YAMAHA YZ250F 2015 Owners Manual
Manufacturer: YAMAHA, Model Year: 2015, Model line: YZ250F, Model: YAMAHA YZ250F 2015Pages: 356, PDF Size: 11.39 MB
Page 161 of 356
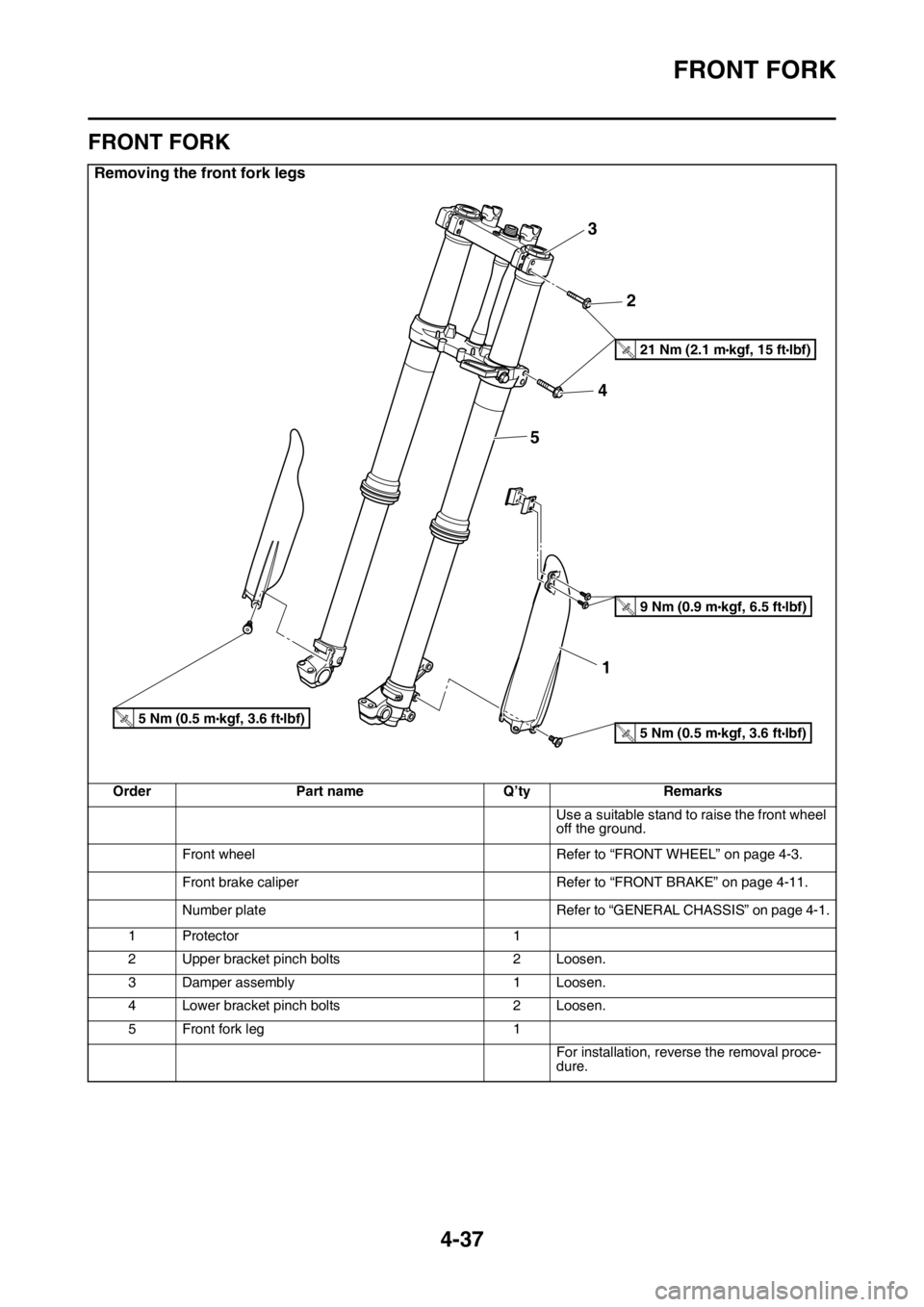
FRONT FORK
4-37
EAS1SM5166
FRONT FORK
Removing the front fork legs
Order Part name Q’ty Remarks
Use a suitable stand to raise the front wheel
off the ground.
Front wheel Refer to “FRONT WHEEL” on page 4-3.
Front brake caliper Refer to “FRONT BRAKE” on page 4-11.
Number plate Refer to “GENERAL CHASSIS” on page 4-1.
1 Protector 1
2 Upper bracket pinch bolts 2 Loosen.
3 Damper assembly 1 Loosen.
4 Lower bracket pinch bolts 2 Loosen.
5 Front fork leg 1
For installation, reverse the removal proce-
dure.
3
2
4
5
1
T.R.21 Nm (2.1 mlbf) kgf, 15 ft
T.R.9 Nm (0.9 mlbf) kgf, 6.5 ft
T.R.5 Nm (0.5 mlbf) kgf, 3.6 ftT.R.5 Nm (0.5 mlbf) kgf, 3.6 ft
Page 162 of 356
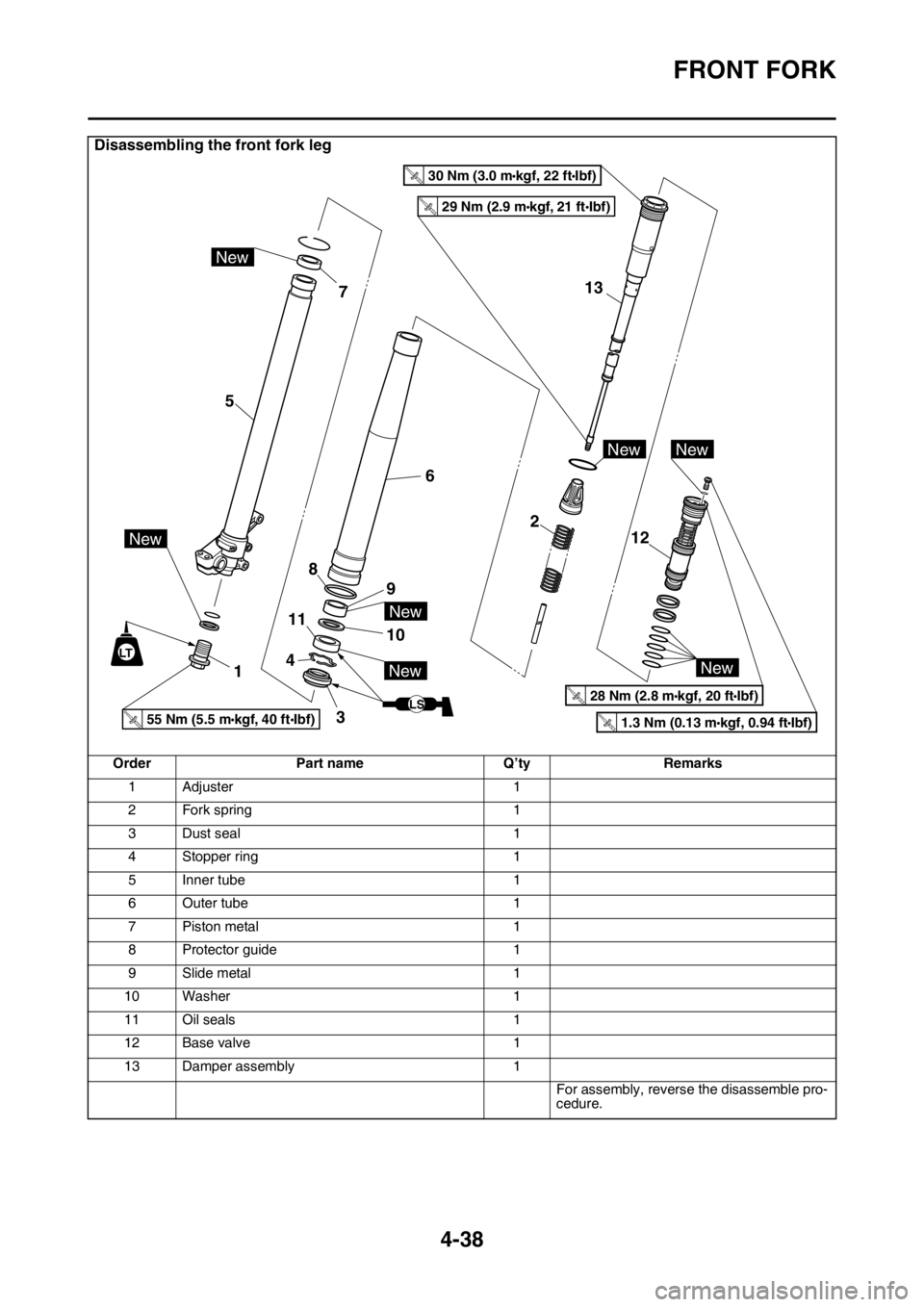
FRONT FORK
4-38
Disassembling the front fork leg
Order Part name Q’ty Remarks
1Adjuster 1
2 Fork spring 1
3 Dust seal 1
4 Stopper ring 1
5 Inner tube 1
6 Outer tube 1
7 Piston metal 1
8Protector guide 1
9 Slide metal 1
10 Washer 1
11 Oil seals 1
12 Base valve 1
13 Damper assembly 1
For assembly, reverse the disassemble pro-
cedure.
LS
13
2 6
9 8
10 11
4
3 1 57
12
New
NewNew
New
New
New
New
LT
29 Nm (2.9 mkgf, 21 ftIbf)T.R.
55 Nm (5.5 mkgf, 40 ftIbf)T.R.1.3 Nm (0.13 mkgf, 0.94 ftIbf)T.R.
28 Nm (2.8 mkgf, 20 ftIbf)T.R.
30 Nm (3.0 mkgf, 22 ftIbf)T.R.
Page 163 of 356
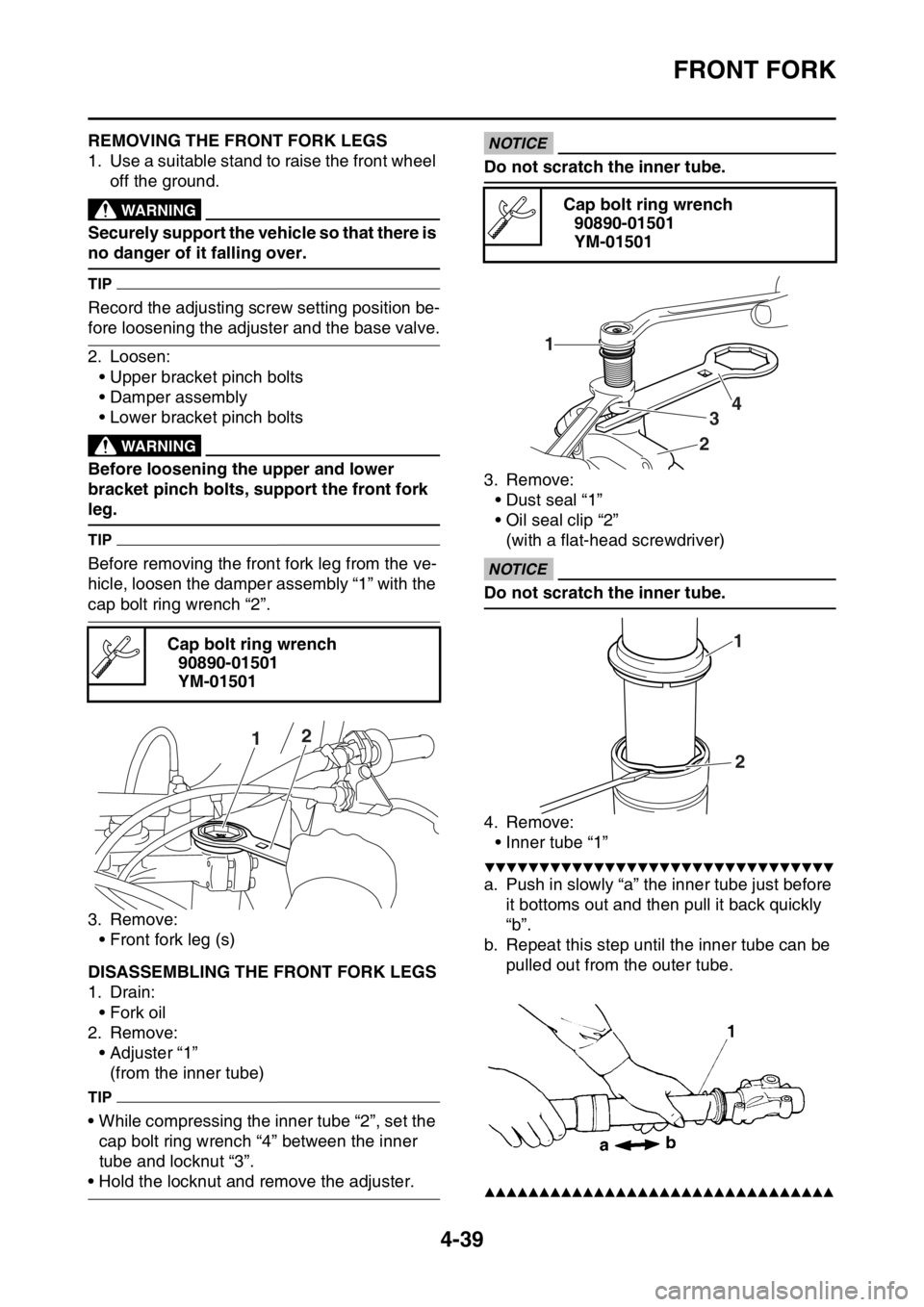
FRONT FORK
4-39
EAS1SM5167REMOVING THE FRONT FORK LEGS
1. Use a suitable stand to raise the front wheel
off the ground.
EWA13120
WARNING
Securely support the vehicle so that there is
no danger of it falling over.
TIP
Record the adjusting screw setting position be-
fore loosening the adjuster and the base valve.
2. Loosen:
• Upper bracket pinch bolts
• Damper assembly
• Lower bracket pinch bolts
EWA13640
WARNING
Before loosening the upper and lower
bracket pinch bolts, support the front fork
leg.
TIP
Before removing the front fork leg from the ve-
hicle, loosen the damper assembly “1” with the
cap bolt ring wrench “2”.
3. Remove:
• Front fork leg (s)
EAS1SM5168DISASSEMBLING THE FRONT FORK LEGS
1. Drain:
• Fork oil
2. Remove:
• Adjuster “1”
(from the inner tube)
TIP
• While compressing the inner tube “2”, set the
cap bolt ring wrench “4” between the inner
tube and locknut “3”.
• Hold the locknut and remove the adjuster.
ECA14180
NOTICE
Do not scratch the inner tube.
3. Remove:
• Dust seal “1”
• Oil seal clip “2”
(with a flat-head screwdriver)
ECA14180
NOTICE
Do not scratch the inner tube.
4. Remove:
• Inner tube “1”
▼▼▼▼▼▼▼▼▼▼▼▼▼▼▼▼▼▼▼▼▼▼▼▼▼▼▼▼▼▼▼▼
a. Push in slowly “a” the inner tube just before
it bottoms out and then pull it back quickly
“b”.
b. Repeat this step until the inner tube can be
pulled out from the outer tube.
▲▲▲▲▲▲▲▲▲▲▲▲▲▲▲▲▲▲▲▲▲▲▲▲▲▲▲▲▲▲▲▲
Cap bolt ring wrench
90890-01501
YM-01501
12
Cap bolt ring wrench
90890-01501
YM-01501
1
234
1
2
Page 164 of 356
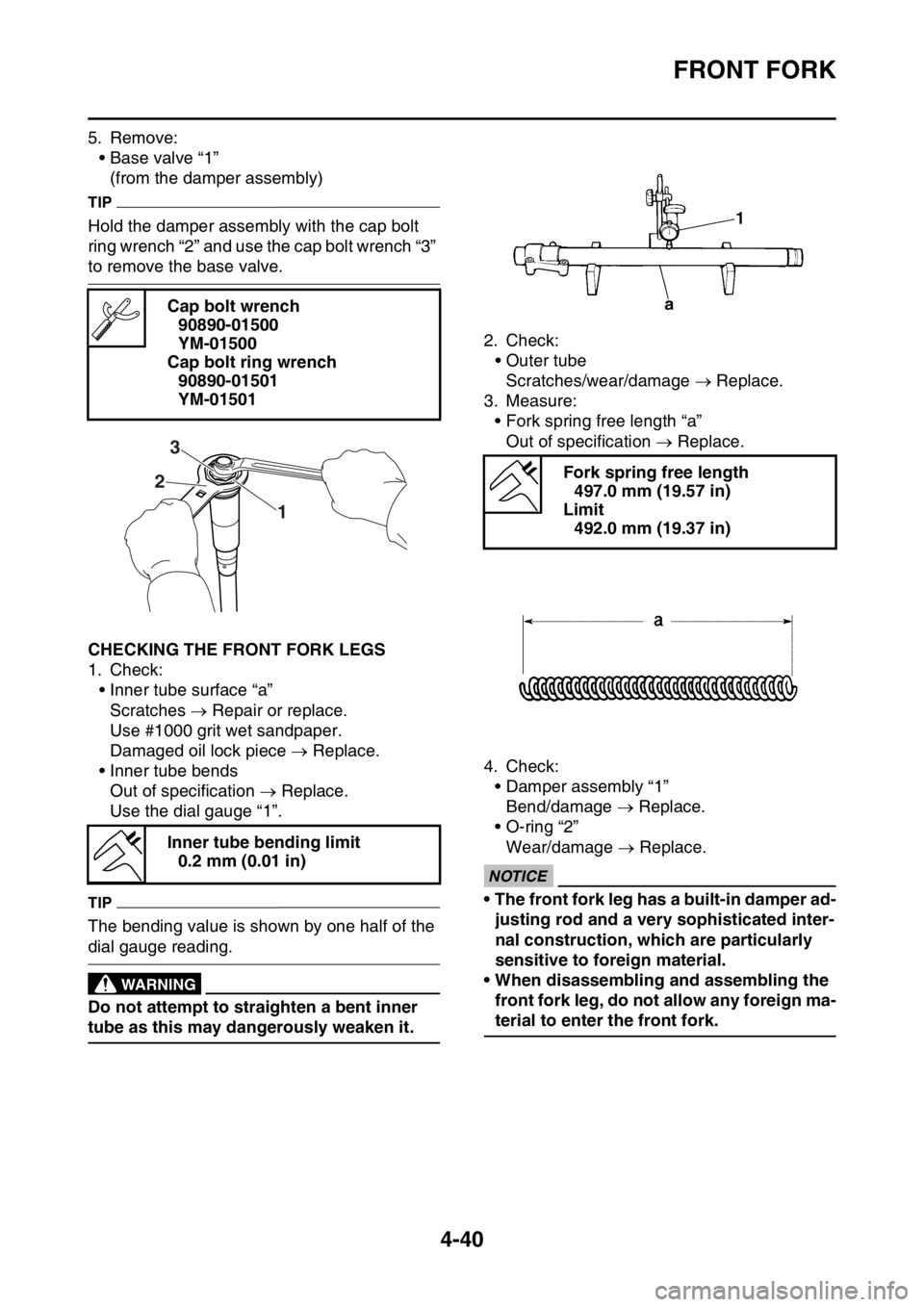
FRONT FORK
4-40
5. Remove:
• Base valve “1”
(from the damper assembly)
TIP
Hold the damper assembly with the cap bolt
ring wrench “2” and use the cap bolt wrench “3”
to remove the base valve.
EAS1SM5169CHECKING THE FRONT FORK LEGS
1. Check:
• Inner tube surface “a”
Scratches Repair or replace.
Use #1000 grit wet sandpaper.
Damaged oil lock piece Replace.
• Inner tube bends
Out of specification Replace.
Use the dial gauge “1”.
TIP
The bending value is shown by one half of the
dial gauge reading.
EWA13650
WARNING
Do not attempt to straighten a bent inner
tube as this may dangerously weaken it.2. Check:
• Outer tube
Scratches/wear/damage Replace.
3. Measure:
• Fork spring free length “a”
Out of specification Replace.
4. Check:
• Damper assembly “1”
Bend/damage Replace.
• O-ring “2”
Wear/damage Replace.
ECA1DX1010
NOTICE
• The front fork leg has a built-in damper ad-
justing rod and a very sophisticated inter-
nal construction, which are particularly
sensitive to foreign material.
• When disassembling and assembling the
front fork leg, do not allow any foreign ma-
terial to enter the front fork. Cap bolt wrench
90890-01500
YM-01500
Cap bolt ring wrench
90890-01501
YM-01501
Inner tube bending limit
0.2 mm (0.01 in)
1 23
Fork spring free length
497.0 mm (19.57 in)
Limit
492.0 mm (19.37 in)
Page 165 of 356
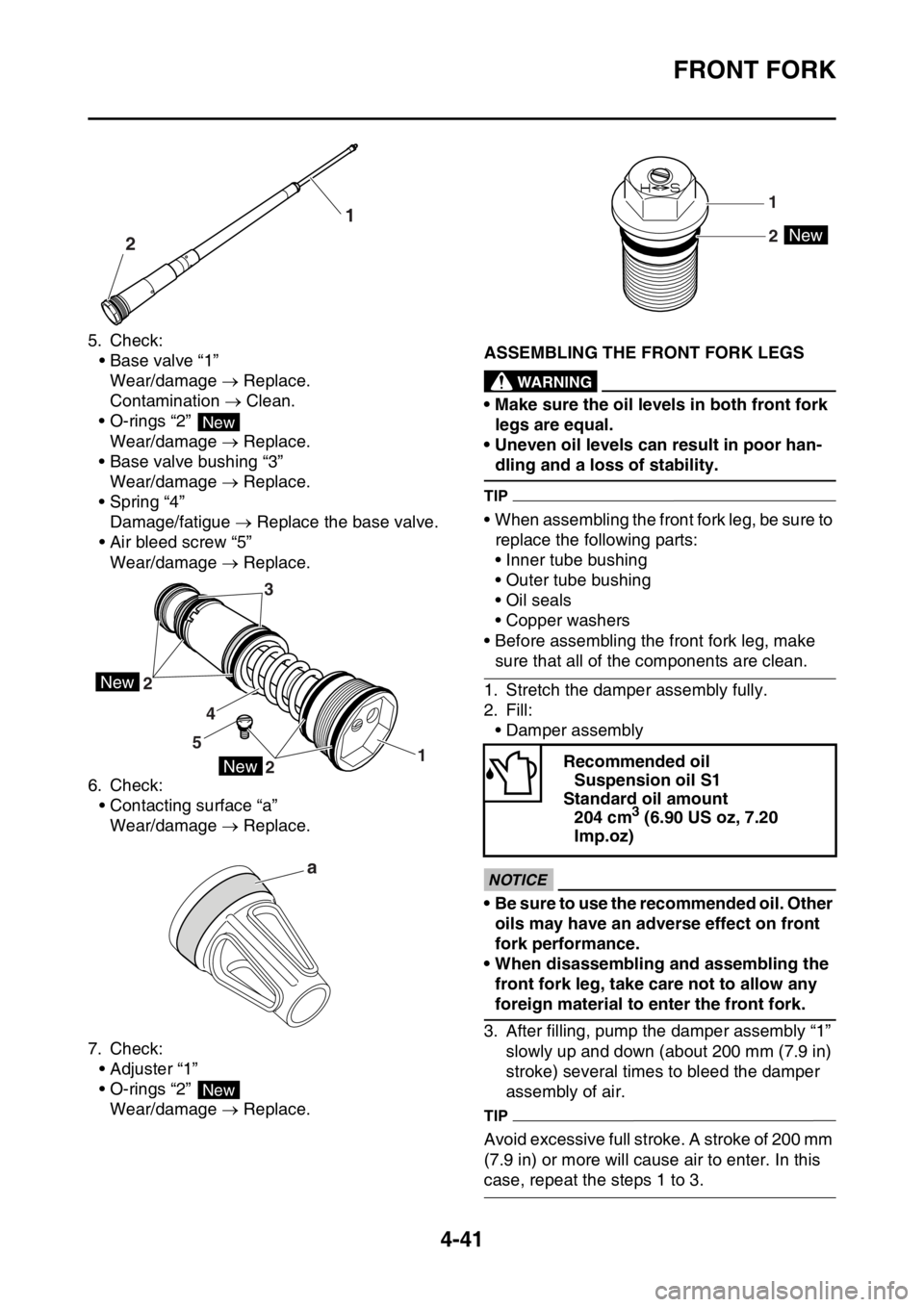
FRONT FORK
4-41
5. Check:
• Base valve “1”
Wear/damage Replace.
Contamination Clean.
• O-rings “2”
Wear/damage Replace.
• Base valve bushing “3”
Wear/damage Replace.
• Spring “4”
Damage/fatigue Replace the base valve.
• Air bleed screw “5”
Wear/damage Replace.
6. Check:
• Contacting surface “a”
Wear/damage Replace.
7. Check:
• Adjuster “1”
• O-rings “2”
Wear/damage Replace.EAS1SM5170ASSEMBLING THE FRONT FORK LEGSEWA13660
WARNING
• Make sure the oil levels in both front fork
legs are equal.
• Uneven oil levels can result in poor han-
dling and a loss of stability.
TIP
• When assembling the front fork leg, be sure to
replace the following parts:
• Inner tube bushing
• Outer tube bushing
• Oil seals
• Copper washers
• Before assembling the front fork leg, make
sure that all of the components are clean.
1. Stretch the damper assembly fully.
2. Fill:
• Damper assembly
ECA14210
NOTICE
• Be sure to use the recommended oil. Other
oils may have an adverse effect on front
fork performance.
• When disassembling and assembling the
front fork leg, take care not to allow any
foreign material to enter the front fork.
3. After filling, pump the damper assembly “1”
slowly up and down (about 200 mm (7.9 in)
stroke) several times to bleed the damper
assembly of air.
TIP
Avoid excessive full stroke. A stroke of 200 mm
(7.9 in) or more will cause air to enter. In this
case, repeat the steps 1 to 3.
21
New
New
New
2
21 543
a
New
Recommended oil
Suspension oil S1
Standard oil amount
204 cm
3 (6.90 US oz, 7.20
Imp.oz)
New
1
2
Page 166 of 356
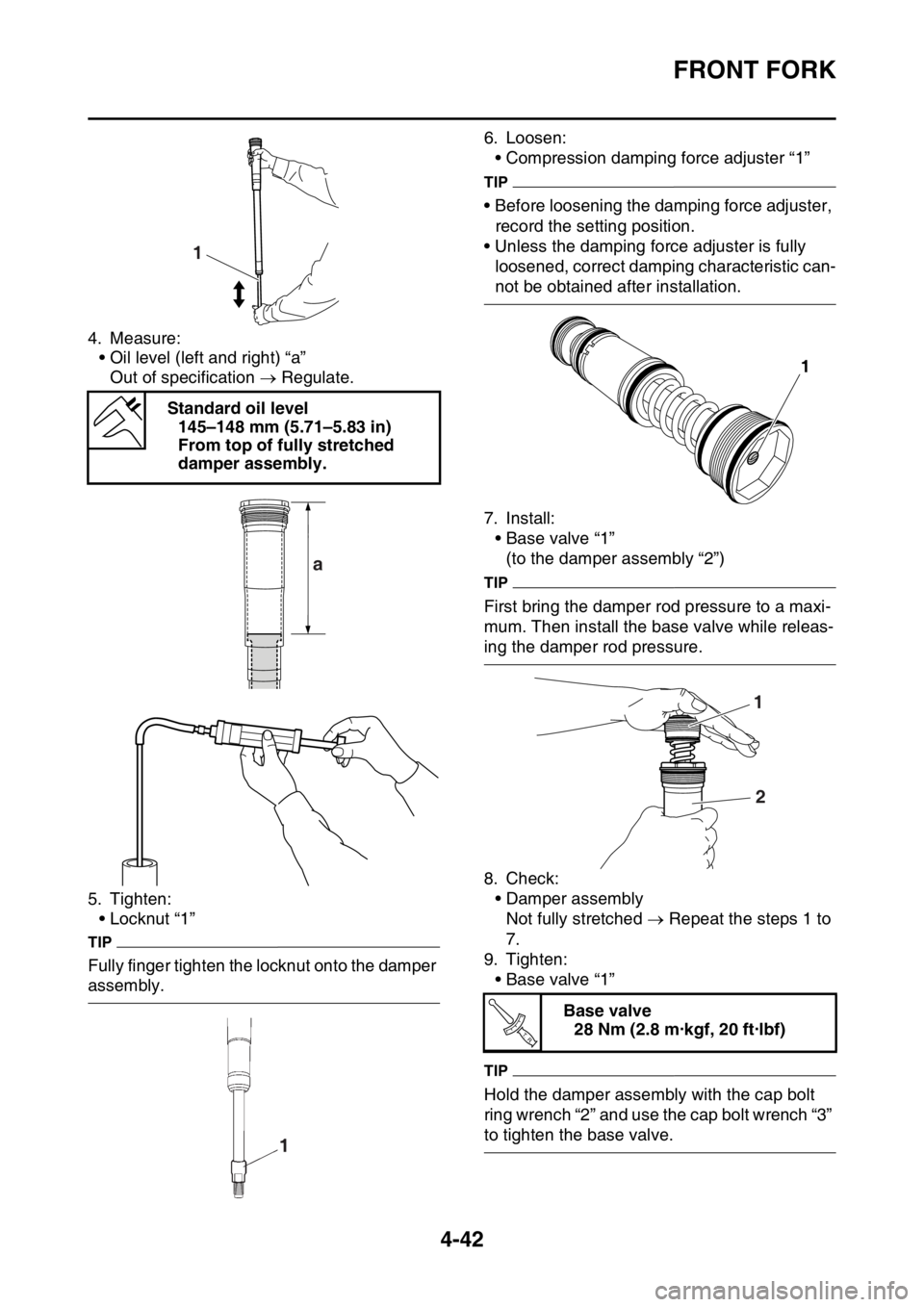
FRONT FORK
4-42
4. Measure:
• Oil level (left and right) “a”
Out of specification Regulate.
5. Tighten:
• Locknut “1”
TIP
Fully finger tighten the locknut onto the damper
assembly.6. Loosen:
• Compression damping force adjuster “1”
TIP
• Before loosening the damping force adjuster,
record the setting position.
• Unless the damping force adjuster is fully
loosened, correct damping characteristic can-
not be obtained after installation.
7. Install:
• Base valve “1”
(to the damper assembly “2”)
TIP
First bring the damper rod pressure to a maxi-
mum. Then install the base valve while releas-
ing the damper rod pressure.
8. Check:
• Damper assembly
Not fully stretched Repeat the steps 1 to
7.
9. Tighten:
• Base valve “1”
TIP
Hold the damper assembly with the cap bolt
ring wrench “2” and use the cap bolt wrench “3”
to tighten the base valve. Standard oil level
145–148 mm (5.71–5.83 in)
From top of fully stretched
damper assembly.
1
a
Base valve
28 Nm (2.8 m·kgf, 20 ft·lbf)
1
1
2
T R..
Page 167 of 356
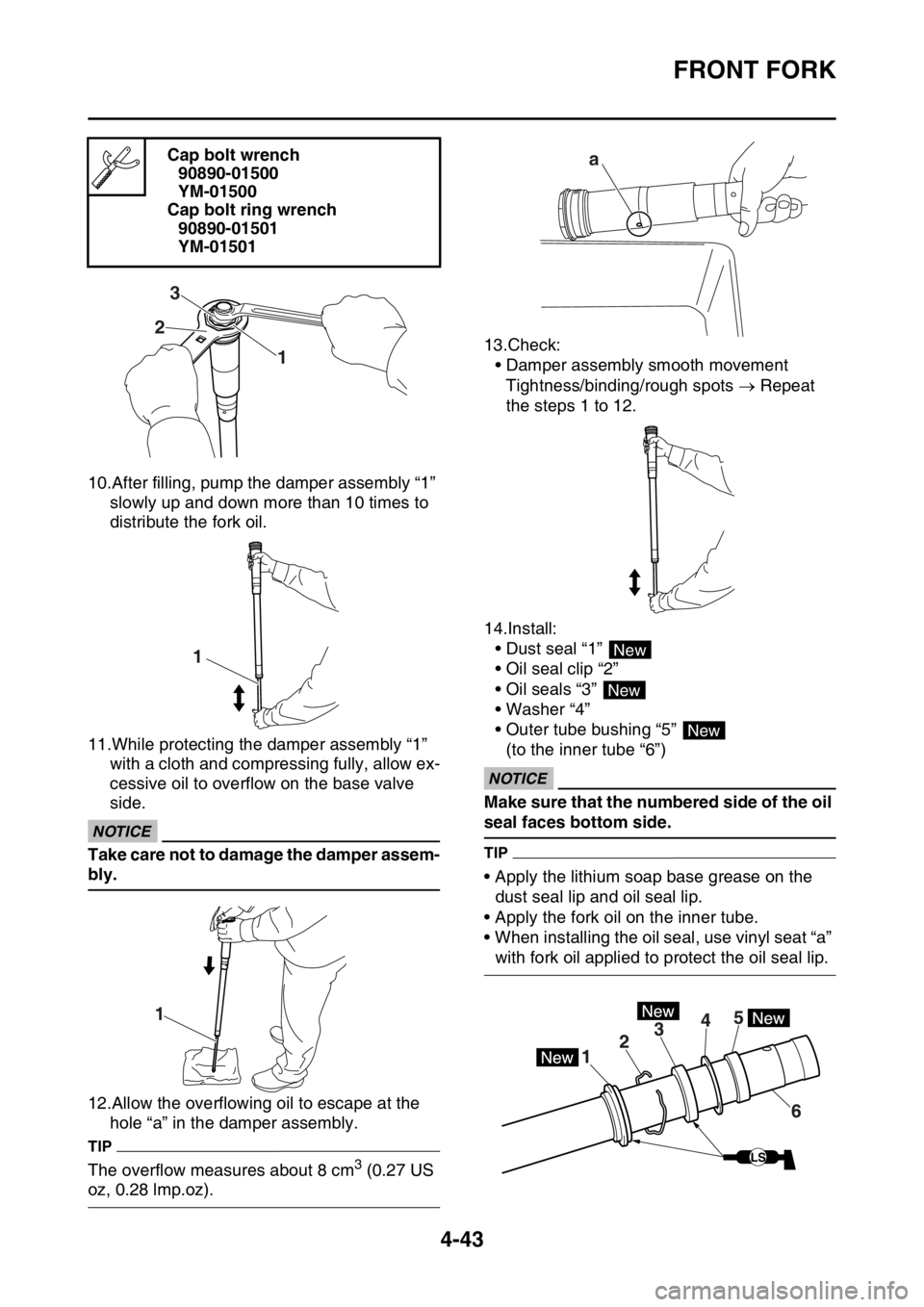
FRONT FORK
4-43
10.After filling, pump the damper assembly “1”
slowly up and down more than 10 times to
distribute the fork oil.
11.While protecting the damper assembly “1”
with a cloth and compressing fully, allow ex-
cessive oil to overflow on the base valve
side.
ECA32D1010
NOTICE
Take care not to damage the damper assem-
bly.
12.Allow the overflowing oil to escape at the
hole “a” in the damper assembly.
TIP
The overflow measures about 8 cm3 (0.27 US
oz, 0.28 lmp.oz).13.Check:
• Damper assembly smooth movement
Tightness/binding/rough spots Repeat
the steps 1 to 12.
14.Install:
• Dust seal “1”
• Oil seal clip “2”
• Oil seals “3”
• Washer “4”
• Outer tube bushing “5”
(to the inner tube “6”)
ECA32D1010
NOTICE
Make sure that the numbered side of the oil
seal faces bottom side.
TIP
• Apply the lithium soap base grease on the
dust seal lip and oil seal lip.
• Apply the fork oil on the inner tube.
• When installing the oil seal, use vinyl seat “a”
with fork oil applied to protect the oil seal lip. Cap bolt wrench
90890-01500
YM-01500
Cap bolt ring wrench
90890-01501
YM-01501
1 23
1
1
a
New
New
New
LS
Page 168 of 356
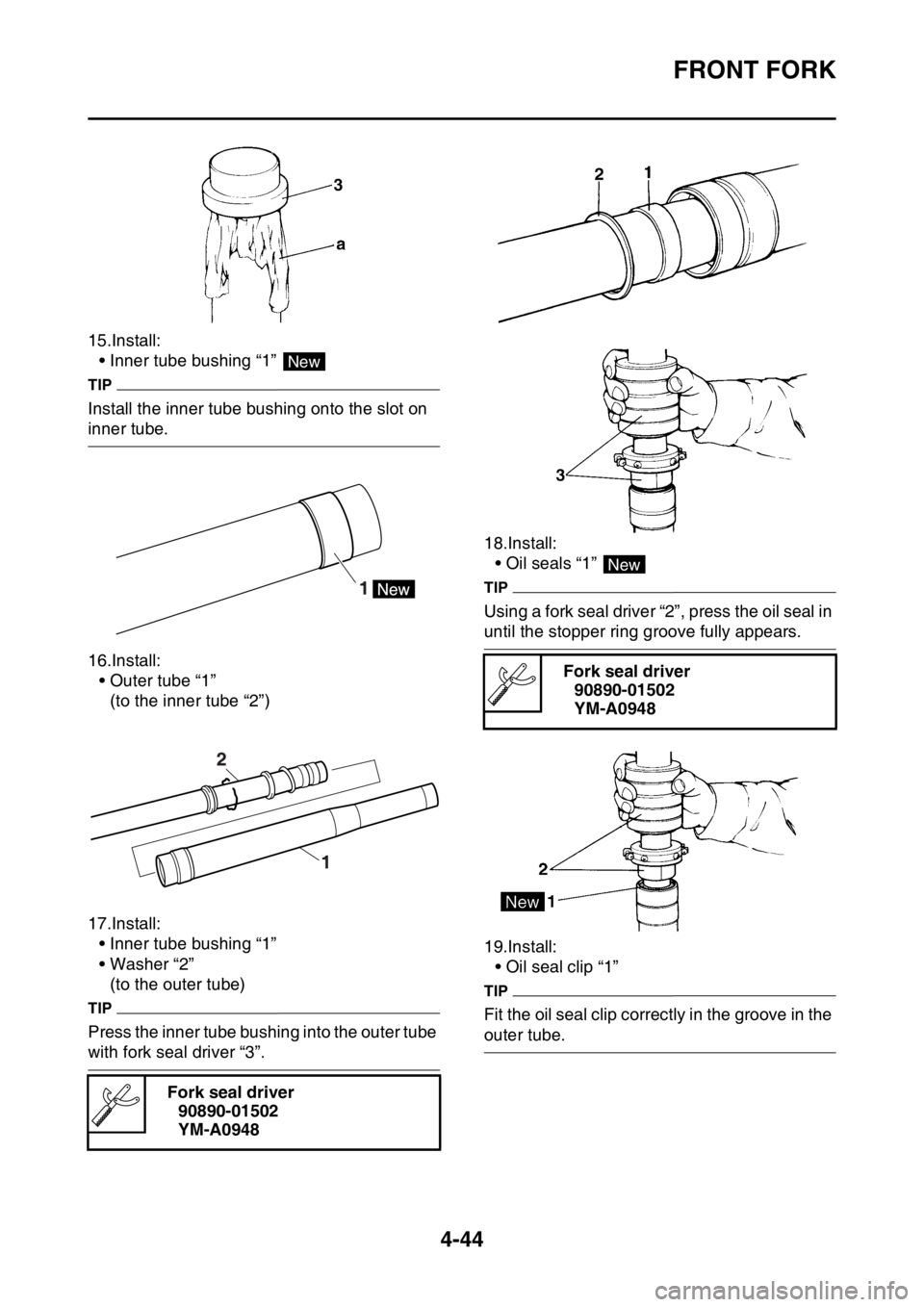
FRONT FORK
4-44
15.Install:
• Inner tube bushing “1”
TIP
Install the inner tube bushing onto the slot on
inner tube.
16.Install:
• Outer tube “1”
(to the inner tube “2”)
17.Install:
• Inner tube bushing “1”
• Washer “2”
(to the outer tube)
TIP
Press the inner tube bushing into the outer tube
with fork seal driver “3”.18.Install:
• Oil seals “1”
TIP
Using a fork seal driver “2”, press the oil seal in
until the stopper ring groove fully appears.
19.Install:
• Oil seal clip “1”
TIP
Fit the oil seal clip correctly in the groove in the
outer tube.
Fork seal driver
90890-01502
YM-A0948
New
Fork seal driver
90890-01502
YM-A0948
New
Page 169 of 356
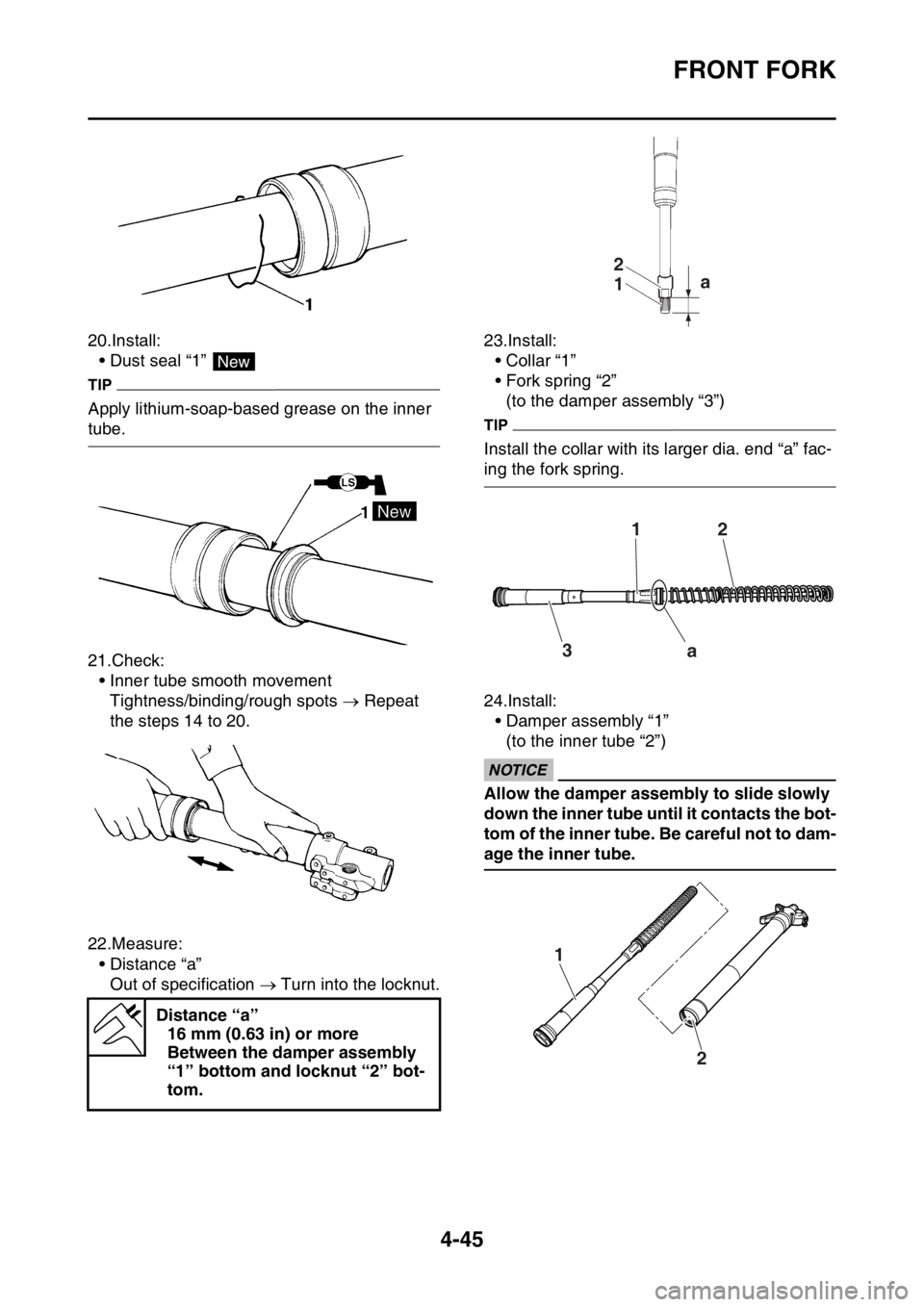
FRONT FORK
4-45
20.Install:
• Dust seal “1”
TIP
Apply lithium-soap-based grease on the inner
tube.
21.Check:
• Inner tube smooth movement
Tightness/binding/rough spots Repeat
the steps 14 to 20.
22.Measure:
• Distance “a”
Out of specification Turn into the locknut.23.Install:
• Collar “1”
• Fork spring “2”
(to the damper assembly “3”)TIP
Install the collar with its larger dia. end “a” fac-
ing the fork spring.
24.Install:
• Damper assembly “1”
(to the inner tube “2”)
ECA32D1010
NOTICE
Allow the damper assembly to slide slowly
down the inner tube until it contacts the bot-
tom of the inner tube. Be careful not to dam-
age the inner tube.
Distance “a”
16 mm (0.63 in) or more
Between the damper assembly
“1” bottom and locknut “2” bot-
tom.
New
1 2a
12
3
a
1
2
Page 170 of 356
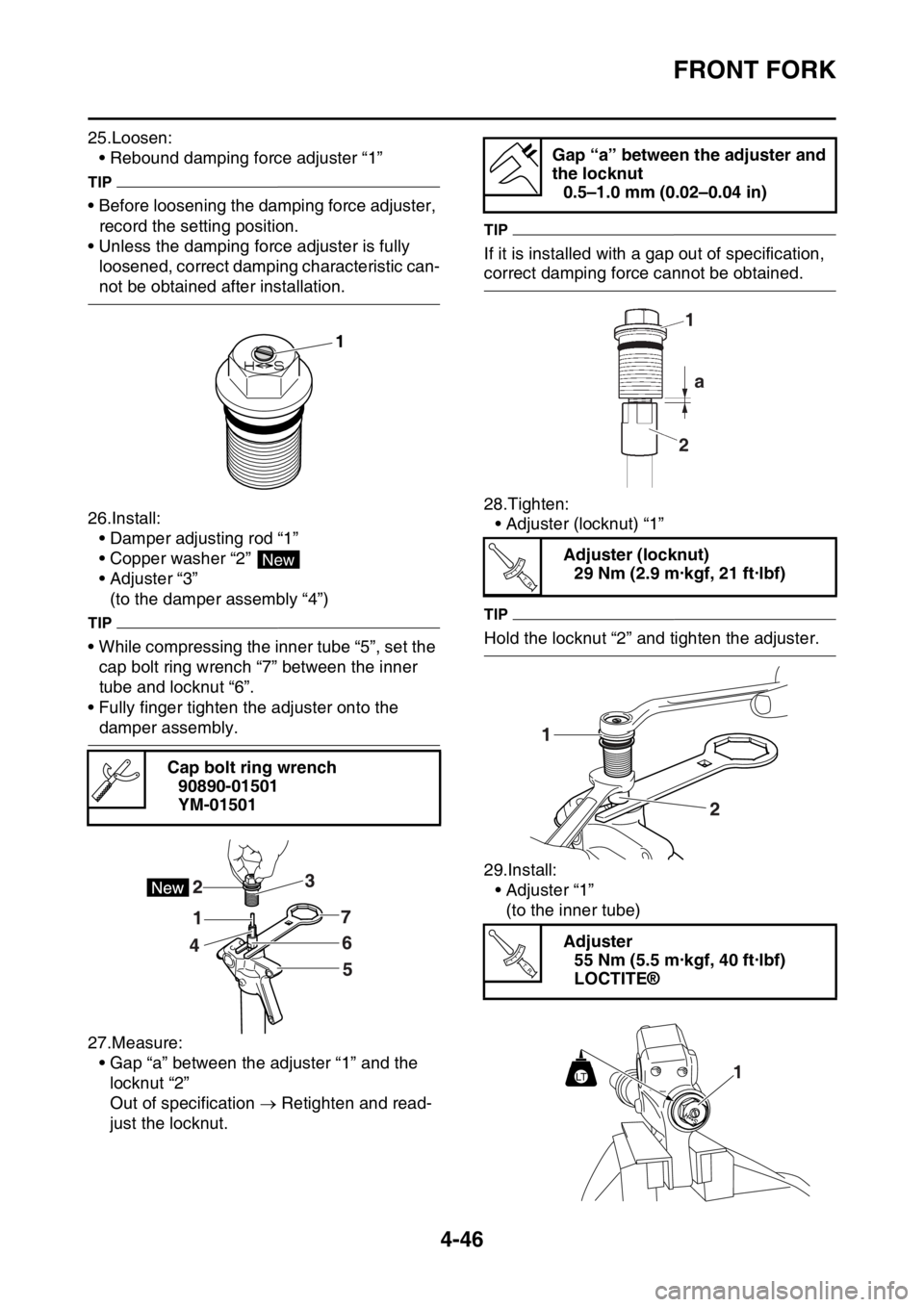
FRONT FORK
4-46
25.Loosen:
• Rebound damping force adjuster “1”
TIP
• Before loosening the damping force adjuster,
record the setting position.
• Unless the damping force adjuster is fully
loosened, correct damping characteristic can-
not be obtained after installation.
26.Install:
• Damper adjusting rod “1”
• Copper washer “2”
• Adjuster “3”
(to the damper assembly “4”)
TIP
• While compressing the inner tube “5”, set the
cap bolt ring wrench “7” between the inner
tube and locknut “6”.
• Fully finger tighten the adjuster onto the
damper assembly.
27.Measure:
• Gap “a” between the adjuster “1” and the
locknut “2”
Out of specification Retighten and read-
just the locknut.
TIP
If it is installed with a gap out of specification,
correct damping force cannot be obtained.
28.Tighten:
• Adjuster (locknut) “1”
TIP
Hold the locknut “2” and tighten the adjuster.
29.Install:
• Adjuster “1”
(to the inner tube) Cap bolt ring wrench
90890-01501
YM-01501
1
New
Gap “a” between the adjuster and
the locknut
0.5–1.0 mm (0.02–0.04 in)
Adjuster (locknut)
29 Nm (2.9 m·kgf, 21 ft·lbf)
Adjuster
55 Nm (5.5 m·kgf, 40 ft·lbf)
LOCTITE®
1
2a
T R..
T R..
1LT