clutch SUZUKI SWIFT 2000 1.G Transmission Service Owner's Manual
[x] Cancel search | Manufacturer: SUZUKI, Model Year: 2000, Model line: SWIFT, Model: SUZUKI SWIFT 2000 1.GPages: 447, PDF Size: 10.54 MB
Page 76 of 447
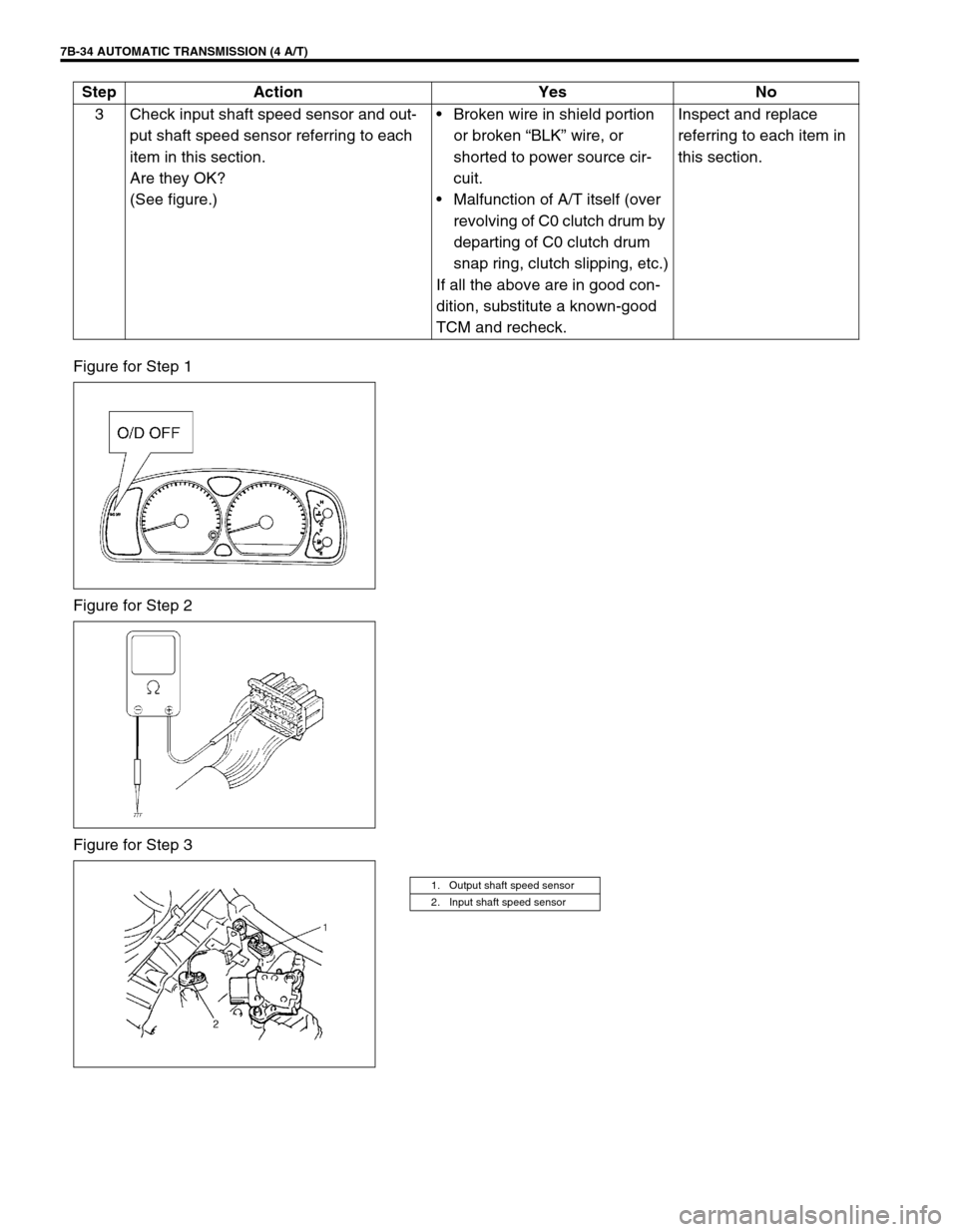
7B-34 AUTOMATIC TRANSMISSION (4 A/T)
Figure for Step 1
Figure for Step 2
Figure for Step 33 Check input shaft speed sensor and out-
put shaft speed sensor referring to each
item in this section.
Are they OK?
(See figure.)Broken wire in shield portion
or broken “BLK” wire, or
shorted to power source cir-
cuit.
Malfunction of A/T itself (over
revolving of C0 clutch drum by
departing of C0 clutch drum
snap ring, clutch slipping, etc.)
If all the above are in good con-
dition, substitute a known-good
TCM and recheck.Inspect and replace
referring to each item in
this section. Step Action Yes No
1. Output shaft speed sensor
2. Input shaft speed sensor
Page 77 of 447
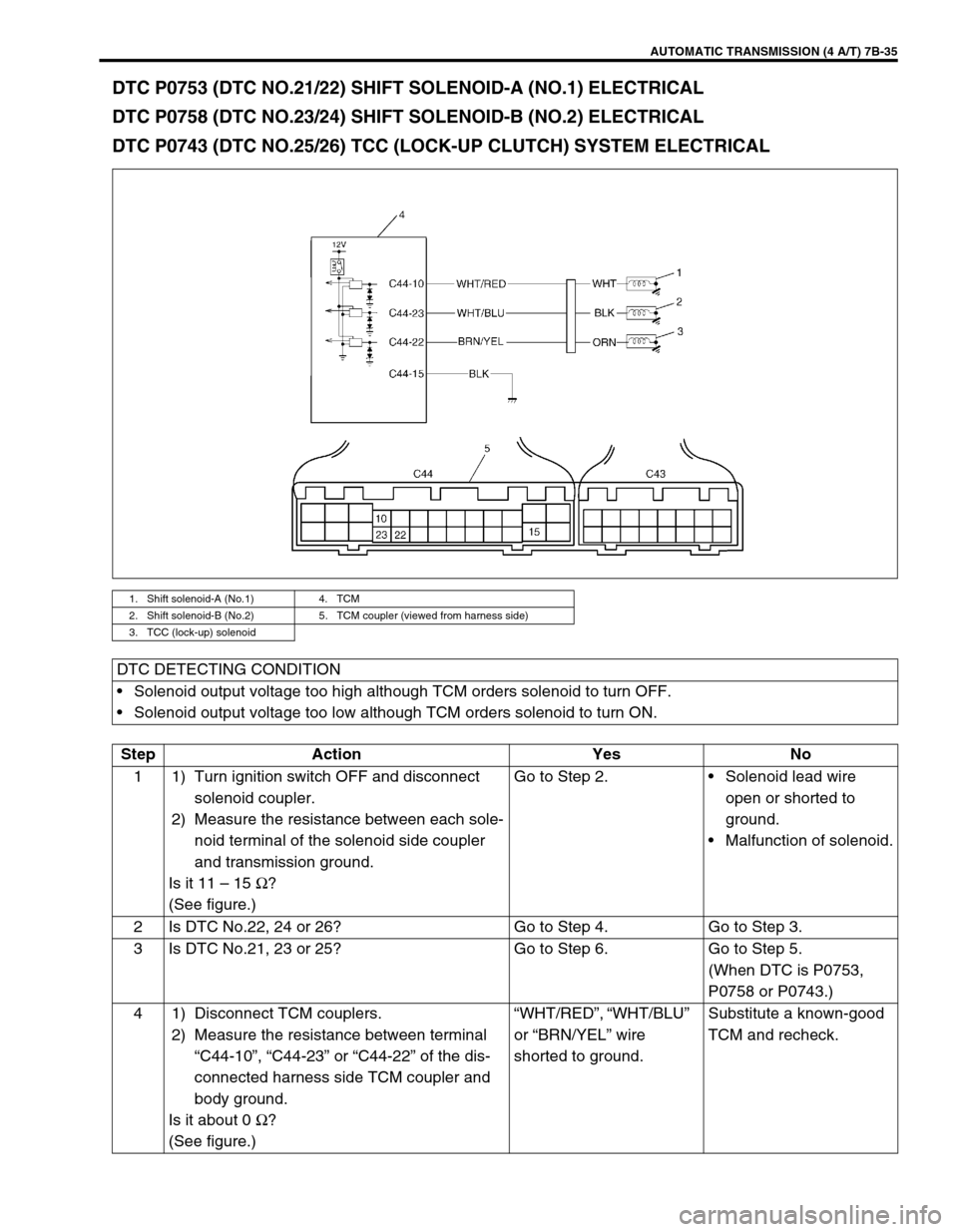
AUTOMATIC TRANSMISSION (4 A/T) 7B-35
DTC P0753 (DTC NO.21/22) SHIFT SOLENOID-A (NO.1) ELECTRICAL
DTC P0758 (DTC NO.23/24) SHIFT SOLENOID-B (NO.2) ELECTRICAL
DTC P0743 (DTC NO.25/26) TCC (LOCK-UP CLUTCH) SYSTEM ELECTRICAL
1. Shift solenoid-A (No.1) 4. TCM
2. Shift solenoid-B (No.2) 5. TCM coupler (viewed from harness side)
3. TCC (lock-up) solenoid
DTC DETECTING CONDITION
Solenoid output voltage too high although TCM orders solenoid to turn OFF.
Solenoid output voltage too low although TCM orders solenoid to turn ON.
Step Action Yes No
1 1) Turn ignition switch OFF and disconnect
solenoid coupler.
2) Measure the resistance between each sole-
noid terminal of the solenoid side coupler
and transmission ground.
Is it 11 – 15 Ω
?
(See figure.)Go to Step 2.Solenoid lead wire
open or shorted to
ground.
Malfunction of solenoid.
2 Is DTC No.22, 24 or 26? Go to Step 4. Go to Step 3.
3 Is DTC No.21, 23 or 25? Go to Step 6. Go to Step 5.
(When DTC is P0753,
P0758 or P0743.)
4 1) Disconnect TCM couplers.
2) Measure the resistance between terminal
“C44-10”, “C44-23” or “C44-22” of the dis-
connected harness side TCM coupler and
body ground.
Is it about 0 Ω
?
(See figure.)“WHT/RED”, “WHT/BLU”
or “BRN/YEL” wire
shorted to ground.Substitute a known-good
TCM and recheck.
Page 112 of 447
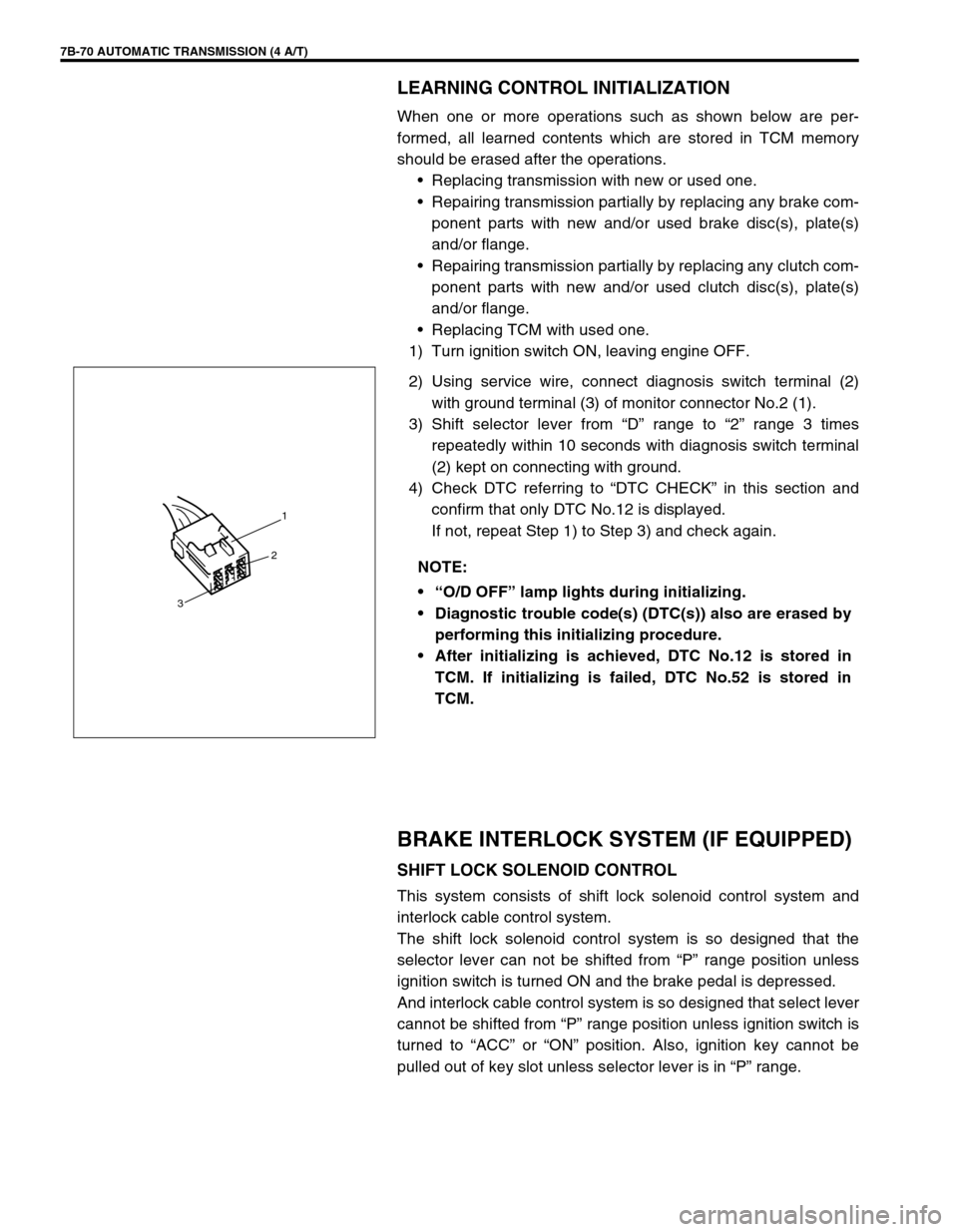
7B-70 AUTOMATIC TRANSMISSION (4 A/T)
LEARNING CONTROL INITIALIZATION
When one or more operations such as shown below are per-
formed, all learned contents which are stored in TCM memory
should be erased after the operations.
Replacing transmission with new or used one.
Repairing transmission partially by replacing any brake com-
ponent parts with new and/or used brake disc(s), plate(s)
and/or flange.
Repairing transmission partially by replacing any clutch com-
ponent parts with new and/or used clutch disc(s), plate(s)
and/or flange.
Replacing TCM with used one.
1) Turn ignition switch ON, leaving engine OFF.
2) Using service wire, connect diagnosis switch terminal (2)
with ground terminal (3) of monitor connector No.2 (1).
3) Shift selector lever from “D” range to “2” range 3 times
repeatedly within 10 seconds with diagnosis switch terminal
(2) kept on connecting with ground.
4) Check DTC referring to “DTC CHECK” in this section and
confirm that only DTC No.12 is displayed.
If not, repeat Step 1) to Step 3) and check again.
BRAKE INTERLOCK SYSTEM (IF EQUIPPED)
SHIFT LOCK SOLENOID CONTROL
This system consists of shift lock solenoid control system and
interlock cable control system.
The shift lock solenoid control system is so designed that the
selector lever can not be shifted from “P” range position unless
ignition switch is turned ON and the brake pedal is depressed.
And interlock cable control system is so designed that select lever
cannot be shifted from “P” range position unless ignition switch is
turned to “ACC” or “ON” position. Also, ignition key cannot be
pulled out of key slot unless selector lever is in “P” range. NOTE:
“O/D OFF” lamp lights during initializing.
Diagnostic trouble code(s) (DTC(s)) also are erased by
performing this initializing procedure.
After initializing is achieved, DTC No.12 is stored in
TCM. If initializing is failed, DTC No.52 is stored in
TCM.
1
2
3
Page 117 of 447
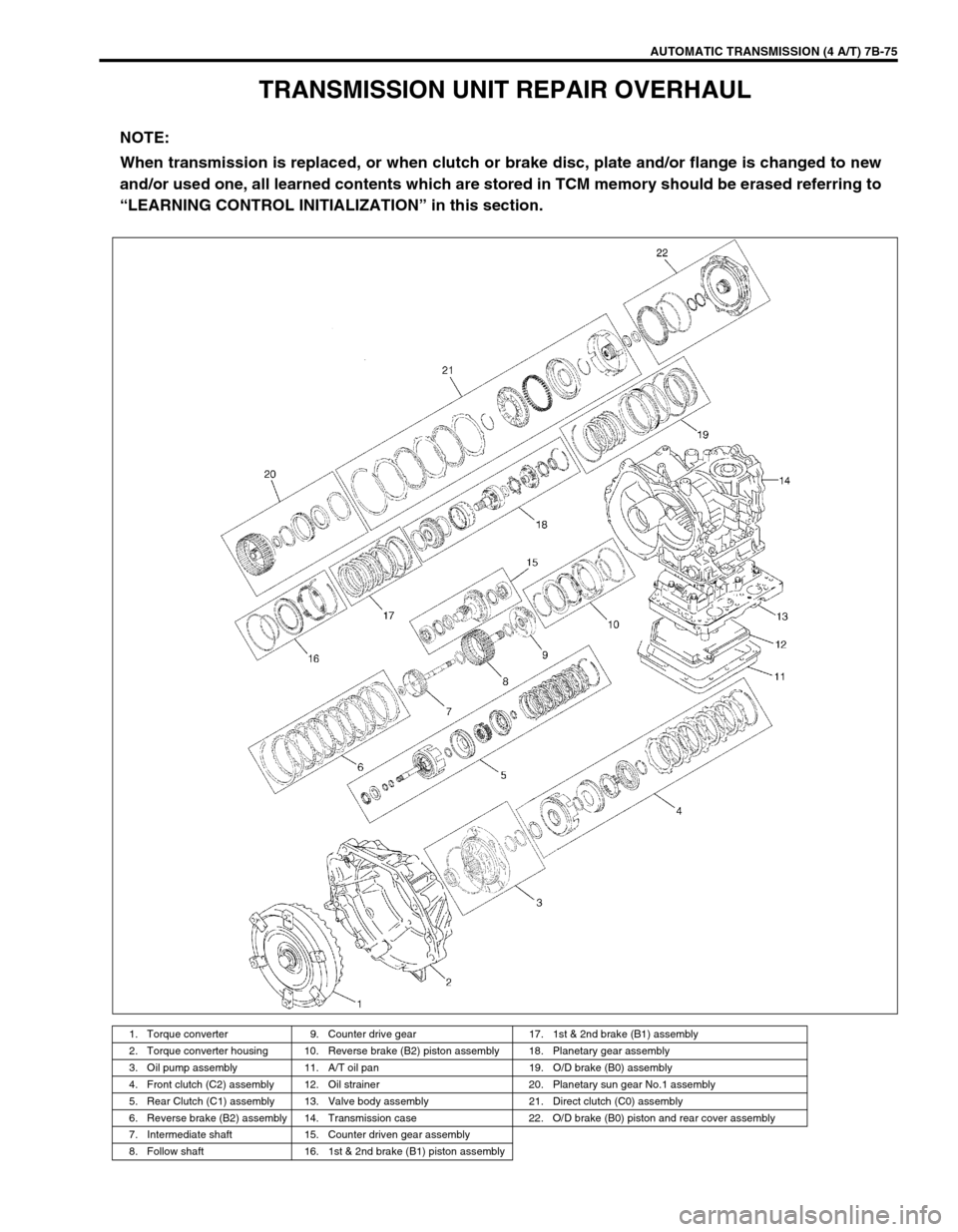
AUTOMATIC TRANSMISSION (4 A/T) 7B-75
TRANSMISSION UNIT REPAIR OVERHAUL
NOTE:
When transmission is replaced, or when clutch or brake disc, plate and/or flange is changed to new
and/or used one, all learned contents which are stored in TCM memory should be erased referring to
“LEARNING CONTROL INITIALIZATION” in this section.
1. Torque converter 9. Counter drive gear 17. 1st & 2nd brake (B1) assembly
2. Torque converter housing 10. Reverse brake (B2) piston assembly 18. Planetary gear assembly
3. Oil pump assembly 11. A/T oil pan 19. O/D brake (B0) assembly
4. Front clutch (C2) assembly 12. Oil strainer 20. Planetary sun gear No.1 assembly
5. Rear Clutch (C1) assembly 13. Valve body assembly 21. Direct clutch (C0) assembly
6. Reverse brake (B2) assembly 14. Transmission case 22. O/D brake (B0) piston and rear cover assembly
7. Intermediate shaft 15. Counter driven gear assembly
8. Follow shaft 16. 1st & 2nd brake (B1) piston assembly
Page 123 of 447
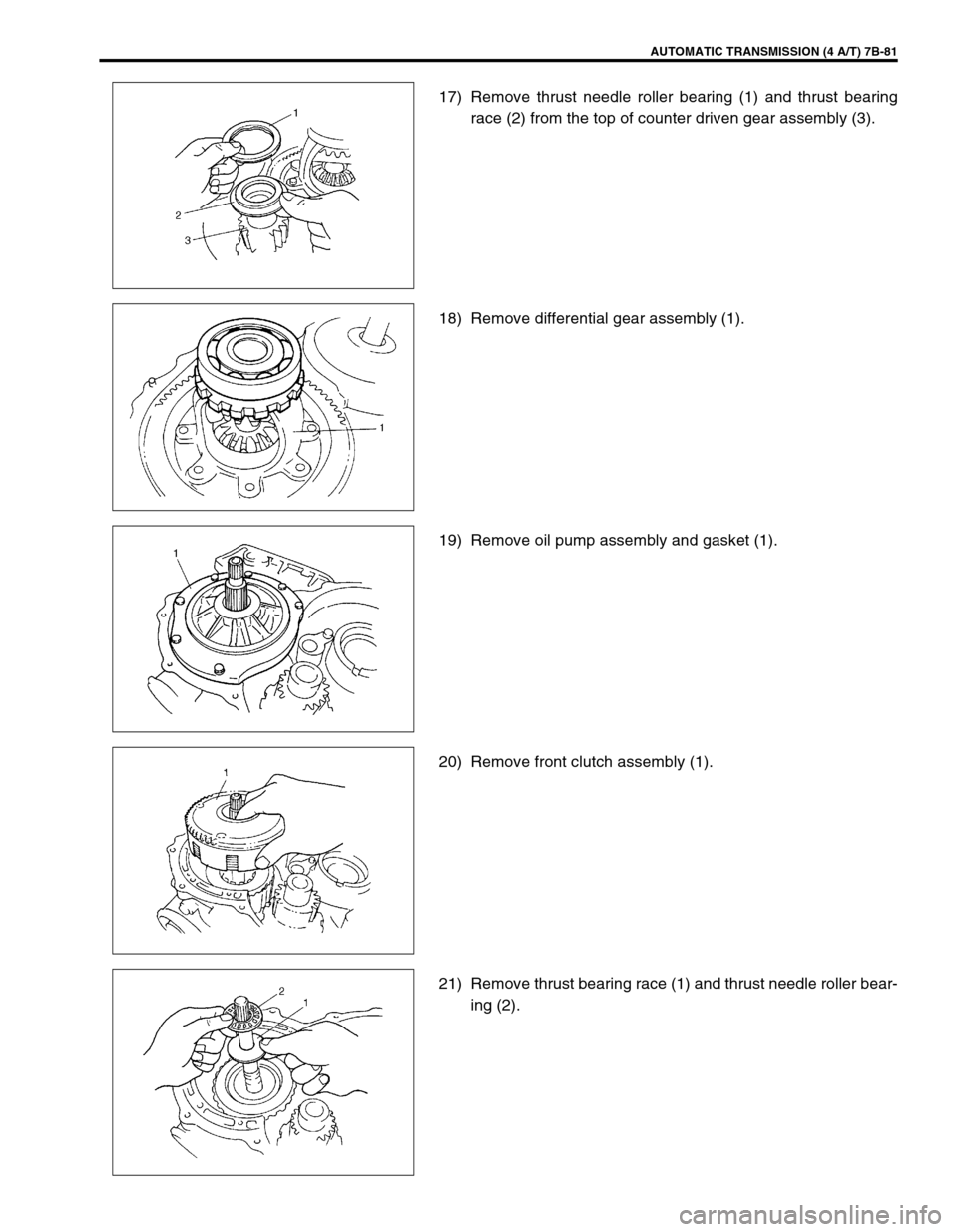
AUTOMATIC TRANSMISSION (4 A/T) 7B-81
17) Remove thrust needle roller bearing (1) and thrust bearing
race (2) from the top of counter driven gear assembly (3).
18) Remove differential gear assembly (1).
19) Remove oil pump assembly and gasket (1).
20) Remove front clutch assembly (1).
21) Remove thrust bearing race (1) and thrust needle roller bear-
ing (2).
Page 124 of 447
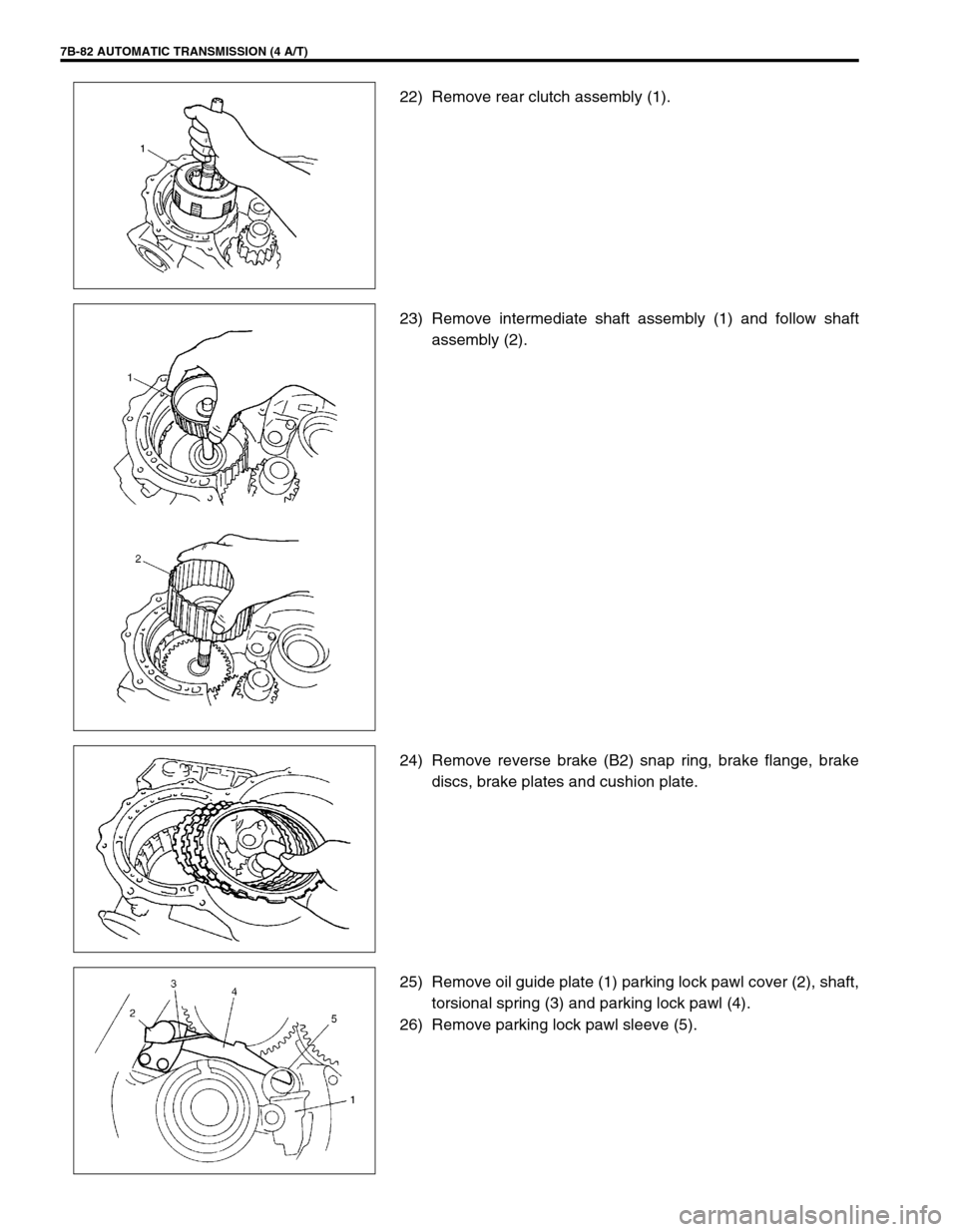
7B-82 AUTOMATIC TRANSMISSION (4 A/T)
22) Remove rear clutch assembly (1).
23) Remove intermediate shaft assembly (1) and follow shaft
assembly (2).
24) Remove reverse brake (B2) snap ring, brake flange, brake
discs, brake plates and cushion plate.
25) Remove oil guide plate (1) parking lock pawl cover (2), shaft,
torsional spring (3) and parking lock pawl (4).
26) Remove parking lock pawl sleeve (5).
Page 126 of 447
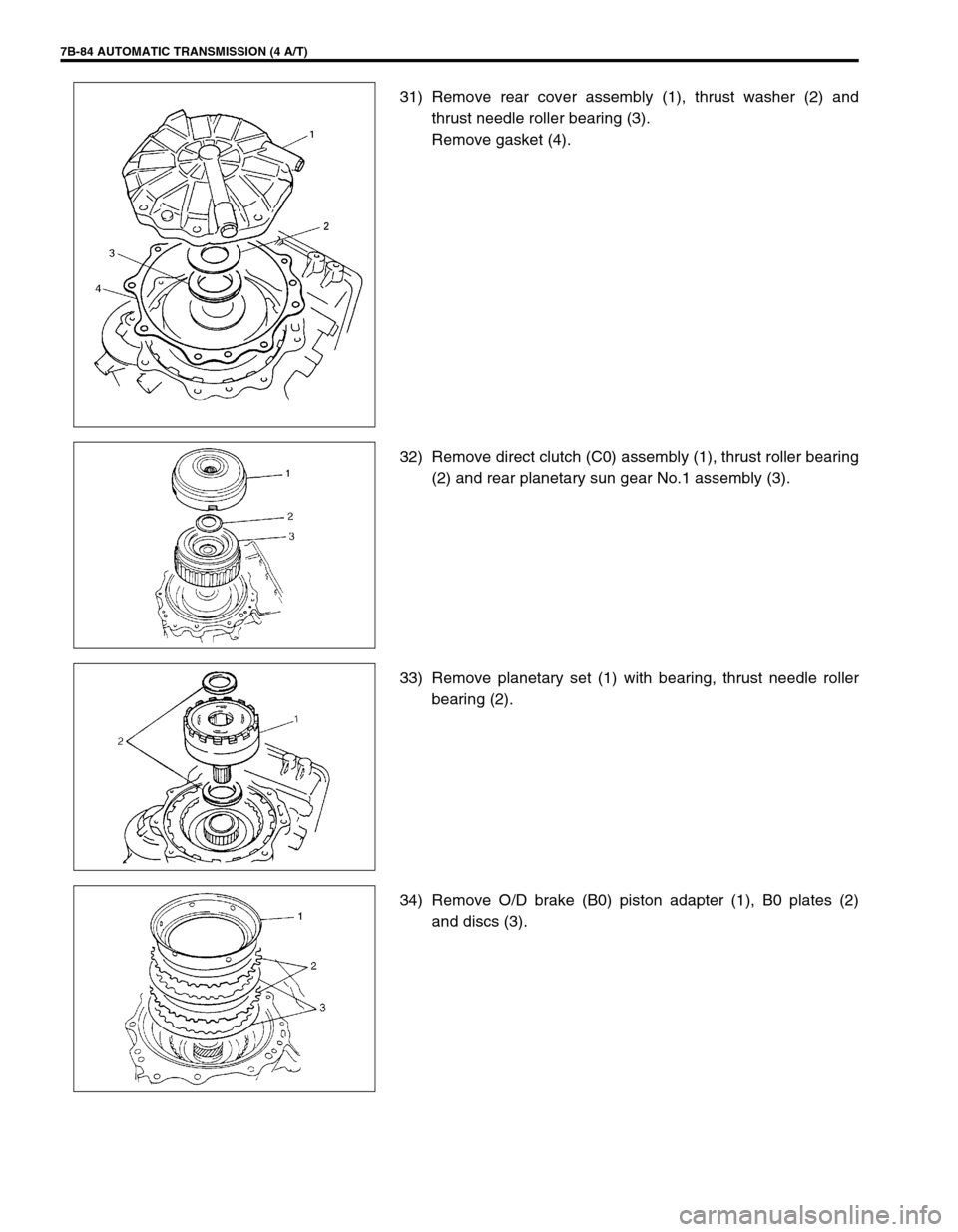
7B-84 AUTOMATIC TRANSMISSION (4 A/T)
31) Remove rear cover assembly (1), thrust washer (2) and
thrust needle roller bearing (3).
Remove gasket (4).
32) Remove direct clutch (C0) assembly (1), thrust roller bearing
(2) and rear planetary sun gear No.1 assembly (3).
33) Remove planetary set (1) with bearing, thrust needle roller
bearing (2).
34) Remove O/D brake (B0) piston adapter (1), B0 plates (2)
and discs (3).
Page 129 of 447
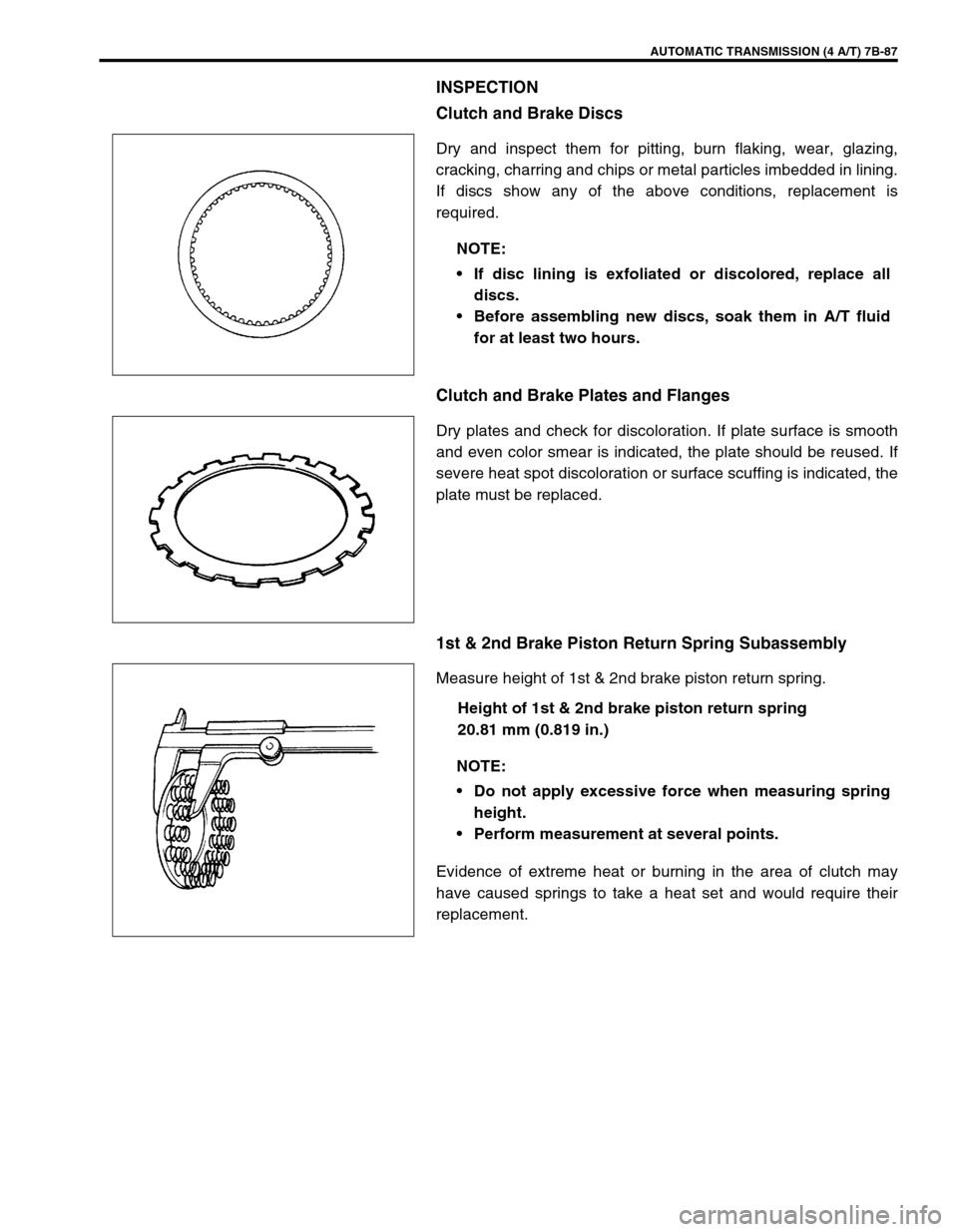
AUTOMATIC TRANSMISSION (4 A/T) 7B-87
INSPECTION
Clutch and Brake Discs
Dry and inspect them for pitting, burn flaking, wear, glazing,
cracking, charring and chips or metal particles imbedded in lining.
If discs show any of the above conditions, replacement is
required.
Clutch and Brake Plates and Flanges
Dry plates and check for discoloration. If plate surface is smooth
and even color smear is indicated, the plate should be reused. If
severe heat spot discoloration or surface scuffing is indicated, the
plate must be replaced.
1st & 2nd Brake Piston Return Spring Subassembly
Measure height of 1st & 2nd brake piston return spring.
Height of 1st & 2nd brake piston return spring
20.81 mm (0.819 in.)
Evidence of extreme heat or burning in the area of clutch may
have caused springs to take a heat set and would require their
replacement.NOTE:
If disc lining is exfoliated or discolored, replace all
discs.
Before assembling new discs, soak them in A/T fluid
for at least two hours.
NOTE:
Do not apply excessive force when measuring spring
height.
Perform measurement at several points.
Page 130 of 447
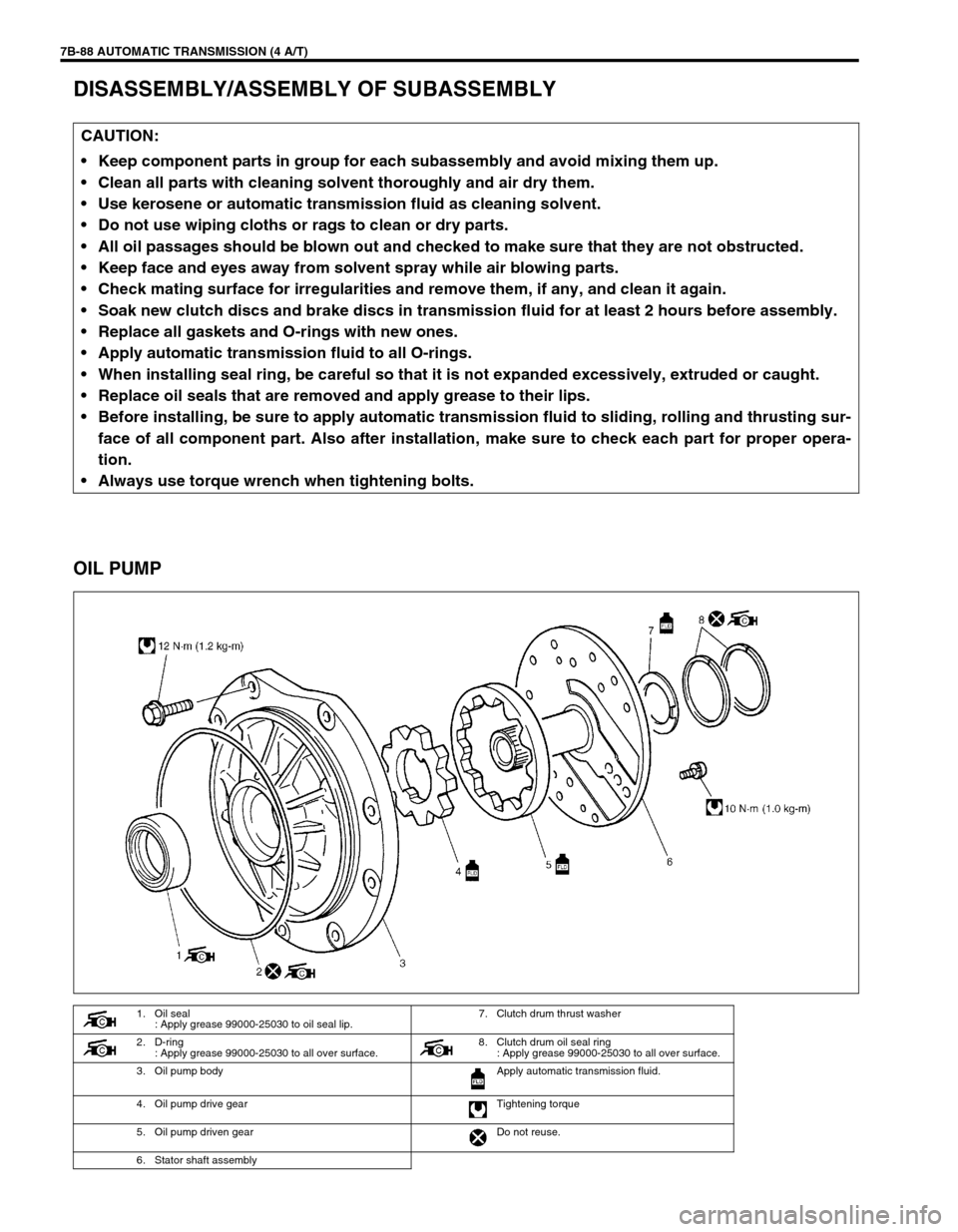
7B-88 AUTOMATIC TRANSMISSION (4 A/T)
DISASSEMBLY/ASSEMBLY OF SUBASSEMBLY
OIL PUMP
CAUTION:
Keep component parts in group for each subassembly and avoid mixing them up.
Clean all parts with cleaning solvent thoroughly and air dry them.
Use kerosene or automatic transmission fluid as cleaning solvent.
Do not use wiping cloths or rags to clean or dry parts.
All oil passages should be blown out and checked to make sure that they are not obstructed.
Keep face and eyes away from solvent spray while air blowing parts.
Check mating surface for irregularities and remove them, if any, and clean it again.
Soak new clutch discs and brake discs in transmission fluid for at least 2 hours before assembly.
Replace all gaskets and O-rings with new ones.
Apply automatic transmission fluid to all O-rings.
When installing seal ring, be careful so that it is not expanded excessively, extruded or caught.
Replace oil seals that are removed and apply grease to their lips.
Before installing, be sure to apply automatic transmission fluid to sliding, rolling and thrusting sur-
face of all component part. Also after installation, make sure to check each part for proper opera-
tion.
Always use torque wrench when tightening bolts.
1. Oil seal
: Apply grease 99000-25030 to oil seal lip.7. Clutch drum thrust washer
2. D-ring
: Apply grease 99000-25030 to all over surface. 8. Clutch drum oil seal ring
: Apply grease 99000-25030 to all over surface.
3. Oil pump body Apply automatic transmission fluid.
4. Oil pump drive gear Tightening torque
5. Oil pump driven gear Do not reuse.
6. Stator shaft assembly
Page 131 of 447
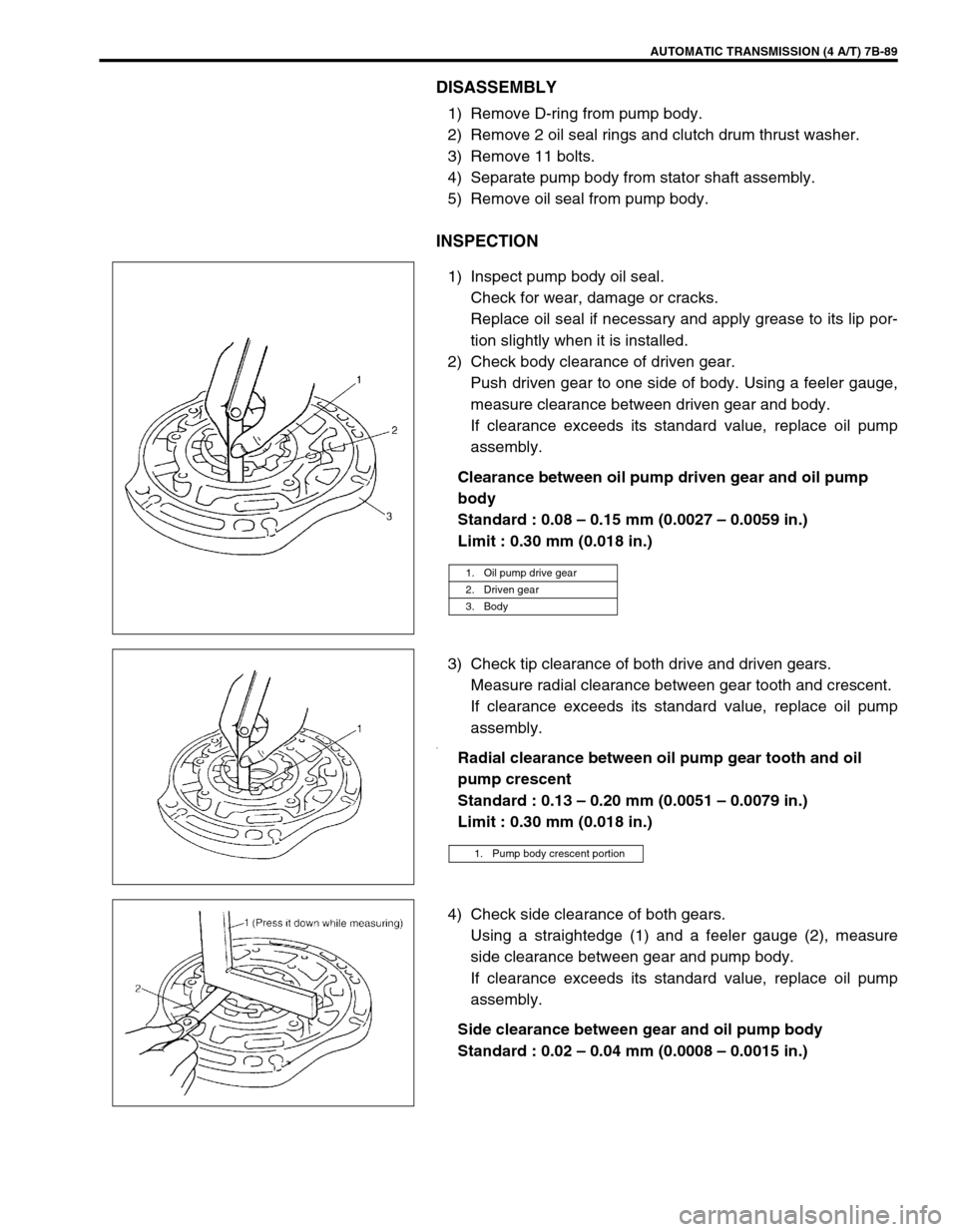
AUTOMATIC TRANSMISSION (4 A/T) 7B-89
DISASSEMBLY
1) Remove D-ring from pump body.
2) Remove 2 oil seal rings and clutch drum thrust washer.
3) Remove 11 bolts.
4) Separate pump body from stator shaft assembly.
5) Remove oil seal from pump body.
INSPECTION
1) Inspect pump body oil seal.
Check for wear, damage or cracks.
Replace oil seal if necessary and apply grease to its lip por-
tion slightly when it is installed.
2) Check body clearance of driven gear.
Push driven gear to one side of body. Using a feeler gauge,
measure clearance between driven gear and body.
If clearance exceeds its standard value, replace oil pump
assembly.
Clearance between oil pump driven gear and oil pump
body
Standard : 0.08 – 0.15 mm (0.0027 – 0.0059 in.)
Limit : 0.30 mm (0.018 in.)
3) Check tip clearance of both drive and driven gears.
Measure radial clearance between gear tooth and crescent.
If clearance exceeds its standard value, replace oil pump
assembly.
.Radial clearance between oil pump gear tooth and oil
pump crescent
Standard : 0.13 – 0.20 mm (0.0051 – 0.0079 in.)
Limit : 0.30 mm (0.018 in.)
4) Check side clearance of both gears.
Using a straightedge (1) and a feeler gauge (2), measure
side clearance between gear and pump body.
If clearance exceeds its standard value, replace oil pump
assembly.
Side clearance between gear and oil pump body
Standard : 0.02 – 0.04 mm (0.0008 – 0.0015 in.)
1. Oil pump drive gear
2. Driven gear
3. Body
1. Pump body crescent portion