roof SUZUKI SWIFT 2000 1.G Transmission Service Workshop Manual
[x] Cancel search | Manufacturer: SUZUKI, Model Year: 2000, Model line: SWIFT, Model: SUZUKI SWIFT 2000 1.GPages: 447, PDF Size: 10.54 MB
Page 305 of 447
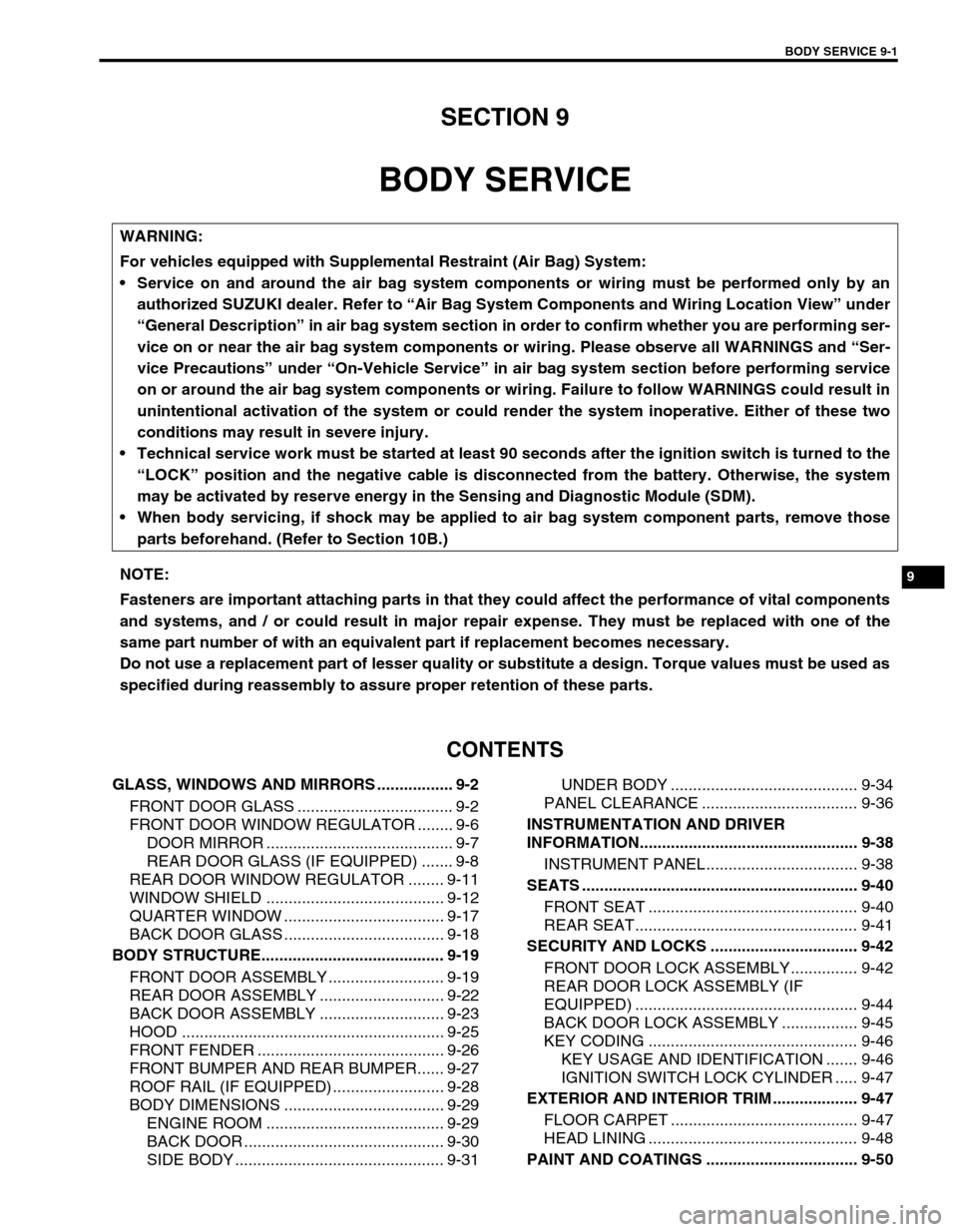
BODY SERVICE 9-1
6F1
6F2
6G
6H
6K
7A
7A1
7B1
7C1
7D
7E
7F
8A
8B
8C
8D
8E
9
10
10A
10B
SECTION 9
BODY SERVICE
CONTENTS
GLASS, WINDOWS AND MIRRORS ................. 9-2
FRONT DOOR GLASS ................................... 9-2
FRONT DOOR WINDOW REGULATOR ........ 9-6
DOOR MIRROR .......................................... 9-7
REAR DOOR GLASS (IF EQUIPPED) ....... 9-8
REAR DOOR WINDOW REGULATOR ........ 9-11
WINDOW SHIELD ........................................ 9-12
QUARTER WINDOW .................................... 9-17
BACK DOOR GLASS .................................... 9-18
BODY STRUCTURE......................................... 9-19
FRONT DOOR ASSEMBLY .......................... 9-19
REAR DOOR ASSEMBLY ............................ 9-22
BACK DOOR ASSEMBLY ............................ 9-23
HOOD ........................................................... 9-25
FRONT FENDER .......................................... 9-26
FRONT BUMPER AND REAR BUMPER...... 9-27
ROOF RAIL (IF EQUIPPED) ......................... 9-28
BODY DIMENSIONS .................................... 9-29
ENGINE ROOM ........................................ 9-29
BACK DOOR ............................................. 9-30
SIDE BODY ............................................... 9-31UNDER BODY .......................................... 9-34
PANEL CLEARANCE ................................... 9-36
INSTRUMENTATION AND DRIVER
INFORMATION................................................. 9-38
INSTRUMENT PANEL .................................. 9-38
SEATS .............................................................. 9-40
FRONT SEAT ............................................... 9-40
REAR SEAT.................................................. 9-41
SECURITY AND LOCKS ................................. 9-42
FRONT DOOR LOCK ASSEMBLY............... 9-42
REAR DOOR LOCK ASSEMBLY (IF
EQUIPPED) .................................................. 9-44
BACK DOOR LOCK ASSEMBLY ................. 9-45
KEY CODING ............................................... 9-46
KEY USAGE AND IDENTIFICATION ....... 9-46
IGNITION SWITCH LOCK CYLINDER ..... 9-47
EXTERIOR AND INTERIOR TRIM ................... 9-47
FLOOR CARPET .......................................... 9-47
HEAD LINING ............................................... 9-48
PAINT AND COATINGS .................................. 9-50 WARNING:
For vehicles equipped with Supplemental Restraint (Air Bag) System:
Service on and around the air bag system components or wiring must be performed only by an
authorized SUZUKI dealer. Refer to “Air Bag System Components and Wiring Location View” under
“General Description” in air bag system section in order to confirm whether you are performing ser-
vice on or near the air bag system components or wiring. Please observe all WARNINGS and “Ser-
vice Precautions” under “On-Vehicle Service” in air bag system section before performing service
on or around the air bag system components or wiring. Failure to follow WARNINGS could result in
unintentional activation of the system or could render the system inoperative. Either of these two
conditions may result in severe injury.
Technical service work must be started at least 90 seconds after the ignition switch is turned to the
“LOCK” position and the negative cable is disconnected from the battery. Otherwise, the system
may be activated by reserve energy in the Sensing and Diagnostic Module (SDM).
When body servicing, if shock may be applied to air bag system component parts, remove those
parts beforehand. (Refer to Section 10B.)
NOTE:
Fasteners are important attaching parts in that they could affect the performance of vital components
and systems, and / or could result in major repair expense. They must be replaced with one of the
same part number of with an equivalent part if replacement becomes necessary.
Do not use a replacement part of lesser quality or substitute a design. Torque values must be used as
specified during reassembly to assure proper retention of these parts.
Page 332 of 447
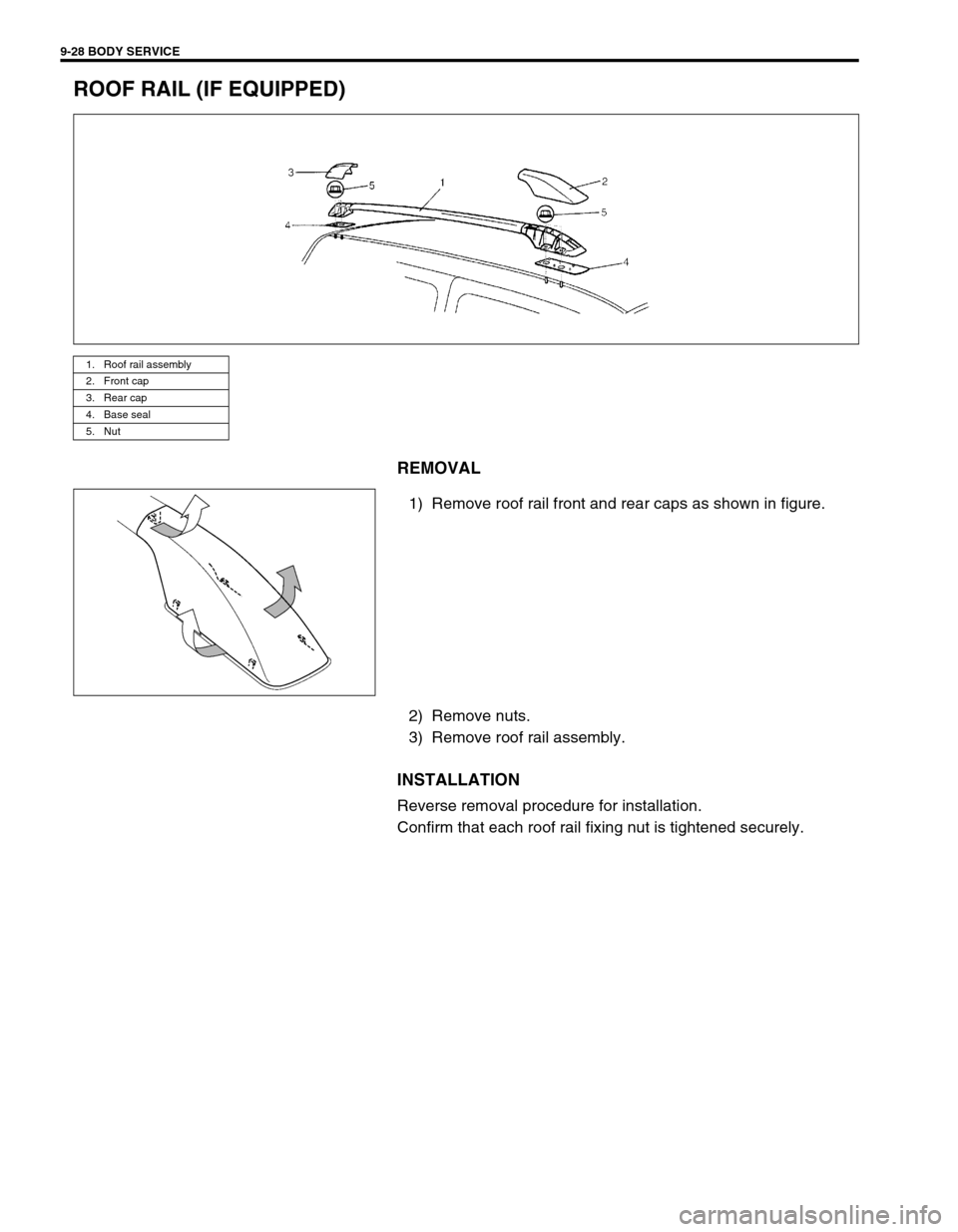
9-28 BODY SERVICE
ROOF RAIL (IF EQUIPPED)
REMOVAL
1) Remove roof rail front and rear caps as shown in figure.
2) Remove nuts.
3) Remove roof rail assembly.
INSTALLATION
Reverse removal procedure for installation.
Confirm that each roof rail fixing nut is tightened securely.
1. Roof rail assembly
2. Front cap
3. Rear cap
4. Base seal
5. Nut
Page 352 of 447
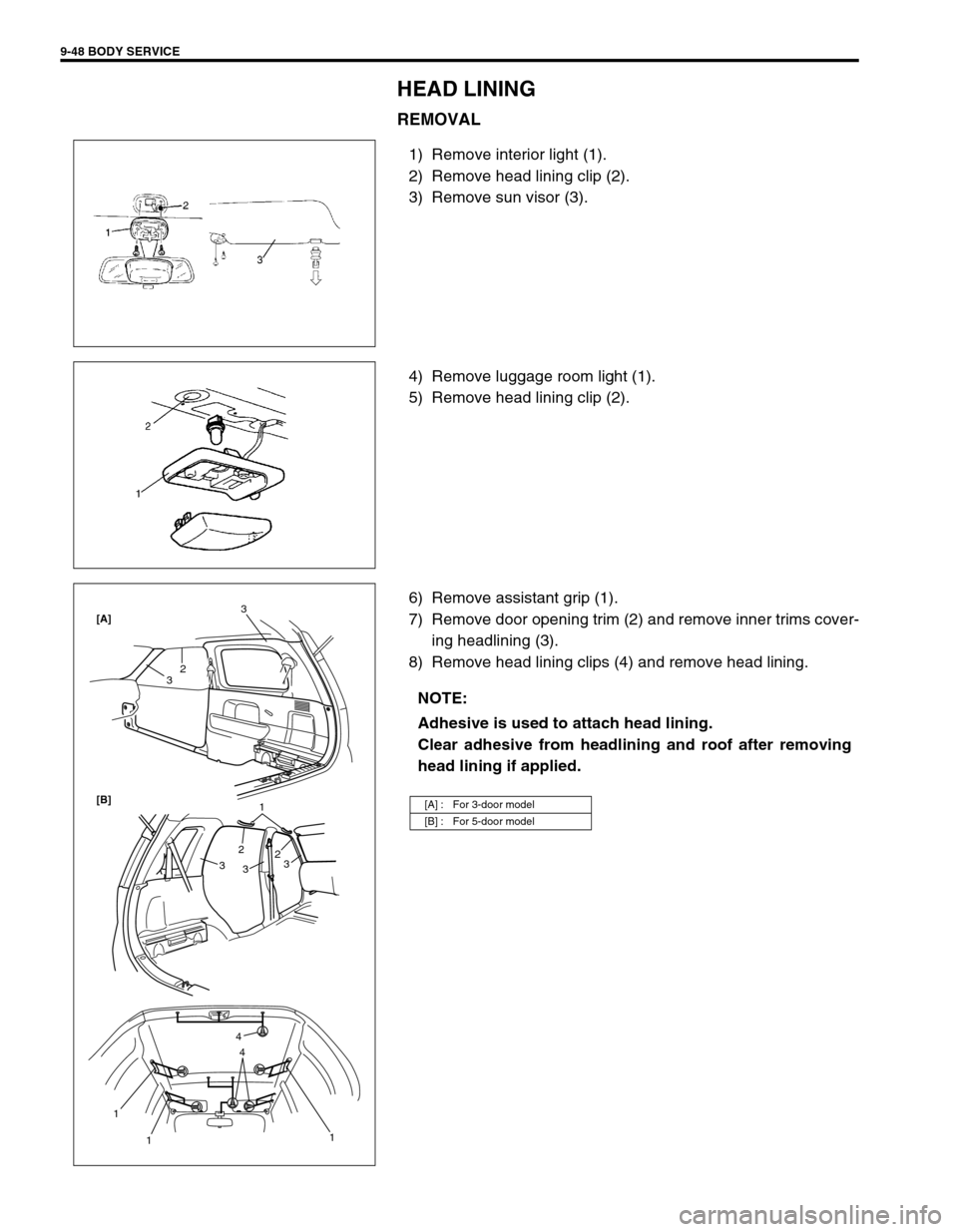
9-48 BODY SERVICE
HEAD LINING
REMOVAL
1) Remove interior light (1).
2) Remove head lining clip (2).
3) Remove sun visor (3).
4) Remove luggage room light (1).
5) Remove head lining clip (2).
6) Remove assistant grip (1).
7) Remove door opening trim (2) and remove inner trims cover-
ing headlining (3).
8) Remove head lining clips (4) and remove head lining.
NOTE:
Adhesive is used to attach head lining.
Clear adhesive from headlining and roof after removing
head lining if applied.
[A] : For 3-door model
[B] : For 5-door model
1
11
4
4
1
2
2
3
3 3 2
33
[A]
[B]
Page 354 of 447
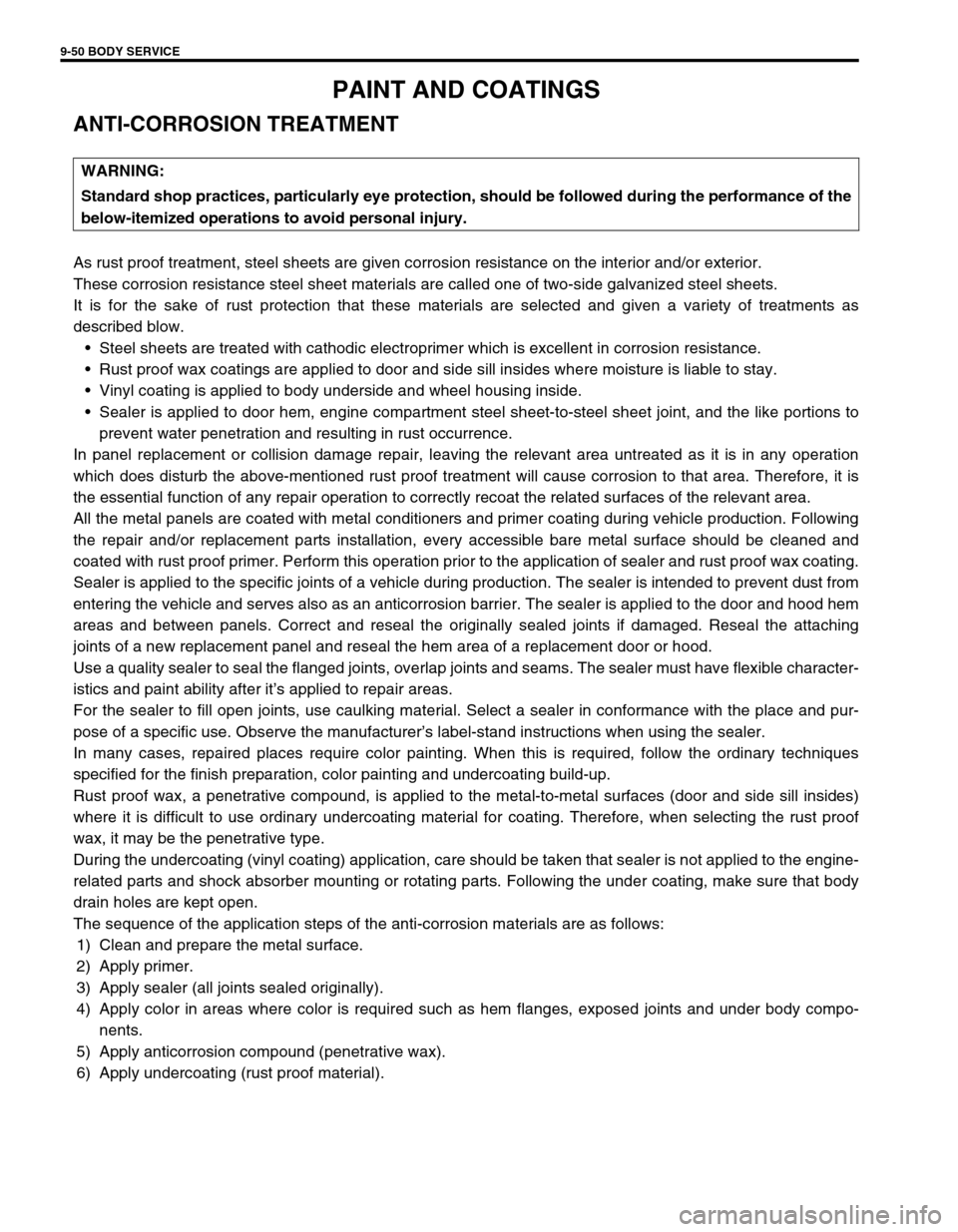
9-50 BODY SERVICE
PAINT AND COATINGS
ANTI-CORROSION TREATMENT
As rust proof treatment, steel sheets are given corrosion resistance on the interior and/or exterior.
These corrosion resistance steel sheet materials are called one of two-side galvanized steel sheets.
It is for the sake of rust protection that these materials are selected and given a variety of treatments as
described blow.
Steel sheets are treated with cathodic electroprimer which is excellent in corrosion resistance.
Rust proof wax coatings are applied to door and side sill insides where moisture is liable to stay.
Vinyl coating is applied to body underside and wheel housing inside.
Sealer is applied to door hem, engine compartment steel sheet-to-steel sheet joint, and the like portions to
prevent water penetration and resulting in rust occurrence.
In panel replacement or collision damage repair, leaving the relevant area untreated as it is in any operation
which does disturb the above-mentioned rust proof treatment will cause corrosion to that area. Therefore, it is
the essential function of any repair operation to correctly recoat the related surfaces of the relevant area.
All the metal panels are coated with metal conditioners and primer coating during vehicle production. Following
the repair and/or replacement parts installation, every accessible bare metal surface should be cleaned and
coated with rust proof primer. Perform this operation prior to the application of sealer and rust proof wax coating.
Sealer is applied to the specific joints of a vehicle during production. The sealer is intended to prevent dust from
entering the vehicle and serves also as an anticorrosion barrier. The sealer is applied to the door and hood hem
areas and between panels. Correct and reseal the originally sealed joints if damaged. Reseal the attaching
joints of a new replacement panel and reseal the hem area of a replacement door or hood.
Use a quality sealer to seal the flanged joints, overlap joints and seams. The sealer must have flexible character-
istics and paint ability after it’s applied to repair areas.
For the sealer to fill open joints, use caulking material. Select a sealer in conformance with the place and pur-
pose of a specific use. Observe the manufacturer’s label-stand instructions when using the sealer.
In many cases, repaired places require color painting. When this is required, follow the ordinary techniques
specified for the finish preparation, color painting and undercoating build-up.
Rust proof wax, a penetrative compound, is applied to the metal-to-metal surfaces (door and side sill insides)
where it is difficult to use ordinary undercoating material for coating. Therefore, when selecting the rust proof
wax, it may be the penetrative type.
During the undercoating (vinyl coating) application, care should be taken that sealer is not applied to the engine-
related parts and shock absorber mounting or rotating parts. Following the under coating, make sure that body
drain holes are kept open.
The sequence of the application steps of the anti-corrosion materials are as follows:
1) Clean and prepare the metal surface.
2) Apply primer.
3) Apply sealer (all joints sealed originally).
4) Apply color in areas where color is required such as hem flanges, exposed joints and under body compo-
nents.
5) Apply anticorrosion compound (penetrative wax).
6) Apply undercoating (rust proof material).WARNING:
Standard shop practices, particularly eye protection, should be followed during the performance of the
below-itemized operations to avoid personal injury.
Page 364 of 447
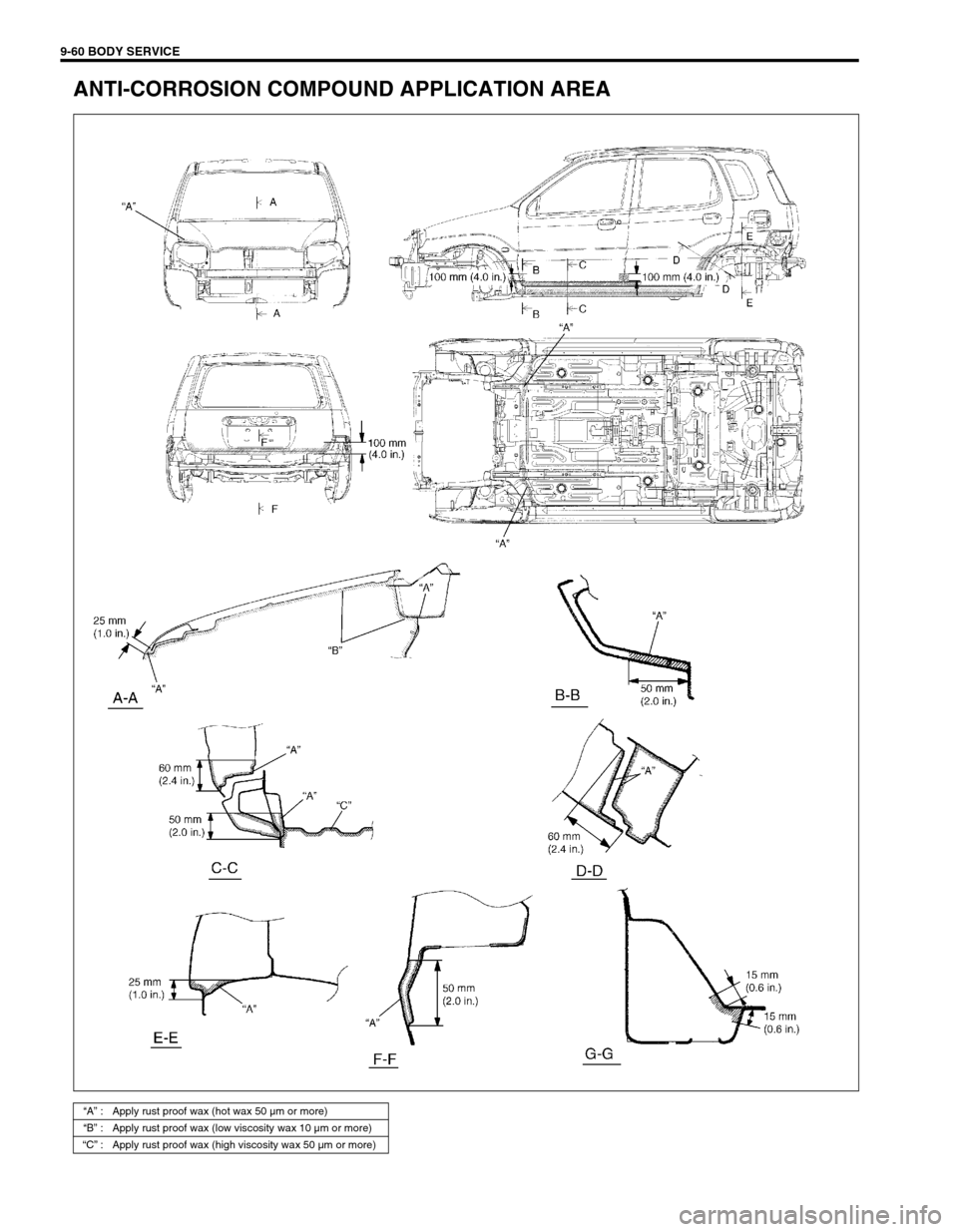
9-60 BODY SERVICE
ANTI-CORROSION COMPOUND APPLICATION AREA
“A” : Apply rust proof wax (hot wax 50 µm or more)
“B” : Apply rust proof wax (low viscosity wax 10 µm or more)
“C” : Apply rust proof wax (high viscosity wax 50 µm or more)