CHEVROLET PLYMOUTH ACCLAIM 1993 Service Manual
Manufacturer: CHEVROLET, Model Year: 1993, Model line: PLYMOUTH ACCLAIM, Model: CHEVROLET PLYMOUTH ACCLAIM 1993Pages: 2438, PDF Size: 74.98 MB
Page 111 of 2438
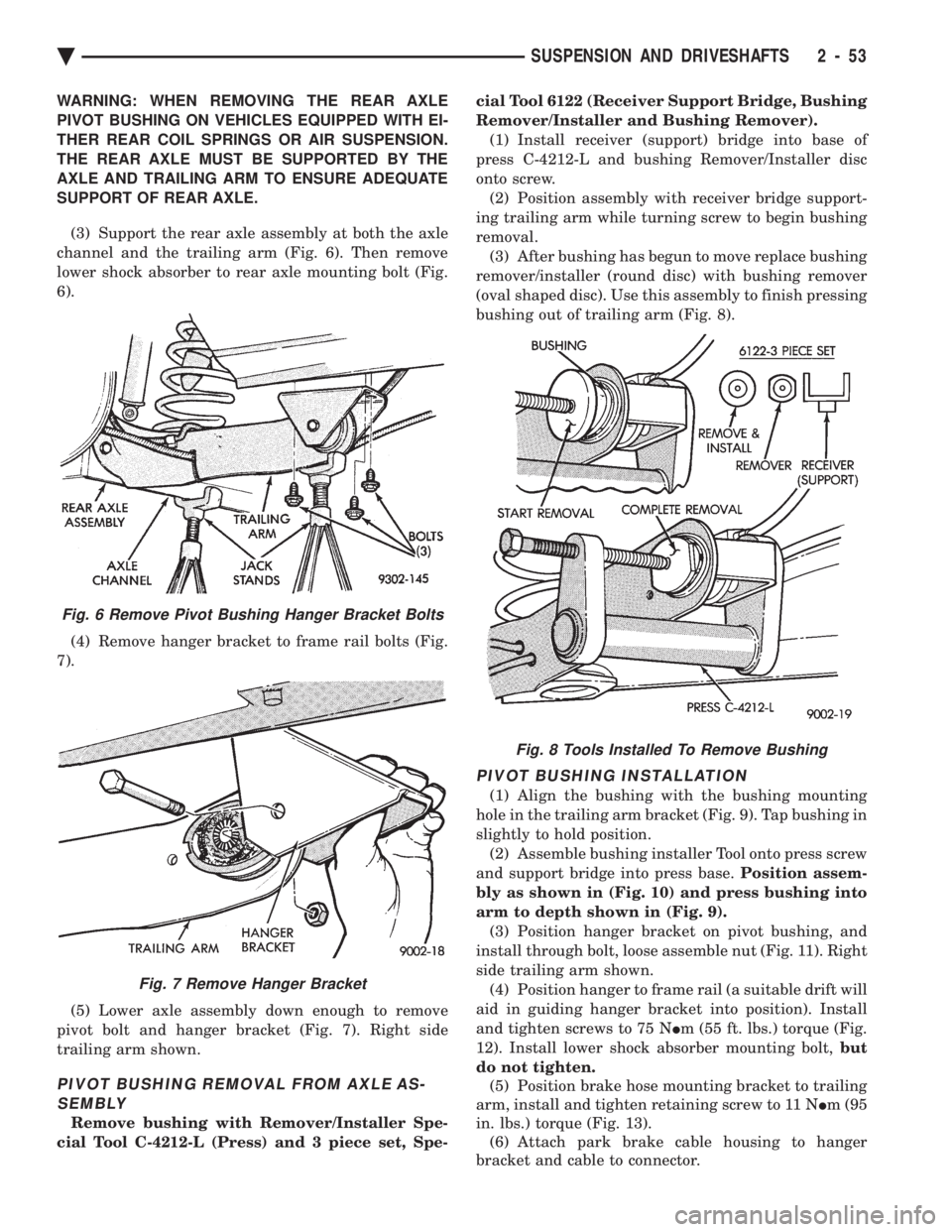
WARNING: WHEN REMOVING THE REAR AXLE
PIVOT BUSHING ON VEHICLES EQUIPPED WITH EI-
THER REAR COIL SPRINGS OR AIR SUSPENSION.
THE REAR AXLE MUST BE SUPPORTED BY THE
AXLE AND TRAILING ARM TO ENSURE ADEQUATE
SUPPORT OF REAR AXLE.
(3) Support the rear axle assembly at both the axle
channel and the trailing arm (Fig. 6). Then remove
lower shock absorber to rear axle mounting bolt (Fig.
6).
(4) Remove hanger bracket to frame rail bolts (Fig.
7).
(5) Lower axle assembly down enough to remove
pivot bolt and hanger bracket (Fig. 7). Right side
trailing arm shown.
PIVOT BUSHING REMOVAL FROM AXLE AS- SEMBLY
Remove bushing with Remover/Installer Spe-
cial Tool C-4212-L (Press) and 3 piece set, Spe- cial Tool 6122 (Receiver Support Bridge, Bushing
Remover/Installer and Bushing Remover). (1) Install receiver (support) bridge into base of
press C-4212-L and bushing Remover/Installer disc
onto screw. (2) Position assembly with receiver bridge support-
ing trailing arm while turning screw to begin bushing
removal. (3) After bushing has begun to move replace bushing
remover/installer (round disc) with bushing remover
(oval shaped disc). Use this assembly to finish pressing
bushing out of trailing arm (Fig. 8).
PIVOT BUSHING INSTALLATION
(1) Align the bushing with the bushing mounting
hole in the trailing arm bracket (Fig. 9). Tap bushing in
slightly to hold position. (2) Assemble bushing installer Tool onto press screw
and support bridge into press base. Position assem-
bly as shown in (Fig. 10) and press bushing into
arm to depth shown in (Fig. 9). (3) Position hanger bracket on pivot bushing, and
install through bolt, loose assemble nut (Fig. 11). Right
side trailing arm shown. (4) Position hanger to frame rail (a suitable drift will
aid in guiding hanger bracket into position). Install
and tighten screws to 75 N Im (55 ft. lbs.) torque (Fig.
12). Install lower shock absorber mounting bolt, but
do not tighten. (5) Position brake hose mounting bracket to trailing
arm, install and tighten retaining screw to 11 N Im (95
in. lbs.) torque (Fig. 13). (6) Attach park brake cable housing to hanger
bracket and cable to connector.
Fig. 8 Tools Installed To Remove Bushing
Fig. 6 Remove Pivot Bushing Hanger Bracket Bolts
Fig. 7 Remove Hanger Bracket
Ä SUSPENSION AND DRIVESHAFTS 2 - 53
Page 112 of 2438
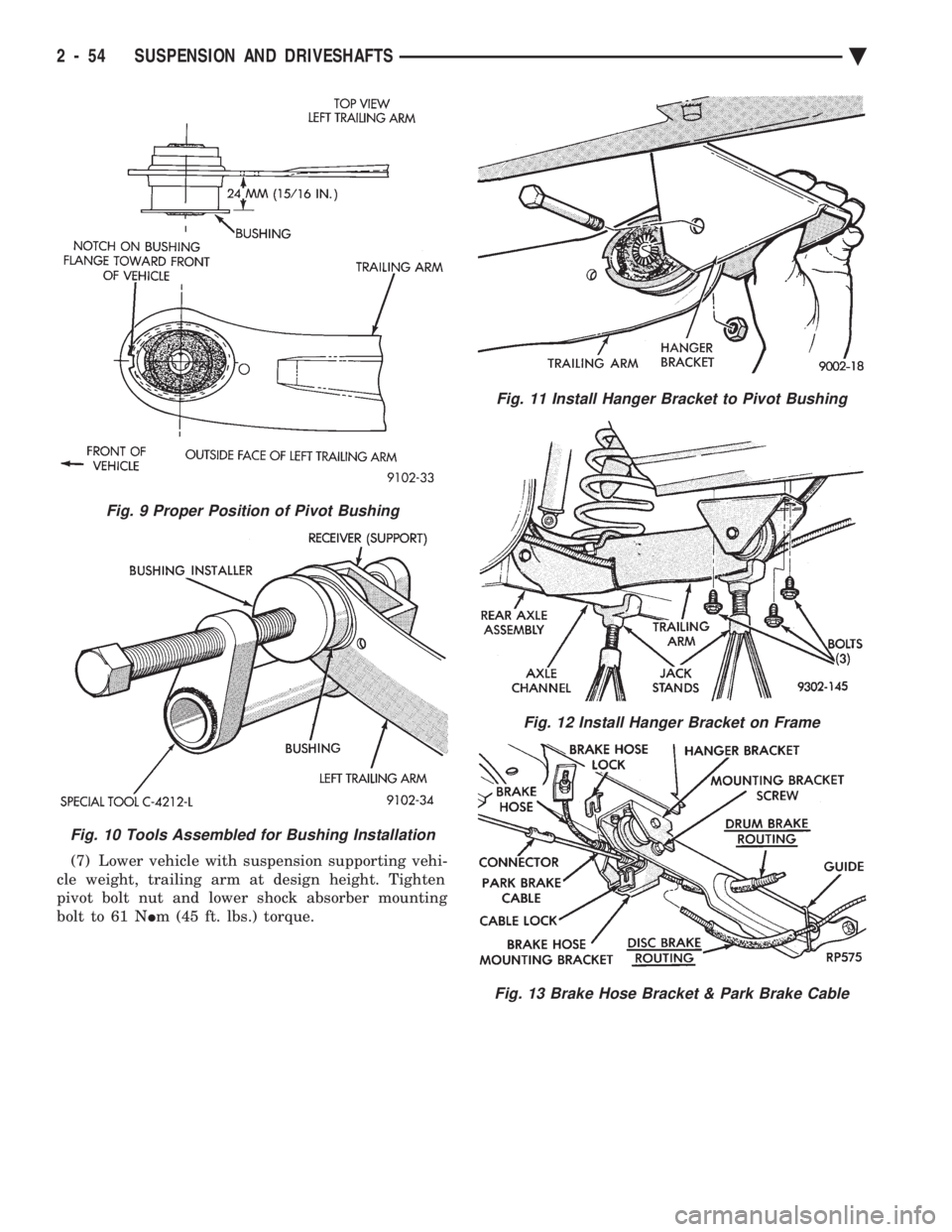
(7) Lower vehicle with suspension supporting vehi-
cle weight, trailing arm at design height. Tighten
pivot bolt nut and lower shock absorber mounting
bolt to 61 N Im (45 ft. lbs.) torque.
Fig. 9 Proper Position of Pivot Bushing
Fig. 10 Tools Assembled for Bushing Installation
Fig. 11 Install Hanger Bracket to Pivot Bushing
Fig. 12 Install Hanger Bracket on Frame
Fig. 13 Brake Hose Bracket & Park Brake Cable
2 - 54 SUSPENSION AND DRIVESHAFTS Ä
Page 113 of 2438
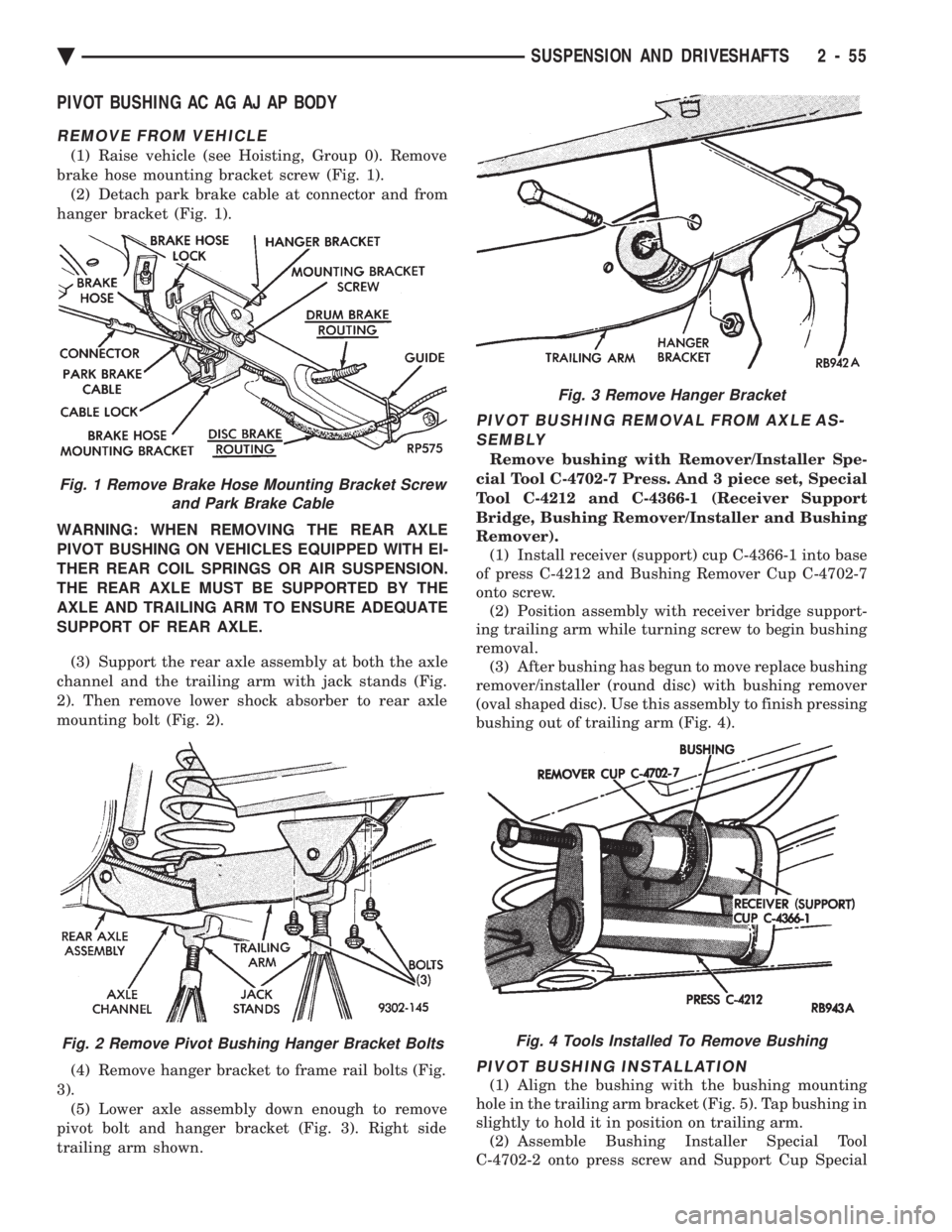
PIVOT BUSHING AC AG AJ AP BODY
REMOVE FROM VEHICLE
(1) Raise vehicle (see Hoisting, Group 0). Remove
brake hose mounting bracket screw (Fig. 1). (2) Detach park brake cable at connector and from
hanger bracket (Fig. 1).
WARNING: WHEN REMOVING THE REAR AXLE
PIVOT BUSHING ON VEHICLES EQUIPPED WITH EI-
THER REAR COIL SPRINGS OR AIR SUSPENSION.
THE REAR AXLE MUST BE SUPPORTED BY THE
AXLE AND TRAILING ARM TO ENSURE ADEQUATE
SUPPORT OF REAR AXLE. (3) Support the rear axle assembly at both the axle
channel and the trailing arm with jack stands (Fig.
2). Then remove lower shock absorber to rear axle
mounting bolt (Fig. 2).
(4) Remove hanger bracket to frame rail bolts (Fig.
3). (5) Lower axle assembly down enough to remove
pivot bolt and hanger bracket (Fig. 3). Right side
trailing arm shown.
PIVOT BUSHING REMOVAL FROM AXLE AS- SEMBLY
Remove bushing with Remover/Installer Spe-
cial Tool C-4702-7 Press. And 3 piece set, Special
Tool C-4212 and C-4366-1 (Receiver Support
Bridge, Bushing Remover/Installer and Bushing
Remover). (1) Install receiver (support) cup C-4366-1 into base
of press C-4212 and Bushing Remover Cup C-4702-7
onto screw. (2) Position assembly with receiver bridge support-
ing trailing arm while turning screw to begin bushing
removal. (3) After bushing has begun to move replace bushing
remover/installer (round disc) with bushing remover
(oval shaped disc). Use this assembly to finish pressing
bushing out of trailing arm (Fig. 4).
PIVOT BUSHING INSTALLATION
(1) Align the bushing with the bushing mounting
hole in the trailing arm bracket (Fig. 5). Tap bushing in
slightly to hold it in position on trailing arm. (2) Assemble Bushing Installer Special Tool
C-4702-2 onto press screw and Support Cup Special
Fig. 1 Remove Brake Hose Mounting Bracket Screw and Park Brake Cable
Fig. 2 Remove Pivot Bushing Hanger Bracket Bolts
Fig. 3 Remove Hanger Bracket
Fig. 4 Tools Installed To Remove Bushing
Ä SUSPENSION AND DRIVESHAFTS 2 - 55
Page 114 of 2438
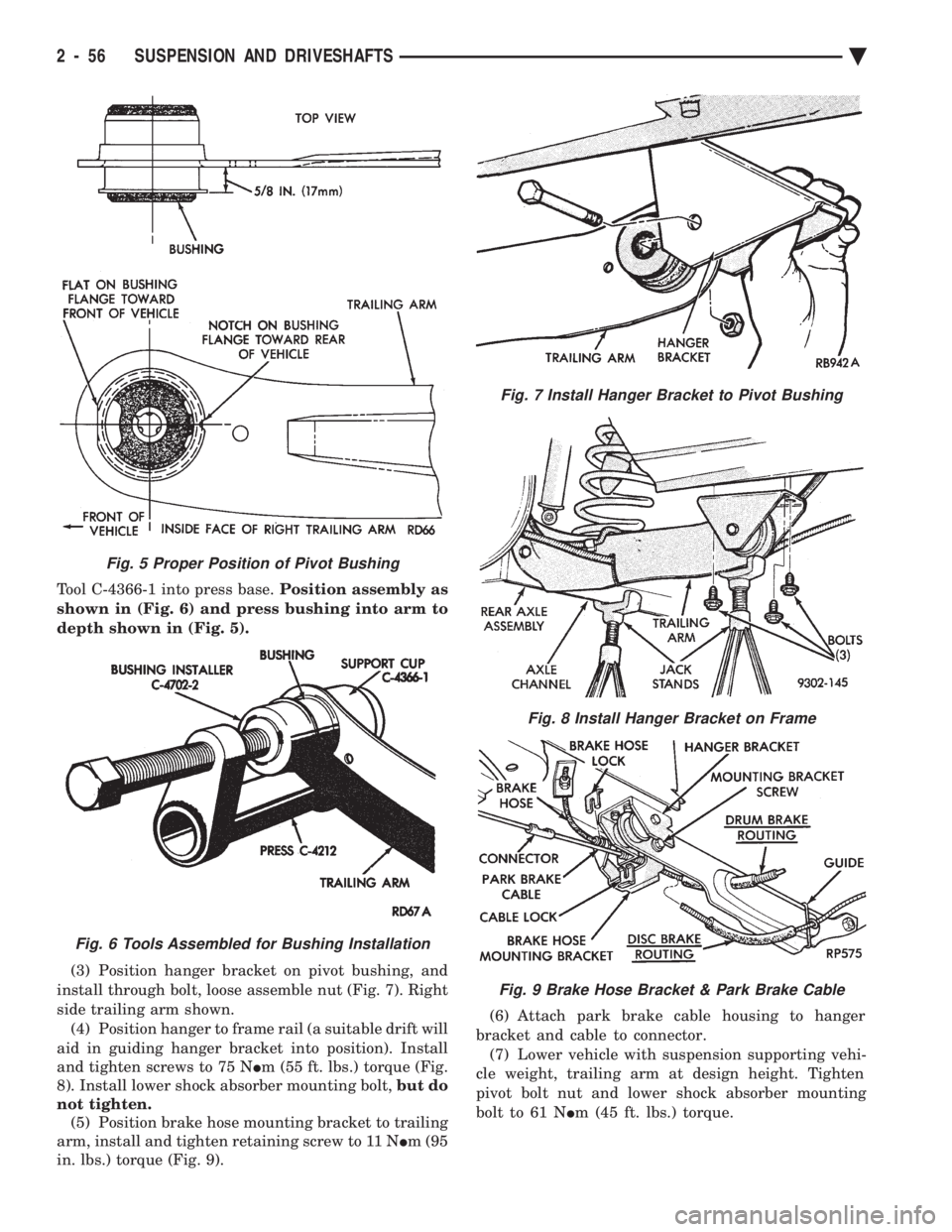
Tool C-4366-1 into press base. Position assembly as
shown in (Fig. 6) and press bushing into arm to
depth shown in (Fig. 5).
(3) Position hanger bracket on pivot bushing, and
install through bolt, loose assemble nut (Fig. 7). Right
side trailing arm shown. (4) Position hanger to frame rail (a suitable drift will
aid in guiding hanger bracket into position). Install
and tighten screws to 75 N Im (55 ft. lbs.) torque (Fig.
8). Install lower shock absorber mounting bolt, but do
not tighten. (5) Position brake hose mounting bracket to trailing
arm, install and tighten retaining screw to 11 N Im (95
in. lbs.) torque (Fig. 9). (6) Attach park brake cable housing to hanger
bracket and cable to connector. (7) Lower vehicle with suspension supporting vehi-
cle weight, trailing arm at design height. Tighten
pivot bolt nut and lower shock absorber mounting
bolt to 61 N Im (45 ft. lbs.) torque.
Fig. 7 Install Hanger Bracket to Pivot Bushing
Fig. 8 Install Hanger Bracket on Frame
Fig. 9 Brake Hose Bracket & Park Brake Cable
Fig. 5 Proper Position of Pivot Bushing
Fig. 6 Tools Assembled for Bushing Installation
2 - 56 SUSPENSION AND DRIVESHAFTS Ä
Page 115 of 2438
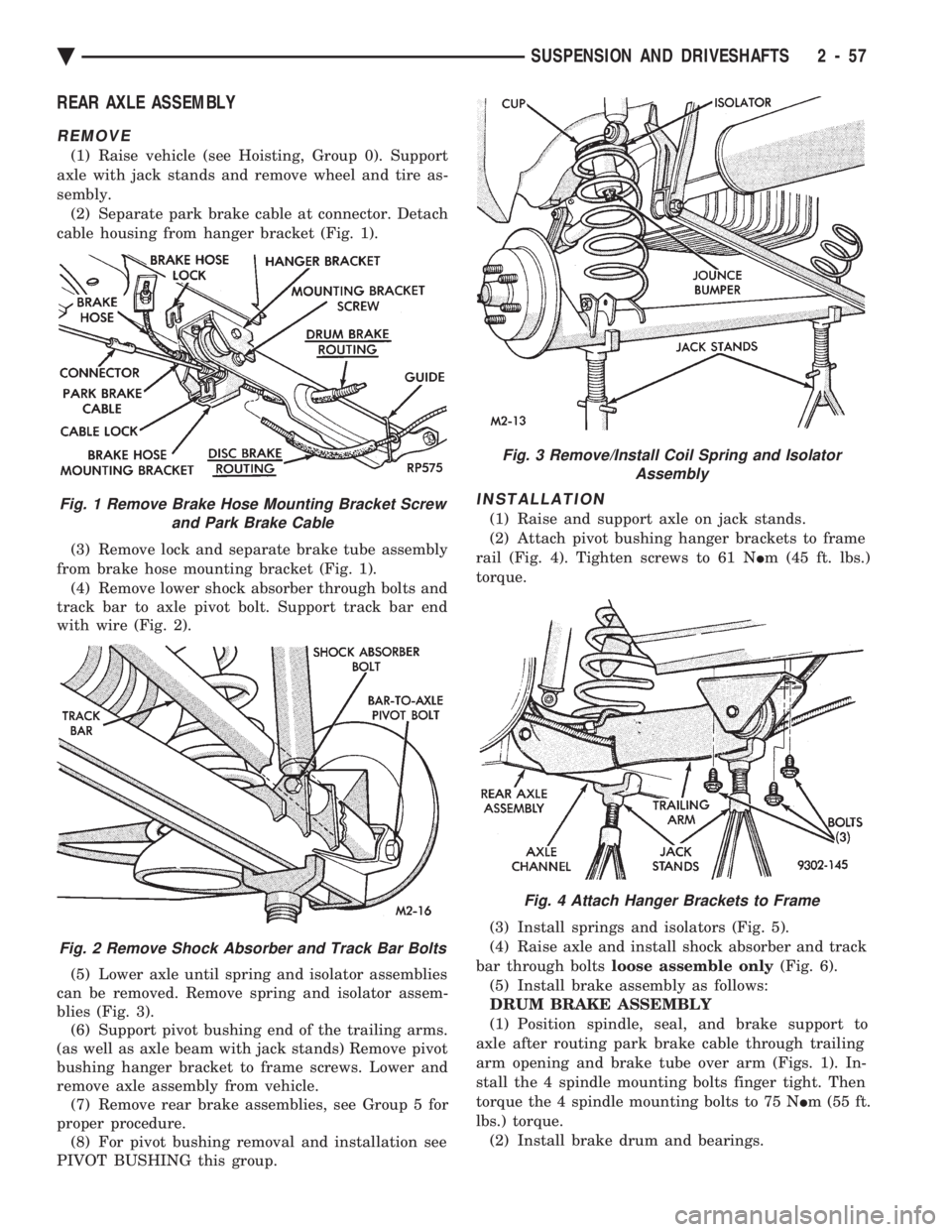
REAR AXLE ASSEMBLY
REMOVE
(1) Raise vehicle (see Hoisting, Group 0). Support
axle with jack stands and remove wheel and tire as-
sembly. (2) Separate park brake cable at connector. Detach
cable housing from hanger bracket (Fig. 1).
(3) Remove lock and separate brake tube assembly
from brake hose mounting bracket (Fig. 1). (4) Remove lower shock absorber through bolts and
track bar to axle pivot bolt. Support track bar end
with wire (Fig. 2).
(5) Lower axle until spring and isolator assemblies
can be removed. Remove spring and isolator assem-
blies (Fig. 3). (6) Support pivot bushing end of the trailing arms.
(as well as axle beam with jack stands) Remove pivot
bushing hanger bracket to frame screws. Lower and
remove axle assembly from vehicle. (7) Remove rear brake assemblies, see Group 5 for
proper procedure. (8) For pivot bushing removal and installation see
PIVOT BUSHING this group.
INSTALLATION
(1) Raise and support axle on jack stands.
(2) Attach pivot bushing hanger brackets to frame
rail (Fig. 4). Tighten screws to 61 N Im (45 ft. lbs.)
torque.
(3) Install springs and isolators (Fig. 5).
(4) Raise axle and install shock absorber and track
bar through bolts loose assemble only (Fig. 6).
(5) Install brake assembly as follows:
DRUM BRAKE ASSEMBLY
(1) Position spindle, seal, and brake support to
axle after routing park brake cable through trailing
arm opening and brake tube over arm (Figs. 1). In-
stall the 4 spindle mounting bolts finger tight. Then
torque the 4 spindle mounting bolts to 75 N Im (55 ft.
lbs.) torque. (2) Install brake drum and bearings.Fig. 1 Remove Brake Hose Mounting Bracket Screw and Park Brake Cable
Fig. 2 Remove Shock Absorber and Track Bar Bolts
Fig. 3 Remove/Install Coil Spring and Isolator Assembly
Fig. 4 Attach Hanger Brackets to Frame
Ä SUSPENSION AND DRIVESHAFTS 2 - 57
Page 116 of 2438
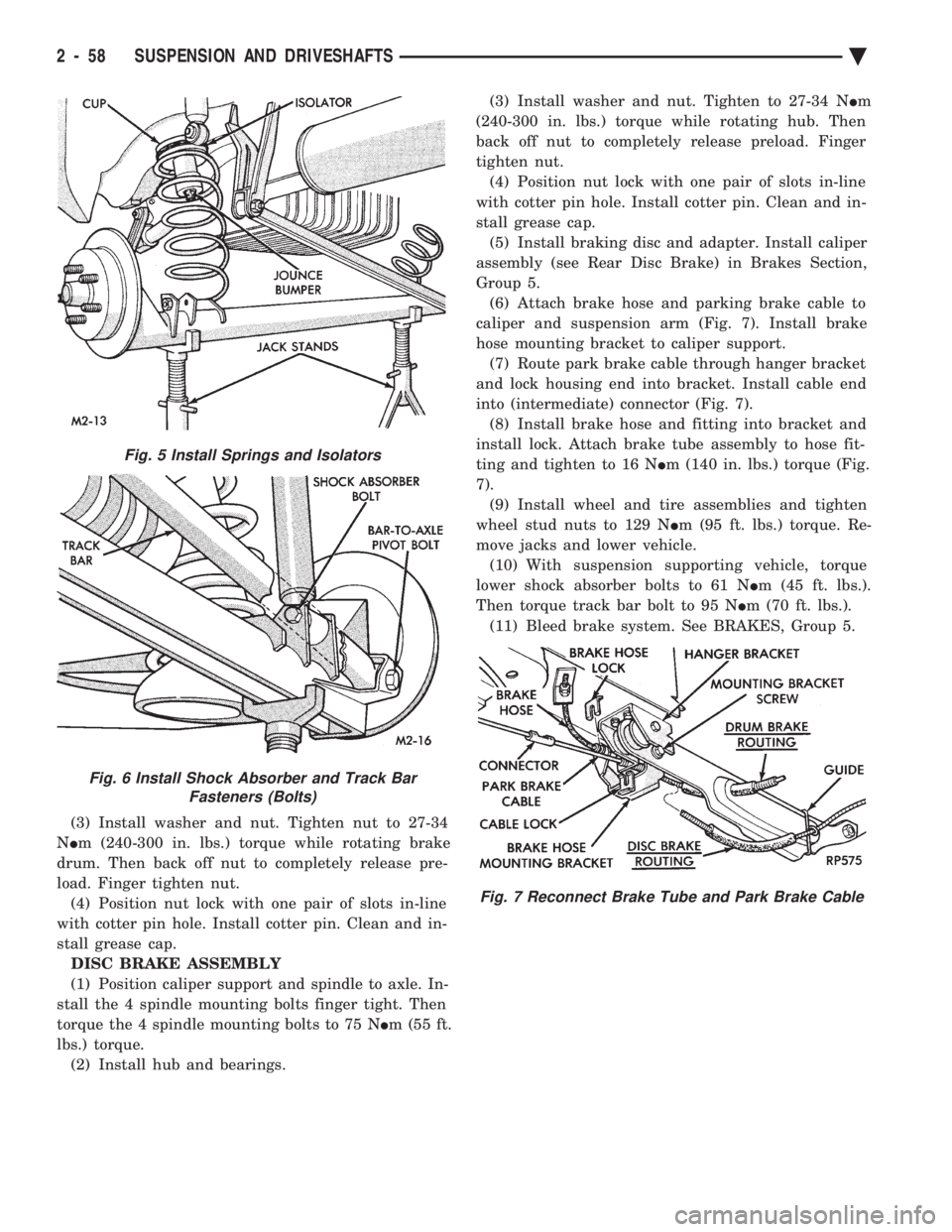
(3) Install washer and nut. Tighten nut to 27-34
N Im (240-300 in. lbs.) torque while rotating brake
drum. Then back off nut to completely release pre-
load. Finger tighten nut. (4) Position nut lock with one pair of slots in-line
with cotter pin hole. Install cotter pin. Clean and in-
stall grease cap. DISC BRAKE ASSEMBLY
(1) Position caliper support and spindle to axle. In-
stall the 4 spindle mounting bolts finger tight. Then
torque the 4 spindle mounting bolts to 75 N Im (55 ft.
lbs.) torque. (2) Install hub and bearings. (3) Install washer and nut. Tighten to 27-34 N
Im
(240-300 in. lbs.) torque while rotating hub. Then
back off nut to completely release preload. Finger
tighten nut. (4) Position nut lock with one pair of slots in-line
with cotter pin hole. Install cotter pin. Clean and in-
stall grease cap. (5) Install braking disc and adapter. Install caliper
assembly (see Rear Disc Brake) in Brakes Section,
Group 5. (6) Attach brake hose and parking brake cable to
caliper and suspension arm (Fig. 7). Install brake
hose mounting bracket to caliper support. (7) Route park brake cable through hanger bracket
and lock housing end into bracket. Install cable end
into (intermediate) connector (Fig. 7). (8) Install brake hose and fitting into bracket and
install lock. Attach brake tube assembly to hose fit-
ting and tighten to 16 N Im (140 in. lbs.) torque (Fig.
7). (9) Install wheel and tire assemblies and tighten
wheel stud nuts to 129 N Im (95 ft. lbs.) torque. Re-
move jacks and lower vehicle. (10) With suspension supporting vehicle, torque
lower shock absorber bolts to 61 N Im (45 ft. lbs.).
Then torque track bar bolt to 95 N Im (70 ft. lbs.).
(11) Bleed brake system. See BRAKES, Group 5.
Fig. 5 Install Springs and Isolators
Fig. 6 Install Shock Absorber and Track Bar Fasteners (Bolts)
Fig. 7 Reconnect Brake Tube and Park Brake Cable
2 - 58 SUSPENSION AND DRIVESHAFTS Ä
Page 117 of 2438
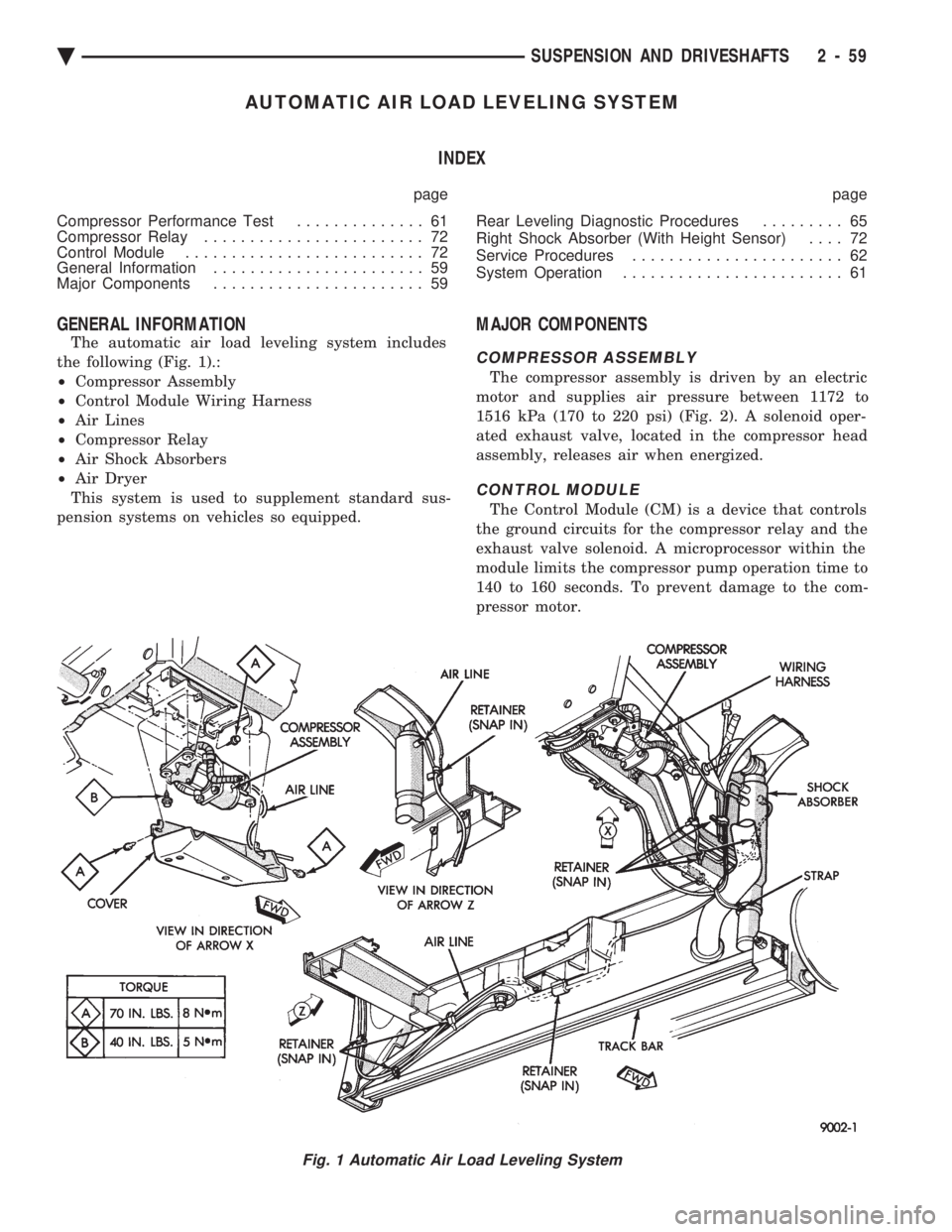
AUTOMATIC AIR LOAD LEVELING SYSTEM INDEX
page page
Compressor Performance Test .............. 61
Compressor Relay ........................ 72
Control Module .......................... 72
General Information ....................... 59
Major Components ....................... 59 Rear Leveling Diagnostic Procedures
......... 65
Right Shock Absorber (With Height Sensor) .... 72
Service Procedures ....................... 62
System Operation ........................ 61
GENERAL INFORMATION
The automatic air load leveling system includes
the following (Fig. 1).:
² Compressor Assembly
² Control Module Wiring Harness
² Air Lines
² Compressor Relay
² Air Shock Absorbers
² Air Dryer
This system is used to supplement standard sus-
pension systems on vehicles so equipped.
MAJOR COMPONENTS
COMPRESSOR ASSEMBLY
The compressor assembly is driven by an electric
motor and supplies air pressure between 1172 to
1516 kPa (170 to 220 psi) (Fig. 2). A solenoid oper-
ated exhaust valve, located in the compressor head
assembly, releases air when energized.
CONTROL MODULE
The Control Module (CM) is a device that controls
the ground circuits for the compressor relay and the
exhaust valve solenoid. A microprocessor within the
module limits the compressor pump operation time to
140 to 160 seconds. To prevent damage to the com-
pressor motor.
Fig. 1 Automatic Air Load Leveling System
Ä SUSPENSION AND DRIVESHAFTS 2 - 59
Page 118 of 2438
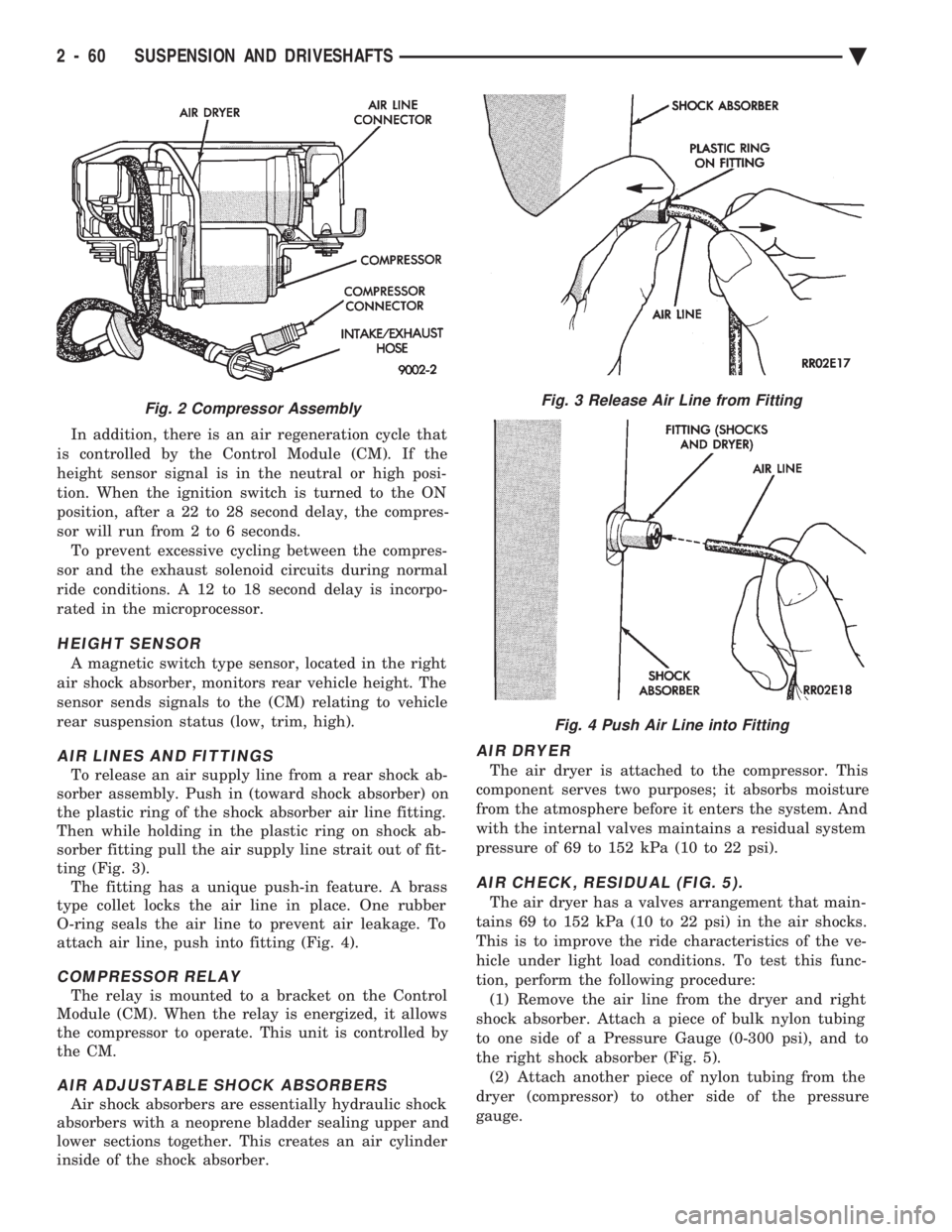
In addition, there is an air regeneration cycle that
is controlled by the Control Module (CM). If the
height sensor signal is in the neutral or high posi-
tion. When the ignition switch is turned to the ON
position, after a 22 to 28 second delay, the compres-
sor will run from 2 to 6 seconds. To prevent excessive cycling between the compres-
sor and the exhaust solenoid circuits during normal
ride conditions. A 12 to 18 second delay is incorpo-
rated in the microprocessor.
HEIGHT SENSOR
A magnetic switch type sensor, located in the right
air shock absorber, monitors rear vehicle height. The
sensor sends signals to the (CM) relating to vehicle
rear suspension status (low, trim, high).
AIR LINES AND FITTINGS
To release an air supply line from a rear shock ab-
sorber assembly. Push in (toward shock absorber) on
the plastic ring of the shock absorber air line fitting.
Then while holding in the plastic ring on shock ab-
sorber fitting pull the air supply line strait out of fit-
ting (Fig. 3). The fitting has a unique push-in feature. A brass
type collet locks the air line in place. One rubber
O-ring seals the air line to prevent air leakage. To
attach air line, push into fitting (Fig. 4).
COMPRESSOR RELAY
The relay is mounted to a bracket on the Control
Module (CM). When the relay is energized, it allows
the compressor to operate. This unit is controlled by
the CM.
AIR ADJUSTABLE SHOCK ABSORBERS
Air shock absorbers are essentially hydraulic shock
absorbers with a neoprene bladder sealing upper and
lower sections together. This creates an air cylinder
inside of the shock absorber.
AIR DRYER
The air dryer is attached to the compressor. This
component serves two purposes; it absorbs moisture
from the atmosphere before it enters the system. And
with the internal valves maintains a residual system
pressure of 69 to 152 kPa (10 to 22 psi).
AIR CHECK, RESIDUAL (FIG. 5).
The air dryer has a valves arrangement that main-
tains 69 to 152 kPa (10 to 22 psi) in the air shocks.
This is to improve the ride characteristics of the ve-
hicle under light load conditions. To test this func-
tion, perform the following procedure: (1) Remove the air line from the dryer and right
shock absorber. Attach a piece of bulk nylon tubing
to one side of a Pressure Gauge (0-300 psi), and to
the right shock absorber (Fig. 5). (2) Attach another piece of nylon tubing from the
dryer (compressor) to other side of the pressure
gauge.
Fig. 2 Compressor AssemblyFig. 3 Release Air Line from Fitting
Fig. 4 Push Air Line into Fitting
2 - 60 SUSPENSION AND DRIVESHAFTS Ä
Page 119 of 2438
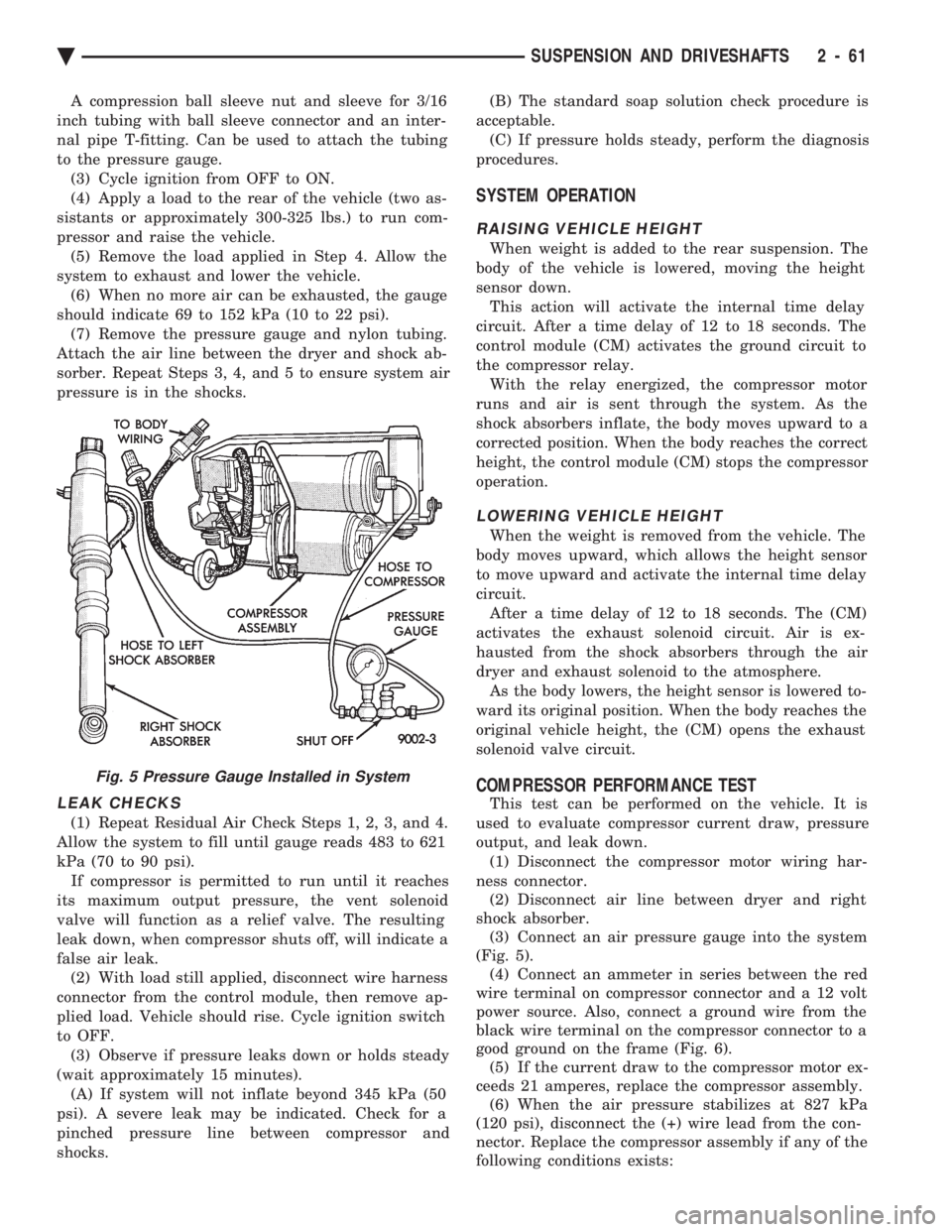
A compression ball sleeve nut and sleeve for 3/16
inch tubing with ball sleeve connector and an inter-
nal pipe T-fitting. Can be used to attach the tubing
to the pressure gauge. (3) Cycle ignition from OFF to ON.
(4) Apply a load to the rear of the vehicle (two as-
sistants or approximately 300-325 lbs.) to run com-
pressor and raise the vehicle. (5) Remove the load applied in Step 4. Allow the
system to exhaust and lower the vehicle. (6) When no more air can be exhausted, the gauge
should indicate 69 to 152 kPa (10 to 22 psi). (7) Remove the pressure gauge and nylon tubing.
Attach the air line between the dryer and shock ab-
sorber. Repeat Steps 3, 4, and 5 to ensure system air
pressure is in the shocks.
LEAK CHECKS
(1) Repeat Residual Air Check Steps 1, 2, 3, and 4.
Allow the system to fill until gauge reads 483 to 621
kPa (70 to 90 psi). If compressor is permitted to run until it reaches
its maximum output pressure, the vent solenoid
valve will function as a relief valve. The resulting
leak down, when compressor shuts off, will indicate a
false air leak. (2) With load still applied, disconnect wire harness
connector from the control module, then remove ap-
plied load. Vehicle should rise. Cycle ignition switch
to OFF. (3) Observe if pressure leaks down or holds steady
(wait approximately 15 minutes). (A) If system will not inflate beyond 345 kPa (50
psi). A severe leak may be indicated. Check for a
pinched pressure line between compressor and
shocks. (B) The standard soap solution check procedure is
acceptable. (C) If pressure holds steady, perform the diagnosis
procedures.
SYSTEM OPERATION
RAISING VEHICLE HEIGHT
When weight is added to the rear suspension. The
body of the vehicle is lowered, moving the height
sensor down. This action will activate the internal time delay
circuit. After a time delay of 12 to 18 seconds. The
control module (CM) activates the ground circuit to
the compressor relay. With the relay energized, the compressor motor
runs and air is sent through the system. As the
shock absorbers inflate, the body moves upward to a
corrected position. When the body reaches the correct
height, the control module (CM) stops the compressor
operation.
LOWERING VEHICLE HEIGHT
When the weight is removed from the vehicle. The
body moves upward, which allows the height sensor
to move upward and activate the internal time delay
circuit. After a time delay of 12 to 18 seconds. The (CM)
activates the exhaust solenoid circuit. Air is ex-
hausted from the shock absorbers through the air
dryer and exhaust solenoid to the atmosphere. As the body lowers, the height sensor is lowered to-
ward its original position. When the body reaches the
original vehicle height, the (CM) opens the exhaust
solenoid valve circuit.
COMPRESSOR PERFORMANCE TEST
This test can be performed on the vehicle. It is
used to evaluate compressor current draw, pressure
output, and leak down. (1) Disconnect the compressor motor wiring har-
ness connector. (2) Disconnect air line between dryer and right
shock absorber. (3) Connect an air pressure gauge into the system
(Fig. 5). (4) Connect an ammeter in series between the red
wire terminal on compressor connector and a 12 volt
power source. Also, connect a ground wire from the
black wire terminal on the compressor connector to a
good ground on the frame (Fig. 6). (5) If the current draw to the compressor motor ex-
ceeds 21 amperes, replace the compressor assembly. (6) When the air pressure stabilizes at 827 kPa
(120 psi), disconnect the (+) wire lead from the con-
nector. Replace the compressor assembly if any of the
following conditions exists:
Fig. 5 Pressure Gauge Installed in System
Ä SUSPENSION AND DRIVESHAFTS 2 - 61
Page 120 of 2438
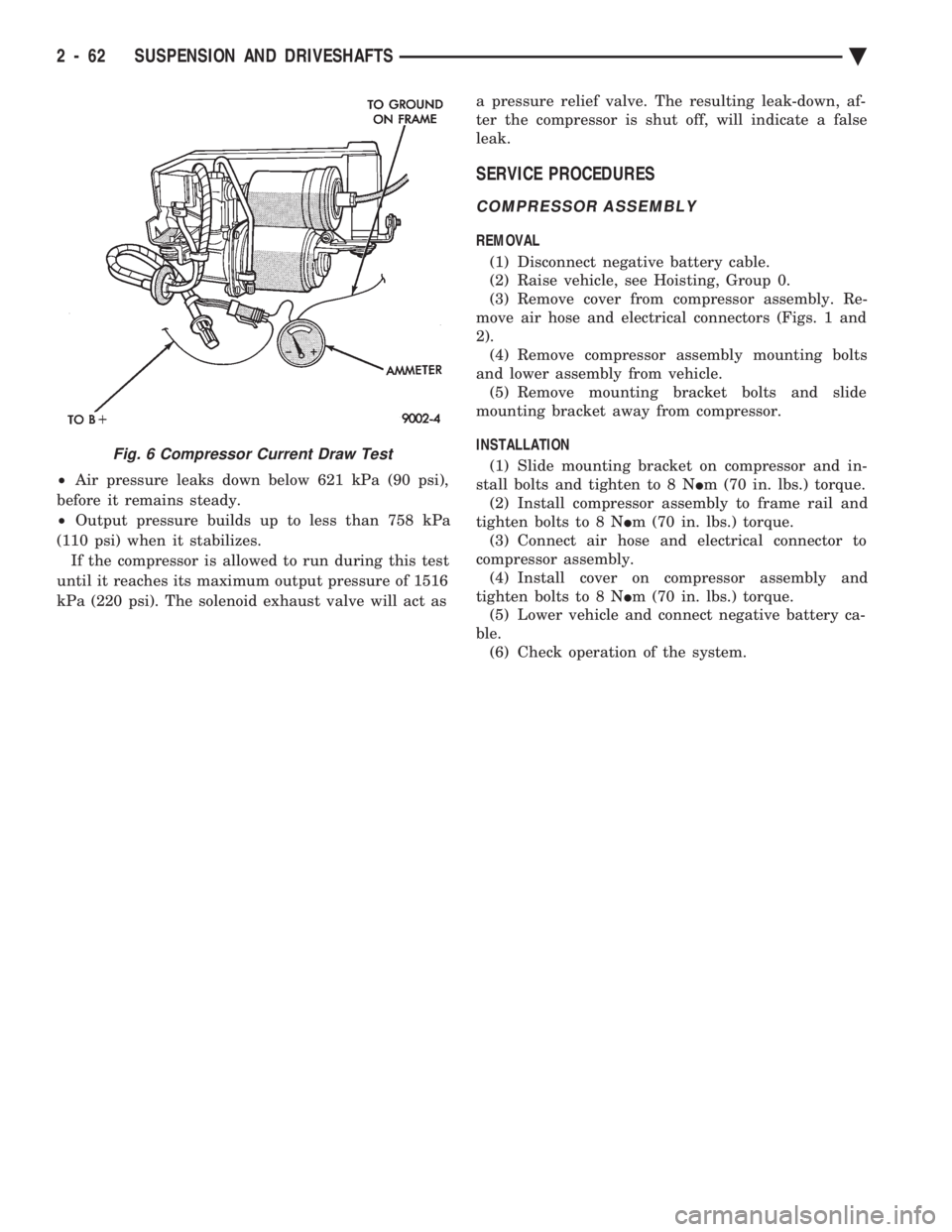
² Air pressure leaks down below 621 kPa (90 psi),
before it remains steady.
² Output pressure builds up to less than 758 kPa
(110 psi) when it stabilizes. If the compressor is allowed to run during this test
until it reaches its maximum output pressure of 1516
kPa (220 psi). The solenoid exhaust valve will act as a pressure relief valve. The resulting leak-down, af-
ter the compressor is shut off, will indicate a false
leak.
SERVICE PROCEDURES
COMPRESSOR ASSEMBLY
REMOVAL
(1) Disconnect negative battery cable.
(2) Raise vehicle, see Hoisting, Group 0.
(3) Remove cover from compressor assembly. Re-
move air hose and electrical connectors (Figs. 1 and
2). (4) Remove compressor assembly mounting bolts
and lower assembly from vehicle. (5) Remove mounting bracket bolts and slide
mounting bracket away from compressor.
INSTALLATION (1) Slide mounting bracket on compressor and in-
stall bolts and tighten to 8 N Im (70 in. lbs.) torque.
(2) Install compressor assembly to frame rail and
tighten bolts to 8 N Im (70 in. lbs.) torque.
(3) Connect air hose and electrical connector to
compressor assembly. (4) Install cover on compressor assembly and
tighten bolts to 8 N Im (70 in. lbs.) torque.
(5) Lower vehicle and connect negative battery ca-
ble. (6) Check operation of the system.
Fig. 6 Compressor Current Draw Test
2 - 62 SUSPENSION AND DRIVESHAFTS Ä