check engine Citroen CX 1974 1.G Repair Manual
[x] Cancel search | Manufacturer: CITROEN, Model Year: 1974, Model line: CX, Model: Citroen CX 1974 1.GPages: 394
Page 241 of 394
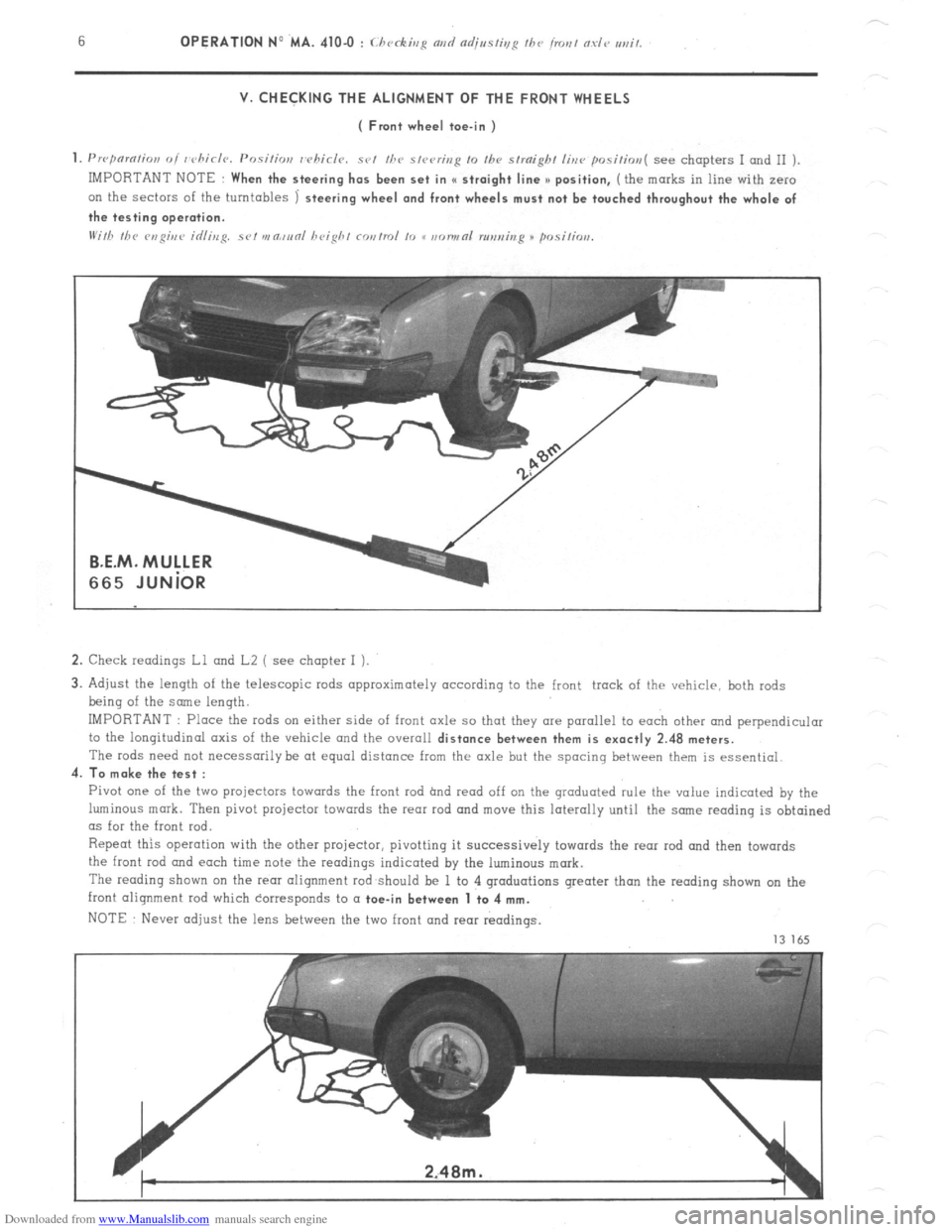
Downloaded from www.Manualslib.com manuals search engine V. CHECKING THE ALIGNMENT OF THE FRONT WHEELS
( Front wheel toe-in )
1. Prrpnmtion oi whirlr~. Positior,
whirls. set /he s,rering 10 Ihv straight line positim~( see chapters I and II )
IMPORTANT NOTE
When the steering has been set in I( straight line >) position, (the marks in line with zero
on the sectors of the turntables
1 steering wheel and front wheels must not be touched throughout the whole of
the testing operation.
2. Check readings Ll and L2 ( see chapter I ).
3. Adjust the length of the telescopic rods approximately according to the front track of the vehicle, both rods
being of the some length.
IMPORTANT : Place the rods on either side of front axle so that they are parallel to each other and perpendicular
to the longitudinal axis of the vehicle and the overall
distance between them is exactly 2.48 meters.
The rods need not necessarily be at equal distance from the axle but the spacing between them is essential.
4.
To make the test :
Pivot one of the two projectors towards the front rod hnd read off on the graduated rule thr value indicated by the
luminous mark. Then pivot projector towards the rear rod and move this laterally until the snne reading is obtained
as for the front rod.
Repeat this operation with the other projector, pivotting it successively towards the rear rod and then towards
the front
rod and each time note the readings indicated by the luminous mark.
The reading shown on the rem alignment rod should be 1 to 4 graduations greater than the reading shown on the
front alignment rod which corresponds to a
toe-in between 1 to 4 mm.
NOTE Never adjust the lens between the two front and rear readings.
13 165
Page 242 of 394
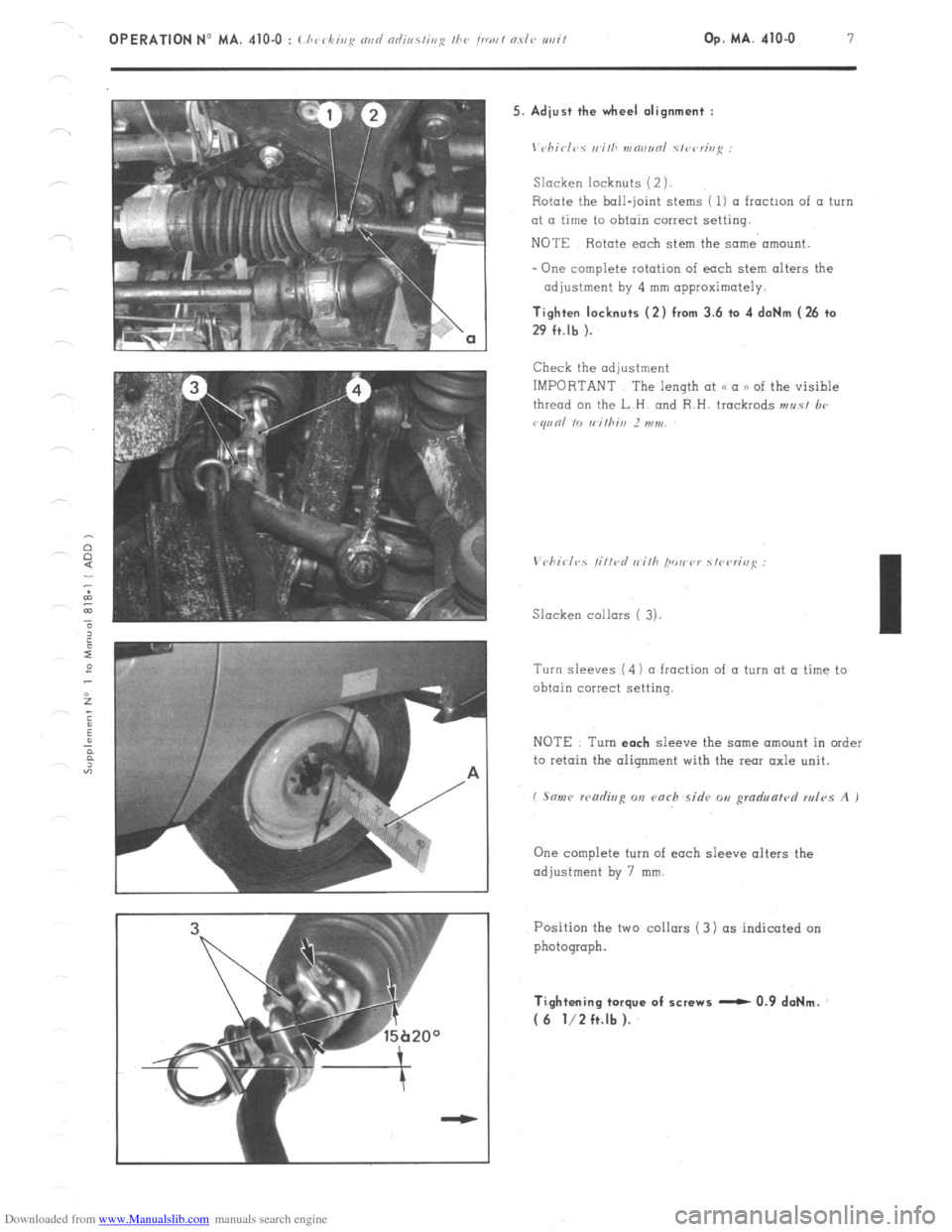
Downloaded from www.Manualslib.com manuals search engine OPERATION No MA. 410-O : I hvr-6iq n,,d od;n.s/isg /hc /~,a, nrle uei/ Op. MA. 410-O 7
’ 15b20° 5. Adiust the wheel alignment :
\‘chirl‘,s II ilh mw,r,ol s/wrh,i: :
Slacken locknuts (2 ).
Rotate the ball-joint stems ( 1) a froctmn of a turn
at a time to obtain correct setting.
NOTE Rotate each stem the same’ amount.
- One complete rotation of each stem alters the
adjustment by 4 mm approximately. Tighten locknuts (2) from 3.6 to 4 daNm (26 to
29 ft.lb ).
Check the adjustment
IMPORTANT The length at (< a n of the visible
thread on the L.H. and R.H. trackrods ,,,r,s/ lx,
vq,,nl IO rrithin 2 ,,,7,,,
Slacken collars ( 3).
Turn sleeves (4) ~1 fraction of a turn at a time to
obtain correct setting.
NOTE Turn each
sleeve the same amount in order
to retain the oiiqnment with the rear axle unit.
I Son<, wcidisp on varh sidv o,, gmd,,lrrn/r,d rules A I
One complete turn of each sleeve alters the
adjustment by 7 mm.
Position the two collars ( 3) (IS indicated on
photograph. Ti.ghtening torque of screws - 0.9 daNm.
( 6 l/2 ft.lb ).
Page 243 of 394
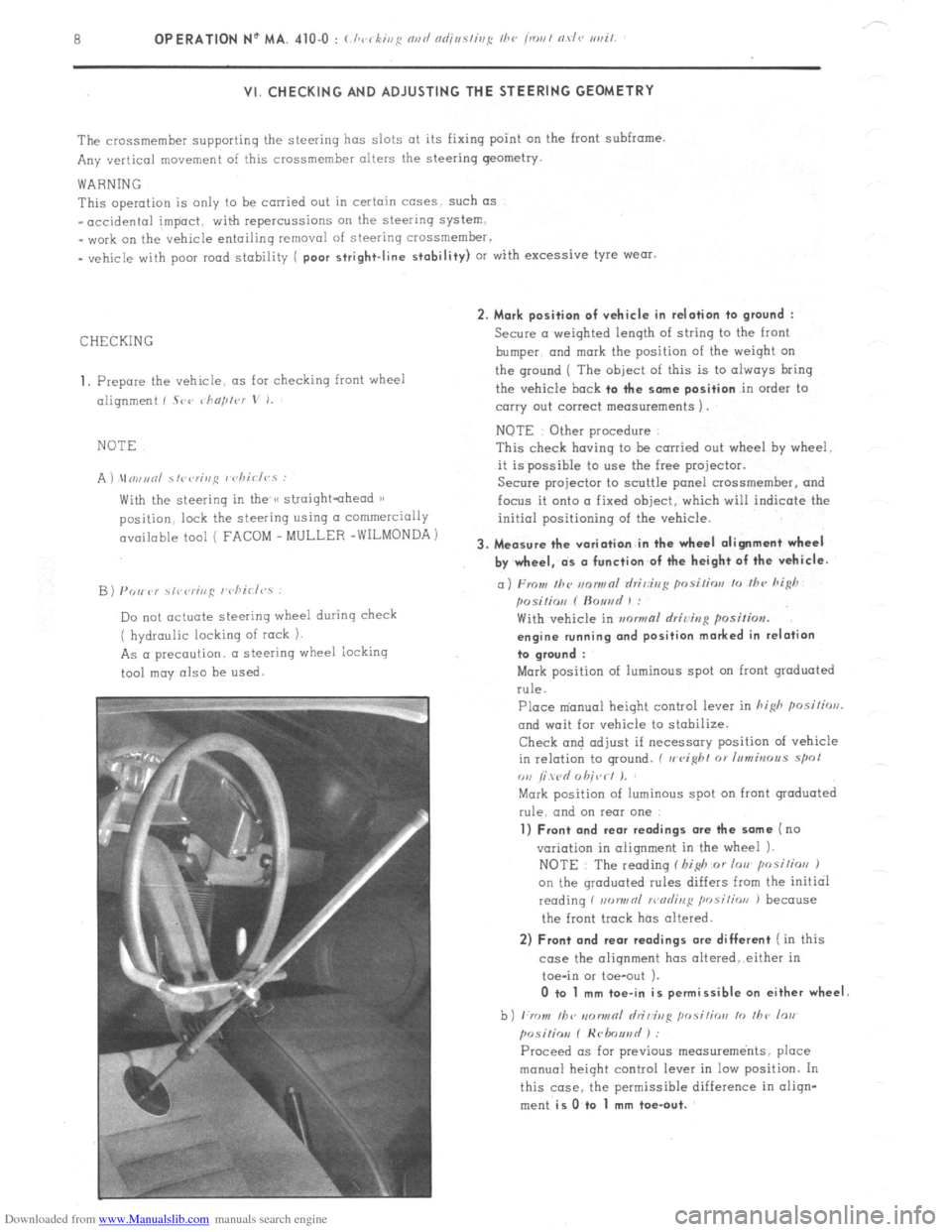
Downloaded from www.Manualslib.com manuals search engine a OPERATION N’ MA. 410-O : (./~rrkiq N,,I/
VI. CHECKING AND ADJUSTING THE STEERING GEOMETRY
The crossmember supporting the steering has slots at its fixing point on the front subframe.
Any vertical movement of this crossmember alters the steering geometry.
WARNING
This operation is only to
be carried out in certain ccxses such as
-accidental impact, with repercussions on the steering system.
-work on the vehicle entoiling removal of steering crossmember.
- vehicle with poor
road stability ( p oar stright-line stability) 01 with excessive tyre weor.
CHECKING
1, Prepare the vehicle. as for checking front wheel
alignment ( Srr ~ho/,lvr
V I.
NOTE
A ) \In,,unl ~fi~<,r;,,~ I chiclvs :
With the steering in the /< straightahead 1)
position. lock the steering using CI commercially
available tool ( FACOM _ MULLER -WILMONDA)
B) PO,, P)’ \,r,rr;ng r’cliirl<,.s :
Do not actuate steering wheel during check
( hydraulic locking of rock 1.
As a precaution. a steering wheel iocking
tool may also be
used. 2. Mark position of vehicle in relation to
ground :
Secure a weighted length of string to the front
bumper. and
mark the position of the weiqht on
the ground ( The
object of this is to always bring
the vehicle
bock to the some position in order to
carry out correct measurements 1.
NOTE Other procedure
This check having to be carried out wheel hy wheel.
it is possible to use the free projector.
Secure projector to scuttle panel crossmemher, and
focus it onto a fixed object, which will indicate the
initial positioning of the vehicle.
3. Measure the variation in the wheel alignment wheel
by wheel, ds o function of the height of the vehicle.
a) From Ihc m~nwnl rlri,:ir,g posi/ior, lo /hc hi@
posilio,, f ftouad 1 :
With vehicle in mwmal rlriving position.
engine running ond position marked in relation
to groond :
Mark position of luminous spot on front graduated
rule.
Place m’anual height control lever in hi&
posilirrrl.
and wait for vehicle to stabilize.
Check and adjust if necessary position of vehicle
in relation to ground. ( II
eight 01 Inmbrous spol
ou /i wd 0 hit,< I J.
Mark position of luminous spot on front graduated
rule. and on rear one
1) Front and rear readings ore the some (no
variation in alignment in the wheel 1.
NOTE : The reading f I,i$ or lorr posilios J
on the qroduated rules differs from the initial
reading f non,,nl >r,nrlinl:
position J because
the front track has altered.
2) Front and rear readings ore different ( in this
case the alignment has oltered,.either in
toe-in or toe-out ).
0 to 1 mm toe-in is permissible on either wheel
b) ,:rr ,,I, /bv IIDIINRI hi&g ,,osi,;orr lo ,I,<, lo,,
posiliov f Hrlmuad ) :
Proceed OS for previous measurements, place
manual height control lever in low position. In
this case. the permissible difference in oliqn-
ment
is O.to 1 mm toe-out.
Page 244 of 394
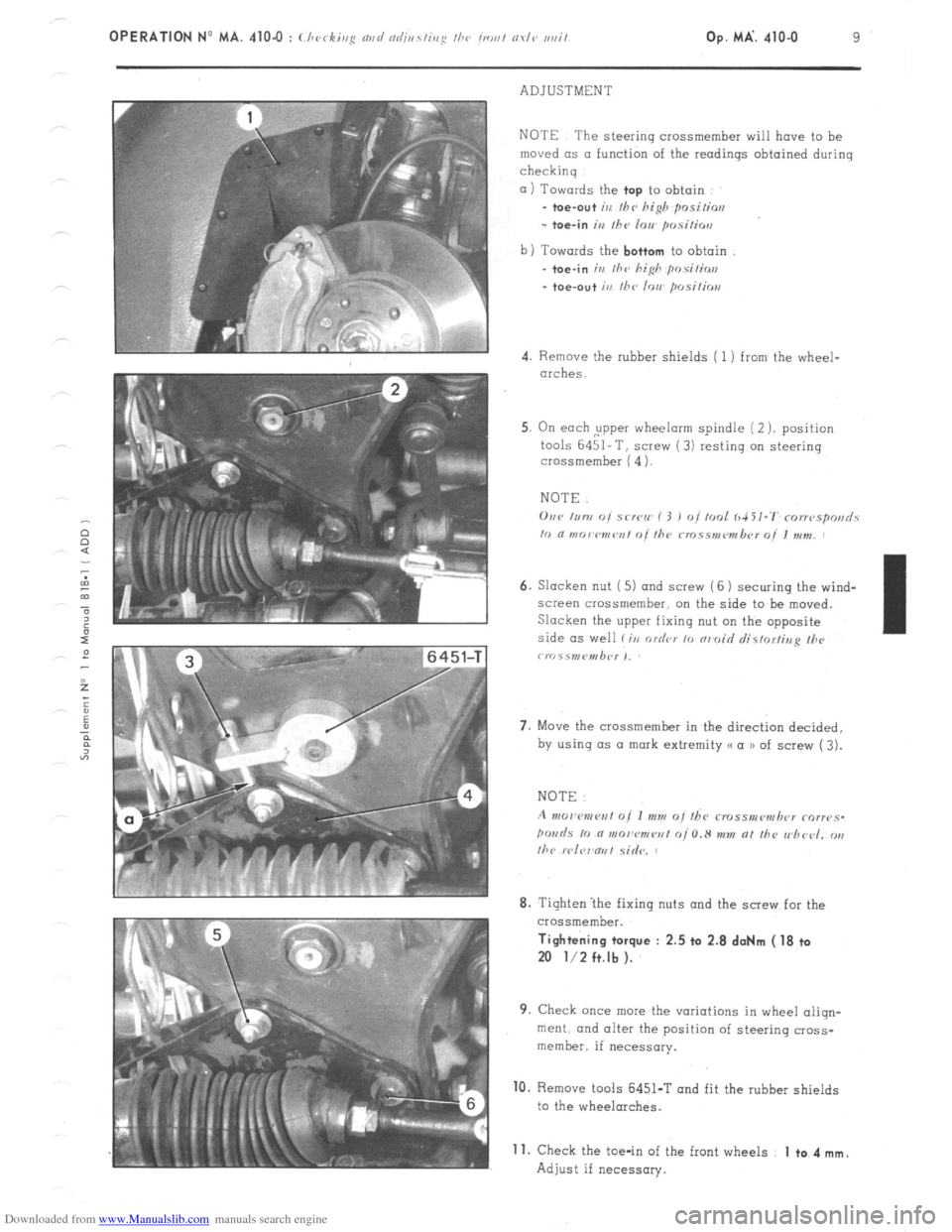
Downloaded from www.Manualslib.com manuals search engine OPERATION No MA. 4104 : (./ , k’ 1
ADJUSTMENT
NOTE The steering crossmember will have to be
moved (IS a function of the readings obtained during
checkinq
01) Towards the top to
obtain
_ toe-out ir, Ihe hish positim
- toe-in irr the 10~ psitios
b) Towards the bottom
to obtain
.
toe-in in Ihr hi& posilins
- toe-out iu fhc IOU posilios
4. Remove the rubber shields ( 1 ) from the wheel-
arches.
5. On each ,upper wheelorm spindle (2 ). position
tools 6451-T, screw (3) resting on steering
crossmember ( 4 1.
NOTE.
6. Slacken nut ( 5) and screw (6 1 securing the wind-
screen crossmember. on the side to be moved.
Slacken the upper fixing nut on the opposite
side as well li,r order 10 nrmoid rlistorfina II><,
crr~.ss,nP”,b<~r ,,
7. Move the crossmember in the direct& decided,
by using (1s a mark extremity (( a u of screw ( 3).
8. Tighten ‘the fixing nuts and the screw for the
crossmember. Tightening torque : 2.5 ta 2.8 doNm ( 18 ta
20 l/2 ft.lb ).
9. Check once mew the variations in wheel aliqn-
merit. and alter the position of steering cross-
member. if necessary. 10.
Remove tools 6451-T and fit the rubber shields
to the wheelarches.
Adjust if necessary. 11.
Check the toe-in of the front wheels 1 to 4 mm.
Page 250 of 394
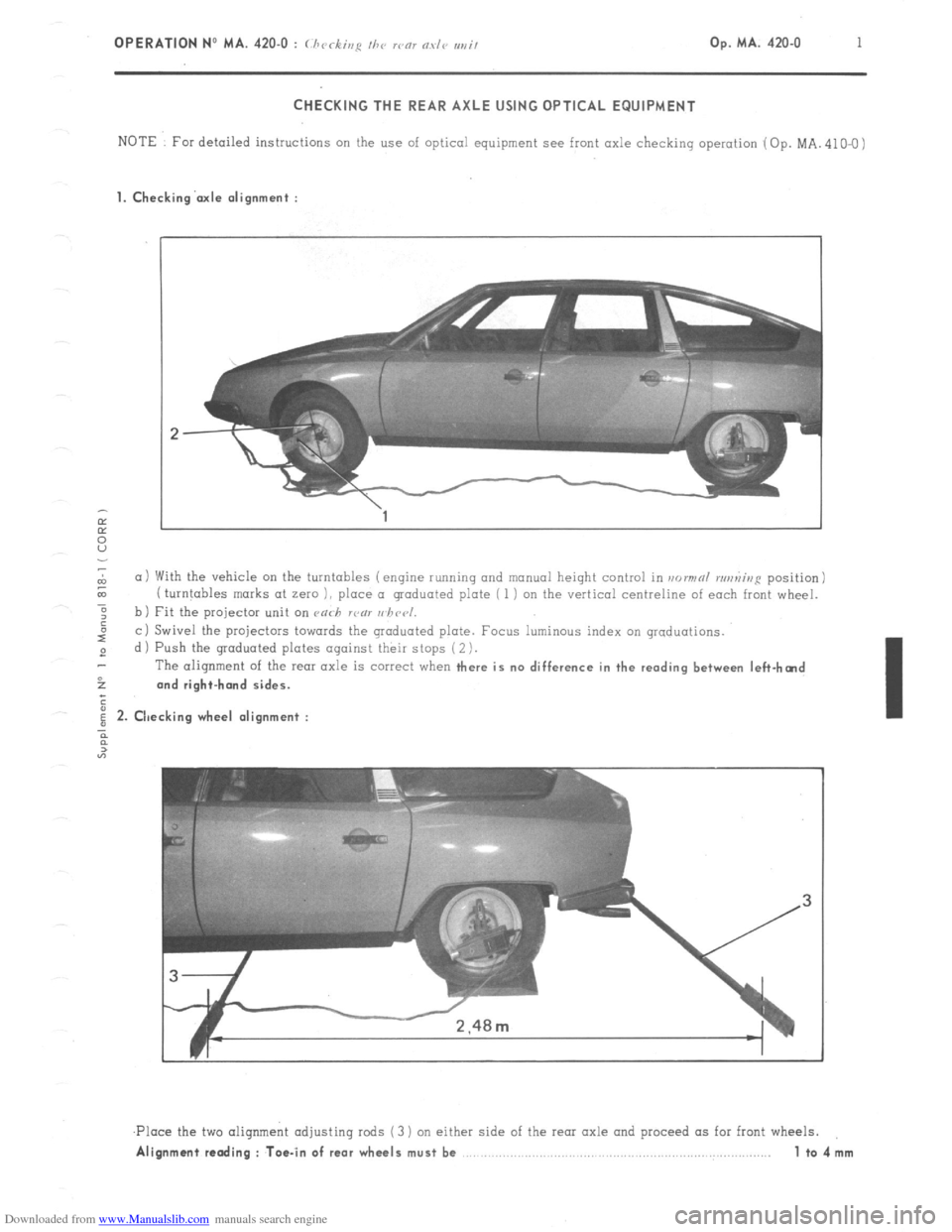
Downloaded from www.Manualslib.com manuals search engine Op. MA. 420.0 1
CHECKING THE REAR AXLE USING OPTICAL EQUIPMENT
NOTE For detailed instructions on the use of optical equipment see front axle checking operation (Op. MA. 410-O)
1. Checking’axle alignment :
L
(11 With the vehicle on the turntables (engine running and manual height control in normnl runniup position)
& ( turntables marks at zero 1, place a graduated plate ( 1 i on the vertical centreline of each front wheel.
-6
: b) Fit the projector unit on ca<-h rcnl uhccl.
I”
c i Swivel the projectors towards the graduated plate. Focus luminous index on graduations.
2 d ) Push the graduated plates against their stops ( 2 ).
The alignment of the
rear axle is correct when there is no difference in the reading between left-hcnd
52 and right-hand sides.
;
i 2. Checking wheel alignment :
n
2
“7
,Ploce the two aliqnmeht adjusting rods (3 ) on either side of the rear axle and proceed as for front wheels.
Alignment reading : Toe-in of rear wheels must be 1 to4mm
Page 251 of 394
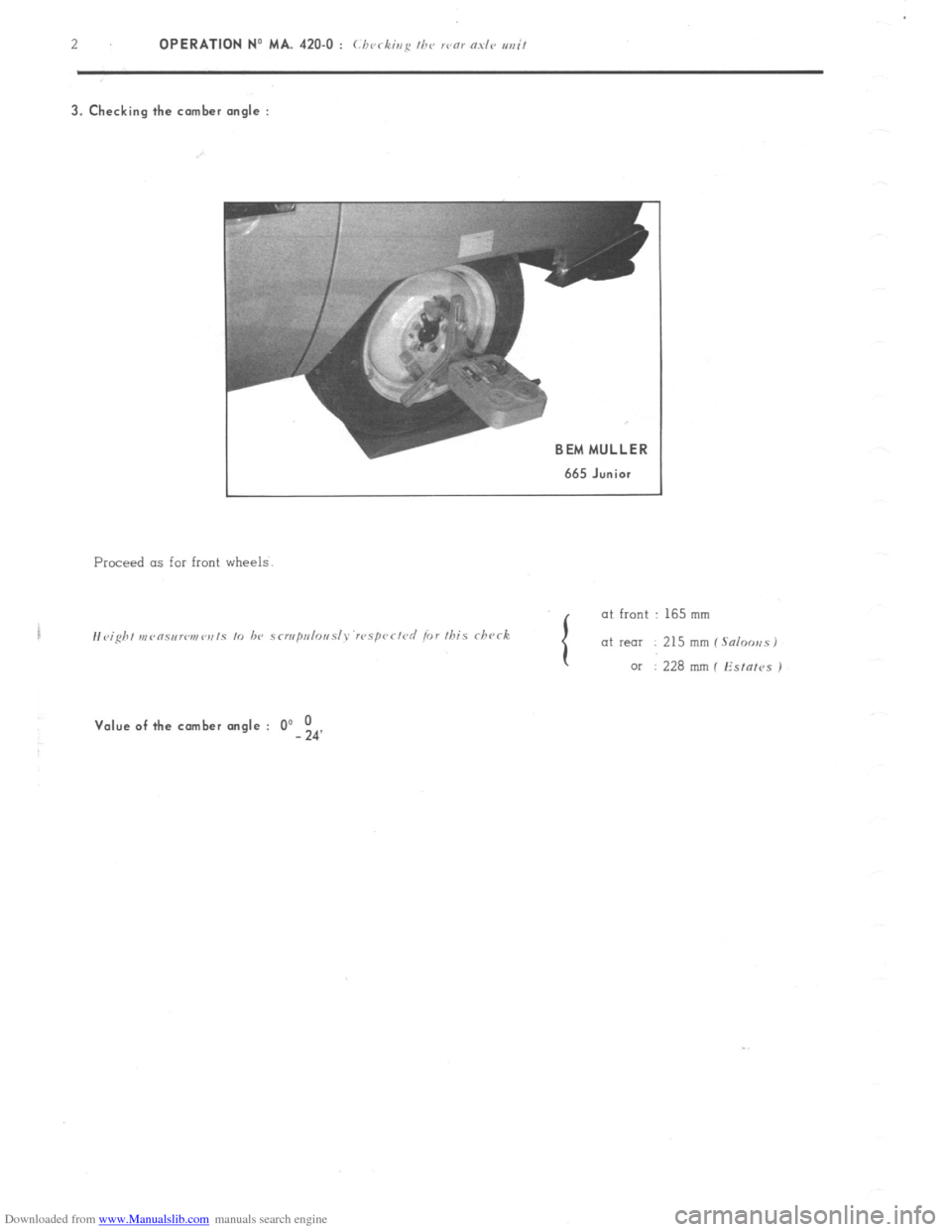
Downloaded from www.Manualslib.com manuals search engine 2 OPERATION No MA. 420.0 : (:h ’ k’ j I/ cc ,,I:, >
BEM MULLER
665 Junior
Proceed as for front wheels
at front : 165 mm
He;@/ ,),~ns,,r‘,,,,~,,,,s lo be srn,p,,lmosly ‘rcs,wrlcd Ior /his rhrck
at rem : 215 mm ~Saloo,rsJ
a : 228
mm f Estatus J V&e of the camber angle : On
-024’
Page 257 of 394
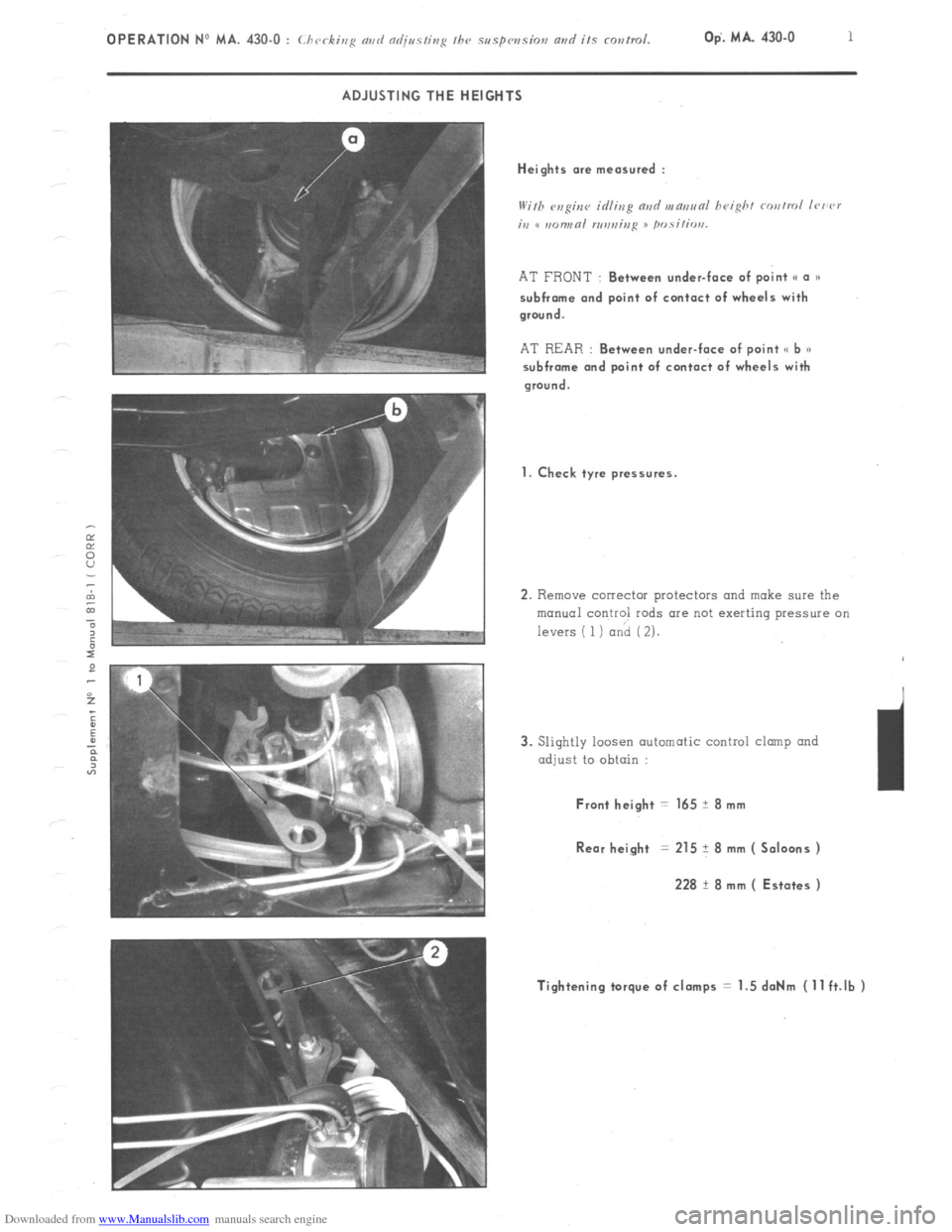
Downloaded from www.Manualslib.com manuals search engine OPERATION No MA. 430-O : Checking md ndjusting the suspcusion and its control. 06. MA. 430-O i
ADJUSTING THE HEIGHTS
AT FRONT : Between under-face of point (c o ))
subfrome ond point of contoct of wheels with
ground.
AT REAR : Between under-face of point <( b a)
subfrome ond point of contact of wheels with
ground.
1. Check tyre pressures.
2. Remove corrector protectors and make sure the
manual control rods are not exerting pressure on
levers ( 1) and ( 2).
3. Slightly loosen automatic control clump and
adjust to obtain :
3
Front height = 165 ? 8 mm
Rear height = 215 ? 8 mm ( Saloons )
228 t 8 mm ( Estates )
Tightening torque of clomps = 1.5 doNm (11 ft.lb )
Page 258 of 394
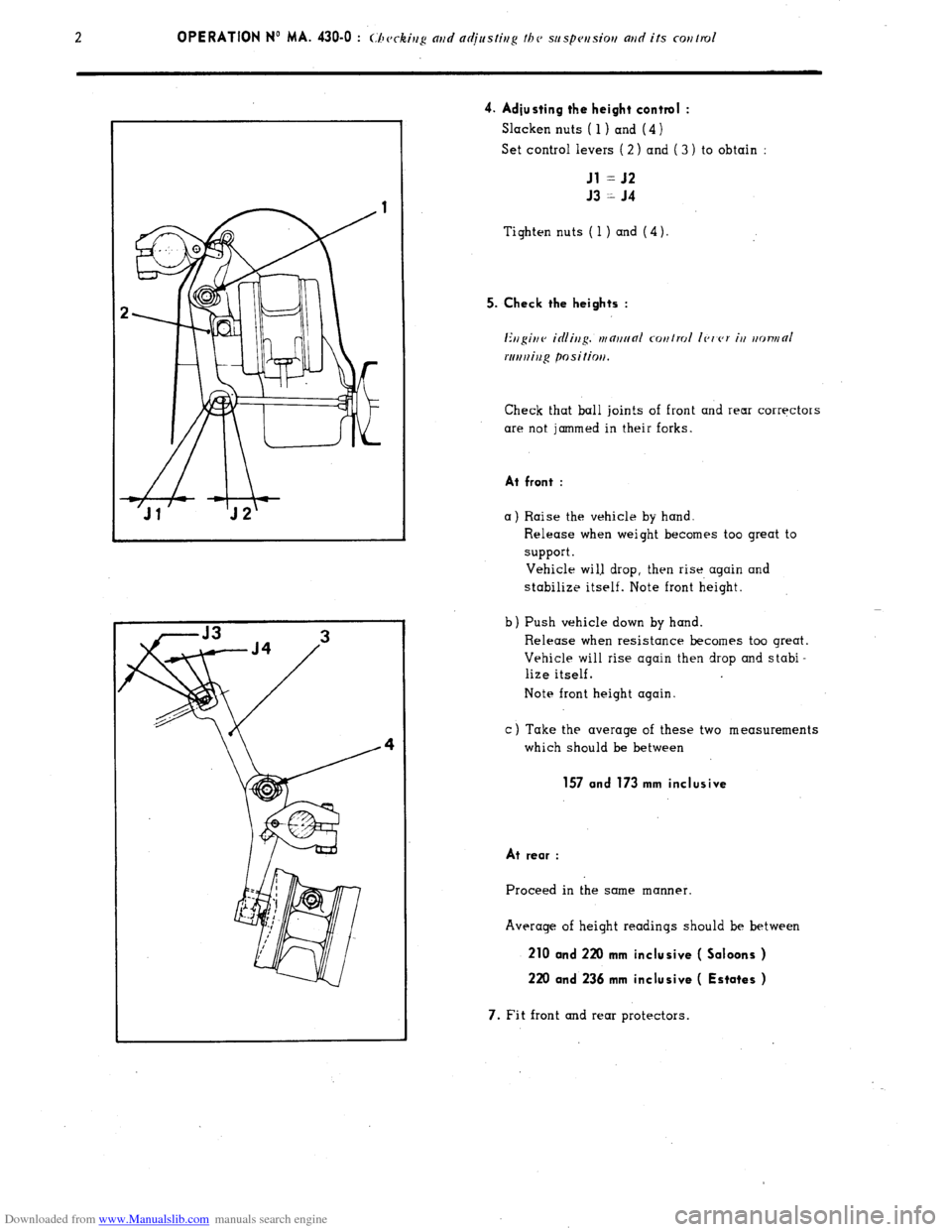
Downloaded from www.Manualslib.com manuals search engine 2 OPERATION No MA. 430-O : ~hwki~zg nrtd nrijustittg the suspwrsiott ntd its cotttrol
4. Adjusting the height control :
Slacken nuts ( 1) and (4 )
Set control levers ( 2 ) and ( 3 ) to obtain :
Jl = J2
J3 = J4
Tighten nuts ( 1 ) and (4).
5. Check the heights :
Ertgittv icilittg. tttnttt~nl cotttrol Ic,t’c,r itt ttotvttO/
rtrrtttiug positiott.
Check that ball join!s of front and rear corrqctors
are not jammed in their forks.
At front :
a) Raise the vehicle by hand.
b Release when weight becomes too great to
support.
Vehicle wi1.l drop, then rise again and
stabilize itself. Note front height.
Push vehicle down by hand
Release when resistance becomes too great.
Vehicle will rise again then drop and stabi-
lize itself.
Note front height again.
c) Take the average of these two measurements
which should be between
157 and 173 mm inclusive
At rear :
Proceed in the same manner.
Average of height readings should be between
210 and 220 mm inclusive ( Saloons )
220 and 236 mm inclusive ( Estates )
7. Fit front and rear protectors.
Page 280 of 394
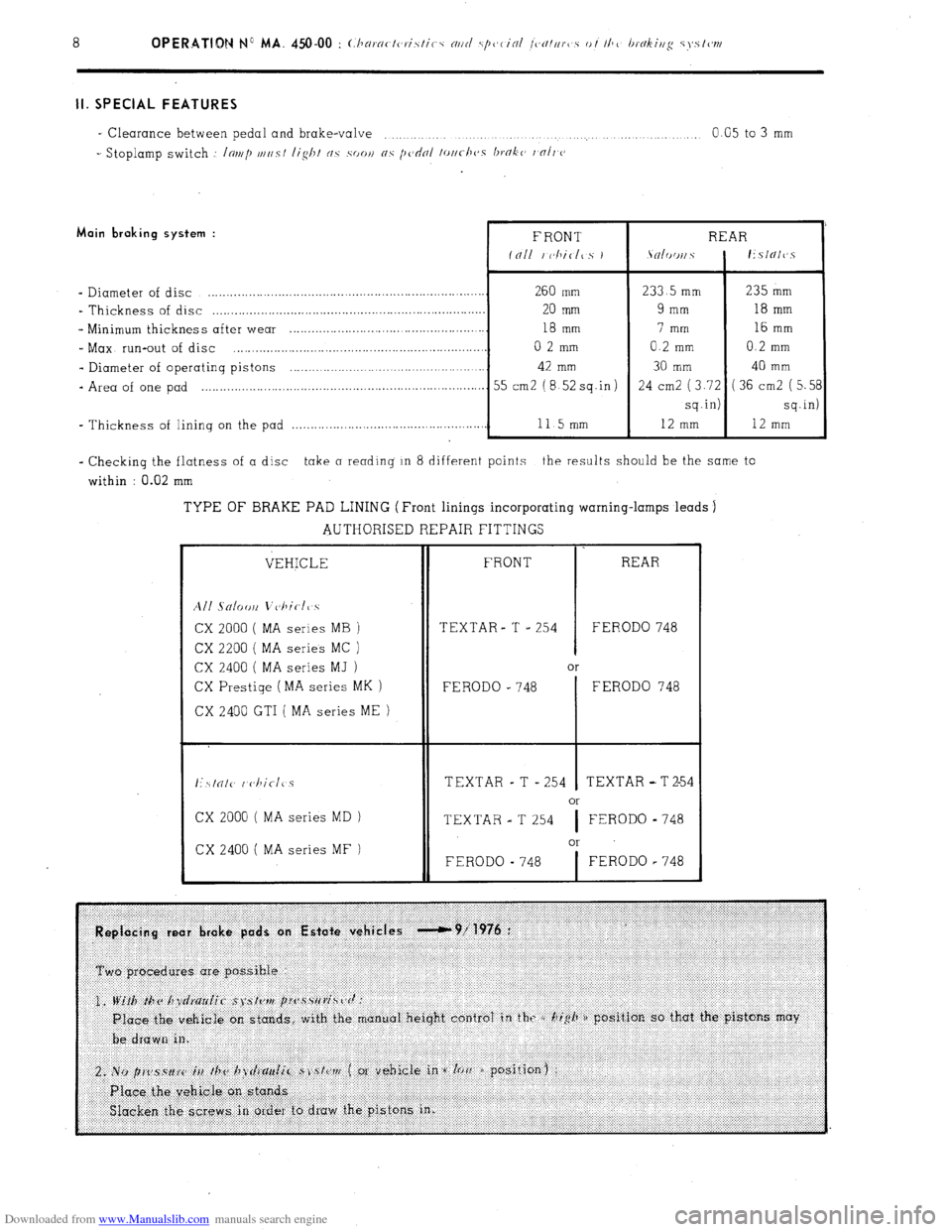
Downloaded from www.Manualslib.com manuals search engine II. SPECIAL FEATURES
- Clearance between pedal and brake-valve
” ..: 0.05 to 3 mm
_ Stoplamp switch ,: Inal/) VII/S/ lislli c/c .soo,~ 05 [I(‘~~II /~//c-/~c,s IJTO~(~ /,fl// (J Main braking system :
- Diameter of disc .......................................................................... 260 mm
- Thickness of disc .........................................................................
20 mm
s Minimum thickness after wear .................................................... 18 mm
_ Max run-out of disc ...................................................................
0 2 mm
- Diameter of operatinq pistons ....................................................
42 mm
- Area of one pad ............................................................................
55 cm2 (8 52sq.in)
- Thickness of lining on the pad .,,_.,..,_.__.._.._,....,.......................... 115mm
233 5 mm 235 mm
9 mm 18 mm
7 mm 16 mm
0.2 mm 0 2 mm
30 mm 40 mm
24 cm2 (3.72 (36cm2 (5.5
sq.in) sq.in
12 mm
12 mm
- Checking the flatness of a disc take a reading in 8 different points the results should be the same to
within : 0.02 mm
TYPE OF BRAKE PAD LINING (Front linings incorporating warning-lamps leads
j
AUTHORISED REPAIR FITTINGS
VEHICLE
All Snlow L’c~l,ir-ll 5
CX 2000
( MA series MB )
CX 2200 ( MA series MC )
CX 2400 ( MA series MJ )
CX Prestiqe (MA series MK )
CX 2400 GTI ( MA series ME )
CX 2000 ( MA series MD )
CX 2400 ( MA series MF )
8
1
FRONT REAR
TEXTAR- T .= 254 FERODO 748
or
FERODO e 748
I FERODO 748
TEXTAR - T - 254 1 TEXTAR -T2-54
or
TEXTAR - T 254
I FERODO - 748
or
FERODO - 748
I FERODO r 748
Page 282 of 394
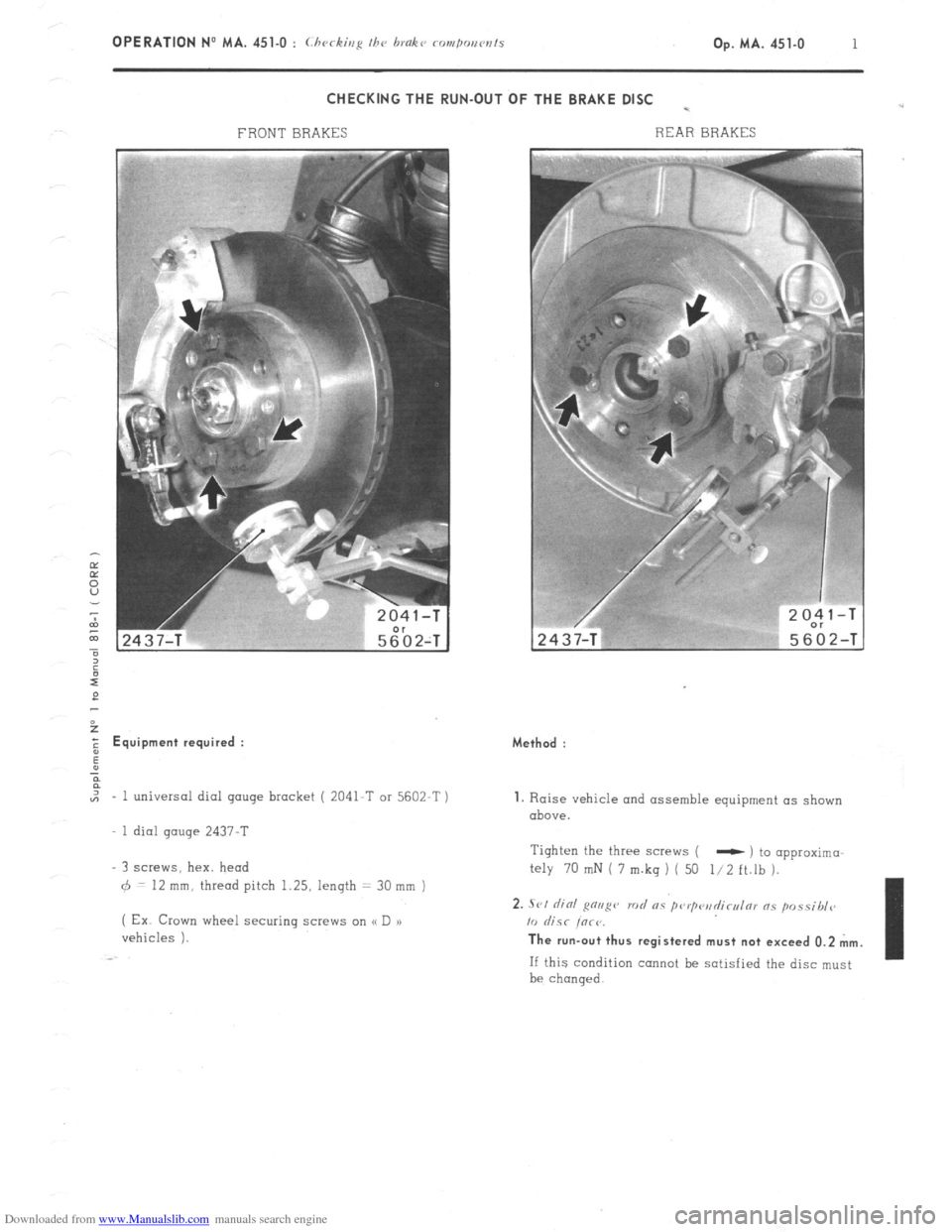
Downloaded from www.Manualslib.com manuals search engine OPERATION No MA. 451-O : Uwckirrg the hrflkv rov,~o,rrnts Op. MA. 451.0 1
CHECKING THE RUN-OUT OF THE BRAKE DISC -
FRONT BRAKES REAR BRAKES 2
E Equipment required :
,,, - 1 universal dial gauge bracket ( 2041-T or 5602-T )
1 dial gauge 2437-T
3 screws, hex. head
6 = 12 mm, thread pitch 1.25, length = 30 mm )
( Ex Crown wheel securing screw on (< D a)
vehicles ). Method :
1. Raise vehicle and assemble equipment as shown
above.
Tighten the three screws (
- ) to opproximo
My 70 mN i 7 m.kq ) ( 50 l/2 ft.lh ).
2. .Sl,l did g”“g” rod RS pwp<‘il~cl,l171 ns p”ssibl<~
10 &SC iorr. The run-out thus registered must not exceed 0.2 mm.
If this condition cannot be satisfied the disc must
be chanqed.