CHEVROLET PLYMOUTH ACCLAIM 1993 Repair Manual
Manufacturer: CHEVROLET, Model Year: 1993, Model line: PLYMOUTH ACCLAIM, Model: CHEVROLET PLYMOUTH ACCLAIM 1993Pages: 2438, PDF Size: 74.98 MB
Page 61 of 2438
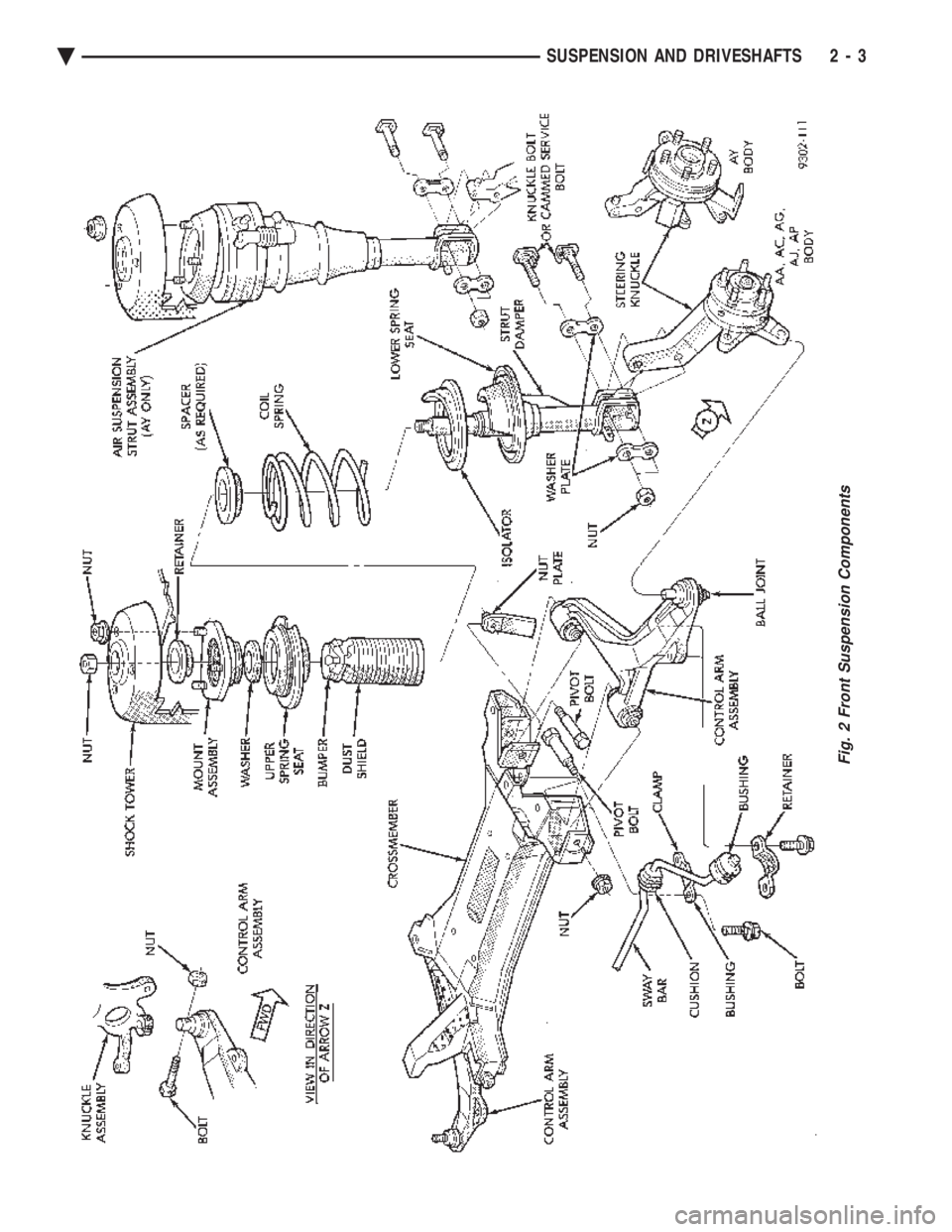
Fig. 2 Front Suspension Components
Ä SUSPENSION AND DRIVESHAFTS 2 - 3
Page 62 of 2438
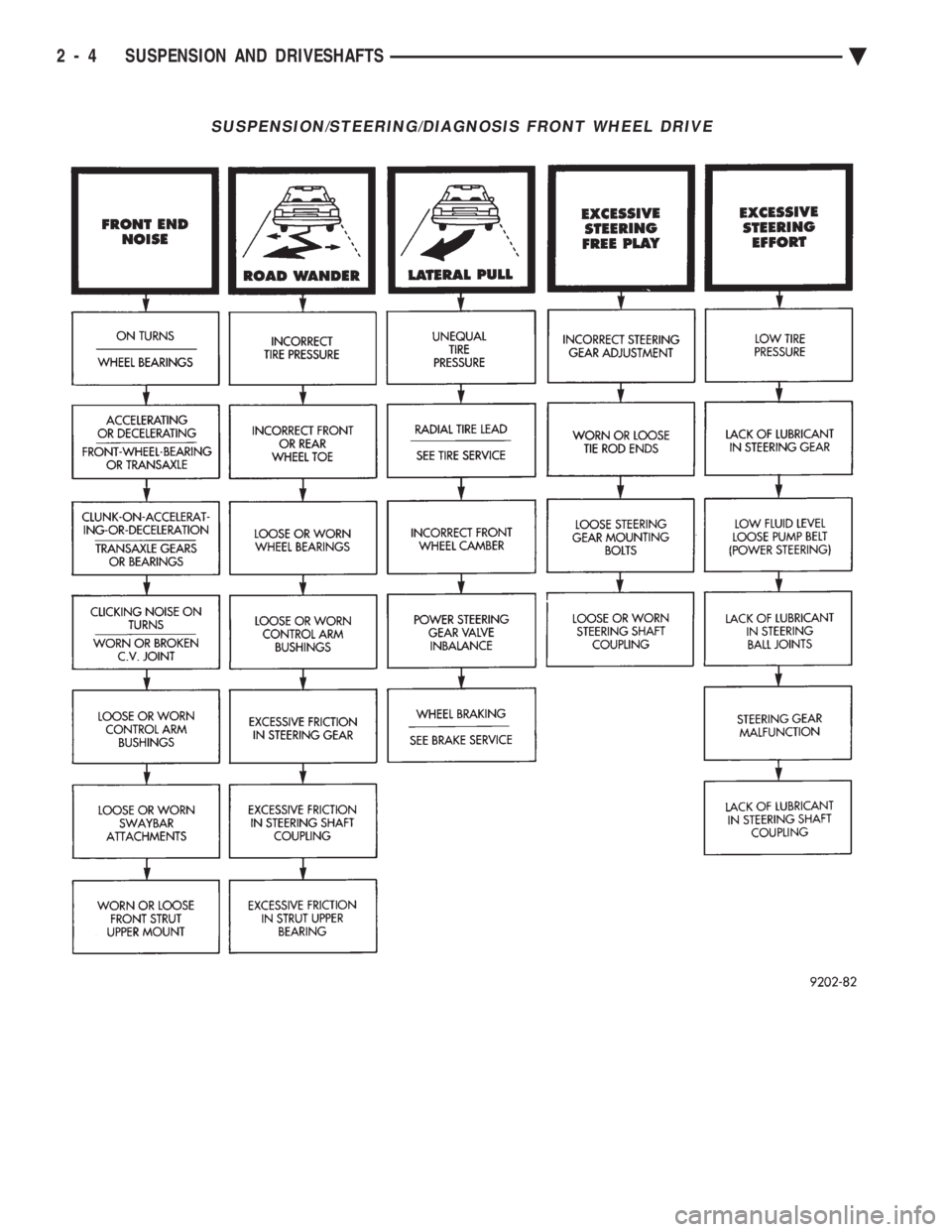
SUSPENSION/STEERING/DIAGNOSIS FRONT WHEEL DRIVE
2 - 4 SUSPENSION AND DRIVESHAFTS Ä
Page 63 of 2438
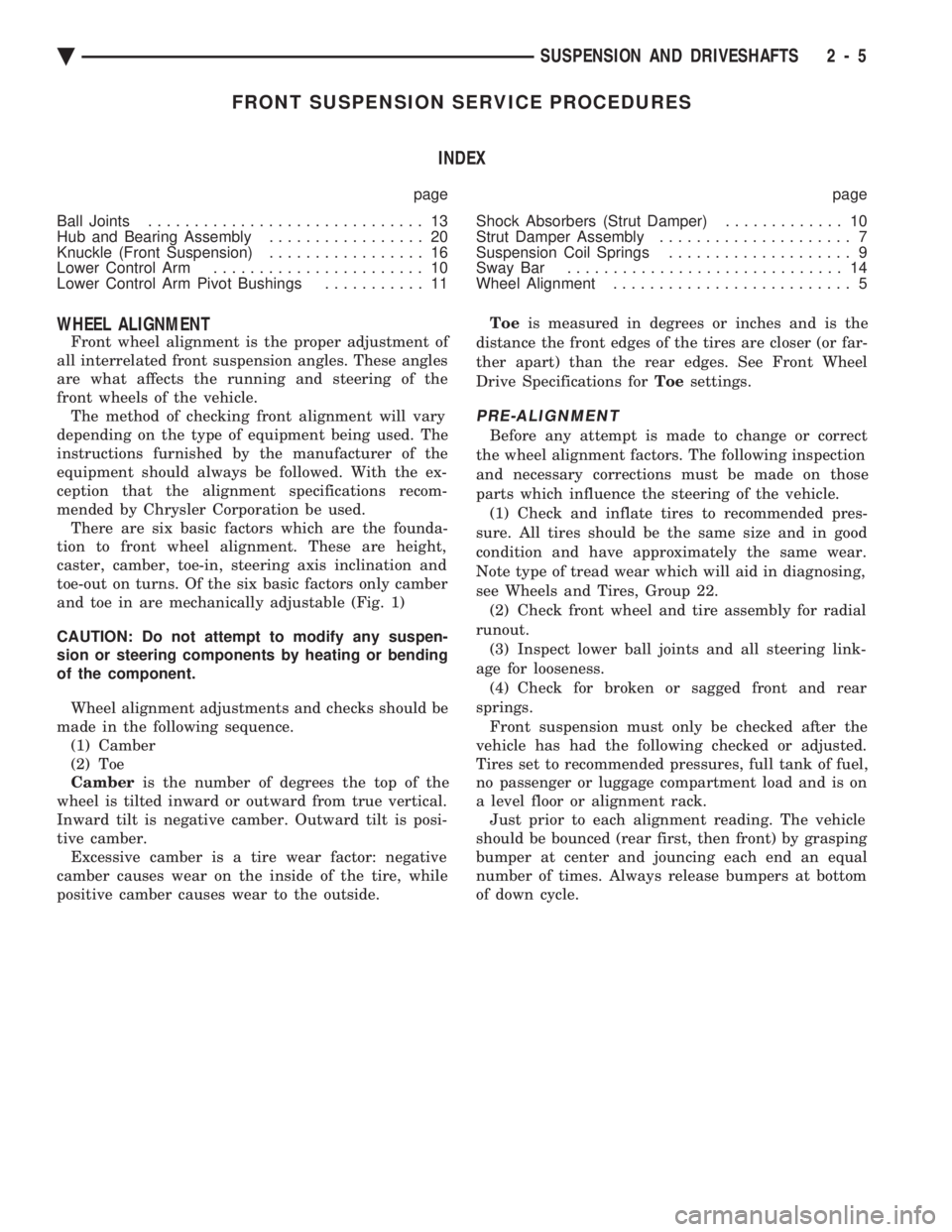
FRONT SUSPENSION SERVICE PROCEDURES INDEX
page page
Ball Joints .............................. 13
Hub and Bearing Assembly ................. 20
Knuckle (Front Suspension) ................. 16
Lower Control Arm ....................... 10
Lower Control Arm Pivot Bushings ........... 11 Shock Absorbers (Strut Damper)
............. 10
Strut Damper Assembly ..................... 7
Suspension Coil Springs .................... 9
Sway Bar .............................. 14
Wheel Alignment .......................... 5
WHEEL ALIGNMENT
Front wheel alignment is the proper adjustment of
all interrelated front suspension angles. These angles
are what affects the running and steering of the
front wheels of the vehicle. The method of checking front alignment will vary
depending on the type of equipment being used. The
instructions furnished by the manufacturer of the
equipment should always be followed. With the ex-
ception that the alignment specifications recom-
mended by Chrysler Corporation be used. There are six basic factors which are the founda-
tion to front wheel alignment. These are height,
caster, camber, toe-in, steering axis inclination and
toe-out on turns. Of the six basic factors only camber
and toe in are mechanically adjustable (Fig. 1)
CAUTION: Do not attempt to modify any suspen-
sion or steering components by heating or bending
of the component.
Wheel alignment adjustments and checks should be
made in the following sequence. (1) Camber
(2) Toe
Camber is the number of degrees the top of the
wheel is tilted inward or outward from true vertical.
Inward tilt is negative camber. Outward tilt is posi-
tive camber. Excessive camber is a tire wear factor: negative
camber causes wear on the inside of the tire, while
positive camber causes wear to the outside. Toe
is measured in degrees or inches and is the
distance the front edges of the tires are closer (or far-
ther apart) than the rear edges. See Front Wheel
Drive Specifications for Toesettings.
PRE-ALIGNMENT
Before any attempt is made to change or correct
the wheel alignment factors. The following inspection
and necessary corrections must be made on those
parts which influence the steering of the vehicle. (1) Check and inflate tires to recommended pres-
sure. All tires should be the same size and in good
condition and have approximately the same wear.
Note type of tread wear which will aid in diagnosing,
see Wheels and Tires, Group 22. (2) Check front wheel and tire assembly for radial
runout. (3) Inspect lower ball joints and all steering link-
age for looseness. (4) Check for broken or sagged front and rear
springs. Front suspension must only be checked after the
vehicle has had the following checked or adjusted.
Tires set to recommended pressures, full tank of fuel,
no passenger or luggage compartment load and is on
a level floor or alignment rack. Just prior to each alignment reading. The vehicle
should be bounced (rear first, then front) by grasping
bumper at center and jouncing each end an equal
number of times. Always release bumpers at bottom
of down cycle.
Ä SUSPENSION AND DRIVESHAFTS 2 - 5
Page 64 of 2438
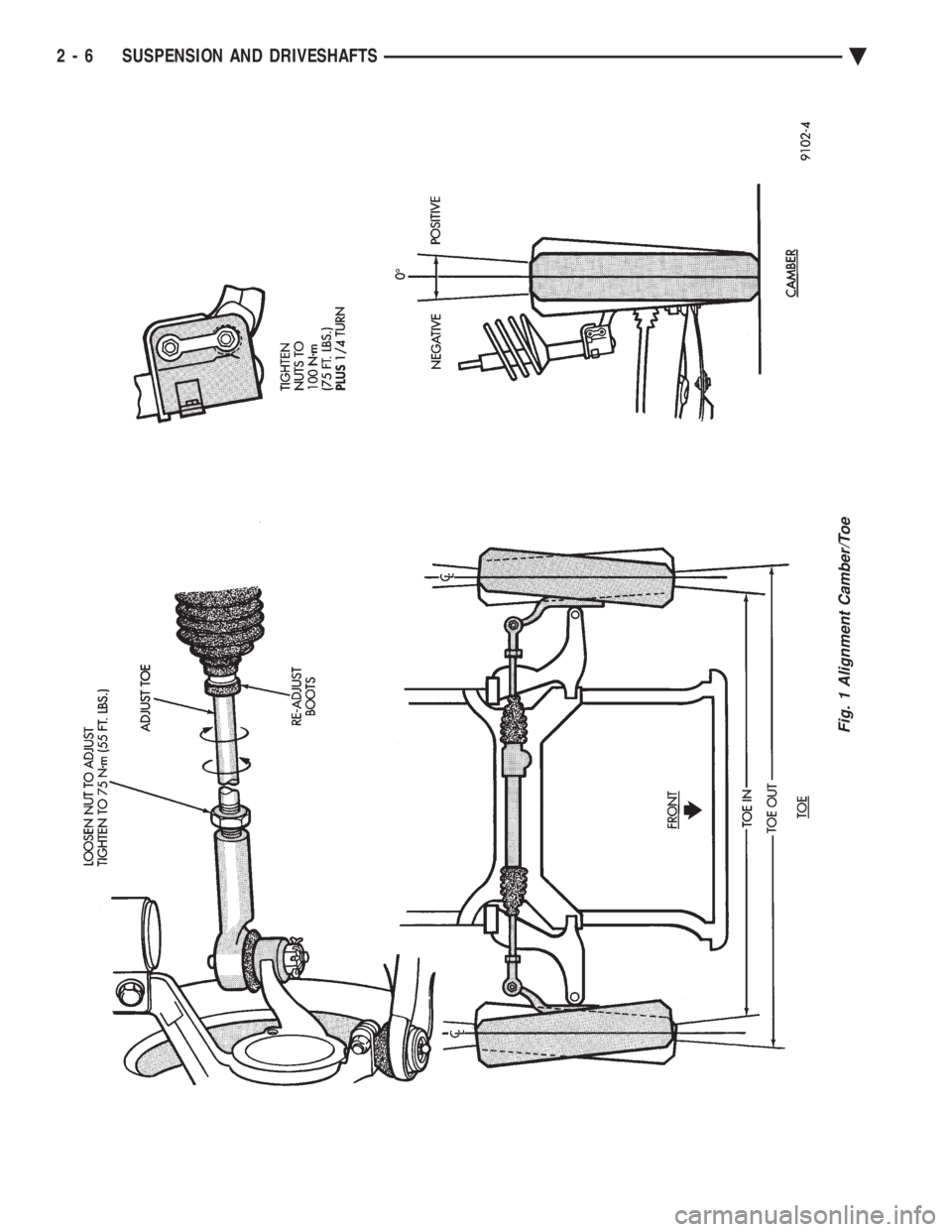
Fig. 1 Alignment Camber/Toe
2 - 6 SUSPENSION AND DRIVESHAFTS Ä
Page 65 of 2438
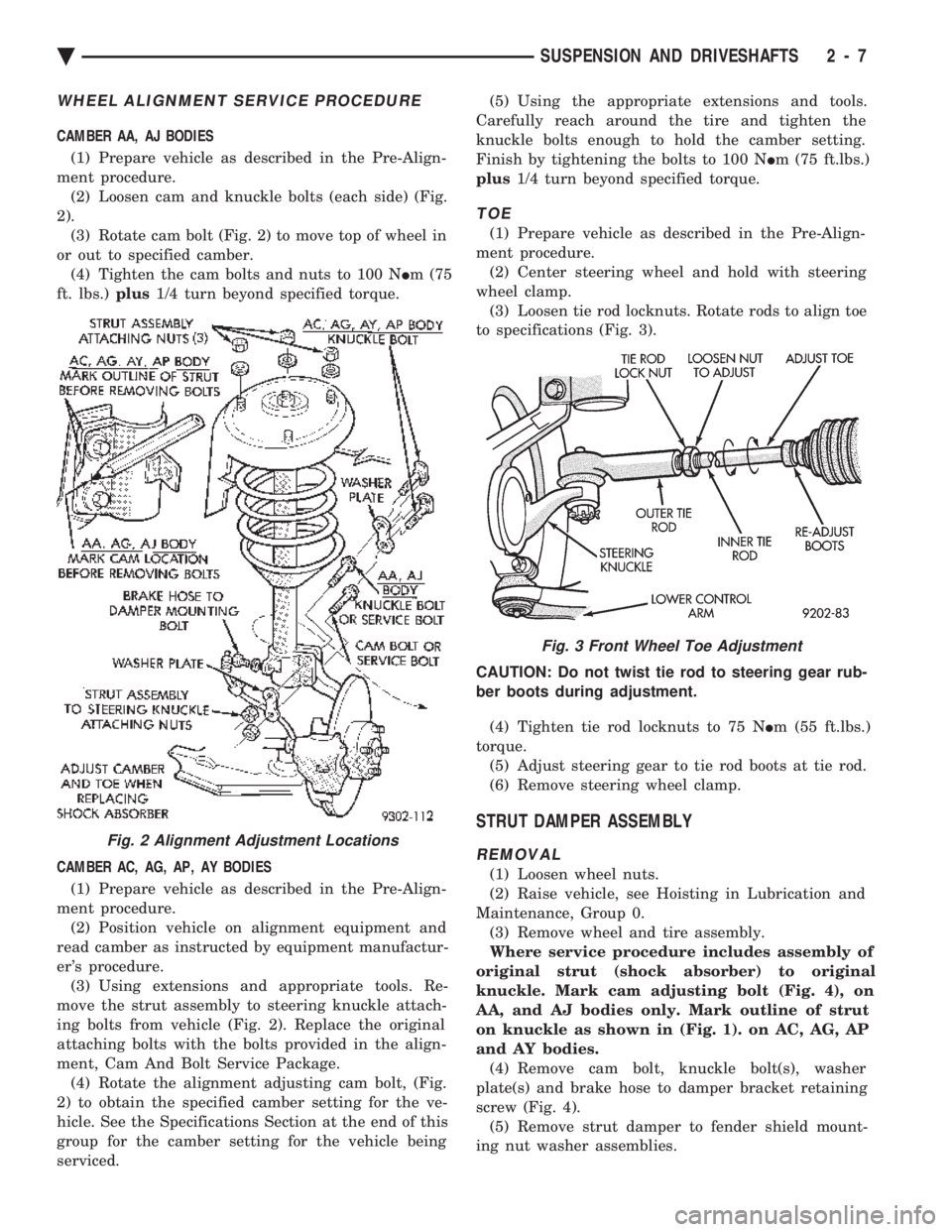
WHEEL ALIGNMENT SERVICE PROCEDURE
CAMBER AA, AJ BODIES (1) Prepare vehicle as described in the Pre-Align-
ment procedure. (2) Loosen cam and knuckle bolts (each side) (Fig.
2). (3) Rotate cam bolt (Fig. 2) to move top of wheel in
or out to specified camber. (4) Tighten the cam bolts and nuts to 100 N Im (75
ft. lbs.) plus1/4 turn beyond specified torque.
CAMBER AC, AG, AP, AY BODIES (1) Prepare vehicle as described in the Pre-Align-
ment procedure. (2) Position vehicle on alignment equipment and
read camber as instructed by equipment manufactur-
er's procedure. (3) Using extensions and appropriate tools. Re-
move the strut assembly to steering knuckle attach-
ing bolts from vehicle (Fig. 2). Replace the original
attaching bolts with the bolts provided in the align-
ment, Cam And Bolt Service Package. (4) Rotate the alignment adjusting cam bolt, (Fig.
2) to obtain the specified camber setting for the ve-
hicle. See the Specifications Section at the end of this
group for the camber setting for the vehicle being
serviced. (5) Using the appropriate extensions and tools.
Carefully reach around the tire and tighten the
knuckle bolts enough to hold the camber setting.
Finish by tightening the bolts to 100 N Im (75 ft.lbs.)
plus 1/4 turn beyond specified torque.
TOE
(1) Prepare vehicle as described in the Pre-Align-
ment procedure. (2) Center steering wheel and hold with steering
wheel clamp. (3) Loosen tie rod locknuts. Rotate rods to align toe
to specifications (Fig. 3).
CAUTION: Do not twist tie rod to steering gear rub-
ber boots during adjustment. (4) Tighten tie rod locknuts to 75 N Im (55 ft.lbs.)
torque. (5) Adjust steering gear to tie rod boots at tie rod.
(6) Remove steering wheel clamp.
STRUT DAMPER ASSEMBLY
REMOVAL
(1) Loosen wheel nuts.
(2) Raise vehicle, see Hoisting in Lubrication and
Maintenance, Group 0. (3) Remove wheel and tire assembly.
Where service procedure includes assembly of
original strut (shock absorber) to original
knuckle. Mark cam adjusting bolt (Fig. 4), on
AA, and AJ bodies only. Mark outline of strut
on knuckle as shown in (Fig. 1). on AC, AG, AP
and AY bodies. (4) Remove cam bolt, knuckle bolt(s), washer
plate(s) and brake hose to damper bracket retaining
screw (Fig. 4). (5) Remove strut damper to fender shield mount-
ing nut washer assemblies.
Fig. 2 Alignment Adjustment Locations
Fig. 3 Front Wheel Toe Adjustment
Ä SUSPENSION AND DRIVESHAFTS 2 - 7
Page 66 of 2438
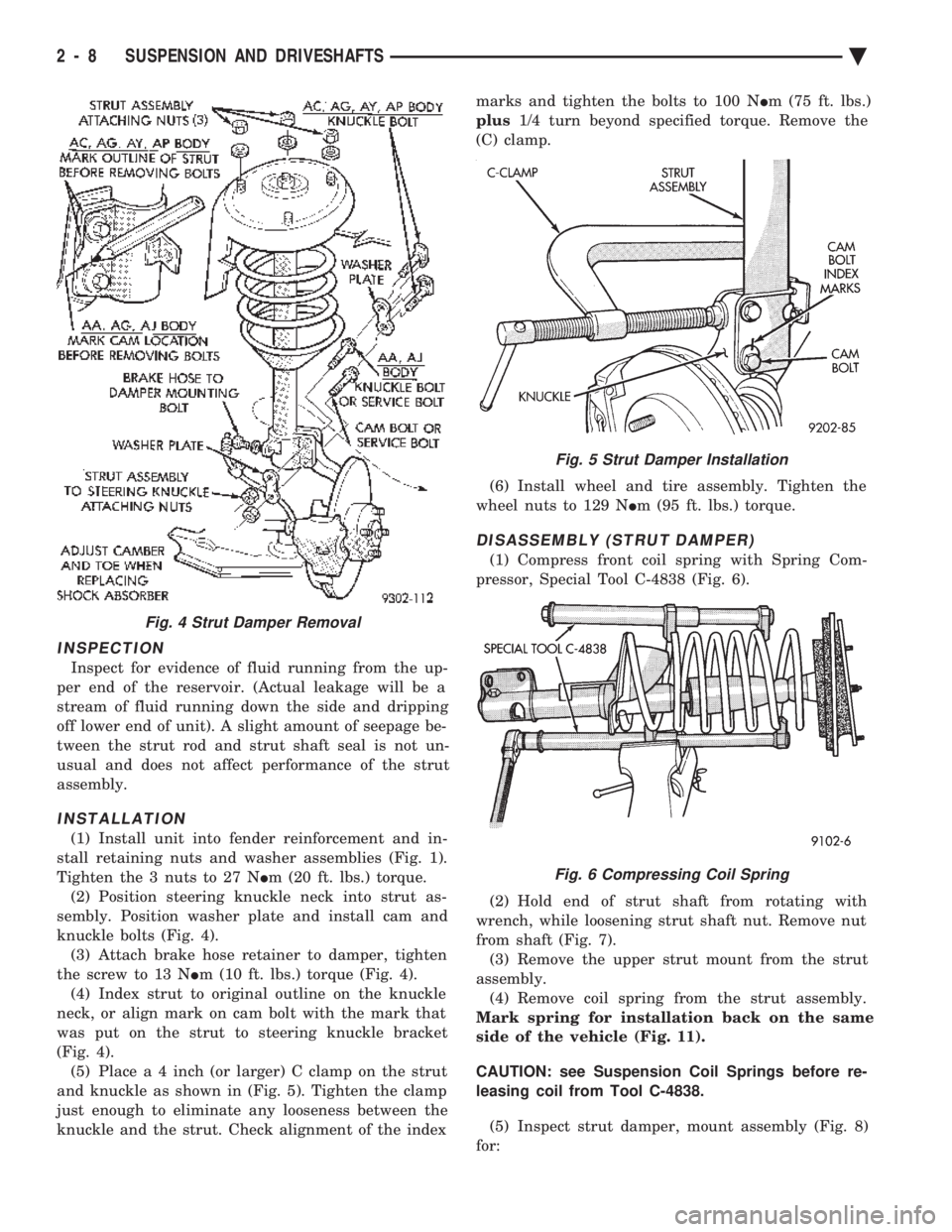
INSPECTION
Inspect for evidence of fluid running from the up-
per end of the reservoir. (Actual leakage will be a
stream of fluid running down the side and dripping
off lower end of unit). A slight amount of seepage be-
tween the strut rod and strut shaft seal is not un-
usual and does not affect performance of the strut
assembly.
INSTALLATION
(1) Install unit into fender reinforcement and in-
stall retaining nuts and washer assemblies (Fig. 1).
Tighten the 3 nuts to 27 N Im (20 ft. lbs.) torque.
(2) Position steering knuckle neck into strut as-
sembly. Position washer plate and install cam and
knuckle bolts (Fig. 4). (3) Attach brake hose retainer to damper, tighten
the screw to 13 N Im (10 ft. lbs.) torque (Fig. 4).
(4) Index strut to original outline on the knuckle
neck, or align mark on cam bolt with the mark that
was put on the strut to steering knuckle bracket
(Fig. 4). (5) Plac e a 4 inch (or larger) C clamp on the strut
and knuckle as shown in (Fig. 5). Tighten the clamp
just enough to eliminate any looseness between the
knuckle and the strut. Check alignment of the index marks and tighten the bolts to 100 N
Im (75 ft. lbs.)
plus 1/4 turn beyond specified torque. Remove the
(C) clamp.
(6) Install wheel and tire assembly. Tighten the
wheel nuts to 129 N Im (95 ft. lbs.) torque.
DISASSEMBLY (STRUT DAMPER)
(1) Compress front coil spring with Spring Com-
pressor, Special Tool C-4838 (Fig. 6).
(2) Hold end of strut shaft from rotating with
wrench, while loosening strut shaft nut. Remove nut
from shaft (Fig. 7). (3) Remove the upper strut mount from the strut
assembly. (4) Remove coil spring from the strut assembly.
Mark spring for installation back on the same
side of the vehicle (Fig. 11).
CAUTION: see Suspension Coil Springs before re-
leasing coil from Tool C-4838.
(5) Inspect strut damper, mount assembly (Fig. 8)
for:
Fig. 4 Strut Damper Removal
Fig. 5 Strut Damper Installation
Fig. 6 Compressing Coil Spring
2 - 8 SUSPENSION AND DRIVESHAFTS Ä
Page 67 of 2438
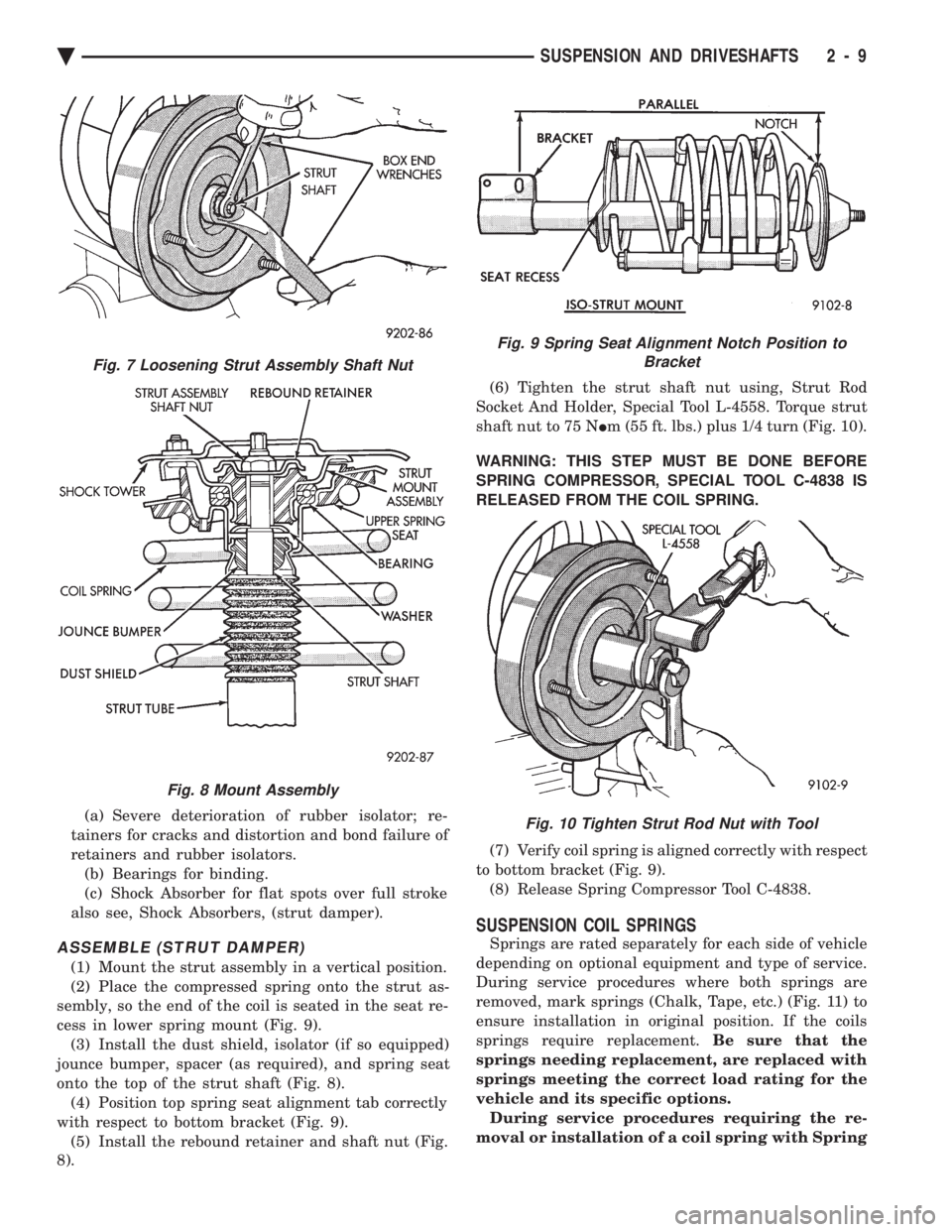
(a) Severe deterioration of rubber isolator; re-
tainers for cracks and distortion and bond failure of
retainers and rubber isolators. (b) Bearings for binding.
(c) Shock Absorber for flat spots over full stroke
also see, Shock Absorbers, (strut damper).
ASSEMBLE (STRUT DAMPER)
(1) Mount the strut assembly in a vertical position.
(2) Place the compressed spring onto the strut as-
sembly, so the end of the coil is seated in the seat re-
cess in lower spring mount (Fig. 9). (3) Install the dust shield, isolator (if so equipped)
jounce bumper, spacer (as required), and spring seat
onto the top of the strut shaft (Fig. 8). (4) Position top spring seat alignment tab correctly
with respect to bottom bracket (Fig. 9). (5) Install the rebound retainer and shaft nut (Fig.
8). (6) Tighten the strut shaft nut using, Strut Rod
Socket And Holder, Special Tool L-4558. Torque strut
shaft nut to 75 N Im (55 ft. lbs.) plus 1/4 turn (Fig. 10).
WARNING: THIS STEP MUST BE DONE BEFORE
SPRING COMPRESSOR, SPECIAL TOOL C-4838 IS
RELEASED FROM THE COIL SPRING.
(7) Verify coil spring is aligned correctly with respect
to bottom bracket (Fig. 9). (8) Release Spring Compressor Tool C-4838.
SUSPENSION COIL SPRINGS
Springs are rated separately for each side of vehicle
depending on optional equipment and type of service.
During service procedures where both springs are
removed, mark springs (Chalk, Tape, etc.) (Fig. 11) to
ensure installation in original position. If the coils
springs require replacement. Be sure that the
springs needing replacement, are replaced with
springs meeting the correct load rating for the
vehicle and its specific options. During service procedures requiring the re-
moval or installation of a coil spring with Spring
Fig. 7 Loosening Strut Assembly Shaft Nut
Fig. 8 Mount Assembly
Fig. 9 Spring Seat Alignment Notch Position to Bracket
Fig. 10 Tighten Strut Rod Nut with Tool
Ä SUSPENSION AND DRIVESHAFTS 2 - 9
Page 68 of 2438
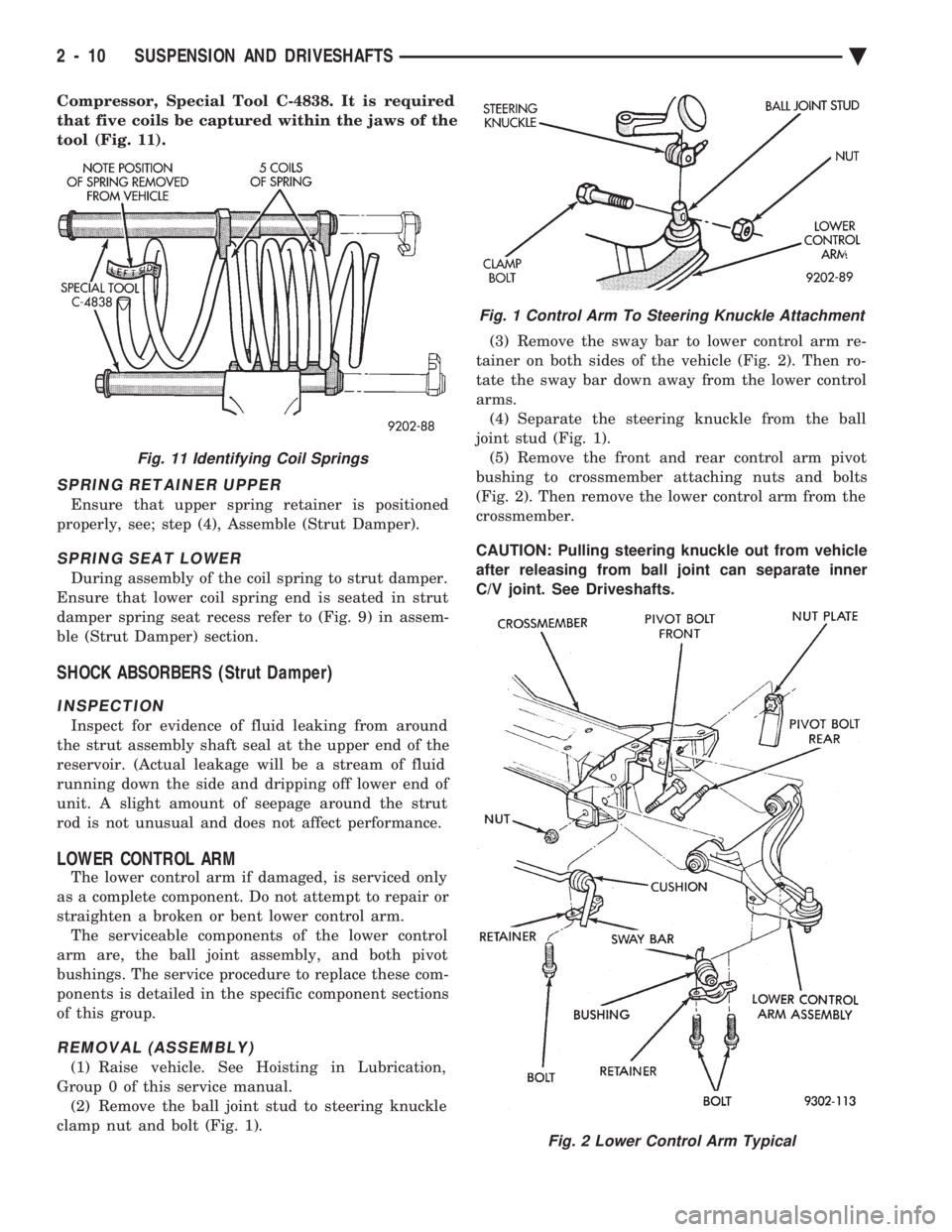
Compressor, Special Tool C-4838. It is required
that five coils be captured within the jaws of the
tool (Fig. 11).
SPRING RETAINER UPPER
Ensure that upper spring retainer is positioned
properly, see; step (4), Assemble (Strut Damper).
SPRING SEAT LOWER
During assembly of the coil spring to strut damper.
Ensure that lower coil spring end is seated in strut
damper spring seat recess refer to (Fig. 9) in assem-
ble (Strut Damper) section.
SHOCK ABSORBERS (Strut Damper)
INSPECTION
Inspect for evidence of fluid leaking from around
the strut assembly shaft seal at the upper end of the
reservoir. (Actual leakage will be a stream of fluid
running down the side and dripping off lower end of
unit. A slight amount of seepage around the strut
rod is not unusual and does not affect performance.
LOWER CONTROL ARM
The lower control arm if damaged, is serviced only
as a complete component. Do not attempt to repair or
straighten a broken or bent lower control arm. The serviceable components of the lower control
arm are, the ball joint assembly, and both pivot
bushings. The service procedure to replace these com-
ponents is detailed in the specific component sections
of this group.
REMOVAL (ASSEMBLY)
(1) Raise vehicle. See Hoisting in Lubrication,
Group 0 of this service manual. (2) Remove the ball joint stud to steering knuckle
clamp nut and bolt (Fig. 1). (3) Remove the sway bar to lower control arm re-
tainer on both sides of the vehicle (Fig. 2). Then ro-
tate the sway bar down away from the lower control
arms. (4) Separate the steering knuckle from the ball
joint stud (Fig. 1). (5) Remove the front and rear control arm pivot
bushing to crossmember attaching nuts and bolts
(Fig. 2). Then remove the lower control arm from the
crossmember.
CAUTION: Pulling steering knuckle out from vehicle
after releasing from ball joint can separate inner
C/V joint. See Driveshafts.
Fig. 11 Identifying Coil Springs
Fig. 1 Control Arm To Steering Knuckle Attachment
Fig. 2 Lower Control Arm Typical
2 - 10 SUSPENSION AND DRIVESHAFTS Ä
Page 69 of 2438
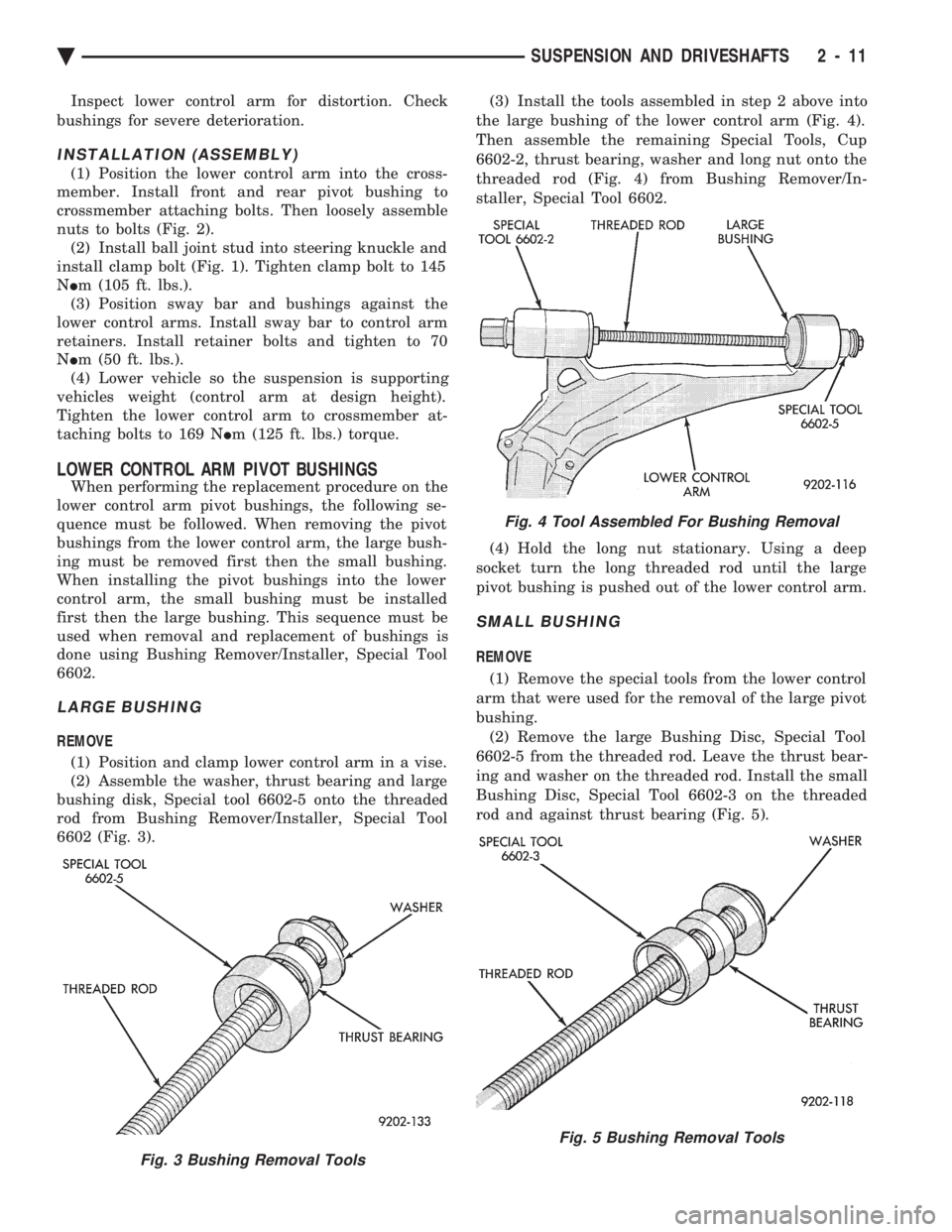
Inspect lower control arm for distortion. Check
bushings for severe deterioration.
INSTALLATION (ASSEMBLY)
(1) Position the lower control arm into the cross-
member. Install front and rear pivot bushing to
crossmember attaching bolts. Then loosely assemble
nuts to bolts (Fig. 2). (2) Install ball joint stud into steering knuckle and
install clamp bolt (Fig. 1). Tighten clamp bolt to 145
N Im (105 ft. lbs.).
(3) Position sway bar and bushings against the
lower control arms. Install sway bar to control arm
retainers. Install retainer bolts and tighten to 70
N Im (50 ft. lbs.).
(4) Lower vehicle so the suspension is supporting
vehicles weight (control arm at design height).
Tighten the lower control arm to crossmember at-
taching bolts to 169 N Im (125 ft. lbs.) torque.
LOWER CONTROL ARM PIVOT BUSHINGS
When performing the replacement procedure on the
lower control arm pivot bushings, the following se-
quence must be followed. When removing the pivot
bushings from the lower control arm, the large bush-
ing must be removed first then the small bushing.
When installing the pivot bushings into the lower
control arm, the small bushing must be installed
first then the large bushing. This sequence must be
used when removal and replacement of bushings is
done using Bushing Remover/Installer, Special Tool
6602.
LARGE BUSHING
REMOVE
(1) Position and clamp lower control arm in a vise.
(2) Assemble the washer, thrust bearing and large
bushing disk, Special tool 6602-5 onto the threaded
rod from Bushing Remover/Installer, Special Tool
6602 (Fig. 3). (3) Install the tools assembled in step 2 above into
the large bushing of the lower control arm (Fig. 4).
Then assemble the remaining Special Tools, Cup
6602-2, thrust bearing, washer and long nut onto the
threaded rod (Fig. 4) from Bushing Remover/In-
staller, Special Tool 6602.
(4) Hold the long nut stationary. Using a deep
socket turn the long threaded rod until the large
pivot bushing is pushed out of the lower control arm.
SMALL BUSHING
REMOVE
(1) Remove the special tools from the lower control
arm that were used for the removal of the large pivot
bushing. (2) Remove the large Bushing Disc, Special Tool
6602-5 from the threaded rod. Leave the thrust bear-
ing and washer on the threaded rod. Install the small
Bushing Disc, Special Tool 6602-3 on the threaded
rod and against thrust bearing (Fig. 5).
Fig. 3 Bushing Removal Tools
Fig. 4 Tool Assembled For Bushing Removal
Fig. 5 Bushing Removal Tools
Ä SUSPENSION AND DRIVESHAFTS 2 - 11
Page 70 of 2438
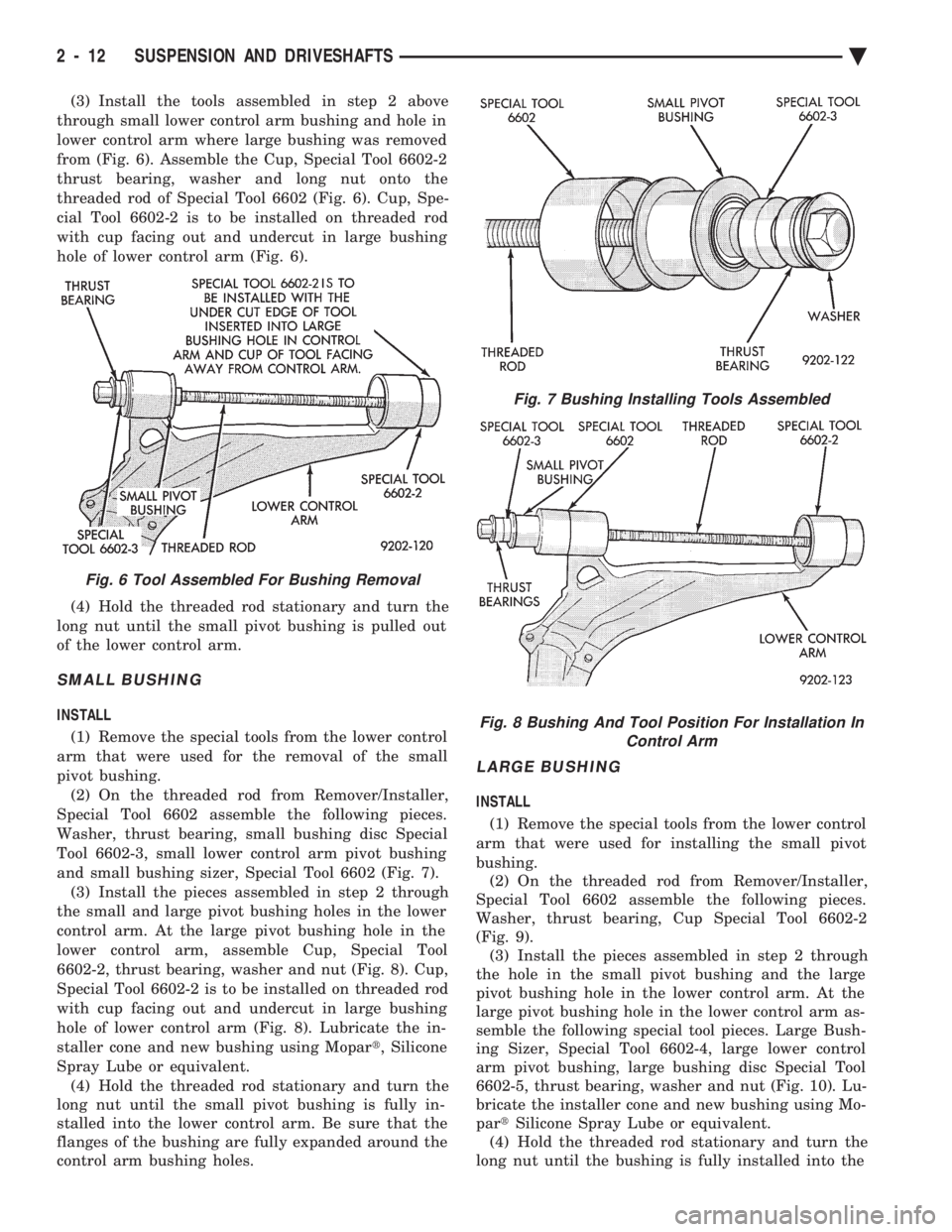
(3) Install the tools assembled in step 2 above
through small lower control arm bushing and hole in
lower control arm where large bushing was removed
from (Fig. 6). Assemble the Cup, Special Tool 6602-2
thrust bearing, washer and long nut onto the
threaded rod of Special Tool 6602 (Fig. 6). Cup, Spe-
cial Tool 6602-2 is to be installed on threaded rod
with cup facing out and undercut in large bushing
hole of lower control arm (Fig. 6).
(4) Hold the threaded rod stationary and turn the
long nut until the small pivot bushing is pulled out
of the lower control arm.
SMALL BUSHING
INSTALL
(1) Remove the special tools from the lower control
arm that were used for the removal of the small
pivot bushing. (2) On the threaded rod from Remover/Installer,
Special Tool 6602 assemble the following pieces.
Washer, thrust bearing, small bushing disc Special
Tool 6602-3, small lower control arm pivot bushing
and small bushing sizer, Special Tool 6602 (Fig. 7). (3) Install the pieces assembled in step 2 through
the small and large pivot bushing holes in the lower
control arm. At the large pivot bushing hole in the
lower control arm, assemble Cup, Special Tool
6602-2, thrust bearing, washer and nut (Fig. 8). Cup,
Special Tool 6602-2 is to be installed on threaded rod
with cup facing out and undercut in large bushing
hole of lower control arm (Fig. 8). Lubricate the in-
staller cone and new bushing using Mopar t, Silicone
Spray Lube or equivalent. (4) Hold the threaded rod stationary and turn the
long nut until the small pivot bushing is fully in-
stalled into the lower control arm. Be sure that the
flanges of the bushing are fully expanded around the
control arm bushing holes.
LARGE BUSHING
INSTALL
(1) Remove the special tools from the lower control
arm that were used for installing the small pivot
bushing. (2) On the threaded rod from Remover/Installer,
Special Tool 6602 assemble the following pieces.
Washer, thrust bearing, Cup Special Tool 6602-2
(Fig. 9). (3) Install the pieces assembled in step 2 through
the hole in the small pivot bushing and the large
pivot bushing hole in the lower control arm. At the
large pivot bushing hole in the lower control arm as-
semble the following special tool pieces. Large Bush-
ing Sizer, Special Tool 6602-4, large lower control
arm pivot bushing, large bushing disc Special Tool
6602-5, thrust bearing, washer and nut (Fig. 10). Lu-
bricate the installer cone and new bushing using Mo-
par tSilicone Spray Lube or equivalent.
(4) Hold the threaded rod stationary and turn the
long nut until the bushing is fully installed into the
Fig. 6 Tool Assembled For Bushing Removal
Fig. 7 Bushing Installing Tools Assembled
Fig. 8 Bushing And Tool Position For Installation In Control Arm
2 - 12 SUSPENSION AND DRIVESHAFTS Ä