odometer CHRYSLER VOYAGER 1996 User Guide
[x] Cancel search | Manufacturer: CHRYSLER, Model Year: 1996, Model line: VOYAGER, Model: CHRYSLER VOYAGER 1996Pages: 1938, PDF Size: 55.84 MB
Page 347 of 1938
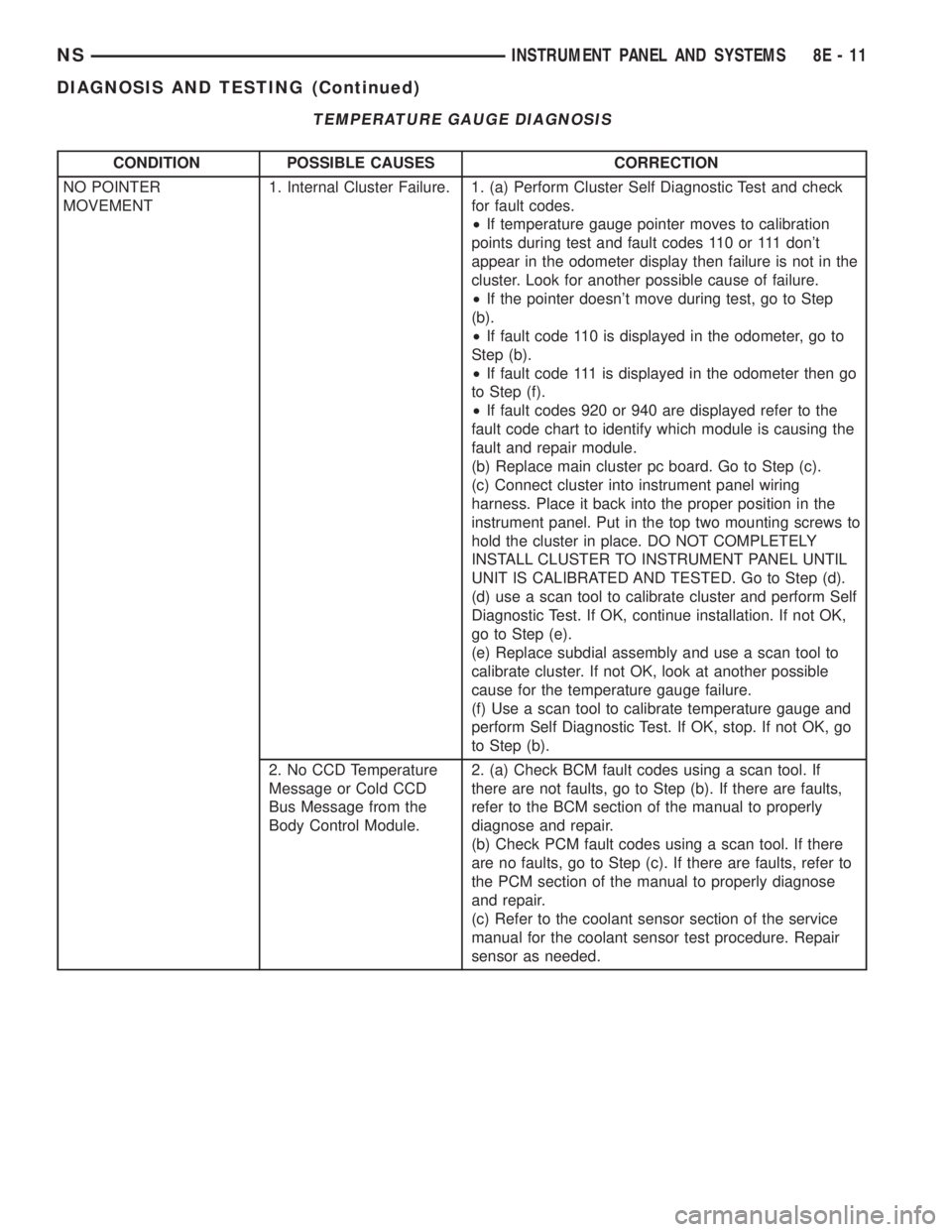
TEMPERATURE GAUGE DIAGNOSIS
CONDITION POSSIBLE CAUSES CORRECTION
NO POINTER
MOVEMENT1. Internal Cluster Failure. 1. (a) Perform Cluster Self Diagnostic Test and check
for fault codes.
²If temperature gauge pointer moves to calibration
points during test and fault codes 110 or 111 don't
appear in the odometer display then failure is not in the
cluster. Look for another possible cause of failure.
²If the pointer doesn't move during test, go to Step
(b).
²If fault code 110 is displayed in the odometer, go to
Step (b).
²If fault code 111 is displayed in the odometer then go
to Step (f).
²If fault codes 920 or 940 are displayed refer to the
fault code chart to identify which module is causing the
fault and repair module.
(b) Replace main cluster pc board. Go to Step (c).
(c) Connect cluster into instrument panel wiring
harness. Place it back into the proper position in the
instrument panel. Put in the top two mounting screws to
hold the cluster in place. DO NOT COMPLETELY
INSTALL CLUSTER TO INSTRUMENT PANEL UNTIL
UNIT IS CALIBRATED AND TESTED. Go to Step (d).
(d) use a scan tool to calibrate cluster and perform Self
Diagnostic Test. If OK, continue installation. If not OK,
go to Step (e).
(e) Replace subdial assembly and use a scan tool to
calibrate cluster. If not OK, look at another possible
cause for the temperature gauge failure.
(f) Use a scan tool to calibrate temperature gauge and
perform Self Diagnostic Test. If OK, stop. If not OK, go
to Step (b).
2. No CCD Temperature
Message or Cold CCD
Bus Message from the
Body Control Module.2. (a) Check BCM fault codes using a scan tool. If
there are not faults, go to Step (b). If there are faults,
refer to the BCM section of the manual to properly
diagnose and repair.
(b) Check PCM fault codes using a scan tool. If there
are no faults, go to Step (c). If there are faults, refer to
the PCM section of the manual to properly diagnose
and repair.
(c) Refer to the coolant sensor section of the service
manual for the coolant sensor test procedure. Repair
sensor as needed.
NSINSTRUMENT PANEL AND SYSTEMS 8E - 11
DIAGNOSIS AND TESTING (Continued)
Page 348 of 1938
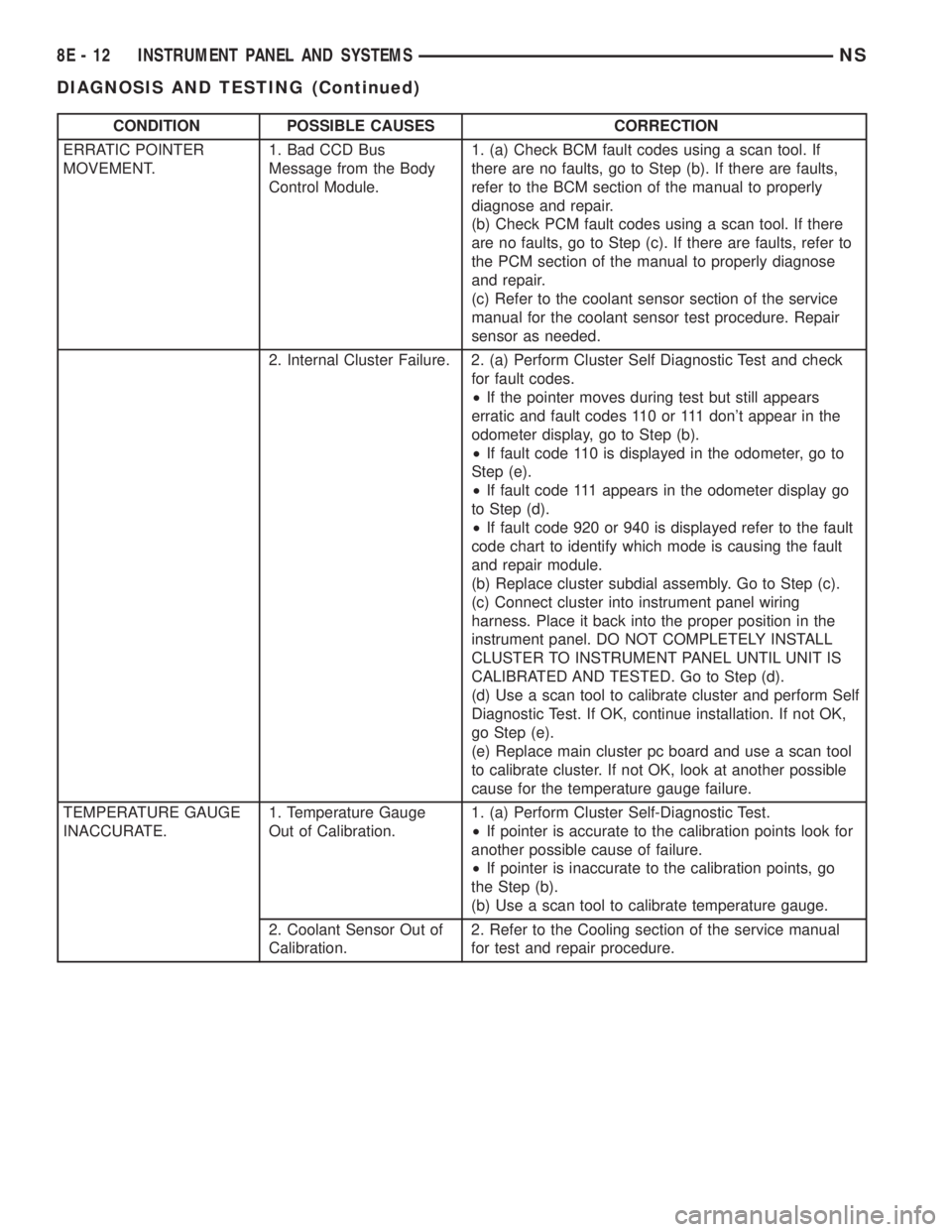
CONDITION POSSIBLE CAUSES CORRECTION
ERRATIC POINTER
MOVEMENT.1. Bad CCD Bus
Message from the Body
Control Module.1. (a) Check BCM fault codes using a scan tool. If
there are no faults, go to Step (b). If there are faults,
refer to the BCM section of the manual to properly
diagnose and repair.
(b) Check PCM fault codes using a scan tool. If there
are no faults, go to Step (c). If there are faults, refer to
the PCM section of the manual to properly diagnose
and repair.
(c) Refer to the coolant sensor section of the service
manual for the coolant sensor test procedure. Repair
sensor as needed.
2. Internal Cluster Failure. 2. (a) Perform Cluster Self Diagnostic Test and check
for fault codes.
²If the pointer moves during test but still appears
erratic and fault codes 110 or 111 don't appear in the
odometer display, go to Step (b).
²If fault code 110 is displayed in the odometer, go to
Step (e).
²If fault code 111 appears in the odometer display go
to Step (d).
²If fault code 920 or 940 is displayed refer to the fault
code chart to identify which mode is causing the fault
and repair module.
(b) Replace cluster subdial assembly. Go to Step (c).
(c) Connect cluster into instrument panel wiring
harness. Place it back into the proper position in the
instrument panel. DO NOT COMPLETELY INSTALL
CLUSTER TO INSTRUMENT PANEL UNTIL UNIT IS
CALIBRATED AND TESTED. Go to Step (d).
(d) Use a scan tool to calibrate cluster and perform Self
Diagnostic Test. If OK, continue installation. If not OK,
go Step (e).
(e) Replace main cluster pc board and use a scan tool
to calibrate cluster. If not OK, look at another possible
cause for the temperature gauge failure.
TEMPERATURE GAUGE
INACCURATE.1. Temperature Gauge
Out of Calibration.1. (a) Perform Cluster Self-Diagnostic Test.
²If pointer is accurate to the calibration points look for
another possible cause of failure.
²If pointer is inaccurate to the calibration points, go
the Step (b).
(b) Use a scan tool to calibrate temperature gauge.
2. Coolant Sensor Out of
Calibration.2. Refer to the Cooling section of the service manual
for test and repair procedure.
8E - 12 INSTRUMENT PANEL AND SYSTEMSNS
DIAGNOSIS AND TESTING (Continued)
Page 349 of 1938
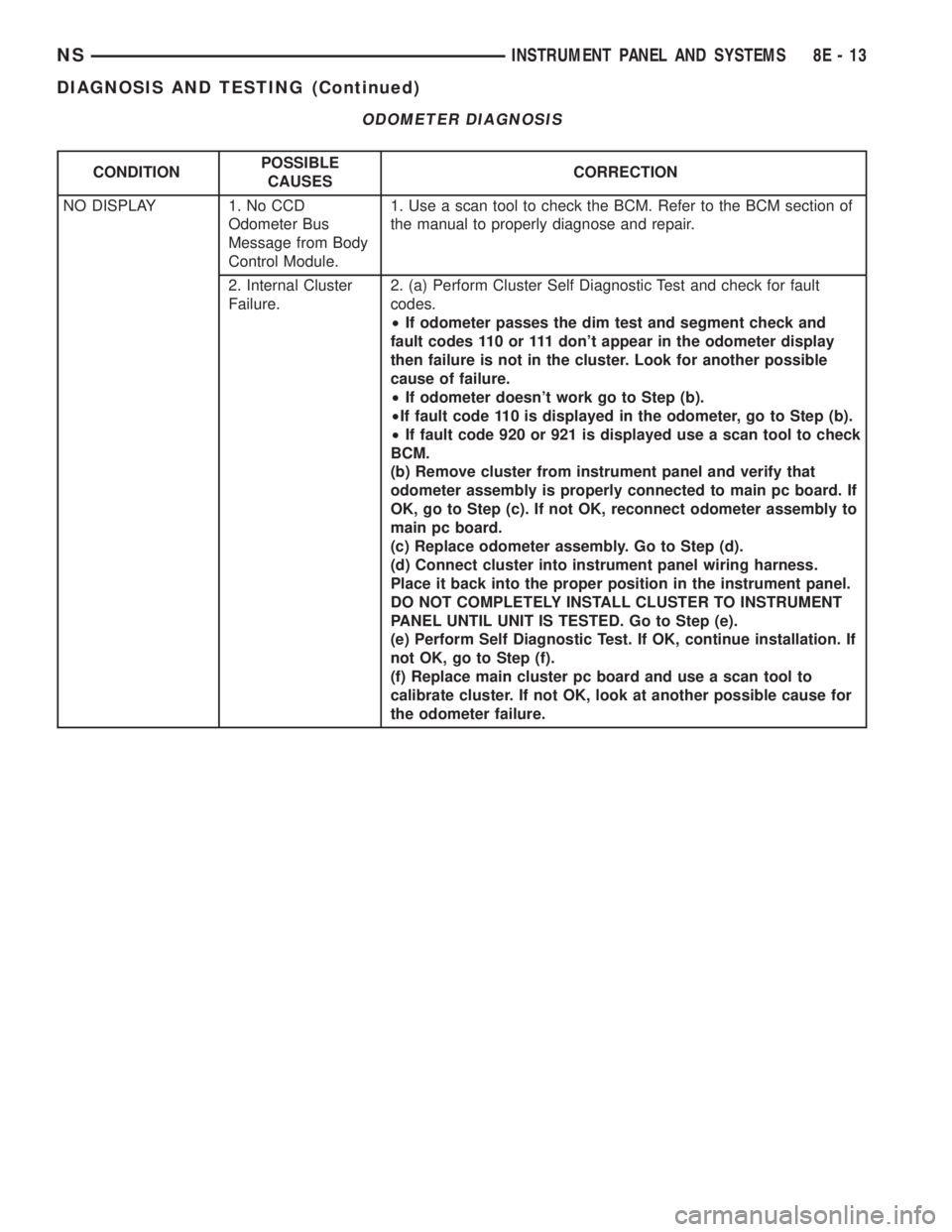
ODOMETER DIAGNOSIS
CONDITIONPOSSIBLE
CAUSESCORRECTION
NO DISPLAY 1. No CCD
Odometer Bus
Message from Body
Control Module.1. Use a scan tool to check the BCM. Refer to the BCM section of
the manual to properly diagnose and repair.
2. Internal Cluster
Failure.2. (a) Perform Cluster Self Diagnostic Test and check for fault
codes.
²If odometer passes the dim test and segment check and
fault codes 110 or 111 don't appear in the odometer display
then failure is not in the cluster. Look for another possible
cause of failure.
²If odometer doesn't work go to Step (b).
²If fault code 110 is displayed in the odometer, go to Step (b).
²If fault code 920 or 921 is displayed use a scan tool to check
BCM.
(b) Remove cluster from instrument panel and verify that
odometer assembly is properly connected to main pc board. If
OK, go to Step (c). If not OK, reconnect odometer assembly to
main pc board.
(c) Replace odometer assembly. Go to Step (d).
(d) Connect cluster into instrument panel wiring harness.
Place it back into the proper position in the instrument panel.
DO NOT COMPLETELY INSTALL CLUSTER TO INSTRUMENT
PANEL UNTIL UNIT IS TESTED. Go to Step (e).
(e) Perform Self Diagnostic Test. If OK, continue installation. If
not OK, go to Step (f).
(f) Replace main cluster pc board and use a scan tool to
calibrate cluster. If not OK, look at another possible cause for
the odometer failure.
NSINSTRUMENT PANEL AND SYSTEMS 8E - 13
DIAGNOSIS AND TESTING (Continued)
Page 350 of 1938
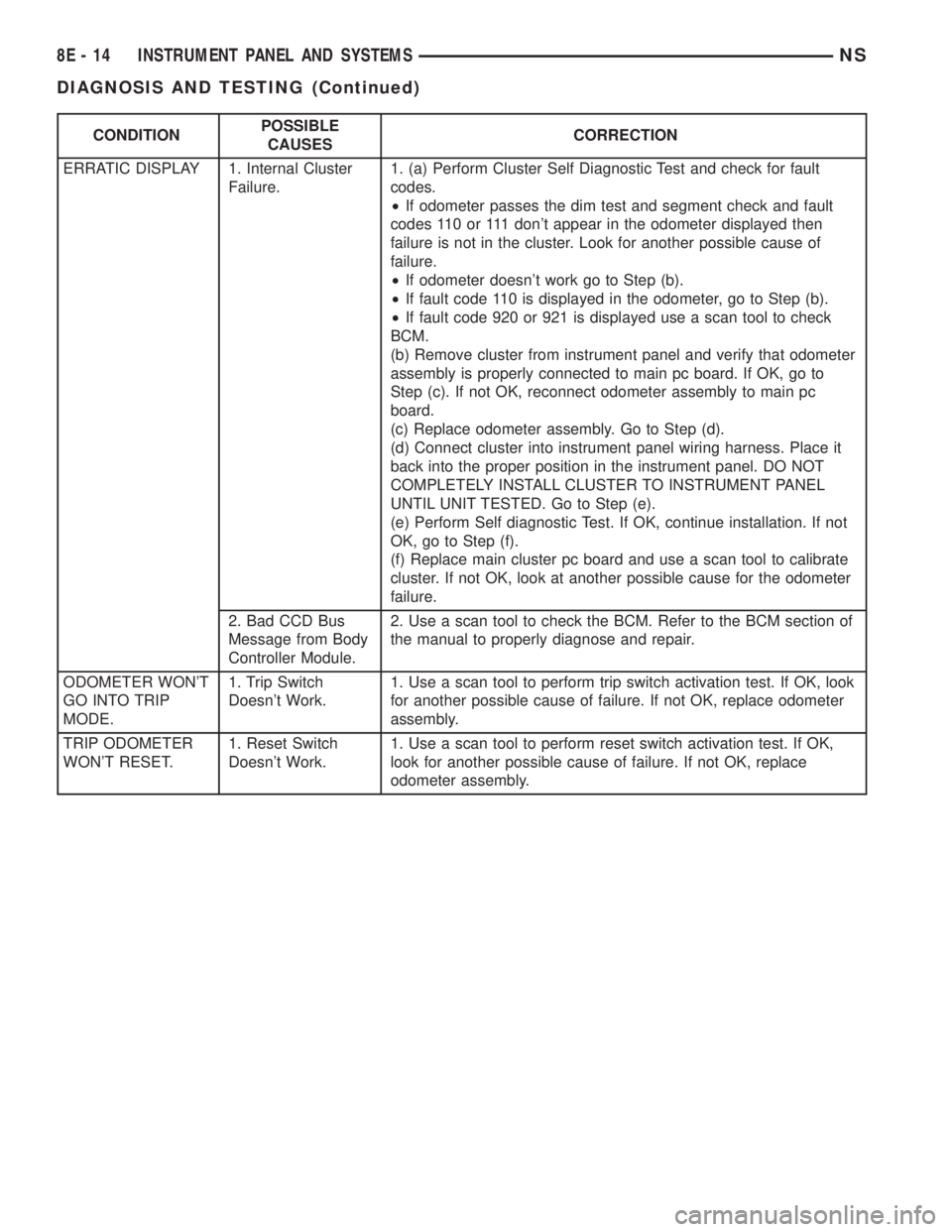
CONDITIONPOSSIBLE
CAUSESCORRECTION
ERRATIC DISPLAY 1. Internal Cluster
Failure.1. (a) Perform Cluster Self Diagnostic Test and check for fault
codes.
²If odometer passes the dim test and segment check and fault
codes 110 or 111 don't appear in the odometer displayed then
failure is not in the cluster. Look for another possible cause of
failure.
²If odometer doesn't work go to Step (b).
²If fault code 110 is displayed in the odometer, go to Step (b).
²If fault code 920 or 921 is displayed use a scan tool to check
BCM.
(b) Remove cluster from instrument panel and verify that odometer
assembly is properly connected to main pc board. If OK, go to
Step (c). If not OK, reconnect odometer assembly to main pc
board.
(c) Replace odometer assembly. Go to Step (d).
(d) Connect cluster into instrument panel wiring harness. Place it
back into the proper position in the instrument panel. DO NOT
COMPLETELY INSTALL CLUSTER TO INSTRUMENT PANEL
UNTIL UNIT TESTED. Go to Step (e).
(e) Perform Self diagnostic Test. If OK, continue installation. If not
OK, go to Step (f).
(f) Replace main cluster pc board and use a scan tool to calibrate
cluster. If not OK, look at another possible cause for the odometer
failure.
2. Bad CCD Bus
Message from Body
Controller Module.2. Use a scan tool to check the BCM. Refer to the BCM section of
the manual to properly diagnose and repair.
ODOMETER WON'T
GO INTO TRIP
MODE.1. Trip Switch
Doesn't Work.1. Use a scan tool to perform trip switch activation test. If OK, look
for another possible cause of failure. If not OK, replace odometer
assembly.
TRIP ODOMETER
WON'T RESET.1. Reset Switch
Doesn't Work.1. Use a scan tool to perform reset switch activation test. If OK,
look for another possible cause of failure. If not OK, replace
odometer assembly.
8E - 14 INSTRUMENT PANEL AND SYSTEMSNS
DIAGNOSIS AND TESTING (Continued)
Page 351 of 1938
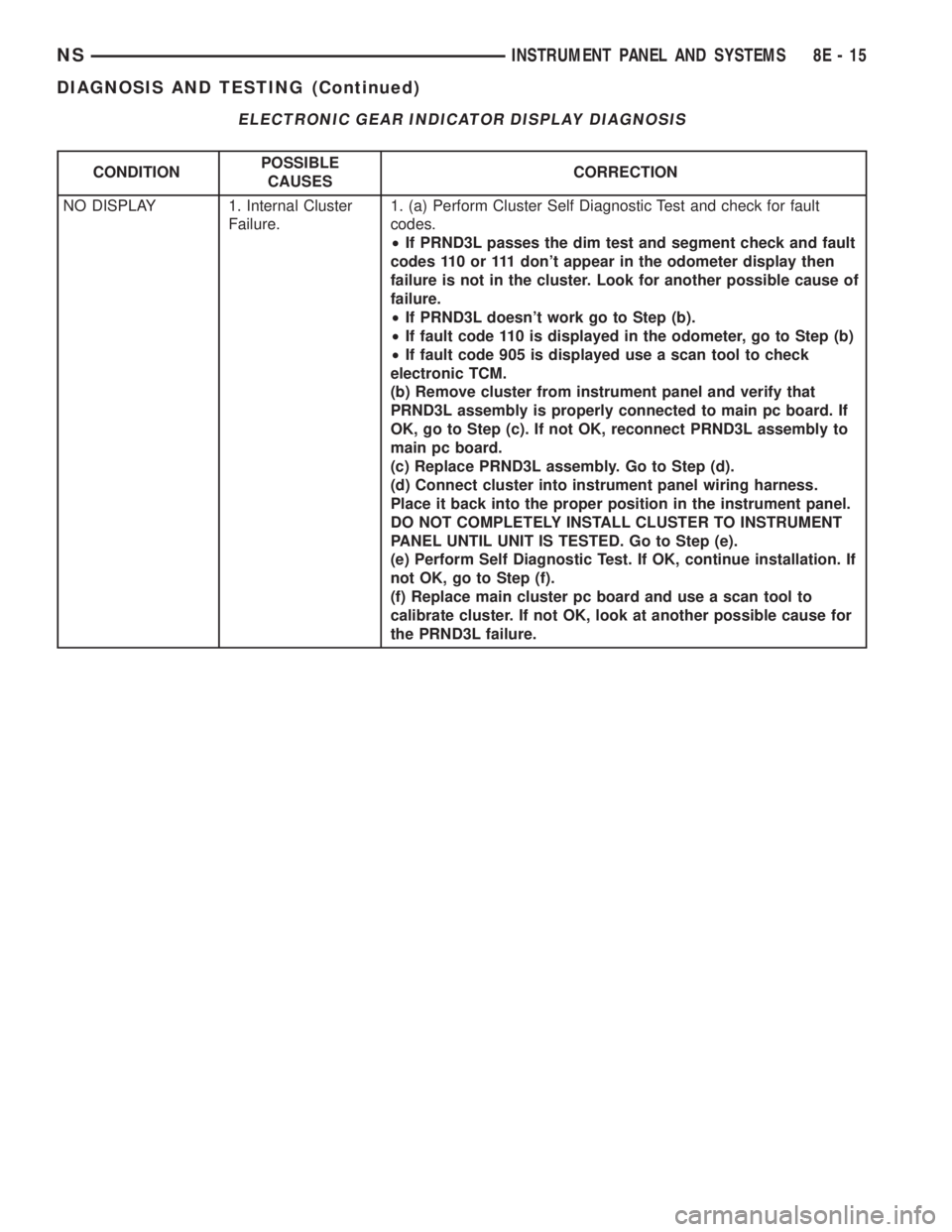
ELECTRONIC GEAR INDICATOR DISPLAY DIAGNOSIS
CONDITIONPOSSIBLE
CAUSESCORRECTION
NO DISPLAY 1. Internal Cluster
Failure.1. (a) Perform Cluster Self Diagnostic Test and check for fault
codes.
²If PRND3L passes the dim test and segment check and fault
codes 110 or 111 don't appear in the odometer display then
failure is not in the cluster. Look for another possible cause of
failure.
²If PRND3L doesn't work go to Step (b).
²If fault code 110 is displayed in the odometer, go to Step (b)
²If fault code 905 is displayed use a scan tool to check
electronic TCM.
(b) Remove cluster from instrument panel and verify that
PRND3L assembly is properly connected to main pc board. If
OK, go to Step (c). If not OK, reconnect PRND3L assembly to
main pc board.
(c) Replace PRND3L assembly. Go to Step (d).
(d) Connect cluster into instrument panel wiring harness.
Place it back into the proper position in the instrument panel.
DO NOT COMPLETELY INSTALL CLUSTER TO INSTRUMENT
PANEL UNTIL UNIT IS TESTED. Go to Step (e).
(e) Perform Self Diagnostic Test. If OK, continue installation. If
not OK, go to Step (f).
(f) Replace main cluster pc board and use a scan tool to
calibrate cluster. If not OK, look at another possible cause for
the PRND3L failure.
NSINSTRUMENT PANEL AND SYSTEMS 8E - 15
DIAGNOSIS AND TESTING (Continued)
Page 352 of 1938
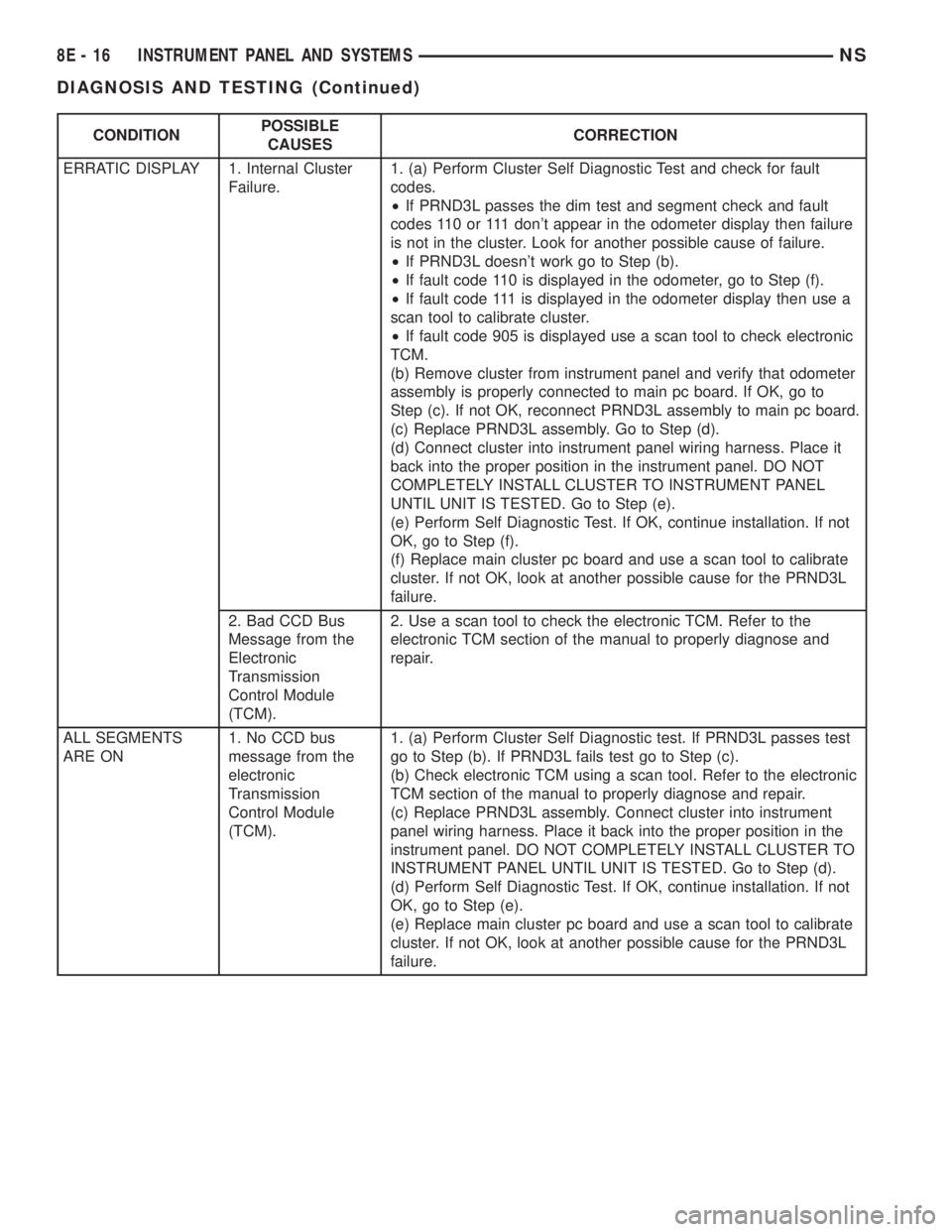
CONDITIONPOSSIBLE
CAUSESCORRECTION
ERRATIC DISPLAY 1. Internal Cluster
Failure.1. (a) Perform Cluster Self Diagnostic Test and check for fault
codes.
²If PRND3L passes the dim test and segment check and fault
codes 110 or 111 don't appear in the odometer display then failure
is not in the cluster. Look for another possible cause of failure.
²If PRND3L doesn't work go to Step (b).
²If fault code 110 is displayed in the odometer, go to Step (f).
²If fault code 111 is displayed in the odometer display then use a
scan tool to calibrate cluster.
²If fault code 905 is displayed use a scan tool to check electronic
TCM.
(b) Remove cluster from instrument panel and verify that odometer
assembly is properly connected to main pc board. If OK, go to
Step (c). If not OK, reconnect PRND3L assembly to main pc board.
(c) Replace PRND3L assembly. Go to Step (d).
(d) Connect cluster into instrument panel wiring harness. Place it
back into the proper position in the instrument panel. DO NOT
COMPLETELY INSTALL CLUSTER TO INSTRUMENT PANEL
UNTIL UNIT IS TESTED. Go to Step (e).
(e) Perform Self Diagnostic Test. If OK, continue installation. If not
OK, go to Step (f).
(f) Replace main cluster pc board and use a scan tool to calibrate
cluster. If not OK, look at another possible cause for the PRND3L
failure.
2. Bad CCD Bus
Message from the
Electronic
Transmission
Control Module
(TCM).2. Use a scan tool to check the electronic TCM. Refer to the
electronic TCM section of the manual to properly diagnose and
repair.
ALL SEGMENTS
ARE ON1. No CCD bus
message from the
electronic
Transmission
Control Module
(TCM).1. (a) Perform Cluster Self Diagnostic test. If PRND3L passes test
go to Step (b). If PRND3L fails test go to Step (c).
(b) Check electronic TCM using a scan tool. Refer to the electronic
TCM section of the manual to properly diagnose and repair.
(c) Replace PRND3L assembly. Connect cluster into instrument
panel wiring harness. Place it back into the proper position in the
instrument panel. DO NOT COMPLETELY INSTALL CLUSTER TO
INSTRUMENT PANEL UNTIL UNIT IS TESTED. Go to Step (d).
(d) Perform Self Diagnostic Test. If OK, continue installation. If not
OK, go to Step (e).
(e) Replace main cluster pc board and use a scan tool to calibrate
cluster. If not OK, look at another possible cause for the PRND3L
failure.
8E - 16 INSTRUMENT PANEL AND SYSTEMSNS
DIAGNOSIS AND TESTING (Continued)
Page 355 of 1938
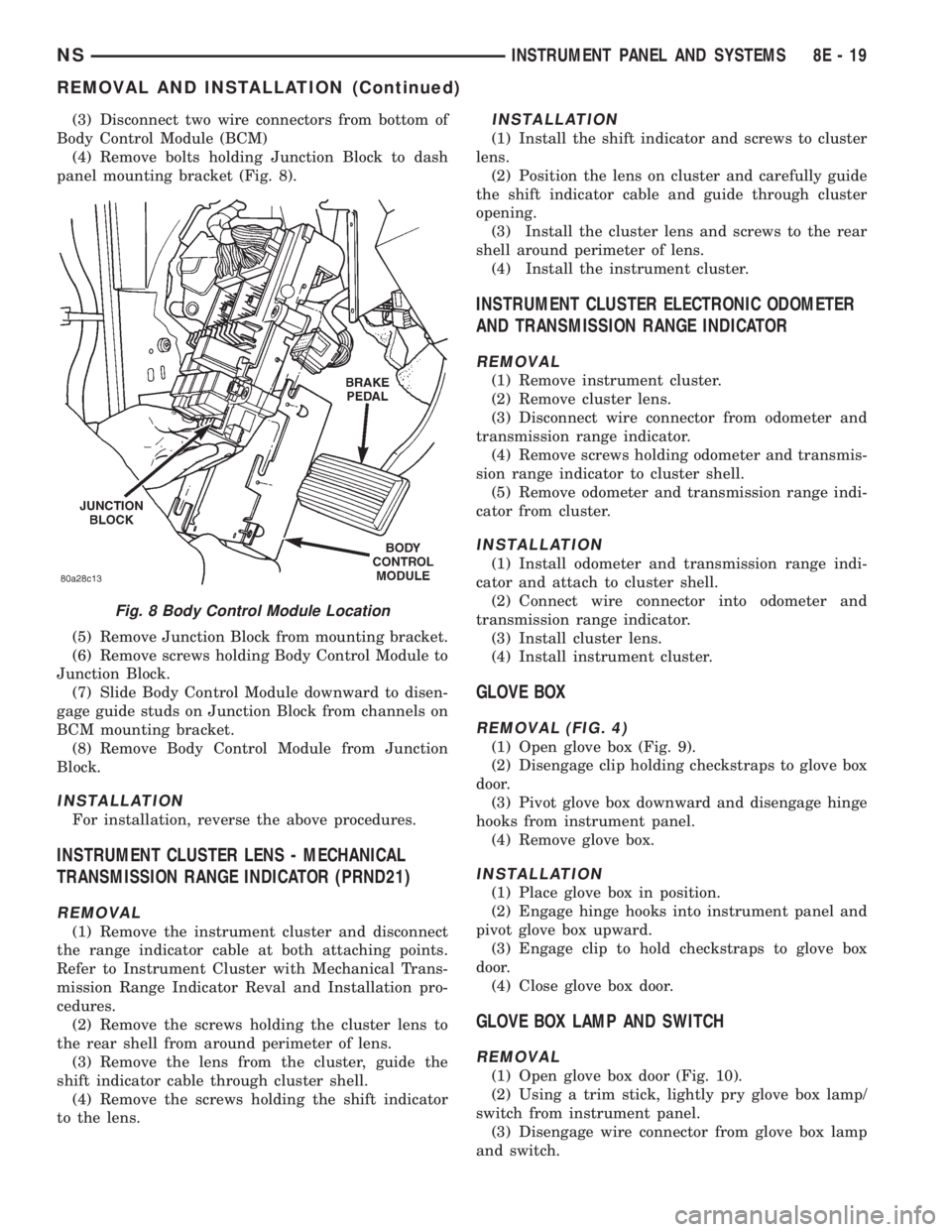
(3) Disconnect two wire connectors from bottom of
Body Control Module (BCM)
(4) Remove bolts holding Junction Block to dash
panel mounting bracket (Fig. 8).
(5) Remove Junction Block from mounting bracket.
(6) Remove screws holding Body Control Module to
Junction Block.
(7) Slide Body Control Module downward to disen-
gage guide studs on Junction Block from channels on
BCM mounting bracket.
(8) Remove Body Control Module from Junction
Block.
INSTALLATION
For installation, reverse the above procedures.
INSTRUMENT CLUSTER LENS - MECHANICAL
TRANSMISSION RANGE INDICATOR (PRND21)
REMOVAL
(1) Remove the instrument cluster and disconnect
the range indicator cable at both attaching points.
Refer to Instrument Cluster with Mechanical Trans-
mission Range Indicator Reval and Installation pro-
cedures.
(2) Remove the screws holding the cluster lens to
the rear shell from around perimeter of lens.
(3) Remove the lens from the cluster, guide the
shift indicator cable through cluster shell.
(4) Remove the screws holding the shift indicator
to the lens.
INSTALLATION
(1) Install the shift indicator and screws to cluster
lens.
(2) Position the lens on cluster and carefully guide
the shift indicator cable and guide through cluster
opening.
(3) Install the cluster lens and screws to the rear
shell around perimeter of lens.
(4) Install the instrument cluster.
INSTRUMENT CLUSTER ELECTRONIC ODOMETER
AND TRANSMISSION RANGE INDICATOR
REMOVAL
(1) Remove instrument cluster.
(2) Remove cluster lens.
(3) Disconnect wire connector from odometer and
transmission range indicator.
(4) Remove screws holding odometer and transmis-
sion range indicator to cluster shell.
(5) Remove odometer and transmission range indi-
cator from cluster.
INSTALLATION
(1) Install odometer and transmission range indi-
cator and attach to cluster shell.
(2) Connect wire connector into odometer and
transmission range indicator.
(3) Install cluster lens.
(4) Install instrument cluster.
GLOVE BOX
REMOVAL (FIG. 4)
(1) Open glove box (Fig. 9).
(2) Disengage clip holding checkstraps to glove box
door.
(3) Pivot glove box downward and disengage hinge
hooks from instrument panel.
(4) Remove glove box.
INSTALLATION
(1) Place glove box in position.
(2) Engage hinge hooks into instrument panel and
pivot glove box upward.
(3) Engage clip to hold checkstraps to glove box
door.
(4) Close glove box door.
GLOVE BOX LAMP AND SWITCH
REMOVAL
(1) Open glove box door (Fig. 10).
(2) Using a trim stick, lightly pry glove box lamp/
switch from instrument panel.
(3) Disengage wire connector from glove box lamp
and switch.
Fig. 8 Body Control Module Location
NSINSTRUMENT PANEL AND SYSTEMS 8E - 19
REMOVAL AND INSTALLATION (Continued)
Page 374 of 1938
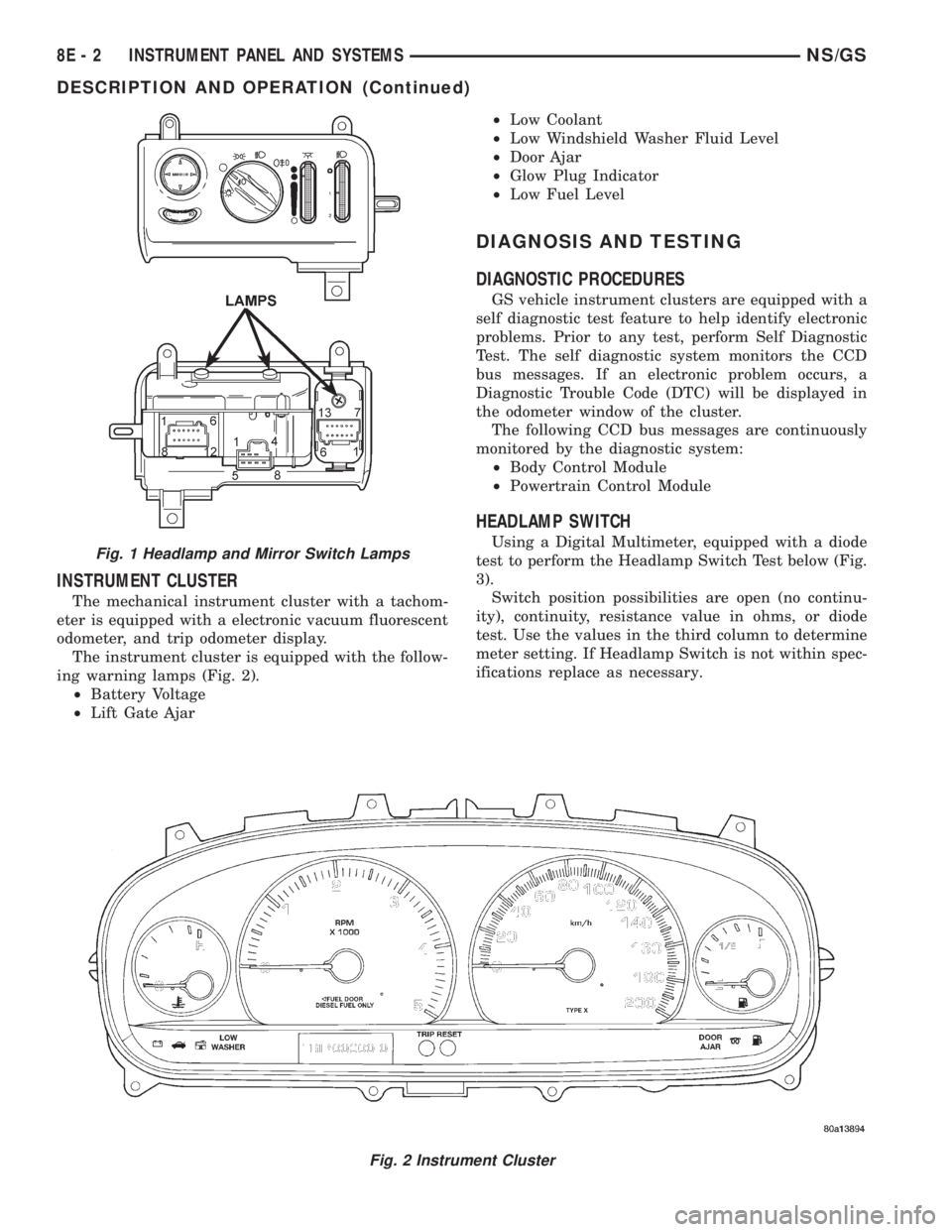
INSTRUMENT CLUSTER
The mechanical instrument cluster with a tachom-
eter is equipped with a electronic vacuum fluorescent
odometer, and trip odometer display.
The instrument cluster is equipped with the follow-
ing warning lamps (Fig. 2).
²Battery Voltage
²Lift Gate Ajar²Low Coolant
²Low Windshield Washer Fluid Level
²Door Ajar
²Glow Plug Indicator
²Low Fuel Level
DIAGNOSIS AND TESTING
DIAGNOSTIC PROCEDURES
GS vehicle instrument clusters are equipped with a
self diagnostic test feature to help identify electronic
problems. Prior to any test, perform Self Diagnostic
Test. The self diagnostic system monitors the CCD
bus messages. If an electronic problem occurs, a
Diagnostic Trouble Code (DTC) will be displayed in
the odometer window of the cluster.
The following CCD bus messages are continuously
monitored by the diagnostic system:
²Body Control Module
²Powertrain Control Module
HEADLAMP SWITCH
Using a Digital Multimeter, equipped with a diode
test to perform the Headlamp Switch Test below (Fig.
3).
Switch position possibilities are open (no continu-
ity), continuity, resistance value in ohms, or diode
test. Use the values in the third column to determine
meter setting. If Headlamp Switch is not within spec-
ifications replace as necessary.
Fig. 2 Instrument Cluster
Fig. 1 Headlamp and Mirror Switch Lamps
8E - 2 INSTRUMENT PANEL AND SYSTEMSNS/GS
DESCRIPTION AND OPERATION (Continued)
Page 375 of 1938
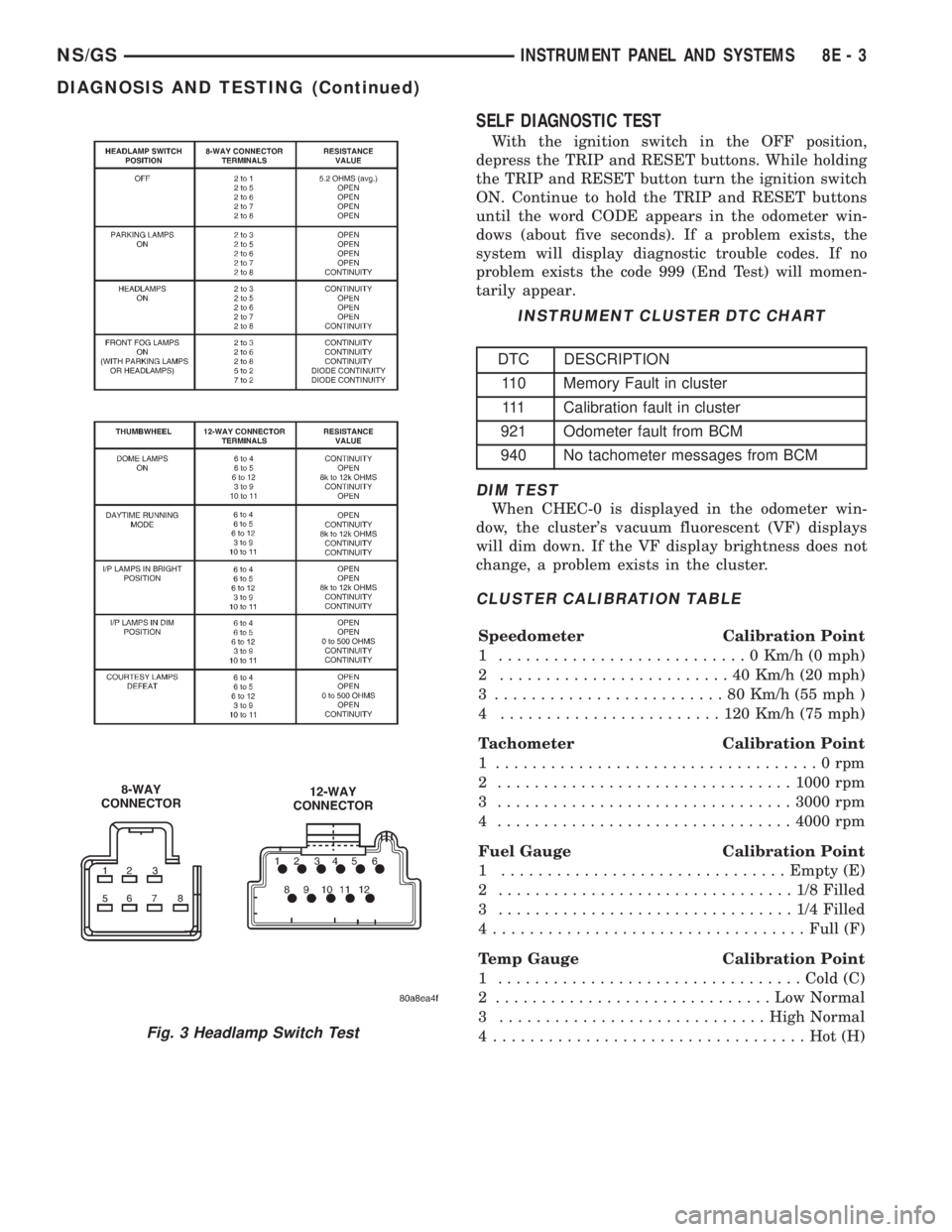
SELF DIAGNOSTIC TEST
With the ignition switch in the OFF position,
depress the TRIP and RESET buttons. While holding
the TRIP and RESET button turn the ignition switch
ON. Continue to hold the TRIP and RESET buttons
until the word CODE appears in the odometer win-
dows (about five seconds). If a problem exists, the
system will display diagnostic trouble codes. If no
problem exists the code 999 (End Test) will momen-
tarily appear.
DIM TEST
When CHEC-0 is displayed in the odometer win-
dow, the cluster's vacuum fluorescent (VF) displays
will dim down. If the VF display brightness does not
change, a problem exists in the cluster.
CLUSTER CALIBRATION TABLE
Speedometer Calibration Point
1 ...........................0Km/h (0 mph)
2 .........................40Km/h (20 mph)
3 .........................80Km/h (55 mph )
4 ........................120Km/h (75 mph)
Tachometer Calibration Point
1 ...................................0rpm
2 ................................1000 rpm
3 ................................3000 rpm
4 ................................4000 rpm
Fuel Gauge Calibration Point
1 ...............................Empty (E)
2 ................................1/8Filled
3 ................................1/4Filled
4..................................Full (F)
Temp Gauge Calibration Point
1 .................................Cold (C)
2 ..............................LowNormal
3 .............................High Normal
4 ..................................Hot(H)
Fig. 3 Headlamp Switch Test
INSTRUMENT CLUSTER DTC CHART
DTC DESCRIPTION
110 Memory Fault in cluster
111 Calibration fault in cluster
921 Odometer fault from BCM
940 No tachometer messages from BCM
NS/GSINSTRUMENT PANEL AND SYSTEMS 8E - 3
DIAGNOSIS AND TESTING (Continued)
Page 376 of 1938
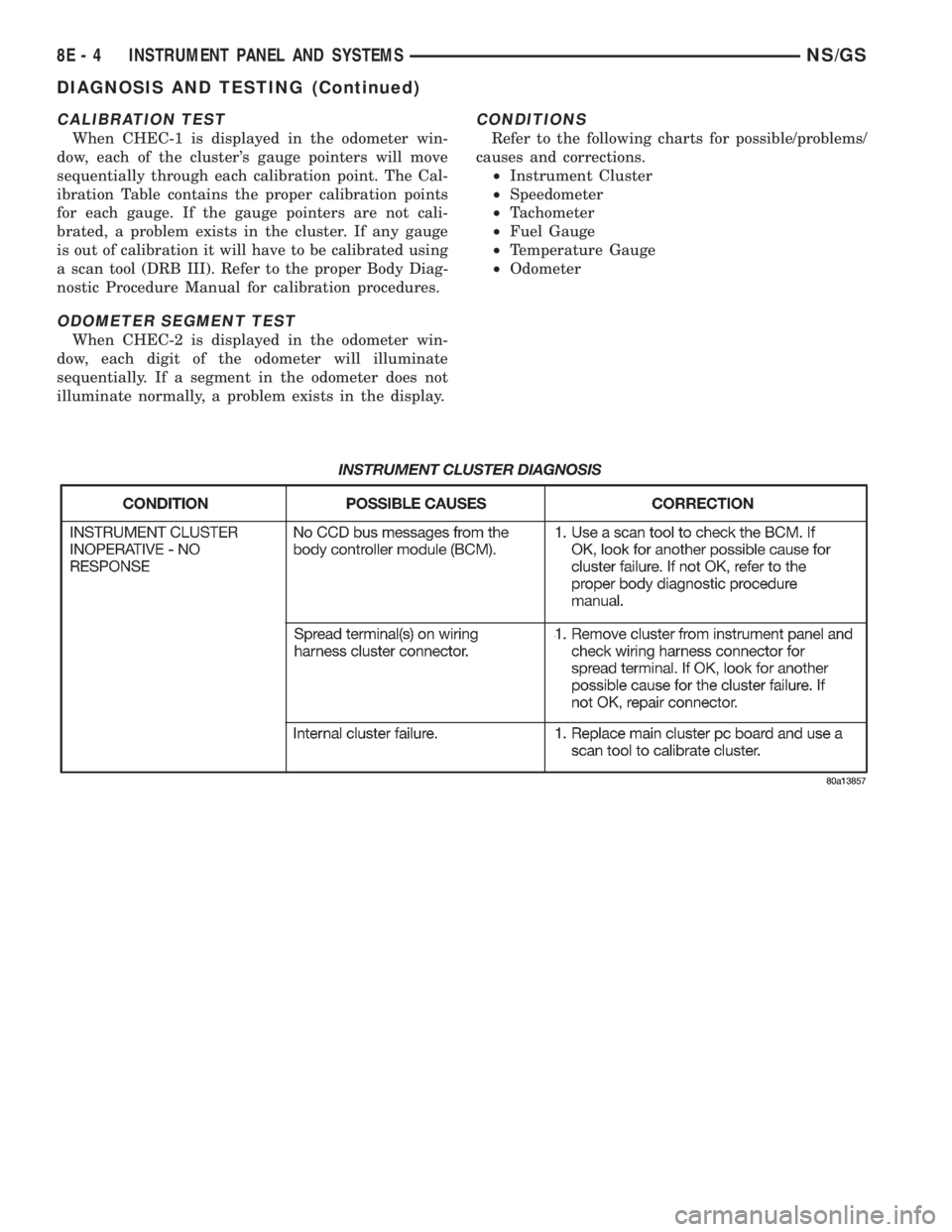
CALIBRATION TEST
When CHEC-1 is displayed in the odometer win-
dow, each of the cluster's gauge pointers will move
sequentially through each calibration point. The Cal-
ibration Table contains the proper calibration points
for each gauge. If the gauge pointers are not cali-
brated, a problem exists in the cluster. If any gauge
is out of calibration it will have to be calibrated using
a scan tool (DRB III). Refer to the proper Body Diag-
nostic Procedure Manual for calibration procedures.
ODOMETER SEGMENT TEST
When CHEC-2 is displayed in the odometer win-
dow, each digit of the odometer will illuminate
sequentially. If a segment in the odometer does not
illuminate normally, a problem exists in the display.
CONDITIONS
Refer to the following charts for possible/problems/
causes and corrections.
²Instrument Cluster
²Speedometer
²Tachometer
²Fuel Gauge
²Temperature Gauge
²Odometer
8E - 4 INSTRUMENT PANEL AND SYSTEMSNS/GS
DIAGNOSIS AND TESTING (Continued)