Display SUZUKI SX4 2006 1.G Service Workshop Manual
[x] Cancel search | Manufacturer: SUZUKI, Model Year: 2006, Model line: SX4, Model: SUZUKI SX4 2006 1.GPages: 1556, PDF Size: 37.31 MB
Page 11 of 1556
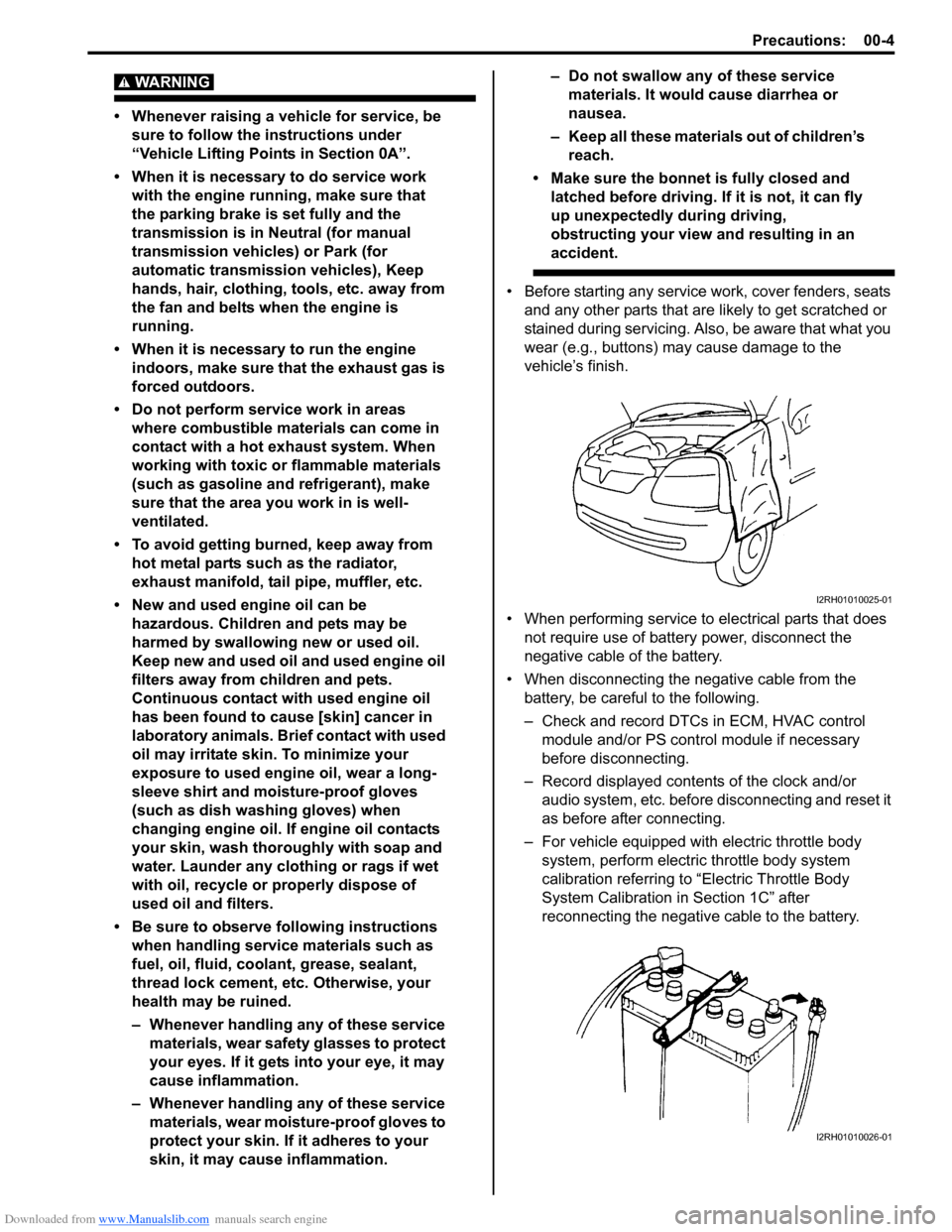
Downloaded from www.Manualslib.com manuals search engine Precautions: 00-4
WARNING!
• Whenever raising a vehicle for service, be
sure to follow the instructions under
“Vehicle Lifting Points in Section 0A”.
• When it is necessary to do service work
with the engine running, make sure that
the parking brake is set fully and the
transmission is in Neutral (for manual
transmission vehicles) or Park (for
automatic transmission vehicles), Keep
hands, hair, clothing, tools, etc. away from
the fan and belts when the engine is
running.
• When it is necessary to run the engine
indoors, make sure that the exhaust gas is
forced outdoors.
• Do not perform service work in areas
where combustible materials can come in
contact with a hot exhaust system. When
working with toxic or flammable materials
(such as gasoline and refrigerant), make
sure that the area you work in is well-
ventilated.
• To avoid getting burned, keep away from
hot metal parts such as the radiator,
exhaust manifold, tail pipe, muffler, etc.
• New and used engine oil can be
hazardous. Children and pets may be
harmed by swallowing new or used oil.
Keep new and used oil and used engine oil
filters away from children and pets.
Continuous contact with used engine oil
has been found to cause [skin] cancer in
laboratory animals. Brief contact with used
oil may irritate skin. To minimize your
exposure to used engine oil, wear a long-
sleeve shirt and moisture-proof gloves
(such as dish washing gloves) when
changing engine oil. If engine oil contacts
your skin, wash thoroughly with soap and
water. Launder any clothing or rags if wet
with oil, recycle or properly dispose of
used oil and filters.
• Be sure to observe following instructions
when handling service materials such as
fuel, oil, fluid, coolant, grease, sealant,
thread lock cement, etc. Otherwise, your
health may be ruined.
– Whenever handling any of these service
materials, wear safety glasses to protect
your eyes. If it gets into your eye, it may
cause inflammation.
– Whenever handling any of these service
materials, wear moisture-proof gloves to
protect your skin. If it adheres to your
skin, it may cause inflammation.– Do not swallow any of these service
materials. It would cause diarrhea or
nausea.
– Keep all these materials out of children’s
reach.
• Make sure the bonnet is fully closed and
latched before driving. If it is not, it can fly
up unexpectedly during driving,
obstructing your view and resulting in an
accident.
• Before starting any service work, cover fenders, seats
and any other parts that are likely to get scratched or
stained during servicing. Also, be aware that what you
wear (e.g., buttons) may cause damage to the
vehicle’s finish.
• When performing service to electrical parts that does
not require use of battery power, disconnect the
negative cable of the battery.
• When disconnecting the negative cable from the
battery, be careful to the following.
– Check and record DTCs in ECM, HVAC control
module and/or PS control module if necessary
before disconnecting.
– Record displayed contents of the clock and/or
audio system, etc. before disconnecting and reset it
as before after connecting.
– For vehicle equipped with electric throttle body
system, perform electric throttle body system
calibration referring to “Electric Throttle Body
System Calibration in Section 1C” after
reconnecting the negative cable to the battery.
I2RH01010025-01
I2RH01010026-01
Page 52 of 1556
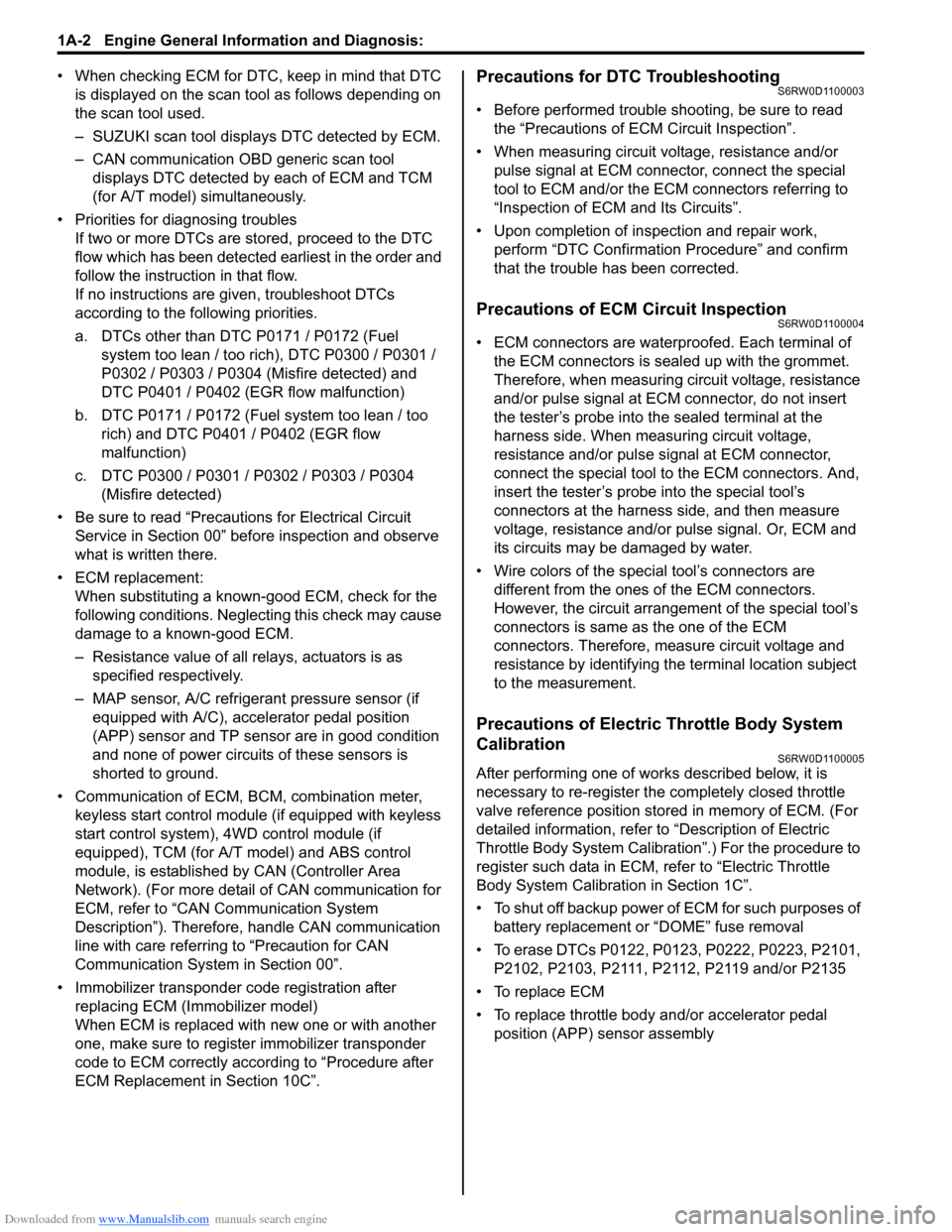
Downloaded from www.Manualslib.com manuals search engine 1A-2 Engine General Information and Diagnosis:
• When checking ECM for DTC, keep in mind that DTC
is displayed on the scan tool as follows depending on
the scan tool used.
– SUZUKI scan tool displays DTC detected by ECM.
– CAN communication OBD generic scan tool
displays DTC detected by each of ECM and TCM
(for A/T model) simultaneously.
• Priorities for diagnosing troubles
If two or more DTCs are stored, proceed to the DTC
flow which has been detected earliest in the order and
follow the instruction in that flow.
If no instructions are given, troubleshoot DTCs
according to the following priorities.
a. DTCs other than DTC P0171 / P0172 (Fuel
system too lean / too rich), DTC P0300 / P0301 /
P0302 / P0303 / P0304 (Misfire detected) and
DTC P0401 / P0402 (EGR flow malfunction)
b. DTC P0171 / P0172 (Fuel system too lean / too
rich) and DTC P0401 / P0402 (EGR flow
malfunction)
c. DTC P0300 / P0301 / P0302 / P0303 / P0304
(Misfire detected)
• Be sure to read “Precautions for Electrical Circuit
Service in Section 00” before inspection and observe
what is written there.
• ECM replacement:
When substituting a known-good ECM, check for the
following conditions. Neglecting this check may cause
damage to a known-good ECM.
– Resistance value of all relays, actuators is as
specified respectively.
– MAP sensor, A/C refrigerant pressure sensor (if
equipped with A/C), accelerator pedal position
(APP) sensor and TP sensor are in good condition
and none of power circuits of these sensors is
shorted to ground.
• Communication of ECM, BCM, combination meter,
keyless start control module (if equipped with keyless
start control system), 4WD control module (if
equipped), TCM (for A/T model) and ABS control
module, is established by CAN (Controller Area
Network). (For more detail of CAN communication for
ECM, refer to “CAN Communication System
Description”). Therefore, handle CAN communication
line with care referring to “Precaution for CAN
Communication System in Section 00”.
• Immobilizer transponder code registration after
replacing ECM (Immobilizer model)
When ECM is replaced with new one or with another
one, make sure to register immobilizer transponder
code to ECM correctly according to “Procedure after
ECM Replacement in Section 10C”.Precautions for DTC TroubleshootingS6RW0D1100003
• Before performed trouble shooting, be sure to read
the “Precautions of ECM Circuit Inspection”.
• When measuring circuit voltage, resistance and/or
pulse signal at ECM connector, connect the special
tool to ECM and/or the ECM connectors referring to
“Inspection of ECM and Its Circuits”.
• Upon completion of inspection and repair work,
perform “DTC Confirmation Procedure” and confirm
that the trouble has been corrected.
Precautions of ECM Circuit InspectionS6RW0D1100004
• ECM connectors are waterproofed. Each terminal of
the ECM connectors is sealed up with the grommet.
Therefore, when measuring circuit voltage, resistance
and/or pulse signal at ECM connector, do not insert
the tester’s probe into the sealed terminal at the
harness side. When measuring circuit voltage,
resistance and/or pulse signal at ECM connector,
connect the special tool to the ECM connectors. And,
insert the tester’s probe into the special tool’s
connectors at the harness side, and then measure
voltage, resistance and/or pulse signal. Or, ECM and
its circuits may be damaged by water.
• Wire colors of the special tool’s connectors are
different from the ones of the ECM connectors.
However, the circuit arrangement of the special tool’s
connectors is same as the one of the ECM
connectors. Therefore, measure circuit voltage and
resistance by identifying the terminal location subject
to the measurement.
Precautions of Electric Throttle Body System
Calibration
S6RW0D1100005
After performing one of works described below, it is
necessary to re-register the completely closed throttle
valve reference position stored in memory of ECM. (For
detailed information, refer to “Description of Electric
Throttle Body System Calibration”.) For the procedure to
register such data in ECM, refer to “Electric Throttle
Body System Calibration in Section 1C”.
• To shut off backup power of ECM for such purposes of
battery replacement or “DOME” fuse removal
• To erase DTCs P0122, P0123, P0222, P0223, P2101,
P2102, P2103, P2111, P2112, P2119 and/or P2135
• To replace ECM
• To replace throttle body and/or accelerator pedal
position (APP) sensor assembly
Page 54 of 1556
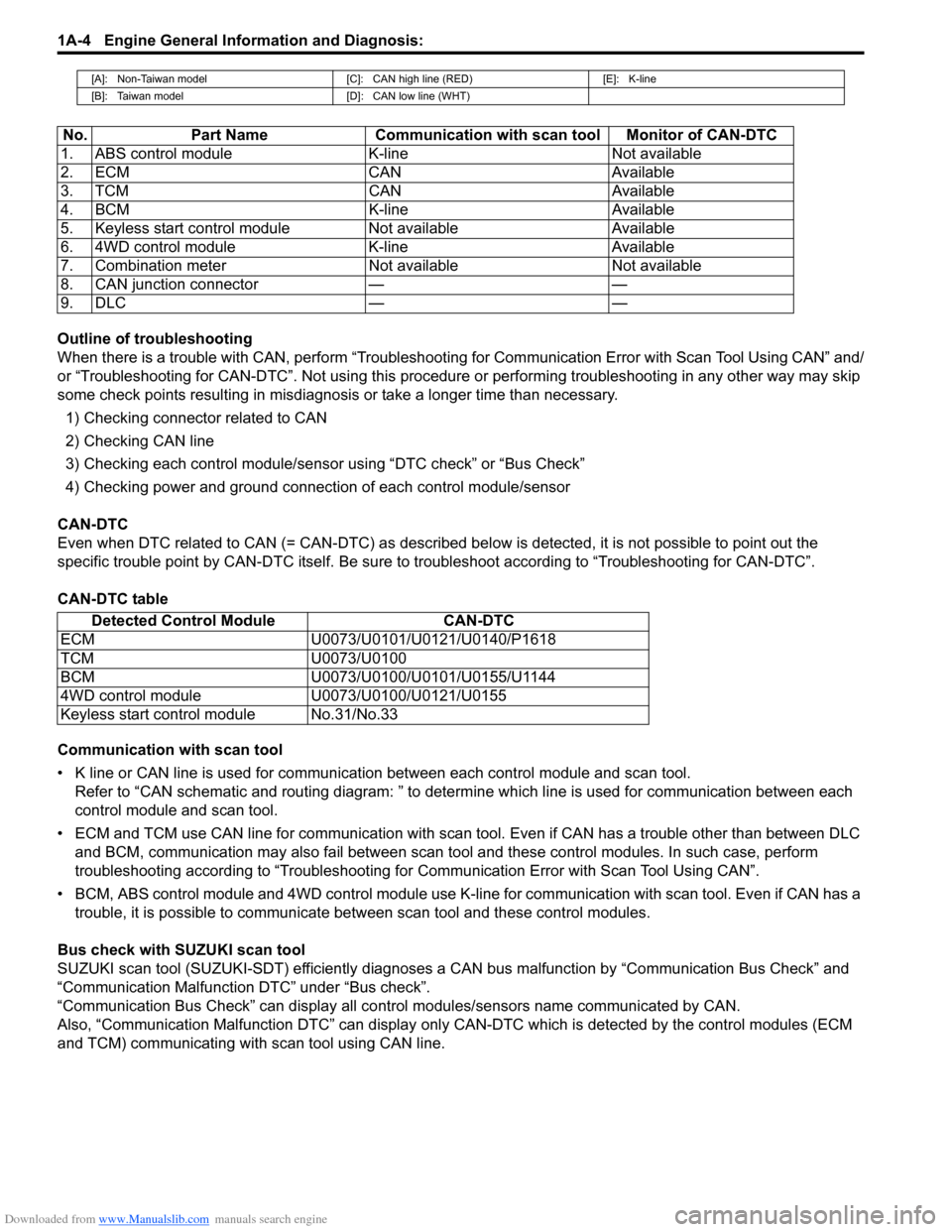
Downloaded from www.Manualslib.com manuals search engine 1A-4 Engine General Information and Diagnosis:
Outline of troubleshooting
When there is a trouble with CAN, perform “Troubleshooting for Communication Error with Scan Tool Using CAN” and/
or “Troubleshooting for CAN-DTC”. Not using this procedure or performing troubleshooting in any other way may skip
some check points resulting in misdiagnosis or take a longer time than necessary.
1) Checking connector related to CAN
2) Checking CAN line
3) Checking each control module/sensor using “DTC check” or “Bus Check”
4) Checking power and ground connection of each control module/sensor
CAN-DTC
Even when DTC related to CAN (= CAN-DTC) as described below is detected, it is not possible to point out the
specific trouble point by CAN-DTC itself. Be sure to troubleshoot according to “Troubleshooting for CAN-DTC”.
CAN-DTC table
Communication with scan tool
• K line or CAN line is used for communication between each control module and scan tool.
Refer to “CAN schematic and routing diagram: ” to determine which line is used for communication between each
control module and scan tool.
• ECM and TCM use CAN line for communication with scan tool. Even if CAN has a trouble other than between DLC
and BCM, communication may also fail between scan tool and these control modules. In such case, perform
troubleshooting according to “Troubleshooting for Communication Error with Scan Tool Using CAN”.
• BCM, ABS control module and 4WD control module use K-line for communication with scan tool. Even if CAN has a
trouble, it is possible to communicate between scan tool and these control modules.
Bus check with SUZUKI scan tool
SUZUKI scan tool (SUZUKI-SDT) efficiently diagnoses a CAN bus malfunction by “Communication Bus Check” and
“Communication Malfunction DTC” under “Bus check”.
“Communication Bus Check” can display all control modules/sensors name communicated by CAN.
Also, “Communication Malfunction DTC” can display only CAN-DTC which is detected by the control modules (ECM
and TCM) communicating with scan tool using CAN line.
[A]: Non-Taiwan model [C]: CAN high line (RED) [E]: K-line
[B]: Taiwan model [D]: CAN low line (WHT)
No. Part Name Communication with scan tool Monitor of CAN-DTC
1. ABS control module K-line Not available
2. ECM CAN Available
3. TCM CAN Available
4. BCM K-line Available
5. Keyless start control module Not available Available
6. 4WD control module K-line Available
7. Combination meter Not available Not available
8. CAN junction connector — —
9. DLC — —
Detected Control Module CAN-DTC
ECM U0073/U0101/U0121/U0140/P1618
TCM U0073/U0100
BCM U0073/U0100/U0101/U0155/U1144
4WD control module U0073/U0100/U0121/U0155
Keyless start control module No.31/No.33
Page 76 of 1556
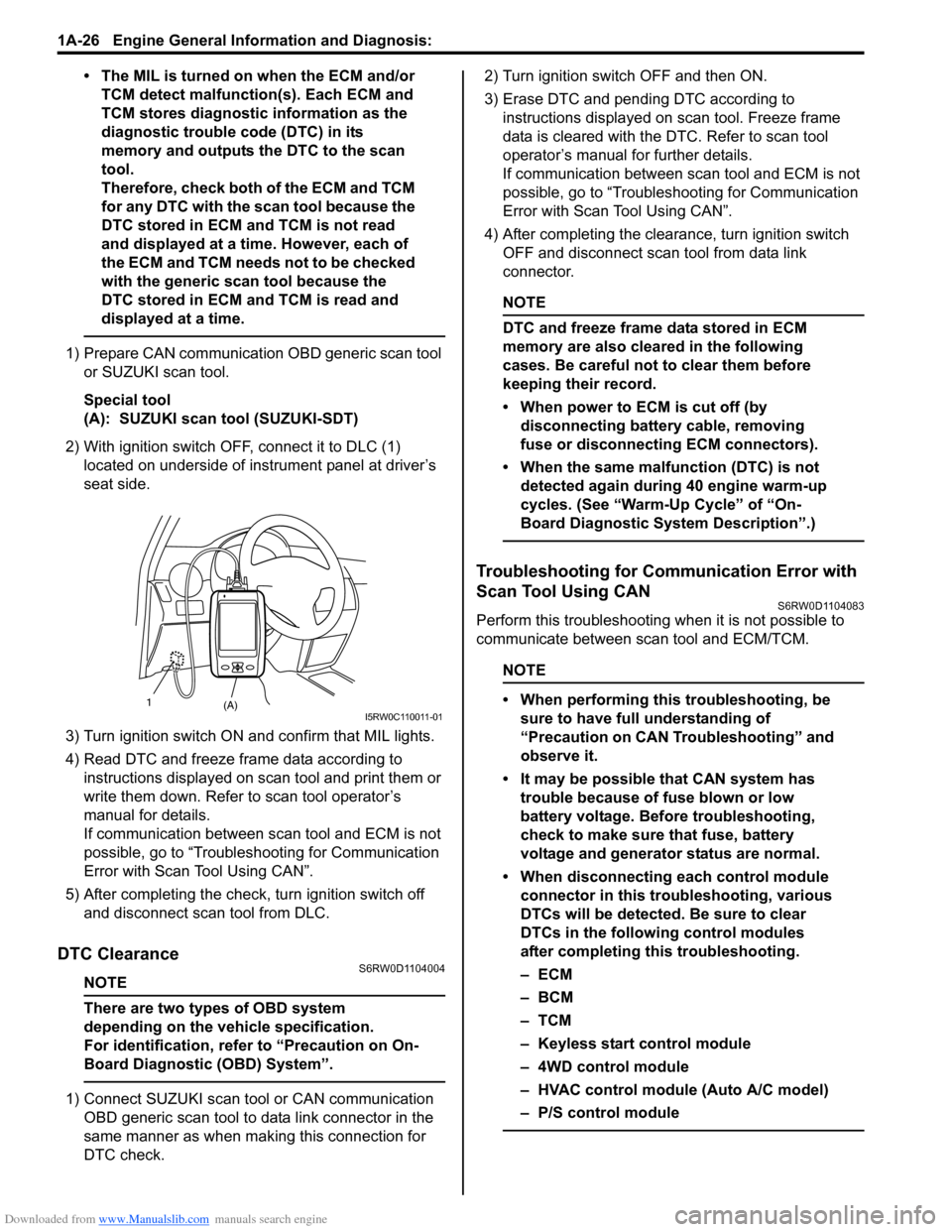
Downloaded from www.Manualslib.com manuals search engine 1A-26 Engine General Information and Diagnosis:
• The MIL is turned on when the ECM and/or
TCM detect malfunction(s). Each ECM and
TCM stores diagnostic information as the
diagnostic trouble code (DTC) in its
memory and outputs the DTC to the scan
tool.
Therefore, check both of the ECM and TCM
for any DTC with the scan tool because the
DTC stored in ECM and TCM is not read
and displayed at a time. However, each of
the ECM and TCM needs not to be checked
with the generic scan tool because the
DTC stored in ECM and TCM is read and
displayed at a time.
1) Prepare CAN communication OBD generic scan tool
or SUZUKI scan tool.
Special tool
(A): SUZUKI scan tool (SUZUKI-SDT)
2) With ignition switch OFF, connect it to DLC (1)
located on underside of instrument panel at driver’s
seat side.
3) Turn ignition switch ON and confirm that MIL lights.
4) Read DTC and freeze frame data according to
instructions displayed on scan tool and print them or
write them down. Refer to scan tool operator’s
manual for details.
If communication between scan tool and ECM is not
possible, go to “Troubleshooting for Communication
Error with Scan Tool Using CAN”.
5) After completing the check, turn ignition switch off
and disconnect scan tool from DLC.
DTC ClearanceS6RW0D1104004
NOTE
There are two types of OBD system
depending on the vehicle specification.
For identification, refer to “Precaution on On-
Board Diagnostic (OBD) System”.
1) Connect SUZUKI scan tool or CAN communication
OBD generic scan tool to data link connector in the
same manner as when making this connection for
DTC check.2) Turn ignition switch OFF and then ON.
3) Erase DTC and pending DTC according to
instructions displayed on scan tool. Freeze frame
data is cleared with the DTC. Refer to scan tool
operator’s manual for further details.
If communication between scan tool and ECM is not
possible, go to “Troubleshooting for Communication
Error with Scan Tool Using CAN”.
4) After completing the clearance, turn ignition switch
OFF and disconnect scan tool from data link
connector.
NOTE
DTC and freeze frame data stored in ECM
memory are also cleared in the following
cases. Be careful not to clear them before
keeping their record.
• When power to ECM is cut off (by
disconnecting battery cable, removing
fuse or disconnecting ECM connectors).
• When the same malfunction (DTC) is not
detected again during 40 engine warm-up
cycles. (See “Warm-Up Cycle” of “On-
Board Diagnostic System Description”.)
Troubleshooting for Communication Error with
Scan Tool Using CAN
S6RW0D1104083
Perform this troubleshooting when it is not possible to
communicate between scan tool and ECM/TCM.
NOTE
• When performing this troubleshooting, be
sure to have full understanding of
“Precaution on CAN Troubleshooting” and
observe it.
• It may be possible that CAN system has
trouble because of fuse blown or low
battery voltage. Before troubleshooting,
check to make sure that fuse, battery
voltage and generator status are normal.
• When disconnecting each control module
connector in this troubleshooting, various
DTCs will be detected. Be sure to clear
DTCs in the following control modules
after completing this troubleshooting.
–ECM
–BCM
–TCM
– Keyless start control module
– 4WD control module
– HVAC control module (Auto A/C model)
– P/S control module
(A) 1I5RW0C110011-01
Page 86 of 1556
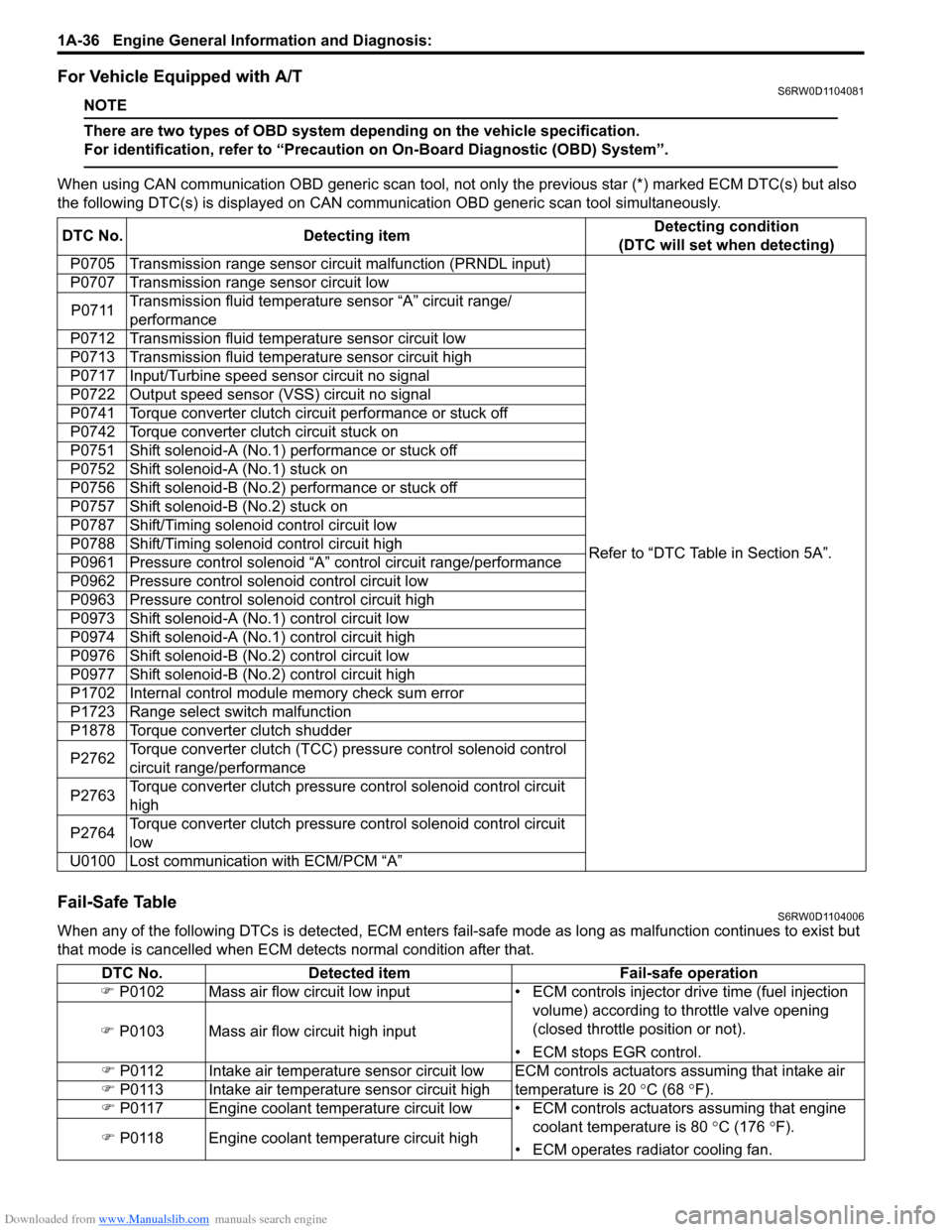
Downloaded from www.Manualslib.com manuals search engine 1A-36 Engine General Information and Diagnosis:
For Vehicle Equipped with A/TS6RW0D1104081
NOTE
There are two types of OBD system depending on the vehicle specification.
For identification, refer to “Precaution on On-Board Diagnostic (OBD) System”.
When using CAN communication OBD generic scan tool, not only the previous star (*) marked ECM DTC(s) but also
the following DTC(s) is displayed on CAN communication OBD generic scan tool simultaneously.
Fail-Safe TableS6RW0D1104006
When any of the following DTCs is detected, ECM enters fail-safe mode as long as malfunction continues to exist but
that mode is cancelled when ECM detects normal condition after that. DTC No. Detecting itemDetecting condition
(DTC will set when detecting)
P0705 Transmission range sensor circuit malfunction (PRNDL input)
Refer to “DTC Table in Section 5A”. P0707 Transmission range sensor circuit low
P0711Transmission fluid temperature sensor “A” circuit range/
performance
P0712 Transmission fluid temperature sensor circuit low
P0713 Transmission fluid temperature sensor circuit high
P0717 Input/Turbine speed sensor circuit no signal
P0722 Output speed sensor (VSS) circuit no signal
P0741 Torque converter clutch circuit performance or stuck off
P0742 Torque converter clutch circuit stuck on
P0751 Shift solenoid-A (No.1) performance or stuck off
P0752 Shift solenoid-A (No.1) stuck on
P0756 Shift solenoid-B (No.2) performance or stuck off
P0757 Shift solenoid-B (No.2) stuck on
P0787 Shift/Timing solenoid control circuit low
P0788 Shift/Timing solenoid control circuit high
P0961 Pressure control solenoid “A” control circuit range/performance
P0962 Pressure control solenoid control circuit low
P0963 Pressure control solenoid control circuit high
P0973 Shift solenoid-A (No.1) control circuit low
P0974 Shift solenoid-A (No.1) control circuit high
P0976 Shift solenoid-B (No.2) control circuit low
P0977 Shift solenoid-B (No.2) control circuit high
P1702 Internal control module memory check sum error
P1723 Range select switch malfunction
P1878 Torque converter clutch shudder
P2762Torque converter clutch (TCC) pressure control solenoid control
circuit range/performance
P2763Torque converter clutch pressure control solenoid control circuit
high
P2764Torque converter clutch pressure control solenoid control circuit
low
U0100 Lost communication with ECM/PCM “A”
DTC No. Detected item Fail-safe operation
) P0102 Mass air flow circuit low input • ECM controls injector drive time (fuel injection
volume) according to throttle valve opening
(closed throttle position or not).
• ECM stops EGR control. ) P0103 Mass air flow circuit high input
) P0112 Intake air temperature sensor circuit low ECM controls actuators assuming that intake air
temperature is 20 °C (68 °F). ) P0113 Intake air temperature sensor circuit high
) P0117 Engine coolant temperature circuit low • ECM controls actuators assuming that engine
coolant temperature is 80 °C (176 °F).
• ECM operates radiator cooling fan. ) P0118 Engine coolant temperature circuit high
Page 88 of 1556
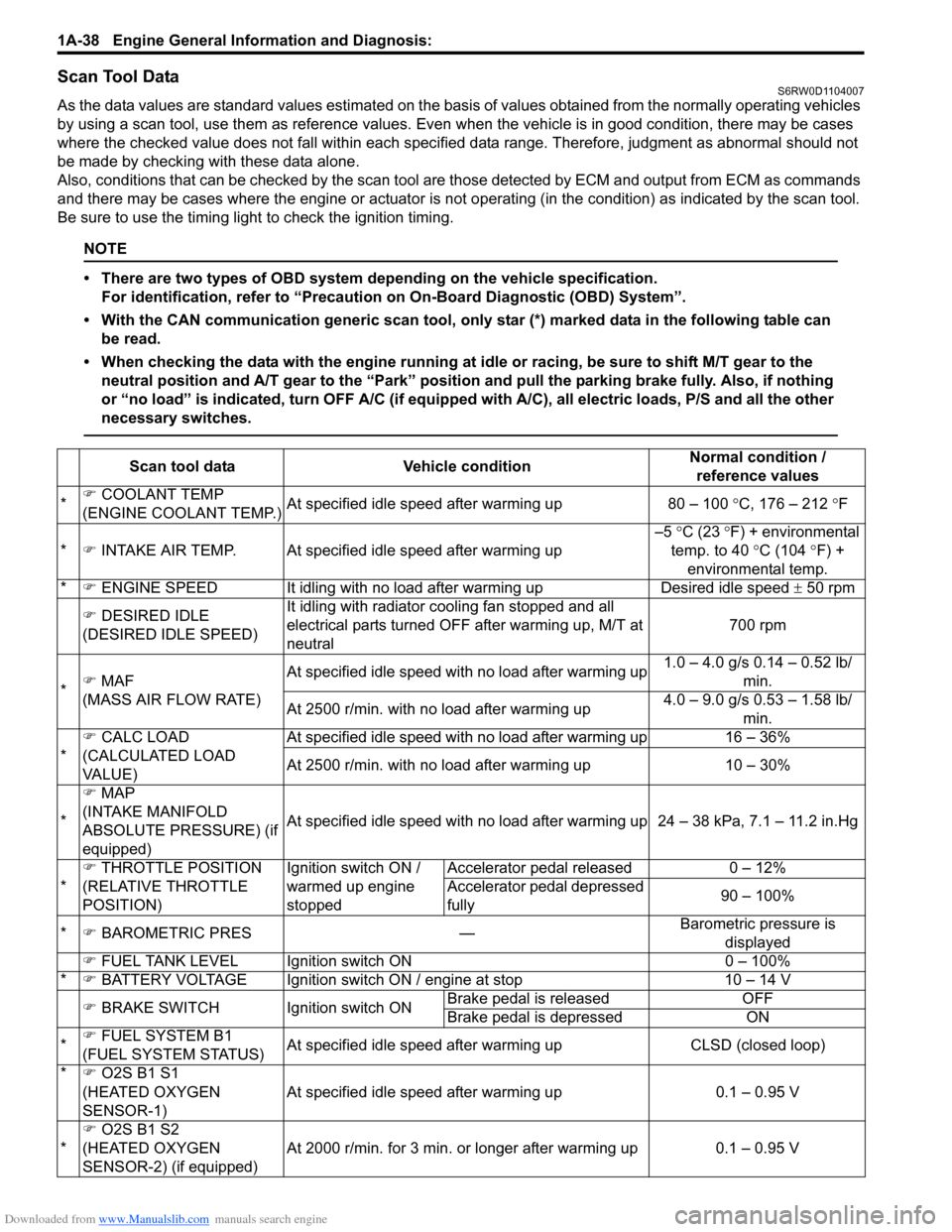
Downloaded from www.Manualslib.com manuals search engine 1A-38 Engine General Information and Diagnosis:
Scan Tool DataS6RW0D1104007
As the data values are standard values estimated on the basis of values obtained from the normally operating vehicles
by using a scan tool, use them as reference values. Even when the vehicle is in good condition, there may be cases
where the checked value does not fall within each specified data range. Therefore, judgment as abnormal should not
be made by checking with these data alone.
Also, conditions that can be checked by the scan tool are those detected by ECM and output from ECM as commands
and there may be cases where the engine or actuator is not operating (in the condition) as indicated by the scan tool.
Be sure to use the timing light to check the ignition timing.
NOTE
• There are two types of OBD system depending on the vehicle specification.
For identification, refer to “Precaution on On-Board Diagnostic (OBD) System”.
• With the CAN communication generic scan tool, only star (*) marked data in the following table can
be read.
• When checking the data with the engine running at idle or racing, be sure to shift M/T gear to the
neutral position and A/T gear to the “Park” position and pull the parking brake fully. Also, if nothing
or “no load” is indicated, turn OFF A/C (if equipped with A/C), all electric loads, P/S and all the other
necessary switches.
Scan tool data Vehicle conditionNormal condition /
reference values
* ) COOLANT TEMP
(ENGINE COOLANT TEMP.)At specified idle speed after warming up 80 – 100 °C, 176 – 212 °F
* ) INTAKE AIR TEMP. At specified idle speed after warming up–5 °C (23 °F) + environmental
temp. to 40 °C (104 °F) +
environmental temp.
* ) ENGINE SPEED It idling with no load after warming up Desired idle speed ± 50 rpm
) DESIRED IDLE
(DESIRED IDLE SPEED)It idling with radiator cooling fan stopped and all
electrical parts turned OFF after warming up, M/T at
neutral700 rpm
* ) MAF
(MASS AIR FLOW RATE)At specified idle speed with no load after warming up1.0 – 4.0 g/s 0.14 – 0.52 lb/
min.
At 2500 r/min. with no load after warming up4.0 – 9.0 g/s 0.53 – 1.58 lb/
min.
* ) CALC LOAD
(CALCULATED LOAD
VA L U E )At specified idle speed with no load after warming up 16 – 36%
At 2500 r/min. with no load after warming up 10 – 30%
* ) MAP
(INTAKE MANIFOLD
ABSOLUTE PRESSURE) (if
equipped)At specified idle speed with no load after warming up 24 – 38 kPa, 7.1 – 11.2 in.Hg
* ) THROTTLE POSITION
(RELATIVE THROTTLE
POSITION)Ignition switch ON /
warmed up engine
stoppedAccelerator pedal released 0 – 12%
Accelerator pedal depressed
fully90 – 100%
* ) BAROMETRIC PRES —Barometric pressure is
displayed
) FUEL TANK LEVEL Ignition switch ON 0 – 100%
* ) BATTERY VOLTAGE Ignition switch ON / engine at stop 10 – 14 V
) BRAKE SWITCH Ignition switch ONBrake pedal is released OFF
Brake pedal is depressed ON
* ) FUEL SYSTEM B1
(FUEL SYSTEM STATUS)At specified idle speed after warming up CLSD (closed loop)
* ) O2S B1 S1
(HEATED OXYGEN
SENSOR-1)At specified idle speed after warming up 0.1 – 0.95 V
* )
O2S B1 S2
(HEATED OXYGEN
SENSOR-2) (if equipped)At 2000 r/min. for 3 min. or longer after warming up 0.1 – 0.95 V
Page 91 of 1556
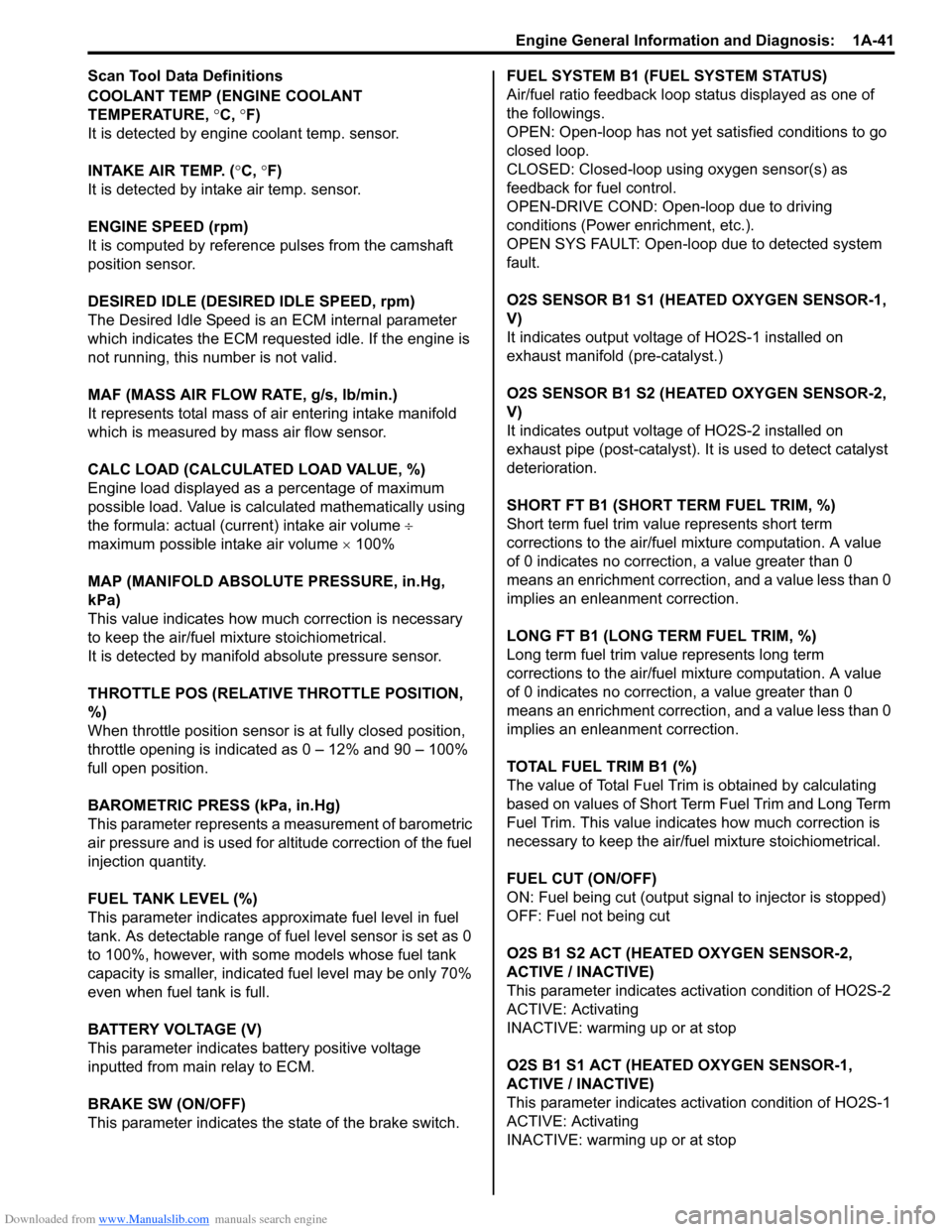
Downloaded from www.Manualslib.com manuals search engine Engine General Information and Diagnosis: 1A-41
Scan Tool Data Definitions
COOLANT TEMP (ENGINE COOLANT
TEMPERATURE, °C, °F)
It is detected by engine coolant temp. sensor.
INTAKE AIR TEMP. (°C, °F)
It is detected by intake air temp. sensor.
ENGINE SPEED (rpm)
It is computed by reference pulses from the camshaft
position sensor.
DESIRED IDLE (DESIRED IDLE SPEED, rpm)
The Desired Idle Speed is an ECM internal parameter
which indicates the ECM requested idle. If the engine is
not running, this number is not valid.
MAF (MASS AIR FLOW RATE, g/s, lb/min.)
It represents total mass of air entering intake manifold
which is measured by mass air flow sensor.
CALC LOAD (CALCULATED LOAD VALUE, %)
Engine load displayed as a percentage of maximum
possible load. Value is calculated mathematically using
the formula: actual (current) intake air volume ÷
maximum possible intake air volume × 100%
MAP (MANIFOLD ABSOLUTE PRESSURE, in.Hg,
kPa)
This value indicates how much correction is necessary
to keep the air/fuel mixture stoichiometrical.
It is detected by manifold absolute pressure sensor.
THROTTLE POS (RELATIVE THROTTLE POSITION,
%)
When throttle position sensor is at fully closed position,
throttle opening is indicated as 0 – 12% and 90 – 100%
full open position.
BAROMETRIC PRESS (kPa, in.Hg)
This parameter represents a measurement of barometric
air pressure and is used for altitude correction of the fuel
injection quantity.
FUEL TANK LEVEL (%)
This parameter indicates approximate fuel level in fuel
tank. As detectable range of fuel level sensor is set as 0
to 100%, however, with some models whose fuel tank
capacity is smaller, indicated fuel level may be only 70%
even when fuel tank is full.
BATTERY VOLTAGE (V)
This parameter indicates battery positive voltage
inputted from main relay to ECM.
BRAKE SW (ON/OFF)
This parameter indicates the state of the brake switch.FUEL SYSTEM B1 (FUEL SYSTEM STATUS)
Air/fuel ratio feedback loop status displayed as one of
the followings.
OPEN: Open-loop has not yet satisfied conditions to go
closed loop.
CLOSED: Closed-loop using oxygen sensor(s) as
feedback for fuel control.
OPEN-DRIVE COND: Open-loop due to driving
conditions (Power enrichment, etc.).
OPEN SYS FAULT: Open-loop due to detected system
fault.
O2S SENSOR B1 S1 (HEATED OXYGEN SENSOR-1,
V)
It indicates output voltage of HO2S-1 installed on
exhaust manifold (pre-catalyst.)
O2S SENSOR B1 S2 (HEATED OXYGEN SENSOR-2,
V)
It indicates output voltage of HO2S-2 installed on
exhaust pipe (post-catalyst). It is used to detect catalyst
deterioration.
SHORT FT B1 (SHORT TERM FUEL TRIM, %)
Short term fuel trim value represents short term
corrections to the air/fuel mixture computation. A value
of 0 indicates no correction, a value greater than 0
means an enrichment correction, and a value less than 0
implies an enleanment correction.
LONG FT B1 (LONG TERM FUEL TRIM, %)
Long term fuel trim value represents long term
corrections to the air/fuel mixture computation. A value
of 0 indicates no correction, a value greater than 0
means an enrichment correction, and a value less than 0
implies an enleanment correction.
TOTAL FUEL TRIM B1 (%)
The value of Total Fuel Trim is obtained by calculating
based on values of Short Term Fuel Trim and Long Term
Fuel Trim. This value indicates how much correction is
necessary to keep the air/fuel mixture stoichiometrical.
FUEL CUT (ON/OFF)
ON: Fuel being cut (output signal to injector is stopped)
OFF: Fuel not being cut
O2S B1 S2 ACT (HEATED OXYGEN SENSOR-2,
ACTIVE / INACTIVE)
This parameter indicates activation condition of HO2S-2
ACTIVE: Activating
INACTIVE: warming up or at stop
O2S B1 S1 ACT (HEATED OXYGEN SENSOR-1,
ACTIVE / INACTIVE)
This parameter indicates activation condition of HO2S-1
ACTIVE: Activating
INACTIVE: warming up or at stop
Page 92 of 1556
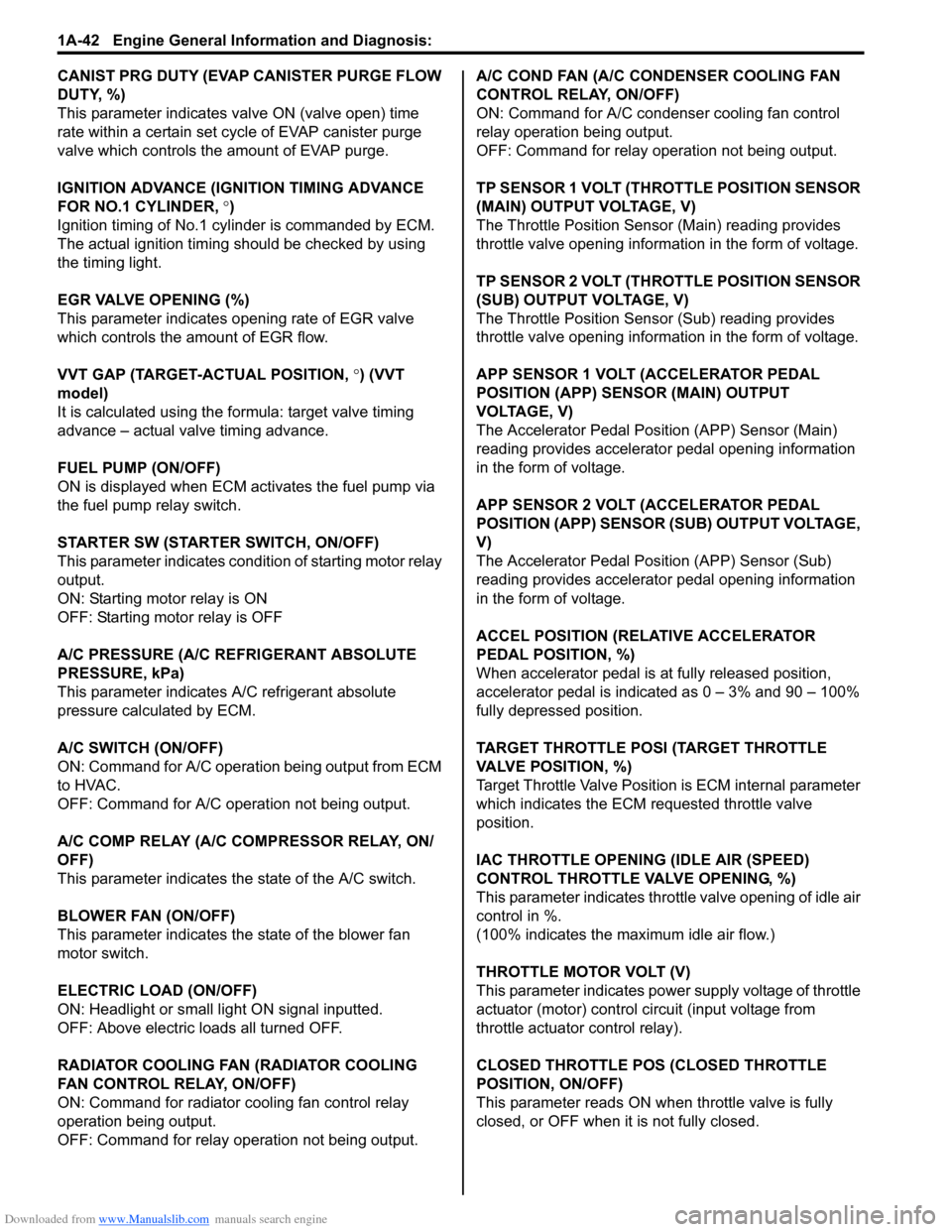
Downloaded from www.Manualslib.com manuals search engine 1A-42 Engine General Information and Diagnosis:
CANIST PRG DUTY (EVAP CANISTER PURGE FLOW
DUTY, %)
This parameter indicates valve ON (valve open) time
rate within a certain set cycle of EVAP canister purge
valve which controls the amount of EVAP purge.
IGNITION ADVANCE (IGNITION TIMING ADVANCE
FOR NO.1 CYLINDER, °)
Ignition timing of No.1 cylinder is commanded by ECM.
The actual ignition timing should be checked by using
the timing light.
EGR VALVE OPENING (%)
This parameter indicates opening rate of EGR valve
which controls the amount of EGR flow.
VVT GAP (TARGET-ACTUAL POSITION, °) (VVT
model)
It is calculated using the formula: target valve timing
advance – actual valve timing advance.
FUEL PUMP (ON/OFF)
ON is displayed when ECM activates the fuel pump via
the fuel pump relay switch.
STARTER SW (STARTER SWITCH, ON/OFF)
This parameter indicates condition of starting motor relay
output.
ON: Starting motor relay is ON
OFF: Starting motor relay is OFF
A/C PRESSURE (A/C REFRIGERANT ABSOLUTE
PRESSURE, kPa)
This parameter indicates A/C refrigerant absolute
pressure calculated by ECM.
A/C SWITCH (ON/OFF)
ON: Command for A/C operation being output from ECM
to HVAC.
OFF: Command for A/C operation not being output.
A/C COMP RELAY (A/C COMPRESSOR RELAY, ON/
OFF)
This parameter indicates the state of the A/C switch.
BLOWER FAN (ON/OFF)
This parameter indicates the state of the blower fan
motor switch.
ELECTRIC LOAD (ON/OFF)
ON: Headlight or small light ON signal inputted.
OFF: Above electric loads all turned OFF.
RADIATOR COOLING FAN (RADIATOR COOLING
FAN CONTROL RELAY, ON/OFF)
ON: Command for radiator cooling fan control relay
operation being output.
OFF: Command for relay operation not being output.A/C COND FAN (A/C CONDENSER COOLING FAN
CONTROL RELAY, ON/OFF)
ON: Command for A/C condenser cooling fan control
relay operation being output.
OFF: Command for relay operation not being output.
TP SENSOR 1 VOLT (THROTTLE POSITION SENSOR
(MAIN) OUTPUT VOLTAGE, V)
The Throttle Position Sensor (Main) reading provides
throttle valve opening information in the form of voltage.
TP SENSOR 2 VOLT (THROTTLE POSITION SENSOR
(SUB) OUTPUT VOLTAGE, V)
The Throttle Position Sensor (Sub) reading provides
throttle valve opening information in the form of voltage.
APP SENSOR 1 VOLT (ACCELERATOR PEDAL
POSITION (APP) SENSOR (MAIN) OUTPUT
VOLTAGE, V)
The Accelerator Pedal Position (APP) Sensor (Main)
reading provides accelerator pedal opening information
in the form of voltage.
APP SENSOR 2 VOLT (ACCELERATOR PEDAL
POSITION (APP) SENSOR (SUB) OUTPUT VOLTAGE,
V)
The Accelerator Pedal Position (APP) Sensor (Sub)
reading provides accelerator pedal opening information
in the form of voltage.
ACCEL POSITION (RELATIVE ACCELERATOR
PEDAL POSITION, %)
When accelerator pedal is at fully released position,
accelerator pedal is indicated as 0 – 3% and 90 – 100%
fully depressed position.
TARGET THROTTLE POSI (TARGET THROTTLE
VALVE POSITION, %)
Target Throttle Valve Position is ECM internal parameter
which indicates the ECM requested throttle valve
position.
IAC THROTTLE OPENING (IDLE AIR (SPEED)
CONTROL THROTTLE VALVE OPENING, %)
This parameter indicates throttle valve opening of idle air
control in %.
(100% indicates the maximum idle air flow.)
THROTTLE MOTOR VOLT (V)
This parameter indicates power supply voltage of throttle
actuator (motor) control circuit (input voltage from
throttle actuator control relay).
CLOSED THROTTLE POS (CLOSED THROTTLE
POSITION, ON/OFF)
This parameter reads ON when throttle valve is fully
closed, or OFF when it is not fully closed.
Page 108 of 1556
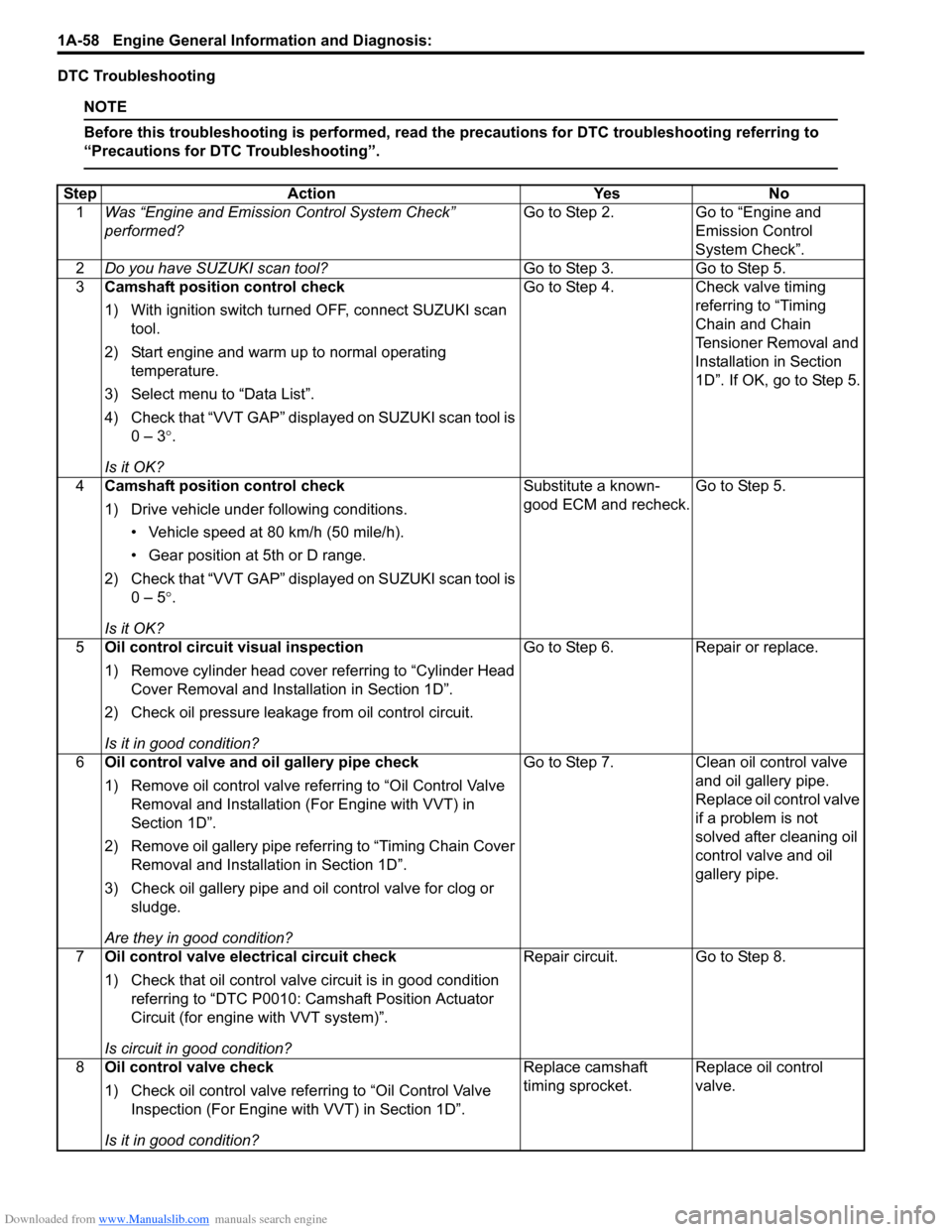
Downloaded from www.Manualslib.com manuals search engine 1A-58 Engine General Information and Diagnosis:
DTC Troubleshooting
NOTE
Before this troubleshooting is performed, read the precautions for DTC troubleshooting referring to
“Precautions for DTC Troubleshooting”.
Step Action Yes No
1Was “Engine and Emission Control System Check”
performed?Go to Step 2. Go to “Engine and
Emission Control
System Check”.
2Do you have SUZUKI scan tool?Go to Step 3. Go to Step 5.
3Camshaft position control check
1) With ignition switch turned OFF, connect SUZUKI scan
tool.
2) Start engine and warm up to normal operating
temperature.
3) Select menu to “Data List”.
4) Check that “VVT GAP” displayed on SUZUKI scan tool is
0 – 3°.
Is it OK?Go to Step 4. Check valve timing
referring to “Timing
Chain and Chain
Tensioner Removal and
Installation in Section
1D”. If OK, go to Step 5.
4Camshaft position control check
1) Drive vehicle under following conditions.
• Vehicle speed at 80 km/h (50 mile/h).
• Gear position at 5th or D range.
2) Check that “VVT GAP” displayed on SUZUKI scan tool is
0 – 5°.
Is it OK?Substitute a known-
good ECM and recheck.Go to Step 5.
5Oil control circuit visual inspection
1) Remove cylinder head cover referring to “Cylinder Head
Cover Removal and Installation in Section 1D”.
2) Check oil pressure leakage from oil control circuit.
Is it in good condition?Go to Step 6. Repair or replace.
6Oil control valve and oil gallery pipe check
1) Remove oil control valve referring to “Oil Control Valve
Removal and Installation (For Engine with VVT) in
Section 1D”.
2) Remove oil gallery pipe referring to “Timing Chain Cover
Removal and Installation in Section 1D”.
3) Check oil gallery pipe and oil control valve for clog or
sludge.
Are they in good condition?Go to Step 7. Clean oil control valve
and oil gallery pipe.
Replace oil control valve
if a problem is not
solved after cleaning oil
control valve and oil
gallery pipe.
7Oil control valve electrical circuit check
1) Check that oil control valve circuit is in good condition
referring to “DTC P0010: Camshaft Position Actuator
Circuit (for engine with VVT system)”.
Is circuit in good condition?Repair circuit. Go to Step 8.
8Oil control valve check
1) Check oil control valve referring to “Oil Control Valve
Inspection (For Engine with VVT) in Section 1D”.
Is it in good condition?Replace camshaft
timing sprocket.Replace oil control
valve.
Page 116 of 1556
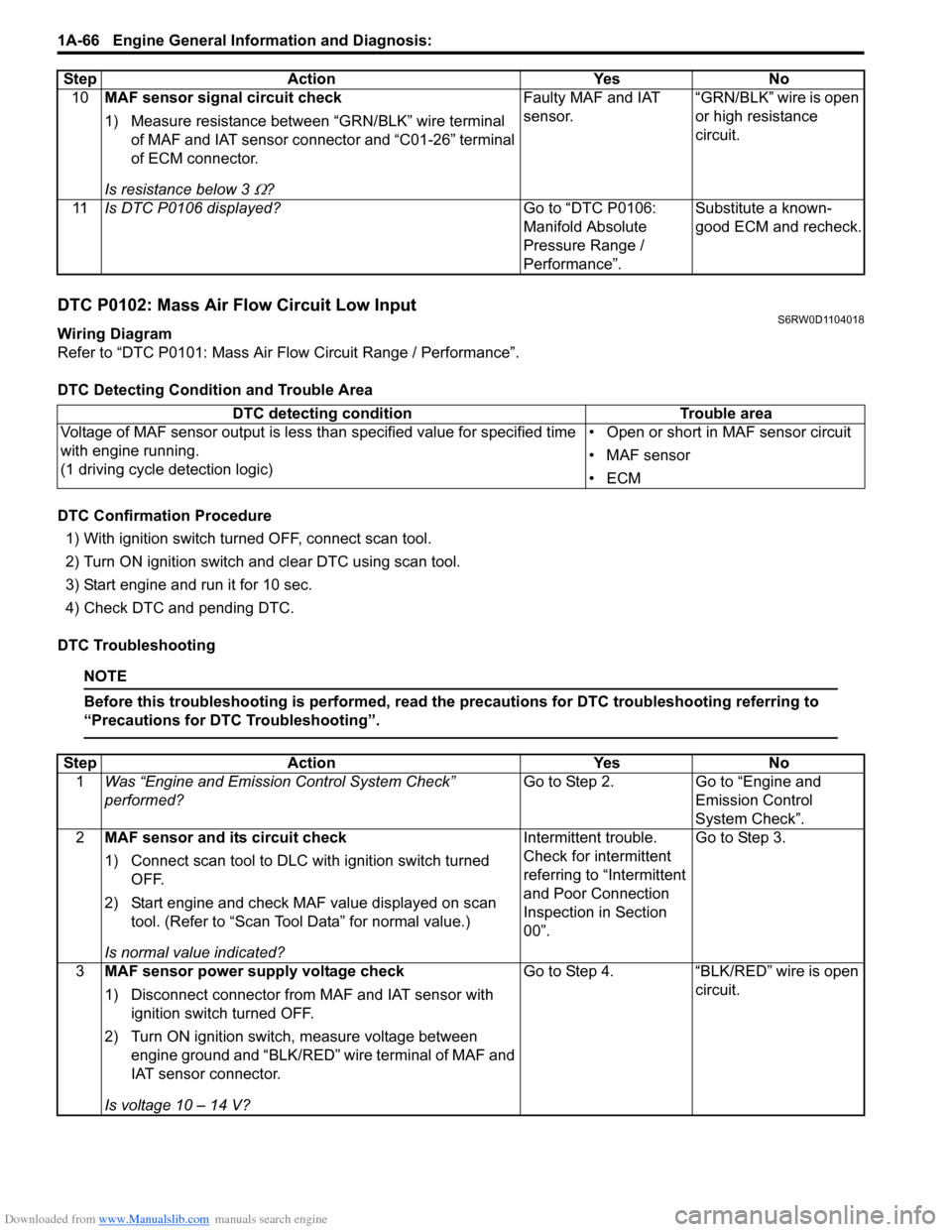
Downloaded from www.Manualslib.com manuals search engine 1A-66 Engine General Information and Diagnosis:
DTC P0102: Mass Air Flow Circuit Low InputS6RW0D1104018
Wiring Diagram
Refer to “DTC P0101: Mass Air Flow Circuit Range / Performance”.
DTC Detecting Condition and Trouble Area
DTC Confirmation Procedure
1) With ignition switch turned OFF, connect scan tool.
2) Turn ON ignition switch and clear DTC using scan tool.
3) Start engine and run it for 10 sec.
4) Check DTC and pending DTC.
DTC Troubleshooting
NOTE
Before this troubleshooting is performed, read the precautions for DTC troubleshooting referring to
“Precautions for DTC Troubleshooting”.
10MAF sensor signal circuit check
1) Measure resistance between “GRN/BLK” wire terminal
of MAF and IAT sensor connector and “C01-26” terminal
of ECM connector.
Is resistance below 3
Ω?Faulty MAF and IAT
sensor.“GRN/BLK” wire is open
or high resistance
circuit.
11Is DTC P0106 displayed?Go to “DTC P0106:
Manifold Absolute
Pressure Range /
Performance”.Substitute a known-
good ECM and recheck. Step Action Yes No
DTC detecting condition Trouble area
Voltage of MAF sensor output is less than specified value for specified time
with engine running.
(1 driving cycle detection logic)• Open or short in MAF sensor circuit
• MAF sensor
•ECM
Step Action Yes No
1Was “Engine and Emission Control System Check”
performed?Go to Step 2. Go to “Engine and
Emission Control
System Check”.
2MAF sensor and its circuit check
1) Connect scan tool to DLC with ignition switch turned
OFF.
2) Start engine and check MAF value displayed on scan
tool. (Refer to “Scan Tool Data” for normal value.)
Is normal value indicated?Intermittent trouble.
Check for intermittent
referring to “Intermittent
and Poor Connection
Inspection in Section
00”.Go to Step 3.
3MAF sensor power supply voltage check
1) Disconnect connector from MAF and IAT sensor with
ignition switch turned OFF.
2) Turn ON ignition switch, measure voltage between
engine ground and “BLK/RED” wire terminal of MAF and
IAT sensor connector.
Is voltage 10 – 14 V?Go to Step 4. “BLK/RED” wire is open
circuit.