YAMAHA YZ250F 2015 Owners Manual
Manufacturer: YAMAHA, Model Year: 2015, Model line: YZ250F, Model: YAMAHA YZ250F 2015Pages: 356, PDF Size: 11.39 MB
Page 111 of 356
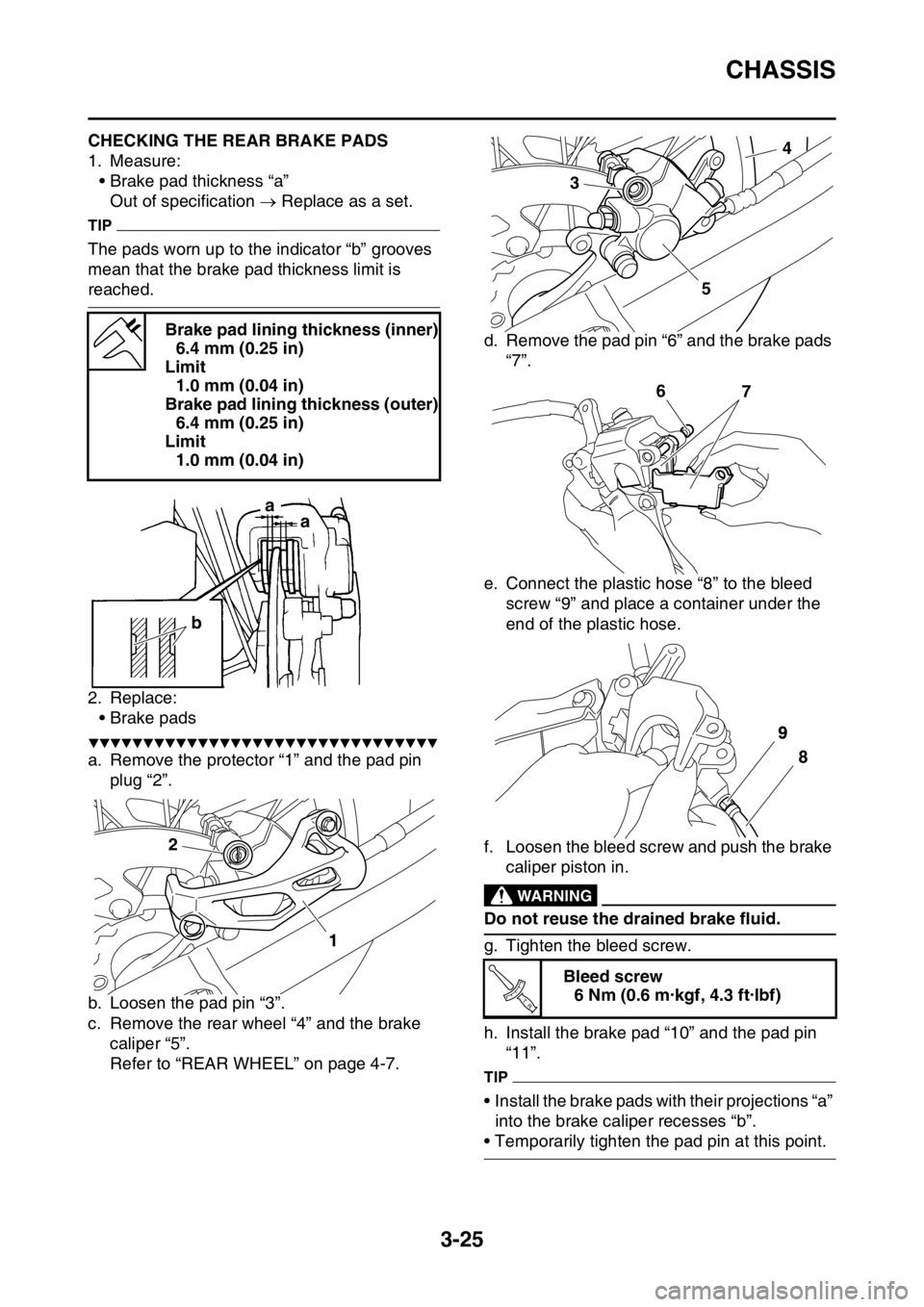
CHASSIS
3-25
EAS1SM5096CHECKING THE REAR BRAKE PADS
1. Measure:
• Brake pad thickness “a”
Out of specification Replace as a set.
TIP
The pads worn up to the indicator “b” grooves
mean that the brake pad thickness limit is
reached.
2. Replace:
• Brake pads
▼▼▼▼▼▼▼▼▼▼▼▼▼▼▼▼▼▼▼▼▼▼▼▼▼▼▼▼▼▼▼▼
a. Remove the protector “1” and the pad pin
plug “2”.
b. Loosen the pad pin “3”.
c. Remove the rear wheel “4” and the brake
caliper “5”.
Refer to “REAR WHEEL” on page 4-7.d. Remove the pad pin “6” and the brake pads
“7”.
e. Connect the plastic hose “8” to the bleed
screw “9” and place a container under the
end of the plastic hose.
f. Loosen the bleed screw and push the brake
caliper piston in.
EWA@
WARNING
Do not reuse the drained brake fluid.
g. Tighten the bleed screw.
h. Install the brake pad “10” and the pad pin
“11”.
TIP
• Install the brake pads with their projections “a”
into the brake caliper recesses “b”.
• Temporarily tighten the pad pin at this point. Brake pad lining thickness (inner)
6.4 mm (0.25 in)
Limit
1.0 mm (0.04 in)
Brake pad lining thickness (outer)
6.4 mm (0.25 in)
Limit
1.0 mm (0.04 in)
ba
a
1 2
Bleed screw
6 Nm (0.6 m·kgf, 4.3 ft·lbf)
34
5
7 6
9
8
T R..
Page 112 of 356
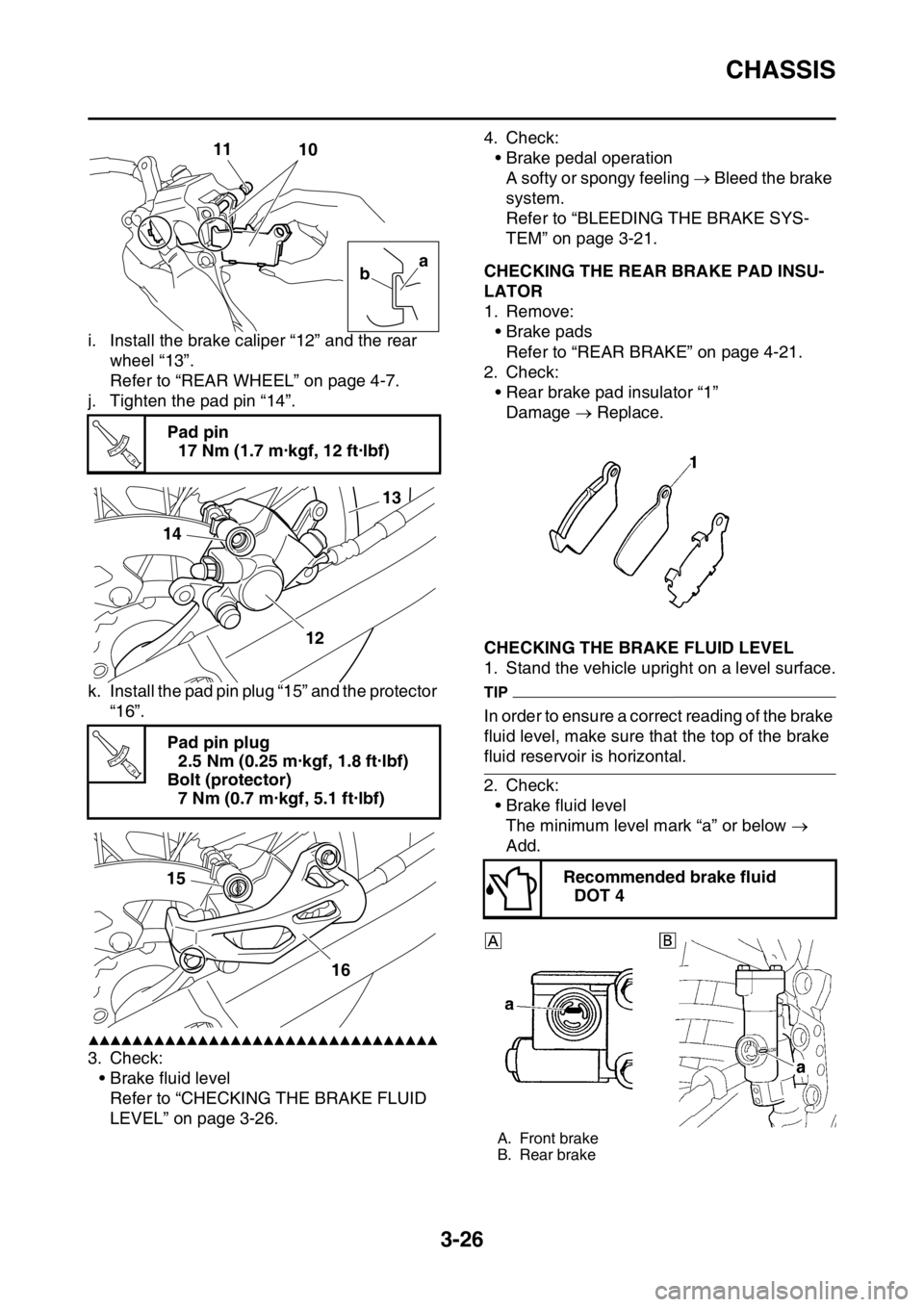
CHASSIS
3-26
i. Install the brake caliper “12” and the rear
wheel “13”.
Refer to “REAR WHEEL” on page 4-7.
j. Tighten the pad pin “14”.
k. Install the pad pin plug “15” and the protector
“16”.
▲▲▲▲▲▲▲▲▲▲▲▲▲▲▲▲▲▲▲▲▲▲▲▲▲▲▲▲▲▲▲▲
3. Check:
• Brake fluid level
Refer to “CHECKING THE BRAKE FLUID
LEVEL” on page 3-26.4. Check:
• Brake pedal operation
A softy or spongy feeling Bleed the brake
system.
Refer to “BLEEDING THE BRAKE SYS-
TEM” on page 3-21.
EAS1SM5097CHECKING THE REAR BRAKE PAD INSU-
LATOR
1. Remove:
• Brake pads
Refer to “REAR BRAKE” on page 4-21.
2. Check:
• Rear brake pad insulator “1”
Damage Replace.
EAS1SM5098CHECKING THE BRAKE FLUID LEVEL
1. Stand the vehicle upright on a level surface.
TIP
In order to ensure a correct reading of the brake
fluid level, make sure that the top of the brake
fluid reservoir is horizontal.
2. Check:
• Brake fluid level
The minimum level mark “a” or below
Add.
EWA13090
Pad pin
17 Nm (1.7 m·kgf, 12 ft·lbf)
Pad pin plug
2.5 Nm (0.25 m·kgf, 1.8 ft·lbf)
Bolt (protector)
7 Nm (0.7 m·kgf, 5.1 ft·lbf)
10 11
a
b
T R..
13
14
12
T R..
15
16Recommended brake fluid
DOT 4
A. Front brake
B. Rear brake
Page 113 of 356
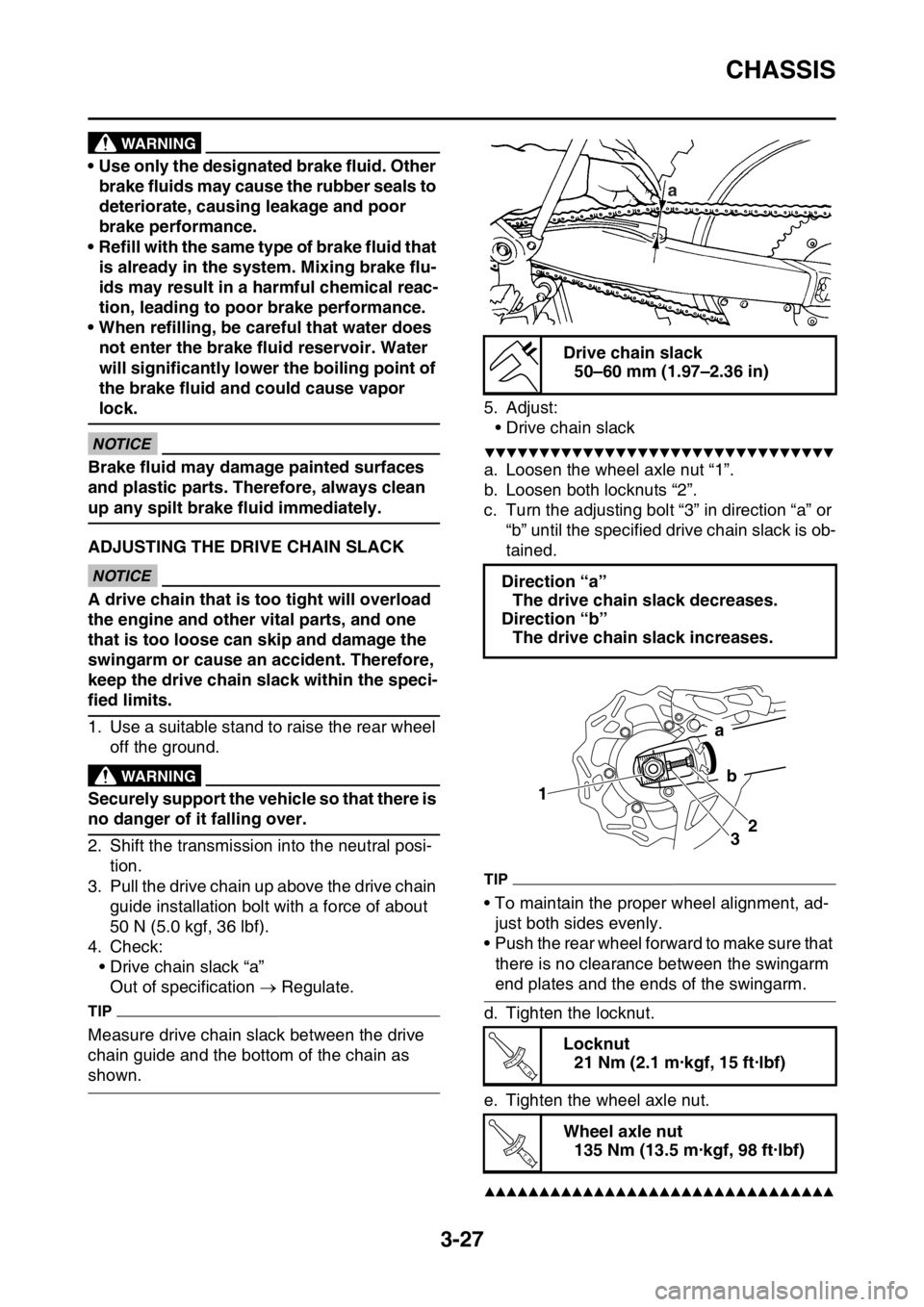
CHASSIS
3-27
WARNING
• Use only the designated brake fluid. Other
brake fluids may cause the rubber seals to
deteriorate, causing leakage and poor
brake performance.
• Refill with the same type of brake fluid that
is already in the system. Mixing brake flu-
ids may result in a harmful chemical reac-
tion, leading to poor brake performance.
• When refilling, be careful that water does
not enter the brake fluid reservoir. Water
will significantly lower the boiling point of
the brake fluid and could cause vapor
lock.
ECA13540
NOTICE
Brake fluid may damage painted surfaces
and plastic parts. Therefore, always clean
up any spilt brake fluid immediately.
EAS1SM5099ADJUSTING THE DRIVE CHAIN SLACKECA13550
NOTICE
A drive chain that is too tight will overload
the engine and other vital parts, and one
that is too loose can skip and damage the
swingarm or cause an accident. Therefore,
keep the drive chain slack within the speci-
fied limits.
1. Use a suitable stand to raise the rear wheel
off the ground.
EWA13120
WARNING
Securely support the vehicle so that there is
no danger of it falling over.
2. Shift the transmission into the neutral posi-
tion.
3. Pull the drive chain up above the drive chain
guide installation bolt with a force of about
50 N (5.0 kgf, 36 lbf).
4. Check:
• Drive chain slack “a”
Out of specification Regulate.
TIP
Measure drive chain slack between the drive
chain guide and the bottom of the chain as
shown.5. Adjust:
• Drive chain slack
▼▼▼▼▼▼▼▼▼▼▼▼▼▼▼▼▼▼▼▼▼▼▼▼▼▼▼▼▼▼▼▼
a. Loosen the wheel axle nut “1”.
b. Loosen both locknuts “2”.
c. Turn the adjusting bolt “3” in direction “a” or
“b” until the specified drive chain slack is ob-
tained.
TIP
• To maintain the proper wheel alignment, ad-
just both sides evenly.
• Push the rear wheel forward to make sure that
there is no clearance between the swingarm
end plates and the ends of the swingarm.
d. Tighten the locknut.
e. Tighten the wheel axle nut.
▲▲▲▲▲▲▲▲▲▲▲▲▲▲▲▲▲▲▲▲▲▲▲▲▲▲▲▲▲▲▲▲
Drive chain slack
50–60 mm (1.97–2.36 in)
Direction “a”
The drive chain slack decreases.
Direction “b”
The drive chain slack increases.
Locknut
21 Nm (2.1 m·kgf, 15 ft·lbf)
Wheel axle nut
135 Nm (13.5 m·kgf, 98 ft·lbf)
a
1
32
a
b
T R..
T R..
Page 114 of 356
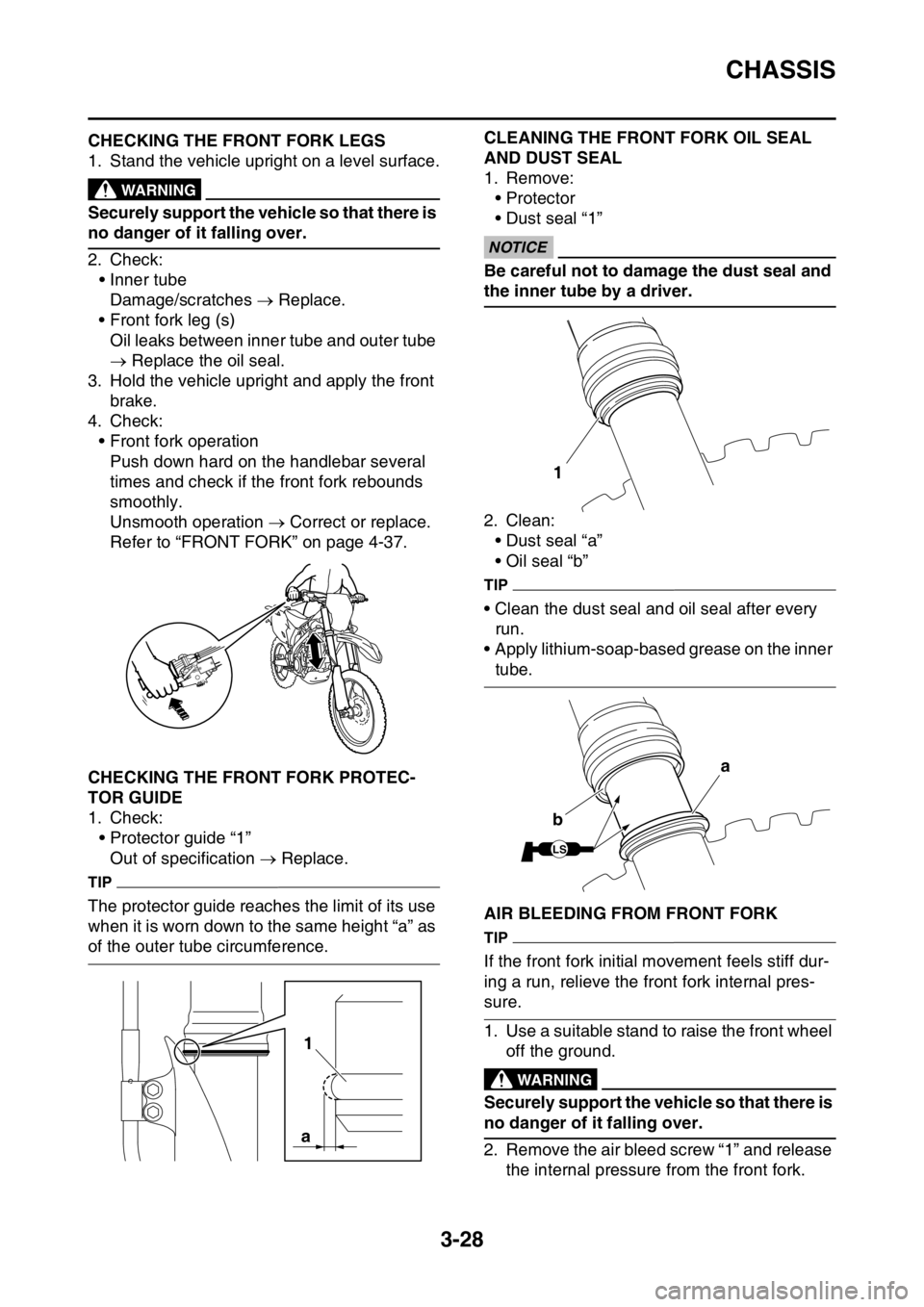
CHASSIS
3-28
EAS1SM5100CHECKING THE FRONT FORK LEGS
1. Stand the vehicle upright on a level surface.
EWA13120
WARNING
Securely support the vehicle so that there is
no danger of it falling over.
2. Check:
• Inner tube
Damage/scratches Replace.
• Front fork leg (s)
Oil leaks between inner tube and outer tube
Replace the oil seal.
3. Hold the vehicle upright and apply the front
brake.
4. Check:
• Front fork operation
Push down hard on the handlebar several
times and check if the front fork rebounds
smoothly.
Unsmooth operation Correct or replace.
Refer to “FRONT FORK” on page 4-37.
EAS1SM5101CHECKING THE FRONT FORK PROTEC-
TOR GUIDE
1. Check:
• Protector guide “1”
Out of specification Replace.
TIP
The protector guide reaches the limit of its use
when it is worn down to the same height “a” as
of the outer tube circumference.
EAS1SM5102
CLEANING THE FRONT FORK OIL SEAL
AND DUST SEAL
1. Remove:
•Protector
• Dust seal “1”
ECA?
NOTICE
Be careful not to damage the dust seal and
the inner tube by a driver.
2. Clean:
• Dust seal “a”
• Oil seal “b”
TIP
• Clean the dust seal and oil seal after every
run.
• Apply lithium-soap-based grease on the inner
tube.
EAS1SM5103AIR BLEEDING FROM FRONT FORK
TIP
If the front fork initial movement feels stiff dur-
ing a run, relieve the front fork internal pres-
sure.
1. Use a suitable stand to raise the front wheel
off the ground.
EWA@
WARNING
Securely support the vehicle so that there is
no danger of it falling over.
2. Remove the air bleed screw “1” and release
the internal pressure from the front fork.
1
a
1
LS
a
b
Page 115 of 356
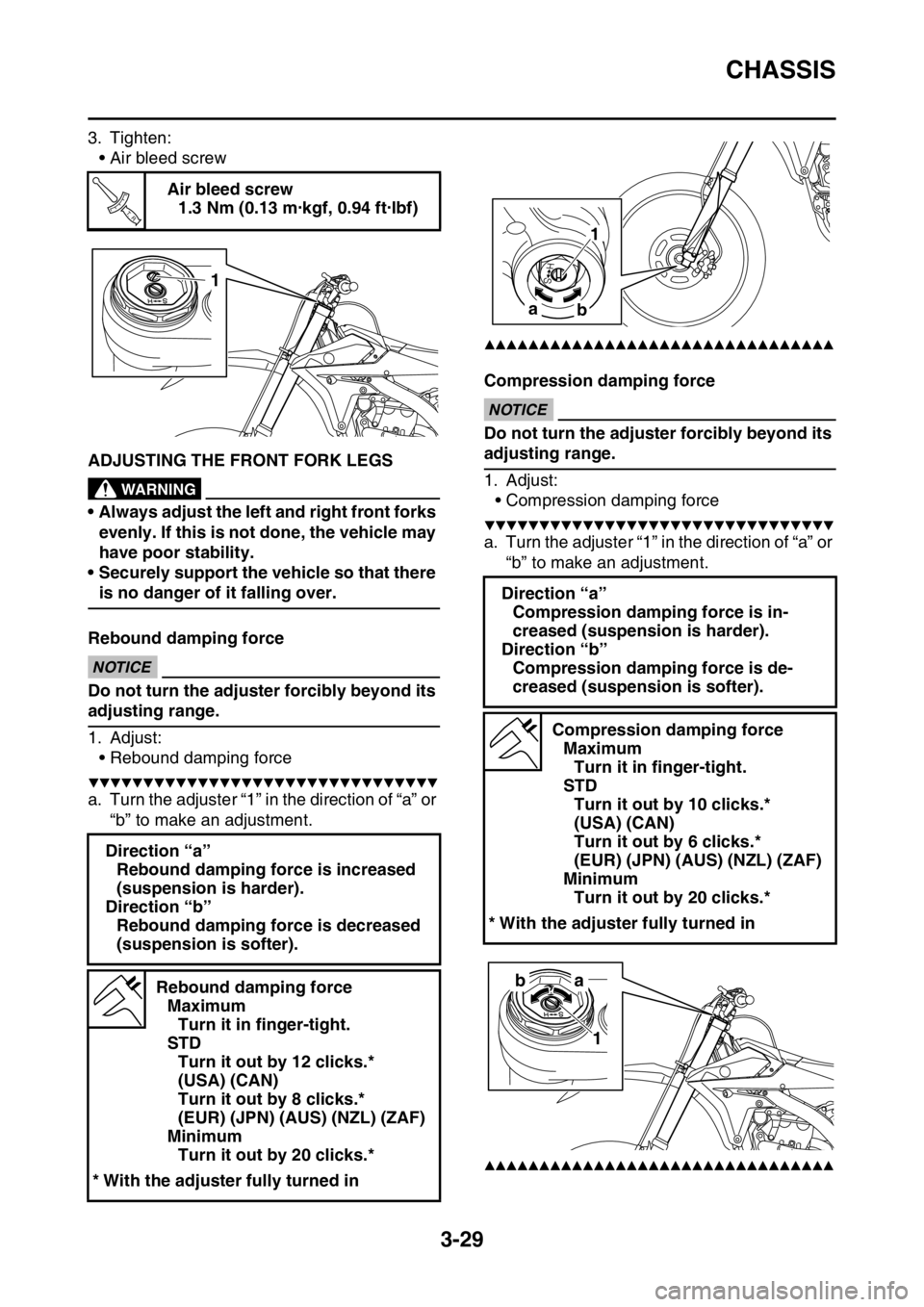
CHASSIS
3-29
3. Tighten:
• Air bleed screw
EAS1SM5104ADJUSTING THE FRONT FORK LEGSEWA32D1006
WARNING
• Always adjust the left and right front forks
evenly. If this is not done, the vehicle may
have poor stability.
• Securely support the vehicle so that there
is no danger of it falling over.
Rebound damping force
ECA@
NOTICE
Do not turn the adjuster forcibly beyond its
adjusting range.
1. Adjust:
• Rebound damping force
▼▼▼▼▼▼▼▼▼▼▼▼▼▼▼▼▼▼▼▼▼▼▼▼▼▼▼▼▼▼▼▼
a. Turn the adjuster “1” in the direction of “a” or
“b” to make an adjustment.
▲▲▲▲▲▲▲▲▲▲▲▲▲▲▲▲▲▲▲▲▲▲▲▲▲▲▲▲▲▲▲▲
Compression damping forceECA@
NOTICE
Do not turn the adjuster forcibly beyond its
adjusting range.
1. Adjust:
• Compression damping force
▼▼▼▼▼▼▼▼▼▼▼▼▼▼▼▼▼▼▼▼▼▼▼▼▼▼▼▼▼▼▼▼
a. Turn the adjuster “1” in the direction of “a” or
“b” to make an adjustment.
▲▲▲▲▲▲▲▲▲▲▲▲▲▲▲▲▲▲▲▲▲▲▲▲▲▲▲▲▲▲▲▲
Air bleed screw
1.3 Nm (0.13 m·kgf, 0.94 ft·lbf)
Direction “a”
Rebound damping force is increased
(suspension is harder).
Direction “b”
Rebound damping force is decreased
(suspension is softer).
Rebound damping force
Maximum
Turn it in finger-tight.
STD
Turn it out by 12 clicks.*
(USA) (CAN)
Turn it out by 8 clicks.*
(EUR) (JPN) (AUS) (NZL) (ZAF)
Minimum
Turn it out by 20 clicks.*
* With the adjuster fully turned in
T R..
1
Direction “a”
Compression damping force is in-
creased (suspension is harder).
Direction “b”
Compression damping force is de-
creased (suspension is softer).
Compression damping force
Maximum
Turn it in finger-tight.
STD
Turn it out by 10 clicks.*
(USA) (CAN)
Turn it out by 6 clicks.*
(EUR) (JPN) (AUS) (NZL) (ZAF)
Minimum
Turn it out by 20 clicks.*
* With the adjuster fully turned in
1
a
b
a b
1
Page 116 of 356
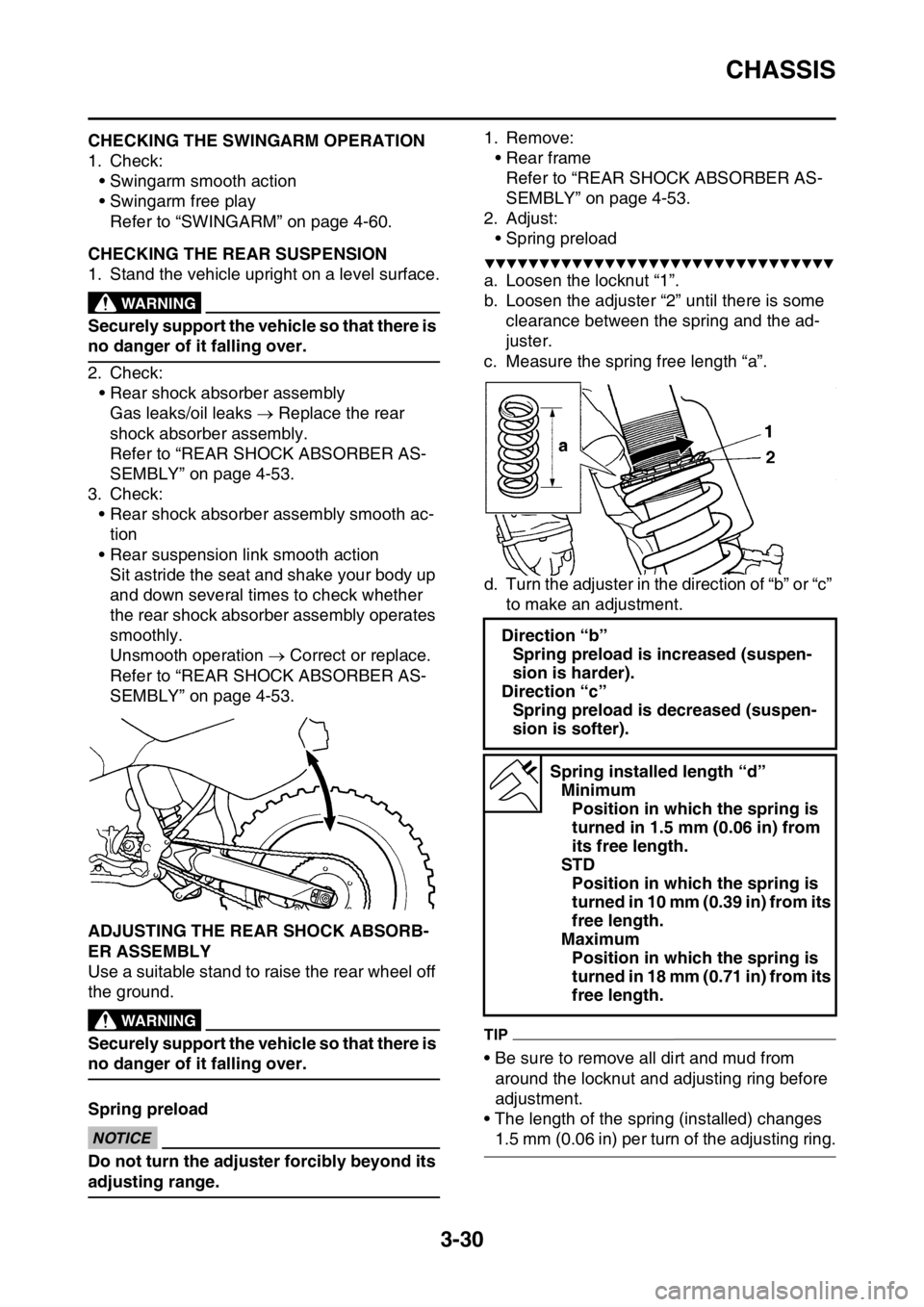
CHASSIS
3-30
EAS1SM5105CHECKING THE SWINGARM OPERATION
1. Check:
• Swingarm smooth action
• Swingarm free play
Refer to “SWINGARM” on page 4-60.
EAS1SM5106CHECKING THE REAR SUSPENSION
1. Stand the vehicle upright on a level surface.
EWA@
WARNING
Securely support the vehicle so that there is
no danger of it falling over.
2. Check:
• Rear shock absorber assembly
Gas leaks/oil leaks Replace the rear
shock absorber assembly.
Refer to “REAR SHOCK ABSORBER AS-
SEMBLY” on page 4-53.
3. Check:
• Rear shock absorber assembly smooth ac-
tion
• Rear suspension link smooth action
Sit astride the seat and shake your body up
and down several times to check whether
the rear shock absorber assembly operates
smoothly.
Unsmooth operation Correct or replace.
Refer to “REAR SHOCK ABSORBER AS-
SEMBLY” on page 4-53.
EAS1SM5107ADJUSTING THE REAR SHOCK ABSORB-
ER ASSEMBLY
Use a suitable stand to raise the rear wheel off
the ground.
EWA13120
WARNING
Securely support the vehicle so that there is
no danger of it falling over.
Spring preload
ECA@
NOTICE
Do not turn the adjuster forcibly beyond its
adjusting range.1. Remove:
• Rear frame
Refer to “REAR SHOCK ABSORBER AS-
SEMBLY” on page 4-53.
2. Adjust:
• Spring preload
▼▼▼▼▼▼▼▼▼▼▼▼▼▼▼▼▼▼▼▼▼▼▼▼▼▼▼▼▼▼▼▼
a. Loosen the locknut “1”.
b. Loosen the adjuster “2” until there is some
clearance between the spring and the ad-
juster.
c. Measure the spring free length “a”.
d. Turn the adjuster in the direction of “b” or “c”
to make an adjustment.
TIP
• Be sure to remove all dirt and mud from
around the locknut and adjusting ring before
adjustment.
• The length of the spring (installed) changes
1.5 mm (0.06 in) per turn of the adjusting ring.
Direction “b”
Spring preload is increased (suspen-
sion is harder).
Direction “c”
Spring preload is decreased (suspen-
sion is softer).
Spring installed length “d”
Minimum
Position in which the spring is
turned in 1.5 mm (0.06 in) from
its free length.
STD
Position in which the spring is
turned in 10 mm (0.39 in) from its
free length.
Maximum
Position in which the spring is
turned in 18 mm (0.71 in) from its
free length.
Page 117 of 356
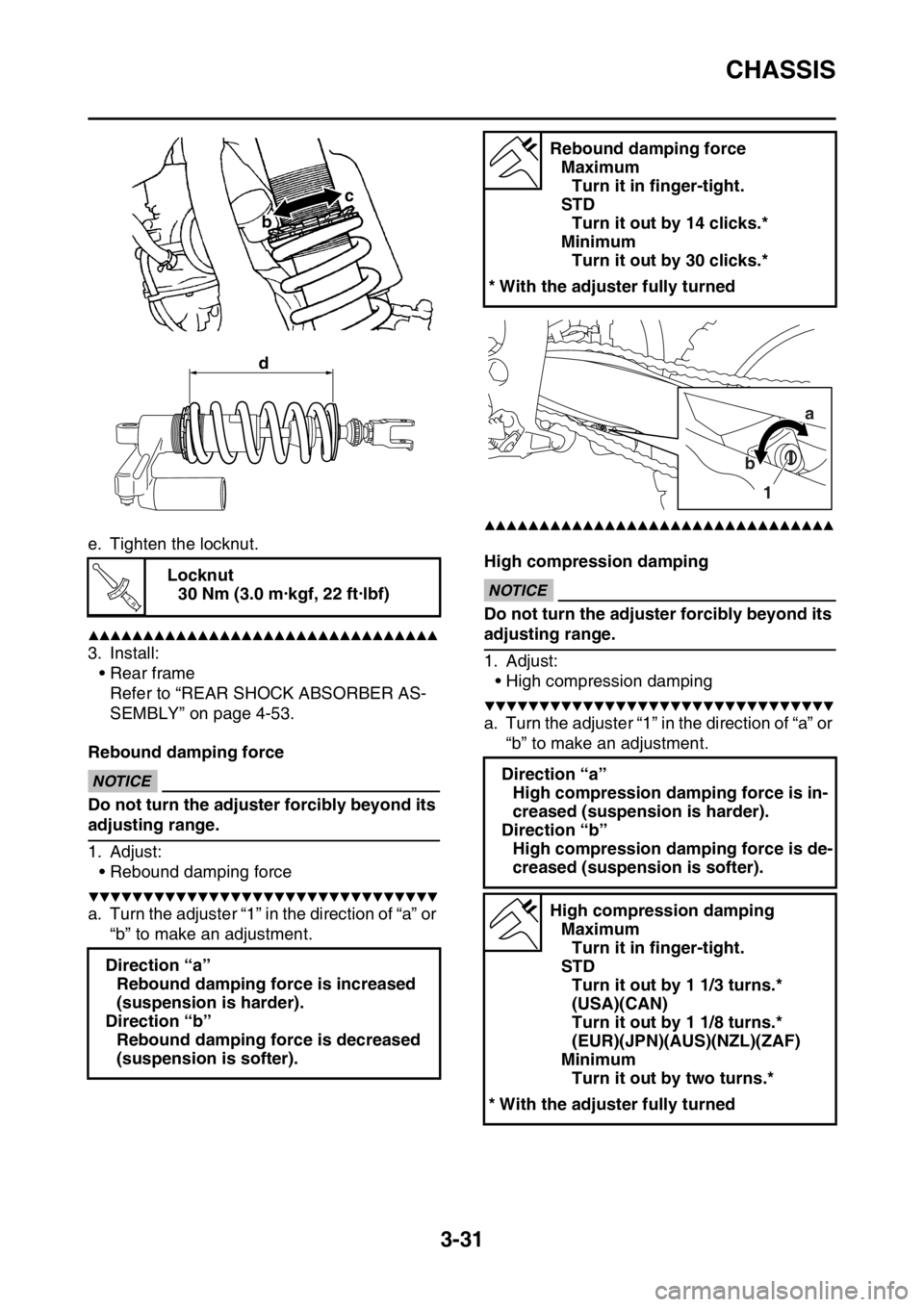
CHASSIS
3-31
e. Tighten the locknut.
▲▲▲▲▲▲▲▲▲▲▲▲▲▲▲▲▲▲▲▲▲▲▲▲▲▲▲▲▲▲▲▲
3. Install:
• Rear frame
Refer to “REAR SHOCK ABSORBER AS-
SEMBLY” on page 4-53.
Rebound damping force
ECA@
NOTICE
Do not turn the adjuster forcibly beyond its
adjusting range.
1. Adjust:
• Rebound damping force
▼▼▼▼▼▼▼▼▼▼▼▼▼▼▼▼▼▼▼▼▼▼▼▼▼▼▼▼▼▼▼▼
a. Turn the adjuster “1” in the direction of “a” or
“b” to make an adjustment.
▲▲▲▲▲▲▲▲▲▲▲▲▲▲▲▲▲▲▲▲▲▲▲▲▲▲▲▲▲▲▲▲
High compression dampingECA@
NOTICE
Do not turn the adjuster forcibly beyond its
adjusting range.
1. Adjust:
• High compression damping
▼▼▼▼▼▼▼▼▼▼▼▼▼▼▼▼▼▼▼▼▼▼▼▼▼▼▼▼▼▼▼▼
a. Turn the adjuster “1” in the direction of “a” or
“b” to make an adjustment. Locknut
30 Nm (3.0 m·kgf, 22 ft·lbf)
Direction “a”
Rebound damping force is increased
(suspension is harder).
Direction “b”
Rebound damping force is decreased
(suspension is softer).
c
b
d
T R..
Rebound damping force
Maximum
Turn it in finger-tight.
STD
Turn it out by 14 clicks.*
Minimum
Turn it out by 30 clicks.*
* With the adjuster fully turned
Direction “a”
High compression damping force is in-
creased (suspension is harder).
Direction “b”
High compression damping force is de-
creased (suspension is softer).
High compression damping
Maximum
Turn it in finger-tight.
STD
Turn it out by 1 1/3 turns.*
(USA)(CAN)
Turn it out by 1 1/8 turns.*
(EUR)(JPN)(AUS)(NZL)(ZAF)
Minimum
Turn it out by two turns.*
* With the adjuster fully turned
a
b
1
Page 118 of 356
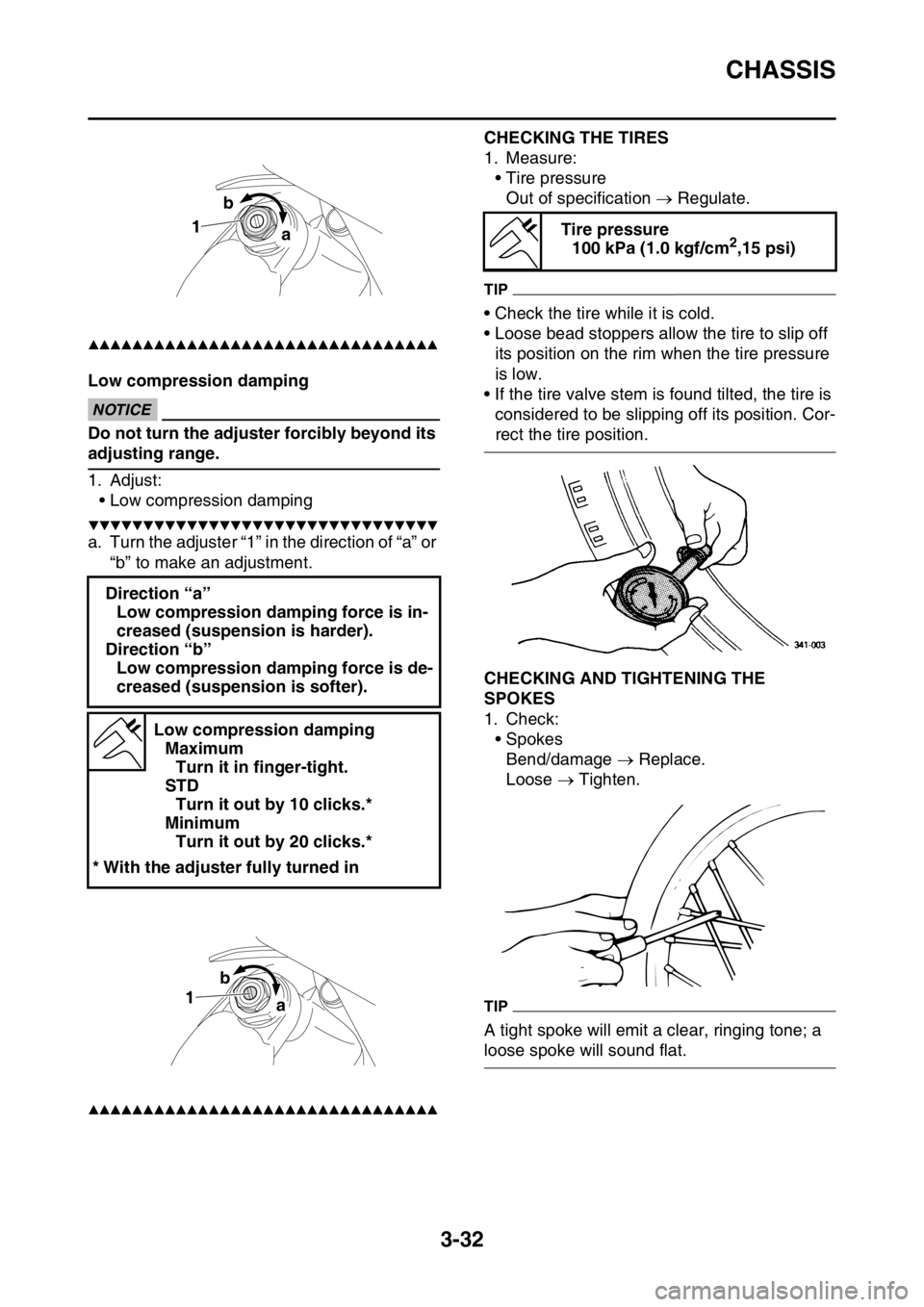
CHASSIS
3-32
▲▲▲▲▲▲▲▲▲▲▲▲▲▲▲▲▲▲▲▲▲▲▲▲▲▲▲▲▲▲▲▲
Low compression dampingECA@
NOTICE
Do not turn the adjuster forcibly beyond its
adjusting range.
1. Adjust:
• Low compression damping
▼▼▼▼▼▼▼▼▼▼▼▼▼▼▼▼▼▼▼▼▼▼▼▼▼▼▼▼▼▼▼▼
a. Turn the adjuster “1” in the direction of “a” or
“b” to make an adjustment.
▲▲▲▲▲▲▲▲▲▲▲▲▲▲▲▲▲▲▲▲▲▲▲▲▲▲▲▲▲▲▲▲
EAS1SM5108
CHECKING THE TIRES
1. Measure:
• Tire pressure
Out of specification Regulate.
TIP
• Check the tire while it is cold.
• Loose bead stoppers allow the tire to slip off
its position on the rim when the tire pressure
is low.
• If the tire valve stem is found tilted, the tire is
considered to be slipping off its position. Cor-
rect the tire position.
EAS1SM5109CHECKING AND TIGHTENING THE
SPOKES
1. Check:
• Spokes
Bend/damage Replace.
Loose Tighten.
TIP
A tight spoke will emit a clear, ringing tone; a
loose spoke will sound flat. Direction “a”
Low compression damping force is in-
creased (suspension is harder).
Direction “b”
Low compression damping force is de-
creased (suspension is softer).
Low compression damping
Maximum
Turn it in finger-tight.
STD
Turn it out by 10 clicks.*
Minimum
Turn it out by 20 clicks.*
* With the adjuster fully turned in
1
a b
1ba
Tire pressure
100 kPa (1.0 kgf/cm2,15 psi)
Page 119 of 356
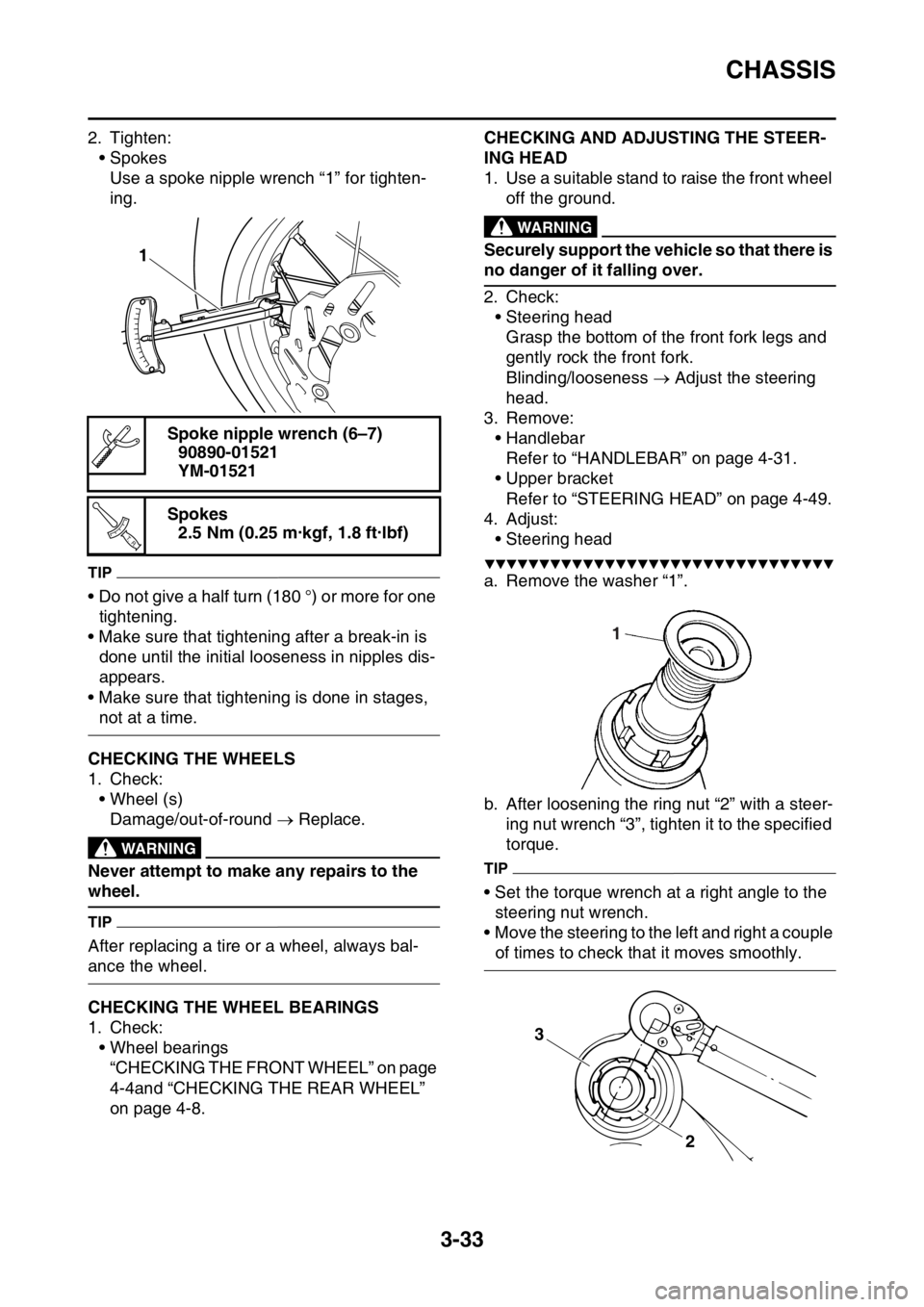
CHASSIS
3-33
2. Tighten:
• Spokes
Use a spoke nipple wrench “1” for tighten-
ing.
TIP
• Do not give a half turn (180 °) or more for one
tightening.
• Make sure that tightening after a break-in is
done until the initial looseness in nipples dis-
appears.
• Make sure that tightening is done in stages,
not at a time.
EAS1SM5110CHECKING THE WHEELS
1. Check:
• Wheel (s)
Damage/out-of-round Replace.
EWA13260
WARNING
Never attempt to make any repairs to the
wheel.
TIP
After replacing a tire or a wheel, always bal-
ance the wheel.
EAS1SM5111CHECKING THE WHEEL BEARINGS
1. Check:
• Wheel bearings
“CHECKING THE FRONT WHEEL” on page
4-4and “CHECKING THE REAR WHEEL”
on page 4-8.
EAS1SM5112
CHECKING AND ADJUSTING THE STEER-
ING HEAD
1. Use a suitable stand to raise the front wheel
off the ground.
EWA13120
WARNING
Securely support the vehicle so that there is
no danger of it falling over.
2. Check:
• Steering head
Grasp the bottom of the front fork legs and
gently rock the front fork.
Blinding/looseness Adjust the steering
head.
3. Remove:
• Handlebar
Refer to “HANDLEBAR” on page 4-31.
• Upper bracket
Refer to “STEERING HEAD” on page 4-49.
4. Adjust:
• Steering head
▼▼▼▼▼▼▼▼▼▼▼▼▼▼▼▼▼▼▼▼▼▼▼▼▼▼▼▼▼▼▼▼
a. Remove the washer “1”.
b. After loosening the ring nut “2” with a steer-
ing nut wrench “3”, tighten it to the specified
torque.
TIP
• Set the torque wrench at a right angle to the
steering nut wrench.
• Move the steering to the left and right a couple
of times to check that it moves smoothly. Spoke nipple wrench (6–7)
90890-01521
YM-01521
Spokes
2.5 Nm (0.25 m·kgf, 1.8 ft·lbf)
1
T R..
1
3
2
Page 120 of 356
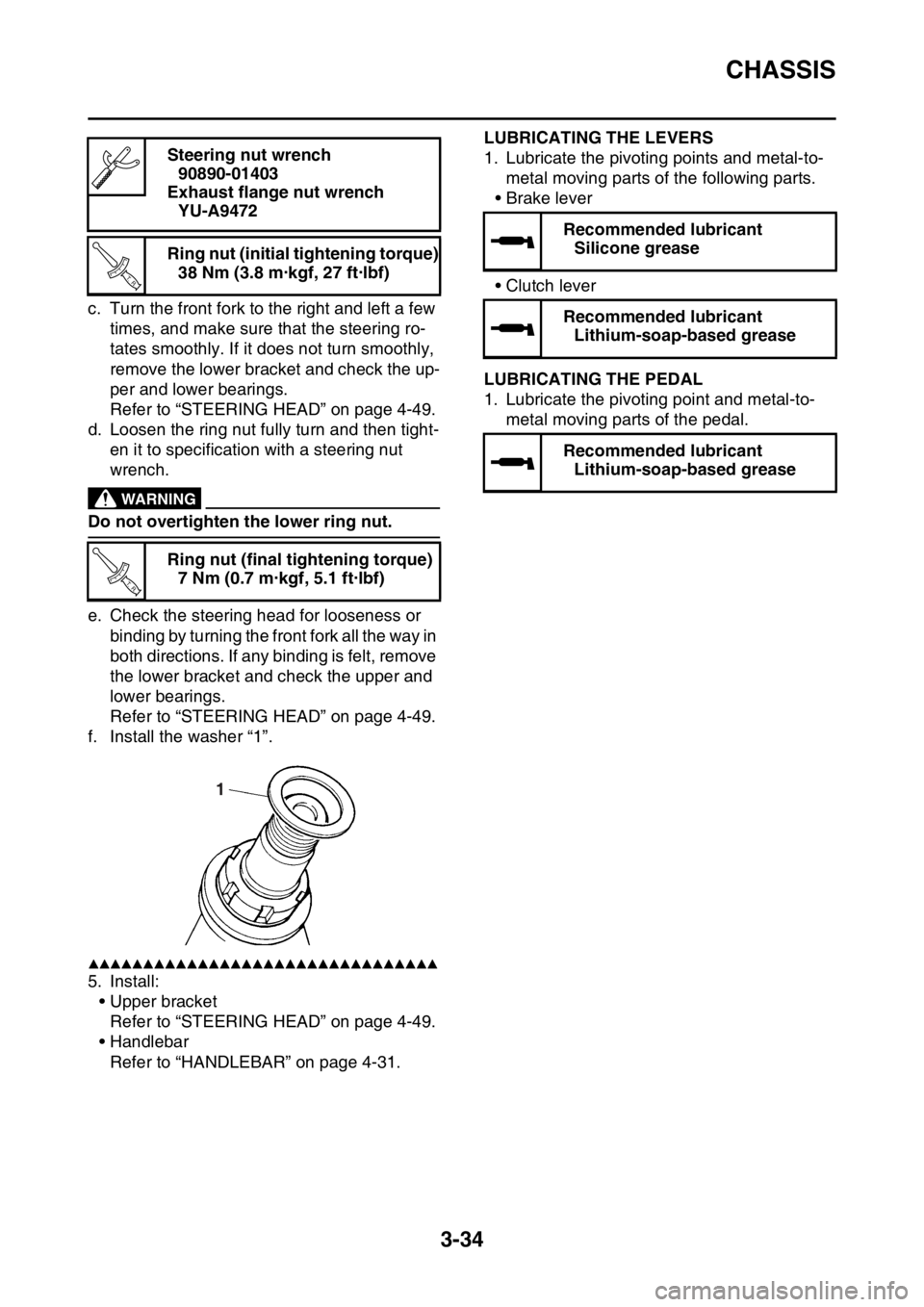
CHASSIS
3-34
c. Turn the front fork to the right and left a few
times, and make sure that the steering ro-
tates smoothly. If it does not turn smoothly,
remove the lower bracket and check the up-
per and lower bearings.
Refer to “STEERING HEAD” on page 4-49.
d. Loosen the ring nut fully turn and then tight-
en it to specification with a steering nut
wrench.
EWA13140
WARNING
Do not overtighten the lower ring nut.
e. Check the steering head for looseness or
binding by turning the front fork all the way in
both directions. If any binding is felt, remove
the lower bracket and check the upper and
lower bearings.
Refer to “STEERING HEAD” on page 4-49.
f. Install the washer “1”.
▲▲▲▲▲▲▲▲▲▲▲▲▲▲▲▲▲▲▲▲▲▲▲▲▲▲▲▲▲▲▲▲
5. Install:
• Upper bracket
Refer to “STEERING HEAD” on page 4-49.
• Handlebar
Refer to “HANDLEBAR” on page 4-31.
EAS1SM5113
LUBRICATING THE LEVERS
1. Lubricate the pivoting points and metal-to-
metal moving parts of the following parts.
•Brake lever
• Clutch lever
EAS1SM5114LUBRICATING THE PEDAL
1. Lubricate the pivoting point and metal-to-
metal moving parts of the pedal. Steering nut wrench
90890-01403
Exhaust flange nut wrench
YU-A9472
Ring nut (initial tightening torque)
38 Nm (3.8 m·kgf, 27 ft·lbf)
Ring nut (final tightening torque)
7 Nm (0.7 m·kgf, 5.1 ft·lbf)
T R..
T R..
1
Recommended lubricant
Silicone grease
Recommended lubricant
Lithium-soap-based grease
Recommended lubricant
Lithium-soap-based grease