automatic transmission fluid SUZUKI SWIFT 2000 1.G Transmission Service Owner's Guide
[x] Cancel search | Manufacturer: SUZUKI, Model Year: 2000, Model line: SWIFT, Model: SUZUKI SWIFT 2000 1.GPages: 447, PDF Size: 10.54 MB
Page 138 of 447
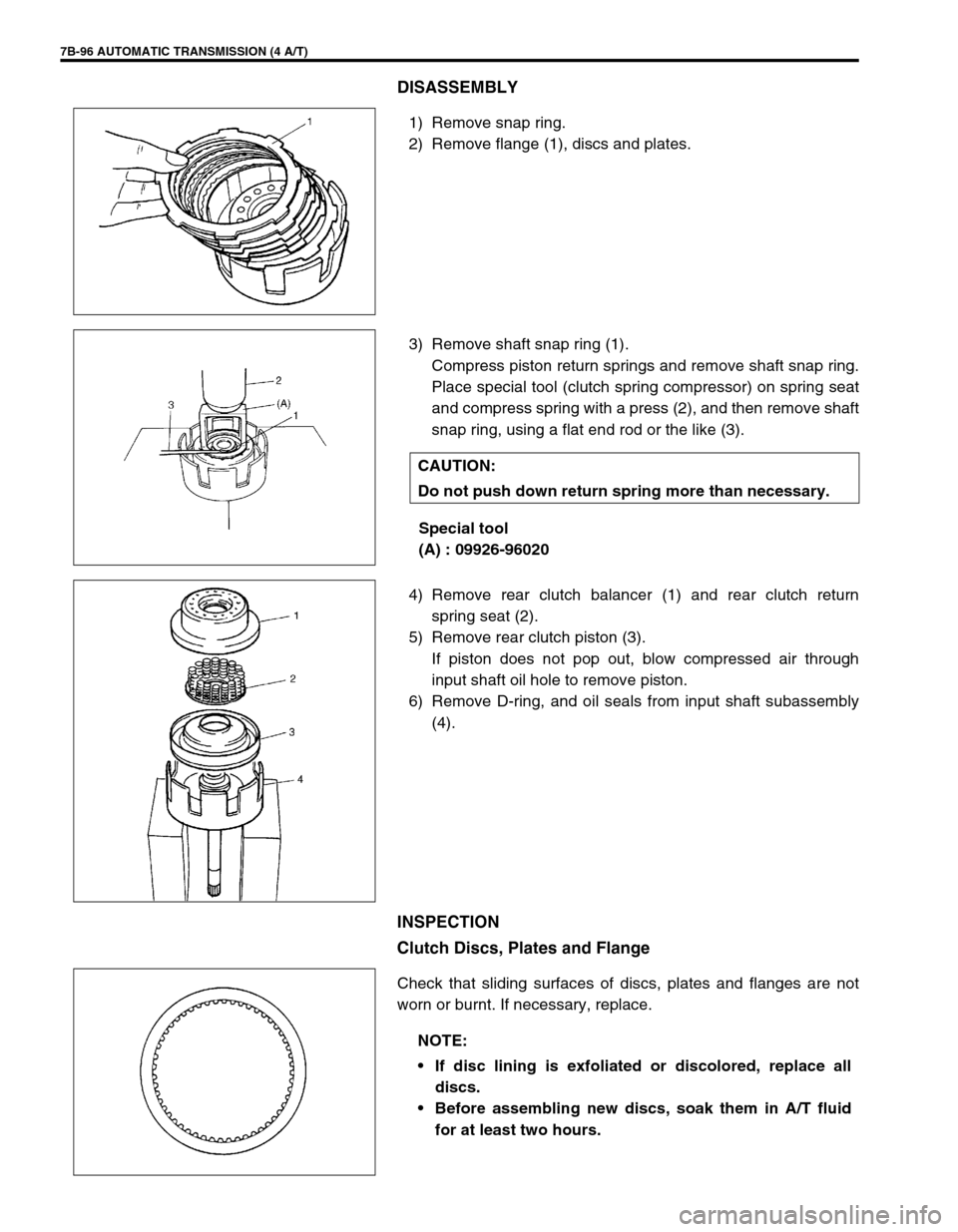
7B-96 AUTOMATIC TRANSMISSION (4 A/T)
DISASSEMBLY
1) Remove snap ring.
2) Remove flange (1), discs and plates.
3) Remove shaft snap ring (1).
Compress piston return springs and remove shaft snap ring.
Place special tool (clutch spring compressor) on spring seat
and compress spring with a press (2), and then remove shaft
snap ring, using a flat end rod or the like (3).
Special tool
(A) : 09926-96020
4) Remove rear clutch balancer (1) and rear clutch return
spring seat (2).
5) Remove rear clutch piston (3).
If piston does not pop out, blow compressed air through
input shaft oil hole to remove piston.
6) Remove D-ring, and oil seals from input shaft subassembly
(4).
INSPECTION
Clutch Discs, Plates and Flange
Check that sliding surfaces of discs, plates and flanges are not
worn or burnt. If necessary, replace.
CAUTION:
Do not push down return spring more than necessary.
NOTE:
If disc lining is exfoliated or discolored, replace all
discs.
Before assembling new discs, soak them in A/T fluid
for at least two hours.
Page 140 of 447
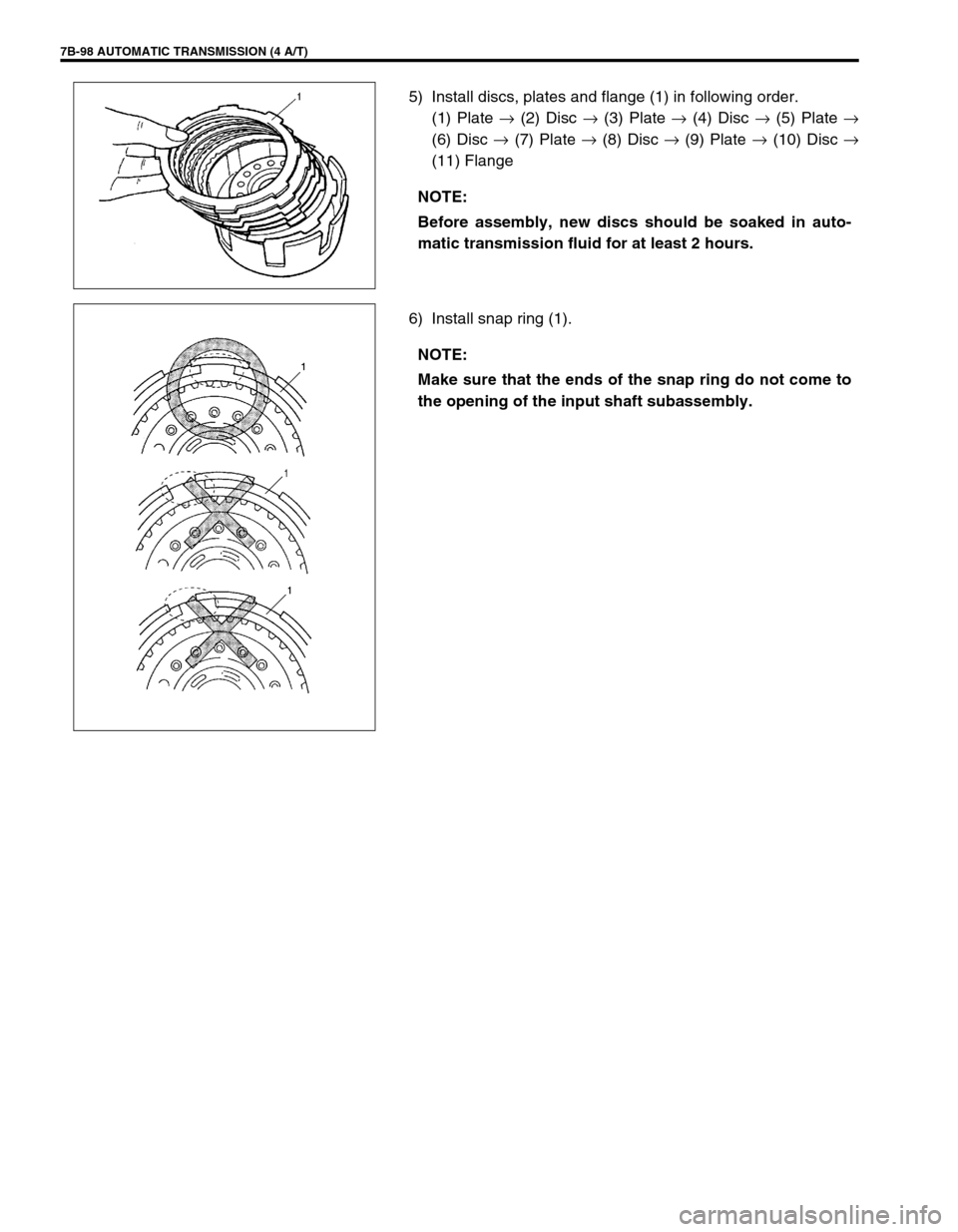
7B-98 AUTOMATIC TRANSMISSION (4 A/T)
5) Install discs, plates and flange (1) in following order.
(1) Plate →
(2) Disc →
(3) Plate →
(4) Disc →
(5) Plate →
(6) Disc →
(7) Plate →
(8) Disc →
(9) Plate →
(10) Disc →
(11) Flange
6) Install snap ring (1).NOTE:
Before assembly, new discs should be soaked in auto-
matic transmission fluid for at least 2 hours.
NOTE:
Make sure that the ends of the snap ring do not come to
the opening of the input shaft subassembly.
Page 142 of 447
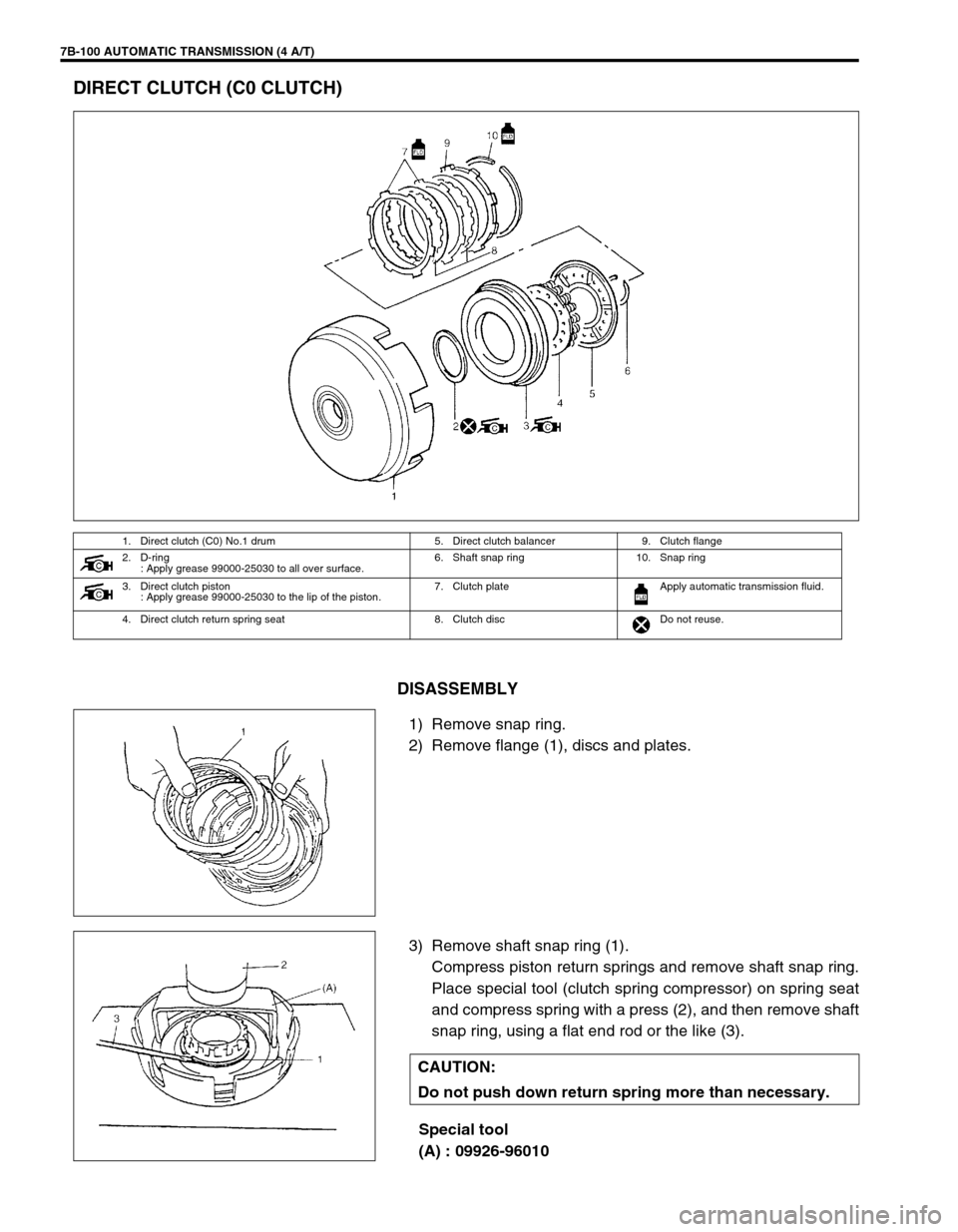
7B-100 AUTOMATIC TRANSMISSION (4 A/T)
DIRECT CLUTCH (C0 CLUTCH)
DISASSEMBLY
1) Remove snap ring.
2) Remove flange (1), discs and plates.
3) Remove shaft snap ring (1).
Compress piston return springs and remove shaft snap ring.
Place special tool (clutch spring compressor) on spring seat
and compress spring with a press (2), and then remove shaft
snap ring, using a flat end rod or the like (3).
Special tool
(A) : 09926-96010
1. Direct clutch (C0) No.1 drum 5. Direct clutch balancer 9. Clutch flange
2. D-ring
: Apply grease 99000-25030 to all over surface.6. Shaft snap ring 10. Snap ring
3. Direct clutch piston
: Apply grease 99000-25030 to the lip of the piston.7. Clutch plate Apply automatic transmission fluid.
4. Direct clutch return spring seat 8. Clutch disc Do not reuse.
CAUTION:
Do not push down return spring more than necessary.
Page 143 of 447
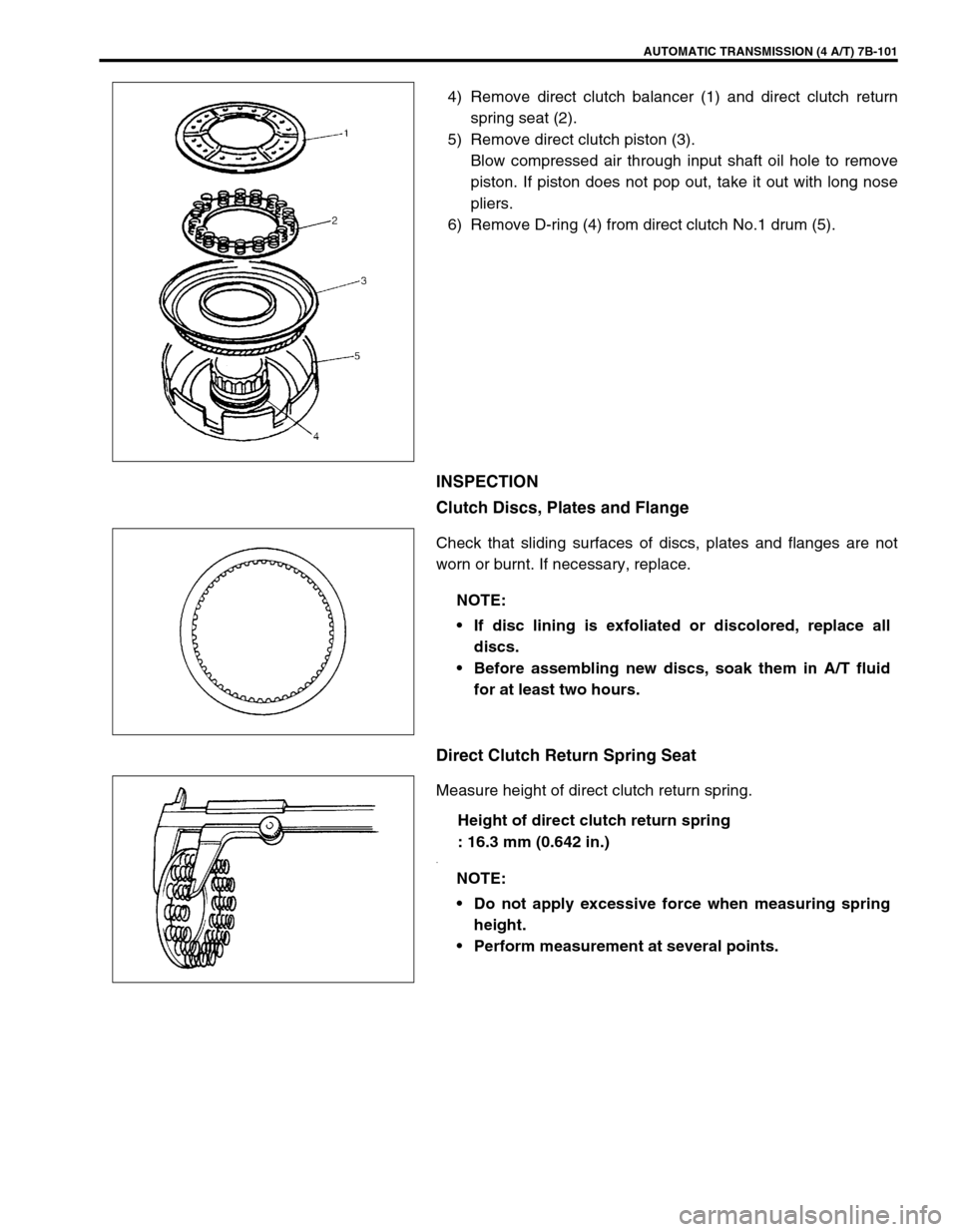
AUTOMATIC TRANSMISSION (4 A/T) 7B-101
4) Remove direct clutch balancer (1) and direct clutch return
spring seat (2).
5) Remove direct clutch piston (3).
Blow compressed air through input shaft oil hole to remove
piston. If piston does not pop out, take it out with long nose
pliers.
6) Remove D-ring (4) from direct clutch No.1 drum (5).
INSPECTION
Clutch Discs, Plates and Flange
Check that sliding surfaces of discs, plates and flanges are not
worn or burnt. If necessary, replace.
Direct Clutch Return Spring Seat
Measure height of direct clutch return spring.
Height of direct clutch return spring
: 16.3 mm (0.642 in.)
.
NOTE:
If disc lining is exfoliated or discolored, replace all
discs.
Before assembling new discs, soak them in A/T fluid
for at least two hours.
NOTE:
Do not apply excessive force when measuring spring
height.
Perform measurement at several points.
Page 144 of 447
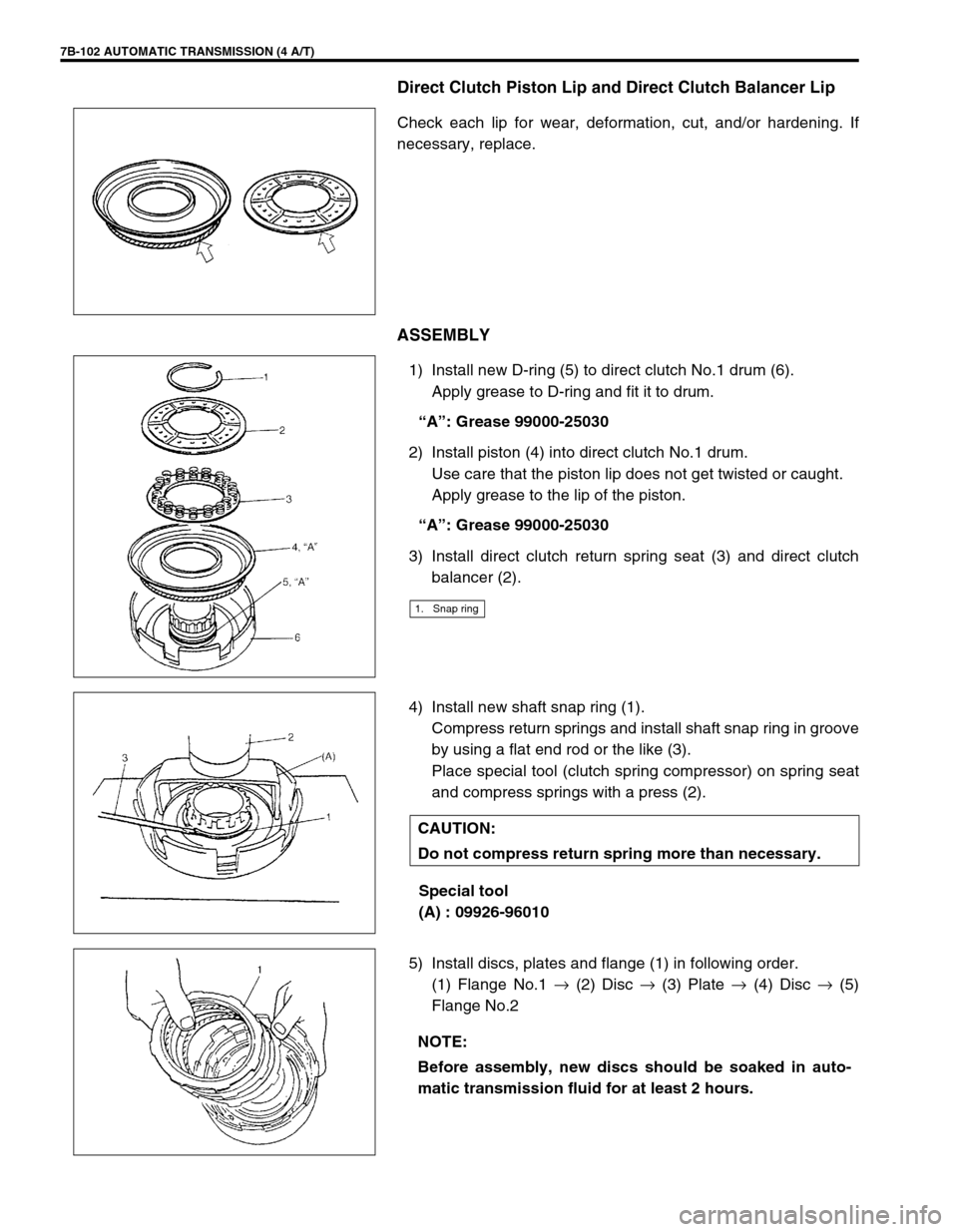
7B-102 AUTOMATIC TRANSMISSION (4 A/T)
Direct Clutch Piston Lip and Direct Clutch Balancer Lip
Check each lip for wear, deformation, cut, and/or hardening. If
necessary, replace.
ASSEMBLY
1) Install new D-ring (5) to direct clutch No.1 drum (6).
Apply grease to D-ring and fit it to drum.
“A”: Grease 99000-25030
2) Install piston (4) into direct clutch No.1 drum.
Use care that the piston lip does not get twisted or caught.
Apply grease to the lip of the piston.
“A”: Grease 99000-25030
3) Install direct clutch return spring seat (3) and direct clutch
balancer (2).
4) Install new shaft snap ring (1).
Compress return springs and install shaft snap ring in groove
by using a flat end rod or the like (3).
Place special tool (clutch spring compressor) on spring seat
and compress springs with a press (2).
Special tool
(A) : 09926-96010
5) Install discs, plates and flange (1) in following order.
(1) Flange No.1 →
(2) Disc →
(3) Plate →
(4) Disc →
(5)
Flange No.2
1. Snap ring
CAUTION:
Do not compress return spring more than necessary.
NOTE:
Before assembly, new discs should be soaked in auto-
matic transmission fluid for at least 2 hours.
Page 146 of 447
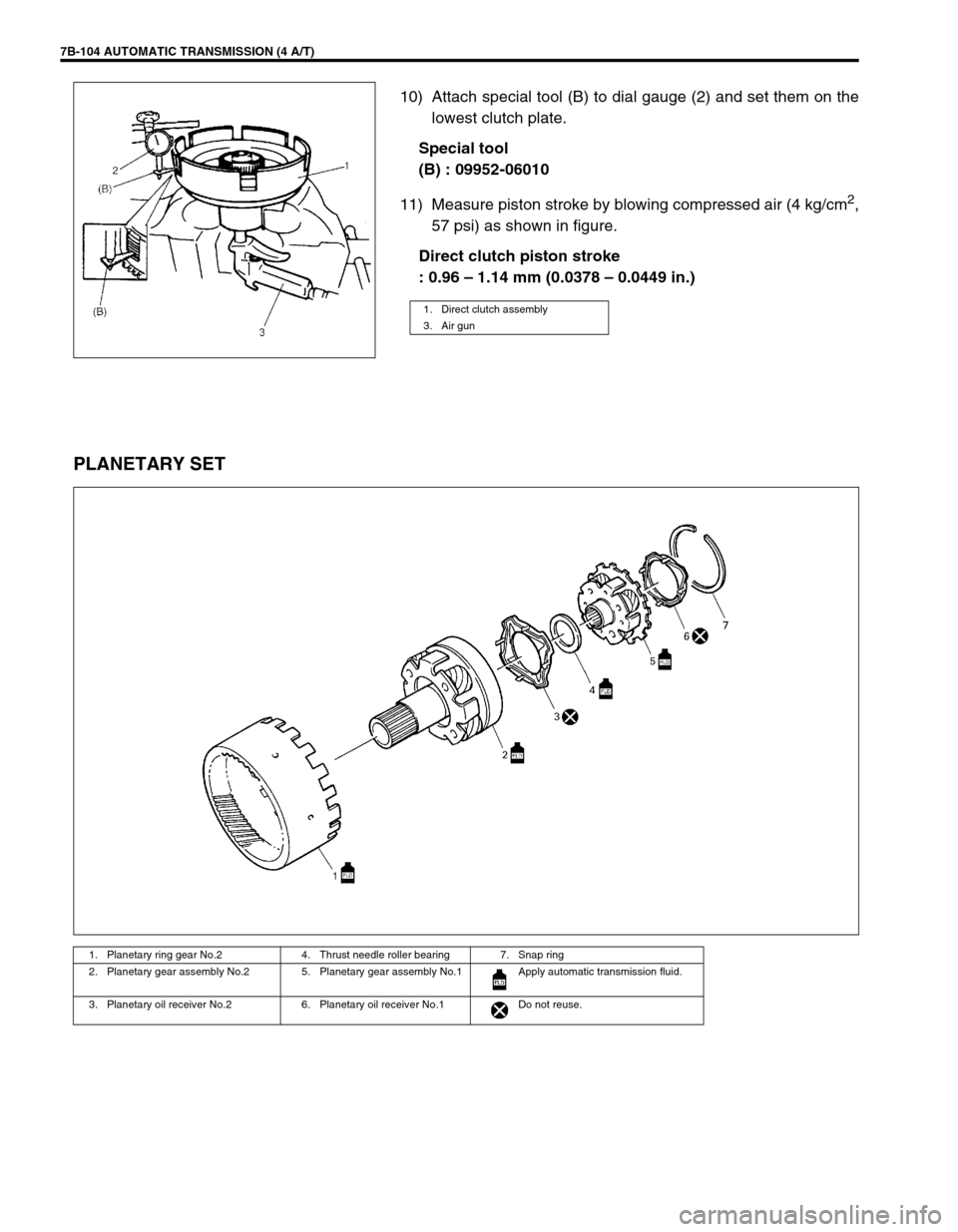
7B-104 AUTOMATIC TRANSMISSION (4 A/T)
10) Attach special tool (B) to dial gauge (2) and set them on the
lowest clutch plate.
Special tool
(B) : 09952-06010
11) Measure piston stroke by blowing compressed air (4 kg/cm
2,
57 psi) as shown in figure.
Direct clutch piston stroke
: 0.96 – 1.14 mm (0.0378 – 0.0449 in.)
PLANETARY SET
1. Direct clutch assembly
3. Air gun
1. Planetary ring gear No.2 4. Thrust needle roller bearing 7. Snap ring
2. Planetary gear assembly No.2 5. Planetary gear assembly No.1 Apply automatic transmission fluid.
3. Planetary oil receiver No.2 6. Planetary oil receiver No.1 Do not reuse.
Page 148 of 447
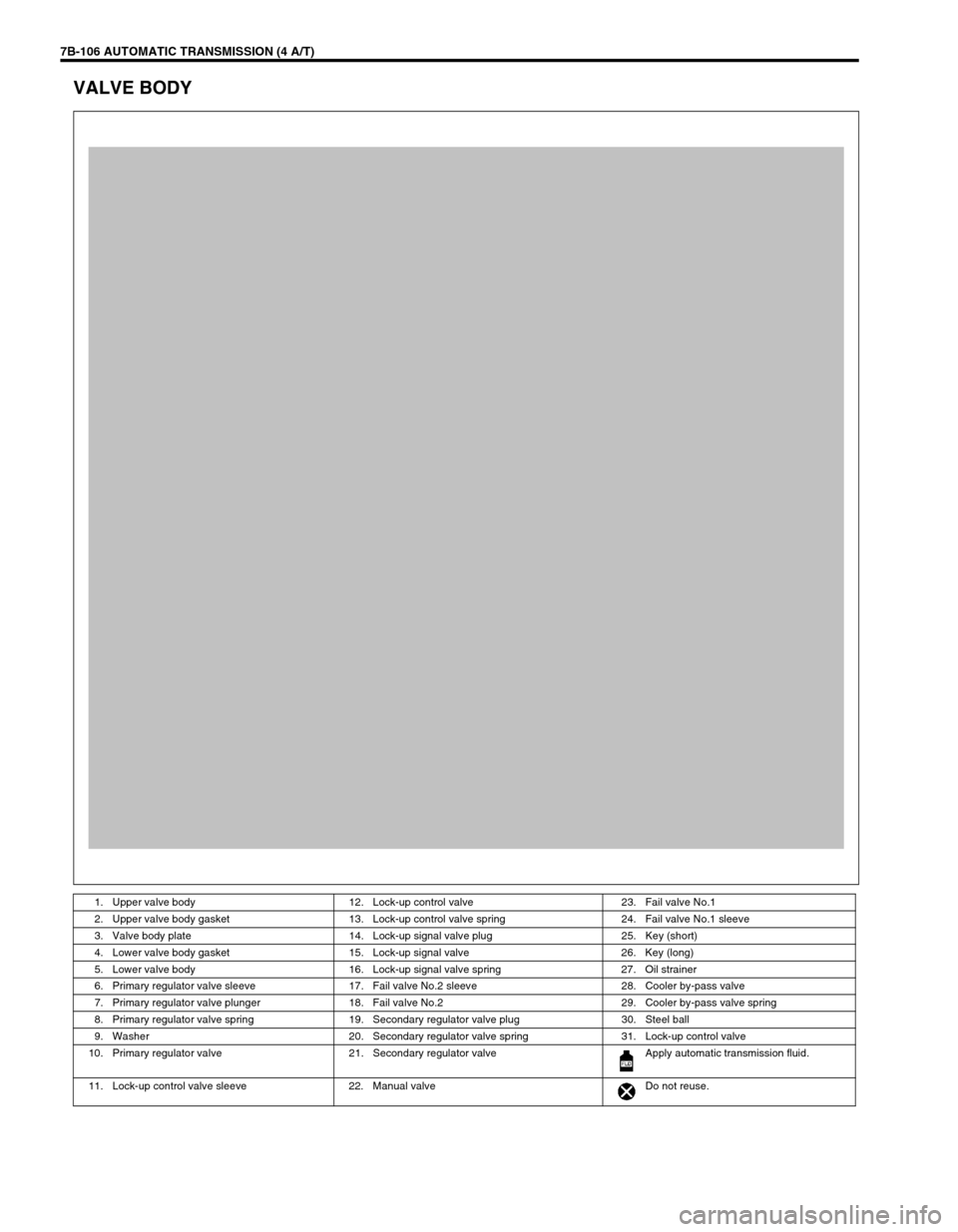
7B-106 AUTOMATIC TRANSMISSION (4 A/T)
VALVE BODY
1. Upper valve body 12. Lock-up control valve 23. Fail valve No.1
2. Upper valve body gasket 13. Lock-up control valve spring 24. Fail valve No.1 sleeve
3. Valve body plate 14. Lock-up signal valve plug 25. Key (short)
4. Lower valve body gasket 15. Lock-up signal valve 26. Key (long)
5. Lower valve body 16. Lock-up signal valve spring 27. Oil strainer
6. Primary regulator valve sleeve 17. Fail valve No.2 sleeve 28. Cooler by-pass valve
7. Primary regulator valve plunger 18. Fail valve No.2 29. Cooler by-pass valve spring
8. Primary regulator valve spring 19. Secondary regulator valve plug 30. Steel ball
9. Washer 20. Secondary regulator valve spring 31. Lock-up control valve
10. Primary regulator valve 21. Secondary regulator valve Apply automatic transmission fluid.
11. Lock-up control valve sleeve 22. Manual valve Do not reuse.
Page 151 of 447
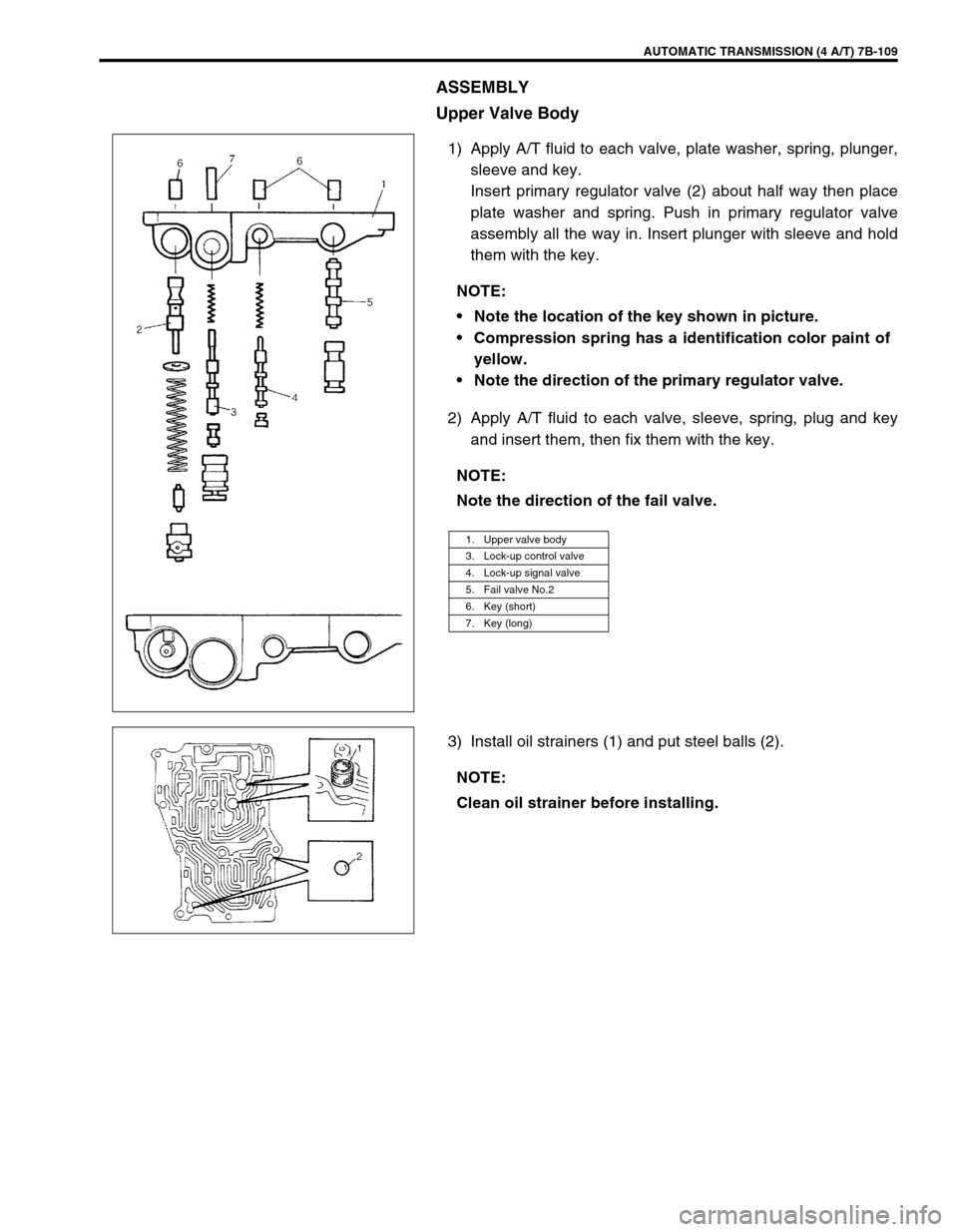
AUTOMATIC TRANSMISSION (4 A/T) 7B-109
ASSEMBLY
Upper Valve Body
1) Apply A/T fluid to each valve, plate washer, spring, plunger,
sleeve and key.
Insert primary regulator valve (2) about half way then place
plate washer and spring. Push in primary regulator valve
assembly all the way in. Insert plunger with sleeve and hold
them with the key.
2) Apply A/T fluid to each valve, sleeve, spring, plug and key
and insert them, then fix them with the key.
3) Install oil strainers (1) and put steel balls (2).NOTE:
Note the location of the key shown in picture.
Compression spring has a identification color paint of
yellow.
Note the direction of the primary regulator valve.
NOTE:
Note the direction of the fail valve.
1. Upper valve body
3. Lock-up control valve
4. Lock-up signal valve
5. Fail valve No.2
6. Key (short)
7. Key (long)
NOTE:
Clean oil strainer before installing.
Page 152 of 447
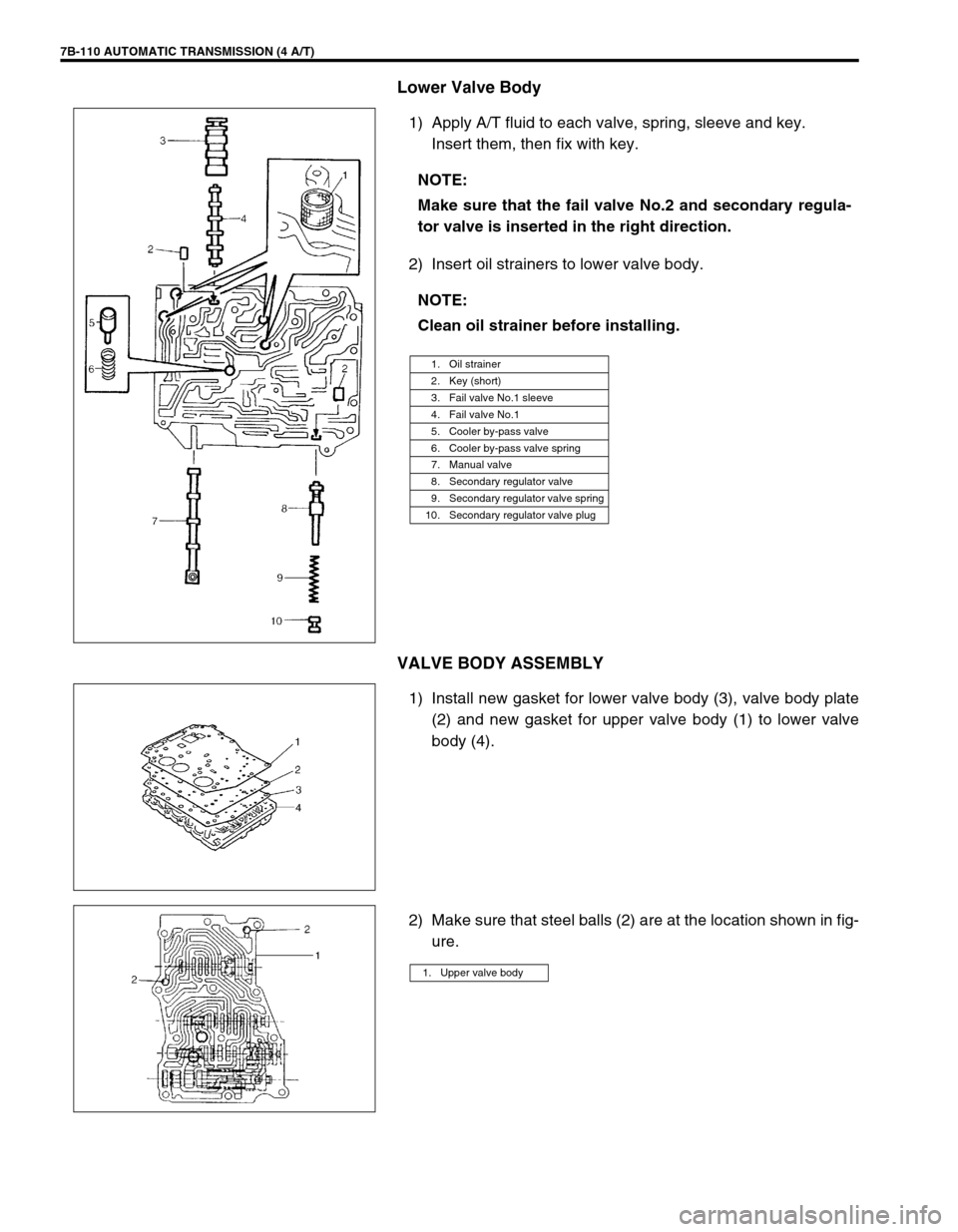
7B-110 AUTOMATIC TRANSMISSION (4 A/T)
Lower Valve Body
1) Apply A/T fluid to each valve, spring, sleeve and key.
Insert them, then fix with key.
2) Insert oil strainers to lower valve body.
VALVE BODY ASSEMBLY
1) Install new gasket for lower valve body (3), valve body plate
(2) and new gasket for upper valve body (1) to lower valve
body (4).
2) Make sure that steel balls (2) are at the location shown in fig-
ure. NOTE:
Make sure that the fail valve No.2 and secondary regula-
tor valve is inserted in the right direction.
NOTE:
Clean oil strainer before installing.
1. Oil strainer
2. Key (short)
3. Fail valve No.1 sleeve
4. Fail valve No.1
5. Cooler by-pass valve
6. Cooler by-pass valve spring
7. Manual valve
8. Secondary regulator valve
9. Secondary regulator valve spring
10. Secondary regulator valve plug
1. Upper valve body
Page 154 of 447
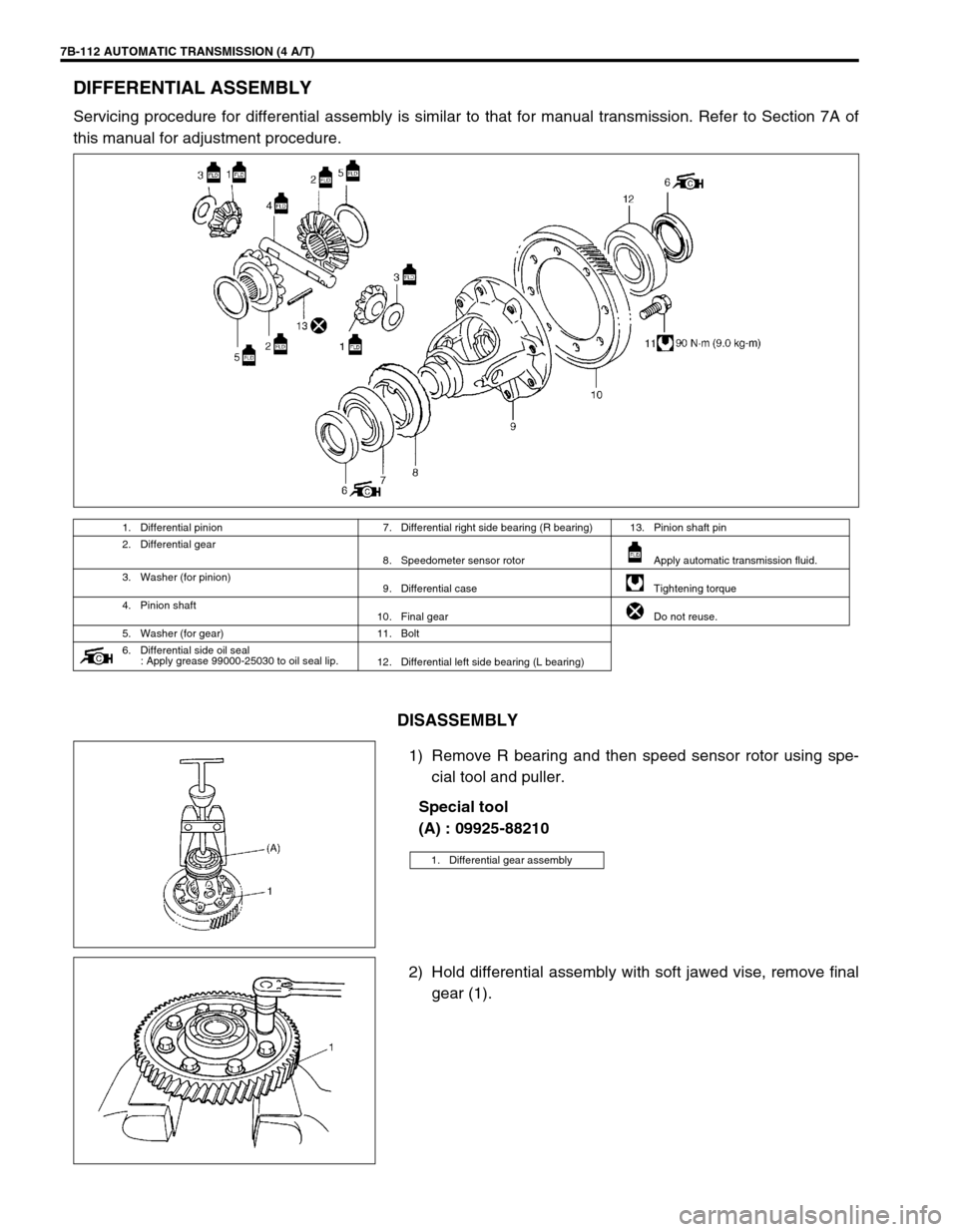
7B-112 AUTOMATIC TRANSMISSION (4 A/T)
DIFFERENTIAL ASSEMBLY
Servicing procedure for differential assembly is similar to that for manual transmission. Refer to Section 7A of
this manual for adjustment procedure.
DISASSEMBLY
1) Remove R bearing and then speed sensor rotor using spe-
cial tool and puller.
Special tool
(A) : 09925-88210
2) Hold differential assembly with soft jawed vise, remove final
gear (1).
1. Differential pinion 7. Differential right side bearing (R bearing) 13. Pinion shaft pin
2. Differential gear
8. Speedometer sensor rotor Apply automatic transmission fluid.
3. Washer (for pinion)
9. Differential case Tightening torque
4. Pinion shaft
10. Final gear Do not reuse.
5. Washer (for gear) 11. Bolt
6. Differential side oil seal
: Apply grease 99000-25030 to oil seal lip.
12. Differential left side bearing (L bearing)
1. Differential gear assembly