ing harness BMW M3 1995 E36 Owner's Manual
[x] Cancel search | Manufacturer: BMW, Model Year: 1995, Model line: M3, Model: BMW M3 1995 E36Pages: 759
Page 84 of 759
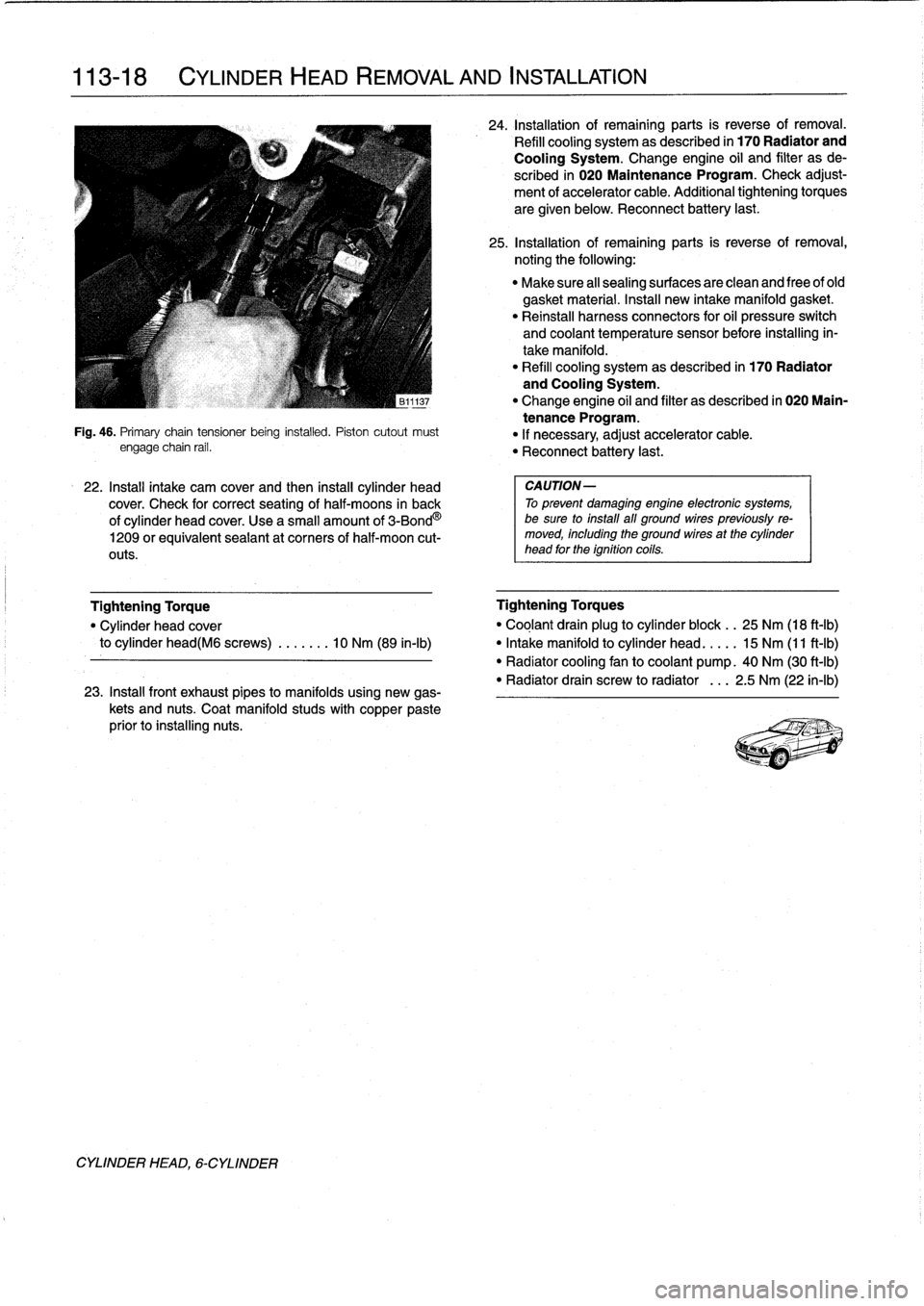
113-
1
8
CYLINDER
HEAD
REMOVAL
AND
INSTALLATION
CYLINDER
HEAD,
6-CYLINDER
Fig
.
46
.
Primary
chaintensioner
being
installed
.
Piston
cutout
must
engage
chain
rail
.
22
.
Install
intake
cam
cover
and
then
install
cylinder
head
cover
.
Check
for
correct
seating
of
half-moons
in
back
of
cylinder
head
cover
.
Use
a
small
amount
of
3-Bond
O
1209
orequivalent
seaiant
at
corners
of
half-moon
cut-
outs
.
23
.
Install
front
exhaust
pipes
to
manifolds
using
new
gas-
kets
and
nuts
.
Coat
manifold
studs
with
copper
paste
prior
to
installing
nuts
.
24
.
Installationof
remaining
parts
is
reverse
of
removal
.
Refill
cooling
system
as
described
in
170
Radiator
and
Cooling
System
.
Change
engine
oil
and
filter
as
de
scribed
in
020
Maintenance
Program
.
Check
adjust-
ment
of
accelerator
cable
.
Additional
tightening
torques
are
given
below
.
Reconnect
battery
last
.
25
.
Installationof
remaining
parts
is
reverse
of
removal,
noting
the
following
:
"
Make
sure
all
sealing
surfaces
are
clean
and
free
of
old
gasket
material
.
Insta¡¡
new
intake
manifold
gasket
.
"
Reinstall
harness
connectors
for
oil
pressure
switch
and
coolant
temperature
sensor
before
installing
in-
take
manifold
.
"
Refill
cooling
systemas
described
in
170
Radiator
and
Cooling
System
.
"
Change
engine
oil
and
filter
as
described
in
020
Main-
tenance
Program
.
"
If
necessary,
adjust
accelerator
cable
.
"
Reconnect
battery
last
.
CAUTION-
To
prevent
damaging
engine
electronic
systems,
be
sure
to
install
all
ground
wirespreviously
re-
moved,
including
the
ground
wires
at
the
cylinder
head
for
the
ignition
coils
.
Tightening
Torque
Tightening
Torques
"
Cylinder
head
cover
"
Coglant
drain
plug
to
cylinder
block
.
.
25
Nm
(18
ft-Ib)
to
cylinder
head(M6
screws)
.
.
.....
10
Nm
(89
in-lb)
"
Intake
manifold
to
cylinder
head
.
...
.
15
Nm
(11
ft-Ib)
"
Radiator
cooling
fan
to
coolant
pump
.
40
Nm
(30
ft-Ib)
"
Radiator
drain
screw
to
radiator
.
..
2
.5
Nm
(22
in-lb)
Page 110 of 759
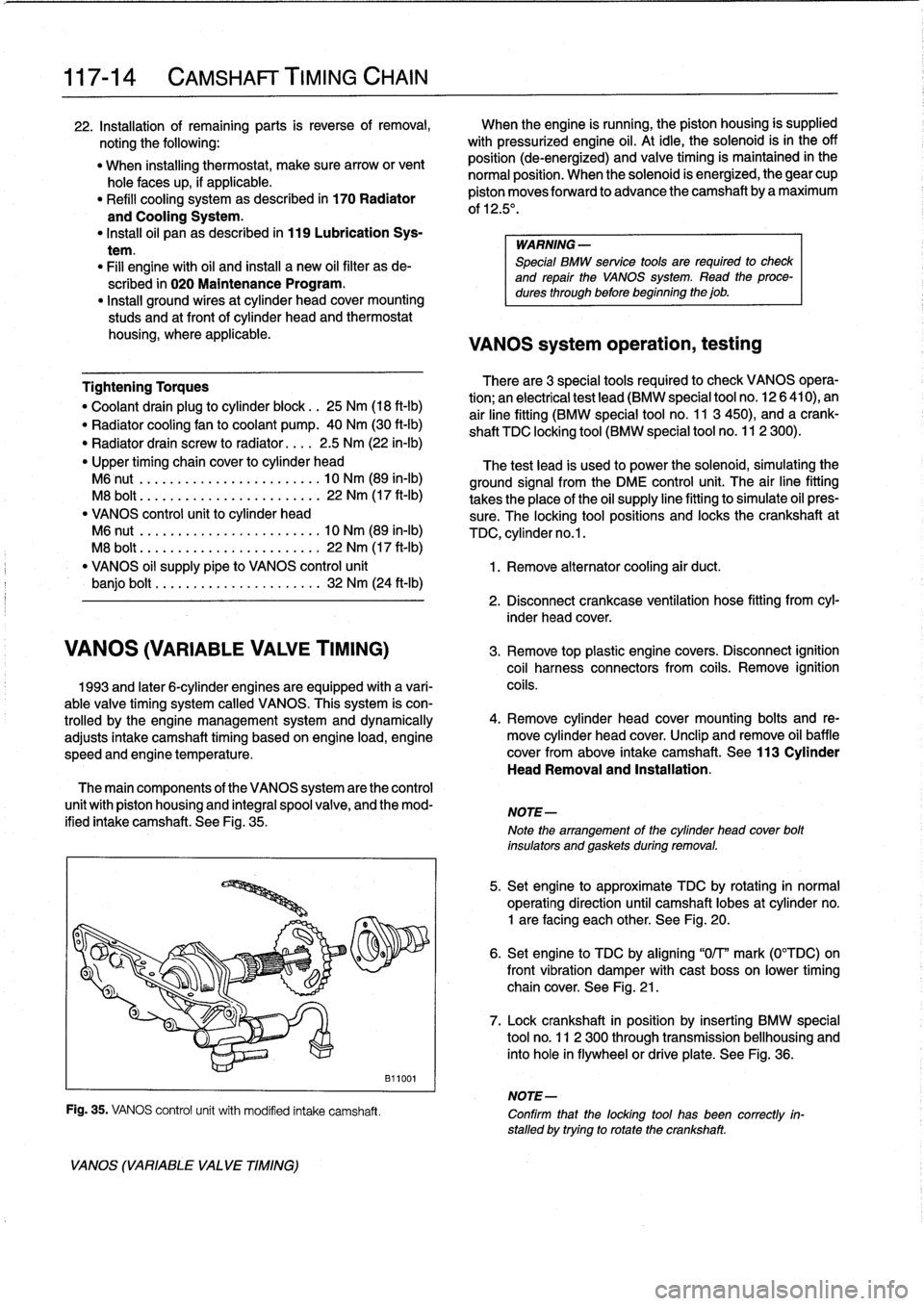
117-
1
4
CAMSHAFT
TIMING
CHAIN
22
.
Installation
of
remaining
parts
is
reverse
of
removal,
When
theengine
is
running,
the
piston
housing
is
supplied
noting
the
following
:
with
pressurized
engine
oil
.
At
idie,
the
solenoid
isin
the
off
"
When
installing
thermostat,
make
sure
arrow
or
vent
position
(de-energized)
and
valve
timing
is
maintained
in
the
hole
faces
up,
if
applicable
.
normal
position
:
When
the
solenoid
is
energized,
the
gear
cup
"
Refill
cooling
systemas
described
in
170
Radiator
piston
moves
forward
to
advance
the
camshaftby
a
maximum
and
Coming
System
.
of
12
.5
.
"
Install
oil
pan
as
described
in
119
Lubrication
Sys-
tem
.
"
Fill
engine
with
oil
and
install
a
new
oil
filter
as
de-
scribed
in
020
Maintenance
Program
.
"
Insta¡¡
ground
wires
at
cylinder
head
cover
mounting
studs
and
at
front
of
cylinder
head
and
thermostat
housing,
where
applicable
.
VANOS
system
operation,
testing
Tightening
Torques
There
are3
special
tools
required
to
check
VANOS
opera-
"
Coolant
drain
plugto
cylinder
block
.
.
25
Nm
(18
ft-Ib)
tion
;
an
electricaltest
lead
(BMW
special
tool
no
.
12
6
410),
an
"
Radiator
cooling
fan
to
coolant
pump
.
40
Nm
(30
ft-Ib)
air
line
fitting
(BMW
special
tool
no
.
11
3
450),
and
a
crank-
"
Radiator
drain
screw
to
radiator
...
.
2
.5
Nm
(22
in-Ib)
shaft
TDC
locking
tool
(BMW
special
tool
no
.
112
300)
.
"
Upper
timing
chaincover
to
cylinder
head
The
test
leal
is
used
to
power
the
solenoid,
simulating
the
M6
nut
...
.....
.............
..
.
10
Nm
(89
in-lb)
ground
signal
from
the
DME
control
unit
.
The
air
line
fitting
M8
bolt
.....
....
.
.
.............
22
Nm
(17
ft-Ib)
takes
the
place
of
the
oil
supply
line
fitting
to
simulate
oil
Ares-
"
VANOS
control
unit
to
cylinder
head
sure
.
The
locking
tool
positions
and
locks
the
crankshaft
at
M6
nut
.........
..
..
.
..........
10
Nm
(89
in-lb)
TDC,
cylinder
no
.
l.
M8
bolt
........
...
.............
22
Nm
(17
ft-Ib)
"
VANOS
oil
supply
pipe
to
VANOS
control
unit
1
.
Remove
alternator
cooling
air
duct
.
banjo
bolt
.......
..
..
.
..........
32
Nm
(24
ft-Ib)
VANOS
(VARIABLE
VALVE
TIMING)
3
.
Remove
top
plastic
enginecovers
.
Disconnect
ignition
coil
harness
connectors
fromcofs
.
Remove
ignition
1993
and
later
6-cylinder
engines
are
equipped
with
a
vari-
coils
.
able
valve
timing
system
called
VANOS
.
This
system
is
con-
trolled
by
the
engine
management
system
and
dynamically
4
.
Remove
cylinder
head
cover
mounting
bolts
and
re-
adjusts
intake
camshaft
timing
based
on
engine
load,
engine
move
cylinder
head
cover
.
Unclip
andremove
oil
baffle
speed
and
engine
temperature
.
cover
from
above
intake
camshaft
.
See
113
Cylinder
Head
Removal
and
installation
.
The
main
components
of
the
VANOS
system
are
the
control
unit
with
piston
housing
and
integral
spool
valve,
and
the
mod-
ified
intake
camshaft
.
See
Fig
.
35
.
VANOS
(VARIABLE
VA
LVE
TIMING)
Fig
.
35
.
VANOS
control
unit
with
modified
intake
camshaft
.
B11001
WARNING
-
Special
BMW
service
tools
are
required
to
check
and
repair
the
VANOS
System
.
Read
theproce-
dures
through
before
beginning
the
job
.
2
.
Disconnect
crankcase
ventilation
hose
fitting
from
cyl-
inder
head
cover
.
NOTE-
Note
the
arrangement
of
the
cylinder
head
cover
bolt
insulators
and
gaskets
during
removal
.
5
.
Set
engine
to
approximate
TDC
by
rotating
in
normal
operating
direction
until
camshaft
lobes
at
cylinder
no
.
1
are
facing
each
other
.
See
Fig
.
20
.
6
.
Set
engine
to
TDC
by
aligning
"0/T"
mark
(0°TDC)on
front
vibration
damper
withcast
boss
on
lower
timing
chain
cover
.
See
Fig
.
21
.
7
.
Lock
crankshaft
in
position
by
inserting
BMW
special
tool
no
.
11
2
300
through
transmission
bellhousing
and
into
hole
in
flywheelor
driveplate
.
See
Fig
.
36
.
NOTE-
Confirm
that
the
locking
tool
has
been
correctly
in-
stalled
by
trying
to
rotatethe
crankshaft
.
Page 111 of 759
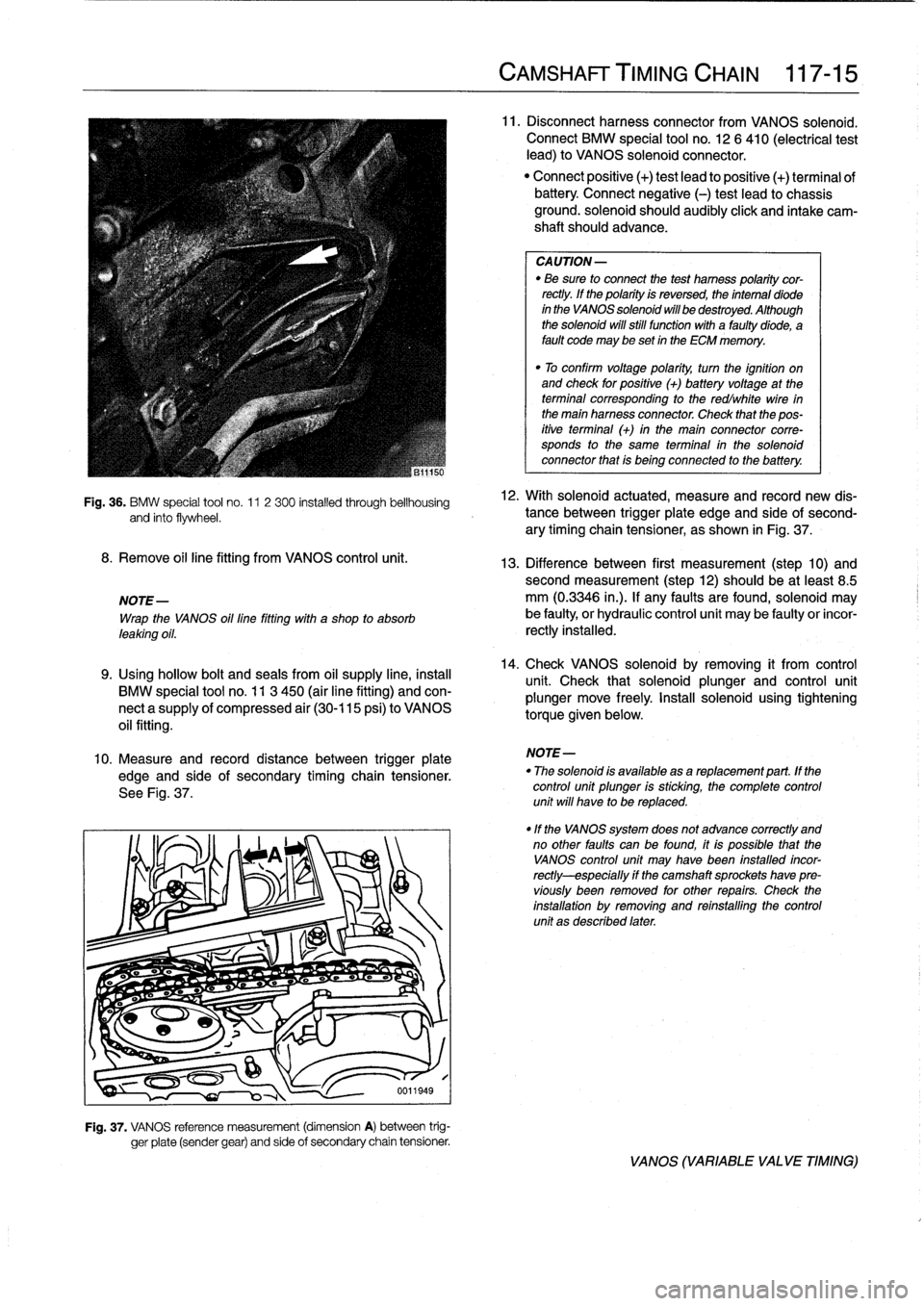
Fig
.
36
.
BMW
special
tool
no
.
11
2
300
installed
through
bellhousing
and
finto
flywheel
.
8
.
Remove
oil
line
fitting
from
VANOS
control
unit
.
NOTE-
Wrap
the
VANOS
oil
line
fitting
with
a
shop
to
absorb
leaking
oil
.
9
.
Using
hollow
bolt
and
seals
from
oil
supply
line,
instan
BMW
special
tool
no
.
11
3
450
(air
line
fitting)
and
con-
nect
a
supply
of
compressed
air
(30-115
psi)
to
VANOS
oil
fitting
.
10
.
Measure
and
record
distance
between
trigger
plate
edge
and
side
of
secondary
timing
chain
tensioner
.
See
Fig
.
37
.
Fig
.
37
.
VANOS
reference
measurement
(dimension
A)
between
trig-
ger
píate
(sender
gear)
and
side
of
secondary
chain
tensioner
.
CAMSHAFT
TIMING
CHAIN
117-
1
5
11
.
Disconnectharness
connector
from
VANOS
solenoid
.
Connect
BMW
special
tool
no
.
12
6
410
(electrical
test
lead)
to
VANOS
solenoid
connector
.
"
Connect
positive
(+)
test
lead
to
positive
(+)
terminal
ofbattery
Connect
negative
(-)
test
leadto
chassis
ground
.
solenoid
should
audibly
click
and
intake
cam-
shaft
should
advance
.
CA
UTION-
"
Be
sure
to
connect
the
test
hamess
polaritycor-
rectly
.
lf
the
polarity
is
reversed,
the
intemal
diode
in
the
VANOS
solenoid
will
be
destroyed
.
Although
the
solenoid
will
still
functionwith
a
faultydiode,
a
fault
code
may
be
set
in
the
ECM
memory
.
"
To
confirm
voltage
polarity,
turn
the
ignition
on
and
check
for
positive
(+)
batteryvoltage
at
the
terminal
corresponding
to
the
redlwhite
wire
in
the
main
harness
connector
.
Check
that
the
pos-
itive
terminal
(+)
in
the
main
connector
corre-
sponds
to
the
same
terminal
in
the
solenoid
connector
that
is
being
connected
to
the
battery
.
12
.
With
solenoid
actuated,
measure
and
record
new
dis-
tance
between
trigger
plate
edge
and
side'of
second-
ary
timing
chain
tensioner,
as
shown
in
Fig
.
37
.
13
.
Difference
between
first
measurement
(step
10)
andsecond
measurement
(step12)
should
be
at
least
8
.5
mm
(0
.3346
in
.)
.
lf
any
faults
arefound,
solenoid
may
be
faulty,
or
hydraulic
control
unit
may
be
faulty
or
incor-
rectly
installed
.
14
.
Check
VANOS
solenoid
byremoving
it
from
control
unit
.
Check
that
solenoid
plunger
and
control
unit
plunger
move
freely
.
Install
solenoid
using
tighteníng
torque
given
below
.
NOTE-
"
The
solenoid
is
available
asareplacement
part
.
lf
the
control
unit
plunger
is
sticking,
the
complete
control
unit
will
have
to
be
replaced
.
"lf
the
VANOS
system
does
not
advance
correctly
and
no
other
faults
can
be
found,
itis
possible
that
the
VANOS
control
unit
may
Nave
been
fnstalled
incor-
rectly-especially
if
the
camshaft
sprockets
have
pre-
víously
been
removed
for
other
repairs
.
Check
the
installation
by
removing
and
reinstalling
the
control
unit
as
described
later
.
VANOS
(VARIABLE
VALVE
TIMING)
Page 112 of 759
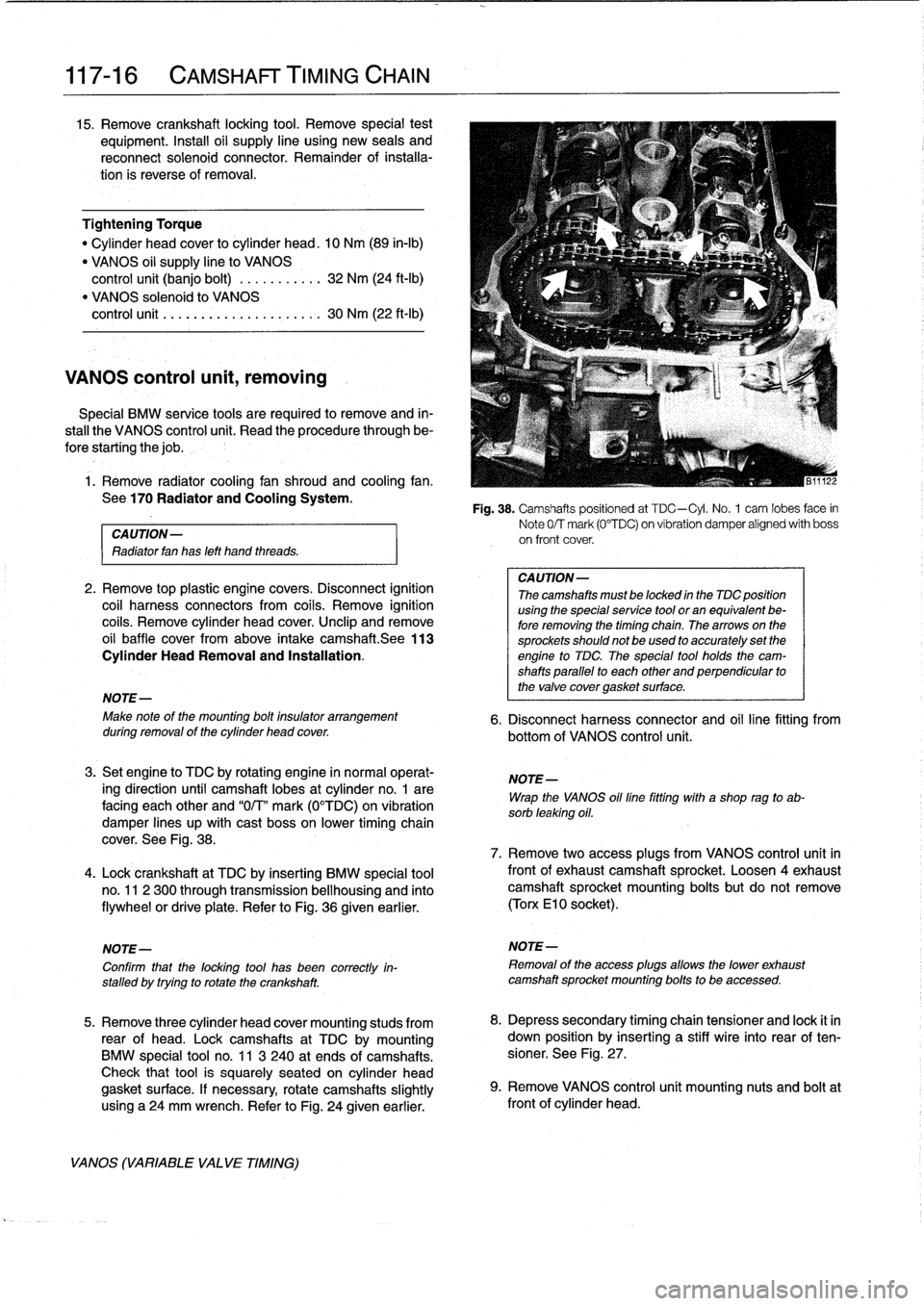
117-
1
6
CAMSHAFT
TIMING
CHAIN
15
.
Remove
crankshaft
locking
tool
.
Remove
special
test
equipment
.
Insta¡¡
oil
supply
line
using
new
seals
and
reconnect
solenoid
connector
.
Remainder
of
installa-
tion
is
reverse
of
removal
.
Tightening
Torque
"
Cylinder
head
cover
to
cylinder
head
.
10
Nm
(89
in-lb)
"
VANOS
oil
supply
line
to
VANOS
control
unit
(banjo
bolt)
..
.........
32
Nm
(24
ft-Ib)
"
VANOS
solenoidlo
VANOS
control
unit
........
.
.
.
..
........
30
Nm
(22
ft-Ib)
VANOS
control
unit,
removing
Special
BMW
service
tools
are
required
lo
remove
and
in-
stall
the
VANOS
control
unit
.
Read
the
procedure
through
be-
forestarting
the
job
.
1
.
Remove
radiator
cooling
fan
shroud
and
cooling
fan
.
See
170
Radiator
and
Cooling
System
.
CAUTION-
Radiator
fan
has
left
hand
threads
.
2
.
Remove
top
plastic
engine
covers
.
Disconnect
ignition
coil
harness
connectors
from
coils
.
Remove
ignition
coils
.
Remove
cylinder
head
cover
.
Unclip
andremove
oil
baffle
cover
from
above
intake
camshaft
.See
113
Cylinder
Head
Removal
and
Installation
.
NOTE-
Make
note
of
the
mounting
bolt
insulator
arrangement
during
removal
of
the
cylinder
head
cover
.
3
.
Set
engine
lo
TDC
by
rotating
engine
in
normal
operat-
ing
direction
until
camshaft
lobes
at
cylinder
no
.
1
are
facing
each
other
and
"0/T"
mark
(0°TDC)
on
vibration
damper
lines
up
with
cast
boss
on
lower
timing
chain
cover
.
See
Fig
.
38
.
4
.
Lock
crankshaft
at
TDC
by
inserting
BMW
special
tool
no
.
11
2
300
through
transmission
bellhousing
and
finto
flywheel
or
drive
plate
.
Refer
to
Fig
.
36
given
earlier
.
NOTE-
Confirm
that
the
locking
tool
has
been
correctly
in-
stalled
by
trying
to
rotatethe
crankshaft
.
5
.
Remove
three
cylinder
head
cover
mounting
studs
from
rear
of
head
.
Lockcamshafts
at
TDC
bymounting
BMW
special
tool
no
.
11
3
240
at
ends
of
camshafts
.
Check
that
tool
is
squarely
seated
on
cylinder
head
gasket
surface
.
If
necessary,
rotate
camshafts
slightly
using
a24
mm
wrench
.
Refer
to
Fig
.
24
given
earlier
.
VANOS
(VARIABLE
VALVE
TIMING)
Fig
.
38
.
Camshafts
positioned
at
TDC-Cyl
.
No
.
1
cam
lobes
face
in
Note
0/T
mark
(0°TDC)
on
vibration
damper
alígned
with
boss
on
front
cover
.
CA
UTION-
Thecamshafts
mustbe
locked
in
the
TDC
position
using
the
specialservice
tool
or
an
equivalent
be-
fore
removing
the
timing
chain
.
Thearrows
on
the
sprockets
should
not
be
used
to
accurately
set
the
engine
to
TDC
The
special
tool
holds
the
cam-
shafts
parallel
to
each
other
and
perpendicular
to
the
valve
cover
gasket
surface
.
6
.
Disconnect
harness
connector
and
oil
line
fitting
from
bottom
of
VANOS
control
unit
.
NOTE-
Wrap
the
VANOS
oilfine
fitting
with
a
shop
rag
to
ab-
sorb
leaking
oil
.
7
.
Remove
two
access
plugs
from
VANOS
control
unit
in
frontof
exhaustcamshaft
sprocket
.
Loosen
4exhaustcamshaft
sprocket
mounting
bolts
but
do
not
remove
(Torx
El
0
socket)
.
NOTE-
Removal
of
the
access
plugs
allows
the
lower
exhaust
camshaft
sprocket
mounting
bolts
to
be
accessed
.
8
.
Depress
secondary
timing
chain
tensioner
and
lock
it
in
down
position
by
inserting
a
stiff
wire
into
rear
of
ten-
sioner
.
See
Fig
.
27
.
9
.
Remove
VANOS
control
unít
mounting
nuts
and
boltat
front
of
cylinder
head
.
Page 114 of 759
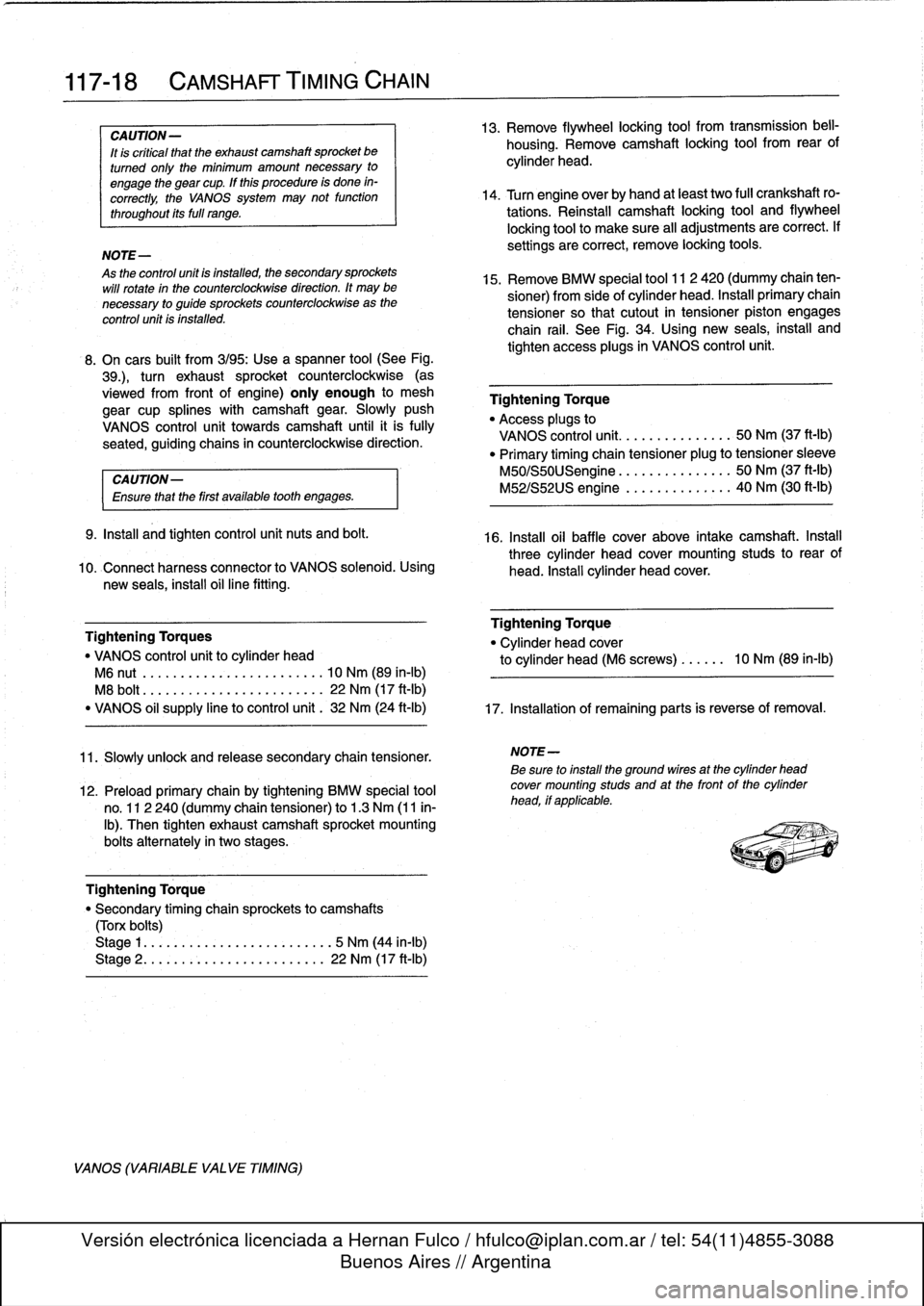
117-
1
8
CAMSHAFT
TIMING
CHAIN
CAUTION-
It
is
crítical
that
the
exhaustcamshaft
sprocket
be
turned
only
the
mínimum
amount
necessary
to
engage
the
gear
cup
.
If
this
procedure
is
done
ín-
correctly,
the
VANOS
system
may
not
function
throughout
íts
full
range
.
NOTE-
As
the
control
unit
isinstalled,
the
secondary
sprockets
will
rotate
in
the
counterclockwise
direction
.
It
may
be
necessary
to
guide
sprockets
counterclockwise
as
the
control
unit
is
installed
.
8
.
On
cars
built
from3/95
:
Use
a
spanner
tool
(See
Fig
.
39
.),
turn
exhaust
sprocket
counterclockwise
(as
víewed
from
front
of
engine)
only
enough
to
mesh
gear
cup
splines
with
camshaftgear
.
Slowly
push
VANOS
control
unit
towards
camshaft
until
it
is
fully
seated,guiding
chains
in
counterclockwise
direction
.
CA
UTION-
Ensure
that
the
first
available
tooth
engages
.
9
.
Install
and
tightencontrol
unit
nuts
and
bolt
.
10
.
Connect
harness
connector
to
VANOS
solenoid
.
Using
new
seals,
insta¡¡
oil
line
fitting
.
Tightening
Torques
"
VANOS
control
unitto
cylinder
head
M6
nut
.....
..
..
.
.
.............
10
Nm
(89
in-lb)
M8
bolt
.....
.
.
.
.
..
.............
22
Nm
(17
ft-Ib)
"
VANOS
oil
supply
line
to
control
unit
.
32
Nm
(24
ft-Ib)
11
.
Slowlyunlock
and
release
secondary
chain
tensioner
.
12
.
Preloadprimary
chain
by
tightening
BMW
special
tool
no
.
112
240
(dummy
chain
tensioner)
to
1
.3
Nm
(11
in-
lb)
.
Then
tighten
exhaust
camshaft
sprocket
mounting
bolts
alternately
in
two
stages
.
Tightening
Torque
"
Secondarytiming
chain
sprockets
to
camshafts
(Tora
boits)
Stage
1
..
...............
...
.
.
...
5
Nm
(44
in-lb)
Stage
2
..
...............
...
.
.
..
22
Nm
(17
ft-Ib)
VANOS
(VARIABLE
VALVE
TIMING)
13
.
Remove
flywheel
locking
tool
from
transmission
bell-
housing
.
Remove
camshaft
locking
tool
from
rear
of
cylinder
head
.
14
.
Turn
engine
over
by
hand
at
least
two
fui¡
crankshaft
ro-
tations
.
Reinstall
camshaft
locking
tool
and
flywheel
locking
toolto
make
sure
all
adjustments
are
correct
.
If
settings
are
correct,
remove
locking
tools
.
15
.
Remove
BMW
special
tool
112
420
(dummy
chain
ten-
sioner)
from
side
of
cylinder
head
.
Install
primary
chain
tensioner
so
that
cutout
in
tensioner
piston
engages
chain
rail
.
See
Fig
.
34
.
Using
new
seals,
install
and
tighten
access
plugs
in
VANOS
control
unit
.
Tightening
Torque
"
Access
plugs
to
VANOS
control
unit
.
..
.
.....
.
..
...
50
Nm
(37
ft-lb)
"
Primary
timing
chain
tensioner
plug
to
tensioner
sleeve
M50/S50USengine
.
.
..
.
.
...
.
...
..
50
Nm
(37
ft-Ib)
M52/S52US
engine
...
..
...
...
...
40
Nm
(30
ft-Ib)
16
.
Install
oil
baffle
cover
above
intake
camshaft
.
Install
three
cylinder
head
covermounting
studs
to
rear
of
head
.
Instali
cylinder
head
cover
.
Tightening
Torque
"
Cylinder
head
cover
to
cylinder
head
(M6
screws)
......
10
Nm
(89
in-Ib)
17
.
Installationof
remaining
parts
is
reverse
of
removal
.
NOTE-
Be
sure
to
install
the
ground
wíres
at
the
cylinder
head
cover
mounting
studs
and
at
the
front
of
the
cylinder
head,
if
applicable
.
Page 115 of 759
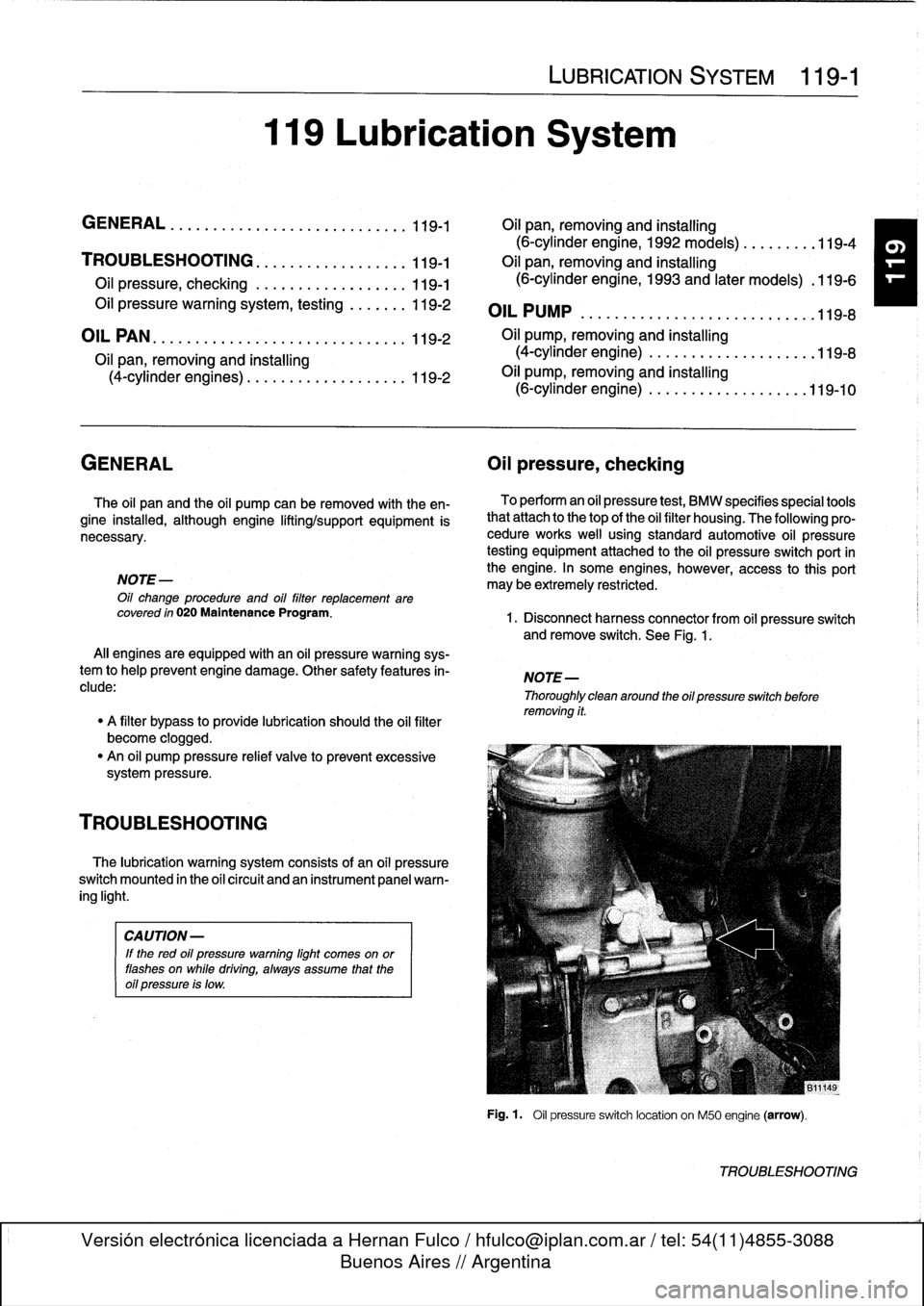
119
Lubrication
System
LUBRICATION
SYSTEM
119-1
GENERAL
.
.
.
.
.
.
...
.
.
.
.
.
.
.
...,
,
...
.
.
.
.
119-1
OH
pan,
removing
and
installing
(6-cylinder
engine,
1992
models)
.
.
.
.
.
.
.
.
.
119-4
TROUBLESHOOTING
.
.
.
.
.
.
...
.
.
.
.....
.
119-1
Oil
pan,
removing
and
installing
Oil
pressure,
checking
.
.
.
.
.
.
...
.
.
.
.
.
.
.
.
.
119-1
(6-cylinder
engine,
1993
and
later
models)
.119-6
Oil
pressure
warning
system,
testing
.
.
.
.
.
.
.
119-2
OIL
PUMP
.
.......
.
.............
.119-8
OIL
PAN
.
.
.
.
.
.....
.
.
.
.
.
......
.
.
.
.
.
.
.
..
119-2
Oil
pump,
removing
and
installing
Oil
pan,
removing
and
installing
(4-cylinder
engine)
.
.
.
...
.
..........
.
.
.119-8
(4-cylinder
engines)
.
.
...
.
....
.
.
.
.
.
.
.
..
119-2
Oil
pump,
removing
and
installing
(6-cylinder
engine)
.
.
.....
.
.........
.
.119-10
GENERAL
Oil
pressure,
checking
The
oil
pan
and
the
oil
pump
can
be
removed
with
theen-
gine
installed,
although
engine
liftinglsupport
equipment
is
necessary
.
NOTE-
Oil
change
procedure
and
oil
filter
replacement
are
covered
in
020
Maintenance
Program
.
Al¡
engines
are
equipped
with
an
oil
pressure
warning
sys-
tem
to
help
prevent
engine
damage
.
Other
safety
features
in-
clude
:
"
A
filter
bypass
to
provide
lubrication
should
the
oil
filter
become
clogged
.
"
An
oil
pump
pressure
relief
valve
to
prevent
excessive
system
pressure
.
TROUBLESHOOTING
The
lubrication
warning
system
consists
of
an
oil
pressure
switch
mounted
in
the
oil
circuit
and
an
instrument
panel
warn-
ing
light
.
CAUTION-
If
the
red
oil
pressurewarning
light
comes
on
or
flashes
on
while
driving,
always
assume
that
the
oil
pressure
is
low
.
To
perform
an
oíl
pressure
test,
BMW
specifies
special
tools
that
attach
to
thetop
of
the
oíl
filter
housing
.
The
following
pro-
cedure
works
well
using
standard
automotive
oil
pressure
testing
equipment
attached
to
the
oil
pressure
switch
port
in
the
engine
.
In
some
engines,
however,
access
tothis
port
may
be
extremely
restricted
.
1
.
Disconnect
harness
connector
from
oil
pressure
switch
andremove
switch
.
See
Fig
.
1
.
NOTE-
Thoroughly
clean
around
the
oil
pressure
switchbefore
removing
it
.
Fig
.
1
.
Oil
pressure
switch
location
on
M50
engine
(arrow)
.
TROUBLESHOOTING
Page 120 of 759
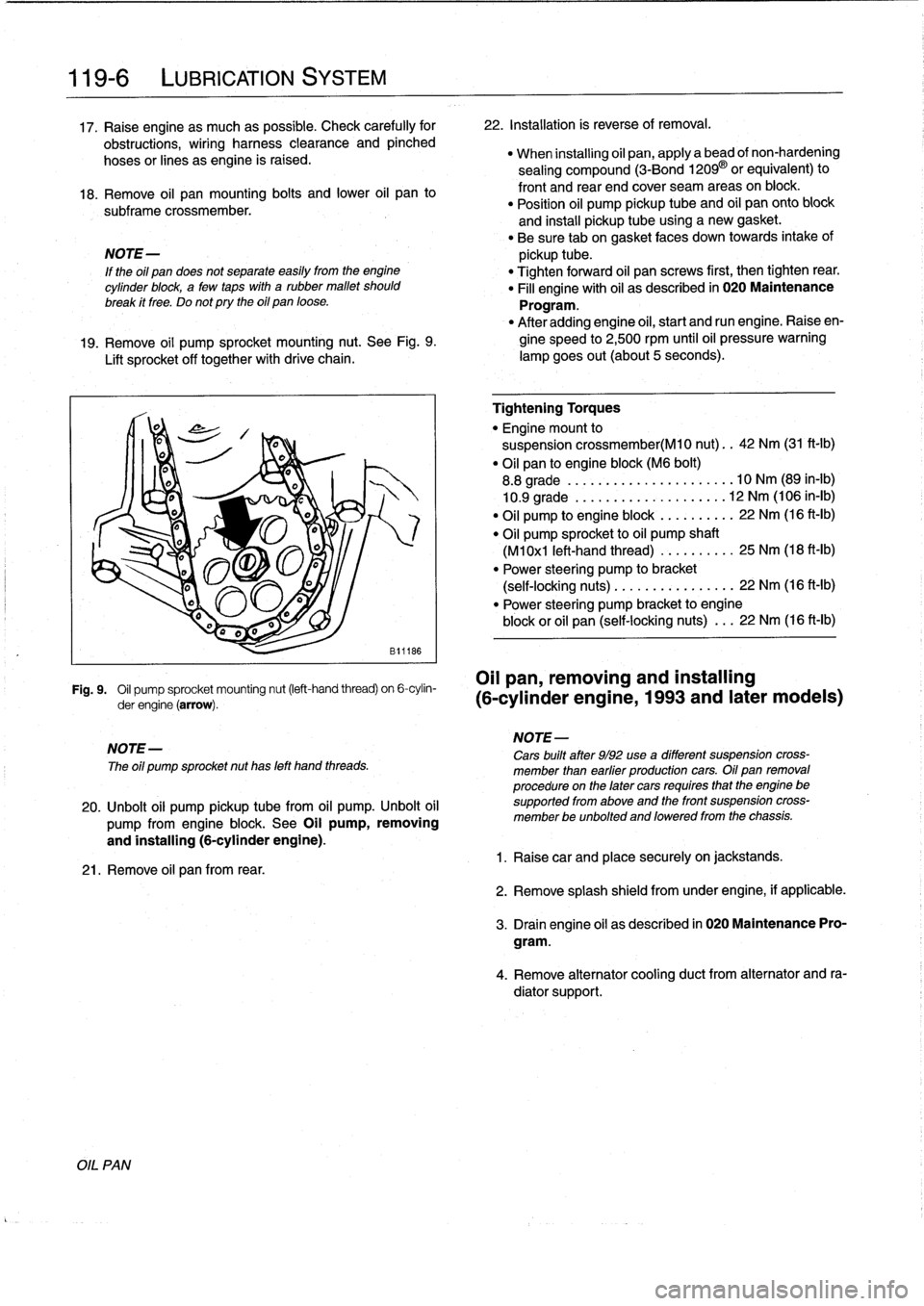
119-
6
LUBRICATION
SYSTEM
17
.
Raise
engine
as
much
as
possible
.
Check
carefully
for
22
.
Installation
is
reverse
of
removal
.
obstructions,
wiring
harness
clearance
and
pinched
hoses
or
lines
as
engine
is
raised
.
"
When
installing
oil
pan,
apply
a
b
d
of
non-hardening
sealing
compound
(3-Bond
1209
0
or
equivalent)
to
18
.
Remove
oil
pan
mounting
bolts
and
lower
oil
pan
to
front
and
rear
end
cover
seam
areas
on
block
.
subframe
crossmember
.
"
Position
oil
pump
pickup
tube
and
oil
pan
onto
block
and
install
pickup
tube
using
a
new
gasket
.
"
Be
sure
tab
on
gasket
faces
down
towards
intake
of
NOTE-
pickup
tube
.
If
the
oil
pan
does
not
separate
easily
from
the
engine
"
Tightenforward
oil
pan
screws
first,
then
tighten
rear
.
cylinder
block,
afew
taps
with
arubber
mallet
should
"
Fill
engine
with
oil
as
described
in
020
Maintenance
break
it
free
.
Do
not
pry
the
oil
pan
loose
.
Program
.
"
After
adding
engine
oil,
start
and
run
engine
.
Raise
en-
19
.
Remove
oil
pump
sprocket
mounting
nut
.
See
Fig
.
9
.
gine
speed
to
2,500
rpm
until
oil
pressure
warning
Lift
sprocket
off
together
with
drive
chain
.
lampgoes
out(about
5seconds)
.
Fig
.
9
.
Oil
pump
sprocket
mounting
nut
(left-hand
thread)
on
6-cylin-
OII
pan,
removing
and
installing
derengine(arrow)
.
(6-cylinder
engine,
1993
and
later
modeis)
NOTE-
The
oíl
pump
sprocket
nut
has
left
hand
threads
.
20
.
Unbolt
oil
pump
pickup
tubefrom
oil
pump
.
Unbolt
oil
pump
from
engine
block
.
See
Oil
pump,
removing
and
installing
(6-cylinder
engine)
.
21
.
Remove
oil
pan
from
rear
.
Tightening
Torques
"
Engine
mount
to
suspension
crossmember(M10
nut)
..
42
Nm
(31
ft-Ib)
"
Oil
pan
to
engine
block
(M6
bolt)
8
.8
grade
....
..
.
...
...
.
........
10
Nm
(89
in-lb)
10
.9
grade
.
.
..
.
..
...
.
.
.
.
.
.....
12
Nm
(106
in-lb)
"
Oil
pump
to
engine
block
.
...
...
.
..
22
Nm
(16
ft-Ib)
"
Oil
pump
sprocket
to
oil
pump
shaft
(M1
0x1
left-hand
thread)
...
..
.
.
..
.
25
Nm
(18
ft-Ib)
"
Power
steering
pump
to
bracket
(self-locking
nuts)
.....
.
....
..
.
...
22
Nm
(16
ft-lb)
"
Power
steering
pump
bracket
to
engine
block
or
oil
pan
(self-locking
nuts)
.
..
22
Nm
(16
ft-Ib)
NOTE-
Cars
built
after
9/92
use
a
different
suspension
cross-
member
¡han
earfier
productíon
cars
.
Oil
pan
removal
procedure
on
the
later
cars
requíres
that
the
engine
be
supported
from
aboye
and
the
front
suspension
cross-
member
be
unbolted
and
loweredfrom
the
chassis
.
1
.
Raisecar
and
place
securely
on
jackstands
.
2
.
Remove
splash
shield
fromunder
engine,
if
applicable
.
3
.
Drain
engine
oil
as
descríbed
in
020
Maintenance
Pro-
gram
.
4
.
Remove
alternator
cooling
duct
from
alternator
and
ra-
diator
support
.
Page 127 of 759
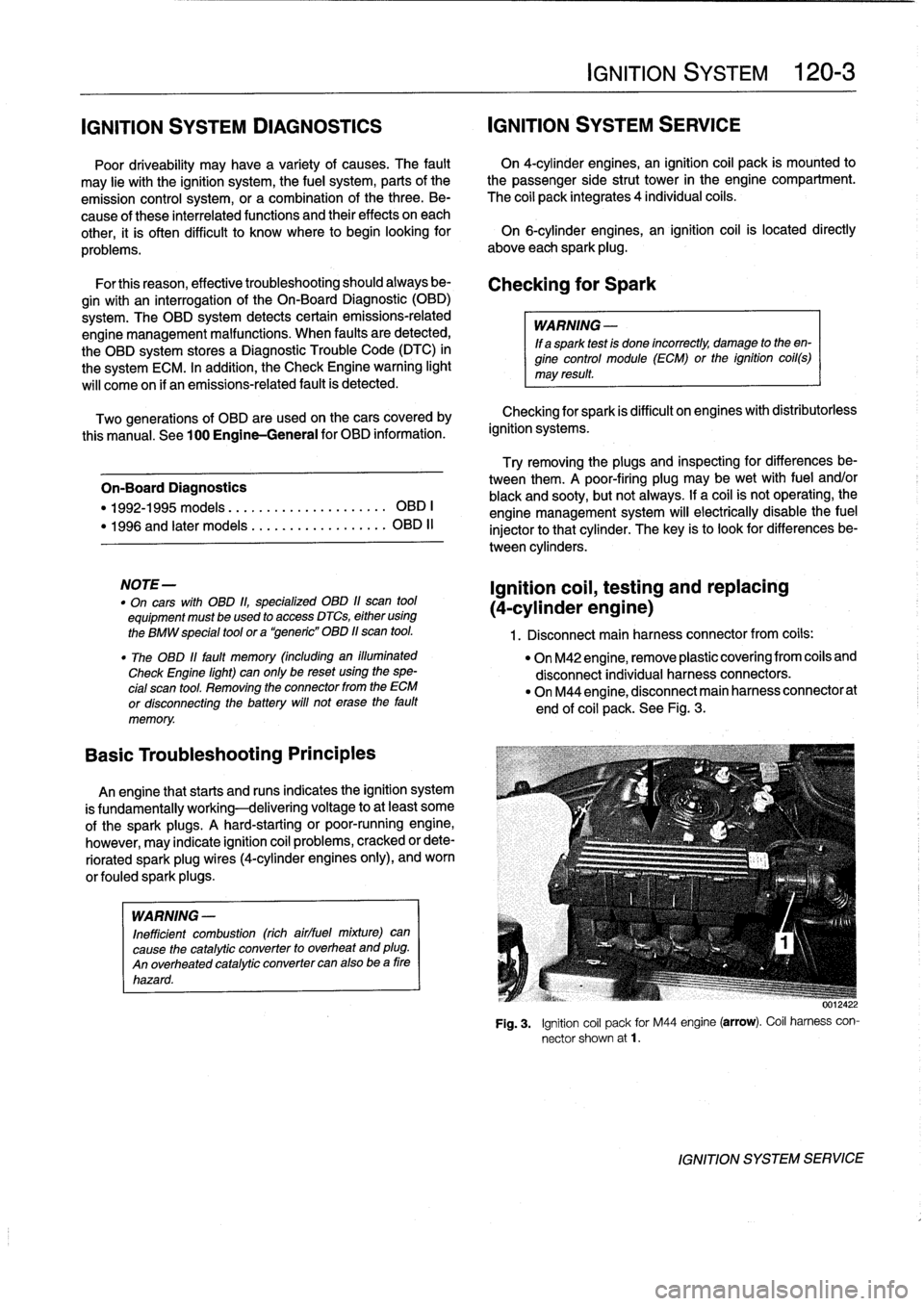
IGNITION
SYSTEM
DIAGNOSTICS
IGNITION
SYSTEM
SERVICE
Poor
driveability
may
have
a
variety
of
causes
.
The
fault
On
4-cylinder
engines,
an
ignition
coil
pack
is
mounted
to
may
lie
with
the
ignition
system,
the
fuel
system,
parts
of
the
the
passenger
side
strut
tower
in
the
engine
compartment
.
emission
control
system,
or
a
combination
of
the
three
.
Be-
The
coil
pack
integrates
4
individual
coils
.
cause
of
these
interrelated
functions
and
their
effects
oneach
other,
it
is
often
difficult
to
know
where
to
begin
looking
for
On
6-cylinder
engines,
an
ignition
coil
is
located
directly
problems
.
above
each
spark
plug
.
For
this
reason,
effective
troubleshooting
should
alwaysbe-
gin
with
an
interrogation
of
the
On-Board
Diagnostic
(OBD)
system
.
The
OBD
system
detects
certain
emissions-related
engine
management
malfunctions
.
When
faults
are
detected,
the
OBD
system
stores
a
Diagnostic
Trouble
Code
(DTC)
in
the
system
ECM
.
In
addition,
the
Check
Enginewarning
light
will
come
on
if
an
emissions-related
fault
is
detected
.
Two
generations
of
OBD
areusedon
the
cars
coveredby
this
manual
.
See
100
Engine-General
for
OBD
information
.
On-Board
Diagnostics
"
1992-1995
models
............
...
.
..
...
OBD
I
"
1996
and
later
models
.........
.......
..
OBD
II
NOTE-
"
On
carswith
OBD
ti,
specialized
OBD
11
scan
tool
equipment
mustbeused
to
access
DTCs,
either
using
the
BMW
special
tool
or
a
`generic"
OBD
11
scan
tool
.
"
The
OBD
11
fault
memory
(including
an
illuminated
Check
Engine
light)
can
only
be
reset
using
the
spe-
cial
scan
tool
.
Removing
the
connector
from
the
ECM
or
dísconnecting
the
battery
will
not
erase
the
fault
memory
.
Basic
Troubleshooting
Principies
An
engine
that
starts
and
runs
indicates
the
ignition
system
is
fundamentally
working-delivering
voltage
toat
least
some
of
the
sparkplugs
.
A
hard-starting
or
poor-running
engine,
however,
may
indicate
ignition
coil
problems,
cracked
or
dete-
riorated
spark
plug
wires
(4-cylinder
engines
only),
and
worn
or
fouled
spark
plugs
.
WARNING
-
Inefficient
combustion
(richair/fuel
mixture)
can
cause
the
catalytic
converter
to
overheat
and
plug
.
An
overheated
catalytic
converter
can
also
bea
tire
hazard
.
Checking
for
Spark
IGNITION
SYSTEM
120-
3
WARNING
-
If
a
spark
test
is
done
incorrectly,
damage
to
theen-
gine
control
module
(ECM)
or
the
ignitioncoil(s)
may
result
.
Checking
for
spark
is
difficult
onengines
with
distributorless
ignition
systems
.
Try
Rmovng
the
plugs
and
inspecting
for
differences
be-
tween
them
.
A
poor-firing
plug
may
be
wet
with
fuel
and/or
black
and
sooty,
butnot
always
.
If
a
coil
is
not
operating,
the
engine
management
system
will
electrically
disable
the
fuel
injectorto
that
cylinder
.
The
key
is
to
look
for
differences
be-
tween
cylinders
.
Ignition
coil,
testing
and
replacing
(4-cylinder
engine)
1.
Disconnect
mainharness
connector
from
coils
:
"
On
M42
engine,
remove
plastic
covering
from
coils
and
disconnect
individual
harness
connectors
.
"
On
M44
engine,
disconnect
main
harness
connectorat
end
of
coil
pack
.
See
Fig
.
3
.
Fig
.
3
.
Ignition
coil
pack
for
M44
engine
(arrow)
.
Coil
harness
con-
nector
shown
at1
.
IGNITION
SYSTEM
SERVICE
Page 128 of 759
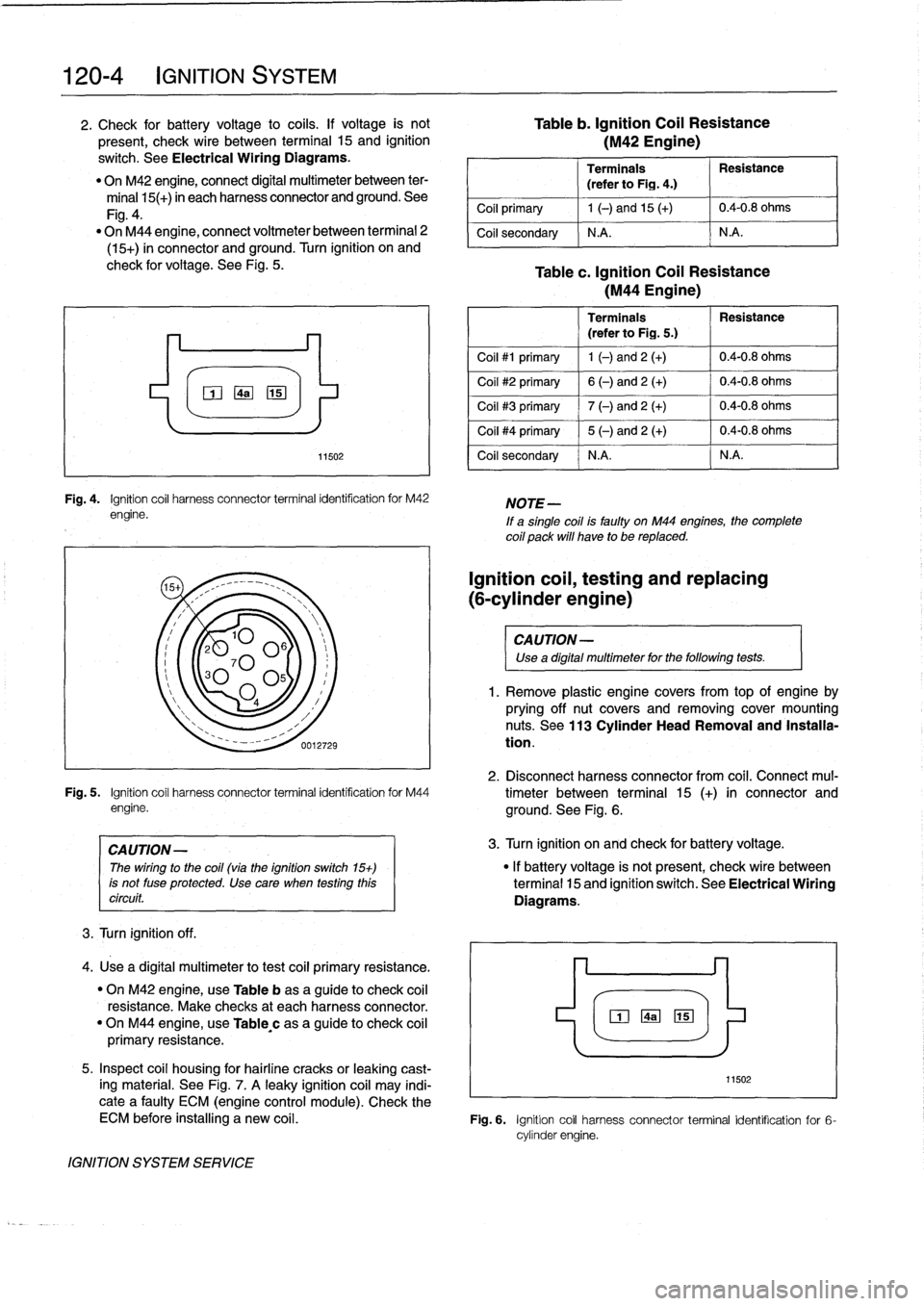
120-
4
IGNITION
SYSTEM
2
.
Check
for
battery
voltage
o
cofs
.
If
voltage
is
not
Table
b
.
Ignition
Coil
Resistance
present,
check
wire
between
terminal
15
and
ignition
(M42
Engine)
switch
.
See
Electrical
Wiring
Diagrams
.
"
On
M42
engine,
connect
digital
multimeter
between
ter-
minal
15(+)
in
each
harness
connector
and
ground
.
See
Fig
.
4
.
"
On
M44
engine,
connect
voltmeter
between
terminal
2
(15+)
in
connector
and
ground
.
Turn
ignition
on
and
check
for
voltage
.
See
Fig
.
5
.
3
.
Turn
ignition
off
.
0
4a15
Fig
.
4
.
Ignition
coil
harness
connector
terminal
identification
for
M42
engine
.
Fig
.
5
.
Ignition
coil
harness
connector
terminal
identification
for
M44
engine
.
CAUTION-
The
wiring
to
the
coil(via
the
ignition
switch
15+)
is
not
fuse
protected
.
Use
care
when
testing
thiscircuit
.
4
.
Use
a
digital
multimeter
totest
coil
primary
resistance
.
"
On
M42
engine,
use
Table
b
asa
guide
to
check
coil
resistance
.
Make
checks
at
each
harness
connector
.
"
On
M44
engine,
use
Table,c
as
a
guide
to
check
coil
primary
resistance
.
5
.
Inspect
coil
housing
for
hairline
cracks
or
leaking
cast-
ing
material
.
See
Fig
.
7
.
A
leaky
ignition
coil
may
indi-
11502
cate
a
faulty
ECM
(engine
control
module)
.
Check
the
ECM
before
installing
a
new
coil
.
Fig
.
6
.
Ignition
coil
harnessconnector
terminal
identification
for
6-
cylinder
engine
.
IGNITION
SYSTEM
SERVICE
11502
Terminals
Resistance
(refer
to
Fig
.
4
.)
Coil
primary
1
(-)
and
15
(+)
10
.4-0
.8
ohms
Coil
secondary
N
.A
.
N
.A
.
Table
c
.
Ignition
Coil
Resistance
(M44
Engine)
Terminais
Resistance
(referto
Fig
.
5
.)
Coil
#1
primary
1
(-)
and
2
(+)
0
.4-0
.8
ohms
Coil
#2
primary
6
(-)
and2
(+)
0
.4-0
.8
ohms
Coil
#3
primary
7
(-)
and
2
(+)
0
.4-0
.8
ohms
Coil
#4
primary
5
(-)
and2
(+)
0
.4-0
.8
ohms
Coil
secondary
N
.A
.
N
.A
.
NOTE-
If
a
single
coilís
faulty
on
M44
engines,
the
complete
coil
pack
will
have
to
be
replaced
.
Ignition
coil,
testing
and
replacing
(6-cylinder
engine)
CAUTION-
Use
a
digital
multimeter
for
the
following
tests
.
1.
Remove
plastic
enginecovers
from
top
of
engine
by
prying
off
nut
covers
and
removingcover
mounting
nuts
.
See
113
Cylinder
HeadRemoval
and
Installa-
tion
.
2
.
Disconnect
harnessconnectorfromcof
.
Connect
mul-
timeter
between
terminal
15
(+)
in
connector
and
ground
.
See
Fig
.
6
.
3
.
Turn
ignition
on
and
check
for
batteryvoltage
.
"
If
batteryvoltage
is
not
present,
check
wire
between
terminal
15
and
ignition
switch
.
See
Electrical
Wiring
Diagrams
.
"mozo
Page 130 of 759
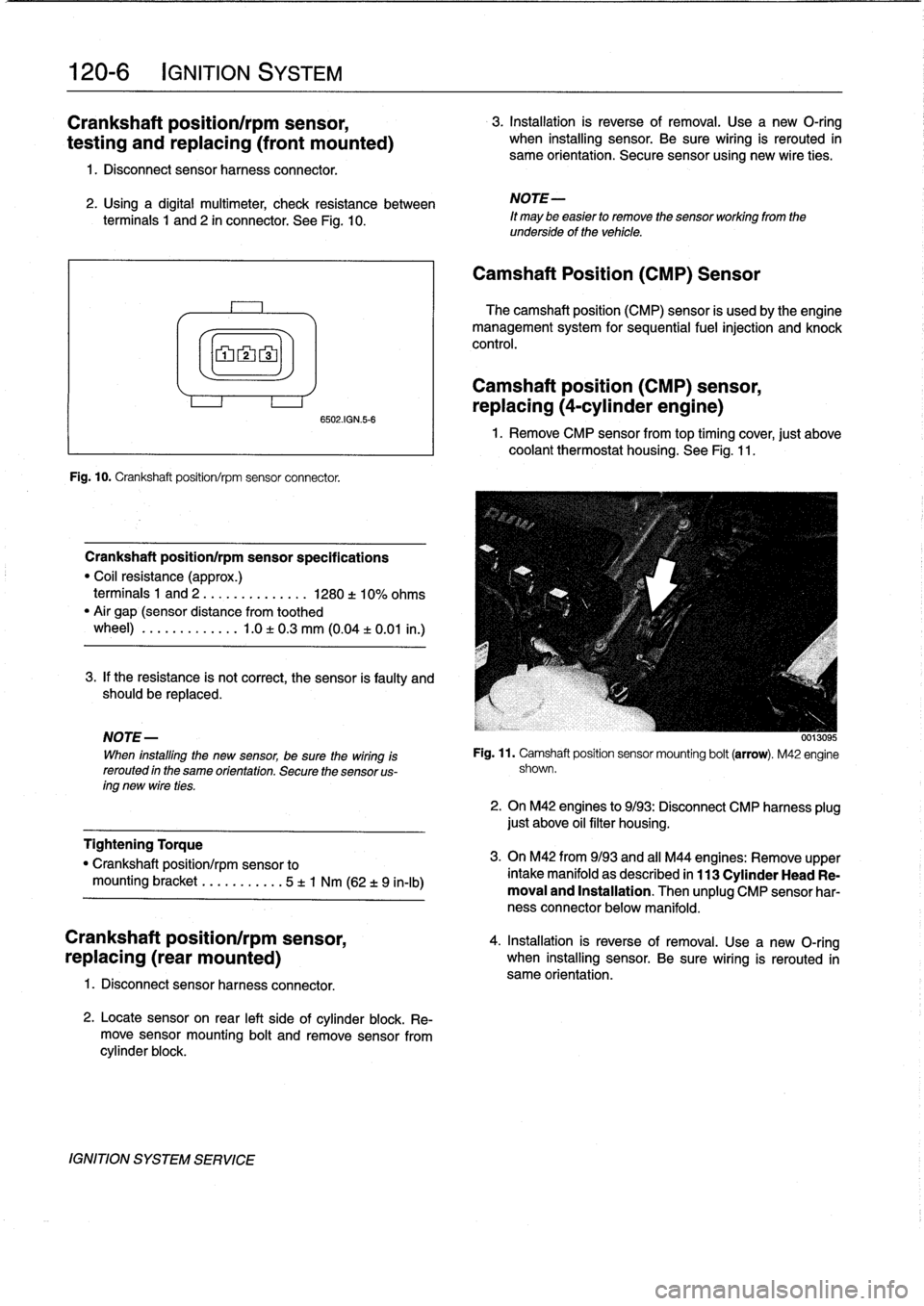
120-
6
IGNITION
SYSTEM
Crankshaft
position/rpm
sensor,
testing
and
replacing
(front
mounted)
1
.
Disconnect
sensor
harness
connector
.
2
.
Using
a
digital
multimeter,
check
resistance
between
terminals
1
and
2
in
connector
.
See
Fig
.
10
.
n1
n2n3
Fig
.
10
.
Crankshaft
position/rpm
sensorconnector
.
Crankshaft
positionlrpm
sensor
specifications
"
Coil
resistance
(approx
.)
terminais
1
and
2
....
.
..
...
....
1280
±
10%
ohms
"
Air
gap
(sensor
distance
from
toothed
wheel)
..
.
.
........
.1
.0
±
0
.3
mm
(0
.04
±
0
.01
in
.)
3
.
If
the
resistance
is
not
correct,
the
sensor
is
faulty
and
should
be
replaced
.
NOTE
-
When
installing
the
new
sensor,
be
sure
thewiring
Is
rerouted
in
the
same
orientation
.
Secure
the
sensor
us-
ing
new
wire
ties
.
Tightening
Torque
"
Crankshaft
position/rpm
sensor
to
mounting
bracket
.........
.
.
5
t
1
Nm
(62
t
9
in-lb)
Crankshaft
position/rpm
sensor,
4
.
Installation
is
reverse
of
removal
.
Use
a
new
O-ring
replacing
(rear
mounted)
when
installing
sensor
.
Be
sure
wiring
is
rerouted
in
same
orientation
.
1
.
Disconnect
sensor
harness
connector
.
6502AGN56
2
.
Locatesensor
on
rear
left
sideof
cylinder
block
.
Re-
move
sensormounting
bolt
and
remove
sensorfrom
cylinder
block
.
IGNITION
SYSTEM
SERVICE
3
.
Installation
is
reverse
of
removal
.
Use
a
new
O-ring
when
installing
sensor
.
Be
sure
wiring
is
rerouted
in
same
orientation
.
Secure
sensor
using
new
wire
ties
.
NOTE-
It
may
be
easier
to
remove
the
sensor
working
from
the
underside
of
the
vehicle
.
Camshaft
Position
(CMP)
Sensor
The
camshaft
position
(CMP)
sensor
is
usedby
the
engine
management
system
for
sequential
fuel
injection
and
knock
control
.
Camshaft
position
(CMP)
sensor,
replacing
(4-cylinder
engine)
1
.
Remove
CMP
sensorfromtop
timing
cover,
just
above
coolantthermostat
housing
.
See
Fig
.
11
.
Fig
.
11
.
Camshaft
position
sensor
mounting
bolt
(arrow)
.
M42
engine
shown
.
2
.
On
M42
engines
to
9/93
:
Disconnect
CMP
harness
plug
just
above
oil
filter
housing
.
3
.
On
M42
from9/93
and
all
M44
engines
:
Remove
upper
intake
manifold
as
described
in
113
Cylinder
Head
Re-
moval
and
Installation
.
Then
unplug
CMP
sensor
har-
ness
connector
below
manifold
.