automatic transmission fluid SUZUKI SWIFT 2000 1.G Transmission Service Workshop Manual
[x] Cancel search | Manufacturer: SUZUKI, Model Year: 2000, Model line: SWIFT, Model: SUZUKI SWIFT 2000 1.GPages: 447, PDF Size: 10.54 MB
Page 44 of 447
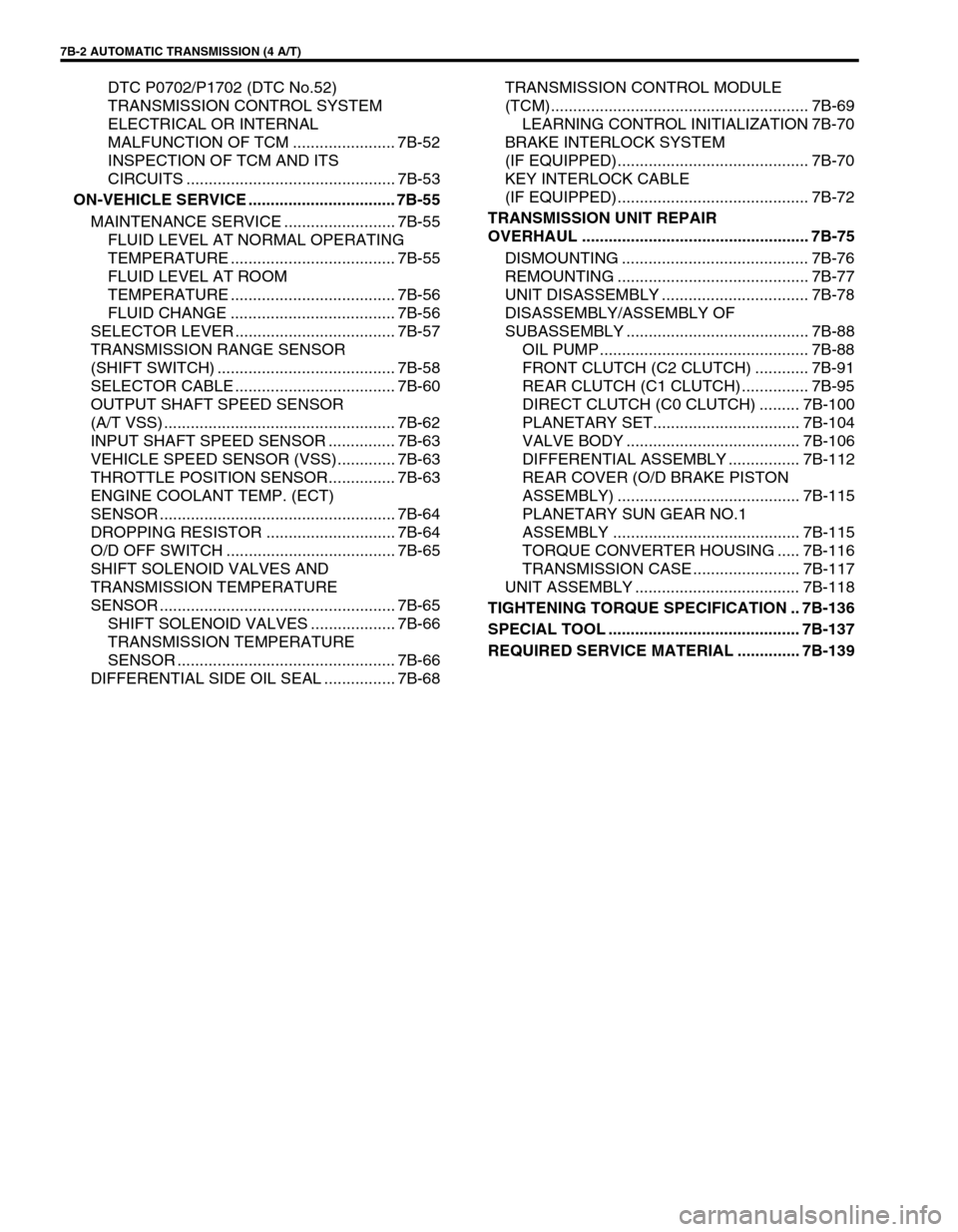
7B-2 AUTOMATIC TRANSMISSION (4 A/T)
DTC P0702/P1702 (DTC No.52)
TRANSMISSION CONTROL SYSTEM
ELECTRICAL OR INTERNAL
MALFUNCTION OF TCM ....................... 7B-52
INSPECTION OF TCM AND ITS
CIRCUITS ............................................... 7B-53
ON-VEHICLE SERVICE ................................. 7B-55
MAINTENANCE SERVICE ......................... 7B-55
FLUID LEVEL AT NORMAL OPERATING
TEMPERATURE ..................................... 7B-55
FLUID LEVEL AT ROOM
TEMPERATURE ..................................... 7B-56
FLUID CHANGE ..................................... 7B-56
SELECTOR LEVER .................................... 7B-57
TRANSMISSION RANGE SENSOR
(SHIFT SWITCH) ........................................ 7B-58
SELECTOR CABLE .................................... 7B-60
OUTPUT SHAFT SPEED SENSOR
(A/T VSS) .................................................... 7B-62
INPUT SHAFT SPEED SENSOR ............... 7B-63
VEHICLE SPEED SENSOR (VSS)............. 7B-63
THROTTLE POSITION SENSOR............... 7B-63
ENGINE COOLANT TEMP. (ECT)
SENSOR ..................................................... 7B-64
DROPPING RESISTOR ............................. 7B-64
O/D OFF SWITCH ...................................... 7B-65
SHIFT SOLENOID VALVES AND
TRANSMISSION TEMPERATURE
SENSOR ..................................................... 7B-65
SHIFT SOLENOID VALVES ................... 7B-66
TRANSMISSION TEMPERATURE
SENSOR ................................................. 7B-66
DIFFERENTIAL SIDE OIL SEAL ................ 7B-68TRANSMISSION CONTROL MODULE
(TCM).......................................................... 7B-69
LEARNING CONTROL INITIALIZATION 7B-70
BRAKE INTERLOCK SYSTEM
(IF EQUIPPED)........................................... 7B-70
KEY INTERLOCK CABLE
(IF EQUIPPED)........................................... 7B-72
TRANSMISSION UNIT REPAIR
OVERHAUL ................................................... 7B-75
DISMOUNTING .......................................... 7B-76
REMOUNTING ........................................... 7B-77
UNIT DISASSEMBLY ................................. 7B-78
DISASSEMBLY/ASSEMBLY OF
SUBASSEMBLY ......................................... 7B-88
OIL PUMP ............................................... 7B-88
FRONT CLUTCH (C2 CLUTCH) ............ 7B-91
REAR CLUTCH (C1 CLUTCH) ............... 7B-95
DIRECT CLUTCH (C0 CLUTCH) ......... 7B-100
PLANETARY SET................................. 7B-104
VALVE BODY ....................................... 7B-106
DIFFERENTIAL ASSEMBLY ................ 7B-112
REAR COVER (O/D BRAKE PISTON
ASSEMBLY) ......................................... 7B-115
PLANETARY SUN GEAR NO.1
ASSEMBLY .......................................... 7B-115
TORQUE CONVERTER HOUSING ..... 7B-116
TRANSMISSION CASE ........................ 7B-117
UNIT ASSEMBLY ..................................... 7B-118
TIGHTENING TORQUE SPECIFICATION .. 7B-136
SPECIAL TOOL ........................................... 7B-137
REQUIRED SERVICE MATERIAL .............. 7B-139
Page 46 of 447
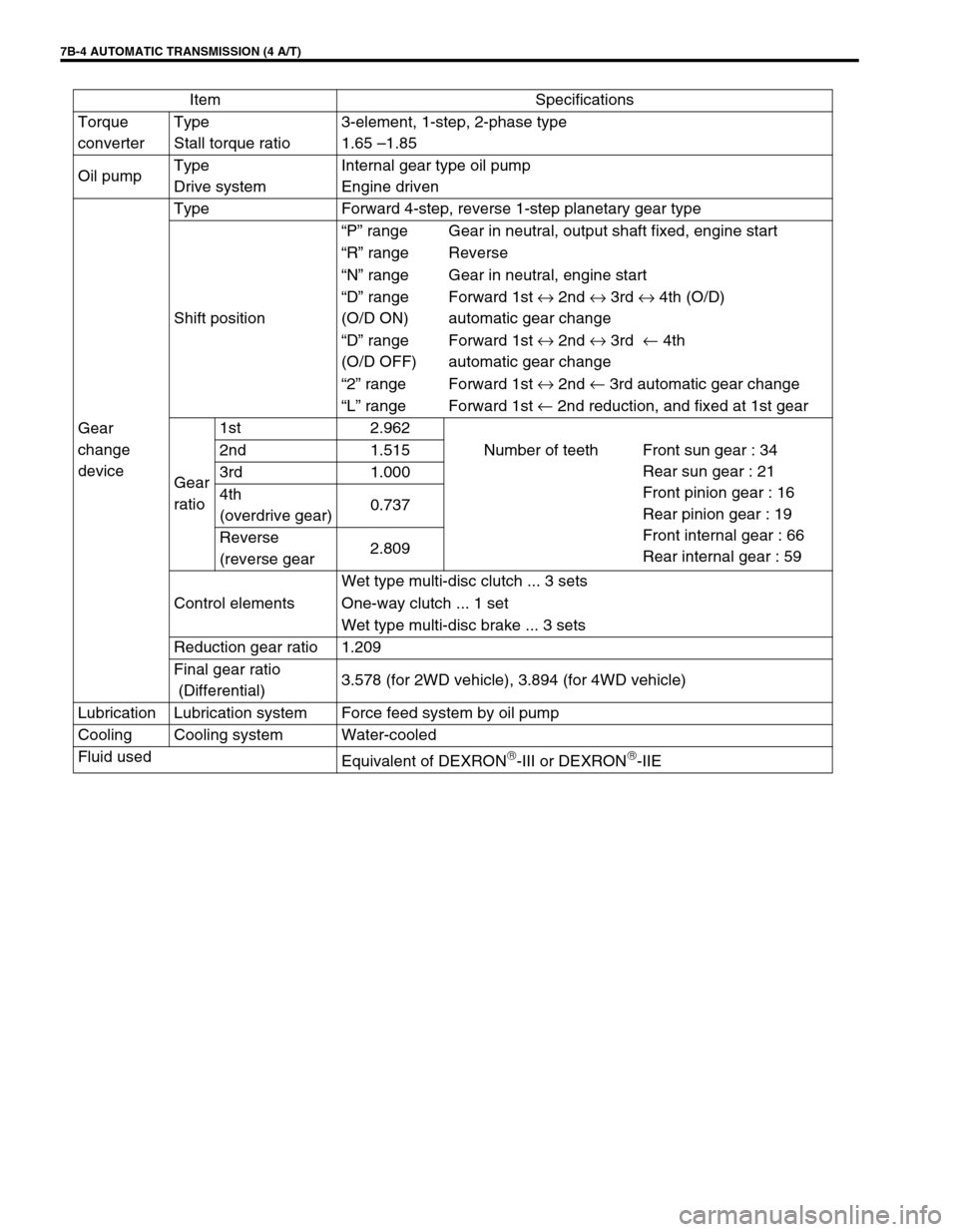
7B-4 AUTOMATIC TRANSMISSION (4 A/T)
Item Specifications
Torque
converterType
Stall torque ratio3-element, 1-step, 2-phase type
1.65 –1.85
Oil pumpType
Drive systemInternal gear type oil pump
Engine driven
Gear
change
deviceType Forward 4-step, reverse 1-step planetary gear type
Shift position“P” range Gear in neutral, output shaft fixed, engine start
“R” range Reverse
“N” range Gear in neutral, engine start
“D” range
(O/D ON)Forward 1st ↔
2nd ↔
3rd ↔
4th (O/D)
automatic gear change
“D” range
(O/D OFF)Forward 1st ↔
2nd ↔
3rd ←
4th
automatic gear change
“2” range Forward 1st ↔
2nd ←
3rd automatic gear change
“L” range Forward 1st ←
2nd reduction, and fixed at 1st gear
Gear
ratio1st 2.962
2nd 1.515 Number of teeth Front sun gear : 34
Rear sun gear : 21
Front pinion gear : 16
Rear pinion gear : 19
Front internal gear : 66
Rear internal gear : 59 3rd 1.000
4th
(overdrive gear)0.737
Reverse
(reverse gear2.809
Control elementsWet type multi-disc clutch ... 3 sets
One-way clutch ... 1 set
Wet type multi-disc brake ... 3 sets
Reduction gear ratio 1.209
Final gear ratio
(Differential)3.578 (for 2WD vehicle), 3.894 (for 4WD vehicle)
Lubrication Lubrication system Force feed system by oil pump
Cooling Cooling system Water-cooled
Fluid used
Equivalent of DEXRON
-III or DEXRON-IIE
Page 48 of 447
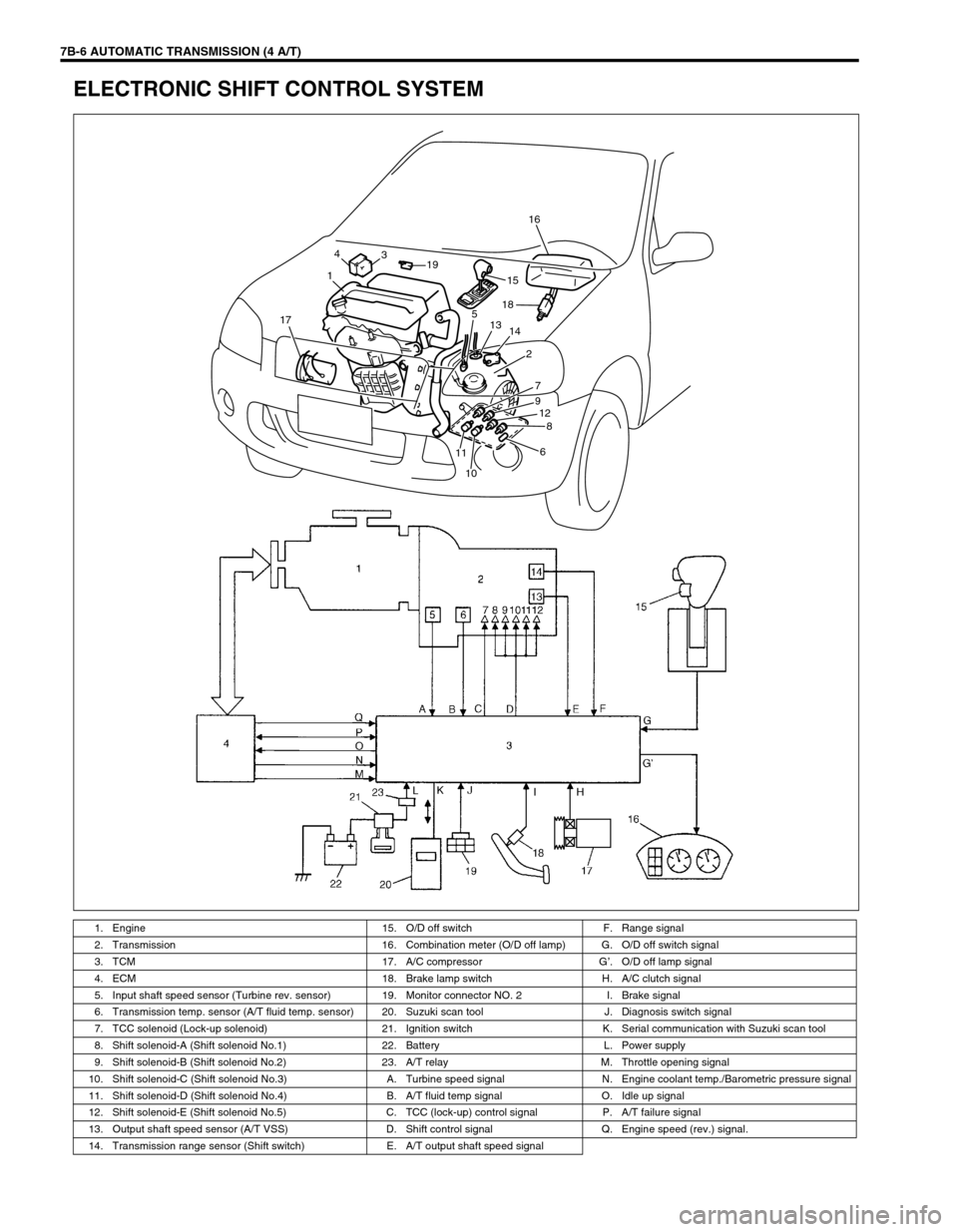
7B-6 AUTOMATIC TRANSMISSION (4 A/T)
ELECTRONIC SHIFT CONTROL SYSTEM
1. Engine 15. O/D off switch F. Range signal
2. Transmission 16. Combination meter (O/D off lamp) G. O/D off switch signal
3. TCM 17. A/C compressor G’. O/D off lamp signal
4. ECM 18. Brake lamp switch H. A/C clutch signal
5. Input shaft speed sensor (Turbine rev. sensor) 19. Monitor connector NO. 2 I. Brake signal
6. Transmission temp. sensor (A/T fluid temp. sensor) 20. Suzuki scan tool J. Diagnosis switch signal
7. TCC solenoid (Lock-up solenoid) 21. Ignition switch K. Serial communication with Suzuki scan tool
8. Shift solenoid-A (Shift solenoid No.1) 22. Battery L. Power supply
9. Shift solenoid-B (Shift solenoid No.2) 23. A/T relay M. Throttle opening signal
10. Shift solenoid-C (Shift solenoid No.3) A. Turbine speed signal N. Engine coolant temp./Barometric pressure signal
11. Shift solenoid-D (Shift solenoid No.4) B. A/T fluid temp signal O. Idle up signal
12. Shift solenoid-E (Shift solenoid No.5) C. TCC (lock-up) control signal P. A/T failure signal
13. Output shaft speed sensor (A/T VSS) D. Shift control signal Q. Engine speed (rev.) signal.
14. Transmission range sensor (Shift switch) E. A/T output shaft speed signal
14
3
19
15
1816
14 13 5
2
7
9
12
8
6
10 17
11
Page 49 of 447
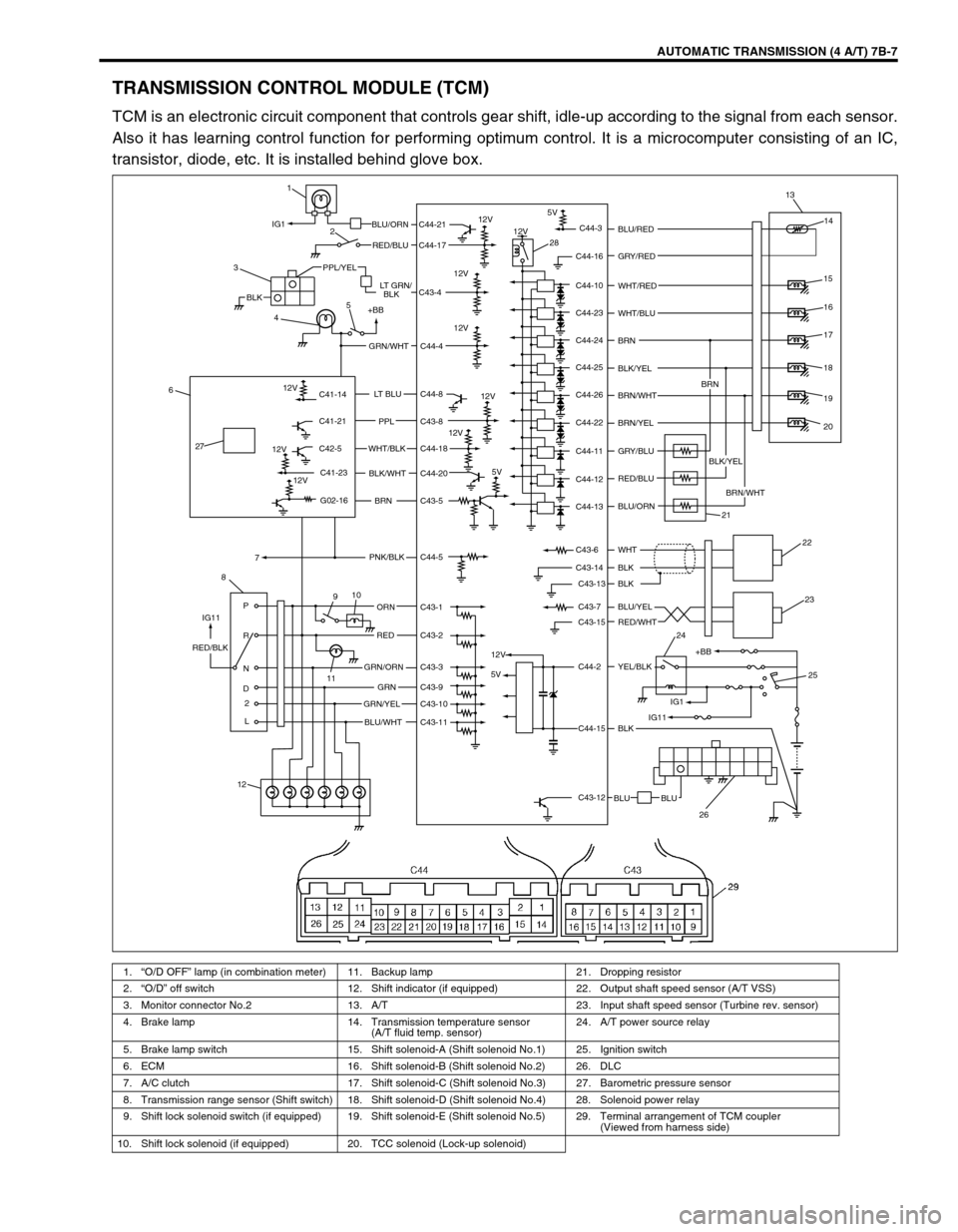
AUTOMATIC TRANSMISSION (4 A/T) 7B-7
TRANSMISSION CONTROL MODULE (TCM)
TCM is an electronic circuit component that controls gear shift, idle-up according to the signal from each sensor.
Also it has learning control function for performing optimum control. It is a microcomputer consisting of an IC,
transistor, diode, etc. It is installed behind glove box.
1.“O/D OFF” lamp (in combination meter) 11. Backup lamp 21. Dropping resistor
2.“O/D” off switch 12. Shift indicator (if equipped) 22. Output shaft speed sensor (A/T VSS)
3. Monitor connector No.2 13. A/T 23. Input shaft speed sensor (Turbine rev. sensor)
4. Brake lamp 14. Transmission temperature sensor
(A/T fluid temp. sensor)24. A/T power source relay
5. Brake lamp switch 15. Shift solenoid-A (Shift solenoid No.1) 25. Ignition switch
6. ECM 16. Shift solenoid-B (Shift solenoid No.2) 26. DLC
7. A/C clutch 17. Shift solenoid-C (Shift solenoid No.3) 27. Barometric pressure sensor
8. Transmission range sensor (Shift switch) 18. Shift solenoid-D (Shift solenoid No.4) 28. Solenoid power relay
9. Shift lock solenoid switch (if equipped) 19. Shift solenoid-E (Shift solenoid No.5) 29. Terminal arrangement of TCM coupler
(Viewed from harness side)
10. Shift lock solenoid (if equipped) 20. TCC solenoid (Lock-up solenoid)
C41-14
C41-21
C42-5
C41-23
G02-16
BLKBLKLT GRN/ RED/BLU BLU/ORN
PPL/YEL
3
45
+BB
GRN/WHT
LT BLU
PPL
WHT/BLK
BLK/WHT
BRN
PNK/BLK 6
7
8
C44-8
C43-8
C44-18
C44-20
C43-5
C44-5
910
ORN
RED
GRN/ORN RED/BLK
GRNC43-1
C43-2
C43-3
C43-9
C43-10
C43-11 GRN/YEL
BLU/WHT P
R
N
D
2
L11
12C44-21
C44-17
C43-4
C44-4
12V 12V
12V
12V
12V IG1
IG115V
5VC44-3
C44-16
C44-10
C44-23
C44-24
C44-25
C44-26
C44-22
C44-11
C44-12
C44-13
C43-6
C43-14
C43-13
C43-7
C43-15
C44-2
C44-15
C43-12
BLU BLUBLK
BLK BLK
BLU/YEL
YEL/BLK RED/WHT WHT BLU/ORN RED/BLU GRY/BLU
BLK/YEL WHT/BLU
BRN/WHT BRN/WHT BRN WHT/RED
BLK/YEL
BRN/YEL BLU/RED
GRY/RED13
14
15
16
17
19
20 BRN
21
22
23
+BB 24
25
26
12V
12V
12V
12V
18
12V
IG1
IG11
5V
1
2
28
27
Page 51 of 447

AUTOMATIC TRANSMISSION (4 A/T) 7B-9
A/T hardware itself
(DTC P0730)Difference in detected
revolution between
input shaft speed
sensor and output
shaft speed sensor is
too wide.“P” range →
P, “R” range →
R, “N” range →
N,
“D”/“2”/“L” range “To be controlled as follows :
1) When detecting trouble at first, gear is selected well-suited
gear calculated with parameters of each sensor’s rev. num-
ber and gear position just when the trouble occurred. Lock-
up function is turned OFF.
2) If A/T can transmit driving force under the above condition,
gear is fixed the selected gear until ignition switch is turned
OFF.
3) If A/T can not transmit driving force under the above condi-
tion, after once vehicle stop, gear which can transmit drive
force is searched one by one until gear is found out. After
gear is found out, position of gear is held until ignition switch
is turned OFF.
Transmission
range sensor cir-
cuit
(DTC P0705)No shift switch signal
is inputted or two or
more shift switch sig-
nals are inputted at
the same time.When vehicle running, shift range position is fixed to shift
range position right before the trouble occurred until vehicle
stop and lock-up function is turned OFF.
When vehicle is at stop after or during detecting the trouble,
gear is fixed as the followings and lock-up function is turned
OFF.
–When 2 adjoining gear position signals are inputted.
“P”, “R” range →
R, “R”, “N” range →
R,
“N”, “D” range →
D, “D”, “2” range →
D,
“2”, “L” range →
2nd
–When 2 or more signals excepting above or no signal are
inputted.
“P” range →
P, “R” range →
R,
“N” range →
N, “D”/“2”/“L” range →
3rd
Transmission tem-
perature sensor cir-
cuit
(DTC P0710)A/T fluid temp. sig-
nal input voltage is
too low.
A/T fluid temp. sig-
nal input voltage
does not go down
although standard
value of engine
rev. signal is input-
ted.When detecting circuit open, TCM control as fluid tempera-
ture is 100°C (212°F).
Lock-up function is turned OFF.
Engine speed input
circuit
(DTC P0725)Inputted engine rev.
signal is too low or
too high.Engine rev. is processed as 4000 rpm.
No compensation or judgement for gear shift control, for
which engine rev. is considered, is processed.
Lock-up function is turned OFF.
Engine coolant
temp./Barometric
pressure signal cir-
cuit
(DTC P1709)No or abnormal
engine coolant temp.
signal is inputtedNo compensation for gear shift control, for which engine cool-
ant temp. and barometric pressure are considered, is pro-
cessed.
Lock -up function is turned OFF. Area Detecting condition Fail safe function
Page 58 of 447
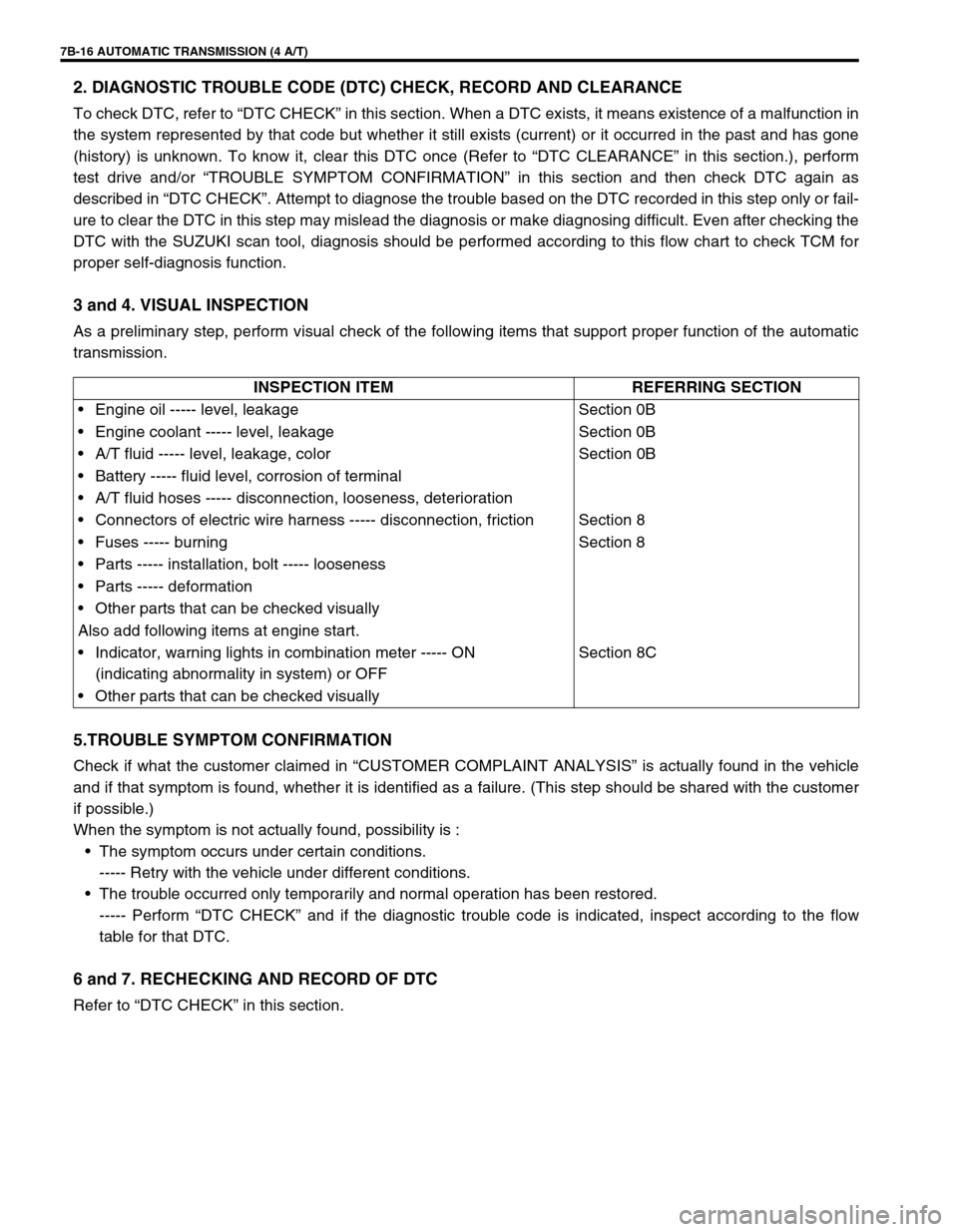
7B-16 AUTOMATIC TRANSMISSION (4 A/T)
2. DIAGNOSTIC TROUBLE CODE (DTC) CHECK, RECORD AND CLEARANCE
To check DTC, refer to “DTC CHECK” in this section. When a DTC exists, it means existence of a malfunction in
the system represented by that code but whether it still exists (current) or it occurred in the past and has gone
(history) is unknown. To know it, clear this DTC once (Refer to “DTC CLEARANCE” in this section.), perform
test drive and/or “TROUBLE SYMPTOM CONFIRMATION” in this section and then check DTC again as
described in “DTC CHECK”. Attempt to diagnose the trouble based on the DTC recorded in this step only or fail-
ure to clear the DTC in this step may mislead the diagnosis or make diagnosing difficult. Even after checking the
DTC with the SUZUKI scan tool, diagnosis should be performed according to this flow chart to check TCM for
proper self-diagnosis function.
3 and 4. VISUAL INSPECTION
As a preliminary step, perform visual check of the following items that support proper function of the automatic
transmission.
5.TROUBLE SYMPTOM CONFIRMATION
Check if what the customer claimed in “CUSTOMER COMPLAINT ANALYSIS” is actually found in the vehicle
and if that symptom is found, whether it is identified as a failure. (This step should be shared with the customer
if possible.)
When the symptom is not actually found, possibility is :
The symptom occurs under certain conditions.
----- Retry with the vehicle under different conditions.
The trouble occurred only temporarily and normal operation has been restored.
----- Perform “DTC CHECK” and if the diagnostic trouble code is indicated, inspect according to the flow
table for that DTC.
6 and 7. RECHECKING AND RECORD OF DTC
Refer to “DTC CHECK” in this section.INSPECTION ITEM REFERRING SECTION
Engine oil ----- level, leakage Section 0B
Engine coolant ----- level, leakage Section 0B
A/T fluid ----- level, leakage, color Section 0B
Battery ----- fluid level, corrosion of terminal
A/T fluid hoses ----- disconnection, looseness, deterioration
Connectors of electric wire harness ----- disconnection, friction Section 8
Fuses ----- burning Section 8
Parts ----- installation, bolt ----- looseness
Parts ----- deformation
Other parts that can be checked visually
Also add following items at engine start.
Indicator, warning lights in combination meter ----- ON
(indicating abnormality in system) or OFFSection 8C
Other parts that can be checked visually
Page 59 of 447
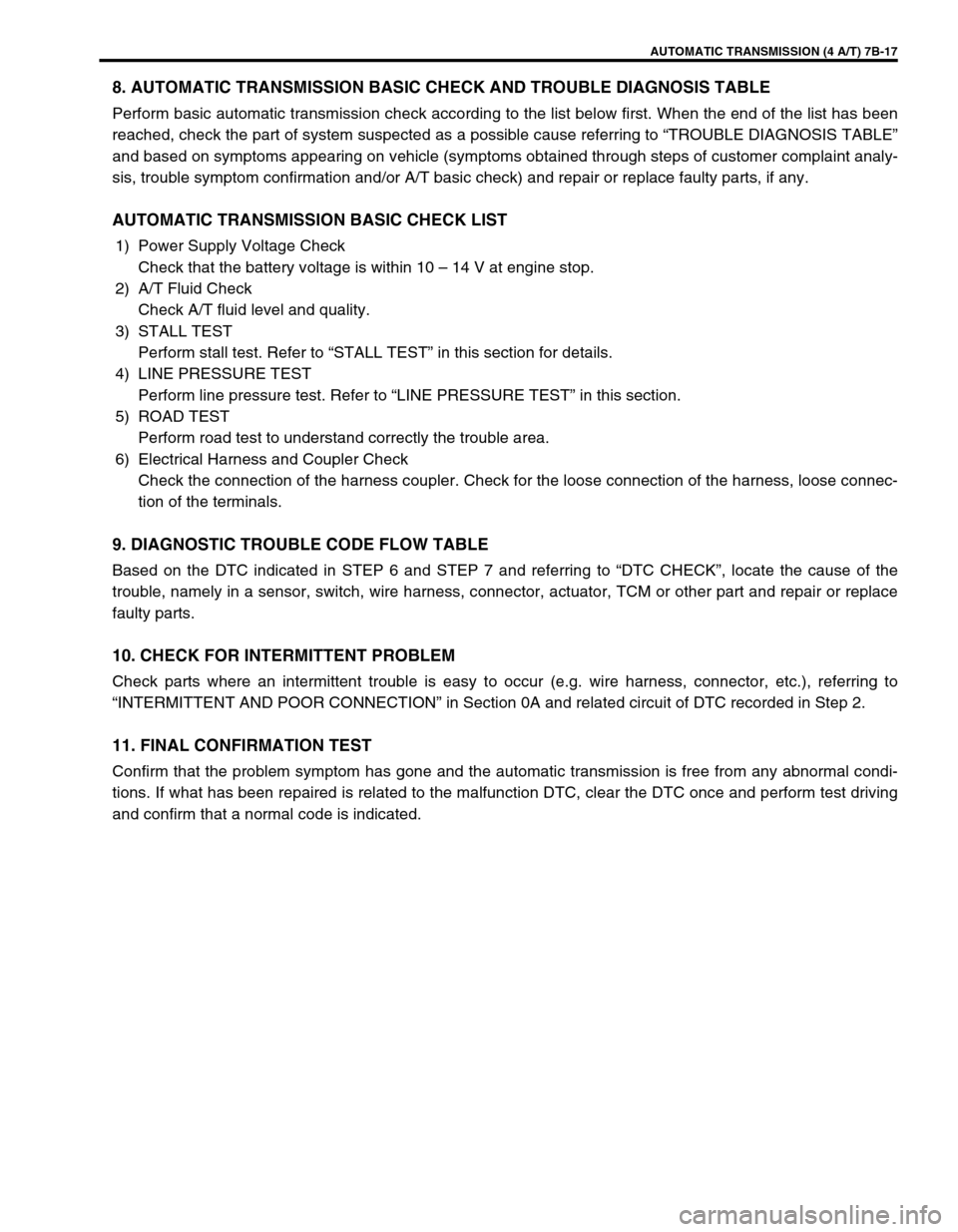
AUTOMATIC TRANSMISSION (4 A/T) 7B-17
8. AUTOMATIC TRANSMISSION BASIC CHECK AND TROUBLE DIAGNOSIS TABLE
Perform basic automatic transmission check according to the list below first. When the end of the list has been
reached, check the part of system suspected as a possible cause referring to “TROUBLE DIAGNOSIS TABLE”
and based on symptoms appearing on vehicle (symptoms obtained through steps of customer complaint analy-
sis, trouble symptom confirmation and/or A/T basic check) and repair or replace faulty parts, if any.
AUTOMATIC TRANSMISSION BASIC CHECK LIST
1) Power Supply Voltage Check
Check that the battery voltage is within 10 – 14 V at engine stop.
2) A/T Fluid Check
Check A/T fluid level and quality.
3) STALL TEST
Perform stall test. Refer to “STALL TEST” in this section for details.
4) LINE PRESSURE TEST
Perform line pressure test. Refer to “LINE PRESSURE TEST” in this section.
5) ROAD TEST
Perform road test to understand correctly the trouble area.
6) Electrical Harness and Coupler Check
Check the connection of the harness coupler. Check for the loose connection of the harness, loose connec-
tion of the terminals.
9. DIAGNOSTIC TROUBLE CODE FLOW TABLE
Based on the DTC indicated in STEP 6 and STEP 7 and referring to “DTC CHECK”, locate the cause of the
trouble, namely in a sensor, switch, wire harness, connector, actuator, TCM or other part and repair or replace
faulty parts.
10. CHECK FOR INTERMITTENT PROBLEM
Check parts where an intermittent trouble is easy to occur (e.g. wire harness, connector, etc.), referring to
“INTERMITTENT AND POOR CONNECTION” in Section 0A and related circuit of DTC recorded in Step 2.
11. FINAL CONFIRMATION TEST
Confirm that the problem symptom has gone and the automatic transmission is free from any abnormal condi-
tions. If what has been repaired is related to the malfunction DTC, clear the DTC once and perform test driving
and confirm that a normal code is indicated.
Page 62 of 447
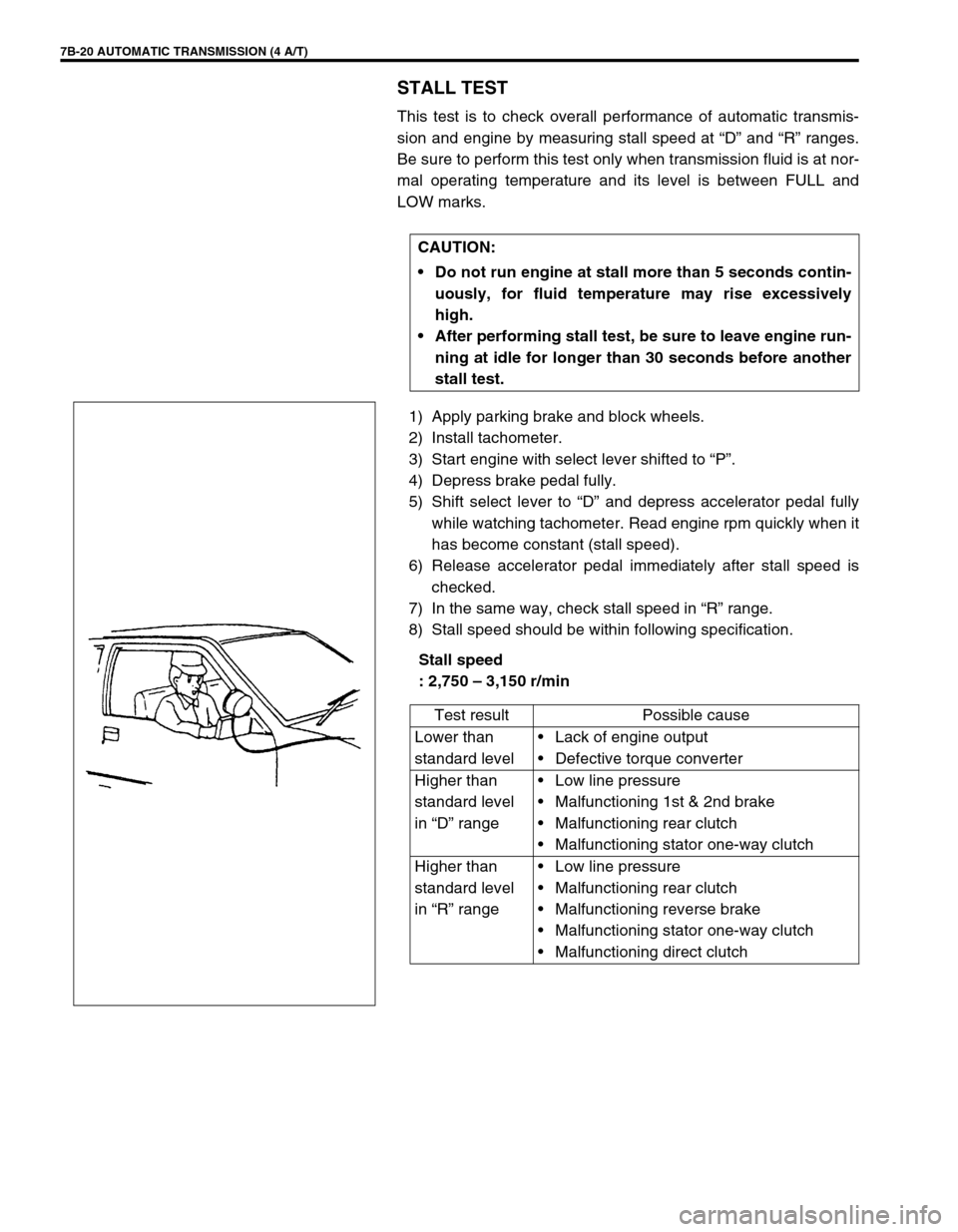
7B-20 AUTOMATIC TRANSMISSION (4 A/T)
STALL TEST
This test is to check overall performance of automatic transmis-
sion and engine by measuring stall speed at “D” and “R” ranges.
Be sure to perform this test only when transmission fluid is at nor-
mal operating temperature and its level is between FULL and
LOW marks.
1) Apply parking brake and block wheels.
2) Install tachometer.
3) Start engine with select lever shifted to “P”.
4) Depress brake pedal fully.
5) Shift select lever to “D” and depress accelerator pedal fully
while watching tachometer. Read engine rpm quickly when it
has become constant (stall speed).
6) Release accelerator pedal immediately after stall speed is
checked.
7) In the same way, check stall speed in “R” range.
8) Stall speed should be within following specification.
Stall speed
: 2,750 – 3,150 r/min CAUTION:
Do not run engine at stall more than 5 seconds contin-
uously, for fluid temperature may rise excessively
high.
After performing stall test, be sure to leave engine run-
ning at idle for longer than 30 seconds before another
stall test.
Test result Possible cause
Lower than
standard levelLack of engine output
Defective torque converter
Higher than
standard level
in “D” rangeLow line pressure
Malfunctioning 1st & 2nd brake
Malfunctioning rear clutch
Malfunctioning stator one-way clutch
Higher than
standard level
in “R” rangeLow line pressure
Malfunctioning rear clutch
Malfunctioning reverse brake
Malfunctioning stator one-way clutch
Malfunctioning direct clutch
Page 63 of 447

AUTOMATIC TRANSMISSION (4 A/T) 7B-21
TIME LAG TEST
This test is to check conditions of clutch, reverse brake and fluid
pressure. “Time lag” means time elapsed since select lever is
shifted with engine idling till shock is felt.
1) With chocks placed in front and behind front and rear wheels
respectively, depress brake pedal.
2) Start engine.
3) With stop watch ready, shift select lever from “N” to “D”
range and measure time from that moment till shock is felt.
4) Similarly measure time lag by shifting select lever from “N” to
“R” range.
Specification for time lag
“N”
→
→ → → “D” : Less than 1.0 sec.
“N”
→
→→ → “R” : Less than 1.2 sec.
NOTE:
Make sure that selector cable is properly adjusted.
When repeating this test, be sure to wait at least
minute after select lever is shifted back to “N” range.
Engine should be warmed up fully for this test.
Test result Possible cause
When “N” →
“D”
time lag exceeds specification.Low line pressure
Worn rear clutch
Worn 1st & 2nd brake
When “N” →
“R”
time lag exceeds specification.Low line pressure
Worn rear clutch
Worn direct clutch
Worn reverse brake
Page 64 of 447
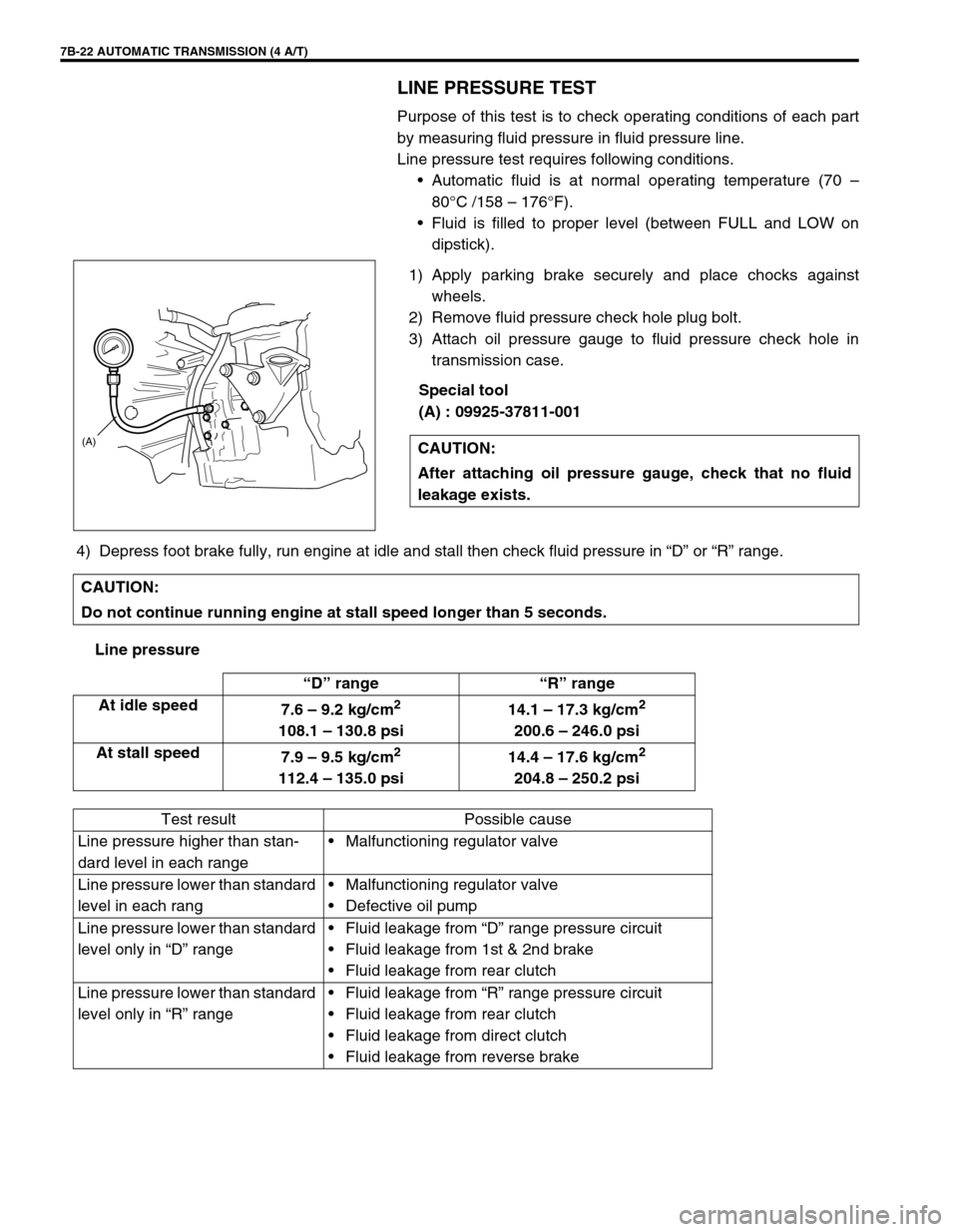
7B-22 AUTOMATIC TRANSMISSION (4 A/T)
LINE PRESSURE TEST
Purpose of this test is to check operating conditions of each part
by measuring fluid pressure in fluid pressure line.
Line pressure test requires following conditions.
Automatic fluid is at normal operating temperature (70 –
80°C /158 – 176°F).
Fluid is filled to proper level (between FULL and LOW on
dipstick).
1) Apply parking brake securely and place chocks against
wheels.
2) Remove fluid pressure check hole plug bolt.
3) Attach oil pressure gauge to fluid pressure check hole in
transmission case.
Special tool
(A) : 09925-37811-001
4) Depress foot brake fully, run engine at idle and stall then check fluid pressure in “D” or “R” range.
Line pressureCAUTION:
After attaching oil pressure gauge, check that no fluid
leakage exists.
(A)
CAUTION:
Do not continue running engine at stall speed longer than 5 seconds.
“D” range “R” range
At idle speed
7.6 – 9.2 kg/cm
2
108.1 – 130.8 psi14.1 – 17.3 kg/cm
2
200.6 – 246.0 psi
At stall speed
7.9 – 9.5 kg/cm
2
112.4 – 135.0 psi14.4 – 17.6 kg/cm
2
204.8 – 250.2 psi
Test result Possible cause
Line pressure higher than stan-
dard level in each rangeMalfunctioning regulator valve
Line pressure lower than standard
level in each rangMalfunctioning regulator valve
Defective oil pump
Line pressure lower than standard
level only in “D” rangeFluid leakage from “D” range pressure circuit
Fluid leakage from 1st & 2nd brake
Fluid leakage from rear clutch
Line pressure lower than standard
level only in “R” rangeFluid leakage from “R” range pressure circuit
Fluid leakage from rear clutch
Fluid leakage from direct clutch
Fluid leakage from reverse brake