DAEWOO LACETTI 2004 Service Repair Manual
Manufacturer: DAEWOO, Model Year: 2004, Model line: LACETTI, Model: DAEWOO LACETTI 2004Pages: 2643, PDF Size: 80.54 MB
Page 1041 of 2643
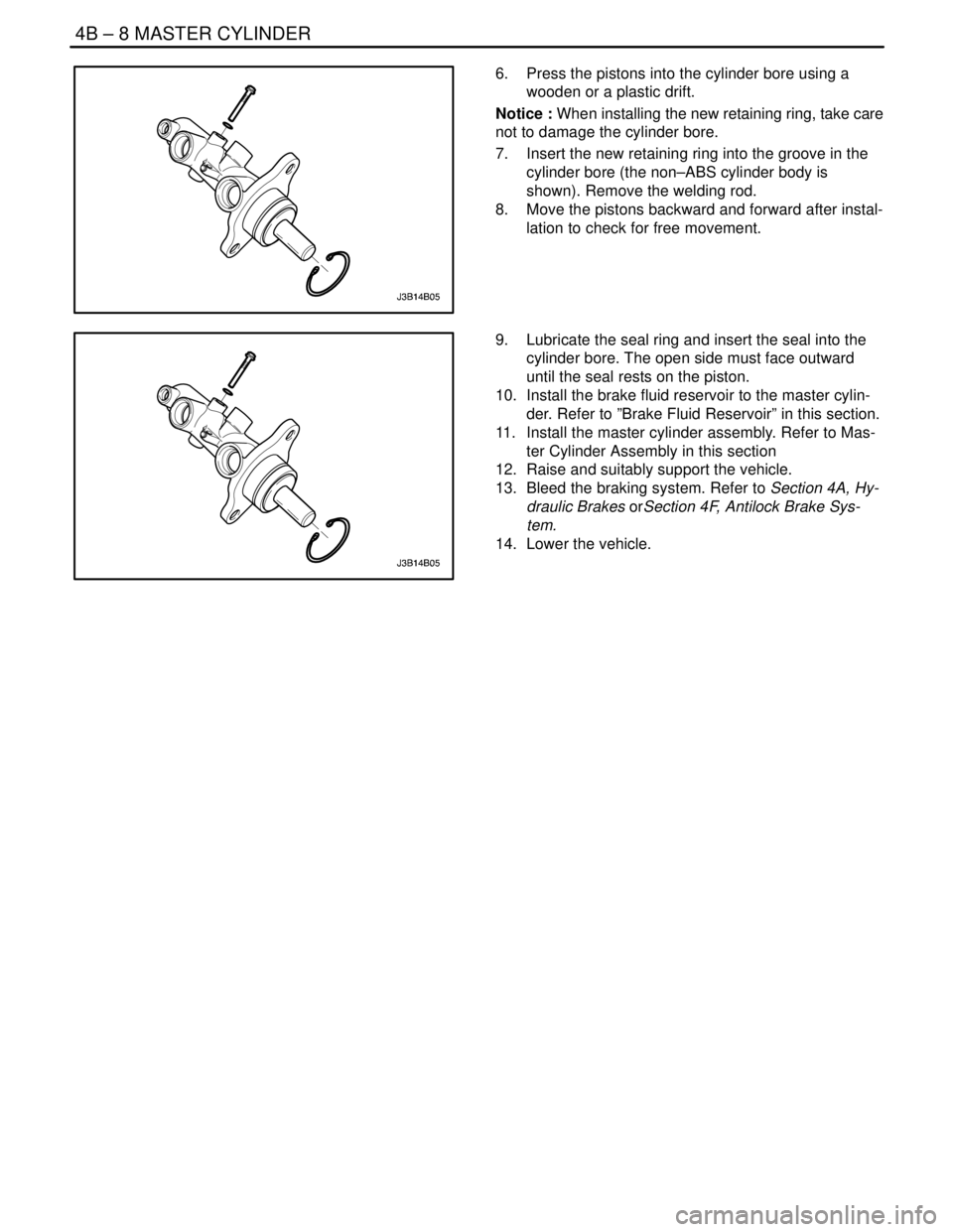
4B – 8IMASTER CYLINDER
DAEWOO V–121 BL4
6. Press the pistons into the cylinder bore using a
wooden or a plastic drift.
Notice : When installing the new retaining ring, take care
not to damage the cylinder bore.
7. Insert the new retaining ring into the groove in the
cylinder bore (the non–ABS cylinder body is
shown). Remove the welding rod.
8. Move the pistons backward and forward after instal-
lation to check for free movement.
9. Lubricate the seal ring and insert the seal into the
cylinder bore. The open side must face outward
until the seal rests on the piston.
10. Install the brake fluid reservoir to the master cylin-
der. Refer to ”Brake Fluid Reservoir” in this section.
11. Install the master cylinder assembly. Refer to Mas-
ter Cylinder Assembly in this section
12. Raise and suitably support the vehicle.
13. Bleed the braking system. Refer to Section 4A, Hy-
draulic Brakes orSection 4F, Antilock Brake Sys-
tem.
14. Lower the vehicle.
Page 1042 of 2643
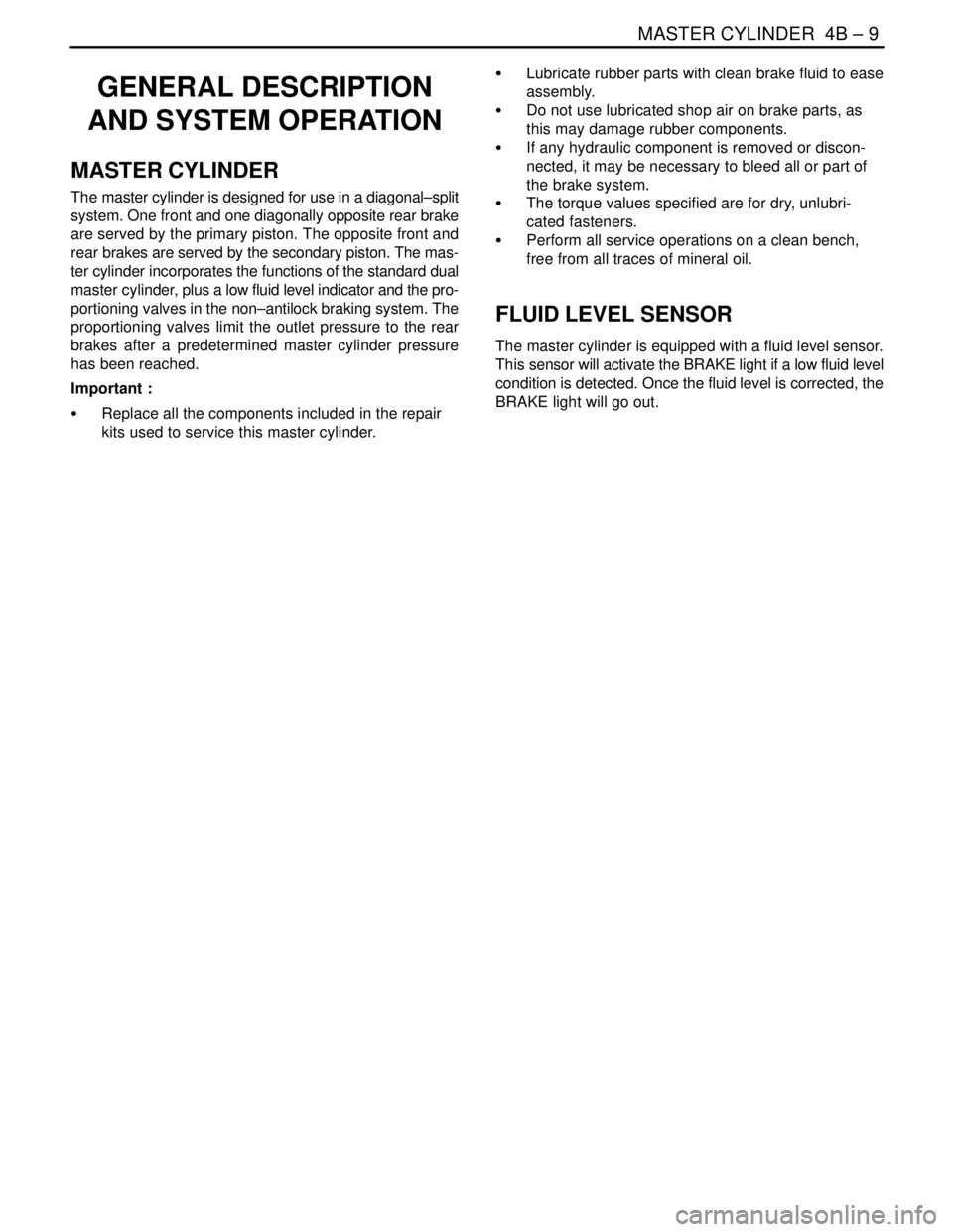
MASTER CYLINDER 4B – 9
DAEWOO V–121 BL4
GENERAL DESCRIPTION
AND SYSTEM OPERATION
MASTER CYLINDER
The master cylinder is designed for use in a diagonal–split
system. One front and one diagonally opposite rear brake
are served by the primary piston. The opposite front and
rear brakes are served by the secondary piston. The mas-
ter cylinder incorporates the functions of the standard dual
master cylinder, plus a low fluid level indicator and the pro-
portioning valves in the non–antilock braking system. The
proportioning valves limit the outlet pressure to the rear
brakes after a predetermined master cylinder pressure
has been reached.
Important :
S Replace all the components included in the repair
kits used to service this master cylinder.S Lubricate rubber parts with clean brake fluid to ease
assembly.
S Do not use lubricated shop air on brake parts, as
this may damage rubber components.
S If any hydraulic component is removed or discon-
nected, it may be necessary to bleed all or part of
the brake system.
S The torque values specified are for dry, unlubri-
cated fasteners.
S Perform all service operations on a clean bench,
free from all traces of mineral oil.
FLUID LEVEL SENSOR
The master cylinder is equipped with a fluid level sensor.
This sensor will activate the BRAKE light if a low fluid level
condition is detected. Once the fluid level is corrected, the
BRAKE light will go out.
Page 1043 of 2643
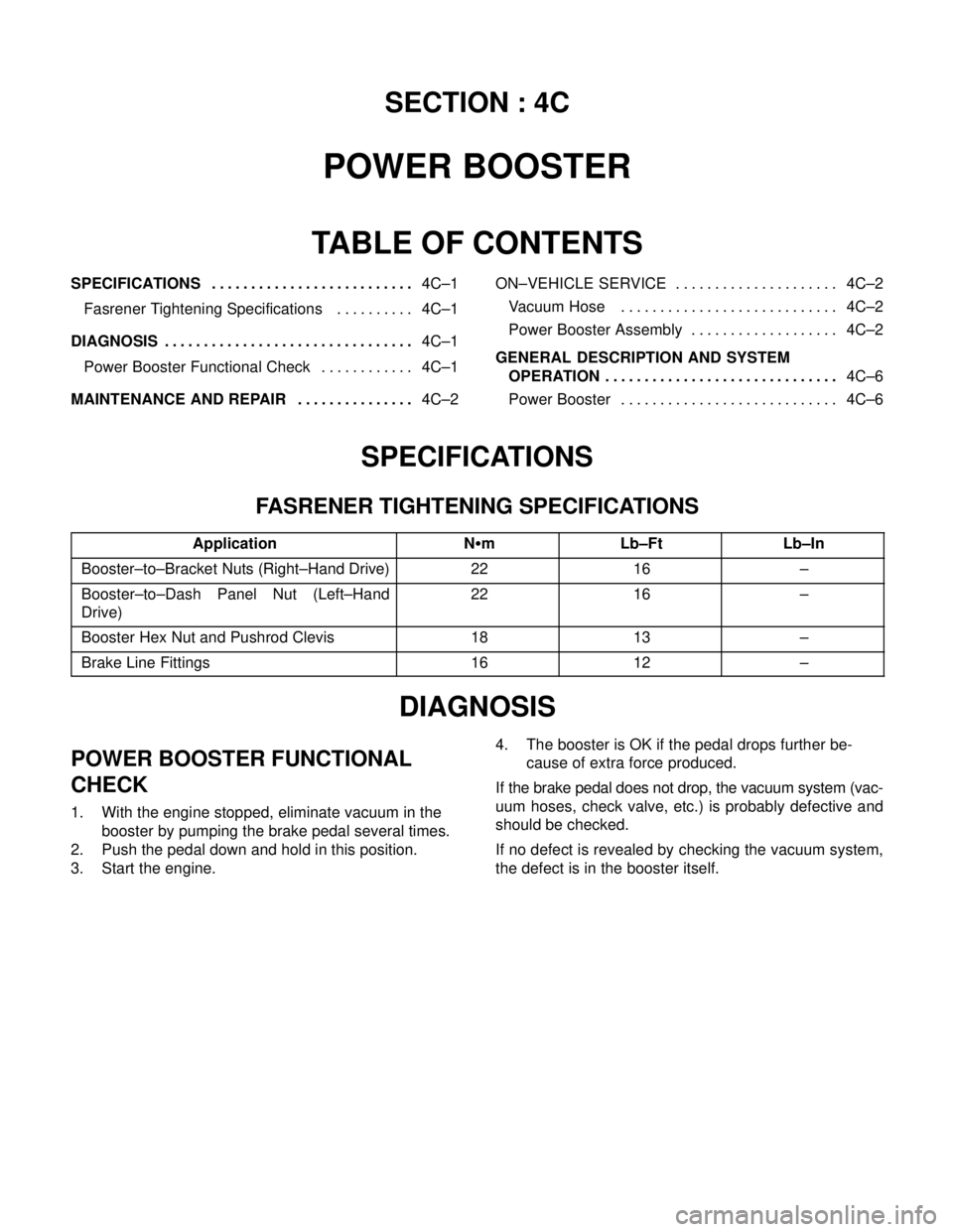
SECTION : 4C
POWER BOOSTER
TABLE OF CONTENTS
SPECIFICATIONS4C–1 . . . . . . . . . . . . . . . . . . . . . . . . . .
Fasrener Tightening Specifications 4C–1. . . . . . . . . .
DIAGNOSIS4C–1 . . . . . . . . . . . . . . . . . . . . . . . . . . . . . . . .
Power Booster Functional Check 4C–1. . . . . . . . . . . .
MAINTENANCE AND REPAIR4C–2 . . . . . . . . . . . . . . . ON–VEHICLE SERVICE 4C–2. . . . . . . . . . . . . . . . . . . . .
Vacuum Hose 4C–2. . . . . . . . . . . . . . . . . . . . . . . . . . . .
Power Booster Assembly 4C–2. . . . . . . . . . . . . . . . . . .
GENERAL DESCRIPTION AND SYSTEM
OPERATION4C–6 . . . . . . . . . . . . . . . . . . . . . . . . . . . . . .
Power Booster 4C–6. . . . . . . . . . . . . . . . . . . . . . . . . . . .
SPECIFICATIONS
FASRENER TIGHTENING SPECIFICATIONS
ApplicationNSmLb–FtLb–In
Booster–to–Bracket Nuts (Right–Hand Drive)2216–
Booster–to–Dash Panel Nut (Left–Hand
Drive)2216–
Booster Hex Nut and Pushrod Clevis1813–
Brake Line Fittings1612–
DIAGNOSIS
POWER BOOSTER FUNCTIONAL
CHECK
1. With the engine stopped, eliminate vacuum in the
booster by pumping the brake pedal several times.
2. Push the pedal down and hold in this position.
3. Start the engine.4. The booster is OK if the pedal drops further be-
cause of extra force produced.
If the brake pedal does not drop, the vacuum system (vac-
uum hoses, check valve, etc.) is probably defective and
should be checked.
If no defect is revealed by checking the vacuum system,
the defect is in the booster itself.
Page 1044 of 2643
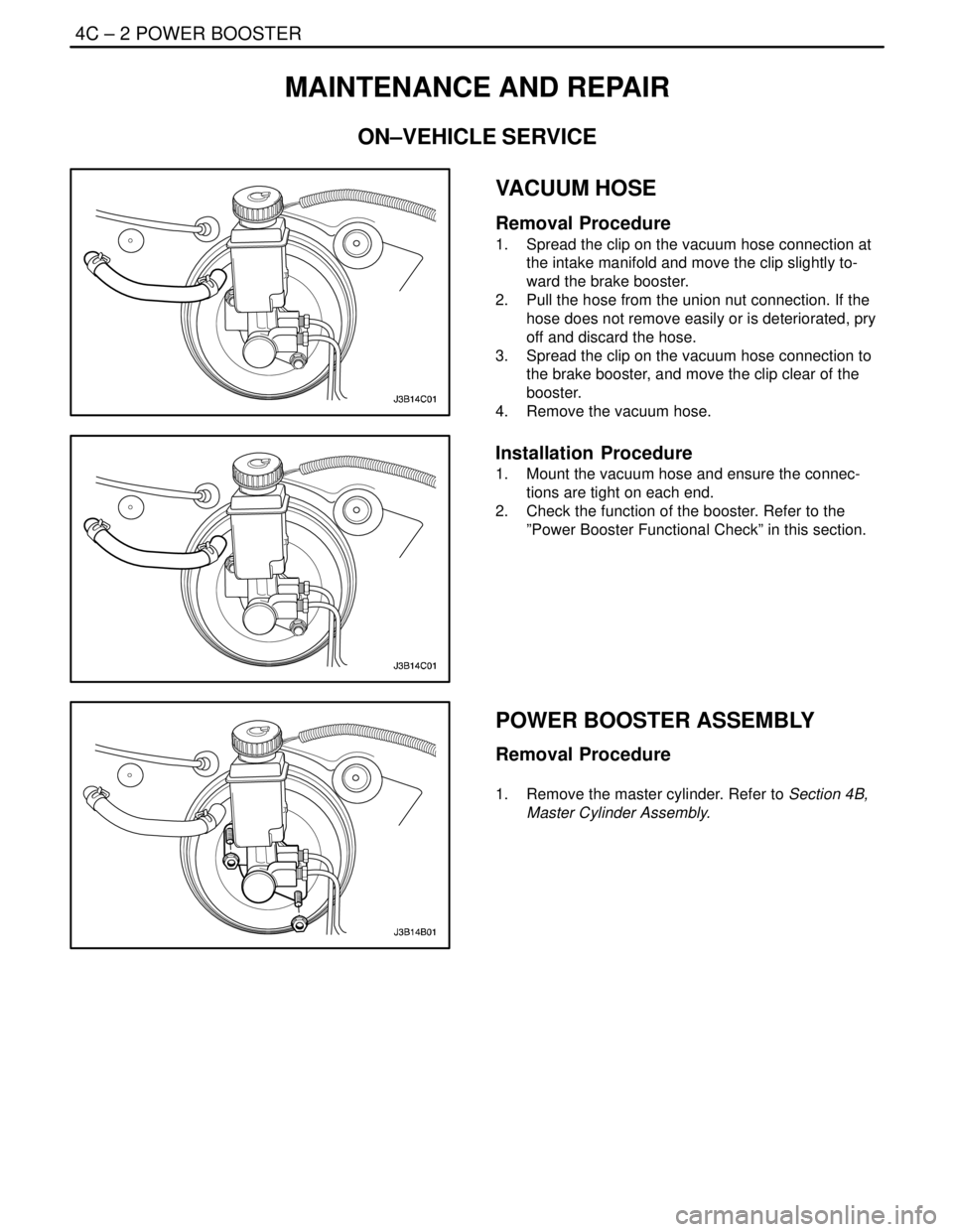
4C – 2IPOWER BOOSTER
DAEWOO V–121 BL4
MAINTENANCE AND REPAIR
ON–VEHICLE SERVICE
VACUUM HOSE
Removal Procedure
1. Spread the clip on the vacuum hose connection at
the intake manifold and move the clip slightly to-
ward the brake booster.
2. Pull the hose from the union nut connection. If the
hose does not remove easily or is deteriorated, pry
off and discard the hose.
3. Spread the clip on the vacuum hose connection to
the brake booster, and move the clip clear of the
booster.
4. Remove the vacuum hose.
Installation Procedure
1. Mount the vacuum hose and ensure the connec-
tions are tight on each end.
2. Check the function of the booster. Refer to the
”Power Booster Functional Check” in this section.
POWER BOOSTER ASSEMBLY
Removal Procedure
1. Remove the master cylinder. Refer to Section 4B,
Master Cylinder Assembly.
Page 1045 of 2643
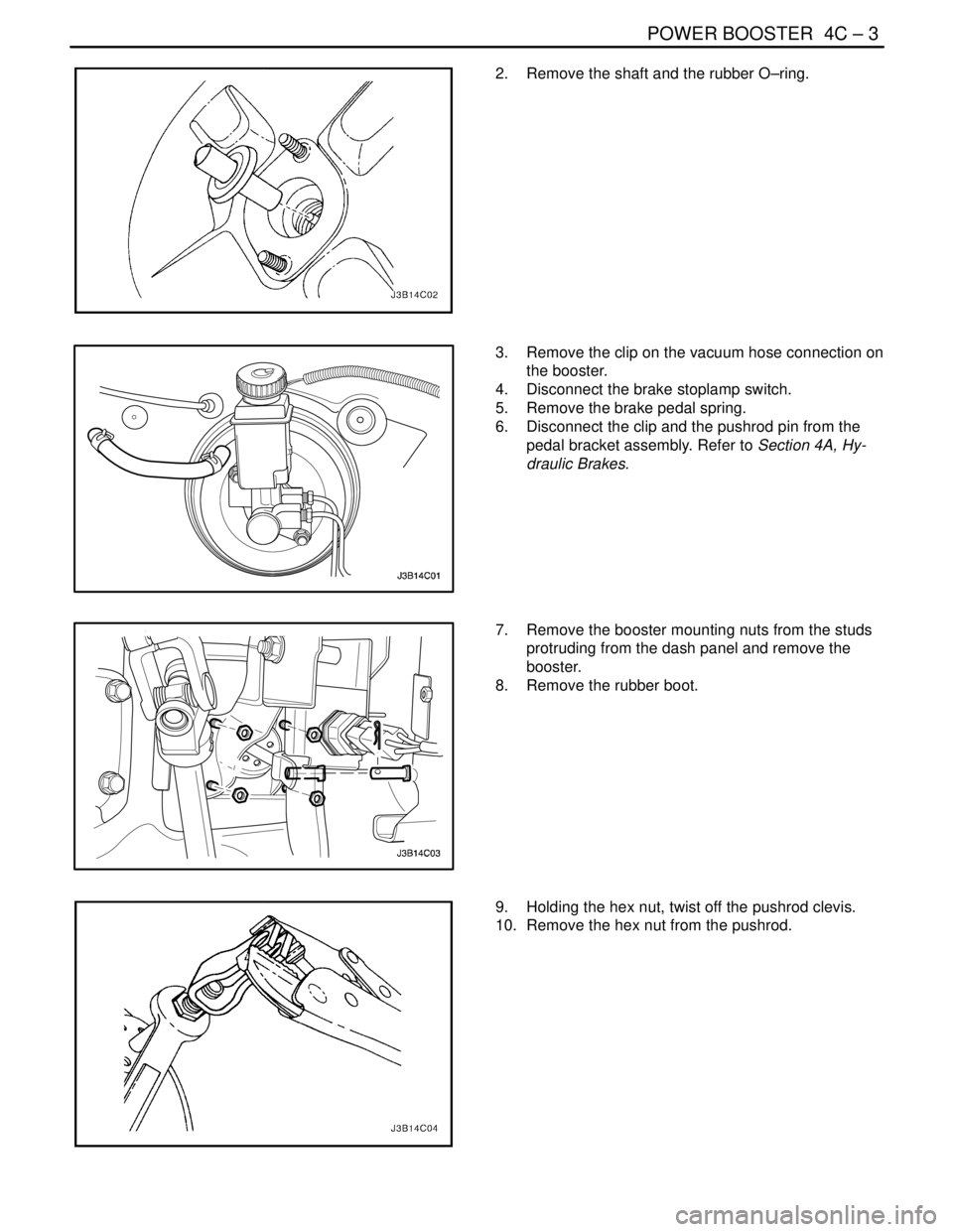
POWER BOOSTER 4C – 3
DAEWOO V–121 BL4
2. Remove the shaft and the rubber O–ring.
3. Remove the clip on the vacuum hose connection on
the booster.
4. Disconnect the brake stoplamp switch.
5. Remove the brake pedal spring.
6. Disconnect the clip and the pushrod pin from the
pedal bracket assembly. Refer to Section 4A, Hy-
draulic Brakes.
7. Remove the booster mounting nuts from the studs
protruding from the dash panel and remove the
booster.
8. Remove the rubber boot.
9. Holding the hex nut, twist off the pushrod clevis.
10. Remove the hex nut from the pushrod.
Page 1046 of 2643
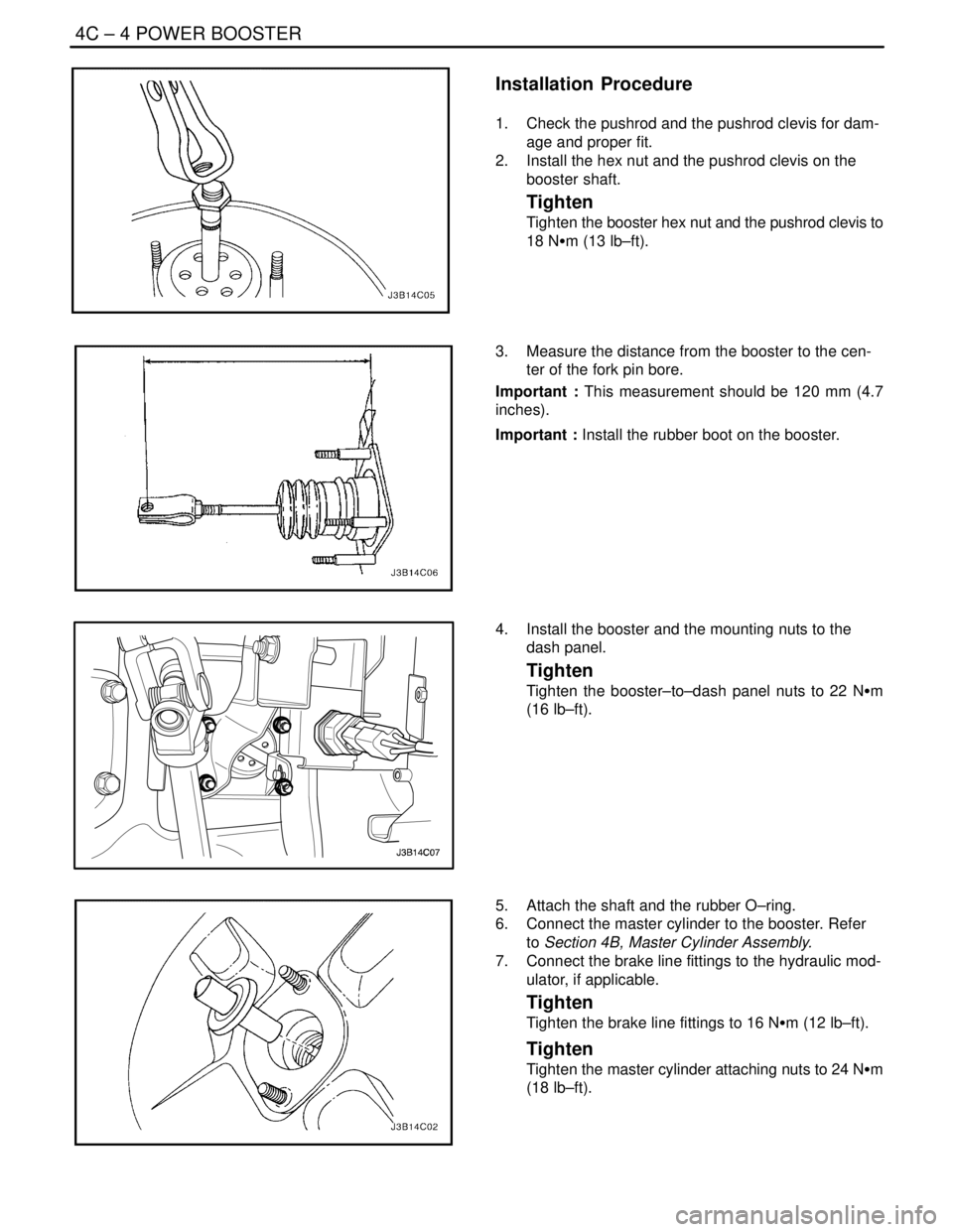
4C – 4IPOWER BOOSTER
DAEWOO V–121 BL4
Installation Procedure
1. Check the pushrod and the pushrod clevis for dam-
age and proper fit.
2. Install the hex nut and the pushrod clevis on the
booster shaft.
Tighten
Tighten the booster hex nut and the pushrod clevis to
18 NSm (13 lb–ft).
3. Measure the distance from the booster to the cen-
ter of the fork pin bore.
Important : This measurement should be 120 mm (4.7
inches).
Important : Install the rubber boot on the booster.
4. Install the booster and the mounting nuts to the
dash panel.
Tighten
Tighten the booster–to–dash panel nuts to 22 NSm
(16 lb–ft).
5. Attach the shaft and the rubber O–ring.
6. Connect the master cylinder to the booster. Refer
to Section 4B, Master Cylinder Assembly.
7. Connect the brake line fittings to the hydraulic mod-
ulator, if applicable.
Tighten
Tighten the brake line fittings to 16 NSm (12 lb–ft).
Tighten
Tighten the master cylinder attaching nuts to 24 NSm
(18 lb–ft).
Page 1047 of 2643
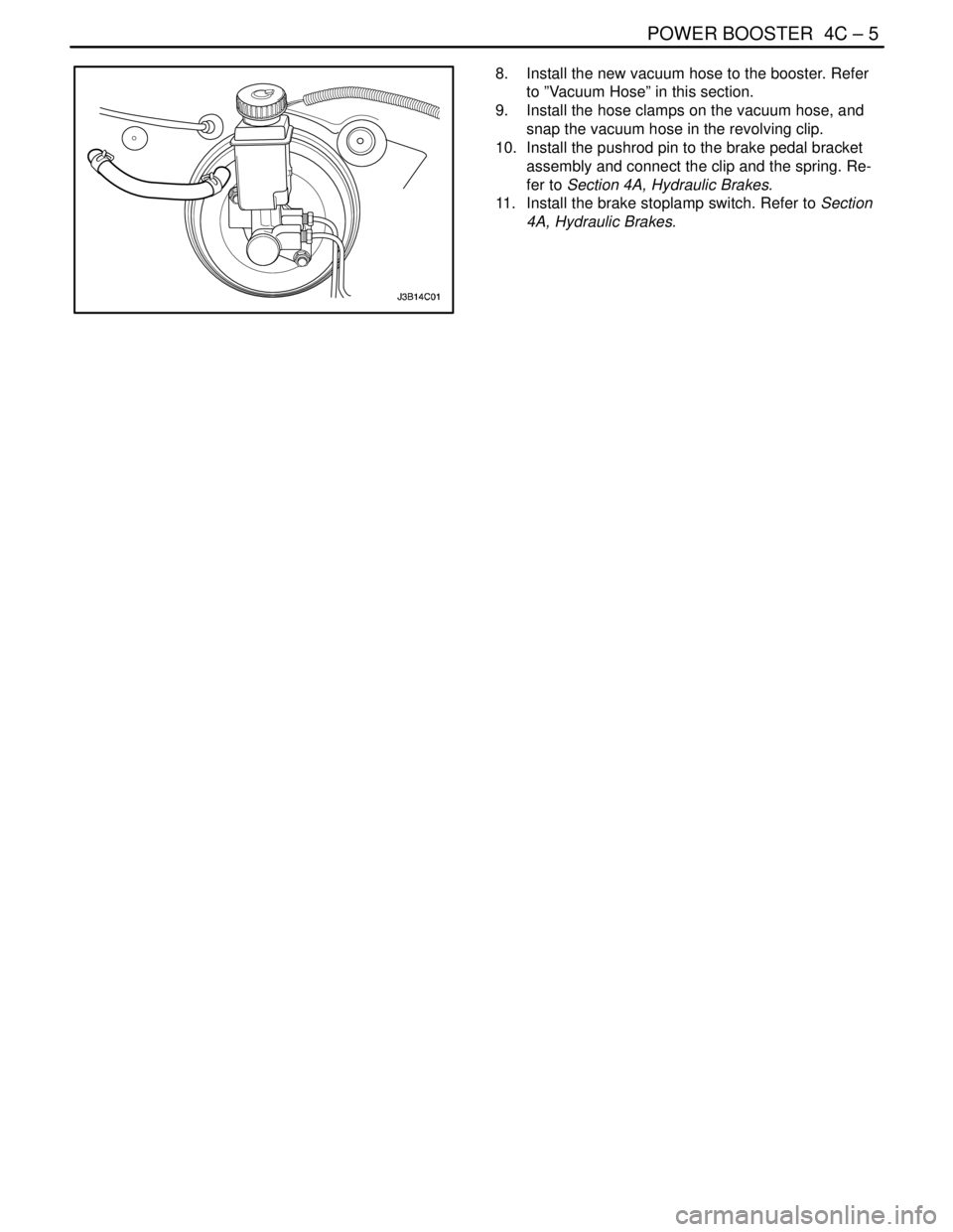
POWER BOOSTER 4C – 5
DAEWOO V–121 BL4
8. Install the new vacuum hose to the booster. Refer
to ”Vacuum Hose” in this section.
9. Install the hose clamps on the vacuum hose, and
snap the vacuum hose in the revolving clip.
10. Install the pushrod pin to the brake pedal bracket
assembly and connect the clip and the spring. Re-
fer to Section 4A, Hydraulic Brakes.
11. Install the brake stoplamp switch. Refer to Section
4A, Hydraulic Brakes.
Page 1048 of 2643
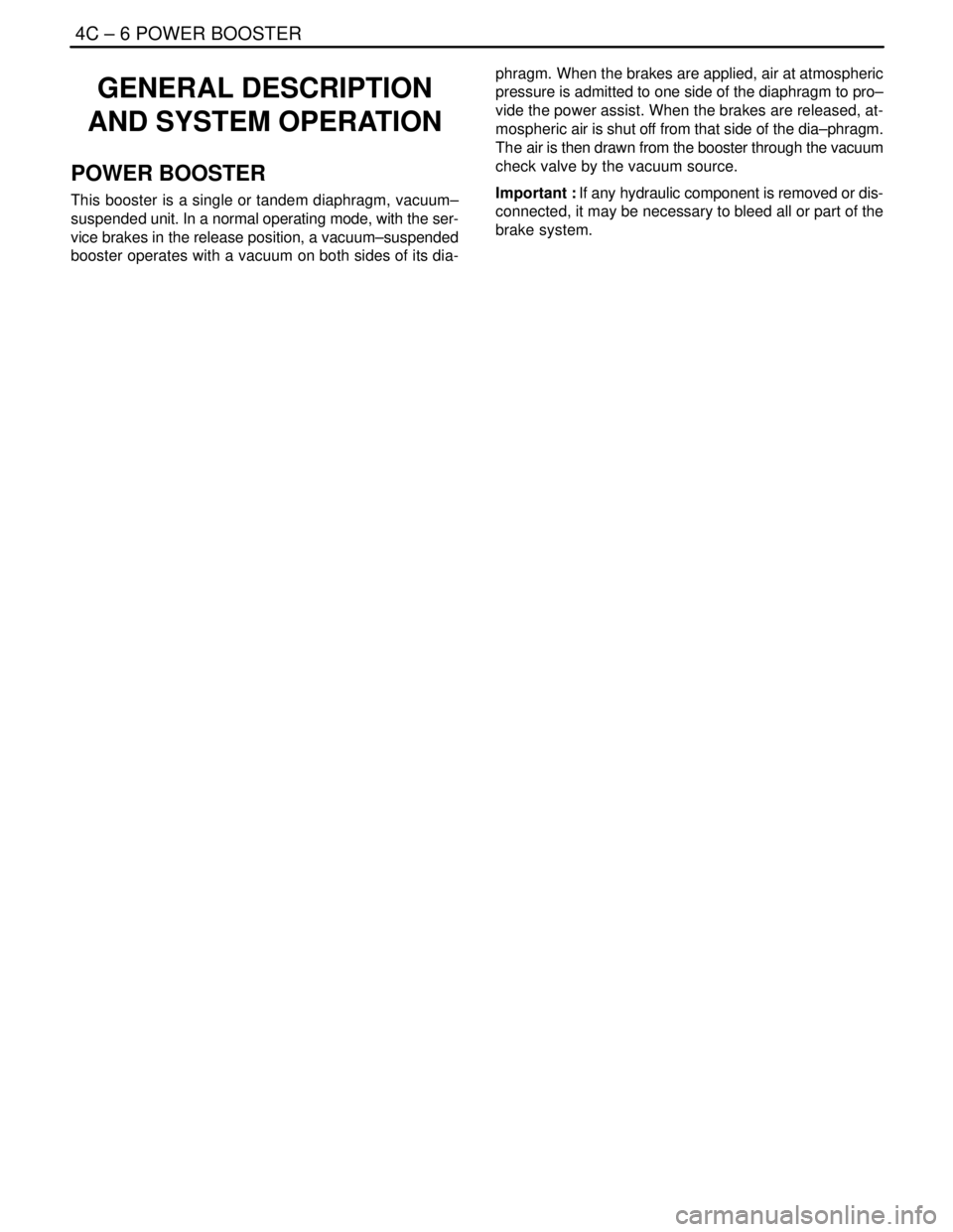
4C – 6IPOWER BOOSTER
DAEWOO V–121 BL4
GENERAL DESCRIPTION
AND SYSTEM OPERATION
POWER BOOSTER
This booster is a single or tandem diaphragm, vacuum–
suspended unit. In a normal operating mode, with the ser-
vice brakes in the release position, a vacuum–suspended
booster operates with a vacuum on both sides of its dia-phragm. When the brakes are applied, air at atmospheric
pressure is admitted to one side of the diaphragm to pro–
vide the power assist. When the brakes are released, at-
mospheric air is shut off from that side of the dia–phragm.
The air is then drawn from the booster through the vacuum
check valve by the vacuum source.
Important : If any hydraulic component is removed or dis-
connected, it may be necessary to bleed all or part of the
brake system.
Page 1049 of 2643
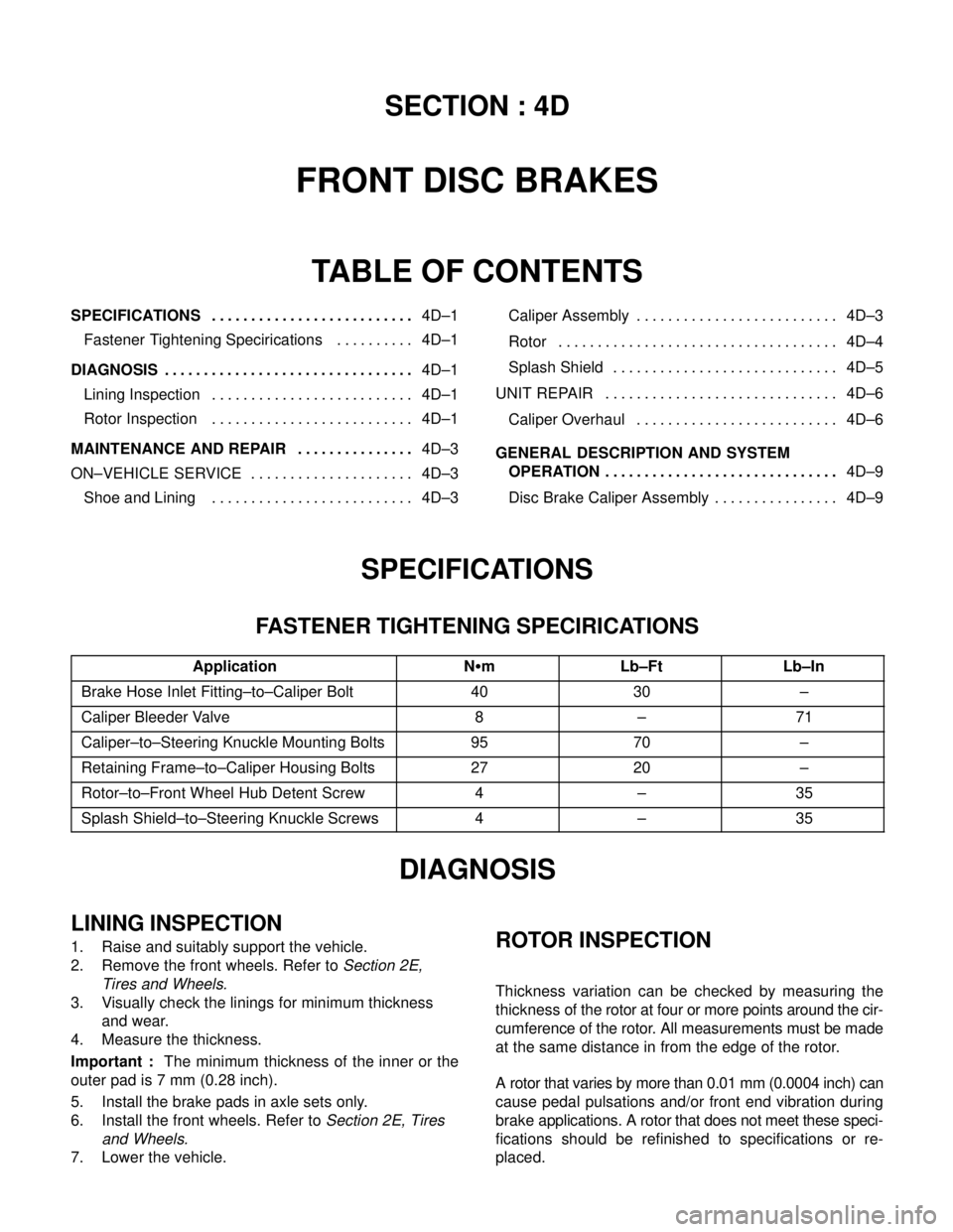
SECTION : 4D
FRONT DISC BRAKES
TABLE OF CONTENTS
SPECIFICATIONS4D–1 . . . . . . . . . . . . . . . . . . . . . . . . . .
Fastener Tightening Specirications 4D–1. . . . . . . . . .
DIAGNOSIS4D–1 . . . . . . . . . . . . . . . . . . . . . . . . . . . . . . . .
Lining Inspection 4D–1. . . . . . . . . . . . . . . . . . . . . . . . . .
Rotor Inspection 4D–1. . . . . . . . . . . . . . . . . . . . . . . . . .
MAINTENANCE AND REPAIR4D–3 . . . . . . . . . . . . . . .
ON–VEHICLE SERVICE 4D–3. . . . . . . . . . . . . . . . . . . . .
Shoe and Lining 4D–3. . . . . . . . . . . . . . . . . . . . . . . . . . Caliper Assembly 4D–3. . . . . . . . . . . . . . . . . . . . . . . . . .
Rotor 4D–4. . . . . . . . . . . . . . . . . . . . . . . . . . . . . . . . . . . .
Splash Shield 4D–5. . . . . . . . . . . . . . . . . . . . . . . . . . . . .
UNIT REPAIR 4D–6. . . . . . . . . . . . . . . . . . . . . . . . . . . . . .
Caliper Overhaul 4D–6. . . . . . . . . . . . . . . . . . . . . . . . . .
GENERAL DESCRIPTION AND SYSTEM
OPERATION4D–9 . . . . . . . . . . . . . . . . . . . . . . . . . . . . . .
Disc Brake Caliper Assembly 4D–9. . . . . . . . . . . . . . . .
SPECIFICATIONS
FASTENER TIGHTENING SPECIRICATIONS
ApplicationNSmLb–FtLb–In
Brake Hose Inlet Fitting–to–Caliper Bolt4030–
Caliper Bleeder Valve8–71
Caliper–to–Steering Knuckle Mounting Bolts9570–
Retaining Frame–to–Caliper Housing Bolts2720–
Rotor–to–Front Wheel Hub Detent Screw4–35
Splash Shield–to–Steering Knuckle Screws4–35
DIAGNOSIS
LINING INSPECTION
1. Raise and suitably support the vehicle.
2. Remove the front wheels. Refer to Section 2E,
Tires and Wheels.
3. Visually check the linings for minimum thickness
and wear.
4. Measure the thickness.
Important : The minimum thickness of the inner or the
outer pad is 7 mm (0.28 inch).
5. Install the brake pads in axle sets only.
6. Install the front wheels. Refer to Section 2E, Tires
and Wheels.
7. Lower the vehicle.ROTOR INSPECTION
Thickness variation can be checked by measuring the
thickness of the rotor at four or more points around the cir-
cumference of the rotor. All measurements must be made
at the same distance in from the edge of the rotor.
A rotor that varies by more than 0.01 mm (0.0004 inch) can
cause pedal pulsations and/or front end vibration during
brake applications. A rotor that does not meet these speci-
fications should be refinished to specifications or re-
placed.
Page 1050 of 2643
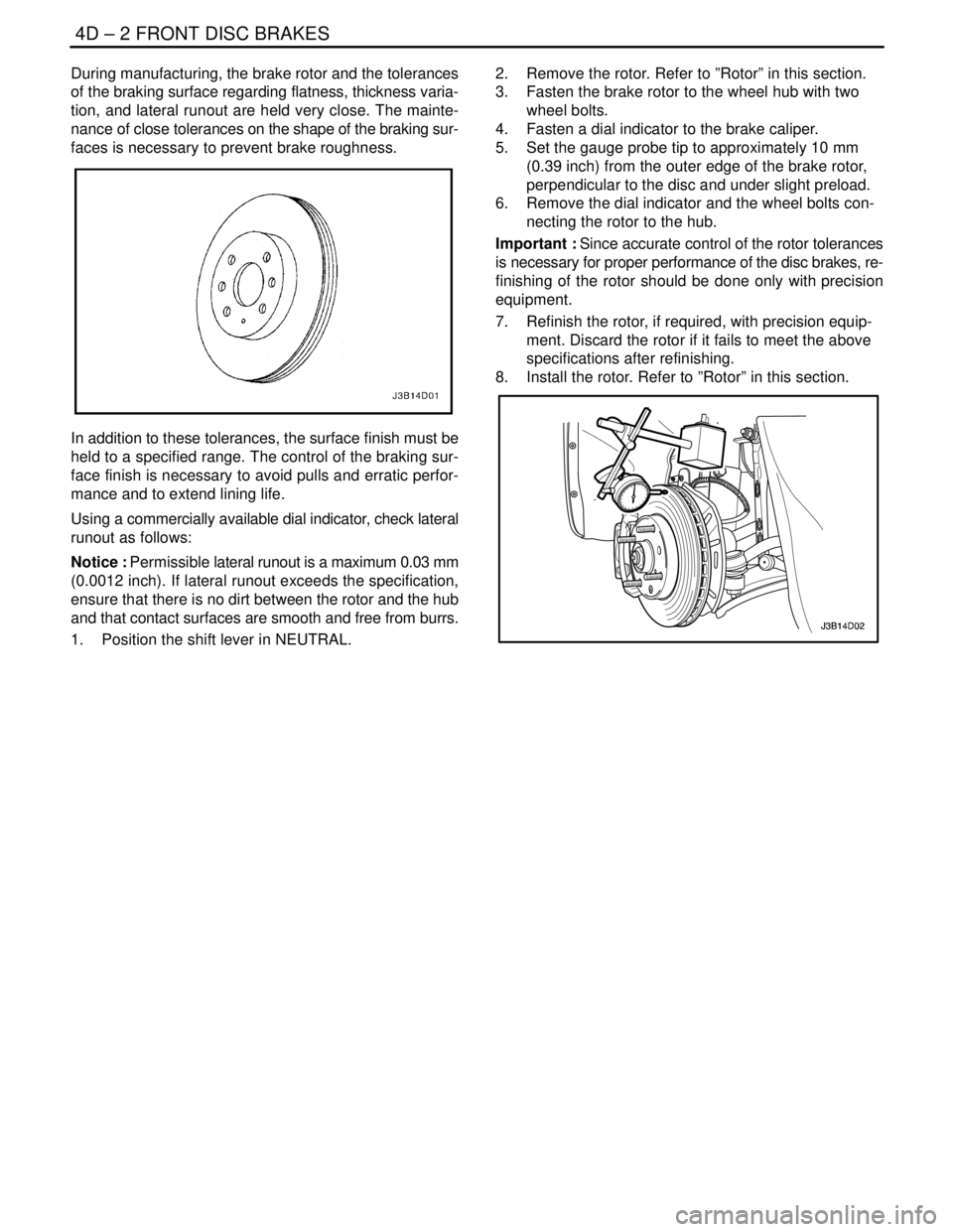
4D – 2IFRONT DISC BRAKES
DAEWOO V–121 BL4
During manufacturing, the brake rotor and the tolerances
of the braking surface regarding flatness, thickness varia-
tion, and lateral runout are held very close. The mainte-
nance of close tolerances on the shape of the braking sur-
faces is necessary to prevent brake roughness.
In addition to these tolerances, the surface finish must be
held to a specified range. The control of the braking sur-
face finish is necessary to avoid pulls and erratic perfor-
mance and to extend lining life.
Using a commercially available dial indicator, check lateral
runout as follows:
Notice : Permissible lateral runout is a maximum 0.03 mm
(0.0012 inch). If lateral runout exceeds the specification,
ensure that there is no dirt between the rotor and the hub
and that contact surfaces are smooth and free from burrs.
1. Position the shift lever in NEUTRAL.2. Remove the rotor. Refer to ”Rotor” in this section.
3. Fasten the brake rotor to the wheel hub with two
wheel bolts.
4. Fasten a dial indicator to the brake caliper.
5. Set the gauge probe tip to approximately 10 mm
(0.39 inch) from the outer edge of the brake rotor,
perpendicular to the disc and under slight preload.
6. Remove the dial indicator and the wheel bolts con-
necting the rotor to the hub.
Important : Since accurate control of the rotor tolerances
is necessary for proper performance of the disc brakes, re-
finishing of the rotor should be done only with precision
equipment.
7. Refinish the rotor, if required, with precision equip-
ment. Discard the rotor if it fails to meet the above
specifications after refinishing.
8. Install the rotor. Refer to ”Rotor” in this section.