maintenance ASTON MARTIN V8 VANTAGE 2010 Service Manual
[x] Cancel search | Manufacturer: ASTON MARTIN, Model Year: 2010, Model line: V8 VANTAGE, Model: ASTON MARTIN V8 VANTAGE 2010Pages: 947, PDF Size: 43.21 MB
Page 321 of 947
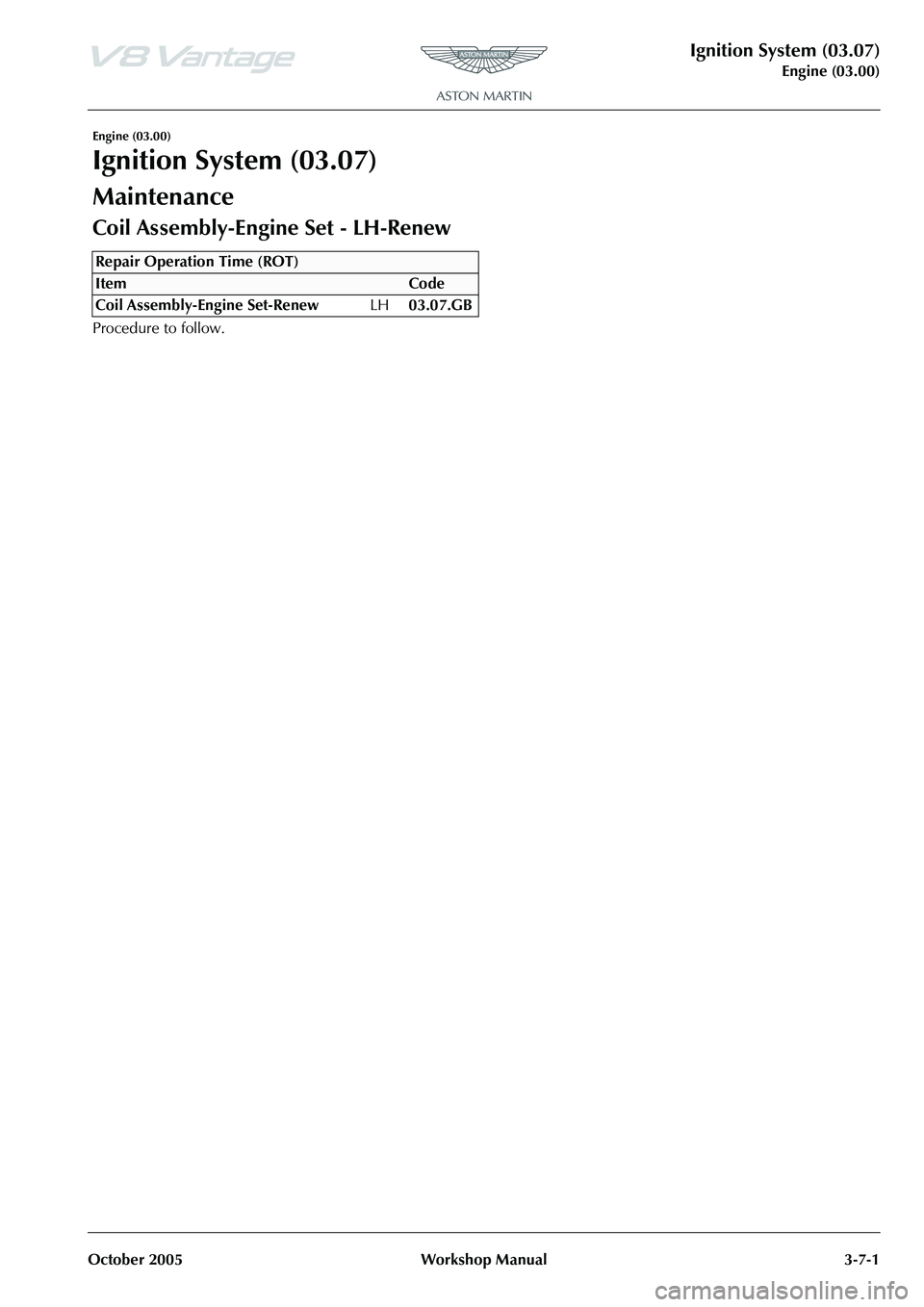
Ignition System (03.07)
Engine (03.00)
October 2005 Workshop Manual 3-7-1
Engine (03.00)
Ignition System (03.07)
Maintenance
Repair Operation Time (ROT)
Page 323 of 947
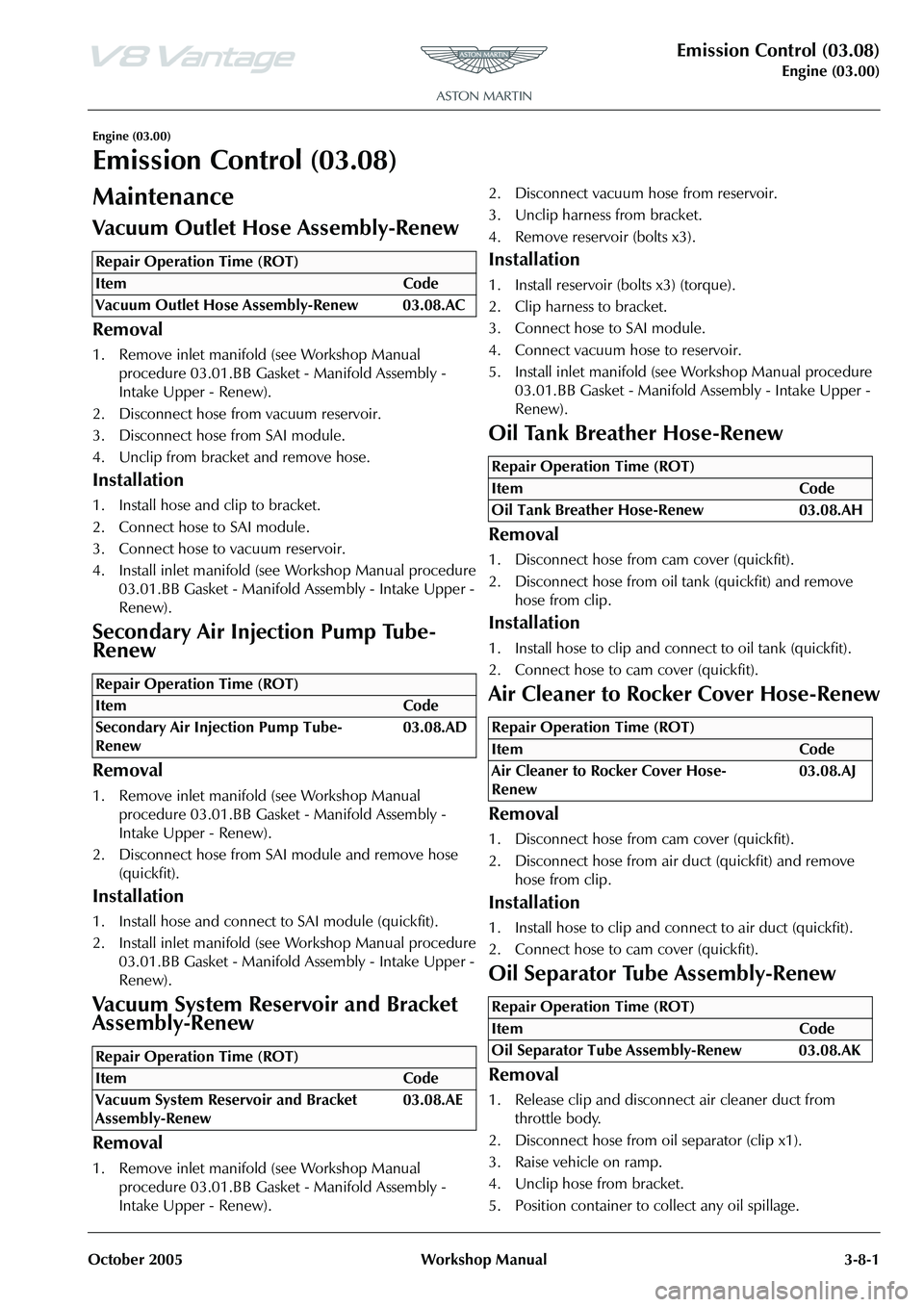
Emission Control (03.08)
Engine (03.00)
October 2005 Workshop Manual 3-8-1
Engine (03.00)
Emission Control (03.08)
Maintenance
Removal
1. Release clip and disconnect air cleaner duct from
throttle body.
2. Disconnect hose from oil separator (clip x1).
3. Raise vehicle on ramp.
4. Unclip hose from bracket.
5. Position container to collect any oil spillage.
Repair Operation Time (ROT)
Repair Operation Time (ROT)
Repair Operation Time (ROT)
Repair Operation Time (ROT)
Repair Operation Time (ROT)
Repair Operation Time (ROT)
Page 327 of 947
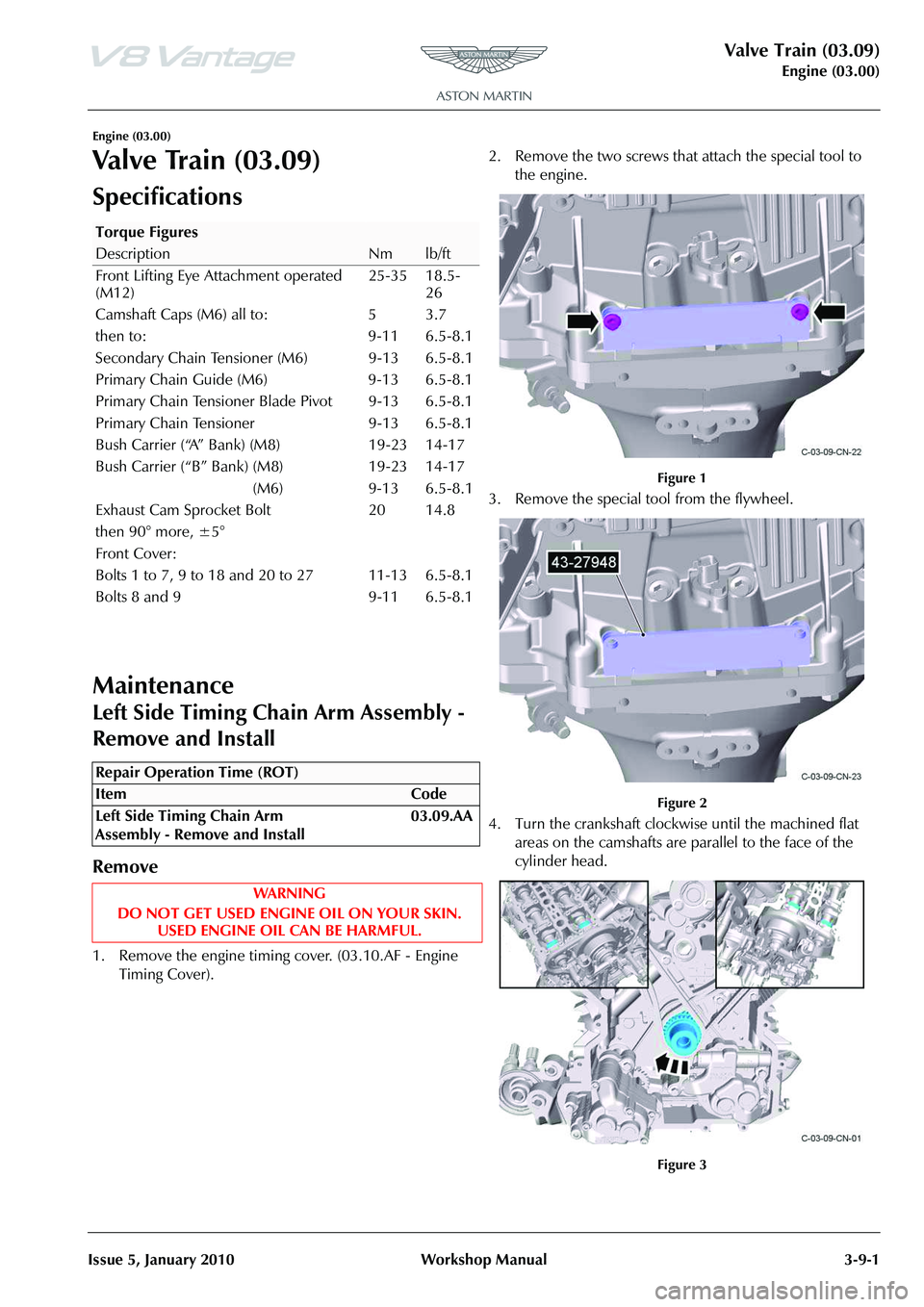
Valve Train (03.09)
Engine (03.00)
Issue 5, January 2010 Workshop Manual 3-9-1
Engine (03.00)
Valve Train (03.09)
Specifications
Maintenance
Left Side Timing Chain Arm Assembly -
Remove and Install
Remove
1. Remove the engine timing cover. (03.10.AF - Engine Timing Cover). 2. Remove the two screws that attach the special tool to
the engine.
Figure 1
3. Remove the special tool from the flywheel.
Figure 2
4. Turn the crankshaft clockwise until the machined flat areas on the camshafts are parallel to the face of the
cylinder head.
Figure 3
Torque Figures
DescriptionNmlb/ft
Front Lifting Eye Attachment operated
(M12) 25-35 18.5-
26
Camshaft Caps (M6) all to: 5 3.7
then to: 9-11 6.5-8.1
Secondary Chain Tensioner (M6) 9-13 6.5-8.1
Primary Chain Guide (M6) 9-13 6.5-8.1
Primary Chain Tensioner Blade Pivot 9-13 6.5-8.1
Primary Chain Tensioner 9-13 6.5-8.1
Bush Carrier (“A” Bank) (M8) 19-23 14-17
Bush Carrier (“B” Bank) (M8) 19-23 14-17
(M6) 9-13 6.5-8.1
Exhaust Cam Sprocket Bolt
then 90° more, ±5° 20 14.8
Front Cover:
Bolts 1 to 7, 9 to 18 and 20 to 27
Bolts 8 and 9 11-13
9-116.5-8.1
6.5-8.1
Repair Operation Time (ROT)
Page 359 of 947
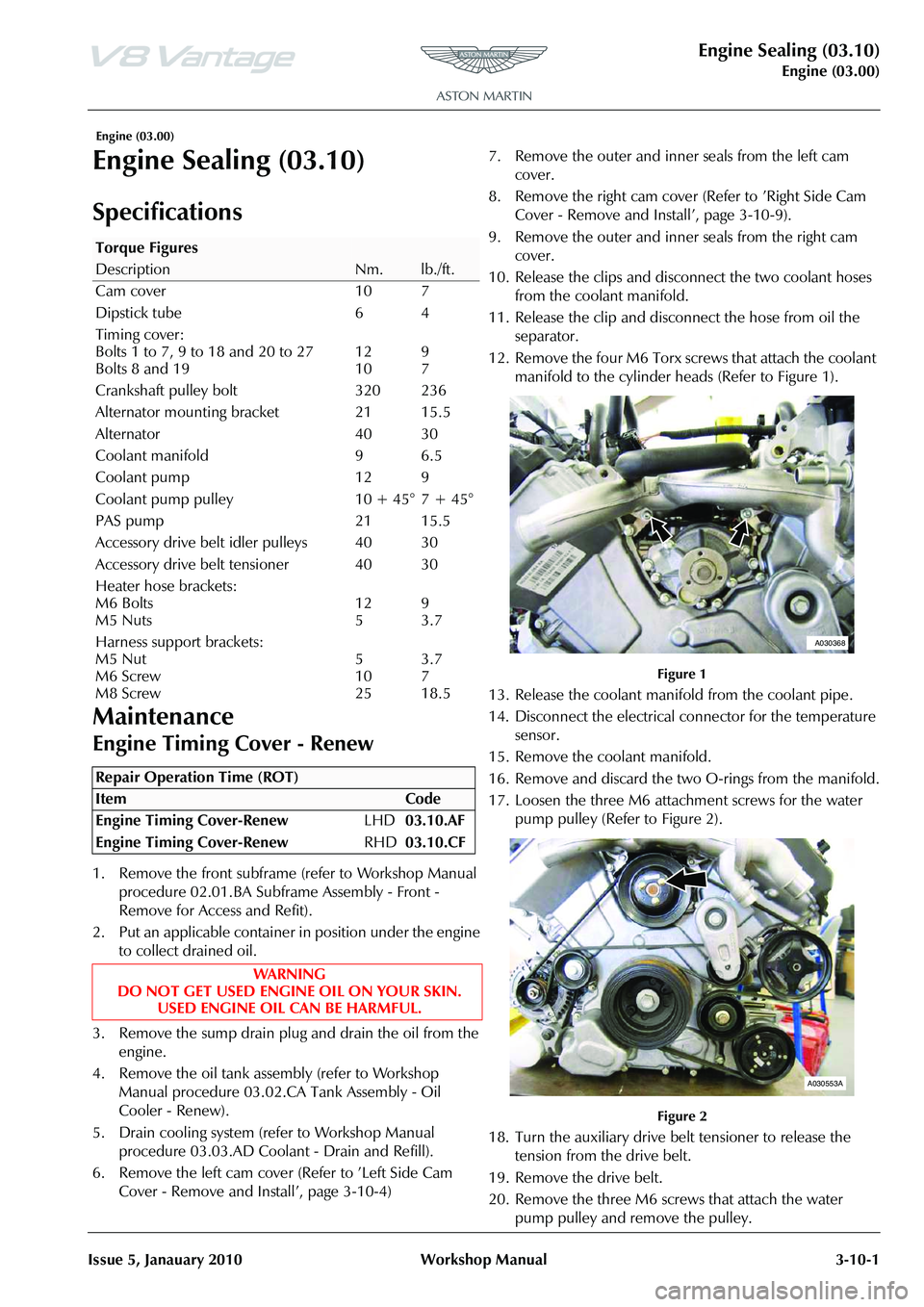
Engine Sealing (03.10)
Engine (03.00)
Issue 5, Janauary 2010 Workshop Manual 3-10-1
Engine (03.00)
Engine Sealing (03.10)
Specifications
Maintenance
Engine Timing Cover - Renew
1. Remove the front subframe (refer to Workshop Manual procedure 02.01.BA Subframe Assembly - Front -
Remove for Access and Refit).
2. Put an applicable container in position under the engine
to collect drained oil.
3. Remove the sump drain plug and drain the oil from the engine.
4. Remove the oil tank assembly (refer to Workshop Manual procedure 03.02.CA Tank Assembly - Oil
Cooler - Renew).
5. Drain cooling system (refer to Workshop Manual procedure 03.03.AD Coolant - Drain and Refill).
6. Remove the left cam cover (Refer to ’Left Side Cam Cover - Remove and Install’, page 3-10-4) 7. Remove the outer and inner seals from the left cam
cover.
8. Remove the right cam cover (Refer to ’Right Side Cam Cover - Remove and Install’, page 3-10-9).
9. Remove the outer and inner seals from the right cam cover.
10. Release the clips and disconnect the two coolant hoses from the coolant manifold.
11. Release the clip and disconnect the hose from oil the separator.
12. Remove the four M6 Torx screws that attach the coolant manifold to the cylinder heads (Refer to Figure 1).
Figure 1
13. Release the coolant manifold from the coolant pipe.
14. Disconnect the electrical connector for the temperature sensor.
15. Remove the coolant manifold.
16. Remove and discard the two O-rings from the manifold.
17. Loosen the three M6 attachment screws for the water pump pulley (Refer to Figure 2).
Figure 2
18. Turn the auxiliary drive be lt tensioner to release the
tension from the drive belt.
19. Remove the drive belt.
20. Remove the three M6 screws that attach the water pump pulley and remove the pulley.
Torque Figures
DescriptionNm.lb./ft.
Cam cover 10 7
Dipstick tube 6 4
Timing cover:
Bolts 1 to 7, 9 to 18 and 20 to 27
Bolts 8 and 19
12
10
9
7
Crankshaft pulley bolt 320 236
Alternator mounting bracket 21 15.5
Alternator 40 30
Coolant manifold 9 6.5
Coolant pump 12 9
Coolant pump pulley 10 + 45° 7 + 45°
PAS pump 21 15.5
Accessory drive belt idler pulleys 40 30
Accessory drive be lt tensioner 40 30
Heater hose brackets:
M6 Bolts
M5 Nuts
12
5
9
3.7
Harness support brackets:
M5 Nut
M6 Screw
M8 Screw
5
10
25
3.7
7
18.5
Repair Operation Time (ROT)
A030368
A030553A
Page 373 of 947
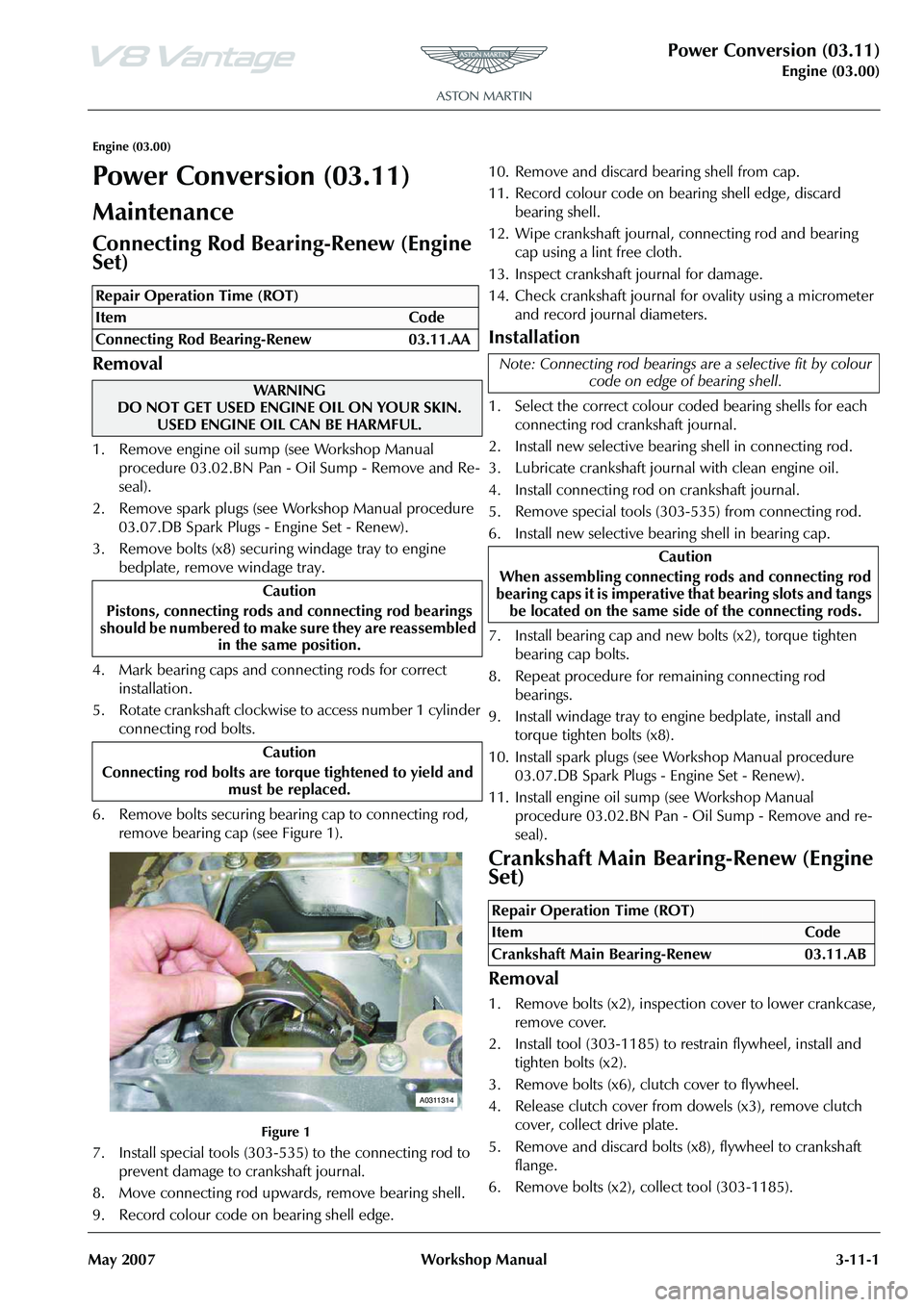
Power Conversion (03.11)
Engine (03.00)
May 2007 Workshop Manual 3-11-1
Engine (03.00)
Power Conversion (03.11)
Maintenance
Connecting Rod Bearing-Renew (Engine
Set)
Removal
1. Remove engine oil sump (see Workshop Manual
procedure 03.02.BN Pan - Oil Sump - Remove and Re-
seal).
2. Remove spark plugs (see Workshop Manual procedure 03.07.DB Spark Plugs - Engine Set - Renew).
3. Remove bolts (x8) securing windage tray to engine bedplate, remove windage tray.
4. Mark bearing caps and connecting rods for correct installation.
5. Rotate crankshaft clockwise to access number 1 cylinder connecting rod bolts.
6. Remove bolts securing bearing cap to connecting rod, remove bearing cap (see Figure 1).
Figure 1
7. Install special tools (303-535) to the connecting rod to prevent damage to crankshaft journal.
8. Move connecting rod upwards, remove bearing shell.
9. Record colour code on bearing shell edge. 10. Remove and discard bearing shell from cap.
11. Record colour code on bearing shell edge, discard
bearing shell.
12. Wipe crankshaft journal, connecting rod and bearing cap using a lint free cloth.
13. Inspect crankshaft journal for damage.
14. Check crankshaft journal for ovality using a micrometer and record journal diameters.
Installation
1. Select the correct colour coded bearing shells for each connecting rod crankshaft journal.
2. Install new selective bearing shell in connecting rod.
3. Lubricate crankshaft journal with clean engine oil.
4. Install connecting rod on crankshaft journal.
5. Remove special tools (303-535) from connecting rod.
6. Install new selective bearing shell in bearing cap.
7. Install bearing cap and new bolts (x2), torque tighten bearing cap bolts.
8. Repeat procedure for remaining connecting rod bearings.
9. Install windage tray to engine bedplate, install and torque tighten bolts (x8).
10. Install spark plugs (see Workshop Manual procedure 03.07.DB Spark Plugs - Engine Set - Renew).
11. Install engine oil sump (see Workshop Manual
procedure 03.02.BN Pan - Oil Sump - Remove and re-
seal).
Crankshaft Main Bearing-Renew (Engine
Set)
Removal
1. Remove bolts (x2), inspection cover to lower crankcase, remove cover.
2. Install tool (303-1185) to restrain flywheel, install and tighten bolts (x2).
3. Remove bolts (x6), clutch cover to flywheel.
4. Release clutch cover from dowels (x3), remove clutch cover, collect drive plate.
5. Remove and discard bolts (x8), flywheel to crankshaft flange.
6. Remove bolts (x2), collect tool (303-1185).
Repair Operation Time (ROT)
WA R N I N G
DO NOT GET USED ENGINE OIL ON YOUR SKIN. USED ENGINE OIL CAN BE HARMFUL.
Caution
Pistons, connecting rods an d connecting rod bearings
should be numbered to make sure they are reassembled
in the same position.
Caution
Connecting rod bolts are tor qu
e tightened to yield and
mu st be replaced.
A0311314
Note: Connecting rod bearings ar e a selective fit by colour
code on edge of bearing shell.
Caution
When assembling connecting rods and connecting rod
bearing caps it is imperative that bearing slots and tangs
be located on the same side of the connecting rods.
Repair Operation Time (ROT)
Page 411 of 947
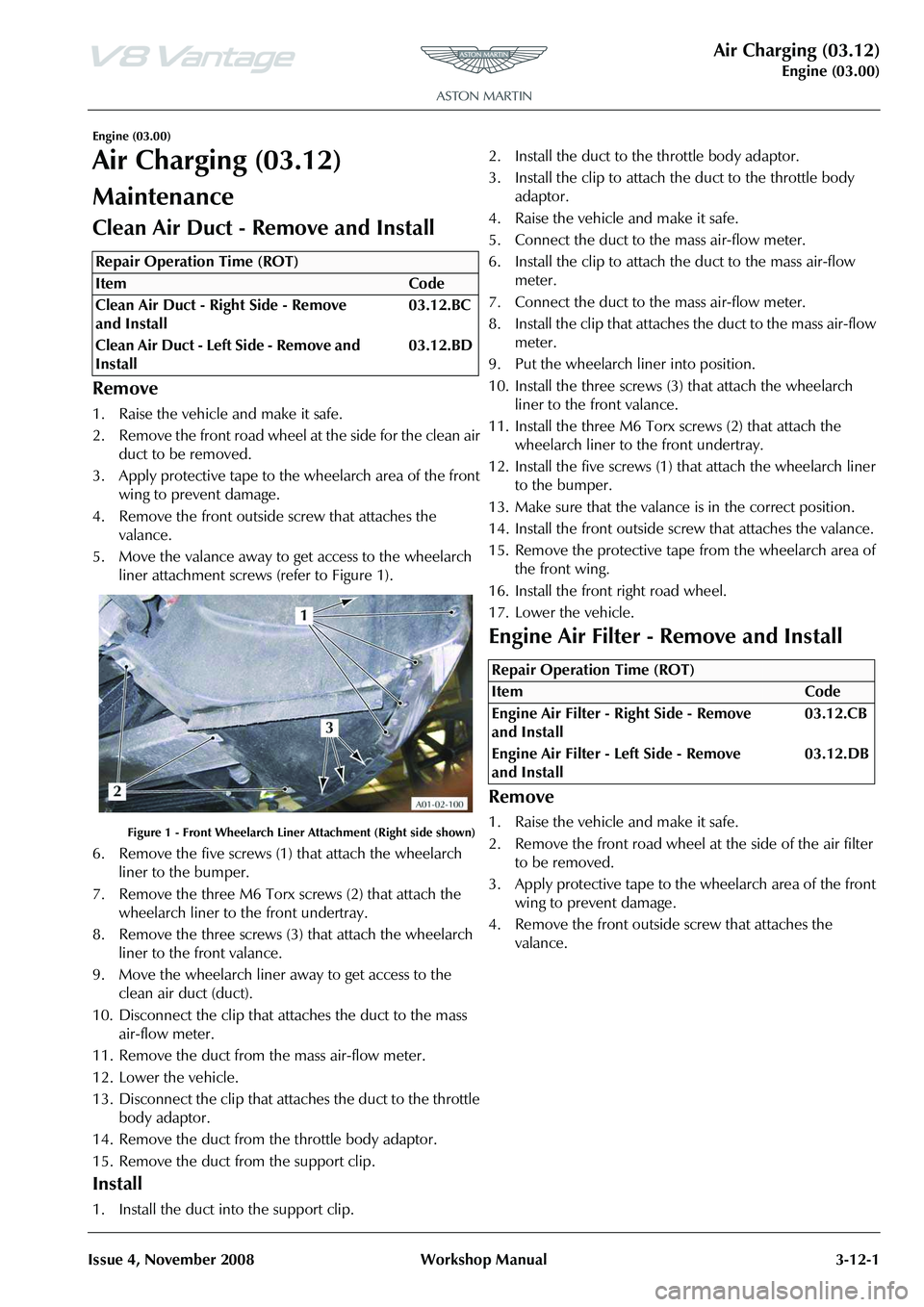
Air Charging (03.12)
Engine (03.00)
Issue 4, November 2008 Workshop Manual 3-12-1
Engine (03.00)
Air Charging (03.12)
Maintenance
Remove
1. Raise the vehicle and make it safe.
2. Remove the front road wheel at the side of the air filter
to be removed.
3. Apply protective tape to the wheelarch area of the front wing to prevent damage.
4. Remove the front outside screw that attaches the valance.
Repair Operation Time (ROT)
Repair Operation Time (ROT)
Page 417 of 947
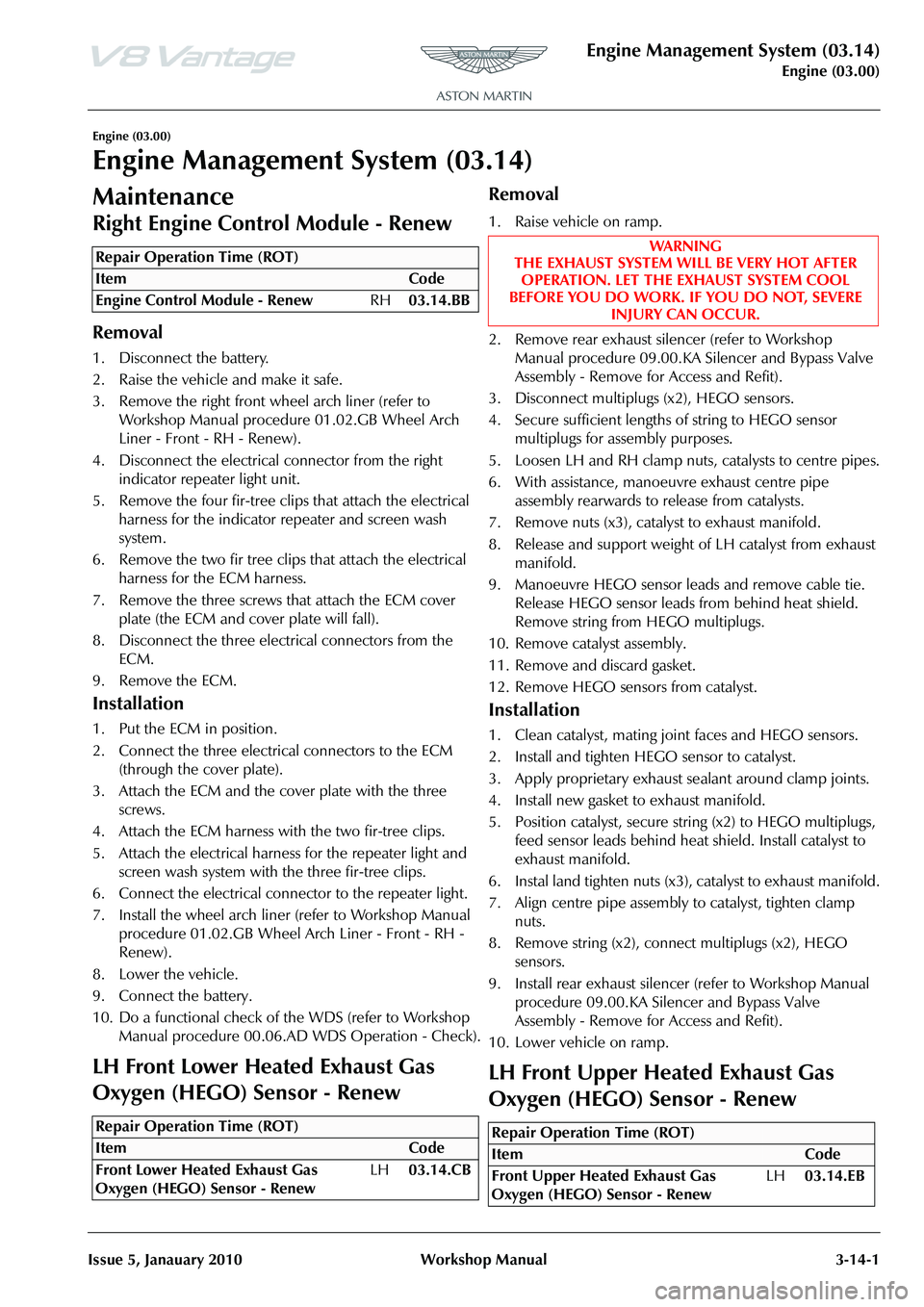
Engine Management System (03.14)
Engine (03.00)
Issue 5, Janauary 2010 Workshop Manual 3-14-1
Engine (03.00)
Engine Management System (03.14)
Maintenance
LH Front Lower Heated Exhaust Gas
Oxygen (HEGO) Sensor - Renew
Removal
1. Raise vehicle on ramp.
2. Remove rear exhaust silencer (refer to Workshop Manual procedure 09.00.KA Silencer and Bypass Valve
Assembly - Remo ve for Access and Refit).
3. Disconnect multiplugs (x2), HEGO sensors.
4. Secure sufficient lengths of string to HEGO sensor multiplugs for assembly purposes.
5. Loosen LH and RH clamp nuts, catalysts to centre pipes.
6. With assistance, manoeuvre exhaust centre pipe assembly rearwards to release from catalysts.
7. Remove nuts (x3), catalyst to exhaust manifold.
8. Release and support weight of LH catalyst from exhaust
manifold.
9. Manoeuvre HEGO sensor leads and remove cable tie. Release HEGO sensor leads from behind heat shield.
Remove string from HEGO multiplugs.
10. Remove catalyst assembly.
11. Remove and discard gasket.
12. Remove HEGO sens ors from catalyst.
Installation
1. Clean catalyst, mating joint faces and HEGO sensors.
2. Install and tighten HEGO sensor to catalyst.
3. Apply proprietary exhaust se alant around clamp joints.
4. Install new gasket to exhaust manifold.
5. Position catalyst, secure string (x2) to HEGO multiplugs, feed sensor leads behind heat shield. Install catalyst to
exhaust manifold.
6. Instal land tighten nuts (x3), catalyst to exhaust manifold.
7. Align centre pipe assembly to catalyst, tighten clamp
nuts.
8. Remove string (x2), conne ct multiplugs (x2), HEGO
sensors.
9. Install rear exhaust silencer (refer to Workshop Manual procedure 09.00.KA Silencer and Bypass Valve
Assembly - Remo ve for Access and Refit).
10. Lower vehicle on ramp.
LH Front Upper Heated Exhaust Gas
Oxygen (HEGO) Sensor - Renew
Repair Operation Time (ROT)
Repair Operation Time (ROT)
WA R N I N G
THE EXHAUST SYSTEM WILL BE VERY HOT AFTER OPERATION. LET THE EXHAUST SYSTEM COOL
BEFORE YOU DO WORK. IF YOU DO NOT, SEVERE
INJURY CAN OCCUR.
Repair Operation Time (ROT)
Page 423 of 947
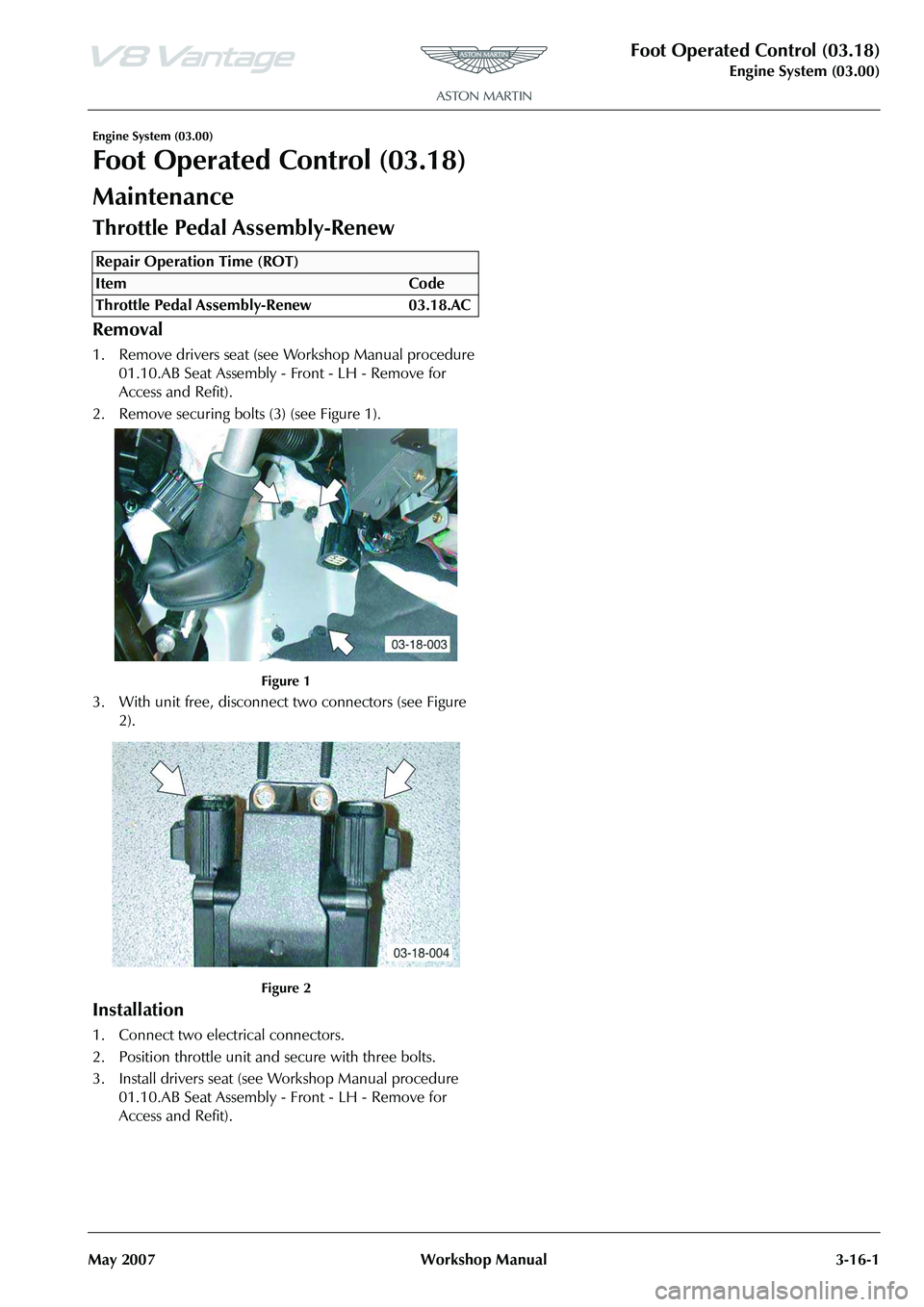
Foot Operated Control (03.18)
Engine System (03.00)
May 2007 Workshop Manual 3-16-1
Engine System (03.00)
Foot Operated Control (03.18)
Maintenance
Throttle Pedal Assembly-Renew
Removal
1. Remove drivers seat (see Workshop Manual procedure
01.10.AB Seat Assembly - Front - LH - Remove for
Access and Refit).
2. Remove securing bolts (3) (see Figure 1).
Figure 1
3. With unit free, disconnect two connectors (see Figure
2).
Figure 2
Installation
1. Connect two electrical connectors.
2. Position throttle unit and secure with three bolts.
3. Install drivers seat (see Workshop Manual procedure 01.10.AB Seat Assembly - Front - LH - Remove for
Access and Refit).
Repair Operation Time (ROT)
Page 425 of 947
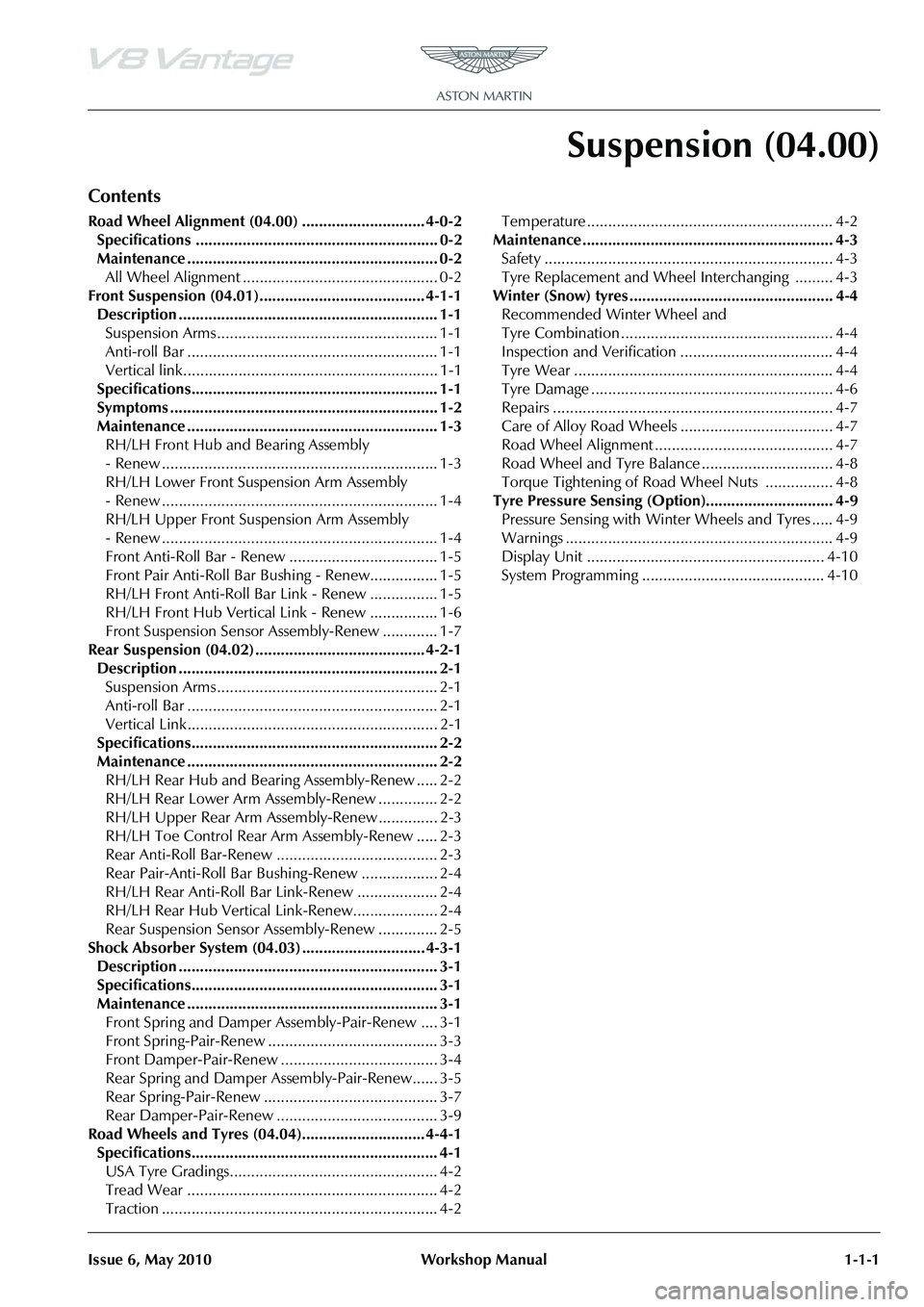
Issue 6, May 2010 Workshop Manual 1-1-1
Suspension (04.00)
Contents
Road Wheel Alignment (04.00) ............................. 4-0-2Specifications ......................................................... 0-2
Maintenance ........................................................... 0-2All Wheel Alignment .............................................. 0-2
Front Suspension (04.01)....................................... 4-1-1 Description ............................................................. 1-1Suspension Arms .................................................... 1-1
Anti-roll Bar ........................................................... 1-1
Vertical link............................................................ 1-1
Specifications.......................................................... 1-1
Symptoms ............................................................... 1-2
Maintenance ........................................................... 1-3 RH/LH Front Hub and Bearing Assembly
- Renew ................................................................. 1-3
RH/LH Lower Front Suspension Arm Assembly
- Renew ................................................................. 1-4
RH/LH Upper Front Suspension Arm Assembly
- Renew ................................................................. 1-4
Front Anti-Roll Bar - Renew ................................... 1-5
Front Pair Anti-Roll Bar Bushing - Renew................ 1-5
RH/LH Front Anti-Roll Bar Link - Renew ................ 1-5
RH/LH Front Hub Vertical Link - Renew ................ 1-6
Front Suspension Sensor Assembly-Renew ............. 1-7
Rear Suspension (04.02) ........................................ 4-2-1 Description ............................................................. 2-1Suspension Arms .................................................... 2-1
Anti-roll Bar ........................................................... 2-1
Vertical Link........................................................... 2-1
Specifications.......................................................... 2-2
Maintenance ........................................................... 2-2 RH/LH Rear Hub and Bearin g Assembly-Renew ..... 2-2
RH/LH Rear Lower Arm Assembly-Renew .............. 2-2
RH/LH Upper Rear Arm Assembly-Renew .............. 2-3
RH/LH Toe Control Rear Arm Assembly-Renew ..... 2-3
Rear Anti-Roll Bar-Renew ...................................... 2-3
Rear Pair-Anti-Roll Bar Bushing-Renew .................. 2-4
RH/LH Rear Anti-Roll Bar Link-Renew ................... 2-4
RH/LH Rear Hub Vertical Link-Renew.................... 2-4
Rear Suspension Sensor Assembly-Renew .............. 2-5
Shock Absorber System (04.03) ............................. 4-3-1 Description ............................................................. 3-1
Specifications.......................................................... 3-1
Maintenance ........................................................... 3-1Front Spring and Damper Assembly-Pair-Renew .... 3-1
Front Spring-Pair-Renew ........................................ 3-3
Front Damper-Pair-Renew ..................................... 3-4
Rear Spring and Damper Assembly-Pair-Renew...... 3-5
Rear Spring-Pair-Renew ......................................... 3-7
Rear Damper-Pair-Renew ...................................... 3-9
Road Wheels and Tyres (04.04)............................. 4-4-1 Specifications.......................................................... 4-1USA Tyre Gradings................................................. 4-2
Tread Wear ........................................................... 4-2
Traction ................................................................. 4-2 Temperature .......................................................... 4-2
Maintenance ........................................................... 4-3 Safety .................................................................... 4-3
Tyre Replacement and Wheel Interchanging ......... 4-3
Winter (Snow) tyres ................................................ 4-4 Recommended Winter Wheel and
Tyre Combination .................................................. 4-4
Inspection and Verification . ................................... 4-4
Tyre Wear ............................................................. 4-4
Tyre Damage ......................................................... 4-6
Repairs .................................................................. 4-7
Care of Alloy Road Wheels .................................... 4-7
Road Wheel Alignment .......................................... 4-7
Road Wheel and Tyre Balance ............................... 4-8
Torque Tightening of Road Wheel Nuts ................ 4-8
Tyre Pressure Sensing (Option).............................. 4-9 Pressure Sensing with Wint er Wheels and Tyres ..... 4-9
Warnings ............................................................... 4-9
Display Unit ........................................................ 4-10
System Programming ........................................... 4-10
Page 426 of 947
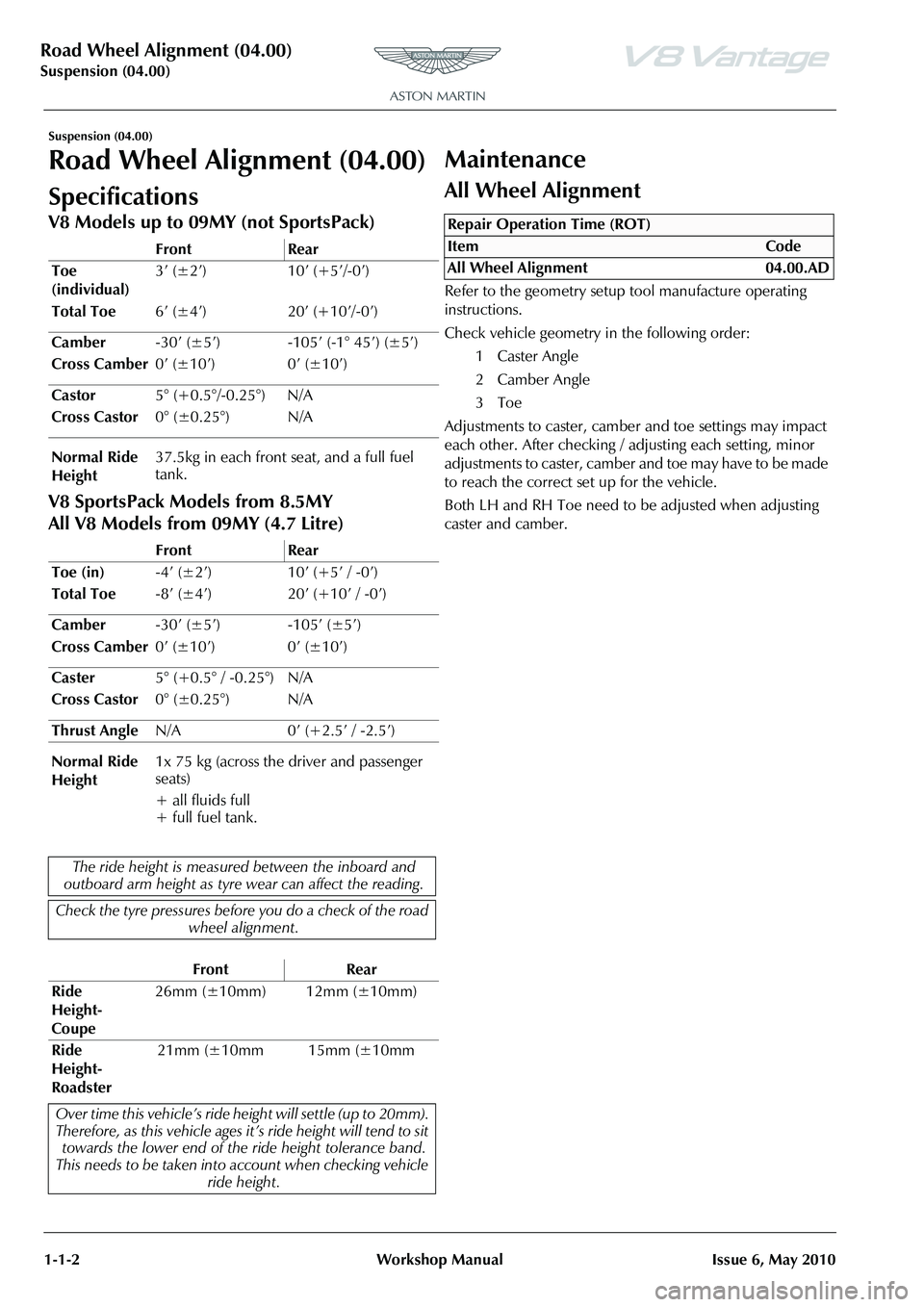
Road Wheel Alignment (04.00)
Suspension (04.00)1-1-2 Workshop Manual Issue 6, May 2010
Suspension (04.00)
Road Wheel Alignment (04.00)
Specifications
V8 Models up to 09MY (not SportsPack)
V8 SportsPack Models from 8.5MY
All V8 Models from 09MY (4.7 Litre)
Maintenance
All Wheel Alignment
Refer to the geometry setup tool manufacture operating
instructions.
Check vehicle geometry in the following order:
1 Caster Angle
2 Camber Angle
3Toe
Adjustments to caster, camber and toe settings may impact
each other. After checking / adjusting each setting, minor
adjustments to caster, camber and toe may have to be made
to reach the correct set up for the vehicle.
Both LH and RH Toe need to be adjusted when adjusting
caster and camber.
Front Rear
Toe
(individual) 3’ (±2’) 10’ (+5’/-0’)
Total Toe 6’ (±4’) 20’ (+10’/-0’)
Camber -30’ (±5’) -105’ (-1° 45’) (±5’)
Cross Camber 0’ (±10’) 0’ (±10’)
Castor 5° (+0.5°/-0.25°) N/A
Cross Castor 0° (±0.25°) N/A
Normal Ride
Height 37.5kg in each front seat, and a full fuel
tank.
Front Rear
Toe (in) -4