Citroen CX 1982 1.G Workshop Manual
Manufacturer: CITROEN, Model Year: 1982, Model line: CX, Model: Citroen CX 1982 1.GPages: 394
Page 281 of 394
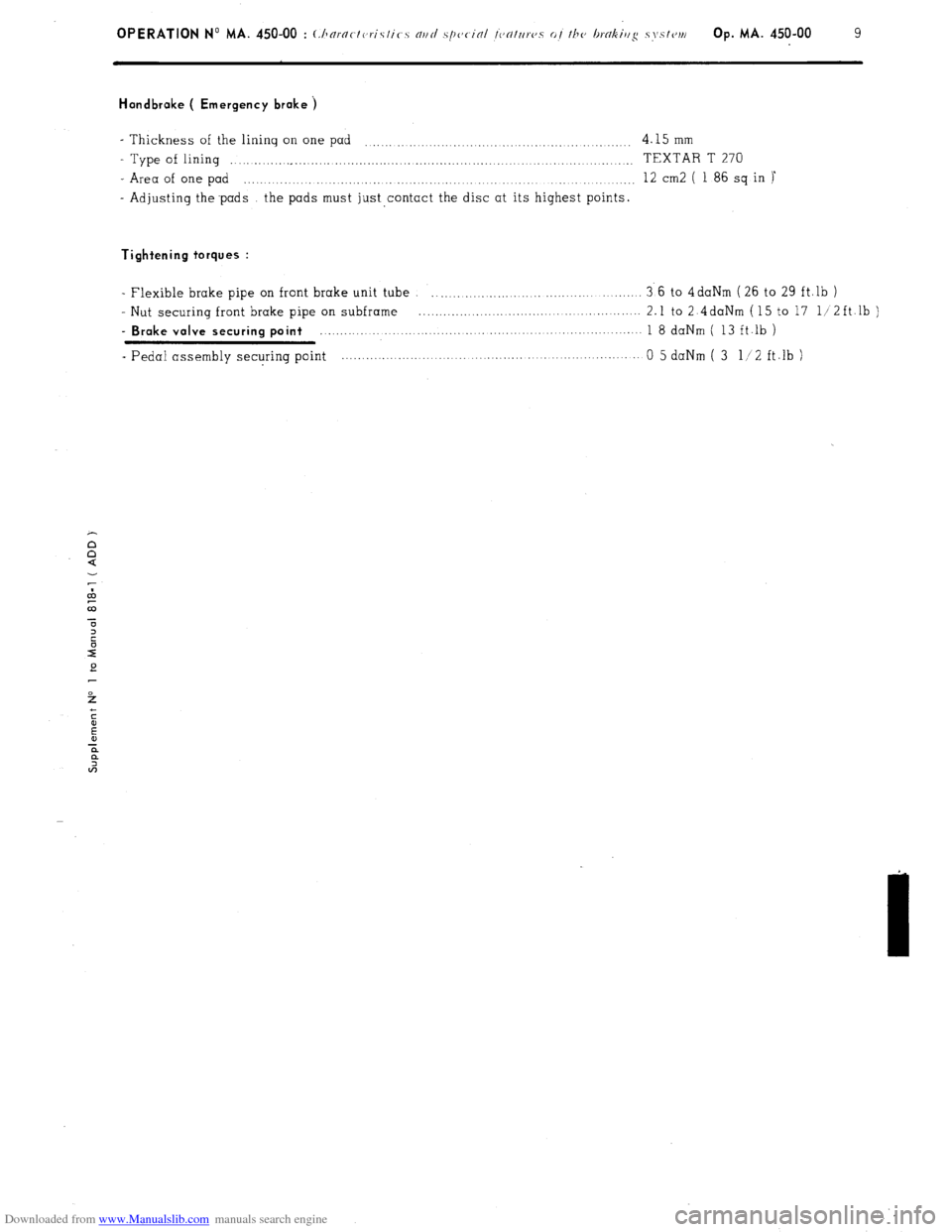
Downloaded from www.Manualslib.com manuals search engine OPERATION No MA. 450-00 : (:/~ornc.t(,ris/i(- c/r/d ,S/ICJC inl /c,c//r~rc,s ot the brcrkillg s~‘.stc~rt~ Op. MA. 450-00 9
Handbroke ( Emergency broke )
- Thickness of the lininq on one pad
4.15 mm _...... .._.......... _.. .,..........
- Type of lining .__............................._....._._..... .._.... .._.. .._.
TEXTAR T 270
- Area of one pad
._..
12 cm2 ( 1 86 sq in )’
- Adjusting the -pads the pads must just contact the disc at its highest points.
Tightening torques :
- Flexible brake pipe on front brake unit tube .............. ..... ....... ........... ........ 3 6 to 4daNm (26 to 29 ft.lb )
- Nut securing front brake pipe on subframe .................................................
2.1 to 2 4daNm (15 to 17 1/2ft.lb )
- Brake valve securing point .................. .............................. ........... ........ 1 8 daNm ( 13 ft.lb )
. Pedal assembly securing point .....................
...... ..................................
0 5 daNm ( 3 l/2 ft.lb )
Page 282 of 394
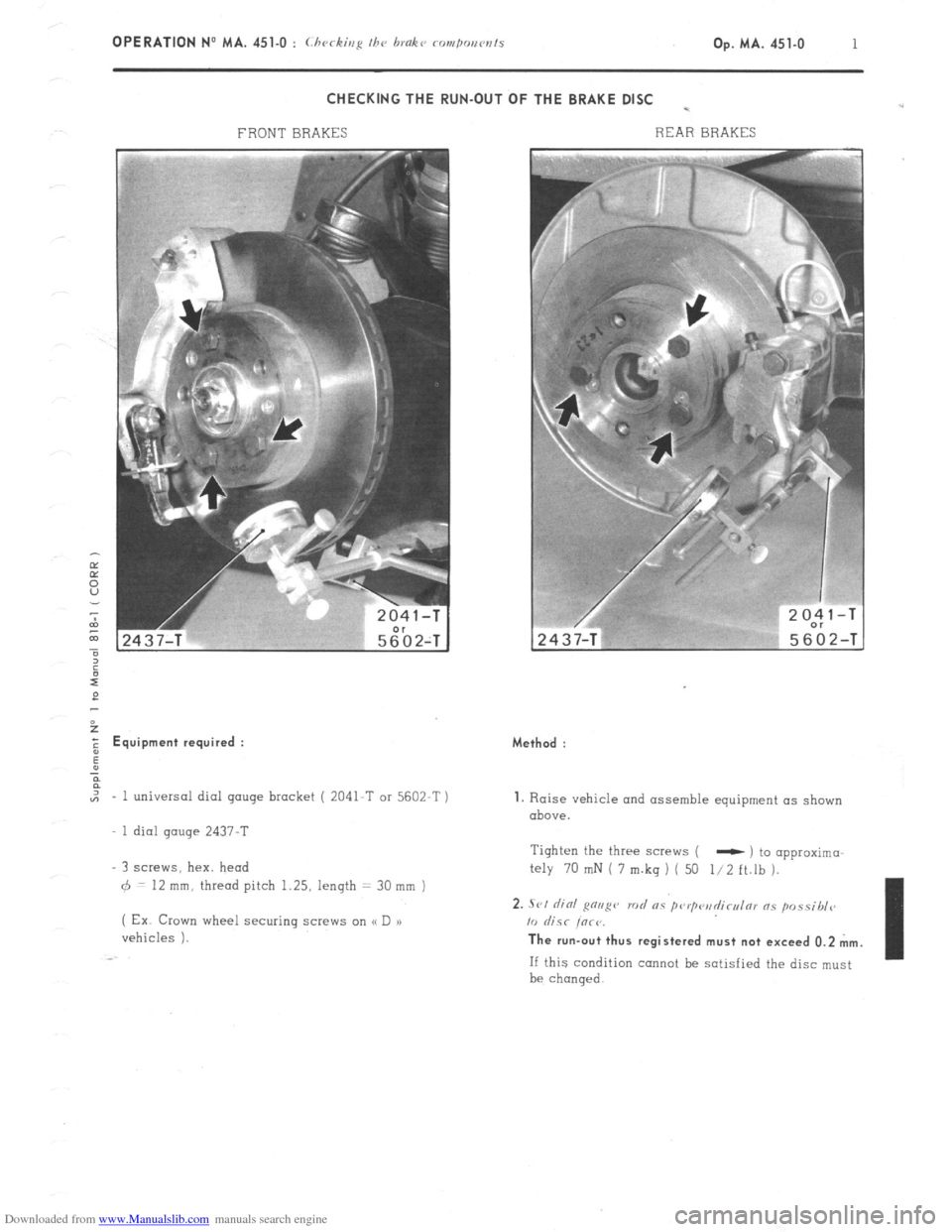
Downloaded from www.Manualslib.com manuals search engine OPERATION No MA. 451-O : Uwckirrg the hrflkv rov,~o,rrnts Op. MA. 451.0 1
CHECKING THE RUN-OUT OF THE BRAKE DISC -
FRONT BRAKES REAR BRAKES 2
E Equipment required :
,,, - 1 universal dial gauge bracket ( 2041-T or 5602-T )
1 dial gauge 2437-T
3 screws, hex. head
6 = 12 mm, thread pitch 1.25, length = 30 mm )
( Ex Crown wheel securing screw on (< D a)
vehicles ). Method :
1. Raise vehicle and assemble equipment as shown
above.
Tighten the three screws (
- ) to opproximo
My 70 mN i 7 m.kq ) ( 50 l/2 ft.lh ).
2. .Sl,l did g”“g” rod RS pwp<‘il~cl,l171 ns p”ssibl<~
10 &SC iorr. The run-out thus registered must not exceed 0.2 mm.
If this condition cannot be satisfied the disc must
be chanqed.
Page 283 of 394
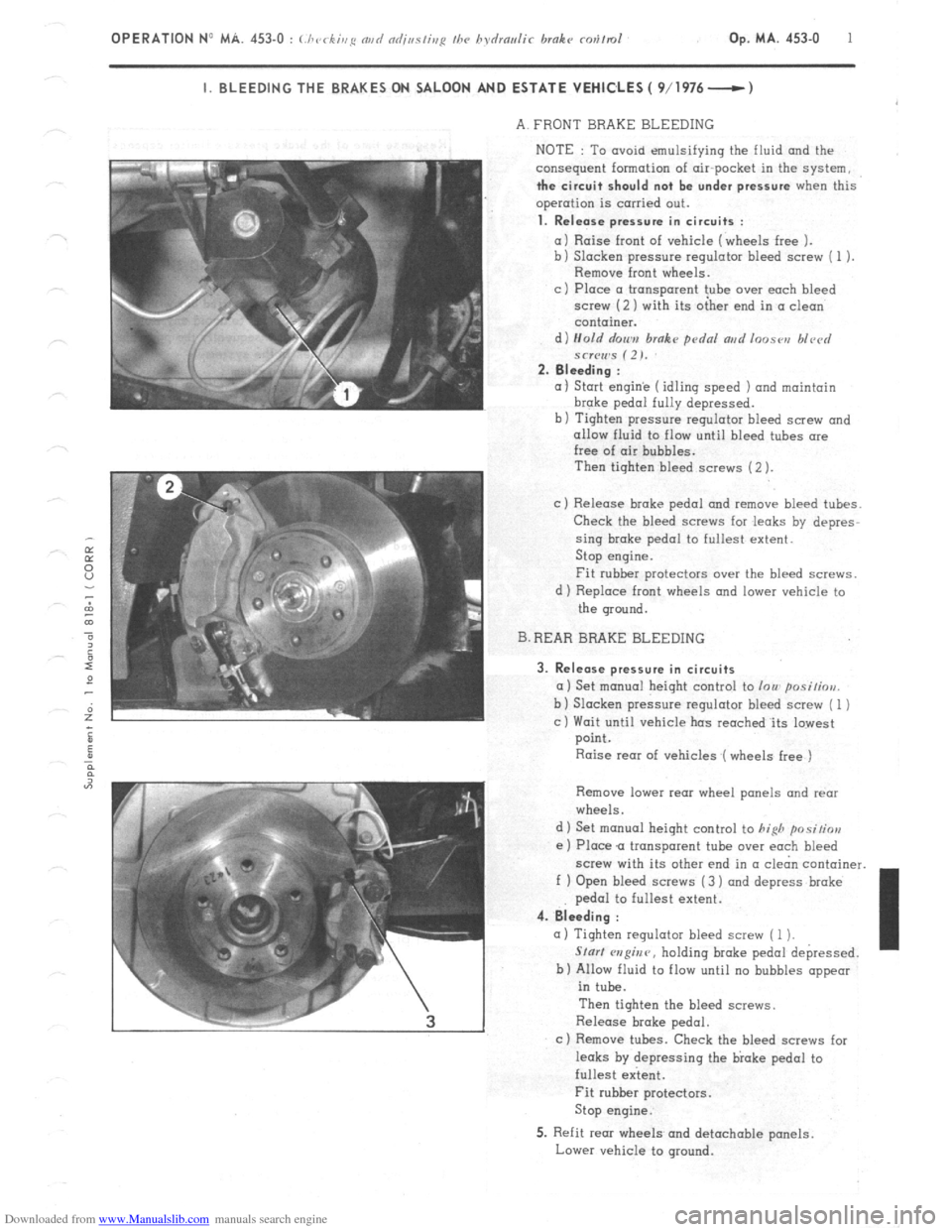
Downloaded from www.Manualslib.com manuals search engine Op. MA. 453-O 1
I. BLEEDING THE BRAKES ON SALOON AND ESTATE VEHICLES ( 9/1976- )
A. FRONT BRAKE BLEEDING
NOTE : To avoid emulsifying the fluid
and the
consequent formation of air-pocket in the system,
the circuit should not be under pressure when this
operation is carried out.
1. Release pressure in circuits :
a) Raise front of vehicle (wheels free 1.
b) Slacken pressure regulator bleed screw ( 1 ).
Remove front wheels.
c ) Place CI transparent tube over each bleed
screw (2 ) with its oiher end in CI clean
container.
d) Hold r/on,,,
brake pdnl ar,d loose,, blvcrl
*cr(Iws (2). 2. Bleeding :
(I 1 Start engin’e (idling speed 1 and maintain brake
pedal fully depressed.
b) Tighten pressure regulator bleed screw and
allow fluid to flow until bleed tubes ore
free of air bubbles.
Then tighten bleed screws (2 ).
c) Release broke pedal and remove bleed tubes.
Check the bleed screws for .leaks by depres-
sing brake pedal to fullest extent.
Stop engine.
Fit rubber protectors over the bleed screws.
d 1 Replace front wheels and lower vehicle to
the ground.
B. REAR BRAKE BLEEDING
3. Release pressure in circuits
a) Set monuol height control to lou posi/iou.
b 1 Slacken pressure regulator bleed screw ( 1 )
c) Wait until vehicle has reoched.its lowest
point.
Raise rear of vehicles (wheels free )
Remove lower rear wheel panels and rear
wheels.
d 1 Set manual height control to
hifih positior,
e ) Place Q transparent tube over each bleed
screw with its other end in (I cl&n container.
f ) Open bleed screws (3 ) and depress broke
pedal to fullest extent. 4. Bleeding :
(I) Tighten regulator bleed screw ( 1 1.
Slur/ w?@nr, holding broke pedal depressed.
b) Allow fluid to flow until no bubbles appear
in tube.
Then tighten the bleed screws.
Release brake pedal.
c ) Remove tubes. Check the bleed screws for
leaks by depressing the bloke pedal to
fullest extent. I
Fit rubber protectors.
Stop engine.
5. Refit rear wheels and detachable panels.
Lower vehicle to ground.
Page 284 of 394
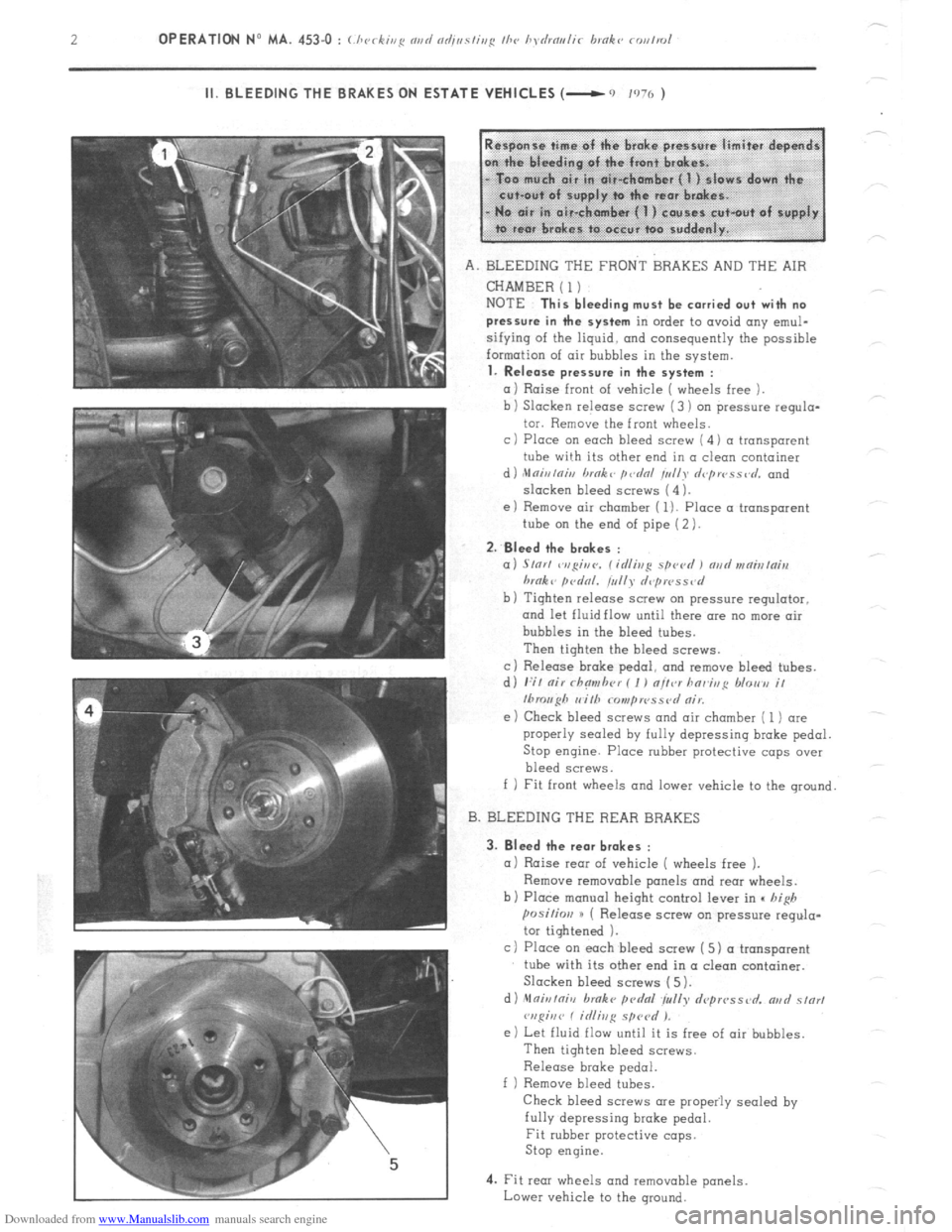
Downloaded from www.Manualslib.com manuals search engine 2 OPERATION N” MA. 453-O : (./ ‘cc ,,,g md ndjaslisg I/w hsdrmlir hrnkr rev/m/
k.
II. BLEEDING THE BRAKES ON ESTA ,TE VEHICLES (- 0 ,970 )
A. BLEEDING THE FRONT BRAKES AND THE AIR
CHAMBER ( 1)
NOTE
This bleeding must be carried out with no
pressure in the system
in order to avoid any emul-
sifying of the liquid. and consequently the possible
formation of air bubbles in the system.
1. Release pressure in the system :
a 1 Raise front of vehicle ( wheels free ).
b ) Slacken release screw (3 ) on $ressure requlo-
tor. Remove the front wheels.
c 1 Place on each bleed screw ( 4 1 a transparent
tube wi!h its other end in a clean container
d ) ,Mnir,lnh, brnk L p&d /u//y d<~pwss,~d. and
slacken bleed screws (4 ).
e) Remove air chamber ( 1). Place a transparent
tube on the end of pipe (2 ).
2.
Bleed the br.kes :
a) S/or/ ~v,gir,c,. C id/ivg spevd I md vrnialni,r
hrnk L firdnl. tullr d,~pwss<~d
b) Tighten release screw on pressure regulator.
and let fluid flow until there are no more air
bubbles in the bleed tubes.
Then tighten the bleed screws.
c) Release broke pedo1, and remove bleed tubes.
d) I:;/ nir rhnmhrr ( I ) nltcr hnr~htg /dorm i/
Ibrouph I, i/h Nmp IPSS ?,I nir.
e ) Check bleed screws and air chamber ( 1) are
properly sealed
by fully depressing brake pedal.
Stop engine. Place rubber protective caps over
bleed screws.
f 1 Fit front wheels and lower vehicle to the ground
B. BLEEDING THE REAR BRAKES
3.
Bleed the rear brakes :
a 1 Raise rear of vehicle ( wheels free ).
Remove removable panels and rear wheels.
b) Place manual height control lever in c high
posi~im H ( Release screw on pressure regula-
tor tightened 1.
c) Place on each bleed screw ( 5) a transparent
tube with its other end in a clean container.
Slacken bleed screws (5).
d) nlfliuiniv broke pcdfll ~yrrlly depwssvd. ar,d s/or,
vspiuv C idiivg sprcd ).
e) Let fluid flow until it is free of air bubbles.
Then tighten bleed screws.
Release brake pedal.
f ) Remove bleed tubes.
Check bleed screws are propeily sealed by
fully depressing broke pedal.
Fit rubber protective cops.
Stop engine.
4. Fit rear wheels and removable panels
Lower vehicle to the ground.
Page 285 of 394
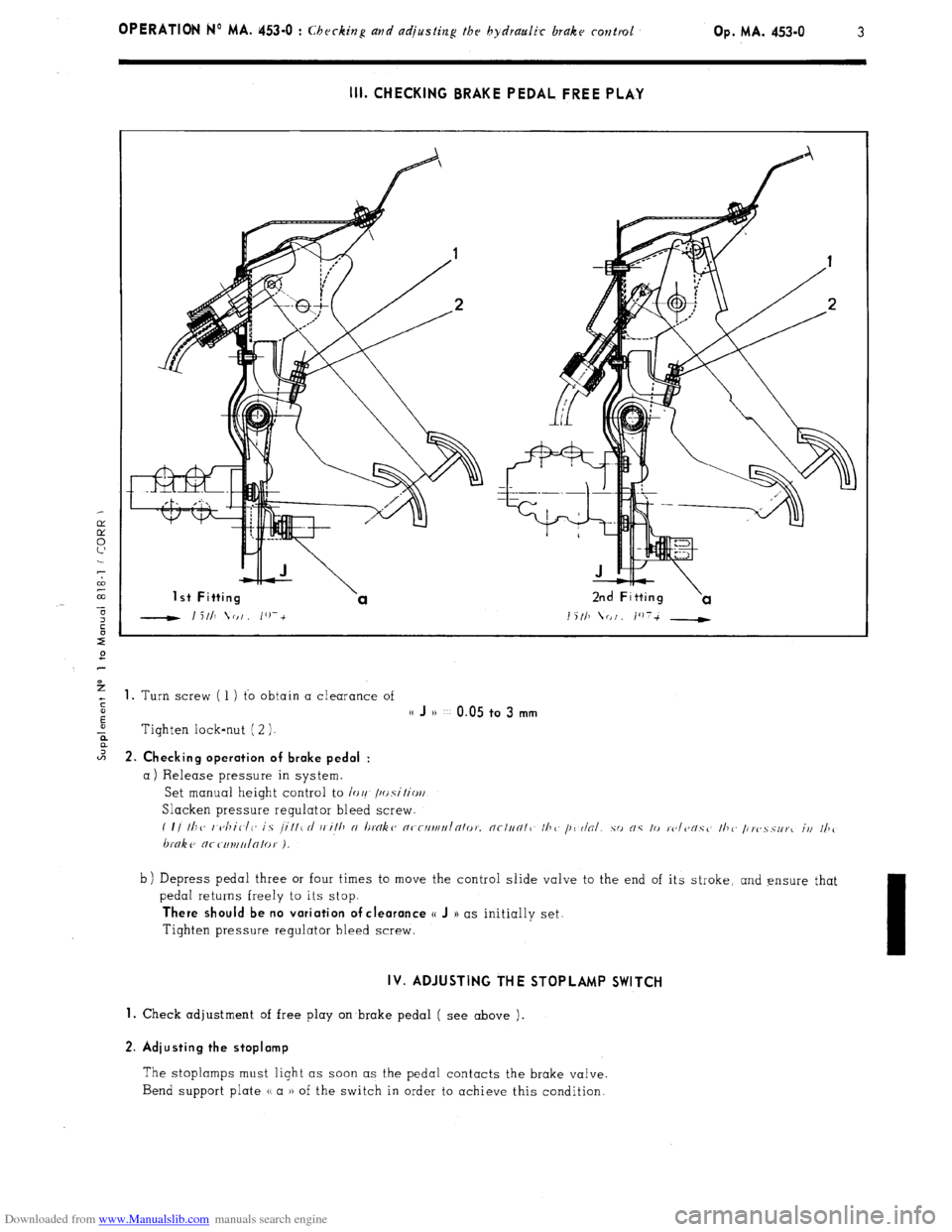
Downloaded from www.Manualslib.com manuals search engine OPERATION No MA. 453=0 : Ch J k’ ( c zng and adjjusfing thr hydraulk brake rontrol Op. MA. 453-O 3
III. CHECKING BRAKE PEDAL FREE PLAY
1 st Fitting 2nd Fitting
1 5 111 (I I /‘)7-t __t i%
+ 1. Turn screw ( 1 ) to obtain a clearance of
s
E
(( J )) ~~ 0.05 to 3 mm
-ii Tighten lock-nut ( 2 ).
2 2. Ch k’ ec Ing operation of brake pedal :
a) Release pressure in system.
Set manual height control to /or! /~~.s\‘itio~/
Slacken pressure regulator bleed screw.
( I/ Ill<, I <~/liClC~ is /ill1 rl i, ill, N I~tYlk~~ n~-rllrlll,Inlo,~. nc/un/1 II?<, /I< r/al.
hnke nr c111uu/n/0,. ).
b) Depress pedal three or four times to move the control slide valve to the end of its stroke, and ensure that
pedal returns freely to its stop.
There should be no variation of clearance o J )) as initially set.
Tighten pressure regulator bleed screw.
IV. ADJUSTING THE STOPLAMP SWITCH
1.
Check adjustment of free play on brake pedal ( see above ).
2. Adiusting the stoplamp
The stoplamps must light as soon as the pedal contacts the brake valve.
Bend support plate u a )) of the switch in order to achieve this condition.
Page 286 of 394
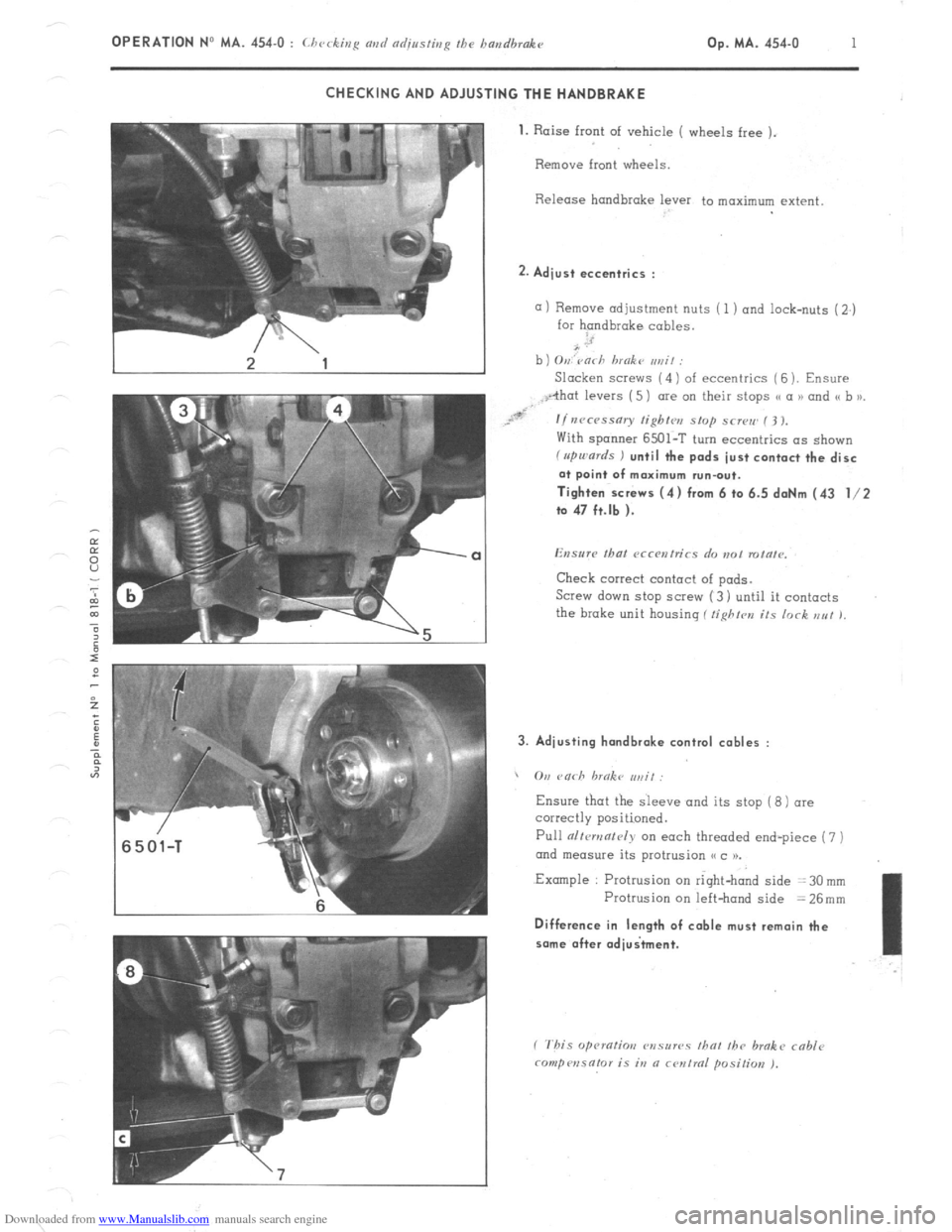
Downloaded from www.Manualslib.com manuals search engine OPERATION No MA. 454-O : Lhcckiu~ avd adjnsfbrR fhe bandbrake op. MA. 454-u I CHECKING AND ADJUSTING THE HANDBRAKE
1.
Raise front of vehicle ( wheels free ).
Remove front wheels.
Release handbrake lever to maximum extent 2. Adjust eccentrics :
a) Remove adjustment nuts ( 1 ) and lock-nuts (2.)
for handbrake cables.
b ) O,,,‘varh hmokt~ ,,rzit :
Slacken SCI~WS (4) of eccentrics ( 6 ). Ensure
With spanner 6501-T turn eccentrics as shown f rrpu,ards ) until the pads just contact the disc
at point of maximum run-out.
Tighten screws (4) from 6 to 6.5 daNm (43 l/2
to 47 ft.lb ).
Check correct contact of pads.
Screw down stop SCI~W (3) until it contacts
the brake unit housing ( tighfrn its lock EN! 1, 3. Adjusting hondbrake control cables :
, On rnrh hrnkc ,,,, if:
Ensure
Pull alfcmnf~~iy on each threaded end-piece (7 )
ond measure its protrusion (< c 1).
.Example : Protrusion on right-hand side = 30 mm
Protrusion on left-hand side = 26mm Difference in length of cable must remain the
some after adiuitment.
Page 287 of 394
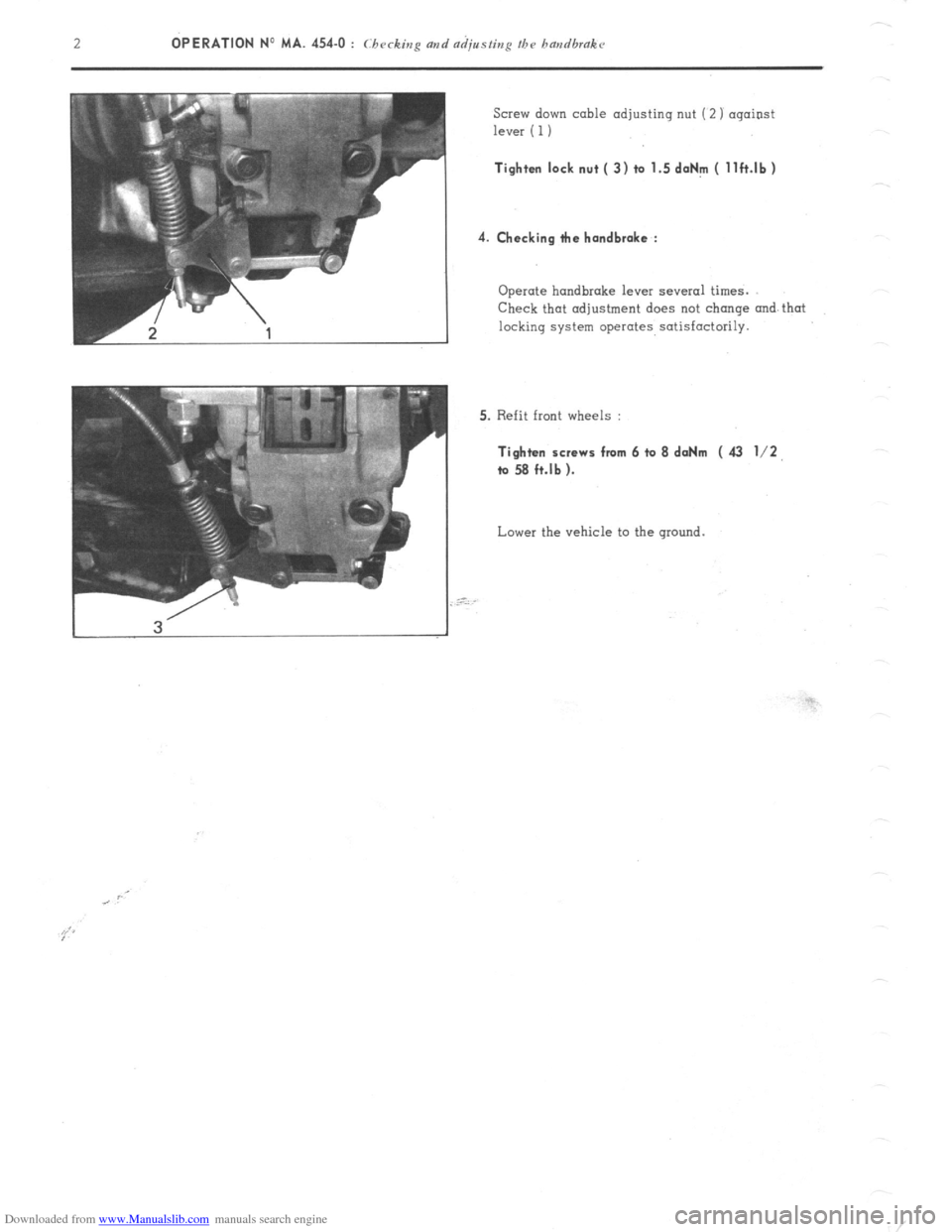
Downloaded from www.Manualslib.com manuals search engine OPERATION No MA. 454-O : Ch ec tzg and a&sting the handbrakc k’
Screw down cable adjusting nut (2) against
lever ( 1) Tighten lock nut ( 3) to 1.5 doNm ( llft.lb)
4. Checking tie handbrake :
Operate handbrake lever several times.
Check that adjustment does not change and that
locking system operates satisfactorily.
5. Refit front wheels : Tighten screws from 6 to 8 daNm ( 43 l/2,
ta 58 ft.lb ).
Lower the vehicle to the ground.
Page 288 of 394
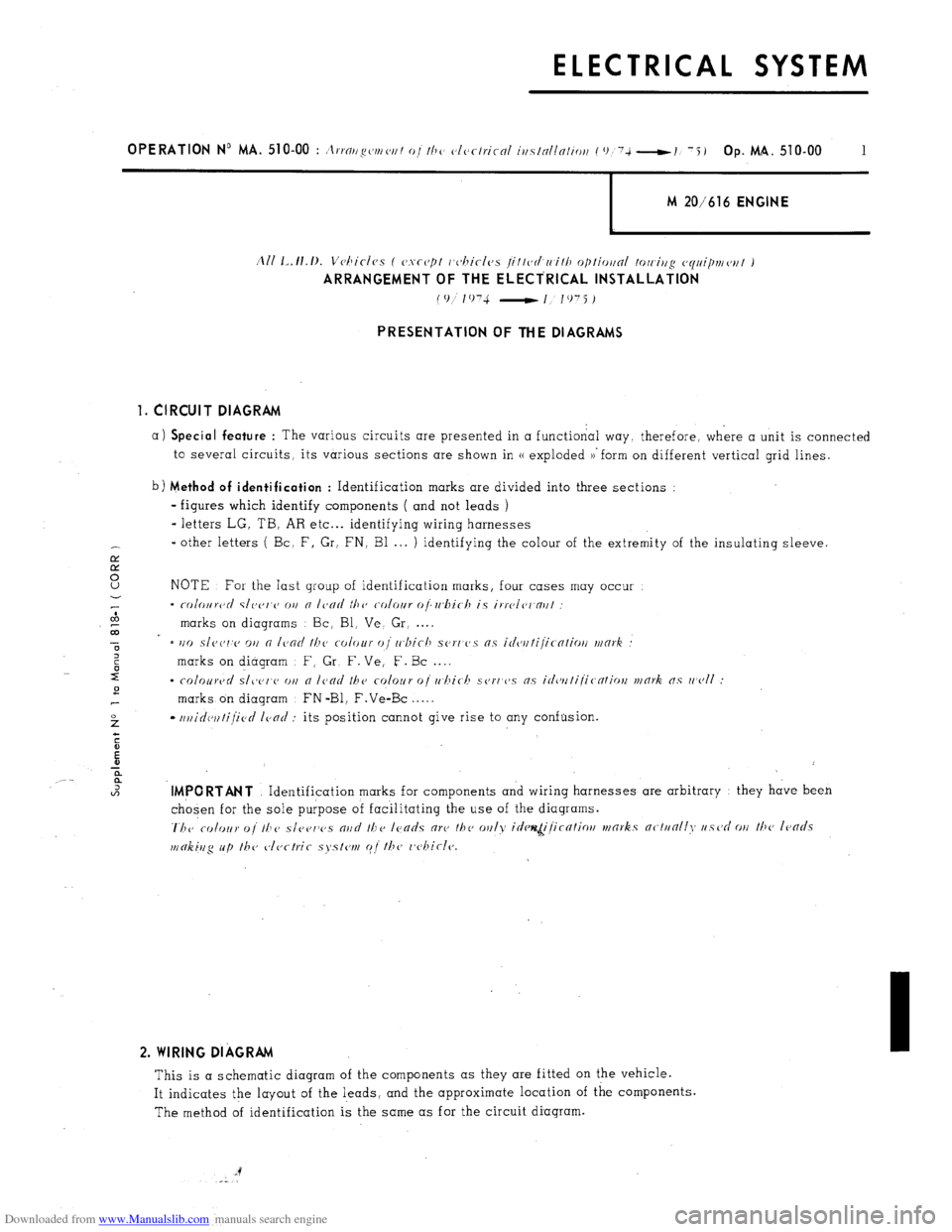
Downloaded from www.Manualslib.com manuals search engine ELECTRICAL SYSTEM
M 20/616 ENGINE
PRESENTATION OF THE DIAGRAMS
1. CIRCUIT DIAGRAM
a) Special feature
: The various circuits are presented in a functional way. therefore, where a unit is connected
to several circuits, its various sections are shown in (( exploded ~‘form on different vertical grid lines. b) Method of identification
: Identification marks are divided into three sections :
- figures which identify components ( and not leads )
- letters LG. TB. AR etc... identifying wiring harnesses
_
other letters ( Bc. F, Gr, FN, Bl . . . ) identifying the colour of the extremity of the insulating sleeve.
NOTE For the Iast group of identification marks, four cases may occur
- coloiirc~rl slc,c,f,c~ 01l 0 Ic’cirf tllc, colour of wbic-h is irrc’l~~r.nrlI
marks on diagrams Bc, Bl, Ve. Gr. . . . .
= l/o s/oc,r,c, 01) 0 I~~ocl //Ic, c-olour of whit11 .ser1’c’s ns icfc~rltijicntiot, work
marks on diagram F, Gr, F. Ve, E. Bc . . . .
- colourc~ri .s/t,c~c~c, O,I n Icncl the colour uj rrhich SCJ~,‘C’.T ns ic/cvrtijitntiorL mnrk 0.5 rr~ol/ :
marks on diagram : FN -Bl, F.Ve-Bc . . . . .
-
trr/id~~~~li~~c~d I~>nd : its position cannot give rise to any confusion. .lMPORTANT
Identification marks for components and wiring harnesses are arbitrary they have been
chosen for the sole purpose of facilitating the use of the diagrams.
‘1.17~~ colour 01’ II,c~ sl~~c~~~c~s n~ld the I~~atls ore the rnr~ly id~~~~i,/t’cntiot~ vrork,s nc-/uoll\, uscjd OII tlj~~ I~~ncls
making up /h(, cllectric s~~stern c;/ the l,c~hir-Ie. 2. WIRING DIAGRAM
This is a schematic diagram of the components as they are fitted on the vehicle.
It indicates the layout of the leads, and the approximate location of the components.
The method of identification is the same as for the circuit diagram.
Page 289 of 394
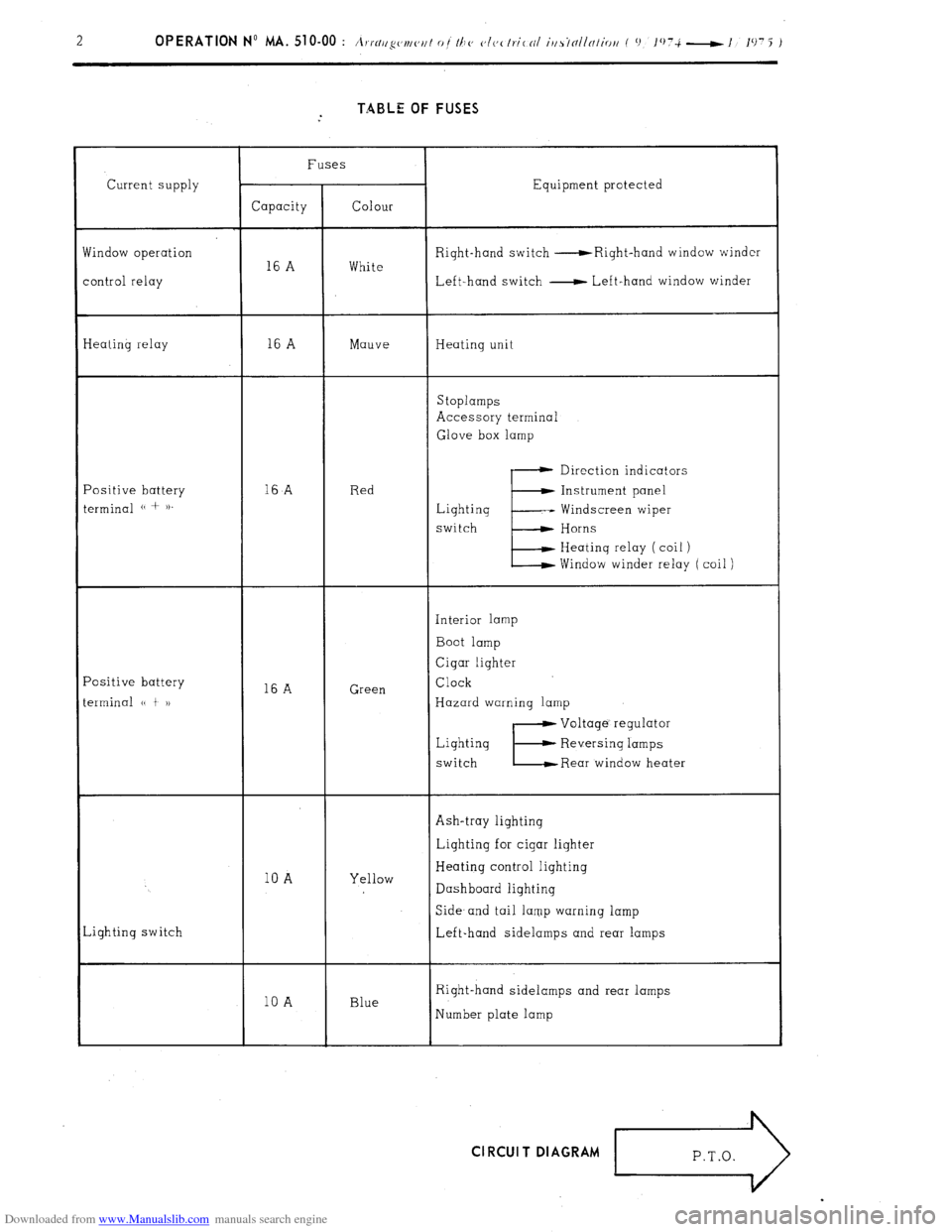
Downloaded from www.Manualslib.com manuals search engine TABLE OF FUSES
Current supply
findow operation
ontrol relay Fuses
Equipment protected
Capacity Colour
Right-hand switch -Right-hand window winder
16 A White
Left-hand switch - Left-hand window winder
Ieating relay 16 A Mauve Heating unit
Stoplamps
Accessory terminal
Glove box lamp
‘ositive battery
erminal (( + )). 16
A Red Direction indicators
E Instrument panel
Lighting -- Windscreen wiper
switch Horns
Heating relay ( coil )
Window winder relay ( coil )
‘ositive battery
erminal (( t 1) 16 A Green Interior lamp
Boot lamp
Cigar lighter
Clock
Hazard warning lamp
Lighting
switch
E
Voltage’ regulator
Reversing lamps
Rear window heater
Ash-tray lighting
10 A Yellow Lighting for cigar lighter
Heating control lighting
Dashboard lighting
,ighting switch Side- and tail lamp warning lamp
Left-hand sidelamps and rear lamps
10 A Blue Right-hand sidelamps and rear lamps
Number plate lamp Cl RCUI T DIAGRAM
r>
Page 290 of 394
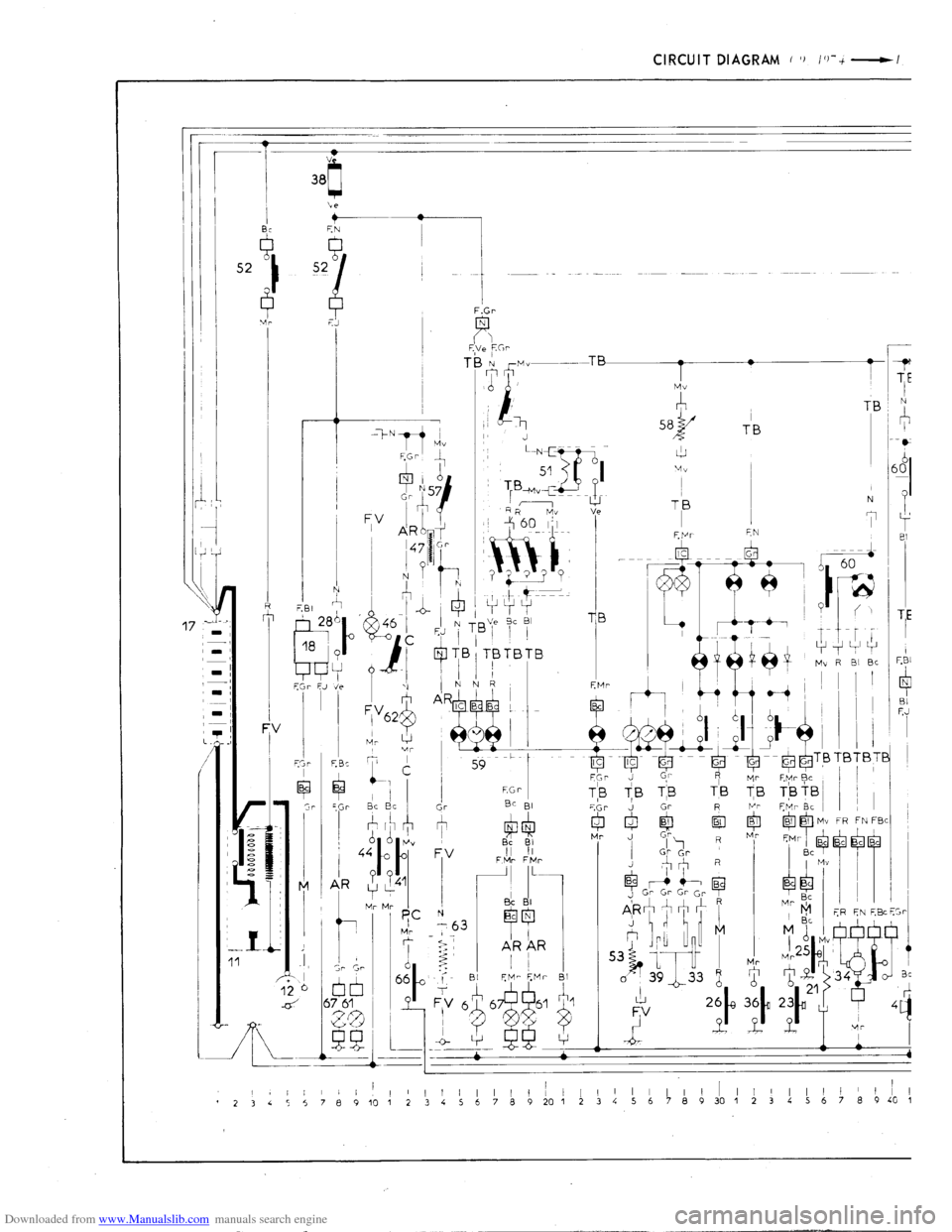
Downloaded from www.Manualslib.com manuals search engine