transmission ASTON MARTIN V8 VANTAGE 2010 Manual Online
[x] Cancel search | Manufacturer: ASTON MARTIN, Model Year: 2010, Model line: V8 VANTAGE, Model: ASTON MARTIN V8 VANTAGE 2010Pages: 947, PDF Size: 43.21 MB
Page 877 of 947
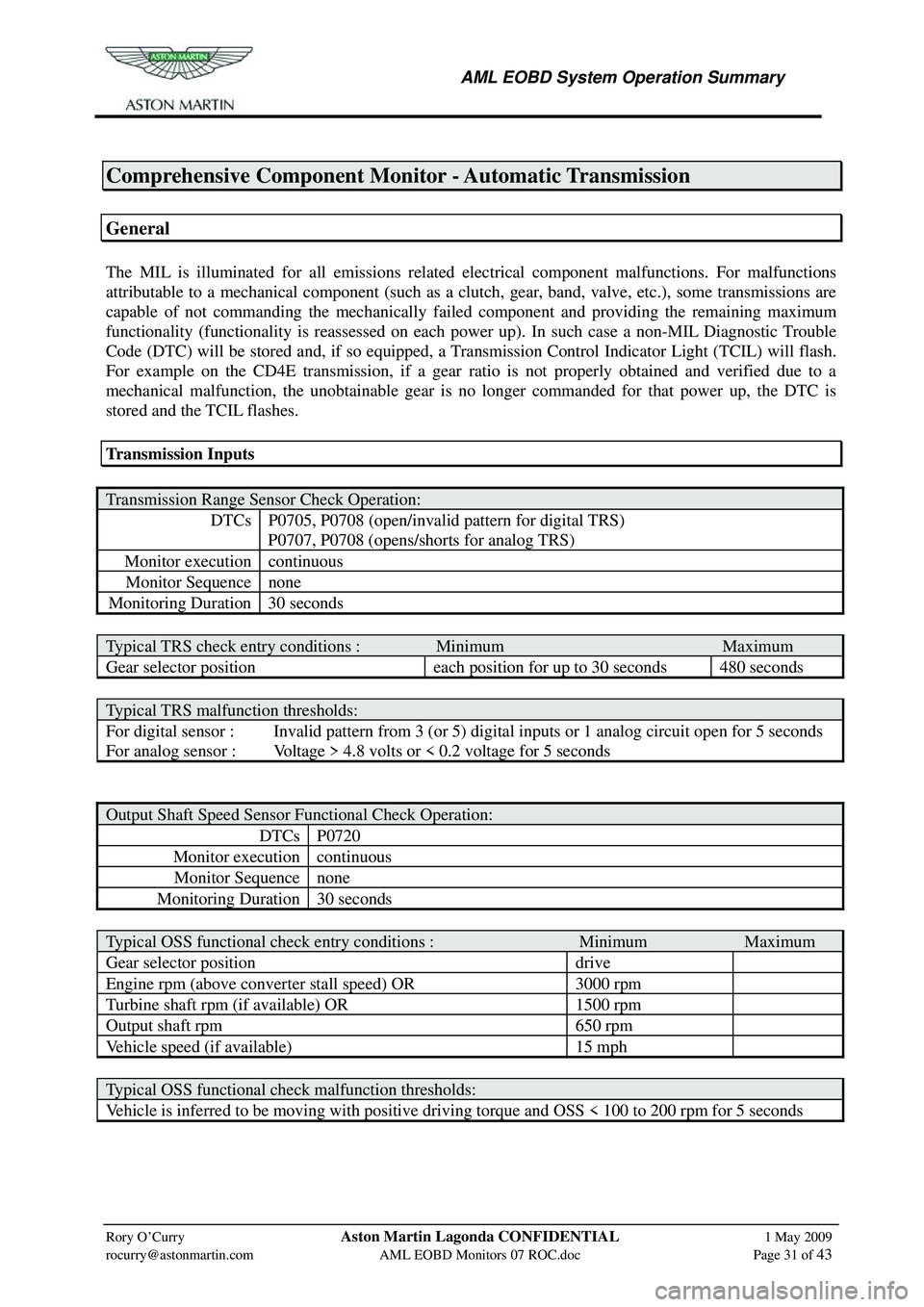
AML EOBD System Operation Summary
Rory O’Curry Aston Martin Lagonda CONFIDENTIAL 1 May 2009
[email protected] AML EOBD Monitors 07 ROC.doc Page 31 of 43
Comprehensive Component Monitor - Automatic Transmission
General
The MIL is illuminated for all emissions related electrical component malfunctions. For malfunctions
attributable to a mechanical component (such as a clutch, gear, band, valve, etc.), some transmissions are
capable of not commanding the mechanically faile d component and providing the remaining maximum
functionality (functionality is reassessed on each power up). In such case a non-MIL Diagnostic Trouble
Code (DTC) will be stored and, if so equipped, a Transmission Control Indicator Light (TCIL) will flash.
For example on the CD4E transmission, if a gear ratio is not properly obtained and verified due to a
mechanical malfunction, the unobtainable gear is no longer commanded for that power up, the DTC is
stored and the TCIL flashes.
Transmission Inputs
Transmission Range Sensor Check Operation:
DTCs P0705, P0708 (open/invalid pattern for digital TRS)
P0707, P0708 (opens/shorts for analog TRS)
Monitor execution continuous
Monitor Sequence none
Monitoring Duration 30 seconds
Typical TRS check entry conditions : Minimum Maximum
Gear selector position each position for up to 30 seconds 480 seconds
Typical TRS malfunction thresholds:
For digital sensor : Invalid pattern from 3 (or 5) digital inputs or 1 analog circuit open for 5 seconds
For analog sensor : Voltage > 4.8 volts or < 0.2 voltage for 5 seconds
Output Shaft Speed Sensor Functional Check Operation:
DTCs P0720
Monitor execution continuous
Monitor Sequence none
Monitoring Duration 30 seconds
Typical OSS functional check entry conditions : Minimum Maximum
Gear selector position drive
Engine rpm (above converter stall speed) OR 3000 rpm
Turbine shaft rpm (if available) OR 1500 rpm
Output shaft rpm 650 rpm
Vehicle speed (if available) 15 mph
Typical OSS functional check malfunction thresholds:
Vehicle is inferred to be moving with positive driving torque and OSS < 100 to 200 rpm for 5 seconds
Page 879 of 947

AML EOBD System Operation Summary
Rory O’Curry Aston Martin Lagonda CONFIDENTIAL 1 May 2009
[email protected] AML EOBD Monitors 07 ROC.doc Page 33 of 43
Transmission Outputs
Shift Solenoid Check Operation:
DTCs SS A - P0750 electrical, P1714 ISIG functional,
SS B - P0755 electrical, P1715 ISIG functional,
SS C - P0760 electrical, P1716 ISIG functional,
SS D - P0765 electrical, P1717 ISIG functional
SS E - P0770 electrical
Monitor execution electrical - continuous, functi onal - during off to on solenoid transitions
Monitor Sequence none
Typical SS malfunction thresholds:
Output driver feedback circuit does not match commanded driver state for 5 seconds.
ISIG functional check: ISIG chip hardware circu it does not detect characteristic current dip and rise
produced by solenoid movement for 10 solenoid events.
Torque Converter Clutch Check Operation:
DTCs P0743 electrical, P1740 ISIG functional
Monitor execution electrical – continuous, functi onal - during off to on solenoid transitions
Monitor Sequence none
Typical TCC malfunction thresholds:
Output driver feedback circuit does not match commanded driver state for 5 seconds
(> 1.0 volt if commanded on, < 2.0 volts if commanded off.)
ISIG functional check: ISIG chip hardware circu it does not detect characteristic current dip and rise
produced by solenoid movement.
Electronic Pressure Control Check Operation:
DTCs P1747 electrical, P1789, P0797 short to ground (low pressure)
P0745, P0775, P0795 mechanical functional
Monitor execution Continuous
Monitor Sequence None
Monitoring Duration Electrical: 5 seconds,
Mechanical functional: up to 30 seconds
Typical EPC malfunction thresholds:
Current feedback circuit is less than commanded current for 5 seconds
Transmission CCM temporary disablement conditions (other than entry requirements) :
None.
Page 880 of 947
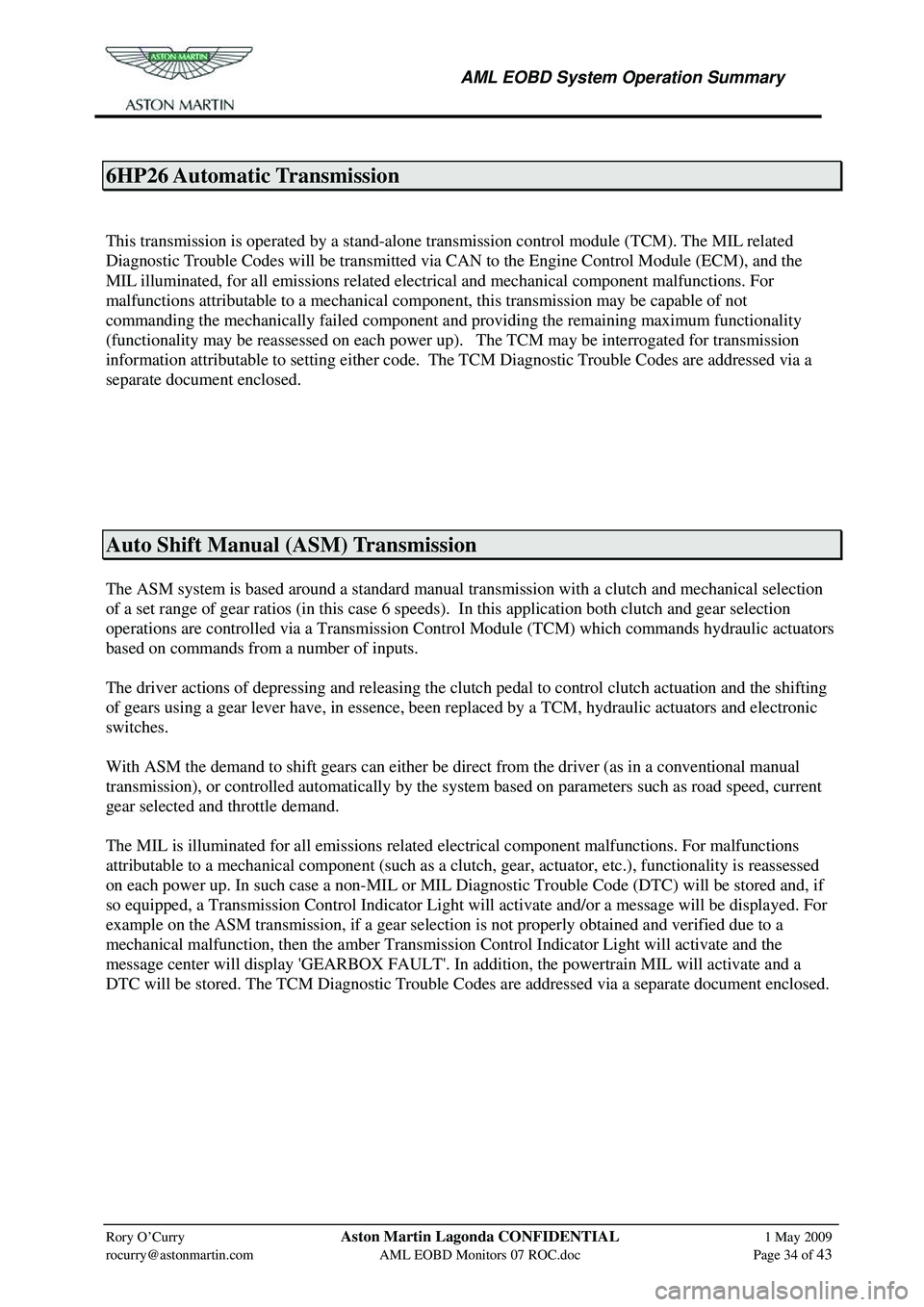
AML EOBD System Operation Summary
Rory O’Curry Aston Martin Lagonda CONFIDENTIAL 1 May 2009
[email protected] AML EOBD Monitors 07 ROC.doc Page 34 of 43
6HP26 Automatic Transmission
This transmission is operated by a stand-alone transmission control module (TCM). The MIL related
Diagnostic Trouble Codes will be transmitted via CAN to the Engine Control Module (ECM), and the
MIL illuminated, for all emissions related electrical and mechanical component malfunctions. For
malfunctions attributable to a mechanical component, this transmission may be capable of not
commanding the mechanically failed component a nd providing the remaining maximum functionality
(functionality may be reassessed on each power up). The TCM may be interrogated for transmission
information attributable to setting either code. The TCM Diagnostic Trouble Codes are addressed via a
separate document enclosed.
Auto Shift Manual (ASM) Transmission
The ASM system is based around a standard manual transmission with a clutch and mechanical selection
of a set range of gear ratios (in this case 6 speeds). In this application both clutch and gear selection
operations are controlled via a Transmission Contro l Module (TCM) which commands hydraulic actuators
based on commands from a number of inputs.
The driver actions of depressing and releasing the clutch pedal to control clutch actuation and the shifting
of gears using a gear lever have, in essence, been re placed by a TCM, hydraulic actuators and electronic
switches.
With ASM the demand to shift gears can either be direct from the driver (as in a conventional manual
transmission), or controlled automatically by the system based on parameters such as road speed, current
gear selected and throttle demand.
The MIL is illuminated for all emissions related electrical component malfunctions. For malfunctions
attributable to a mechanical component (such as a cl utch, gear, actuator, etc.), functionality is reassessed
on each power up. In such case a non-MIL or MIL Diagnos tic Trouble Code (DTC) will be stored and, if
so equipped, a Transmission Control Indicator Light will activate and/or a message will be displayed. For
example on the ASM transmission, if a gear selection is not properly obtained and verified due to a
mechanical malfunction, then the amber Transmission Control Indicator Light will activate and the
message center will display 'GEARBOX FAULT'. In addition, the powertrain MIL will activate and a
DTC will be stored. The TCM Diagnostic Trouble Cod es are addressed via a separate document enclosed.
Page 883 of 947

AML EOBD System Operation Summary
Rory O’Curry Aston Martin Lagonda CONFIDENTIAL 1 May 2009
[email protected] AML EOBD Monitors 07 ROC.doc Page 37 of 43
Glossary of Terms
A/D Analogue to Digital
ASM Auto Shift Manul
BTDC Before Top Dead Centre
CALID CALibration IDentification
CD4E Automatic Transmission for Intermediate size Family saloon.
CID Camshaft Identification.
CKP Crankshaft Position
CMP Camshaft Position
COP Coil on Plug
CPC Camshaft Position Control
CVN Calibration Verification Number
DPFE Delta Pressure Feedback
DTC Diagnostic Trouble Code
ECT Engine Coolant Temperature
EDIS Electronic Distributorless Ignition System
EGR Exhaust Gas Re-circulation.
EOBD European On Bard Diagnostics
EPC Electronic Pressure Control
ETC Electronic Throttle Control
ETM Electronic Throttle Monitor
EVR Electronic Vacuum Regulator
EWMA Exponentially Weighted Moving Average
FMEM Failure Mode and Effects Management
FN Automatic Transmission for Medium size Family Saloon
FWD Front Wheel Drive
HDR High Data Rate
HO2S Heated Oxygen Sensor.
IAC Idle Air Control
IDM Ignition Diagnostic Monitor
IMRC Inlet Manifold Runner Control
IPC Independent Plausibility Checker
KAM Keep Alive Memory
LDR Low Data Rate
LTFT Long Term Fuel Trim
MAF Mass Air Flow
MAP Manifold Absolute Pressure
MIL Malfunction Indicator Lamp
OSS Output Shaft Speed
PCM Powertrain Control Module
PIP Profile Ignition Pickup
RWD Rear Wheel Drive
SAE Society of Automotive Engineers
SAIR Secondary AIR
SCV Swirl Control Valve
STFT Short Term Fuel Trim
TCC Torque Converter Clutch
TCIL Transmission Control Indicator Lamp
TP Throttle Position
TPPC Throttle Plate Position Controller
TRS Transmission Range Sensor
TSS Turbine Shaft Speed
VID Vehicle IDentification
VIN Vehicle Identification No.
VQZ VQuizzer
VMV Vapour Management Valve
Page 890 of 947
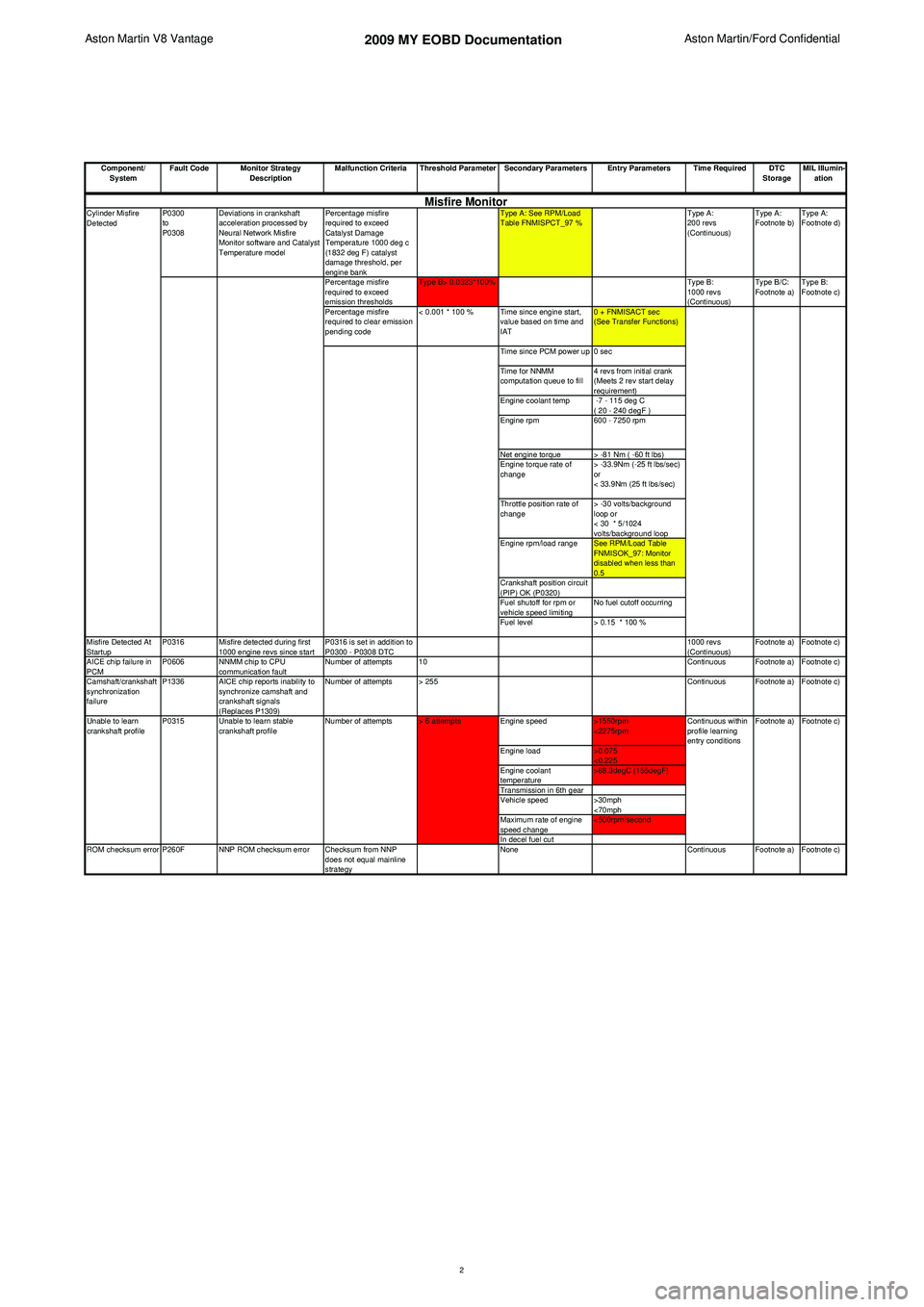
Aston Martin V8 Vantage 2009 MY EOBD DocumentationAston Martin/Ford Confidential
Component/ System Fault Code Monitor Strategy
Description Malfunction Criteria Threshold Parameter Secondary Parameters Entry Parameters Time Required DTC
StorageMIL Illumin-
ation
P0300
to
P0308 Deviations in crankshaft
acceleration processed by
Neural Network Misfire
Monitor software and Catalyst
Temperature model Percentage misfire
required to exceed
Catalyst Damage
Temperature 1000 deg c
(1832 deg F) catalyst
damage threshold, per
engine bank Type A: See RPM/Load
Table FNMISPCT_97 %
Type A:
200 revs
(Continuous)Type A:
Footnote b)
Type A:
Footnote d)
Percentage misfire
required to exceed
emission thresholds Type B> 0.0323*100% Type B:
1000 revs
(Continuous)Type B/C:
Footnote a)
Type B:
Footnote c)
Percentage misfire
required to clear emission
pending code < 0.001 * 100 % Time since engine start,
value based on time and
IAT 0 + FNMISACT sec
(See Transfer Functions)
Time since PCM power up 0 sec
Time for NNMM
computation queue to fill 4 revs from initial crank
(Meets 2 rev start delay
requirement)
Engine coolant temp -7 - 115 deg C ( 20 - 240 degF )
Engine rpm 600 - 7250 rpm
Net engine torque > -81 Nm ( -60 ft lbs)
Engine torque rate of
change > -33.9Nm (-25 ft lbs/sec)
or
< 33.9Nm (25 ft lbs/sec)
Throttle position rate of
change > -30 volts/background
loop or
< 30 * 5/1024
volts/background loop
Engine rpm/load range See RPM/Load Table FNMISOK_97: Monitor
disabled when less than
0.5
Crankshaft position circuit
(PIP) OK (P0320)
Fuel shutoff for rpm or
vehicle speed limiting No fuel cutoff occurring
Fuel level > 0.15 * 100 %
Misfire Detected At
Startup P0316 Misfire detected during first
1000 engine revs since start P0316 is set in addition to
P0300 - P0308 DTC 1000 revs
(Continuous)Footnote a) Footnote c)
AICE chip failure in
PCM P0606 NNMM chip to CPU
communication fault Number of attempts 10
Continuous Footnote a) Footnote c)
Camshaft/crankshaft
synchronization
failure P1336 AICE chip reports inability to
synchronize camshaft and
crankshaft signals
(Replaces P1309) Number of attempts > 255
Continuous Footnote a) Footnote c)
Engine speed >1550rpm
<2275rpm
Engine load >0.075
<0.225
Engine coolant
temperature >68.3degC (155degF)
Transmission in 6th gear
Vehicle speed >30mph
<70mph
Maximum rate of engine
speed change <500rpm/second
In decel fuel cut
ROM checksum error P260F NNP ROM checksum error Checksum from NNP does not equal mainline
strategyNone
Continuous Footnote a) Footnote c)
Cylinder Misfire
DetectedMisfire Monitor
Footnote c)
Unable to learn
crankshaft profile P0315 Unable to learn stable
crankshaft profile Number of attempts > 6 attempts Continuous within
profile learning
entry conditionsFootnote a)
2
Page 903 of 947
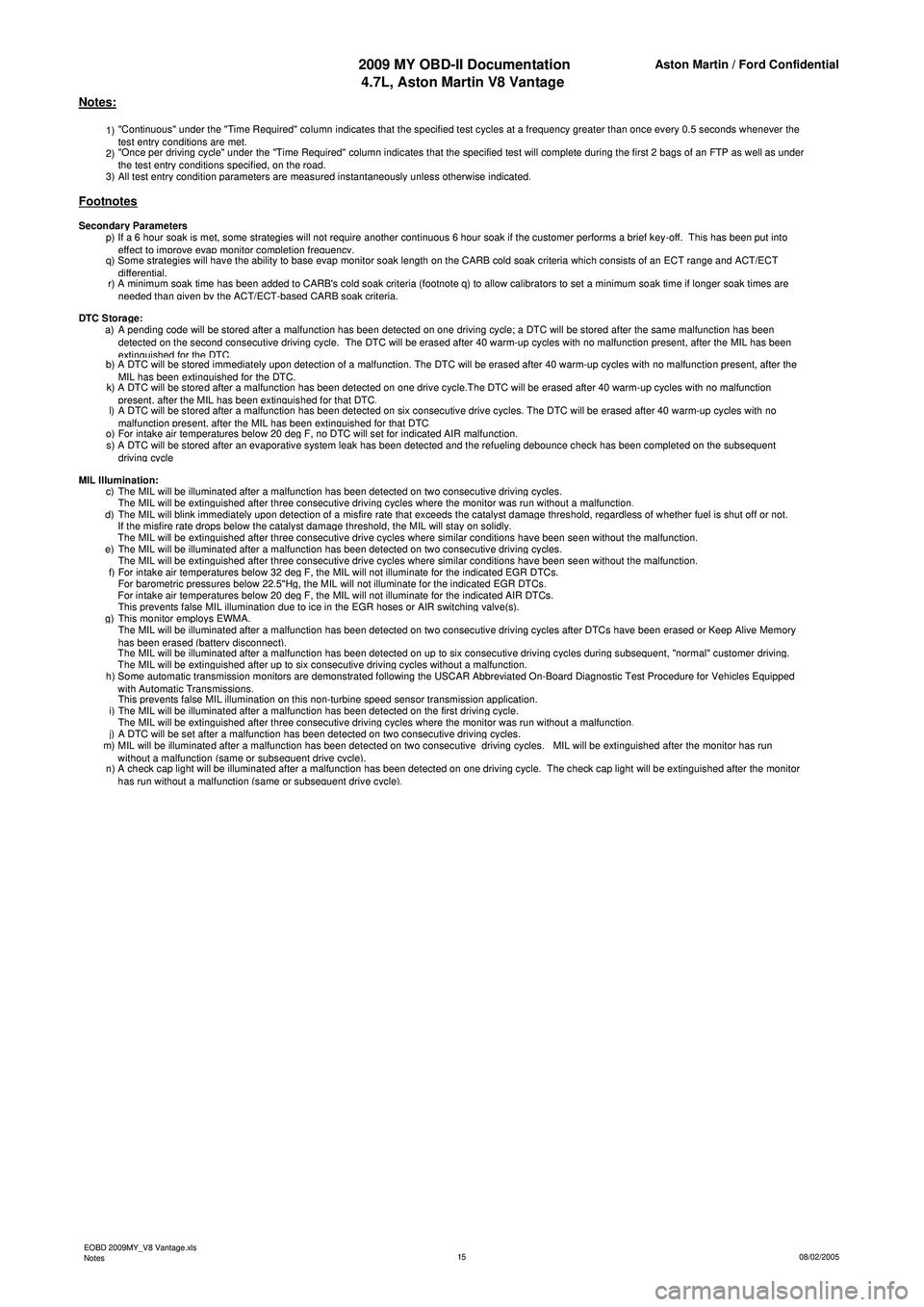
2009 MY OBD-II Documentation4.7L, Aston Martin V8 VantageAston Martin / Ford Confidential
1) "Continuous" under the "Time Required" column indicates that the specified test cycles at a frequency greater than once every 0.5 seconds whenever the
test entry conditions are met.
2) "Once per driving cycle" under the "Time Required" column indicates that the specified test will complete during the first 2 bags of an FTP as well as under
the test entr
y conditions specified, on the road.
3)All test entry condition parameters are measured instantaneously unless otherwise indicated.
p) If a 6 hour soak is met, some strategies will not require another continuous 6 hour soak if the customer performs a brief key-off. This has been put into
effect to improve evap monitor completion frequency.
q) Some strategies will have the ability to base evap monitor soak length on the CARB cold soak criteria which consists of an ECT range and ACT/ECT
differential.
r) A minimum soak time has been added to CARB's cold soak criteria (footnote q) to allow calibrators to set a minimum soak time if longer soak times are
n
eeded than given by the ACT/ECT-based CARB soak criteria.
a) A pending code will be stored after a malfunction has been detected on one driving cycle; a DTC will be stored after the same malfunction has been detected on the second consecutive driving cycle. The DTC will be erased after 40 warm-up cycles with no malfunction present, after the MIL has been
extinguished for the DTC.b) A DTC will be stored immediately upon detection of a malfunction. The DTC will be erased after 40 warm-up cycles with no malfunction present, after the MIL has been extinguished for the DTC.k) A DTC will be stored after a malfunction has been detected on one drive cycle.The DTC will be erased after 40 warm-up cycles with no malfunction present, after the MIL has been extinguished for that DTC.l) A DTC will be stored after a malfunction has been detected on six consecutive drive cycles. The DTC will be erased after 40 warm-up cycles with no malfunction present, after the MIL has been extinguished for that DTC.o)For intake air temperatures below 20 deg F, no DTC will set for indicated AIR malfunction.
s) A DTC will be stored after an evaporative system leak has been detected and the refueling debounce check has been completed on the subsequent
driving cycle
c)The MIL will be illuminated after a malfunction has been detected on two consecutive driving cycles.
The MIL will be extinguished after three consecutive driving cycles where the monitor was run without a malfunction.d)The MIL will blink immediately upon detection of a misfire rate that exceeds the catalyst damage threshold, regardless of whether fuel is shut off or not.
If the misfire rate drops below the catalyst damage threshold, the MIL will stay on solidly.
The MIL will be extinguished after three consecutive drive cycles where similar conditions have been seen without the malfunction.e)The MIL will be illuminated after a malfunction has been detected on two consecutive driving cycles.
The MIL will be extinguished after three consecutive drive cycles where similar conditions have been seen without the malfunction.f)For intake air temperatures below 32 deg F, the MIL will not illuminate for the indicated EGR DTCs.
For barometric pressures below 22.5"Hg, the MIL will not illuminate for the indicated EGR DTCs.
For intake air temperatures below 20 deg F, the MIL will not illuminate for the indicated AIR DTCs.
This prevents false MIL illumination due to ice in the EGR hoses or AIR switching valve(s).g)This monitor employs EWMA.
The MIL will be illuminated after a malfunction has been detected on two consecutive driving cycles after DTCs have been erased or Keep Alive Memory
h
as been erased (battery disconnect).
The MIL will be illuminated after a malfunction has been detected on up to six consecutive driving cycles during subsequent, "normal" customer driving.
The MIL will be extinguished after up to six consecutive driving cycles without a malfunction.
h) Some automatic transmission monitors are demonstrated following the USCAR Abbreviated On-Board Diagnostic Test Procedure for Vehicles Equipped
wi
th Automatic Transmissions.
This prevents false MIL illumination on this non-turbine speed sensor transmission application.
i)The MIL will be illuminated after a malfunction has been detected on the first driving cycle.
The MIL will be extinguished after three consecutive driving cycles where the monitor was run without a malfunction.j)A DTC will be set after a malfunction has been detected on two consecutive driving cycles.
m) MIL will be illuminated after a malfunction has been detected on two consecutive driving cycles. MIL will be extinguished after the monitor has run
wi
thout a malfunction (same or subsequent drive cycle).
n) A check cap light will be illuminated after a malfunction has been detected on one driving cycle. The check cap light will be extinguished after the monitor
h
as run without a malfunction (same or subsequent drive cycle).
MIL Illumination:
Notes:
Footnotes
Secondary Parameters
DTC Stora
ge:
EOBD 2009MY_V8 Vantage.xls
Notes 08/02/2005
15
Page 931 of 947
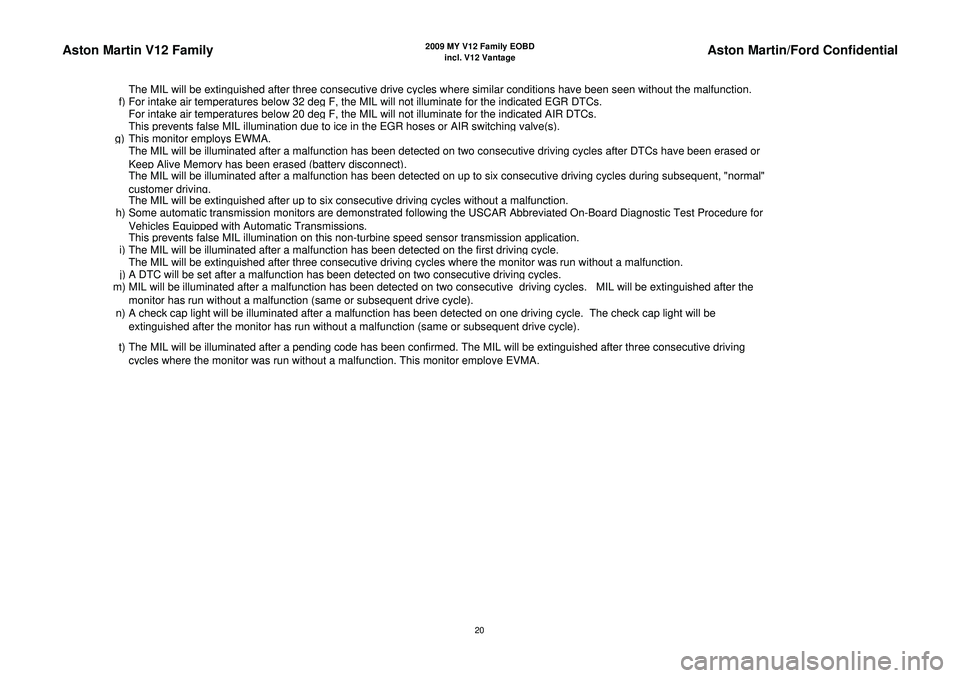
Aston Martin V12 Family
2009 MY V12 Family EOBDincl. V12 Vantage
Aston Martin/Ford Confidential
The MIL will be extin
guished after three consecutive drive c
ycles where similar conditions have been seen without the malfunction.
f
)For intake air tem
peratures below 32 de
g F, the MIL will not illuminate for the indicated EGR DTCs.
For intake air tem
peratures below 20 de
g F, the MIL will not illuminate for the indicated AIR DTCs.
This
prevents false MIL illumination due to ice in the EGR hoses or AIR switchin
g valve
(s).
g)
This monitor em
ploys EWMA.
The MIL will be illuminated after a malfunction has been detected on two consecutive driving cycles after DTCs have been erased or
Kee
p Alive Memor
y has been erased
(batter
y disconnect
).
The MIL will be illuminated after a malfunction has been detected on up to six consecutive driving cycles during subsequent, "normal"
customer drivin
g.
The MIL will be extin
guished after u
p to six consecutive drivin
g cycles without a malfunction.
h) Some automatic transmission monitors are demonstrated following the USCAR Abbreviated On-Board Diagnostic Test Procedure for
Vehicles E
quipp
ed with Automatic Transmissions.
This
prevents false MIL illumination on this non-turbine s
peed sensor transmission a
pp
lication.
i
)The MIL will be illuminated after a malfunction has been detected on the first drivin
g cycle.
The MIL will be extin
guished after three consecutive drivin
g cycles where the monitor was run without a malfunction.
j)A DTC will be set after a malfunction has been detected on two consecutive drivin
g cycles.
m) MIL will be illuminated after a malfunction has been detected on two consecutive driving cycles. MIL will be extinguished after the
monitor has run without a malfunction
(same or subse
quent drive c
ycle
).
n) A check cap light will be illuminated after a malfunction has been detected on one driving cycle. The check cap light will be
extinguished after the monitor has run without a malfunction (same or subsequent drive cycle).
t) The MIL will be illuminated after a pending code has been confirmed. The MIL will be extinguished after three consecutive driving c
ycles where the monitor was run without a malfunction. This monitor em
ploye EVMA.
20
Page 933 of 947
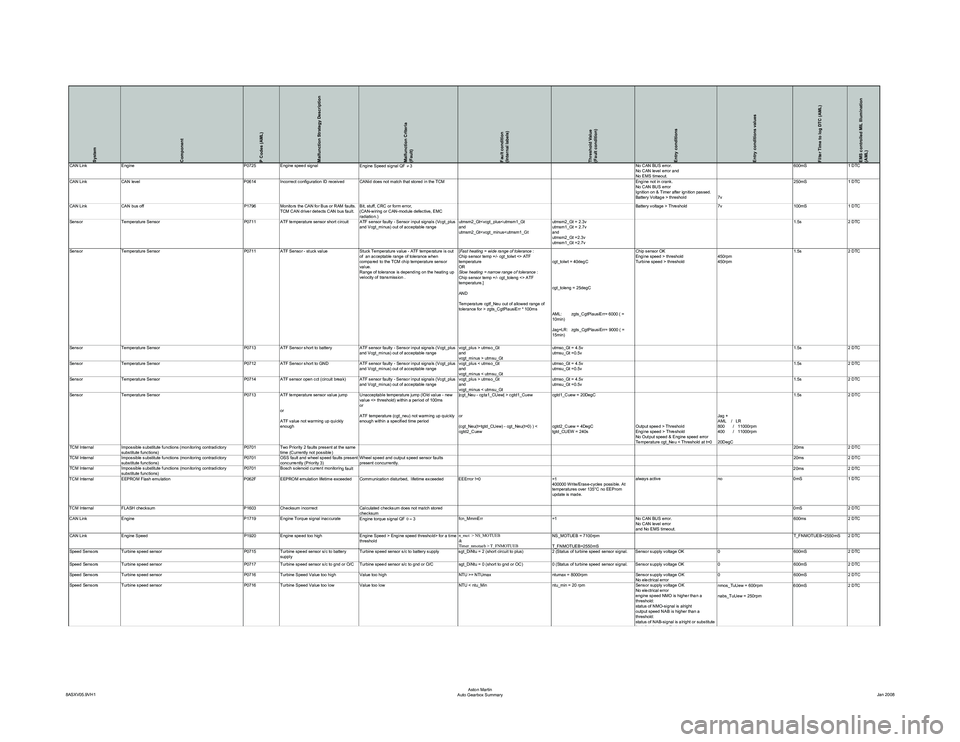
System
Component
P Codes (AML)
Malfunction Strategy Description
Malfunction Criteria
(Fault)
Fault condition
(Internal labels)
Threshold Value
(Fault condition)
Entry conditions
Entry conditions values
Filter Time to log DTC (AML)
EMS controlled MIL Illumination
(AML)
CAN LinkEngine P0725Engine speed signal
Engine Speed signal QF ≠ 3 No CAN BUS error.
No CAN level error and
No EMS timeout.600mS
1 DTC
CAN Link CAN level P0614Incorrect configuration ID received CANid does not match that stored in the TCM Engine not in crank.
No CAN BUS error
Ignition on & Timer after ignition passed.
Battery Voltage > threshold7v250mS
1 DTC
CAN Link CAN bus off P1796Monitors the CAN for Bus or RAM faults.
TCM CAN driver detects CAN bus fault. Bit, stuff, CRC or form error,
(CAN-wiring or CAN-module defective, EMC
radiation.) Battery voltage > Threshold
7v100mS1 DTC
Sensor Temperature Sensor P0711 ATF temperature sensor short circuit ATF sensor faulty - Sensor input signals (Vcgt_plus
and Vcgt_minus) out of acceptable range utmsm2_Gt
utmsm2_Gt
and
utmsm2_Gt =2.3v
utmsm1_Gt =2.7v 1.5s
2 DTC
Sensor Temperature Sensor P0711ATF Sensor - stuck value Stuck Temperature value - ATF temperature is out
of an acceptable range of tolerance when
compared to the TCM chip temperature sensor
value.
Range of tolerance is depending on the heating up
velocity of transmission . [
Fast heating = wide range of tolerance :
Chip sensor temp +/- cgt_tolwt <> ATF
temperature
OR
Slow heating = narrow range of tolerance :
Chip sensor temp +/- cgt_toleng <> ATF
temperature.]
AND
Temperature cgtf_Neu out of allowed range of
tolerance for > zgts_CgtPlausiErr * 100ms cgt_tolwt = 40degC
cgt_toleng = 25degC
AML: zgts_CgtPlausiErr= 6000 ( =
10min)
Jag+LR: zgts_CgtPlausiErr= 9000 ( =
15min)Chip sensor OK
Engine speed > threshold
Turbine speed > threshold
450rpm
450rpm1.5s
2 DTC
Sensor Temperature Sensor P0713ATF Sensor short to battery ATF sensor faulty - Sensor input signals (Vcgt_plus
and Vcgt_minus) out of acceptable range vcgt_plus > utmso_Gt
and
vcgt_minus > utmsu_Gtutmso_Gt = 4.5v
utmsu_Gt =0.5v
1.5s
2 DTC
Sensor Temperature Sensor P0712ATF Sensor short to GND ATF sensor faulty - Sensor input signals (Vcgt_plus
and Vcgt_minus) out of acceptable range vcgt_plus < utmso_Gt
and
vcgt_minus < utmsu_Gtutmso_Gt = 4.5v
utmsu_Gt =0.5v
1.5s
2 DTC
Sensor Temperature Sensor P0714ATF sensor open cct (circuit break) ATF sensor faulty - Sensor input signals (Vcgt_plus
and Vcgt_minus) out of acceptable range vcgt_plus > utmso_Gt
and
vcgt_minus < utmsu_Gtutmso_Gt = 4.5v
utmsu_Gt =0.5v
1.5s
2 DTC
Sensor Temperature Sensor P0713 ATF temperature sensor value jump
or
ATF value not warming up quickly
enough Unacceptable temperature jump (lOld value - new
value <> threshold) within a period of 100ms
or
ATF temperature (cgt_neu) not warming up quickly
enough within a specified time period
|cgt_Neu - cgta1_CUew| > cgtd1_Cuew
or
(cgt_Neu(t=tgtd_CUew) - cgt_Neu(t=0) ) <
cgtd2_Cuewcgtd1_Cuew = 20DegC
cgtd2_Cuew = 4DegC
tgtd_CUEW = 240s
Output speed > Threshold
Engine speed > Threshold
No Output speed & Engine speed error
Temperature cgt_Neu < Threshold at t=0Jag +
AML / LR
800 / 11000rpm
400 / 11000rpm
20DegC1.5s
2 DTC
TCM Internal Impossible substitute functions (monitoring contradictory
substitute functions) P0701
Two Priority 2 faults present at the same
time (Currently not possible) 20ms
2 DTC
TCM Internal Impossible substitute functions (monitoring contradictory
substitute functions) P0701
OSS fault and wheel speed faults present
concurrently (Priority 3) Wheel speed and output speed sensor faults
present concurrently. 20ms
2 DTC
TCM Internal Impossible substitute functions (monitoring contradictory
substitute functions) P0701
Bosch solenoid current monitorin
g fault 20ms 2 DTC
TCM Internal EEPROM Flash emulation P062FEEPROM emulation lifetime exceeded Communication disturbed, lifetime exceeded EEError !=0 =1
400000 Write/Erase-cycles possible. At
temperatures over 135°C no EEProm
update is made.always active
no0mS1 DTC
TCM Internal FLASH checksum P1603Checksum incorrect Calculated checksum does not match stored
checksum 0mS
2 DTC
CAN Link Engine P1719Engine Torque signal inaccurate
Engine torque signal QF 0 = 3 fcn_MmmErr
=1No CAN BUS error.
No CAN level error
and No EMS timeout. 600ms
2 DTC
CAN Link Engine Speed P1920Engine speed too high Engine Speed > Engine speed threshold> for a time
threshold n_mot > NS_MOTUEB
&
Timer_nmotueb > T_FNMOTUEBNS_MOTUEB = 7100rpm
T_FNMOTUEB=2550mS T_FNMOTUEB=2550mS 2 DTC
Speed Sensors Turbine speed sensor P0715Turbine speed sensor s/c to battery
supply Turbine speed sensor s/c to battery supply sgt_DiNtu = 2 (short circuit to plus)
2 (Status of turbine speed sensor signal. Sensor supply voltage OK0600mS2 DTC
Speed Sensors Turbine speed sensor P0717Turbine speed sensor s/c to gnd or O/C Turbine speed sensor s/c to gnd or O/C sgt_DiNtu = 0 (short to gnd or OC)0 (Status of turbine speed sensor signal. Sensor supply voltage OK 0600mS2 DTC
Speed Sensors Turbine speed sensor P0716Turbine Speed Value too high Value too high NTU >= NTUmaxntumax = 8000rpmSensor supply voltage OK
No electrical error 0
600mS2 DTC
Speed Sensors Turbine speed sensor P0716Turbine Speed Value too low Value too low NTU < ntu_Minntu_min = 20 rpmSensor supply voltage OK
No electrical error
engine speed NMO is higher than a
threshold:
status of NMO-signal is alright
output speed NAB is higher than a
threshold:
status of NAB-signal is alright or substitute
fltfl fb Ei t t
nmos_TuUew = 600rpm
nabs_TuUew = 250rpm 600mS
2 DTC
8ASXV05.9VH1 Aston Martin
Auto Gearbox Summary Jan 2008
Page 934 of 947
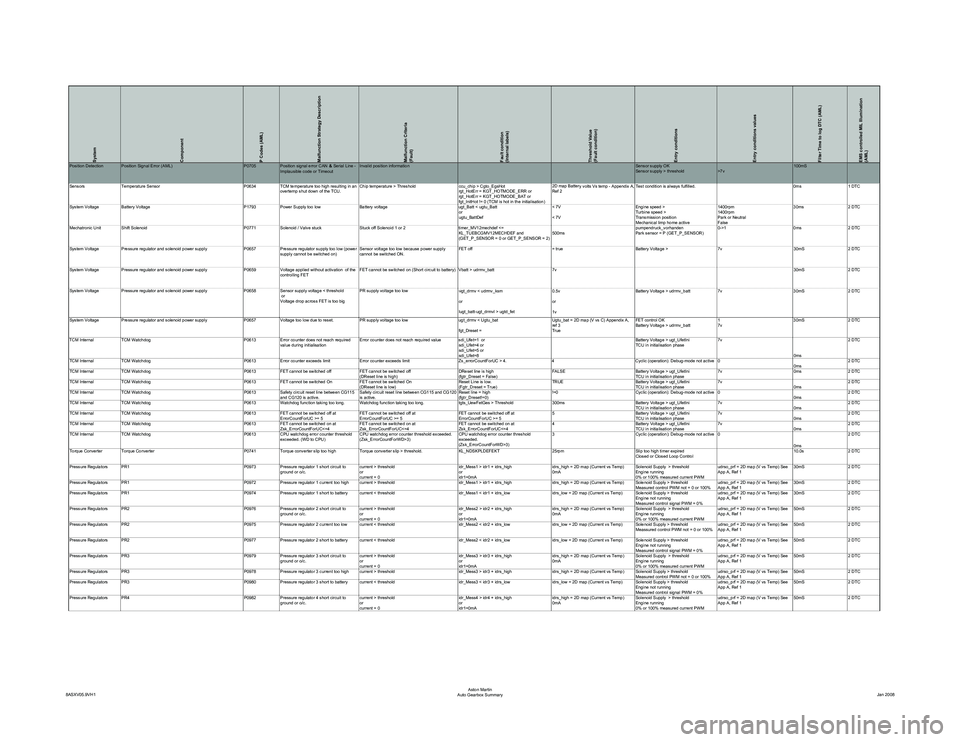
System
Component
P Codes (AML)
Malfunction Strategy Description
Malfunction Criteria
(Fault)
Fault condition
(Internal labels)
Threshold Value
(Fault condition)
Entry conditions
Entry conditions values
Filter Time to log DTC (AML)
EMS controlled MIL Illumination
(AML)
y volts Vs temp - Appendix A,
Ref 2 Test condition is always fulfilled. 0ms 1 DTC
System Voltage Battery Voltage P1793 Power Supply too low Battery voltage ugt_Batt < ugtu_Batt or
ugtu_BattDef< 7V
< 7VEngine speed >
Turbine speed >
Transmission position
Mechanical limp home active1400rpm
1400rpm
Park or Neutral
False30ms
2 DTC
Mechatronic Unit Shift Solenoid P0771Solenoid / Valve stuck Stuck off Solenoid 1 or 2 timer_MV12mechdef <=
KL_TUEBCGMV12MECHDEF and
(GET_P_SENSOR = 0 or GET_P_SENSOR = 2) 500mspumpendruck_vorhanden
Park sensor = P (GET_P_SENSOR)0->1
0ms2 DTC
System Voltage Pressure regulator and solenoid power supply P0657Pressure regulator supply too low (power
supply cannot be switched on) Sensor voltage too low because power supply
cannot be switched ON. FET off
= trueBattery Voltage > 7v30mS2 DTC
System Voltage Pressure regulator and solenoid power supply P0659Voltage applied without activation of the
controlling FET FET cannot be switched on (Short circuit to battery) Vbatt > udrmv_batt
7v 30mS2 DTC
System Voltage Pressure regulator and solenoid power supply P0658Sensor supply voltage < threshold
or
Voltage drop across FET is too big PR supply voltage too low
u
gt_drmv < udrmv_ksm
or
lugt_batt-ugt_drmvl > ugtd_fet 0.5v
or
1vBattery Voltage > udrmv_batt
7v30mS2 DTC
System Voltage Pressure regulator and solenoid power supply P0657Voltage too low due to reset. PR supply voltage too low ugt_drmv < Ugtu_bat
fgt_Dreset = Ugtu_bat = 2D map (V vs C) Appendix A,
ref 3
TrueFET control OK
Battery Voltage > udrmv_batt
1
7v30mS
2 DTC
TCM Internal TCM Watchdog P0613Error counter does not reach required
value during initialisation Error counter does not reach required value sdi_Ufet=1 or
sdi_Ufet=4 or
sdi_Ufet=5 or
sdi_Ufet=8 Battery Voltage > ugt_UfetIni
TCU in initialisation phase
7v
0ms2 DTC
TCM Internal TCM Watchdog P0613Error counter exceeds limit Error counter exceeds limit Zs_errorCountForUC > 4.4Cyclic (operation): Debug-mode not active 0
0ms2 DTC
TCM Internal TCM Watchdog P0613FET cannot be switched off FET cannot be switched off
(DReset line is high) DReset line is high
(fgtr_Dreset = False)FALSE
Battery Voltage > ugt_UfetIni
TCU in initialisation phase7v
0ms2 DTC
TCM Internal TCM Watchdog P0613FET cannot be switched On FET cannot be switched On
(DReset line is low) Reset Line is low.
(Fgtr_Dreset = True)TRUE
Battery Voltage > ugt_UfetIni
TCU in initialisation phase7v
0ms2 DTC
TCM Internal TCM Watchdog P0613Safety circuit reset line between CG115
and CG120 is active. Safety circuit reset line between CG115 and CG120
is active. Reset line = high
(fgtr_Dreset!=0)!=0
Cyclic (operation): Debug-mode not active 0
0ms2 DTC
TCM Internal TCM Watchdog P0613Watchdog function taking too long. Watchdog function taking too long. tgts_UewFetGes > Threshold300msBattery Voltage > ugt_UfetIni
TCU in initialisation phase7v
0ms2 DTC
TCM Internal TCM Watchdog P0613FET cannot be switched off at
ErrorCountForUC >= 5 FET cannot be switched off at
ErrorCountForUC >= 5 FET cannot be switched off at
ErrorCountForUC >= 55
Battery Voltage > ugt_UfetIni
TCU in initialisation phase7v
0ms2 DTC
TCM Internal TCM Watchdog P0613FET cannot be switched on at
Zsk_ErrorCountForUC<=4 FET cannot be switched on at
Zsk_ErrorCountForUC<=4 FET cannot be switched on at
Zsk_ErrorCountForUC<=44
Battery Voltage > ugt_UfetIni
TCU in initialisation phase7v
0ms2 DTC
TCM Internal TCM Watchdog P0613CPU watchdog error counter threshold
exceeded. (WD to CPU) CPU watchdog error counter threshold exceeded.
(Zsk_ErrorCountForWD>3) CPU watchdog error counter threshold
exceeded.
(Zsk_ErrorCountForWD>3)3
Cyclic (operation): Debug-mode not active 0
0ms2 DTC
Torque Converter Torque Converter P0741Torque converter slip too high Torque converter slip > threshold. KL_NDSKPLDEFEKT25rpmSlip too high timer expired
Closed or Closed Loop Control 10.0s
2 DTC
Pressure Regulators PR1 P0973Pressure regulator 1 short circuit to
ground or o/c. current > threshold
or
current = 0 idr_Mess1 > idr1 + idrs_high
or
idr1=0mAidrs_high = 2D map (Current vs Temp)
0mA
Solenoid Supply > threshold
Engine running
0% or 100% measured current PWMudrso_prf = 2D map (V vs Temp) See
App A, Ref 1
30mS
2 DTC
Pressure Regulators PR1 P0972Pressure regulator 1 current too high current > threshold idr_Mess1 > idr1 + idrs_highidrs_high = 2D map (Current vs Temp) Solenoid Supply > threshold
Measured control PWM not = 0 or 100%udrso_prf = 2D map (V vs Temp) See
App A, Ref 130mS
2 DTC
Pressure Regulators PR1 P0974Pressure regulator 1 short to battery current < threshold idr_Mess1 < idr1 + idrs_lowidrs_low = 2D map (Current vs Temp) Solenoid Supply > threshold
Engine not running
Measured control signal PWM = 0%udrso_prf = 2D map (V vs Temp) See
App A, Ref 1
30mS
2 DTC
Pressure Regulators PR2 P0976Pressure regulator 2 short circuit to
ground or o/c. current > threshold
or
current = 0 idr_Mess2 > idr2 + idrs_high
or
idr1=0mAidrs_high = 2D map (Current vs Temp)
0mA
Solenoid Supply > threshold
Engine running
0% or 100% measured current PWMudrso_prf = 2D map (V vs Temp) See
App A, Ref 1
50mS
2 DTC
Pressure Regulators PR2 P0975Pressure regulator 2 current too low current < threshold idr_Mess2 < idr2 + idrs_lowidrs_low = 2D map (Current vs Temp) Solenoid Supply > threshold
Meassured control PWM not = 0 or 100%udrso_prf = 2D map (V vs Temp) See
App A, Ref 150mS
2 DTC
Pressure Regulators PR2 P0977Pressure regulator 2 short to battery current < threshold idr_Mess2 < idr2 + idrs_lowidrs_low = 2D map (Current vs Temp) Solenoid Supply > threshold
Engine not running
Measured control signal PWM = 0%udrso_prf = 2D map (V vs Temp) See
App A, Ref 1
50mS
2 DTC
Pressure Regulators PR3 P0979Pressure regulator 3 short circuit to
ground or o/c. current > threshold
or
current = 0 idr_Mess3 > idr3 + idrs_high
or
idr1=0mAidrs_high = 2D map (Current vs Temp)
0mA
Solenoid Supply > threshold
Engine running
0% or 100% measured current PWMudrso_prf = 2D map (V vs Temp) See
App A, Ref 1
50mS
2 DTC
Pressure Regulators PR3 P0978Pressure regulator 3 current too high current > threshold idr_Mess3 > idr3 + idrs_highidrs_high = 2D map (Current vs Temp) Solenoid Supply > threshold
Measured control PWM not = 0 or 100%udrso_prf = 2D map (V vs Temp) See
App A, Ref 150mS
2 DTC
Pressure Regulators PR3 P0980Pressure regulator 3 short to battery current < threshold idr_Mess3 < idr3 + idrs_lowidrs_low = 2D map (Current vs Temp) Solenoid Supply > threshold
Engine not running
Measured control signal PWM = 0%udrso_prf = 2D map (V vs Temp) See
App A, Ref 1
50mS
2 DTC
Pressure Regulators PR4 P0982Pressure regulator 4 short circuit to
ground or o/c. current > threshold
or
current = 0 idr_Mess4 > idr4 + idrs_high
or
idr1=0mAidrs_high = 2D map (Current vs Temp)
0mA
Solenoid Supply > threshold
Engine running
0% or 100% measured current PWMudrso_prf = 2D map (V vs Temp) See
App A, Ref 1
50mS
2 DTC
8ASXV05.9VH1 Aston Martin
Auto Gearbox Summary Jan 2008
Page 935 of 947
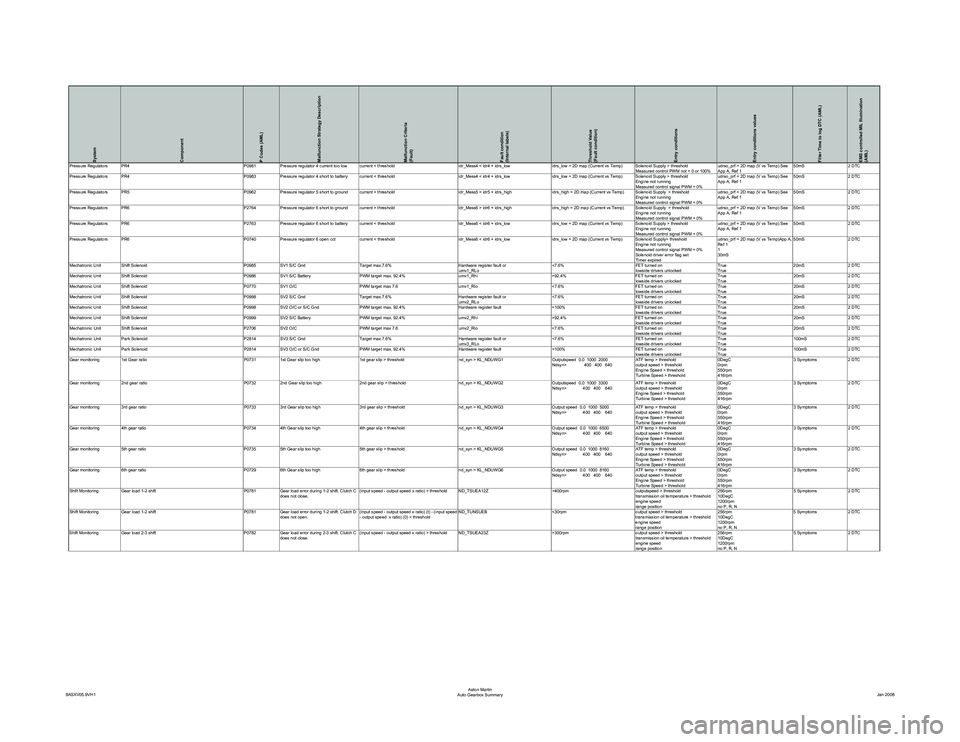
System
Component
P Codes (AML)
Malfunction Strategy Description
Malfunction Criteria
(Fault)
Fault condition
(Internal labels)
Threshold Value
(Fault condition)
Entry conditions
Entry conditions values
Filter Time to log DTC (AML)
EMS controlled MIL Illumination
(AML)
(V vs Temp
)App A,
Ref 1
1
30mS 50mS
2 DTC
Mechatronic Unit Shift Solenoid P0985SV1 S/C Gnd Target max.7.6% Hardware register fault or
umv1_RLo <7.6%
FET turned on
lowside drivers unlockedTrue
True20mS
2 DTC
Mechatronic Unit Shift Solenoid P0986SV1 S/C Battery PWM target max. 92.4% umv1_Rhi>92.4%FET turned on
lowside drivers unlocked True
True20mS
2 DTC
Mechatronic Unit Shift Solenoid P0770SV1 O/C PWM target max 7.6 umv1_Rlo<7.6%FET turned on
lowside drivers unlocked True
True20mS
2 DTC
Mechatronic Unit Shift Solenoid P0998SV2 S/C Gnd Target max.7.6% Hardware register fault or
umv2_RLo <7.6%
FET turned on
lowside drivers unlockedTrue
True20mS
2 DTC
Mechatronic Unit Shift Solenoid P0998SV2 O/C or S/C Gnd PWM target max. 92.4% Hardware register fault=100%FET turned on
lowside drivers unlocked True
True20mS
2 DTC
Mechatronic Unit Shift Solenoid P0999SV2 S/C Battery PWM target max. 92.4% umv2_Rhi>92.4%FET turned on
lowside drivers unlocked True
True20mS
2 DTC
Mechatronic Unit Shift Solenoid P2706SV2 O/C PWM target max 7.6 umv2_Rlo<7.6%FET turned on
lowside drivers unlocked True
True20mS
2 DTC
Mechatronic Unit Park Solenoid P2814SV3 S/C Gnd Target max.7.6% Hardware register fault or
umv3_RLo <7.6%
FET turned on
lowside drivers unlockedTrue
True100mS
2 DTC
Mechatronic Unit Park Solenoid P2814SV3 O/C or S/C Gnd PWM target max. 92.4% Hardware register fault=100%FET turned on
lowside drivers unlocked True
True100mS
2 DTC
Gear monitoring 1st Gear ratio P07311st Gear slip too high 1st gear slip > threshold nd_syn > KL_NDUWG1Outputspeed 0.0 1000 2000
Ndsyn> 400 400 640 ATF temp > threshold
output speed > threshold
Engine Speed > threshold
Turbine Speed > threshold0DegC
0rpm
550rpm
416rpm3 Symptoms
2 DTC
Gear monitoring 2nd gear ratio P07322nd Gear slip too high 2nd gear slip > threshold nd_syn > KL_NDUWG2Outputspeed 0.0 1000 3300
Ndsyn> 400 400 640 ATF temp > threshold
output speed > threshold
Engine Speed > threshold
Turbine Speed > threshold0DegC
0rpm
550rpm
416rpm3 Symptoms
2 DTC
Gear monitoring 3rd gear ratio P07333rd Gear slip too high 3rd gear slip > threshold nd_syn > KL_NDUWG3Output speed 0.0 1000 5000
Ndsyn> 400 400 640 ATF temp > threshold
output speed > threshold
Engine Speed > threshold
Turbine Speed > threshold0DegC
0rpm
550rpm
416rpm3 Symptoms
2 DTC
Gear monitoring 4th gear ratio P07344th Gear slip too high 4th gear slip > threshold nd_syn > KL_NDUWG4Output speed 0.0 1000 6500
Ndsyn> 400 400 640 ATF temp > threshold
output speed > threshold
Engine Speed > threshold
Turbine Speed > threshold0DegC
0rpm
550rpm
416rpm3 Symptoms
2 DTC
Gear monitoring 5th gear ratio P07355th Gear slip too high 5th gear slip > threshold nd_syn > KL_NDUWG5Output speed 0.0 1000 8160
Ndsyn> 400 400 640 ATF temp > threshold
output speed > threshold
Engine Speed > threshold
Turbine Speed > threshold0DegC
0rpm
550rpm
416rpm3 Symptoms
2 DTC
Gear monitoring 6th gear ratio P07296th Gear slip too high 6th gear slip > threshold nd_syn > KL_NDUWG6Output speed 0.0 1000 8160
Ndsyn> 400 400 640 ATF temp > threshold
output speed > threshold
Engine Speed > threshold
Turbine Speed > threshold0DegC
0rpm
550rpm
416rpm3 Symptoms
2 DTC
Shift Monitoring Gear load 1-2 shift P0781Gear load error during 1-2 shift. Clutch C
does not close. (input speed - output speed x ratio) > threshold ND_TSUEA12Z
>400rpmoutputspeed > threshold
transmission oil temperature > threshold
engine speed
range position 256rpm
10DegC
1200rpm
no P, R, N5 Symptoms
2 DTC
Shift Monitoring Gear load 1-2 shift P0781Gear load error during 1-2 shift. Clutch D
does not open.
(input speed - output speed x ratio
) (t) - (input speed
- output speed x ratio) (0) < threshold ND_TUNSUEB
<30rpmoutput speed > threshold
transmission oil temperature > threshold
engine speed
range position 256rpm
10DegC
1200rpm
no P, R, N5 Symptoms
2 DTC
Shift Monitoring Gear load 2-3 shift P0782Gear load error during 2-3 shift. Clutch C
does not close. (input speed - output speed x ratio) > threshold ND_TSUEA23Z
>300rpmoutput speed > threshold
transmission oil temperature > threshold
engine speed
range position 256rpm
10DegC
1200rpm
no P, R, N5 Symptoms
2 DTC
8ASXV05.9VH1 Aston Martin
Auto Gearbox Summary Jan 2008