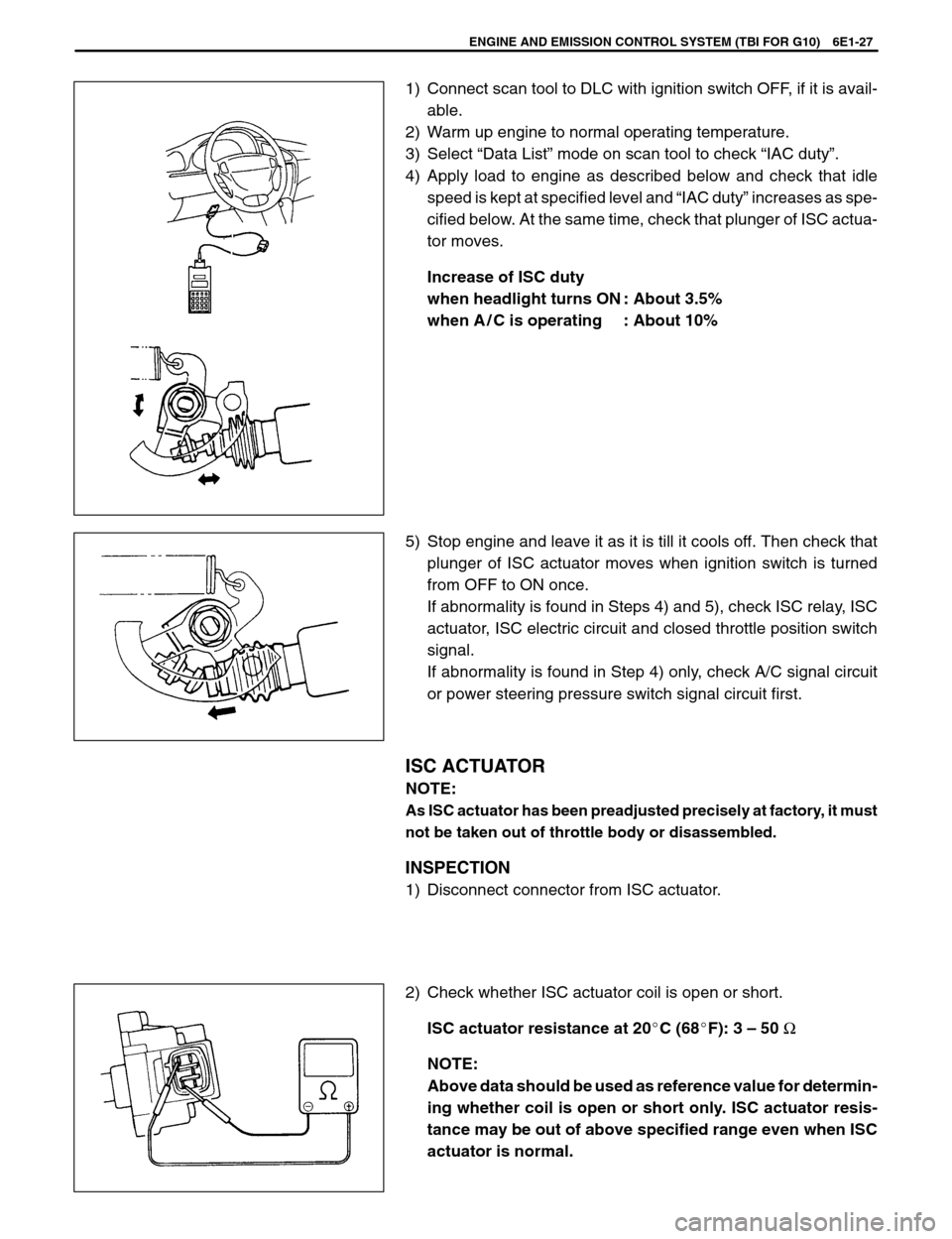
ENGINE AND EMISSION CONTROL SYSTEM (TBI FOR G10) 6E1-27
1) Connect scan tool to DLC with ignition switch OFF, if it is avail-
able.
2) Warm up engine to normal operating temperature.
3) Select “Data List” mode on scan tool to check “IAC duty”.
4) Apply load to engine as described below and check that idle
speed is kept at specified level and “IAC duty” increases as spe-
cified below. At the same time, check that plunger of ISC actua-
tor moves.
Increase of ISC duty
when headlight turns ON : About 3.5%
when A / C is operating : About 10%
5) Stop engine and leave it as it is till it cools off. Then check that
plunger of ISC actuator moves when ignition switch is turned
from OFF to ON once.
If abnormality is found in Steps 4) and 5), check ISC relay, ISC
actuator, ISC electric circuit and closed throttle position switch
signal.
If abnormality is found in Step 4) only, check A/C signal circuit
or power steering pressure switch signal circuit first.
ISC ACTUATOR
NOTE:
As ISC actuator has been preadjusted precisely at factory, it must
not be taken out of throttle body or disassembled.
INSPECTION
1) Disconnect connector from ISC actuator.
2) Check whether ISC actuator coil is open or short.
ISC actuator resistance at 20C (68F): 3 – 50 Ω
NOTE:
Above data should be used as reference value for determin-
ing whether coil is open or short only. ISC actuator resis-
tance may be out of above specified range even when ISC
actuator is normal.
Page 426 of 557
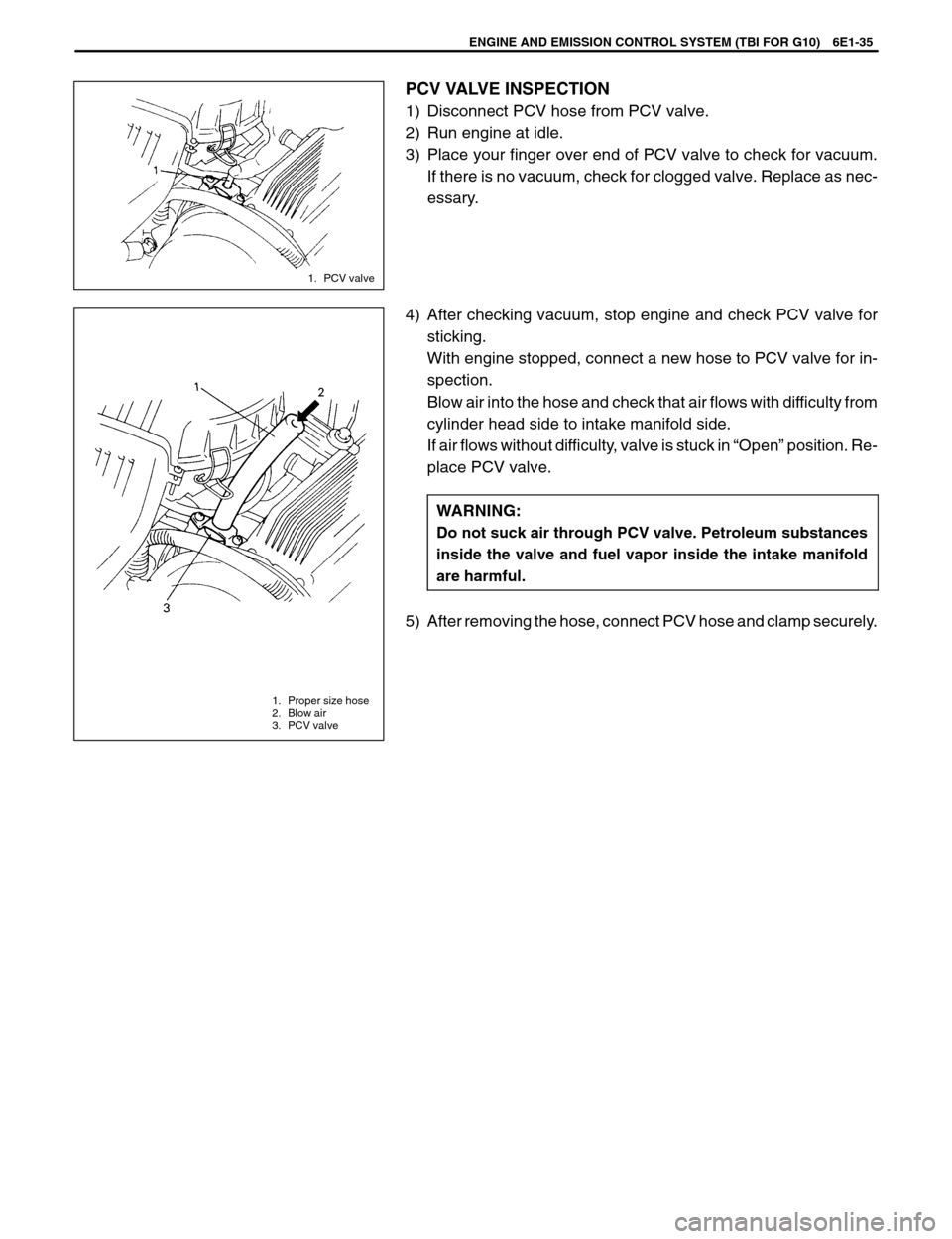
ENGINE AND EMISSION CONTROL SYSTEM (TBI FOR G10) 6E1-35
1. PCV valve
1. Proper size hose
2. Blow air
3. PCV valve
PCV VALVE INSPECTION
1) Disconnect PCV hose from PCV valve.
2) Run engine at idle.
3) Place your finger over end of PCV valve to check for vacuum.
If there is no vacuum, check for clogged valve. Replace as nec-
essary.
4) After checking vacuum, stop engine and check PCV valve for
sticking.
With engine stopped, connect a new hose to PCV valve for in-
spection.
Blow air into the hose and check that air flows with difficulty from
cylinder head side to intake manifold side.
If air flows without difficulty, valve is stuck in “Open” position. Re-
place PCV valve.
WARNING:
Do not suck air through PCV valve. Petroleum substances
inside the valve and fuel vapor inside the intake manifold
are harmful.
5) After removing the hose, connect PCV hose and clamp securely.
Page 435 of 557
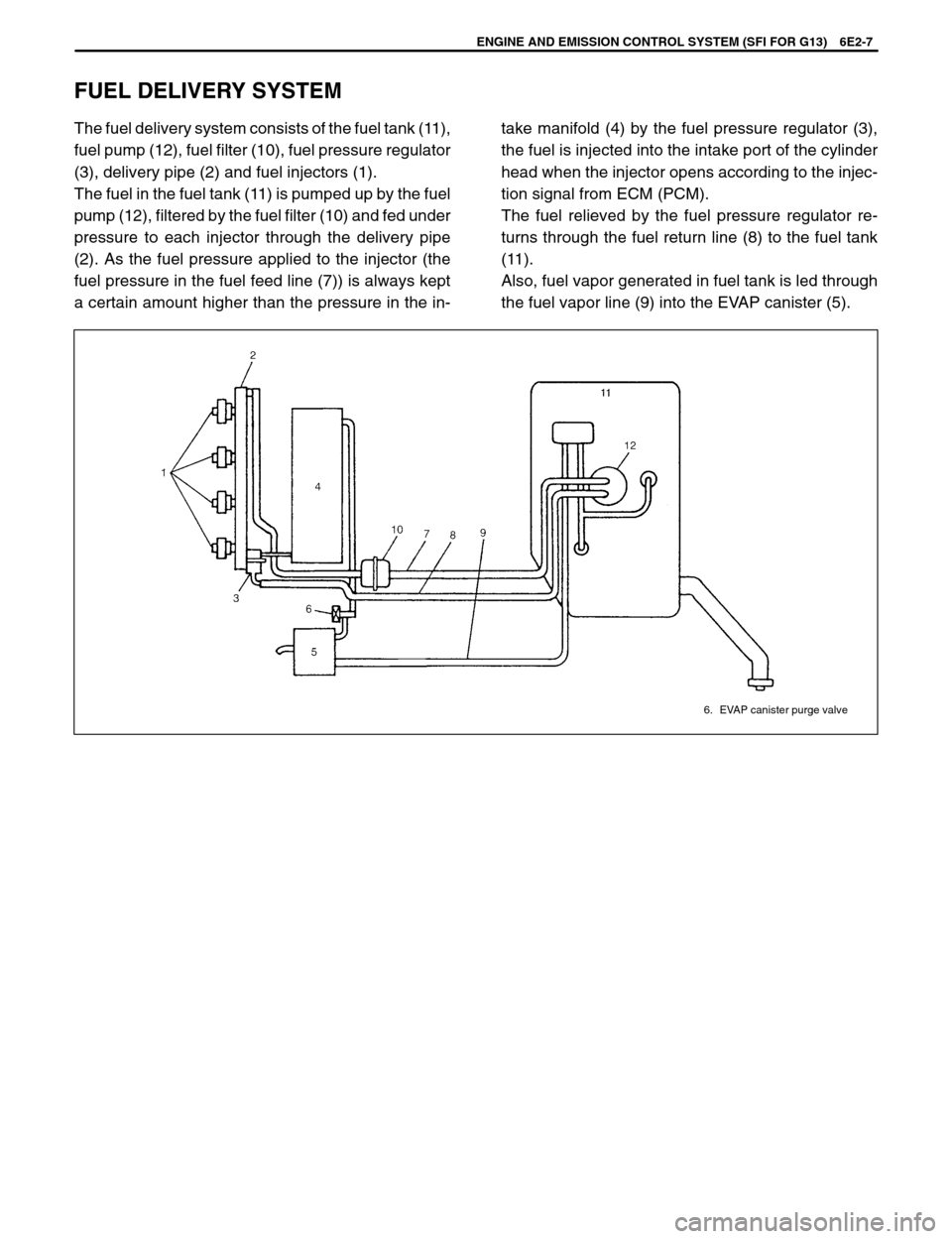
6. EVAP canister purge valve
ENGINE AND EMISSION CONTROL SYSTEM (SFI FOR G13) 6E2-7
The fuel delivery system consists of the fuel tank (11),
fuel pump (12), fuel filter (10), fuel pressure regulator
(3), delivery pipe (2) and fuel injectors (1).
The fuel in the fuel tank (11) is pumped up by the fuel
pump (12), filtered by the fuel filter (10) and fed under
pressure to each injector through the delivery pipe
(2). As the fuel pressure applied to the injector (the
fuel pressure in the fuel feed line (7)) is always kept
a certain amount higher than the pressure in the in-take manifold (4) by the fuel pressure regulator (3),
the fuel is injected into the intake port of the cylinder
head when the injector opens according to the injec-
tion signal from ECM (PCM).
The fuel relieved by the fuel pressure regulator re-
turns through the fuel return line (8) to the fuel tank
(11).
Also, fuel vapor generated in fuel tank is led through
the fuel vapor line (9) into the EVAP canister (5).
FUEL DELIVERY SYSTEM