charging DATSUN 210 1979 User Guide
[x] Cancel search | Manufacturer: DATSUN, Model Year: 1979, Model line: 210, Model: DATSUN 210 1979Pages: 548, PDF Size: 28.66 MB
Page 277 of 548
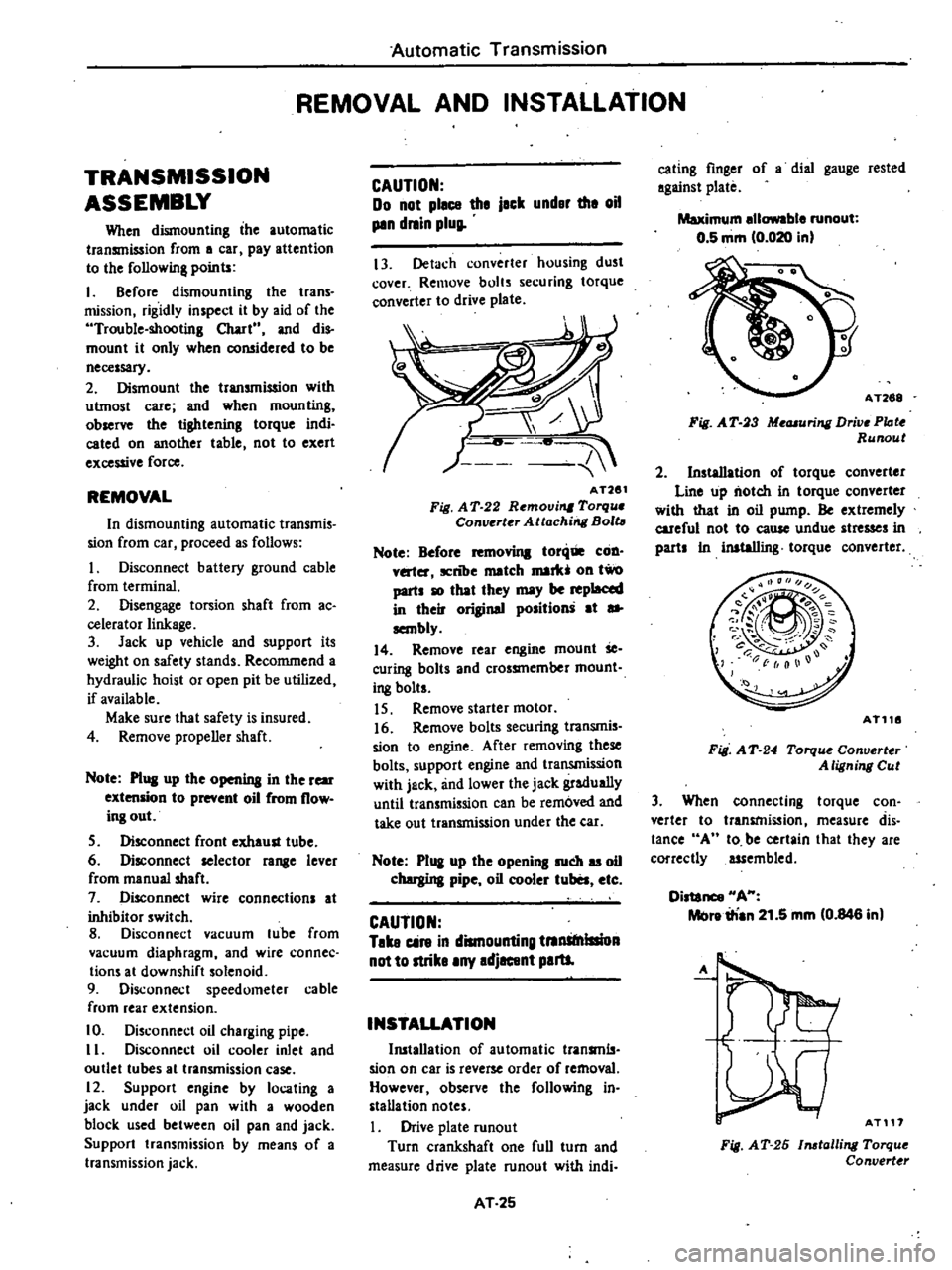
Automatic
Transmission
REMOVAL
AND
INSTALLATION
TRANSMISSION
ASSEMBLY
When
dismounting
the
automatic
transmission
from
a
car
pay
attention
to
the
following
points
I
Before
dismounting
the
trans
mission
rigidly
inspect
it
by
aid
of
the
Trouble
shooting
Chart
and
dis
mount
it
only
when
coll5idered
to
be
necessary
2
Dismount
the
transmission
with
utmost
care
and
when
mounting
observe
the
tightening
torque
indi
cated
on
another
table
not
to
exert
excessive
force
REMOVAL
In
dismounting
automatic
transmis
sion
from
car
proceed
as
follows
I
Disconnect
battery
ground
cable
from
terminal
2
Disengage
torsion
shaft
from
ac
eelerator
linkage
3
Jack
up
vehicle
and
support
its
weight
on
safety
stands
Recommend
a
hydraulic
hoist
or
open
pit
be
utilized
if
available
Make
sure
that
safety
is
insured
4
Remove
propeller
shaft
Note
Pl
ll
up
the
openina
in
the
rear
extension
to
prevent
oil
from
flow
ing
out
S
Disconnect
front
exhaust
tube
6
Disconnect
selector
ra
8e
lever
from
manual
shaft
7
Disconnect
wire
connections
at
inhibitor
switch
8
Disconnect
vacuum
lube
from
vacuum
diaphragm
and
wire
connee
tions
at
downshift
solenoid
9
Disconnect
speedometer
cable
from
rear
exlension
10
Disconnect
oil
charging
pipe
II
Disconnect
oil
cooler
inlet
and
outlet
tubes
al
transmission
case
12
Support
engine
by
locating
a
jack
under
oil
pan
with
a
wooden
block
used
between
oil
pan
and
jack
Support
transmission
by
means
of
a
transmission
jack
CAUTION
Do
not
plecs
the
jack
under
the
oil
pin
dnin
plug
13
Detach
converter
housing
dust
cover
Remove
bolts
securing
torque
converter
to
drive
plate
AT261
Fig
A
T
22
Removi
Torqu
Converter
Attachirrg
Bolt
Note
Before
toni
COD
v
ter
ICnlJe
match
mark
011
two
parts
10
that
they
may
be
replaced
in
their
original
position
at
sa
sembly
14
Remove
rear
engine
mount
Se
curing
bolts
and
crossmember
mount
i
8
bolts
IS
Remove
starter
motor
16
Remove
bolts
securing
transmis
sion
to
engine
After
removing
these
bolts
support
engine
and
transmission
with
jack
and
lower
the
jack
gradually
until
transmission
can
be
removed
and
take
out
transmission
under
the
ear
Note
P1
I
up
the
opening
such
u
oil
chergina
pipe
oil
cooler
tuba
etc
CAUTION
Take
cin
in
dismounting
tnnStnlllioA
not
to
strike
any
adjacent
paru
INSTALLATION
Ill5tallation
of
automatic
transmls
sian
on
car
is
reverse
order
of
removal
However
observe
the
following
in
stallation
notes
Drive
plate
runout
Turn
crankshaft
one
full
turn
and
measure
drive
plate
runout
with
indi
AT
25
eating
finger
of
a
dial
gauge
rested
against
plate
Maximum
ellowable
runout
0
5
mm
0
020
in
AT268
Fig
A
T
3
Me
uring
Drive
PIote
Runout
2
Installation
of
torque
converter
Line
up
notch
in
torque
converter
with
that
in
oil
pump
Be
extremely
careful
not
to
eause
undue
stresses
in
parts
In
inataIIing
torque
converter
AT116
Fig
A
T
24
Torqu
Converter
A
ligning
Cut
3
When
connecting
torque
con
verter
to
transmission
measure
dis
tance
A
10
be
certain
that
they
are
correctly
assembled
Distance
HA
Melre
irian
21
5
mm
0
846
in
A
AT117
Fig
AT
26
1116talling
Torque
Convert
r
Page 291 of 548
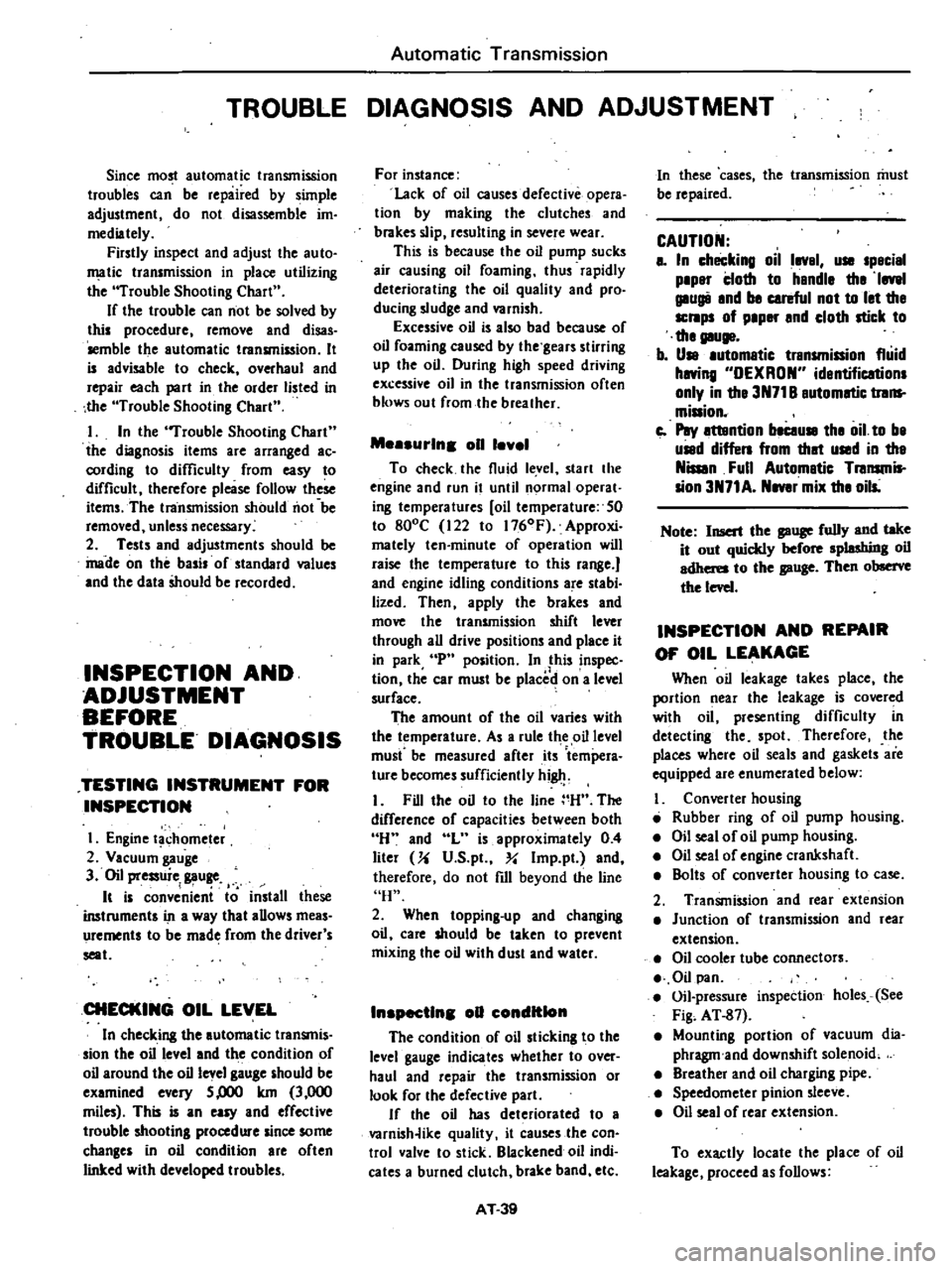
Automatic
Transmission
TROUBLE
DIAGNOSIS
AND
ADJUSTMENT
Since
mo
automatic
transmission
troubles
can
be
repaired
by
simple
adjustment
do
not
disassemble
im
media
tely
Firstly
inspect
and
adjust
the
auto
D1
3tic
transmission
in
place
utilizing
the
Trouble
Shooting
Chart
If
the
trouble
can
not
be
solved
by
this
procedure
remove
and
disas
semble
the
automatic
tlllnsmission
It
is
advisable
to
check
overhaul
and
repair
each
part
in
the
order
listed
in
the
Trouble
Shooting
Chart
In
the
Trouble
Shooting
Chart
the
diagnosis
items
are
arranged
ac
cording
to
difficulty
from
easy
to
difficult
therefore
please
follow
these
items
The
tlllnsmission
should
riot
be
removed
unless
necessary
2
Tests
and
adjustments
should
be
inade
on
the
basil
of
standard
values
and
the
data
Should
be
recorded
INSPECTION
AND
ADJUSTMENT
BEFORE
TROUBLE
DIAGNOSIS
TESTING
INSTRUMENT
FOR
INSPECTION
I
Engine
t
chometer
2
Vacuum
gauge
3
Oil
pressure
gauge
It
is
convenieni
to
install
these
instruments
in
a
way
that
allows
meas
urements
to
be
made
from
the
driver
s
seat
CHECKING
OIL
LEVEL
In
checkIng
the
automatic
transmis
sion
the
oil
level
and
the
condition
of
oil
around
the
oil
level
gauge
should
be
examined
every
S
ooo
Ion
3
000
miles
This
is
an
easy
and
effective
trouble
shooting
procedure
since
some
changes
in
oil
condition
are
often
linked
with
developed
troubles
For
instance
Lack
of
oil
causes
defective
opera
tion
by
making
the
clutches
and
brakes
slip
resulting
in
severe
wear
This
is
because
the
oil
pump
sucks
air
causing
oil
foaming
thus
rapidly
deteriorating
the
oil
quality
and
pro
ducing
sludge
and
varnish
Excessive
oil
is
also
bad
because
of
oil
foaming
caused
by
the
gears
stirring
up
the
oil
During
high
speed
driving
excessive
oil
in
the
transmission
often
hlows
out
from
the
brealher
Me
urlns
011
level
To
check
the
nuid
leyel
sian
Ihe
engine
and
run
it
until
normal
operat
ing
temperatures
oil
temperature
SO
to
800C
122
to
1160F
Approxi
mately
ten
minute
of
operation
will
raise
the
temperature
to
this
range
and
engine
idling
conditions
are
stabi
lized
Then
apply
the
brakes
and
move
the
transmission
shift
lever
through
aU
drive
positions
and
place
it
in
park
P
position
In
his
inspec
tion
the
car
must
be
placc
d
on
a
level
surface
The
amount
of
the
oil
varies
with
the
temperature
As
a
rule
the
oil
level
must
be
measured
after
its
tempera
ture
becomes
sufficiently
high
I
Fill
the
oil
to
the
line
H
The
difference
of
capacities
between
both
H
and
L
is
approximately
0
4
liter
J
U
S
pt
Y
Imp
pt
and
therefore
do
not
fill
beyond
the
line
H
2
When
topping
up
and
changing
oil
care
should
be
taken
to
prevent
mixing
the
oil
with
dusl
and
water
In
pectlns
oU
condition
The
condition
of
oil
sticking
to
the
level
gauge
indicates
whether
to
OVOl
haul
and
repair
the
transmission
or
luok
for
Ihe
defective
part
If
the
oil
has
deteriorated
to
a
varnish
ike
quality
it
causes
the
con
trol
valve
to
stick
Blackened
oil
indi
cates
a
burned
clutch
brake
band
etc
AT
39
In
these
cases
the
transmission
must
be
repaired
CAUTION
I
In
checking
oil
IlVal
use
special
piper
Cloth
tohandla
the
18V81
llIugi
Ind
be
careful
not
to
let
the
scraps
of
paper
end
cloth
stick
to
the
IlIUp
b
U
lutomatic
transmission
fluid
having
OEXRON
ida
ons
only
in
the
3N71
B
eutomatic
trans
mission
c
Pay
IttBntion
blcau
the
oil
to
be
used
differs
from
that
used
in
the
Nissen
Full
Autometic
TllInsmis
sion
3N71A
N8V8r
mill
thl
oils
Note
Insert
the
gauge
fully
and
take
it
out
quickly
before
splesbing
oil
edheres
to
the
gauge
Then
observe
the
level
INSPECTION
AND
REPAIR
OF
OIL
LEAKAGE
When
oil
leakage
takes
place
the
portion
near
the
leakage
is
covered
with
oil
presenting
difficulty
in
detecting
the
spot
Therefore
the
places
where
oil
seals
and
gaskets
are
equipped
are
enumerated
below
Converter
housing
Rubber
ring
of
oil
pump
housing
Oil
seal
of
oil
pump
housing
Oil
seal
of
engine
crankshaft
Bolts
of
converter
housing
to
case
2
Transmission
and
rear
extension
Junction
of
transmission
and
rear
extension
Oil
cooler
tube
connectors
Oil
pan
Oil
pressure
inspection
holes
See
Fig
AT
81
Mounting
portion
of
vacuum
dia
phragm
and
downshift
solenoid
Breather
and
oil
charging
pipe
Speedometer
pinion
sleeve
Oil
seal
of
rear
extension
To
exactly
locate
Ihe
place
of
oil
leakage
proceed
as
follows
Page 300 of 548
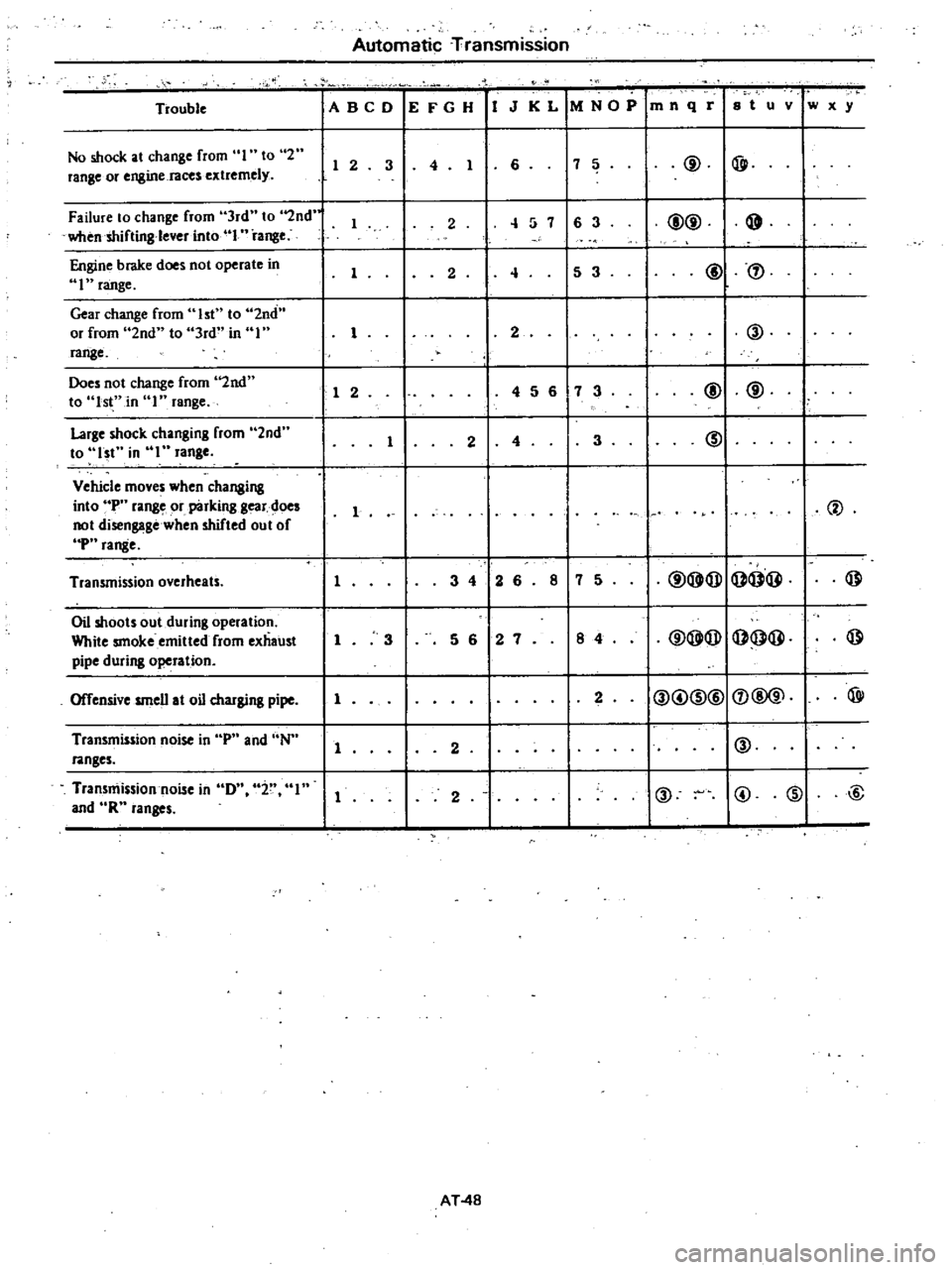
Automatic
Transmission
Trouble
ABeD
E
FG
H
1
J
KL
MNOP
mnqr
8
t
u
v
w
x
y
No
shock
at
change
from
I
to
2
6
7
5
@
@
lange
or
engine
races
extlemely
1
2
3
4
1
Failure
to
change
from
3rd
to
2nd
1
2
4
7
6
3
@@
@
when
shifting
lever
into
I
range
Engine
brake
does
not
operate
in
1
2
4
5
3
@
I
range
Gear
change
from
1st
to
2nd
or
from
2nd
to
3rd
in
1
1
2
@
range
Does
not
change
from
200
1
2
4
5
6
7
3
@
@
to
lst
in
1
range
Large
shock
changing
from
2nd
1
2
4
3
@
to
lst
in
I
range
Vehicle
moves
when
changing
into
P
range
or
pinking
gear
doe
1
2
not
disengage
when
shifted
out
of
P
range
Transmission
overheats
1
3
4
2
6
8
7
5
@@@
@@@
@
Oil
shoots
out
during
operation
White
smoke
emitted
from
exhaust
1
3
5
6
2
7
8
4
@@@
@@@
@
pipe
during
operation
Offensive
smeU
at
oil
charging
pipe
1
2
@@@@
@@
@i
Transmission
noise
in
p
and
ON
1
2
@
ranges
Transmission
noise
in
D
i
I
1
2
@
@
@
@
and
R
langes
AT
48
Page 447 of 548
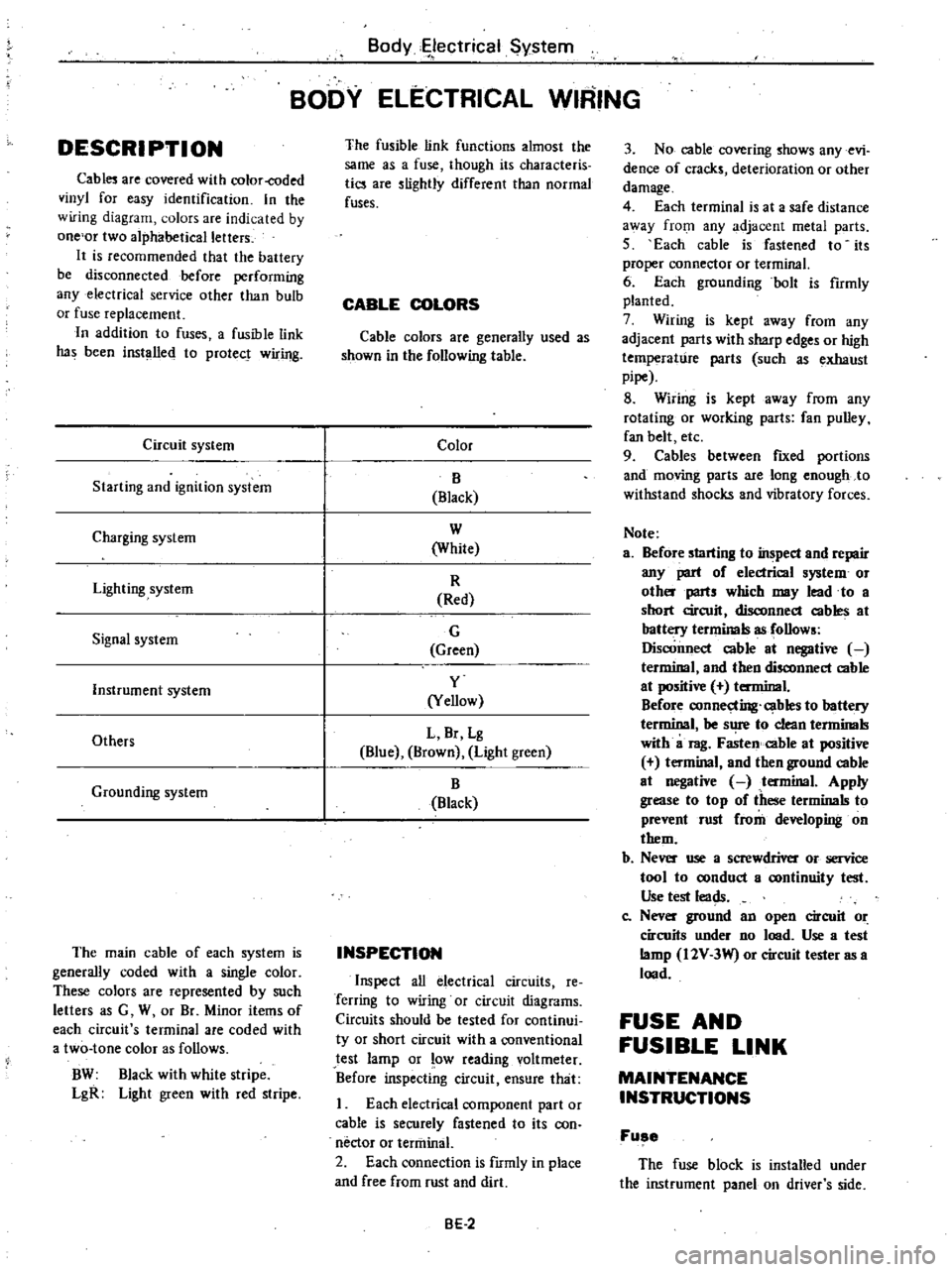
DESCRI
PTI
ON
Cabl
are
covered
with
color
coded
vinyl
for
easy
identification
In
the
wiring
diagram
olors
are
indicated
by
one
or
two
alphabetical
letters
It
is
recommended
that
the
battery
be
disconnected
before
performing
any
electrical
service
other
than
bulb
or
fuse
replacement
In
addition
to
fuses
a
fusible
link
has
been
installed
to
protect
wiring
Circuit
system
Starting
and
ignition
system
Charging
system
Lighting
system
Signal
system
Instrument
system
Others
Grounding
system
The
main
cable
of
each
system
is
generally
coded
with
a
single
color
These
colors
are
represented
by
such
letters
as
G
W
or
Br
Minor
items
of
each
circuit
s
terminal
are
coded
with
a
two
tone
color
as
follows
BW
Black
with
white
stripe
LgR
Light
green
with
red
stripe
Body
ectrical
System
BODY
ELECTRICAL
WIRING
The
fusible
link
functions
almost
the
same
as
a
fuse
though
its
characteris
tics
are
slightly
different
than
normal
fuses
CABLE
COLORS
Cable
colors
are
generally
used
as
shown
in
the
following
table
Color
B
Black
W
White
R
Red
G
Green
y
Yellow
L
Br
Lg
Blue
Brown
Light
green
B
Black
INSPECTION
Inspect
all
electrical
circuits
Ie
Terring
to
wiring
or
circuit
diagrams
Circuits
should
be
tested
for
continui
ty
or
short
circuit
with
a
conventional
test
lamp
or
low
reading
voltmeter
Before
inspecting
circuit
ensure
that
I
Each
electrical
component
part
or
cable
is
securely
fastened
to
its
con
nector
or
tenninal
2
Each
connection
is
fIrmly
in
place
and
free
from
rust
and
dirt
BE
2
3
No
cable
covering
shows
any
evi
dence
of
cracks
deterioration
or
other
damage
4
Each
terminal
is
at
a
safe
distance
3
Vay
from
any
adjacent
metal
parts
5
Each
cable
is
fastened
to
its
proper
connector
or
terminal
6
Each
grounding
bolt
is
fumly
planted
7
Wiring
is
kept
away
from
any
adjacent
parts
with
sharp
edges
or
high
temperature
parts
such
as
exhaust
pipe
8
Wiring
is
kept
away
from
any
rotating
or
working
parts
fan
pulley
fan
belt
etc
9
Cables
between
fIXed
portions
and
moving
parts
are
long
enough
to
withstand
shocks
and
vibratory
forces
Note
a
Before
starting
to
inspect
and
repair
any
part
of
electrical
system
or
oth
parts
which
may
lead
to
a
short
circuit
disconnect
cables
at
battery
terminals
as
follows
Disconnect
cable
at
negative
terminal
and
then
disconnect
cable
at
positive
terminal
Before
connecting
cables
to
battery
terminal
be
s
1
to
clean
tenninals
with
a
rag
Fasten
cable
at
positive
t
minal
and
then
ground
cable
at
negative
tenninal
Apply
grease
to
top
of
these
terminals
to
prevent
rust
from
developing
on
them
b
Ne
use
a
screwdriver
or
service
tool
to
oonduct
a
oontinuity
test
Use
test
leads
Co
Nev
ground
an
open
circuit
or
circuits
under
no
lood
Use
a
test
lamp
I2V
3W
or
circuit
tester
as
a
lood
FUSE
AND
FUSIBLE
LINK
MAINTENANCE
INSTRUCTIONS
Fuse
The
fuse
block
is
installed
under
the
instrument
panel
on
driver
s
side
Page 480 of 548
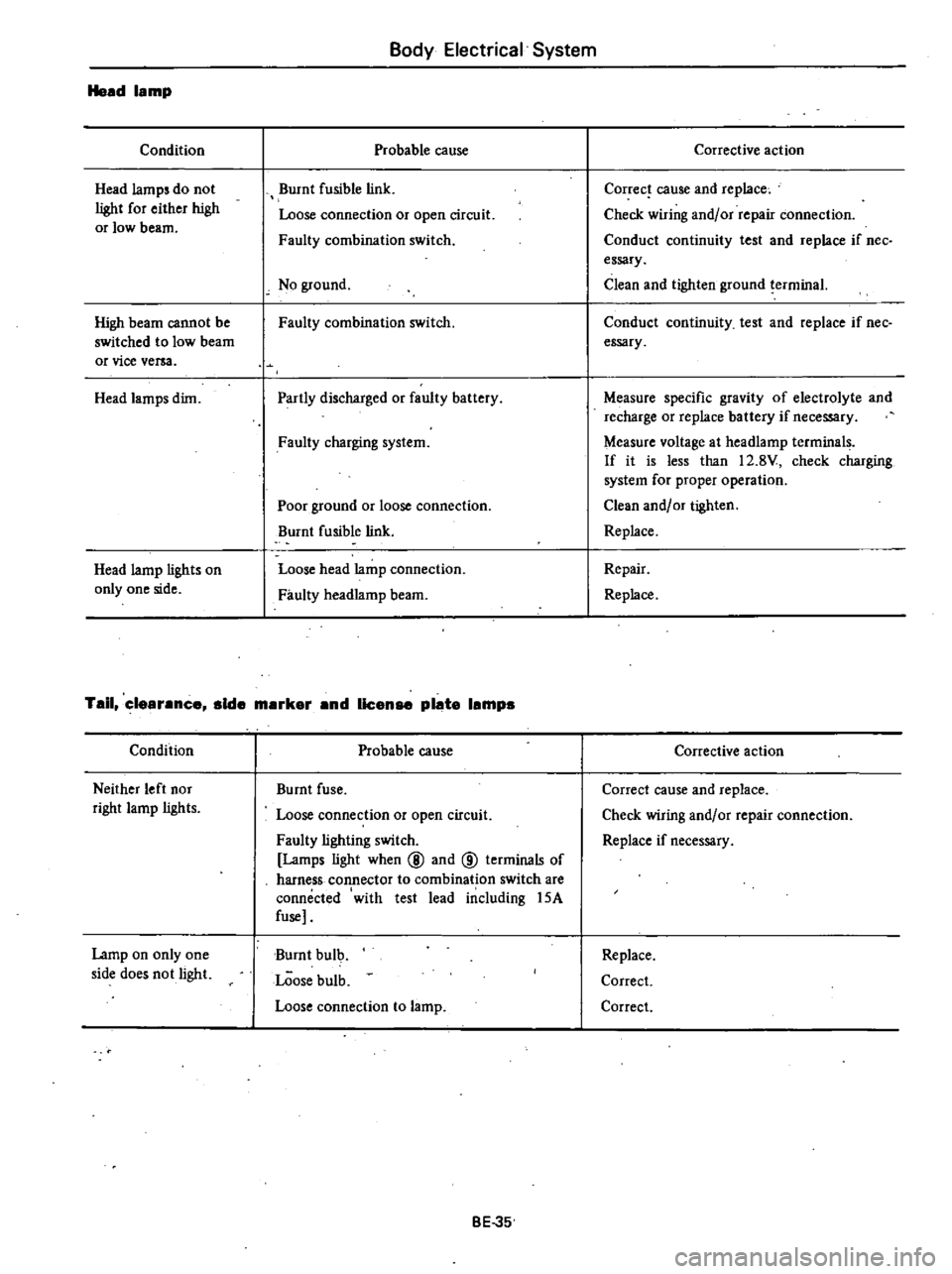
Head
lamp
Condition
Head
lamp
do
not
light
for
either
high
or
low
beam
High
beam
cannot
be
switched
to
low
beam
or
vice
versa
Head
lamps
dim
Head
lamp
lights
on
only
one
side
Body
Electrical
System
Probable
cause
Burnt
fusible
link
Loose
connection
or
open
circuit
Faulty
combination
switch
No
ground
Faulty
combination
switch
Partly
discharged
or
faulty
battery
Faulty
charging
system
Poor
ground
or
loose
connection
Burnt
fusible
link
Loose
head
lamp
connection
Faulty
headlamp
beam
Tail
clearance
aide
marker
and
license
plate
lampa
Condition
Neither
left
nor
right
lamp
lights
Lamp
on
only
one
side
does
not
light
Probable
cause
Burnt
fuse
Loose
connection
or
open
circuit
Faulty
lighting
switch
Lamps
light
when
@
and
@
terminals
of
harness
connector
to
combination
switch
are
connected
with
test
lead
iIlc1uding
15A
fuse
Burnt
bulb
LOose
bulb
Loose
connection
to
lamp
BE
35
Corrective
action
Corree
cause
and
rep1ace
Check
wiring
and
or
repair
connection
Conduct
continuity
test
and
replace
if
nee
essary
Clean
and
tighten
ground
terminal
Conduct
continuity
test
and
replace
if
nee
essary
Measure
specific
gravity
of
electrolyte
and
recharge
or
replace
battery
if
necessary
Measure
voltage
at
headlamp
terminals
If
it
is
less
than
12
8V
check
charging
system
for
proper
operation
Clean
and
or
tighten
Replace
Repair
Replace
Corrective
action
Correct
cause
and
replace
Check
wiring
and
or
repair
connection
Replace
if
necessary
Replace
Correct
Correct
Page 491 of 548
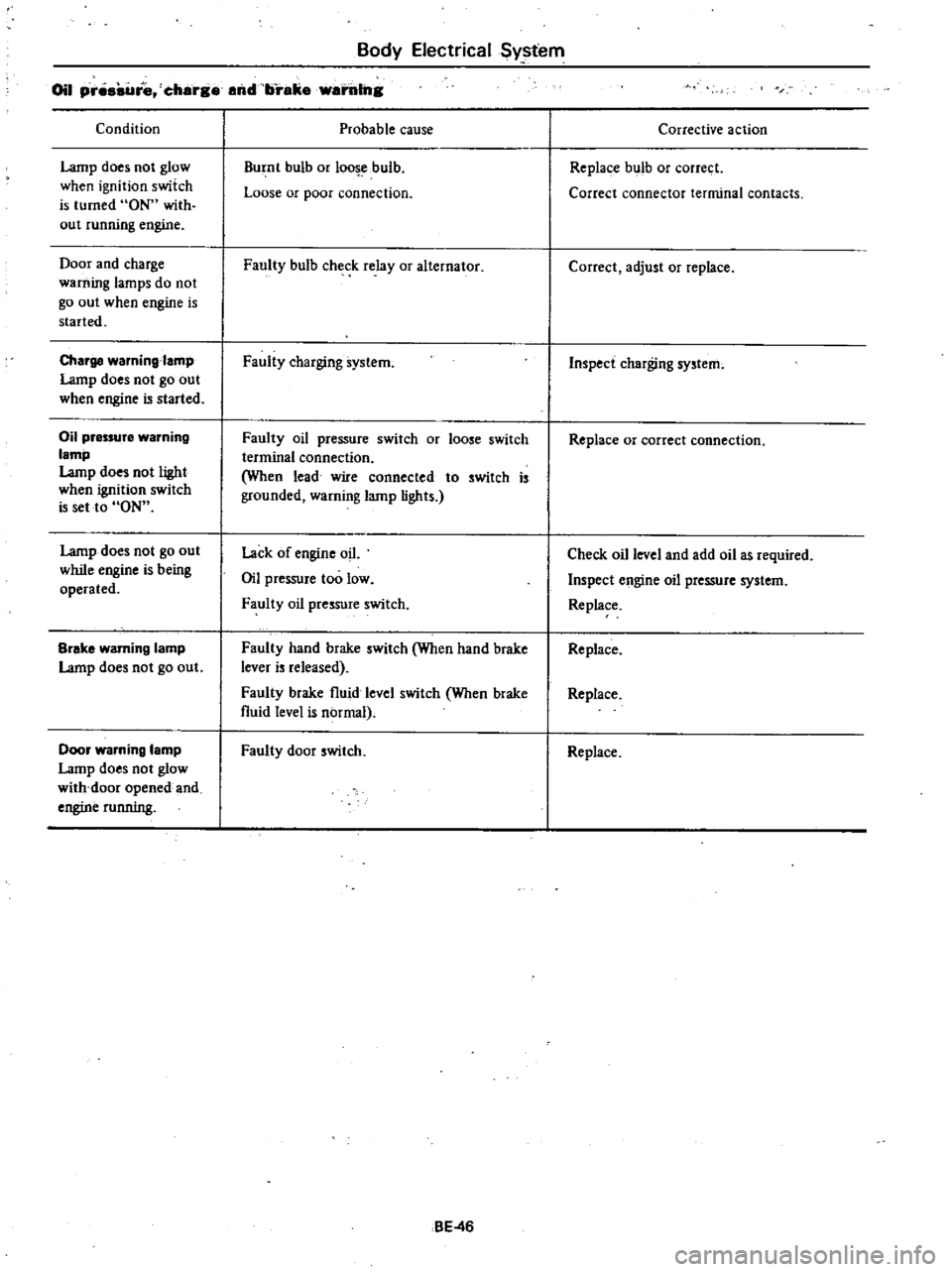
Body
Electrical
Sy
tem
Oil
pr
re
charg
and
brake
warillng
Condition
Lamp
does
not
glow
when
ignition
switch
is
turned
ON
with
out
running
engine
Door
and
charge
warning
lamps
do
not
go
out
when
engine
is
started
Charge
waming
amp
Lamp
does
not
go
out
when
engine
is
started
Oil
pressure
warning
lamp
Lamp
does
not
light
when
ignition
switch
is
set
to
ON
Lamp
does
not
go
out
while
engine
is
being
operated
Brake
warning
lamp
Lamp
does
not
go
out
Door
warning
lamp
Lamp
does
not
glow
with
door
opened
and
engine
running
Probable
cause
Burnt
bulb
or
loo
ebulb
Loose
or
poor
connection
Faully
bulb
check
relay
or
alternator
Faully
charging
system
Faully
oil
pressure
switch
or
loose
switch
terminal
connection
When
lead
wire
connected
to
switch
is
grounded
warning
lamp
lights
Lack
of
engine
oil
Oil
pressure
too
low
Faully
oil
pressure
switch
Faulty
hand
brake
switch
When
hand
brake
lever
is
released
Faully
brake
fluid
level
switch
When
brake
fluid
level
is
normal
Faully
door
switch
BE
46
Corrective
action
Replace
bulb
or
correct
Correct
connector
terminal
contacts
Correct
adjust
or
replace
Inspect
charging
system
Replace
or
correct
connection
Check
oil
level
and
add
oil
as
required
Inspect
engine
oil
pressure
system
Replace
Replace
Replace
Replace
Page 499 of 548
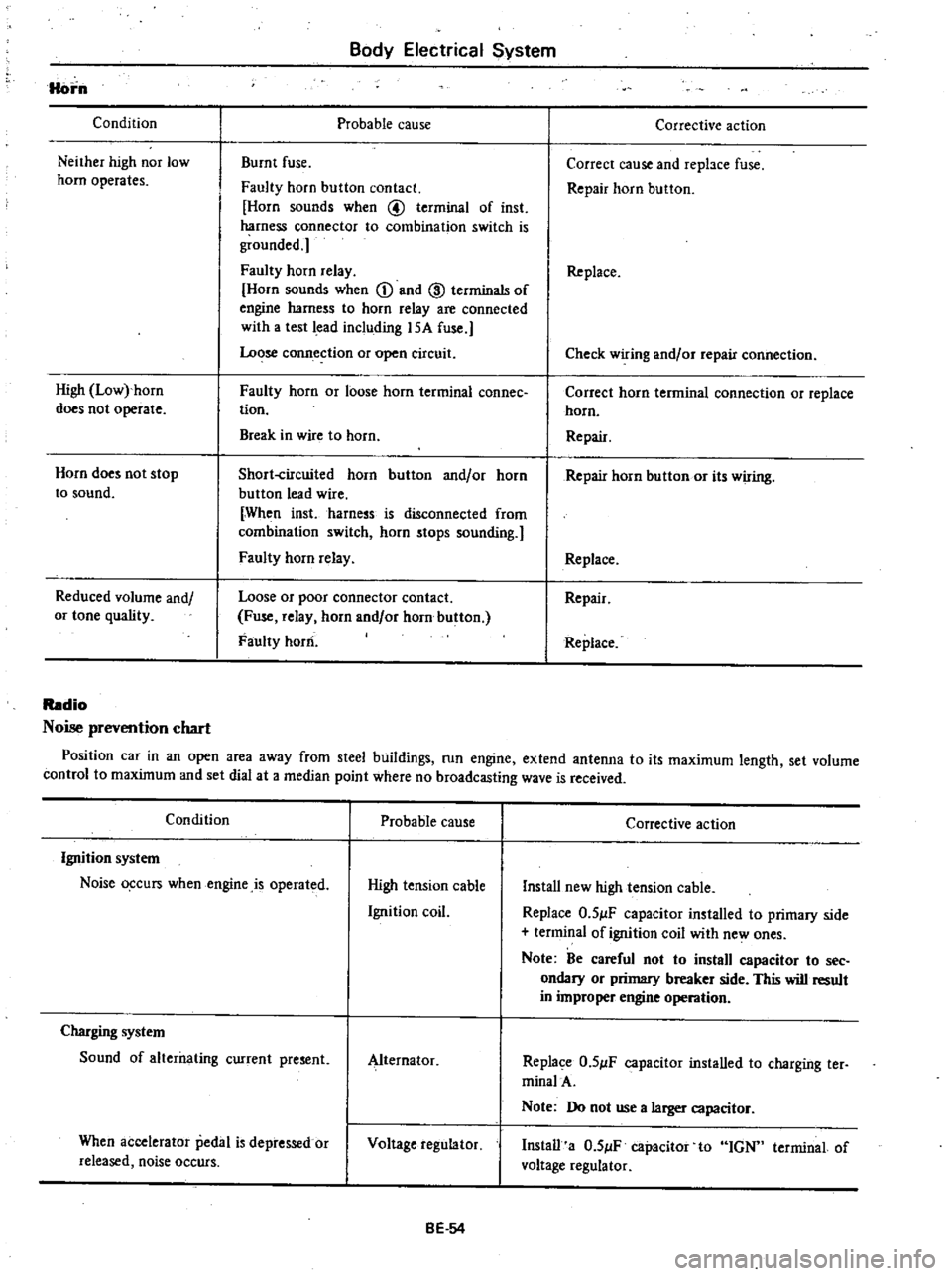
Horn
Condition
Neither
high
nor
low
horn
operates
High
Low
horn
does
not
operate
Horn
does
not
stop
to
sound
Reduced
volume
and
or
tone
quality
Body
Electrical
System
Probable
cause
Burnt
fuse
Faulty
horn
button
contact
Horn
sounds
when
@
terminal
of
inst
harness
connector
to
combination
switch
is
grounded
Faulty
horn
relay
Horn
sounds
when
CD
and
ID
terminals
of
engine
harness
to
horn
relay
are
connected
with
a
test
lead
including
15A
fuse
Lo
se
conn
ection
or
open
circuit
Faulty
horn
or
loose
horn
terminal
connee
tion
Break
in
wire
to
horn
Short
circuited
horn
button
and
or
horn
button
lead
wire
When
inst
harness
is
disconnected
from
combination
switch
horn
stops
sounding
Faulty
horn
relay
Loose
or
poor
connector
contact
Fuse
relay
horn
and
or
horn
button
Faulty
horn
Corrective
action
Correct
cause
and
repbce
fuse
Repair
horn
button
Replace
Check
wiring
and
or
repair
connection
Correct
horn
terminal
connection
or
replace
horn
Repair
Repair
horn
button
or
its
wiring
Replace
Repair
Replace
Radio
Noise
prevention
chart
Position
car
in
an
open
area
away
from
steel
buildings
run
engine
extend
antenna
to
its
maximum
length
set
volume
control
to
maximum
and
set
dial
at
a
median
point
where
no
broadcasting
wave
is
received
Condition
Probable
cause
Ignition
system
Noise
o
curs
when
engine
is
operated
High
tension
cable
Ignition
coil
Charging
system
Sound
of
alterilating
current
present
Alternator
When
accelerator
pedal
is
depressed
or
released
noise
occurs
Voltage
regulator
BE
54
Corrective
action
Install
new
high
tension
cable
Replace
O
5
lF
capacitor
installed
to
primary
side
terminal
of
ignition
coil
with
ne
ones
Note
Be
careful
not
to
install
capacitor
to
see
ondary
or
primary
breaker
side
This
will
result
in
improper
engine
operation
Replace
O
5
lF
capacitor
installed
to
charging
ter
minalA
Note
Do
not
use
a
larger
capacitor
Install
a
O
5
lF
capacitor
to
IGN
terminal
of
voltage
regulator
Page 502 of 548
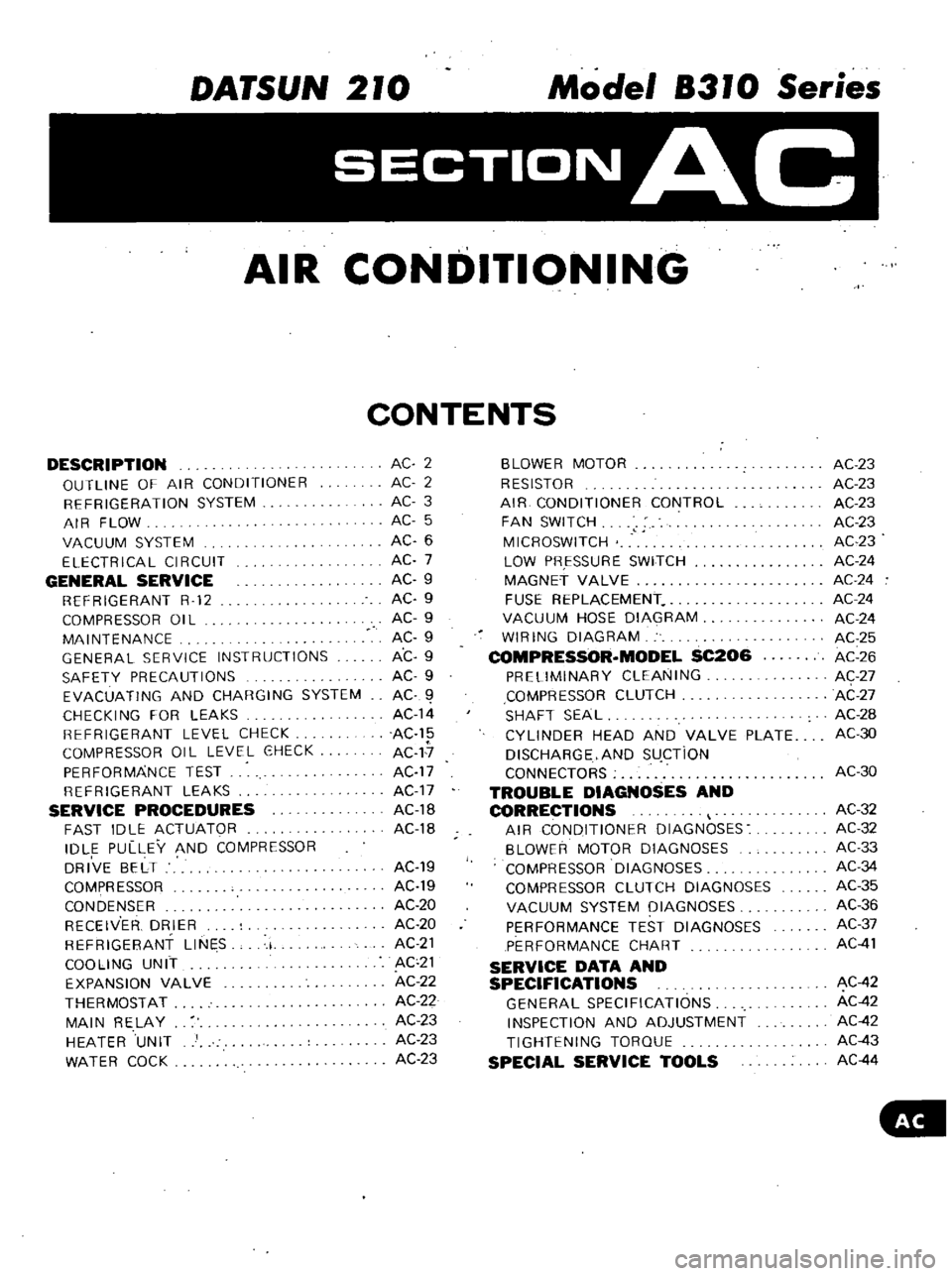
DATSUN
210
Model
8310
Series
SECTIONAC
AIR
CONDITIONING
CONTENTS
DESCRIPTION
OUTLINE
OF
AIR
CONDITIONER
REFRIGERATION
SYSTEM
AIR
FLOW
VACUUM
SYSTEM
ELECTRICAL
CIRCUIT
GENERAL
SERVICE
REFRIGERANT
R
12
COMPRESSOR
OIL
MAINTENANCE
GENERAL
SERVICE
INSTRUCTIONS
SAFETY
PRECAUTIONS
EVACUATING
AND
CHARGING
SYSTEM
CHECKI
NG
FOR
LEAKS
REFRIGERANT
LEVEL
CHECK
COMPRESSOR
OIL
LEVEL
OHECK
PERFORMANCE
TEST
REFRIGERANT
LEAKS
SERVICE
PROCEDURES
FAST
IDLE
ACTUATOR
IDL
E
PULLEY
AND
COMPRESSOR
DRIVE
BELT
COMPR
ESSOR
CONDENSER
RECEIV
ER
DRIER
REFRIGERANT
LINES
I
COOLING
UNIT
EXPANSION
VALVE
THERMOSTAT
MAIN
RELAY
HEATER
UNIT
WATER
COCK
AC
2
AC
2
AC
3
AC
5
AC
6
AC
7
AC
9
AC
9
AC
9
AC
9
AC
9
AC
9
AC
1
AC14
AC15
AC
17
AC17
AC17
AC18
AC1B
AC19
AC19
AC
20
AC
20
AC
21
ACc21
AC
22
AC
22
AC
23
AC
23
AC
23
BLOWER
MOTOR
RESISTOR
AIR
CONDITIONER
CONTROL
FAN
SWITCH
MICROSWITCH
LOW
PRESSURE
SWITCH
MAGNET
VALVE
FUSE
REPLACEMENT
VACUUM
HOSE
DIAGRAM
WIRING
DIAGRAM
COMPRESSOR
MODEL
SC206
PRELIMINARY
CLEANING
COMPRESSOR
CLUTCH
SHAFT
SEAL
CYLINDER
HEAD
AND
VALVE
PLATE
DISCHARGE
AND
sU
CTiON
CONNECTORS
TROUBLE
DIAGNOSES
AND
CORRECTIONS
AIR
CONDITIONER
DIAGNOSES
BLOWER
MOTOR
DIAGNOSES
COMPRESSOR
DIAGNOSES
COMPRESSOR
CLUTCH
DIAGNOSES
VACUUM
SYSTEM
DIAGNOSES
PERFORMANCE
TEST
DIAGNOSES
PERFORMANCE
CHART
SERVICE
DATA
AND
SPECIFICATIONS
GENERAL
SPECIFICATIONS
INSPECTION
AND
ADJUSTMENT
TIGHTENING
TORQUE
SPECIAL
SERVICE
TOOLS
AC
23
AC
23
AC
23
AC
23
AC23
AC
24
AC
24
AC24
AC
24
AC
25
AC
26
AC
27
AC
27
AC
28
AC30
AC30
AC32
AC
32
AC
33
AC34
AC35
AC36
AC37
AC
41
AC
42
AC
42
AC
42
AC
43
AC
44
Page 510 of 548
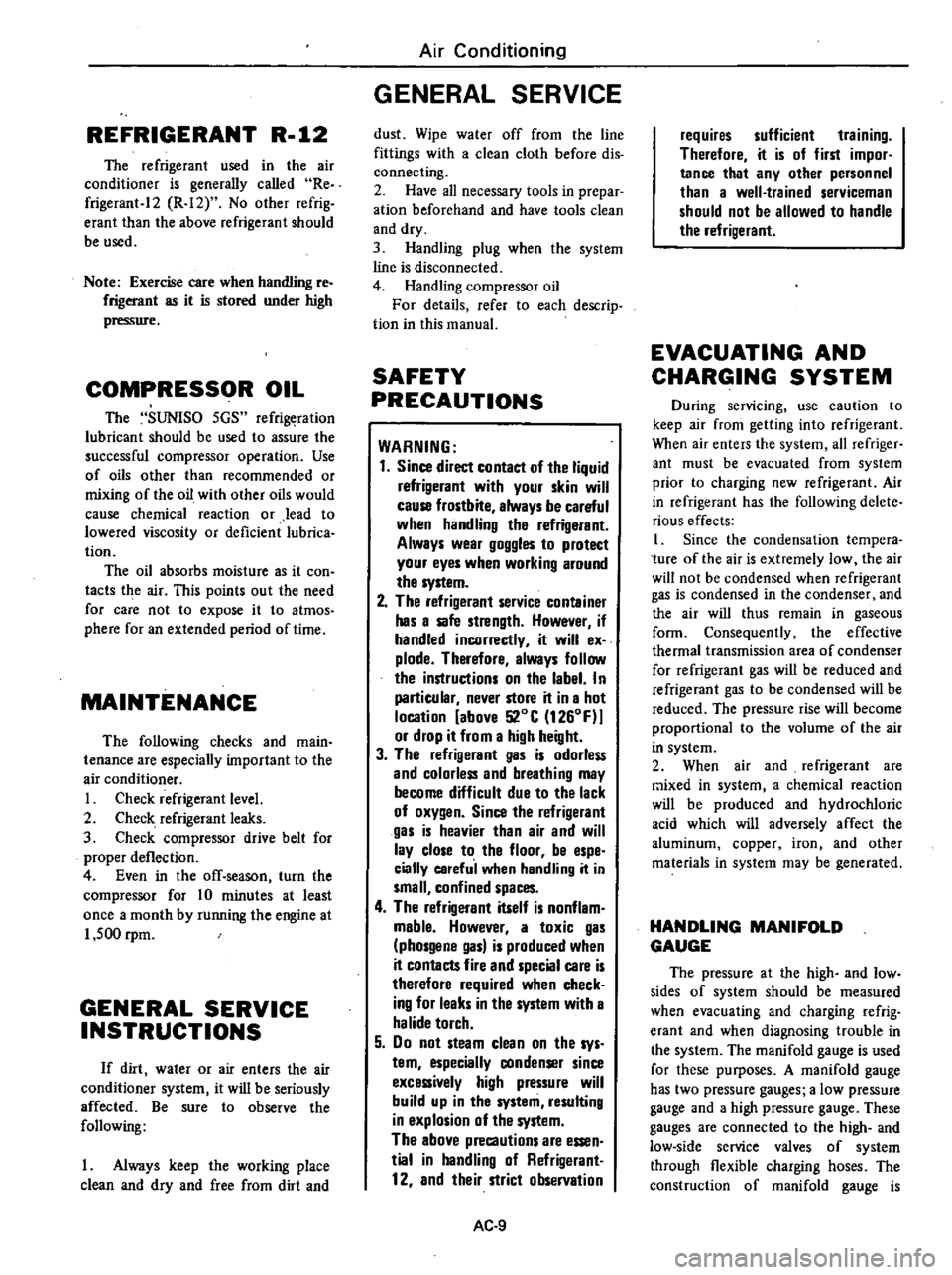
REFRIGERANT
R
12
The
refrigerant
used
in
the
air
conditioner
is
generally
called
Re
frigerant
12
R
12
No
other
refrig
erant
than
the
above
refrigerant
should
be
used
Note
Exercise
care
when
handling
re
frigerant
as
it
is
stored
under
high
pressure
COMPRESSOR
OIL
The
SUNISO
5GS
refrig
ration
lubricant
should
be
used
to
assure
the
successful
compressor
operation
Use
of
oils
other
than
recommended
or
mixing
of
the
oil
with
other
oils
would
cause
chemical
reaction
or
lead
to
lowered
viscosity
or
deficient
lubrica
tion
The
oil
absorbs
moisture
as
it
con
tacts
the
air
This
points
out
the
need
for
care
not
to
expose
it
to
atmos
phere
for
an
extended
period
of
time
MAINTENANCE
The
following
checks
and
main
tenance
are
especially
important
to
the
air
conditioner
I
Check
refrigerant
level
2
Check
refrigerant
leaks
3
Check
compressor
drive
belt
for
proper
deflection
4
Even
in
the
off
season
turn
the
compressor
for
10
minutes
at
least
once
a
month
by
running
the
engine
at
1
500
rpm
GENERAL
SERVICE
INSTRUCTIONS
If
dirt
water
or
air
enters
the
air
conditioner
system
it
will
be
seriously
affected
Be
sure
to
observe
the
following
I
Always
keep
the
working
place
clean
and
dry
and
free
from
dirt
and
Air
Conditioning
GENERAL
SERVICE
dust
Wipe
water
off
from
the
line
fittings
with
a
clean
cloth
before
dis
connecting
2
Have
all
necessary
tools
in
prepar
ation
beforehand
and
have
tools
clean
and
dry
3
Handling
plug
when
the
system
line
is
disconnected
4
Handling
compressor
oil
For
details
refer
to
each
descrip
tion
in
this
manual
SAFETY
PRECAUTIONS
WARNING
1
Since
direct
contact
of
the
liquid
refrigerant
with
your
skin
will
cause
frostbite
always
be
carelul
when
handling
the
refrigerant
Always
wear
goggles
to
protect
your
eyes
when
working
around
the
system
2
The
refrigerant
service
container
has
a
safe
strength
However
if
handled
incorrectly
it
will
ex
plode
Therelore
always
follow
the
instructions
On
the
label
In
particular
never
store
it
in
a
hot
location
above
520e
1260F
or
drop
it
from
a
high
height
3
The
refrigerant
gas
is
odorless
and
colorless
and
breathing
may
become
difficult
due
to
the
lack
of
oxygen
Since
the
relrigerant
gas
is
heavier
than
air
and
will
lay
close
to
the
floor
be
espe
cially
careful
when
handling
it
in
small
confined
spaces
4
The
refrigerant
itself
is
nonflam
mable
However
a
toxic
gas
phosgene
gas
is
produced
when
it
contacu
fire
and
special
care
is
therefore
required
when
check
ing
for
leaks
in
the
system
with
a
halide
torch
5
Do
not
steam
clean
On
the
sys
tem
especially
condenser
since
excessively
high
pressure
will
build
up
in
the
system
resulting
in
explosion
of
the
system
The
above
precautions
are
essen
tial
in
handling
of
Refrigerant
12
and
their
strict
observation
AC
9
requires
sufficient
training
Therefore
it
is
of
first
impor
tance
that
any
other
personnel
than
a
well
trained
serviceman
should
not
be
allowed
to
handle
the
refrigerant
EVACUATING
AND
CHARGING
SYSTEM
During
servicing
use
caution
to
keep
air
from
getting
into
refrigerant
When
air
enters
the
system
all
refriger
ant
must
be
evacuated
from
system
prior
to
charging
new
refrigerant
Air
in
refrigerant
has
the
following
delete
rious
effects
1
Since
the
condensation
tempera
ture
of
the
air
is
extremely
low
the
air
will
not
be
condensed
when
refrigerant
gas
is
condensed
in
the
condenser
and
the
air
will
thus
remain
in
gaseous
fonn
Consequently
the
effective
thermal
transmission
area
of
condenser
for
refrigerant
gas
will
be
reduced
and
refrigerant
gas
to
be
condensed
will
be
reduced
The
pressure
rise
will
become
proportional
to
the
volume
of
the
air
in
system
2
When
air
and
refrigerant
are
r
tixed
in
system
a
chemical
reaction
will
be
produced
and
hydrochloric
acid
which
will
adversely
affect
the
aluminum
copper
iron
and
other
materials
in
system
may
be
generated
HANDLING
MANIFOLD
GAUGE
The
pressure
at
the
high
and
low
sides
of
system
should
be
measured
when
evacuating
and
charging
refrig
erant
and
when
diagnosing
trouble
in
the
system
The
manifold
gauge
is
used
for
these
purposes
A
manifold
gauge
has
two
pressure
gauges
a
low
pressure
gauge
and
a
high
pressure
gauge
These
gauges
are
connected
to
the
high
and
low
side
service
valves
of
system
through
flexible
charging
hoses
The
construction
of
manifold
gauge
is
Page 511 of 548
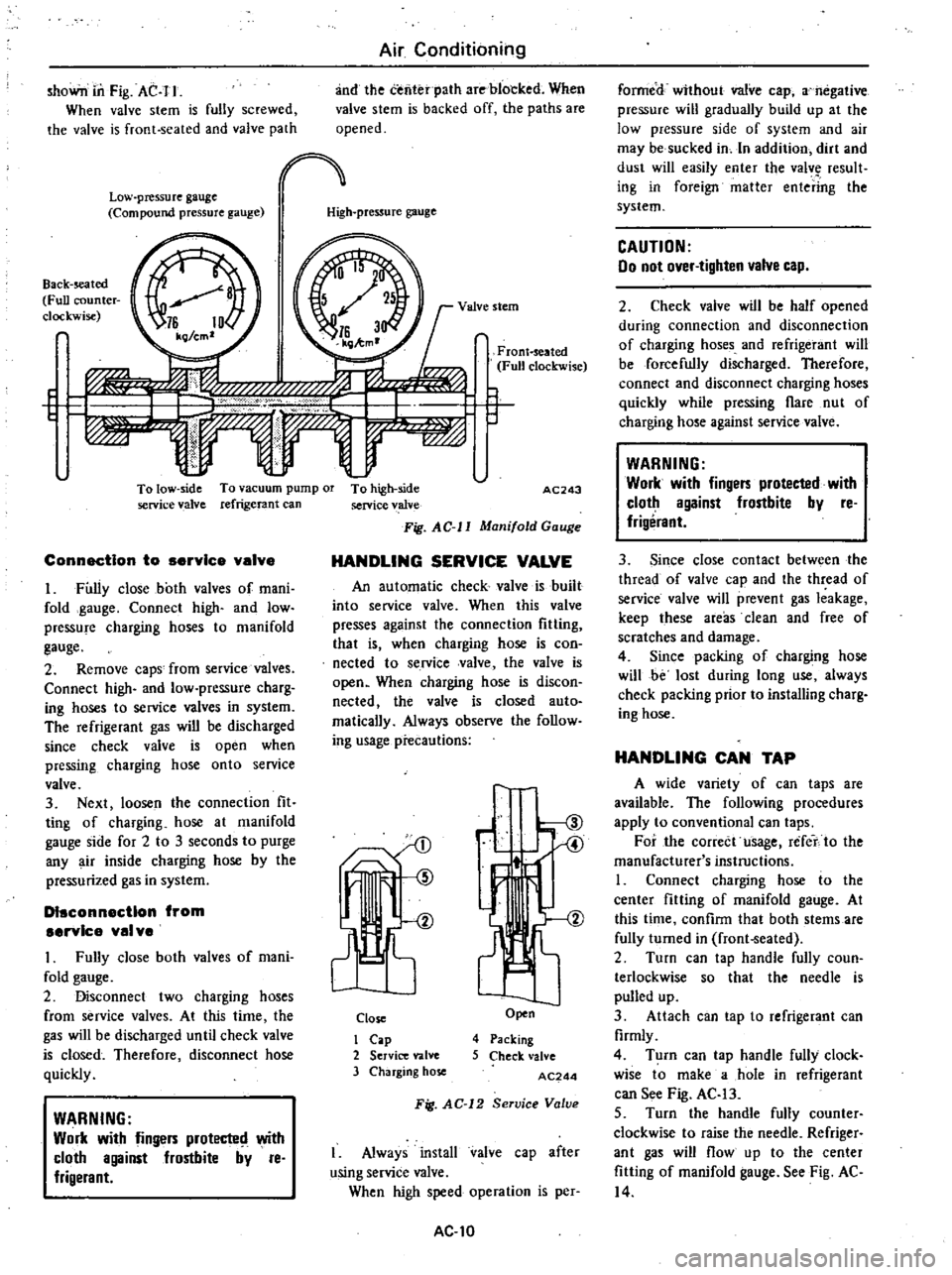
shoWn
in
Fig
AC
I
I
When
valve
stem
is
fully
screwed
the
valve
is
front
seated
and
valve
path
Low
pressure
gauge
Compound
pressure
gauge
Air
Conditioning
and
the
tenter
path
are
blocked
When
valve
stem
is
backed
off
the
paths
are
opened
High
pressure
gauge
Back
seated
Full
counter
clockwise
I
VA
l
C
f
f
f
J
l
r
To
low
side
To
vacuum
pump
01
To
high
side
service
valve
refrigerant
can
service
valve
Fig
AC
II
Manifold
Gauge
ConnectIon
to
service
valve
I
Fully
close
both
valves
of
mani
fold
gauge
Connect
high
and
low
pressure
charging
hoses
to
manifold
gauge
2
Remove
caps
from
service
valves
Connect
high
and
low
pressure
charg
ing
hoses
to
service
valves
in
system
The
refrigerant
gas
will
be
discharged
since
check
valve
is
open
when
pressing
charging
hose
onto
service
valve
3
Next
loosen
the
connection
fit
ting
of
charging
hose
at
manifold
gauge
side
for
2
to
3
seconds
to
purge
any
air
inside
charging
hose
by
the
pressurized
gas
in
system
DIsconnection
from
servIce
val
ve
I
Fully
close
both
valves
of
mani
fold
gauge
2
Disconnect
two
charging
hoses
from
service
valves
At
this
time
the
gas
will
be
discharged
until
check
valve
is
closed
Therefore
disconnect
hose
quickly
WARNING
Work
with
fingers
protecte
with
cloth
against
frostbite
by
reo
frigerant
FronHeated
Fun
clockwise
r
AC243
HANDLING
SERVICE
VALVE
An
automatic
check
valve
is
built
into
service
valve
When
this
valve
presses
against
the
connection
fiUing
that
is
when
charging
hose
is
con
nected
to
service
valve
the
valve
is
open
When
charging
hose
is
discon
nected
the
valve
is
closed
auto
matically
Always
observe
the
follow
ing
usage
precautions
1ts
Close
I
Cap
2
Service
valve
3
Charging
hose
ir
Open
4
Packing
5
Check
valve
AC244
Fig
AC
12
Service
Valve
I
Always
install
valve
cap
after
using
service
valve
When
high
speed
operation
is
per
AC
I0
formed
without
valve
cap
a
negative
pressure
will
gradually
build
up
at
the
low
pressure
side
of
system
and
air
may
be
sucked
in
In
addition
dirt
and
dust
will
easily
enter
the
valv
result
ing
in
foreign
matter
entering
the
system
CAUTION
00
not
over
tighten
valve
cap
2
Check
valve
wiJI
be
half
opened
during
connection
and
disconnection
of
charging
hoses
and
refrigerant
will
be
forcefully
discharged
Therefore
connect
and
disconnect
charging
hoses
quickly
while
pressing
flare
nut
of
charging
hose
against
service
valve
WARNING
Work
with
fingers
protected
with
cloth
against
frostbite
by
reo
frigerant
3
Since
close
contact
between
the
thread
of
valve
cap
and
the
thread
of
service
valve
will
prevent
gas
leakage
keep
these
areas
clean
and
free
of
scratches
and
damage
4
Since
packing
of
charging
hose
will
be
lost
during
long
use
always
check
packing
prior
to
installing
charg
ing
hose
HANDLING
CAN
TAP
A
wide
variety
of
can
taps
are
available
The
following
procedures
apply
to
conventional
can
taps
For
the
correct
usage
refet
to
the
manufacturer
s
instructions
I
Connect
charging
hose
to
the
center
fitting
of
manifold
gauge
At
this
time
confirm
that
both
stems
are
fully
turned
in
frontoSeated
2
Turn
can
tap
handle
fully
coun
terlockwise
so
that
the
needle
is
pulled
up
3
Attach
can
tap
to
refrigerant
can
firmly
4
Turn
can
tap
handle
fully
clock
wise
to
make
a
hole
in
refrigerant
can
See
Fig
AC
13
5
Turn
the
handle
fully
counter
clockwise
to
raise
the
needle
Refriger
ant
gas
will
flow
up
to
the
center
fitting
of
manifold
gauge
See
Fig
AC
14