reset CHERY TIGGO 2009 Service Repair Manual
[x] Cancel search | Manufacturer: CHERY, Model Year: 2009, Model line: TIGGO, Model: CHERY TIGGO 2009Pages: 1903, PDF Size: 33.38 MB
Page 306 of 1903
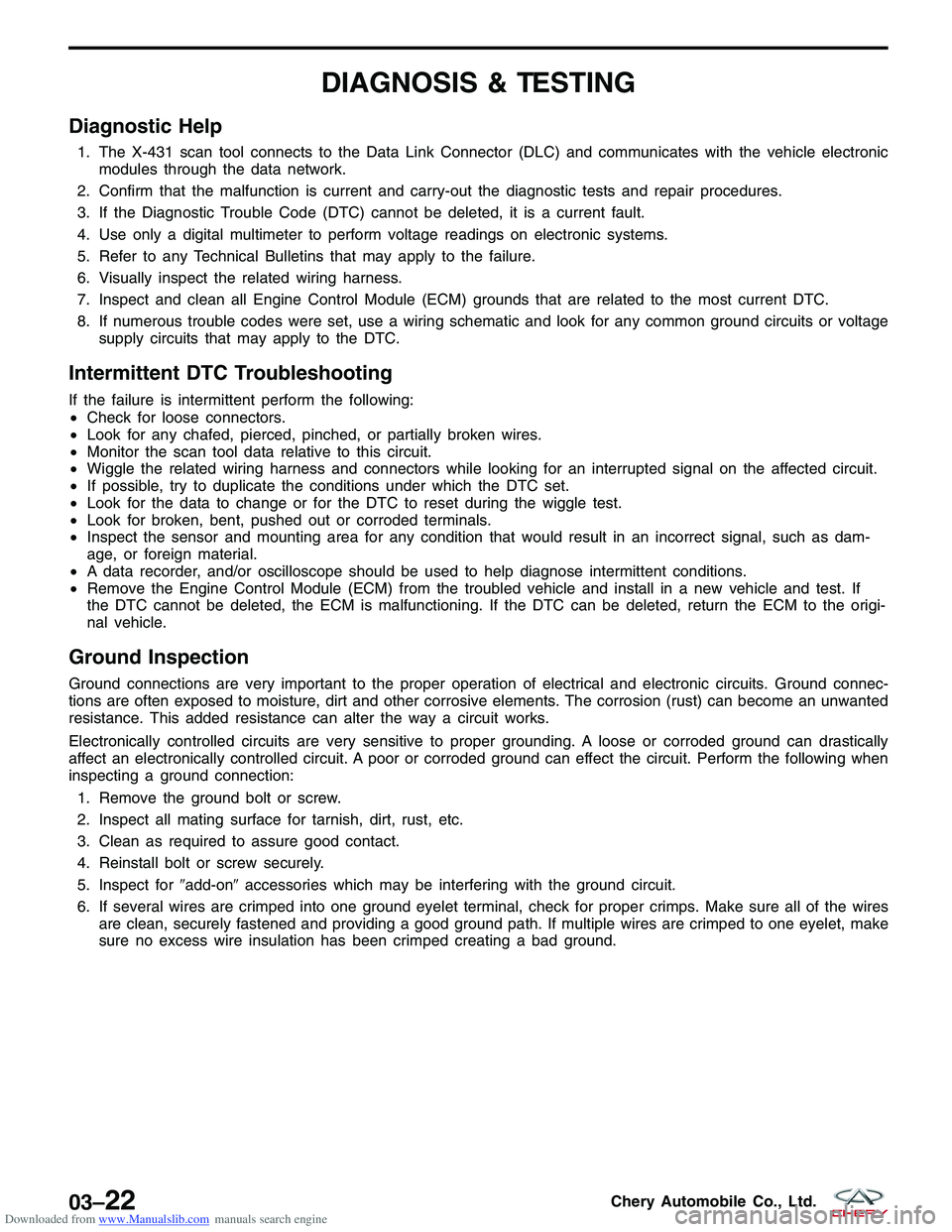
Downloaded from www.Manualslib.com manuals search engine DIAGNOSIS & TESTING
Diagnostic Help
1. The X-431 scan tool connects to the Data Link Connector (DLC) and communicates with the vehicle electronicmodules through the data network.
2. Confirm that the malfunction is current and carry-out the diagnostic tests and repair procedures.
3. If the Diagnostic Trouble Code (DTC) cannot be deleted, it is a current fault.
4. Use only a digital multimeter to perform voltage readings on electronic systems.
5. Refer to any Technical Bulletins that may apply to the failure.
6. Visually inspect the related wiring harness.
7. Inspect and clean all Engine Control Module (ECM) grounds that are related to the most current DTC.
8. If numerous trouble codes were set, use a wiring schematic and look for any common ground circuits or voltage supply circuits that may apply to the DTC.
Intermittent DTC Troubleshooting
If the failure is intermittent perform the following:
•Check for loose connectors.
• Look for any chafed, pierced, pinched, or partially broken wires.
• Monitor the scan tool data relative to this circuit.
• Wiggle the related wiring harness and connectors while looking for an interrupted signal on the affected circuit.
• If possible, try to duplicate the conditions under which the DTC set.
• Look for the data to change or for the DTC to reset during the wiggle test.
• Look for broken, bent, pushed out or corroded terminals.
• Inspect the sensor and mounting area for any condition that would result in an incorrect signal, such as dam-
age, or foreign material.
• A data recorder, and/or oscilloscope should be used to help diagnose intermittent conditions.
• Remove the Engine Control Module (ECM) from the troubled vehicle and install in a new vehicle and test. If
the DTC cannot be deleted, the ECM is malfunctioning. If the DTC can be deleted, return the ECM to the origi-
nal vehicle.
Ground Inspection
Ground connections are very important to the proper operation of electrical and electronic circuits. Ground connec-
tions are often exposed to moisture, dirt and other corrosive elements. The corrosion (rust) can become an unwanted
resistance. This added resistance can alter the way a circuit works.
Electronically controlled circuits are very sensitive to proper grounding. A loose or corroded ground can drastically
affect an electronically controlled circuit. A poor or corroded ground can effect the circuit. Perform the following when
inspecting a ground connection:
1. Remove the ground bolt or screw.
2. Inspect all mating surface for tarnish, dirt, rust, etc.
3. Clean as required to assure good contact.
4. Reinstall bolt or screw securely.
5. Inspect for add-onaccessories which may be interfering with the ground circuit.
6. If several wires are crimped into one ground eyelet terminal, check for proper crimps. Make sure all of the wires are clean, securely fastened and providing a good ground path. If multiple wires are crimped to one eyelet, make
sure no excess wire insulation has been crimped creating a bad ground.
03–22Chery Automobile Co., Ltd.
Page 531 of 1903
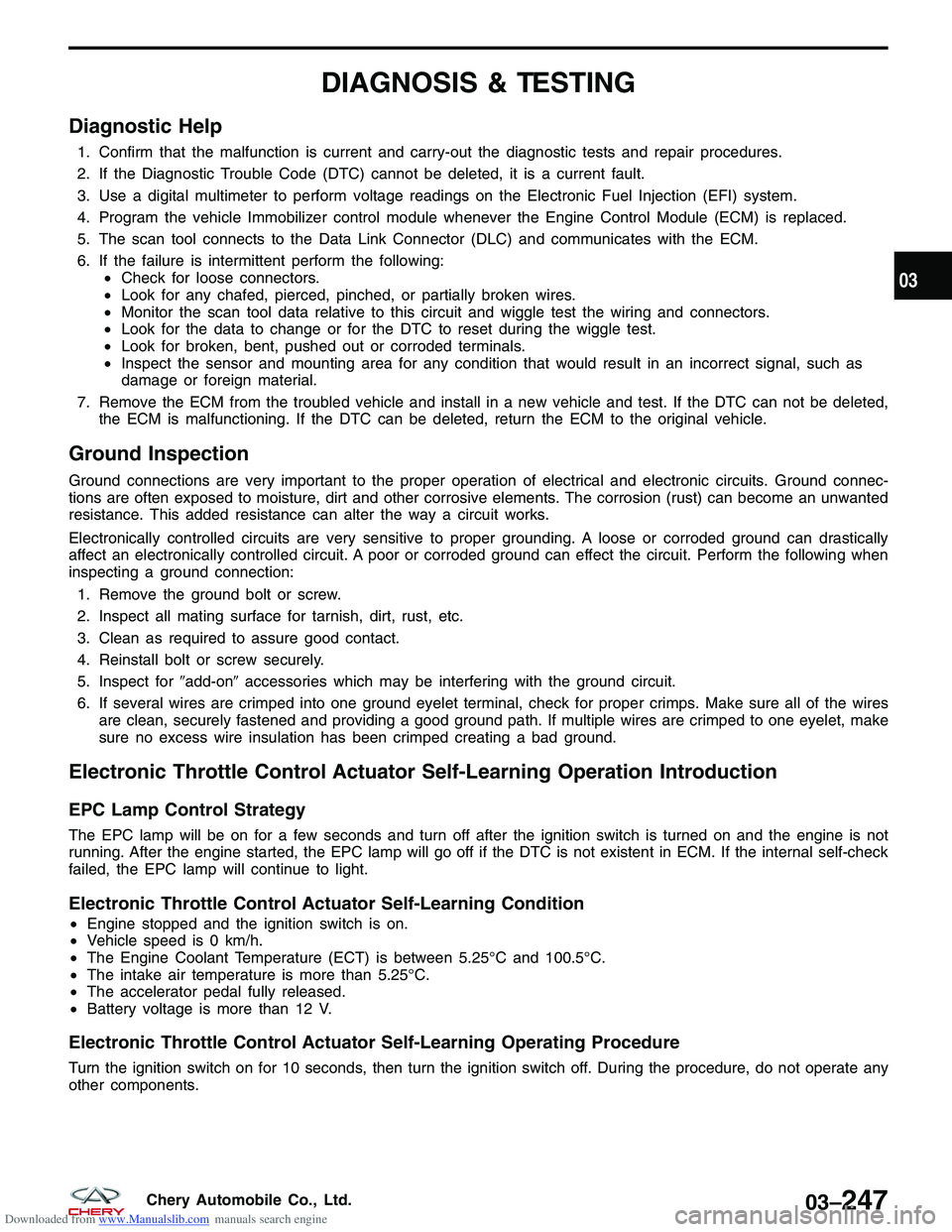
Downloaded from www.Manualslib.com manuals search engine DIAGNOSIS & TESTING
Diagnostic Help
1. Confirm that the malfunction is current and carry-out the diagnostic tests and repair procedures.
2. If the Diagnostic Trouble Code (DTC) cannot be deleted, it is a current fault.
3. Use a digital multimeter to perform voltage readings on the Electronic Fuel Injection (EFI) system.
4. Program the vehicle Immobilizer control module whenever the Engine Control Module (ECM) is replaced.
5. The scan tool connects to the Data Link Connector (DLC) and communicates with the ECM.
6. If the failure is intermittent perform the following:•Check for loose connectors.
• Look for any chafed, pierced, pinched, or partially broken wires.
• Monitor the scan tool data relative to this circuit and wiggle test the wiring and connectors.
• Look for the data to change or for the DTC to reset during the wiggle test.
• Look for broken, bent, pushed out or corroded terminals.
• Inspect the sensor and mounting area for any condition that would result in an incorrect signal, such as
damage or foreign material.
7. Remove the ECM from the troubled vehicle and install in a new vehicle and test. If the DTC can not be deleted, the ECM is malfunctioning. If the DTC can be deleted, return the ECM to the original vehicle.
Ground Inspection
Ground connections are very important to the proper operation of electrical and electronic circuits. Ground connec-
tions are often exposed to moisture, dirt and other corrosive elements. The corrosion (rust) can become an unwanted
resistance. This added resistance can alter the way a circuit works.
Electronically controlled circuits are very sensitive to proper grounding. A loose or corroded ground can drastically
affect an electronically controlled circuit. A poor or corroded ground can effect the circuit. Perform the following when
inspecting a ground connection:
1. Remove the ground bolt or screw.
2. Inspect all mating surface for tarnish, dirt, rust, etc.
3. Clean as required to assure good contact.
4. Reinstall bolt or screw securely.
5. Inspect for add-onaccessories which may be interfering with the ground circuit.
6. If several wires are crimped into one ground eyelet terminal, check for proper crimps. Make sure all of the wires are clean, securely fastened and providing a good ground path. If multiple wires are crimped to one eyelet, make
sure no excess wire insulation has been crimped creating a bad ground.
Electronic Throttle Control Actuator Self-Learning Operation Introduction
EPC Lamp Control Strategy
The EPC lamp will be on for a few seconds and turn off after the ignition switch is turned on and the engine is not
running. After the engine started, the EPC lamp will go off if the DTC is not existent in ECM. If the internal self-check
failed, the EPC lamp will continue to light.
Electronic Throttle Control Actuator Self-Learning Condition
•Engine stopped and the ignition switch is on.
• Vehicle speed is 0 km/h.
• The Engine Coolant Temperature (ECT) is between 5.25°C and 100.5°C.
• The intake air temperature is more than 5.25°C.
• The accelerator pedal fully released.
• Battery voltage is more than 12 V.
Electronic Throttle Control Actuator Self-Learning Operating Procedure
Turn the ignition switch on for 10 seconds, then turn the ignition switch off. During the procedure, do not operate any
other components.
03
03–247Chery Automobile Co., Ltd.
Page 742 of 1903
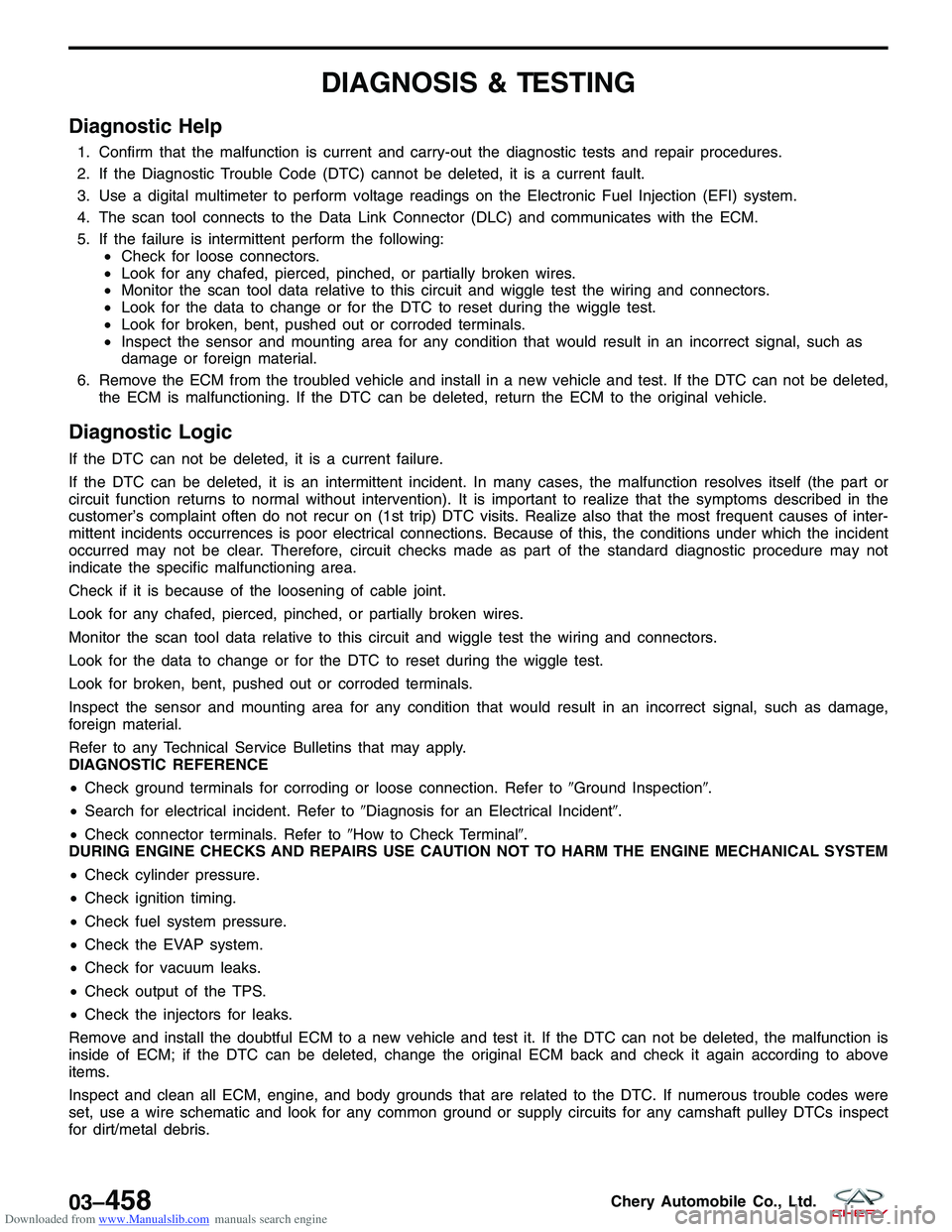
Downloaded from www.Manualslib.com manuals search engine DIAGNOSIS & TESTING
Diagnostic Help
1. Confirm that the malfunction is current and carry-out the diagnostic tests and repair procedures.
2. If the Diagnostic Trouble Code (DTC) cannot be deleted, it is a current fault.
3. Use a digital multimeter to perform voltage readings on the Electronic Fuel Injection (EFI) system.
4. The scan tool connects to the Data Link Connector (DLC) and communicates with the ECM.
5. If the failure is intermittent perform the following:•Check for loose connectors.
• Look for any chafed, pierced, pinched, or partially broken wires.
• Monitor the scan tool data relative to this circuit and wiggle test the wiring and connectors.
• Look for the data to change or for the DTC to reset during the wiggle test.
• Look for broken, bent, pushed out or corroded terminals.
• Inspect the sensor and mounting area for any condition that would result in an incorrect signal, such as
damage or foreign material.
6. Remove the ECM from the troubled vehicle and install in a new vehicle and test. If the DTC can not be deleted, the ECM is malfunctioning. If the DTC can be deleted, return the ECM to the original vehicle.
Diagnostic Logic
If the DTC can not be deleted, it is a current failure.
If the DTC can be deleted, it is an intermittent incident. In many cases, the malfunction resolves itself (the part or
circuit function returns to normal without intervention). It is important to realize that the symptoms described in the
customer’s complaint often do not recur on (1st trip) DTC visits. Realize also that the most frequent causes of inter-
mittent incidents occurrences is poor electrical connections. Because of this, the conditions under which the incident
occurred may not be clear. Therefore, circuit checks made as part of the standard diagnostic procedure may not
indicate the specific malfunctioning area.
Check if it is because of the loosening of cable joint.
Look for any chafed, pierced, pinched, or partially broken wires.
Monitor the scan tool data relative to this circuit and wiggle test the wiring and connectors.
Look for the data to change or for the DTC to reset during the wiggle test.
Look for broken, bent, pushed out or corroded terminals.
Inspect the sensor and mounting area for any condition that would result in an incorrect signal, such as damage,
foreign material.
Refer to any Technical Service Bulletins that may apply.
DIAGNOSTIC REFERENCE
•Check ground terminals for corroding or loose connection. Refer to Ground Inspection.
• Search for electrical incident. Refer to Diagnosis for an Electrical Incident.
• Check connector terminals. Refer to How to Check Terminal.
DURING ENGINE CHECKS AND REPAIRS USE CAUTION NOT TO HARM THE ENGINE MECHANICAL SYSTEM
• Check cylinder pressure.
• Check ignition timing.
• Check fuel system pressure.
• Check the EVAP system.
• Check for vacuum leaks.
• Check output of the TPS.
• Check the injectors for leaks.
Remove and install the doubtful ECM to a new vehicle and test it. If the DTC can not be deleted, the malfunction is
inside of ECM; if the DTC can be deleted, change the original ECM back and check it again according to above
items.
Inspect and clean all ECM, engine, and body grounds that are related to the DTC. If numerous trouble codes were
set, use a wire schematic and look for any common ground or supply circuits for any camshaft pulley DTCs inspect
for dirt/metal debris.
03–458Chery Automobile Co., Ltd.
Page 810 of 1903
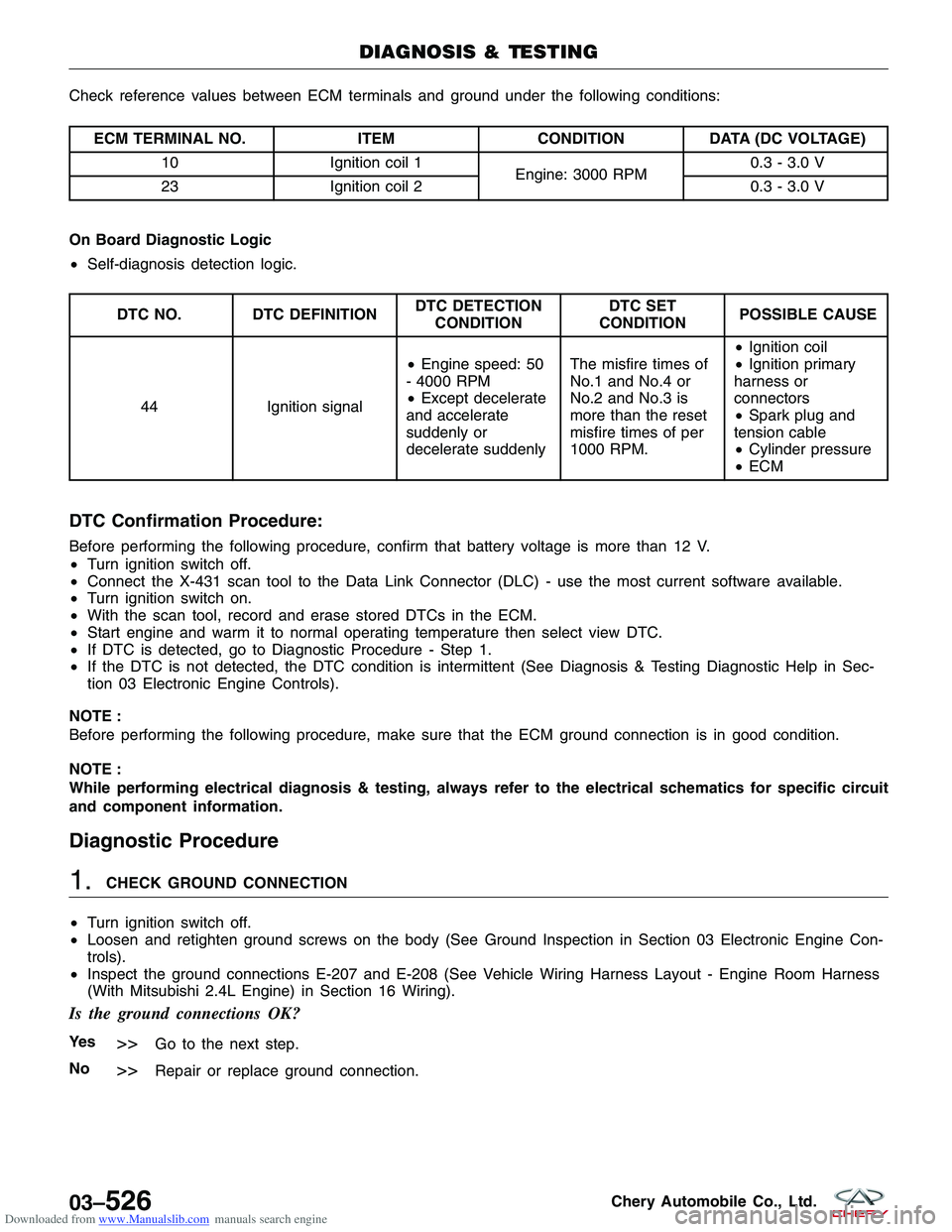
Downloaded from www.Manualslib.com manuals search engine Check reference values between ECM terminals and ground under the following conditions:
ECM TERMINAL NO.ITEMCONDITIONDATA (DC VOLTAGE)
10 Ignition coil 1
Engine: 3000 RPM 0.3 - 3.0 V
23 Ignition coil 2 0.3 - 3.0 V
On Board Diagnostic Logic
• Self-diagnosis detection logic.
DTC NO. DTC DEFINITION DTC DETECTION
CONDITION DTC SET
CONDITION POSSIBLE CAUSE
44 Ignition signal •
Engine speed: 50
- 4000 RPM
• Except decelerate
and accelerate
suddenly or
decelerate suddenly The misfire times of
No.1 and No.4 or
No.2 and No.3 is
more than the reset
misfire times of per
1000 RPM.•
Ignition coil
• Ignition primary
harness or
connectors
• Spark plug and
tension cable
• Cylinder pressure
• ECM
DTC Confirmation Procedure:
Before performing the following procedure, confirm that battery voltage is more than 12 V.
• Turn ignition switch off.
• Connect the X-431 scan tool to the Data Link Connector (DLC) - use the most current software available.
• Turn ignition switch on.
• With the scan tool, record and erase stored DTCs in the ECM.
• Start engine and warm it to normal operating temperature then select view DTC.
• If DTC is detected, go to Diagnostic Procedure - Step 1.
• If the DTC is not detected, the DTC condition is intermittent (See Diagnosis & Testing Diagnostic Help in Sec-
tion 03 Electronic Engine Controls).
NOTE :
Before performing the following procedure, make sure that the ECM ground connection is in good condition.
NOTE :
While performing electrical diagnosis & testing, always refer to the electrical schematics for specific circuit
and component information.
Diagnostic Procedure
1.CHECK GROUND CONNECTION
• Turn ignition switch off.
• Loosen and retighten ground screws on the body (See Ground Inspection in Section 03 Electronic Engine Con-
trols).
• Inspect the ground connections E-207 and E-208 (See Vehicle Wiring Harness Layout - Engine Room Harness
(With Mitsubishi 2.4L Engine) in Section 16 Wiring).
Is the ground connections OK?
Ye s>>Go to the next step.
No
>>Repair or replace ground connection.
DIAGNOSIS & TESTING
03–526Chery Automobile Co., Ltd.
Page 962 of 1903
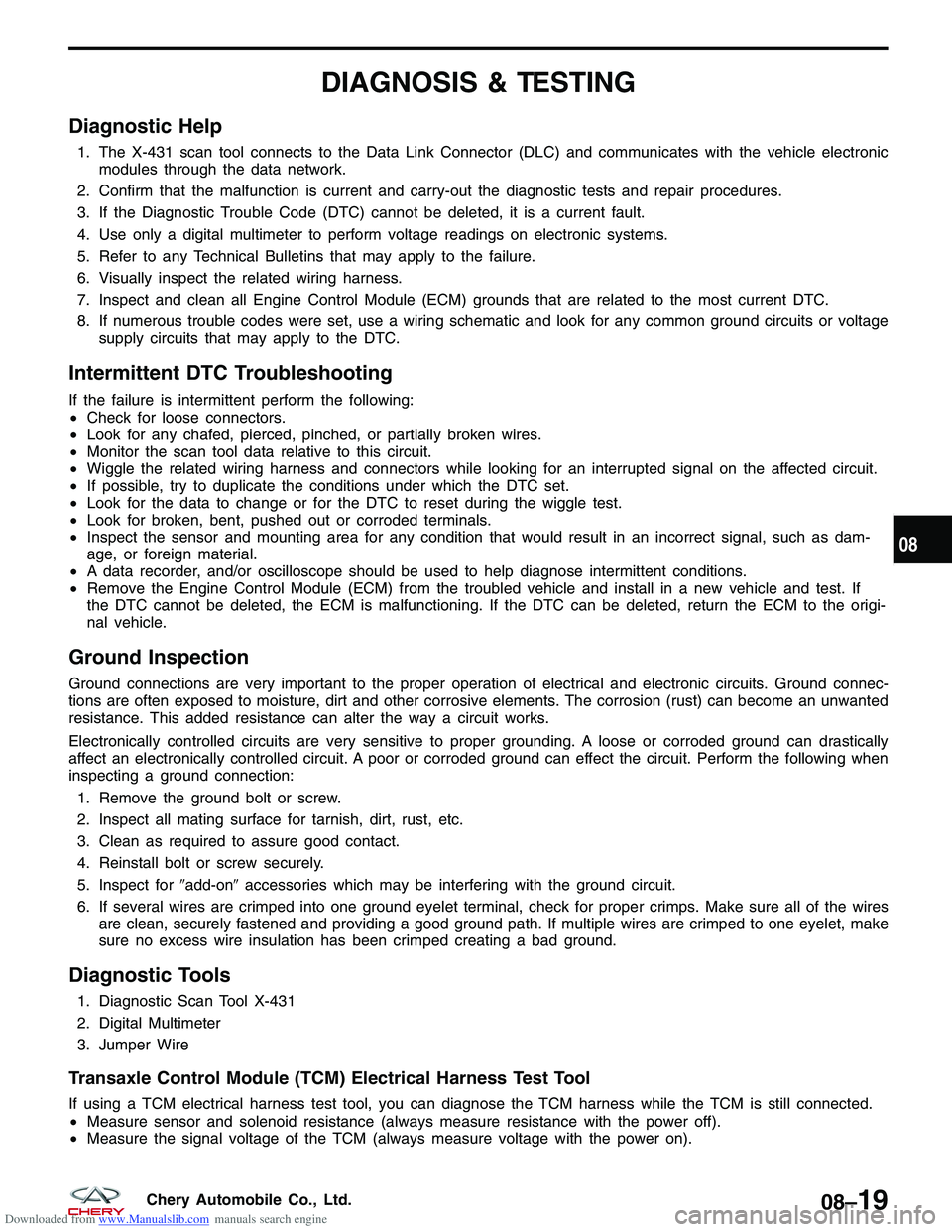
Downloaded from www.Manualslib.com manuals search engine DIAGNOSIS & TESTING
Diagnostic Help
1. The X-431 scan tool connects to the Data Link Connector (DLC) and communicates with the vehicle electronicmodules through the data network.
2. Confirm that the malfunction is current and carry-out the diagnostic tests and repair procedures.
3. If the Diagnostic Trouble Code (DTC) cannot be deleted, it is a current fault.
4. Use only a digital multimeter to perform voltage readings on electronic systems.
5. Refer to any Technical Bulletins that may apply to the failure.
6. Visually inspect the related wiring harness.
7. Inspect and clean all Engine Control Module (ECM) grounds that are related to the most current DTC.
8. If numerous trouble codes were set, use a wiring schematic and look for any common ground circuits or voltage supply circuits that may apply to the DTC.
Intermittent DTC Troubleshooting
If the failure is intermittent perform the following:
•Check for loose connectors.
• Look for any chafed, pierced, pinched, or partially broken wires.
• Monitor the scan tool data relative to this circuit.
• Wiggle the related wiring harness and connectors while looking for an interrupted signal on the affected circuit.
• If possible, try to duplicate the conditions under which the DTC set.
• Look for the data to change or for the DTC to reset during the wiggle test.
• Look for broken, bent, pushed out or corroded terminals.
• Inspect the sensor and mounting area for any condition that would result in an incorrect signal, such as dam-
age, or foreign material.
• A data recorder, and/or oscilloscope should be used to help diagnose intermittent conditions.
• Remove the Engine Control Module (ECM) from the troubled vehicle and install in a new vehicle and test. If
the DTC cannot be deleted, the ECM is malfunctioning. If the DTC can be deleted, return the ECM to the origi-
nal vehicle.
Ground Inspection
Ground connections are very important to the proper operation of electrical and electronic circuits. Ground connec-
tions are often exposed to moisture, dirt and other corrosive elements. The corrosion (rust) can become an unwanted
resistance. This added resistance can alter the way a circuit works.
Electronically controlled circuits are very sensitive to proper grounding. A loose or corroded ground can drastically
affect an electronically controlled circuit. A poor or corroded ground can effect the circuit. Perform the following when
inspecting a ground connection:
1. Remove the ground bolt or screw.
2. Inspect all mating surface for tarnish, dirt, rust, etc.
3. Clean as required to assure good contact.
4. Reinstall bolt or screw securely.
5. Inspect for add-onaccessories which may be interfering with the ground circuit.
6. If several wires are crimped into one ground eyelet terminal, check for proper crimps. Make sure all of the wires are clean, securely fastened and providing a good ground path. If multiple wires are crimped to one eyelet, make
sure no excess wire insulation has been crimped creating a bad ground.
Diagnostic Tools
1. Diagnostic Scan Tool X-431
2. Digital Multimeter
3. Jumper Wire
Transaxle Control Module (TCM) Electrical Harness Test Tool
If using a TCM electrical harness test tool, you can diagnose the TCM harness while the TCM is still connected.
•Measure sensor and solenoid resistance (always measure resistance with the power off).
• Measure the signal voltage of the TCM (always measure voltage with the power on).
08
08–19Chery Automobile Co., Ltd.
Page 974 of 1903
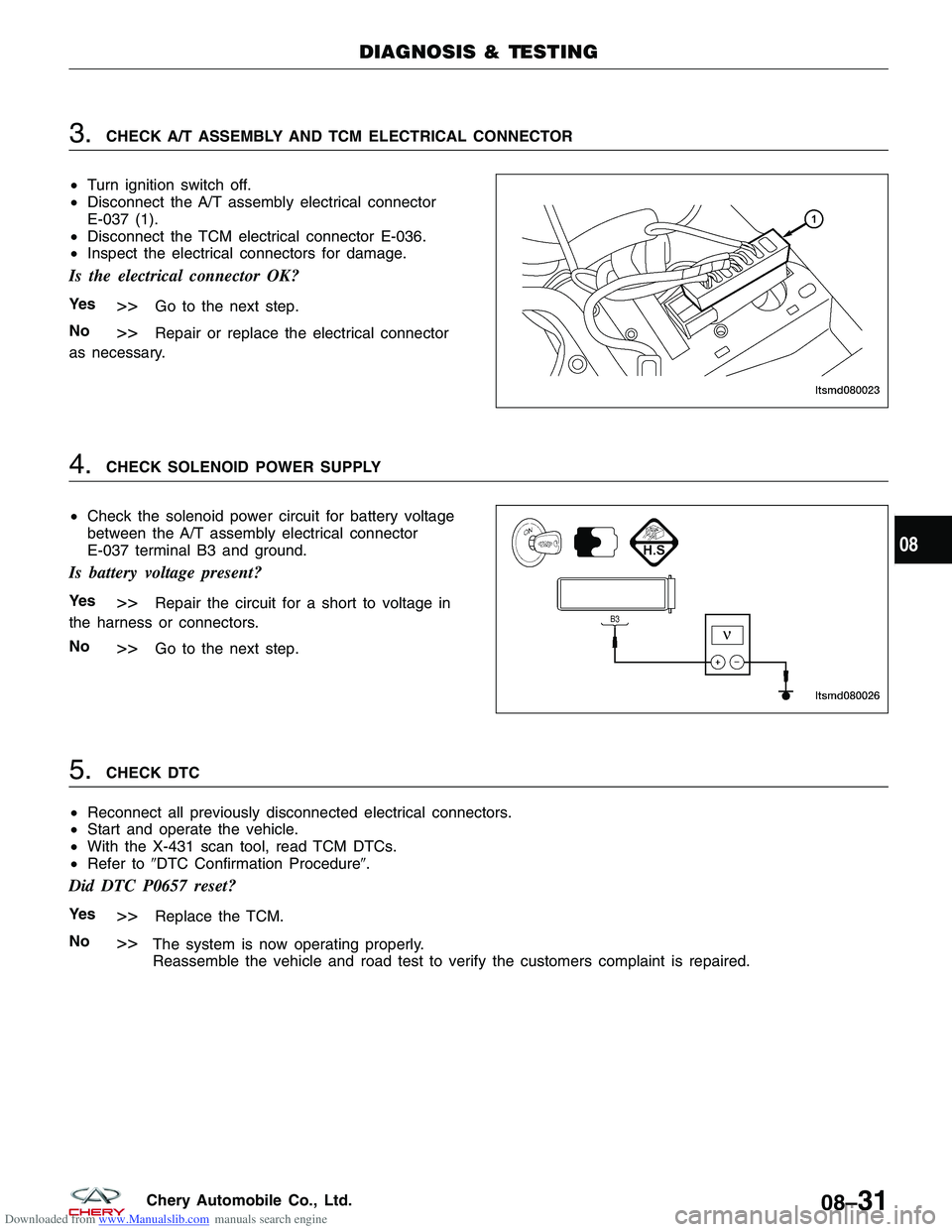
Downloaded from www.Manualslib.com manuals search engine 3.CHECK A/T ASSEMBLY AND TCM ELECTRICAL CONNECTOR
• Turn ignition switch off.
• Disconnect the A/T assembly electrical connector
E-037 (1).
• Disconnect the TCM electrical connector E-036.
• Inspect the electrical connectors for damage.
Is the electrical connector OK?
Ye s>>Go to the next step.
No
>>Repair or replace the electrical connector
as necessary.
4.CHECK SOLENOID POWER SUPPLY
• Check the solenoid power circuit for battery voltage
between the A/T assembly electrical connector
E-037 terminal B3 and ground.
Is battery voltage present?
Ye s>>Repair the circuit for a short to voltage in
the harness or connectors.
No
>>Go to the next step.
5.CHECK DTC
• Reconnect all previously disconnected electrical connectors.
• Start and operate the vehicle.
• With the X-431 scan tool, read TCM DTCs.
• Refer to DTC Confirmation Procedure.
Did DTC P0657 reset?
Ye s>>Replace the TCM.
No
>>The system is now operating properly.
Reassemble the vehicle and road test to verify the customers complaint is repaired.
DIAGNOSIS & TESTING
LTSMD080023
LTSMD080026
08
08–31Chery Automobile Co., Ltd.
Page 1101 of 1903
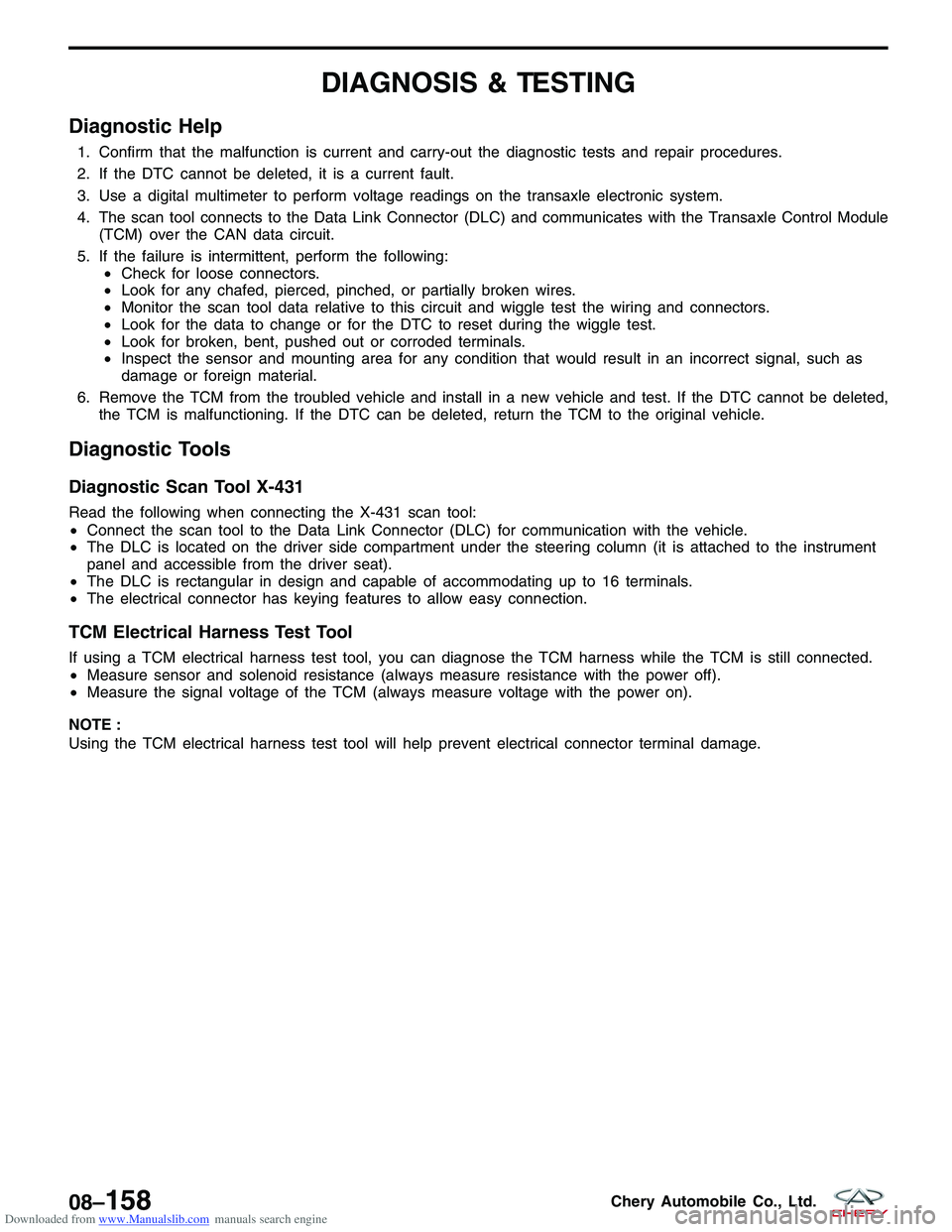
Downloaded from www.Manualslib.com manuals search engine DIAGNOSIS & TESTING
Diagnostic Help
1. Confirm that the malfunction is current and carry-out the diagnostic tests and repair procedures.
2. If the DTC cannot be deleted, it is a current fault.
3. Use a digital multimeter to perform voltage readings on the transaxle electronic system.
4. The scan tool connects to the Data Link Connector (DLC) and communicates with the Transaxle Control Module(TCM) over the CAN data circuit.
5. If the failure is intermittent, perform the following: •Check for loose connectors.
• Look for any chafed, pierced, pinched, or partially broken wires.
• Monitor the scan tool data relative to this circuit and wiggle test the wiring and connectors.
• Look for the data to change or for the DTC to reset during the wiggle test.
• Look for broken, bent, pushed out or corroded terminals.
• Inspect the sensor and mounting area for any condition that would result in an incorrect signal, such as
damage or foreign material.
6. Remove the TCM from the troubled vehicle and install in a new vehicle and test. If the DTC cannot be deleted, the TCM is malfunctioning. If the DTC can be deleted, return the TCM to the original vehicle.
Diagnostic Tools
Diagnostic Scan Tool X-431
Read the following when connecting the X-431 scan tool:
•Connect the scan tool to the Data Link Connector (DLC) for communication with the vehicle.
• The DLC is located on the driver side compartment under the steering column (it is attached to the instrument
panel and accessible from the driver seat).
• The DLC is rectangular in design and capable of accommodating up to 16 terminals.
• The electrical connector has keying features to allow easy connection.
TCM Electrical Harness Test Tool
If using a TCM electrical harness test tool, you can diagnose the TCM harness while the TCM is still connected.
•Measure sensor and solenoid resistance (always measure resistance with the power off).
• Measure the signal voltage of the TCM (always measure voltage with the power on).
NOTE :
Using the TCM electrical harness test tool will help prevent electrical connector terminal damage.
08–158Chery Automobile Co., Ltd.
Page 1307 of 1903
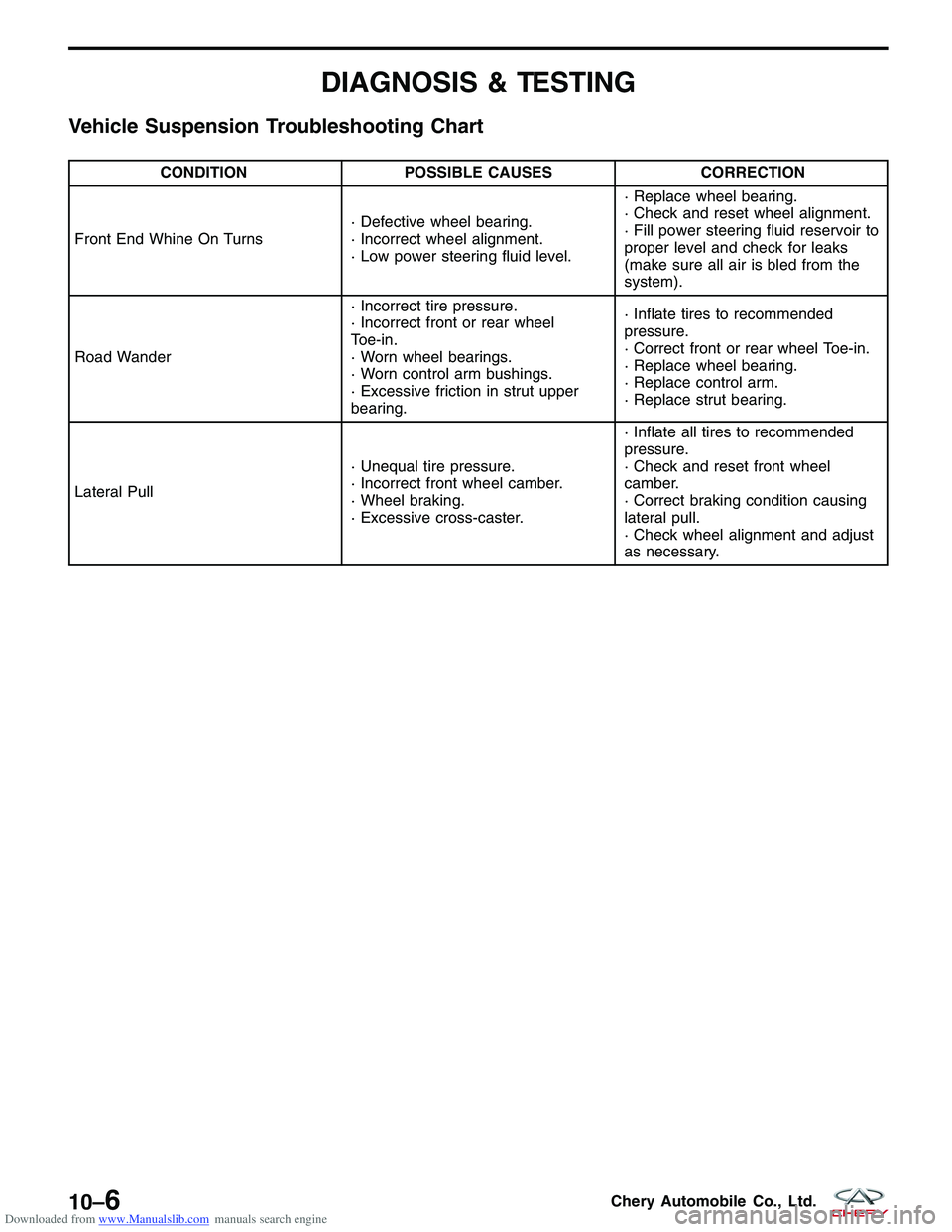
Downloaded from www.Manualslib.com manuals search engine DIAGNOSIS & TESTING
Vehicle Suspension Troubleshooting Chart
CONDITIONPOSSIBLE CAUSES CORRECTION
Front End Whine On Turns · Defective wheel bearing.
· Incorrect wheel alignment.
· Low power steering fluid level.· Replace wheel bearing.
· Check and reset wheel alignment.
· Fill power steering fluid reservoir to
proper level and check for leaks
(make sure all air is bled from the
system).
Road Wander · Incorrect tire pressure.
· Incorrect front or rear wheel
Toe-in.
· Worn wheel bearings.
· Worn control arm bushings.
· Excessive friction in strut upper
bearing.· Inflate tires to recommended
pressure.
· Correct front or rear wheel Toe-in.
· Replace wheel bearing.
· Replace control arm.
· Replace strut bearing.
Lateral Pull · Unequal tire pressure.
· Incorrect front wheel camber.
· Wheel braking.
· Excessive cross-caster.· Inflate all tires to recommended
pressure.
· Check and reset front wheel
camber.
· Correct braking condition causing
lateral pull.
· Check wheel alignment and adjust
as necessary.
10–6Chery Automobile Co., Ltd.
Page 1379 of 1903
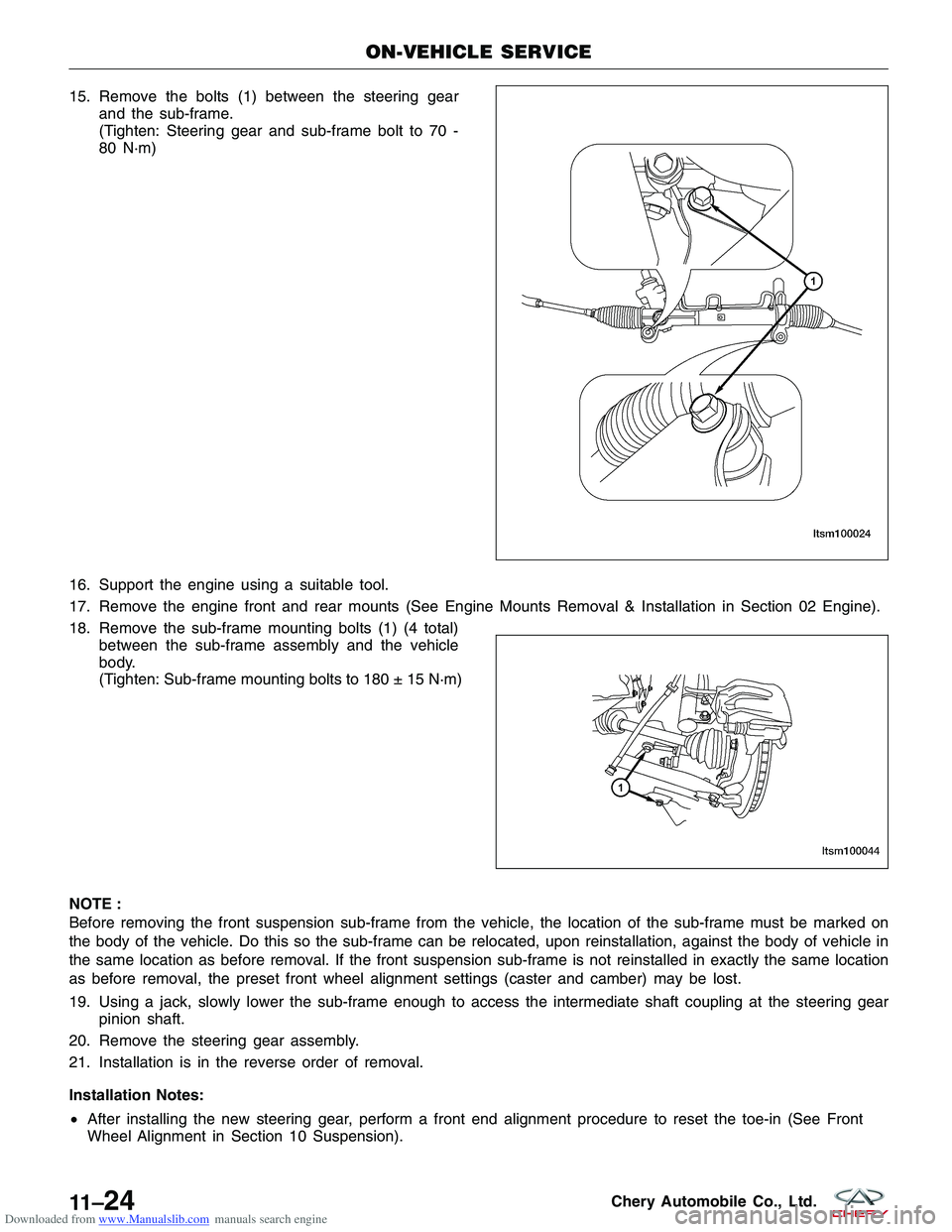
Downloaded from www.Manualslib.com manuals search engine 15. Remove the bolts (1) between the steering gearand the sub-frame.
(Tighten: Steering gear and sub-frame bolt to 70 -
80 N·m)
16. Support the engine using a suitable tool.
17. Remove the engine front and rear mounts (See Engine Mounts Removal & Installation in Section 02 Engine).
18. Remove the sub-frame mounting bolts (1) (4 total) between the sub-frame assembly and the vehicle
body.
(Tighten: Sub-frame mounting bolts to 180 ± 15 N·m)
180 ± 15 N·m)
NOTE :
Before removing the front suspension sub-frame from the vehicle, the location of the sub-frame must be marked on
the body of the vehicle. Do this so the sub-frame can be relocated, upon reinstallation, against the body of vehicle in
the same location as before removal. If the front suspension sub-frame is not reinstalled in exactly the same location
as before removal, the preset front wheel alignment settings (caster and camber) may be lost.
19. Using a jack, slowly lower the sub-frame enough to access the intermediate shaft coupling at the steering gear pinion shaft.
20. Remove the steering gear assembly.
21. Installation is in the reverse order of removal.
Installation Notes:
• After installing the new steering gear, perform a front end alignment procedure to reset the toe-in (See Front
Wheel Alignment in Section 10 Suspension).
ON-VEHICLE SERVICE
LTSM100024
LTSM100044
11 –24Chery Automobile Co., Ltd.
Page 1383 of 1903
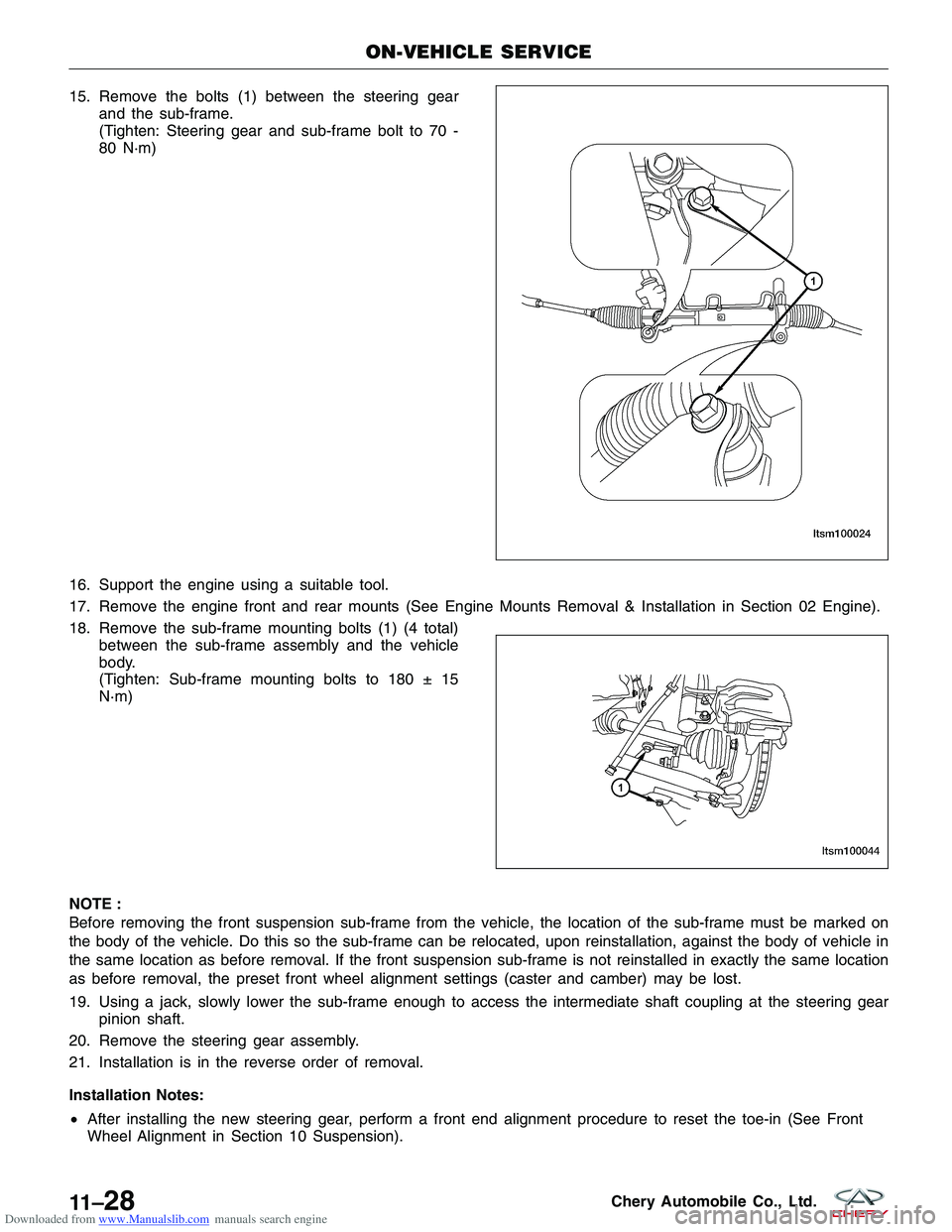
Downloaded from www.Manualslib.com manuals search engine 15. Remove the bolts (1) between the steering gearand the sub-frame.
(Tighten: Steering gear and sub-frame bolt to 70 -
80 N·m)
16. Support the engine using a suitable tool.
17. Remove the engine front and rear mounts (See Engine Mounts Removal & Installation in Section 02 Engine).
18. Remove the sub-frame mounting bolts (1) (4 total) between the sub-frame assembly and the vehicle
body.
(Tighten: Sub-frame mounting bolts to 180 ± 15
N·m)
NOTE :
Before removing the front suspension sub-frame from the vehicle, the location of the sub-frame must be marked on
the body of the vehicle. Do this so the sub-frame can be relocated, upon reinstallation, against the body of vehicle in
the same location as before removal. If the front suspension sub-frame is not reinstalled in exactly the same location
as before removal, the preset front wheel alignment settings (caster and camber) may be lost.
19. Using a jack, slowly lower the sub-frame enough to access the intermediate shaft coupling at the steering gear pinion shaft.
20. Remove the steering gear assembly.
21. Installation is in the reverse order of removal.
Installation Notes:
• After installing the new steering gear, perform a front end alignment procedure to reset the toe-in (See Front
Wheel Alignment in Section 10 Suspension).
ON-VEHICLE SERVICE
LTSM100024
LTSM100044
11 –28Chery Automobile Co., Ltd.