sensor SUZUKI SX4 2006 1.G Service User Guide
[x] Cancel search | Manufacturer: SUZUKI, Model Year: 2006, Model line: SX4, Model: SUZUKI SX4 2006 1.GPages: 1556, PDF Size: 37.31 MB
Page 52 of 1556
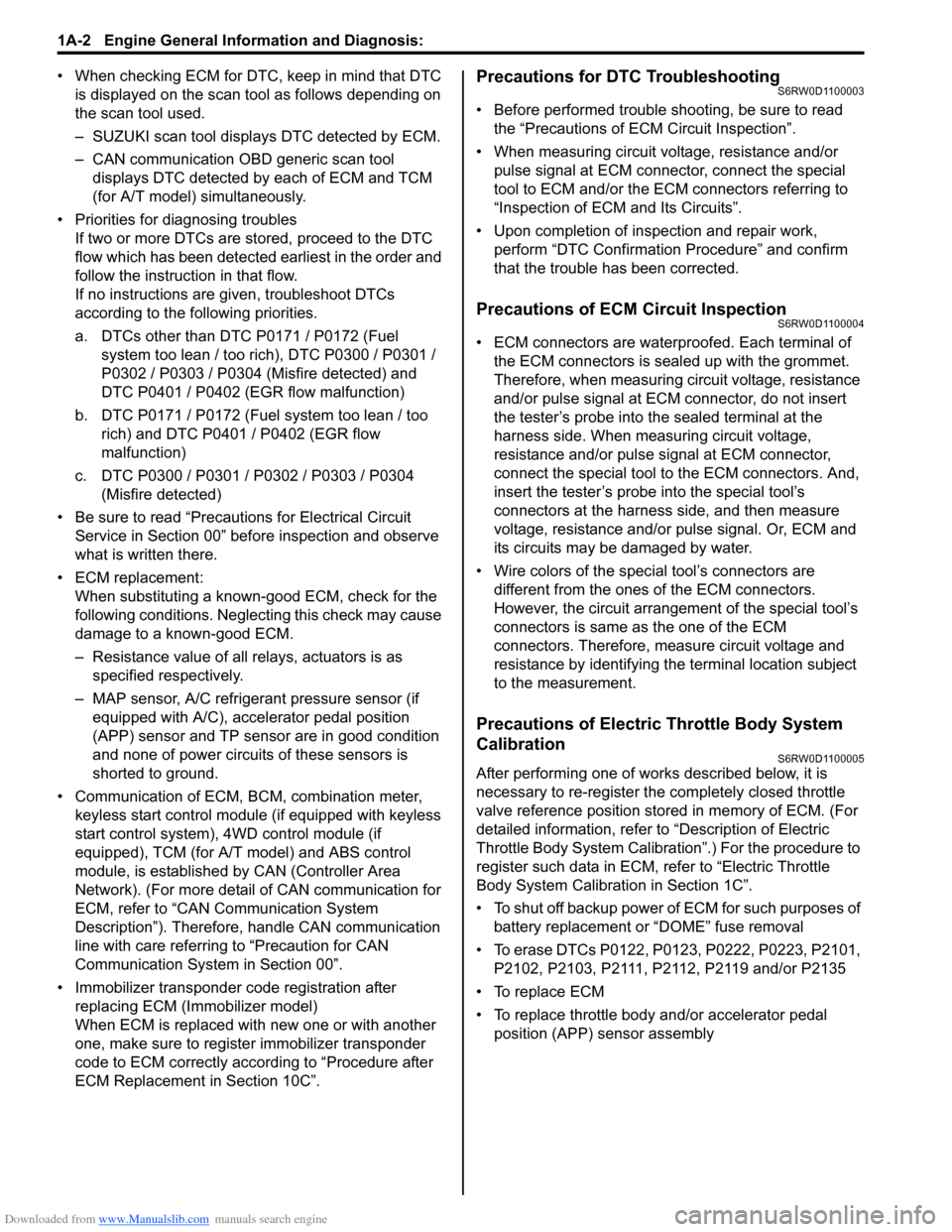
Downloaded from www.Manualslib.com manuals search engine 1A-2 Engine General Information and Diagnosis:
• When checking ECM for DTC, keep in mind that DTC
is displayed on the scan tool as follows depending on
the scan tool used.
– SUZUKI scan tool displays DTC detected by ECM.
– CAN communication OBD generic scan tool
displays DTC detected by each of ECM and TCM
(for A/T model) simultaneously.
• Priorities for diagnosing troubles
If two or more DTCs are stored, proceed to the DTC
flow which has been detected earliest in the order and
follow the instruction in that flow.
If no instructions are given, troubleshoot DTCs
according to the following priorities.
a. DTCs other than DTC P0171 / P0172 (Fuel
system too lean / too rich), DTC P0300 / P0301 /
P0302 / P0303 / P0304 (Misfire detected) and
DTC P0401 / P0402 (EGR flow malfunction)
b. DTC P0171 / P0172 (Fuel system too lean / too
rich) and DTC P0401 / P0402 (EGR flow
malfunction)
c. DTC P0300 / P0301 / P0302 / P0303 / P0304
(Misfire detected)
• Be sure to read “Precautions for Electrical Circuit
Service in Section 00” before inspection and observe
what is written there.
• ECM replacement:
When substituting a known-good ECM, check for the
following conditions. Neglecting this check may cause
damage to a known-good ECM.
– Resistance value of all relays, actuators is as
specified respectively.
– MAP sensor, A/C refrigerant pressure sensor (if
equipped with A/C), accelerator pedal position
(APP) sensor and TP sensor are in good condition
and none of power circuits of these sensors is
shorted to ground.
• Communication of ECM, BCM, combination meter,
keyless start control module (if equipped with keyless
start control system), 4WD control module (if
equipped), TCM (for A/T model) and ABS control
module, is established by CAN (Controller Area
Network). (For more detail of CAN communication for
ECM, refer to “CAN Communication System
Description”). Therefore, handle CAN communication
line with care referring to “Precaution for CAN
Communication System in Section 00”.
• Immobilizer transponder code registration after
replacing ECM (Immobilizer model)
When ECM is replaced with new one or with another
one, make sure to register immobilizer transponder
code to ECM correctly according to “Procedure after
ECM Replacement in Section 10C”.Precautions for DTC TroubleshootingS6RW0D1100003
• Before performed trouble shooting, be sure to read
the “Precautions of ECM Circuit Inspection”.
• When measuring circuit voltage, resistance and/or
pulse signal at ECM connector, connect the special
tool to ECM and/or the ECM connectors referring to
“Inspection of ECM and Its Circuits”.
• Upon completion of inspection and repair work,
perform “DTC Confirmation Procedure” and confirm
that the trouble has been corrected.
Precautions of ECM Circuit InspectionS6RW0D1100004
• ECM connectors are waterproofed. Each terminal of
the ECM connectors is sealed up with the grommet.
Therefore, when measuring circuit voltage, resistance
and/or pulse signal at ECM connector, do not insert
the tester’s probe into the sealed terminal at the
harness side. When measuring circuit voltage,
resistance and/or pulse signal at ECM connector,
connect the special tool to the ECM connectors. And,
insert the tester’s probe into the special tool’s
connectors at the harness side, and then measure
voltage, resistance and/or pulse signal. Or, ECM and
its circuits may be damaged by water.
• Wire colors of the special tool’s connectors are
different from the ones of the ECM connectors.
However, the circuit arrangement of the special tool’s
connectors is same as the one of the ECM
connectors. Therefore, measure circuit voltage and
resistance by identifying the terminal location subject
to the measurement.
Precautions of Electric Throttle Body System
Calibration
S6RW0D1100005
After performing one of works described below, it is
necessary to re-register the completely closed throttle
valve reference position stored in memory of ECM. (For
detailed information, refer to “Description of Electric
Throttle Body System Calibration”.) For the procedure to
register such data in ECM, refer to “Electric Throttle
Body System Calibration in Section 1C”.
• To shut off backup power of ECM for such purposes of
battery replacement or “DOME” fuse removal
• To erase DTCs P0122, P0123, P0222, P0223, P2101,
P2102, P2103, P2111, P2112, P2119 and/or P2135
• To replace ECM
• To replace throttle body and/or accelerator pedal
position (APP) sensor assembly
Page 54 of 1556
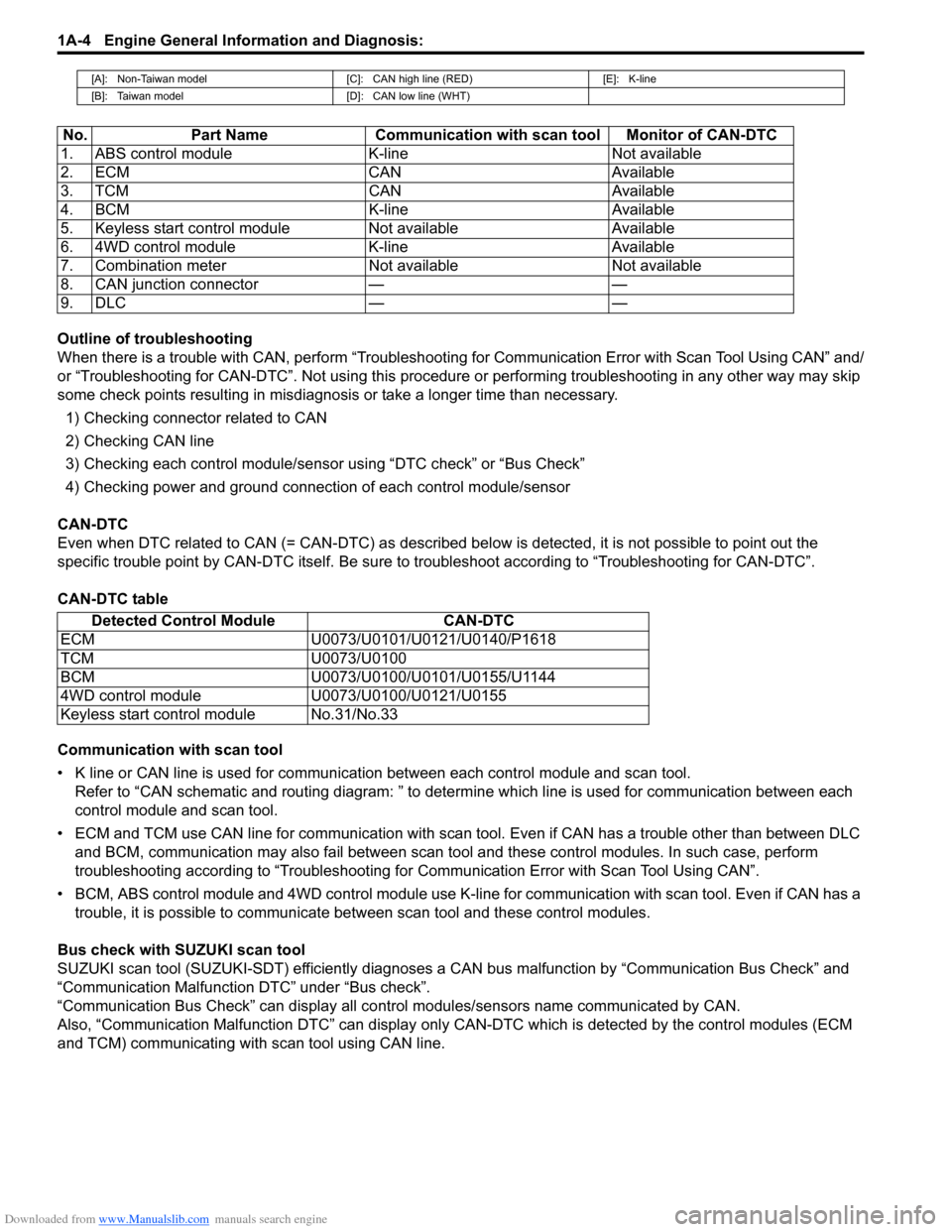
Downloaded from www.Manualslib.com manuals search engine 1A-4 Engine General Information and Diagnosis:
Outline of troubleshooting
When there is a trouble with CAN, perform “Troubleshooting for Communication Error with Scan Tool Using CAN” and/
or “Troubleshooting for CAN-DTC”. Not using this procedure or performing troubleshooting in any other way may skip
some check points resulting in misdiagnosis or take a longer time than necessary.
1) Checking connector related to CAN
2) Checking CAN line
3) Checking each control module/sensor using “DTC check” or “Bus Check”
4) Checking power and ground connection of each control module/sensor
CAN-DTC
Even when DTC related to CAN (= CAN-DTC) as described below is detected, it is not possible to point out the
specific trouble point by CAN-DTC itself. Be sure to troubleshoot according to “Troubleshooting for CAN-DTC”.
CAN-DTC table
Communication with scan tool
• K line or CAN line is used for communication between each control module and scan tool.
Refer to “CAN schematic and routing diagram: ” to determine which line is used for communication between each
control module and scan tool.
• ECM and TCM use CAN line for communication with scan tool. Even if CAN has a trouble other than between DLC
and BCM, communication may also fail between scan tool and these control modules. In such case, perform
troubleshooting according to “Troubleshooting for Communication Error with Scan Tool Using CAN”.
• BCM, ABS control module and 4WD control module use K-line for communication with scan tool. Even if CAN has a
trouble, it is possible to communicate between scan tool and these control modules.
Bus check with SUZUKI scan tool
SUZUKI scan tool (SUZUKI-SDT) efficiently diagnoses a CAN bus malfunction by “Communication Bus Check” and
“Communication Malfunction DTC” under “Bus check”.
“Communication Bus Check” can display all control modules/sensors name communicated by CAN.
Also, “Communication Malfunction DTC” can display only CAN-DTC which is detected by the control modules (ECM
and TCM) communicating with scan tool using CAN line.
[A]: Non-Taiwan model [C]: CAN high line (RED) [E]: K-line
[B]: Taiwan model [D]: CAN low line (WHT)
No. Part Name Communication with scan tool Monitor of CAN-DTC
1. ABS control module K-line Not available
2. ECM CAN Available
3. TCM CAN Available
4. BCM K-line Available
5. Keyless start control module Not available Available
6. 4WD control module K-line Available
7. Combination meter Not available Not available
8. CAN junction connector — —
9. DLC — —
Detected Control Module CAN-DTC
ECM U0073/U0101/U0121/U0140/P1618
TCM U0073/U0100
BCM U0073/U0100/U0101/U0155/U1144
4WD control module U0073/U0100/U0121/U0155
Keyless start control module No.31/No.33
Page 57 of 1556
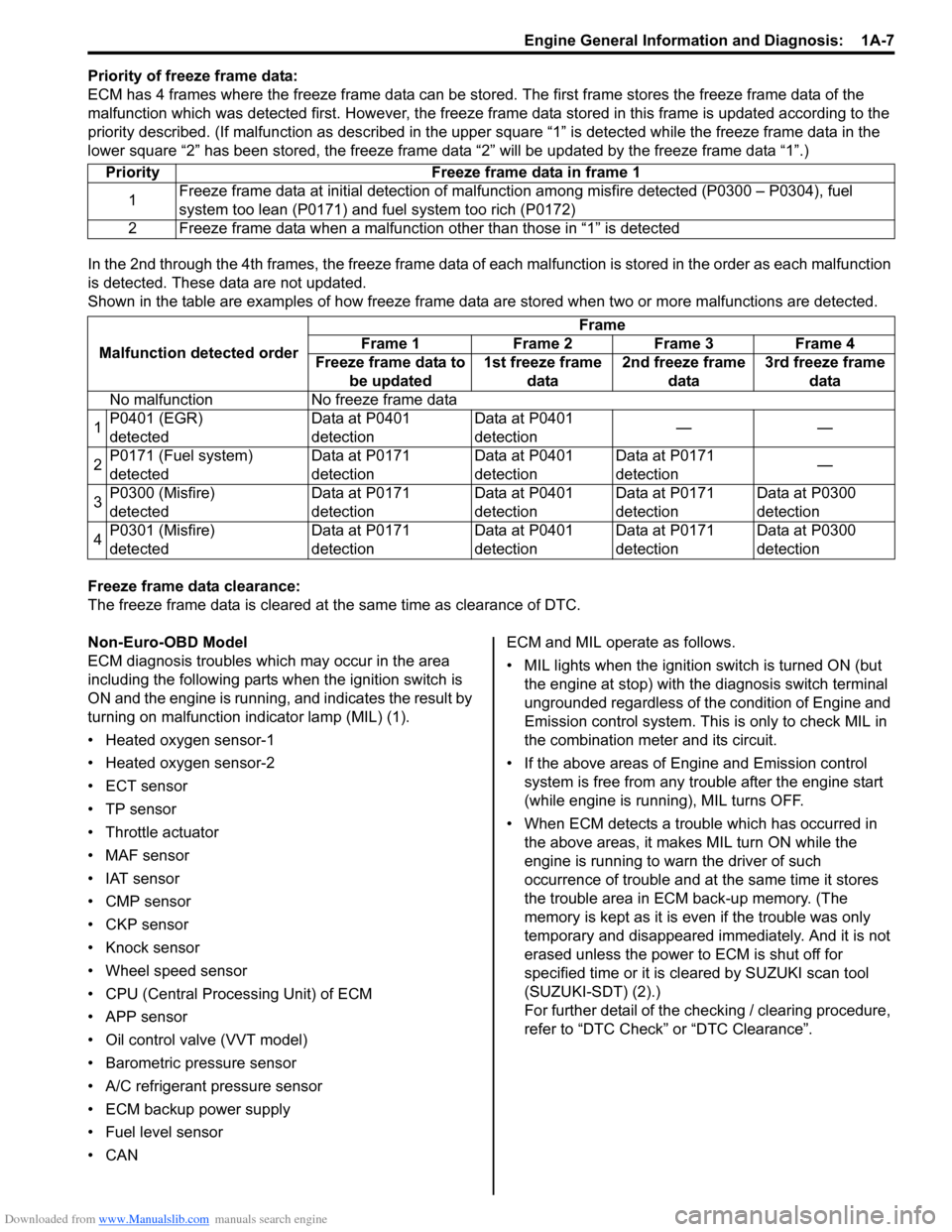
Downloaded from www.Manualslib.com manuals search engine Engine General Information and Diagnosis: 1A-7
Priority of freeze frame data:
ECM has 4 frames where the freeze frame data can be stored. The first frame stores the freeze frame data of the
malfunction which was detected first. However, the freeze frame data stored in this frame is updated according to the
priority described. (If malfunction as described in the upper square “1” is detected while the freeze frame data in the
lower square “2” has been stored, the freeze frame data “2” will be updated by the freeze frame data “1”.)
In the 2nd through the 4th frames, the freeze frame data of each malfunction is stored in the order as each malfunction
is detected. These data are not updated.
Shown in the table are examples of how freeze frame data are stored when two or more malfunctions are detected.
Freeze frame data clearance:
The freeze frame data is cleared at the same time as clearance of DTC.
Non-Euro-OBD Model
ECM diagnosis troubles which may occur in the area
including the following parts when the ignition switch is
ON and the engine is running, and indicates the result by
turning on malfunction indicator lamp (MIL) (1).
• Heated oxygen sensor-1
• Heated oxygen sensor-2
• ECT sensor
•TP sensor
• Throttle actuator
• MAF sensor
• IAT sensor
• CMP sensor
• CKP sensor
• Knock sensor
• Wheel speed sensor
• CPU (Central Processing Unit) of ECM
• APP sensor
• Oil control valve (VVT model)
• Barometric pressure sensor
• A/C refrigerant pressure sensor
• ECM backup power supply
• Fuel level sensor
•CANECM and MIL operate as follows.
• MIL lights when the ignition switch is turned ON (but
the engine at stop) with the diagnosis switch terminal
ungrounded regardless of the condition of Engine and
Emission control system. This is only to check MIL in
the combination meter and its circuit.
• If the above areas of Engine and Emission control
system is free from any trouble after the engine start
(while engine is running), MIL turns OFF.
• When ECM detects a trouble which has occurred in
the above areas, it makes MIL turn ON while the
engine is running to warn the driver of such
occurrence of trouble and at the same time it stores
the trouble area in ECM back-up memory. (The
memory is kept as it is even if the trouble was only
temporary and disappeared immediately. And it is not
erased unless the power to ECM is shut off for
specified time or it is cleared by SUZUKI scan tool
(SUZUKI-SDT) (2).)
For further detail of the checking / clearing procedure,
refer to “DTC Check” or “DTC Clearance”. Priority Freeze frame data in frame 1
1Freeze frame data at initial detection of malfunction among misfire detected (P0300 – P0304), fuel
system too lean (P0171) and fuel system too rich (P0172)
2 Freeze frame data when a malfunction other than those in “1” is detected
Malfunction detected orderFrame
Frame 1 Frame 2 Frame 3 Frame 4
Freeze frame data to
be updated1st freeze frame
data2nd freeze frame
data3rd freeze frame
data
No malfunction No freeze frame data
1P0401 (EGR)
detectedData at P0401
detectionData at P0401
detection——
2P0171 (Fuel system)
detectedData at P0171
detectionData at P0401
detectionData at P0171
detection—
3P0300 (Misfire)
detectedData at P0171
detectionData at P0401
detectionData at P0171
detectionData at P0300
detection
4P0301 (Misfire)
detectedData at P0171
detectionData at P0401
detectionData at P0171
detectionData at P0300
detection
Page 58 of 1556
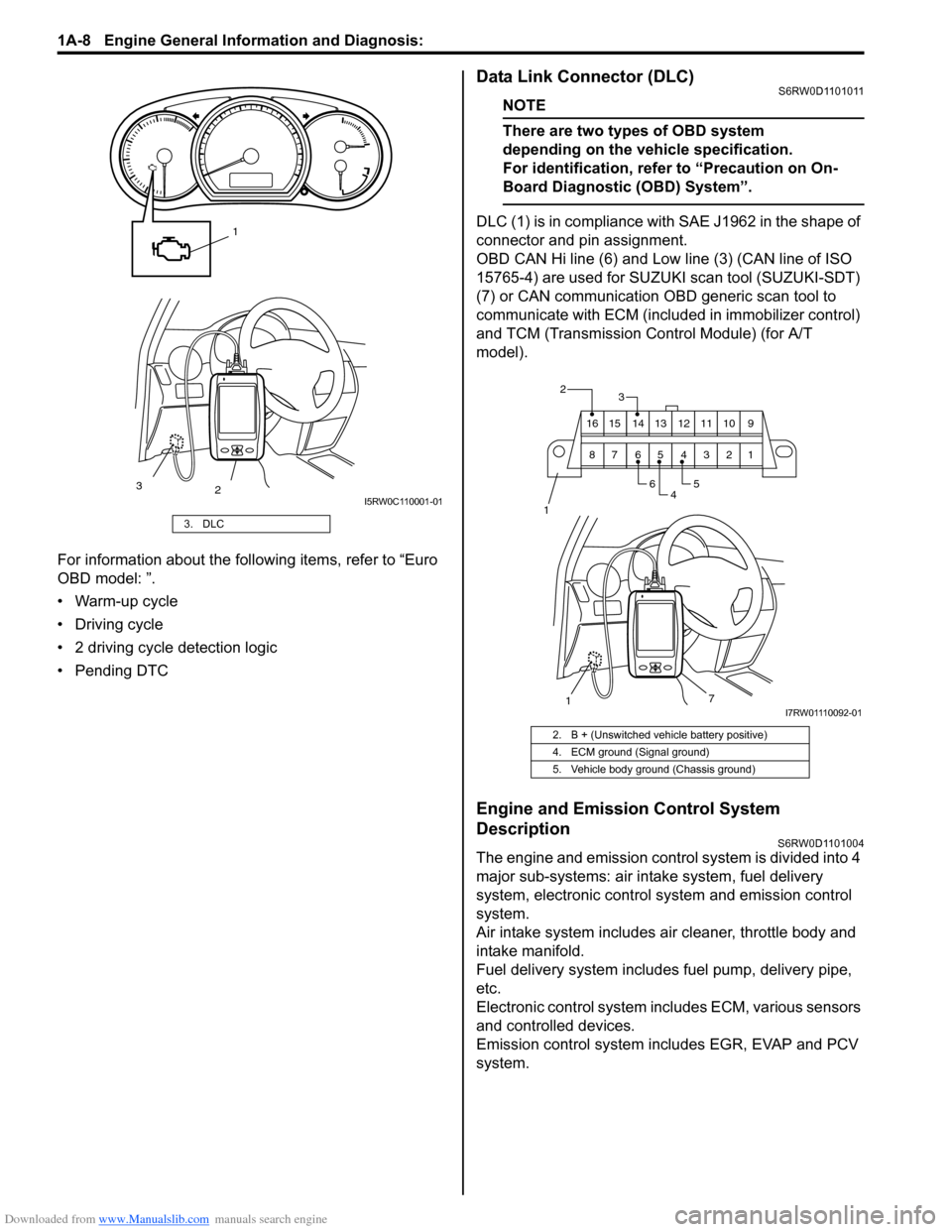
Downloaded from www.Manualslib.com manuals search engine 1A-8 Engine General Information and Diagnosis:
For information about the following items, refer to “Euro
OBD model: ”.
• Warm-up cycle
• Driving cycle
• 2 driving cycle detection logic
• Pending DTC
Data Link Connector (DLC)S6RW0D1101011
NOTE
There are two types of OBD system
depending on the vehicle specification.
For identification, refer to “Precaution on On-
Board Diagnostic (OBD) System”.
DLC (1) is in compliance with SAE J1962 in the shape of
connector and pin assignment.
OBD CAN Hi line (6) and Low line (3) (CAN line of ISO
15765-4) are used for SUZUKI scan tool (SUZUKI-SDT)
(7) or CAN communication OBD generic scan tool to
communicate with ECM (included in immobilizer control)
and TCM (Transmission Control Module) (for A/T
model).
Engine and Emission Control System
Description
S6RW0D1101004
The engine and emission control system is divided into 4
major sub-systems: air intake system, fuel delivery
system, electronic control system and emission control
system.
Air intake system includes air cleaner, throttle body and
intake manifold.
Fuel delivery system includes fuel pump, delivery pipe,
etc.
Electronic control system includes ECM, various sensors
and controlled devices.
Emission control system includes EGR, EVAP and PCV
system.
3. DLC
1
2 3
I5RW0C110001-01
2. B + (Unswitched vehicle battery positive)
4. ECM ground (Signal ground)
5. Vehicle body ground (Chassis ground)
2
45 6
1
9 10 11 12 13 14 15 16
1 2 3 4 5 6 7 8
7
3
1I7RW01110092-01
Page 61 of 1556
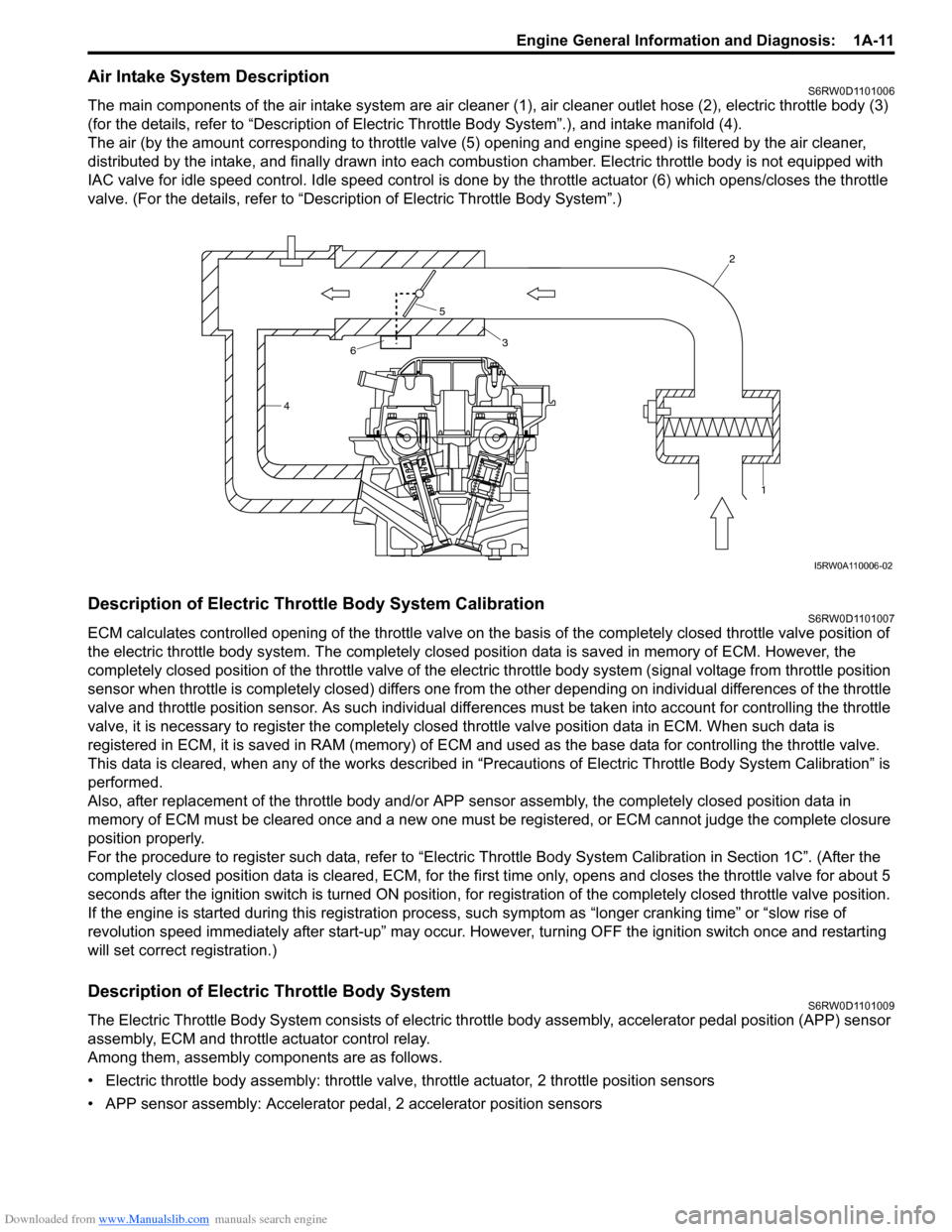
Downloaded from www.Manualslib.com manuals search engine Engine General Information and Diagnosis: 1A-11
Air Intake System DescriptionS6RW0D1101006
The main components of the air intake system are air cleaner (1), air cleaner outlet hose (2), electric throttle body (3)
(for the details, refer to “Description of Electric Throttle Body System”.), and intake manifold (4).
The air (by the amount corresponding to throttle valve (5) opening and engine speed) is filtered by the air cleaner,
distributed by the intake, and finally drawn into each combustion chamber. Electric throttle body is not equipped with
IAC valve for idle speed control. Idle speed control is done by the throttle actuator (6) which opens/closes the throttle
valve. (For the details, refer to “Description of Electric Throttle Body System”.)
Description of Electric Throttle Body System CalibrationS6RW0D1101007
ECM calculates controlled opening of the throttle valve on the basis of the completely closed throttle valve position of
the electric throttle body system. The completely closed position data is saved in memory of ECM. However, the
completely closed position of the throttle valve of the electric throttle body system (signal voltage from throttle position
sensor when throttle is completely closed) differs one from the other depending on individual differences of the throttle
valve and throttle position sensor. As such individual differences must be taken into account for controlling the throttle
valve, it is necessary to register the completely closed throttle valve position data in ECM. When such data is
registered in ECM, it is saved in RAM (memory) of ECM and used as the base data for controlling the throttle valve.
This data is cleared, when any of the works described in “Precautions of Electric Throttle Body System Calibration” is
performed.
Also, after replacement of the throttle body and/or APP sensor assembly, the completely closed position data in
memory of ECM must be cleared once and a new one must be registered, or ECM cannot judge the complete closure
position properly.
For the procedure to register such data, refer to “Electric Throttle Body System Calibration in Section 1C”. (After the
completely closed position data is cleared, ECM, for the first time only, opens and closes the throttle valve for about 5
seconds after the ignition switch is turned ON position, for registration of the completely closed throttle valve position.
If the engine is started during this registration process, such symptom as “longer cranking time” or “slow rise of
revolution speed immediately after start-up” may occur. However, turning OFF the ignition switch once and restarting
will set correct registration.)
Description of Electric Throttle Body SystemS6RW0D1101009
The Electric Throttle Body System consists of electric throttle body assembly, accelerator pedal position (APP) sensor
assembly, ECM and throttle actuator control relay.
Among them, assembly components are as follows.
• Electric throttle body assembly: throttle valve, throttle actuator, 2 throttle position sensors
• APP sensor assembly: Accelerator pedal, 2 accelerator position sensors
42
1
3
5
6
I5RW0A110006-02
Page 62 of 1556
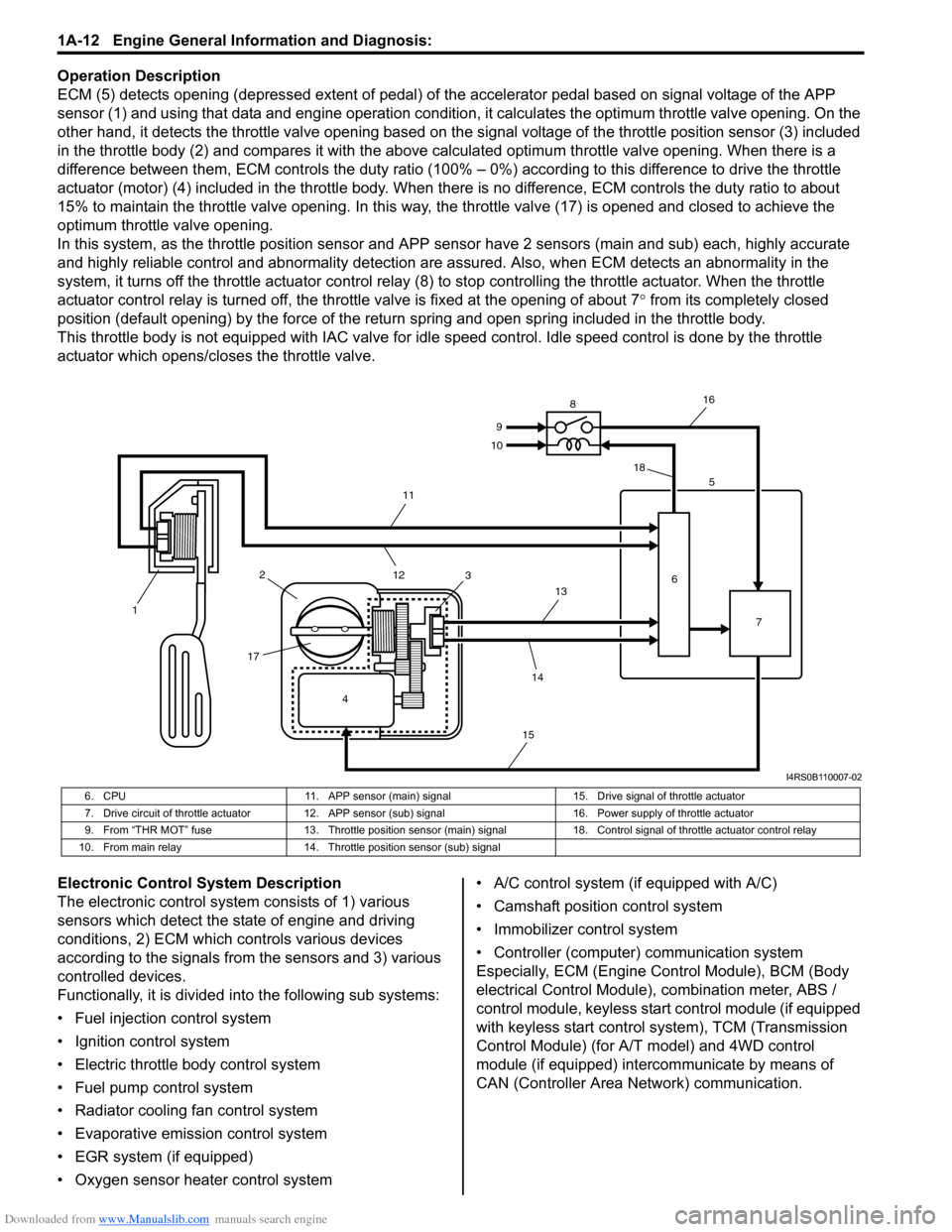
Downloaded from www.Manualslib.com manuals search engine 1A-12 Engine General Information and Diagnosis:
Operation Description
ECM (5) detects opening (depressed extent of pedal) of the accelerator pedal based on signal voltage of the APP
sensor (1) and using that data and engine operation condition, it calculates the optimum throttle valve opening. On the
other hand, it detects the throttle valve opening based on the signal voltage of the throttle position sensor (3) included
in the throttle body (2) and compares it with the above calculated optimum throttle valve opening. When there is a
difference between them, ECM controls the duty ratio (100% – 0%) according to this difference to drive the throttle
actuator (motor) (4) included in the throttle body. When there is no difference, ECM controls the duty ratio to about
15% to maintain the throttle valve opening. In this way, the throttle valve (17) is opened and closed to achieve the
optimum throttle valve opening.
In this system, as the throttle position sensor and APP sensor have 2 sensors (main and sub) each, highly accurate
and highly reliable control and abnormality detection are assured. Also, when ECM detects an abnormality in the
system, it turns off the throttle actuator control relay (8) to stop controlling the throttle actuator. When the throttle
actuator control relay is turned off, the throttle valve is fixed at the opening of about 7° from its completely closed
position (default opening) by the force of the return spring and open spring included in the throttle body.
This throttle body is not equipped with IAC valve for idle speed control. Idle speed control is done by the throttle
actuator which opens/closes the throttle valve.
Electronic Control System Description
The electronic control system consists of 1) various
sensors which detect the state of engine and driving
conditions, 2) ECM which controls various devices
according to the signals from the sensors and 3) various
controlled devices.
Functionally, it is divided into the following sub systems:
• Fuel injection control system
• Ignition control system
• Electric throttle body control system
• Fuel pump control system
• Radiator cooling fan control system
• Evaporative emission control system
• EGR system (if equipped)
• Oxygen sensor heater control system• A/C control system (if equipped with A/C)
• Camshaft position control system
• Immobilizer control system
• Controller (computer) communication system
Especially, ECM (Engine Control Module), BCM (Body
electrical Control Module), combination meter, ABS /
control module, keyless start control module (if equipped
with keyless start control system), TCM (Transmission
Control Module) (for A/T model) and 4WD control
module (if equipped) intercommunicate by means of
CAN (Controller Area Network) communication.
4 12
1735
6
7 8
9
10
11
12
13
14
1516
18
I4RS0B110007-02
6. CPU 11. APP sensor (main) signal 15. Drive signal of throttle actuator
7. Drive circuit of throttle actuator 12. APP sensor (sub) signal 16. Power supply of throttle actuator
9. From “THR MOT” fuse 13. Throttle position sensor (main) signal 18. Control signal of throttle actuator control relay
10. From main relay 14. Throttle position sensor (sub) signal
Page 63 of 1556
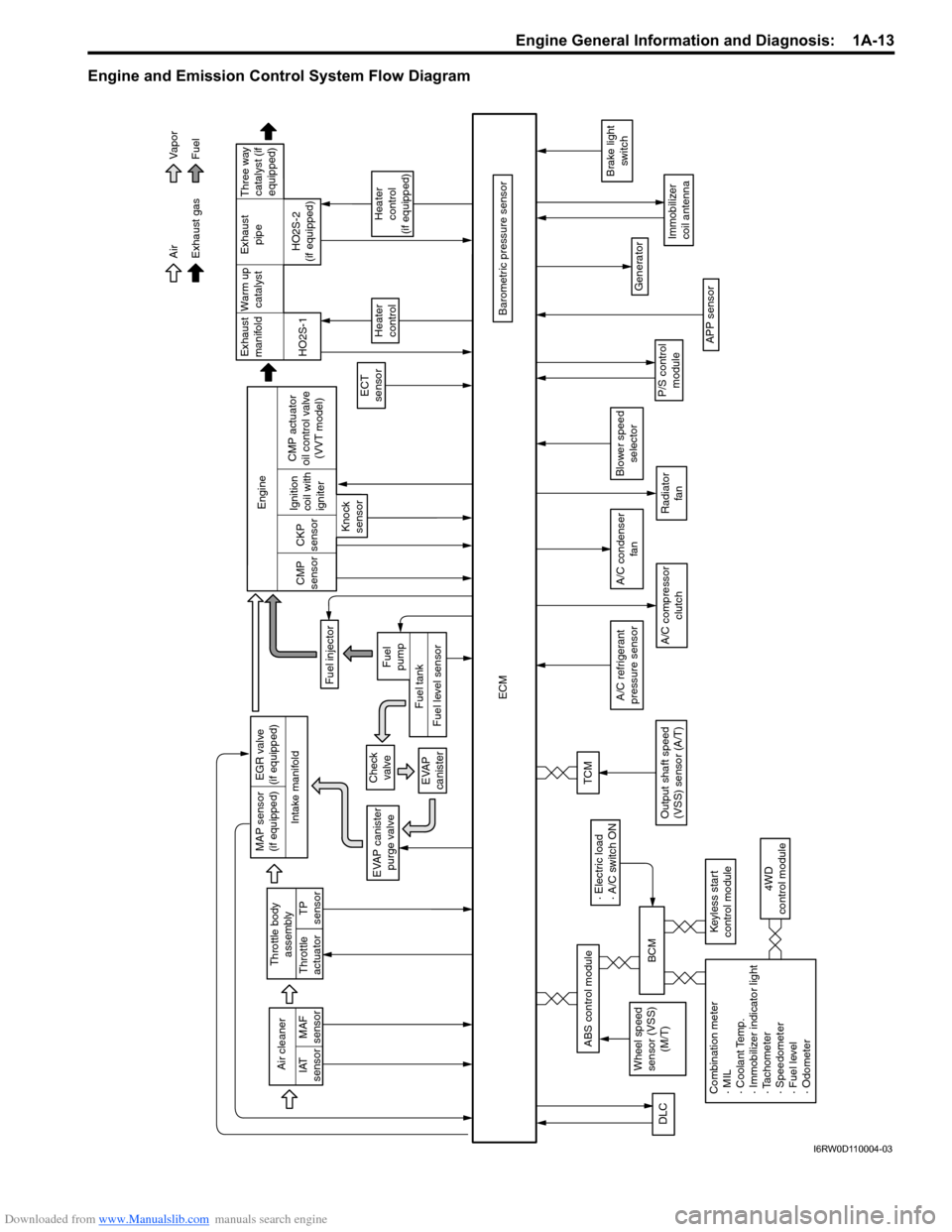
Downloaded from www.Manualslib.com manuals search engine Engine General Information and Diagnosis: 1A-13
Engine and Emission Control System Flow Diagram
Intake manifoldExhaust
manifold
Exhaust gas Air
Fuel Vapor
War m up
catalystExhaust
pipe
EVAP canister
purge valve
Fuel injector
ECT
sensor
ECM
Heater
control
Heater
control
(if equipped)
Barometric pressure sensor HO2S-1HO2S-2
(if equipped) Engine
CMP
sensorCKP
sensor
Knock
sensorIgnition
coil with
igniter
APP sensor
A/C compressor
clutch
Generator
Immobilizer
coil antenna
P/S control
module
Brake light
switch
Air cleaner
IAT
sensorMAF
sensor
A/C refrigerant
pressure sensor
TP
sensor Throttle body
assembly
Throttle
actuator
A/C condenser
fan
DLC
Radiator
fan
Combination meter
· MIL
· Coolant Temp.
· Immobilizer indicator light
· Tachometer
· Speedometer
· Fuel level
· Odometer4WD
control module
Wheel speed
sensor (VSS)
(M/T)
· Electric load
· A/C switch ON
BCM
Keyless start
control module
ABS control module
Blower speed
selector
MAP sensor
(if equipped)EGR valve
(if equipped)
Check
valve
EVAP
canister
Fuel level sensorFuel tankFuel
pump
CMP actuator
oil control valve
(VVT model)
TCM
Output shaft speed
(VSS) sensor (A/T)
Three way
catalyst (if
equipped)
I6RW0D110004-03
Page 64 of 1556
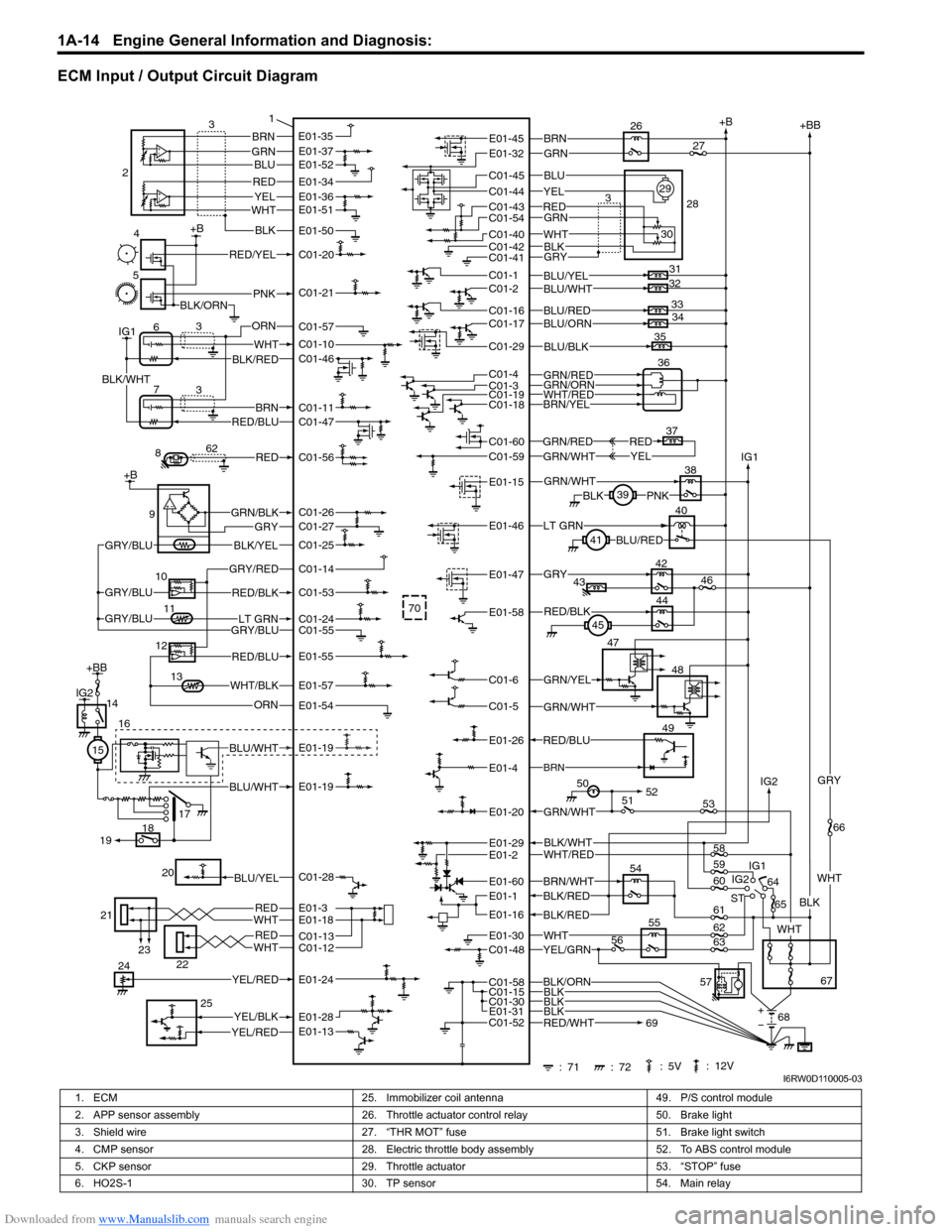
Downloaded from www.Manualslib.com manuals search engine 1A-14 Engine General Information and Diagnosis:
ECM Input / Output Circuit Diagram
51 50
+B
54
IG1+BB
ST64
65
67
BLK/WHTWHT/RED
BRN/WHTBLK/RED
BLK/RED
57
: 71
: 72 : 5V : 12V68 IG1
BLK
WHT
GRY
YEL/GRNWHT
66
58
61
62
63 55
70
60 59
53
WHT
4+B
5
PNK
RED/YEL
BLK/ORN
C01-20
C01-21
8RED62C01-56
13WHT/BLKE01-57
ORNE01-54
21
23WHTRED
WHTRED
22
E01-3E01-18
C01-13C01-12
YEL/RED 24E01-24
YEL/BLK
YEL/RED 25E01-28E01-13
E01-30
E01-16
E01-60E01-1
E01-29
GRN/WHTE01-20
C01-48
E01-2
GRN/YEL47
48
GRN/WHTC01-5
C01-6
44
45RED/BLKE01-58
42
43GRY46E01-47
40LT GRN41BLU/REDE01-46
38
39
PNKBLKGRN/WHTE01-15
GRN/REDGRN/WHT37YELREDC01-59C01-60
35BLU/BLKC01-29
31
32
33
34BLU/YELBLU/WHT
BLU/REDBLU/ORNC01-17C01-16
C01-1C01-2
BLK/ORNBLKC01-30
C01-58C01-15
E01-31BLKBLK
49RED/BLU
BRNE01-4
E01-26 9
GRY
BLK/YELGRY/BLU
GRN/BLKC01-26C01-27
C01-25 +B
IG16
7WHT
BRNRED/BLU
BLK/WHT
3 3
ORN
BLK/RED
C01-57
C01-10
C01-11
C01-46
C01-47
GRY/REDC01-14
11LT GRNGRY/BLUGRY/BLU12RED/BLU
C01-55
E01-55
C01-24
10
RED/BLKGRY/BLUC01-53
IG2
IG2
69RED/WHTC01-52
26
RED
BRNGRN
BLU
GRN
WHTBLK
28
30 2927
3YEL
GRYC01-41C01-42C01-40
C01-43C01-44
C01-45
E01-45E01-32
C01-54
BRN/YELWHT/RED
GRN/REDGRN/ORN
C01-18C01-1936C01-3C01-4
56
1
52
IG2+BB
BLU/WHT
BLU/WHT
14
15
17
16
E01-19
E01-19
18
19
BRNGRNBLU
REDYELWHT
E01-353
BLK
E01-37E01-52
E01-34E01-36E01-51
E01-50
2
20BLU/YELC01-28
I6RW0D110005-03
1. ECM 25. Immobilizer coil antenna 49. P/S control module
2. APP sensor assembly 26. Throttle actuator control relay 50. Brake light
3. Shield wire 27. “THR MOT” fuse 51. Brake light switch
4. CMP sensor 28. Electric throttle body assembly 52. To ABS control module
5. CKP sensor 29. Throttle actuator 53. “STOP” fuse
6. HO2S-1 30. TP sensor 54. Main relay
Page 65 of 1556
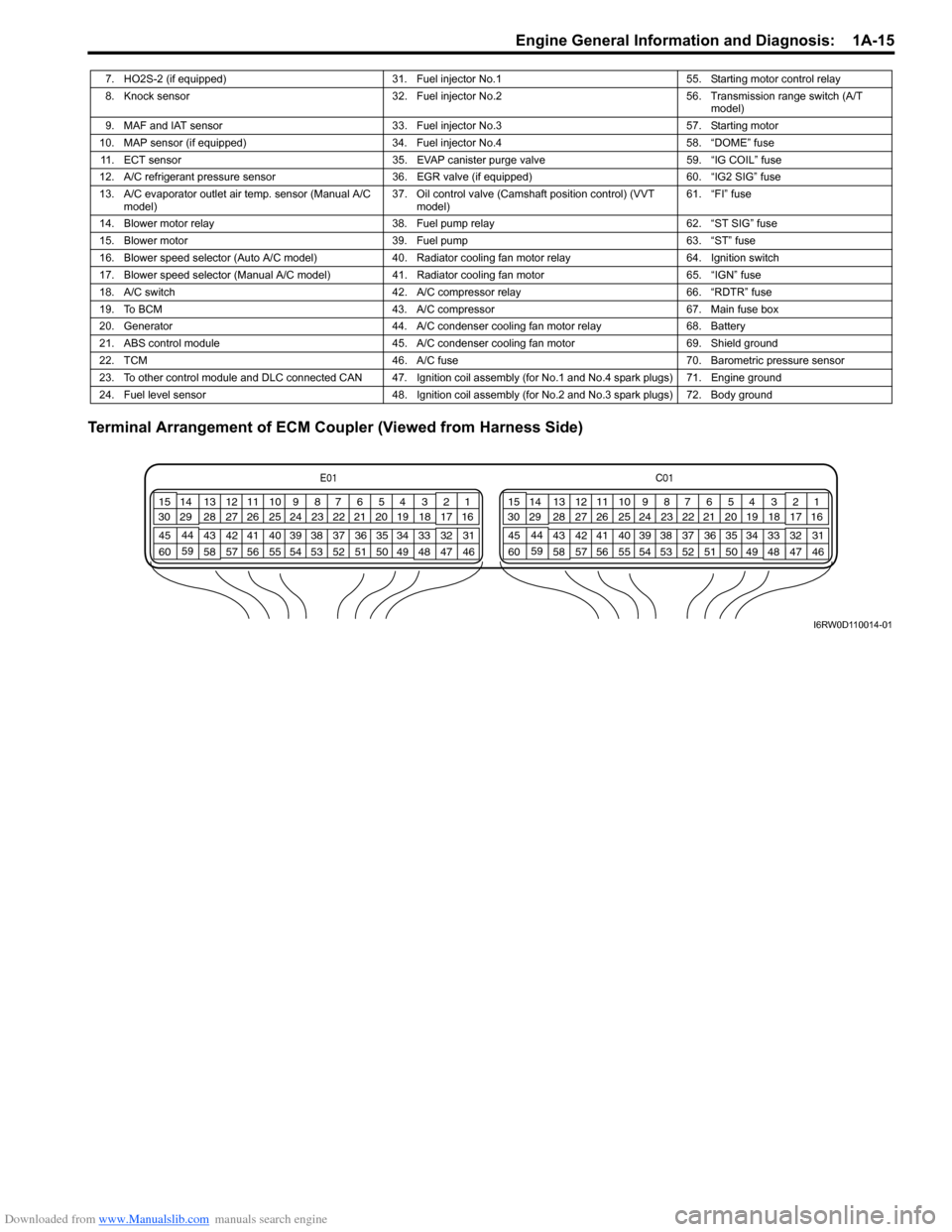
Downloaded from www.Manualslib.com manuals search engine Engine General Information and Diagnosis: 1A-15
Terminal Arrangement of ECM Coupler (Viewed from Harness Side)
7. HO2S-2 (if equipped) 31. Fuel injector No.1 55. Starting motor control relay
8. Knock sensor 32. Fuel injector No.2 56. Transmission range switch (A/T
model)
9. MAF and IAT sensor 33. Fuel injector No.3 57. Starting motor
10. MAP sensor (if equipped) 34. Fuel injector No.4 58. “DOME” fuse
11. ECT sensor 35. EVAP canister purge valve 59. “IG COIL” fuse
12. A/C refrigerant pressure sensor 36. EGR valve (if equipped) 60. “IG2 SIG” fuse
13. A/C evaporator outlet air temp. sensor (Manual A/C
model)37. Oil control valve (Camshaft position control) (VVT
model)61. “FI” fuse
14. Blower motor relay 38. Fuel pump relay 62. “ST SIG” fuse
15. Blower motor 39. Fuel pump 63. “ST” fuse
16. Blower speed selector (Auto A/C model) 40. Radiator cooling fan motor relay 64. Ignition switch
17. Blower speed selector (Manual A/C model) 41. Radiator cooling fan motor 65. “IGN” fuse
18. A/C switch 42. A/C compressor relay 66. “RDTR” fuse
19. To BCM 43. A/C compressor 67. Main fuse box
20. Generator 44. A/C condenser cooling fan motor relay 68. Battery
21. ABS control module 45. A/C condenser cooling fan motor 69. Shield ground
22. TCM 46. A/C fuse 70. Barometric pressure sensor
23. To other control module and DLC connected CAN 47. Ignition coil assembly (for No.1 and No.4 spark plugs) 71. Engine ground
24. Fuel level sensor 48. Ignition coil assembly (for No.2 and No.3 spark plugs) 72. Body ground
E01C01
3 4
18 19 5 6 7 10 11
17 20
47 46 49 50 51 21 22
5216 259
24 14
29
55 57 54 53 59
60 582
26 27 28 15
30
56 4832 31 34 35 36 37 40 42 39 38 44
45 43 41 331 12 13
238 3 4
18 19 5 6 7 10 11
17 20
47 46 49 50 51 21 22
5216 259
24 14
29
55 57 54 53 59
60 582
26 27 28 15
30
56 4832 31 34 35 36 37 40 42 39 38 44
45 43 41 331 12 13
238
I6RW0D110014-01
Page 66 of 1556
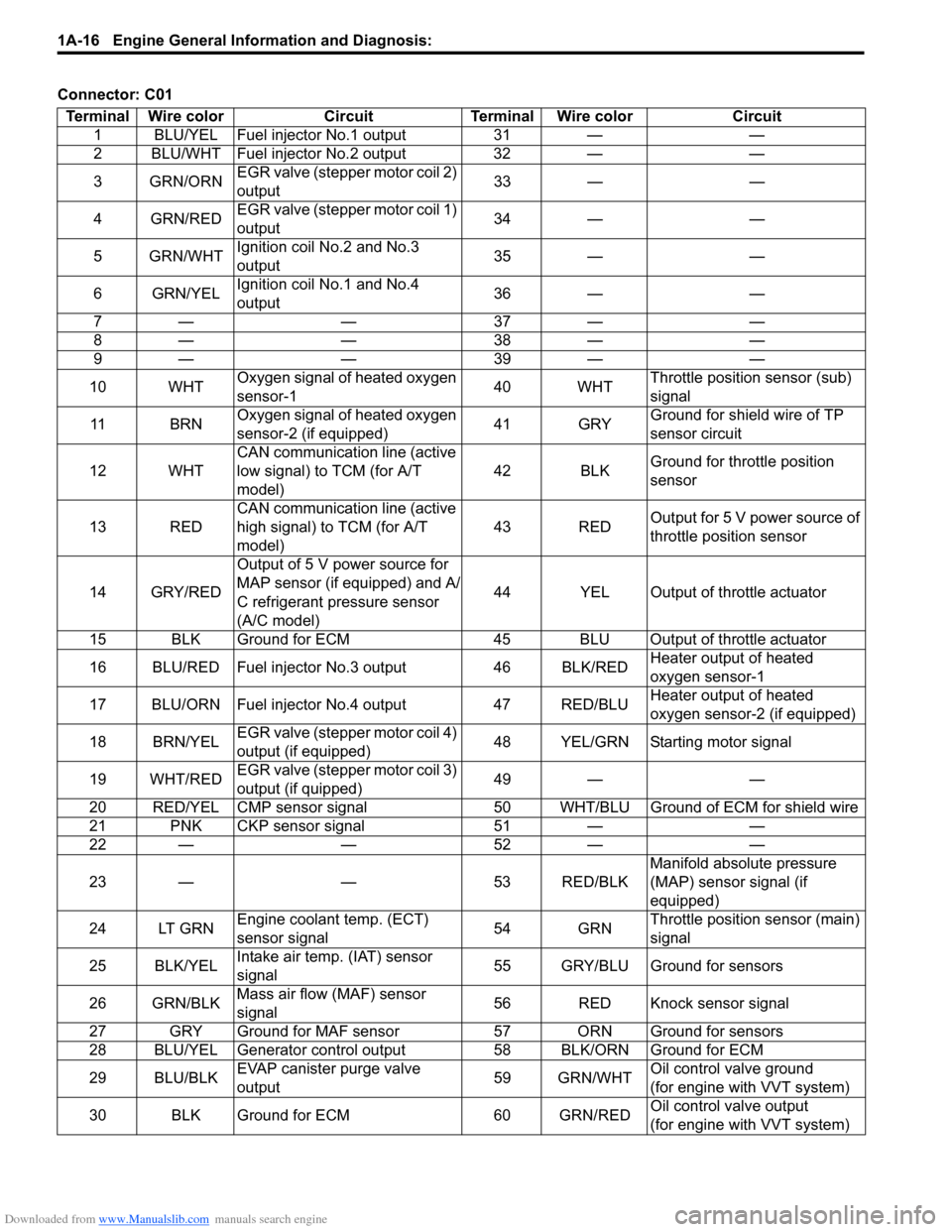
Downloaded from www.Manualslib.com manuals search engine 1A-16 Engine General Information and Diagnosis:
Connector: C01
Terminal Wire color Circuit Terminal Wire color Circuit
1 BLU/YEL Fuel injector No.1 output 31 — —
2 BLU/WHT Fuel injector No.2 output 32 — —
3 GRN/ORNEGR valve (stepper motor coil 2)
output33 — —
4 GRN/REDEGR valve (stepper motor coil 1)
output34 — —
5 GRN/WHTIgnition coil No.2 and No.3
output35 — —
6 GRN/YELIgnition coil No.1 and No.4
output36 — —
7— — 37— —
8— — 38— —
9— — 39— —
10 WHTOxygen signal of heated oxygen
sensor-140 WHTThrottle position sensor (sub)
signal
11 B R NOxygen signal of heated oxygen
sensor-2 (if equipped)41 GRYGround for shield wire of TP
sensor circuit
12 WHTCAN communication line (active
low signal) to TCM (for A/T
model)42 BLKGround for throttle position
sensor
13 REDCAN communication line (active
high signal) to TCM (for A/T
model) 43 REDOutput for 5 V power source of
throttle position sensor
14 GRY/REDOutput of 5 V power source for
MAP sensor (if equipped) and A/
C refrigerant pressure sensor
(A/C model)44 YEL Output of throttle actuator
15 BLK Ground for ECM 45 BLU Output of throttle actuator
16 BLU/RED Fuel injector No.3 output 46 BLK/REDHeater output of heated
oxygen sensor-1
17 BLU/ORN Fuel injector No.4 output 47 RED/BLUHeater output of heated
oxygen sensor-2 (if equipped)
18 BRN/YELEGR valve (stepper motor coil 4)
output (if equipped)48 YEL/GRN Starting motor signal
19 WHT/REDEGR valve (stepper motor coil 3)
output (if quipped)49 — —
20 RED/YEL CMP sensor signal 50 WHT/BLU Ground of ECM for shield wire
21 PNK CKP sensor signal 51 — —
22 — — 52 — —
23 — — 53 RED/BLKManifold absolute pressure
(MAP) sensor signal (if
equipped)
24 LT GRNEngine coolant temp. (ECT)
sensor signal54 GRNThrottle position sensor (main)
signal
25 BLK/YELIntake air temp. (IAT) sensor
signal55 GRY/BLU Ground for sensors
26 GRN/BLKMass air flow (MAF) sensor
signal56 RED Knock sensor signal
27 GRY Ground for MAF sensor 57 ORN Ground for sensors
28 BLU/YEL Generator control output 58 BLK/ORN Ground for ECM
29 BLU/BLKEVAP canister purge valve
output59 GRN/WHTOil control valve ground
(for engine with VVT system)
30 BLK Ground for ECM 60 GRN/REDOil control valve output
(for engine with VVT system)