check engine SUZUKI SX4 2006 1.G Service Workshop Manual
[x] Cancel search | Manufacturer: SUZUKI, Model Year: 2006, Model line: SX4, Model: SUZUKI SX4 2006 1.GPages: 1556, PDF Size: 37.31 MB
Page 776 of 1556
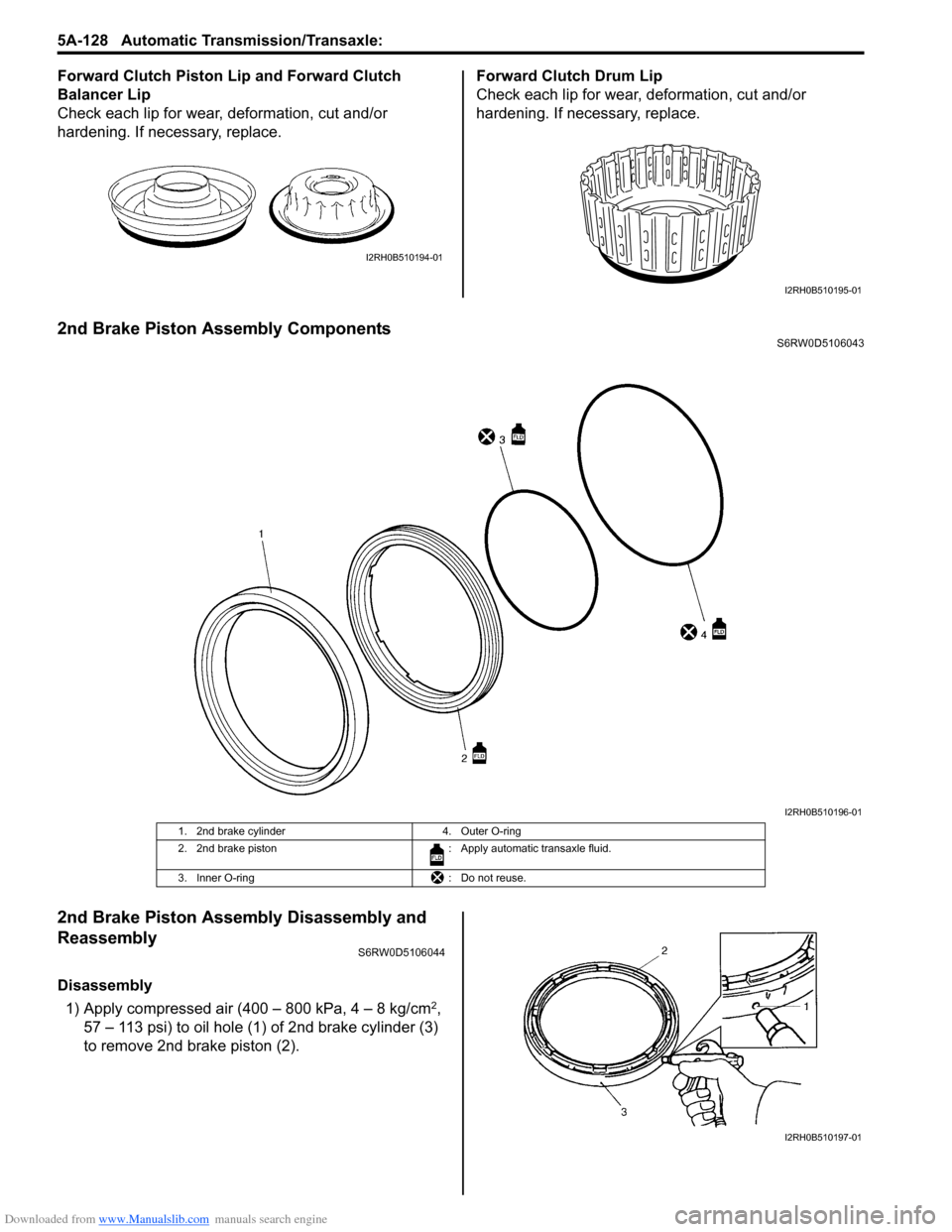
Downloaded from www.Manualslib.com manuals search engine 5A-128 Automatic Transmission/Transaxle:
Forward Clutch Piston Lip and Forward Clutch
Balancer Lip
Check each lip for wear, deformation, cut and/or
hardening. If necessary, replace.Forward Clutch Drum Lip
Check each lip for wear, deformation, cut and/or
hardening. If necessary, replace.
2nd Brake Piston Assembly ComponentsS6RW0D5106043
2nd Brake Piston Assembly Disassembly and
Reassembly
S6RW0D5106044
Disassembly
1) Apply compressed air (400 – 800 kPa, 4 – 8 kg/cm
2,
57 – 113 psi) to oil hole (1) of 2nd brake cylinder (3)
to remove 2nd brake piston (2).
I2RH0B510194-01
I2RH0B510195-01
I2RH0B510196-01
1. 2nd brake cylinder 4. Outer O-ring
2. 2nd brake piston : Apply automatic transaxle fluid.
3. Inner O-ring : Do not reuse.
I2RH0B510197-01
Page 779 of 1556
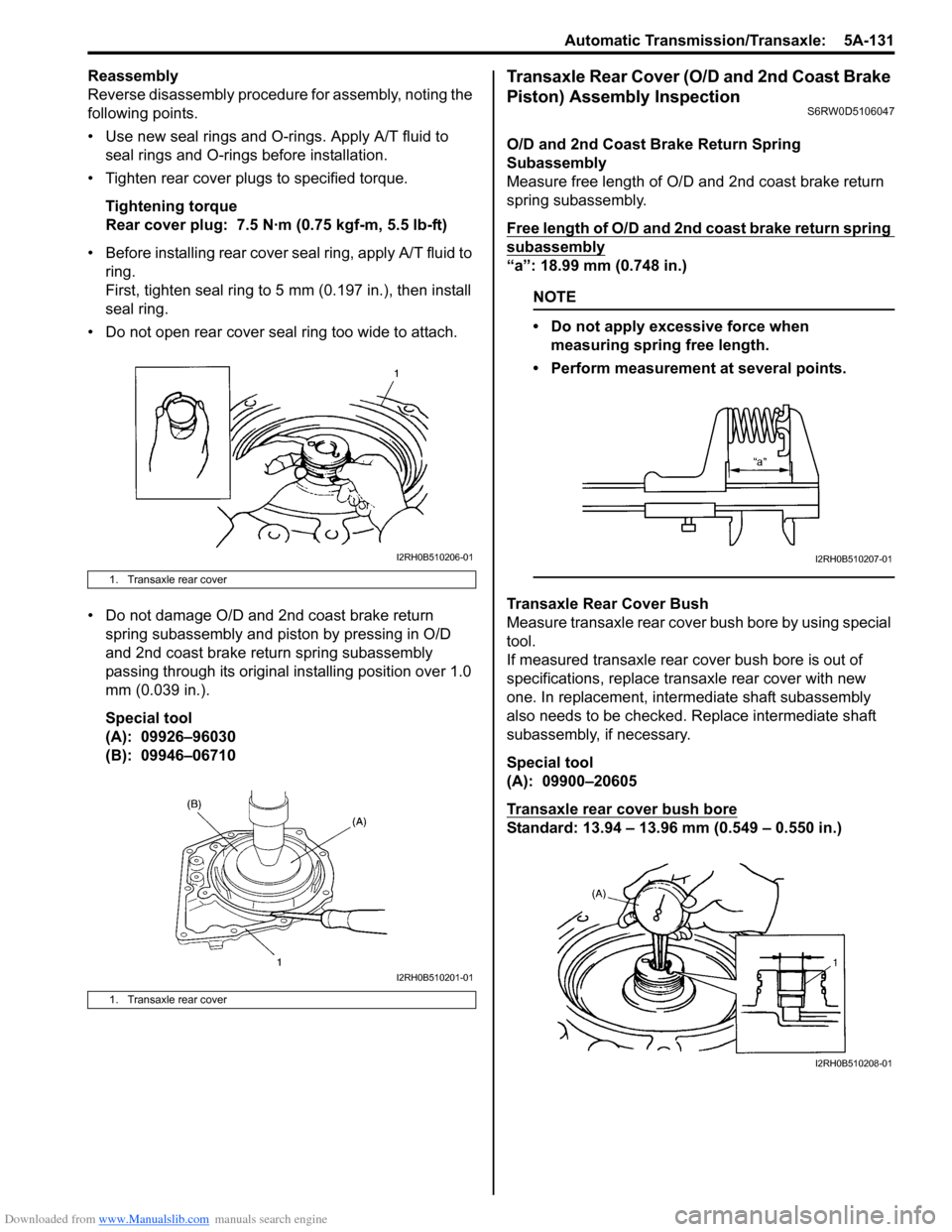
Downloaded from www.Manualslib.com manuals search engine Automatic Transmission/Transaxle: 5A-131
Reassembly
Reverse disassembly procedure for assembly, noting the
following points.
• Use new seal rings and O-rings. Apply A/T fluid to
seal rings and O-rings before installation.
• Tighten rear cover plugs to specified torque.
Tightening torque
Rear cover plug: 7.5 N·m (0.75 kgf-m, 5.5 lb-ft)
• Before installing rear cover seal ring, apply A/T fluid to
ring.
First, tighten seal ring to 5 mm (0.197 in.), then install
seal ring.
• Do not open rear cover seal ring too wide to attach.
• Do not damage O/D and 2nd coast brake return
spring subassembly and piston by pressing in O/D
and 2nd coast brake return spring subassembly
passing through its original installing position over 1.0
mm (0.039 in.).
Special tool
(A): 09926–96030
(B): 09946–06710Transaxle Rear Cover (O/D and 2nd Coast Brake
Piston) Assembly Inspection
S6RW0D5106047
O/D and 2nd Coast Brake Return Spring
Subassembly
Measure free length of O/D and 2nd coast brake return
spring subassembly.
Free length of O/D and 2nd coast brake return spring
subassembly
“a”: 18.99 mm (0.748 in.)
NOTE
• Do not apply excessive force when
measuring spring free length.
• Perform measurement at several points.
Transaxle Rear Cover Bush
Measure transaxle rear cover bush bore by using special
tool.
If measured transaxle rear cover bush bore is out of
specifications, replace transaxle rear cover with new
one. In replacement, intermediate shaft subassembly
also needs to be checked. Replace intermediate shaft
subassembly, if necessary.
Special tool
(A): 09900–20605
Transaxle rear cover bush bore
Standard: 13.94 – 13.96 mm (0.549 – 0.550 in.)
1. Transaxle rear cover
1. Transaxle rear cover
I2RH0B510206-01
I2RH0B510201-01
I2RH0B510207-01
I2RH0B510208-01
Page 789 of 1556
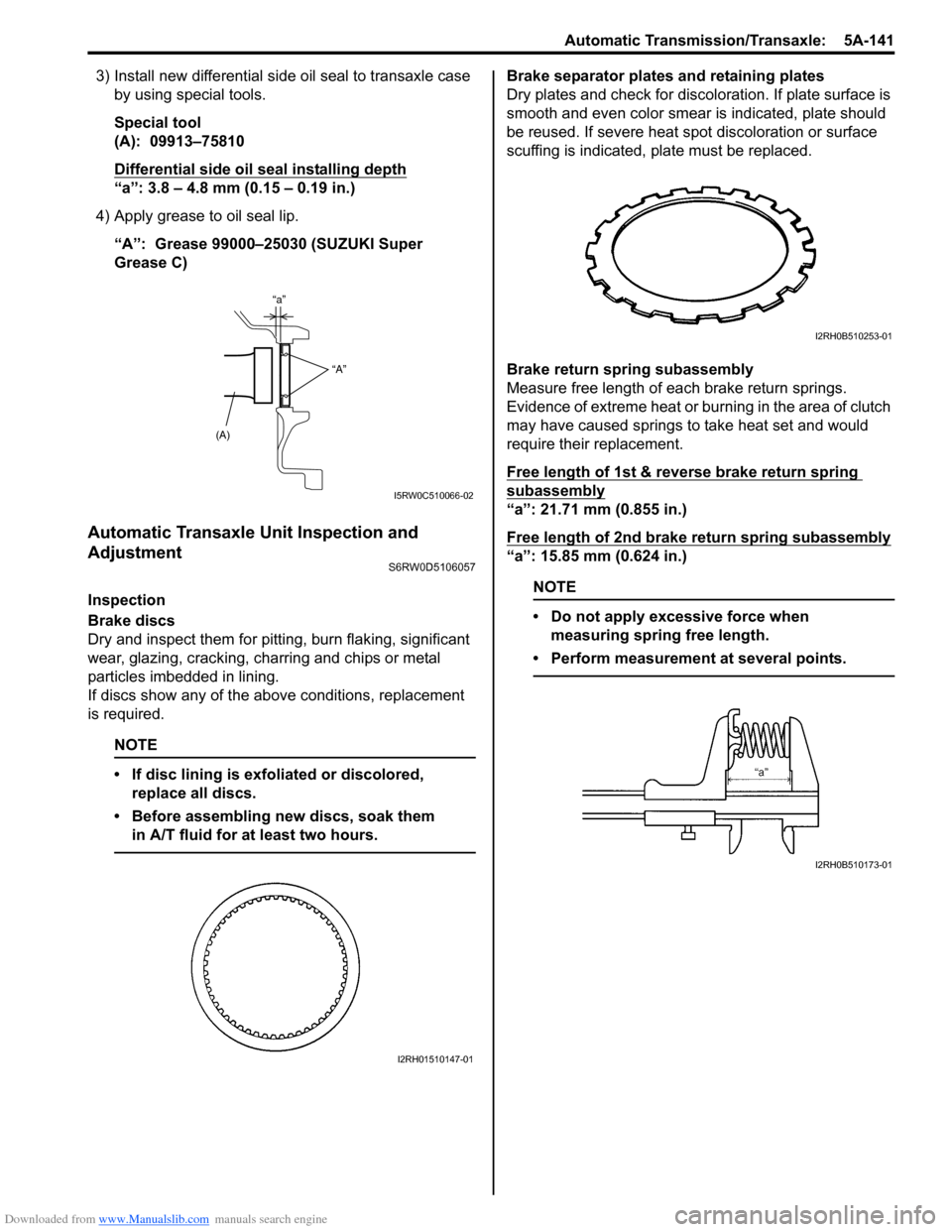
Downloaded from www.Manualslib.com manuals search engine Automatic Transmission/Transaxle: 5A-141
3) Install new differential side oil seal to transaxle case
by using special tools.
Special tool
(A): 09913–75810
Differential side oil seal installing depth
“a”: 3.8 – 4.8 mm (0.15 – 0.19 in.)
4) Apply grease to oil seal lip.
“A”: Grease 99000–25030 (SUZUKI Super
Grease C)
Automatic Transaxle Unit Inspection and
Adjustment
S6RW0D5106057
Inspection
Brake discs
Dry and inspect them for pitting, burn flaking, significant
wear, glazing, cracking, charring and chips or metal
particles imbedded in lining.
If discs show any of the above conditions, replacement
is required.
NOTE
• If disc lining is exfoliated or discolored,
replace all discs.
• Before assembling new discs, soak them
in A/T fluid for at least two hours.
Brake separator plates and retaining plates
Dry plates and check for discoloration. If plate surface is
smooth and even color smear is indicated, plate should
be reused. If severe heat spot discoloration or surface
scuffing is indicated, plate must be replaced.
Brake return spring subassembly
Measure free length of each brake return springs.
Evidence of extreme heat or burning in the area of clutch
may have caused springs to take heat set and would
require their replacement.
Free length of 1st & reverse brake return spring
subassembly
“a”: 21.71 mm (0.855 in.)
Free length of 2nd brake return spring subassembly
“a”: 15.85 mm (0.624 in.)
NOTE
• Do not apply excessive force when
measuring spring free length.
• Perform measurement at several points.
(A)“a”
“A”
I5RW0C510066-02
I2RH01510147-01
I2RH0B510253-01
I2RH0B510173-01
Page 792 of 1556
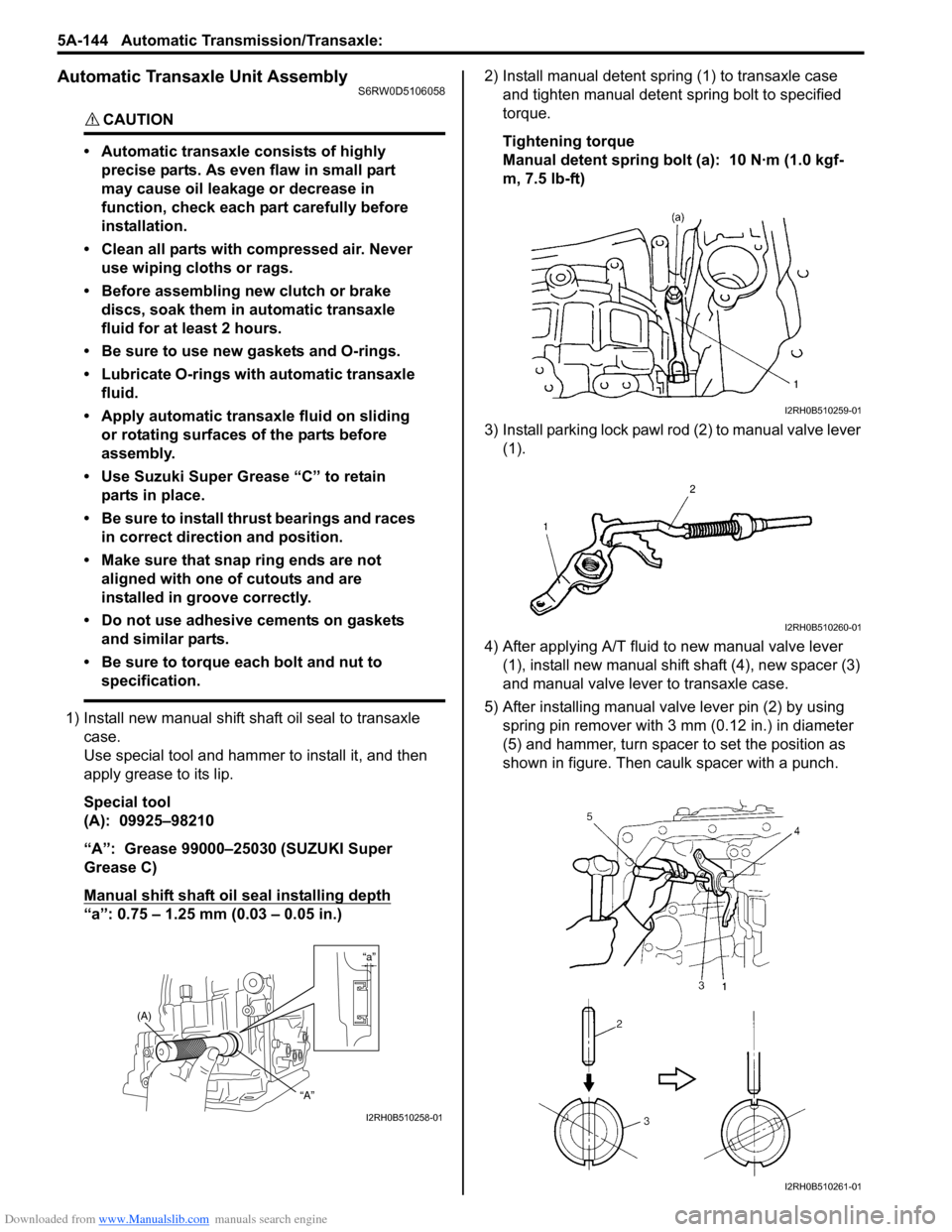
Downloaded from www.Manualslib.com manuals search engine 5A-144 Automatic Transmission/Transaxle:
Automatic Transaxle Unit AssemblyS6RW0D5106058
CAUTION!
• Automatic transaxle consists of highly
precise parts. As even flaw in small part
may cause oil leakage or decrease in
function, check each part carefully before
installation.
• Clean all parts with compressed air. Never
use wiping cloths or rags.
• Before assembling new clutch or brake
discs, soak them in automatic transaxle
fluid for at least 2 hours.
• Be sure to use new gaskets and O-rings.
• Lubricate O-rings with automatic transaxle
fluid.
• Apply automatic transaxle fluid on sliding
or rotating surfaces of the parts before
assembly.
• Use Suzuki Super Grease “C” to retain
parts in place.
• Be sure to install thrust bearings and races
in correct direction and position.
• Make sure that snap ring ends are not
aligned with one of cutouts and are
installed in groove correctly.
• Do not use adhesive cements on gaskets
and similar parts.
• Be sure to torque each bolt and nut to
specification.
1) Install new manual shift shaft oil seal to transaxle
case.
Use special tool and hammer to install it, and then
apply grease to its lip.
Special tool
(A): 09925–98210
“A”: Grease 99000–25030 (SUZUKI Super
Grease C)
Manual shift shaft oil seal installing depth
“a”: 0.75 – 1.25 mm (0.03 – 0.05 in.)2) Install manual detent spring (1) to transaxle case
and tighten manual detent spring bolt to specified
torque.
Tightening torque
Manual detent spring bolt (a): 10 N·m (1.0 kgf-
m, 7.5 lb-ft)
3) Install parking lock pawl rod (2) to manual valve lever
(1).
4) After applying A/T fluid to new manual valve lever
(1), install new manual shift shaft (4), new spacer (3)
and manual valve lever to transaxle case.
5) After installing manual valve lever pin (2) by using
spring pin remover with 3 mm (0.12 in.) in diameter
(5) and hammer, turn spacer to set the position as
shown in figure. Then caulk spacer with a punch.
“a”
(A)
“A”
I2RH0B510258-01
I2RH0B510259-01
I2RH0B510260-01
I2RH0B510261-01
Page 796 of 1556
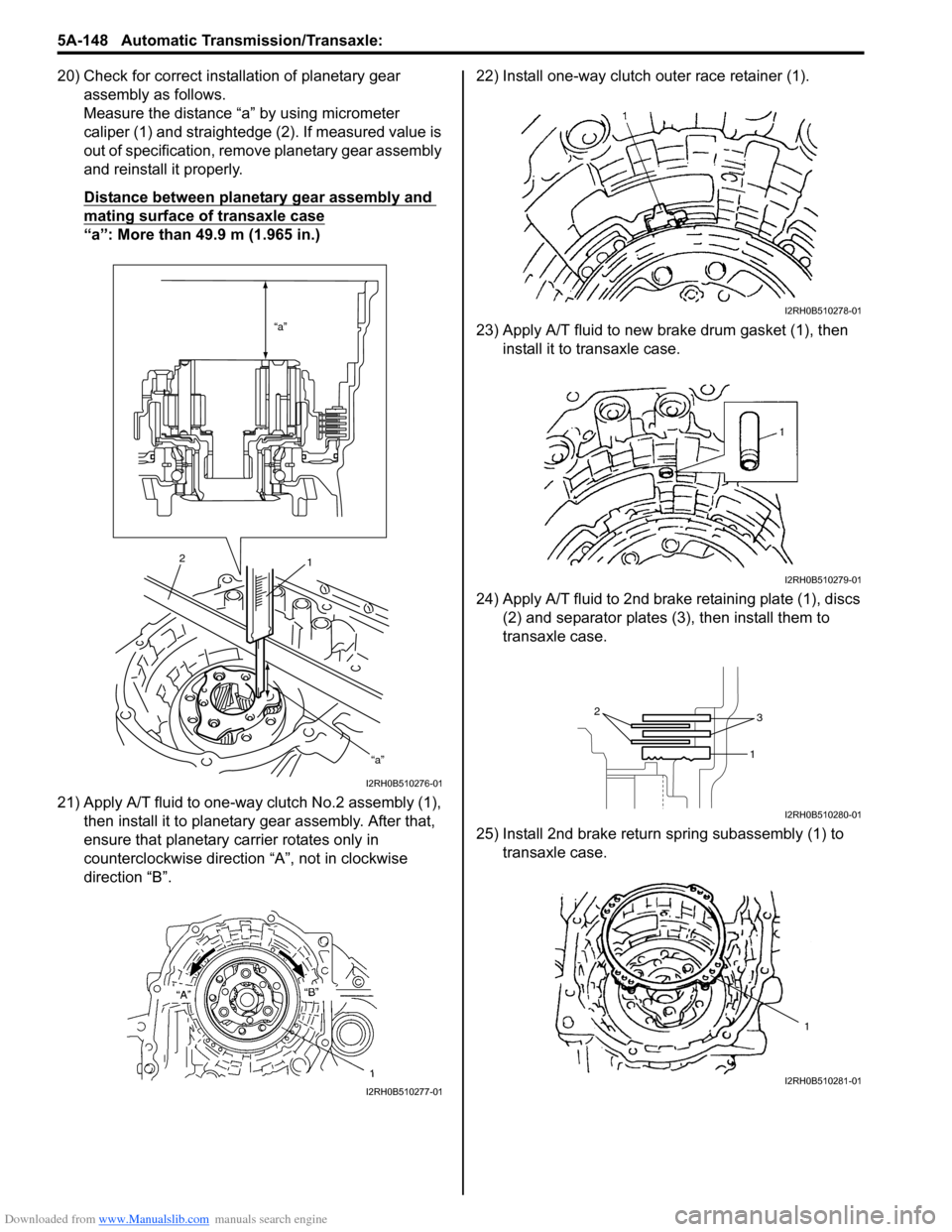
Downloaded from www.Manualslib.com manuals search engine 5A-148 Automatic Transmission/Transaxle:
20) Check for correct installation of planetary gear
assembly as follows.
Measure the distance “a” by using micrometer
caliper (1) and straightedge (2). If measured value is
out of specification, remove planetary gear assembly
and reinstall it properly.
Distance between planetary gear assembly and
mating surface of transaxle case
“a”: More than 49.9 m (1.965 in.)
21) Apply A/T fluid to one-way clutch No.2 assembly (1),
then install it to planetary gear assembly. After that,
ensure that planetary carrier rotates only in
counterclockwise direction “A”, not in clockwise
direction “B”.22) Install one-way clutch outer race retainer (1).
23) Apply A/T fluid to new brake drum gasket (1), then
install it to transaxle case.
24) Apply A/T fluid to 2nd brake retaining plate (1), discs
(2) and separator plates (3), then install them to
transaxle case.
25) Install 2nd brake return spring subassembly (1) to
transaxle case.
“a”
“a”
2
1
I2RH0B510276-01
I2RH0B510277-01
I2RH0B510278-01
I2RH0B510279-01
2
3
1
I2RH0B510280-01
1
I2RH0B510281-01
Page 797 of 1556
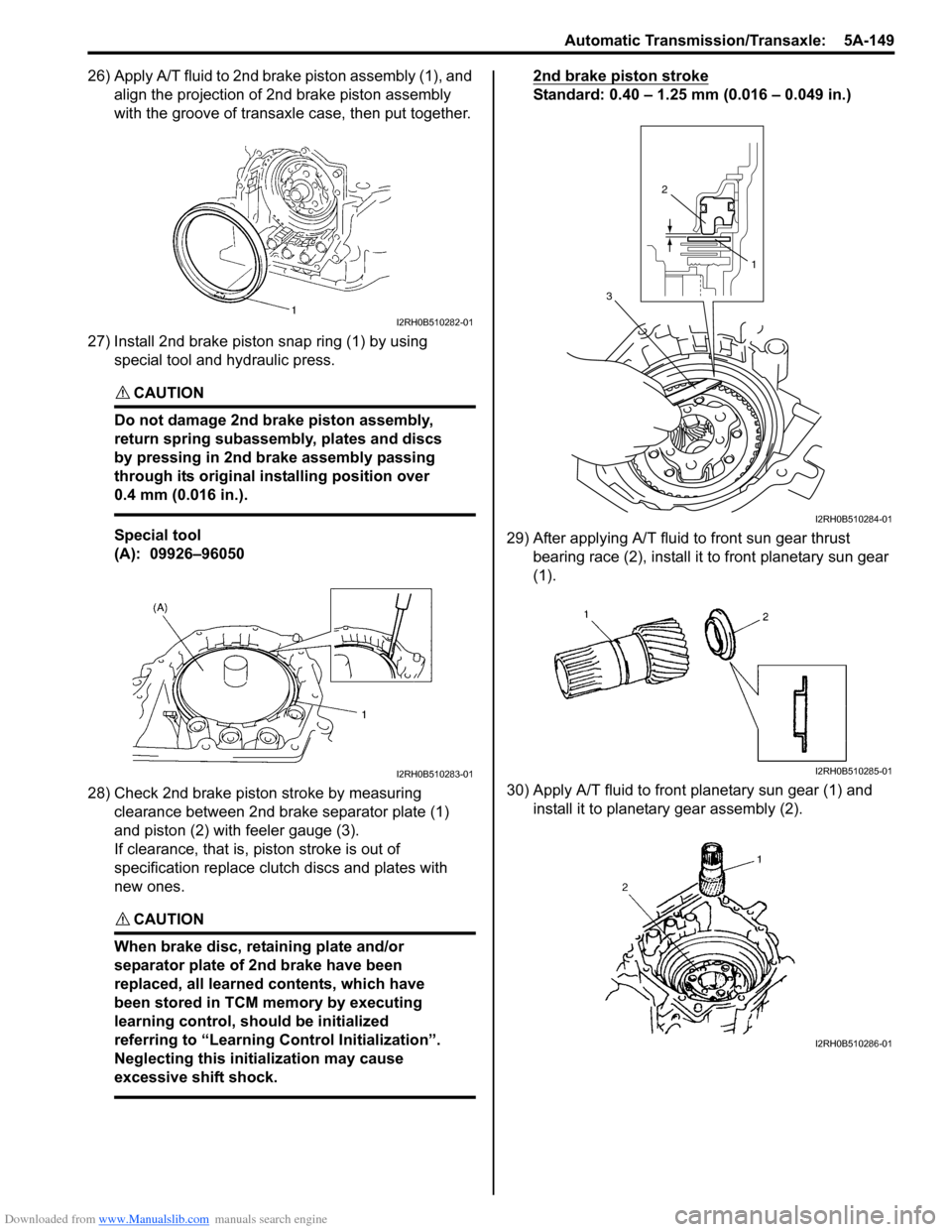
Downloaded from www.Manualslib.com manuals search engine Automatic Transmission/Transaxle: 5A-149
26) Apply A/T fluid to 2nd brake piston assembly (1), and
align the projection of 2nd brake piston assembly
with the groove of transaxle case, then put together.
27) Install 2nd brake piston snap ring (1) by using
special tool and hydraulic press.
CAUTION!
Do not damage 2nd brake piston assembly,
return spring subassembly, plates and discs
by pressing in 2nd brake assembly passing
through its original installing position over
0.4 mm (0.016 in.).
Special tool
(A): 09926–96050
28) Check 2nd brake piston stroke by measuring
clearance between 2nd brake separator plate (1)
and piston (2) with feeler gauge (3).
If clearance, that is, piston stroke is out of
specification replace clutch discs and plates with
new ones.
CAUTION!
When brake disc, retaining plate and/or
separator plate of 2nd brake have been
replaced, all learned contents, which have
been stored in TCM memory by executing
learning control, should be initialized
referring to “Learning Control Initialization”.
Neglecting this initialization may cause
excessive shift shock.
2nd brake piston stroke
Standard: 0.40 – 1.25 mm (0.016 – 0.049 in.)
29) After applying A/T fluid to front sun gear thrust
bearing race (2), install it to front planetary sun gear
(1).
30) Apply A/T fluid to front planetary sun gear (1) and
install it to planetary gear assembly (2).
I2RH0B510282-01
I2RH0B510283-01
32
1
I2RH0B510284-01
I2RH0B510285-01
I2RH0B510286-01
Page 799 of 1556
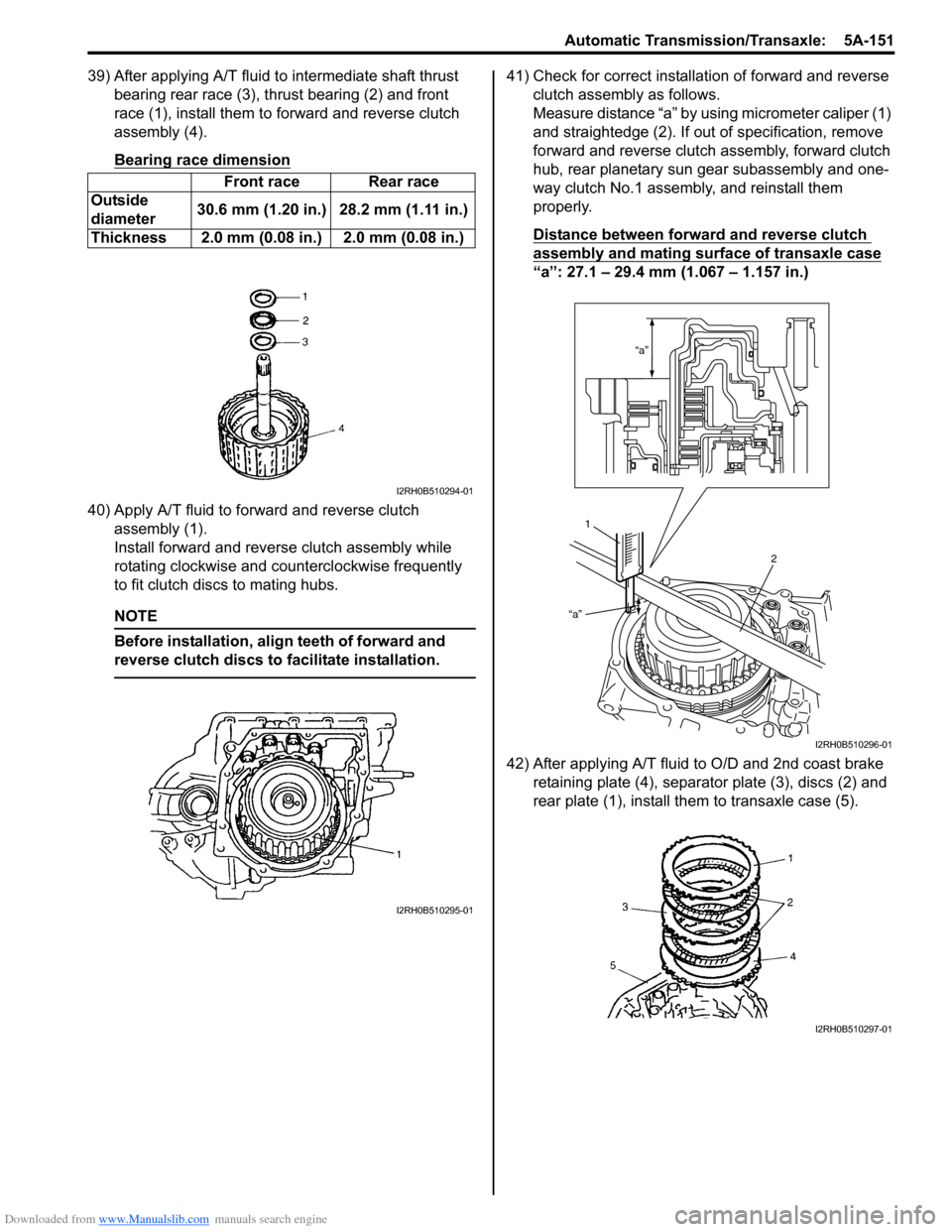
Downloaded from www.Manualslib.com manuals search engine Automatic Transmission/Transaxle: 5A-151
39) After applying A/T fluid to intermediate shaft thrust
bearing rear race (3), thrust bearing (2) and front
race (1), install them to forward and reverse clutch
assembly (4).
Bearing race dimension
40) Apply A/T fluid to forward and reverse clutch
assembly (1).
Install forward and reverse clutch assembly while
rotating clockwise and counterclockwise frequently
to fit clutch discs to mating hubs.
NOTE
Before installation, align teeth of forward and
reverse clutch discs to facilitate installation.
41) Check for correct installation of forward and reverse
clutch assembly as follows.
Measure distance “a” by using micrometer caliper (1)
and straightedge (2). If out of specification, remove
forward and reverse clutch assembly, forward clutch
hub, rear planetary sun gear subassembly and one-
way clutch No.1 assembly, and reinstall them
properly.
Distance between forward and reverse clutch
assembly and mating surface of transaxle case
“a”: 27.1 – 29.4 mm (1.067 – 1.157 in.)
42) After applying A/T fluid to O/D and 2nd coast brake
retaining plate (4), separator plate (3), discs (2) and
rear plate (1), install them to transaxle case (5). Front race Rear race
Outside
diameter30.6 mm (1.20 in.) 28.2 mm (1.11 in.)
Thickness 2.0 mm (0.08 in.) 2.0 mm (0.08 in.)
I2RH0B510294-01
I2RH0B510295-01
“a”
“a”
1
2
I2RH0B510296-01
I2RH0B510297-01
Page 802 of 1556
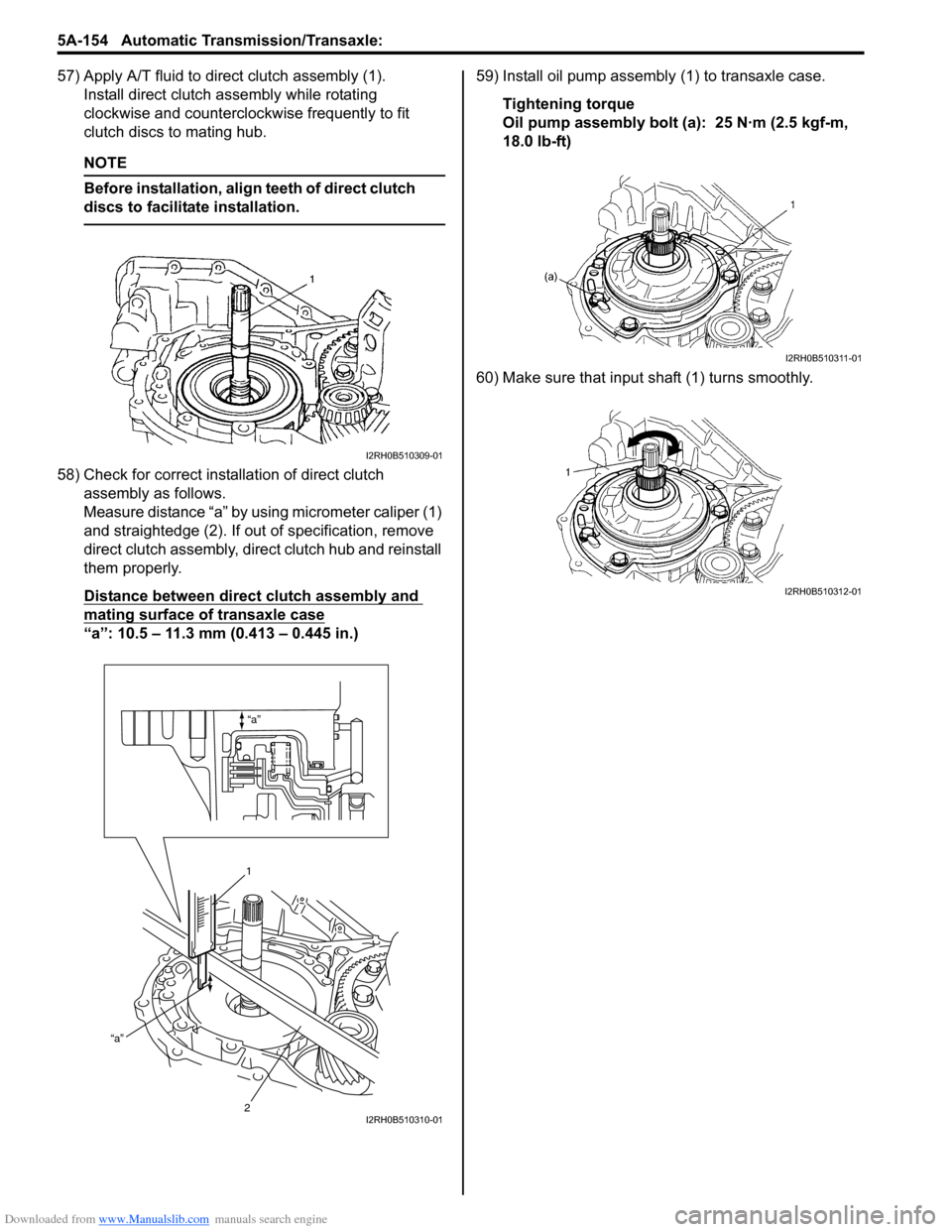
Downloaded from www.Manualslib.com manuals search engine 5A-154 Automatic Transmission/Transaxle:
57) Apply A/T fluid to direct clutch assembly (1).
Install direct clutch assembly while rotating
clockwise and counterclockwise frequently to fit
clutch discs to mating hub.
NOTE
Before installation, align teeth of direct clutch
discs to facilitate installation.
58) Check for correct installation of direct clutch
assembly as follows.
Measure distance “a” by using micrometer caliper (1)
and straightedge (2). If out of specification, remove
direct clutch assembly, direct clutch hub and reinstall
them properly.
Distance between direct clutch assembly and
mating surface of transaxle case
“a”: 10.5 – 11.3 mm (0.413 – 0.445 in.)59) Install oil pump assembly (1) to transaxle case.
Tightening torque
Oil pump assembly bolt (a): 25 N·m (2.5 kgf-m,
18.0 lb-ft)
60) Make sure that input shaft (1) turns smoothly.
I2RH0B510309-01
“a”
“a”
1
2
I2RH0B510310-01
I2RH0B510311-01
I2RH0B510312-01
Page 804 of 1556
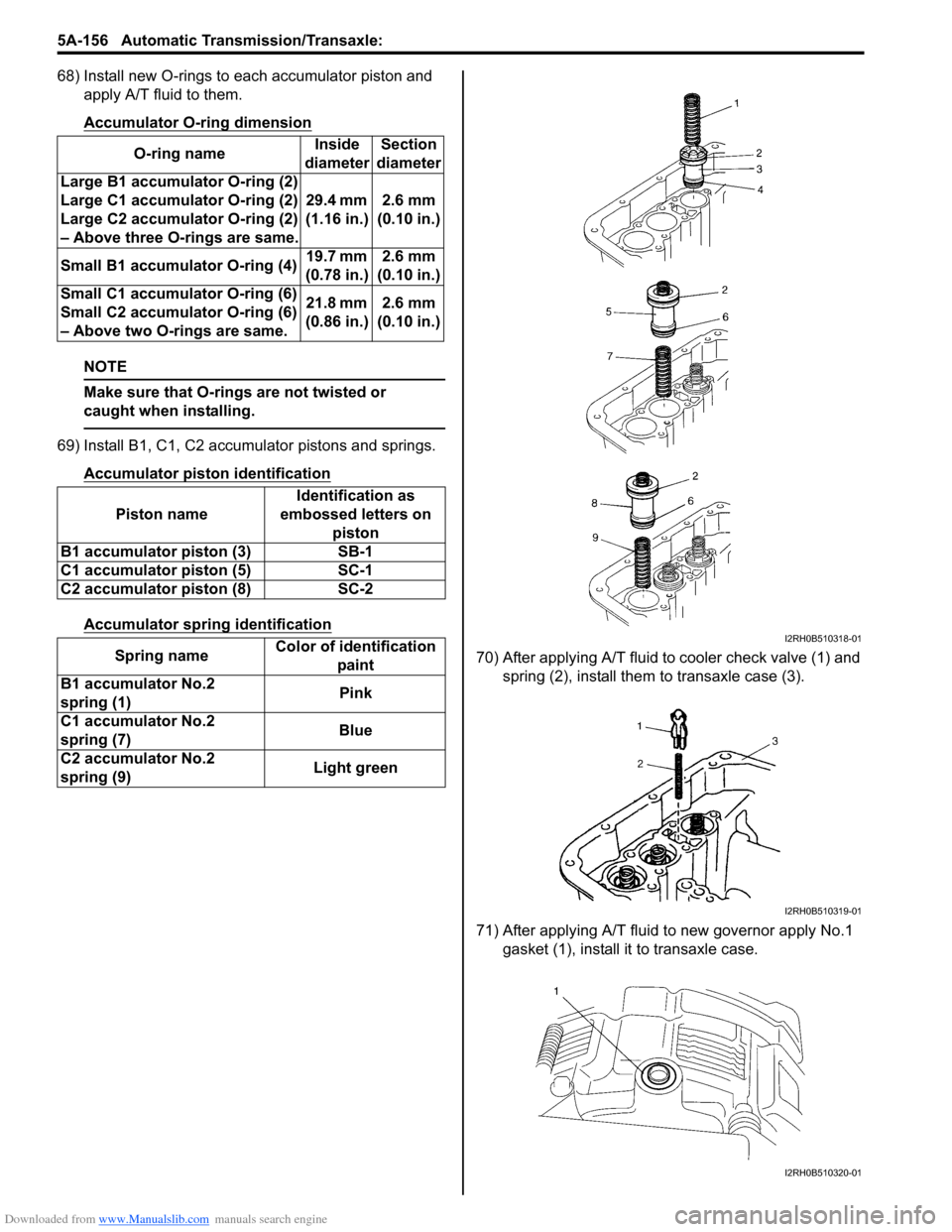
Downloaded from www.Manualslib.com manuals search engine 5A-156 Automatic Transmission/Transaxle:
68) Install new O-rings to each accumulator piston and
apply A/T fluid to them.
Accumulator O-ring dimension
NOTE
Make sure that O-rings are not twisted or
caught when installing.
69) Install B1, C1, C2 accumulator pistons and springs.
Accumulator piston identification
Accumulator spring identification
70) After applying A/T fluid to cooler check valve (1) and
spring (2), install them to transaxle case (3).
71) After applying A/T fluid to new governor apply No.1
gasket (1), install it to transaxle case. O-ring nameInside
diameterSection
diameter
Large B1 accumulator O-ring (2)
Large C1 accumulator O-ring (2)
Large C2 accumulator O-ring (2)
– Above three O-rings are same.29.4 mm
(1.16 in.)2.6 mm
(0.10 in.)
Small B1 accumulator O-ring (4)19.7 mm
(0.78 in.)2.6 mm
(0.10 in.)
Small C1 accumulator O-ring (6)
Small C2 accumulator O-ring (6)
– Above two O-rings are same.21.8 mm
(0.86 in.)2.6 mm
(0.10 in.)
Piston nameIdentification as
embossed letters on
piston
B1 accumulator piston (3) SB-1
C1 accumulator piston (5) SC-1
C2 accumulator piston (8) SC-2
Spring nameColor of identification
paint
B1 accumulator No.2
spring (1)Pink
C1 accumulator No.2
spring (7)Blue
C2 accumulator No.2
spring (9)Light green
I2RH0B510318-01
I2RH0B510319-01
I2RH0B510320-01
Page 808 of 1556
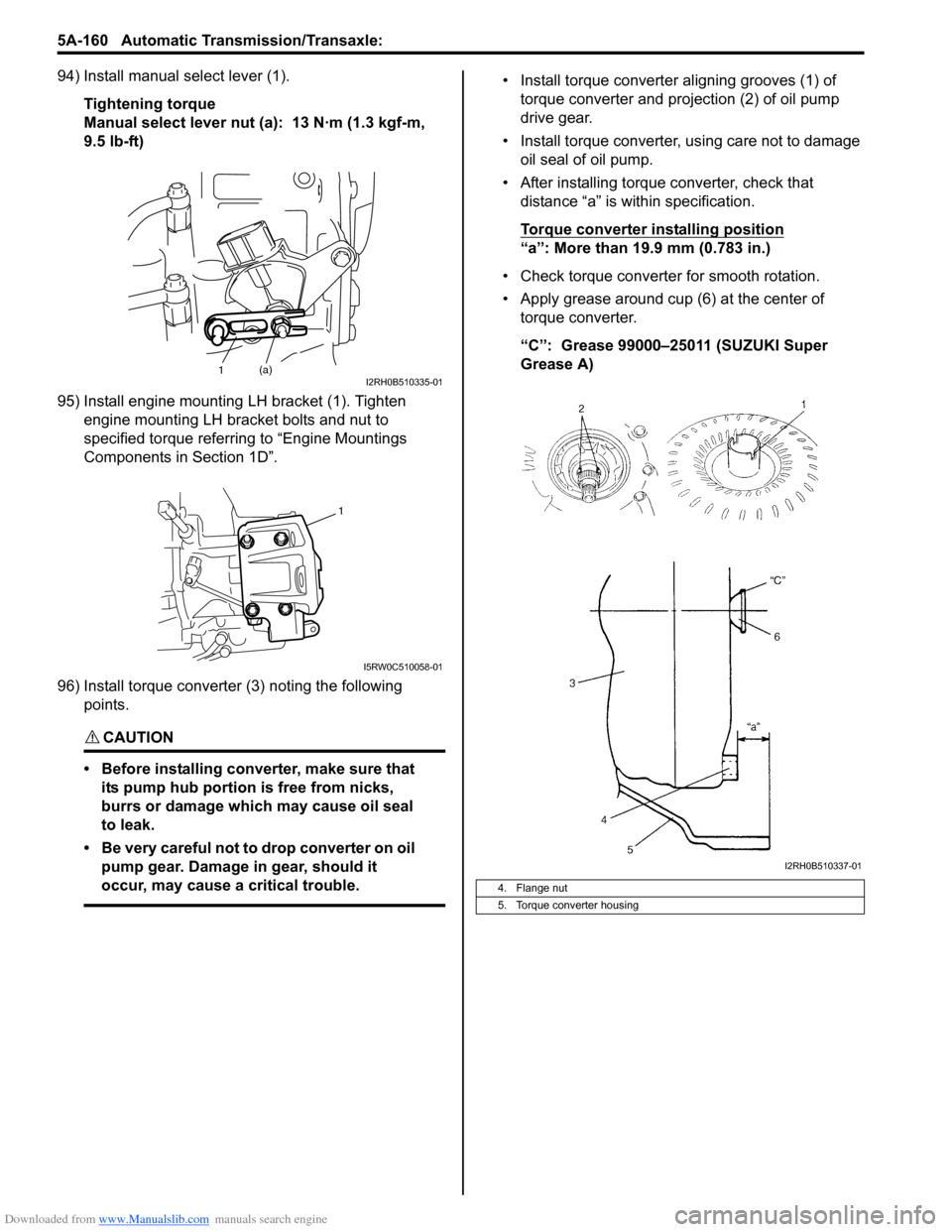
Downloaded from www.Manualslib.com manuals search engine 5A-160 Automatic Transmission/Transaxle:
94) Install manual select lever (1).
Tightening torque
Manual select lever nut (a): 13 N·m (1.3 kgf-m,
9.5 lb-ft)
95) Install engine mounting LH bracket (1). Tighten
engine mounting LH bracket bolts and nut to
specified torque referring to “Engine Mountings
Components in Section 1D”.
96) Install torque converter (3) noting the following
points.
CAUTION!
• Before installing converter, make sure that
its pump hub portion is free from nicks,
burrs or damage which may cause oil seal
to leak.
• Be very careful not to drop converter on oil
pump gear. Damage in gear, should it
occur, may cause a critical trouble.
• Install torque converter aligning grooves (1) of
torque converter and projection (2) of oil pump
drive gear.
• Install torque converter, using care not to damage
oil seal of oil pump.
• After installing torque converter, check that
distance “a” is within specification.
Torque converter installing position
“a”: More than 19.9 mm (0.783 in.)
• Check torque converter for smooth rotation.
• Apply grease around cup (6) at the center of
torque converter.
“C”: Grease 99000–25011 (SUZUKI Super
Grease A)
1(a)I2RH0B510335-01
1
I5RW0C510058-01
4. Flange nut
5. Torque converter housing
I2RH0B510337-01