YAMAHA YZ250F 2015 Owners Manual
Manufacturer: YAMAHA, Model Year: 2015, Model line: YZ250F, Model: YAMAHA YZ250F 2015Pages: 356, PDF Size: 11.39 MB
Page 101 of 356
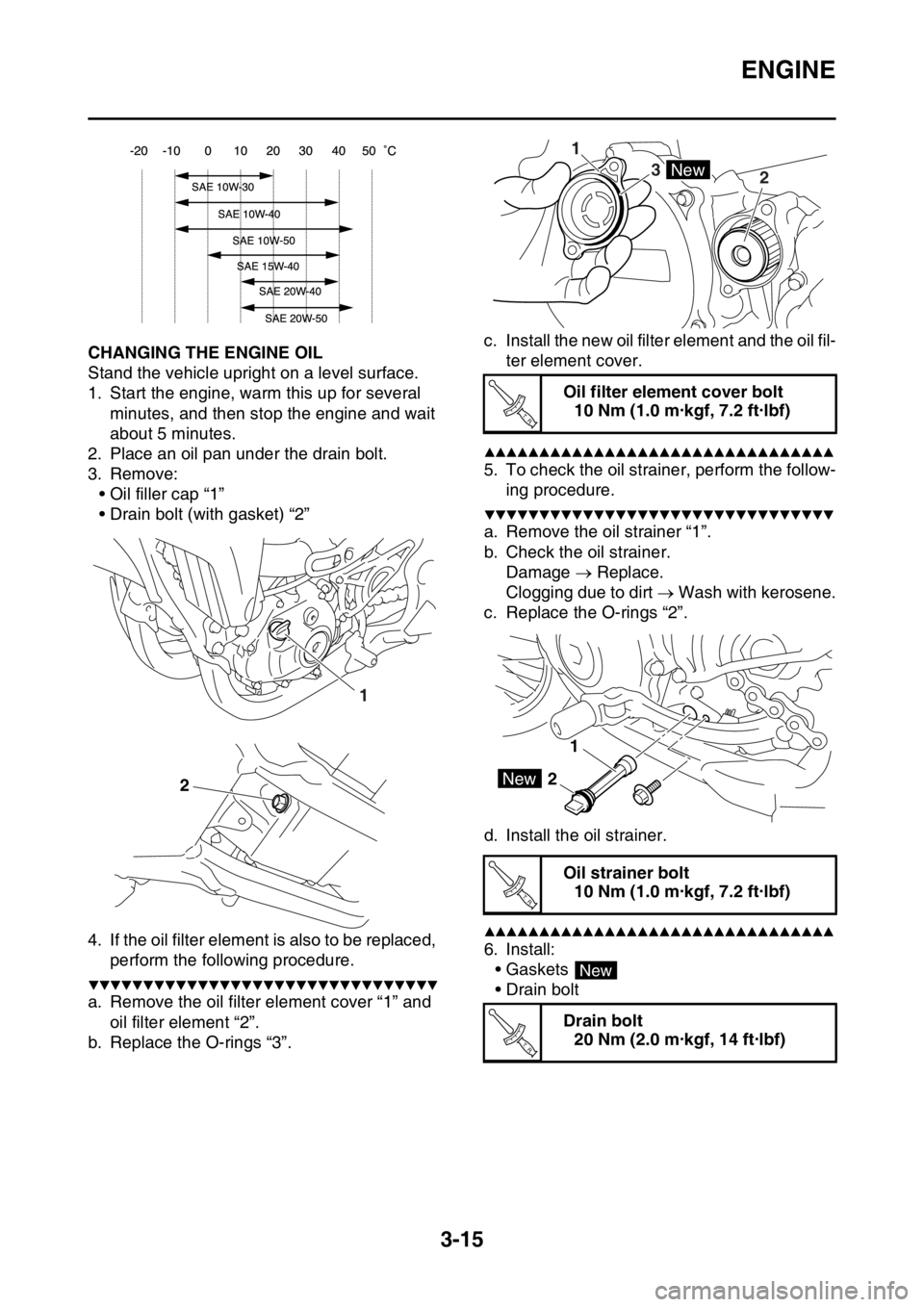
ENGINE
3-15
EAS1SM5087CHANGING THE ENGINE OIL
Stand the vehicle upright on a level surface.
1. Start the engine, warm this up for several
minutes, and then stop the engine and wait
about 5 minutes.
2. Place an oil pan under the drain bolt.
3. Remove:
• Oil filler cap “1”
• Drain bolt (with gasket) “2”
4. If the oil filter element is also to be replaced,
perform the following procedure.
▼▼▼▼▼▼▼▼▼▼▼▼▼▼▼▼▼▼▼▼▼▼▼▼▼▼▼▼▼▼▼▼
a. Remove the oil filter element cover “1” and
oil filter element “2”.
b. Replace the O-rings “3”.c. Install the new oil filter element and the oil fil-
ter element cover.
▲▲▲▲▲▲▲▲▲▲▲▲▲▲▲▲▲▲▲▲▲▲▲▲▲▲▲▲▲▲▲▲
5. To check the oil strainer, perform the follow-
ing procedure.
▼▼▼▼▼▼▼▼▼▼▼▼▼▼▼▼▼▼▼▼▼▼▼▼▼▼▼▼▼▼▼▼
a. Remove the oil strainer “1”.
b. Check the oil strainer.
Damage Replace.
Clogging due to dirt Wash with kerosene.
c. Replace the O-rings “2”.
d. Install the oil strainer.
▲▲▲▲▲▲▲▲▲▲▲▲▲▲▲▲▲▲▲▲▲▲▲▲▲▲▲▲▲▲▲▲
6. Install:
•Gaskets
• Drain bolt
1
2
Oil filter element cover bolt
10 Nm (1.0 m·kgf, 7.2 ft·lbf)
Oil strainer bolt
10 Nm (1.0 m·kgf, 7.2 ft·lbf)
Drain bolt
20 Nm (2.0 m·kgf, 14 ft·lbf)
1
3
2
New
T R..
1
2New
T R..
New
T R..
Page 102 of 356
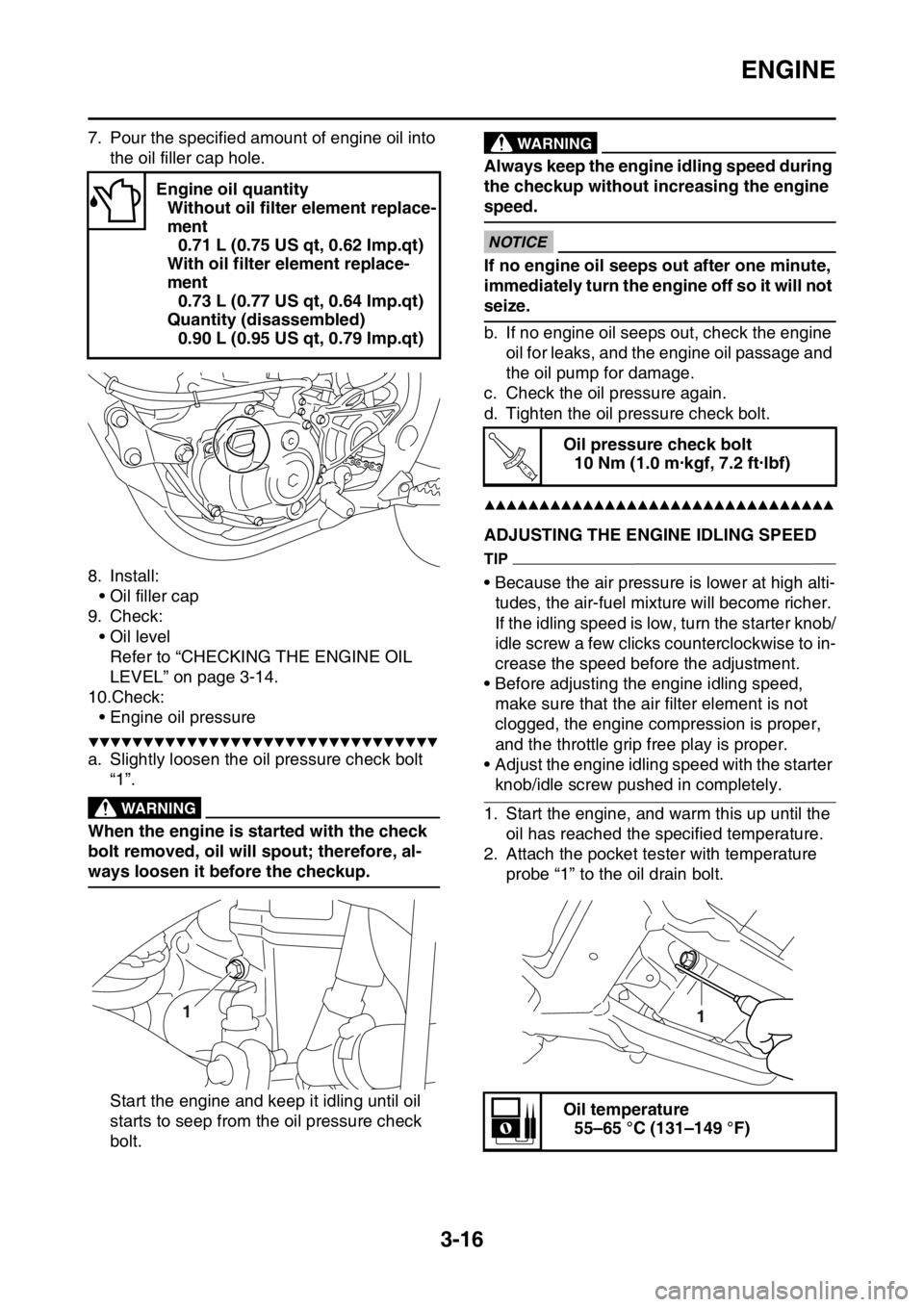
ENGINE
3-16
7. Pour the specified amount of engine oil into
the oil filler cap hole.
8. Install:
• Oil filler cap
9. Check:
• Oil level
Refer to “CHECKING THE ENGINE OIL
LEVEL” on page 3-14.
10.Check:
• Engine oil pressure
▼▼▼▼▼▼▼▼▼▼▼▼▼▼▼▼▼▼▼▼▼▼▼▼▼▼▼▼▼▼▼▼
a. Slightly loosen the oil pressure check bolt
“1”.
EWA
WARNING
When the engine is started with the check
bolt removed, oil will spout; therefore, al-
ways loosen it before the checkup.
Start the engine and keep it idling until oil
starts to seep from the oil pressure check
bolt.
EWA
WARNING
Always keep the engine idling speed during
the checkup without increasing the engine
speed.
ECA
NOTICE
If no engine oil seeps out after one minute,
immediately turn the engine off so it will not
seize.
b. If no engine oil seeps out, check the engine
oil for leaks, and the engine oil passage and
the oil pump for damage.
c. Check the oil pressure again.
d. Tighten the oil pressure check bolt.
▲▲▲▲▲▲▲▲▲▲▲▲▲▲▲▲▲▲▲▲▲▲▲▲▲▲▲▲▲▲▲▲
EAS1SM5088ADJUSTING THE ENGINE IDLING SPEED
TIP
• Because the air pressure is lower at high alti-
tudes, the air-fuel mixture will become richer.
If the idling speed is low, turn the starter knob/
idle screw a few clicks counterclockwise to in-
crease the speed before the adjustment.
• Before adjusting the engine idling speed,
make sure that the air filter element is not
clogged, the engine compression is proper,
and the throttle grip free play is proper.
• Adjust the engine idling speed with the starter
knob/idle screw pushed in completely.
1. Start the engine, and warm this up until the
oil has reached the specified temperature.
2. Attach the pocket tester with temperature
probe “1” to the oil drain bolt. Engine oil quantity
Without oil filter element replace-
ment
0.71 L (0.75 US qt, 0.62 Imp.qt)
With oil filter element replace-
ment
0.73 L (0.77 US qt, 0.64 Imp.qt)
Quantity (disassembled)
0.90 L (0.95 US qt, 0.79 Imp.qt)
1
Oil pressure check bolt
10 Nm (1.0 m·kgf, 7.2 ft·lbf)
Oil temperature
55–65 °C (131–149 °F)
T R..
1
Page 103 of 356
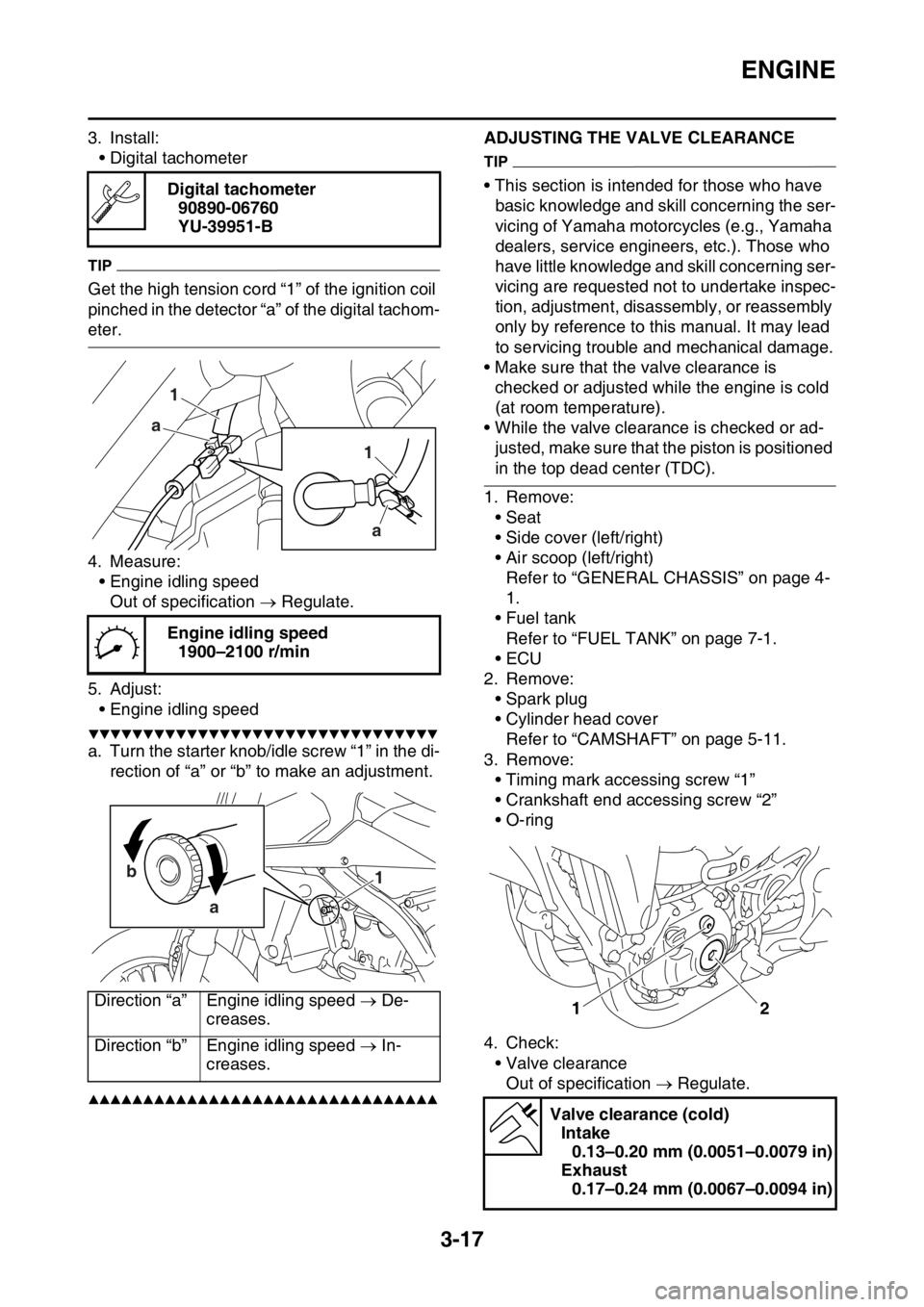
ENGINE
3-17
3. Install:
• Digital tachometer
TIP
Get the high tension cord “1” of the ignition coil
pinched in the detector “a” of the digital tachom-
eter.
4. Measure:
• Engine idling speed
Out of specification Regulate.
5. Adjust:
• Engine idling speed
▼▼▼▼▼▼▼▼▼▼▼▼▼▼▼▼▼▼▼▼▼▼▼▼▼▼▼▼▼▼▼▼
a. Turn the starter knob/idle screw “1” in the di-
rection of “a” or “b” to make an adjustment.
▲▲▲▲▲▲▲▲▲▲▲▲▲▲▲▲▲▲▲▲▲▲▲▲▲▲▲▲▲▲▲▲
EAS1SM5089
ADJUSTING THE VALVE CLEARANCE
TIP
• This section is intended for those who have
basic knowledge and skill concerning the ser-
vicing of Yamaha motorcycles (e.g., Yamaha
dealers, service engineers, etc.). Those who
have little knowledge and skill concerning ser-
vicing are requested not to undertake inspec-
tion, adjustment, disassembly, or reassembly
only by reference to this manual. It may lead
to servicing trouble and mechanical damage.
• Make sure that the valve clearance is
checked or adjusted while the engine is cold
(at room temperature).
• While the valve clearance is checked or ad-
justed, make sure that the piston is positioned
in the top dead center (TDC).
1. Remove:
• Seat
• Side cover (left/right)
• Air scoop (left/right)
Refer to “GENERAL CHASSIS” on page 4-
1.
• Fuel tank
Refer to “FUEL TANK” on page 7-1.
•ECU
2. Remove:
• Spark plug
• Cylinder head cover
Refer to “CAMSHAFT” on page 5-11.
3. Remove:
• Timing mark accessing screw “1”
• Crankshaft end accessing screw “2”
• O-ring
4. Check:
• Valve clearance
Out of specification Regulate. Digital tachometer
90890-06760
YU-39951-B
Engine idling speed
1900–2100 r/min
Direction “a” Engine idling speed De-
creases.
Direction “b” Engine idling speed In-
creases.
1 1
a a
1 b
a
Valve clearance (cold)
Intake
0.13–0.20 mm (0.0051–0.0079 in)
Exhaust
0.17–0.24 mm (0.0067–0.0094 in)
1
2
Page 104 of 356
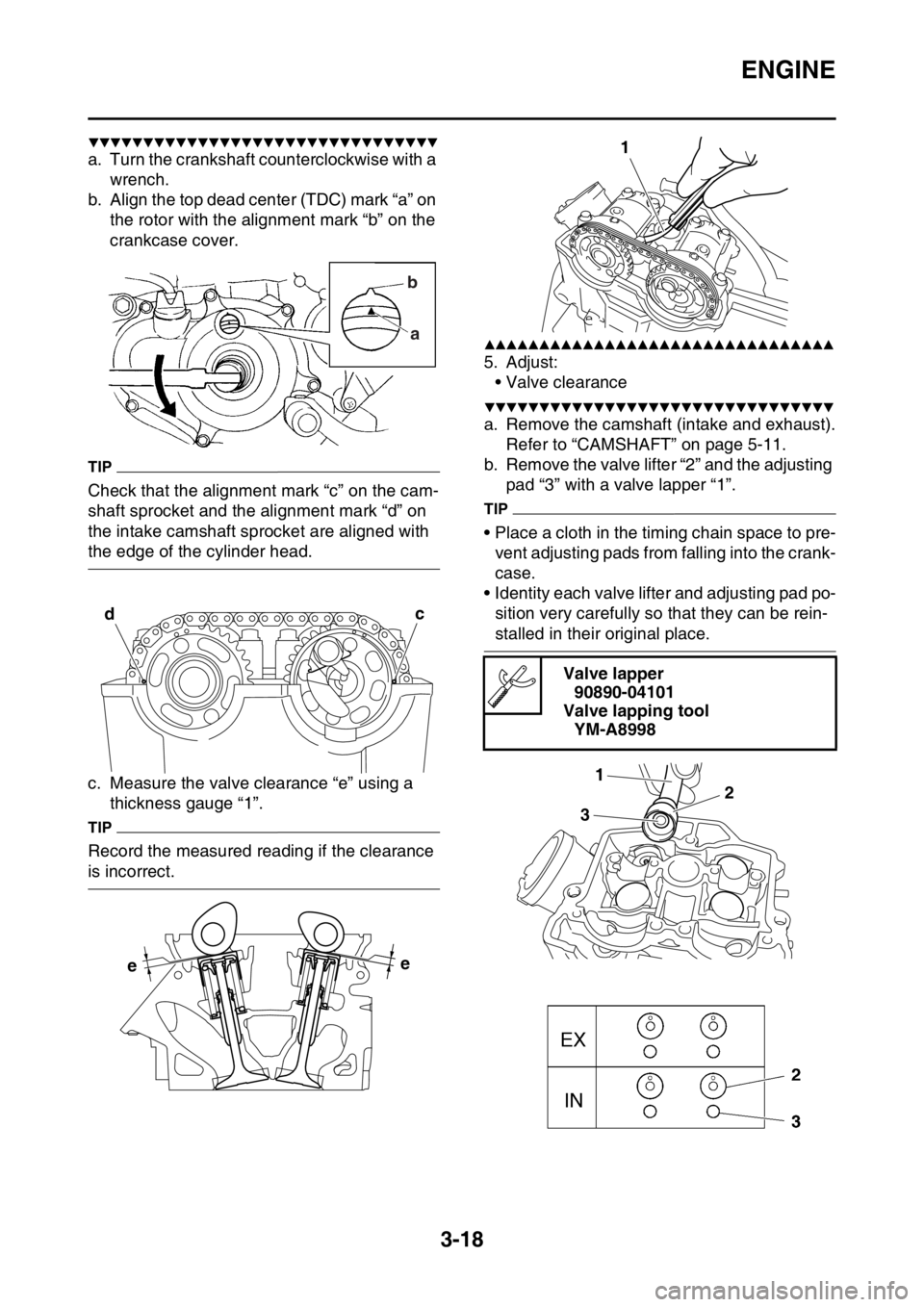
ENGINE
3-18
▼▼▼▼▼▼▼▼▼▼▼▼▼▼▼▼▼▼▼▼▼▼▼▼▼▼▼▼▼▼▼▼
a. Turn the crankshaft counterclockwise with a
wrench.
b. Align the top dead center (TDC) mark “a” on
the rotor with the alignment mark “b” on the
crankcase cover.
TIP
Check that the alignment mark “c” on the cam-
shaft sprocket and the alignment mark “d” on
the intake camshaft sprocket are aligned with
the edge of the cylinder head.
c. Measure the valve clearance “e” using a
thickness gauge “1”.
TIP
Record the measured reading if the clearance
is incorrect.
▲▲▲▲▲▲▲▲▲▲▲▲▲▲▲▲▲▲▲▲▲▲▲▲▲▲▲▲▲▲▲▲
5. Adjust:
• Valve clearance
▼▼▼▼▼▼▼▼▼▼▼▼▼▼▼▼▼▼▼▼▼▼▼▼▼▼▼▼▼▼▼▼
a. Remove the camshaft (intake and exhaust).
Refer to “CAMSHAFT” on page 5-11.
b. Remove the valve lifter “2” and the adjusting
pad “3” with a valve lapper “1”.
TIP
• Place a cloth in the timing chain space to pre-
vent adjusting pads from falling into the crank-
case.
• Identity each valve lifter and adjusting pad po-
sition very carefully so that they can be rein-
stalled in their original place.
b
a
dc
ee
Valve lapper
90890-04101
Valve lapping tool
YM-A8998
1
1
32
Page 105 of 356
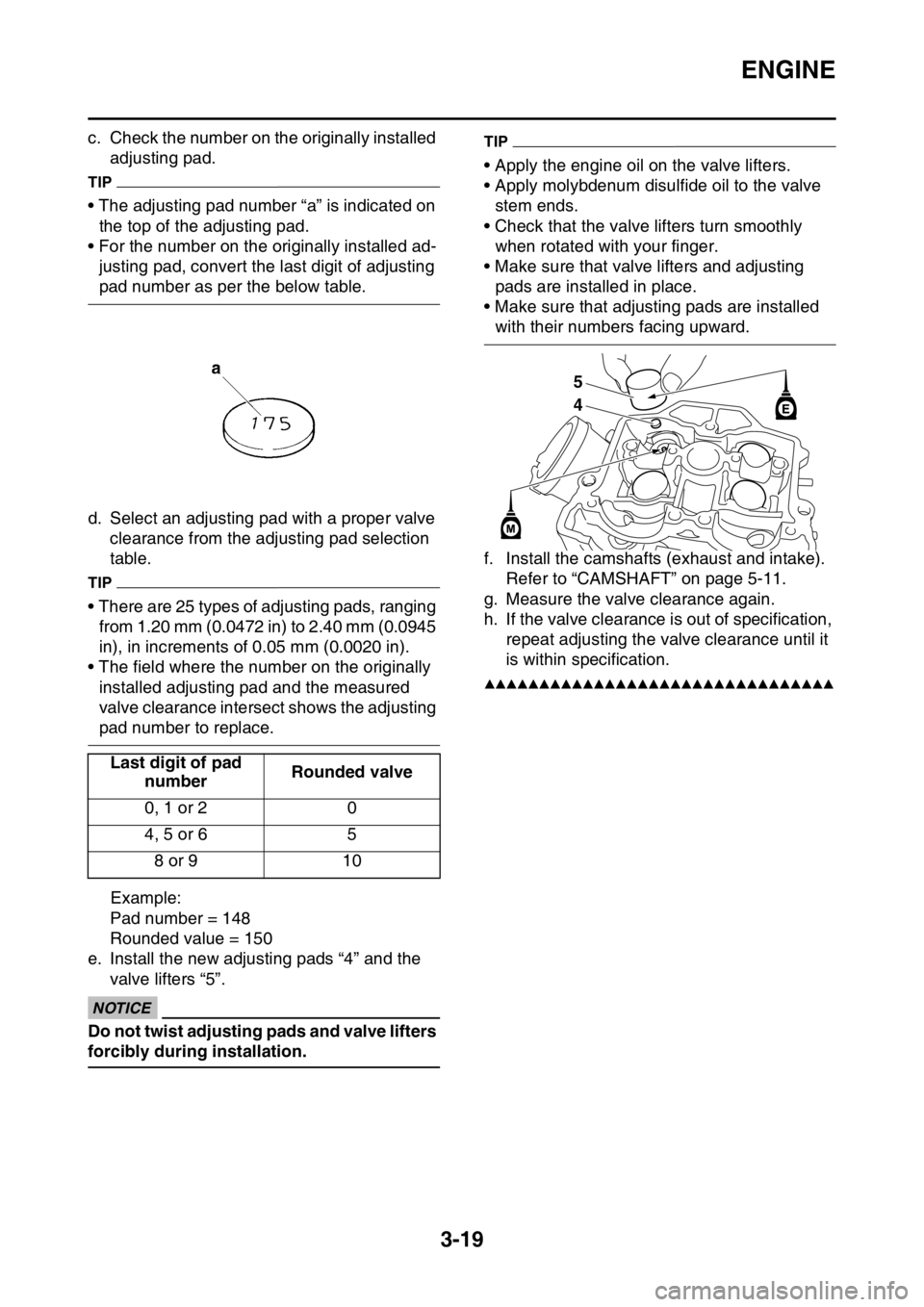
ENGINE
3-19
c. Check the number on the originally installed
adjusting pad.
TIP
• The adjusting pad number “a” is indicated on
the top of the adjusting pad.
• For the number on the originally installed ad-
justing pad, convert the last digit of adjusting
pad number as per the below table.
d. Select an adjusting pad with a proper valve
clearance from the adjusting pad selection
table.
TIP
• There are 25 types of adjusting pads, ranging
from 1.20 mm (0.0472 in) to 2.40 mm (0.0945
in), in increments of 0.05 mm (0.0020 in).
• The field where the number on the originally
installed adjusting pad and the measured
valve clearance intersect shows the adjusting
pad number to replace.
Example:
Pad number = 148
Rounded value = 150
e. Install the new adjusting pads “4” and the
valve lifters “5”.
ECA@
NOTICE
Do not twist adjusting pads and valve lifters
forcibly during installation.
TIP
• Apply the engine oil on the valve lifters.
• Apply molybdenum disulfide oil to the valve
stem ends.
• Check that the valve lifters turn smoothly
when rotated with your finger.
• Make sure that valve lifters and adjusting
pads are installed in place.
• Make sure that adjusting pads are installed
with their numbers facing upward.
f. Install the camshafts (exhaust and intake).
Refer to “CAMSHAFT” on page 5-11.
g. Measure the valve clearance again.
h. If the valve clearance is out of specification,
repeat adjusting the valve clearance until it
is within specification.
▲▲▲▲▲▲▲▲▲▲▲▲▲▲▲▲▲▲▲▲▲▲▲▲▲▲▲▲▲▲▲▲
Last digit of pad
numberRounded valve
0, 1 or 2 0
4, 5 or 6 5
8 or 9 10
4 5
Page 106 of 356
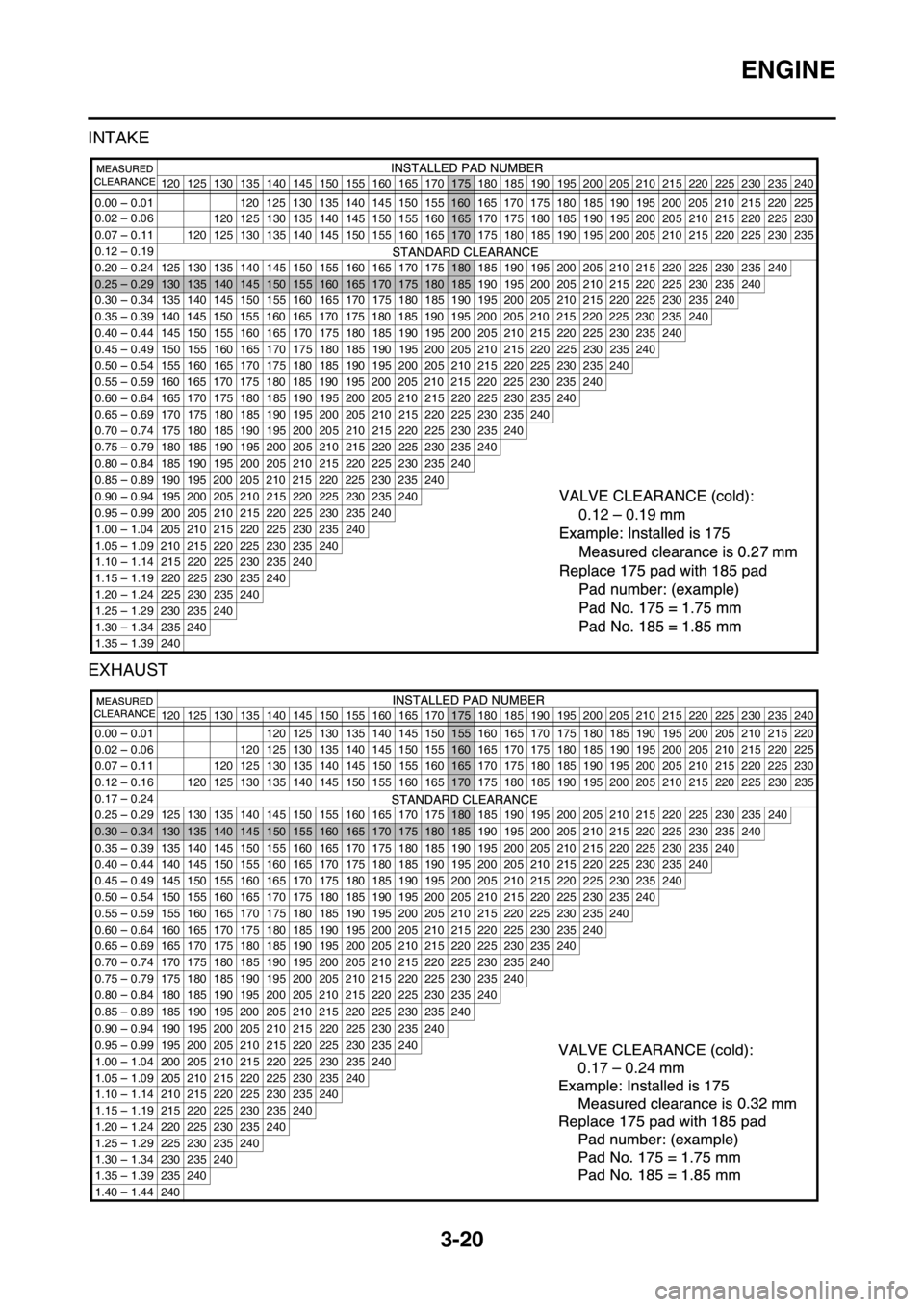
ENGINE
3-20
INTAKE
EXHAUST
120 125 130 135 140 145 150 155 160 165 170175 180 185 190 195 200 205 210 215 220 225 230 235 240
0.02
0.06 0.00 0.01
120 125 130 135 140 145 150 155160165 170 175 180 185 190 195 200 205 210 215 220 225 230 120 125 130 135 140 145 150 155 160 165 170 175 180 185 190 195 200 205 210 215 220 225
0.07
0.11120 125 130 135 140 145 150 155 160 165170 175 180 185 190 195 200 205 210 215 220 225 230 235
0.12
0.19
0.20
0.24125130135140145150155160165170175180 185 190 195 200 205 210 215 220 225 230 235240
0.250.29130135140145150155160165170175180185 190 195 200 205 210 215 220 225 230 235240
0.30 0.34 135 140 145 150 155 160 165 170 175 180 185 190 195 200 205 210 215 220 225 230 235240
0.35 0.39 140 145 150 155 160 165 170 175 180 185 190 195 200 205 210 215 220 225 230 235240
0.40 0.44 145 150 155 160 165 170 175 180 185 190 195 200 205 210 215 220 225 230 235240
0.45 0.49 150 155 160 165 170 175 180 185 190 195 200 205 210 215 220 225 230 235240
0.50 0.54 155 160 165 170 175 180 185 190 195 200 205 210 215 220 225 230 235240
0.55 0.59 160 165 170 175 180 185 190 195 200 205 210 215 220 225 230 235240
0.600.64 165 170 175 180 185 190 195 200 205 210 215 220 225 230 235240
0.65 0.69 170 175 180 185 190 195 200 205 210 215 220 225 230 235240
0.70 0.74 175 180 185 190 195 200 205 210 215 220 225 230 235240
0.75 0.79 180 185 190 195 200 205 210 215 220 225 230 235240
0.80 0.84 185 190 195 200 205 210 215 220 225 230 235240
0.85 0.89 190 195 200 205 210 215 220 225 230 235240
0.90 0.94 195 200 205 210 215 220 225 230 235240
0.95 0.99 200 205 210 215 220 225 230 235240
1.001.04 205 210 215 220 225 230 235240
1.05 1.09 210 215 220 225 230 235240
1.10 1.14 215 220 225 230 235240
1.15 1.19 220 225 230 235240
1.20 1.24 225 230 235240
1.25 1.29 230 235240
1.30 1.34 235240
1.35 1.39 240
0.19
0.12
120 125 130 135 140 145 150 155 160 165 170175 180 185 190 195 200 205 210 215 220 225 230 235 240
0.00
0.01 120 125 130 135 140 145150155 160 165 170 175 180 185 190 195 200 205 210 215 220
0.02
0.06120 125 130 135 140 145 150 155160 165 170 175 180 185 190 195 200 205 210 215 220 225
0.07
0.11120 125 130 135 140 145 150 155 160165 170 175 180 185 190 195 200 205 210 215 220 225 230
0.12 0.16120125130135140145150155160165170 175 180 185 190 195 200 205 210 215 220 225230235
0.17
0.24
0.25 0.29 125 130 135 140 145 150 155 160 165 170 175180 185 190 195 200 205 210 215 220 225230235240
0.30 0.34130135140145150155160165170175180185 190 195 200 205 210 215 220 225230235240
0.35 0.39 135 140 145 150 155 160 165 170 175 180 185 190 195 200 205 210 215 220 225230235240
0.40 0.44 140 145 150 155 160 165 170 175 180 185 190 195 200 205 210 215 220 225230235240
0.45 0.49 145 150 155 160 165 170 175 180 185 190 195 200 205 210 215 220 225230235240
0.50 0.54 150 155 160 165 170 175 180 185 190 195 200 205 210 215 220 225230235240
0.55 0.59 155 160 165 170 175 180 185 190 195 200 205 210 215 220 225230235240
0.60 0.64 160 165 170 175 180 185 190 195 200 205 210 215 220 225230235240
0.65 0.69 165 170 175 180 185 190 195 200 205 210 215 220 225230235240
0.70 0.74 170 175 180 185 190 195 200 205 210 215 220 225230235240
0.75 0.79 175 180 185 190 195 200 205 210 215 220 225230235240
0.80 0.84 180 185 190 195 200 205 210 215 220 225230235240
0.85 0.89 185 190 195 200 205 210 215 220 225230235240
0.90 0.94 190 195 200 205 210 215 220 225230235240
0.95 0.99 195 200 205 210 215 220 225230235240
1.00 1.04 200 205 210 215 220 225230235240
1.05 1.09 205 210 215 220 225230235240
1.10 1.14 210 215 220 225230235240
1.15 1.19 215 220 225230235240
1.20 1.24 220 225230235240
1.25 1.29 225230235240
1.30 1.34 230235240
1.35 1.39 235240
1.40 1.44 240
0.24
0.17
Page 107 of 356
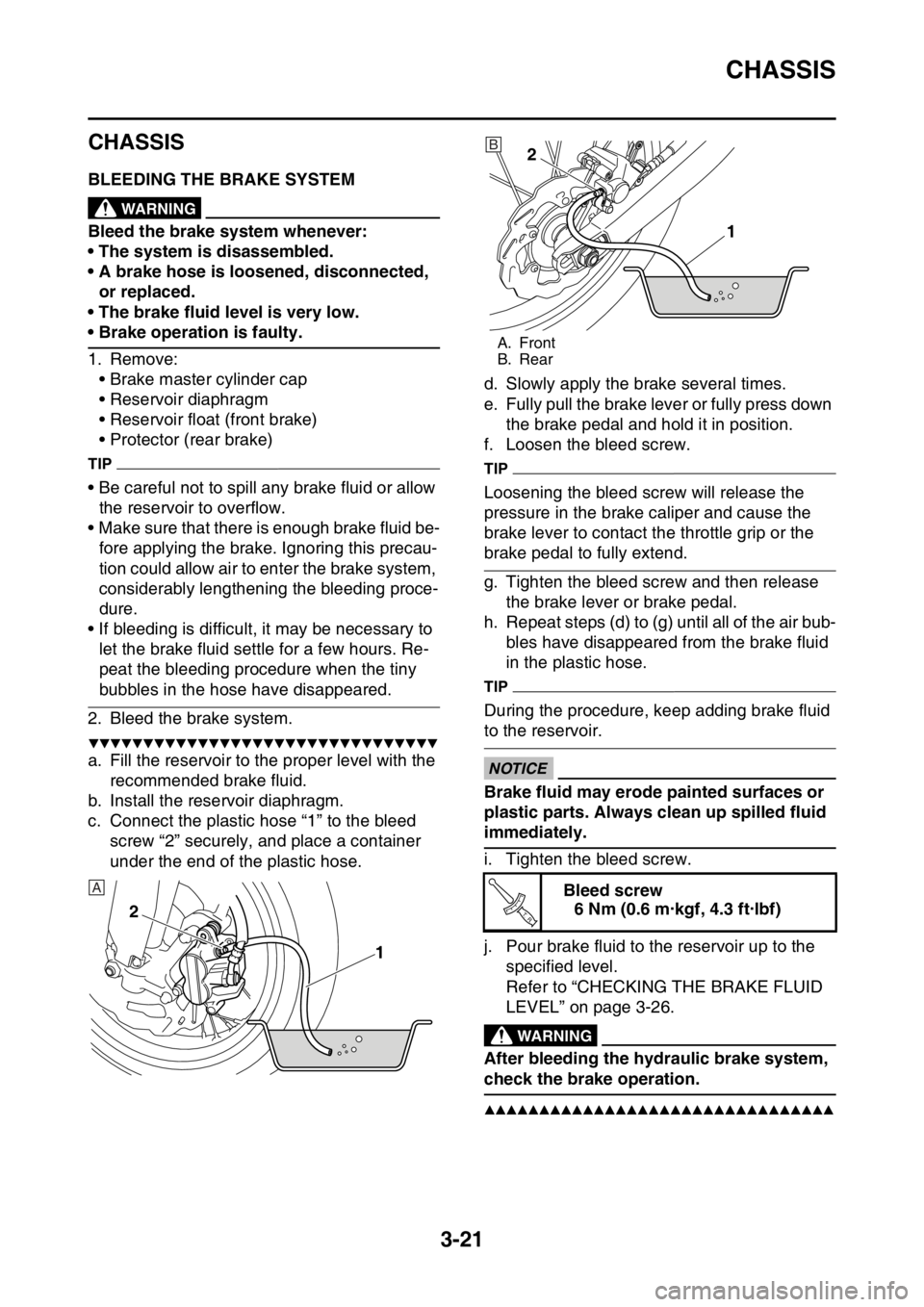
CHASSIS
3-21
EAS1SM5090
CHASSIS
EAS1SM5091BLEEDING THE BRAKE SYSTEMEWA13100
WARNING
Bleed the brake system whenever:
• The system is disassembled.
• A brake hose is loosened, disconnected,
or replaced.
• The brake fluid level is very low.
• Brake operation is faulty.
1. Remove:
• Brake master cylinder cap
• Reservoir diaphragm
• Reservoir float (front brake)
• Protector (rear brake)
TIP
• Be careful not to spill any brake fluid or allow
the reservoir to overflow.
• Make sure that there is enough brake fluid be-
fore applying the brake. Ignoring this precau-
tion could allow air to enter the brake system,
considerably lengthening the bleeding proce-
dure.
• If bleeding is difficult, it may be necessary to
let the brake fluid settle for a few hours. Re-
peat the bleeding procedure when the tiny
bubbles in the hose have disappeared.
2. Bleed the brake system.
▼▼▼▼▼▼▼▼▼▼▼▼▼▼▼▼▼▼▼▼▼▼▼▼▼▼▼▼▼▼▼▼
a. Fill the reservoir to the proper level with the
recommended brake fluid.
b. Install the reservoir diaphragm.
c. Connect the plastic hose “1” to the bleed
screw “2” securely, and place a container
under the end of the plastic hose.d. Slowly apply the brake several times.
e. Fully pull the brake lever or fully press down
the brake pedal and hold it in position.
f. Loosen the bleed screw.
TIP
Loosening the bleed screw will release the
pressure in the brake caliper and cause the
brake lever to contact the throttle grip or the
brake pedal to fully extend.
g. Tighten the bleed screw and then release
the brake lever or brake pedal.
h. Repeat steps (d) to (g) until all of the air bub-
bles have disappeared from the brake fluid
in the plastic hose.
TIP
During the procedure, keep adding brake fluid
to the reservoir.
ECA
NOTICE
Brake fluid may erode painted surfaces or
plastic parts. Always clean up spilled fluid
immediately.
i. Tighten the bleed screw.
j. Pour brake fluid to the reservoir up to the
specified level.
Refer to “CHECKING THE BRAKE FLUID
LEVEL” on page 3-26.
EWA13110
WARNING
After bleeding the hydraulic brake system,
check the brake operation.
▲▲▲▲▲▲▲▲▲▲▲▲▲▲▲▲▲▲▲▲▲▲▲▲▲▲▲▲▲▲▲▲
1 2
A
A. Front
B. Rear
Bleed screw
6 Nm (0.6 m·kgf, 4.3 ft·lbf)
2
1B
T R..
Page 108 of 356
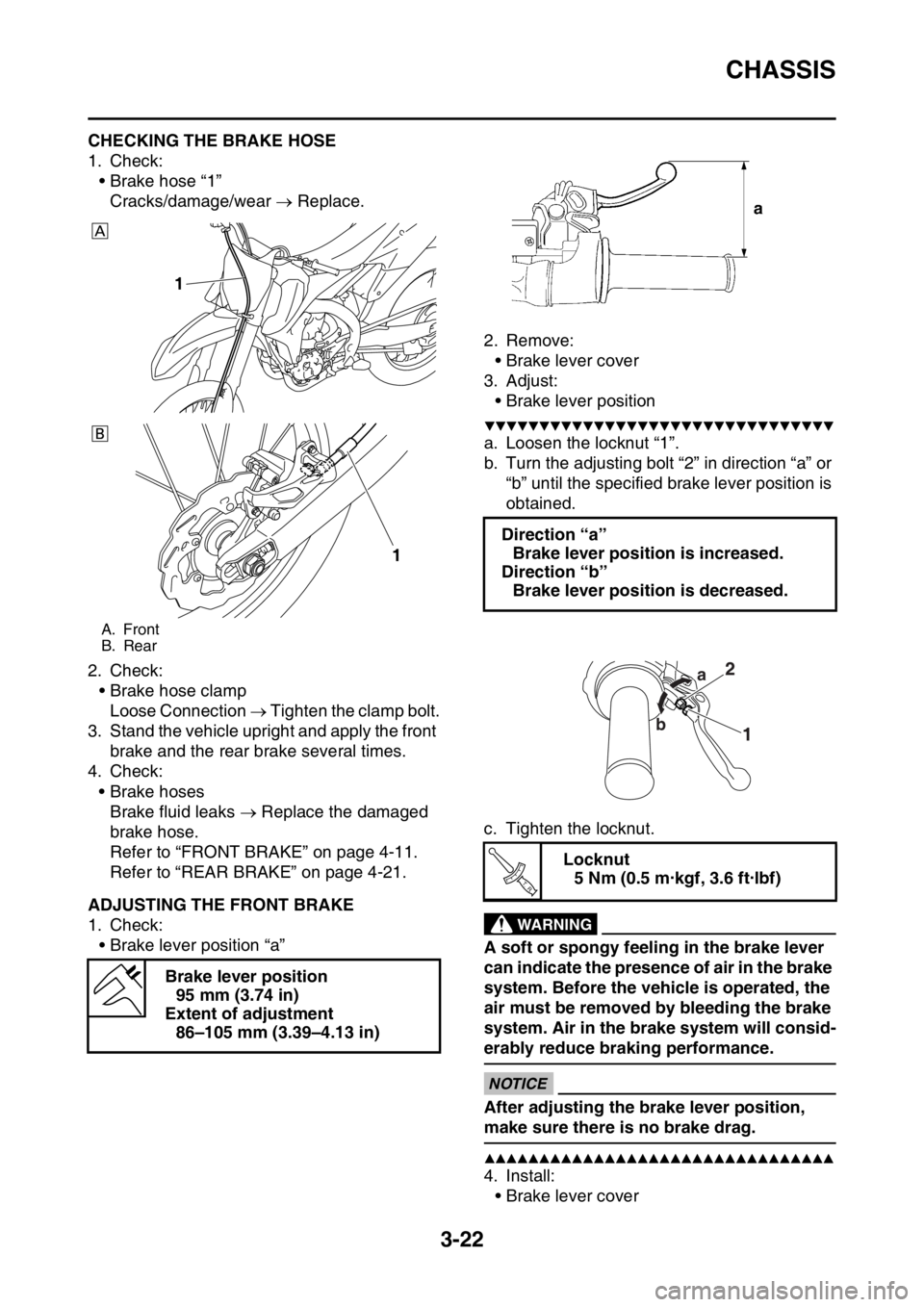
CHASSIS
3-22
EAS1SM5092CHECKING THE BRAKE HOSE
1. Check:
• Brake hose “1”
Cracks/damage/wear Replace.
2. Check:
• Brake hose clamp
Loose Connection Tighten the clamp bolt.
3. Stand the vehicle upright and apply the front
brake and the rear brake several times.
4. Check:
• Brake hoses
Brake fluid leaks Replace the damaged
brake hose.
Refer to “FRONT BRAKE” on page 4-11.
Refer to “REAR BRAKE” on page 4-21.
EAS1SM5093ADJUSTING THE FRONT BRAKE
1. Check:
• Brake lever position “a”2. Remove:
• Brake lever cover
3. Adjust:
• Brake lever position
▼▼▼▼▼▼▼▼▼▼▼▼▼▼▼▼▼▼▼▼▼▼▼▼▼▼▼▼▼▼▼▼
a. Loosen the locknut “1”.
b. Turn the adjusting bolt “2” in direction “a” or
“b” until the specified brake lever position is
obtained.
c. Tighten the locknut.
EWA13050
WARNING
A soft or spongy feeling in the brake lever
can indicate the presence of air in the brake
system. Before the vehicle is operated, the
air must be removed by bleeding the brake
system. Air in the brake system will consid-
erably reduce braking performance.
ECA13490
NOTICE
After adjusting the brake lever position,
make sure there is no brake drag.
▲▲▲▲▲▲▲▲▲▲▲▲▲▲▲▲▲▲▲▲▲▲▲▲▲▲▲▲▲▲▲▲
4. Install:
• Brake lever cover
A. Front
B. Rear
Brake lever position
95 mm (3.74 in)
Extent of adjustment
86–105 mm (3.39–4.13 in)
1
1
Direction “a”
Brake lever position is increased.
Direction “b”
Brake lever position is decreased.
Locknut
5 Nm (0.5 m·kgf, 3.6 ft·lbf)
a
b
T R..
Page 109 of 356
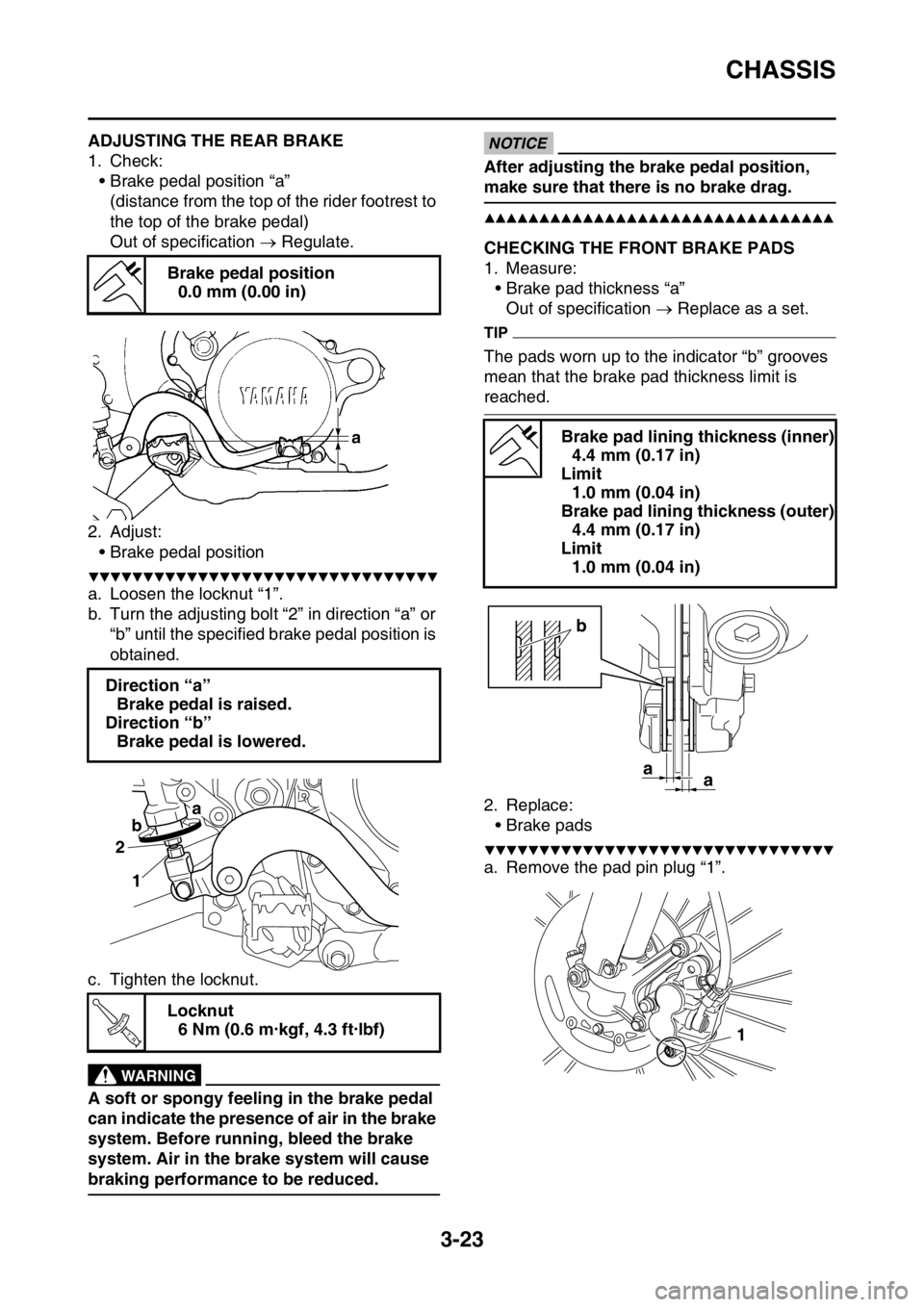
CHASSIS
3-23
EAS1SM5094ADJUSTING THE REAR BRAKE
1. Check:
• Brake pedal position “a”
(distance from the top of the rider footrest to
the top of the brake pedal)
Out of specification Regulate.
2. Adjust:
• Brake pedal position
▼▼▼▼▼▼▼▼▼▼▼▼▼▼▼▼▼▼▼▼▼▼▼▼▼▼▼▼▼▼▼▼
a. Loosen the locknut “1”.
b. Turn the adjusting bolt “2” in direction “a” or
“b” until the specified brake pedal position is
obtained.
c. Tighten the locknut.
EWA1DX1001
WARNING
A soft or spongy feeling in the brake pedal
can indicate the presence of air in the brake
system. Before running, bleed the brake
system. Air in the brake system will cause
braking performance to be reduced.
ECA13510
NOTICE
After adjusting the brake pedal position,
make sure that there is no brake drag.
▲▲▲▲▲▲▲▲▲▲▲▲▲▲▲▲▲▲▲▲▲▲▲▲▲▲▲▲▲▲▲▲
EAS1SM5095CHECKING THE FRONT BRAKE PADS
1. Measure:
• Brake pad thickness “a”
Out of specification Replace as a set.
TIP
The pads worn up to the indicator “b” grooves
mean that the brake pad thickness limit is
reached.
2. Replace:
• Brake pads
▼▼▼▼▼▼▼▼▼▼▼▼▼▼▼▼▼▼▼▼▼▼▼▼▼▼▼▼▼▼▼▼
a. Remove the pad pin plug “1”. Brake pedal position
0.0 mm (0.00 in)
Direction “a”
Brake pedal is raised.
Direction “b”
Brake pedal is lowered.
Locknut
6 Nm (0.6 m·kgf, 4.3 ft·lbf)1 2
a
b
T R..
Brake pad lining thickness (inner)
4.4 mm (0.17 in)
Limit
1.0 mm (0.04 in)
Brake pad lining thickness (outer)
4.4 mm (0.17 in)
Limit
1.0 mm (0.04 in)
a
b
a
1
Page 110 of 356
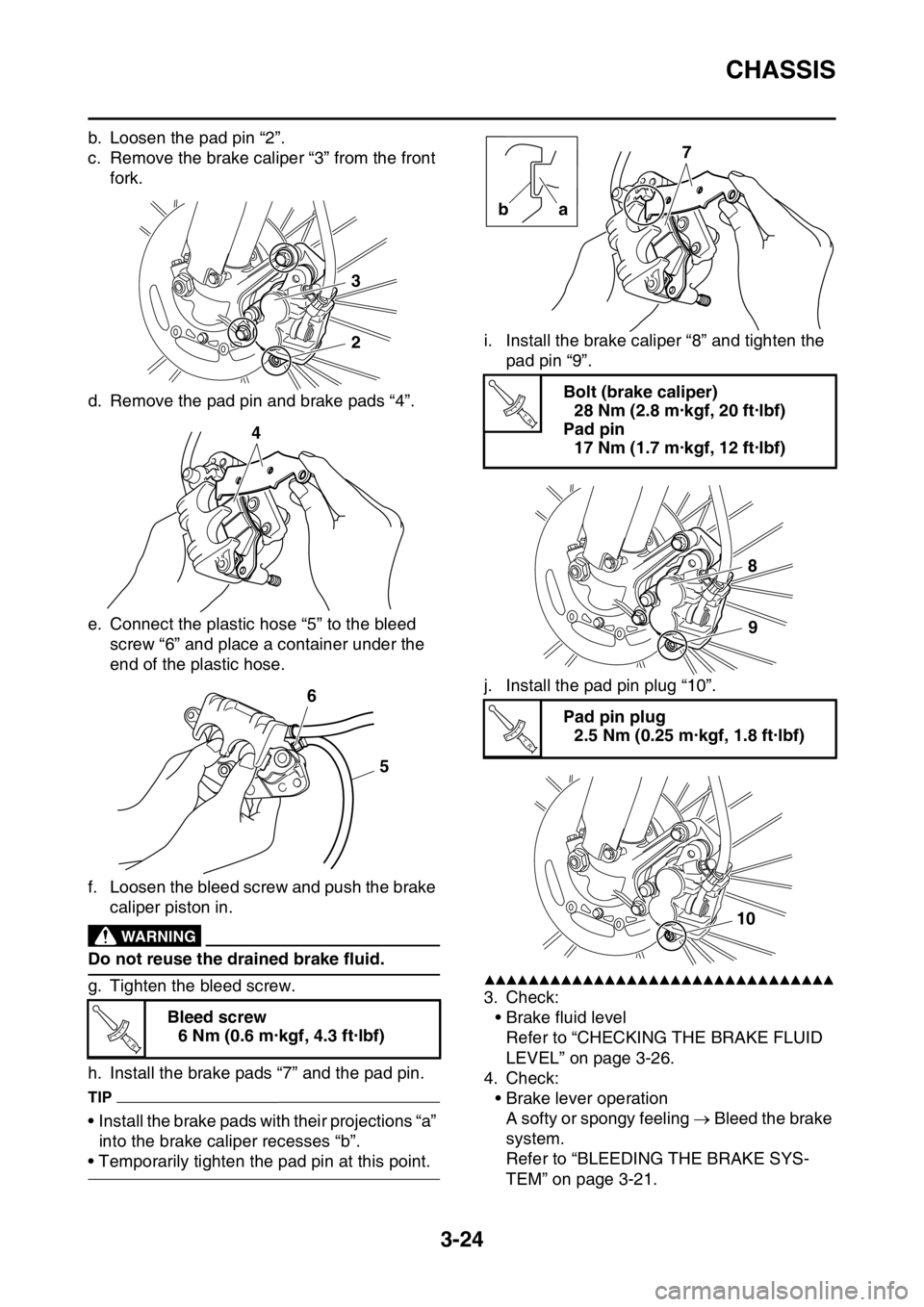
CHASSIS
3-24
b. Loosen the pad pin “2”.
c. Remove the brake caliper “3” from the front
fork.
d. Remove the pad pin and brake pads “4”.
e. Connect the plastic hose “5” to the bleed
screw “6” and place a container under the
end of the plastic hose.
f. Loosen the bleed screw and push the brake
caliper piston in.
EWA@
WARNING
Do not reuse the drained brake fluid.
g. Tighten the bleed screw.
h. Install the brake pads “7” and the pad pin.
TIP
• Install the brake pads with their projections “a”
into the brake caliper recesses “b”.
• Temporarily tighten the pad pin at this point.i. Install the brake caliper “8” and tighten the
pad pin “9”.
j. Install the pad pin plug “10”.
▲▲▲▲▲▲▲▲▲▲▲▲▲▲▲▲▲▲▲▲▲▲▲▲▲▲▲▲▲▲▲▲
3. Check:
• Brake fluid level
Refer to “CHECKING THE BRAKE FLUID
LEVEL” on page 3-26.
4. Check:
• Brake lever operation
A softy or spongy feeling Bleed the brake
system.
Refer to “BLEEDING THE BRAKE SYS-
TEM” on page 3-21. Bleed screw
6 Nm (0.6 m·kgf, 4.3 ft·lbf)
3
2
4
6
5
T R..
Bolt (brake caliper)
28 Nm (2.8 m·kgf, 20 ft·lbf)
Pad pin
17 Nm (1.7 m·kgf, 12 ft·lbf)
Pad pin plug
2.5 Nm (0.25 m·kgf, 1.8 ft·lbf)
7
a b
T R..
8
9
T R..
10