fuel ASTON MARTIN V8 VANTAGE 2010 Owners Manual
[x] Cancel search | Manufacturer: ASTON MARTIN, Model Year: 2010, Model line: V8 VANTAGE, Model: ASTON MARTIN V8 VANTAGE 2010Pages: 947, PDF Size: 43.21 MB
Page 881 of 947
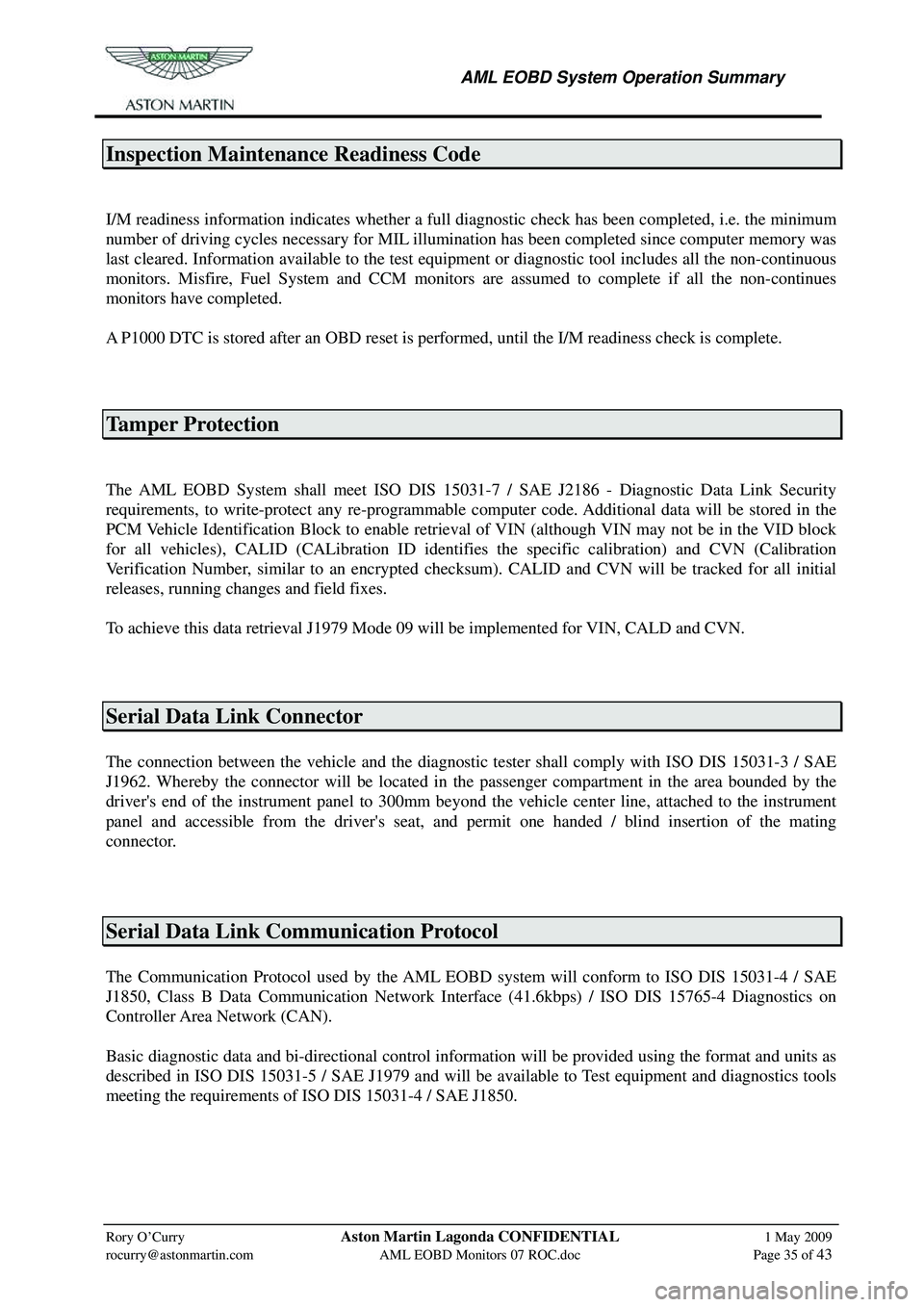
AML EOBD System Operation Summary
Rory O’Curry Aston Martin Lagonda CONFIDENTIAL 1 May 2009
[email protected] AML EOBD Monitors 07 ROC.doc Page 35 of 43
Inspection Maintenance Readiness Code
I/M readiness information indicates whether a full diagnos tic check has been completed, i.e. the minimum
number of driving cycles necessary for MIL illumination has been completed since computer memory was
last cleared. Information available to the test equi pment or diagnostic tool includes all the non-continuous
monitors. Misfire, Fuel System and CCM monitors are assumed to complete if all the non-continues
monitors have completed.
A P1000 DTC is stored after an OBD reset is performed, until the I/M readiness check is complete.
Tamper Protection
The AML EOBD System shall meet ISO DIS 15031-7 / SAE J2186 - Diagnostic Data Link Security
requirements, to write-protect any re-programmable co mputer code. Additional data will be stored in the
PCM Vehicle Identification Block to enable retrieva l of VIN (although VIN may not be in the VID block
for all vehicles), CALID (CALibration ID identifi es the specific calibration) and CVN (Calibration
Verification Number, similar to an encrypted check sum). CALID and CVN will be tracked for all initial
releases, running changes and field fixes.
To achieve this data retrieva l J1979 Mode 09 will be implemented for VIN, CALD and CVN.
Serial Data Link Connector
The connection between the vehicle and the diagnostic tester shall comply with ISO DIS 15031-3 / SAE
J1962. Whereby the connector will be located in the passenger compartment in the area bounded by the
driver's end of the instrument panel to 300mm beyond the vehicle center line, attached to the instrument
panel and accessible from the driver's seat, and permit one handed / blind insertion of the mating
connector.
Serial Data Link Communication Protocol
The Communication Protocol used by the AML EOBD system will conform to ISO DIS 15031-4 / SAE
J1850, Class B Data Communication Network In terface (41.6kbps) / ISO DIS 15765-4 Diagnostics on
Controller Area Network (CAN).
Basic diagnostic data and bi-directional control inform ation will be provided using the format and units as
described in ISO DIS 15031-5 / SAE J1979 and will be av ailable to Test equipment and diagnostics tools
meeting the requirements of ISO DIS 15031-4 / SAE J1850.
Page 883 of 947

AML EOBD System Operation Summary
Rory O’Curry Aston Martin Lagonda CONFIDENTIAL 1 May 2009
[email protected] AML EOBD Monitors 07 ROC.doc Page 37 of 43
Glossary of Terms
A/D Analogue to Digital
ASM Auto Shift Manul
BTDC Before Top Dead Centre
CALID CALibration IDentification
CD4E Automatic Transmission for Intermediate size Family saloon.
CID Camshaft Identification.
CKP Crankshaft Position
CMP Camshaft Position
COP Coil on Plug
CPC Camshaft Position Control
CVN Calibration Verification Number
DPFE Delta Pressure Feedback
DTC Diagnostic Trouble Code
ECT Engine Coolant Temperature
EDIS Electronic Distributorless Ignition System
EGR Exhaust Gas Re-circulation.
EOBD European On Bard Diagnostics
EPC Electronic Pressure Control
ETC Electronic Throttle Control
ETM Electronic Throttle Monitor
EVR Electronic Vacuum Regulator
EWMA Exponentially Weighted Moving Average
FMEM Failure Mode and Effects Management
FN Automatic Transmission for Medium size Family Saloon
FWD Front Wheel Drive
HDR High Data Rate
HO2S Heated Oxygen Sensor.
IAC Idle Air Control
IDM Ignition Diagnostic Monitor
IMRC Inlet Manifold Runner Control
IPC Independent Plausibility Checker
KAM Keep Alive Memory
LDR Low Data Rate
LTFT Long Term Fuel Trim
MAF Mass Air Flow
MAP Manifold Absolute Pressure
MIL Malfunction Indicator Lamp
OSS Output Shaft Speed
PCM Powertrain Control Module
PIP Profile Ignition Pickup
RWD Rear Wheel Drive
SAE Society of Automotive Engineers
SAIR Secondary AIR
SCV Swirl Control Valve
STFT Short Term Fuel Trim
TCC Torque Converter Clutch
TCIL Transmission Control Indicator Lamp
TP Throttle Position
TPPC Throttle Plate Position Controller
TRS Transmission Range Sensor
TSS Turbine Shaft Speed
VID Vehicle IDentification
VIN Vehicle Identification No.
VQZ VQuizzer
VMV Vapour Management Valve
Page 884 of 947
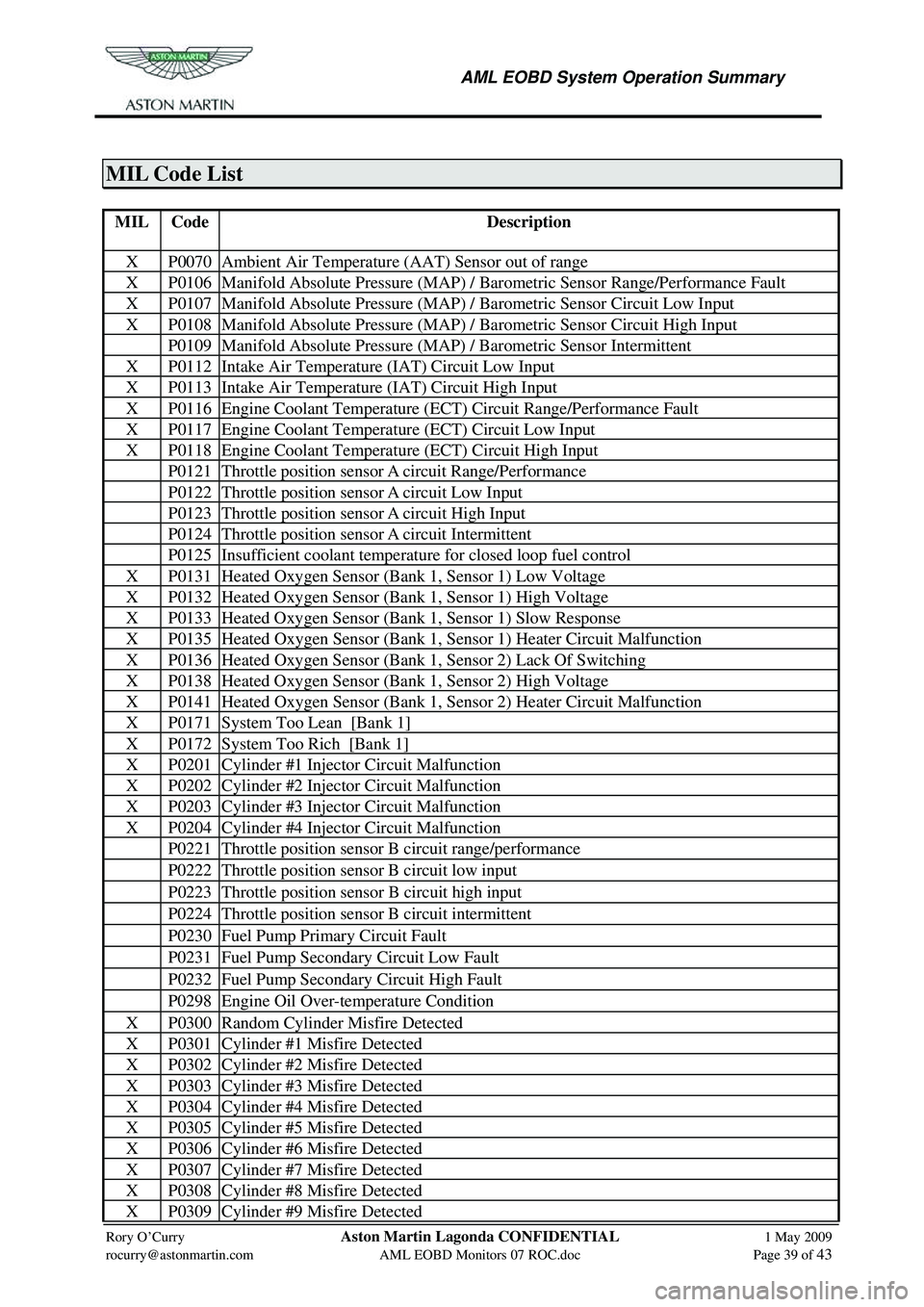
AML EOBD System Operation Summary
Rory O’Curry Aston Martin Lagonda CONFIDENTIAL 1 May 2009
[email protected] AML EOBD Monitors 07 ROC.doc Page 39 of 43
MIL Code List
MIL Code Description
X P0070 Ambient Air Temperature (AAT) Sensor out of range
X P0106 Manifold Absolute Pressure (MAP) / Barometric Sensor Range/Performance Fault
X P0107 Manifold Absolute Pressure (MAP) / Barometric Sensor Circuit Low Input
X P0108 Manifold Absolute Pressure (MAP) / Barometric Sensor Circuit High Input
P0109 Manifold Absolute Pressure (MAP) / Barometric Sensor Intermittent
X P0112 Intake Air Temperature (IAT) Circuit Low Input
X P0113 Intake Air Temperature (IAT) Circuit High Input
X P0116 Engine Coolant Temperature (ECT) Circuit Range/Performance Fault
X P0117 Engine Coolant Temperature (ECT) Circuit Low Input
X P0118 Engine Coolant Temperature (ECT) Circuit High Input
P0121 Throttle position sensor A circuit Range/Performance
P0122 Throttle position sensor A circuit Low Input
P0123 Throttle position sensor A circuit High Input
P0124 Throttle position sensor A circuit Intermittent
P0125 Insufficient coolant temperature for closed loop fuel control
X P0131 Heated Oxygen Sensor (Bank 1, Sensor 1) Low Voltage
X P0132 Heated Oxygen Sensor (Bank 1, Sensor 1) High Voltage
X P0133 Heated Oxygen Sensor (Ba nk 1, Sensor 1) Slow Response
X P0135 Heated Oxygen Sensor (Bank 1, Sensor 1) Heater Circuit Malfunction
X P0136 Heated Oxygen Sensor (Bank 1, Sensor 2) Lack Of Switching
X P0138 Heated Oxygen Sensor (Bank 1, Sensor 2) High Voltage
X P0141 Heated Oxygen Sensor (Bank 1, Sensor 2) Heater Circuit Malfunction
X P0171 System Too Lean [Bank 1]
X P0172 System Too Rich [Bank 1]
X P0201 Cylinder #1 Injector Circuit Malfunction
X P0202 Cylinder #2 Injector Circuit Malfunction
X P0203 Cylinder #3 Injector Circuit Malfunction
X P0204 Cylinder #4 Injector Circuit Malfunction
P0221 Throttle position sensor B circuit range/performance
P0222 Throttle position sensor B circuit low input
P0223 Throttle position sensor B circuit high input
P0224 Throttle position sensor B circuit intermittent
P0230 Fuel Pump Primary Circuit Fault
P0231 Fuel Pump Secondary Circuit Low Fault
P0232 Fuel Pump Secondary Circuit High Fault
P0298 Engine Oil Over-temperature Condition
X P0300 Random Cylinder Misfire Detected
X P0301 Cylinder #1 Misfire Detected
X P0302 Cylinder #2 Misfire Detected
X P0303 Cylinder #3 Misfire Detected
X P0304 Cylinder #4 Misfire Detected
X P0305 Cylinder #5 Misfire Detected
X P0306 Cylinder #6 Misfire Detected
X P0307 Cylinder #7 Misfire Detected
X P0308 Cylinder #8 Misfire Detected
X P0309 Cylinder #9 Misfire Detected
Page 885 of 947
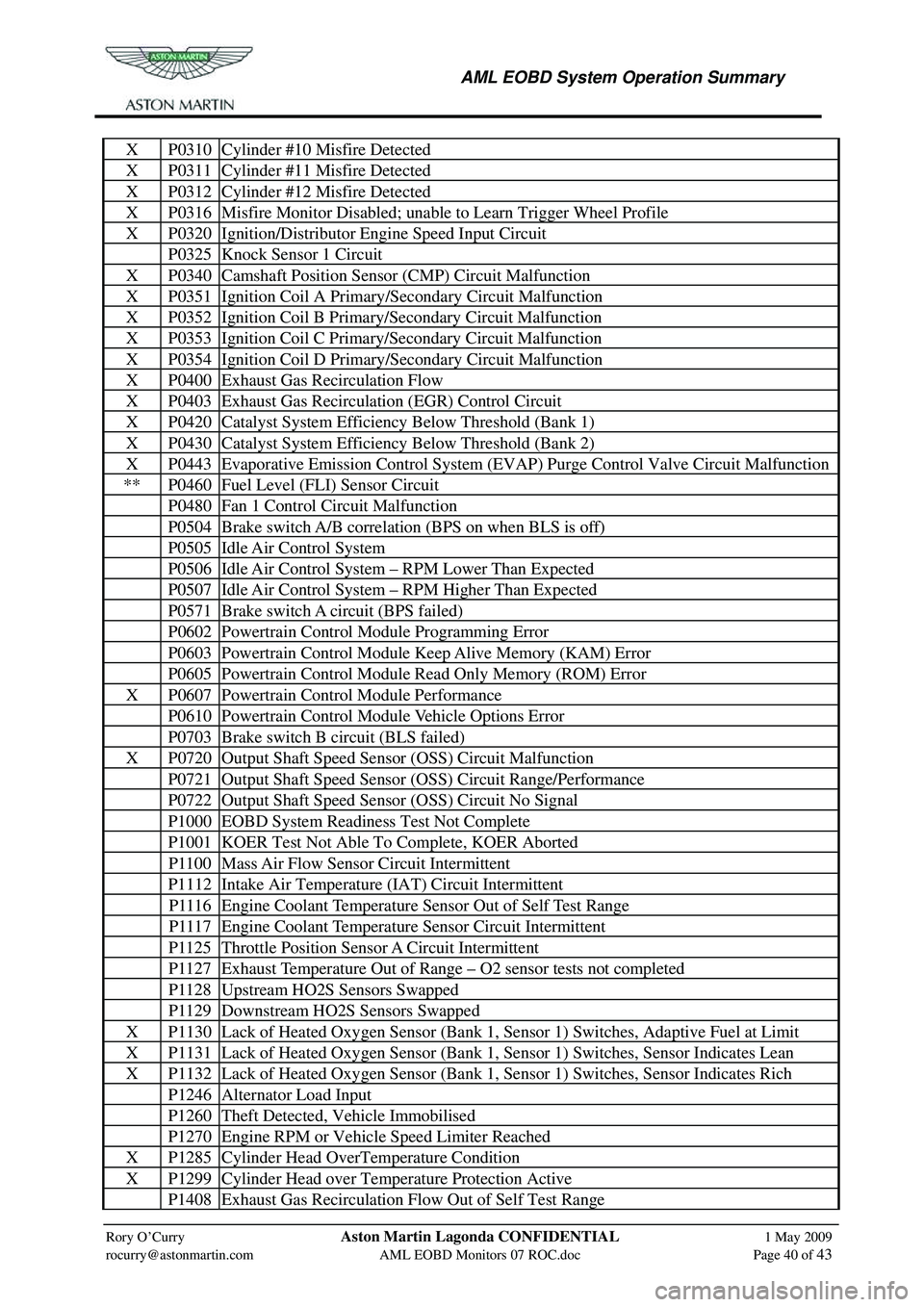
AML EOBD System Operation Summary
Rory O’Curry Aston Martin Lagonda CONFIDENTIAL 1 May 2009
[email protected] AML EOBD Monitors 07 ROC.doc Page 40 of 43
X P0310 Cylinder #10 Misfire Detected
X P0311 Cylinder #11 Misfire Detected
X P0312 Cylinder #12 Misfire Detected
X P0316 Misfire Monitor Disabled; unable to Learn Trigger Wheel Profile
X P0320 Ignition/Distributor Engine Speed Input Circuit
P0325 Knock Sensor 1 Circuit
X P0340 Camshaft Position Sens or (CMP) Circuit Malfunction
X P0351 Ignition Coil A Primary/Secondary Circuit Malfunction
X P0352 Ignition Coil B Primary/Secondary Circuit Malfunction
X P0353 Ignition Coil C Primary/Secondary Circuit Malfunction
X P0354 Ignition Coil D Primary/Secondary Circuit Malfunction
X P0400 Exhaust Gas Recirculation Flow
X P0403 Exhaust Gas Recirculation (EGR) Control Circuit
X P0420 Catalyst System Efficiency Below Threshold (Bank 1)
X P0430 Catalyst System Efficiency Below Threshold (Bank 2)
X P0443 Evaporative Emission Control System (EVAP) Purge Control Valve Circuit Malfunction
** P0460 Fuel Level (FLI) Sensor Circuit
P0480 Fan 1 Control Circuit Malfunction
P0504 Brake switch A/B correlation (BPS on when BLS is off)
P0505 Idle Air Control System
P0506 Idle Air Control System – RPM Lower Than Expected
P0507 Idle Air Control System – RPM Higher Than Expected
P0571 Brake switch A circuit (BPS failed)
P0602 Powertrain Control Module Programming Error
P0603 Powertrain Control Module Keep Alive Memory (KAM) Error
P0605 Powertrain Control Module Read Only Memory (ROM) Error
X P0607 Powertrain Control Module Performance
P0610 Powertrain Control Module Vehicle Options Error
P0703 Brake switch B circuit (BLS failed)
X P0720 Output Shaft Speed Sensor (OSS) Circuit Malfunction
P0721 Output Shaft Speed Sensor (OSS) Circuit Range/Performance
P0722 Output Shaft Speed Sensor (OSS) Circuit No Signal
P1000 EOBD System Readiness Test Not Complete
P1001 KOER Test Not Able To Complete, KOER Aborted
P1100 Mass Air Flow Sensor Circuit Intermittent
P1112 Intake Air Temperature (IAT) Circuit Intermittent
P1116 Engine Coolant Temperature Sensor Out of Self Test Range
P1117 Engine Coolant Temperature Sensor Circuit Intermittent
P1125 Throttle Position Sensor A Circuit Intermittent
P1127 Exhaust Temperature Out of Range – O2 sensor tests not completed
P1128 Upstream HO2S Sensors Swapped
P1129 Downstream HO2S Sensors Swapped
X P1130 Lack of Heated Oxygen Sensor (Bank 1, Sensor 1) Switches, Adaptive Fuel at Limit
X P1131 Lack of Heated Oxygen Sensor (Bank 1, Sensor 1) Switches, Sensor Indicates Lean
X P1132 Lack of Heated Oxygen Sensor (Bank 1, Sensor 1) Switches, Sensor Indicates Rich
P1246 Alternator Load Input
P1260 Theft Detected, Vehicle Immobilised
P1270 Engine RPM or Vehicle Speed Limiter Reached
X P1285 Cylinder Head OverTemperature Condition
X P1299 Cylinder Head over Temperature Protection Active
P1408 Exhaust Gas Recirculation Flow Out of Self Test Range
Page 889 of 947
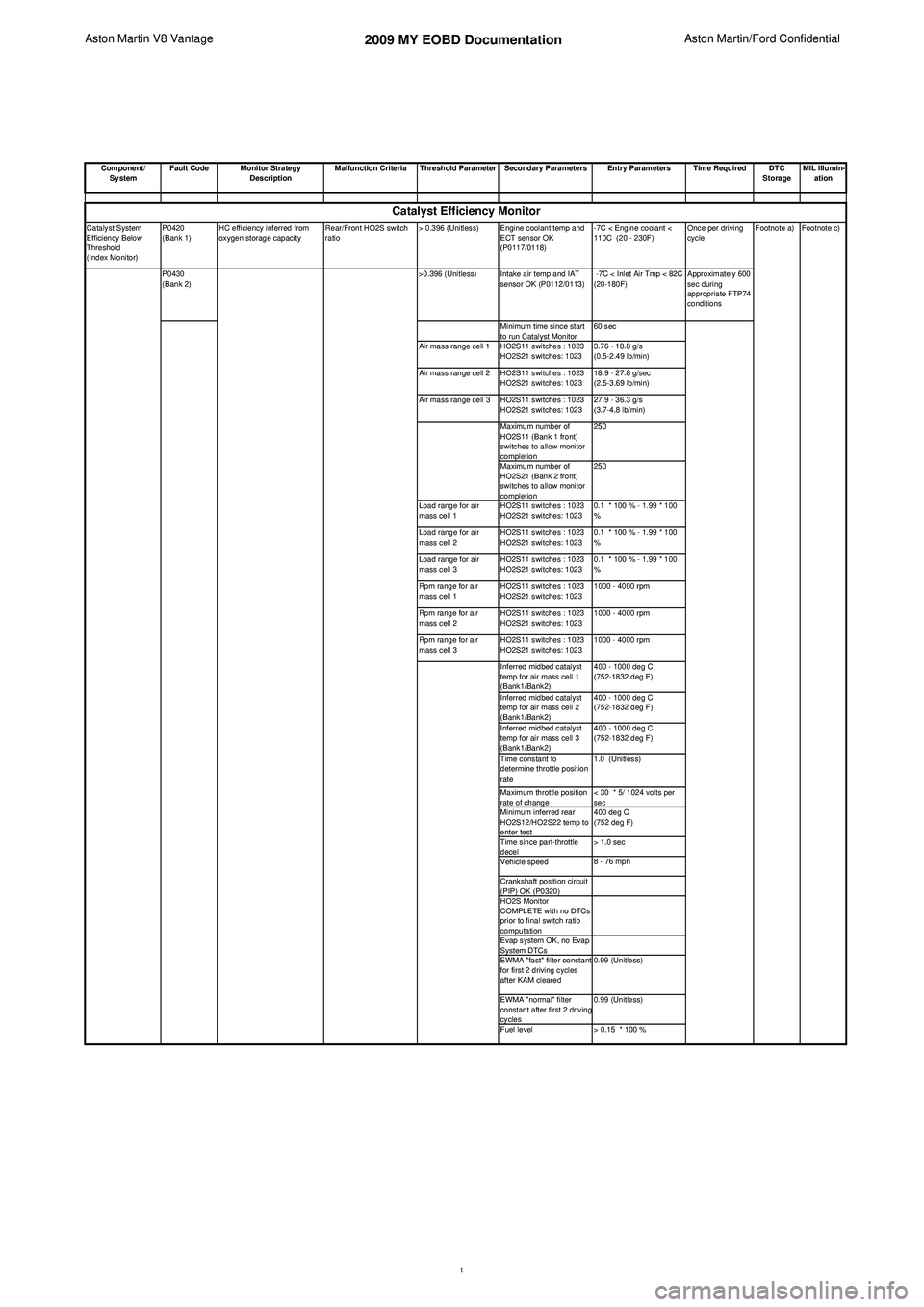
Aston Martin V8 Vantage 2009 MY EOBD DocumentationAston Martin/Ford Confidential
Component/ System Fault Code Monitor Strategy
Description Malfunction Criteria Threshold Parameter Secondary Parameters Entry Parameters Time Required DTC
StorageMIL Illumin-
ation
Catalyst System
Efficiency Below
Threshold
(Index Monitor) P0420
(Bank 1)
HC efficiency inferred from
oxygen storage capacity Rear/Front HO2S switch
ratio> 0.396 (Unitless) Engine coolant temp and
ECT sensor OK
(P0117/0118) -7C < Engine coolant <
110C (20 - 230F)
Once per driving
cycle
P0430
(Bank 2) >0.396 (Unitless) Intake air temp and IAT
sensor OK (P0112/0113) -7C < Inlet Air Tmp < 82C
(20-180F) Approximately 600
sec during
appropriate FTP74
conditions
Minimum time since start
to run Catalyst Monitor 60 sec
Air mass range cell 1 HO2S11 switches : 1023 HO2S21 switches: 1023 3.76 - 18.8 g/s
(0.5-2.49 lb/min)
Air mass range cell 2 HO2S11 switches : 1023 HO2S21 switches: 1023 18.9 - 27.8 g/sec
(2.5-3.69 lb/min)
Air mass range cell 3 HO2S11 switches : 1023 HO2S21 switches: 1023 27.9 - 36.3 g/s
(3.7-4.8 lb/min)
Maximum number of
HO2S11 (Bank 1 front)
switches to allow monitor
completion 250
Maximum number of
HO2S21 (Bank 2 front)
switches to allow monitor
completion 250
Load range for air
mass cell 1 HO2S11 switches : 1023
HO2S21 switches: 1023 0.1 * 100 % - 1.99 * 100
%
Load range for air
mass cell 2 HO2S11 switches : 1023
HO2S21 switches: 1023 0.1 * 100 % - 1.99 * 100
%
Load range for air
mass cell 3 HO2S11 switches : 1023
HO2S21 switches: 1023 0.1 * 100 % - 1.99 * 100
%
Rpm range for air
mass cell 1 HO2S11 switches : 1023
HO2S21 switches: 1023 1000 - 4000 rpm
Rpm range for air
mass cell 2 HO2S11 switches : 1023
HO2S21 switches: 1023 1000 - 4000 rpm
Rpm range for air
mass cell 3 HO2S11 switches : 1023
HO2S21 switches: 1023 1000 - 4000 rpm
Inferred midbed catalyst
temp for air mass cell 1
(Bank1/Bank2) 400 - 1000 deg C
(752-1832 deg F)
Inferred midbed catalyst
temp for air mass cell 2
(Bank1/Bank2) 400 - 1000 deg C
(752-1832 deg F)
Inferred midbed catalyst
temp for air mass cell 3
(Bank1/Bank2) 400 - 1000 deg C
(752-1832 deg F)
Time constant to
determine throttle position
rate 1.0 (Unitless)
Maximum throttle position
rate of change < 30 * 5/ 1024 volts per
sec
Minimum inferred rear
HO2S12/HO2S22 temp to
enter test 400 deg C
(752 deg F)
Time since part-throttle
decel > 1.0 sec
Vehicle speed 8 - 76 mph
Crankshaft position circuit
(PIP) OK (P0320)
HO2S Monitor
COMPLETE with no DTCs
prior to final switch ratio
computation
Evap system OK, no Evap
System DTCs
EWMA "fast" filter constant
for first 2 driving cycles
after KAM cleared 0.99 (Unitless)
EWMA "normal" filter
constant after first 2 driving
cycles 0.99 (Unitless)
Fuel level > 0.15 * 100 % Footnote a)
Footnote c)
Catalyst Efficiency Monitor
1
Page 890 of 947
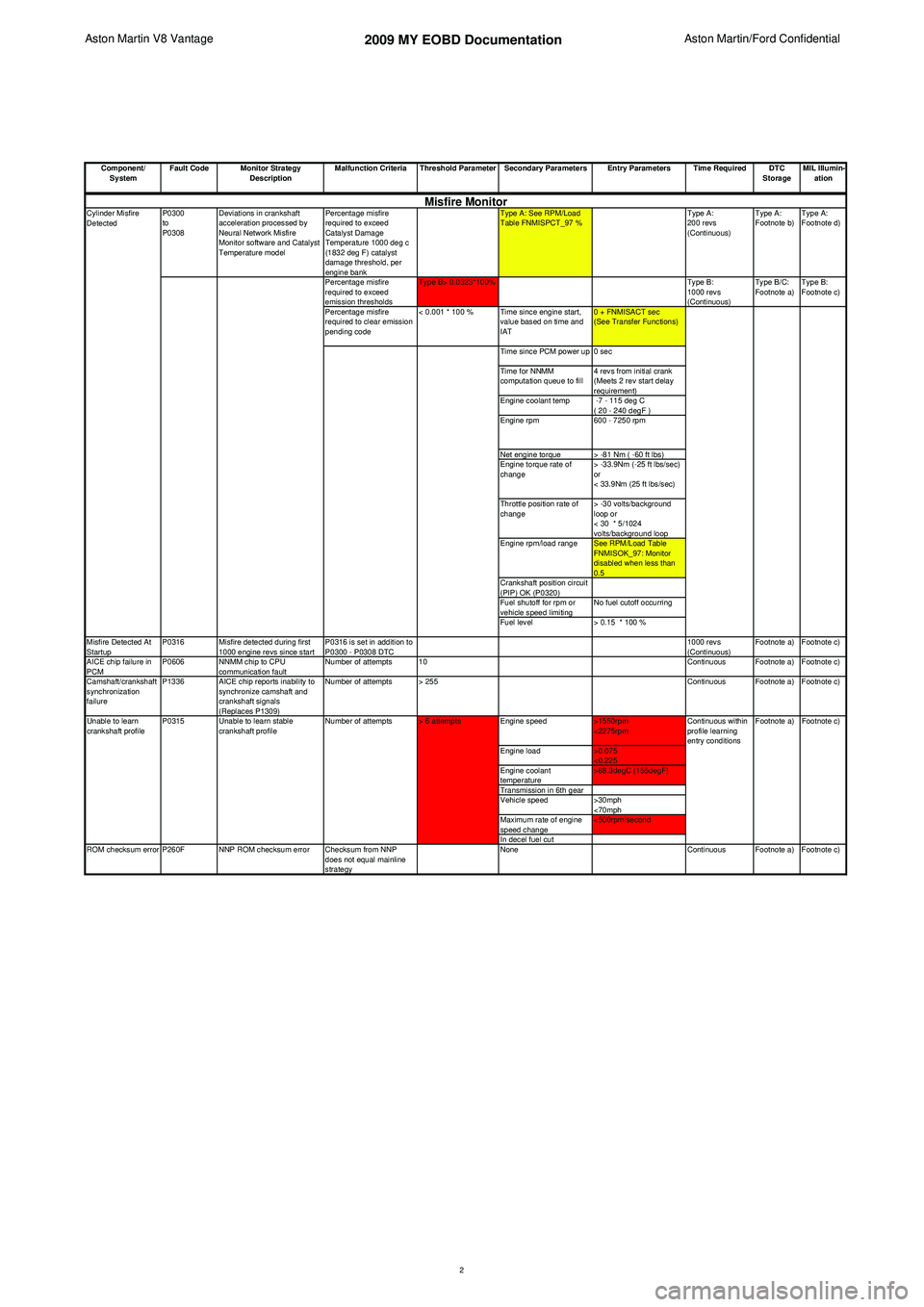
Aston Martin V8 Vantage 2009 MY EOBD DocumentationAston Martin/Ford Confidential
Component/ System Fault Code Monitor Strategy
Description Malfunction Criteria Threshold Parameter Secondary Parameters Entry Parameters Time Required DTC
StorageMIL Illumin-
ation
P0300
to
P0308 Deviations in crankshaft
acceleration processed by
Neural Network Misfire
Monitor software and Catalyst
Temperature model Percentage misfire
required to exceed
Catalyst Damage
Temperature 1000 deg c
(1832 deg F) catalyst
damage threshold, per
engine bank Type A: See RPM/Load
Table FNMISPCT_97 %
Type A:
200 revs
(Continuous)Type A:
Footnote b)
Type A:
Footnote d)
Percentage misfire
required to exceed
emission thresholds Type B> 0.0323*100% Type B:
1000 revs
(Continuous)Type B/C:
Footnote a)
Type B:
Footnote c)
Percentage misfire
required to clear emission
pending code < 0.001 * 100 % Time since engine start,
value based on time and
IAT 0 + FNMISACT sec
(See Transfer Functions)
Time since PCM power up 0 sec
Time for NNMM
computation queue to fill 4 revs from initial crank
(Meets 2 rev start delay
requirement)
Engine coolant temp -7 - 115 deg C ( 20 - 240 degF )
Engine rpm 600 - 7250 rpm
Net engine torque > -81 Nm ( -60 ft lbs)
Engine torque rate of
change > -33.9Nm (-25 ft lbs/sec)
or
< 33.9Nm (25 ft lbs/sec)
Throttle position rate of
change > -30 volts/background
loop or
< 30 * 5/1024
volts/background loop
Engine rpm/load range See RPM/Load Table FNMISOK_97: Monitor
disabled when less than
0.5
Crankshaft position circuit
(PIP) OK (P0320)
Fuel shutoff for rpm or
vehicle speed limiting No fuel cutoff occurring
Fuel level > 0.15 * 100 %
Misfire Detected At
Startup P0316 Misfire detected during first
1000 engine revs since start P0316 is set in addition to
P0300 - P0308 DTC 1000 revs
(Continuous)Footnote a) Footnote c)
AICE chip failure in
PCM P0606 NNMM chip to CPU
communication fault Number of attempts 10
Continuous Footnote a) Footnote c)
Camshaft/crankshaft
synchronization
failure P1336 AICE chip reports inability to
synchronize camshaft and
crankshaft signals
(Replaces P1309) Number of attempts > 255
Continuous Footnote a) Footnote c)
Engine speed >1550rpm
<2275rpm
Engine load >0.075
<0.225
Engine coolant
temperature >68.3degC (155degF)
Transmission in 6th gear
Vehicle speed >30mph
<70mph
Maximum rate of engine
speed change <500rpm/second
In decel fuel cut
ROM checksum error P260F NNP ROM checksum error Checksum from NNP does not equal mainline
strategyNone
Continuous Footnote a) Footnote c)
Cylinder Misfire
DetectedMisfire Monitor
Footnote c)
Unable to learn
crankshaft profile P0315 Unable to learn stable
crankshaft profile Number of attempts > 6 attempts Continuous within
profile learning
entry conditionsFootnote a)
2
Page 891 of 947
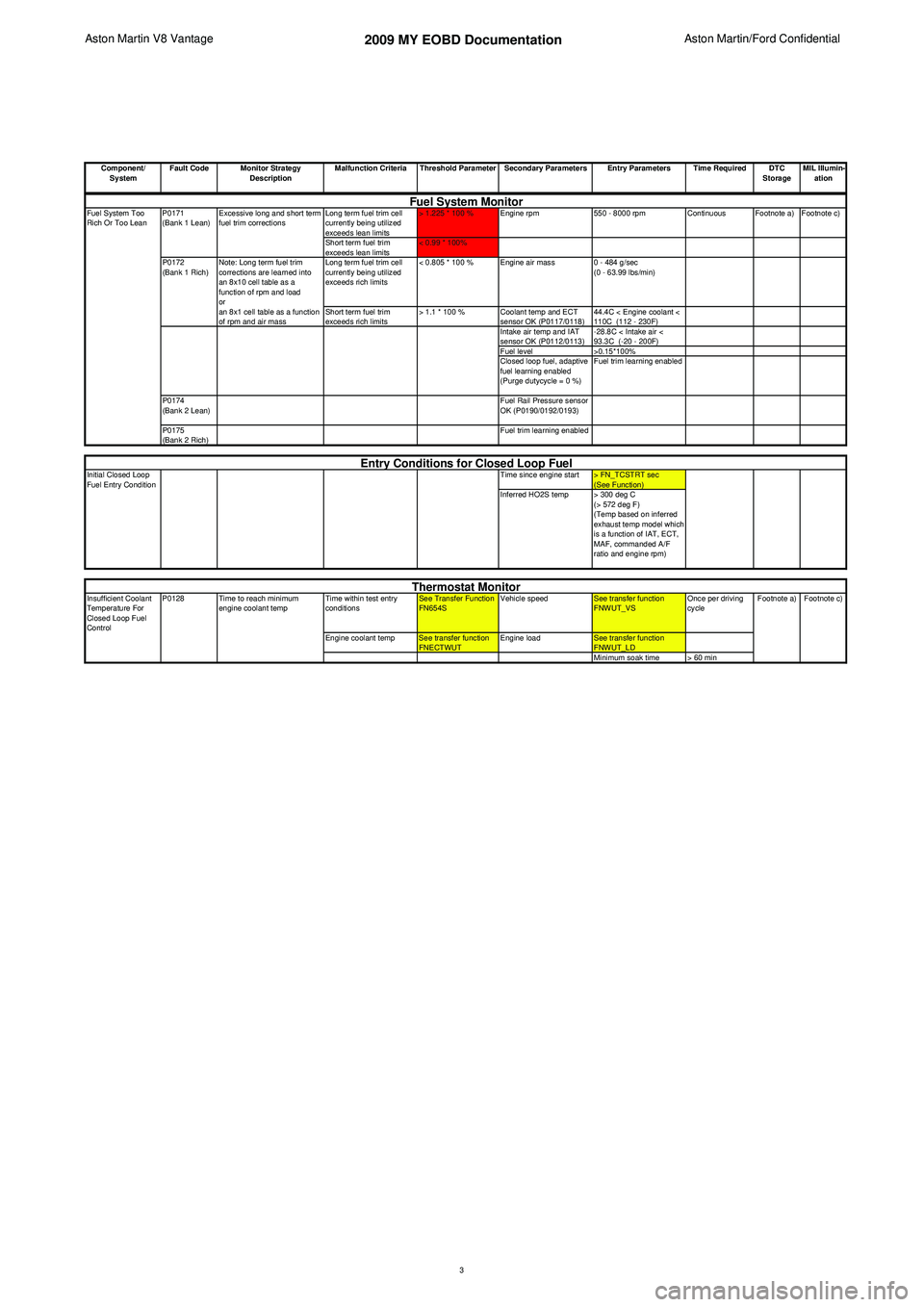
Aston Martin V8 Vantage 2009 MY EOBD DocumentationAston Martin/Ford Confidential
Component/ System Fault Code Monitor Strategy
Description Malfunction Criteria Threshold Parameter Secondary Parameters Entry Parameters Time Required DTC
StorageMIL Illumin-
ation
Long term fuel trim cell
currently being utilized
exceeds lean limits > 1.225 * 100 % Engine rpm
550 - 8000 rpmContinuous Footnote a) Footnote c)
Short term fuel trim
exceeds lean limits < 0.99 * 100%
Long term fuel trim cell
currently being utilized
exceeds rich limits < 0.805 * 100 % Engine air mass
0 - 484 g/sec
(0 - 63.99 lbs/min)
Short term fuel trim
exceeds rich limits > 1.1 * 100 % Coolant temp and ECT
sensor OK (P0117/0118) 44.4C < Engine coolant <
110C (112 - 230F)
Intake air temp and IAT
sensor OK (P0112/0113) -28.8C < Intake air <
93.3C (-20 - 200F)
Fuel level >0.15*100%
Closed loop fuel, adaptive
fuel learning enabled
(Purge dutycycle = 0 %) Fuel trim learning enabled
P0174
(Bank 2 Lean) Fuel Rail Pressure sensor
OK (P0190/0192/0193)
P0175
(Bank 2 Rich) Fuel trim learning enabled
Time since engine start > FN_TCSTRT sec
(See Function)
Inferred HO2S temp > 300 deg C (> 572 deg F)
(Temp based on inferred
exhaust temp model which
is a function of IAT, ECT,
MAF, commanded A/F
ratio and engine rpm)
Time within test entry
conditions See Transfer Function
FN654SVehicle speed
See transfer function
FNWUT_VS Once per driving
cycle
Engine coolant temp See transfer function FNECTWUTEngine load
See transfer function
FNWUT_LD
Minimum soak time > 60 min
Entry Conditions for Closed Loop Fuel
Thermostat MonitorInitial Closed Loop
Fuel Entry Condition Note: Long term fuel trim
corrections are learned into
an 8x10 cell table as a
function of rpm and load
or
an 8x1 cell table as a function
of rpm and air mass
P0172
(Bank 1 Rich)
Fuel System MonitorFuel System Too
Rich Or Too Lean
P0171
(Bank 1 Lean)Excessive long and short term
fuel trim corrections
Footnote c)
Insufficient Coolant
Temperature For
Closed Loop Fuel
Control P0128 Time to reach minimum
engine coolant temp Footnote a)
3
Page 892 of 947
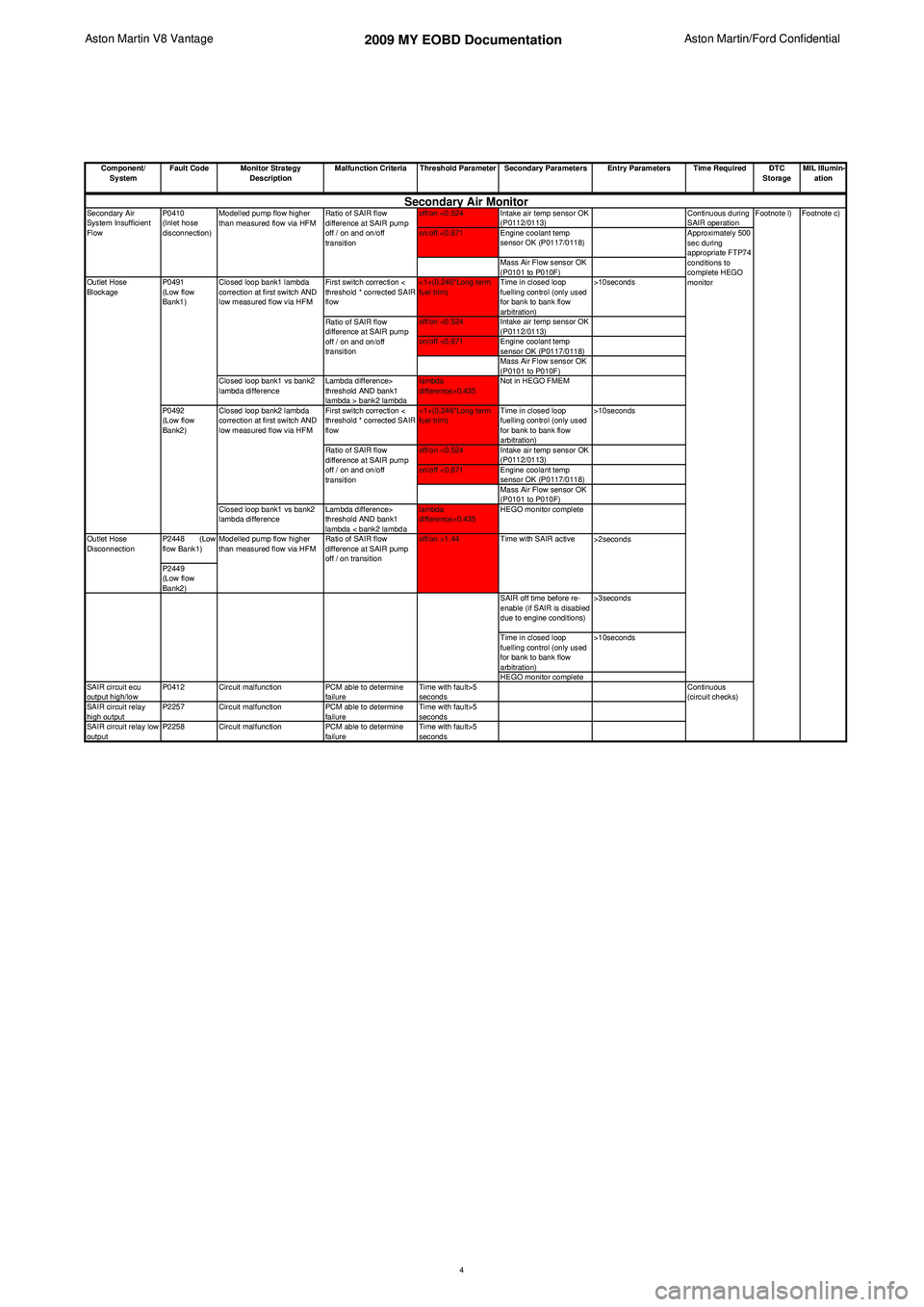
Aston Martin V8 Vantage 2009 MY EOBD DocumentationAston Martin/Ford Confidential
Component/ System Fault Code Monitor Strategy
Description Malfunction Criteria Threshold Parameter Secondary Parameters Entry Parameters Time Required DTC
StorageMIL Illumin-
ation
off/on <0.524 Intake air temp sensor OK (P0112/0113) Continuous during
SAIR operation
on/off <0.671 Engine coolant temp sensor OK (P0117/0118)
Mass Air Flow sensor OK
(P0101 to P010F)
First switch correction <
threshold * corrected SAIR
flow <1+(0.246*Long term
fuel trim)
Time in closed loop
fuelling control (only used
for bank to bank flow
arbitration) >10seconds
off/on <0.524 Intake air temp sensor OK (P0112/0113)
on/off <0.671 Engine coolant temp sensor OK (P0117/0118)
Mass Air Flow sensor OK
(P0101 to P010F)
Closed loop bank1 vs bank2
lambda difference Lambda difference>
threshold AND bank1
lambda > bank2 lambdalambda
difference>0.435
Not in HEGO FMEM
First switch correction <
threshold * corrected SAIR
flow <1+(0.246*Long term
fuel trim)
Time in closed loop
fuelling control (only used
for bank to bank flow
arbitration) >10seconds
off/on <0.524 Intake air temp sensor OK (P0112/0113)
on/off <0.671 Engine coolant temp sensor OK (P0117/0118)
Mass Air Flow sensor OK
(P0101 to P010F)
Closed loop bank1 vs bank2
lambda difference Lambda difference>
threshold AND bank1
lambda < bank2 lambdalambda
difference>0.435
HEGO monitor complete
P2448 (Low
flow Bank1)
P2449
(Low flow
Bank2) SAIR off time before re-
enable (if SAIR is disabled
due to engine conditions)>3seconds
Time in closed loop
fuelling control (only used
for bank to bank flow
arbitration) >10seconds
HEGO monitor complete
SAIR circuit ecu
output high/low P0412 Circuit malfunction
PCM able to determine
failure Time with fault>5
seconds
SAIR circuit relay
high output P2257 Circuit malfunction
PCM able to determine
failure Time with fault>5
seconds
SAIR circuit relay low
output P2258 Circuit malfunction
PCM able to determine
failure Time with fault>5
seconds
Ratio of SAIR flow
difference at SAIR pump
off / on and on/off
transition
Modelled pump flow higher
than measured flow via HFM
Ratio of SAIR flow
difference at SAIR pump
off / on and on/off
transition
Ratio of SAIR flow
difference at SAIR pump
off / on and on/off
transition
>2secondsFootnote c)
Approximately 500
sec during
appropriate FTP74
conditions to
complete HEGO
monitorSecondary Air Monitor
Modelled pump flow higher
than measured flow via HFM Ratio of SAIR flow
difference at SAIR pump
off / on transitionoff/on >1.44
Outlet Hose
Disconnection Footnote l)
Continuous
(circuit checks)
Outlet Hose
Blockage
P0492
(Low flow
Bank2)
P0410
(Inlet hose
disconnection)
Secondary Air
System Insufficient
Flow
Closed loop bank1 lambda
correction at first switch AND
low measured flow via HFM
Closed loop bank2 lambda
correction at first switch AND
low measured flow via HFM
P0491
(Low flow
Bank1)
Time with SAIR active
4
Page 895 of 947
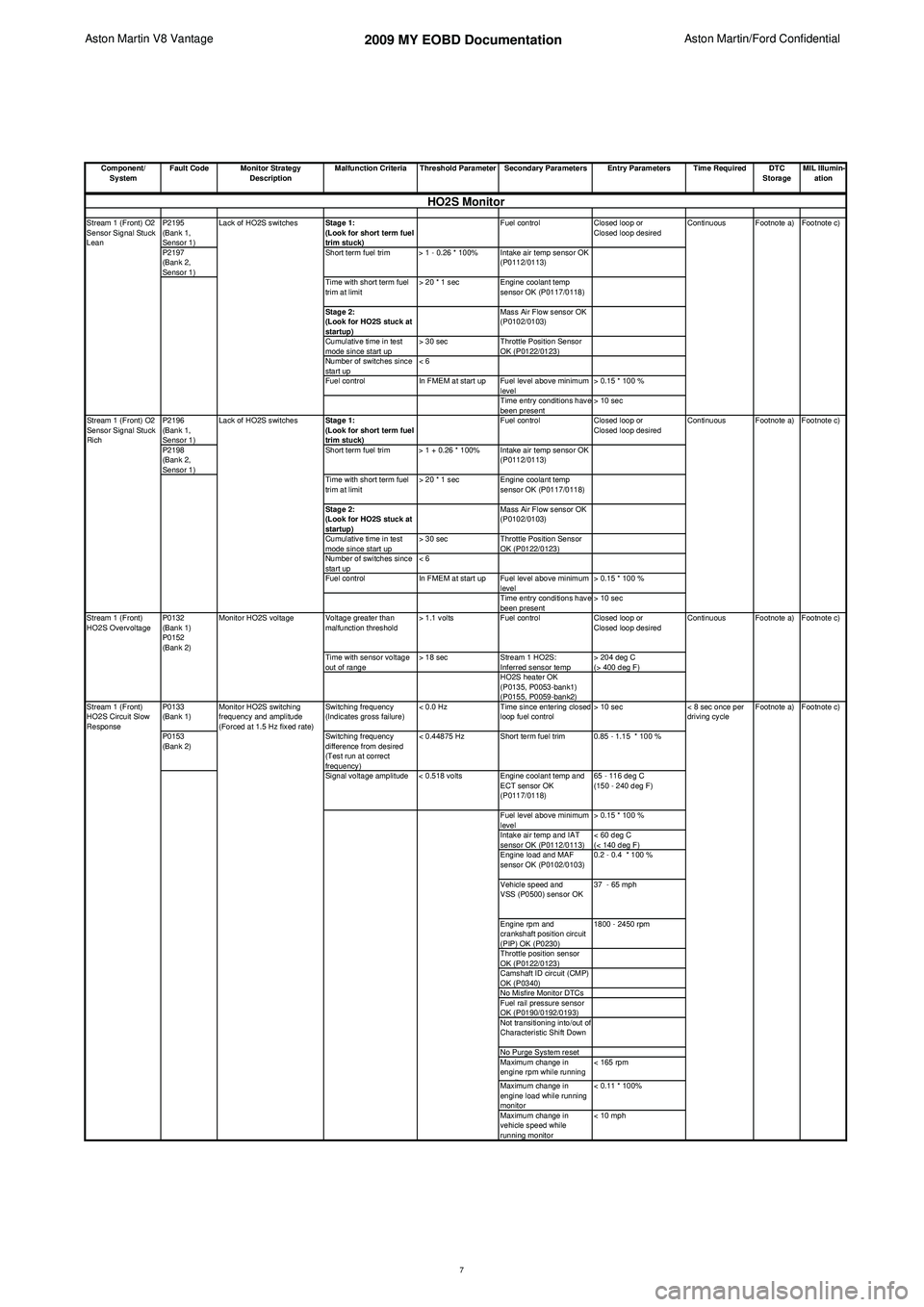
Aston Martin V8 Vantage 2009 MY EOBD DocumentationAston Martin/Ford Confidential
Component/ System Fault Code Monitor Strategy
Description Malfunction Criteria Threshold Parameter Secondary Parameters Entry Parameters Time Required DTC
StorageMIL Illumin-
ation
P2195
(Bank 1,
Sensor 1) Stage 1:
(Look for short term fuel
trim stuck) Fuel control Closed loop or
Closed loop desired
P2197
(Bank 2,
Sensor 1) Short term fuel trim > 1 - 0.26 * 100% Intake air temp sensor OK
(P0112/0113)
Time with short term fuel
trim at limit > 20 * 1 sec
Engine coolant temp
sensor OK (P0117/0118)
Stage 2:
(Look for HO2S stuck at
startup) Mass Air Flow sensor OK
(P0102/0103)
Cumulative time in test
mode since start up > 30 sec
Throttle Position Sensor
OK (P0122/0123)
Number of switches since
start up < 6
Fuel control In FMEM at start up Fuel level above minimum
level > 0.15 * 100 %
Time entry conditions have
been present > 10 sec
P2196
(Bank 1,
Sensor 1) Stage 1:
(Look for short term fuel
trim stuck) Fuel control
Closed loop or
Closed loop desired
P2198
(Bank 2,
Sensor 1) Short term fuel trim > 1 + 0.26 * 100% Intake air temp sensor OK
(P0112/0113)
Time with short term fuel
trim at limit > 20 * 1 sec
Engine coolant temp
sensor OK (P0117/0118)
Stage 2:
(Look for HO2S stuck at
startup) Mass Air Flow sensor OK
(P0102/0103)
Cumulative time in test
mode since start up > 30 sec
Throttle Position Sensor
OK (P0122/0123)
Number of switches since
start up < 6
Fuel control In FMEM at start up Fuel level above minimum
level > 0.15 * 100 %
Time entry conditions have
been present > 10 sec
Voltage greater than
malfunction threshold > 1.1 volts
Fuel control Closed loop or
Closed loop desired
Time with sensor voltage
out of range > 18 sec
Stream 1 HO2S:
Inferred sensor temp > 204 deg C
(> 400 deg F)
HO2S heater OK
(P0135, P0053-bank1)
(P0155, P0059-bank2)
P0133
(Bank 1) Switching frequency
(Indicates gross failure)< 0.0 Hz
Time since entering closed
loop fuel control > 10 sec
P0153
(Bank 2) Switching frequency
difference from desired
(Test run at correct
frequency)< 0.44875 Hz Short term fuel trim 0.85 - 1.15 * 100 %
Signal voltage amplitude < 0.518 volts Engine coolant temp and ECT sensor OK
(P0117/0118)65 - 116 deg C
(150 - 240 deg F)
Fuel level above minimum
level > 0.15 * 100 %
Intake air temp and IAT
sensor OK (P0112/0113) < 60 deg C
(< 140 deg F)
Engine load and MAF
sensor OK (P0102/0103) 0.2 - 0.4 * 100 %
Vehicle speed and
VSS (P0500) sensor OK 37 - 65 mph
Engine rpm and
crankshaft position circuit
(PIP) OK (P0230) 1800 - 2450 rpm
Throttle position sensor
OK (P0122/0123)
Camshaft ID circuit (CMP)
OK (P0340)
No Misfire Monitor DTCs
Fuel rail pressure sensor
OK (P0190/0192/0193)
Not transitioning into/out of
Characteristic Shift Down
No Purge System reset
Maximum change in
engine rpm while running
it
< 165 rpm
Maximum change in
engine load while running
monitor < 0.11 * 100%
Maximum change in
vehicle speed while
running monitor < 10 mphContinuous
Footnote a)
Footnote a)
Monitor HO2S voltage Footnote a) Footnote c)
Stream 1 (Front)
HO2S Overvoltage
< 8 sec once per
driving cycle
Stream 1 (Front)
HO2S Circuit Slow
Response Monitor HO2S switching
frequency and amplitude
(Forced at 1.5 Hz fixed rate)
P0132
(Bank 1)
P0152
(Bank 2)
Continuous Footnote a) Footnote c)Footnote c)
Continuous
Stream 1 (Front) O2
Sensor Signal Stuck
Lean
Lack of HO2S switches
Lack of HO2S switches
HO2S Monitor
Footnote c)
Stream 1 (Front) O2
Sensor Signal Stuck
Rich
7
Page 896 of 947
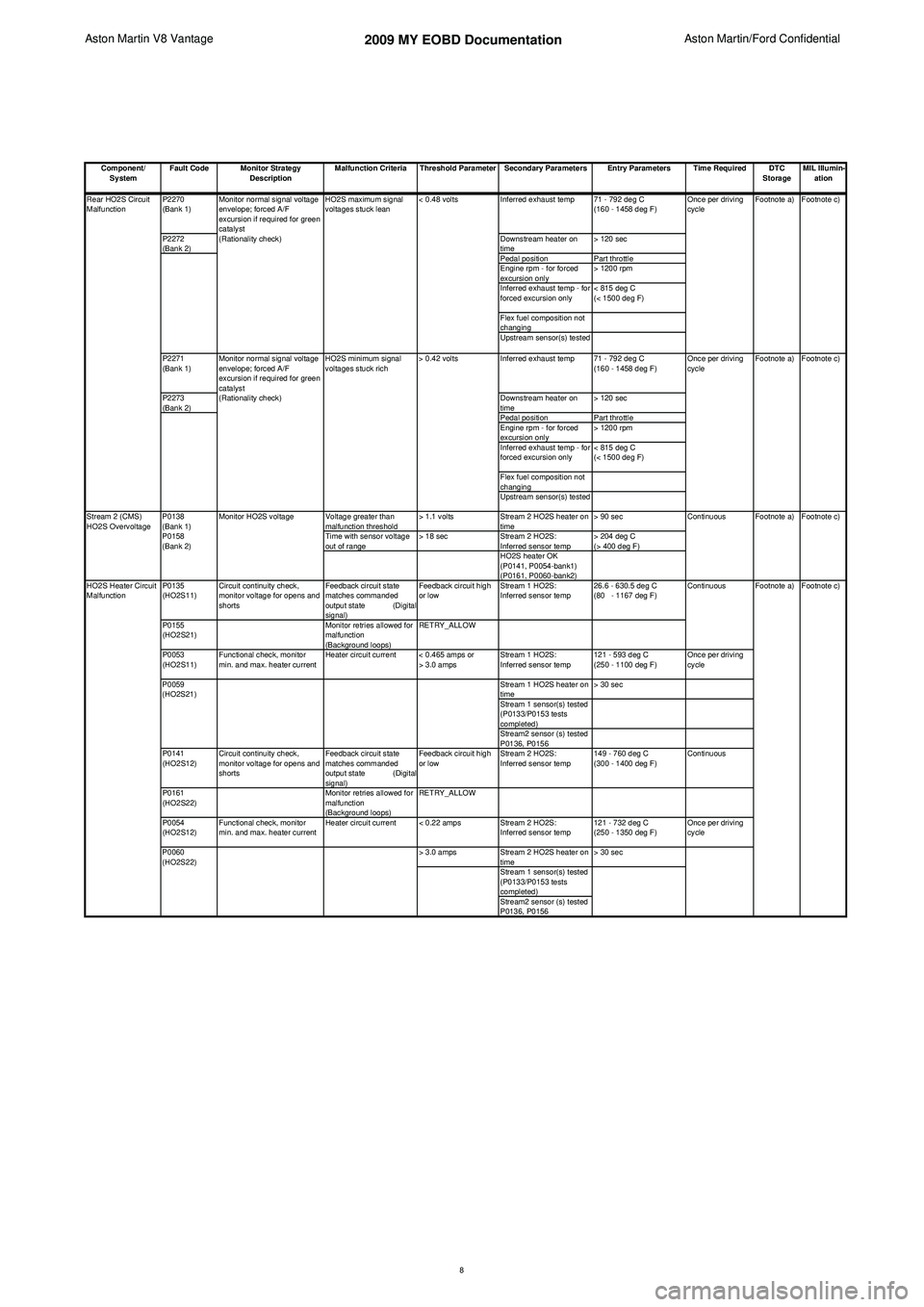
Aston Martin V8 Vantage 2009 MY EOBD DocumentationAston Martin/Ford Confidential
Component/ System Fault Code Monitor Strategy
Description Malfunction Criteria Threshold Parameter Secondary Parameters Entry Parameters Time Required DTC
StorageMIL Illumin-
ation
P2270
(Bank 1) Inferred exhaust temp 71 - 792 deg C
(160 - 1458 deg F)
P2272
(Bank 2) Downstream heater on
time> 120 sec
Pedal position Part throttle
Engine rpm - for forced
excursion only > 1200 rpm
Inferred exhaust temp - for
forced excursion only < 815 deg C
(< 1500 deg F)
Flex fuel composition not
changing
Upstream sensor(s) tested
P2271
(Bank 1) Inferred exhaust temp 71 - 792 deg C
(160 - 1458 deg F)
P2273
(Bank 2) Downstream heater on
time> 120 sec
Pedal position Part throttle
Engine rpm - for forced
excursion only > 1200 rpm
Inferred exhaust temp - for
forced excursion only < 815 deg C
(< 1500 deg F)
Flex fuel composition not
changing
Upstream sensor(s) tested
Voltage greater than
malfunction threshold > 1.1 volts
Stream 2 HO2S heater on
time > 90 sec
Time with sensor voltage
out of range > 18 sec
Stream 2 HO2S:
Inferred sensor temp > 204 deg C
(> 400 deg F)
HO2S heater OK
(P0141, P0054-bank1)
(P0161, P0060-bank2)
P0135
(HO2S11) Circuit continuity check,
monitor voltage for opens and
shorts Feedback circuit state
matches commanded
output state (Digital
signal)Feedback circuit high
or low
Stream 1 HO2S:
Inferred sensor temp 26.6 - 630.5 deg C
(80 - 1167 deg F)
P0155
(HO2S21) Monitor retries allowed for
malfunction
(Background loops)RETRY_ALLOW
P0053
(HO2S11) Functional check, monitor
min. and max. heater current Heater circuit current < 0.465 amps or
> 3.0 ampsStream 1 HO2S:
Inferred sensor temp 121 - 593 deg C
(250 - 1100 deg F)Once per driving
cycle
Stream 1 HO2S heater on
time > 30 sec
Stream 1 sensor(s) tested
(P0133/P0153 tests
completed)
Stream2 sensor (s) tested
P0136, P0156
P0141
(HO2S12) Circuit continuity check,
monitor voltage for opens and
shorts Feedback circuit state
matches commanded
output state (Digital
signal)Feedback circuit high
or low
Stream 2 HO2S:
Inferred sensor temp 149 - 760 deg C
(300 - 1400 deg F)Continuous
P0161
(HO2S22) Monitor retries allowed for
malfunction
(Background loops)RETRY_ALLOW
P0054
(HO2S12) Functional check, monitor
min. and max. heater current Heater circuit current < 0.22 amps
Stream 2 HO2S:
Inferred sensor temp 121 - 732 deg C
(250 - 1350 deg F)Once per driving
cycle
> 3.0 amps Stream 2 HO2S heater on
time > 30 sec
Stream 1 sensor(s) tested
(P0133/P0153 tests
completed)
Stream2 sensor (s) tested
P0136, P0156
HO2S Heater Circuit
Malfunction
P0060
(HO2S22) Footnote a)
Continuous
Footnote a)
Once per driving
cycle
Once per driving
cycle
Monitor normal signal voltage
envelope; forced A/F
excursion if required for green
catalyst
(Rationality check)
Footnote c)
P0059
(HO2S21)
Stream 2 (CMS)
HO2S Overvoltage
P0138
(Bank 1)
P0158
(Bank 2)Monitor HO2S voltage
Monitor normal signal voltage
envelope; forced A/F
excursion if required for green
catalyst
(Rationality check)
Rear HO2S Circuit
Malfunction
HO2S minimum signal
voltages stuck rich> 0.42 volts
HO2S maximum signal
voltages stuck lean
< 0.48 volts
Footnote c)
Footnote a)
Footnote a)
Footnote c)
Footnote c)
Continuous
8