CHEVROLET PLYMOUTH ACCLAIM 1993 Service Manual
Manufacturer: CHEVROLET, Model Year: 1993, Model line: PLYMOUTH ACCLAIM, Model: CHEVROLET PLYMOUTH ACCLAIM 1993Pages: 2438, PDF Size: 74.98 MB
Page 101 of 2438
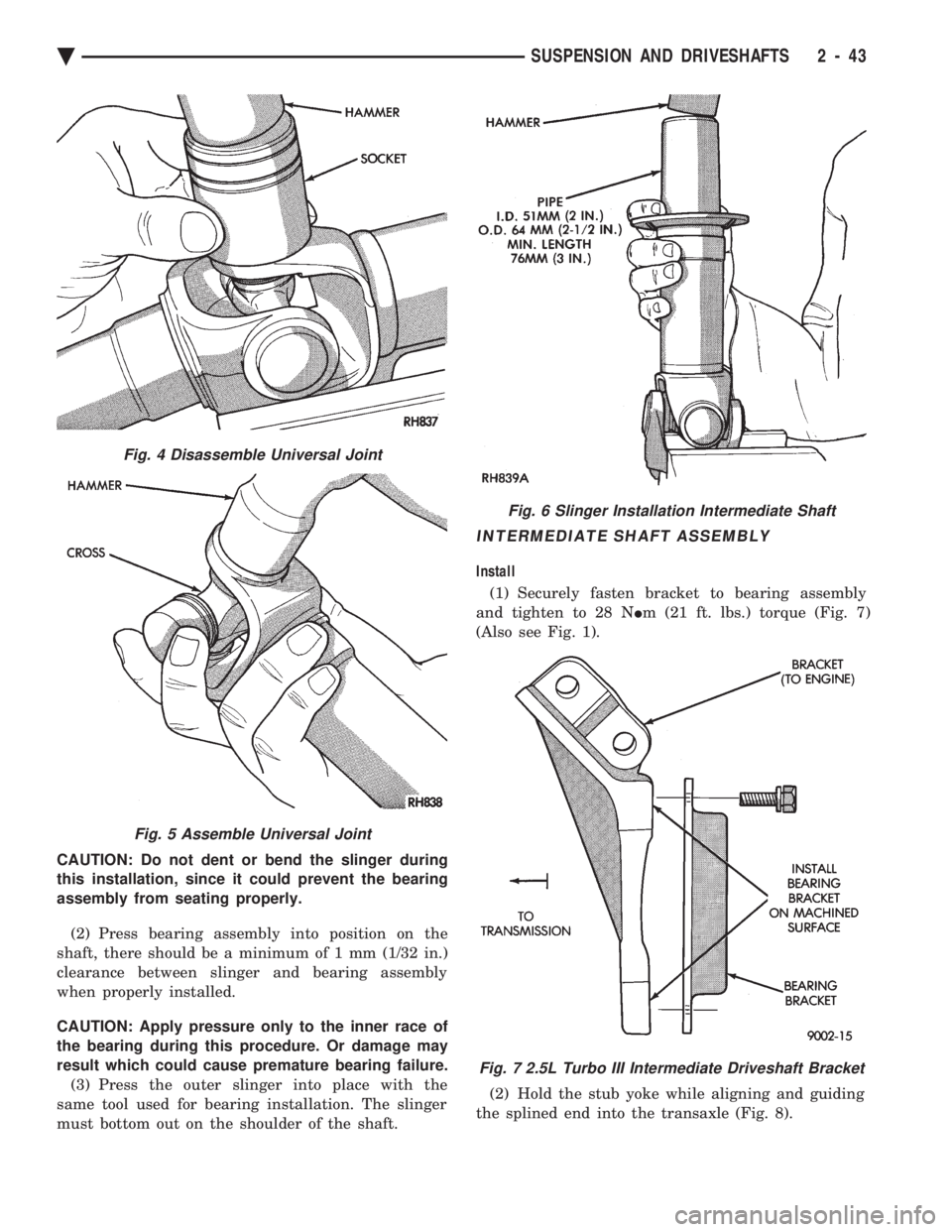
CAUTION: Do not dent or bend the slinger during
this installation, since it could prevent the bearing
assembly from seating properly. (2) Press bearing assembly into position on the
shaft, there should be a minimum of 1 mm (1/32 in.)
clearance between slinger and bearing assembly
when properly installed.
CAUTION: Apply pressure only to the inner race of
the bearing during this procedure. Or damage may
result which could cause premature bearing failure. (3) Press the outer slinger into place with the
same tool used for bearing installation. The slinger
must bottom out on the shoulder of the shaft.
INTERMEDIATE SHAFT ASSEMBLY
Install
(1) Securely fasten bracket to bearing assembly
and tighten to 28 N Im (21 ft. lbs.) torque (Fig. 7)
(Also see Fig. 1).
(2) Hold the stub yoke while aligning and guiding
the splined end into the transaxle (Fig. 8).
Fig. 4 Disassemble Universal Joint
Fig. 5 Assemble Universal Joint
Fig. 6 Slinger Installation Intermediate Shaft
Fig. 7 2.5L Turbo III Intermediate Driveshaft Bracket
Ä SUSPENSION AND DRIVESHAFTS 2 - 43
Page 102 of 2438
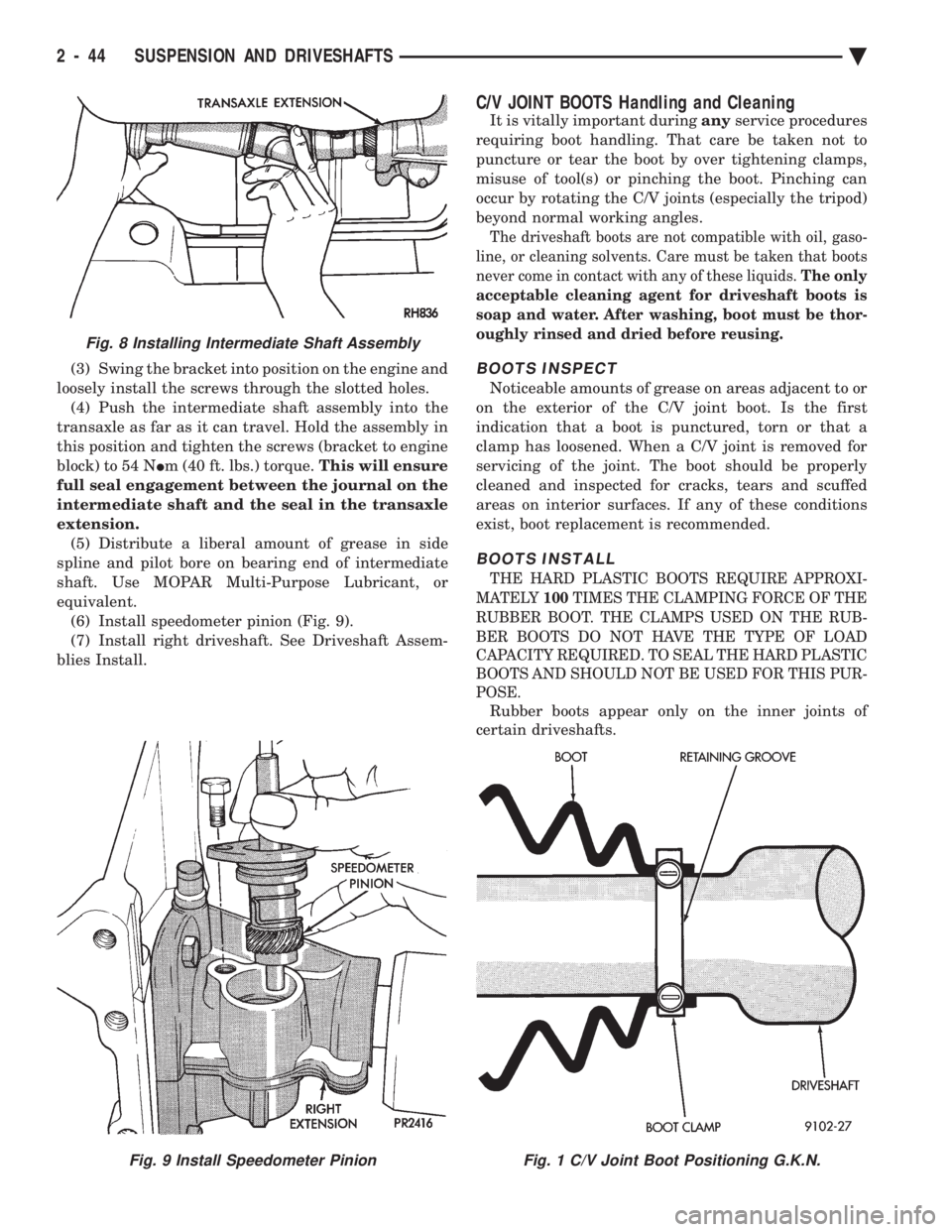
(3) Swing the bracket into position on the engine and
loosely install the screws through the slotted holes. (4) Push the intermediate shaft assembly into the
transaxle as far as it can travel. Hold the assembly in
this position and tighten the screws (bracket to engine
block) to 54 N Im (40 ft. lbs.) torque. This will ensure
full seal engagement between the journal on the
intermediate shaft and the seal in the transaxle
extension. (5) Distribute a liberal amount of grease in side
spline and pilot bore on bearing end of intermediate
shaft. Use MOPAR Multi-Purpose Lubricant, or
equivalent. (6) Install speedometer pinion (Fig. 9).
(7) Install right driveshaft. See Driveshaft Assem-
blies Install.
C/V JOINT BOOTS Handling and Cleaning
It is vitally important during anyservice procedures
requiring boot handling. That care be taken not to
puncture or tear the boot by over tightening clamps,
misuse of tool(s) or pinching the boot. Pinching can
occur by rotating the C/V joints (especially the tripod)
beyond normal working angles.
The driveshaft boots are not compatible with oil, gaso-
line, or cleaning solvents. Care must be taken that boots
never come in contact with any of these liquids. The only
acceptable cleaning agent for driveshaft boots is
soap and water. After washing, boot must be thor-
oughly rinsed and dried before reusing.
BOOTS INSPECT
Noticeable amounts of grease on areas adjacent to or
on the exterior of the C/V joint boot. Is the first
indication that a boot is punctured, torn or that a
clamp has loosened. When a C/V joint is removed for
servicing of the joint. The boot should be properly
cleaned and inspected for cracks, tears and scuffed
areas on interior surfaces. If any of these conditions
exist, boot replacement is recommended.
BOOTS INSTALL
THE HARD PLASTIC BOOTS REQUIRE APPROXI-
MATELY 100TIMES THE CLAMPING FORCE OF THE
RUBBER BOOT. THE CLAMPS USED ON THE RUB-
BER BOOTS DO NOT HAVE THE TYPE OF LOAD
CAPACITY REQUIRED. TO SEAL THE HARD PLASTIC
BOOTS AND SHOULD NOT BE USED FOR THIS PUR-
POSE.
Rubber boots appear only on the inner joints of
certain driveshafts.
Fig. 9 Install Speedometer PinionFig. 1 C/V Joint Boot Positioning G.K.N.
Fig. 8 Installing Intermediate Shaft Assembly
2 - 44 SUSPENSION AND DRIVESHAFTS Ä
Page 103 of 2438
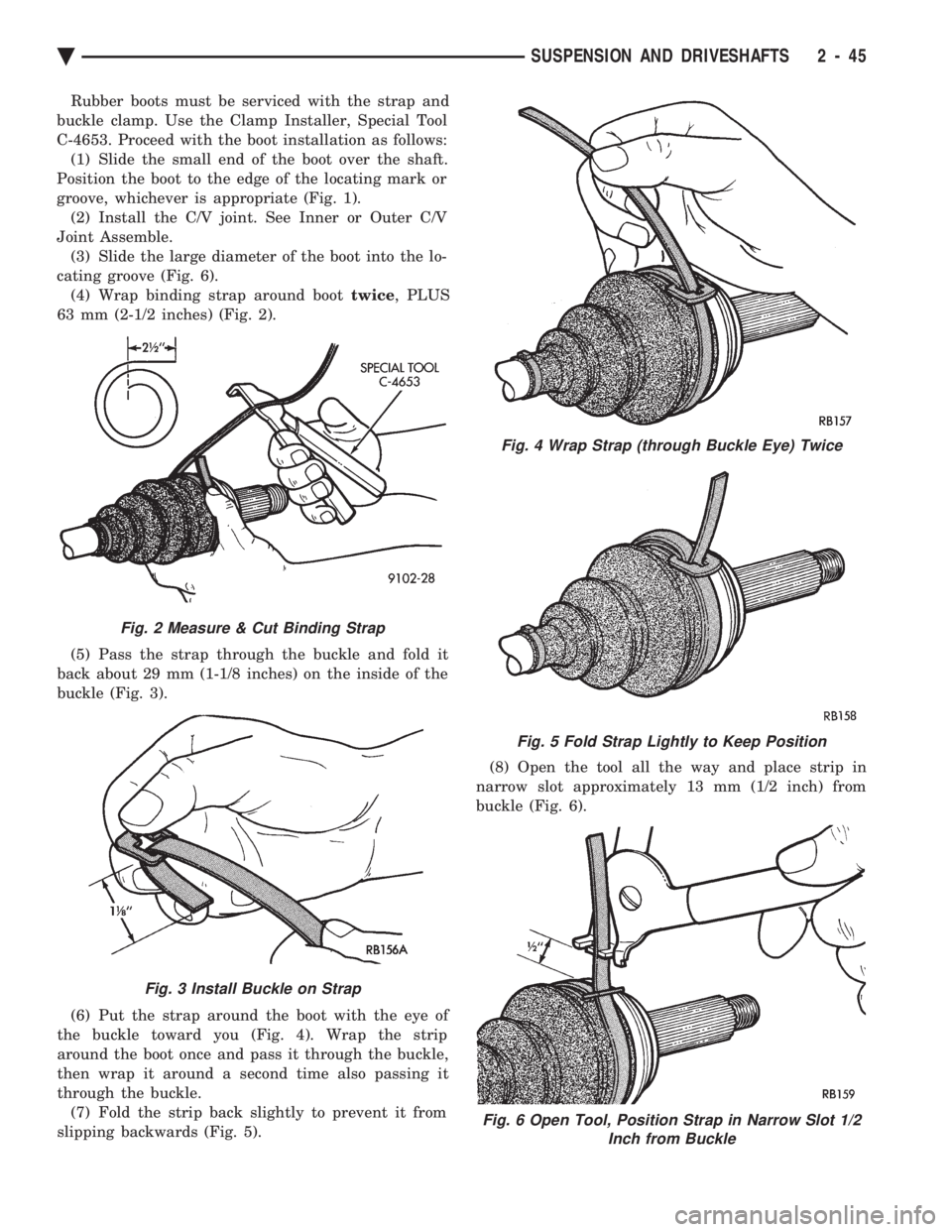
Rubber boots must be serviced with the strap and
buckle clamp. Use the Clamp Installer, Special Tool
C-4653. Proceed with the boot installation as follows: (1) Slide the small end of the boot over the shaft.
Position the boot to the edge of the locating mark or
groove, whichever is appropriate (Fig. 1). (2) Install the C/V joint. See Inner or Outer C/V
Joint Assemble. (3) Slide the large diameter of the boot into the lo-
cating groove (Fig. 6). (4) Wrap binding strap around boot twice, PLUS
63 mm (2-1/2 inches) (Fig. 2).
(5) Pass the strap through the buckle and fold it
back about 29 mm (1-1/8 inches) on the inside of the
buckle (Fig. 3).
(6) Put the strap around the boot with the eye of
the buckle toward you (Fig. 4). Wrap the strip
around the boot once and pass it through the buckle,
then wrap it around a second time also passing it
through the buckle. (7) Fold the strip back slightly to prevent it from
slipping backwards (Fig. 5). (8) Open the tool all the way and place strip in
narrow slot approximately 13 mm (1/2 inch) from
buckle (Fig. 6).
Fig. 2 Measure & Cut Binding Strap
Fig. 3 Install Buckle on Strap
Fig. 4 Wrap Strap (through Buckle Eye) Twice
Fig. 5 Fold Strap Lightly to Keep Position
Fig. 6 Open Tool, Position Strap in Narrow Slot 1/2 Inch from Buckle
Ä SUSPENSION AND DRIVESHAFTS 2 - 45
Page 104 of 2438
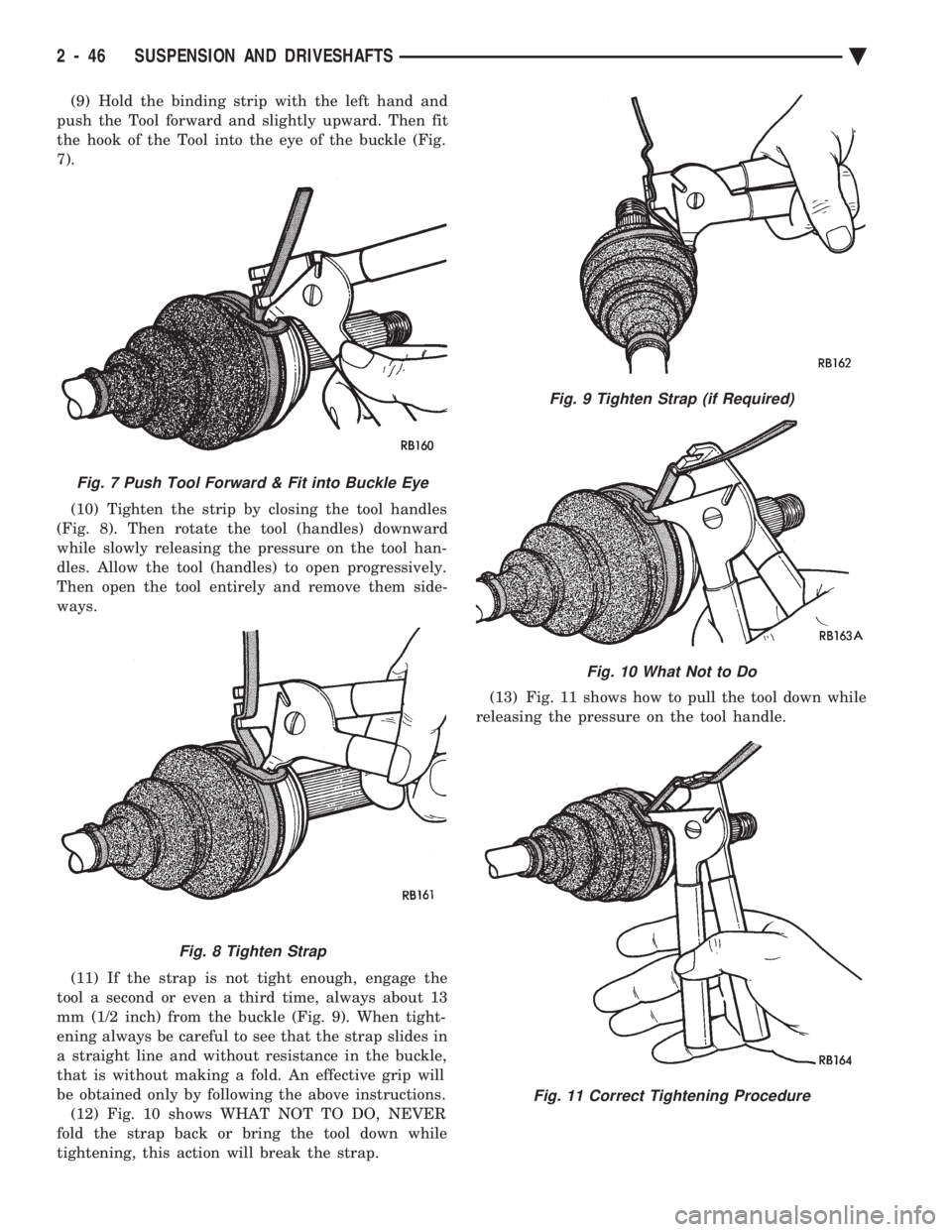
(9) Hold the binding strip with the left hand and
push the Tool forward and slightly upward. Then fit
the hook of the Tool into the eye of the buckle (Fig.
7).
(10) Tighten the strip by closing the tool handles
(Fig. 8). Then rotate the tool (handles) downward
while slowly releasing the pressure on the tool han-
dles. Allow the tool (handles) to open progressively.
Then open the tool entirely and remove them side-
ways.
(11) If the strap is not tight enough, engage the
tool a second or even a third time, always about 13
mm (1/2 inch) from the buckle (Fig. 9). When tight-
ening always be careful to see that the strap slides in
a straight line and without resistance in the buckle,
that is without making a fold. An effective grip will
be obtained only by following the above instructions. (12) Fig. 10 shows WHAT NOT TO DO, NEVER
fold the strap back or bring the tool down while
tightening, this action will break the strap. (13) Fig. 11 shows how to pull the tool down while
releasing the pressure on the tool handle.
Fig. 7 Push Tool Forward & Fit into Buckle Eye
Fig. 8 Tighten Strap
Fig. 9 Tighten Strap (if Required)
Fig. 10 What Not to Do
Fig. 11 Correct Tightening Procedure
2 - 46 SUSPENSION AND DRIVESHAFTS Ä
Page 105 of 2438
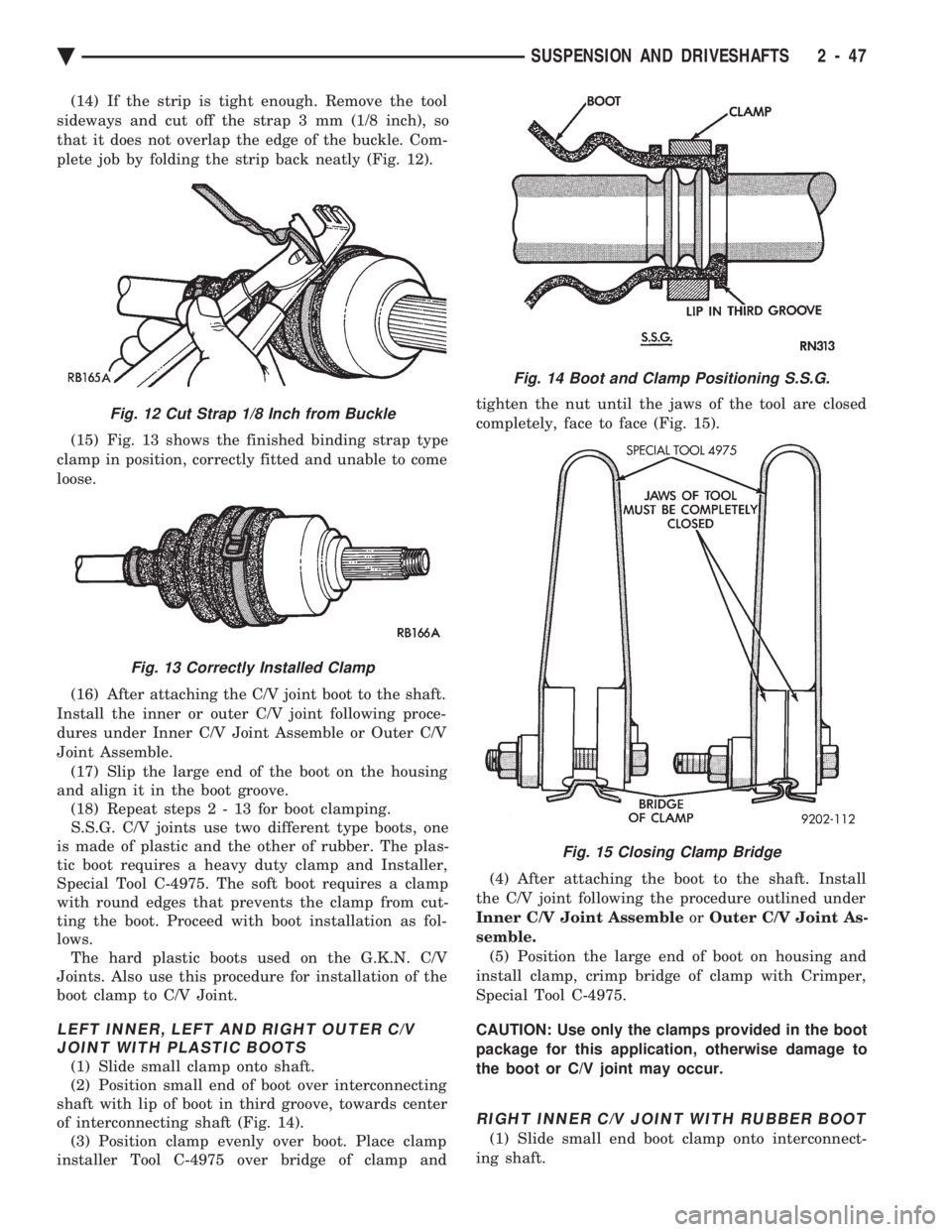
(14) If the strip is tight enough. Remove the tool
sideways and cut off the strap 3 mm (1/8 inch), so
that it does not overlap the edge of the buckle. Com-
plete job by folding the strip back neatly (Fig. 12).
(15) Fig. 13 shows the finished binding strap type
clamp in position, correctly fitted and unable to come
loose.
(16) After attaching the C/V joint boot to the shaft.
Install the inner or outer C/V joint following proce-
dures under Inner C/V Joint Assemble or Outer C/V
Joint Assemble. (17) Slip the large end of the boot on the housing
and align it in the boot groove. (18) Repeat step s2-13forboot clamping.
S.S.G. C/V joints use two different type boots, one
is made of plastic and the other of rubber. The plas-
tic boot requires a heavy duty clamp and Installer,
Special Tool C-4975. The soft boot requires a clamp
with round edges that prevents the clamp from cut-
ting the boot. Proceed with boot installation as fol-
lows. The hard plastic boots used on the G.K.N. C/V
Joints. Also use this procedure for installation of the
boot clamp to C/V Joint.
LEFT INNER, LEFT AND RIGHT OUTER C/V JOINT WITH PLASTIC BOOTS
(1) Slide small clamp onto shaft.
(2) Position small end of boot over interconnecting
shaft with lip of boot in third groove, towards center
of interconnecting shaft (Fig. 14). (3) Position clamp evenly over boot. Place clamp
installer Tool C-4975 over bridge of clamp and tighten the nut until the jaws of the tool are closed
completely, face to face (Fig. 15).
(4) After attaching the boot to the shaft. Install
the C/V joint following the procedure outlined under
Inner C/V Joint Assemble orOuter C/V Joint As-
semble. (5) Position the large end of boot on housing and
install clamp, crimp bridge of clamp with Crimper,
Special Tool C-4975.
CAUTION: Use only the clamps provided in the boot
package for this application, otherwise damage to
the boot or C/V joint may occur.
RIGHT INNER C/V JOINT WITH RUBBER BOOT
(1) Slide small end boot clamp onto interconnect-
ing shaft.
Fig. 12 Cut Strap 1/8 Inch from Buckle
Fig. 13 Correctly Installed Clamp
Fig. 14 Boot and Clamp Positioning S.S.G.
Fig. 15 Closing Clamp Bridge
Ä SUSPENSION AND DRIVESHAFTS 2 - 47
Page 106 of 2438
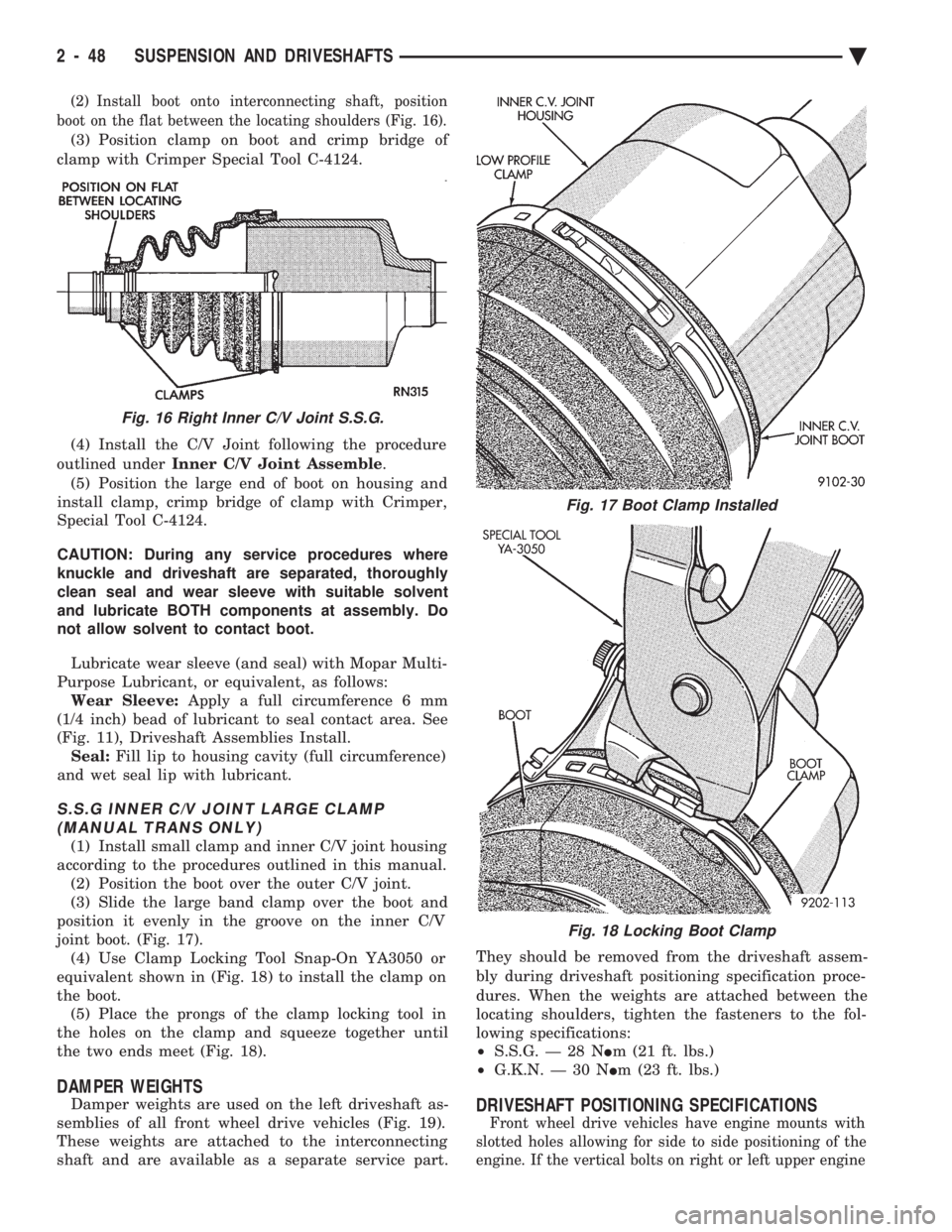
(2) Install boot onto interconnecting shaft, position
boot on the flat between the locating shoulders (Fig. 16).
(3) Position clamp on boot and crimp bridge of
clamp with Crimper Special Tool C-4124.
(4) Install the C/V Joint following the procedure
outlined under Inner C/V Joint Assemble .
(5) Position the large end of boot on housing and
install clamp, crimp bridge of clamp with Crimper,
Special Tool C-4124.
CAUTION: During any service procedures where
knuckle and driveshaft are separated, thoroughly
clean seal and wear sleeve with suitable solvent
and lubricate BOTH components at assembly. Do
not allow solvent to contact boot.
Lubricate wear sleeve (and seal) with Mopar Multi-
Purpose Lubricant, or equivalent, as follows: Wear Sleeve: Apply a full circumference 6 mm
(1/4 inch) bead of lubricant to seal contact area. See
(Fig. 11), Driveshaft Assemblies Install. Seal: Fill lip to housing cavity (full circumference)
and wet seal lip with lubricant.
S.S.G INNER C/V JOINT LARGE CLAMP (MANUAL TRANS ONLY)
(1) Install small clamp and inner C/V joint housing
according to the procedures outlined in this manual. (2) Position the boot over the outer C/V joint.
(3) Slide the large band clamp over the boot and
position it evenly in the groove on the inner C/V
joint boot. (Fig. 17). (4) Use Clamp Locking Tool Snap-On YA3050 or
equivalent shown in (Fig. 18) to install the clamp on
the boot. (5) Place the prongs of the clamp locking tool in
the holes on the clamp and squeeze together until
the two ends meet (Fig. 18).
DAMPER WEIGHTS
Damper weights are used on the left driveshaft as-
semblies of all front wheel drive vehicles (Fig. 19).
These weights are attached to the interconnecting
shaft and are available as a separate service part. They should be removed from the driveshaft assem-
bly during driveshaft positioning specification proce-
dures. When the weights are attached between the
locating shoulders, tighten the fasteners to the fol-
lowing specifications:
² S.S.G. Ð 28 N Im (21 ft. lbs.)
² G.K.N. Ð 30 N Im (23 ft. lbs.)DRIVESHAFT POSITIONING SPECIFICATIONS
Front wheel drive vehicles have engine mounts with
slotted holes allowing for side to side positioning of the
engine. If the vertical bolts on right or left upper engine
Fig. 16 Right Inner C/V Joint S.S.G.
Fig. 17 Boot Clamp Installed
Fig. 18 Locking Boot Clamp
2 - 48 SUSPENSION AND DRIVESHAFTS Ä
Page 107 of 2438
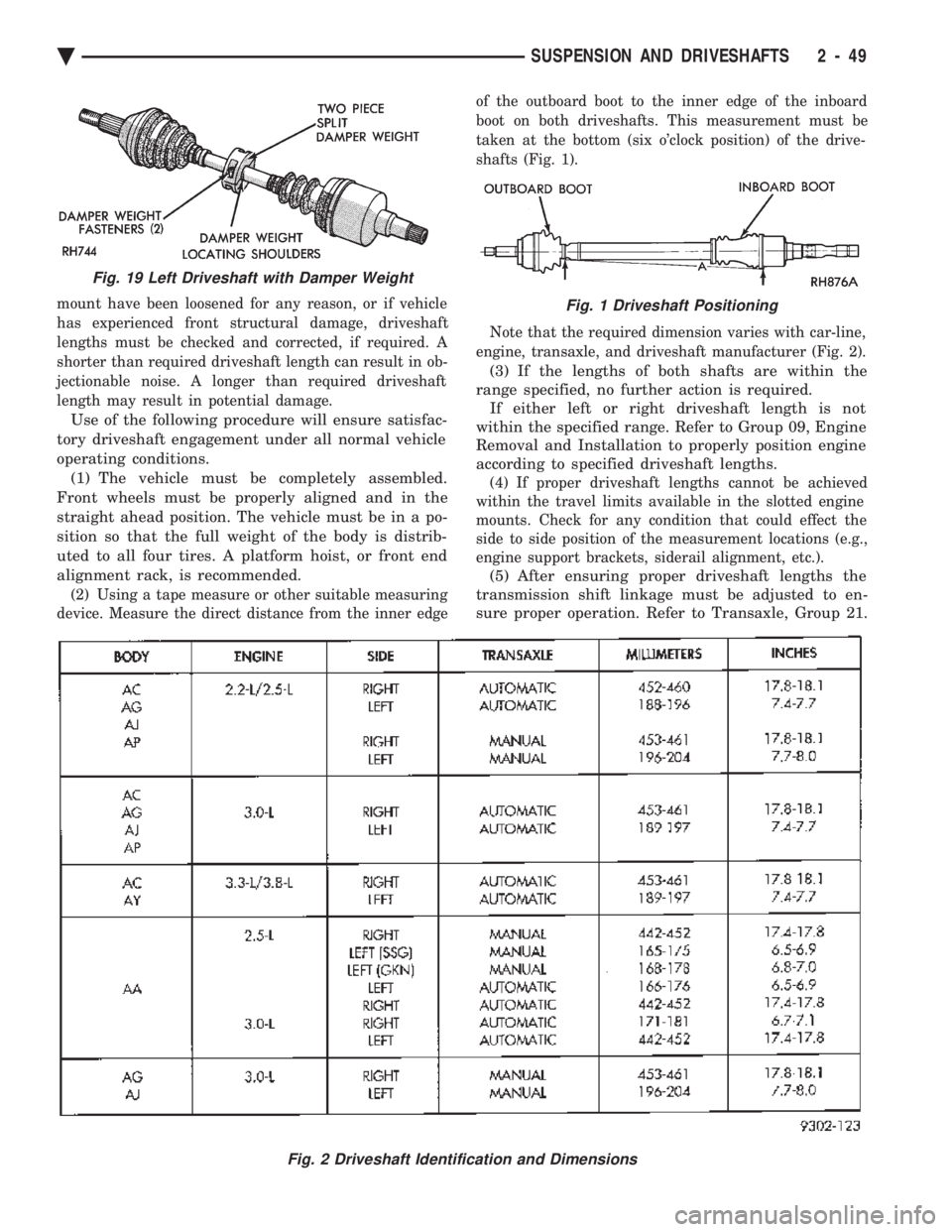
mount have been loosened for any reason, or if vehicle
has experienced front structural damage, driveshaft
lengths must be checked and corrected, if required. A
shorter than required driveshaft length can result in ob-
jectionable noise. A longer than required driveshaft
length may result in potential damage.
Use of the following procedure will ensure satisfac-
tory driveshaft engagement under all normal vehicle
operating conditions. (1) The vehicle must be completely assembled.
Front wheels must be properly aligned and in the
straight ahead position. The vehicle must be in a po-
sition so that the full weight of the body is distrib-
uted to all four tires. A platform hoist, or front end
alignment rack, is recommended.
(2) Using a tape measure or other suitable measuring
device. Measure the direct distance from the inner edge of the outboard boot to the inner edge of the inboard
boot on both driveshafts. This measurement must be
taken at the bottom (six o'clock position) of the drive-
shafts (Fig. 1).
Note that the required dimension varies with car-line,
engine, transaxle, and driveshaft manufacturer (Fig. 2).
(3) If the lengths of both shafts are within the
range specified, no further action is required. If either left or right driveshaft length is not
within the specified range. Refer to Group 09, Engine
Removal and Installation to properly position engine
according to specified driveshaft lengths.
(4) If proper driveshaft lengths cannot be achieved
within the travel limits available in the slotted engine
mounts. Check for any condition that could effect the
side to side position of the measurement locations (e.g.,
engine support brackets, siderail alignment, etc.).
(5) After ensuring proper driveshaft lengths the
transmission shift linkage must be adjusted to en-
sure proper operation. Refer to Transaxle, Group 21.
Fig. 2 Driveshaft Identification and Dimensions
Fig. 19 Left Driveshaft with Damper Weight
Fig. 1 Driveshaft Positioning
Ä SUSPENSION AND DRIVESHAFTS 2 - 49
Page 108 of 2438
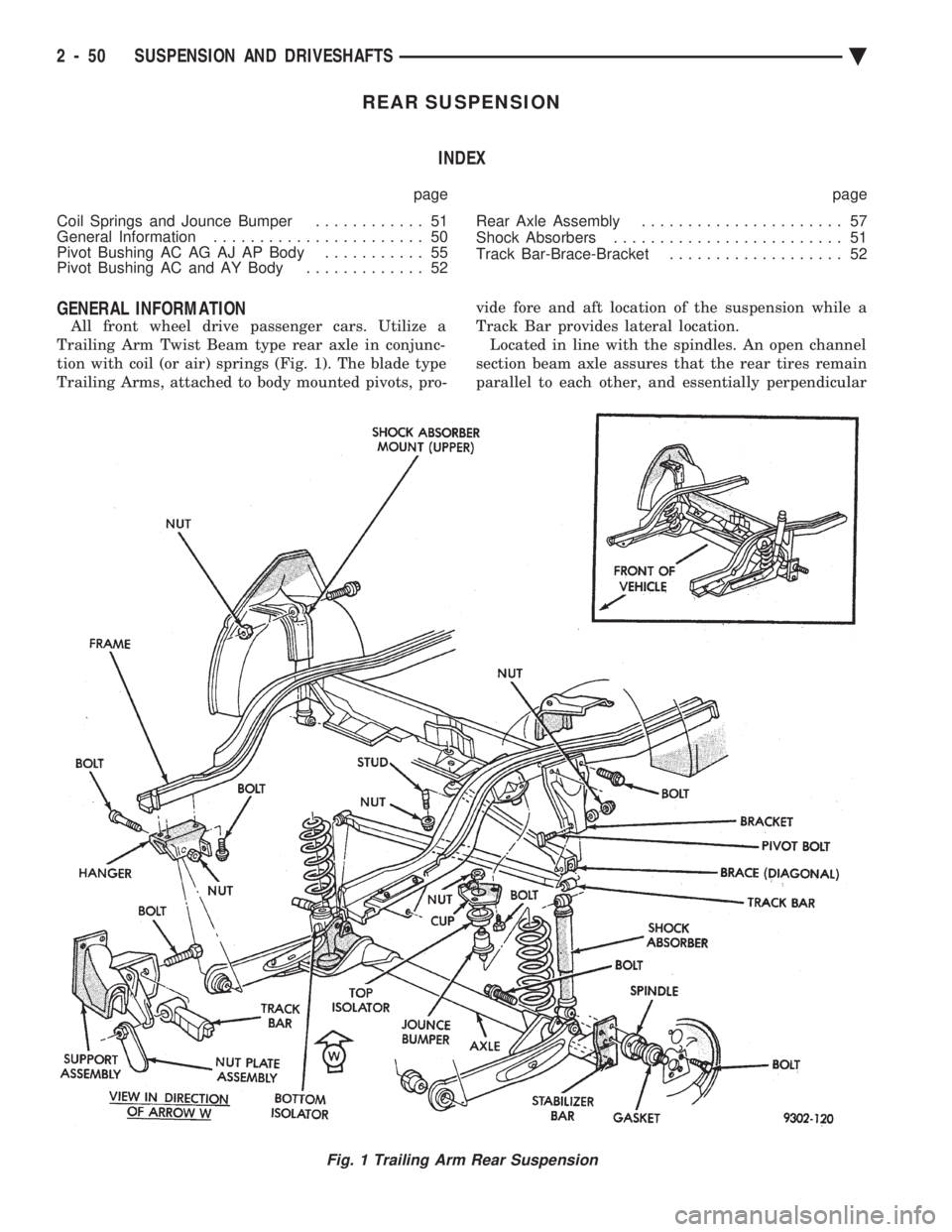
REAR SUSPENSION INDEX
page page
Coil Springs and Jounce Bumper ............ 51
General Information ....................... 50
Pivot Bushing AC AG AJ AP Body ........... 55
Pivot Bushing AC and AY Body ............. 52 Rear Axle Assembly
...................... 57
Shock Absorbers ......................... 51
Track Bar-Brace-Bracket ................... 52
GENERAL INFORMATION
All front wheel drive passenger cars. Utilize a
Trailing Arm Twist Beam type rear axle in conjunc-
tion with coil (or air) springs (Fig. 1). The blade type
Trailing Arms, attached to body mounted pivots, pro- vide fore and aft location of the suspension while a
Track Bar provides lateral location. Located in line with the spindles. An open channel
section beam axle assures that the rear tires remain
parallel to each other, and essentially perpendicular
Fig. 1 Trailing Arm Rear Suspension
2 - 50 SUSPENSION AND DRIVESHAFTS Ä
Page 109 of 2438
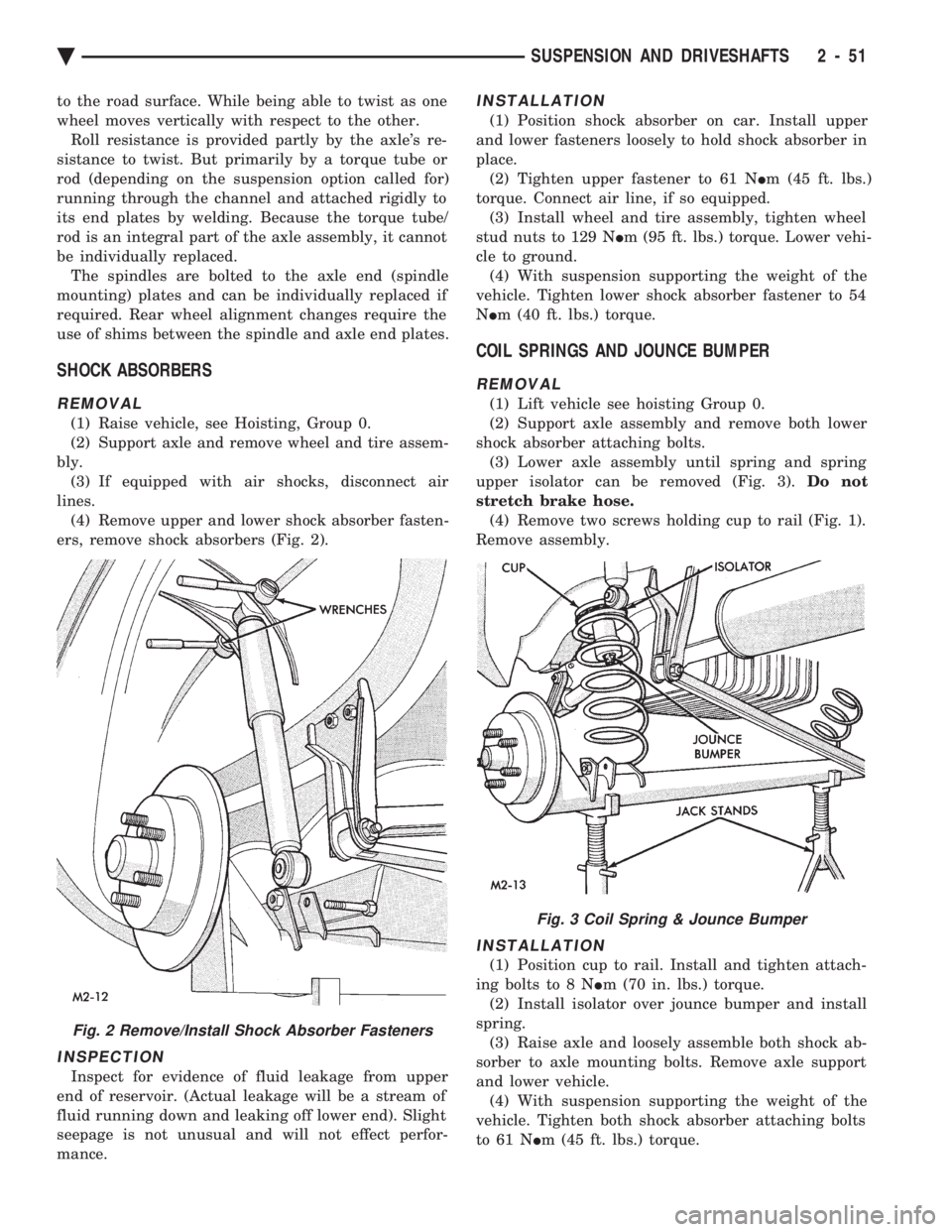
to the road surface. While being able to twist as one
wheel moves vertically with respect to the other.Roll resistance is provided partly by the axle's re-
sistance to twist. But primarily by a torque tube or
rod (depending on the suspension option called for)
running through the channel and attached rigidly to
its end plates by welding. Because the torque tube/
rod is an integral part of the axle assembly, it cannot
be individually replaced. The spindles are bolted to the axle end (spindle
mounting) plates and can be individually replaced if
required. Rear wheel alignment changes require the
use of shims between the spindle and axle end plates.
SHOCK ABSORBERS
REMOVAL
(1) Raise vehicle, see Hoisting, Group 0.
(2) Support axle and remove wheel and tire assem-
bly. (3) If equipped with air shocks, disconnect air
lines. (4) Remove upper and lower shock absorber fasten-
ers, remove shock absorbers (Fig. 2).
INSPECTION
Inspect for evidence of fluid leakage from upper
end of reservoir. (Actual leakage will be a stream of
fluid running down and leaking off lower end). Slight
seepage is not unusual and will not effect perfor-
mance.
INSTALLATION
(1) Position shock absorber on car. Install upper
and lower fasteners loosely to hold shock absorber in
place. (2) Tighten upper fastener to 61 N Im (45 ft. lbs.)
torque. Connect air line, if so equipped. (3) Install wheel and tire assembly, tighten wheel
stud nuts to 129 N Im (95 ft. lbs.) torque. Lower vehi-
cle to ground. (4) With suspension supporting the weight of the
vehicle. Tighten lower shock absorber fastener to 54
N Im (40 ft. lbs.) torque.
COIL SPRINGS AND JOUNCE BUMPER
REMOVAL
(1) Lift vehicle see hoisting Group 0.
(2) Support axle assembly and remove both lower
shock absorber attaching bolts. (3) Lower axle assembly until spring and spring
upper isolator can be removed (Fig. 3). Do not
stretch brake hose. (4) Remove two screws holding cup to rail (Fig. 1).
Remove assembly.
INSTALLATION
(1) Position cup to rail. Install and tighten attach-
ing bolts to 8 N Im (70 in. lbs.) torque.
(2) Install isolator over jounce bumper and install
spring. (3) Raise axle and loosely assemble both shock ab-
sorber to axle mounting bolts. Remove axle support
and lower vehicle. (4) With suspension supporting the weight of the
vehicle. Tighten both shock absorber attaching bolts
to 61 N Im (45 ft. lbs.) torque.
Fig. 2 Remove/Install Shock Absorber Fasteners
Fig. 3 Coil Spring & Jounce Bumper
Ä SUSPENSION AND DRIVESHAFTS 2 - 51
Page 110 of 2438
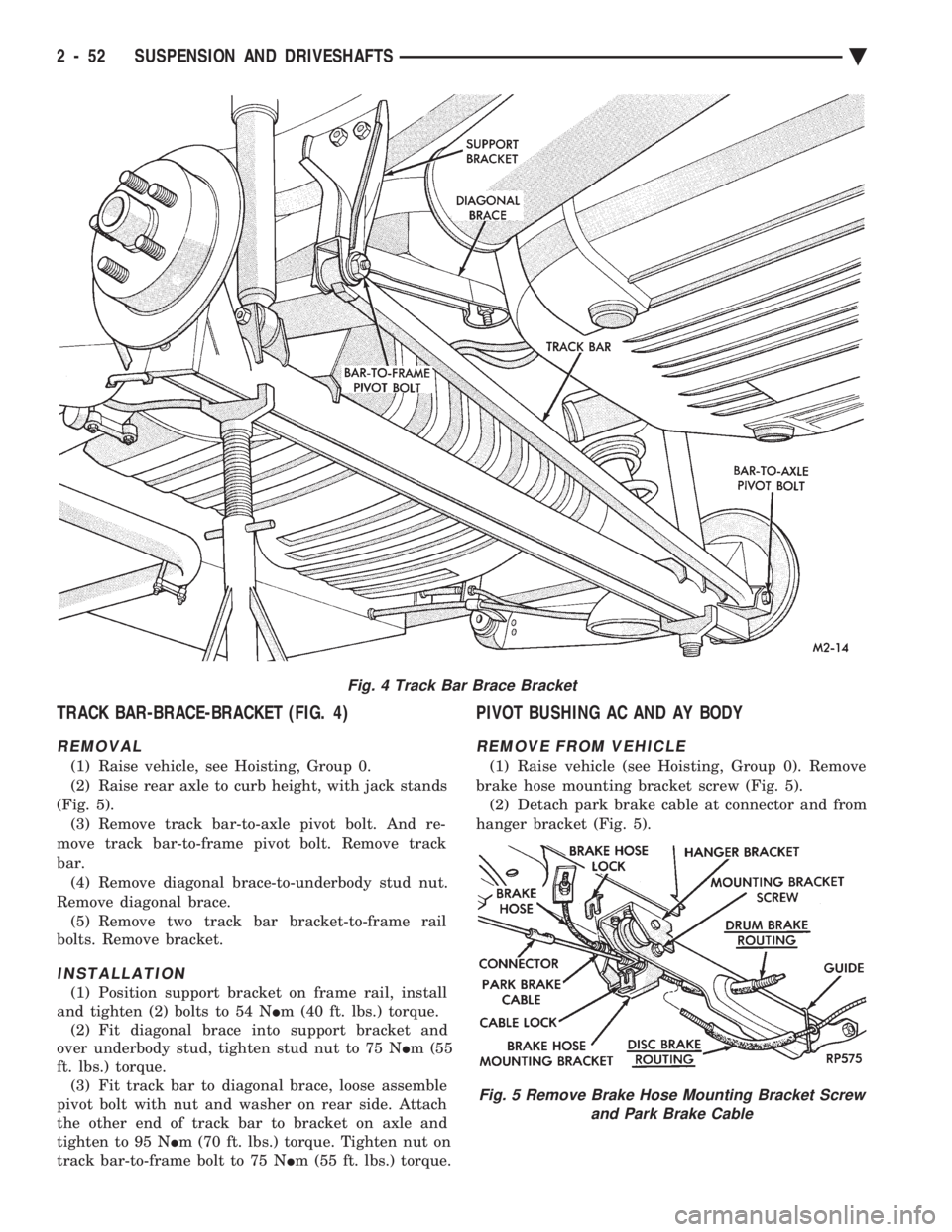
TRACK BAR-BRACE-BRACKET (FIG. 4)
REMOVAL
(1) Raise vehicle, see Hoisting, Group 0.
(2) Raise rear axle to curb height, with jack stands
(Fig. 5). (3) Remove track bar-to-axle pivot bolt. And re-
move track bar-to-frame pivot bolt. Remove track
bar. (4) Remove diagonal brace-to-underbody stud nut.
Remove diagonal brace. (5) Remove two track bar bracket-to-frame rail
bolts. Remove bracket.
INSTALLATION
(1) Position support bracket on frame rail, install
and tighten (2) bolts to 54 N Im (40 ft. lbs.) torque.
(2) Fit diagonal brace into support bracket and
over underbody stud, tighten stud nut to 75 N Im (55
ft. lbs.) torque. (3) Fit track bar to diagonal brace, loose assemble
pivot bolt with nut and washer on rear side. Attach
the other end of track bar to bracket on axle and
tighten to 95 N Im (70 ft. lbs.) torque. Tighten nut on
track bar-to-frame bolt to 75 N Im (55 ft. lbs.) torque.
PIVOT BUSHING AC AND AY BODY
REMOVE FROM VEHICLE
(1) Raise vehicle (see Hoisting, Group 0). Remove
brake hose mounting bracket screw (Fig. 5). (2) Detach park brake cable at connector and from
hanger bracket (Fig. 5).
Fig. 4 Track Bar Brace Bracket
Fig. 5 Remove Brake Hose Mounting Bracket Screw and Park Brake Cable
2 - 52 SUSPENSION AND DRIVESHAFTS Ä