Code 21 BMW 328i 1998 E36 Owner's Manual
[x] Cancel search | Manufacturer: BMW, Model Year: 1998, Model line: 328i, Model: BMW 328i 1998 E36Pages: 759
Page 111 of 759
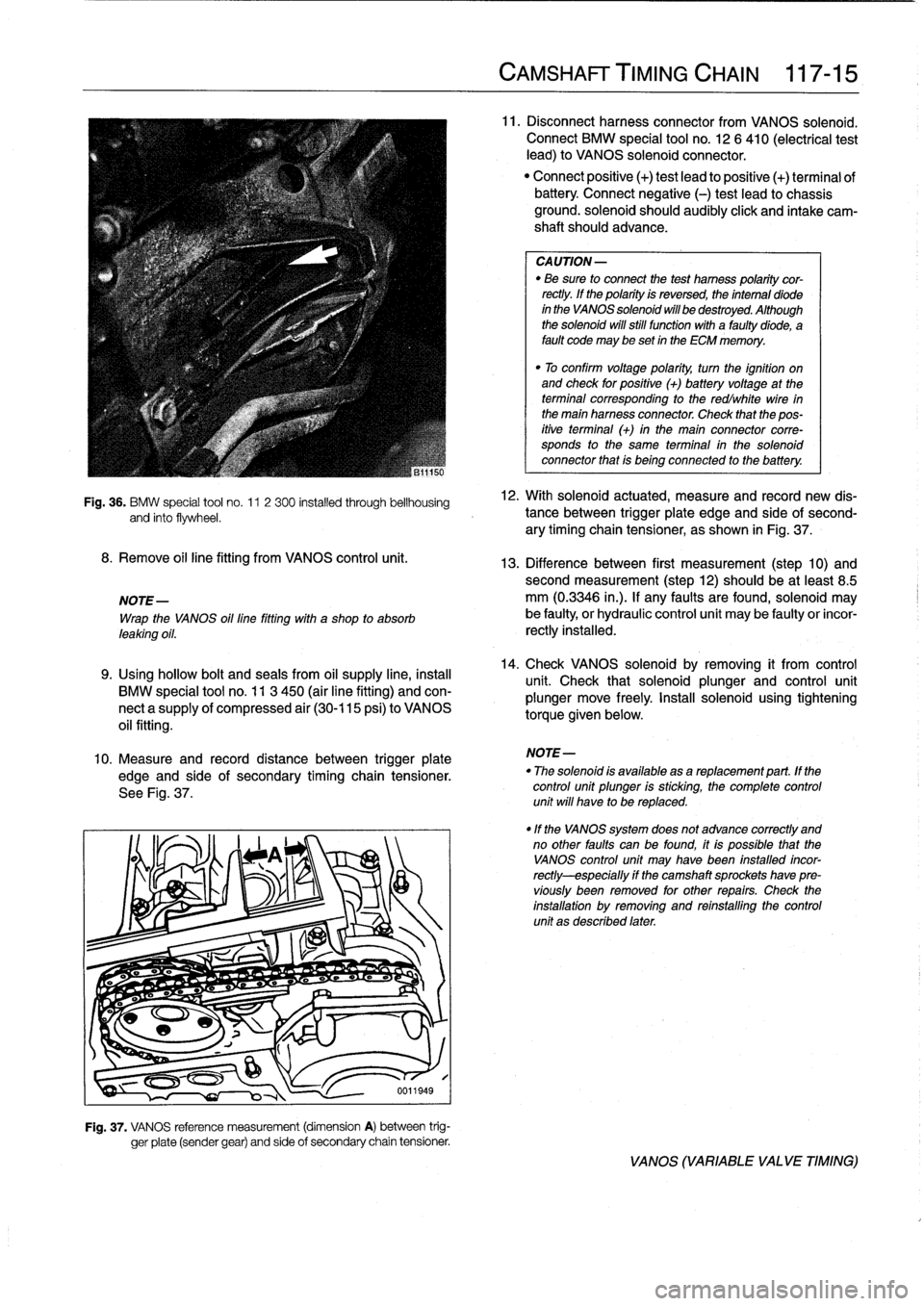
Fig
.
36
.
BMW
special
tool
no
.
11
2
300
installed
through
bellhousing
and
finto
flywheel
.
8
.
Remove
oil
line
fitting
from
VANOS
control
unit
.
NOTE-
Wrap
the
VANOS
oil
line
fitting
with
a
shop
to
absorb
leaking
oil
.
9
.
Using
hollow
bolt
and
seals
from
oil
supply
line,
instan
BMW
special
tool
no
.
11
3
450
(air
line
fitting)
and
con-
nect
a
supply
of
compressed
air
(30-115
psi)
to
VANOS
oil
fitting
.
10
.
Measure
and
record
distance
between
trigger
plate
edge
and
side
of
secondary
timing
chain
tensioner
.
See
Fig
.
37
.
Fig
.
37
.
VANOS
reference
measurement
(dimension
A)
between
trig-
ger
píate
(sender
gear)
and
side
of
secondary
chain
tensioner
.
CAMSHAFT
TIMING
CHAIN
117-
1
5
11
.
Disconnectharness
connector
from
VANOS
solenoid
.
Connect
BMW
special
tool
no
.
12
6
410
(electrical
test
lead)
to
VANOS
solenoid
connector
.
"
Connect
positive
(+)
test
lead
to
positive
(+)
terminal
ofbattery
Connect
negative
(-)
test
leadto
chassis
ground
.
solenoid
should
audibly
click
and
intake
cam-
shaft
should
advance
.
CA
UTION-
"
Be
sure
to
connect
the
test
hamess
polaritycor-
rectly
.
lf
the
polarity
is
reversed,
the
intemal
diode
in
the
VANOS
solenoid
will
be
destroyed
.
Although
the
solenoid
will
still
functionwith
a
faultydiode,
a
fault
code
may
be
set
in
the
ECM
memory
.
"
To
confirm
voltage
polarity,
turn
the
ignition
on
and
check
for
positive
(+)
batteryvoltage
at
the
terminal
corresponding
to
the
redlwhite
wire
in
the
main
harness
connector
.
Check
that
the
pos-
itive
terminal
(+)
in
the
main
connector
corre-
sponds
to
the
same
terminal
in
the
solenoid
connector
that
is
being
connected
to
the
battery
.
12
.
With
solenoid
actuated,
measure
and
record
new
dis-
tance
between
trigger
plate
edge
and
side'of
second-
ary
timing
chain
tensioner,
as
shown
in
Fig
.
37
.
13
.
Difference
between
first
measurement
(step
10)
andsecond
measurement
(step12)
should
be
at
least
8
.5
mm
(0
.3346
in
.)
.
lf
any
faults
arefound,
solenoid
may
be
faulty,
or
hydraulic
control
unit
may
be
faulty
or
incor-
rectly
installed
.
14
.
Check
VANOS
solenoid
byremoving
it
from
control
unit
.
Check
that
solenoid
plunger
and
control
unit
plunger
move
freely
.
Install
solenoid
using
tighteníng
torque
given
below
.
NOTE-
"
The
solenoid
is
available
asareplacement
part
.
lf
the
control
unit
plunger
is
sticking,
the
complete
control
unit
will
have
to
be
replaced
.
"lf
the
VANOS
system
does
not
advance
correctly
and
no
other
faults
can
be
found,
itis
possible
that
the
VANOS
control
unit
may
Nave
been
fnstalled
incor-
rectly-especially
if
the
camshaft
sprockets
have
pre-
víously
been
removed
for
other
repairs
.
Check
the
installation
by
removing
and
reinstalling
the
control
unit
as
described
later
.
VANOS
(VARIABLE
VALVE
TIMING)
Page 125 of 759
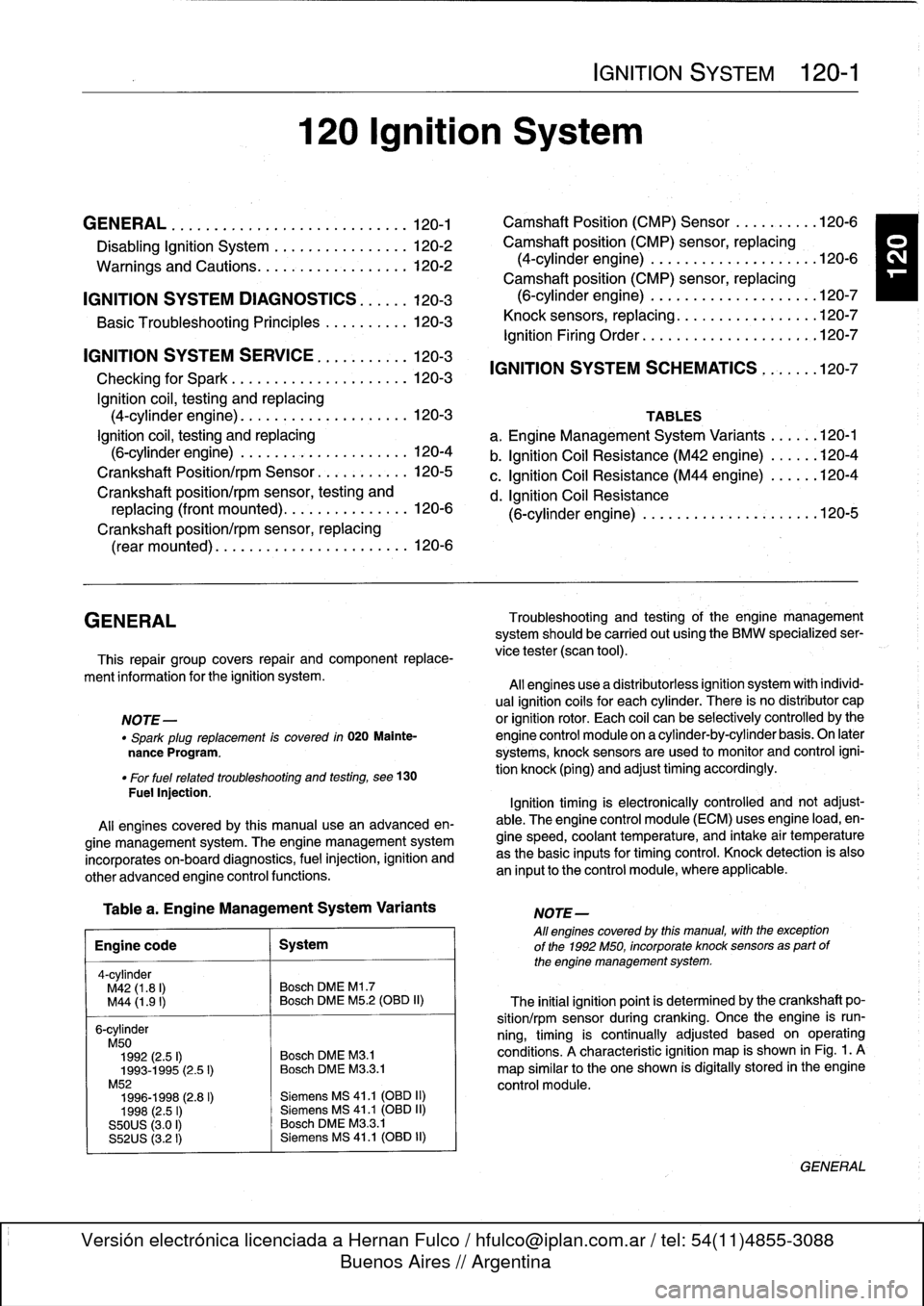
GENERAL
.
........
.
...........
.
.
.
.
.
.
.
120-1
Camshaft
Position
(CMP)
Sensor
....
.
.
.
...
120-6
Disabling
Ignition
System
.
.
.
.
.....
.
.
.
.
.
.
.
120-2
Camshaft
position
(CMP)
sensor,
replacing
Warnings
and
Cautions
.
.
.
.
.
.
.....
.
.
.
.
.
.
.
120-2
(4-cylinder
engine)
..
.
.
.
.
.
.
.
.
.
.
.
.
.
.
.
...
120-6
Camshaft
position
(CMP)
sensor,
replacing
IGNITION
SYSTEM
DIAGNOSTICS
.
.
.
.
.
.
120-3
(6-cylinder
engine)
..
.
.
.
.
.
.
.
.
.
.
.
.
.
.
.
.
.
.
120-7
Basic
Troubleshooting
Principles
...
.
.
.
.
.
.
.
120-3
Knock
sensors,
replacing
.
.
...
.
.
.
.
.
.
.
.
.
.
.
.
120-7
Ignition
Firing
Order
.....
.
...
.
.
.
.....
.
.
.
.120-7
IGNITION
SYSTEM
SERVICE
.
.........
.
120-3
Checking
for
Spark
..
.
.
.
.
.
.
.
.
.
.......
.
.
.
120-3
Ignition
coil,
testing
and
replacing
(4-cylinder
engine)
.
.
.
.
.
.
.
.
.
.
.........
.
120-3
Ignition
coil,
testing
and
replacing
(6-cylinder
engine)
.........
.
..........
120-4
Crankshaft
Positionlrpm
Sensor
.......
.
...
120-5
Crankshaft
position/rpm
sensor,
testing
and
replacing
(front
mounted)
.........
.
.
.
.
.
.
120-6
Crankshaft
position/rpm
sensor,replacing
(rear
mounted)
.....
.
.....
.
.....
.
.
.
.
.
.
120-6
GENERAL
Troubleshooting
and
testing
of
the
engine
management
system
should
be
carried
out
using
the
BMW
specialized
ser
This
repair
group
covers
repair
andcomponent
replace-
vice
tester
(scan
tool)
.
ment
information
for
the
ignition
system
.
All
engines
use
a
distributorless
ignition
system
with
indívid-
ual
ignitioncoils
for
each
cylinder
.
There
is
no
distributor
cap
NOTE-
or
ignition
rotor
.
Each
coil
can
be
selectively
controlled
by
the
"
Spark
plug
replacement
is
covered
in
020
Mainte-
engine
control
module
on
a
cylinder-by-cylinder
basis
.
On
later
nance
Program
.
systems,
knock
sensors
are
used
to
monitor
and
control
igni-
"
For
fuel
related
troubleshooting
and
testing,
see
130
tion
knock
(ping)
and
adjusttiming
accordingly
.
Fuel
lnjection
.
Ignition
timing
is
electronically
controlled
and
not
adjust-
All
engines
covered
by
this
manual
use
an
advanced
en-
able
.
The
engine
control
module
(ECM)
usesengine
load,
en-
gine
management
system
.
The
engine
management
system
gine
speed,
coolant
temperature,
and
intake
air
temperature
incorporates
on-board
diagnostics,
fuel
injection,
ignition
and
as
the
basic
inputs
for
timing
control
.
Knock
detection
is
also
other
advanced
engine
control
functions
.
an
input
to
the
control
module,
where
applicable
.
Table
a
.
Engine
Management
System
Variants
Engine
code
1
System
4-cylinder
M42
(1.8
I)
Bosch
DME
Ml
.7
M44
(1
.9
I)
Bosch
DME
M5
.2
(OBD
II)
6-cylinder
M50
1992
(2.5
I)
Bosch
DME
M8
.1
1993-1995
(2
.5
I)
Bosch
DME
M33
.1
M52
1996-1998
(2.8
I)
Siemens
MS
41
.1
(OBD
II)
1998
(2
.5
I)
Siemens
MS
41
.1
(013D
11)
S50US
(3.0
I)
Bosch
DME
M3
.3.1
S52US
(3.2
I)
Siemens
MS
41
.1
(OBD
II)
120
Ignition
System
IGNITION
SYSTEM
120-1
IGNITION
SYSTEM
SCHEMATICS
...
.
.
.
.120-7
TABLES
a
.
Engine
Management
System
Variants
......
120-1
b
.
Ignition
Coil
Resistance
(M42
engine)
......
120-4
c
.
Ignition
Coil
Resistance
(M44
engine)
......
120-4
d
.
Ignition
Coil
Resistance
(6-cylinder
engine)
..
.
.
.
.
.
.
.
.
.
.
.
.....
.
..
120-5
NOTE-
All
engines
coveredby
this
manual,
with
theexception
of
the
1992
M50,
incorporate
knocksensors
as
part
of
the
engine
management
system
.
The
initial
ignition
point
is
determined
by
the
crankshaft
po-
sition/rpm
sensor
during
cranking
.
Once
the
engine
is
run-
ning,
timing
is
continually
adjusted
based
on
operating
conditions
.
A
characteristic
ignition
map
is
shown
in
Fig
.
1
.
A
map
similar
to
the
one
shown
is
digitally
stored
in
the
engine
control
module
.
GENERAL
Page 127 of 759
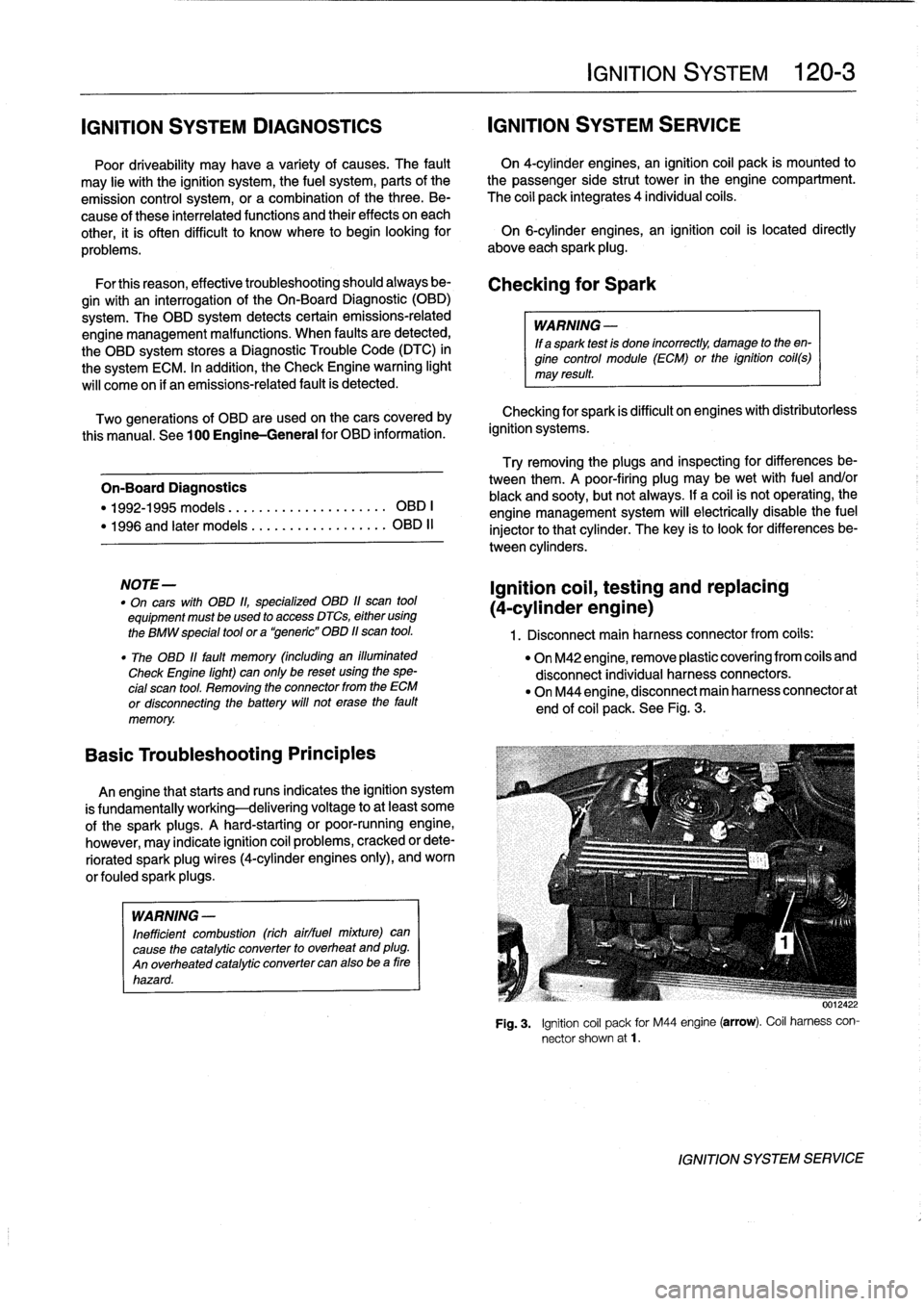
IGNITION
SYSTEM
DIAGNOSTICS
IGNITION
SYSTEM
SERVICE
Poor
driveability
may
have
a
variety
of
causes
.
The
fault
On
4-cylinder
engines,
an
ignition
coil
pack
is
mounted
to
may
lie
with
the
ignition
system,
the
fuel
system,
parts
of
the
the
passenger
side
strut
tower
in
the
engine
compartment
.
emission
control
system,
or
a
combination
of
the
three
.
Be-
The
coil
pack
integrates
4
individual
coils
.
cause
of
these
interrelated
functions
and
their
effects
oneach
other,
it
is
often
difficult
to
know
where
to
begin
looking
for
On
6-cylinder
engines,
an
ignition
coil
is
located
directly
problems
.
above
each
spark
plug
.
For
this
reason,
effective
troubleshooting
should
alwaysbe-
gin
with
an
interrogation
of
the
On-Board
Diagnostic
(OBD)
system
.
The
OBD
system
detects
certain
emissions-related
engine
management
malfunctions
.
When
faults
are
detected,
the
OBD
system
stores
a
Diagnostic
Trouble
Code
(DTC)
in
the
system
ECM
.
In
addition,
the
Check
Enginewarning
light
will
come
on
if
an
emissions-related
fault
is
detected
.
Two
generations
of
OBD
areusedon
the
cars
coveredby
this
manual
.
See
100
Engine-General
for
OBD
information
.
On-Board
Diagnostics
"
1992-1995
models
............
...
.
..
...
OBD
I
"
1996
and
later
models
.........
.......
..
OBD
II
NOTE-
"
On
carswith
OBD
ti,
specialized
OBD
11
scan
tool
equipment
mustbeused
to
access
DTCs,
either
using
the
BMW
special
tool
or
a
`generic"
OBD
11
scan
tool
.
"
The
OBD
11
fault
memory
(including
an
illuminated
Check
Engine
light)
can
only
be
reset
using
the
spe-
cial
scan
tool
.
Removing
the
connector
from
the
ECM
or
dísconnecting
the
battery
will
not
erase
the
fault
memory
.
Basic
Troubleshooting
Principies
An
engine
that
starts
and
runs
indicates
the
ignition
system
is
fundamentally
working-delivering
voltage
toat
least
some
of
the
sparkplugs
.
A
hard-starting
or
poor-running
engine,
however,
may
indicate
ignition
coil
problems,
cracked
or
dete-
riorated
spark
plug
wires
(4-cylinder
engines
only),
and
worn
or
fouled
spark
plugs
.
WARNING
-
Inefficient
combustion
(richair/fuel
mixture)
can
cause
the
catalytic
converter
to
overheat
and
plug
.
An
overheated
catalytic
converter
can
also
bea
tire
hazard
.
Checking
for
Spark
IGNITION
SYSTEM
120-
3
WARNING
-
If
a
spark
test
is
done
incorrectly,
damage
to
theen-
gine
control
module
(ECM)
or
the
ignitioncoil(s)
may
result
.
Checking
for
spark
is
difficult
onengines
with
distributorless
ignition
systems
.
Try
Rmovng
the
plugs
and
inspecting
for
differences
be-
tween
them
.
A
poor-firing
plug
may
be
wet
with
fuel
and/or
black
and
sooty,
butnot
always
.
If
a
coil
is
not
operating,
the
engine
management
system
will
electrically
disable
the
fuel
injectorto
that
cylinder
.
The
key
is
to
look
for
differences
be-
tween
cylinders
.
Ignition
coil,
testing
and
replacing
(4-cylinder
engine)
1.
Disconnect
mainharness
connector
from
coils
:
"
On
M42
engine,
remove
plastic
covering
from
coils
and
disconnect
individual
harness
connectors
.
"
On
M44
engine,
disconnect
main
harness
connectorat
end
of
coil
pack
.
See
Fig
.
3
.
Fig
.
3
.
Ignition
coil
pack
for
M44
engine
(arrow)
.
Coil
harness
con-
nector
shown
at1
.
IGNITION
SYSTEM
SERVICE
Page 129 of 759
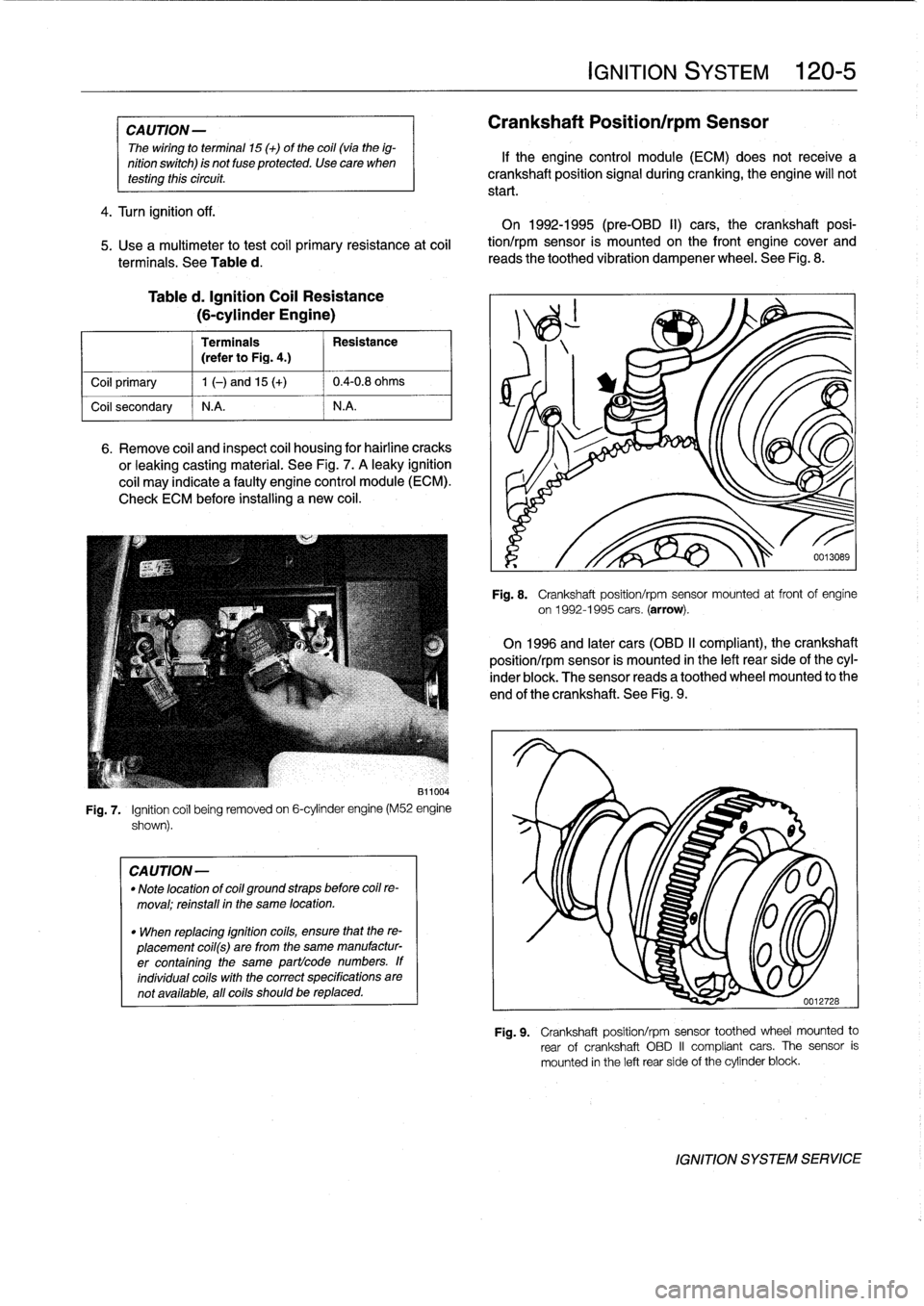
CAUTION
-
The
wiring
to
termina¡
15
(+)
of
the
coil(vía
the
ig-
nition
switch)
is
not
fuse
protected
.
Use
care
when
testíng
thiscircuit
.
4
.
Turn
ignition
off
.
5
.
Use
a
multimeter
to
test
coil
primary
resistanceat
coil
terminals
.
See
Table
d
.
Table
d
.
Ignition
Coil
Resistance
(6-cylinder
Engine)
Terminals
Resistance
(referto
Fig
.
4
.)
Coil
primary
1
1
(-)
and
15
(+)
X
0
.4-0
.8
ohms
Coil
secondary
l
N
.A
.
N
.A
.
6
.
Remove
coil
and
inspect
coil
housing
for
hairline
cracks
or
leaking
casting
material
.
See
Fig
.
7
.
A
leaky
ignition
coil
may
indícate
a
faulty
engine
control
module
(ECM)
.
Check
ECM
before
installing
a
new
coil
.
811004
Fig
.
7
.
Ignition
coil
being
removed
on
6-cylinder
engine
(M52
engine
shown)
.
CA
UTION-
"
Note
location
of
coil
ground
straps
before
coilre-
moval
;
reinstallin
the
same
location
.
"
When
replacing
ignition
coils,
ensure
that
the
re-
placement
coil(s)
are
from
the
same
manufactur-
er
containing
the
same
partlcode
numbers
.
If
individual
coils
with
the
correct
specifications
are
not
available,
all
coils
should
be
replaced
.
IGNITION
SYSTEM
120-
5
Crankshaft
Position/rpm
Sensor
If
the
engine
control
module
(ECM)
does
not
receive
a
crankshaft
position
signal
during
cranking,
the
engine
will
not
start
.
On
1992-1995(pre-OBD
II)
cars,
the
crankshaft
posi-
tion/rpm
sensor
is
mounted
on
the
front
engine
cover
and
reads
the
toothed
vibration
dampener
wheel
.
See
Fig
.
8
.
Fig
.
8
.
Crankshaft
position/rpm
sensor
mounted
at
front
of
engine
on
1992-1995
cars
.
(arrow)
.
On
1996
and
latee
cars
(OBD
II
compliant),
the
crankshaft
position/rpm
sensor
is
mounted
in
the
left
rear
side
of
the
cyl-
inderblock
.
The
sensor
reads
a
toothed
wheel
mounted
to
the
end
of
the
crankshaft
.
See
Fig
.
9
.
Fig
.
9
.
Crankshaft
position/rpm
sensor
toothed
wheel
mounted
to
rear
of
crankshaft
OBD
II
compliant
cars
.
The
sensor
is
mounted
in
the
left
rear
side
of
the
cylinder
block
.
IGNITION
SYSTEM
SERVICE
Page 131 of 759
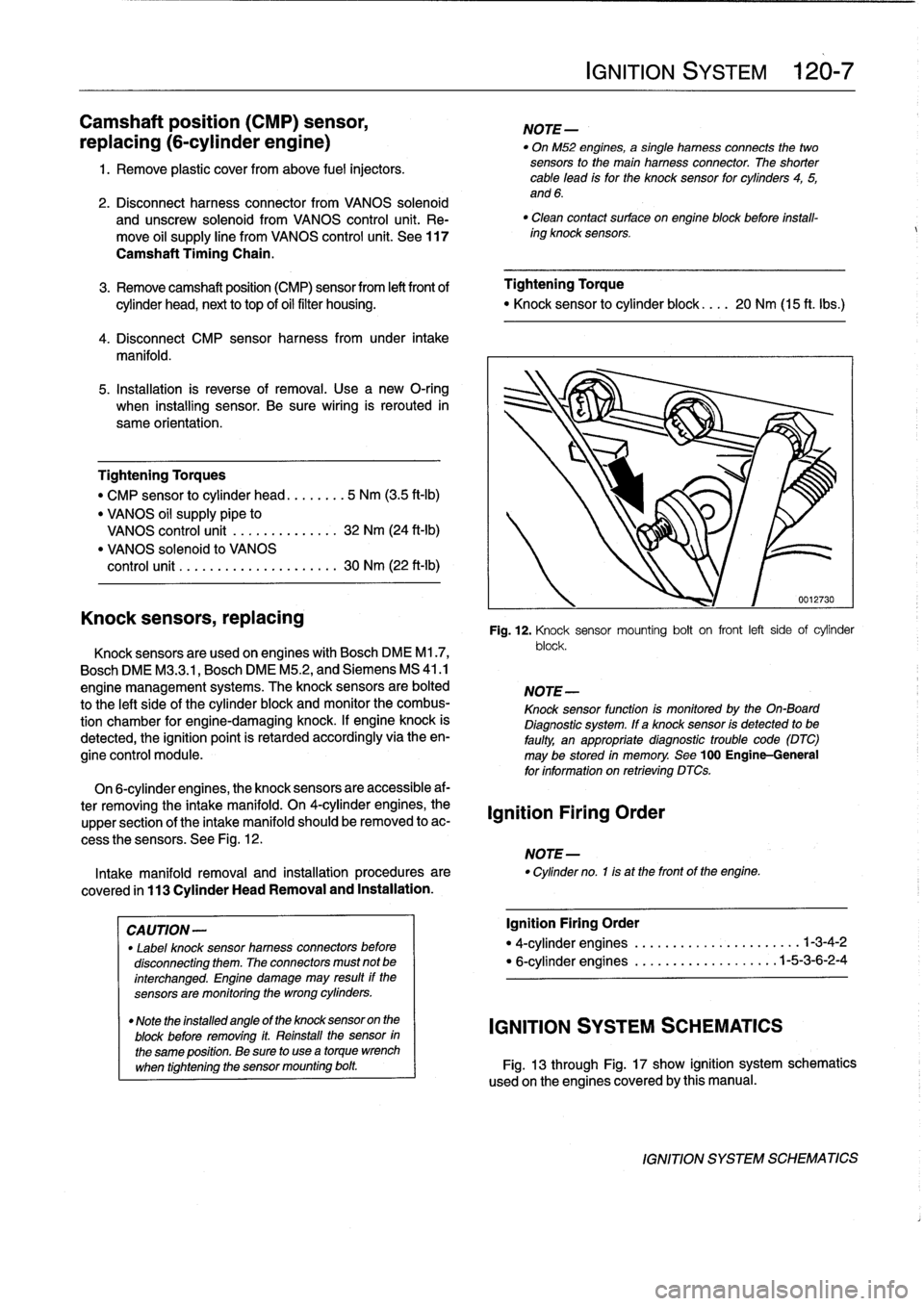
Camshaft
position
(CMP)
sensor,
replacing
(6-cylinder
engine)
1
.
Remove
plastic
cover
from
above
fuel
injectors
.
2
.
Disconnect
harness
connector
from
VANOS
solenoid
and
unscrew
solenoid
from
VANOS
control
unit
.
Re-
"
Clean
contactsurface
on
engine
block
before
fnstall
move
oil
supply
line
from
VANOS
control
unit
.
See
117
ing
knock
sensors
.
Camshaft
Timing
Chain
.
3
.
Remove
camshaft
position
(CMP)
sensor
from
left
frontof
cylinder
head,
next
to
top
of
oil
filter
housing
.
"
Knock
sensor
to
cylinder
block
....
20
Nm
(15
ft
.
lbs
.)
4
.
Disconnect
CMP
sensor
harnessfrom
under
intake
manifold
.
5
.
Installation
is
reverse
of
removal
.
Use
a
new
O-ring
when
installing
sensor
.
Be
sure
wiring
is
rerouted
in
same
orientation
.
Tightening
Torques
"
CMP
sensor
to
cylinder
head
....
.
.
..
5
Nm
(3
.5
ft-Ib)
"
VANOS
oil
supply
pipe
to
VANOS
control
unit
...........
.
..
32
Nm
(24
ft-Ib)
"
VANOS
solenoid
to
VANOS
control
unit
...
.
.................
30
Nm
(22
ft-Ib)
Knock
sensors,
replacing
Knock
sensors
are
usedon
engines
with
Bosch
DME
M1
.7,
Bosch
DME
M3
.3
.1,
Bosch
DME
M5
.2,
and
Siemens
MS
41
.1
engine
management
systems
.
The
knocksensors
are
bolted
to
the
left
sideof
the
cylinder
block
and
monitor
the
combus-
tion
chamber
for
engine-damaging
knock
.
If
engine
knock
is
detected,
the
ignition
point
is
retarded
accordingly
via
the
en-
gine
control
module
.
CA
UTION-
"
Label
knock
sensorharness
connectors
before
disconnecting
them
.
The
connectors
must
not
be
interchanged
.
Engine
damage
may
result
if
the
sensors
are
monitoring
the
wrong
cytinders
.
"
Note
the
installed
angle
of
the
knock
sensoron
the
block
before
removing
it
.
Reinstall
the
sensor
in
the
same
position
.
Be
sure
to
usea
torque
wrench
when
tightening
the
sensormounting
bola
NOTE
-
"
On
M52
engines,
a
single
harness
connects
the
twosensors
to
the
main
harness
connector
.
The
shorter
cable
lead
fs
for
the
knock
sensor
for
cytinders
4,
5,
and
6
.
Tightening
Torque
IGNITION
SYSTEM
120-
7
0012730
Fig
.
12
.
Knock
sensor
mounting
bolt
on
front
left
side
of
cylinder
block
.
NOTE-
Knock
sensor
function
Is
monitoredby
the
On-Board
Diagnostic
system
.
If
a
knock
sensor
is
detected
to
be
faulty,
an
appropriatediagnostic
trouble
code
(DTC)
may
be
stored
in
memory
.
See
100
Engine-General
for
information
on
retrieving
DTCs
.
On
6-cylinder
engines,
the
knock
sensors
are
accessible
af-
ter
removing
the
intake
manifold
.
On
4-cylinder
engines,
the
upper
section
of
the
intake
manifold
should
be
removed
to
ac-
cess
the
sensors
.
See
Fig
.
12
.
NOTE-
Intakemanifold
removal
and
installation
procedures
are
"
Cylinder
no
.
1is
at
the
front
of
the
engine
.
covered
in
113
Cylinder
HeadRemoval
and
Installation
.
Ignition
Firing
Order
Ignition
Firing
Order
"
4-cylinder
engines
.....
..
...
.
..........
.1-3-4-2
"
6-cylinder
engines
...........
..
.
.
..
..
1-5-3-6-2-4
IGNITION
SYSTEM
SCHEMATICS
Fig
.
13
through
Fig
.
17
show
ignition
system
schematics
usedon
the
enginescoveredby
this
manual
.
IGNITION
SYSTEM
SCHEMATICS
Page 132 of 759
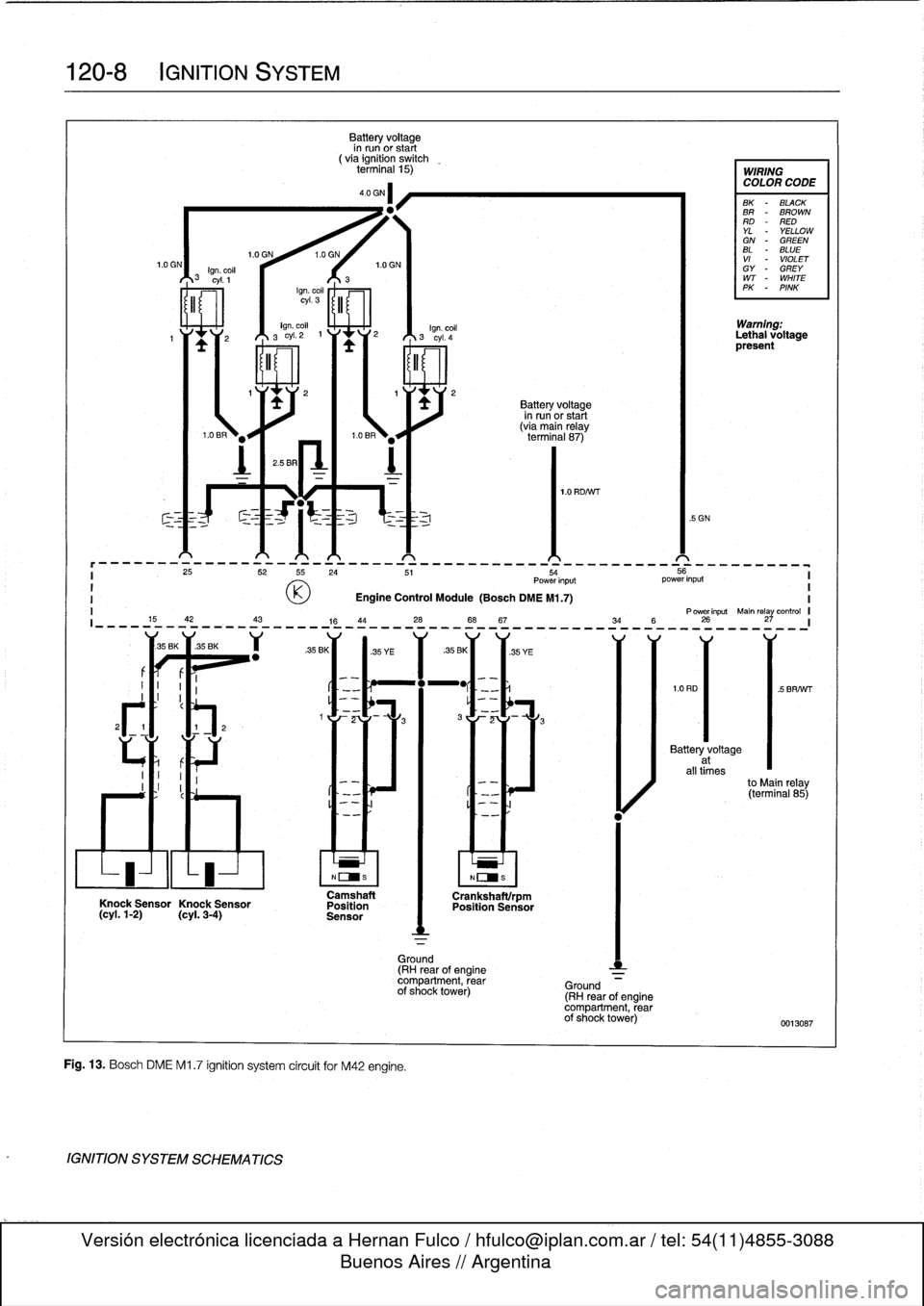
120-8
IGNITION
SYSTEM
1
1
.0
GN
1
.0
Gl
.0
GN
I
Ign
coil
1
.0
GN
.
Tti
%ti
r,
_%ti
_
_
ice_
I
25
52
5524
51
54
56
I
Power
input
power
input
t
U
Engine
Control
Module
(Bosch
DME
Ml
.7)
II
Powerinput
Mainrelaycontrol
I
15
42
43
16442868
67
34
6
26
27
1
-----
__
V
_
--
_
~
8K
.35
BK
.35
13,1
1
.35
YE
1
.35
BK35
VE
.35
3
cyl
.1
1
11
E
S
2
1
.0
BR
2
.5
BR
Ign
.
coil
cyl
.
3
II
Ign
.
coil
Ign
.
coil
3
cyI
.
2
1
Y
_
Y
2
k
3
cyl
.
4
IGNITION
SYSTEM
SCHEMATICS
Battery
voltage
in
run
or
start
(
vía
ignition
switchterminal
15)
WIRING
COLOR
CODE
4
.0
GN
1
.0
BR'V
.
Camshaft
Knock
Sensor
Knock
Sensor
Position
(cyl
.1-2)
(cyl
.3-4)
Sensor
Fig
.
13
.
Bosch
DME
M1
.7
ignition
system
circuit
for
M42
engine
.
Ground
(RH
rearof
engine
compartment,
rear
of
shock
tower)
N[INS
Crankshaftlrpm
Position
Sensor
Battery
voltage
in
run
or
start
(vía
main
relay
terminal
87)
Ground
(RH
rearof
engine
compartment,
rearof
shock
tower)
5GN
BK
-
BLACK
BR
"
BROWN
RD
-
RED
YL-
YELLOW
GN
-
GREEN
BL
-
BLUE
VI
-
VIOLET
GY
-
GREY
WT
-
WHITE
PK
-
PINK
Warning
:
Lethal
voltagepresent
Battery
voltage
at
all
times
to
Main
relay
(terminal
85)
'Y
Y
---------------------
0013087
Page 133 of 759
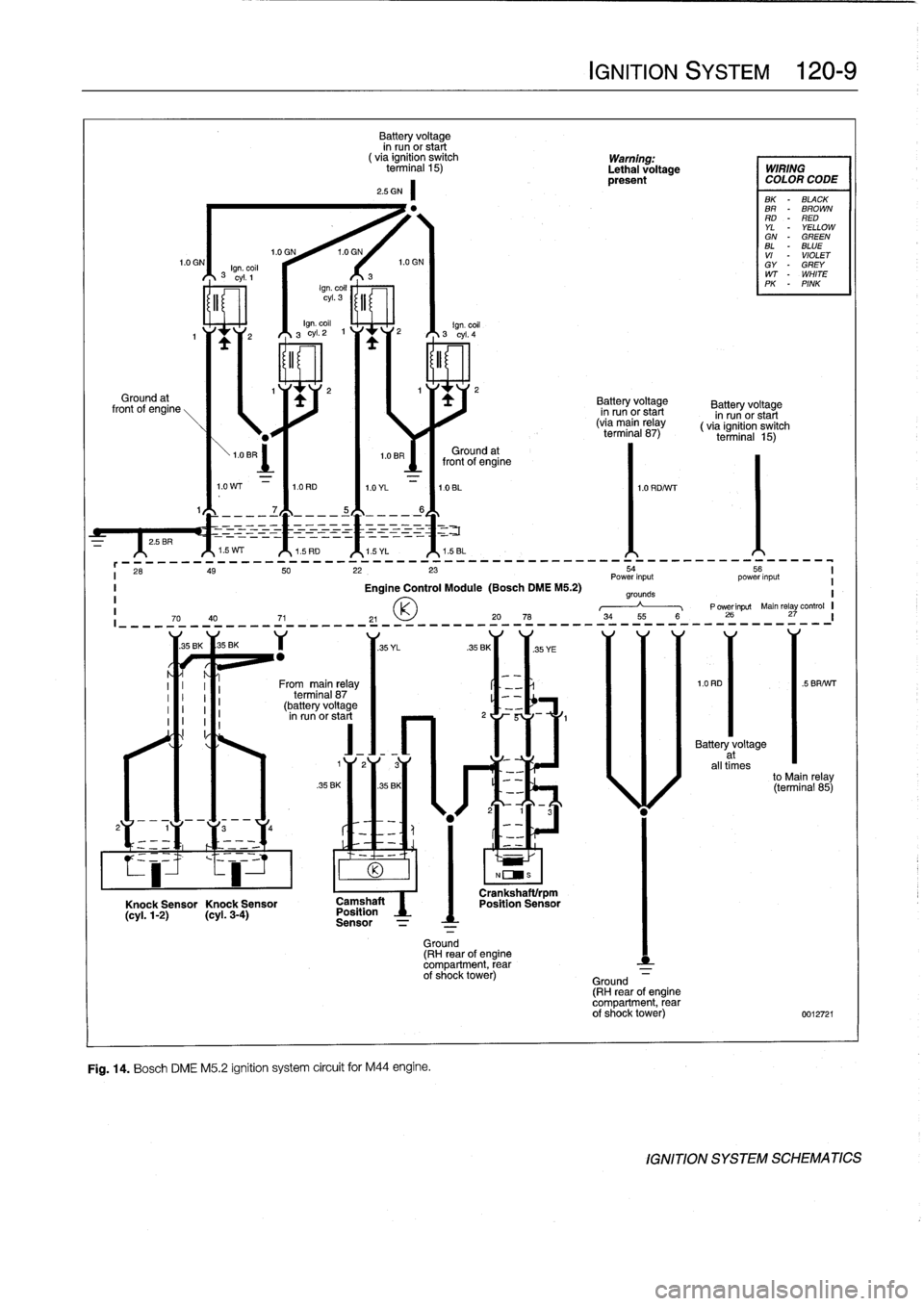
^1
.5WT
^1
.5RD
^1
.5YL
^1
.5BL
r
--__
____-
__-_
___-_
-___-_____--__--
-____-___
____-
i
26
g
5022
23
54
5
I
Power
input
power
input
I
Engine
Control
Module
(Bosch
DME
M5
.2)
I
I
grounds
I
P
owerinput
Main
relay
control
I
70
40
71
21
2078
34
55
626
27
----------------------
-
---------
-
--
-
------------
-
-----------
.,
v
1
1
.1
v
`
1
35BK
35BK
2
(
1Y
¡3
194
Knock
Sensor
Knock
Sensor
(cyl
.1-2)
(cyl
.3-4)
Frommain
relay
terminal
87
(battery
voltage
in
run
or
start
Battery
voltage
in
run
or
start
(
via
ignition
switch
Warnin
terminal
15)
Lethal
óltage
WIRING
present
COLOR
CODE
2
.5
GN
'
1
.0
YL
/
1
.0
BL
/
1
.0
RDNJT
.35
BK
/
/
.35
BK
Camshaft
Position
Sensor
-_
Fig
.
14
.
Bosch
DME
M5
.2
ignition
system
circuit
for
M44
engine
.
Ground
(RH
rear
of
engine
compartment,
rearof
shock
tower)
Crankshaftirpm
Position
Sensor
IGNITION
SYSTEM
120-9
Batteryvoltage
Battery
voltage
in
run
or
start
in
run
or
start
(via
main
relay
(
via
ignition
switch
terminal
87)
terminal
15)
BK
-
BLACX
BR
-
BROWN
RD
-
RED
YL
-
YELLOW
GN
-
GREEN
BL
-
BLUE
VI
-
VIOLET
GY
-
GREY
WT
-
WHITE
PK
-
PINK
Battery
voltage
at
all
times
to
Main
relay
(terminal
85)
Ground
(RH
rear
of
engine
compartment,
rearof
shock
tower)
0012721
lGNITION
SYSTEM
SCHEMATlCS
Page 134 of 759
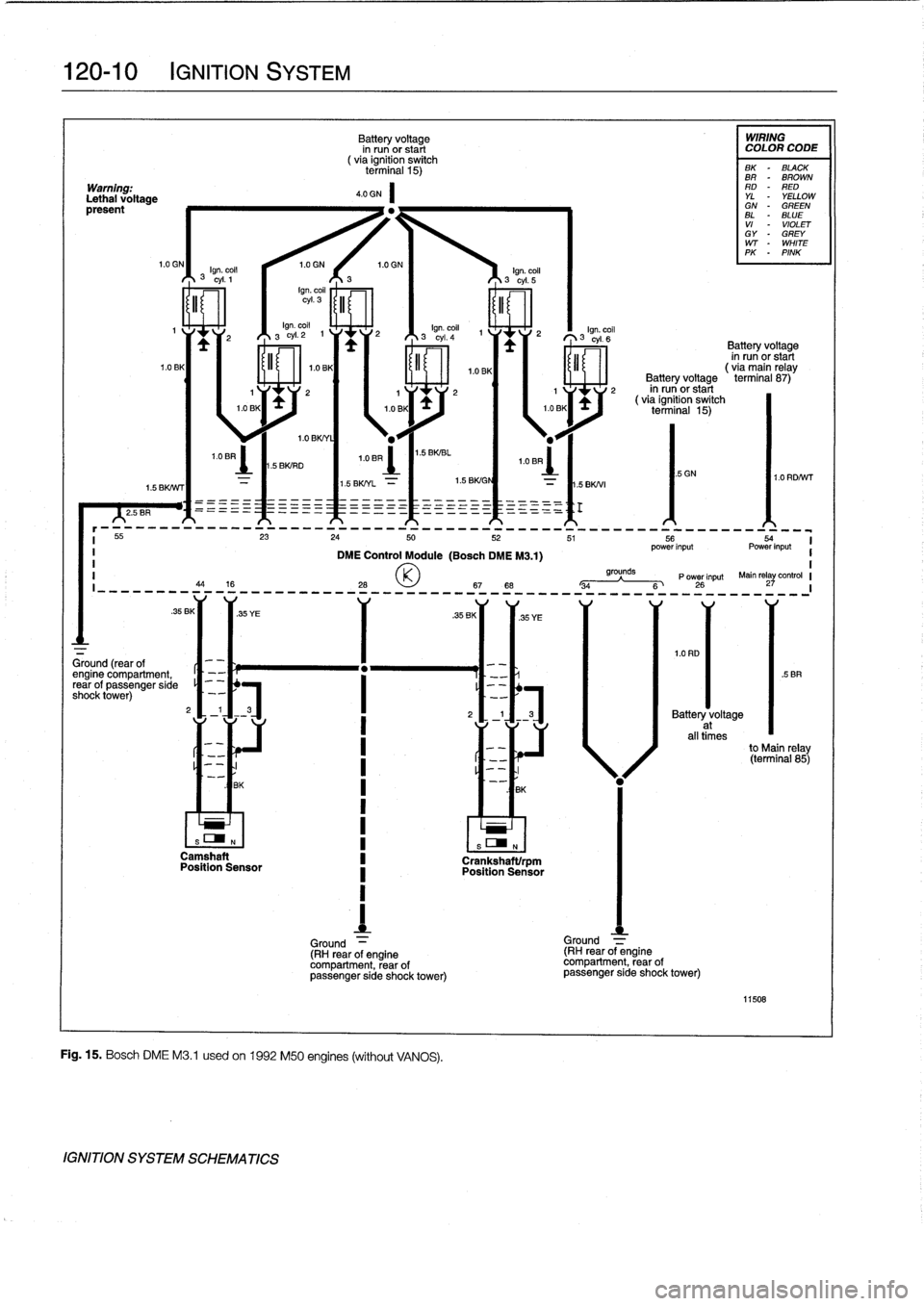
120-10
IGNITION
SYSTEM
Ground
(rear
of
engine
compartment,
rear
of
passenger
side
shock
tower)
.!
BK
Camshaft
Position
Sensor
IGNITION
SYSTEM
SCHEMATICS
Batteryvoltage
in
run
or
start
(
via
ignition
switch
terminal
15)
---------------------------------------------------------
55
S5154
i
power
input
Power
input
1
DME
Control
Module(Bosch
DME
M3
.1)
Ground
-
(RHrear
of
enginecompartment,
rearof
passenger
side
shock
tower)
Fig
.
15
.
Bosch
DME
M3
.1
usedon1992
M50
engines(without
VANOS)
.
.EBK
Crankshaftlrpm
Position
Sensor
5GN
1.0
RD
Ground
(RH
rearof
enginecompartment,
rear
of
passenger
side
shock
tower)
WIRING
COLOR
CODE
BK
-
BLACK
BR
-
BROWN
RD
-
RED
YL
-
YELLOWGN
-
GREEN
BL
-
BLUE
VI-
VIOLET
GY
"
GREY
WT
"
WHITE
PK
-
PINK
Batteryvoltage
in
run
or
start
(
via
main
relay
Battery
voltage
terminal
87)
in
run
or
start
(via
ignition
switch
terminal
15)
11508
1
grounds
Main
rela
control
P
ower
Input
Y
I
-
34
---"--
6
26
27
1
Battery
voltage
at
all
times
to
Main
relay
(terminal
85)
Page 135 of 759
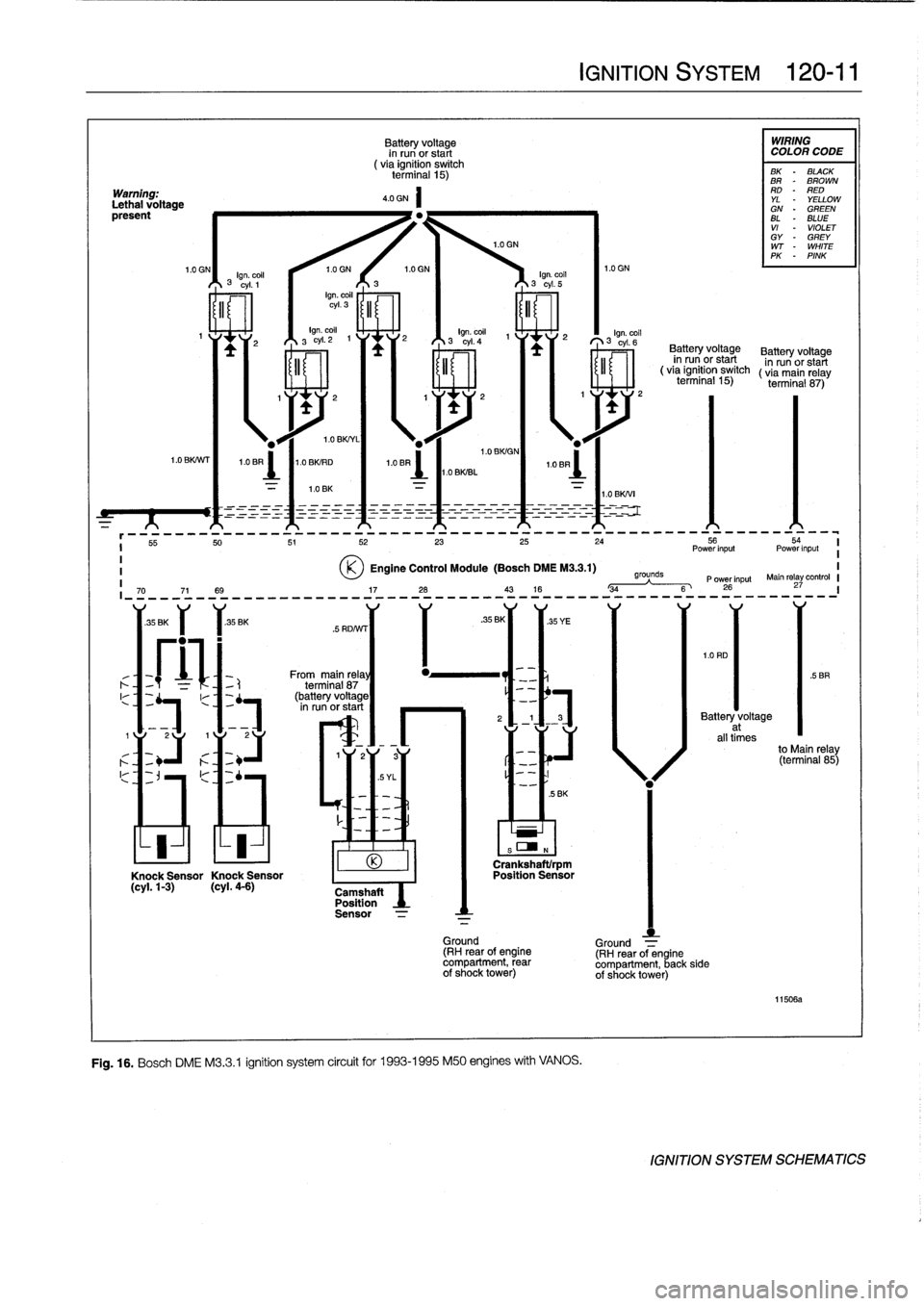
RER
Knock
Sensor
Knock
Sensor
(cyl
.1-3)
(cyl
.4-6)
Batteryvoltage
IMIRING
in
run
or
start
COLORCODE
(
via
ignition
switch
termina¡
15)
BK
BLAOK
BR
BROWN
RD
-
RED
YL
-
YELLOW
GN
"
GREEN
EL
-
BLUF
VI
-
VIOLET
GY
-
GREY
WT
-
WHITE
PK
-
PINK
4
.0
GN
l1/1j\
I'1
/~/1r1
l\r1
1
55
so
si
52
23
25
24
56
54
1
Power
input
Power
input
III
O
Engine
Control
Module
(Bosch
DMEM13
.1)
II
grounds
P
ower
input
Main
relaY
control
I
70
__
_
71
69
17
28
43
16
-34---"-6
26
27
____________________________________________
From
main
relaterminal
87
(battery
voltage
in
run
or
start
.5
YL
Camshaft
Position
Sensor
Ground
(RH
rearof
enginecompartment,
rear
of
shock
tower)
.5
BK
Crankshaft/rpm
Position
Sensor
Fig
.
16
.
Bosch
DME
M33
.1
ignition
system
círcuit
for
1993-1995
M50
engines
with
VANOS
.
IGNITION
SYSTEM
120-11
Ground
=
(RH
rear
of
engine
compartment,
back
sideof
shock
tower)
Batteryvoltage
Battery
voltage
in
run
or
start
in
run
or
start
(
via
ignition
switch
(
via
main
relay
terminal
15)
terminal
87)
1
.0
RD
11506a
.5
BR
Batteryvoltage
at
all
times
to
Main
relay
(terminal
85)
IGNITION
SYSTEM
SCHEMATICS
Page 136 of 759
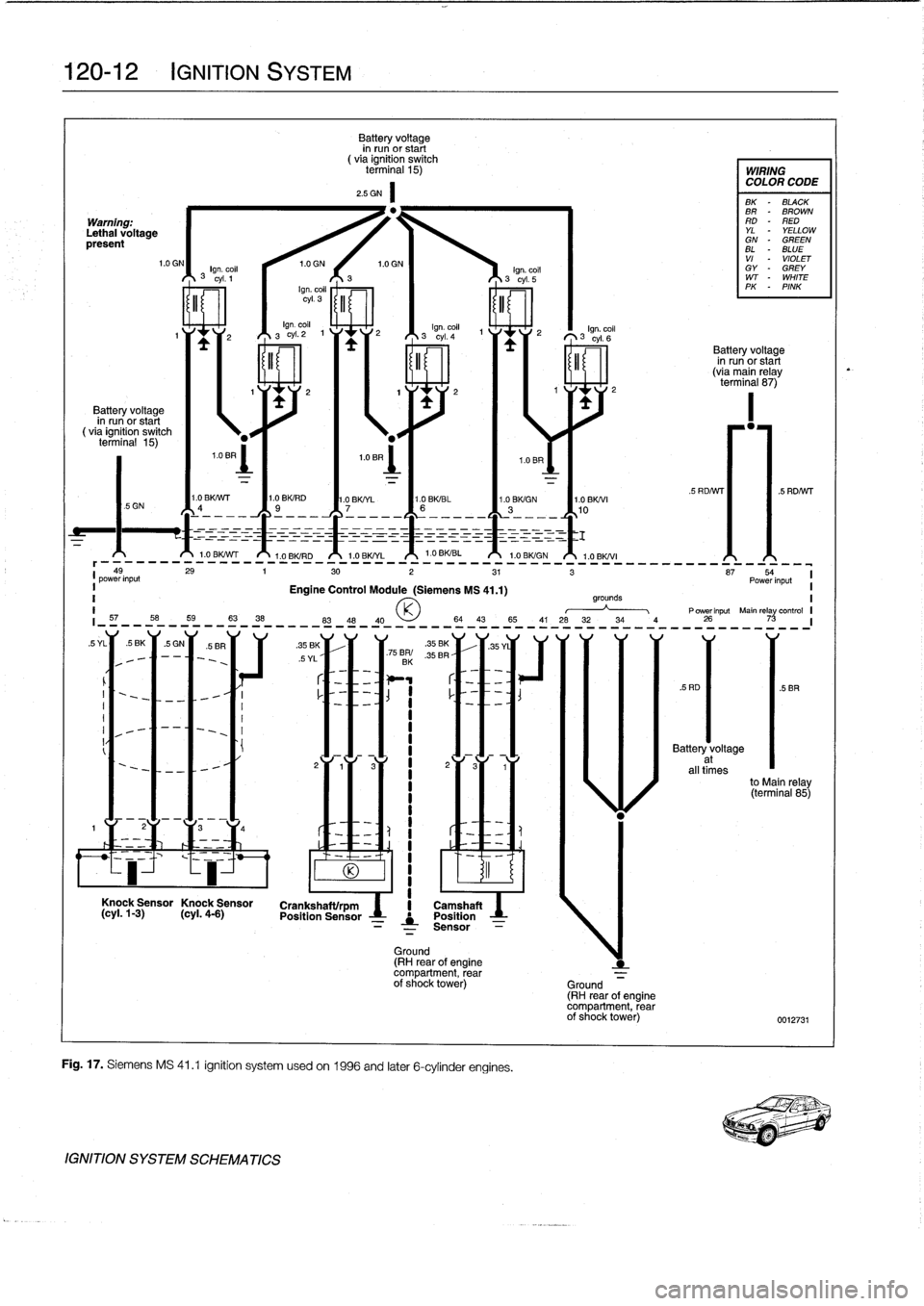
120-12
IGNITION
SYSTEM
Warning
.
Lethal
voltagepresent
Battery
voltage
in
run
or
start
(via
ignitíon
switch
terminal
15)
I
t
IGNITION
SYSTEM
SCHEMATICS
Battery
voltage
in
run
or
start
(
via
ignition
switchterminal
15)
WIRING
COLOR
CODE
Knock
Sensor
Knock
Sensor
Crankshaftlrpm
Camshaft
(cyl
.
1-3)
(cyl
.
4-6)
Position
Sensor
Position
-
-
Sensor
-
Fig
.
17
.
Siemens
MS
41
.1
ignition
systemusedon1996
and
later
6-cylinder
engines
.
1.0
BR
PQ
1
.08~1
.0BKIRD
/1
.0BK/YL
'10BK/BL
'1
.03KIGN
10BKNI
4
1D
BK
-
BLACK
BR
-
BROWN
RD
-
RED
YL
-
YELLOW
GN
-
GREEN
BL
-
BLUE
VI-
VIOLET
GY
-
GREY
WT
-
WHITE
PK
-
PINK
Batteryvoltage
in
run
or
start
(via
main
relay
terminal
87)
!1
rl
1.0
B~
^
1.0
BK/RD
^
1.0
BKIYL
^
1
.0
BK/BL
n
1.0
BK/GN
n
1
.0
BKIVI
%~
r
-------
--------------_____________----_______-_-____
49
29
1
30
2
31
3
8754
1
power
input
Power
input
I
1
Engine
Control
Module
(Siemens
MS
41
.1)
1
1
grounds
1
n
1
Powerinput
Mainrelaycontrol
1
1-
57
___
58
_
59
_
__
63
_
38
83
48
40
64
43
65
41
28
32
34
4
26
73
1
-
-----------
-
_-----
-
------
_
------
-
------
-
---
-
.5Y1-
.5BKY.5GNY.5BRY
Y
.35BKY
1
Y
Y
.35BKY/Y35YY
75
.18R/
.5YL-1
1'
.
Batteryvoltage
at
all
times
to
Main
relay
(terminal
85)
Ground
v
(RH
rear
of
engine
Z
compartment,
rear
=
of
shock
tower)
Ground
(RH
rear
of
enginecompartment,
rearof
shock
tower)
0012731