fuel ASTON MARTIN V8 VANTAGE 2010 Manual Online
[x] Cancel search | Manufacturer: ASTON MARTIN, Model Year: 2010, Model line: V8 VANTAGE, Model: ASTON MARTIN V8 VANTAGE 2010Pages: 947, PDF Size: 43.21 MB
Page 850 of 947
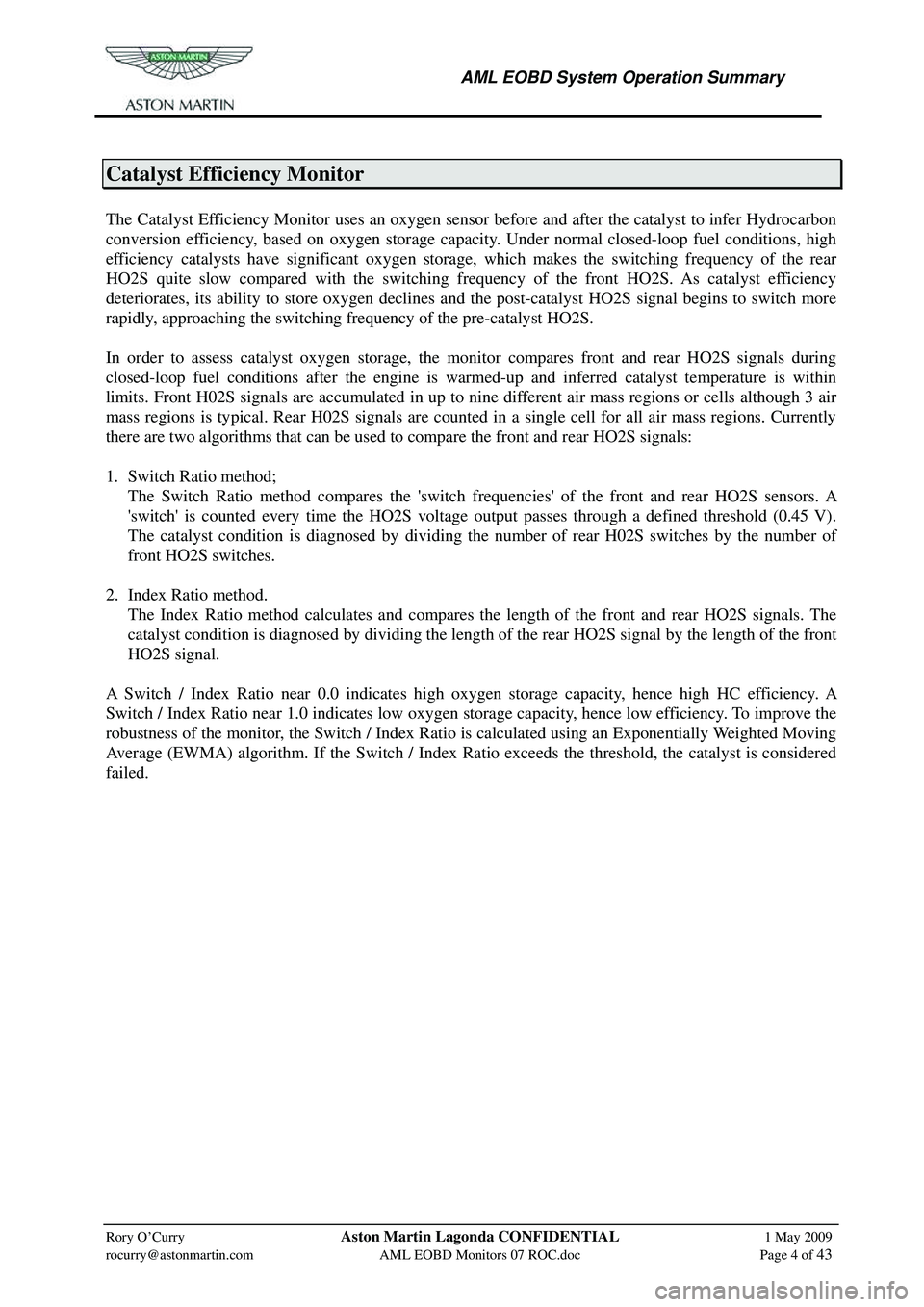
AML EOBD System Operation Summary
Rory O’Curry Aston Martin Lagonda CONFIDENTIAL 1 May 2009
[email protected] AML EOBD Monitors 07 ROC.doc Page 4 of 43
Catalyst Efficiency Monitor
The Catalyst Efficiency Monitor uses an oxygen sensor before and after the catalyst to infer Hydrocarbon
conversion efficiency, based on oxygen storage capac ity. Under normal closed-loop fuel conditions, high
efficiency catalysts have significant oxygen storage, which makes the switching frequency of the rear
HO2S quite slow compared with the switching freque ncy of the front HO2S. As catalyst efficiency
deteriorates, its ability to store oxygen declines and the post-catalyst HO2S signal begins to switch more
rapidly, approaching the switching frequency of the pre-catalyst HO2S.
In order to assess catalyst oxygen storage, the monitor compares front and rear HO2S signals during
closed-loop fuel conditions after the engine is warm ed-up and inferred catalyst temperature is within
limits. Front H02S signals are accumulated in up to ni ne different air mass regions or cells although 3 air
mass regions is typical. Rear H02S signals are counted in a single cell for all air mass regions. Currently
there are two algorithms that can be used to compare the front and rear HO2S signals:
1. Switch Ratio method;
The Switch Ratio method compares the 'switch frequencies' of the front and rear HO2S sensors. A
'switch' is counted every time the HO2S voltage output passes through a defined threshold (0.45 V).
The catalyst condition is diagnosed by dividing the number of rear H02S switches by the number of
front HO2S switches.
2. Index Ratio method.
The Index Ratio method calculates and compares the length of the front and rear HO2S signals. The
catalyst condition is diagnosed by dividing the length of the rear HO2S signal by the length of the front
HO2S signal.
A Switch / Index Ratio near 0.0 indicates high oxygen storage capacity, hence high HC efficiency. A
Switch / Index Ratio near 1.0 indicates low oxygen storage capacity, hence low efficiency. To improve the
robustness of the monitor, the Switch / Index Ratio is calculated using an Exponentially Weighted Moving
Average (EWMA) algorithm. If the Switch / Index Ratio exceeds the threshold, the catalyst is considered
failed.
Page 851 of 947

AML EOBD System Operation Summary
Rory O’Curry Aston Martin Lagonda CONFIDENTIAL 1 May 2009
[email protected] AML EOBD Monitors 07 ROC.doc Page 5 of 43
Catalyst Monitor Operation:
DTCs P0420 Bank 1, P0430 Bank 2 for Series System ( and P0420 Complete
System for 'Y pipe' configuration ).
Monitor execution once per driving cycle
Monitor Sequence HO2S monitor complete and OK
Sensors OK ECT, IAT, TP, VSS, CPS
Monitoring Duration Approximately 900 seconds dur ing appropriate conditions (approximately
200 to 600 oxygen sensor switches are collected).
Typical catalyst monitor entry conditions: Minimum Maximum
Time since engine start-up (70 oF start) 240 seconds
Engine Coolant Temp 160 oF 230 oF
Intake Air Temp 20 oF 180 oF
Engine Load 10%
Throttle Position Part Throttle Part Throttle
Time since entering closed loop fuel 30 sec
Vehicle Speed 5 mph 70 mph
Steady Air Mass Flow 1.0 lb/min 5.0 lb/min
( Note: 25 - 35 mph steady state driving must be performed to complete the monitor )
Typical malfunction thresholds:
Rear-to-front O2 sensor switch-ratio/ Index Ratio > 0.75
Catalyst Monitor temporary disablement conditions (other than entry requirements) :
EGR, Secondary air, Front and Rear O2 sensor, Engine Coolant Temperature, Mass Air Flow sensor, Air
Charge Temperature sensor, Profile Ignition Pickup & Throttle Position monitor failure.
Page 854 of 947
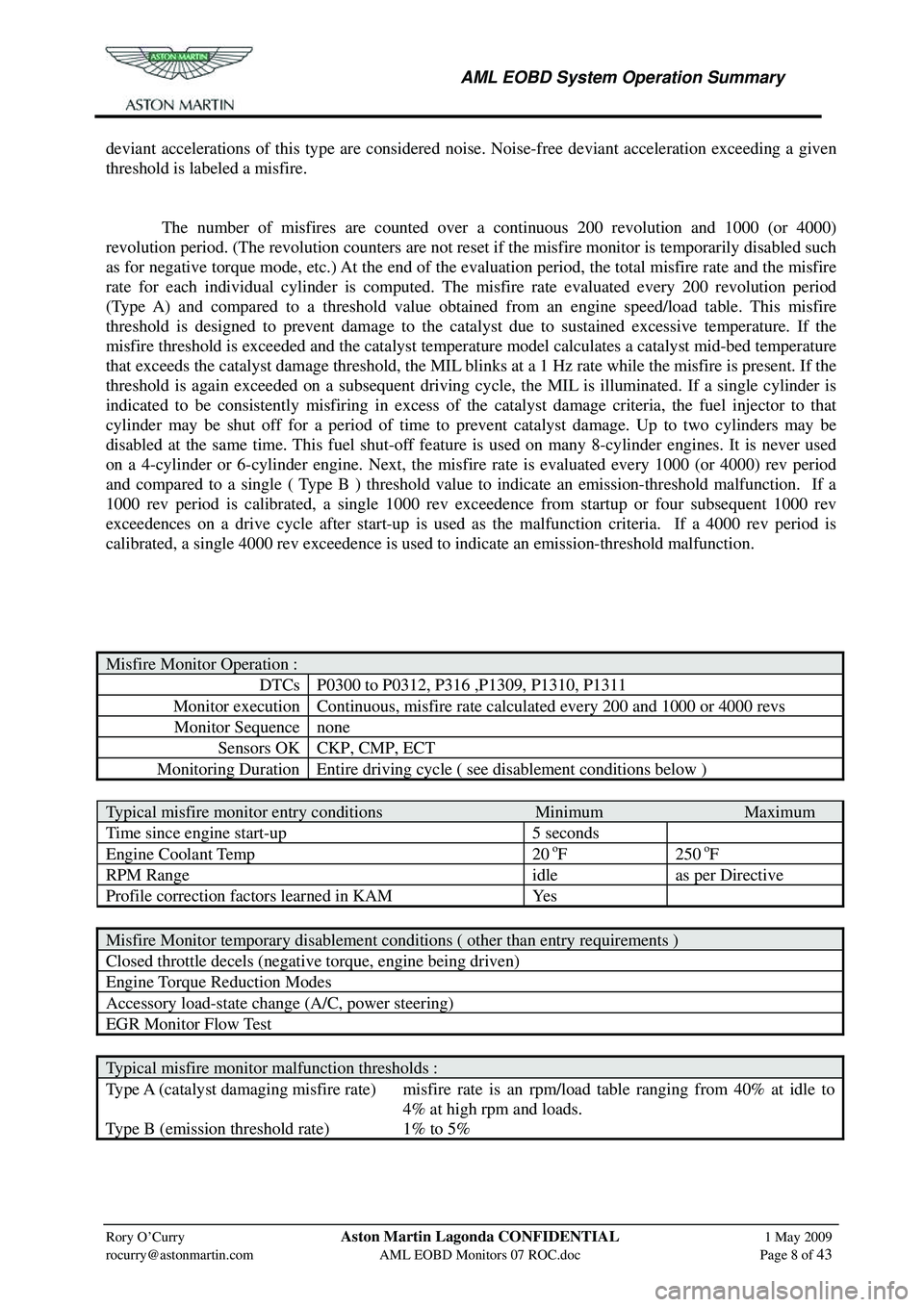
AML EOBD System Operation Summary
Rory O’Curry Aston Martin Lagonda CONFIDENTIAL 1 May 2009
[email protected] AML EOBD Monitors 07 ROC.doc Page 8 of 43
deviant accelerations of this type are considered noise. Noise-free deviant acceleration exceeding a given
threshold is labeled a misfire.
The number of misfires are counted over a continuous 200 revolution and 1000 (or 4000)
revolution period. (The revolution counters are not reset if the misfire monitor is temporarily disabled such
as for negative torque mode, etc.) At the end of the evaluation period, the total misfire rate and the misfire
rate for each individual cylinder is computed. The misfire rate evaluated every 200 revolution period
(Type A) and compared to a threshold value obtaine d from an engine speed/load table. This misfire
threshold is designed to prevent damage to the cat alyst due to sustained excessive temperature. If the
misfire threshold is exceeded and the catalyst temperature model calculates a catalyst mid-bed temperature
that exceeds the catalyst damage threshold, the MIL blinks at a 1 Hz rate while the misfire is present. If the
threshold is again exceeded on a subsequent driving cy cle, the MIL is illuminated. If a single cylinder is
indicated to be consistently misfiring in excess of the catalyst damage criteria, the fuel injector to that
cylinder may be shut off for a period of time to pr event catalyst damage. Up to two cylinders may be
disabled at the same time. This fuel shut-off feature is used on many 8-cylinder engines. It is never used
on a 4-cylinder or 6-cylinder engine. Next, the misf ire rate is evaluated every 1000 (or 4000) rev period
and compared to a single ( Type B ) threshold value to indicate an emission-threshold malfunction. If a
1000 rev period is calibrated, a single 1000 rev exceedence from startup or four subsequent 1000 rev
exceedences on a drive cycle after start-up is used as the malfunction criteria. If a 4000 rev period is
calibrated, a single 4000 rev exceedence is used to indicate an emission-threshold malfunction.
Misfire Monitor Operation :
DTCs P0300 to P0312, P316 ,P1309, P1310, P1311
Monitor execution Continuous, misfire rate calculated every 200 and 1000 or 4000 revs
Monitor Sequence none
Sensors OK CKP, CMP, ECT
Monitoring Duration Entire driving cycle ( see disablement conditions below )
Typical misfire monitor entry conditions Minimum Maximum
Time since engine start-up 5 seconds
Engine Coolant Temp 20 oF 250 oF
RPM Range idle as per Directive
Profile correction factors learned in KAM Yes
Misfire Monitor temporary disablement conditions ( other than entry requirements )
Closed throttle decels (negative torque, engine being driven)
Engine Torque Reduction Modes
Accessory load-state change (A/C, power steering)
EGR Monitor Flow Test
Typical misfire monitor malfunction thresholds :
Type A (catalyst damaging misfire rate) misfire rate is an rpm/load table ranging from 40% at idle to
4% at high rpm and loads.
Type B (emission threshold rate) 1% to 5%
Page 855 of 947
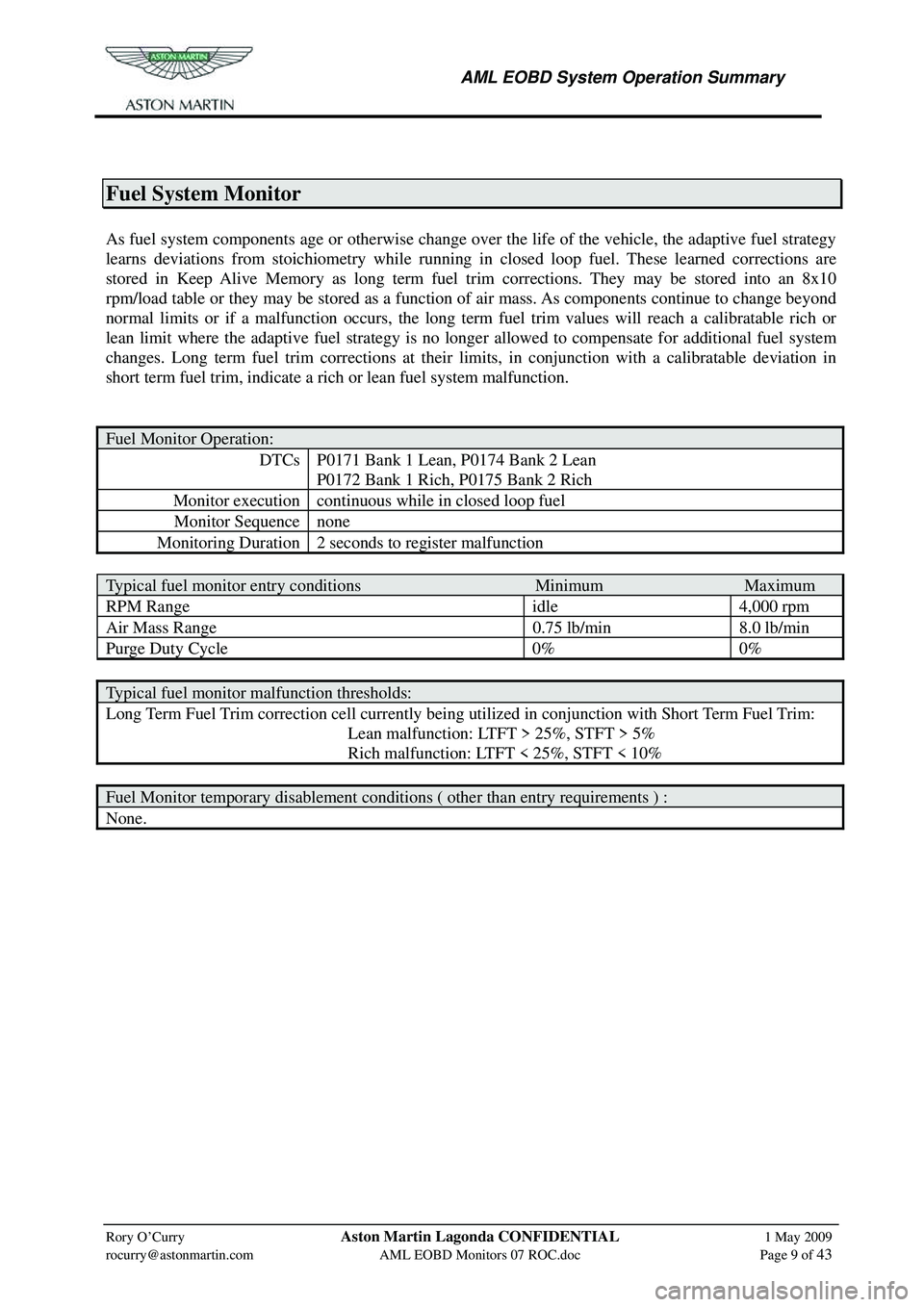
AML EOBD System Operation Summary
Rory O’Curry Aston Martin Lagonda CONFIDENTIAL 1 May 2009
[email protected] AML EOBD Monitors 07 ROC.doc Page 9 of 43
Fuel System Monitor
As fuel system components age or otherwise change over the life of the vehicle, the adaptive fuel strategy
learns deviations from stoichiometry while running in closed loop fuel. These learned corrections are
stored in Keep Alive Memory as long term fuel tr im corrections. They may be stored into an 8x10
rpm/load table or they may be stored as a function of air mass. As components continue to change beyond
normal limits or if a malfunction occurs, the long term fuel trim values will reach a calibratable rich or
lean limit where the adaptive fuel strategy is no longe r allowed to compensate for additional fuel system
changes. Long term fuel trim corrections at their limits, in conjunction with a calibratable deviation in
short term fuel trim, indicate a rich or lean fuel system malfunction.
Fuel Monitor Operation:
DTCs P0171 Bank 1 Lean, P0174 Bank 2 Lean
P0172 Bank 1 Rich, P0175 Bank 2 Rich
Monitor execution continuous while in closed loop fuel
Monitor Sequence none
Monitoring Duration 2 seconds to register malfunction
Typical fuel monitor entry conditions Minimum Maximum
RPM Range idle 4,000 rpm
Air Mass Range 0.75 lb/min 8.0 lb/min
Purge Duty Cycle 0% 0%
Typical fuel monitor malfunction thresholds:
Long Term Fuel Trim correction cell currently being utilized in conjunction with Short Term Fuel Trim:
Lean malfunction: LTFT > 25%, STFT > 5%
Rich malfunction: LTFT < 25%, STFT < 10%
Fuel Monitor temporary disablement conditions ( other than entry requirements ) :
None.
Page 856 of 947
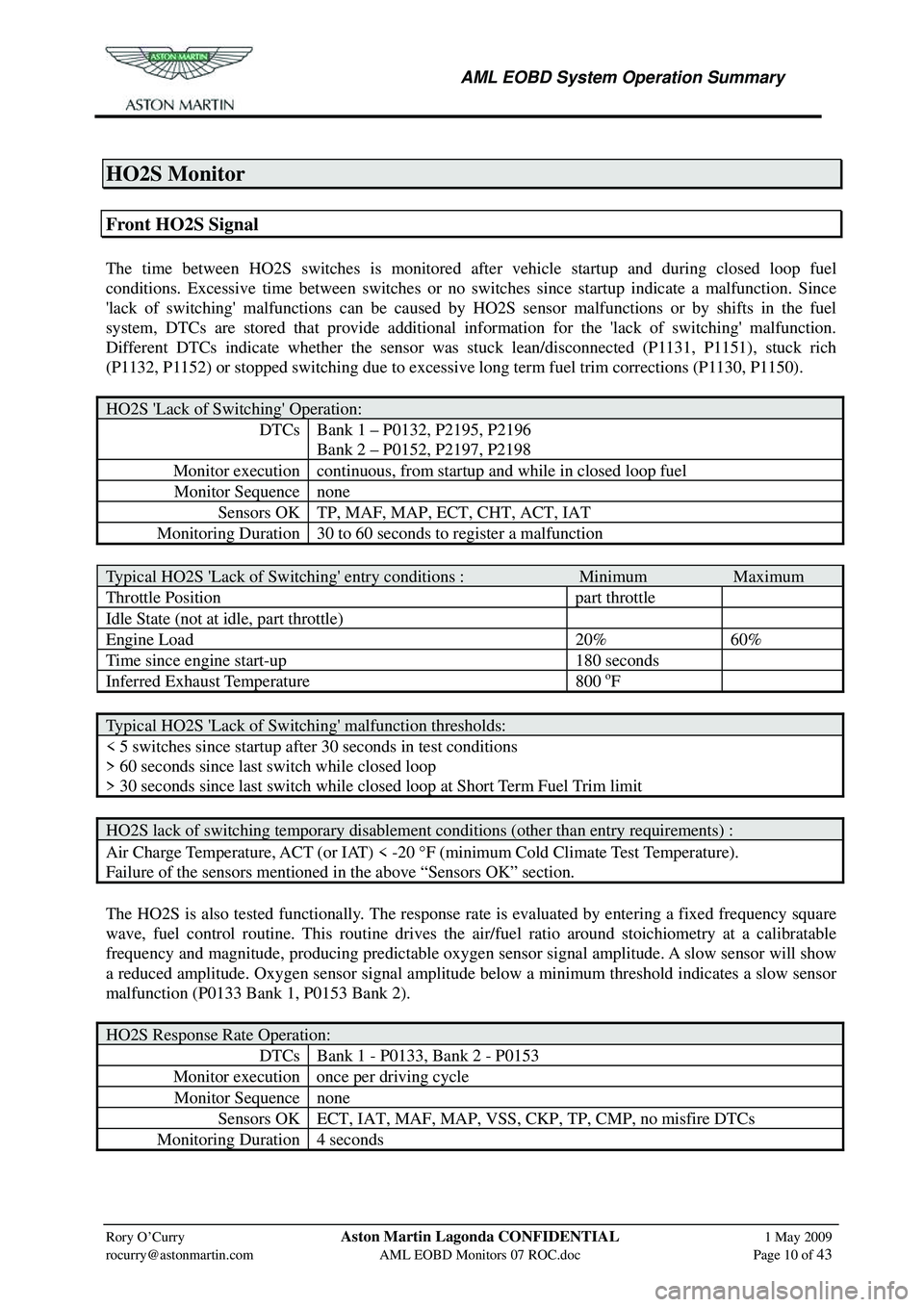
AML EOBD System Operation Summary
Rory O’Curry Aston Martin Lagonda CONFIDENTIAL 1 May 2009
[email protected] AML EOBD Monitors 07 ROC.doc Page 10 of 43
HO2S Monitor
Front HO2S Signal
The time between HO2S switches is monitored after vehicle startup and during closed loop fuel
conditions. Excessive time between switches or no switc hes since startup indicate a malfunction. Since
'lack of switching' malfunctions can be caused by HO2S sensor malfunctions or by shifts in the fuel
system, DTCs are stored that provide additional information for the 'lack of switching' malfunction.
Different DTCs indicate whether the sensor was st uck lean/disconnected (P1131, P1151), stuck rich
(P1132, P1152) or stopped switching due to excessive long term fuel trim corrections (P1130, P1150).
HO2S 'Lack of Switching' Operation:
DTCs Bank 1 – P0132, P2195, P2196
Bank 2 – P0152, P2197, P2198
Monitor execution continuous, from startup and while in closed loop fuel
Monitor Sequence none
Sensors OK TP, MAF, MAP, ECT, CHT, ACT, IAT
Monitoring Duration 30 to 60 seconds to register a malfunction
Typical HO2S 'Lack of Switching' entry conditions : Minimum Maximum
Throttle Position part throttle
Idle State (not at idle, part throttle)
Engine Load 20% 60%
Time since engine start-up 180 seconds
Inferred Exhaust Temperature 800 oF
Typical HO2S 'Lack of Switching' malfunction thresholds:
< 5 switches since startup after 30 seconds in test conditions
> 60 seconds since last switch while closed loop
> 30 seconds since last switch while closed loop at Short Term Fuel Trim limit
HO2S lack of switching temporary disablement conditions (other than entry requirements) :
Air Charge Temperature, ACT (or IAT) < -20 °F (minimum Cold Climate Test Temperature).
Failure of the sensors mentioned in the above “Sensors OK” section.
The HO2S is also tested functionally. The response rate is evaluated by enteri ng a fixed frequency square
wave, fuel control routine. This routine drives the air/fuel ratio around stoichiometry at a calibratable
frequency and magnitude, producing pr edictable oxygen sensor signal amplitude. A slow sensor will show
a reduced amplitude. Oxygen sensor signal amplitude below a minimum threshold indicates a slow sensor
malfunction (P0133 Bank 1, P0153 Bank 2).
HO2S Response Rate Operation:
DTCs Bank 1 - P0133, Bank 2 - P0153
Monitor execution once per driving cycle
Monitor Sequence none
Sensors OK ECT, IAT, MAF, MAP, VSS, CKP, TP, CMP, no misfire DTCs
Monitoring Duration 4 seconds
Page 857 of 947
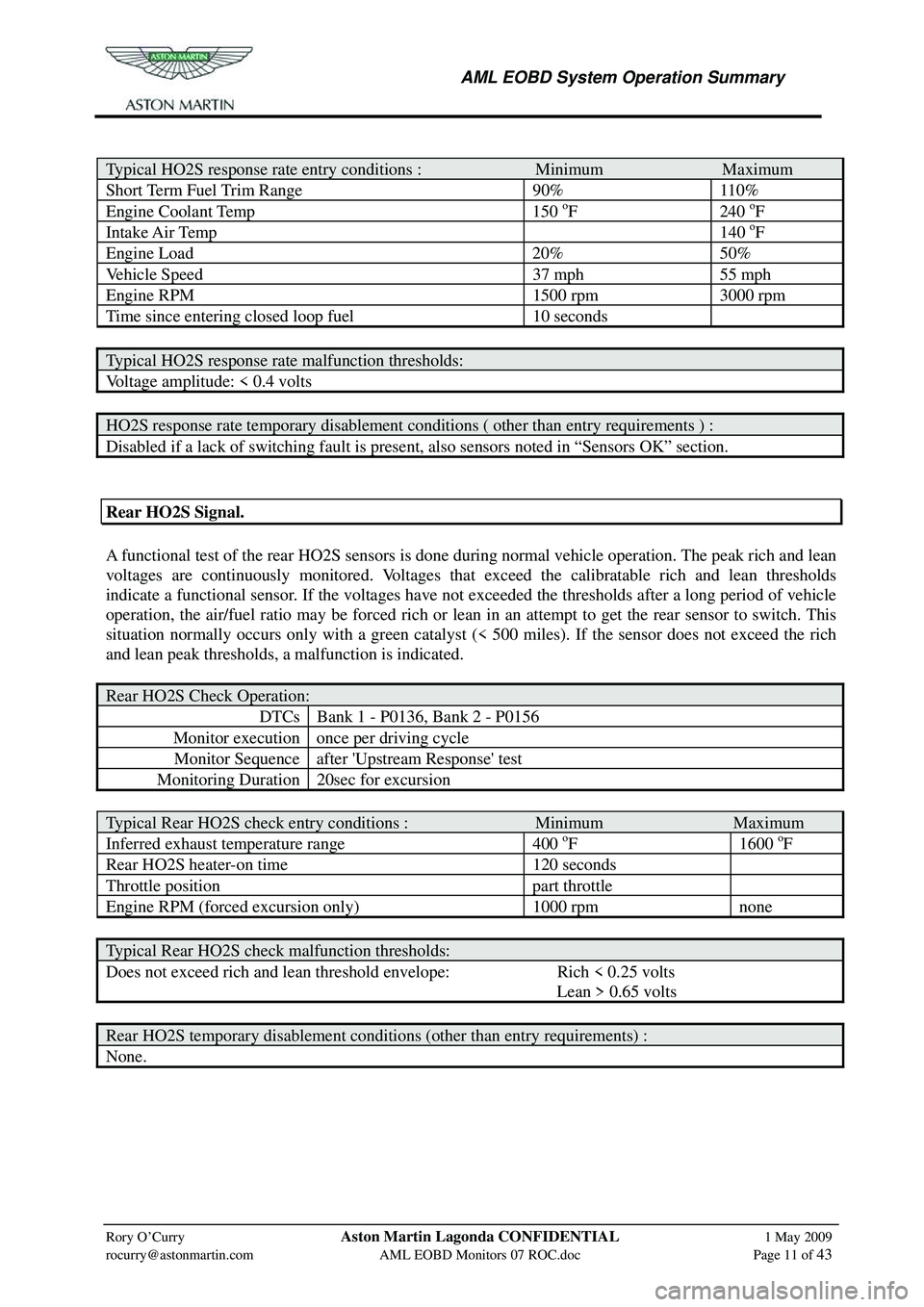
AML EOBD System Operation Summary
Rory O’Curry Aston Martin Lagonda CONFIDENTIAL 1 May 2009
[email protected] AML EOBD Monitors 07 ROC.doc Page 11 of 43
Typical HO2S response rate entry conditions : Minimum Maximum
Short Term Fuel Trim Range 90% 110%
Engine Coolant Temp 150 oF 240 oF
Intake Air Temp 140 oF
Engine Load 20% 50%
Vehicle Speed 37 mph 55 mph
Engine RPM 1500 rpm 3000 rpm
Time since entering closed loop fuel 10 seconds
Typical HO2S response rate malfunction thresholds:
Voltage amplitude: < 0.4 volts
HO2S response rate temporary disablement conditions ( other than entry requirements ) :
Disabled if a lack of switching fault is present, also sensors noted in “Sensors OK” section.
Rear HO2S Signal.
A functional test of the rear HO2S sensors is done dur ing normal vehicle operation. The peak rich and lean
voltages are continuously monitored. Voltages that exceed the calibratable rich and lean thresholds
indicate a functional sensor. If the voltages have not ex ceeded the thresholds after a long period of vehicle
operation, the air/fuel ratio may be forced rich or lean in an attempt to get the rear sensor to switch. This
situation normally occurs only with a green catalyst (< 500 miles). If the sensor does not exceed the rich
and lean peak thresholds, a malfunction is indicated.
Rear HO2S Check Operation:
DTCs Bank 1 - P0136, Bank 2 - P0156
Monitor execution once per driving cycle
Monitor Sequence after 'Upstream Response' test
Monitoring Duration 20sec for excursion
Typical Rear HO2S check entry conditions : Minimum Maximum
Inferred exhaust temperature range 400 oF 1600 oF
Rear HO2S heater-on time 120 seconds
Throttle position part throttle
Engine RPM (forced excursion only) 1000 rpm none
Typical Rear HO2S check malfunction thresholds:
Does not exceed rich and lean threshold envelope: Rich < 0.25 volts
Lean > 0.65 volts
Rear HO2S temporary disablement conditions (other than entry requirements) :
None.
Page 869 of 947
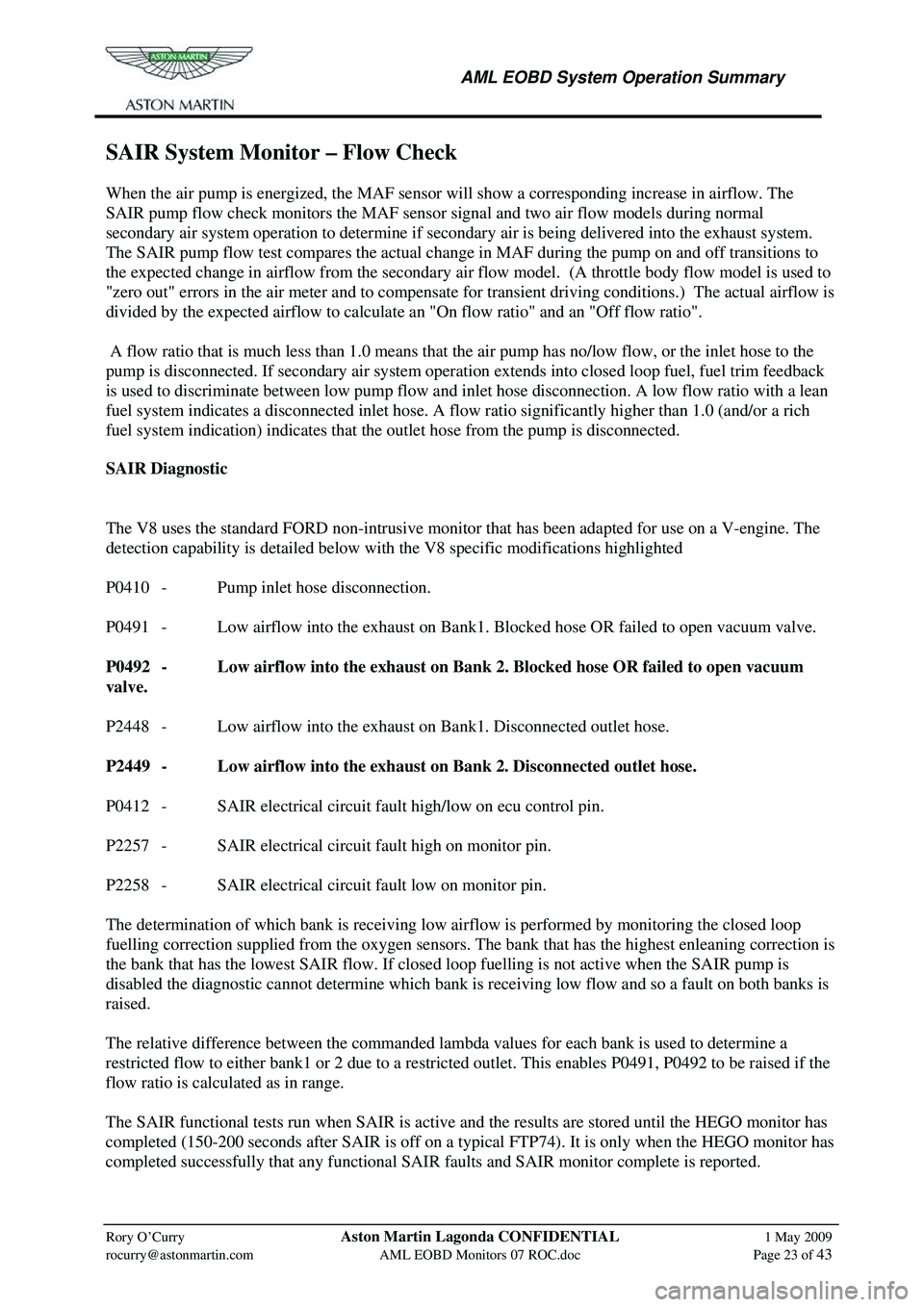
AML EOBD System Operation Summary
Rory O’Curry Aston Martin Lagonda CONFIDENTIAL 1 May 2009
[email protected] AML EOBD Monitors 07 ROC.doc Page 23 of 43
SAIR System Monitor – Flow Check
When the air pump is energized, the MAF sensor will show a corresponding increase in airflow. The
SAIR pump flow check monitors the MAF sensor signal and two air flow models during normal
secondary air system operation to determine if secondary air is being delivered into the exhaust system.
The SAIR pump flow test compares the actual change in MAF during the pump on and off transitions to
the expected change in airflow from the secondary air fl ow model. (A throttle body flow model is used to
"zero out" errors in the air meter and to compensate fo r transient driving conditions.) The actual airflow is
divided by the expected airflow to calculate an "On flow ratio" and an "Off flow ratio".
A flow ratio that is much less than 1.0 means that the air pump has no/low flow, or the inlet hose to the
pump is disconnected. If secondary air system operation ex tends into closed loop fuel, fuel trim feedback
is used to discriminate between low pump flow and in let hose disconnection. A low flow ratio with a lean
fuel system indicates a disconnected inlet hose. A flow ratio significantly higher than 1.0 (and/or a rich
fuel system indication) indicates that th e outlet hose from the pump is disconnected.
SAIR Diagnostic
The V8 uses the standard FORD non-intrusive monitor that has been adapted for use on a V-engine. The
detection capability is detailed below with the V8 specific modifications highlighted
P0410 - Pump inlet hose disconnection.
P0491 - Low airflow into the exhaust on Bank1. Blocked hose OR failed to open vacuum valve.
P0492 - Low airflow into the exhaust on Bank 2. Blocked hose OR failed to open vacuum
valve.
P2448 - Low airflow into the exhaust on Bank1. Disconnected outlet hose.
P2449 - Low airflow into the exhaust on Bank 2. Disconnected outlet hose.
P0412 - SAIR electrical circuit fault high/low on ecu control pin.
P2257 - SAIR electrical circuit fault high on monitor pin.
P2258 - SAIR electrical circuit fault low on monitor pin.
The determination of which bank is receiving low ai rflow is performed by monitoring the closed loop
fuelling correction supplied from the oxygen sensors. The bank that has the highest enleaning correction is
the bank that has the lowest SAIR flow. If closed loop fuelling is not active when the SAIR pump is
disabled the diagnostic cannot determ ine which bank is receiving low flow and so a fault on both banks is
raised.
The relative difference between the commanded lambda values for each bank is used to determine a
restricted flow to either bank1 or 2 due to a restricted outlet. This enables P0491, P0492 to be raised if the
flow ratio is calculated as in range.
The SAIR functional tests run when SAIR is active and the results are stored until the HEGO monitor has
completed (150-200 seconds after SAIR is off on a typical FTP74). It is only when the HEGO monitor has
completed successfully that any functional SAIR fa ults and SAIR monitor complete is reported.
Page 870 of 947
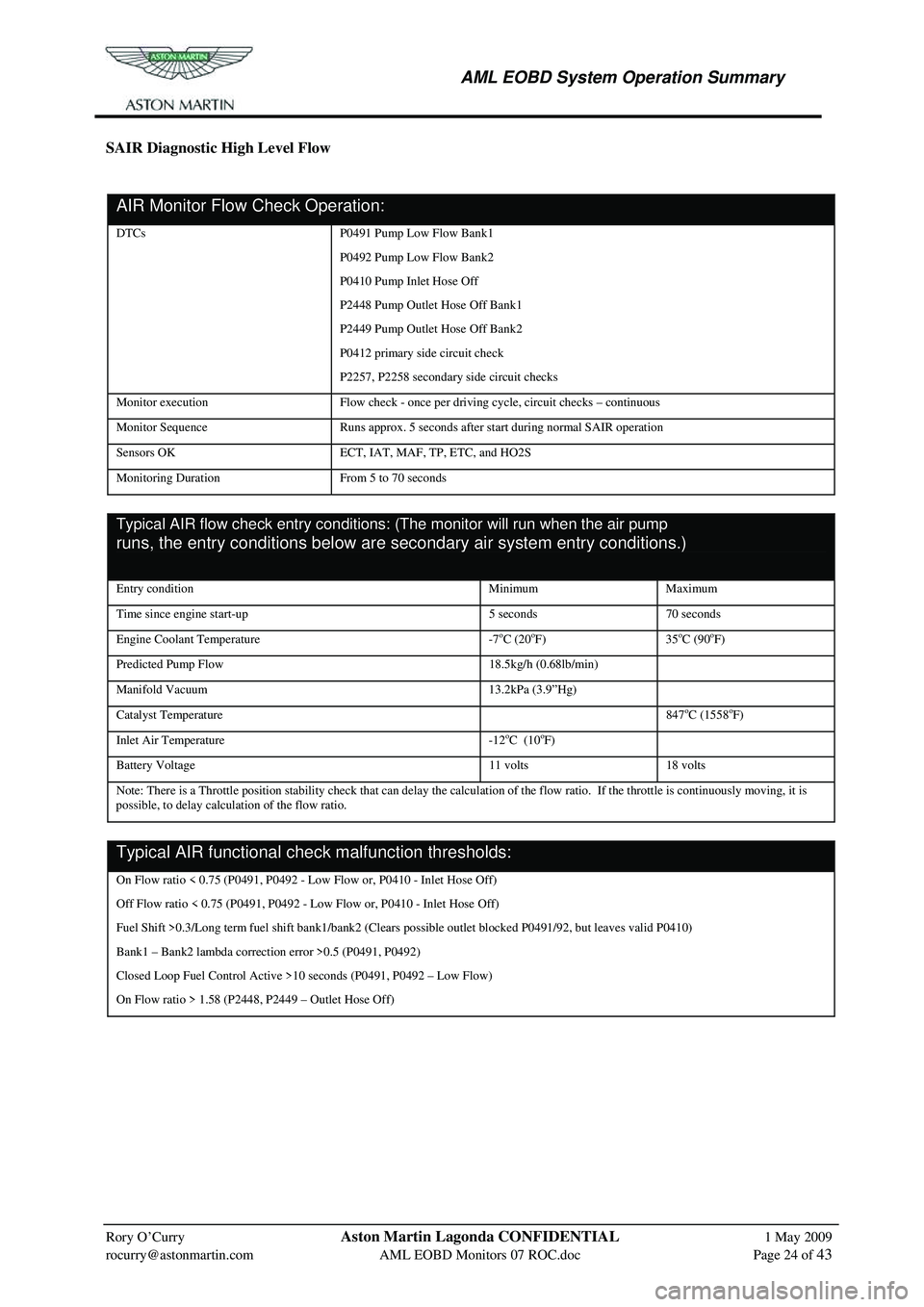
AML EOBD System Operation Summary
Rory O’Curry Aston Martin Lagonda CONFIDENTIAL 1 May 2009
[email protected] AML EOBD Monitors 07 ROC.doc Page 24 of 43
SAIR Diagnostic High Level Flow
AIR Monitor Flow Check Operation: onitor Flow Check Operation:
DTCs P0491 Pump Low Flow Bank1
P0492 Pump Low Flow Bank2
P0410 Pump Inlet Hose Off
P2448 Pump Outlet Hose Off Bank1
P2449 Pump Outlet Hose Off Bank2
P0412 primary side circuit check
P2257, P2258 secondary side circuit checks
Monitor execution Flow check - once per driving cycle, circuit checks – continuous
Monitor Sequence Runs approx. 5 seconds after start during normal SAIR operation
Sensors OK ECT, IAT, MAF, TP, ETC, and HO2S
Monitoring Duration From 5 to 70 seconds
Typical AIR flow check entry conditions: (The monitor will run when the air pump
runs, the entry conditions below are secondary air system entry conditions.) re secondary air
system entry conditions.)
Entry condition Minimum Maximum
Time since engine start-up 5 seconds 70 seconds
Engine Coolant Temperature -7oC (20oF) 35oC (90oF)
Predicted Pump Flow 18.5kg/h (0.68lb/min)
Manifold Vacuum 13.2kPa (3.9”Hg)
Catalyst Temperature 847oC (1558oF)
Inlet Air Temperature -12oC (10oF)
Battery Voltage 11 volts 18 volts
Note: There is a Throttle position stability ch eck that can delay the calculation of the flow ratio. If the throttle is continuously moving, it is
possible, to delay calculation of the flow ratio.
Typical AIR functional check malfunction thresholds:heck malfunction thresholds:
On Flow ratio < 0.75 (P0491, P0492 - Low Flow or, P0410 - Inlet Hose Off)
Off Flow ratio < 0.75 (P0491, P0492 - Lo w Flow or, P0410 - Inlet Hose Off)
Fuel Shift >0.3/Long term fuel shift bank1/bank2 (Clears possible outlet blocked P0491/92, but leaves valid P0410)
Bank1 – Bank2 lambda correcti on error >0.5 (P0491, P0492)
Closed Loop Fuel Control Active >10 seconds (P0491, P0492 – Low Flow)
On Flow ratio > 1.58 (P2448, P2449 – Outlet Hose Off)
Page 871 of 947
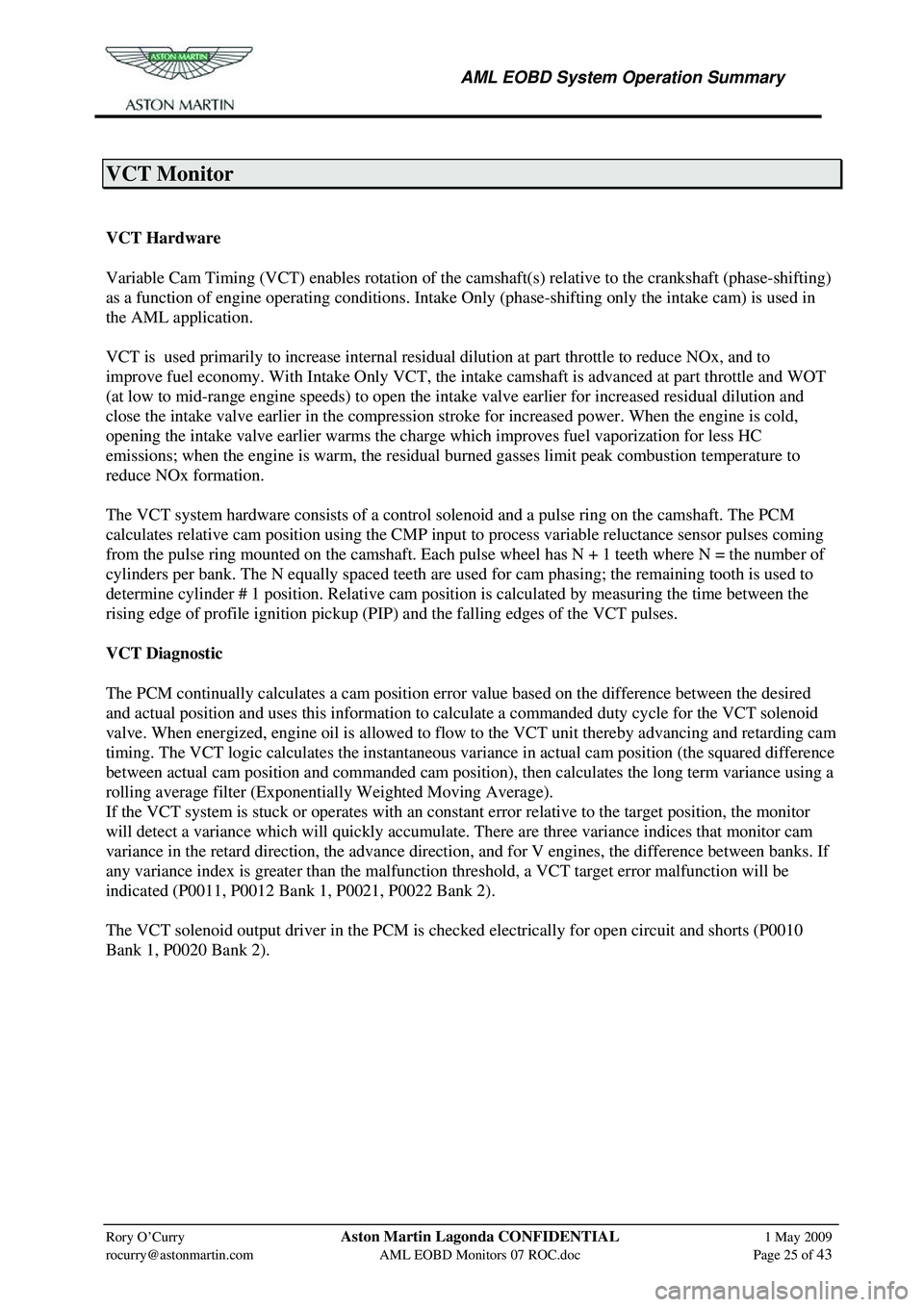
AML EOBD System Operation Summary
Rory O’Curry Aston Martin Lagonda CONFIDENTIAL 1 May 2009
[email protected] AML EOBD Monitors 07 ROC.doc Page 25 of 43
VCT Monitor
Variable Cam Timing System Monitor
VCT Hardware
Variable Cam Timing (VCT) enables rotation of the camshaft(s) relative to the crankshaft (phase-shifting)
as a function of engine operating conditions. Intake Only (phase-shifting only the intake cam) is used in
the AML application.
VCT is used primarily to increase internal residua l dilution at part throttle to reduce NOx, and to
improve fuel economy. With Intake Only VCT, the in take camshaft is advanced at part throttle and WOT
(at low to mid-range engine speeds) to open the in take valve earlier for increased residual dilution and
close the intake valve earlier in the compression stroke for increased power. When the engine is cold,
opening the intake valve earlier warms the charge which improves fuel vaporization for less HC
emissions; when the engine is warm, the residua l burned gasses limit peak combustion temperature to
reduce NOx formation.
The VCT system hardware consists of a contro l solenoid and a pulse ring on the camshaft. The PCM
calculates relative cam position using the CMP input to process variable reluctance sensor pulses coming
from the pulse ring mounted on the camshaft. Each pul se wheel has N + 1 teeth where N = the number of
cylinders per bank. The N equally spaced teeth are used for cam phasing; the remaining tooth is used to
determine cylinder # 1 position. Relative cam position is calculated by measuring the time between the
rising edge of profile ignition pickup (PIP ) and the falling edges of the VCT pulses.
VCT Diagnostic
The PCM continually calculates a cam position error value based on the difference between the desired
and actual position and uses this information to cal culate a commanded duty cycle for the VCT solenoid
valve. When energized, engine oil is allowed to flow to the VCT unit thereby advancing and retarding cam
timing. The VCT logic calculates the instantaneous va riance in actual cam position (the squared difference
between actual cam position and commanded cam position), then calculates the long term variance using a
rolling average filter (Exponentially Weighted Moving Average).
If the VCT system is stuck or operates with an consta nt error relative to the target position, the monitor
will detect a variance which will quickly accumulate. There are three variance indices that monitor cam
variance in the retard direction, the advance directi on, and for V engines, the difference between banks. If
any variance index is greater than the malfunction threshold, a VCT target error malfunction will be
indicated (P0011, P0012 Bank 1, P0021, P0022 Bank 2).
The VCT solenoid output driver in the PCM is check ed electrically for open circuit and shorts (P0010
Bank 1, P0020 Bank 2).
VCT Monitor Operation:
Page 874 of 947
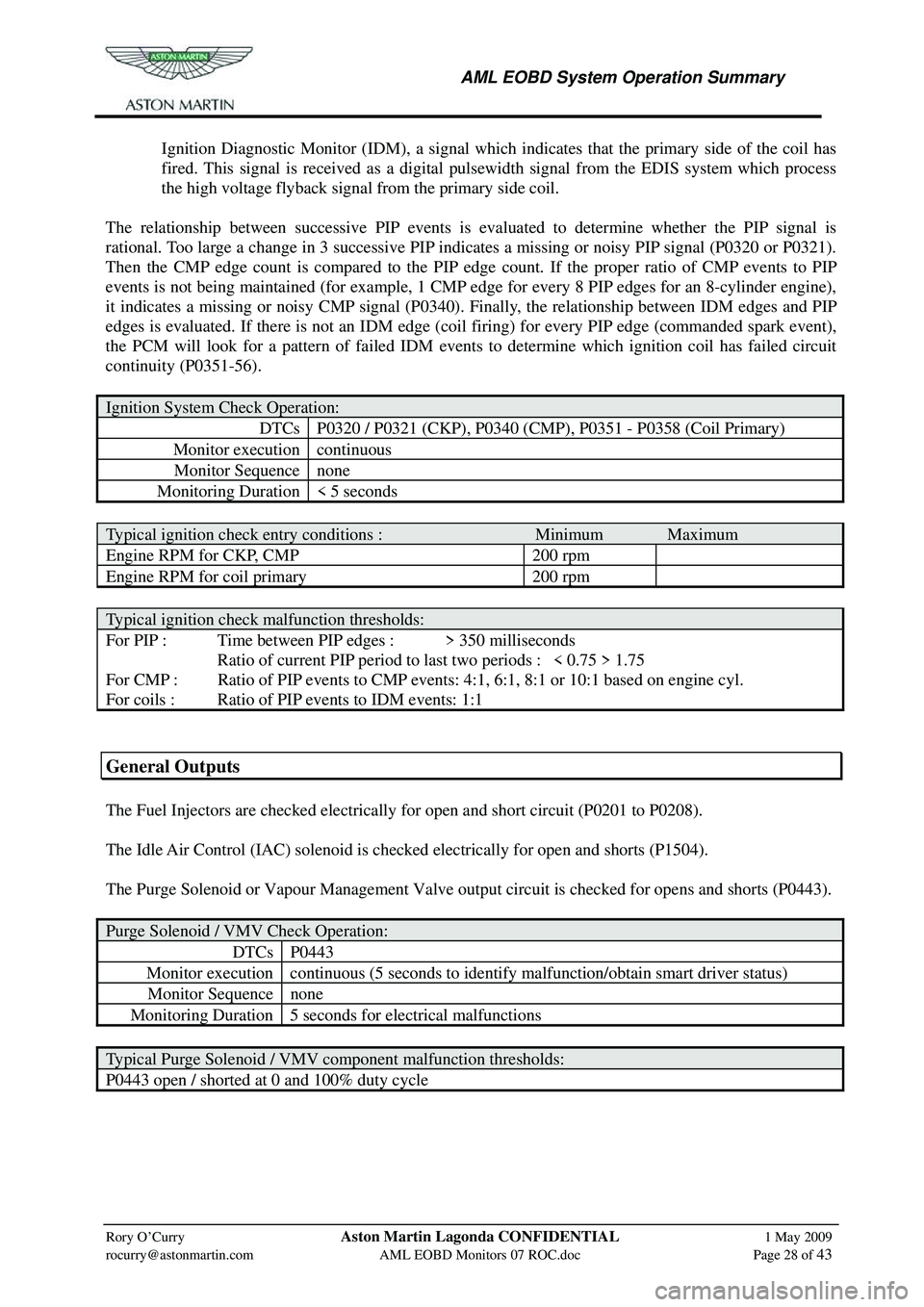
AML EOBD System Operation Summary
Rory O’Curry Aston Martin Lagonda CONFIDENTIAL 1 May 2009
[email protected] AML EOBD Monitors 07 ROC.doc Page 28 of 43
Ignition Diagnostic Monitor (IDM), a signal which indicates that the primary side of the coil has
fired. This signal is received as a digital pulsewidth signal from the EDIS system which process
the high voltage flyback signal from the primary side coil.
The relationship between successive PIP events is ev aluated to determine whether the PIP signal is
rational. Too large a change in 3 successive PIP indicates a missing or noisy PIP signal (P0320 or P0321).
Then the CMP edge count is compared to the PIP e dge count. If the proper ratio of CMP events to PIP
events is not being maintained (for example, 1 CMP e dge for every 8 PIP edges for an 8-cylinder engine),
it indicates a missing or noisy CMP signal (P0340). Finally, the relationship between IDM edges and PIP
edges is evaluated. If there is not an IDM edge (co il firing) for every PIP edge (commanded spark event),
the PCM will look for a pattern of failed IDM events to determine which ignition coil has failed circuit
continuity (P0351-56).
Ignition System Check Operation:
DTCs P0320 / P0321 (CKP), P0340 (CMP), P0351 - P0358 (Coil Primary)
Monitor execution continuous
Monitor Sequence none
Monitoring Duration < 5 seconds
Typical ignition check entry conditions : Minimum Maximum
Engine RPM for CKP, CMP 200 rpm
Engine RPM for coil primary 200 rpm
Typical ignition check malfunction thresholds:
For PIP : Time between PIP edges : > 350 milliseconds
Ratio of current PIP period to last two periods : < 0.75 > 1.75
For CMP : Ratio of PIP events to CMP events: 4:1, 6:1, 8:1 or 10:1 based on engine cyl.
For coils : Ratio of PIP events to IDM events: 1:1
General Outputs
The Fuel Injectors are checked electrically for open and short circuit (P0201 to P0208).
The Idle Air Control (IAC) solenoid is checked electrically for open and shorts (P1504).
The Purge Solenoid or Vapour Management Valve output circuit is checked for opens and shorts (P0443).
Purge Solenoid / VMV Check Operation:
DTCsP0443
Monitor execution continuous (5 seconds to identify malfunction/obtain smart driver status)
Monitor Sequencenone
Monitoring Duration 5 seconds for electrical malfunctions
Typical Purge Solenoid / VMV component malfunction thresholds:
P0443 open / shorted at 0 and 100% duty cycle