compression ratio CHRYSLER CARAVAN 2005 User Guide
[x] Cancel search | Manufacturer: CHRYSLER, Model Year: 2005, Model line: CARAVAN, Model: CHRYSLER CARAVAN 2005Pages: 2339, PDF Size: 59.69 MB
Page 1270 of 2339
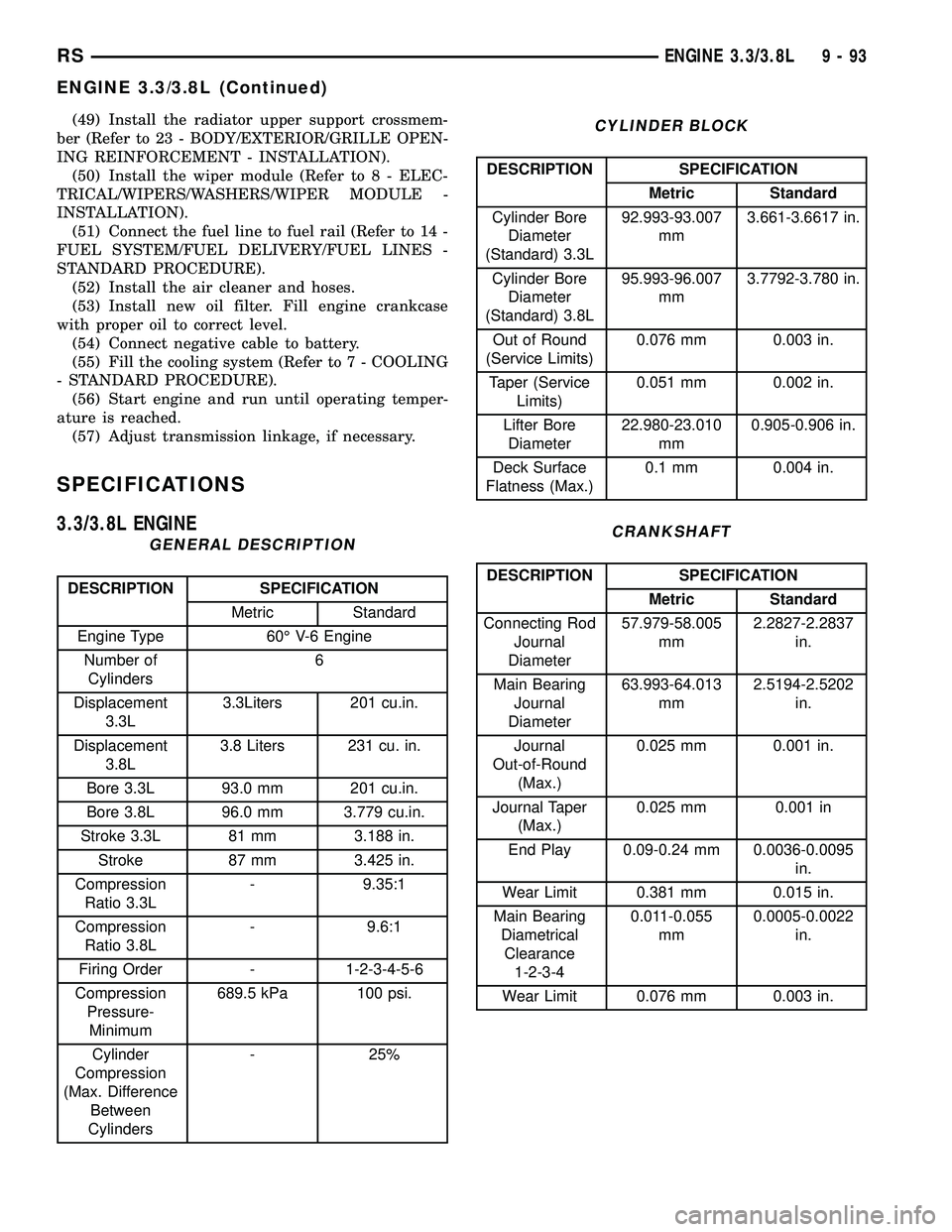
(49) Install the radiator upper support crossmem-
ber (Refer to 23 - BODY/EXTERIOR/GRILLE OPEN-
ING REINFORCEMENT - INSTALLATION).
(50) Install the wiper module (Refer to 8 - ELEC-
TRICAL/WIPERS/WASHERS/WIPER MODULE -
INSTALLATION).
(51) Connect the fuel line to fuel rail (Refer to 14 -
FUEL SYSTEM/FUEL DELIVERY/FUEL LINES -
STANDARD PROCEDURE).
(52) Install the air cleaner and hoses.
(53) Install new oil filter. Fill engine crankcase
with proper oil to correct level.
(54) Connect negative cable to battery.
(55) Fill the cooling system (Refer to 7 - COOLING
- STANDARD PROCEDURE).
(56) Start engine and run until operating temper-
ature is reached.
(57) Adjust transmission linkage, if necessary.
SPECIFICATIONS
3.3/3.8L ENGINE
GENERAL DESCRIPTION
DESCRIPTION SPECIFICATION
Metric Standard
Engine Type 60É V-6 Engine
Number of
Cylinders6
Displacement
3.3L3.3Liters 201 cu.in.
Displacement
3.8L3.8 Liters 231 cu. in.
Bore 3.3L 93.0 mm 201 cu.in.
Bore 3.8L 96.0 mm 3.779 cu.in.
Stroke 3.3L 81 mm 3.188 in.
Stroke 87 mm 3.425 in.
Compression
Ratio 3.3L- 9.35:1
Compression
Ratio 3.8L- 9.6:1
Firing Order - 1-2-3-4-5-6
Compression
Pressure-
Minimum689.5 kPa 100 psi.
Cylinder
Compression
(Max. Difference
Between
Cylinders- 25%
CYLINDER BLOCK
DESCRIPTION SPECIFICATION
Metric Standard
Cylinder Bore
Diameter
(Standard) 3.3L92.993-93.007
mm3.661-3.6617 in.
Cylinder Bore
Diameter
(Standard) 3.8L95.993-96.007
mm3.7792-3.780 in.
Out of Round
(Service Limits)0.076 mm 0.003 in.
Taper (Service
Limits)0.051 mm 0.002 in.
Lifter Bore
Diameter22.980-23.010
mm0.905-0.906 in.
Deck Surface
Flatness (Max.)0.1 mm 0.004 in.
CRANKSHAFT
DESCRIPTION SPECIFICATION
Metric Standard
Connecting Rod
Journal
Diameter57.979-58.005
mm2.2827-2.2837
in.
Main Bearing
Journal
Diameter63.993-64.013
mm2.5194-2.5202
in.
Journal
Out-of-Round
(Max.)0.025 mm 0.001 in.
Journal Taper
(Max.)0.025 mm 0.001 in
End Play 0.09-0.24 mm 0.0036-0.0095
in.
Wear Limit 0.381 mm 0.015 in.
Main Bearing
Diametrical
Clearance
1-2-3-40.011-0.055
mm0.0005-0.0022
in.
Wear Limit 0.076 mm 0.003 in.
RSENGINE 3.3/3.8L9-93
ENGINE 3.3/3.8L (Continued)
Page 1272 of 2339
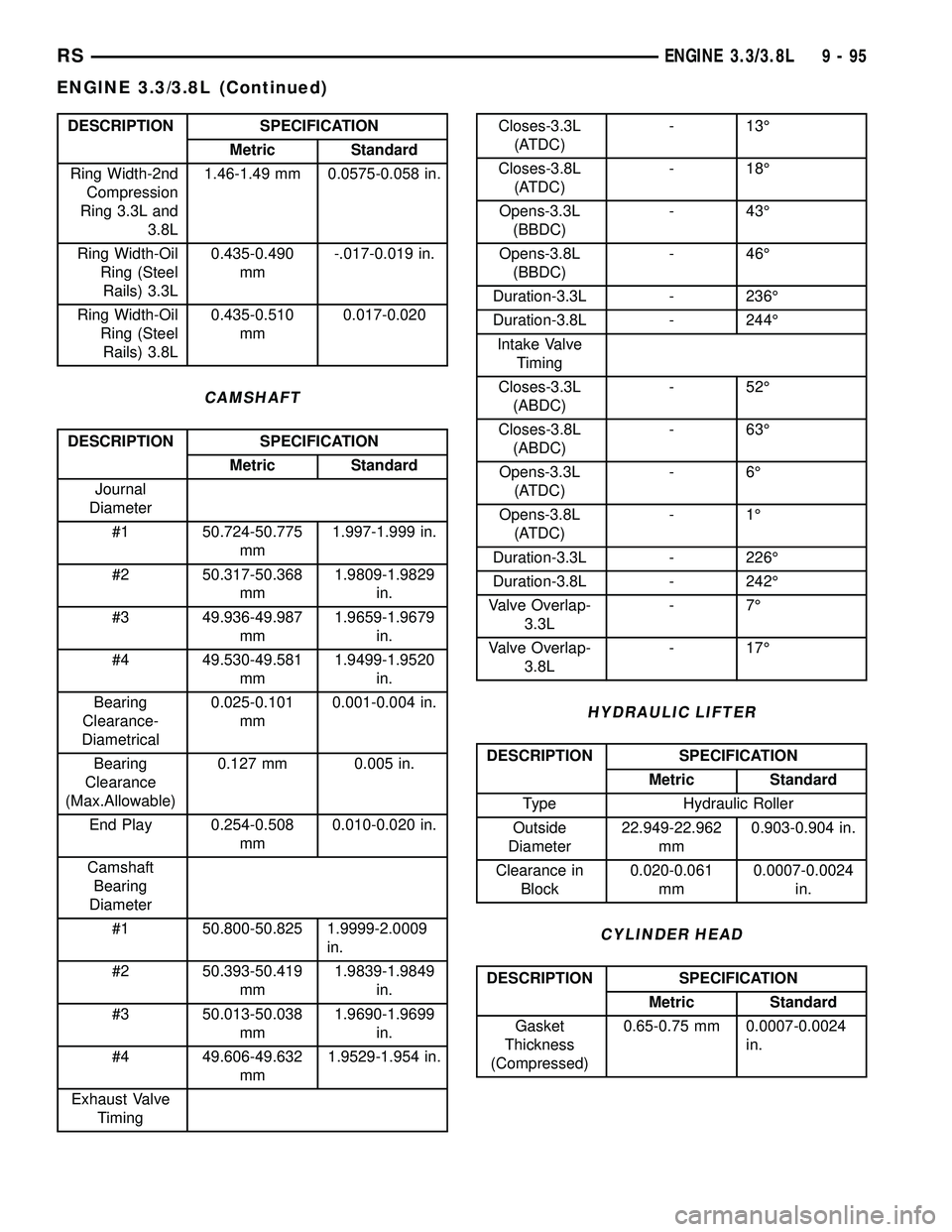
DESCRIPTION SPECIFICATION
Metric Standard
Ring Width-2nd
Compression
Ring 3.3L and
3.8L1.46-1.49 mm 0.0575-0.058 in.
Ring Width-Oil
Ring (Steel
Rails) 3.3L0.435-0.490
mm-.017-0.019 in.
Ring Width-Oil
Ring (Steel
Rails) 3.8L0.435-0.510
mm0.017-0.020
CAMSHAFT
DESCRIPTION SPECIFICATION
Metric Standard
Journal
Diameter
#1 50.724-50.775
mm1.997-1.999 in.
#2 50.317-50.368
mm1.9809-1.9829
in.
#3 49.936-49.987
mm1.9659-1.9679
in.
#4 49.530-49.581
mm1.9499-1.9520
in.
Bearing
Clearance-
Diametrical0.025-0.101
mm0.001-0.004 in.
Bearing
Clearance
(Max.Allowable)0.127 mm 0.005 in.
End Play 0.254-0.508
mm0.010-0.020 in.
Camshaft
Bearing
Diameter
#1 50.800-50.825 1.9999-2.0009
in.
#2 50.393-50.419
mm1.9839-1.9849
in.
#3 50.013-50.038
mm1.9690-1.9699
in.
#4 49.606-49.632
mm1.9529-1.954 in.
Exhaust Valve
Timing
Closes-3.3L
(ATDC)- 13É
Closes-3.8L
(ATDC)- 18É
Opens-3.3L
(BBDC)- 43É
Opens-3.8L
(BBDC)- 46É
Duration-3.3L - 236É
Duration-3.8L - 244É
Intake Valve
Timing
Closes-3.3L
(ABDC)- 52É
Closes-3.8L
(ABDC)- 63É
Opens-3.3L
(ATDC)-6É
Opens-3.8L
(ATDC)-1É
Duration-3.3L - 226É
Duration-3.8L - 242É
Valve Overlap-
3.3L-7É
Valve Overlap-
3.8L- 17É
HYDRAULIC LIFTER
DESCRIPTION SPECIFICATION
Metric Standard
Type Hydraulic Roller
Outside
Diameter22.949-22.962
mm0.903-0.904 in.
Clearance in
Block0.020-0.061
mm0.0007-0.0024
in.
CYLINDER HEAD
DESCRIPTION SPECIFICATION
Metric Standard
Gasket
Thickness
(Compressed)0.65-0.75 mm 0.0007-0.0024
in.
RSENGINE 3.3/3.8L9-95
ENGINE 3.3/3.8L (Continued)
Page 1279 of 2339
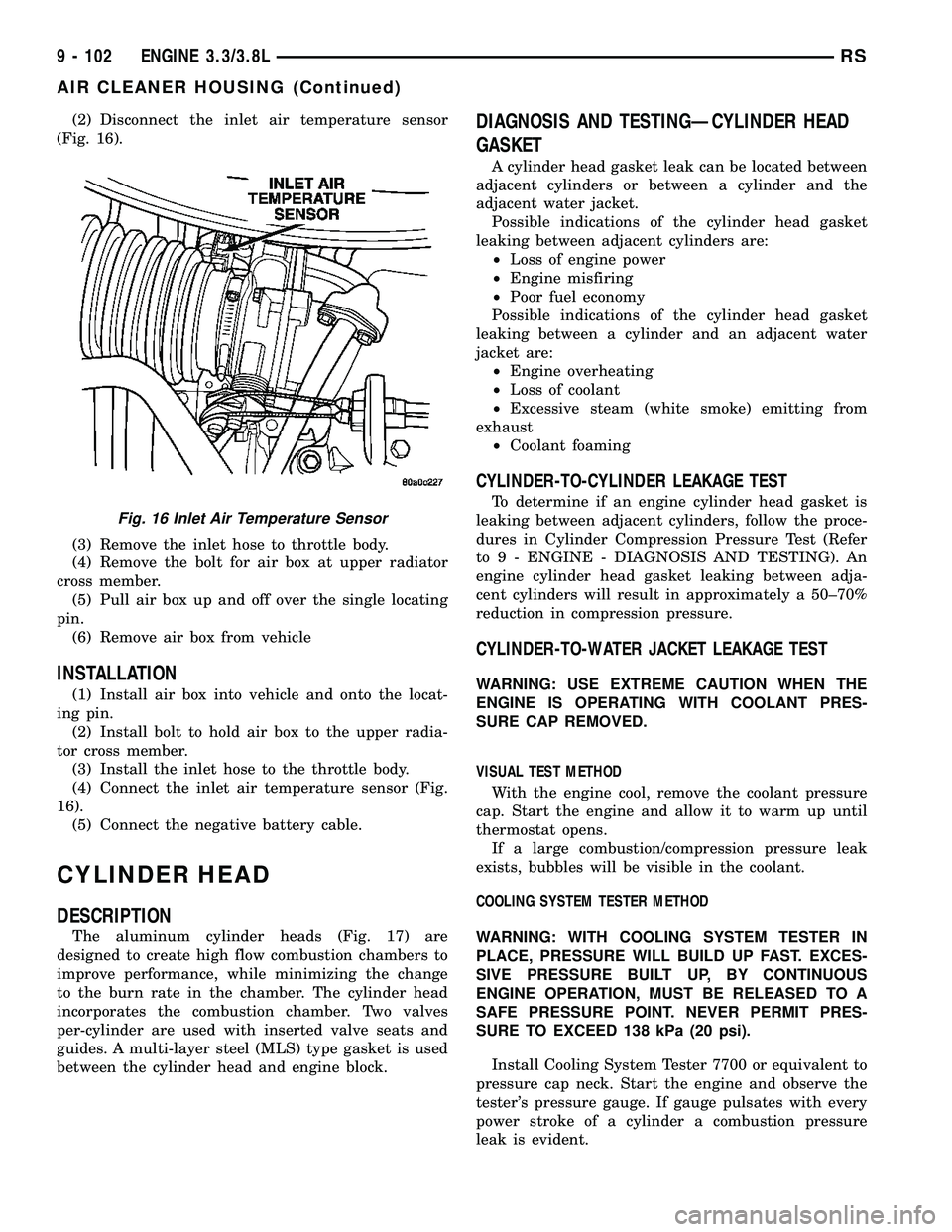
(2) Disconnect the inlet air temperature sensor
(Fig. 16).
(3) Remove the inlet hose to throttle body.
(4) Remove the bolt for air box at upper radiator
cross member.
(5) Pull air box up and off over the single locating
pin.
(6) Remove air box from vehicle
INSTALLATION
(1) Install air box into vehicle and onto the locat-
ing pin.
(2) Install bolt to hold air box to the upper radia-
tor cross member.
(3) Install the inlet hose to the throttle body.
(4) Connect the inlet air temperature sensor (Fig.
16).
(5) Connect the negative battery cable.
CYLINDER HEAD
DESCRIPTION
The aluminum cylinder heads (Fig. 17) are
designed to create high flow combustion chambers to
improve performance, while minimizing the change
to the burn rate in the chamber. The cylinder head
incorporates the combustion chamber. Two valves
per-cylinder are used with inserted valve seats and
guides. A multi-layer steel (MLS) type gasket is used
between the cylinder head and engine block.
DIAGNOSIS AND TESTINGÐCYLINDER HEAD
GASKET
A cylinder head gasket leak can be located between
adjacent cylinders or between a cylinder and the
adjacent water jacket.
Possible indications of the cylinder head gasket
leaking between adjacent cylinders are:
²Loss of engine power
²Engine misfiring
²Poor fuel economy
Possible indications of the cylinder head gasket
leaking between a cylinder and an adjacent water
jacket are:
²Engine overheating
²Loss of coolant
²Excessive steam (white smoke) emitting from
exhaust
²Coolant foaming
CYLINDER-TO-CYLINDER LEAKAGE TEST
To determine if an engine cylinder head gasket is
leaking between adjacent cylinders, follow the proce-
dures in Cylinder Compression Pressure Test (Refer
to 9 - ENGINE - DIAGNOSIS AND TESTING). An
engine cylinder head gasket leaking between adja-
cent cylinders will result in approximately a 50±70%
reduction in compression pressure.
CYLINDER-TO-WATER JACKET LEAKAGE TEST
WARNING: USE EXTREME CAUTION WHEN THE
ENGINE IS OPERATING WITH COOLANT PRES-
SURE CAP REMOVED.
VISUAL TEST METHOD
With the engine cool, remove the coolant pressure
cap. Start the engine and allow it to warm up until
thermostat opens.
If a large combustion/compression pressure leak
exists, bubbles will be visible in the coolant.
COOLING SYSTEM TESTER METHOD
WARNING: WITH COOLING SYSTEM TESTER IN
PLACE, PRESSURE WILL BUILD UP FAST. EXCES-
SIVE PRESSURE BUILT UP, BY CONTINUOUS
ENGINE OPERATION, MUST BE RELEASED TO A
SAFE PRESSURE POINT. NEVER PERMIT PRES-
SURE TO EXCEED 138 kPa (20 psi).
Install Cooling System Tester 7700 or equivalent to
pressure cap neck. Start the engine and observe the
tester's pressure gauge. If gauge pulsates with every
power stroke of a cylinder a combustion pressure
leak is evident.
Fig. 16 Inlet Air Temperature Sensor
9 - 102 ENGINE 3.3/3.8LRS
AIR CLEANER HOUSING (Continued)
Page 1298 of 2339
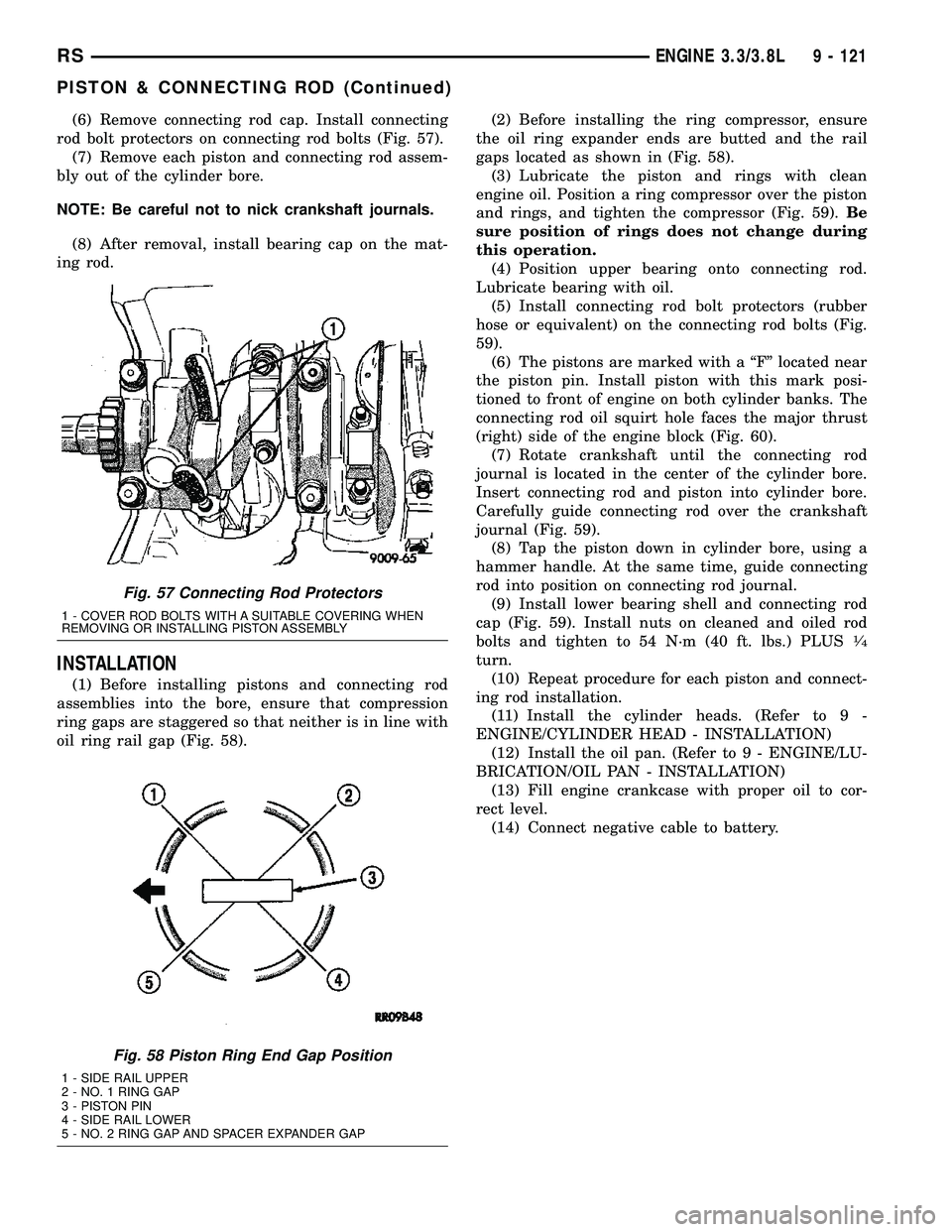
(6) Remove connecting rod cap. Install connecting
rod bolt protectors on connecting rod bolts (Fig. 57).
(7) Remove each piston and connecting rod assem-
bly out of the cylinder bore.
NOTE: Be careful not to nick crankshaft journals.
(8) After removal, install bearing cap on the mat-
ing rod.
INSTALLATION
(1) Before installing pistons and connecting rod
assemblies into the bore, ensure that compression
ring gaps are staggered so that neither is in line with
oil ring rail gap (Fig. 58).(2) Before installing the ring compressor, ensure
the oil ring expander ends are butted and the rail
gaps located as shown in (Fig. 58).
(3) Lubricate the piston and rings with clean
engine oil. Position a ring compressor over the piston
and rings, and tighten the compressor (Fig. 59).Be
sure position of rings does not change during
this operation.
(4) Position upper bearing onto connecting rod.
Lubricate bearing with oil.
(5) Install connecting rod bolt protectors (rubber
hose or equivalent) on the connecting rod bolts (Fig.
59).
(6) The pistons are marked with a ªFº located near
the piston pin. Install piston with this mark posi-
tioned to front of engine on both cylinder banks. The
connecting rod oil squirt hole faces the major thrust
(right) side of the engine block (Fig. 60).
(7) Rotate crankshaft until the connecting rod
journal is located in the center of the cylinder bore.
Insert connecting rod and piston into cylinder bore.
Carefully guide connecting rod over the crankshaft
journal (Fig. 59).
(8) Tap the piston down in cylinder bore, using a
hammer handle. At the same time, guide connecting
rod into position on connecting rod journal.
(9) Install lower bearing shell and connecting rod
cap (Fig. 59). Install nuts on cleaned and oiled rod
bolts and tighten to 54 N´m (40 ft. lbs.) PLUS
1¤4
turn.
(10) Repeat procedure for each piston and connect-
ing rod installation.
(11) Install the cylinder heads. (Refer to 9 -
ENGINE/CYLINDER HEAD - INSTALLATION)
(12) Install the oil pan. (Refer to 9 - ENGINE/LU-
BRICATION/OIL PAN - INSTALLATION)
(13) Fill engine crankcase with proper oil to cor-
rect level.
(14) Connect negative cable to battery.
Fig. 57 Connecting Rod Protectors
1 - COVER ROD BOLTS WITH A SUITABLE COVERING WHEN
REMOVING OR INSTALLING PISTON ASSEMBLY
Fig. 58 Piston Ring End Gap Position
1 - SIDE RAIL UPPER
2 - NO. 1 RING GAP
3 - PISTON PIN
4 - SIDE RAIL LOWER
5 - NO. 2 RING GAP AND SPACER EXPANDER GAP
RSENGINE 3.3/3.8L9 - 121
PISTON & CONNECTING ROD (Continued)
Page 1812 of 2339
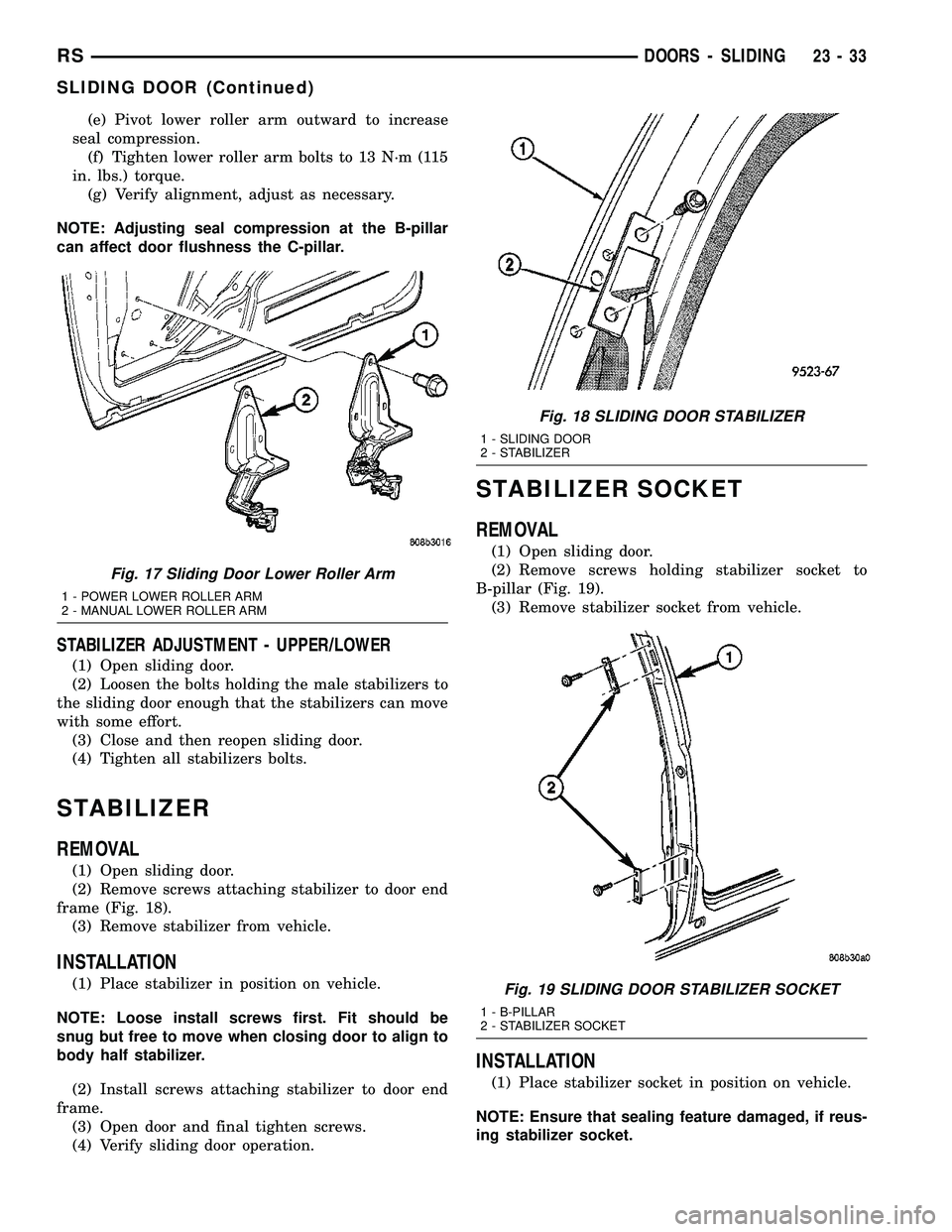
(e) Pivot lower roller arm outward to increase
seal compression.
(f) Tighten lower roller arm bolts to 13 N´m (115
in. lbs.) torque.
(g) Verify alignment, adjust as necessary.
NOTE: Adjusting seal compression at the B-pillar
can affect door flushness the C-pillar.
STABILIZER ADJUSTMENT - UPPER/LOWER
(1) Open sliding door.
(2) Loosen the bolts holding the male stabilizers to
the sliding door enough that the stabilizers can move
with some effort.
(3) Close and then reopen sliding door.
(4) Tighten all stabilizers bolts.
STABILIZER
REMOVAL
(1) Open sliding door.
(2) Remove screws attaching stabilizer to door end
frame (Fig. 18).
(3) Remove stabilizer from vehicle.
INSTALLATION
(1) Place stabilizer in position on vehicle.
NOTE: Loose install screws first. Fit should be
snug but free to move when closing door to align to
body half stabilizer.
(2) Install screws attaching stabilizer to door end
frame.
(3) Open door and final tighten screws.
(4) Verify sliding door operation.
STABILIZER SOCKET
REMOVAL
(1) Open sliding door.
(2) Remove screws holding stabilizer socket to
B-pillar (Fig. 19).
(3) Remove stabilizer socket from vehicle.
INSTALLATION
(1) Place stabilizer socket in position on vehicle.
NOTE: Ensure that sealing feature damaged, if reus-
ing stabilizer socket.
Fig. 17 Sliding Door Lower Roller Arm
1 - POWER LOWER ROLLER ARM
2 - MANUAL LOWER ROLLER ARM
Fig. 18 SLIDING DOOR STABILIZER
1 - SLIDING DOOR
2 - STABILIZER
Fig. 19 SLIDING DOOR STABILIZER SOCKET
1 - B-PILLAR
2 - STABILIZER SOCKET
RSDOORS - SLIDING23-33
SLIDING DOOR (Continued)
Page 2279 of 2339
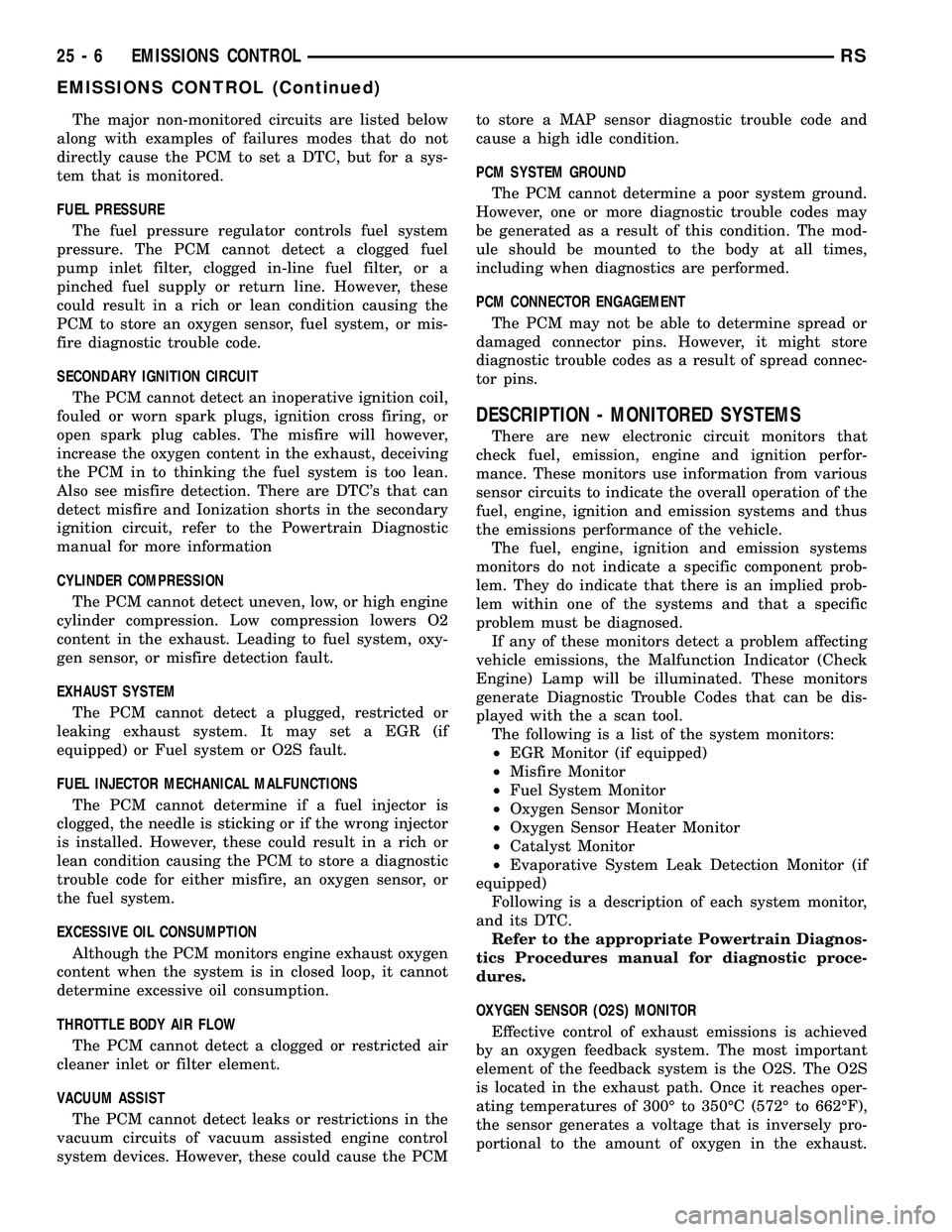
The major non-monitored circuits are listed below
along with examples of failures modes that do not
directly cause the PCM to set a DTC, but for a sys-
tem that is monitored.
FUEL PRESSURE
The fuel pressure regulator controls fuel system
pressure. The PCM cannot detect a clogged fuel
pump inlet filter, clogged in-line fuel filter, or a
pinched fuel supply or return line. However, these
could result in a rich or lean condition causing the
PCM to store an oxygen sensor, fuel system, or mis-
fire diagnostic trouble code.
SECONDARY IGNITION CIRCUIT
The PCM cannot detect an inoperative ignition coil,
fouled or worn spark plugs, ignition cross firing, or
open spark plug cables. The misfire will however,
increase the oxygen content in the exhaust, deceiving
the PCM in to thinking the fuel system is too lean.
Also see misfire detection. There are DTC's that can
detect misfire and Ionization shorts in the secondary
ignition circuit, refer to the Powertrain Diagnostic
manual for more information
CYLINDER COMPRESSION
The PCM cannot detect uneven, low, or high engine
cylinder compression. Low compression lowers O2
content in the exhaust. Leading to fuel system, oxy-
gen sensor, or misfire detection fault.
EXHAUST SYSTEM
The PCM cannot detect a plugged, restricted or
leaking exhaust system. It may set a EGR (if
equipped) or Fuel system or O2S fault.
FUEL INJECTOR MECHANICAL MALFUNCTIONS
The PCM cannot determine if a fuel injector is
clogged, the needle is sticking or if the wrong injector
is installed. However, these could result in a rich or
lean condition causing the PCM to store a diagnostic
trouble code for either misfire, an oxygen sensor, or
the fuel system.
EXCESSIVE OIL CONSUMPTION
Although the PCM monitors engine exhaust oxygen
content when the system is in closed loop, it cannot
determine excessive oil consumption.
THROTTLE BODY AIR FLOW
The PCM cannot detect a clogged or restricted air
cleaner inlet or filter element.
VACUUM ASSIST
The PCM cannot detect leaks or restrictions in the
vacuum circuits of vacuum assisted engine control
system devices. However, these could cause the PCMto store a MAP sensor diagnostic trouble code and
cause a high idle condition.
PCM SYSTEM GROUND
The PCM cannot determine a poor system ground.
However, one or more diagnostic trouble codes may
be generated as a result of this condition. The mod-
ule should be mounted to the body at all times,
including when diagnostics are performed.
PCM CONNECTOR ENGAGEMENT
The PCM may not be able to determine spread or
damaged connector pins. However, it might store
diagnostic trouble codes as a result of spread connec-
tor pins.
DESCRIPTION - MONITORED SYSTEMS
There are new electronic circuit monitors that
check fuel, emission, engine and ignition perfor-
mance. These monitors use information from various
sensor circuits to indicate the overall operation of the
fuel, engine, ignition and emission systems and thus
the emissions performance of the vehicle.
The fuel, engine, ignition and emission systems
monitors do not indicate a specific component prob-
lem. They do indicate that there is an implied prob-
lem within one of the systems and that a specific
problem must be diagnosed.
If any of these monitors detect a problem affecting
vehicle emissions, the Malfunction Indicator (Check
Engine) Lamp will be illuminated. These monitors
generate Diagnostic Trouble Codes that can be dis-
played with the a scan tool.
The following is a list of the system monitors:
²EGR Monitor (if equipped)
²Misfire Monitor
²Fuel System Monitor
²Oxygen Sensor Monitor
²Oxygen Sensor Heater Monitor
²Catalyst Monitor
²Evaporative System Leak Detection Monitor (if
equipped)
Following is a description of each system monitor,
and its DTC.
Refer to the appropriate Powertrain Diagnos-
tics Procedures manual for diagnostic proce-
dures.
OXYGEN SENSOR (O2S) MONITOR
Effective control of exhaust emissions is achieved
by an oxygen feedback system. The most important
element of the feedback system is the O2S. The O2S
is located in the exhaust path. Once it reaches oper-
ating temperatures of 300É to 350ÉC (572É to 662ÉF),
the sensor generates a voltage that is inversely pro-
portional to the amount of oxygen in the exhaust.
25 - 6 EMISSIONS CONTROLRS
EMISSIONS CONTROL (Continued)
Page 2308 of 2339
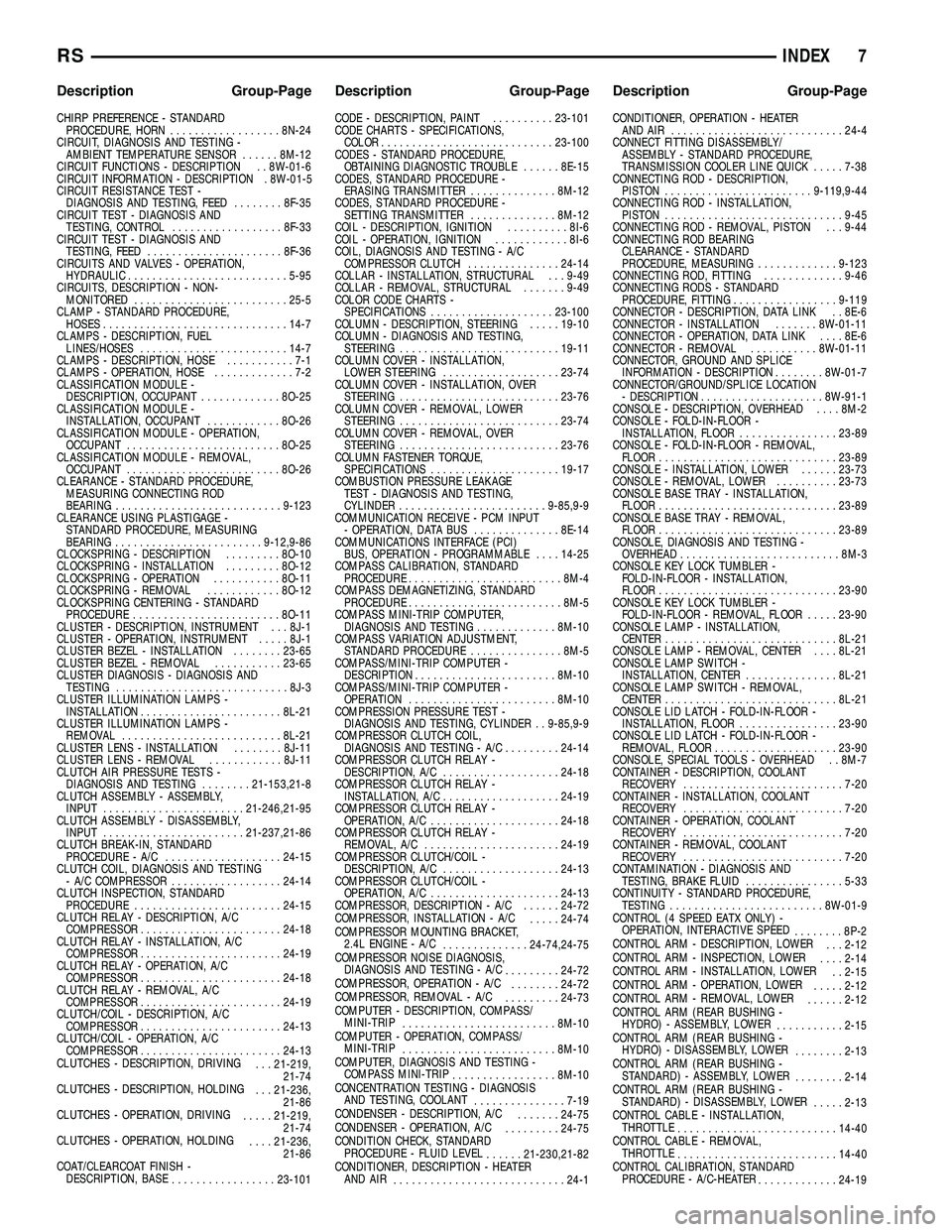
CHIRP PREFERENCE - STANDARDPROCEDURE, HORN .................. 8N-24
CIRCUIT, DIAGNOSIS AND TESTING - AMBIENT TEMPERATURE SENSOR ......8M-12
CIRCUIT FUNCTIONS - DESCRIPTION . . 8W-01-6
CIRCUIT INFORMATION - DESCRIPTION . 8W-01-5
CIRCUIT RESISTANCE TEST - DIAGNOSIS AND TESTING, FEED ........8F-35
CIRCUIT TEST - DIAGNOSIS AND TESTING, CONTROL .................. 8F-33
CIRCUIT TEST - DIAGNOSIS AND TESTING, FEED ...................... 8F-36
CIRCUITS AND VALVES - OPERATION, HYDRAULIC .......................... 5-95
CIRCUITS, DESCRIPTION - NON- MONITORED ......................... 25-5
CLAMP - STANDARD PROCEDURE, HOSES .............................. 14-7
CLAMPS - DESCRIPTION, FUEL LINES/HOSES ........................ 14-7
CLAMPS - DESCRIPTION, HOSE ...........7-1
CLAMPS - OPERATION, HOSE .............7-2
CLASSIFICATION MODULE - DESCRIPTION, OCCUPANT .............8O-25
CLASSIFICATION MODULE - INSTALLATION, OCCUPANT ............8O-26
CLASSIFICATION MODULE - OPERATION, OCCUPANT ......................... 8O-25
CLASSIFICATION MODULE - REMOVAL, OCCUPANT ......................... 8O-26
CLEARANCE - STANDARD PROCEDURE, MEASURING CONNECTING ROD
BEARING ............................ 9-123
CLEARANCE USING PLASTIGAGE - STANDARD PROCEDURE, MEASURING
BEARING ........................ 9-12,9-86
CLOCKSPRING - DESCRIPTION .........8O-10
CLOCKSPRING - INSTALLATION .........8O-12
CLOCKSPRING - OPERATION ...........8O-11
CLOCKSPRING - REMOVAL ............8O-12
CLOCKSPRING CENTERING - STANDARD PROCEDURE ........................ 8O-11
CLUSTER - DESCRIPTION, INSTRUMENT . . . 8J-1
CLUSTER - OPERATION, INSTRUMENT .....8J-1
CLUSTER BEZEL - INSTALLATION ........23-65
CLUSTER BEZEL - REMOVAL ...........23-65
CLUSTER DIAGNOSIS - DIAGNOSIS AND TESTING ............................ 8J-3
CLUSTER ILLUMINATION LAMPS - INSTALLATION ....................... 8L-21
CLUSTER ILLUMINATION LAMPS - REMOVAL .......................... 8L-21
CLUSTER LENS - INSTALLATION ........8J-11
CLUSTER LENS - REMOVAL ............8J-11
CLUTCH AIR PRESSURE TESTS - DIAGNOSIS AND TESTING ........21-153,21-8
CLUTCH ASSEMBLY - ASSEMBLY, INPUT ....................... 21-246,21-95
CLUTCH ASSEMBLY - DISASSEMBLY, INPUT ....................... 21-237,21-86
CLUTCH BREAK-IN, STANDARD PROCEDURE - A/C ................... 24-15
CLUTCH COIL, DIAGNOSIS AND TESTING - A/C COMPRESSOR .................. 24-14
CLUTCH INSPECTION, STANDARD PROCEDURE ........................ 24-15
CLUTCH RELAY - DESCRIPTION, A/C COMPRESSOR ....................... 24-18
CLUTCH RELAY - INSTALLATION, A/C COMPRESSOR ....................... 24-19
CLUTCH RELAY - OPERATION, A/C COMPRESSOR ....................... 24-18
CLUTCH RELAY - REMOVAL, A/C COMPRESSOR ....................... 24-19
CLUTCH/COIL - DESCRIPTION, A/C COMPRESSOR ....................... 24-13
CLUTCH/COIL - OPERATION, A/C COMPRESSOR ....................... 24-13
CLUTCHES - DESCRIPTION, DRIVING . . . 21-219,
21-74
CLUTCHES - DESCRIPTION, HOLDING . . . 21-236,
21-86
CLUTCHES - OPERATION, DRIVING .....21-219,
21-74
CLUTCHES - OPERATION, HOLDING ....21-236,
21-86
COAT/CLEARCOAT FINISH - DESCRIPTION, BASE .................23-101CODE - DESCRIPTION, PAINT
..........23-101
CODE CHARTS - SPECIFICATIONS, COLOR ............................ 23-100
CODES - STANDARD PROCEDURE, OBTAINING DIAGNOSTIC TROUBLE ......8E-15
CODES, STANDARD PROCEDURE - ERASING TRANSMITTER ..............8M-12
CODES, STANDARD PROCEDURE - SETTING TRANSMITTER ..............8M-12
COIL - DESCRIPTION, IGNITION ..........8I-6
COIL - OPERATION, IGNITION ............8I-6
COIL, DIAGNOSIS AND TESTING - A/C COMPRESSOR CLUTCH ...............24-14
COLLAR - INSTALLATION, STRUCTURAL . . . 9-49
COLLAR - REMOVAL, STRUCTURAL .......9-49
COLOR CODE CHARTS - SPECIFICATIONS .................... 23-100
COLUMN - DESCRIPTION, STEERING .....19-10
COLUMN - DIAGNOSIS AND TESTING, STEERING .......................... 19-11
COLUMN COVER - INSTALLATION, LOWER STEERING ................... 23-74
COLUMN COVER - INSTALLATION, OVER STEERING .......................... 23-76
COLUMN COVER - REMOVAL, LOWER STEERING .......................... 23-74
COLUMN COVER - REMOVAL, OVER STEERING .......................... 23-76
COLUMN FASTENER TORQUE, SPECIFICATIONS ..................... 19-17
COMBUSTION PRESSURE LEAKAGE TEST - DIAGNOSIS AND TESTING,
CYLINDER ........................ 9-85,9-9
COMMUNICATION RECEIVE - PCM INPUT - OPERATION, DATA BUS ..............8E-14
COMMUNICATIONS INTERFACE (PCI) BUS, OPERATION - PROGRAMMABLE ....14-25
COMPASS CALIBRATION, STANDARD PROCEDURE ......................... 8M-4
COMPASS DEMAGNETIZING, STANDARD PROCEDURE ......................... 8M-5
COMPASS MINI-TRIP COMPUTER, DIAGNOSIS AND TESTING .............8M-10
COMPASS VARIATION ADJUSTMENT, STANDARD PROCEDURE ...............8M-5
COMPASS/MINI-TRIP COMPUTER - DESCRIPTION ....................... 8M-10
COMPASS/MINI-TRIP COMPUTER - OPERATION ........................ 8M-10
COMPRESSION PRESSURE TEST - DIAGNOSIS AND TESTING, CYLINDER . . 9-85,9-9
COMPRESSOR CLUTCH COIL, DIAGNOSIS AND TESTING - A/ C.........24-14
COMPRESSOR CLUTCH RELAY - DESCRIPTION, A/C ................... 24-18
COMPRESSOR CLUTCH RELAY - INSTALLATION, A/C ................... 24-19
COMPRESSOR CLUTCH RELAY - OPERATION, A/C ..................... 24-18
COMPRESSOR CLUTCH RELAY - REMOVAL, A/C ...................... 24-19
COMPRESSOR CLUTCH/COIL - DESCRIPTION, A/C ................... 24-13
COMPRESSOR CLUTCH/COIL - OPERATION, A/C ..................... 24-13
COMPRESSOR, DESCRIPTION - A/C ......24-72
COMPRESSOR, INSTALLATION - A/C .....24-74
COMPRESSOR MOUNTING BRACKET, 2.4L ENGINE - A/C ..............24-74,24-75
COMPRESSOR NOISE DIAGNOSIS, DIAGNOSIS AND TESTING - A/C .........24-72
COMPRESSOR, OPERATION - A/C ........24-72
COMPRESSOR, REMOVAL - A/C .........24-73
COMPUTER - DESCRIPTION, COMPASS/ MINI-TRIP ......................... 8M-10
COMPUTER - OPERATION, COMPASS/ MINI-TRIP ......................... 8M-10
COMPUTER, DIAGNOSIS AND TESTING - COMPASS MINI-TRIP .................8M-10
CONCENTRATION TESTING - DIAGNOSIS AND TESTING, COOLANT ...............7-19
CONDENSER - DESCRIPTION, A/C .......24-75
CONDENSER - OPERATION, A/C .........24-75
CONDITION CHECK, STANDARD PROCEDURE - FLUID LEVEL ......21-230,21-82
CONDITIONER, DESCRIPTION - HEATER AND AIR ............................ 24-1CONDITIONER, OPERATION - HEATER
AND AIR ............................ 24-4
CONNECT FITTING DISASSEMBLY/ ASSEMBLY - STANDARD PROCEDURE,
TRANSMISSION COOLER LINE QUICK .....7-38
CONNECTING ROD - DESCRIPTION, PISTON ........................ 9-119,9-44
CONNECTING ROD - INSTALLATION, PISTON ............................. 9-45
CONNECTING ROD - REMOVAL, PISTON . . . 9-44
CONNECTING ROD BEARING CLEARANCE - STANDARD
PROCEDURE, MEASURING .............9-123
CONNECTING ROD, FITTING .............9-46
CONNECTING RODS - STANDARD PROCEDURE, FITTING .................9-119
CONNECTOR - DESCRIPTION, DATA LINK . . 8E-6
CONNECTOR - INSTALLATION .......8W-01-11
CONNECTOR - OPERATION, DATA LINK ....8E-6
CONNECTOR - REMOVAL ...........8W-01-11
CONNECTOR, GROUND AND SPLICE INFORMATION - DESCRIPTION ........8W-01-7
CONNECTOR/GROUND/SPLICE LOCATION - DESCRIPTION ....................8W -91-1
CONSOLE - DESCRIPTION, OVERHEAD ....8M-2
CONSOLE - FOLD-IN-FLOOR - INSTALLATION, FLOOR ................23-89
CONSOLE - FOLD-IN-FLOOR - REMOVAL, FLOOR ............................. 23-89
CONSOLE - INSTALLATION, LOWER ......23-73
CONSOLE - REMOVAL, LOWER ..........23-73
CONSOLE BASE TRAY - INSTALLATION, FLOOR ............................. 23-89
CONSOLE BASE TRAY - REMOVAL, FLOOR ............................. 23-89
CONSOLE, DIAGNOSIS AND TESTING - OVERHEAD .......................... 8M-3
CONSOLE KEY LOCK TUMBLER - FOLD-IN-FLOOR - INSTALLATION,
FLOOR ............................. 23-90
CONSOLE KEY LOCK TUMBLER - FOLD-IN-FLOOR - REMOVAL, FLOOR .....23-90
CONSOLE LAMP - INSTALLATION, CENTER ............................ 8L-21
CONSOLE LAMP - REMOVAL, CENTER ....8L-21
CONSOLE LAMP SWITCH - INSTALLATION, CENTER ...............8L-21
CONSOLE LAMP SWITCH - REMOVAL, CENTER ............................ 8L-21
CONSOLE LID LATCH - FOLD-IN-FLOOR - INSTALLATION, FLOOR ................23-90
CONSOLE LID LATCH - FOLD-IN-FLOOR - REMOVAL, FLOOR .................... 23-90
CONSOLE, SPECIAL TOOLS - OVERHEAD . . 8M-7
CONTAINER - DESCRIPTION, COOLANT RECOVERY .......................... 7-20
CONTAINER - INSTALLATION, COOLANT RECOVERY .......................... 7-20
CONTAINER - OPERATION, COOLANT RECOVERY .......................... 7-20
CONTAINER - REMOVAL, COOLANT RECOVERY .......................... 7-20
CONTAMINATION - DIAGNOSIS AND TESTING, BRAKE FLUID ................5-33
CONTINUITY - STANDARD PROCEDURE, TESTING .........................8W -01-9
CONTROL (4 SPEED EATX ONLY) - OPERATION, INTERACTIVE SPEED ........8P-2
CONTROL ARM - DESCRIPTION, LOWER . . . 2-12
CONTROL ARM - INSPECTION, LOWER ....2-14
CONTROL ARM - INSTALLATION, LOWER . . 2-15
CONTROL ARM - OPERATION, LOWER .....2-12
CONTROL ARM - REMOVAL, LOWER ......2-12
CONTROL ARM (REAR BUSHING - HYDRO) - ASSEMBLY, LOWER ...........2-15
CONTROL ARM (REAR BUSHING - HYDRO) - DISASSEMBLY, LOWER ........2-13
CONTROL ARM (REAR BUSHING - STANDARD) - ASSEMBLY, LOWER ........2-14
CONTROL ARM (REAR BUSHING - STANDARD) - DISASSEMBLY, LOWER .....2-13
CONTROL CABLE - INSTALLATION, THROTTLE .......................... 14-40
CONTROL CABLE - REMOVAL, THROTTLE .......................... 14-40
CONTROL CALIBRATION, STANDARD PROCEDURE - A/C-HEATER .............24-19
RS INDEX7
Description Group-Page Description Group-Page Description Group-Page
Page 2310 of 2339
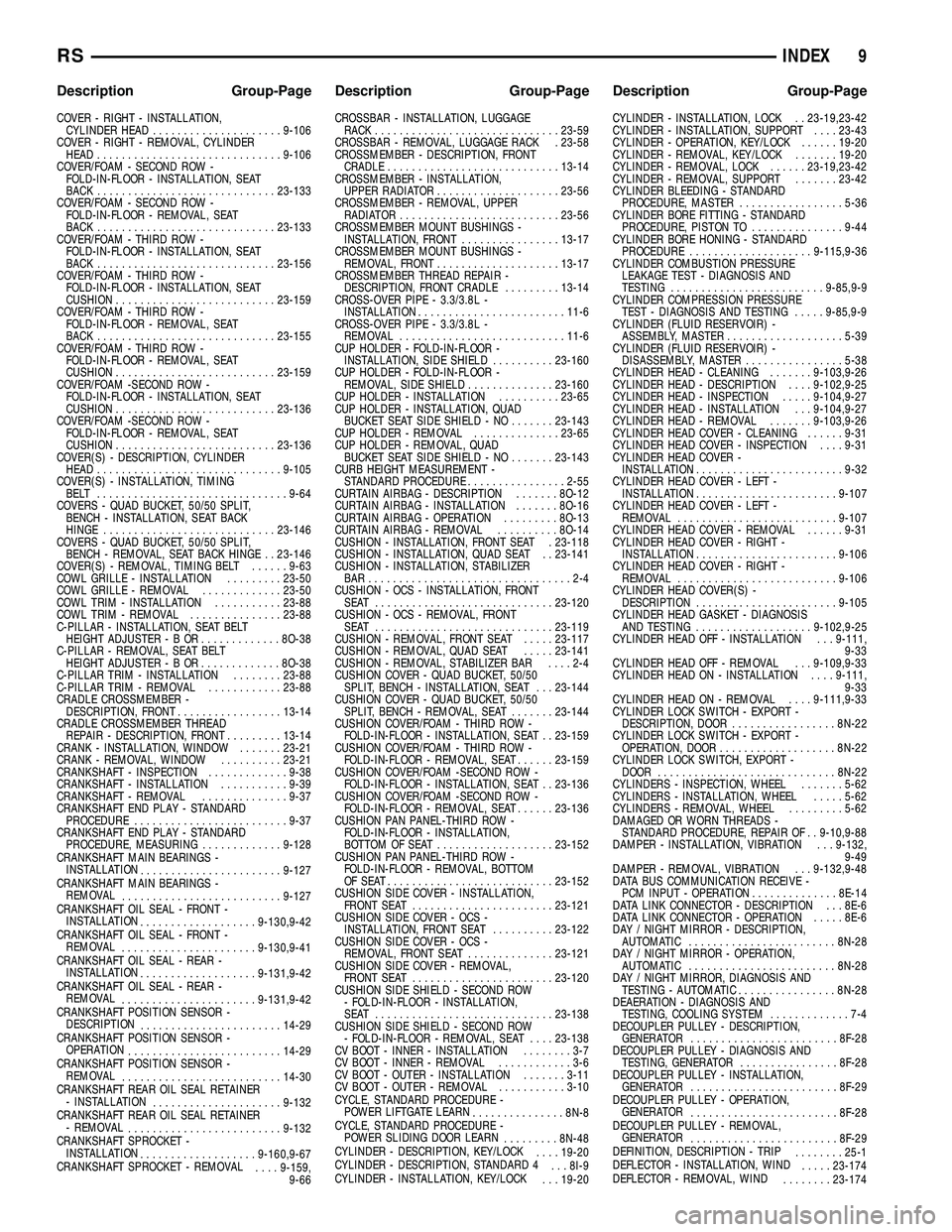
COVER - RIGHT - INSTALLATION,CYLINDER HEAD ..................... 9-106
COVER - RIGHT - REMOVAL, CYLINDER HEAD .............................. 9-106
COVER/FOAM - SECOND ROW - FOLD-IN-FLOOR - INSTALLATION, SEAT
BACK ............................. 23-133
COVER/FOAM - SECOND ROW - FOLD-IN-FLOOR - REMOVAL, SEAT
BACK ............................. 23-133
COVER/FOAM - THIRD ROW - FOLD-IN-FLOOR - INSTALLATION, SEAT
BACK ............................. 23-156
COVER/FOAM - THIRD ROW - FOLD-IN-FLOOR - INSTALLATION, SEAT
CUSHION .......................... 23-159
COVER/FOAM - THIRD ROW - FOLD-IN-FLOOR - REMOVAL, SEAT
BACK ............................. 23-155
COVER/FOAM - THIRD ROW - FOLD-IN-FLOOR - REMOVAL, SEAT
CUSHION .......................... 23-159
COVER/FOAM -SECOND ROW - FOLD-IN-FLOOR - INSTALLATION, SEAT
CUSHION .......................... 23-136
COVER/FOAM -SECOND ROW - FOLD-IN-FLOOR - REMOVAL, SEAT
CUSHION .......................... 23-136
COVER(S) - DESCRIPTION, CYLINDER HEAD .............................. 9-105
COVER(S) - INSTALLATION, TIMING BELT ............................... 9-64
COVERS - QUAD BUCKET, 50/50 SPLIT, BENCH - INSTALLATION, SEAT BACK
HINGE ............................ 23-146
COVERS - QUAD BUCKET, 50/50 SPLIT, BENCH - REMOVAL, SEAT BACK HINGE. . . 23-146
COVER(S) - REMOVAL, TIMING BELT ......9-63
COWL GRILLE - INSTALLATION .........23-50
COWL GRILLE - REMOVAL .............23-50
COWL TRIM - INSTALLATION ...........23-88
COWL TRIM - REMOVAL ...............23-88
C-PILLAR - INSTALLATION, SEAT BELT HEIGHT ADJUSTE R-BOR............. 8O-38
C-PILLAR - REMOVAL, SEAT BELT HEIGHT ADJUSTE R-BOR............. 8O-38
C-PILLAR TRIM - INSTALLATION ........23-88
C-PILLAR TRIM - REMOVAL ............23-88
CRADLE CROSSMEMBER - DESCRIPTION, FRONT .................13-14
CRADLE CROSSMEMBER THREAD REPAIR - DESCRIPTION, FRONT .........13-14
CRANK - INSTALLATION, WINDOW .......23-21
CRANK - REMOVAL, WINDOW ..........23-21
CRANKSHAFT - INSPECTION .............9-38
CRANKSHAFT - INSTALLATION ...........9-39
CRANKSHAFT - REMOVAL ..............9-37
CRANKSHAFT END PLAY - STANDARD PROCEDURE ......................... 9-37
CRANKSHAFT END PLAY - STANDARD PROCEDURE, MEASURING .............9-128
CRANKSHAFT MAIN BEARINGS - INSTALLATION ....................... 9-127
CRANKSHAFT MAIN BEARINGS - REMOVAL .......................... 9-127
CRANKSHAFT OIL SEAL - FRONT - INSTALLATION ................... 9-130,9-42
CRANKSHAFT OIL SEAL - FRONT - REMOVAL ...................... 9-130,9-41
CRANKSHAFT OIL SEAL - REAR - INSTALLATION ................... 9-131,9-42
CRANKSHAFT OIL SEAL - REAR - REMOVAL ...................... 9-131,9-42
CRANKSHAFT POSITION SENSOR - DESCRIPTION ....................... 14-29
CRANKSHAFT POSITION SENSOR - OPERATION ......................... 14-29
CRANKSHAFT POSITION SENSOR - REMOVAL .......................... 14-30
CRANKSHAFT REAR OIL SEAL RETAINER - INSTALLATION ..................... 9-132
CRANKSHAFT REAR OIL SEAL RETAINER - REMOVAL ......................... 9-132
CRANKSHAFT SPROCKET - INSTALLATION ................... 9-160,9-67
CRANKSHAFT SPROCKET - REMOVAL ....9-159,
9-66 CROSSBAR - INSTALLATION, LUGGAGE
RACK .............................. 23-59
CROSSBAR - REMOVAL, LUGGAGE RACK . 23-58
CROSSMEMBER - DESCRIPTION, FRONT CRADLE ............................ 13-14
CROSSMEMBER - INSTALLATION, UPPER RADIATOR .................... 23-56
CROSSMEMBER - REMOVAL, UPPER RADIATOR .......................... 23-56
CROSSMEMBER MOUNT BUSHINGS - INSTALLATION, FRONT ................13-17
CROSSMEMBER MOUNT BUSHINGS - REMOVAL, FRONT .................... 13-17
CROSSMEMBER THREAD REPAIR - DESCRIPTION, FRONT CRADLE .........13-14
CROSS-OVER PIPE - 3.3/3.8L - INSTALLATION ........................ 11-6
CROSS-OVER PIPE - 3.3/3.8L - REMOVAL ........................... 11-6
CUP HOLDER - FOLD-IN-FLOOR - INSTALLATION, SIDE SHIELD ..........23-160
CUP HOLDER - FOLD-IN-FLOOR - REMOVAL, SIDE SHIELD ..............23-160
CUP HOLDER - INSTALLATION ..........23-65
CUP HOLDER - INSTALLATION, QUAD BUCKET SEAT SIDE SHIELD - NO .......23-143
CUP HOLDER - REMOVAL ..............23-65
CUP HOLDER - REMOVAL, QUAD BUCKET SEAT SIDE SHIELD - NO .......23-143
CURB HEIGHT MEASUREMENT - STANDARD PROCEDURE ................2-55
CURTAIN AIRBAG - DESCRIPTION .......8O-12
CURTAIN AIRBAG - INSTALLATION .......8O-16
CURTAIN AIRBAG - OPERATION .........8O-13
CURTAIN AIRBAG - REMOVAL ..........8O-14
CUSHION - INSTALLATION, FRONT SEAT . 23-118
CUSHION - INSTALLATION, QUAD SEAT . . 23-141
CUSHION - INSTALLATION, STABILIZER BAR.................................2-4
CUSHION - OCS - INSTALLATION, FRONT SEAT ............................. 23-120
CUSHION - OCS - REMOVAL, FRONT SEAT ............................. 23-119
CUSHION - REMOVAL, FRONT SEAT .....23-117
CUSHION - REMOVAL, QUAD SEAT .....23-141
CUSHION - REMOVAL, STABILIZER BAR ....2-4
CUSHION COVER - QUAD BUCKET, 50/50 SPLIT, BENCH - INSTALLATION, SEAT . . . 23-144
CUSHION COVER - QUAD BUCKET, 50/50 SPLIT, BENCH - REMOVAL, SEAT .......23-144
CUSHION COVER/FOAM - THIRD ROW - FOLD-IN-FLOOR - INSTALLATION, SEAT . . 23-159
CUSHION COVER/FOAM - THIRD ROW - FOLD-IN-FLOOR - REMOVAL, SEAT ......23-159
CUSHION COVER/FOAM -SECOND ROW - FOLD-IN-FLOOR - INSTALLATION, SEAT . . 23-136
CUSHION COVER/FOAM -SECOND ROW - FOLD-IN-FLOOR - REMOVAL, SEAT ......23-136
CUSHION PAN PANEL-THIRD ROW - FOLD-IN-FLOOR - INSTALLATION,
BOTTOM OF SEAT ................... 23-152
CUSHION PAN PANEL-THIRD ROW - FOLD-IN-FLOOR - REMOVAL, BOTTOM
OF SEAT........................... 23-152
CUSHION SIDE COVER - INSTALLATION, FRONT SEAT ....................... 23-121
CUSHION SIDE COVER - OCS - INSTALLATION, FRONT SEAT ..........23-122
CUSHION SIDE COVER - OCS - REMOVAL, FRONT SEAT ..............23-121
CUSHION SIDE COVER - REMOVAL, FRONT SEAT ....................... 23-120
CUSHION SIDE SHIELD - SECOND ROW - FOLD-IN-FLOOR - INSTALLATION,
SEAT ............................. 23-138
CUSHION SIDE SHIELD - SECOND ROW - FOLD-IN-FLOOR - REMOVAL, SEAT ....23-138
CV BOOT - INNER - INSTALLATION ........3-7
CV BOOT - INNER - REMOVAL ............3-6
CV BOOT - OUTER - INSTALLATION .......3-11
CV BOOT - OUTER - REMOVAL ...........3-10
CYCLE, STANDARD PROCEDURE - POWER LIFTGATE LEARN ...............8N-8
CYCLE, STANDARD PROCEDURE - POWER SLIDING DOOR LEARN .........8N-48
CYLINDER - DESCRIPTION, KEY/LOCK ....19-20
CYLINDER - DESCRIPTION, STANDARD 4 . . . 8I-9
CYLINDER - INSTALLATION, KEY/LOCK . . . 19-20CYLINDER - INSTALLATION, LOCK . . 23-19,23-42
CYLINDER - INSTALLATION, SUPPORT
....23-43
CYLINDER - OPERATION, KEY/LOCK ......19-20
CYLINDER - REMOVAL, KEY/LOCK .......19-20
CYLINDER - REMOVAL, LOCK ......23-19,23-42
CYLINDER - REMOVAL, SUPPORT .......23-42
CYLINDER BLEEDING - STANDARD PROCEDURE, MASTER .................5-36
CYLINDER BORE FITTING - STANDARD PROCEDURE, PISTON TO ...............9-44
CYLINDER BORE HONING - STANDARD PROCEDURE .................... 9-115,9-36
CYLINDER COMBUSTION PRESSURE LEAKAGE TEST - DIAGNOSIS AND
TESTING ......................... 9-85,9-9
CYLINDER COMPRESSION PRESSURE TEST - DIAGNOSIS AND TESTING .....9-85,9-9
CYLINDER (FLUID RESERVOIR) - ASSEMBLY, MASTER ................... 5-39
CYLINDER (FLUID RESERVOIR) - DISASSEMBLY, MASTER ................5-38
CYLINDER HEAD - CLEANING .......9-103,9-26
CYLINDER HEAD - DESCRIPTION ....9-102,9-25
CYLINDER HEAD - INSPECTION .....9-104,9-27
CYLINDER HEAD - INSTALLATION . . . 9-104,9-27
CYLINDER HEAD - REMOVAL .......9-103,9-26
CYLINDER HEAD COVER - CLEANING ......9-31
CYLINDER HEAD COVER - INSPECTION ....9-31
CYLINDER HEAD COVER - INSTALLATION ......................... 9-32
CYLINDER HEAD COVER - LEFT - INSTALLATION ....................... 9-107
CYLINDER HEAD COVER - LEFT - REMOVAL .......................... 9-107
CYLINDER HEAD COVER - REMOVAL ......9-31
CYLINDER HEAD COVER - RIGHT - INSTALLATION ....................... 9-106
CYLINDER HEAD COVER - RIGHT - REMOVAL .......................... 9-106
CYLINDER HEAD COVER(S) - DESCRIPTION ....................... 9-105
CYLINDER HEAD GASKET - DIAGNOSIS AND TESTING ................... 9-102,9-25
CYLINDER HEAD OFF - INSTALLATION . . . 9-111, 9-33
CYLINDER HEAD OFF - REMOVAL . . . 9-109,9-33
CYLINDER HEAD ON - INSTALLATION ....9-111,
9-33
CYLINDER HEAD ON - REMOVAL ....9-111,9-33
CYLINDER LOCK SWITCH - EXPORT - DESCRIPTION, DOOR .................8N-22
CYLINDER LOCK SWITCH - EXPORT - OPERATION, DOOR ................... 8N-22
CYLINDER LOCK SWITCH, EXPORT - DOOR ............................. 8N-22
CYLINDERS - INSPECTION, WHEEL .......5-62
CYLINDERS - INSTALLATION, WHEEL .....5-62
CYLINDERS - REMOVAL, WHEEL .........5-62
DAMAGED OR WORN THREADS - STANDARD PROCEDURE, REPAIR OF . . 9-10,9-88
DAMPER - INSTALLATION, VIBRATION . . . 9-132, 9-49
DAMPER - REMOVAL, VIBRATION . . . 9-132,9-48
DATA BUS COMMUNICATION RECEIVE - PCM INPUT - OPERATION ..............8E-14
DATA LINK CONNECTOR - DESCRIPTION . . . 8E-6
DATA LINK CONNECTOR - OPERATION .....8E-6
DAY / NIGHT MIRROR - DESCRIPTION, AUTOMATIC ........................ 8N-28
DAY / NIGHT MIRROR - OPERATION, AUTOMATIC ........................ 8N-28
DAY / NIGHT MIRROR, DIAGNOSIS AND TESTING - AUTOMATIC ................8N-28
DEAERATION - DIAGNOSIS AND TESTING, COOLING SYSTEM .............7-4
DECOUPLER PULLEY - DESCRIPTION, GENERATOR ........................ 8F-28
DECOUPLER PULLEY - DIAGNOSIS AND TESTING, GENERATOR ................8F-28
DECOUPLER PULLEY - INSTALLATION, GENERATOR ........................ 8F-29
DECOUPLER PULLEY - OPERATION, GENERATOR ........................ 8F-28
DECOUPLER PULLEY - REMOVAL, GENERATOR ........................ 8F-29
DEFINITION, DESCRIPTION - TRIP ........25-1
DEFLECTOR - INSTALLATION, WIND .....23-174
DEFLECTOR - REMOVAL, WIND ........23-174
RS INDEX9
Description Group-Page Description Group-Page Description Group-Page
Page 2325 of 2339
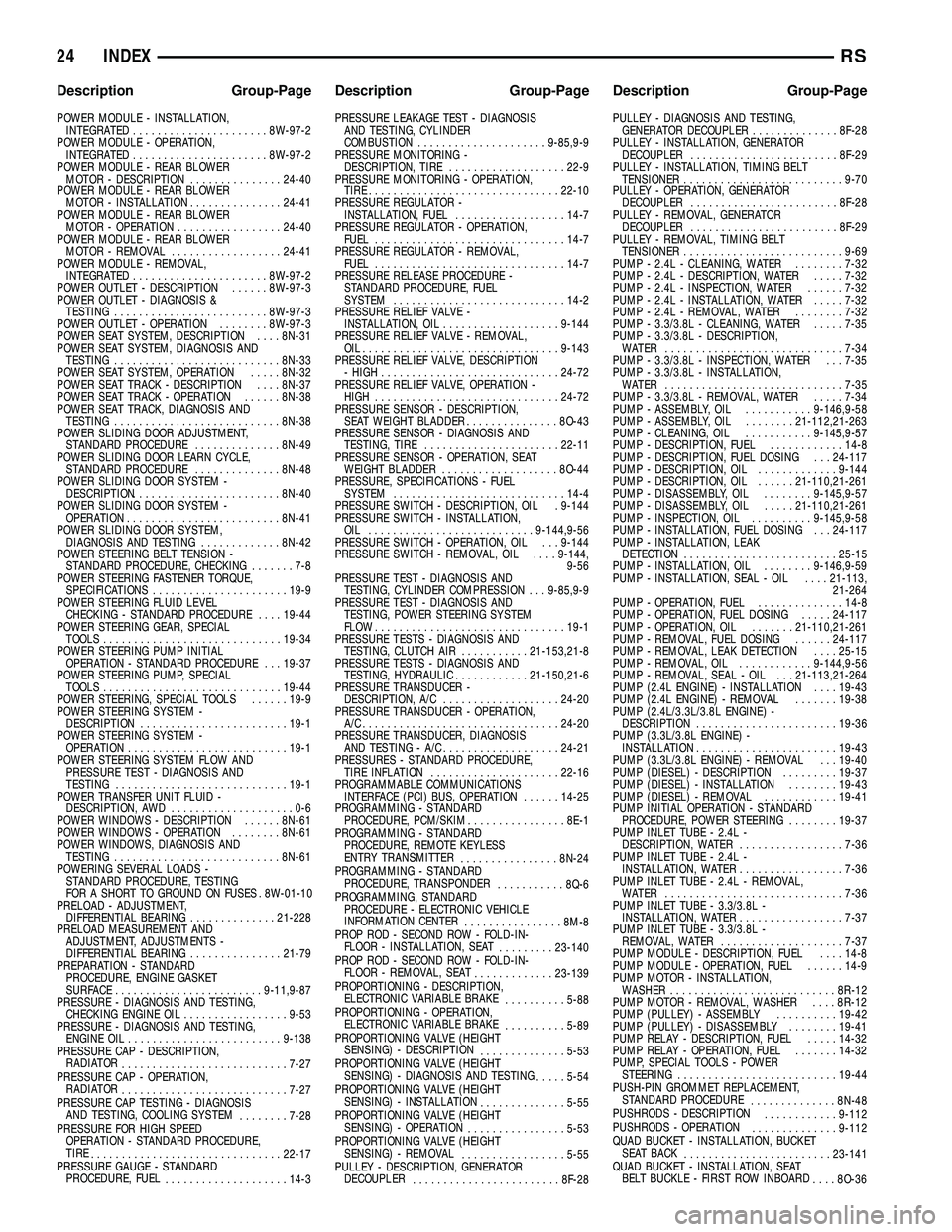
POWER MODULE - INSTALLATION,INTEGRATED ......................8W -97-2
POWER MODULE - OPERATION, INTEGRATED ......................8W -97-2
POWER MODULE - REAR BLOWER MOTOR - DESCRIPTION ...............24-40
POWER MODULE - REAR BLOWER MOTOR - INSTALLATION ...............24-41
POWER MODULE - REAR BLOWER MOTOR - OPERATION .................24-40
POWER MODULE - REAR BLOWER MOTOR - REMOVAL .................. 24-41
POWER MODULE - REMOVAL, INTEGRATED ......................8W -97-2
POWER OUTLET - DESCRIPTION ......8W-97-3
POWER OUTLET - DIAGNOSIS & TESTING .........................8W -97-3
POWER OUTLET - OPERATION ........8W-97-3
POWER SEAT SYSTEM, DESCRIPTION ....8N-31
POWER SEAT SYSTEM, DIAGNOSIS AND TESTING ........................... 8N-33
POWER SEAT SYSTEM, OPERATION .....8N-32
POWER SEAT TRACK - DESCRIPTION ....8N-37
POWER SEAT TRACK - OPERATION ......8N-38
POWER SEAT TRACK, DIAGNOSIS AND TESTING ........................... 8N-38
POWER SLIDING DOOR ADJUSTMENT, STANDARD PROCEDURE ..............8N-49
POWER SLIDING DOOR LEARN CYCLE, STANDARD PROCEDURE ..............8N-48
POWER SLIDING DOOR SYSTEM - DESCRIPTION ........................ 8N-40
POWER SLIDING DOOR SYSTEM - OPERATION ......................... 8N-41
POWER SLIDING DOOR SYSTEM, DIAGNOSIS AND TESTING .............8N-42
POWER STEERING BELT TENSION - STANDARD PROCEDURE, CHECKING .......7-8
POWER STEERING FASTENER TORQUE, SPECIFICATIONS ...................... 19-9
POWER STEERING FLUID LEVEL CHECKING - STANDARD PROCEDURE ....19-44
POWER STEERING GEAR, SPECIAL TOOLS ............................. 19-34
POWER STEERING PUMP INITIAL OPERATION - STANDARD PROCEDURE . . . 19-37
POWER STEERING PUMP, SPECIAL TOOLS ............................. 19-44
POWER STEERING, SPECIAL TOOLS ......19-9
POWER STEERING SYSTEM - DESCRIPTION ........................ 19-1
POWER STEERING SYSTEM - OPERATION .......................... 19-1
POWER STEERING SYSTEM FLOW AND PRESSURE TEST - DIAGNOSIS AND
TESTING ............................ 19-1
POWER TRANSFER UNIT FLUID - DESCRIPTION, AWD ....................0-6
POWER WINDOWS - DESCRIPTION ......8N-61
POWER WINDOWS - OPERATION ........8N-61
POWER WINDOWS, DIAGNOSIS AND TESTING ........................... 8N-61
POWERING SEVERAL LOADS - STANDARD PROCEDURE, TESTING
FOR A SHORT TO GROUND ON FUSES . 8W-01-10
PRELOAD - ADJUSTMENT, DIFFERENTIAL BEARING ..............21-228
PRELOAD MEASUREMENT AND ADJUSTMENT, ADJUSTMENTS -
DIFFERENTIAL BEARING ...............21-79
PREPARATION - STANDARD PROCEDURE, ENGINE GASKET
SURFACE ........................ 9-11,9-87
PRESSURE - DIAGNOSIS AND TESTING, CHECKING ENGINE OIL .................9-53
PRESSURE - DIAGNOSIS AND TESTING, ENGINE OIL ......................... 9-138
PRESSURE CAP - DESCRIPTION, RADIATOR ........................... 7-27
PRESSURE CAP - OPERATION, RADIATOR ........................... 7-27
PRESSURE CAP TESTING - DIAGNOSIS AND TESTING, COOLING SYSTEM ........7-28
PRESSURE FOR HIGH SPEED OPERATION - STANDARD PROCEDURE,
TIRE ............................... 22-17
PRESSURE GAUGE - STANDARD PROCEDURE, FUEL .................... 14-3PRESSURE LEAKAGE TEST - DIAGNOSIS
AND TESTING, CYLINDER
COMBUSTION ..................... 9-85,9-9
PRESSURE MONITORING - DESCRIPTION, TIRE ................... 22-9
PRESSURE MONITORING - OPERATION, TIRE ............................... 22-10
PRESSURE REGULATOR - INSTALLATION, FUEL .................. 14-7
PRESSURE REGULATOR - OPERATION, FUEL ............................... 14-7
PRESSURE REGULATOR - REMOVAL, FUEL ............................... 14-7
PRESSURE RELEASE PROCEDURE - STANDARD PROCEDURE, FUEL
SYSTEM ............................ 14-2
PRESSURE RELIEF VALVE - INSTALLATION, OIL ................... 9-144
PRESSURE RELIEF VALVE - REMOVAL, OIL................................ 9-143
PRESSURE RELIEF VALVE, DESCRIPTION - HIGH ............................. 24-72
PRESSURE RELIEF VALVE, OPERATION - HIGH .............................. 24-72
PRESSURE SENSOR - DESCRIPTION, SEAT WEIGHT BLADDER ...............8O-43
PRESSURE SENSOR - DIAGNOSIS AND TESTING, TIRE ...................... 22-11
PRESSURE SENSOR - OPERATION, SEAT WEIGHT BLADDER ................... 8O-44
PRESSURE, SPECIFICATIONS - FUEL SYSTEM ............................ 14-4
PRESSURE SWITCH - DESCRIPTION, OIL . 9-144
PRESSURE SWITCH - INSTALLATION, OIL ........................... 9-144,9-56
PRESSURE SWITCH - OPERATION, OIL . . . 9-144
PRESSURE SWITCH - REMOVAL, OIL ....9-144,
9-56
PRESSURE TEST - DIAGNOSIS AND TESTING, CYLINDER COMPRESSION . . . 9-85,9-9
PRESSURE TEST - DIAGNOSIS AND TESTING, POWER STEERING SYSTEM
FLOW ............................... 19-1
PRESSURE TESTS - DIAGNOSIS AND TESTING, CLUTCH AIR ...........21-153,21-8
PRESSURE TESTS - DIAGNOSIS AND TESTING, HYDRAULIC ............21-150,21-6
PRESSURE TRANSDUCER - DESCRIPTION, A/C ................... 24-20
PRESSURE TRANSDUCER - OPERATION, A/C................................ 24-20
PRESSURE TRANSDUCER, DIAGNOSIS AND TESTING - A/C ................... 24-21
PRESSURES - STANDARD PROCEDURE, TIRE INFLATION ..................... 22-16
PROGRAMMABLE COMMUNICATIONS INTERFACE (PCI) BUS, OPERATION ......14-25
PROGRAMMING - STANDARD PROCEDURE, PCM/SKIM ................8E-1
PROGRAMMING - STANDARD PROCEDURE, REMOTE KEYLESS
ENTRY TRANSMITTER ................8N-24
PROGRAMMING - STANDARD PROCEDURE, TRANSPONDER ...........8Q-6
PROGRAMMING, STANDARD PROCEDURE - ELECTRONIC VEHICLE
INFORMATION CENTER ................8M-8
PROP ROD - SECOND ROW - FOLD-IN- FLOOR - INSTALLATION, SEAT .........23-140
PROP ROD - SECOND ROW - FOLD-IN- FLOOR - REMOVAL, SEAT .............23-139
PROPORTIONING - DESCRIPTION, ELECTRONIC VARIABLE BRAKE ..........5-88
PROPORTIONING - OPERATION, ELECTRONIC VARIABLE BRAKE ..........5-89
PROPORTIONING VALVE (HEIGHT SENSING) - DESCRIPTION ..............5-53
PROPORTIONING VALVE (HEIGHT SENSING) - DIAGNOSIS AND TESTING .....5-54
PROPORTIONING VALVE (HEIGHT SENSING) - INSTALLATION ..............5-55
PROPORTIONING VALVE (HEIGHT SENSING) - OPERATION ................5-53
PROPORTIONING VALVE (HEIGHT SENSING) - REMOVAL .................5-55
PULLEY - DESCRIPTION, GENERATOR DECOUPLER ........................ 8F-28PULLEY - DIAGNOSIS AND TESTING,
GENERATOR DECOUPLER ..............8F-28
PULLEY - INSTALLATION, GENERATOR DECOUPLER ........................ 8F-29
PULLEY - INSTALLATION, TIMING BELT TENSIONER .......................... 9-70
PULLEY - OPERATION, GENERATOR DECOUPLER ........................ 8F-28
PULLEY - REMOVAL, GENERATOR DECOUPLER ........................ 8F-29
PULLEY - REMOVAL, TIMING BELT TENSIONER .......................... 9-69
PUMP - 2.4L - CLEANING, WATER ........7-32
PUMP - 2.4L - DESCRIPTION, WATER .....7-32
PUMP - 2.4L - INSPECTION, WATER ......7-32
PUMP - 2.4L - INSTALLATION, WATER .....7-32
PUMP - 2.4L - REMOVAL, WATER ........7-32
PUMP - 3.3/3.8L - CLEANING, WATER .....7-35
PUMP - 3.3/3.8L - DESCRIPTION, WATER ............................. 7-34
PUMP - 3.3/3.8L - INSPECTION, WATER . . . 7-35
PUMP - 3.3/3.8L - INSTALLATION, WATER ............................. 7-35
PUMP - 3.3/3.8L - REMOVAL, WATER .....7-34
PUMP - ASSEMBLY, OIL ...........9-146,9-58
PUMP - ASSEMBLY, OIL ........21-112,21-263
PUMP - CLEANING, OIL ...........9-145,9-57
PUMP - DESCRIPTION, FUEL ............14-8
PUMP - DESCRIPTION, FUEL DOSING . . . 24-117
PUMP - DESCRIPTION, OIL .............9-144
PUMP - DESCRIPTION, OIL ......21-110,21-261
PUMP - DISASSEMBLY, OIL ........9-145,9-57
PUMP - DISASSEMBLY, OIL .....21-110,21-261
PUMP - INSPECTION, OIL ..........9-145,9-58
PUMP - INSTALLATION, FUEL DOSING . . . 24-117
PUMP - INSTALLATION, LEAK DETECTION ......................... 25-15
PUMP - INSTALLATION, OIL ........9-146,9-59
PUMP - INSTALLATION, SEAL - OIL ....21-113,
21-264
PUMP - OPERATION, FUEL ..............14-8
PUMP - OPERATION, FUEL DOSING .....24-117
PUMP - OPERATION, OIL .......21-110,21-261
PUMP - REMOVAL, FUEL DOSING ......24-117
PUMP - REMOVAL, LEAK DETECTION ....25-15
PUMP - REMOVAL, OIL ............9-144,9-56
PUMP - REMOVAL, SEAL - OIL . . . 21-113,21-264
PUMP (2.4L ENGINE) - INSTALLATION ....19-43
PUMP (2.4L ENGINE) - REMOVAL .......19-38
PUMP (2.4L/3.3L/3.8L ENGINE) - DESCRIPTION ....................... 19-36
PUMP (3.3L/3.8L ENGINE) - INSTALLATION ....................... 19-43
PUMP (3.3L/3.8L ENGINE) - REMOVAL . . . 19-40
PUMP (DIESEL) - DESCRIPTION .........19-37
PUMP (DIESEL) - INSTALLATION ........19-43
PUMP (DIESEL) - REMOVAL ............19-41
PUMP INITIAL OPERATION - STANDARD PROCEDURE, POWER STEERING ........19-37
PUMP INLET TUBE - 2.4L - DESCRIPTION, WATER .................7-36
PUMP INLET TUBE - 2.4L - INSTALLATION, WATER .................7-36
PUMP INLET TUBE - 2.4L - REMOVAL, WATER ............................. 7-36
PUMP INLET TUBE - 3.3/3.8L - INSTALLATION, WATER .................7-37
PUMP INLET TUBE - 3.3/3.8L - REMOVAL, WATER .................... 7-37
PUMP MODULE - DESCRIPTION, FUEL ....14-8
PUMP MODULE - OPERATION, FUEL ......14-9
PUMP MOTOR - INSTALLATION, WASHER ........................... 8R-12
PUMP MOTOR - REMOVAL, WASHER ....8R-12
PUMP (PULLEY) - ASSEMBLY ..........19-42
PUMP (PULLEY) - DISASSEMBLY ........19-41
PUMP RELAY - DESCRIPTION, FUEL .....14-32
PUMP RELAY - OPERATION, FUEL .......14-32
PUMP, SPECIAL TOOLS - POWER STEERING .......................... 19-44
PUSH-PIN GROMMET REPLACEMENT, STANDARD PROCEDURE ..............8N-48
PUSHRODS - DESCRIPTION ............9-112
PUSHRODS - OPERATION ..............9-112
QUAD BUCKET - INSTALLATION, BUCKET SEAT BACK ........................ 23-141
QUAD BUCKET - INSTALLATION, SEAT BELT BUCKLE - FIRST ROW INBOARD ....8O-36
24 INDEXRS
Description Group-Page Description Group-Page Description Group-Page
Page 2333 of 2339
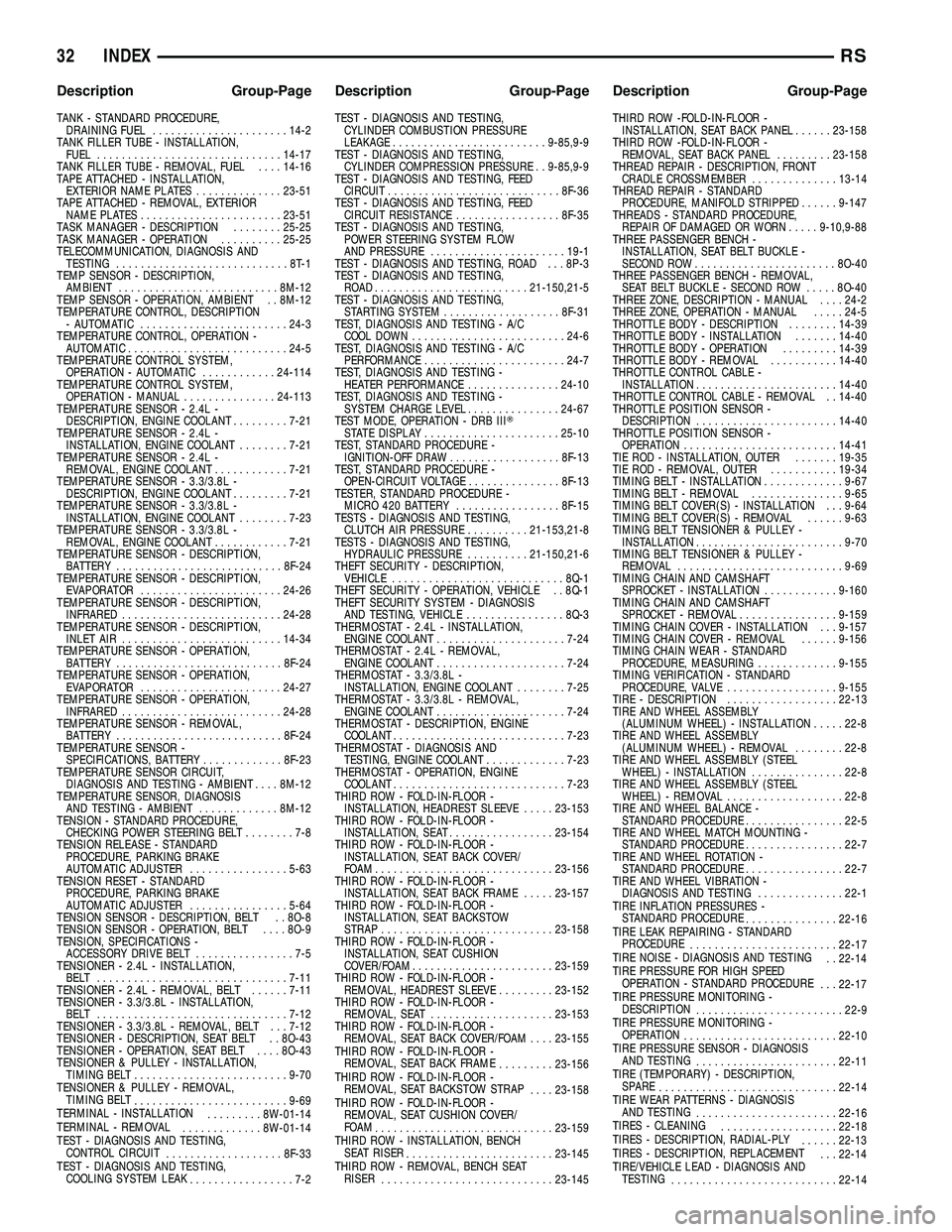
TANK - STANDARD PROCEDURE,DRAINING FUEL ...................... 14-2
TANK FILLER TUBE - INSTALLATION, FUEL .............................. 14-17
TANK FILLER TUBE - REMOVAL, FUEL ....14-16
TAPE ATTACHED - INSTALLATION, EXTERIOR NAME PLATES ..............23-51
TAPE ATTACHED - REMOVAL, EXTERIOR NAME PLATES ....................... 23-51
TASK MANAGER - DESCRIPTION ........25-25
TASK MANAGER - OPERATION ..........25-25
TELECOMMUNICATION, DIAGNOSIS AND TESTING ............................8T-1
TEMP SENSOR - DESCRIPTION, AMBIENT .......................... 8M-12
TEMP SENSOR - OPERATION, AMBIENT . . 8M-12
TEMPERATURE CONTROL, DESCRIPTION - AUTOMATIC ........................ 24-3
TEMPERATURE CONTROL, OPERATION - AUTOMATIC .......................... 24-5
TEMPERATURE CONTROL SYSTEM, OPERATION - AUTOMATIC ............24-114
TEMPERATURE CONTROL SYSTEM, OPERATION - MANUAL ...............24-113
TEMPERATURE SENSOR - 2.4L - DESCRIPTION, ENGINE COOLANT .........7-21
TEMPERATURE SENSOR - 2.4L - INSTALLATION, ENGINE COOLANT ........7-21
TEMPERATURE SENSOR - 2.4L - REMOVAL, ENGINE COOLANT ............7-21
TEMPERATURE SENSOR - 3.3/3.8L - DESCRIPTION, ENGINE COOLANT .........7-21
TEMPERATURE SENSOR - 3.3/3.8L - INSTALLATION, ENGINE COOLANT ........7-23
TEMPERATURE SENSOR - 3.3/3.8L - REMOVAL, ENGINE COOLANT ............7-21
TEMPERATURE SENSOR - DESCRIPTION, BATTERY ........................... 8F-24
TEMPERATURE SENSOR - DESCRIPTION, EVAPORATOR ....................... 24-26
TEMPERATURE SENSOR - DESCRIPTION, INFRARED .......................... 24-28
TEMPERATURE SENSOR - DESCRIPTION, INLET AIR .......................... 14-34
TEMPERATURE SENSOR - OPERATION, BATTERY ........................... 8F-24
TEMPERATURE SENSOR - OPERATION, EVAPORATOR ....................... 24-27
TEMPERATURE SENSOR - OPERATION, INFRARED .......................... 24-28
TEMPERATURE SENSOR - REMOVAL, BATTERY ........................... 8F-24
TEMPERATURE SENSOR - SPECIFICATIONS, BATTERY .............8F-23
TEMPERATURE SENSOR CIRCUIT, DIAGNOSIS AND TESTING - AMBIENT ....8M-12
TEMPERATURE SENSOR, DIAGNOSIS AND TESTING - AMBIENT .............8M-12
TENSION - STANDARD PROCEDURE, CHECKING POWER STEERING BELT ........7-8
TENSION RELEASE - STANDARD PROCEDURE, PARKING BRAKE
AUTOMATIC ADJUSTER ................5-63
TENSION RESET - STANDARD PROCEDURE, PARKING BRAKE
AUTOMATIC ADJUSTER ................5-64
TENSION SENSOR - DESCRIPTION, BELT . . 8O-8
TENSION SENSOR - OPERATION, BELT ....8O-9
TENSION, SPECIFICATIONS - ACCESSORY DRIVE BELT ................7-5
TENSIONER - 2.4L - INSTALLATION, BELT ............................... 7-11
TENSIONER - 2.4L - REMOVAL, BELT ......7-11
TENSIONER - 3.3/3.8L - INSTALLATION, BELT ............................... 7-12
TENSIONER - 3.3/3.8L - REMOVAL, BELT . . . 7-12
TENSIONER - DESCRIPTION, SEAT BELT . . 8O-43
TENSIONER - OPERATION, SEAT BELT ....8O-43
TENSIONER & PULLEY - INSTALLATION, TIMING BELT ......................... 9-70
TENSIONER & PULLEY - REMOVAL, TIMING BELT ......................... 9-69
TERMINAL - INSTALLATION .........8W-01-14
TERMINAL - REMOVAL .............8W-01-14
TEST - DIAGNOSIS AND TESTING, CONTROL CIRCUIT ................... 8F-33
TEST - DIAGNOSIS AND TESTING, COOLING SYSTEM LEAK .................7-2 TEST - DIAGNOSIS AND TESTING,
CYLINDER COMBUSTION PRESSURE
LEAKAGE ......................... 9-85,9-9
TEST - DIAGNOSIS AND TESTING, CYLINDER COMPRESSION PRESSURE . . 9-85,9-9
TEST - DIAGNOSIS AND TESTING, FEED CIRCUIT ............................ 8F-36
TEST - DIAGNOSIS AND TESTING, FEED CIRCUIT RESISTANCE .................8F-35
TEST - DIAGNOSIS AND TESTING, POWER STEERING SYSTEM FLOW
AND PRESSURE ...................... 19-1
TEST - DIAGNOSIS AND TESTING, ROAD . . . 8P-3
TEST - DIAGNOSIS AND TESTING, ROAD ......................... 21-150,21-5
TEST - DIAGNOSIS AND TESTING, STARTING SYSTEM ................... 8F-31
TEST, DIAGNOSIS AND TESTING - A/C COOL DOWN ......................... 24-6
TEST, DIAGNOSIS AND TESTING - A/C PERFORMANCE ....................... 24-7
TEST, DIAGNOSIS AND TESTING - HEATER PERFORMANCE ...............24-10
TEST, DIAGNOSIS AND TESTING - SYSTEM CHARGE LEVEL ...............24-67
TEST MODE, OPERATION - DRB III T
STATE DISPLAY ...................... 25-10
TEST, STANDARD PROCEDURE - IGNITION-OFF DRAW .................. 8F-13
TEST, STANDARD PROCEDURE - OPEN-CIRCUIT VOLTAGE ...............8F-13
TESTER, STANDARD PROCEDURE - MICRO 420 BATTERY .................8F-15
TESTS - DIAGNOSIS AND TESTING, CLUTCH AIR PRESSURE ..........21-153,21-8
TESTS - DIAGNOSIS AND TESTING, HYDRAULIC PRESSURE ..........21-150,21-6
THEFT SECURITY - DESCRIPTION, VEHICLE ............................ 8Q-1
THEFT SECURITY - OPERATION, VEHICLE . . 8Q-1
THEFT SECURITY SYSTEM - DIAGNOSIS AND TESTING, VEHICLE ................8Q-3
THERMOSTAT - 2.4L - INSTALLATION, ENGINE COOLANT ..................... 7-24
THERMOSTAT - 2.4L - REMOVAL, ENGINE COOLANT ..................... 7-24
THERMOSTAT - 3.3/3.8L - INSTALLATION, ENGINE COOLANT ........7-25
THERMOSTAT - 3.3/3.8L - REMOVAL, ENGINE COOLANT ..................... 7-24
THERMOSTAT - DESCRIPTION, ENGINE COOLANT ............................ 7-23
THERMOSTAT - DIAGNOSIS AND TESTING, ENGINE COOLANT .............7-23
THERMOSTAT - OPERATION, ENGINE COOLANT ............................ 7-23
THIRD ROW - FOLD-IN-FLOOR - INSTALLATION, HEADREST SLEEVE .....23-153
THIRD ROW - FOLD-IN-FLOOR - INSTALLATION, SEAT .................23-154
THIRD ROW - FOLD-IN-FLOOR - INSTALLATION, SEAT BACK COVER/
FOAM ............................. 23-156
THIRD ROW - FOLD-IN-FLOOR - INSTALLATION, SEAT BACK FRAME .....23-157
THIRD ROW - FOLD-IN-FLOOR - INSTALLATION, SEAT BACKSTOW
STRAP ............................ 23-158
THIRD ROW - FOLD-IN-FLOOR - INSTALLATION, SEAT CUSHION
COVER/FOAM ....................... 23-159
THIRD ROW - FOLD-IN-FLOOR - REMOVAL, HEADREST SLEEVE .........23-152
THIRD ROW - FOLD-IN-FLOOR - REMOVAL, SEAT .................... 23-153
THIRD ROW - FOLD-IN-FLOOR - REMOVAL, SEAT BACK COVER/FOAM ....23-155
THIRD ROW - FOLD-IN-FLOOR - REMOVAL, SEAT BACK FRAME .........23-156
THIRD ROW - FOLD-IN-FLOOR - REMOVAL, SEAT BACKSTOW STRAP ....23-158
THIRD ROW - FOLD-IN-FLOOR - REMOVAL, SEAT CUSHION COVER/
FOAM ............................. 23-159
THIRD ROW - INSTALLATION, BENCH SEAT RISER ........................ 23-145
THIRD ROW - REMOVAL, BENCH SEAT RISER ............................ 23-145THIRD ROW -FOLD-IN-FLOOR -
INSTALLATION, SEAT BACK PANEL ......23-158
THIRD ROW -FOLD-IN-FLOOR - REMOVAL, SEAT BACK PANEL .........23-158
THREAD REPAIR - DESCRIPTION, FRONT CRADLE CROSSMEMBER ..............13-14
THREAD REPAIR - STANDARD PROCEDURE, MANIFOLD STRIPPED ......9-147
THREADS - STANDARD PROCEDURE, REPAIR OF DAMAGED OR WORN .....9-10,9-88
THREE PASSENGER BENCH - INSTALLATION, SEAT BELT BUCKLE -
SECOND ROW ....................... 8O-40
THREE PASSENGER BENCH - REMOVAL, SEAT BELT BUCKLE - SECOND ROW .....8O-40
THREE ZONE, DESCRIPTION - MANUAL ....24-2
THREE ZONE, OPERATION - MANUAL .....24-5
THROTTLE BODY - DESCRIPTION ........14-39
THROTTLE BODY - INSTALLATION .......14-40
THROTTLE BODY - OPERATION .........14-39
THROTTLE BODY - REMOVAL ...........14-40
THROTTLE CONTROL CABLE - INSTALLATION ....................... 14-40
THROTTLE CONTROL CABLE - REMOVAL . . 14-40
THROTTLE POSITION SENSOR - DESCRIPTION ....................... 14-40
THROTTLE POSITION SENSOR - OPERATION ......................... 14-41
TIE ROD - INSTALLATION, OUTER .......19-35
TIE ROD - REMOVAL, OUTER ...........19-34
TIMING BELT - INSTALLATION .............9-67
TIMING BELT - REMOVAL ...............9-65
TIMING BELT COVER(S) - INSTALLATION . . . 9-64
TIMING BELT COVER(S) - REMOVAL ......9-63
TIMING BELT TENSIONER & PULLEY - INSTALLATION ........................ 9-70
TIMING BELT TENSIONER & PULLEY - REMOVAL ........................... 9-69
TIMING CHAIN AND CAMSHAFT SPROCKET - INSTALLATION ............9-160
TIMING CHAIN AND CAMSHAFT SPROCKET - REMOVAL ................9-159
TIMING CHAIN COVER - INSTALLATION . . . 9-157
TIMING CHAIN COVER - REMOVAL ......9-156
TIMING CHAIN WEAR - STANDARD PROCEDURE, MEASURING .............9-155
TIMING VERIFICATION - STANDARD PROCEDURE, VALVE .................. 9-155
TIRE - DESCRIPTION ..................22-13
TIRE AND WHEEL ASSEMBLY (ALUMINUM WHEEL) - INSTALLATION .....22-8
TIRE AND WHEEL ASSEMBLY (ALUMINUM WHEEL) - REMOVAL ........22-8
TIRE AND WHEEL ASSEMBLY (STEEL WHEEL) - INSTALLATION ...............22-8
TIRE AND WHEEL ASSEMBLY (STEEL WHEEL) - REMOVAL ................... 22-8
TIRE AND WHEEL BALANCE - STANDARD PROCEDURE ................22-5
TIRE AND WHEEL MATCH MOUNTING - STANDARD PROCEDURE ................22-7
TIRE AND WHEEL ROTATION - STANDARD PROCEDURE ................22-7
TIRE AND WHEEL VIBRATION - DIAGNOSIS AND TESTING ..............22-1
TIRE INFLATION PRESSURES - STANDARD PROCEDURE ...............22-16
TIRE LEAK REPAIRING - STANDARD PROCEDURE ........................ 22-17
TIRE NOISE - DIAGNOSIS AND TESTING . . 22-14
TIRE PRESSURE FOR HIGH SPEED OPERATION - STANDARD PROCEDURE . . . 22-17
TIRE PRESSURE MONITORING - DESCRIPTION ........................ 22-9
TIRE PRESSURE MONITORING - OPERATION ......................... 22-10
TIRE PRESSURE SENSOR - DIAGNOSIS AND TESTING ....................... 22-11
TIRE (TEMPORARY) - DESCRIPTION, SPARE ............................. 22-14
TIRE WEAR PATTERNS - DIAGNOSIS AND TESTING ....................... 22-16
TIRES - CLEANING ................... 22-18
TIRES - DESCRIPTION, RADIAL-PLY ......22-13
TIRES - DESCRIPTION, REPLACEMENT . . . 22-14
TIRE/VEHICLE LEAD - DIAGNOSIS AND TESTING ........................... 22-14
32 INDEXRS
Description Group-Page Description Group-Page Description Group-Page