boot BMW 3 SERIES 1983 E30 Owner's Manual
[x] Cancel search | Manufacturer: BMW, Model Year: 1983, Model line: 3 SERIES, Model: BMW 3 SERIES 1983 E30Pages: 228, PDF Size: 7.04 MB
Page 156 of 228

syringe or hand pump, empty the power
steering fluid reservoir.
4On power steering models, remove the
banjo bolts and disconnect the power
steering pressure and return lines from the
steering gear. Place a container under the
lines to catch spilled fluid. Plug the lines to
prevent excessive fluid loss and
contamination. Discard the sealing washers
(new ones should be used when
reassembling).
5Disconnect the track rod ends from the
steering arms (see Section 17).
6Remove the nuts and bolts from the
steering gear mounting brackets (see
illustration). Discard the old nuts.
7Withdraw the assembly from beneath the
vehicle. Take care not to damage the steering
gear boots.
Refitting
8Refitting is the reverse of removal. Make
sure the marks you made on the lower
universal joint and the pinion shaft are aligned
before you tighten the clamping bolts for the
upper and lower universal joints. Use new
self-locking nuts on the steering rackmounting bolts, and new sealing washers on
the hydraulic line fittings. Tighten the
mounting bolts, the track rod end nuts and the
universal joint shaft clamping bolts to the
torque values listed in this Chapter’s Specifi-
cations.
9Lower the vehicle to the ground.
10On power steering models, fill the
reservoir with the recommended fluid (see
Chapter 1) and bleed the power steering
system (see Section 23).
11It’s a good idea to have the front wheel
alignment checked by a dealer service
department or qualified garage.
20 Steering linkage (5-Series)-
inspection, removal and
refitting
4
Inspection
1Raise the vehicle and place it securely on
axle stands.
2Firmly grasp each front tyre at the top and
bottom, then at the front and rear, and check
for play in the steering linkage by rocking the
tyre back and forth. There should be little or
no play in any of the linkage balljoints. Inspect
the Pitman arm, the idler arm, the centre track
rod, the inner track rods, the track rod ends
and the steering arms for any obvious
damage. Try forcing the linkage parts in
opposite directions from one another. There
should be no play between any of them. If any
of the parts are bent or damaged in any way,
or if any of the balljoints are worn, renew the
parts concerned.
Removal
3Before dismantling the steering linkage,
obtain a suitable balljoint separator. A two-jaw
puller or a wedge-type tool will work (although
the wedge-type tends to tear the balljoint
boots). Sometimes, you can also jar a balljoint
taper pin free from its eye by striking opposite
sides of the eye simultaneously with two large
hammers, but the space available to do this is
limited, and the balljoint stud sometimessticks to the eye because of rust and dirt.
There is also a risk of damaging the
component being struck.
4To remove the outer track rods, disconnect
the track rod ends from the steering arms (see
Section 17). Remove the nut that attaches the
balljoint on the inner end of each outer track
rod to the centre track rod (see illustration).
Using a balljoint separator, disconnect the
outer track rods from the centre track rod. If
you’re renewing the balljoint at either end of
the outer track rods, paint or scribe alignment
marks on the threads to mark their respective
positions as a guide to adjustment during
reassembly (see illustration 17.3).
5To remove the centre track rod, remove the
nuts that attach the centre track rod balljoints
to the Pitman arm and the idler arm, and use a
balljoint separator to disconnect the balljoints
from the two arms.
6To remove the Pitman arm, you’ll have to
remove the steering box first (see Section 21).
Look for match marks between the sector
shaft and arm. If there aren’t any, scribe a
mark across the bottom face of both parts.
Remove the Pitman arm pinch-bolt and nut,
then remove the arm with a puller.
7To unbolt the idler arm, first remove the
small cover bolted to the top of the subframe
crossmember. Put a spanner on the bolt, and
remove the nut recessed into the underside of
the subframe crossmember (see illustration).
Check the idler arm rubber bush for wear. If
it’s damaged or worn, renew it.
8Check each balljoint for excessive play or
stiffness, and for split or deteriorated rubber
dust boots. Renew all worn or damaged
balljoints. The inner and outer track rod ends
on the outer track rods can be renewed
individually; if either balljoint on the centre
track rod is damaged or worn, you must
renew the centre track rod.
Refitting
9Refitting is the reverse of the removal
procedure, but observe the following points:
a) Realign the match marks on the Pitman
arm and the steering box sector shaft
when reassembling them.
b) If you’re fitting new inner or outer track
rod ends on the outer track rods, position
them so that the match marks made
during dismantling are aligned, and make
sure they are equally spaced on each
side.
c) Position the track rod end balljoint studs
on the outer track rods at an angle of 90°
to each other.
d) Make sure the left and right outer track
rods are equal in length when they are
fitted.
e) Tighten all retaining bolts to the torque
values listed in this Chapter’s Specifi-
cations.
f) When reassembly of the linkage is
complete, have the front wheel alignment
checked, and if necessary, adjusted.
10•14 Suspension and steering systems
20.7 To unbolt the idler arm from the
subframe crossmember, remove this nut
(arrowed)
20.4 To remove an outer track rod,
remove this nut (arrowed) from the end of
the centre track rod, and use a balljoint
separator to separate the balljoint stud
from the centre track rod (if you’re
renewing the inner track rod end, mark the
threads with paint before loosening the
clamp bolt and nut)
19.6 Rack-and-pinion steering gear
mounting bolts (arrowed) - 3-Series
models - (self-locking nuts not visible in
this photo)
Page 160 of 228
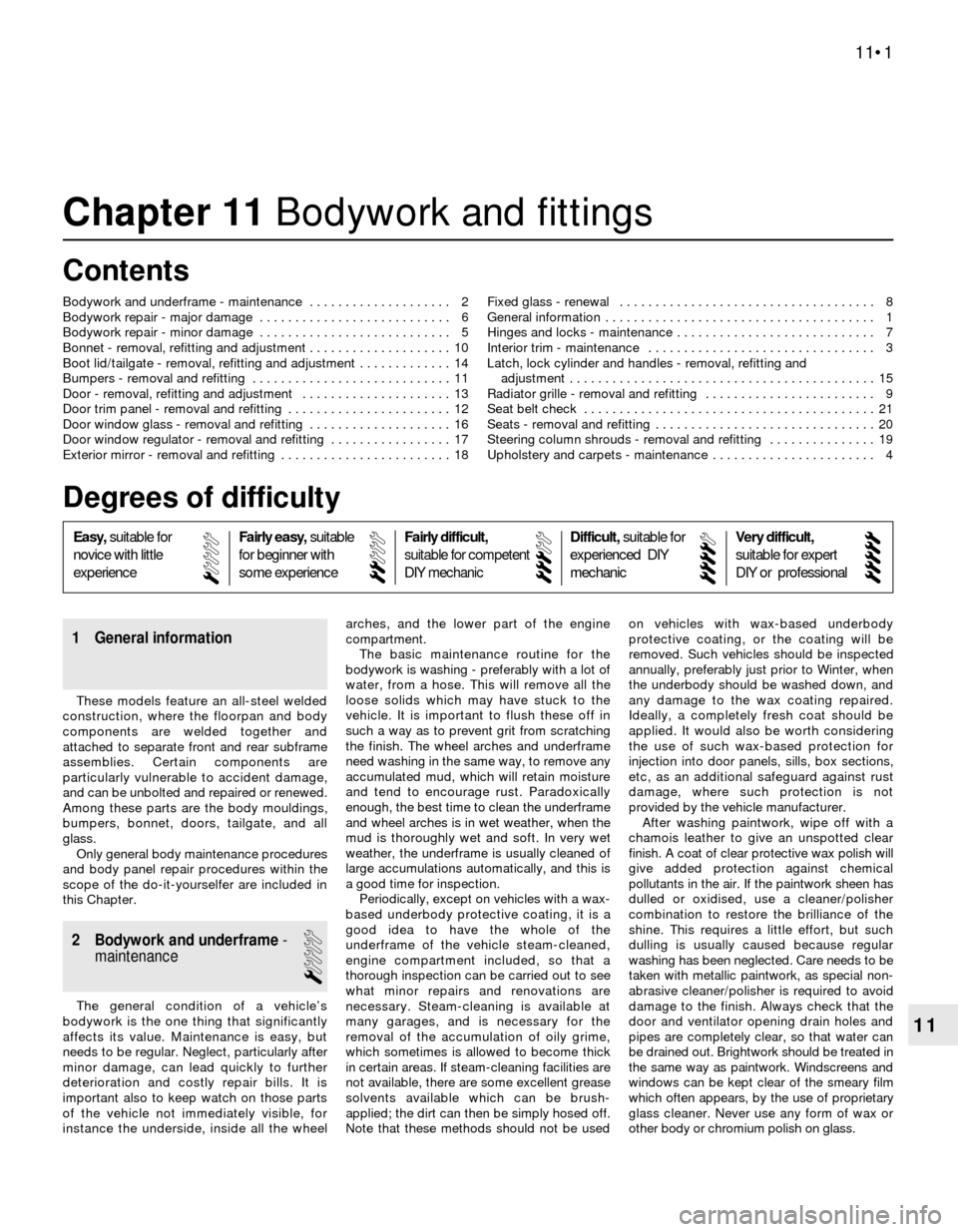
11
1 General information
These models feature an all-steel welded
construction, where the floorpan and body
components are welded together and
attached to separate front and rear subframe
assemblies. Certain components are
particularly vulnerable to accident damage,
and can be unbolted and repaired or renewed.
Among these parts are the body mouldings,
bumpers, bonnet, doors, tailgate, and all
glass.
Only general body maintenance procedures
and body panel repair procedures within the
scope of the do-it-yourselfer are included in
this Chapter.
2 Bodywork and underframe-
maintenance
1
The general condition of a vehicle’s
bodywork is the one thing that significantly
affects its value. Maintenance is easy, but
needs to be regular. Neglect, particularly after
minor damage, can lead quickly to further
deterioration and costly repair bills. It is
important also to keep watch on those parts
of the vehicle not immediately visible, for
instance the underside, inside all the wheelarches, and the lower part of the engine
compartment.
The basic maintenance routine for the
bodywork is washing - preferably with a lot of
water, from a hose. This will remove all the
loose solids which may have stuck to the
vehicle. It is important to flush these off in
such a way as to prevent grit from scratching
the finish. The wheel arches and underframe
need washing in the same way, to remove any
accumulated mud, which will retain moisture
and tend to encourage rust. Paradoxically
enough, the best time to clean the underframe
and wheel arches is in wet weather, when the
mud is thoroughly wet and soft. In very wet
weather, the underframe is usually cleaned of
large accumulations automatically, and this is
a good time for inspection.
Periodically, except on vehicles with a wax-
based underbody protective coating, it is a
good idea to have the whole of the
underframe of the vehicle steam-cleaned,
engine compartment included, so that a
thorough inspection can be carried out to see
what minor repairs and renovations are
necessary. Steam-cleaning is available at
many garages, and is necessary for the
removal of the accumulation of oily grime,
which sometimes is allowed to become thick
in certain areas. If steam-cleaning facilities are
not available, there are some excellent grease
solvents available which can be brush-
applied; the dirt can then be simply hosed off.
Note that these methods should not be usedon vehicles with wax-based underbody
protective coating, or the coating will be
removed. Such vehicles should be inspected
annually, preferably just prior to Winter, when
the underbody should be washed down, and
any damage to the wax coating repaired.
Ideally, a completely fresh coat should be
applied. It would also be worth considering
the use of such wax-based protection for
injection into door panels, sills, box sections,
etc, as an additional safeguard against rust
damage, where such protection is not
provided by the vehicle manufacturer.
After washing paintwork, wipe off with a
chamois leather to give an unspotted clear
finish. A coat of clear protective wax polish will
give added protection against chemical
pollutants in the air. If the paintwork sheen has
dulled or oxidised, use a cleaner/polisher
combination to restore the brilliance of the
shine. This requires a little effort, but such
dulling is usually caused because regular
washing has been neglected. Care needs to be
taken with metallic paintwork, as special non-
abrasive cleaner/polisher is required to avoid
damage to the finish. Always check that the
door and ventilator opening drain holes and
pipes are completely clear, so that water can
be drained out. Brightwork should be treated in
the same way as paintwork. Windscreens and
windows can be kept clear of the smeary film
which often appears, by the use of proprietary
glass cleaner. Never use any form of wax or
other body or chromium polish on glass.
Chapter 11 Bodywork and fittings
Bodywork and underframe - maintenance . . . . . . . . . . . . . . . . . . . . 2
Bodywork repair - major damage . . . . . . . . . . . . . . . . . . . . . . . . . . . 6
Bodywork repair - minor damage . . . . . . . . . . . . . . . . . . . . . . . . . . . 5
Bonnet - removal, refitting and adjustment . . . . . . . . . . . . . . . . . . . . 10
Boot lid/tailgate - removal, refitting and adjustment . . . . . . . . . . . . . 14
Bumpers - removal and refitting . . . . . . . . . . . . . . . . . . . . . . . . . . . . 11
Door - removal, refitting and adjustment . . . . . . . . . . . . . . . . . . . . . 13
Door trim panel - removal and refitting . . . . . . . . . . . . . . . . . . . . . . . 12
Door window glass - removal and refitting . . . . . . . . . . . . . . . . . . . . 16
Door window regulator - removal and refitting . . . . . . . . . . . . . . . . . 17
Exterior mirror - removal and refitting . . . . . . . . . . . . . . . . . . . . . . . . 18Fixed glass - renewal . . . . . . . . . . . . . . . . . . . . . . . . . . . . . . . . . . . . 8
General information . . . . . . . . . . . . . . . . . . . . . . . . . . . . . . . . . . . . . . 1
Hinges and locks - maintenance . . . . . . . . . . . . . . . . . . . . . . . . . . . . 7
Interior trim - maintenance . . . . . . . . . . . . . . . . . . . . . . . . . . . . . . . . 3
Latch, lock cylinder and handles - removal, refitting and
adjustment . . . . . . . . . . . . . . . . . . . . . . . . . . . . . . . . . . . . . . . . . . . 15
Radiator grille - removal and refitting . . . . . . . . . . . . . . . . . . . . . . . . 9
Seat belt check . . . . . . . . . . . . . . . . . . . . . . . . . . . . . . . . . . . . . . . . . 21
Seats - removal and refitting . . . . . . . . . . . . . . . . . . . . . . . . . . . . . . . 20
Steering column shrouds - removal and refitting . . . . . . . . . . . . . . . 19
Upholstery and carpets - maintenance . . . . . . . . . . . . . . . . . . . . . . . 4
11•1
Easy,suitable for
novice with little
experienceFairly easy,suitable
for beginner with
some experienceFairly difficult,
suitable for competent
DIY mechanic
Difficult,suitable for
experienced DIY
mechanicVery difficult,
suitable for expert
DIY or professional
Degrees of difficulty Contents
Page 163 of 228
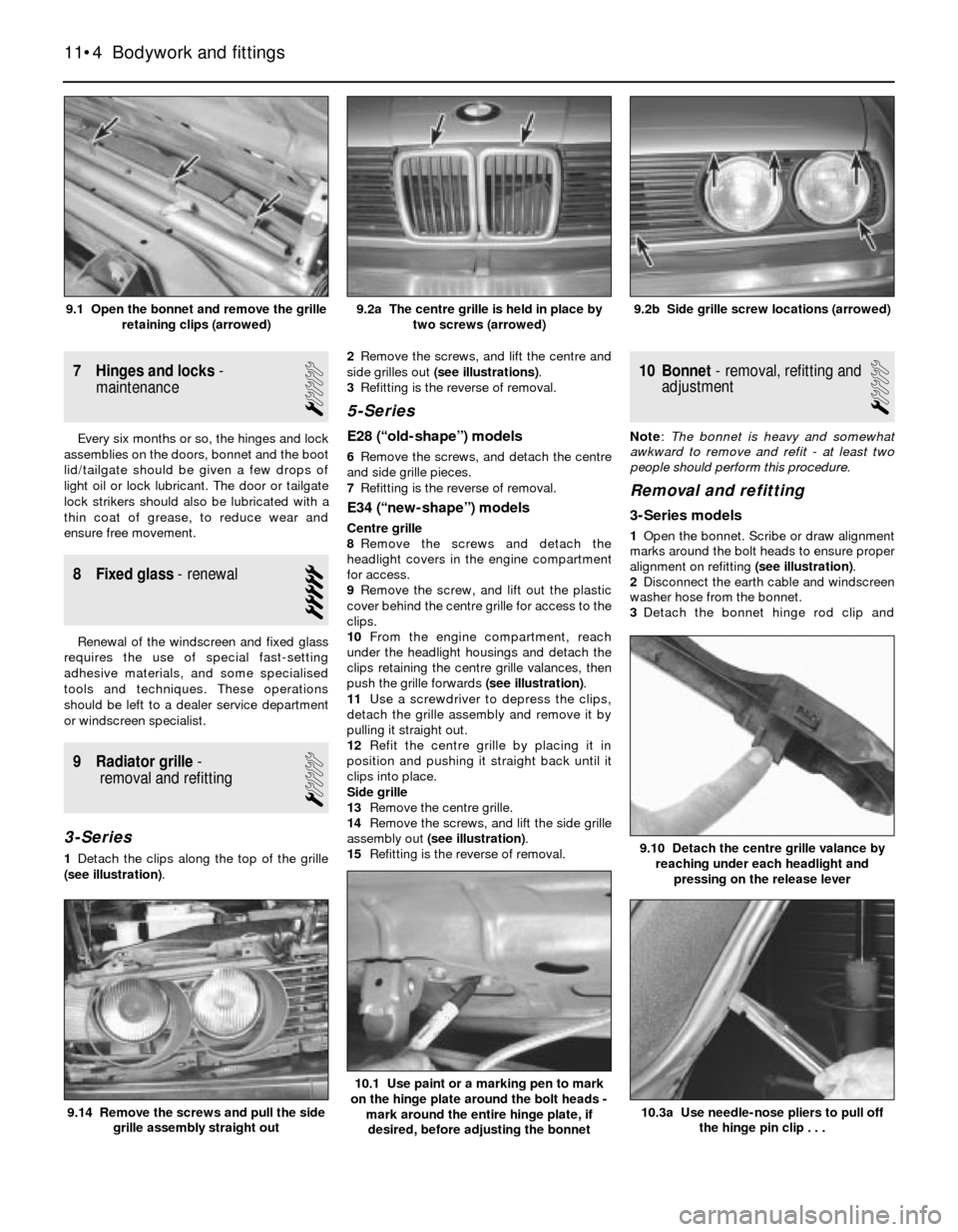
7 Hinges and locks-
maintenance
1
Every six months or so, the hinges and lock
assemblies on the doors, bonnet and the boot
lid/tailgate should be given a few drops of
light oil or lock lubricant. The door or tailgate
lock strikers should also be lubricated with a
thin coat of grease, to reduce wear and
ensure free movement.
8 Fixed glass- renewal
5
Renewal of the windscreen and fixed glass
requires the use of special fast-setting
adhesive materials, and some specialised
tools and techniques. These operations
should be left to a dealer service department
or windscreen specialist.
9 Radiator grille-
removal and refitting
1
3-Series
1Detach the clips along the top of the grille
(see illustration).2Remove the screws, and lift the centre and
side grilles out (see illustrations).
3Refitting is the reverse of removal.
5-Series
E28 (“old-shape”) models
6Remove the screws, and detach the centre
and side grille pieces.
7Refitting is the reverse of removal.
E34 (“new-shape”) models
Centre grille
8Remove the screws and detach the
headlight covers in the engine compartment
for access.
9Remove the screw, and lift out the plastic
cover behind the centre grille for access to the
clips.
10From the engine compartment, reach
under the headlight housings and detach the
clips retaining the centre grille valances, then
push the grille forwards (see illustration).
11Use a screwdriver to depress the clips,
detach the grille assembly and remove it by
pulling it straight out.
12Refit the centre grille by placing it in
position and pushing it straight back until it
clips into place.
Side grille
13Remove the centre grille.
14Remove the screws, and lift the side grille
assembly out (see illustration).
15Refitting is the reverse of removal.
10 Bonnet- removal, refitting and
adjustment
1
Note: The bonnet is heavy and somewhat
awkward to remove and refit - at least two
people should perform this procedure.
Removal and refitting
3-Series models
1Open the bonnet. Scribe or draw alignment
marks around the bolt heads to ensure proper
alignment on refitting (see illustration).
2Disconnect the earth cable and windscreen
washer hose from the bonnet.
3Detach the bonnet hinge rod clip and
11•4 Bodywork and fittings
10.3a Use needle-nose pliers to pull off
the hinge pin clip . . .
10.1 Use paint or a marking pen to mark
on the hinge plate around the bolt heads -
mark around the entire hinge plate, if
desired, before adjusting the bonnet
9.14 Remove the screws and pull the side
grille assembly straight out
9.10 Detach the centre grille valance by
reaching under each headlight and
pressing on the release lever
9.2b Side grille screw locations (arrowed)9.2a The centre grille is held in place by
two screws (arrowed)9.1 Open the bonnet and remove the grille
retaining clips (arrowed)
Page 165 of 228
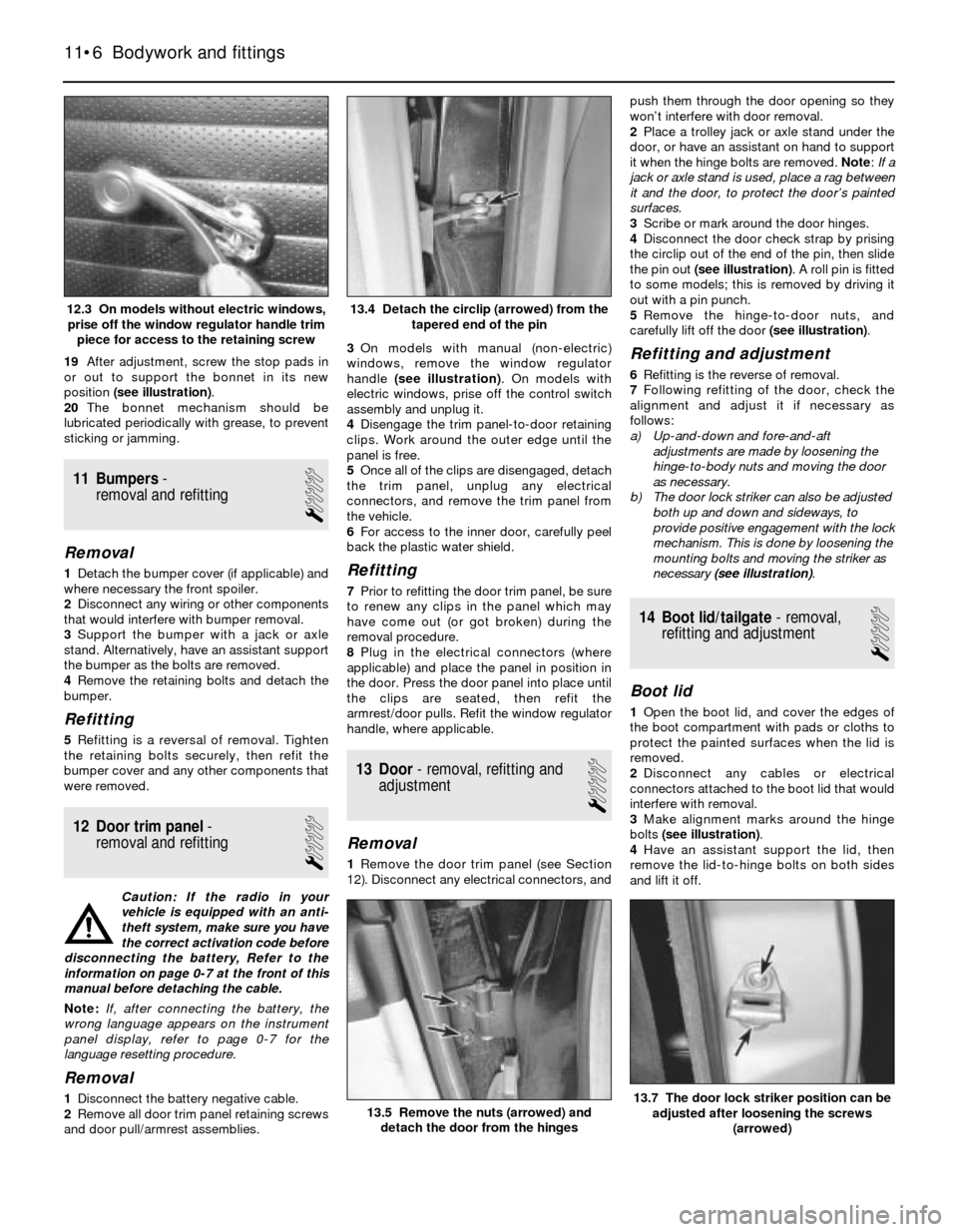
19After adjustment, screw the stop pads in
or out to support the bonnet in its new
position (see illustration).
20The bonnet mechanism should be
lubricated periodically with grease, to prevent
sticking or jamming.
11 Bumpers-
removal and refitting
1
Removal
1Detach the bumper cover (if applicable) and
where necessary the front spoiler.
2Disconnect any wiring or other components
that would interfere with bumper removal.
3Support the bumper with a jack or axle
stand. Alternatively, have an assistant support
the bumper as the bolts are removed.
4Remove the retaining bolts and detach the
bumper.
Refitting
5Refitting is a reversal of removal. Tighten
the retaining bolts securely, then refit the
bumper cover and any other components that
were removed.
12 Door trim panel-
removal and refitting
1
Caution: If the radio in your
vehicle is equipped with an anti-
theft system, make sure you have
the correct activation code before
disconnecting the battery, Refer to the
information on page 0-7 at the front of this
manual before detaching the cable.
Note: If, after connecting the battery, the
wrong language appears on the instrument
panel display, refer to page 0-7 for the
language resetting procedure.
Removal
1Disconnect the battery negative cable.
2Remove all door trim panel retaining screws
and door pull/armrest assemblies.3On models with manual (non-electric)
windows, remove the window regulator
handle (see illustration). On models with
electric windows, prise off the control switch
assembly and unplug it.
4Disengage the trim panel-to-door retaining
clips. Work around the outer edge until the
panel is free.
5Once all of the clips are disengaged, detach
the trim panel, unplug any electrical
connectors, and remove the trim panel from
the vehicle.
6For access to the inner door, carefully peel
back the plastic water shield.
Refitting
7Prior to refitting the door trim panel, be sure
to renew any clips in the panel which may
have come out (or got broken) during the
removal procedure.
8Plug in the electrical connectors (where
applicable) and place the panel in position in
the door. Press the door panel into place until
the clips are seated, then refit the
armrest/door pulls. Refit the window regulator
handle, where applicable.
13 Door- removal, refitting and
adjustment
1
Removal
1Remove the door trim panel (see Section
12). Disconnect any electrical connectors, andpush them through the door opening so they
won’t interfere with door removal.
2Place a trolley jack or axle stand under the
door, or have an assistant on hand to support
it when the hinge bolts are removed. Note: If a
jack or axle stand is used, place a rag between
it and the door, to protect the door’s painted
surfaces.
3Scribe or mark around the door hinges.
4Disconnect the door check strap by prising
the circlip out of the end of the pin, then slide
the pin out (see illustration). A roll pin is fitted
to some models; this is removed by driving it
out with a pin punch.
5Remove the hinge-to-door nuts, and
carefully lift off the door (see illustration).
Refitting and adjustment
6Refitting is the reverse of removal.
7Following refitting of the door, check the
alignment and adjust it if necessary as
follows:
a) Up-and-down and fore-and-aft
adjustments are made by loosening the
hinge-to-body nuts and moving the door
as necessary.
b) The door lock striker can also be adjusted
both up and down and sideways, to
provide positive engagement with the lock
mechanism. This is done by loosening the
mounting bolts and moving the striker as
necessary (see illustration).
14 Boot lid/tailgate- removal,
refitting and adjustment
1
Boot lid
1Open the boot lid, and cover the edges of
the boot compartment with pads or cloths to
protect the painted surfaces when the lid is
removed.
2Disconnect any cables or electrical
connectors attached to the boot lid that would
interfere with removal.
3Make alignment marks around the hinge
bolts (see illustration).
4Have an assistant support the lid, then
remove the lid-to-hinge bolts on both sides
and lift it off.
11•6 Bodywork and fittings
13.7 The door lock striker position can be
adjusted after loosening the screws
(arrowed)13.5 Remove the nuts (arrowed) and
detach the door from the hinges
13.4 Detach the circlip (arrowed) from the
tapered end of the pin12.3 On models without electric windows,
prise off the window regulator handle trim
piece for access to the retaining screw
Page 166 of 228
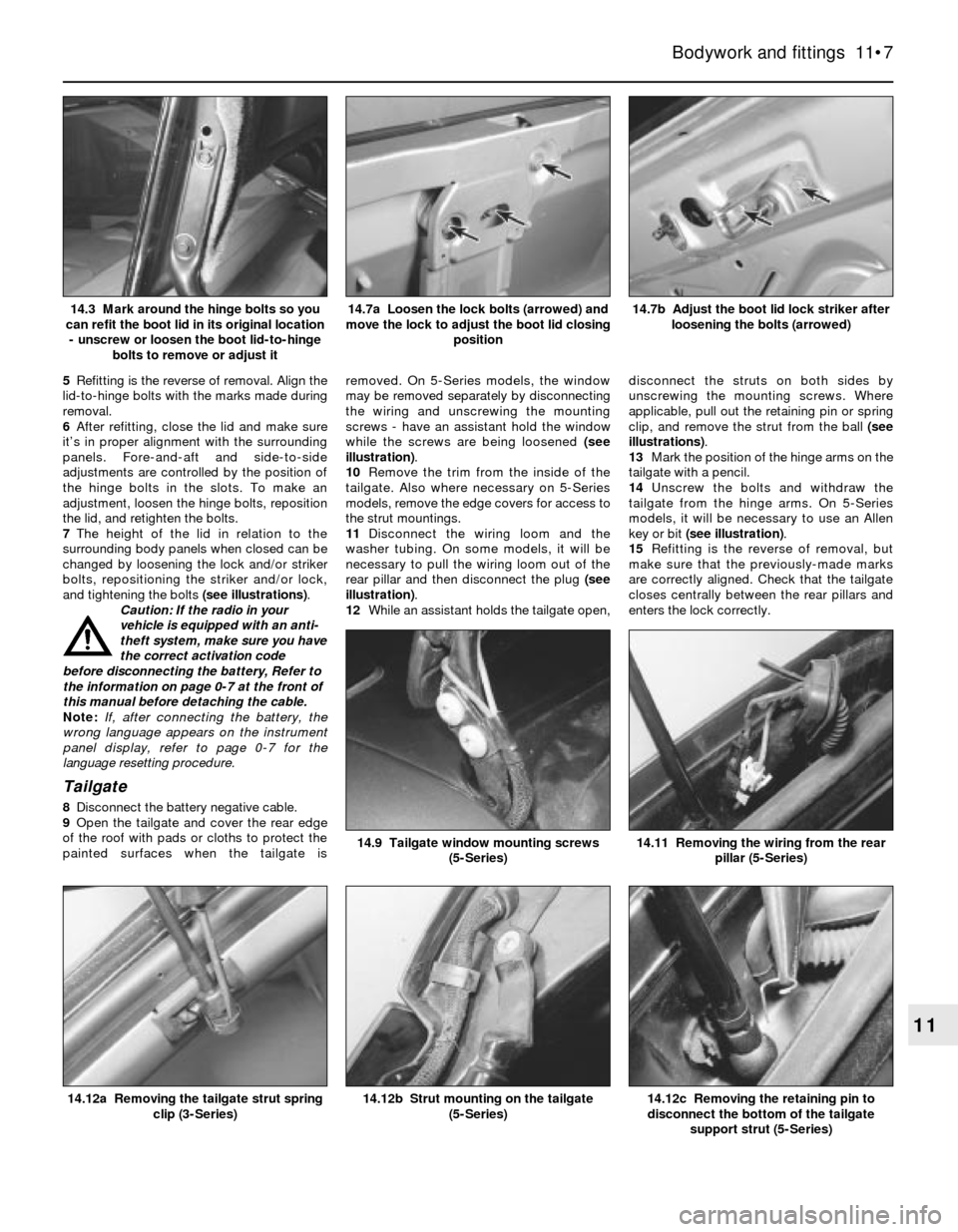
5Refitting is the reverse of removal. Align the
lid-to-hinge bolts with the marks made during
removal.
6After refitting, close the lid and make sure
it’s in proper alignment with the surrounding
panels. Fore-and-aft and side-to-side
adjustments are controlled by the position of
the hinge bolts in the slots. To make an
adjustment, loosen the hinge bolts, reposition
the lid, and retighten the bolts.
7The height of the lid in relation to the
surrounding body panels when closed can be
changed by loosening the lock and/or striker
bolts, repositioning the striker and/or lock,
and tightening the bolts (see illustrations).
Caution: If the radio in your
vehicle is equipped with an anti-
theft system, make sure you have
the correct activation code
before disconnecting the battery, Refer to
the information on page 0-7 at the front of
this manual before detaching the cable.
Note: If, after connecting the battery, the
wrong language appears on the instrument
panel display, refer to page 0-7 for the
language resetting procedure.
Tailgate
8Disconnect the battery negative cable.
9Open the tailgate and cover the rear edge
of the roof with pads or cloths to protect the
painted surfaces when the tailgate isremoved. On 5-Series models, the window
may be removed separately by disconnecting
the wiring and unscrewing the mounting
screws - have an assistant hold the window
while the screws are being loosened (see
illustration).
10Remove the trim from the inside of the
tailgate. Also where necessary on 5-Series
models, remove the edge covers for access to
the strut mountings.
11Disconnect the wiring loom and the
washer tubing. On some models, it will be
necessary to pull the wiring loom out of the
rear pillar and then disconnect the plug (see
illustration).
12While an assistant holds the tailgate open,disconnect the struts on both sides by
unscrewing the mounting screws. Where
applicable, pull out the retaining pin or spring
clip, and remove the strut from the ball (see
illustrations).
13Mark the position of the hinge arms on the
tailgate with a pencil.
14Unscrew the bolts and withdraw the
tailgate from the hinge arms. On 5-Series
models, it will be necessary to use an Allen
key or bit (see illustration).
15Refitting is the reverse of removal, but
make sure that the previously-made marks
are correctly aligned. Check that the tailgate
closes centrally between the rear pillars and
enters the lock correctly.
Bodywork and fittings 11•7
14.7b Adjust the boot lid lock striker after
loosening the bolts (arrowed)14.7a Loosen the lock bolts (arrowed) and
move the lock to adjust the boot lid closing
position14.3 Mark around the hinge bolts so you
can refit the boot lid in its original location
- unscrew or loosen the boot lid-to-hinge
bolts to remove or adjust it
14.12c Removing the retaining pin to
disconnect the bottom of the tailgate
support strut (5-Series)14.12b Strut mounting on the tailgate
(5-Series)14.12a Removing the tailgate strut spring
clip (3-Series)
14.11 Removing the wiring from the rear
pillar (5-Series)14.9 Tailgate window mounting screws
(5-Series)
11
Page 172 of 228
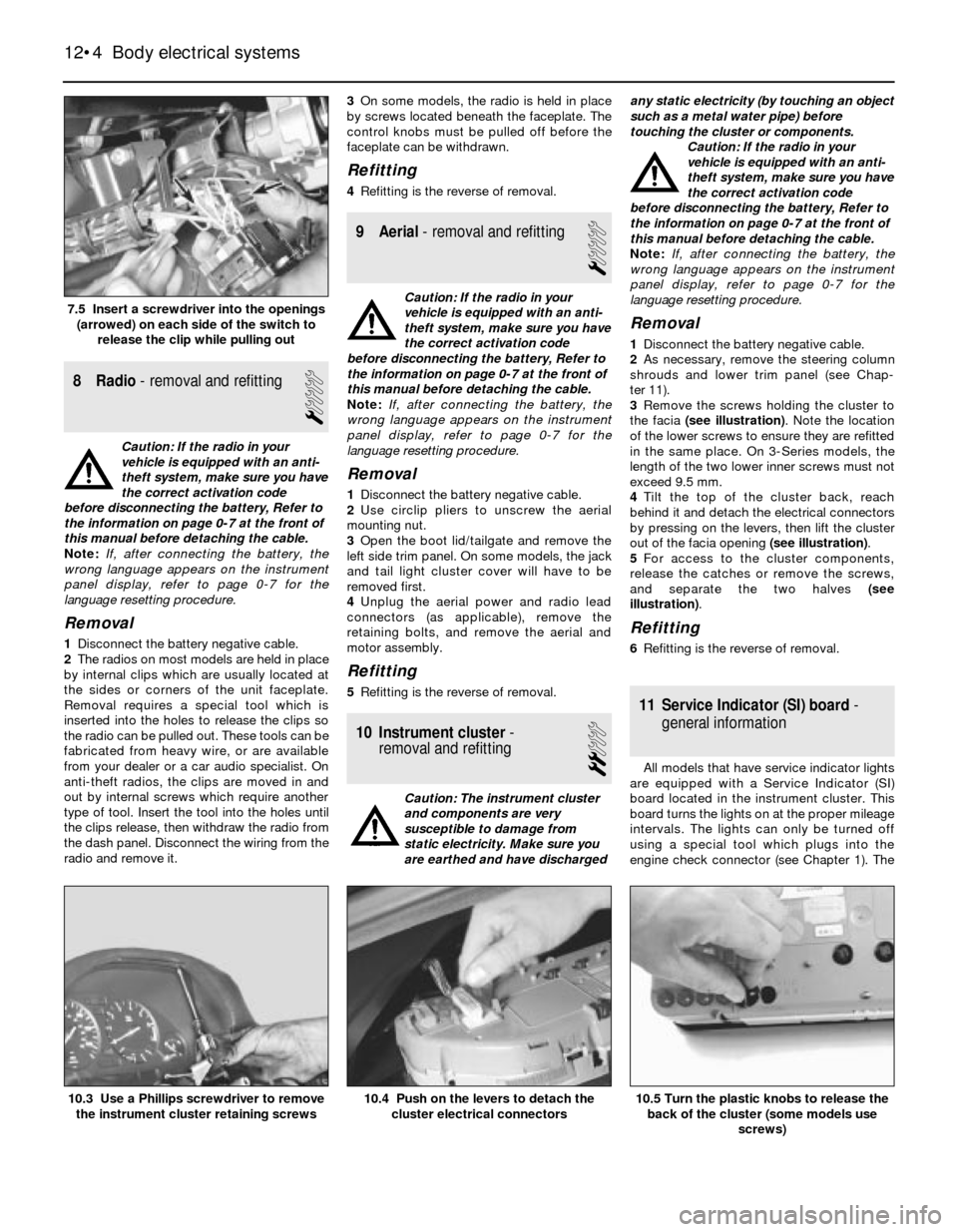
8 Radio- removal and refitting
1
Caution: If the radio in your
vehicle is equipped with an anti-
theft system, make sure you have
the correct activation code
before disconnecting the battery, Refer to
the information on page 0-7 at the front of
this manual before detaching the cable.
Note: If, after connecting the battery, the
wrong language appears on the instrument
panel display, refer to page 0-7 for the
language resetting procedure.
Removal
1Disconnect the battery negative cable.
2The radios on most models are held in place
by internal clips which are usually located at
the sides or corners of the unit faceplate.
Removal requires a special tool which is
inserted into the holes to release the clips so
the radio can be pulled out. These tools can be
fabricated from heavy wire, or are available
from your dealer or a car audio specialist. On
anti-theft radios, the clips are moved in and
out by internal screws which require another
type of tool. Insert the tool into the holes until
the clips release, then withdraw the radio from
the dash panel. Disconnect the wiring from the
radio and remove it.3On some models, the radio is held in place
by screws located beneath the faceplate. The
control knobs must be pulled off before the
faceplate can be withdrawn.
Refitting
4Refitting is the reverse of removal.
9 Aerial- removal and refitting
1
Caution: If the radio in your
vehicle is equipped with an anti-
theft system, make sure you have
the correct activation code
before disconnecting the battery, Refer to
the information on page 0-7 at the front of
this manual before detaching the cable.
Note: If, after connecting the battery, the
wrong language appears on the instrument
panel display, refer to page 0-7 for the
language resetting procedure.
Removal
1Disconnect the battery negative cable.
2Use circlip pliers to unscrew the aerial
mounting nut.
3Open the boot lid/tailgate and remove the
left side trim panel. On some models, the jack
and tail light cluster cover will have to be
removed first.
4Unplug the aerial power and radio lead
connectors (as applicable), remove the
retaining bolts, and remove the aerial and
motor assembly.
Refitting
5Refitting is the reverse of removal.
10 Instrument cluster-
removal and refitting
2
Caution: The instrument cluster
and components are very
susceptible to damage from
static electricity. Make sure you
are earthed and have dischargedany static electricity (by touching an object
such as a metal water pipe) before
touching the cluster or components.
Caution: If the radio in your
vehicle is equipped with an anti-
theft system, make sure you have
the correct activation code
before disconnecting the battery, Refer to
the information on page 0-7 at the front of
this manual before detaching the cable.
Note: If, after connecting the battery, the
wrong language appears on the instrument
panel display, refer to page 0-7 for the
language resetting procedure.
Removal
1Disconnect the battery negative cable.
2As necessary, remove the steering column
shrouds and lower trim panel (see Chap-
ter 11).
3Remove the screws holding the cluster to
the facia (see illustration). Note the location
of the lower screws to ensure they are refitted
in the same place. On 3-Series models, the
length of the two lower inner screws must not
exceed 9.5 mm.
4Tilt the top of the cluster back, reach
behind it and detach the electrical connectors
by pressing on the levers, then lift the cluster
out of the facia opening (see illustration).
5For access to the cluster components,
release the catches or remove the screws,
and separate the two halves (see
illustration).
Refitting
6Refitting is the reverse of removal.
11 Service Indicator (SI) board-
general information
All models that have service indicator lights
are equipped with a Service Indicator (SI)
board located in the instrument cluster. This
board turns the lights on at the proper mileage
intervals. The lights can only be turned off
using a special tool which plugs into the
engine check connector (see Chapter 1). The
12•4 Body electrical systems
10.5 Turn the plastic knobs to release the
back of the cluster (some models use
screws)10.4 Push on the levers to detach the
cluster electrical connectors10.3 Use a Phillips screwdriver to remove
the instrument cluster retaining screws
7.5 Insert a screwdriver into the openings
(arrowed) on each side of the switch to
release the clip while pulling out
Page 218 of 228
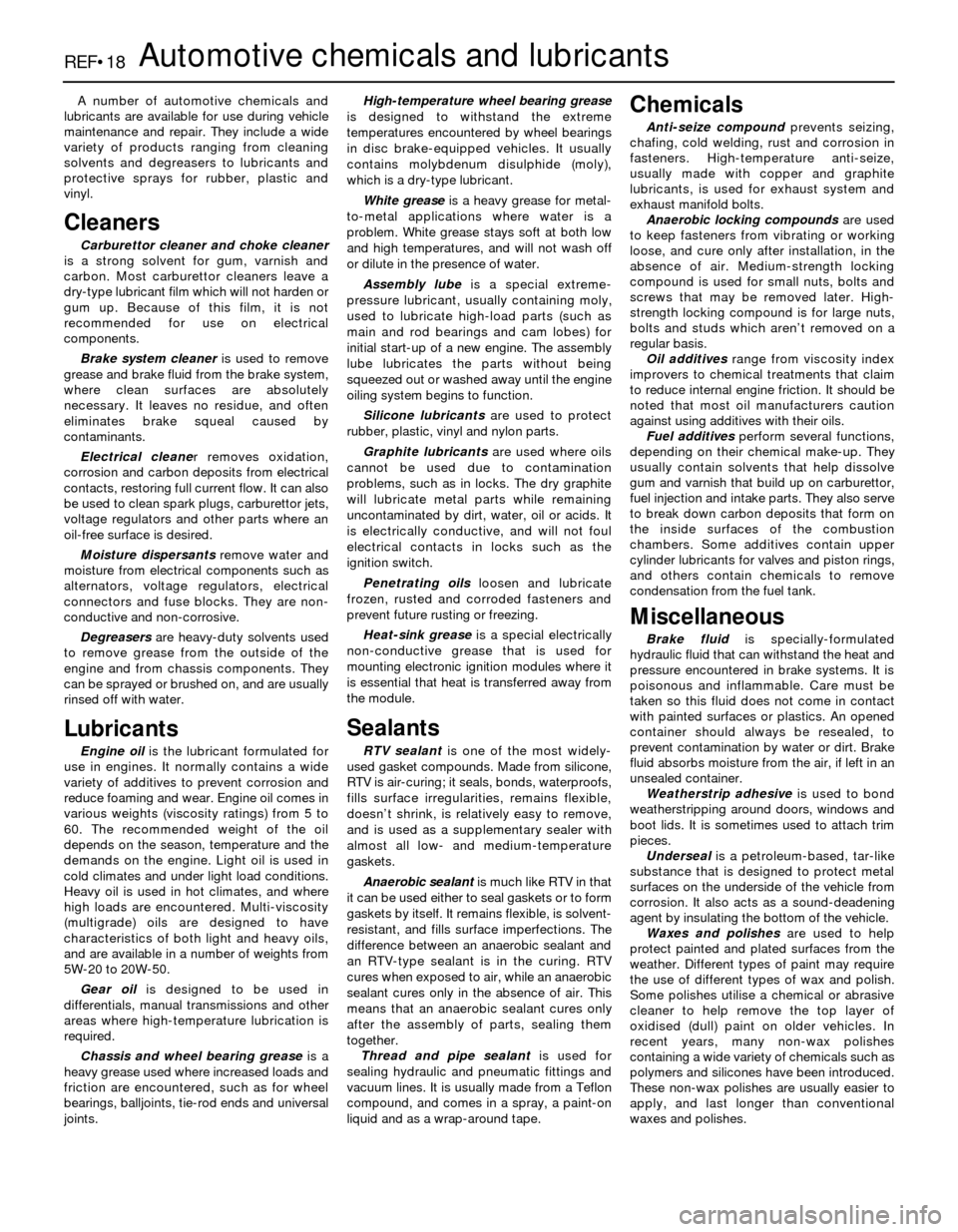
REF•18Automotive chemicals and lubricants
A number of automotive chemicals and
lubricants are available for use during vehicle
maintenance and repair. They include a wide
variety of products ranging from cleaning
solvents and degreasers to lubricants and
protective sprays for rubber, plastic and
vinyl.
Cleaners
Carburettor cleaner and choke cleaner
is a strong solvent for gum, varnish and
carbon. Most carburettor cleaners leave a
dry-type lubricant film which will not harden or
gum up. Because of this film, it is not
recommended for use on electrical
components.
Brake system cleaneris used to remove
grease and brake fluid from the brake system,
where clean surfaces are absolutely
necessary. It leaves no residue, and often
eliminates brake squeal caused by
contaminants.
Electrical cleaner removes oxidation,
corrosion and carbon deposits from electrical
contacts, restoring full current flow. It can also
be used to clean spark plugs, carburettor jets,
voltage regulators and other parts where an
oil-free surface is desired.
Moisture dispersantsremove water and
moisture from electrical components such as
alternators, voltage regulators, electrical
connectors and fuse blocks. They are non-
conductive and non-corrosive.
Degreasersare heavy-duty solvents used
to remove grease from the outside of the
engine and from chassis components. They
can be sprayed or brushed on, and are usually
rinsed off with water.
Lubricants
Engine oilis the lubricant formulated for
use in engines. It normally contains a wide
variety of additives to prevent corrosion and
reduce foaming and wear. Engine oil comes in
various weights (viscosity ratings) from 5 to
60. The recommended weight of the oil
depends on the season, temperature and the
demands on the engine. Light oil is used in
cold climates and under light load conditions.
Heavy oil is used in hot climates, and where
high loads are encountered. Multi-viscosity
(multigrade) oils are designed to have
characteristics of both light and heavy oils,
and are available in a number of weights from
5W-20 to 20W-50.
Gear oilis designed to be used in
differentials, manual transmissions and other
areas where high-temperature lubrication is
required.
Chassis and wheel bearing greaseis a
heavy grease used where increased loads and
friction are encountered, such as for wheel
bearings, balljoints, tie-rod ends and universal
joints.High-temperature wheel bearing grease
is designed to withstand the extreme
temperatures encountered by wheel bearings
in disc brake-equipped vehicles. It usually
contains molybdenum disulphide (moly),
which is a dry-type lubricant.
White greaseis a heavy grease for metal-
to-metal applications where water is a
problem. White grease stays soft at both low
and high temperatures, and will not wash off
or dilute in the presence of water.
Assembly lubeis a special extreme-
pressure lubricant, usually containing moly,
used to lubricate high-load parts (such as
main and rod bearings and cam lobes) for
initial start-up of a new engine. The assembly
lube lubricates the parts without being
squeezed out or washed away until the engine
oiling system begins to function.
Silicone lubricants are used to protect
rubber, plastic, vinyl and nylon parts.
Graphite lubricantsare used where oils
cannot be used due to contamination
problems, such as in locks. The dry graphite
will lubricate metal parts while remaining
uncontaminated by dirt, water, oil or acids. It
is electrically conductive, and will not foul
electrical contacts in locks such as the
ignition switch.
Penetrating oilsloosen and lubricate
frozen, rusted and corroded fasteners and
prevent future rusting or freezing.
Heat-sink greaseis a special electrically
non-conductive grease that is used for
mounting electronic ignition modules where it
is essential that heat is transferred away from
the module.
Sealants
RTV sealantis one of the most widely-
used gasket compounds. Made from silicone,
RTV is air-curing; it seals, bonds, waterproofs,
fills surface irregularities, remains flexible,
doesn’t shrink, is relatively easy to remove,
and is used as a supplementary sealer with
almost all low- and medium-temperature
gaskets.
Anaerobic sealantis much like RTV in that
it can be used either to seal gaskets or to form
gaskets by itself. It remains flexible, is solvent-
resistant, and fills surface imperfections. The
difference between an anaerobic sealant and
an RTV-type sealant is in the curing. RTV
cures when exposed to air, while an anaerobic
sealant cures only in the absence of air. This
means that an anaerobic sealant cures only
after the assembly of parts, sealing them
together.
Thread and pipe sealant is used for
sealing hydraulic and pneumatic fittings and
vacuum lines. It is usually made from a Teflon
compound, and comes in a spray, a paint-on
liquid and as a wrap-around tape.
Chemicals
Anti-seize compoundprevents seizing,
chafing, cold welding, rust and corrosion in
fasteners. High-temperature anti-seize,
usually made with copper and graphite
lubricants, is used for exhaust system and
exhaust manifold bolts.
Anaerobic locking compoundsare used
to keep fasteners from vibrating or working
loose, and cure only after installation, in the
absence of air. Medium-strength locking
compound is used for small nuts, bolts and
screws that may be removed later. High-
strength locking compound is for large nuts,
bolts and studs which aren’t removed on a
regular basis.
Oil additivesrange from viscosity index
improvers to chemical treatments that claim
to reduce internal engine friction. It should be
noted that most oil manufacturers caution
against using additives with their oils.
Fuel additivesperform several functions,
depending on their chemical make-up. They
usually contain solvents that help dissolve
gum and varnish that build up on carburettor,
fuel injection and intake parts. They also serve
to break down carbon deposits that form on
the inside surfaces of the combustion
chambers. Some additives contain upper
cylinder lubricants for valves and piston rings,
and others contain chemicals to remove
condensation from the fuel tank.
Miscellaneous
Brake fluidis specially-formulated
hydraulic fluid that can withstand the heat and
pressure encountered in brake systems. It is
poisonous and inflammable. Care must be
taken so this fluid does not come in contact
with painted surfaces or plastics. An opened
container should always be resealed, to
prevent contamination by water or dirt. Brake
fluid absorbs moisture from the air, if left in an
unsealed container.
Weatherstrip adhesiveis used to bond
weatherstripping around doors, windows and
boot lids. It is sometimes used to attach trim
pieces.
Undersealis a petroleum-based, tar-like
substance that is designed to protect metal
surfaces on the underside of the vehicle from
corrosion. It also acts as a sound-deadening
agent by insulating the bottom of the vehicle.
Waxes and polishesare used to help
protect painted and plated surfaces from the
weather. Different types of paint may require
the use of different types of wax and polish.
Some polishes utilise a chemical or abrasive
cleaner to help remove the top layer of
oxidised (dull) paint on older vehicles. In
recent years, many non-wax polishes
containing a wide variety of chemicals such as
polymers and silicones have been introduced.
These non-wax polishes are usually easier to
apply, and last longer than conventional
waxes and polishes.
Page 225 of 228
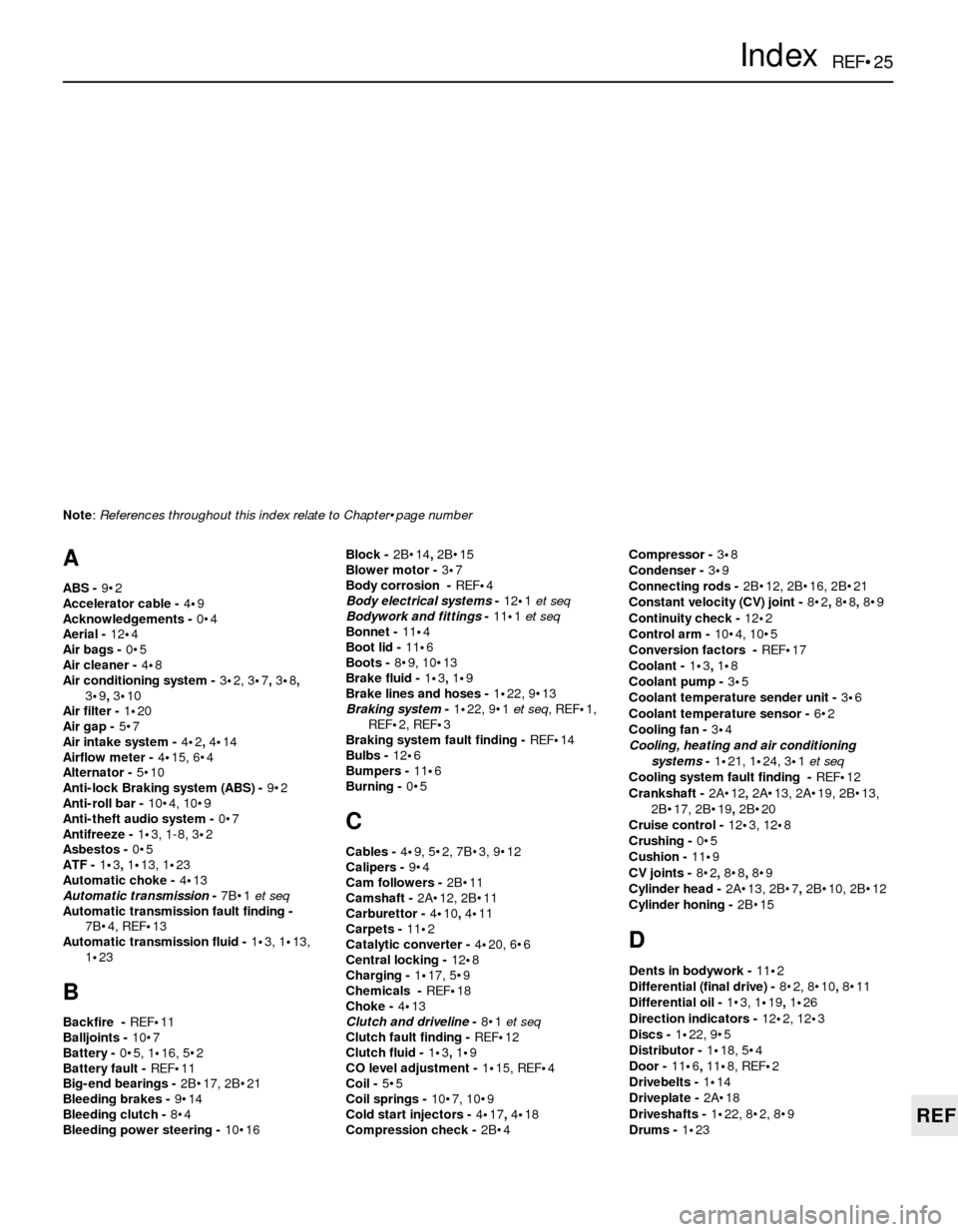
REF•25
REF
Index
Note: References throughout this index relate to Chapter•page number
A
ABS - 9•2
Accelerator cable - 4•9
Acknowledgements - 0•4
Aerial - 12•4
Air bags - 0•5
Air cleaner - 4•8
Air conditioning system - 3•2, 3•7, 3•8,
3•9, 3•10
Air filter - 1•20
Air gap - 5•7
Air intake system - 4•2, 4•14
Airflow meter - 4•15, 6•4
Alternator - 5•10
Anti-lock Braking system (ABS) - 9•2
Anti-roll bar - 10•4, 10•9
Anti-theft audio system - 0•7
Antifreeze - 1•3, 1-8, 3•2
Asbestos - 0•5
ATF - 1•3, 1•13, 1•23
Automatic choke - 4•13
Automatic transmission- 7B•1et seq
Automatic transmission fault finding -
7B•4, REF•13
Automatic transmission fluid - 1•3, 1•13,
1•23
B
Backfire - REF•11
Balljoints - 10•7
Battery - 0•5, 1•16, 5•2
Battery fault - REF•11
Big-end bearings - 2B•17, 2B•21
Bleeding brakes - 9•14
Bleeding clutch - 8•4
Bleeding power steering - 10•16Block - 2B•14, 2B•15
Blower motor - 3•7
Body corrosion - REF•4
Body electrical systems- 12•1et seq
Bodywork and fittings- 11•1et seq
Bonnet - 11•4
Boot lid - 11•6
Boots - 8•9, 10•13
Brake fluid - 1•3, 1•9
Brake lines and hoses - 1•22, 9•13
Braking system- 1•22, 9•1et seq,REF•1,
REF•2, REF•3
Braking system fault finding - REF•14
Bulbs - 12•6
Bumpers - 11•6
Burning - 0•5
C
Cables - 4•9, 5•2, 7B•3, 9•12
Calipers - 9•4
Cam followers - 2B•11
Camshaft - 2A•12, 2B•11
Carburettor - 4•10, 4•11
Carpets - 11•2
Catalytic converter - 4•20, 6•6
Central locking - 12•8
Charging - 1•17, 5•9
Chemicals - REF•18
Choke - 4•13
Clutch and driveline- 8•1et seq
Clutch fault finding - REF•12
Clutch fluid - 1•3, 1•9
CO level adjustment - 1•15, REF•4
Coil - 5•5
Coil springs - 10•7, 10•9
Cold start injectors - 4•17, 4•18
Compression check - 2B•4Compressor - 3•8
Condenser - 3•9
Connecting rods -2B•12, 2B•16, 2B•21
Constant velocity (CV) joint - 8•2, 8•8, 8•9
Continuity check - 12•2
Control arm - 10•4, 10•5
Conversion factors - REF•17
Coolant - 1•3, 1•8
Coolant pump - 3•5
Coolant temperature sender unit - 3•6
Coolant temperature sensor - 6•2
Cooling fan - 3•4
Cooling, heating and air conditioning
systems- 1•21, 1•24, 3•1et seq
Cooling system fault finding - REF•12
Crankshaft - 2A•12, 2A•13, 2A•19, 2B•13,
2B•17, 2B•19, 2B•20
Cruise control - 12•3, 12•8
Crushing - 0•5
Cushion - 11•9
CV joints - 8•2, 8•8, 8•9
Cylinder head - 2A•13, 2B•7, 2B•10, 2B•12
Cylinder honing - 2B•15
D
Dents in bodywork - 11•2
Differential (final drive) - 8•2, 8•10, 8•11
Differential oil -1•3, 1•19, 1•26
Direction indicators - 12•2, 12•3
Discs - 1•22, 9•5
Distributor - 1•18, 5•4
Door - 11•6, 11•8, REF•2
Drivebelts - 1•14
Driveplate - 2A•18
Driveshafts - 1•22, 8•2, 8•9
Drums - 1•23