AUDI S4 1998 B5 / 1.G Engine Manual
Manufacturer: AUDI, Model Year: 1998, Model line: S4, Model: AUDI S4 1998 B5 / 1.GPages: 72, PDF Size: 3.25 MB
Page 21 of 72
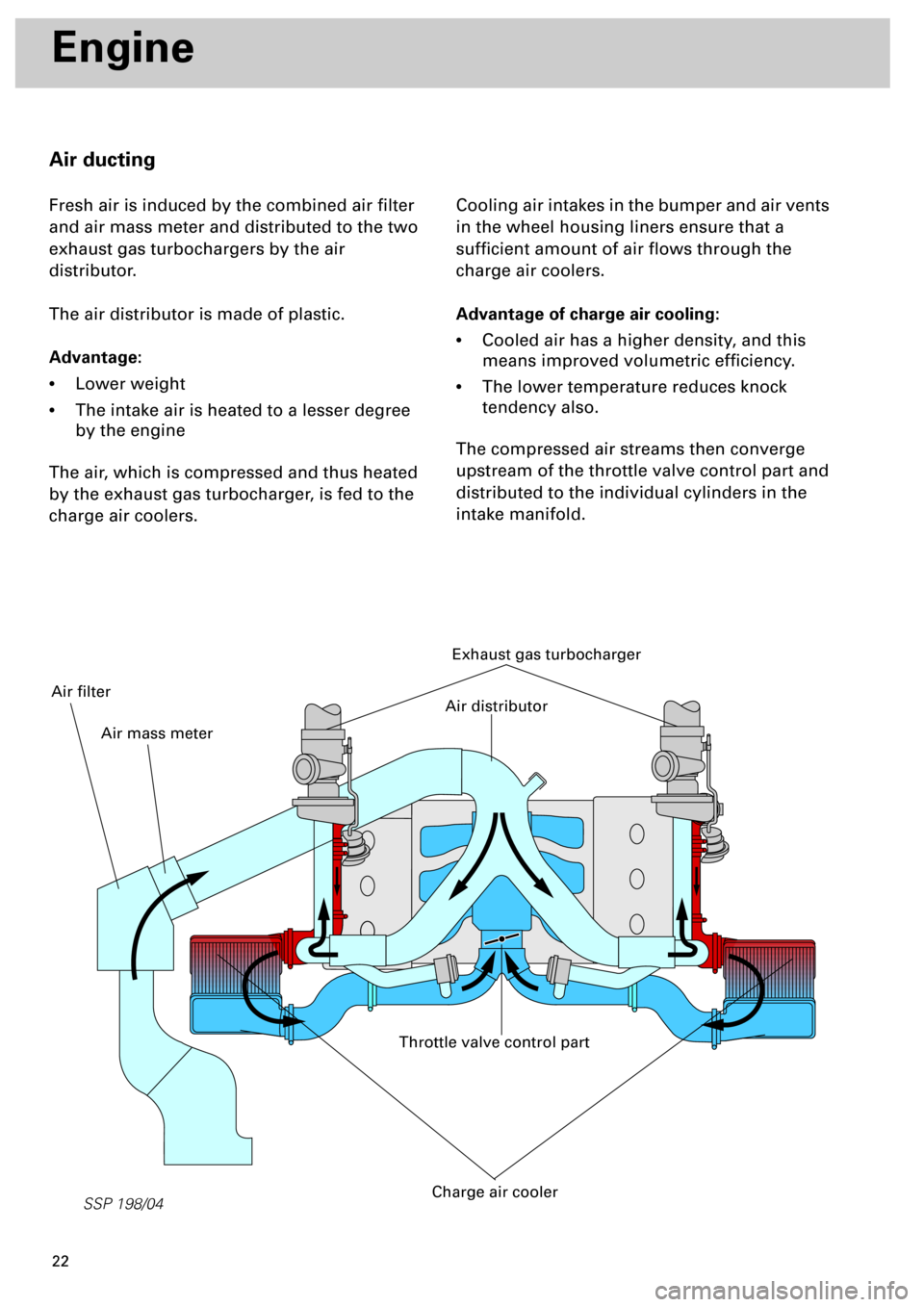
22
SSP 198/04
Engine
Air ducting
Fresh air is induced by the combined air filter
and air mass meter and distributed to the two
exhaust gas turbochargers by the air
distributor.
The air distributor is made of plastic.
Advantage:
•
Lower weight
•
The intake air is heated to a lesser degree
by the engine
The air, which is compressed and thus heated
by the exhaust gas turbocharger, is fed to the
charge air coolers.Cooling air intakes in the bumper and air vents
in the wheel housing liners ensure that a
sufficient amount of air flows through the
charge air coolers.
Advantage of charge air cooling:
•
Cooled air has a higher density, and this
means improved volumetric efficiency.
•
The lower temperature reduces knock
tendency also.
The compressed air streams then converge
upstream of the throttle valve control part and
distributed to the individual cylinders in the
intake manifold.
Exhaust gas turbocharger
Throttle valve control part
Charge air cooler
Air distributor
Air mass meter
Air filter
Page 22 of 72
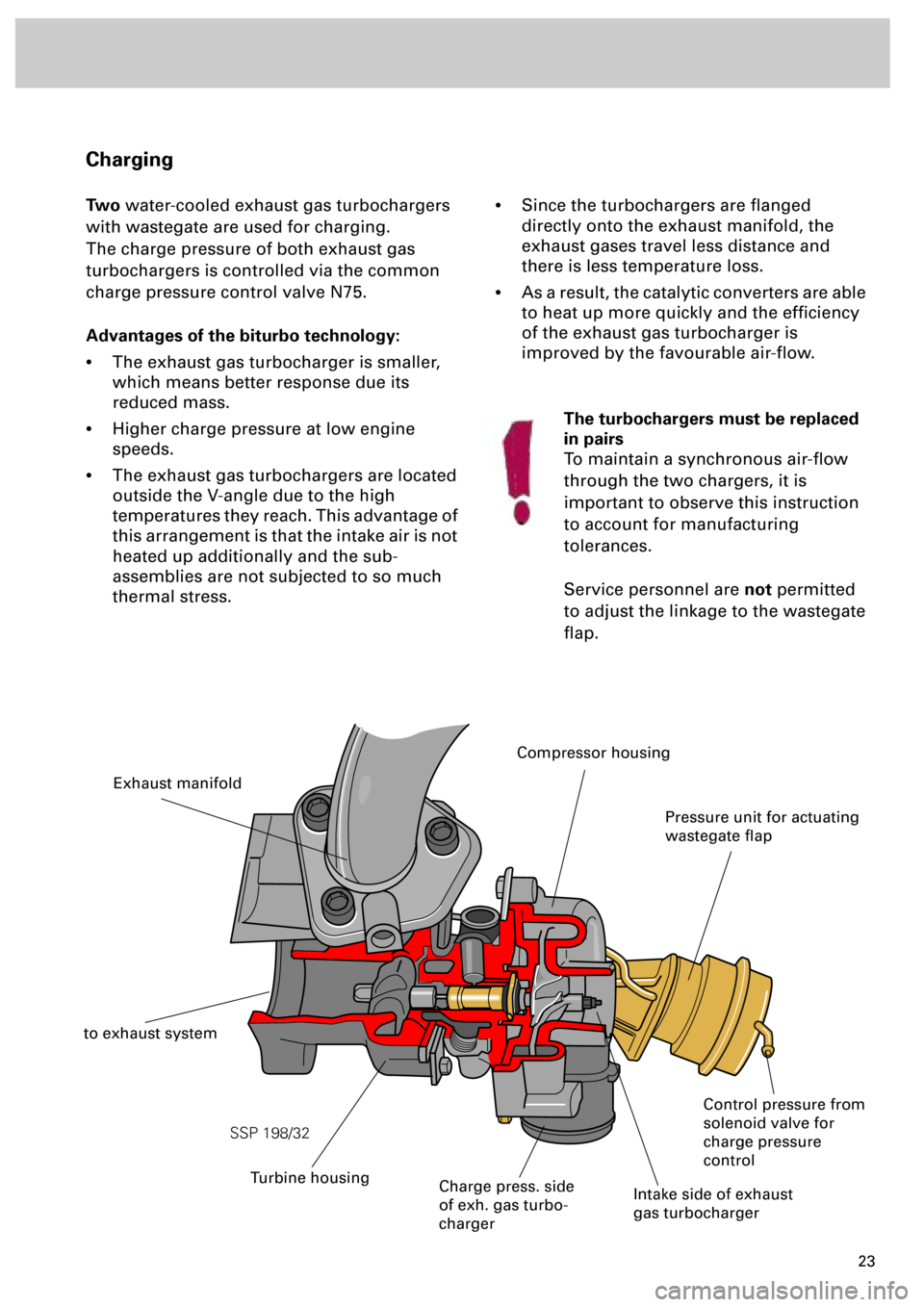
23
SSP 198/32
Charging
Two
water-cooled exhaust gas turbochargers
with wastegate are used for charging.
The charge pressure of both exhaust gas
turbochargers is controlled via the common
charge pressure control valve N75.
Advantages of the biturbo technology:
•
The exhaust gas turbocharger is smaller,
which means better response due its
reduced mass.
•
Higher charge pressure at low engine
speeds.
•
The exhaust gas turbochargers are located
outside the V-angle due to the high
temperatures they reach. This advantage of
this arrangement is that the intake air is not
heated up additionally and the sub-
assemblies are not subjected to so much
thermal stress.
•
Since the turbochargers are flanged
directly onto the exhaust manifold, the
exhaust gases travel less distance and
there is less temperature loss.
•
As a result, the catalytic converters are able
to heat up more quickly and the efficiency
of the exhaust gas turbocharger is
improved by the favourable air-flow.
Intake side of exhaust
gas turbocharger
Charge press. side
of exh. gas turbo-
charger
Exhaust manifold
to exhaust system
Pressure unit for actuating
wastegate flap
Control pressure from
solenoid valve for
charge pressure
control
The turbochargers must be replaced
in pairs
To maintain a synchronous air-flow
through the two chargers, it is
important to observe this instruction
to account for manufacturing
tolerances.
Service personnel are
not
permitted
to adjust the linkage to the wastegate
flap.
Turbine housing
Compressor housing
Page 23 of 72
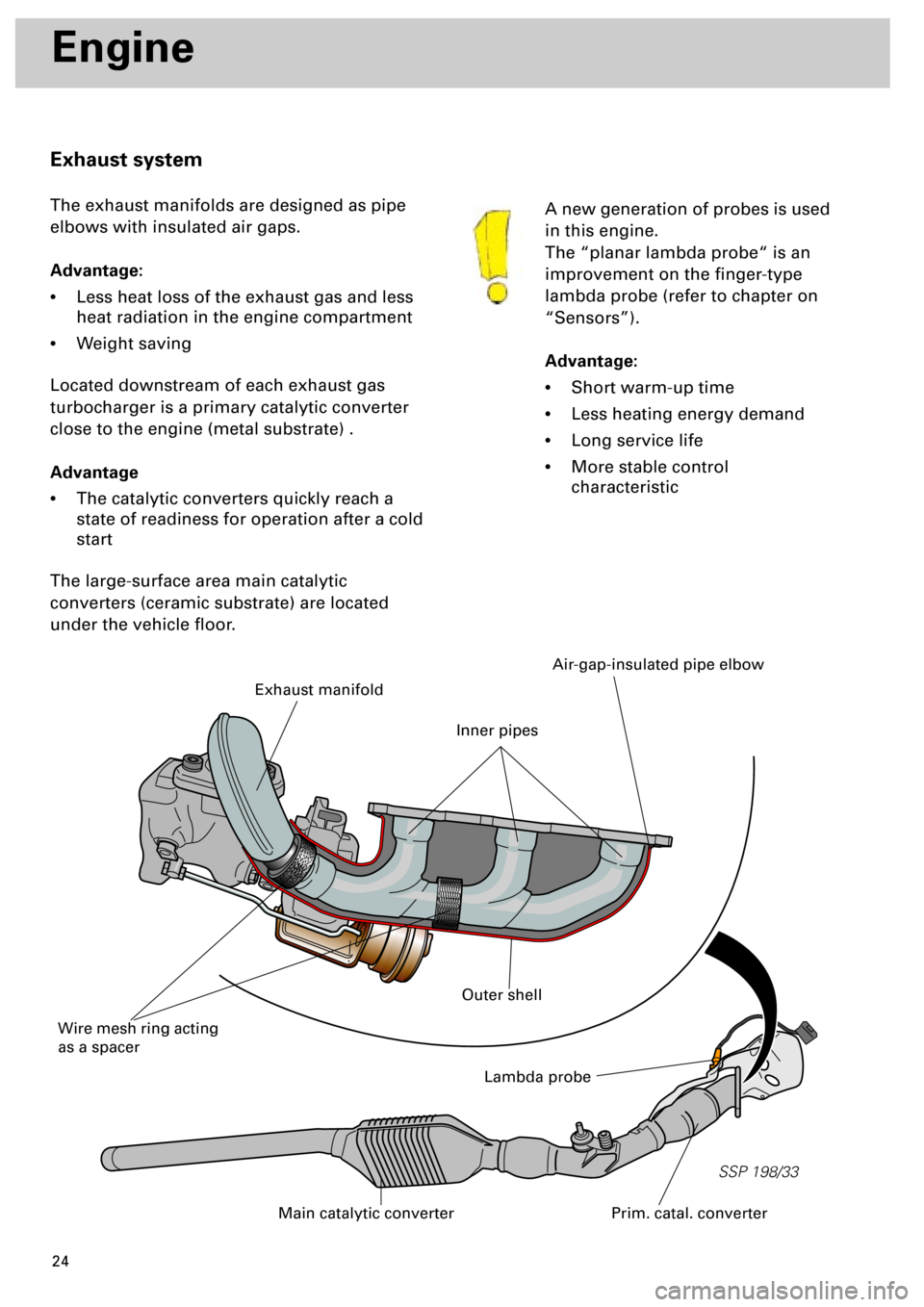
24
SSP 198/33
Engine
A new generation of probes is used
in this engine.
The “planar lambda probe“ is an
improvement on the finger-type
lambda probe (refer to chapter on
“Sensors”).
Advantage:
•
Short warm-up time
•
Less heating energy demand
•
Long service life
•
More stable control
characteristic
Exhaust system
The exhaust manifolds are designed as pipe
elbows with insulated air gaps.
Advantage:
•
Less heat loss of the exhaust gas and less
heat radiation in the engine compartment
•
Weight saving
Located downstream of each exhaust gas
turbocharger is a primary catalytic converter
close to the engine (metal substrate) .
Advantage
•
The catalytic converters quickly reach a
state of readiness for operation after a cold
start
The large-surface area main catalytic
converters (ceramic substrate) are located
under the vehicle floor.
Lambda probe
Prim. catal. converterMain catalytic converter
Exhaust manifold
Wire mesh ring acting
as a spacer
Air-gap-insulated pipe elbow
Outer shell
Inner pipes
Page 24 of 72
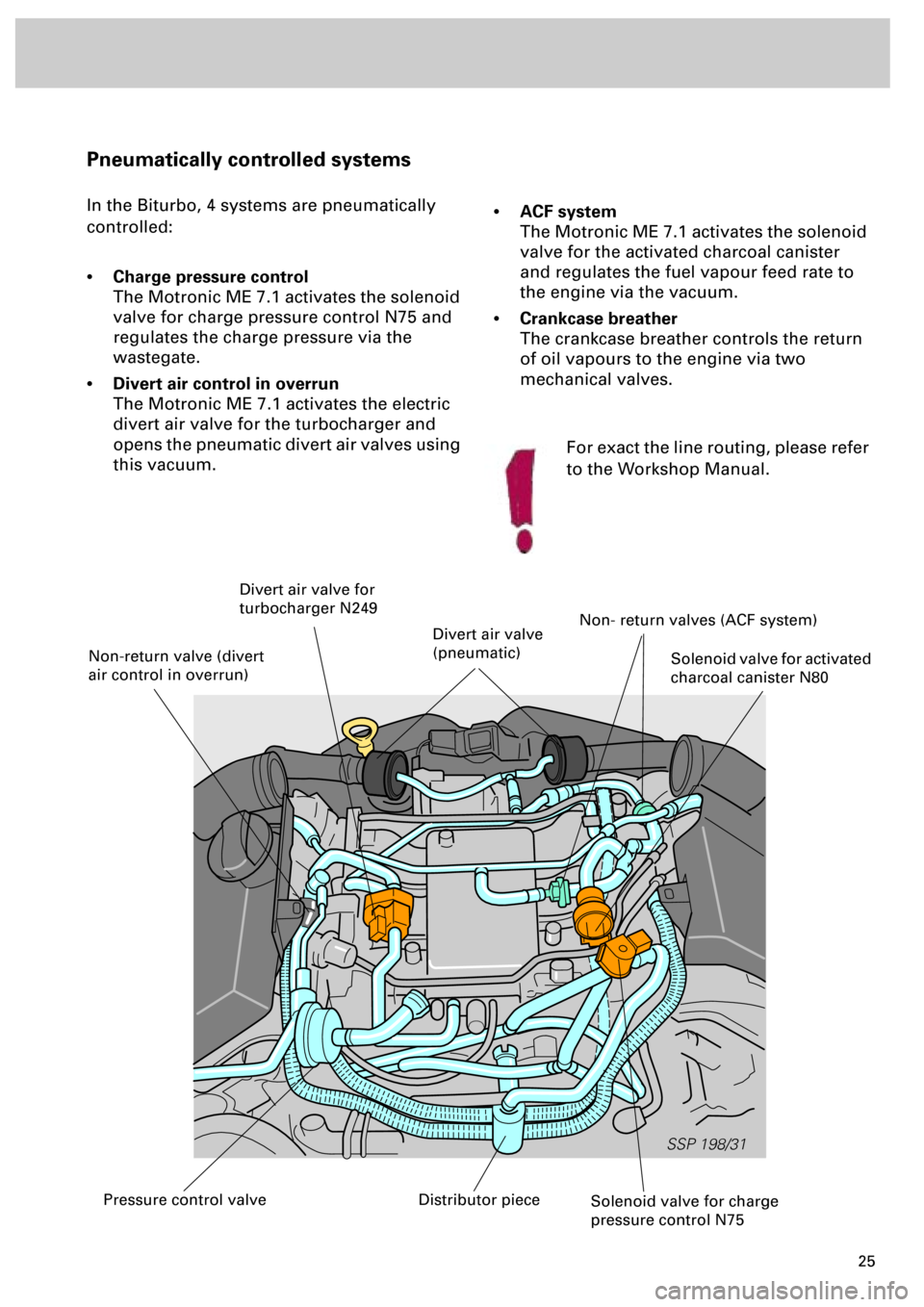
25
SSP 198/31
Pneumatically controlled systems
In the Biturbo, 4 systems are pneumatically
controlled:
•
Charge pressure control
The Motronic ME 7.1 activates the solenoid
valve for charge pressure control N75 and
regulates the charge pressure via the
wastegate.
•
Divert air control in overrun
The Motronic ME 7.1 activates the electric
divert air valve for the turbocharger and
opens the pneumatic divert air valves using
this vacuum.
•
ACF system
The Motronic ME 7.1 activates the solenoid
valve for the activated charcoal canister
and regulates the fuel vapour feed rate to
the engine via the vacuum.
•
Crankcase breather
The crankcase breather controls the return
of oil vapours to the engine via two
mechanical valves.
Solenoid valve for charge
pressure control N75
Solenoid valve for activated
charcoal canister N80
Divert air valve for
turbocharger N249
Non- return valves (ACF system)
Distributor piecePressure control valve
Non-return valve (divert
air control in overrun)
Divert air valve
(pneumatic)
For exact the line routing, please refer
to the Workshop Manual.
Page 25 of 72
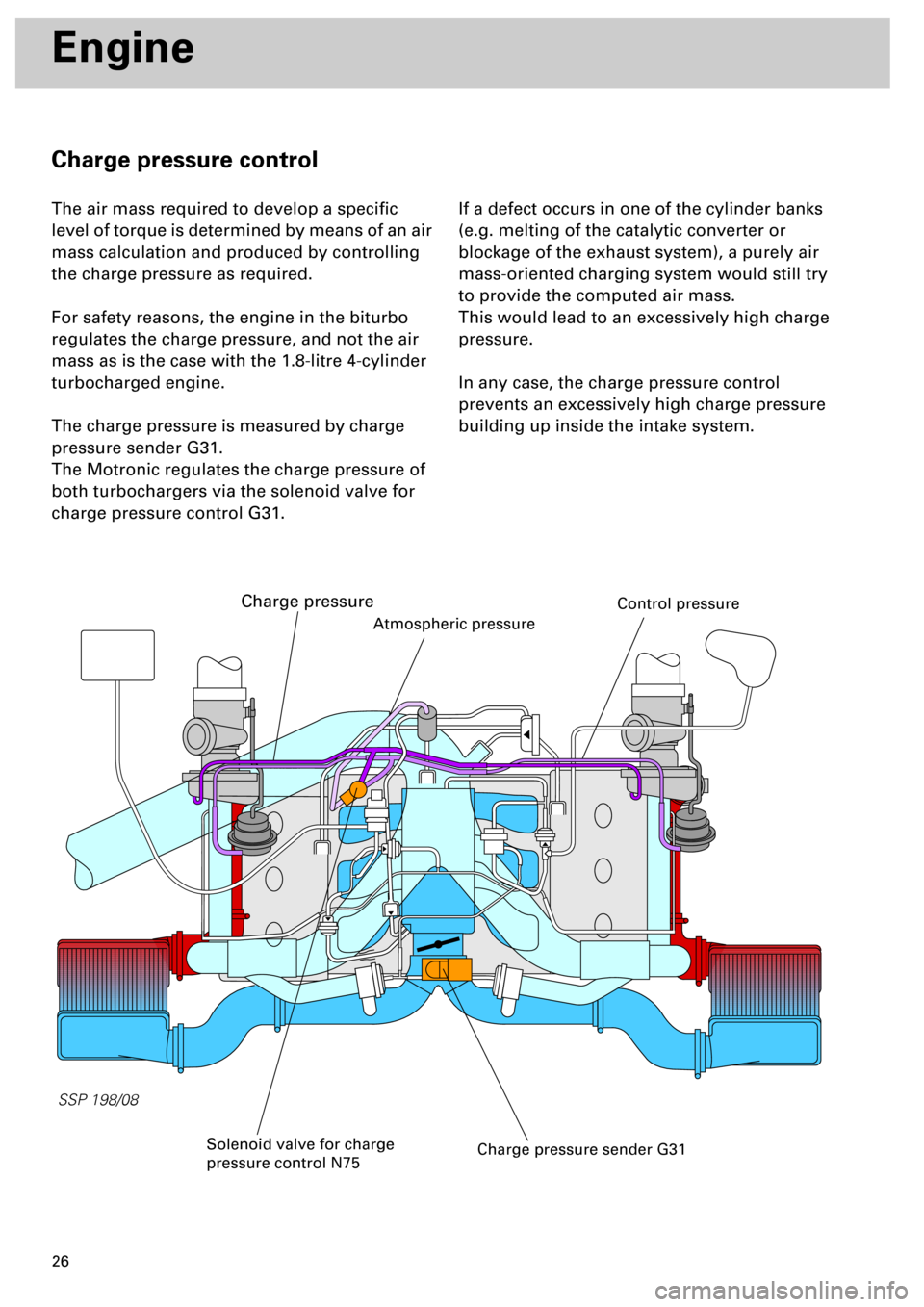
26
SSP 198/08
Engine
Charge pressure control
The air mass required to develop a specific
level of torque is determined by means of an air
mass calculation and produced by controlling
the charge pressure as required.
For safety reasons, the engine in the biturbo
regulates the charge pressure, and not the air
mass as is the case with the 1.8-litre 4-cylinder
turbocharged engine.
The charge pressure is measured by charge
pressure sender G31.
The Motronic regulates the charge pressure of
both turbochargers via the solenoid valve for
charge pressure control G31.
If a defect occurs in one of the cylinder banks
(e.g. melting of the catalytic converter or
blockage of the exhaust system), a purely air
mass-oriented charging system would still try
to provide the computed air mass.
This would lead to an excessively high charge
pressure.
In any case, the charge pressure control
prevents an excessively high charge pressure
building up inside the intake system.
Charge pressure sender G31
Atmospheric pressure
Solenoid valve for charge
pressure control N75
Charge pressure
Control pressure
Page 26 of 72
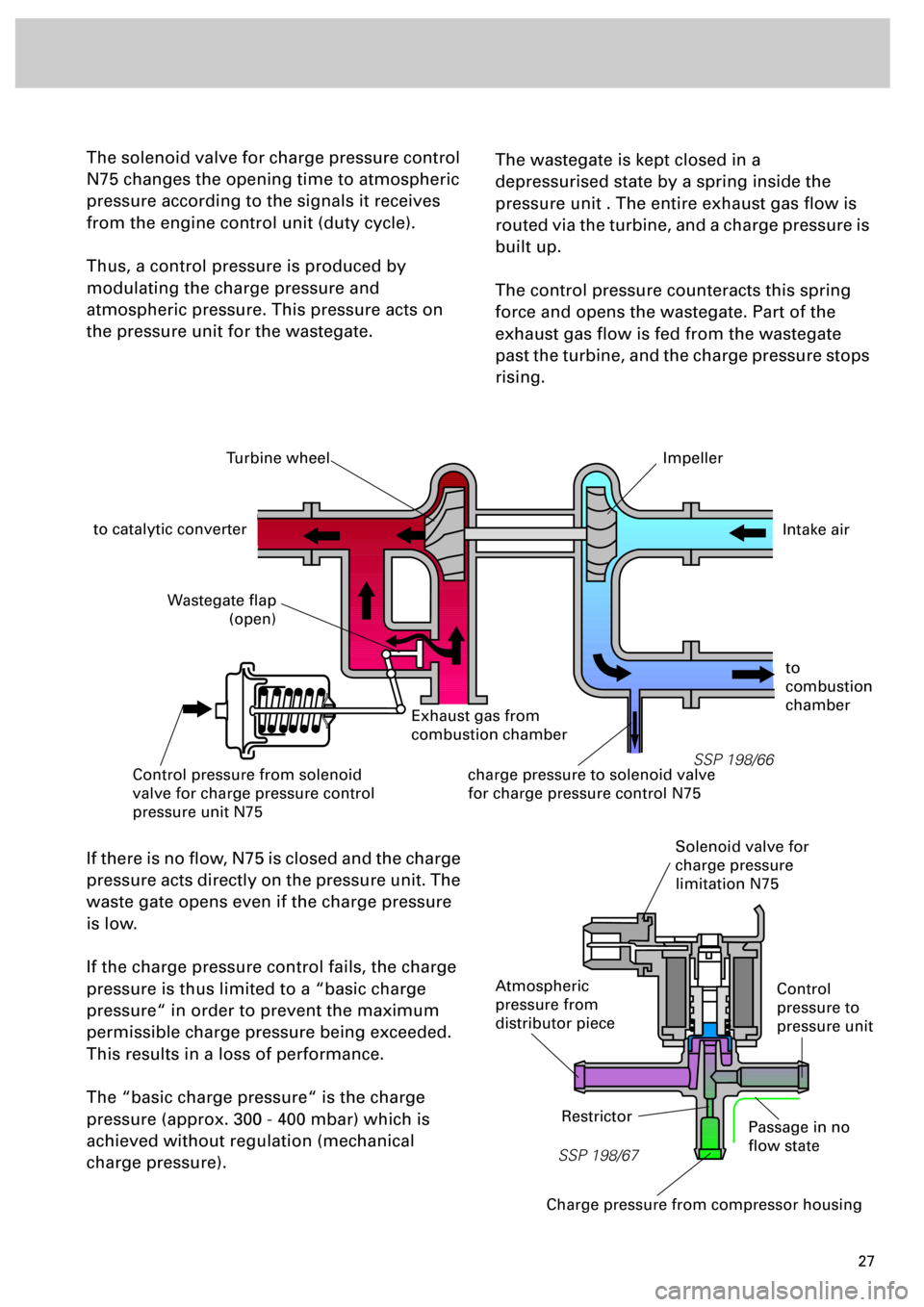
27
The solenoid valve for charge pressure control
N75 changes the opening time to atmospheric
pressure according to the signals it receives
from the engine control unit (duty cycle).
Thus, a control pressure is produced by
modulating the charge pressure and
atmospheric pressure. This pressure acts on
the pressure unit for the wastegate.
The wastegate is kept closed in a
depressurised state by a spring inside the
pressure unit . The entire exhaust gas flow is
routed via the turbine, and a charge pressure is
built up.
The control pressure counteracts this spring
force and opens the wastegate. Part of the
exhaust gas flow is fed from the wastegate
past the turbine, and the charge pressure stops
rising.
If there is no flow, N75 is closed and the charge
pressure acts directly on the pressure unit. The
waste gate opens even if the charge pressure
is low.
If the charge pressure control fails, the charge
pressure is thus limited to a “basic charge
pressure“ in order to prevent the maximum
permissible charge pressure being exceeded.
This results in a loss of performance.
The “basic charge pressure“ is the charge
pressure (approx. 300 - 400 mbar) which is
achieved without regulation (mechanical
charge pressure).
SSP 198/66
Turbine wheel
to catalytic converter
Impeller
Exhaust gas from
combustion chamber
Wastegate flap
(open)
Control pressure from solenoid
valve for charge pressure control
pressure unit N75charge pressure to solenoid valve
for charge pressure control N75
Intake air
to
combustion
chamber
SSP 198/67
Atmospheric
pressure from
distributor piece
Solenoid valve for
charge pressure
limitation N75
Charge pressure from compressor housing
RestrictorPassage in no
flow state
Control
pressure to
pressure unit
Page 27 of 72
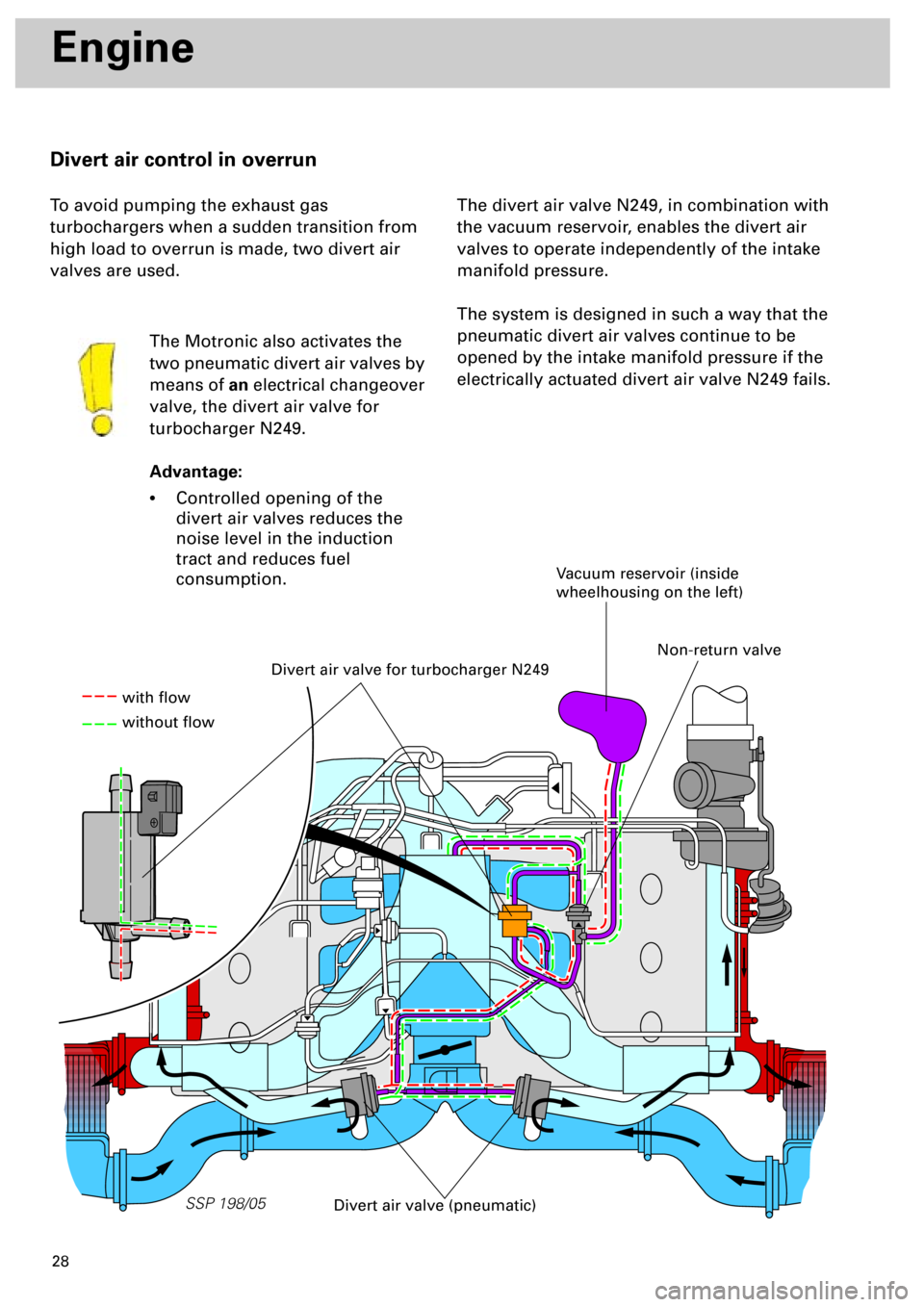
28
SSP 198/05
Engine
Divert air control in overrun
To avoid pumping the exhaust gas
turbochargers when a sudden transition from
high load to overrun is made, two divert air
valves are used.
The Motronic also activates the
two pneumatic divert air valves by
means of
an
electrical changeover
valve, the divert air valve for
turbocharger N249.
Advantage:
•
Controlled opening of the
divert air valves reduces the
noise level in the induction
tract and reduces fuel
consumption.
The divert air valve N249, in combination with
the vacuum reservoir, enables the divert air
valves to operate independently of the intake
manifold pressure.
The system is designed in such a way that the
pneumatic divert air valves continue to be
opened by the intake manifold pressure if the
electrically actuated divert air valve N249 fails.
Divert air valve for turbocharger N249
Vacuum reservoir (inside
wheelhousing on the left)
Divert air valve (pneumatic)
with flow
without flow
Non-return valve
Page 28 of 72
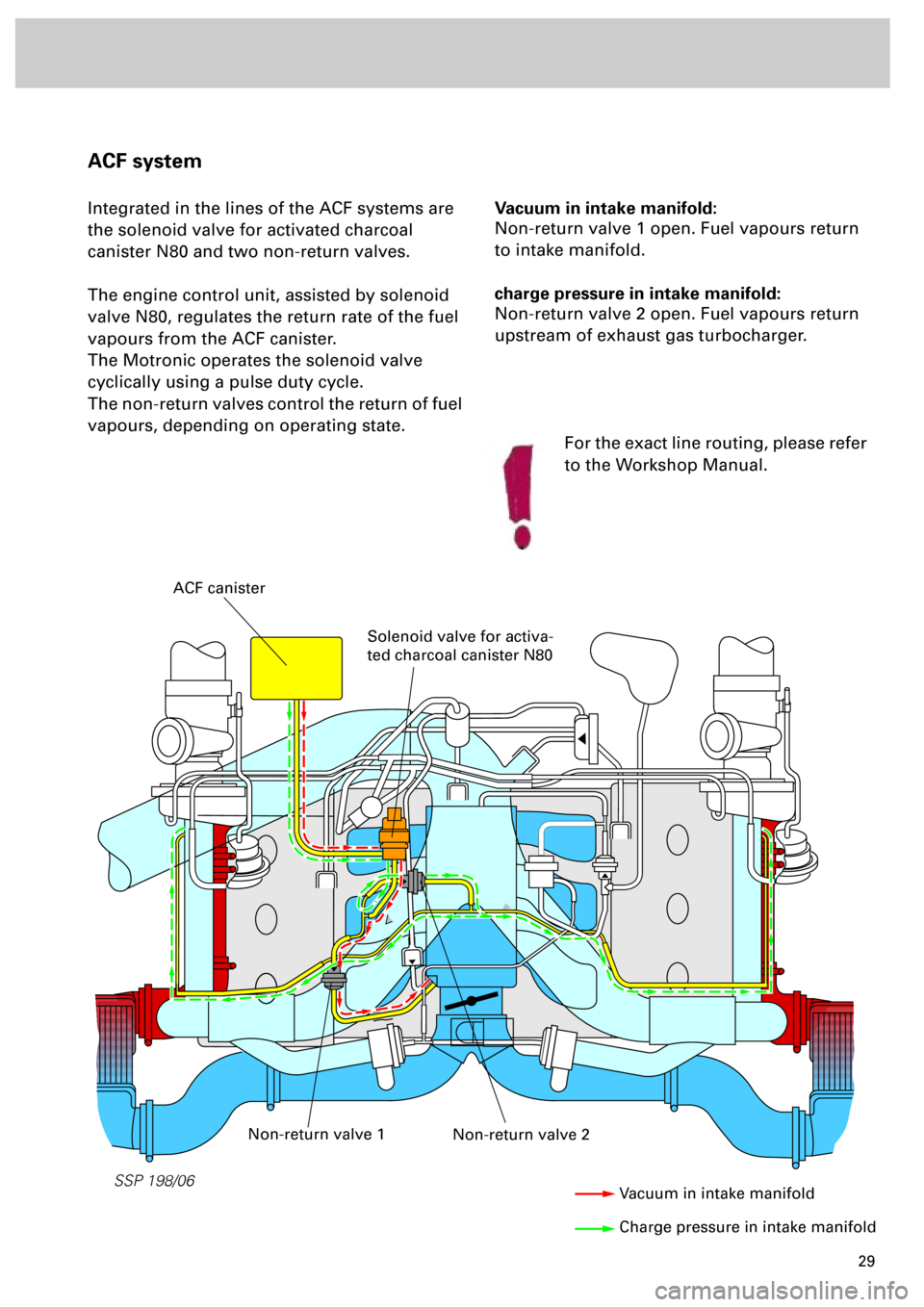
29
SSP 198/06
Vacuum in intake manifold:
Non-return valve 1 open. Fuel vapours return
to intake manifold.
charge pressure in intake manifold:
Non-return valve 2 open. Fuel vapours return
upstream of exhaust gas turbocharger.
ACF system
Integrated in the lines of the ACF systems are
the solenoid valve for activated charcoal
canister N80 and two non-return valves.
The engine control unit, assisted by solenoid
valve N80, regulates the return rate of the fuel
vapours from the ACF canister.
The Motronic operates the solenoid valve
cyclically using a pulse duty cycle.
The non-return valves control the return of fuel
vapours, depending on operating state.
ACF canister
Solenoid valve for activa-
ted charcoal canister N80
Non-return valve 2Non-return valve 1
Vacuum in intake manifold
Charge pressure in intake manifold
For the exact line routing, please refer
to the Workshop Manual.
Page 29 of 72
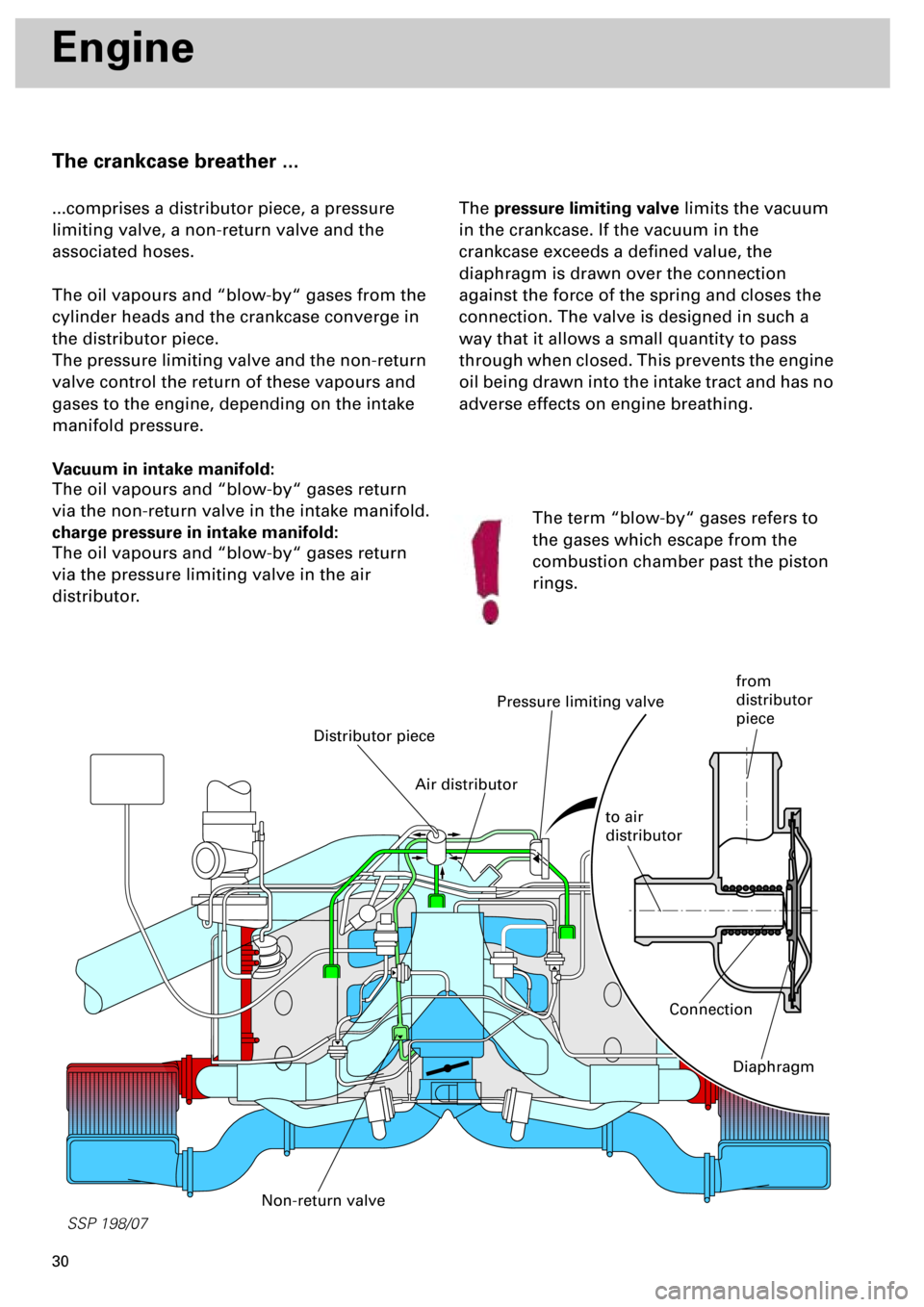
30
SSP 198/07
Engine
The crankcase breather ...
...comprises a distributor piece, a pressure
limiting valve, a non-return valve and the
associated hoses.
The oil vapours and “blow-by“ gases from the
cylinder heads and the crankcase converge in
the distributor piece.
The pressure limiting valve and the non-return
valve control the return of these vapours and
gases to the engine, depending on the intake
manifold pressure.
Vacuum in intake manifold:
The oil vapours and “blow-by“ gases return
via the non-return valve in the intake manifold.
charge pressure in intake manifold:
The oil vapours and “blow-by“ gases return
via the pressure limiting valve in the air
distributor.The pressure limiting valve limits the vacuum
in the crankcase. If the vacuum in the
crankcase exceeds a defined value, the
diaphragm is drawn over the connection
against the force of the spring and closes the
connection. The valve is designed in such a
way that it allows a small quantity to pass
through when closed. This prevents the engine
oil being drawn into the intake tract and has no
adverse effects on engine breathing.
Distributor piece
Pressure limiting valve
Non-return valve
The term “blow-by“ gases refers to
the gases which escape from the
combustion chamber past the piston
rings.
Connection
Diaphragm
Air distributor
to air
distributor
from
distributor
piece
Page 30 of 72
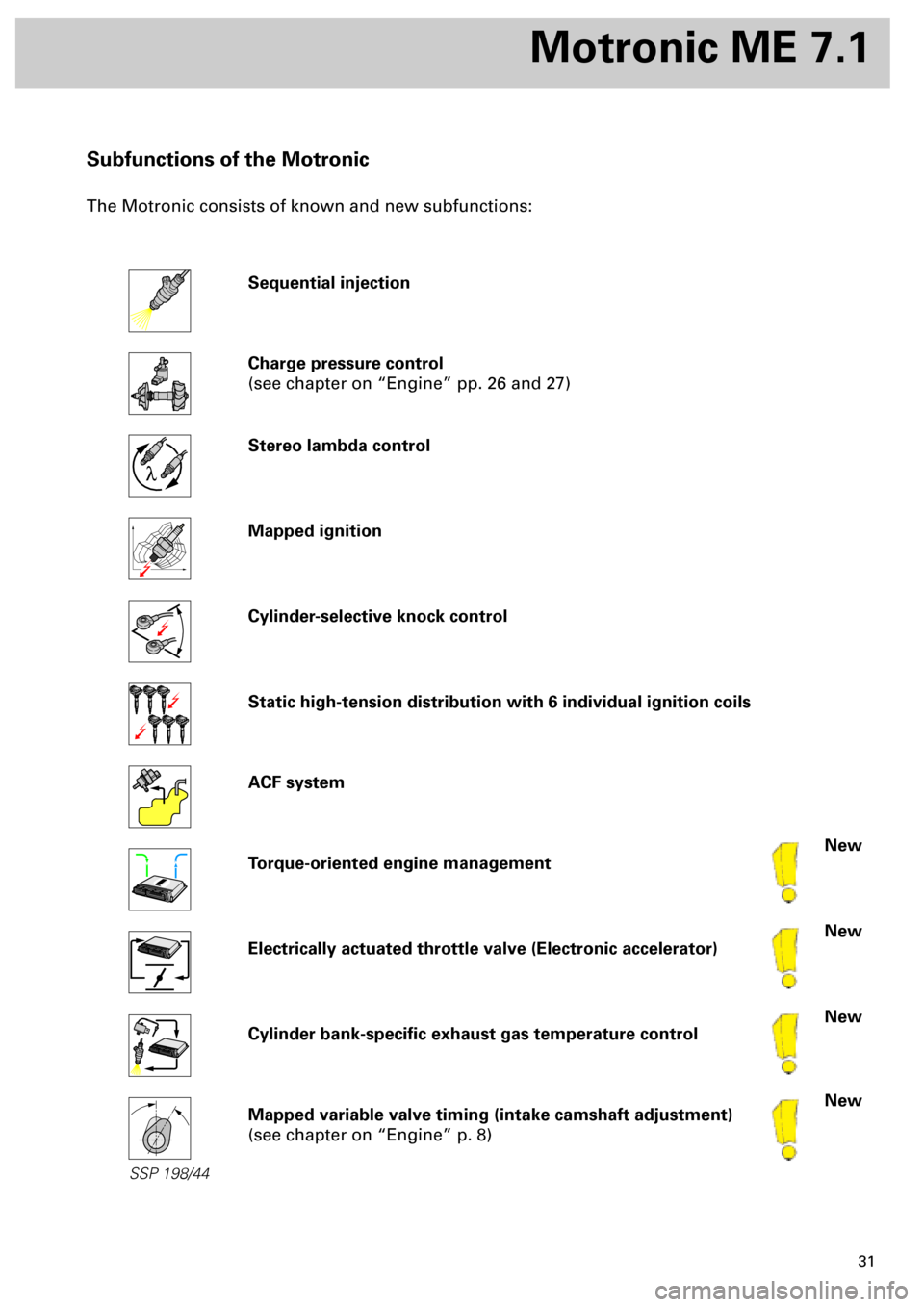
31
Motronic ME 7.1
Subfunctions of the Motronic
The Motronic consists of known and new subfunctions:
Sequential injection
Charge pressure control
(see chapter on “Engine” pp. 26 and 27)
Stereo lambda control
Mapped ignition
Cylinder-selective knock control
Static high-tension distribution with 6 individual ignition coils
ACF system
Torque-oriented engine management
Electrically actuated throttle valve (Electronic accelerator)
Cylinder bank-specific exhaust gas temperature control
Mapped variable valve timing (intake camshaft adjustment)
(see chapter on “Engine” p. 8)
New
New
New
New
l
SSP 198/44