YAMAHA WR 450F 2010 Owners Manual
Manufacturer: YAMAHA, Model Year: 2010, Model line: WR 450F, Model: YAMAHA WR 450F 2010Pages: 230, PDF Size: 13.87 MB
Page 131 of 230
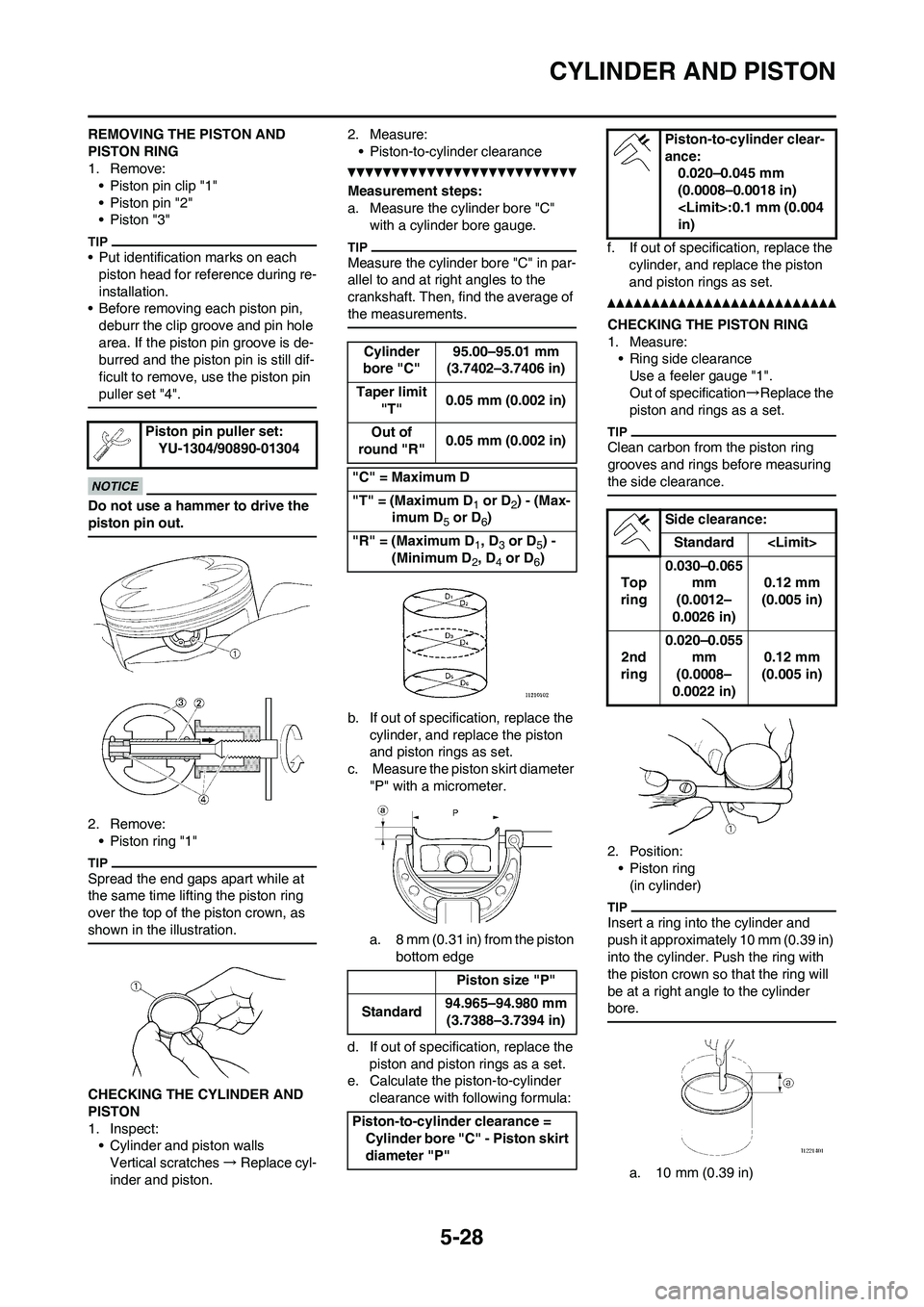
5-28
CYLINDER AND PISTON
REMOVING THE PISTON AND
PISTON RING
1. Remove:
• Piston pin clip "1"
• Piston pin "2"
• Piston "3"
• Put identification marks on each
piston head for reference during re-
installation.
• Before removing each piston pin,
deburr the clip groove and pin hole
area. If the piston pin groove is de-
burred and the piston pin is still dif-
ficult to remove, use the piston pin
puller set "4".
Do not use a hammer to drive the
piston pin out.
2. Remove:
• Piston ring "1"
Spread the end gaps apart while at
the same time lifting the piston ring
over the top of the piston crown, as
shown in the illustration.
CHECKING THE CYLINDER AND
PISTON
1. Inspect:
• Cylinder and piston walls
Vertical scratches→Replace cyl-
inder and piston.2. Measure:
• Piston-to-cylinder clearance
Measurement steps:
a. Measure the cylinder bore "C"
with a cylinder bore gauge.
Measure the cylinder bore "C" in par-
allel to and at right angles to the
crankshaft. Then, find the average of
the measurements.
b. If out of specification, replace the
cylinder, and replace the piston
and piston rings as set.
c. Measure the piston skirt diameter
"P" with a micrometer.
a. 8 mm (0.31 in) from the piston
bottom edge
d. If out of specification, replace the
piston and piston rings as a set.
e. Calculate the piston-to-cylinder
clearance with following formula:f. If out of specification, replace the
cylinder, and replace the piston
and piston rings as set.
CHECKING THE PISTON RING
1. Measure:
• Ring side clearance
Use a feeler gauge "1".
Out of specification→Replace the
piston and rings as a set.
Clean carbon from the piston ring
grooves and rings before measuring
the side clearance.
2. Position:
• Piston ring
(in cylinder)
Insert a ring into the cylinder and
push it approximately 10 mm (0.39 in)
into the cylinder. Push the ring with
the piston crown so that the ring will
be at a right angle to the cylinder
bore.
a. 10 mm (0.39 in) Piston pin puller set:
YU-1304/90890-01304
Cylinder
bore "C"95.00–95.01 mm
(3.7402–3.7406 in)
Taper limit
"T"0.05 mm (0.002 in)
Out of
round "R"0.05 mm (0.002 in)
"C" = Maximum D
"T" = (Maximum D
1 or D2) - (Max-
imum D
5 or D6)
"R" = (Maximum D
1, D3 or D5) -
(Minimum D
2, D4 or D6)
Piston size "P"
Standard94.965–94.980 mm
(3.7388–3.7394 in)
Piston-to-cylinder clearance =
Cylinder bore "C" - Piston skirt
diameter "P"
Piston-to-cylinder clear-
ance:
0.020–0.045 mm
(0.0008–0.0018 in)
in)
Side clearance:
Standard
Top
ring0.030–0.065
mm
(0.0012–
0.0026 in)0.12 mm
(0.005 in)
2nd
ring0.020–0.055
mm
(0.0008–
0.0022 in)0.12 mm
(0.005 in)
Page 132 of 230
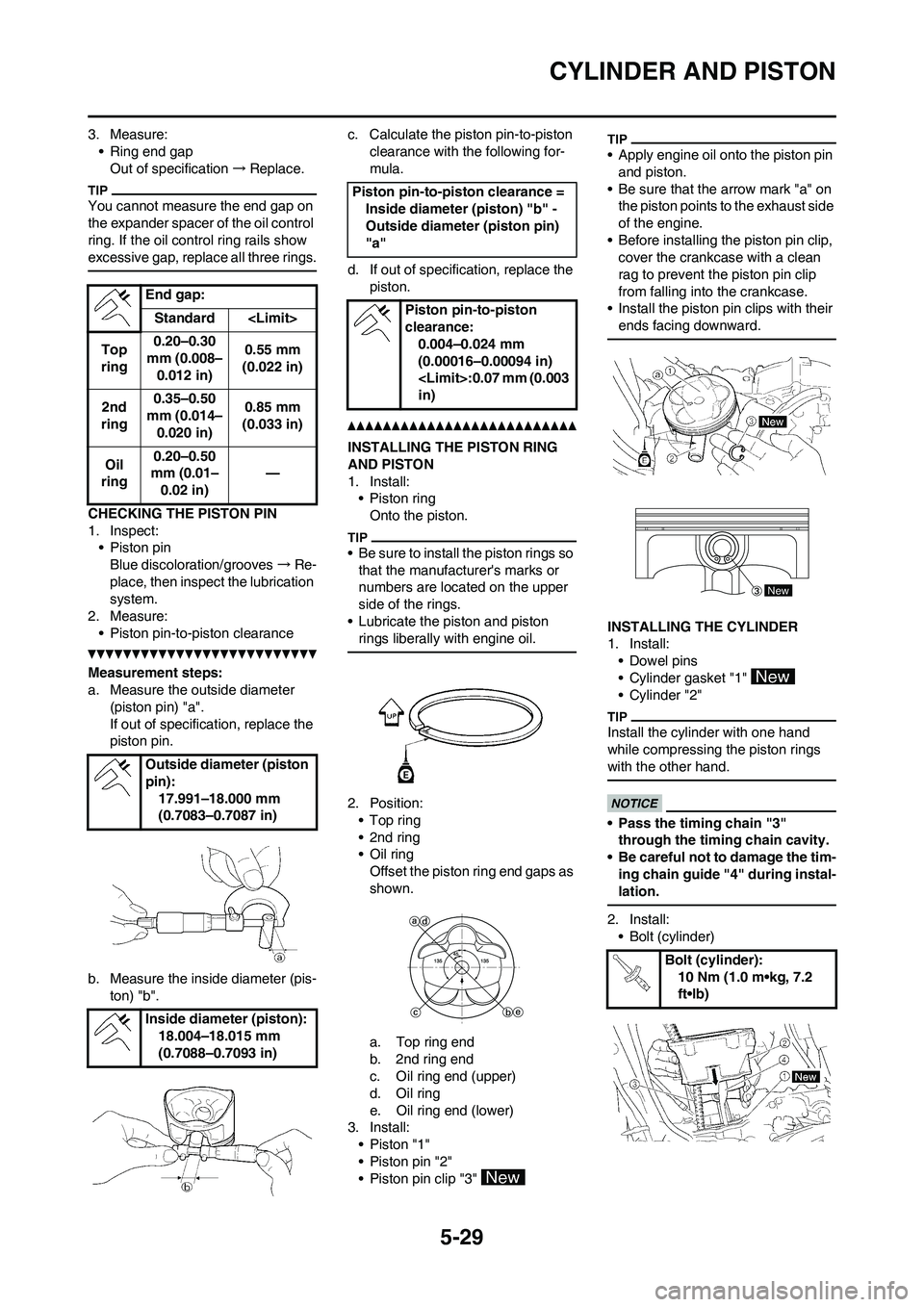
5-29
CYLINDER AND PISTON
3. Measure:
• Ring end gap
Out of specification→Replace.
You cannot measure the end gap on
the expander spacer of the oil control
ring. If the oil control ring rails show
excessive gap, replace all three rings.
CHECKING THE PISTON PIN
1. Inspect:
• Piston pin
Blue discoloration/grooves→Re-
place, then inspect the lubrication
system.
2. Measure:
• Piston pin-to-piston clearance
Measurement steps:
a. Measure the outside diameter
(piston pin) "a".
If out of specification, replace the
piston pin.
b. Measure the inside diameter (pis-
ton) "b".c. Calculate the piston pin-to-piston
clearance with the following for-
mula.
d. If out of specification, replace the
piston.
INSTALLING THE PISTON RING
AND PISTON
1. Install:
•Piston ring
Onto the piston.
• Be sure to install the piston rings so
that the manufacturer's marks or
numbers are located on the upper
side of the rings.
• Lubricate the piston and piston
rings liberally with engine oil.
2. Position:
•Top ring
• 2nd ring
• Oil ring
Offset the piston ring end gaps as
shown.
a. Top ring end
b. 2nd ring end
c. Oil ring end (upper)
d. Oil ring
e. Oil ring end (lower)
3. Install:
•Piston "1"
• Piston pin "2"
• Piston pin clip "3"
• Apply engine oil onto the piston pin
and piston.
• Be sure that the arrow mark "a" on
the piston points to the exhaust side
of the engine.
• Before installing the piston pin clip,
cover the crankcase with a clean
rag to prevent the piston pin clip
from falling into the crankcase.
• Install the piston pin clips with their
ends facing downward.
INSTALLING THE CYLINDER
1. Install:
• Dowel pins
• Cylinder gasket "1"
• Cylinder "2"
Install the cylinder with one hand
while compressing the piston rings
with the other hand.
• Pass the timing chain "3"
through the timing chain cavity.
• Be careful not to damage the tim-
ing chain guide "4" during instal-
lation.
2. Install:
• Bolt (cylinder) End gap:
Standard
Top
ring0.20–0.30
mm (0.008–
0.012 in)0.55 mm
(0.022 in)
2nd
ring0.35–0.50
mm (0.014–
0.020 in)0.85 mm
(0.033 in)
Oil
ring0.20–0.50
mm (0.01–
0.02 in)—
Outside diameter (piston
pin):
17.991–18.000 mm
(0.7083–0.7087 in)
Inside diameter (piston):
18.004–18.015 mm
(0.7088–0.7093 in)
Piston pin-to-piston clearance =
Inside diameter (piston) "b" -
Outside diameter (piston pin)
"a"
Piston pin-to-piston
clearance:
0.004–0.024 mm
(0.00016–0.00094 in)
in)
Bolt (cylinder):
10 Nm (1.0 m•kg, 7.2
ft•lb)
New
Page 133 of 230
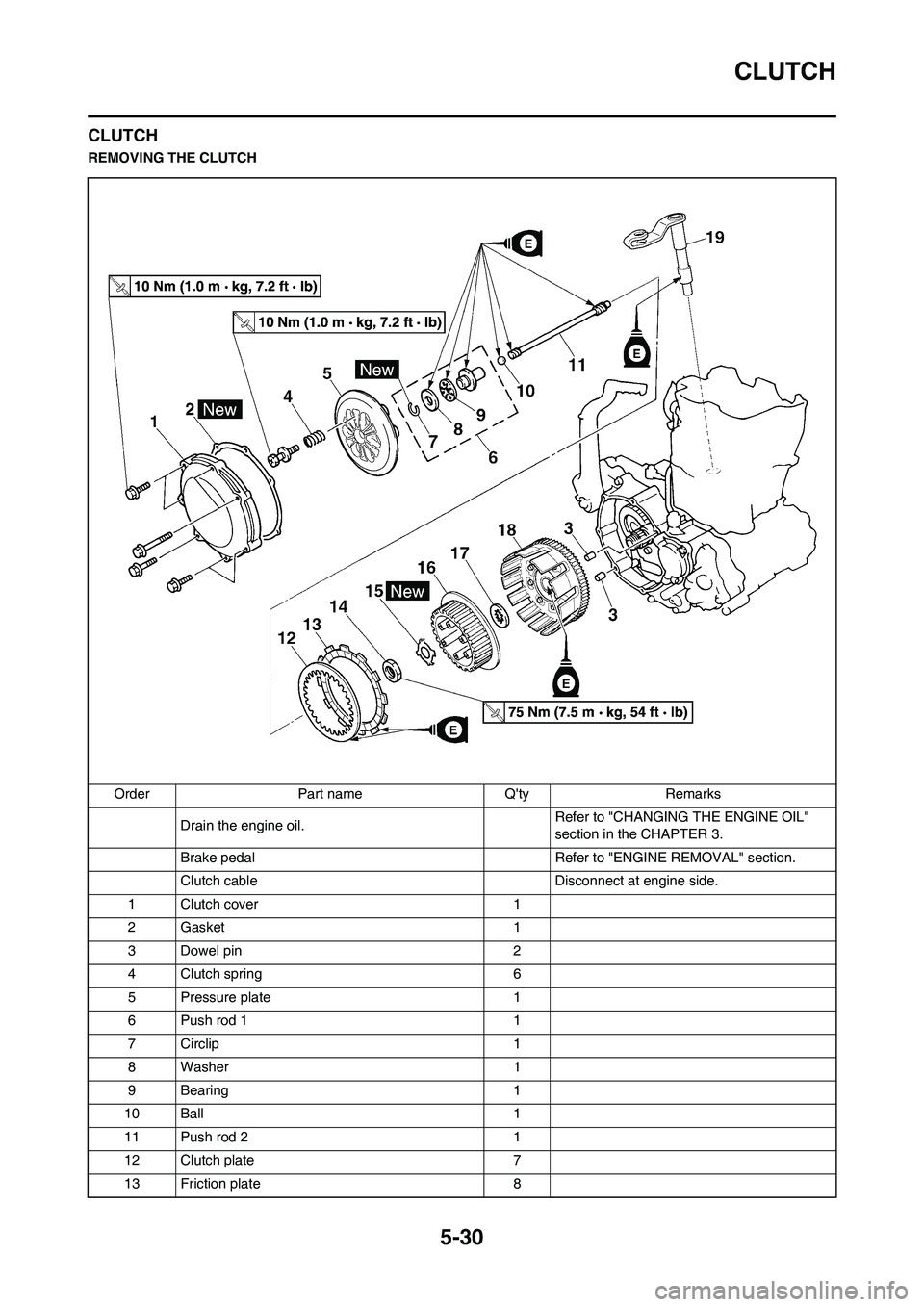
5-30
CLUTCH
CLUTCH
REMOVING THE CLUTCH
Order Part name Q'ty Remarks
Drain the engine oil. Refer to "CHANGING THE ENGINE OIL"
section in the CHAPTER 3.
Brake pedal Refer to "ENGINE REMOVAL" section.
Clutch cable Disconnect at engine side.
1 Clutch cover 1
2 Gasket 1
3 Dowel pin 2
4 Clutch spring 6
5 Pressure plate 1
6 Push rod 1 1
7 Circlip 1
8 Washer 1
9 Bearing 1
10 Ball 1
11 Push rod 2 1
12 Clutch plate 7
13 Friction plate 8
Page 134 of 230
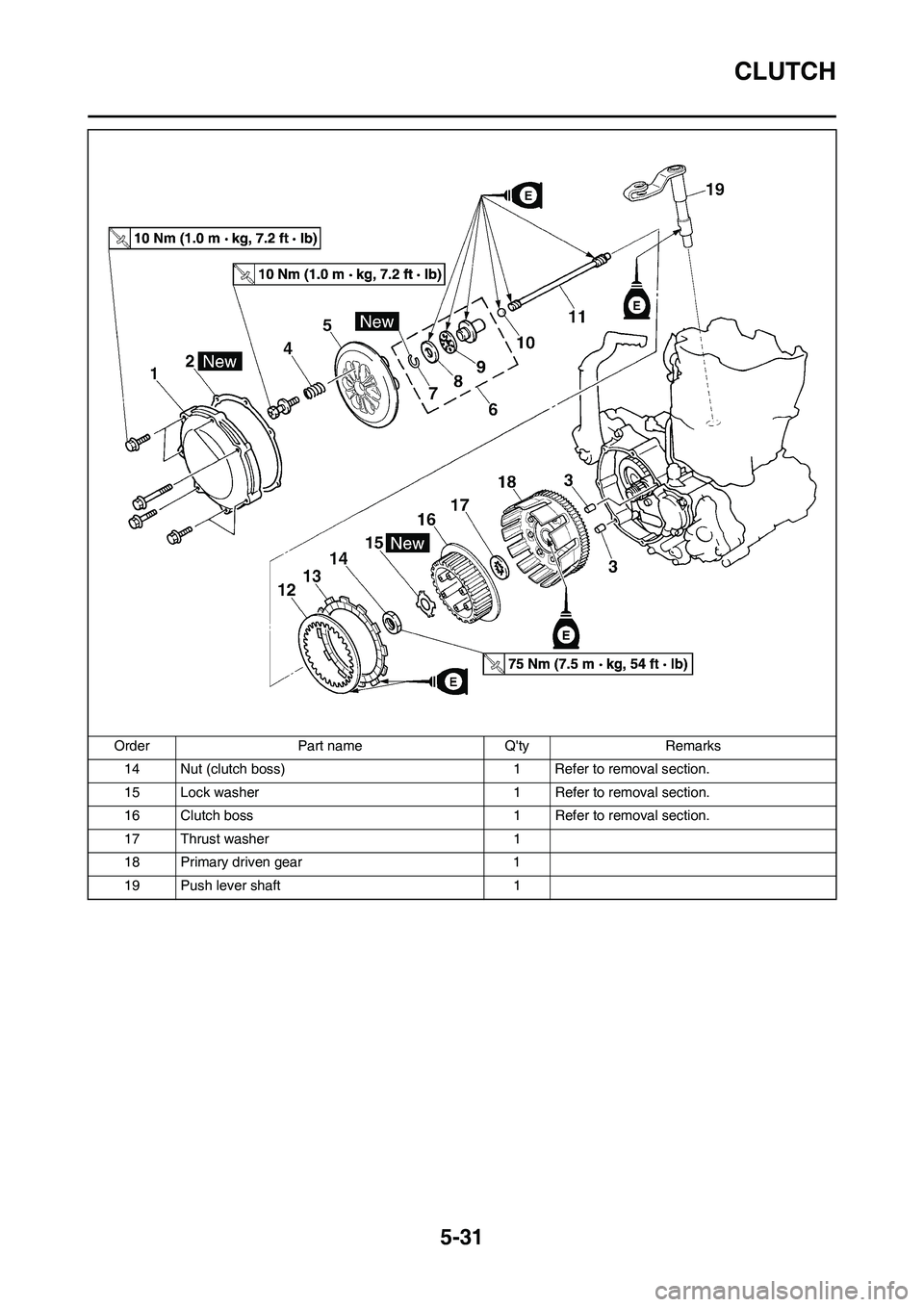
5-31
CLUTCH
14 Nut (clutch boss) 1 Refer to removal section.
15 Lock washer 1 Refer to removal section.
16 Clutch boss 1 Refer to removal section.
17 Thrust washer 1
18 Primary driven gear 1
19 Push lever shaft 1 Order Part name Q'ty Remarks
Page 135 of 230
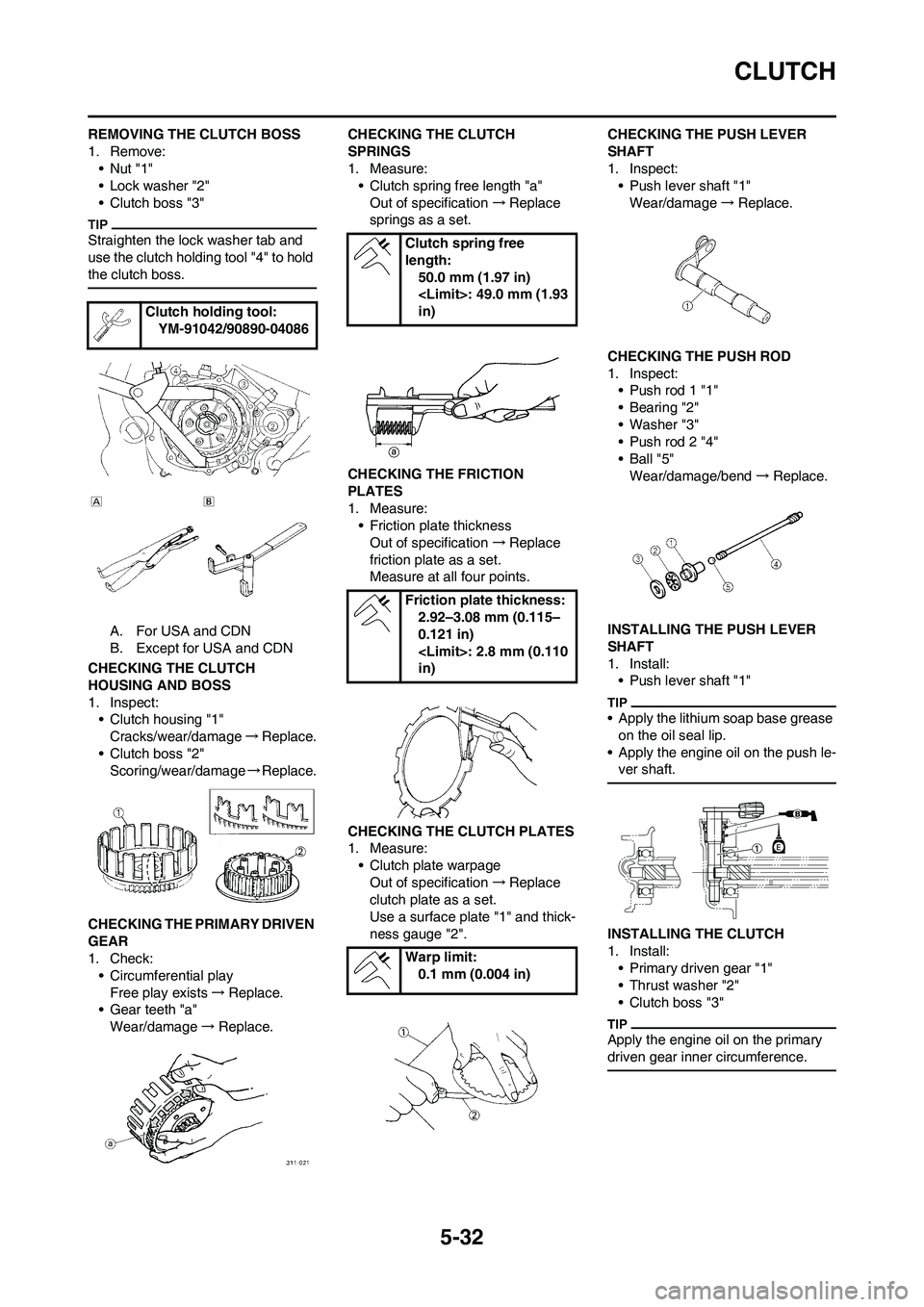
5-32
CLUTCH
REMOVING THE CLUTCH BOSS
1. Remove:
•Nut "1"
• Lock washer "2"
• Clutch boss "3"
Straighten the lock washer tab and
use the clutch holding tool "4" to hold
the clutch boss.
A. For USA and CDN
B. Except for USA and CDN
CHECKING THE CLUTCH
HOUSING AND BOSS
1. Inspect:
• Clutch housing "1"
Cracks/wear/damage→Replace.
• Clutch boss "2"
Scoring/wear/damage→Replace.
CHECKING THE PRIMARY DRIVEN
GEAR
1. Check:
• Circumferential play
Free play exists→Replace.
• Gear teeth "a"
Wear/damage→Replace.CHECKING THE CLUTCH
SPRINGS
1. Measure:
• Clutch spring free length "a"
Out of specification→Replace
springs as a set.
CHECKING THE FRICTION
PLATES
1. Measure:
• Friction plate thickness
Out of specification→Replace
friction plate as a set.
Measure at all four points.
CHECKING THE CLUTCH PLATES
1. Measure:
• Clutch plate warpage
Out of specification→Replace
clutch plate as a set.
Use a surface plate "1" and thick-
ness gauge "2".CHECKING THE PUSH LEVER
SHAFT
1. Inspect:
• Push lever shaft "1"
Wear/damage→Replace.
CHECKING THE PUSH ROD
1. Inspect:
• Push rod 1 "1"
• Bearing "2"
• Washer "3"
• Push rod 2 "4"
•Ball "5"
Wear/damage/bend→Replace.
INSTALLING THE PUSH LEVER
SHAFT
1. Install:
• Push lever shaft "1"
• Apply the lithium soap base grease
on the oil seal lip.
• Apply the engine oil on the push le-
ver shaft.
INSTALLING THE CLUTCH
1. Install:
• Primary driven gear "1"
• Thrust washer "2"
• Clutch boss "3"
Apply the engine oil on the primary
driven gear inner circumference.
Clutch holding tool:
YM-91042/90890-04086
Clutch spring free
length:
50.0 mm (1.97 in)
in)
Friction plate thickness:
2.92–3.08 mm (0.115–
0.121 in)
in)
Warp limit:
0.1 mm (0.004 in)
Page 136 of 230
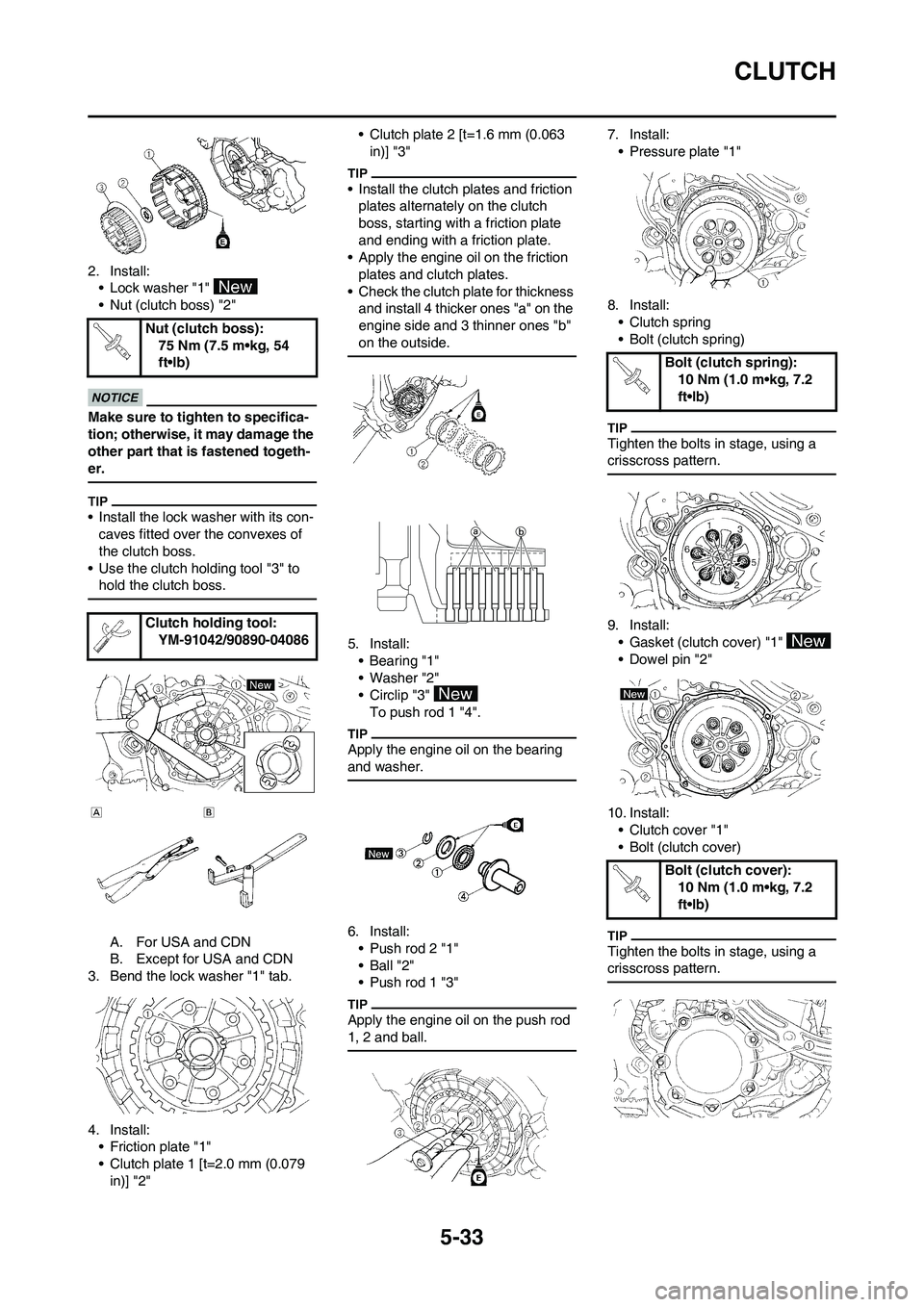
5-33
CLUTCH
2. Install:
• Lock washer "1"
• Nut (clutch boss) "2"
Make sure to tighten to specifica-
tion; otherwise, it may damage the
other part that is fastened togeth-
er.
• Install the lock washer with its con-
caves fitted over the convexes of
the clutch boss.
• Use the clutch holding tool "3" to
hold the clutch boss.
A. For USA and CDN
B. Except for USA and CDN
3. Bend the lock washer "1" tab.
4. Install:
• Friction plate "1"
• Clutch plate 1 [t=2.0 mm (0.079
in)] "2"• Clutch plate 2 [t=1.6 mm (0.063
in)] "3"
• Install the clutch plates and friction
plates alternately on the clutch
boss, starting with a friction plate
and ending with a friction plate.
• Apply the engine oil on the friction
plates and clutch plates.
• Check the clutch plate for thickness
and install 4 thicker ones "a" on the
engine side and 3 thinner ones "b"
on the outside.
5. Install:
•Bearing "1"
• Washer "2"
• Circlip "3"
To push rod 1 "4".
Apply the engine oil on the bearing
and washer.
6. Install:
• Push rod 2 "1"
• Ball "2"
• Push rod 1 "3"
Apply the engine oil on the push rod
1, 2 and ball.
7. Install:
• Pressure plate "1"
8. Install:
• Clutch spring
• Bolt (clutch spring)
Tighten the bolts in stage, using a
crisscross pattern.
9. Install:
• Gasket (clutch cover) "1"
• Dowel pin "2"
10. Install:
• Clutch cover "1"
• Bolt (clutch cover)
Tighten the bolts in stage, using a
crisscross pattern.
Nut (clutch boss):
75 Nm (7.5 m•kg, 54
ft•lb)
Clutch holding tool:
YM-91042/90890-04086
Bolt (clutch spring):
10 Nm (1.0 m•kg, 7.2
ft•lb)
Bolt (clutch cover):
10 Nm (1.0 m•kg, 7.2
ft•lb)
Page 137 of 230
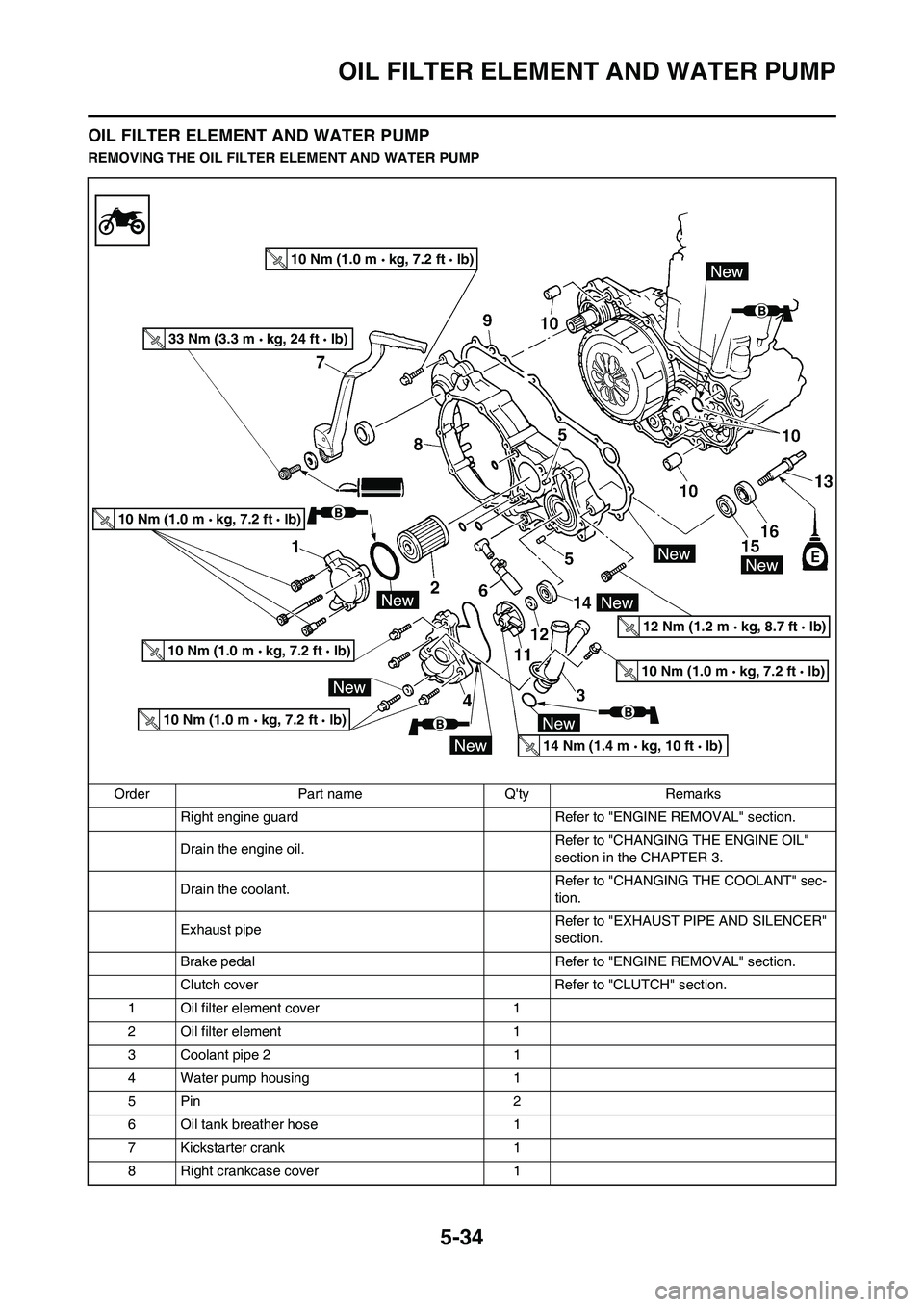
5-34
OIL FILTER ELEMENT AND WATER PUMP
OIL FILTER ELEMENT AND WATER PUMP
REMOVING THE OIL FILTER ELEMENT AND WATER PUMP
Order Part name Q'ty Remarks
Right engine guard Refer to "ENGINE REMOVAL" section.
Drain the engine oil. Refer to "CHANGING THE ENGINE OIL"
section in the CHAPTER 3.
Drain the coolant. Refer to "CHANGING THE COOLANT" sec-
tion.
Exhaust pipe Refer to "EXHAUST PIPE AND SILENCER"
section.
Brake pedal Refer to "ENGINE REMOVAL" section.
Clutch cover Refer to "CLUTCH" section.
1 Oil filter element cover 1
2 Oil filter element 1
3 Coolant pipe 2 1
4 Water pump housing 1
5Pin 2
6 Oil tank breather hose 1
7 Kickstarter crank 1
8 Right crankcase cover 1
10 Nm (1.0 m kg, 7.2 ft lb)
10 Nm (1.0 m kg, 7.2 ft lb)
10 Nm (1.0 m kg, 7.2 ft lb)
10 Nm (1.0 m kg, 7.2 ft lb)
10 Nm (1.0 m kg, 7.2 ft lb)
33 Nm (3.3 m kg, 24 ft lb)
14 Nm (1.4 m kg, 10 ft lb)
12 Nm (1.2 m kg, 8.7 ft lb)
Page 138 of 230
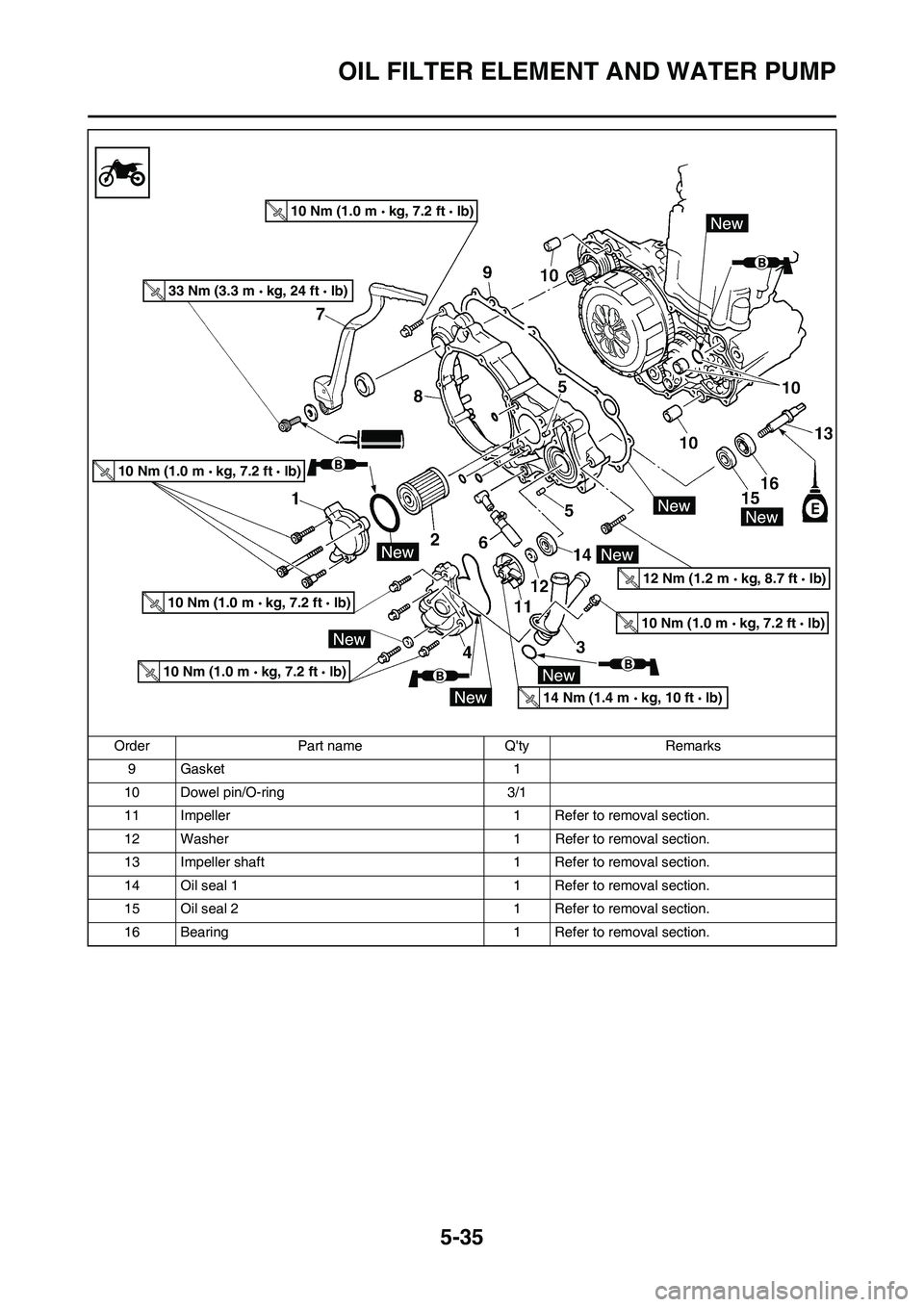
5-35
OIL FILTER ELEMENT AND WATER PUMP
9 Gasket 1
10 Dowel pin/O-ring 3/1
11 Impeller 1 Refer to removal section.
12 Washer 1 Refer to removal section.
13 Impeller shaft 1 Refer to removal section.
14 Oil seal 1 1 Refer to removal section.
15 Oil seal 2 1 Refer to removal section.
16 Bearing 1 Refer to removal section. Order Part name Q'ty Remarks
10 Nm (1.0 m kg, 7.2 ft lb)
10 Nm (1.0 m kg, 7.2 ft lb)
10 Nm (1.0 m kg, 7.2 ft lb)
10 Nm (1.0 m kg, 7.2 ft lb)
10 Nm (1.0 m kg, 7.2 ft lb)
33 Nm (3.3 m kg, 24 ft lb)
14 Nm (1.4 m kg, 10 ft lb)
12 Nm (1.2 m kg, 8.7 ft lb)
Page 139 of 230
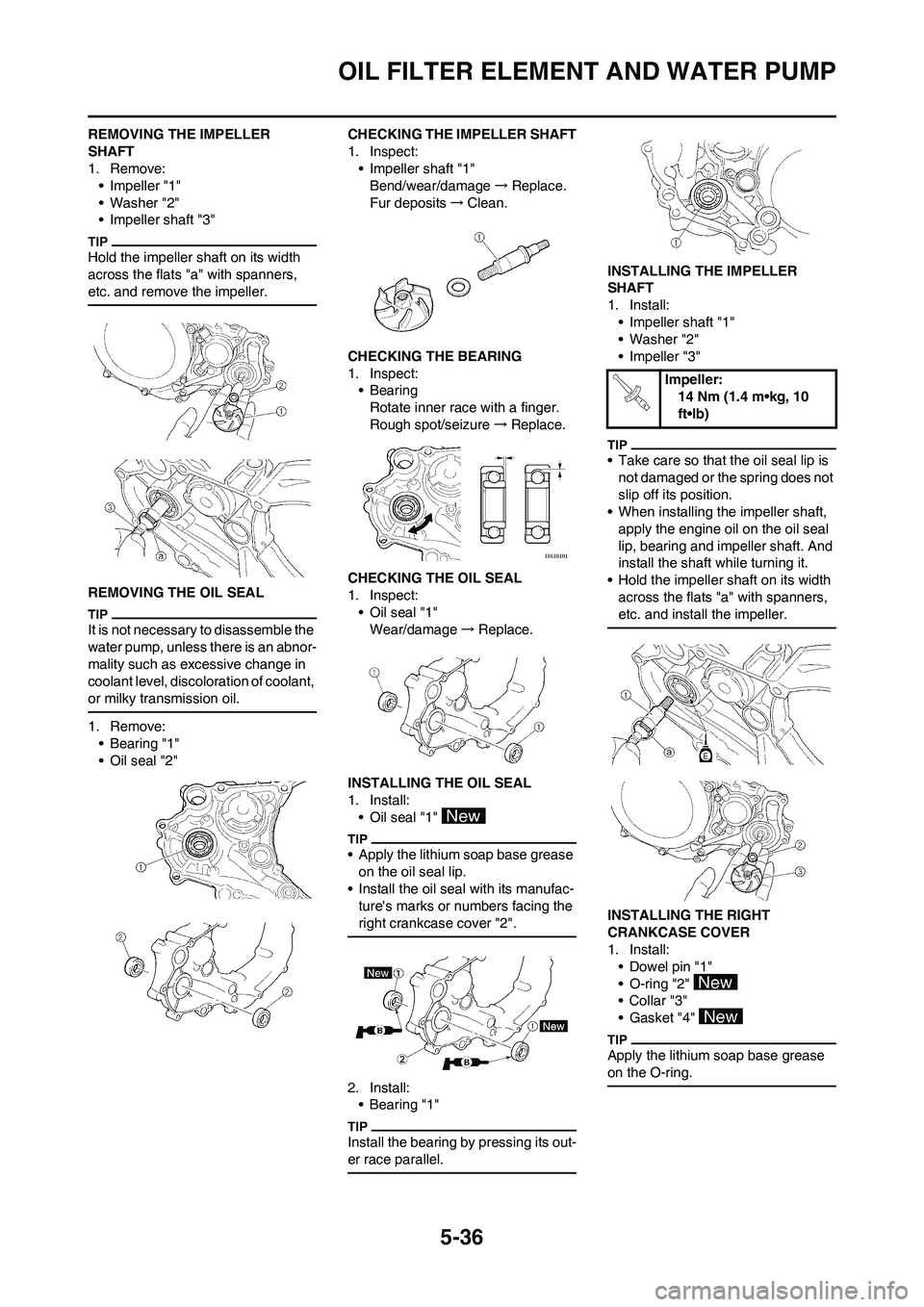
5-36
OIL FILTER ELEMENT AND WATER PUMP
REMOVING THE IMPELLER
SHAFT
1. Remove:
• Impeller "1"
• Washer "2"
• Impeller shaft "3"
Hold the impeller shaft on its width
across the flats "a" with spanners,
etc. and remove the impeller.
REMOVING THE OIL SEAL
It is not necessary to disassemble the
water pump, unless there is an abnor-
mality such as excessive change in
coolant level, discoloration of coolant,
or milky transmission oil.
1. Remove:
• Bearing "1"
• Oil seal "2"CHECKING THE IMPELLER SHAFT
1. Inspect:
• Impeller shaft "1"
Bend/wear/damage→Replace.
Fur deposits→Clean.
CHECKING THE BEARING
1. Inspect:
•Bearing
Rotate inner race with a finger.
Rough spot/seizure→Replace.
CHECKING THE OIL SEAL
1. Inspect:
• Oil seal "1"
Wear/damage→Replace.
INSTALLING THE OIL SEAL
1. Install:
• Oil seal "1"
• Apply the lithium soap base grease
on the oil seal lip.
• Install the oil seal with its manufac-
ture's marks or numbers facing the
right crankcase cover "2".
2. Install:
•Bearing "1"
Install the bearing by pressing its out-
er race parallel.
INSTALLING THE IMPELLER
SHAFT
1. Install:
• Impeller shaft "1"
• Washer "2"
• Impeller "3"
• Take care so that the oil seal lip is
not damaged or the spring does not
slip off its position.
• When installing the impeller shaft,
apply the engine oil on the oil seal
lip, bearing and impeller shaft. And
install the shaft while turning it.
• Hold the impeller shaft on its width
across the flats "a" with spanners,
etc. and install the impeller.
INSTALLING THE RIGHT
CRANKCASE COVER
1. Install:
• Dowel pin "1"
• O-ring "2"
•Collar "3"
• Gasket "4"
Apply the lithium soap base grease
on the O-ring.
Impeller:
14 Nm (1.4 m•kg, 10
ft•lb)
Page 140 of 230
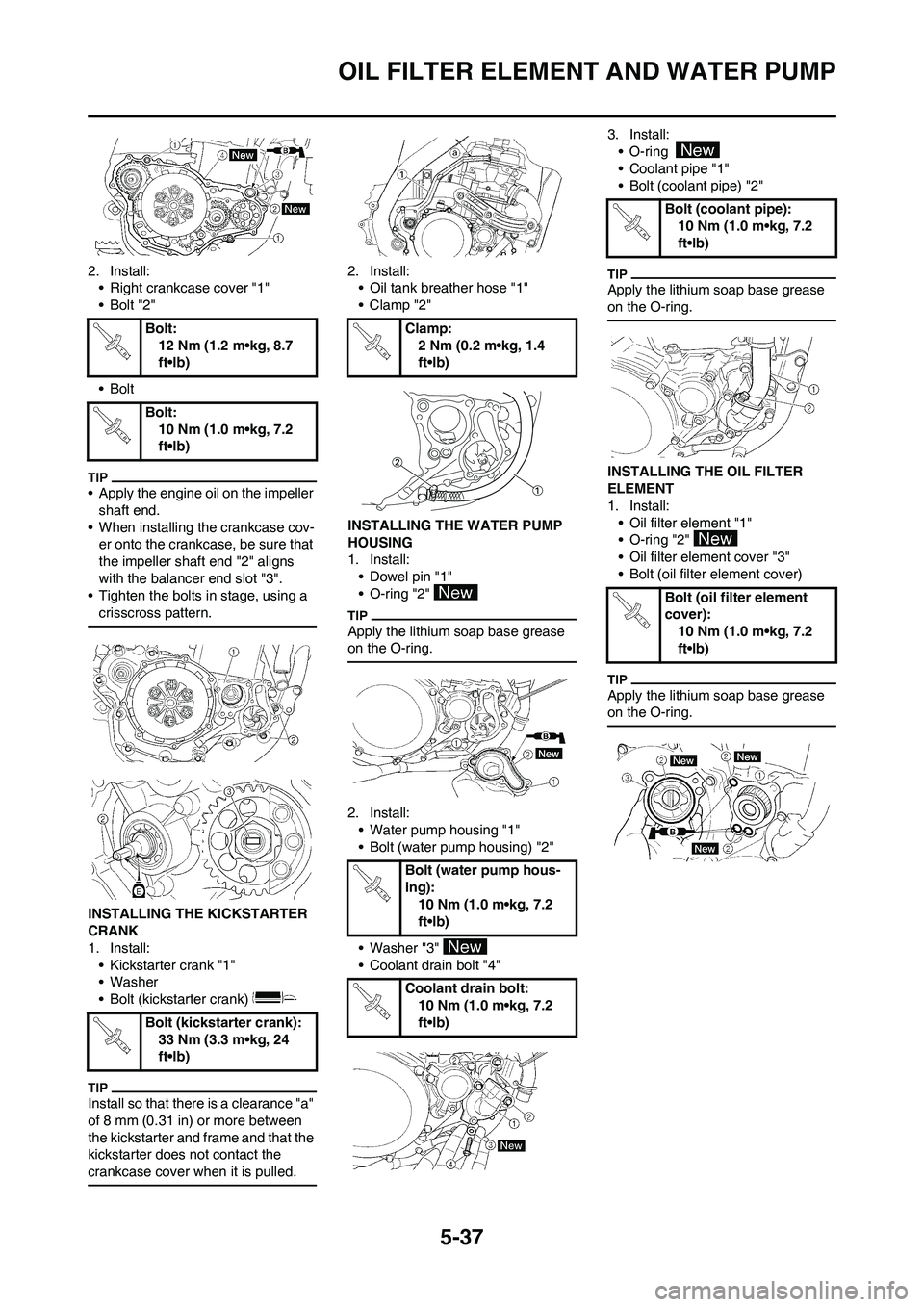
5-37
OIL FILTER ELEMENT AND WATER PUMP
2. Install:
• Right crankcase cover "1"
•Bolt "2"
•Bolt
• Apply the engine oil on the impeller
shaft end.
• When installing the crankcase cov-
er onto the crankcase, be sure that
the impeller shaft end "2" aligns
with the balancer end slot "3".
• Tighten the bolts in stage, using a
crisscross pattern.
INSTALLING THE KICKSTARTER
CRANK
1. Install:
• Kickstarter crank "1"
• Washer
• Bolt (kickstarter crank)
Install so that there is a clearance "a"
of 8 mm (0.31 in) or more between
the kickstarter and frame and that the
kickstarter does not contact the
crankcase cover when it is pulled.
2. Install:
• Oil tank breather hose "1"
•Clamp "2"
INSTALLING THE WATER PUMP
HOUSING
1. Install:
• Dowel pin "1"
• O-ring "2"
Apply the lithium soap base grease
on the O-ring.
2. Install:
• Water pump housing "1"
• Bolt (water pump housing) "2"
• Washer "3"
• Coolant drain bolt "4"3. Install:
• O-ring
• Coolant pipe "1"
• Bolt (coolant pipe) "2"
Apply the lithium soap base grease
on the O-ring.
INSTALLING THE OIL FILTER
ELEMENT
1. Install:
• Oil filter element "1"
• O-ring "2"
• Oil filter element cover "3"
• Bolt (oil filter element cover)
Apply the lithium soap base grease
on the O-ring.
Bolt:
12 Nm (1.2 m•kg, 8.7
ft•lb)
Bolt:
10 Nm (1.0 m•kg, 7.2
ft•lb)
Bolt (kickstarter crank):
33 Nm (3.3 m•kg, 24
ft•lb)Clamp:
2 Nm (0.2 m•kg, 1.4
ft•lb)
Bolt (water pump hous-
ing):
10 Nm (1.0 m•kg, 7.2
ft•lb)
Coolant drain bolt:
10 Nm (1.0 m•kg, 7.2
ft•lb)
Bolt (coolant pipe):
10 Nm (1.0 m•kg, 7.2
ft•lb)
Bolt (oil filter element
cover):
10 Nm (1.0 m•kg, 7.2
ft•lb)