fuse diagram CHRYSLER CARAVAN 2005 Owner's Manual
[x] Cancel search | Manufacturer: CHRYSLER, Model Year: 2005, Model line: CARAVAN, Model: CHRYSLER CARAVAN 2005Pages: 2339, PDF Size: 59.69 MB
Page 1397 of 2339
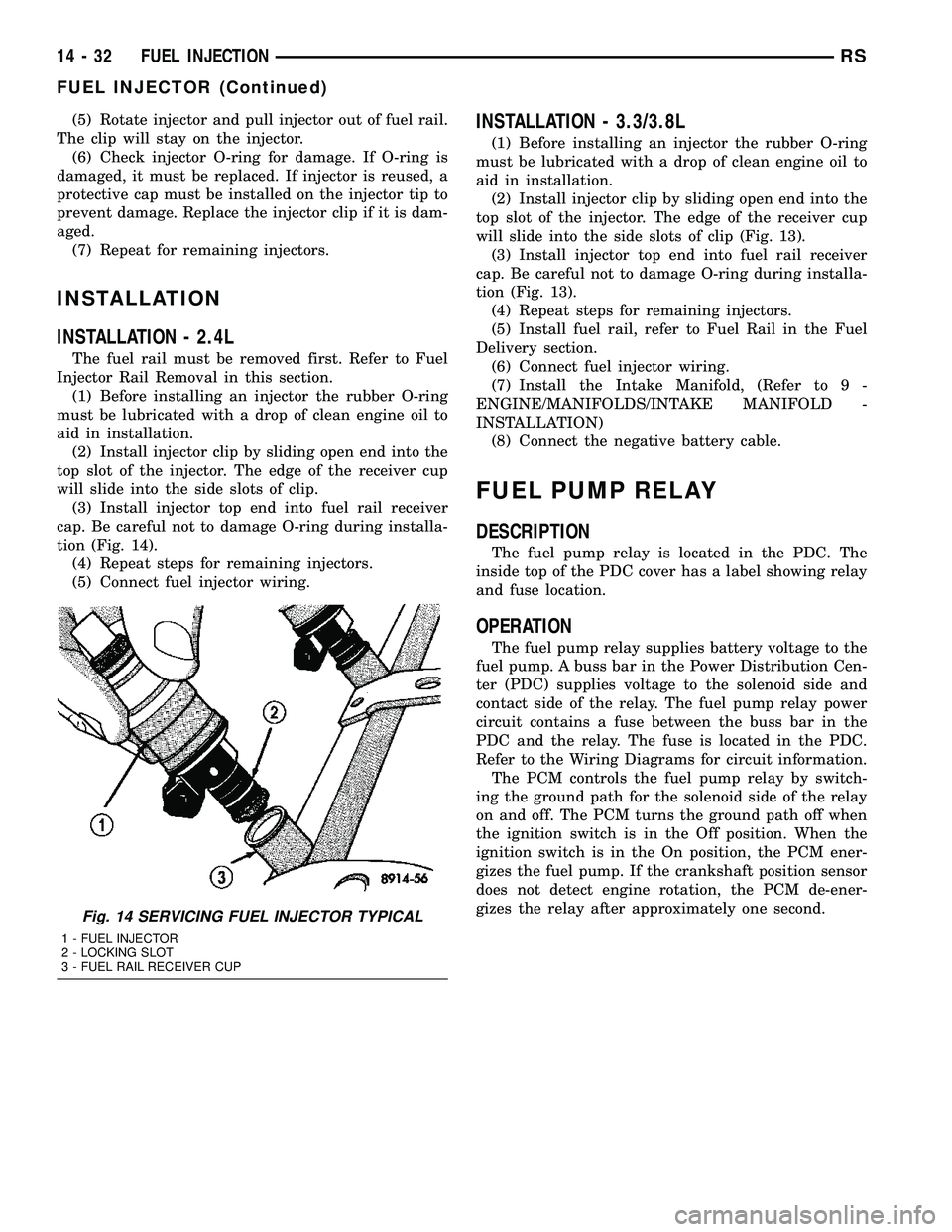
(5) Rotate injector and pull injector out of fuel rail.
The clip will stay on the injector.
(6) Check injector O-ring for damage. If O-ring is
damaged, it must be replaced. If injector is reused, a
protective cap must be installed on the injector tip to
prevent damage. Replace the injector clip if it is dam-
aged.
(7) Repeat for remaining injectors.
INSTALLATION
INSTALLATION - 2.4L
The fuel rail must be removed first. Refer to Fuel
Injector Rail Removal in this section.
(1) Before installing an injector the rubber O-ring
must be lubricated with a drop of clean engine oil to
aid in installation.
(2) Install injector clip by sliding open end into the
top slot of the injector. The edge of the receiver cup
will slide into the side slots of clip.
(3) Install injector top end into fuel rail receiver
cap. Be careful not to damage O-ring during installa-
tion (Fig. 14).
(4) Repeat steps for remaining injectors.
(5) Connect fuel injector wiring.
INSTALLATION - 3.3/3.8L
(1) Before installing an injector the rubber O-ring
must be lubricated with a drop of clean engine oil to
aid in installation.
(2) Install injector clip by sliding open end into the
top slot of the injector. The edge of the receiver cup
will slide into the side slots of clip (Fig. 13).
(3) Install injector top end into fuel rail receiver
cap. Be careful not to damage O-ring during installa-
tion (Fig. 13).
(4) Repeat steps for remaining injectors.
(5) Install fuel rail, refer to Fuel Rail in the Fuel
Delivery section.
(6) Connect fuel injector wiring.
(7) Install the Intake Manifold, (Refer to 9 -
ENGINE/MANIFOLDS/INTAKE MANIFOLD -
INSTALLATION)
(8) Connect the negative battery cable.
FUEL PUMP RELAY
DESCRIPTION
The fuel pump relay is located in the PDC. The
inside top of the PDC cover has a label showing relay
and fuse location.
OPERATION
The fuel pump relay supplies battery voltage to the
fuel pump. A buss bar in the Power Distribution Cen-
ter (PDC) supplies voltage to the solenoid side and
contact side of the relay. The fuel pump relay power
circuit contains a fuse between the buss bar in the
PDC and the relay. The fuse is located in the PDC.
Refer to the Wiring Diagrams for circuit information.
The PCM controls the fuel pump relay by switch-
ing the ground path for the solenoid side of the relay
on and off. The PCM turns the ground path off when
the ignition switch is in the Off position. When the
ignition switch is in the On position, the PCM ener-
gizes the fuel pump. If the crankshaft position sensor
does not detect engine rotation, the PCM de-ener-
gizes the relay after approximately one second.
Fig. 14 SERVICING FUEL INJECTOR TYPICAL
1 - FUEL INJECTOR
2 - LOCKING SLOT
3 - FUEL RAIL RECEIVER CUP
14 - 32 FUEL INJECTIONRS
FUEL INJECTOR (Continued)
Page 2169 of 2339
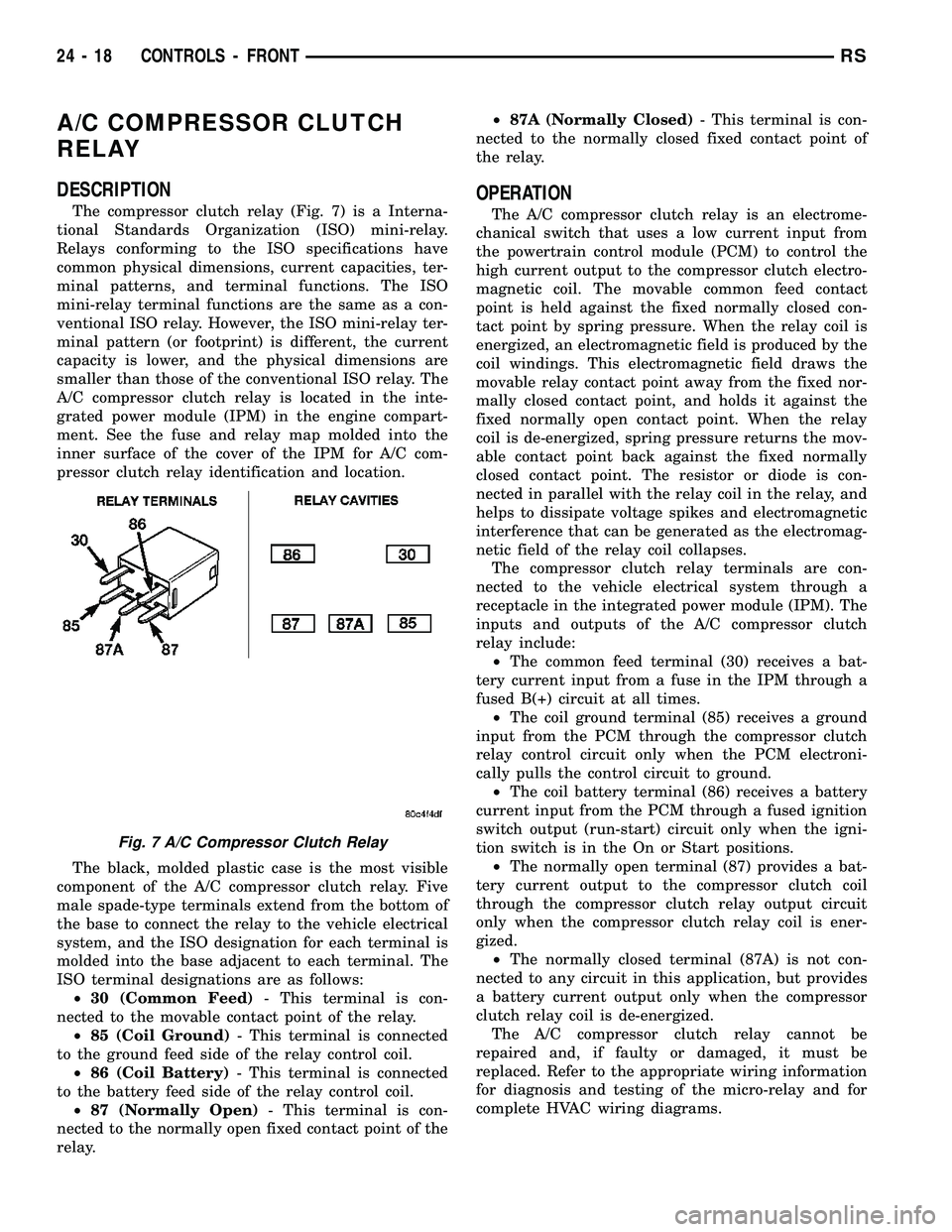
A/C COMPRESSOR CLUTCH
RELAY
DESCRIPTION
The compressor clutch relay (Fig. 7) is a Interna-
tional Standards Organization (ISO) mini-relay.
Relays conforming to the ISO specifications have
common physical dimensions, current capacities, ter-
minal patterns, and terminal functions. The ISO
mini-relay terminal functions are the same as a con-
ventional ISO relay. However, the ISO mini-relay ter-
minal pattern (or footprint) is different, the current
capacity is lower, and the physical dimensions are
smaller than those of the conventional ISO relay. The
A/C compressor clutch relay is located in the inte-
grated power module (IPM) in the engine compart-
ment. See the fuse and relay map molded into the
inner surface of the cover of the IPM for A/C com-
pressor clutch relay identification and location.
The black, molded plastic case is the most visible
component of the A/C compressor clutch relay. Five
male spade-type terminals extend from the bottom of
the base to connect the relay to the vehicle electrical
system, and the ISO designation for each terminal is
molded into the base adjacent to each terminal. The
ISO terminal designations are as follows:
²30 (Common Feed)- This terminal is con-
nected to the movable contact point of the relay.
²85 (Coil Ground)- This terminal is connected
to the ground feed side of the relay control coil.
²86 (Coil Battery)- This terminal is connected
to the battery feed side of the relay control coil.
²87 (Normally Open)- This terminal is con-
nected to the normally open fixed contact point of the
relay.²87A (Normally Closed)- This terminal is con-
nected to the normally closed fixed contact point of
the relay.
OPERATION
The A/C compressor clutch relay is an electrome-
chanical switch that uses a low current input from
the powertrain control module (PCM) to control the
high current output to the compressor clutch electro-
magnetic coil. The movable common feed contact
point is held against the fixed normally closed con-
tact point by spring pressure. When the relay coil is
energized, an electromagnetic field is produced by the
coil windings. This electromagnetic field draws the
movable relay contact point away from the fixed nor-
mally closed contact point, and holds it against the
fixed normally open contact point. When the relay
coil is de-energized, spring pressure returns the mov-
able contact point back against the fixed normally
closed contact point. The resistor or diode is con-
nected in parallel with the relay coil in the relay, and
helps to dissipate voltage spikes and electromagnetic
interference that can be generated as the electromag-
netic field of the relay coil collapses.
The compressor clutch relay terminals are con-
nected to the vehicle electrical system through a
receptacle in the integrated power module (IPM). The
inputs and outputs of the A/C compressor clutch
relay include:
²The common feed terminal (30) receives a bat-
tery current input from a fuse in the IPM through a
fused B(+) circuit at all times.
²The coil ground terminal (85) receives a ground
input from the PCM through the compressor clutch
relay control circuit only when the PCM electroni-
cally pulls the control circuit to ground.
²The coil battery terminal (86) receives a battery
current input from the PCM through a fused ignition
switch output (run-start) circuit only when the igni-
tion switch is in the On or Start positions.
²The normally open terminal (87) provides a bat-
tery current output to the compressor clutch coil
through the compressor clutch relay output circuit
only when the compressor clutch relay coil is ener-
gized.
²The normally closed terminal (87A) is not con-
nected to any circuit in this application, but provides
a battery current output only when the compressor
clutch relay coil is de-energized.
The A/C compressor clutch relay cannot be
repaired and, if faulty or damaged, it must be
replaced. Refer to the appropriate wiring information
for diagnosis and testing of the micro-relay and for
complete HVAC wiring diagrams.
Fig. 7 A/C Compressor Clutch Relay
24 - 18 CONTROLS - FRONTRS
Page 2175 of 2339
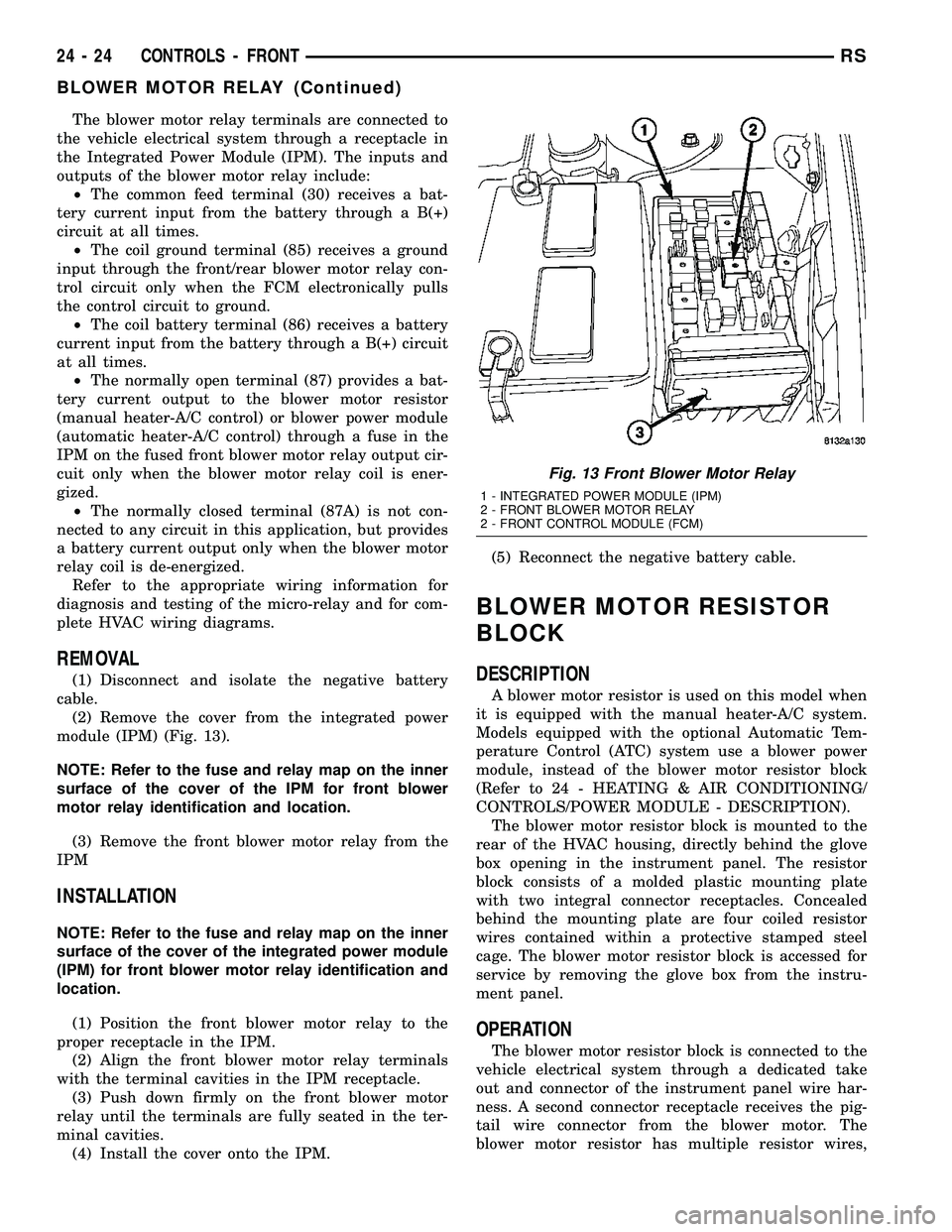
The blower motor relay terminals are connected to
the vehicle electrical system through a receptacle in
the Integrated Power Module (IPM). The inputs and
outputs of the blower motor relay include:
²The common feed terminal (30) receives a bat-
tery current input from the battery through a B(+)
circuit at all times.
²The coil ground terminal (85) receives a ground
input through the front/rear blower motor relay con-
trol circuit only when the FCM electronically pulls
the control circuit to ground.
²The coil battery terminal (86) receives a battery
current input from the battery through a B(+) circuit
at all times.
²The normally open terminal (87) provides a bat-
tery current output to the blower motor resistor
(manual heater-A/C control) or blower power module
(automatic heater-A/C control) through a fuse in the
IPM on the fused front blower motor relay output cir-
cuit only when the blower motor relay coil is ener-
gized.
²The normally closed terminal (87A) is not con-
nected to any circuit in this application, but provides
a battery current output only when the blower motor
relay coil is de-energized.
Refer to the appropriate wiring information for
diagnosis and testing of the micro-relay and for com-
plete HVAC wiring diagrams.
REMOVAL
(1) Disconnect and isolate the negative battery
cable.
(2) Remove the cover from the integrated power
module (IPM) (Fig. 13).
NOTE: Refer to the fuse and relay map on the inner
surface of the cover of the IPM for front blower
motor relay identification and location.
(3) Remove the front blower motor relay from the
IPM
INSTALLATION
NOTE: Refer to the fuse and relay map on the inner
surface of the cover of the integrated power module
(IPM) for front blower motor relay identification and
location.
(1) Position the front blower motor relay to the
proper receptacle in the IPM.
(2) Align the front blower motor relay terminals
with the terminal cavities in the IPM receptacle.
(3) Push down firmly on the front blower motor
relay until the terminals are fully seated in the ter-
minal cavities.
(4) Install the cover onto the IPM.(5) Reconnect the negative battery cable.
BLOWER MOTOR RESISTOR
BLOCK
DESCRIPTION
A blower motor resistor is used on this model when
it is equipped with the manual heater-A/C system.
Models equipped with the optional Automatic Tem-
perature Control (ATC) system use a blower power
module, instead of the blower motor resistor block
(Refer to 24 - HEATING & AIR CONDITIONING/
CONTROLS/POWER MODULE - DESCRIPTION).
The blower motor resistor block is mounted to the
rear of the HVAC housing, directly behind the glove
box opening in the instrument panel. The resistor
block consists of a molded plastic mounting plate
with two integral connector receptacles. Concealed
behind the mounting plate are four coiled resistor
wires contained within a protective stamped steel
cage. The blower motor resistor block is accessed for
service by removing the glove box from the instru-
ment panel.
OPERATION
The blower motor resistor block is connected to the
vehicle electrical system through a dedicated take
out and connector of the instrument panel wire har-
ness. A second connector receptacle receives the pig-
tail wire connector from the blower motor. The
blower motor resistor has multiple resistor wires,
Fig. 13 Front Blower Motor Relay
1 - INTEGRATED POWER MODULE (IPM)
2 - FRONT BLOWER MOTOR RELAY
2 - FRONT CONTROL MODULE (FCM)
24 - 24 CONTROLS - FRONTRS
BLOWER MOTOR RELAY (Continued)
Page 2188 of 2339
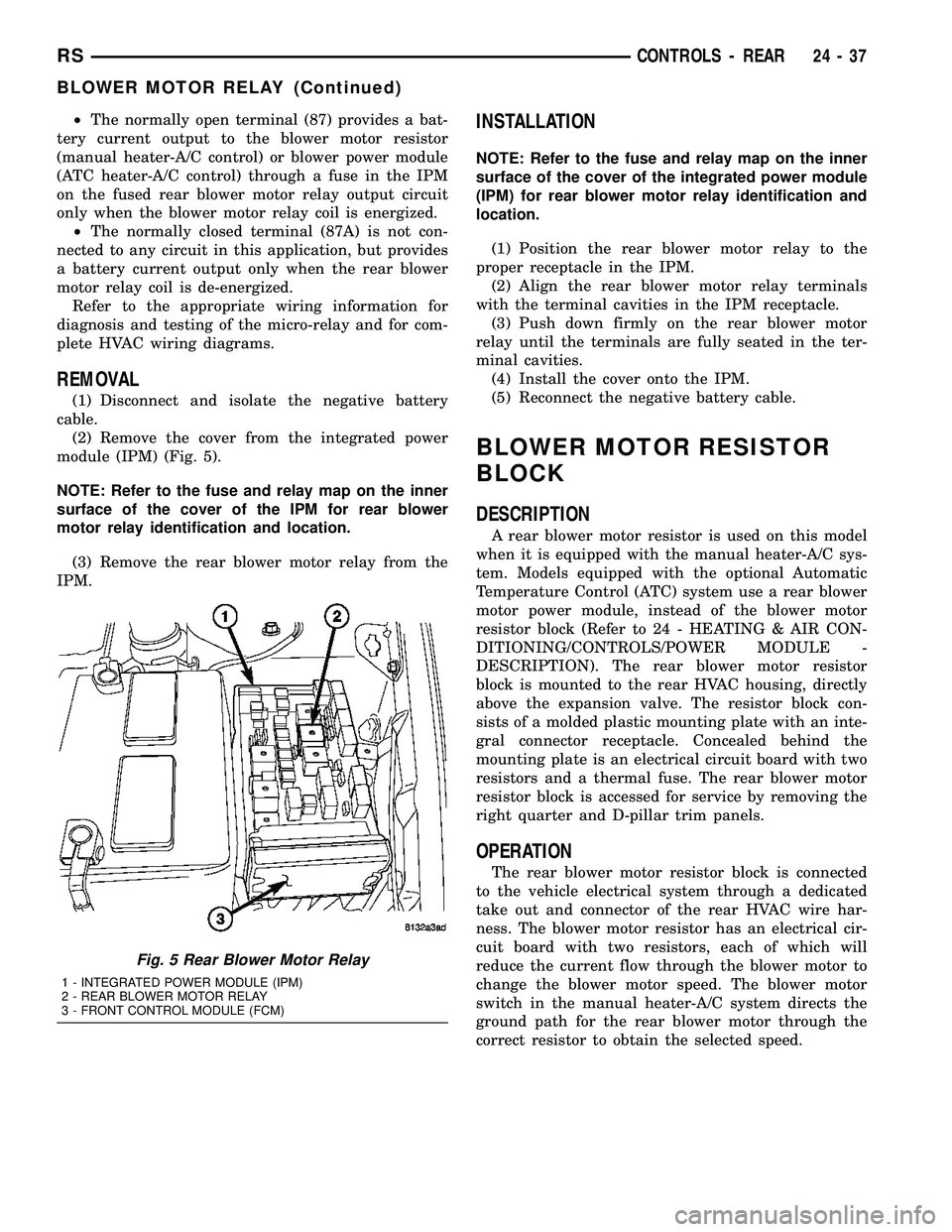
²The normally open terminal (87) provides a bat-
tery current output to the blower motor resistor
(manual heater-A/C control) or blower power module
(ATC heater-A/C control) through a fuse in the IPM
on the fused rear blower motor relay output circuit
only when the blower motor relay coil is energized.
²The normally closed terminal (87A) is not con-
nected to any circuit in this application, but provides
a battery current output only when the rear blower
motor relay coil is de-energized.
Refer to the appropriate wiring information for
diagnosis and testing of the micro-relay and for com-
plete HVAC wiring diagrams.
REMOVAL
(1) Disconnect and isolate the negative battery
cable.
(2) Remove the cover from the integrated power
module (IPM) (Fig. 5).
NOTE: Refer to the fuse and relay map on the inner
surface of the cover of the IPM for rear blower
motor relay identification and location.
(3) Remove the rear blower motor relay from the
IPM.
INSTALLATION
NOTE: Refer to the fuse and relay map on the inner
surface of the cover of the integrated power module
(IPM) for rear blower motor relay identification and
location.
(1) Position the rear blower motor relay to the
proper receptacle in the IPM.
(2) Align the rear blower motor relay terminals
with the terminal cavities in the IPM receptacle.
(3) Push down firmly on the rear blower motor
relay until the terminals are fully seated in the ter-
minal cavities.
(4) Install the cover onto the IPM.
(5) Reconnect the negative battery cable.
BLOWER MOTOR RESISTOR
BLOCK
DESCRIPTION
A rear blower motor resistor is used on this model
when it is equipped with the manual heater-A/C sys-
tem. Models equipped with the optional Automatic
Temperature Control (ATC) system use a rear blower
motor power module, instead of the blower motor
resistor block (Refer to 24 - HEATING & AIR CON-
DITIONING/CONTROLS/POWER MODULE -
DESCRIPTION). The rear blower motor resistor
block is mounted to the rear HVAC housing, directly
above the expansion valve. The resistor block con-
sists of a molded plastic mounting plate with an inte-
gral connector receptacle. Concealed behind the
mounting plate is an electrical circuit board with two
resistors and a thermal fuse. The rear blower motor
resistor block is accessed for service by removing the
right quarter and D-pillar trim panels.
OPERATION
The rear blower motor resistor block is connected
to the vehicle electrical system through a dedicated
take out and connector of the rear HVAC wire har-
ness. The blower motor resistor has an electrical cir-
cuit board with two resistors, each of which will
reduce the current flow through the blower motor to
change the blower motor speed. The blower motor
switch in the manual heater-A/C system directs the
ground path for the rear blower motor through the
correct resistor to obtain the selected speed.
Fig. 5 Rear Blower Motor Relay
1 - INTEGRATED POWER MODULE (IPM)
2 - REAR BLOWER MOTOR RELAY
3 - FRONT CONTROL MODULE (FCM)
RSCONTROLS - REAR24-37
BLOWER MOTOR RELAY (Continued)
Page 2197 of 2339
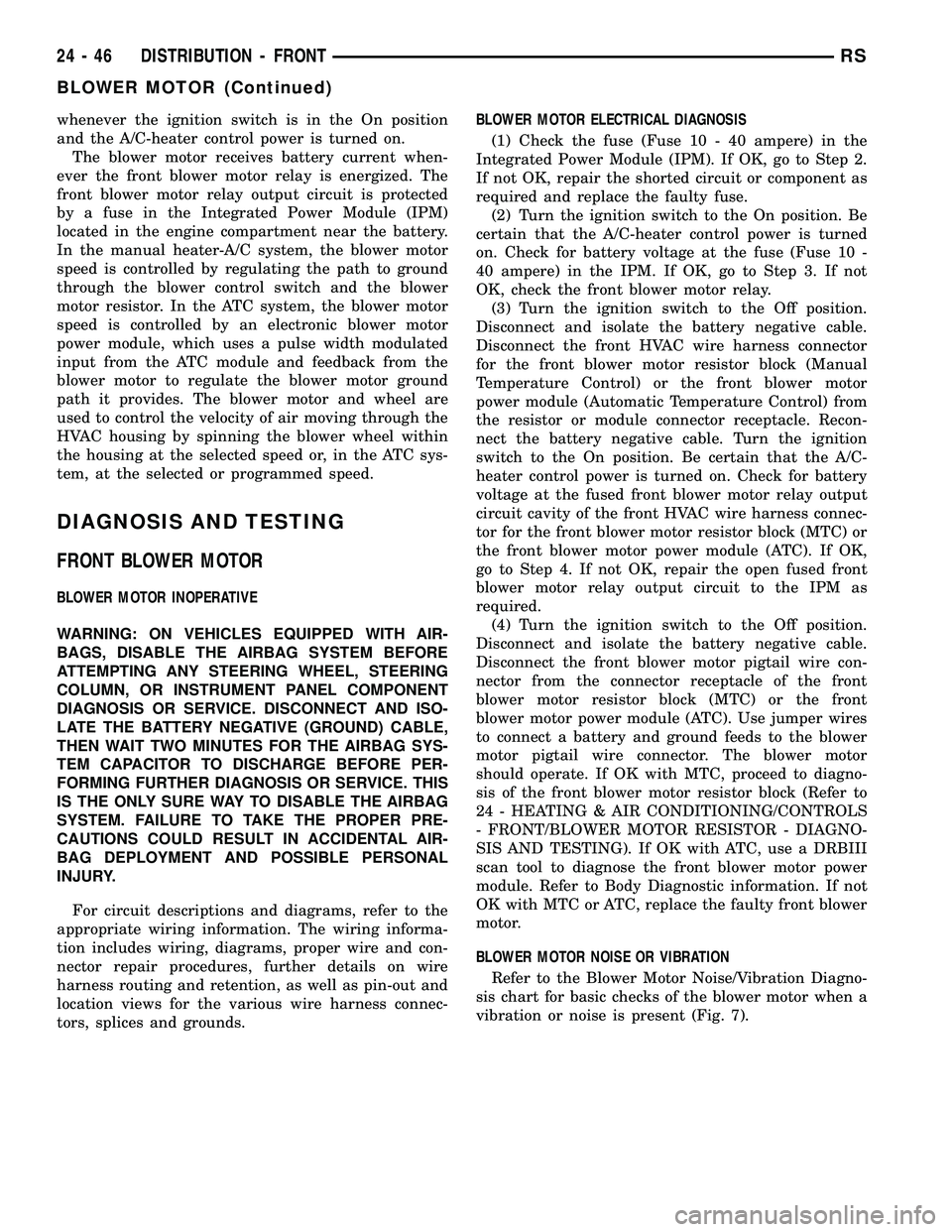
whenever the ignition switch is in the On position
and the A/C-heater control power is turned on.
The blower motor receives battery current when-
ever the front blower motor relay is energized. The
front blower motor relay output circuit is protected
by a fuse in the Integrated Power Module (IPM)
located in the engine compartment near the battery.
In the manual heater-A/C system, the blower motor
speed is controlled by regulating the path to ground
through the blower control switch and the blower
motor resistor. In the ATC system, the blower motor
speed is controlled by an electronic blower motor
power module, which uses a pulse width modulated
input from the ATC module and feedback from the
blower motor to regulate the blower motor ground
path it provides. The blower motor and wheel are
used to control the velocity of air moving through the
HVAC housing by spinning the blower wheel within
the housing at the selected speed or, in the ATC sys-
tem, at the selected or programmed speed.
DIAGNOSIS AND TESTING
FRONT BLOWER MOTOR
BLOWER MOTOR INOPERATIVE
WARNING: ON VEHICLES EQUIPPED WITH AIR-
BAGS, DISABLE THE AIRBAG SYSTEM BEFORE
ATTEMPTING ANY STEERING WHEEL, STEERING
COLUMN, OR INSTRUMENT PANEL COMPONENT
DIAGNOSIS OR SERVICE. DISCONNECT AND ISO-
LATE THE BATTERY NEGATIVE (GROUND) CABLE,
THEN WAIT TWO MINUTES FOR THE AIRBAG SYS-
TEM CAPACITOR TO DISCHARGE BEFORE PER-
FORMING FURTHER DIAGNOSIS OR SERVICE. THIS
IS THE ONLY SURE WAY TO DISABLE THE AIRBAG
SYSTEM. FAILURE TO TAKE THE PROPER PRE-
CAUTIONS COULD RESULT IN ACCIDENTAL AIR-
BAG DEPLOYMENT AND POSSIBLE PERSONAL
INJURY.
For circuit descriptions and diagrams, refer to the
appropriate wiring information. The wiring informa-
tion includes wiring, diagrams, proper wire and con-
nector repair procedures, further details on wire
harness routing and retention, as well as pin-out and
location views for the various wire harness connec-
tors, splices and grounds.BLOWER MOTOR ELECTRICAL DIAGNOSIS
(1) Check the fuse (Fuse 10 - 40 ampere) in the
Integrated Power Module (IPM). If OK, go to Step 2.
If not OK, repair the shorted circuit or component as
required and replace the faulty fuse.
(2) Turn the ignition switch to the On position. Be
certain that the A/C-heater control power is turned
on. Check for battery voltage at the fuse (Fuse 10 -
40 ampere) in the IPM. If OK, go to Step 3. If not
OK, check the front blower motor relay.
(3) Turn the ignition switch to the Off position.
Disconnect and isolate the battery negative cable.
Disconnect the front HVAC wire harness connector
for the front blower motor resistor block (Manual
Temperature Control) or the front blower motor
power module (Automatic Temperature Control) from
the resistor or module connector receptacle. Recon-
nect the battery negative cable. Turn the ignition
switch to the On position. Be certain that the A/C-
heater control power is turned on. Check for battery
voltage at the fused front blower motor relay output
circuit cavity of the front HVAC wire harness connec-
tor for the front blower motor resistor block (MTC) or
the front blower motor power module (ATC). If OK,
go to Step 4. If not OK, repair the open fused front
blower motor relay output circuit to the IPM as
required.
(4) Turn the ignition switch to the Off position.
Disconnect and isolate the battery negative cable.
Disconnect the front blower motor pigtail wire con-
nector from the connector receptacle of the front
blower motor resistor block (MTC) or the front
blower motor power module (ATC). Use jumper wires
to connect a battery and ground feeds to the blower
motor pigtail wire connector. The blower motor
should operate. If OK with MTC, proceed to diagno-
sis of the front blower motor resistor block (Refer to
24 - HEATING & AIR CONDITIONING/CONTROLS
- FRONT/BLOWER MOTOR RESISTOR - DIAGNO-
SIS AND TESTING). If OK with ATC, use a DRBIII
scan tool to diagnose the front blower motor power
module. Refer to Body Diagnostic information. If not
OK with MTC or ATC, replace the faulty front blower
motor.
BLOWER MOTOR NOISE OR VIBRATION
Refer to the Blower Motor Noise/Vibration Diagno-
sis chart for basic checks of the blower motor when a
vibration or noise is present (Fig. 7).
24 - 46 DISTRIBUTION - FRONTRS
BLOWER MOTOR (Continued)
Page 2209 of 2339
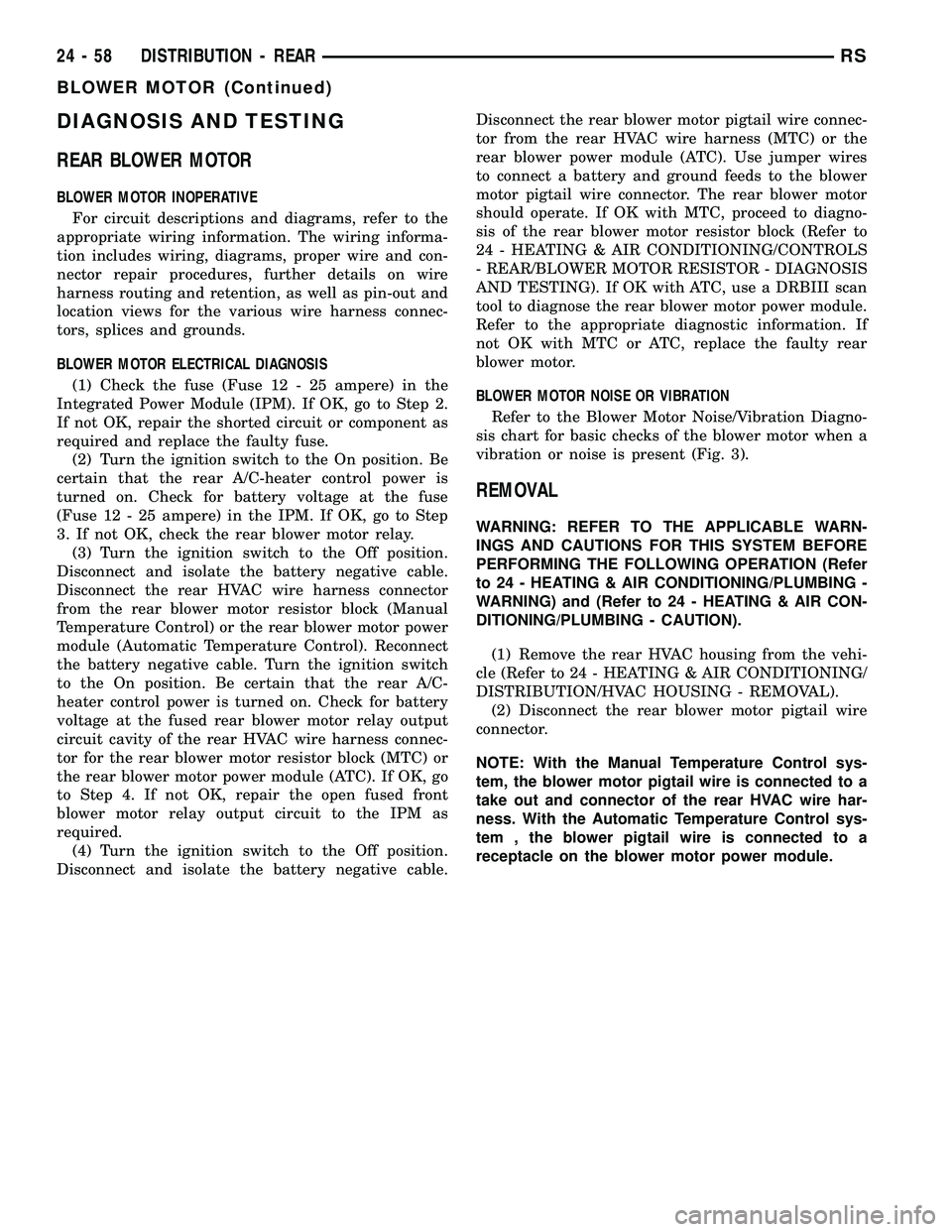
DIAGNOSIS AND TESTING
REAR BLOWER MOTOR
BLOWER MOTOR INOPERATIVE
For circuit descriptions and diagrams, refer to the
appropriate wiring information. The wiring informa-
tion includes wiring, diagrams, proper wire and con-
nector repair procedures, further details on wire
harness routing and retention, as well as pin-out and
location views for the various wire harness connec-
tors, splices and grounds.
BLOWER MOTOR ELECTRICAL DIAGNOSIS
(1) Check the fuse (Fuse 12 - 25 ampere) in the
Integrated Power Module (IPM). If OK, go to Step 2.
If not OK, repair the shorted circuit or component as
required and replace the faulty fuse.
(2) Turn the ignition switch to the On position. Be
certain that the rear A/C-heater control power is
turned on. Check for battery voltage at the fuse
(Fuse 12 - 25 ampere) in the IPM. If OK, go to Step
3. If not OK, check the rear blower motor relay.
(3) Turn the ignition switch to the Off position.
Disconnect and isolate the battery negative cable.
Disconnect the rear HVAC wire harness connector
from the rear blower motor resistor block (Manual
Temperature Control) or the rear blower motor power
module (Automatic Temperature Control). Reconnect
the battery negative cable. Turn the ignition switch
to the On position. Be certain that the rear A/C-
heater control power is turned on. Check for battery
voltage at the fused rear blower motor relay output
circuit cavity of the rear HVAC wire harness connec-
tor for the rear blower motor resistor block (MTC) or
the rear blower motor power module (ATC). If OK, go
to Step 4. If not OK, repair the open fused front
blower motor relay output circuit to the IPM as
required.
(4) Turn the ignition switch to the Off position.
Disconnect and isolate the battery negative cable.Disconnect the rear blower motor pigtail wire connec-
tor from the rear HVAC wire harness (MTC) or the
rear blower power module (ATC). Use jumper wires
to connect a battery and ground feeds to the blower
motor pigtail wire connector. The rear blower motor
should operate. If OK with MTC, proceed to diagno-
sis of the rear blower motor resistor block (Refer to
24 - HEATING & AIR CONDITIONING/CONTROLS
- REAR/BLOWER MOTOR RESISTOR - DIAGNOSIS
AND TESTING). If OK with ATC, use a DRBIII scan
tool to diagnose the rear blower motor power module.
Refer to the appropriate diagnostic information. If
not OK with MTC or ATC, replace the faulty rear
blower motor.
BLOWER MOTOR NOISE OR VIBRATION
Refer to the Blower Motor Noise/Vibration Diagno-
sis chart for basic checks of the blower motor when a
vibration or noise is present (Fig. 3).
REMOVAL
WARNING: REFER TO THE APPLICABLE WARN-
INGS AND CAUTIONS FOR THIS SYSTEM BEFORE
PERFORMING THE FOLLOWING OPERATION (Refer
to 24 - HEATING & AIR CONDITIONING/PLUMBING -
WARNING) and (Refer to 24 - HEATING & AIR CON-
DITIONING/PLUMBING - CAUTION).
(1) Remove the rear HVAC housing from the vehi-
cle (Refer to 24 - HEATING & AIR CONDITIONING/
DISTRIBUTION/HVAC HOUSING - REMOVAL).
(2) Disconnect the rear blower motor pigtail wire
connector.
NOTE: With the Manual Temperature Control sys-
tem, the blower motor pigtail wire is connected to a
take out and connector of the rear HVAC wire har-
ness. With the Automatic Temperature Control sys-
tem , the blower pigtail wire is connected to a
receptacle on the blower motor power module.
24 - 58 DISTRIBUTION - REARRS
BLOWER MOTOR (Continued)
Page 2334 of 2339
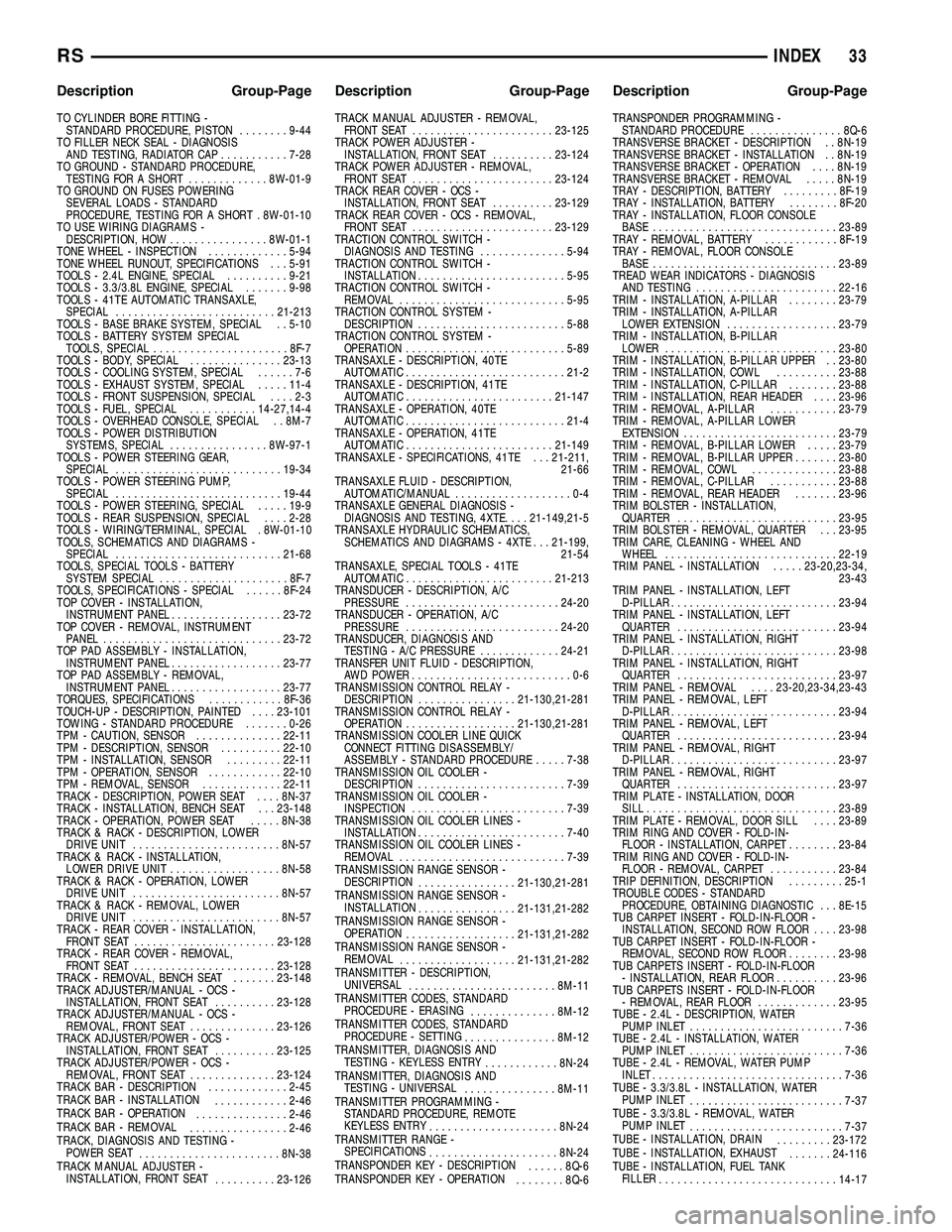
TO CYLINDER BORE FITTING -STANDARD PROCEDURE, PISTON ........9-44
TO FILLER NECK SEAL - DIAGNOSIS AND TESTING, RADIATOR CAP ...........7-28
TO GROUND - STANDARD PROCEDURE, TESTING FOR A SHORT .............8W-01-9
TO GROUND ON FUSES POWERING SEVERAL LOADS - STANDARD
PROCEDURE, TESTING FOR A SHORT . 8W-01-10
TO USE WIRING DIAGRAMS - DESCRIPTION, HOW ................8W -01-1
TONE WHEEL - INSPECTION .............5-94
TONE WHEEL RUNOUT, SPECIFICATIONS . . . 5-91
TOOLS - 2.4L ENGINE, SPECIAL ..........9-21
TOOLS - 3.3/3.8L ENGINE, SPECIAL .......9-98
TOOLS - 41TE AUTOMATIC TRANSAXLE, SPECIAL .......................... 21-213
TOOLS - BASE BRAKE SYSTEM, SPECIAL . . 5-10
TOOLS - BATTERY SYSTEM SPECIAL TOOLS, SPECIAL ...................... 8F-7
TOOLS - BODY, SPECIAL ...............23-13
TOOLS - COOLING SYSTEM, SPECIAL ......7-6
TOOLS - EXHAUST SYSTEM, SPECIAL .....11-4
TOOLS - FRONT SUSPENSION, SPECIAL ....2-3
TOOLS - FUEL, SPECIAL ...........14-27,14-4
TOOLS - OVERHEAD CONSOLE, SPECIAL . . 8M-7
TOOLS - POWER DISTRIBUTION SYSTEMS, SPECIAL ................8W -97-1
TOOLS - POWER STEERING GEAR, SPECIAL ........................... 19-34
TOOLS - POWER STEERING PUMP, SPECIAL ........................... 19-44
TOOLS - POWER STEERING, SPECIAL .....19-9
TOOLS - REAR SUSPENSION, SPECIAL ....2-28
TOOLS - WIRING/TERMINAL, SPECIAL . 8W-01-10
TOOLS, SCHEMATICS AND DIAGRAMS - SPECIAL ........................... 21-68
TOOLS, SPECIAL TOOLS - BATTERY SYSTEM SPECIAL ..................... 8F-7
TOOLS, SPECIFICATIONS - SPECIAL ......8F-24
TOP COVER - INSTALLATION, INSTRUMENT PANEL .................. 23-72
TOP COVER - REMOVAL, INSTRUMENT PANEL ............................. 23-72
TOP PAD ASSEMBLY - INSTALLATION, INSTRUMENT PANEL .................. 23-77
TOP PAD ASSEMBLY - REMOVAL, INSTRUMENT PANEL .................. 23-77
TORQUES, SPECIFICATIONS ............8F-36
TOUCH-UP - DESCRIPTION, PAINTED ....23-101
TOWING - STANDARD PROCEDURE .......0-26
TPM - CAUTION, SENSOR ..............22-11
TPM - DESCRIPTION, SENSOR ..........22-10
TPM - INSTALLATION, SENSOR .........22-11
TPM - OPERATION, SENSOR ............22-10
TPM - REMOVAL, SENSOR .............22-11
TRACK - DESCRIPTION, POWER SEAT ....8N-37
TRACK - INSTALLATION, BENCH SEAT . . . 23-148
TRACK - OPERATION, POWER SEAT .....8N-38
TRACK & RACK - DESCRIPTION, LOWER DRIVE UNIT ........................ 8N-57
TRACK & RACK - INSTALLATION, LOWER DRIVE UNIT .................. 8N-58
TRACK & RACK - OPERATION, LOWER DRIVE UNIT ........................ 8N-57
TRACK & RACK - REMOVAL, LOWER DRIVE UNIT ........................ 8N-57
TRACK - REAR COVER - INSTALLATION, FRONT SEAT ....................... 23-128
TRACK - REAR COVER - REMOVAL, FRONT SEAT ....................... 23-128
TRACK - REMOVAL, BENCH SEAT .......23-148
TRACK ADJUSTER/MANUAL - OCS - INSTALLATION, FRONT SEAT ..........23-128
TRACK ADJUSTER/MANUAL - OCS - REMOVAL, FRONT SEAT ..............23-126
TRACK ADJUSTER/POWER - OCS - INSTALLATION, FRONT SEAT ..........23-125
TRACK ADJUSTER/POWER - OCS - REMOVAL, FRONT SEAT ..............23-124
TRACK BAR - DESCRIPTION .............2-45
TRACK BAR - INSTALLATION ............2-46
TRACK BAR - OPERATION ...............2-46
TRACK BAR - REMOVAL ................2-46
TRACK, DIAGNOSIS AND TESTING - POWER SEAT ....................... 8N-38
TRACK MANUAL ADJUSTER - INSTALLATION, FRONT SEAT ..........23-126TRACK MANUAL ADJUSTER - REMOVAL,
FRONT SEAT ....................... 23-125
TRACK POWER ADJUSTER - INSTALLATION, FRONT SEAT ..........23-124
TRACK POWER ADJUSTER - REMOVAL, FRONT SEAT ....................... 23-124
TRACK REAR COVER - OCS - INSTALLATION, FRONT SEAT ..........23-129
TRACK REAR COVER - OCS - REMOVAL, FRONT SEAT ....................... 23-129
TRACTION CONTROL SWITCH - DIAGNOSIS AND TESTING ..............5-94
TRACTION CONTROL SWITCH - INSTALLATION ........................ 5-95
TRACTION CONTROL SWITCH - REMOVAL ........................... 5-95
TRACTION CONTROL SYSTEM - DESCRIPTION ........................ 5-88
TRACTION CONTROL SYSTEM - OPERATION .......................... 5-89
TRANSAXLE - DESCRIPTION, 40TE AUTOMATIC .......................... 21-2
TRANSAXLE - DESCRIPTION, 41TE AUTOMATIC ........................ 21-147
TRANSAXLE - OPERATION, 40TE AUTOMATIC .......................... 21-4
TRANSAXLE - OPERATION, 41TE AUTOMATIC ........................ 21-149
TRANSAXLE - SPECIFICATIONS, 41TE . . . 21-211, 21-66
TRANSAXLE FLUID - DESCRIPTION, AUTOMATIC/MANUAL ...................0-4
TRANSAXLE GENERAL DIAGNOSIS - DIAGNOSIS AND TESTING, 4XTE .....21-149,21-5
TRANSAXLE HYDRAULIC SCHEMATICS, SCHEMATICS AND DIAGRAMS - 4XTE . . . 21-199, 21-54
TRANSAXLE, SPECIAL TOOLS - 41TE AUTOMATIC ........................ 21-213
TRANSDUCER - DESCRIPTION, A/C PRESSURE ......................... 24-20
TRANSDUCER - OPERATION, A/C PRESSURE ......................... 24-20
TRANSDUCER, DIAGNOSIS AND TESTING - A/C PRESSURE .............24-21
TRANSFER UNIT FLUID - DESCRIPTION, AWD POWER ..........................0-6
TRANSMISSION CONTROL RELAY - DESCRIPTION ................ 21-130,21-281
TRANSMISSION CONTROL RELAY - OPERATION .................. 21-130,21-281
TRANSMISSION COOLER LINE QUICK CONNECT FITTING DISASSEMBLY/
ASSEMBLY - STANDARD PROCEDURE .....7-38
TRANSMISSION OIL COOLER - DESCRIPTION ........................ 7-39
TRANSMISSION OIL COOLER - INSPECTION ......................... 7-39
TRANSMISSION OIL COOLER LINES - INSTALLATION ........................ 7-40
TRANSMISSION OIL COOLER LINES - REMOVAL ........................... 7-39
TRANSMISSION RANGE SENSOR - DESCRIPTION ................ 21-130,21-281
TRANSMISSION RANGE SENSOR - INSTALLATION ................ 21-131,21-282
TRANSMISSION RANGE SENSOR - OPERATION .................. 21-131,21-282
TRANSMISSION RANGE SENSOR - REMOVAL ................... 21-131,21-282
TRANSMITTER - DESCRIPTION, UNIVERSAL ........................ 8M-11
TRANSMITTER CODES, STANDARD PROCEDURE - ERASING ..............8M-12
TRANSMITTER CODES, STANDARD PROCEDURE - SETTING ...............8M-12
TRANSMITTER, DIAGNOSIS AND TESTING - KEYLESS ENTRY ............8N-24
TRANSMITTER, DIAGNOSIS AND TESTING - UNIVERSAL ...............8M-11
TRANSMITTER PROGRAMMING - STANDARD PROCEDURE, REMOTE
KEYLESS ENTRY ..................... 8N-24
TRANSMITTER RANGE - SPECIFICATIONS ..................... 8N-24
TRANSPONDER KEY - DESCRIPTION ......8Q-6
TRANSPONDER KEY - OPERATION ........8Q-6TRANSPONDER PROGRAMMING -
STANDARD PROCEDURE ...............8Q-6
TRANSVERSE BRACKET - DESCRIPTION . . 8N-19
TRANSVERSE BRACKET - INSTALLATION . . 8N-19
TRANSVERSE BRACKET - OPERATION ....8N-19
TRANSVERSE BRACKET - REMOVAL .....8N-19
TRAY - DESCRIPTION, BATTERY .........8F-19
TRAY - INSTALLATION, BATTERY ........8F-20
TRAY - INSTALLATION, FLOOR CONSOLE BASE .............................. 23-89
TRAY - REMOVAL, BATTERY ............8F-19
TRAY - REMOVAL, FLOOR CONSOLE BASE .............................. 23-89
TREAD WEAR INDICATORS - DIAGNOSIS AND TESTING ....................... 22-16
TRIM - INSTALLATION, A-PILLAR ........23-79
TRIM - INSTALLATION, A-PILLAR LOWER EXTENSION .................. 23-79
TRIM - INSTALLATION, B-PILLAR LOWER ............................ 23-80
TRIM - INSTALLATION, B-PILLAR UPPER . . 23-80
TRIM - INSTALLATION, COWL ..........23-88
TRIM - INSTALLATION, C-PILLAR ........23-88
TRIM - INSTALLATION, REAR HEADER ....23-96
TRIM - REMOVAL, A-PILLAR ...........23-79
TRIM - REMOVAL, A-PILLAR LOWER EXTENSION ......................... 23-79
TRIM - REMOVAL, B-PILLAR LOWER .....23-79
TRIM - REMOVAL, B-PILLAR UPPER .......23-80
TRIM - REMOVAL, COWL ..............23-88
TRIM - REMOVAL, C-PILLAR ...........23-88
TRIM - REMOVAL, REAR HEADER .......23-96
TRIM BOLSTER - INSTALLATION, QUARTER .......................... 23-95
TRIM BOLSTER - REMOVAL, QUARTER . . . 23-95
TRIM CARE, CLEANING - WHEEL AND WHEEL ............................ 22-19
TRIM PANEL - INSTALLATION .....23-20,23-34,
23-43
TRIM PANEL - INSTALLATION, LEFT D-PILLAR ........................... 23-94
TRIM PANEL - INSTALLATION, LEFT QUARTER .......................... 23-94
TRIM PANEL - INSTALLATION, RIGHT D-PILLAR ........................... 23-98
TRIM PANEL - INSTALLATION, RIGHT QUARTER .......................... 23-97
TRIM PANEL - REMOVAL ....23-20,23-34,23-43
TRIM PANEL - REMOVAL, LEFT D-PILLAR ........................... 23-94
TRIM PANEL - REMOVAL, LEFT QUARTER .......................... 23-94
TRIM PANEL - REMOVAL, RIGHT D-PILLAR ........................... 23-97
TRIM PANEL - REMOVAL, RIGHT QUARTER .......................... 23-97
TRIM PLATE - INSTALLATION, DOOR SILL ............................... 23-89
TRIM PLATE - REMOVAL, DOOR SILL ....23-89
TRIM RING AND COVER - FOLD-IN- FLOOR - INSTALLATION, CARPET ........23-84
TRIM RING AND COVER - FOLD-IN- FLOOR - REMOVAL, CARPET ...........23-84
TRIP DEFINITION, DESCRIPTION .........25-1
TROUBLE CODES - STANDARD PROCEDURE, OBTAINING DIAGNOSTIC . . . 8E-15
TUB CARPET INSERT - FOLD-IN-FLOOR - INSTALLATION, SECOND ROW FLOOR ....23-98
TUB CARPET INSERT - FOLD-IN-FLOOR - REMOVAL, SECOND ROW FLOOR ........23-98
TUB CARPETS INSERT - FOLD-IN-FLOOR - INSTALLATION, REAR FLOOR ..........23-96
TUB CARPETS INSERT - FOLD-IN-FLOOR - REMOVAL, REAR FLOOR .............23-95
TUBE - 2.4L - DESCRIPTION, WATER PUMP INLET ......................... 7-36
TUBE - 2.4L - INSTALLATION, WATER PUMP INLET ......................... 7-36
TUBE - 2.4L - REMOVAL, WATER PUMP INLET ............................... 7-36
TUBE - 3.3/3.8L - INSTALLATION, WATER PUMP INLET ......................... 7-37
TUBE - 3.3/3.8L - REMOVAL, WATER PUMP INLET ......................... 7-37
TUBE - INSTALLATION, DRAIN .........23-172
TUBE - INSTALLATION, EXHAUST .......24-116
TUBE - INSTALLATION, FUEL TANK FILLER ............................. 14-17
RS INDEX33
Description Group-Page Description Group-Page Description Group-Page