check engine light DATSUN 210 1979 Owner's Guide
[x] Cancel search | Manufacturer: DATSUN, Model Year: 1979, Model line: 210, Model: DATSUN 210 1979Pages: 548, PDF Size: 28.66 MB
Page 516 of 548
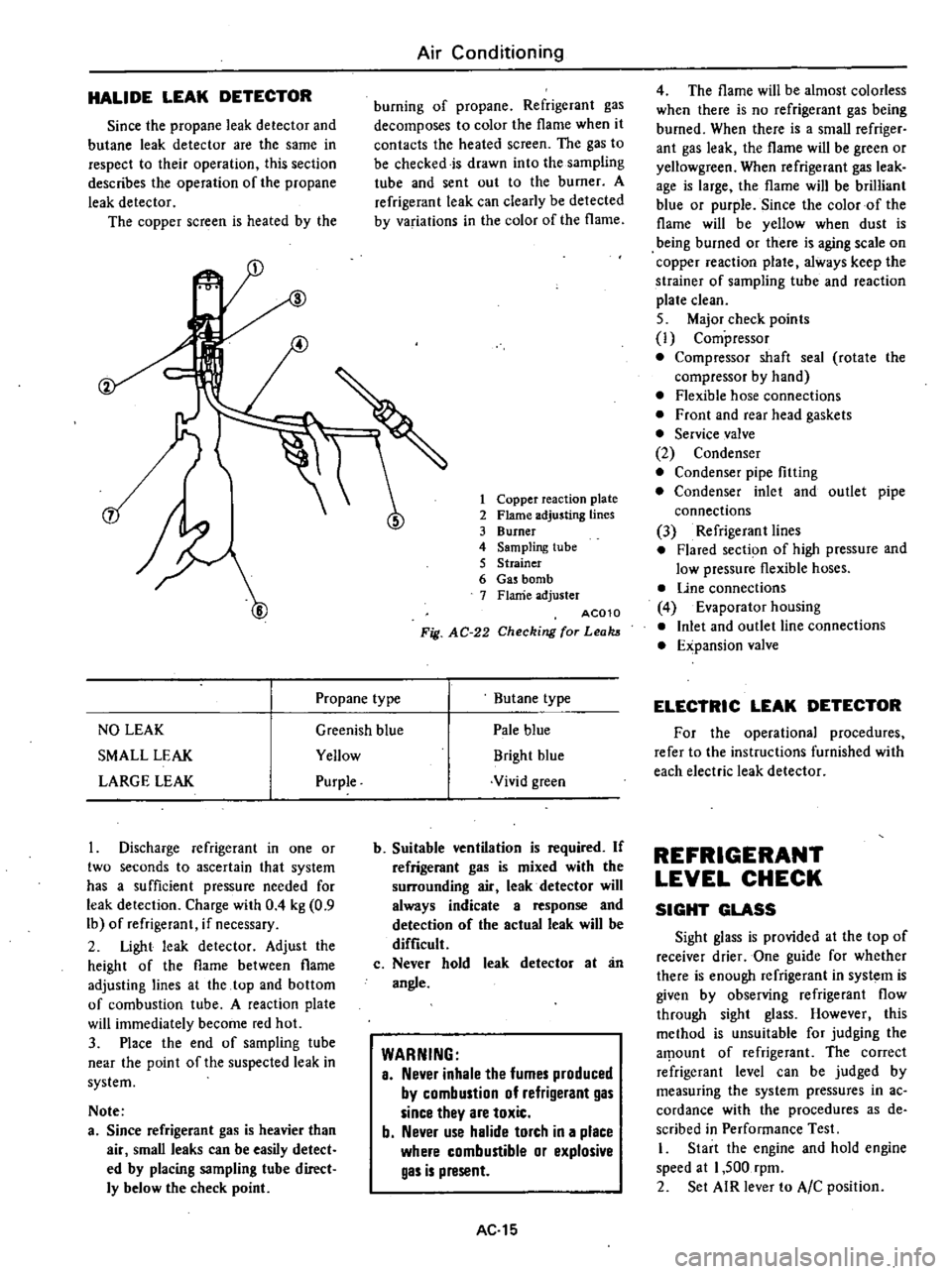
HALIDE
LEAK
DETECTOR
Since
the
propane
leak
detector
and
butane
leak
detector
are
the
same
in
respect
to
their
operation
this
section
describes
the
operation
of
the
propane
leak
detector
The
copper
screen
is
heated
by
the
Air
Conditioning
burning
of
propane
Refrigerant
gas
decomposes
to
color
the
flame
when
it
contacts
the
heated
screen
The
gas
to
be
checked
is
drawn
into
the
sampling
tube
and
sent
out
to
the
burner
A
refrigerant
leak
can
clearly
be
detected
by
variations
in
the
color
of
the
flame
1
Copper
reaction
plate
2
Flame
adjusting
lines
3
Burner
4
Sampling
tube
5
Strainer
6
Gas
bomb
7
Flame
adjuster
AC010
Fig
AC
22
Checking
for
Leaks
4
The
flame
will
be
almost
colorless
when
there
is
no
refrigerant
gas
being
burned
When
there
is
a
small
refriger
ant
gas
leak
the
flame
will
be
green
or
yellowgreen
When
refrigerant
gas
leak
age
is
large
the
flame
will
be
brilliant
blue
or
purple
Since
the
color
of
the
flame
will
be
yellow
when
dust
is
being
burned
or
there
is
aging
scale
on
copper
reaction
plate
always
keep
the
strainer
of
sampling
tube
and
reaction
plate
clean
5
Major
check
points
l
Compressor
Compressor
shaft
seal
rotate
the
compressor
by
hand
Flexible
hose
connections
Front
and
rear
head
gaskets
Service
valve
2
Condenser
Condenser
pipe
fitting
Condenser
inlet
and
outlet
pipe
connections
3
Refrigerant
lines
Flared
section
of
high
pressure
and
low
pressure
flexible
hoses
Une
connections
4
Evaporator
housing
Inlet
and
outlet
line
connections
Expansion
valve
Propane
type
Butane
type
ELECTRIC
LEAK
DETECTOR
NO
LEAK
Greenish
blue
Pale
blue
For
the
operational
procedures
SMALL
LEAK
Yellow
Bright
blue
refer
to
the
instructions
furnished
with
LARGE
LEAK
Purple
Vivid
green
each
electric
leak
detector
Discharge
refrigerant
in
one
or
two
seconds
to
ascertain
that
system
has
a
sufficient
pressure
needed
for
leak
detection
Charge
with
0
4
kg
0
9
Ib
of
refrigeranl
if
necessary
2
Light
leak
detector
Adjust
the
height
of
the
flame
between
flame
adjusting
lines
at
the
top
and
bottom
of
combustion
tube
A
reaction
plate
will
immediately
become
red
hot
3
Place
the
end
of
sampling
tube
near
the
point
of
the
suspected
leak
in
system
Note
a
Since
refrigerant
gas
is
heavier
than
air
small
leaks
can
be
easily
detect
ed
by
placing
sampling
tube
direct
ly
below
the
check
point
b
Suitable
ventilation
is
required
If
refrigerant
gas
is
mixed
with
the
surrounding
air
leak
detector
will
always
indicate
a
response
and
detection
of
the
actual
leak
will
be
difficult
c
Never
hold
leak
detector
at
an
angle
WARNING
a
Never
inhale
the
fumes
produced
by
combustion
of
refrigerant
gas
since
they
are
toxic
b
Never
use
halide
torch
in
a
place
where
combustible
or
explosive
gas
is
present
AC
15
REFRIGERANT
LEVEL
CHECK
SIGHT
GLASS
Sight
glass
is
provided
at
the
top
of
receiver
drier
One
guide
for
whether
there
is
enough
refrigerant
in
syst
m
is
given
by
observing
refrigerant
flow
through
sight
glass
However
this
method
is
unsuitable
for
judging
the
aJTlount
of
refrigerant
The
correct
refrigeranl
level
can
be
judged
by
measuring
the
system
pressures
in
ac
cordance
with
the
procedures
as
de
scribed
in
Performance
Test
1
Start
the
engine
and
hold
engine
speed
al
1
500
rpm
2
Set
AIR
lever
to
AlC
position
Page 517 of 548

I
I
3
Set
temperature
lever
to
max
imum
cold
position
Air
Conditioning
4
Sefblower
to
maximum
speed
S
Check
sight
glass
after
the
lapse
Almost
no
refrigerant
Check
item
Temperature
of
high
prenure
and
low
pressure
lines
Almost
no
difference
between
high
presswc
and
lowpressufC
side
temperature
State
in
sight
gl
ltS3
Bubbles
flow
continu
ously
Bubbles
will
disappear
and
some
thing
like
mist
wiD
flow
when
rerrigel
l
llt
is
nearly
gone
AC256
Pressure
of
system
High
pressure
side
is
abnormally
low
Repair
Stop
compressor
and
conduct
an
overall
check
Note
a
The
bubbles
seen
tbrough
the
sight
glass
are
influenced
by
the
ambient
tempemture
Since
the
bubbles
are
bard
to
show
up
in
comparatively
low
tempemtures
below
200C
680
F
it
is
possible
that
a
slightly
larger
amouot
of
refrigemot
would
be
filled
if
supplied
according
to
tbe
sight
glass
Be
sure
to
recheck
the
amount
when
it
exceedS
20
C
680F
In
higher
tempemture
tbe
bubbles
are
easy
to
show
up
Insufficient
High
pressure
side
is
warm
and
low
pressure
side
is
fairly
cokt
The
bubbles
are
seen
at
intervals
of
1
2
seconds
AC257
Both
pressures
on
high
and
low
pressure
sides
are
slightly
low
Check
for
gas
leakage
repair
as
required
re
plenish
and
chaxge
system
b
Wben
the
screen
in
tbe
receiver
drier
is
clogged
tbe
bubbles
wiD
appear
even
if
the
amount
of
refrig
erant
is
nonnaL
In
this
case
tbe
outlet
side
pipe
of
tbe
receiver
drier
becomes
considembly
cold
AC
16
of
abOut
five
rilintJtes
Jullgeaccording
to
the
following
table
Suitable
Too
much
refrigerant
High
pressure
side
is
hot
and
low
pressure
side
is
cold
High
pressure
side
is
abnormally
hot
Almost
transparent
Bubbles
may
appear
when
engine
speed
is
raised
and
lowered
No
bubbles
can
be
seen
No
clear
difference
exists
these
two
conditions
nl
AC258
Both
pre55ures
on
high
and
low
pressure
sides
are
normal
Both
pressures
on
high
and
low
pressure
sides
are
abnonnally
high
Discharge
refrigerant
from
service
valve
of
low
pressure
side
PERFORMANCE
TEST
Check
for
the
amount
of
refrigerant
in
the
system
can
be
made
by
meas
uring
pressure
on
discharge
side
The
correct
amount
of
refrigerant
is
in
the
system
if
pressure
on
the
discharge
side
i
within
the
specified
range
For
details
refer
to
Trouble
Diagnoses
and
Corrections
for
per
fannance
test
Overcharging
will
show
up
in
higher
presstJre
on
discharge
side
Page 518 of 548
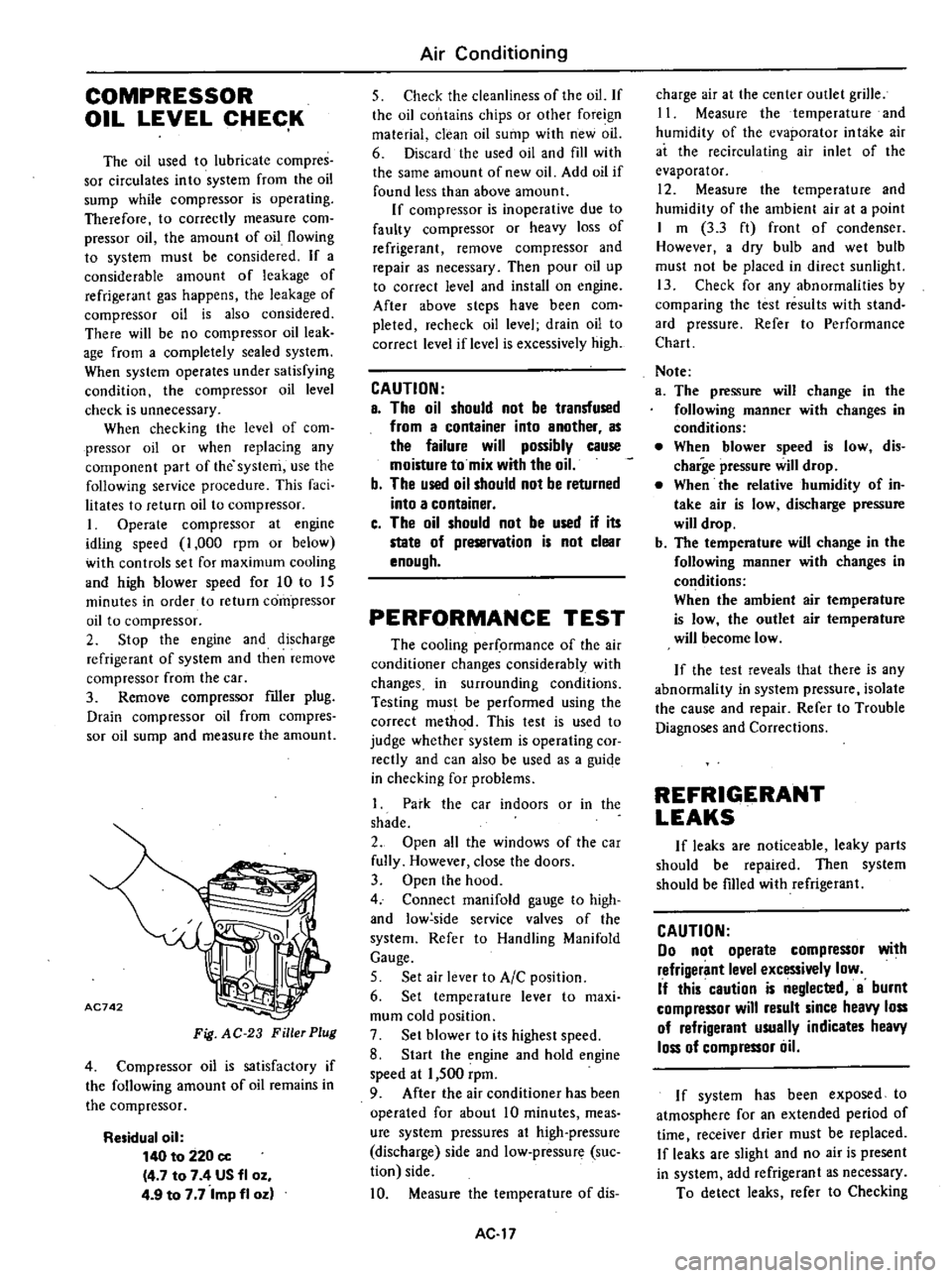
COMPRESSOR
OIL
LEVEL
CHECK
The
oil
used
to
lubricate
compres
sor
circulates
into
system
from
the
oil
sump
while
compressor
is
operating
Therefore
to
correctly
measure
com
pressor
oil
the
amount
of
oil
flowing
to
system
must
be
considered
If
a
considerable
amount
of
leakage
of
refrigerant
gas
happens
the
leakage
of
compressor
oil
is
also
considered
There
will
be
no
compressor
oil
leak
age
from
a
completely
sealed
system
When
system
operates
under
satisfying
condition
the
compressor
oil
level
check
is
unnecessary
When
checking
the
level
of
com
pressor
oil
or
when
replacing
any
component
part
of
the
system
use
the
following
service
procedure
This
facio
litates
to
return
oil
to
compressor
1
Operate
compressor
at
engine
idling
speed
I
OOO
rpm
or
below
with
controls
set
for
maximum
cooling
and
high
blower
speed
for
10
to
15
minutes
in
order
to
return
com
pressor
oil
to
compressor
2
Stop
the
engine
and
discharge
refrigerant
of
system
and
then
remove
compressor
from
the
car
3
Remove
compressor
filler
plug
Drain
compressor
oil
from
compres
sor
oil
sump
and
measure
the
amount
AC742
Fig
AC
23
Filler
Plug
4
Compressor
oil
is
satisfactory
if
the
following
amount
of
oil
remains
in
the
compressor
Residual
oil
140
to
220
cc
4
7
to
7
4
US
fl
oz
4
9
to
7
7
Imp
fl
oz
Air
Conditioning
5
Check
the
cleanliness
of
the
oil
If
the
oil
contains
chips
or
other
foreign
material
clean
oil
sump
with
new
oil
6
Discard
the
used
oil
and
fill
with
the
same
amount
of
new
oil
Add
oil
if
found
less
than
above
amount
If
compressor
is
inoperative
due
to
faulty
compressor
or
heavy
loss
of
refrigerant
remove
compressor
and
repair
as
necessary
Then
pour
oil
up
to
correct
level
and
install
on
engine
After
above
steps
have
been
com
pleted
recheck
oil
level
drain
oil
to
correct
level
if
level
is
excessively
high
CAUTION
a
The
oil
should
not
be
transfused
from
a
container
into
another
as
the
failure
will
possibly
cause
moisture
to
mix
with
the
oil
b
The
used
oil
should
not
be
returned
into
a
container
c
The
oil
should
not
be
used
if
its
state
of
preservation
is
not
clear
enough
PERFORMANCE
TEST
The
cooling
per
ormance
of
the
air
conditioner
changes
considerably
with
changes
in
surrounding
conditions
Testing
must
be
performed
using
the
correct
method
This
test
is
used
to
judge
whether
system
is
operating
cor
rectly
and
can
also
be
used
as
a
guiqe
in
checking
for
problems
1
Park
the
car
indoors
or
in
the
shade
2
Open
all
the
windows
of
the
car
fully
However
close
the
doors
3
Open
the
hood
4
Connect
manifold
gauge
to
high
and
low
side
service
valves
of
the
system
Refer
to
Handling
Manifold
Gauge
5
Set
air
lever
to
AIC
position
6
Set
temperature
lever
to
maxi
mum
cold
position
7
Set
blower
to
its
highest
speed
8
Start
the
engine
and
hold
engine
speed
at
1
500
rpm
9
After
the
air
conditioner
has
been
operated
for
about
10
minutes
meas
ure
system
pressures
at
high
pressure
discharge
side
and
low
pressure
suc
tion
side
10
Measure
the
temperature
of
dis
AC
17
charge
air
at
the
center
outlet
grille
11
Measure
the
temperature
and
humidity
of
the
evaporator
in
take
air
at
the
recirculating
air
inlet
of
the
evaporator
12
Measure
the
temperature
and
humidity
of
the
ambient
air
at
a
point
I
m
3
3
ft
front
of
condenser
However
a
dry
bulb
and
wet
bulb
must
not
be
placed
in
direct
sunlight
13
Check
for
any
abnormalities
by
comparing
the
test
results
with
stand
ard
pressure
Refer
to
Performance
Chart
Note
a
The
pressure
will
change
in
the
following
manner
with
changes
in
conditions
When
blower
speed
is
low
dis
charge
pressure
will
drop
When
the
relative
humidity
of
in
take
air
is
low
discharge
pressure
will
drop
b
The
temperature
will
change
in
the
following
manner
with
changes
in
conditions
When
the
ambient
air
temperature
is
low
the
outlet
air
temperature
will
become
low
If
the
test
reveals
that
there
is
any
abnormality
in
system
pressure
isolate
the
cause
and
repair
Refer
to
Trouble
Diagnoses
and
Corrections
REFRIGERANT
LEAKS
If
leaks
are
noticeable
leaky
parts
should
be
repaired
Then
system
should
be
fIlled
with
refrigerant
CAUTION
00
not
operate
compressor
with
refrigerant
level
excessively
low
If
this
caution
is
neglected
a
burnt
compressor
will
result
since
heavy
loss
of
refrigerant
usually
indicates
heavy
loss
of
compressor
liil
I
f
system
has
been
exposed
to
atmosphere
for
an
extended
period
of
time
I
receiver
drier
must
be
replaced
If
leaks
are
slight
and
no
air
is
present
in
system
add
refrigerant
as
necessary
To
detect
leaks
refer
to
Checking
Page 519 of 548
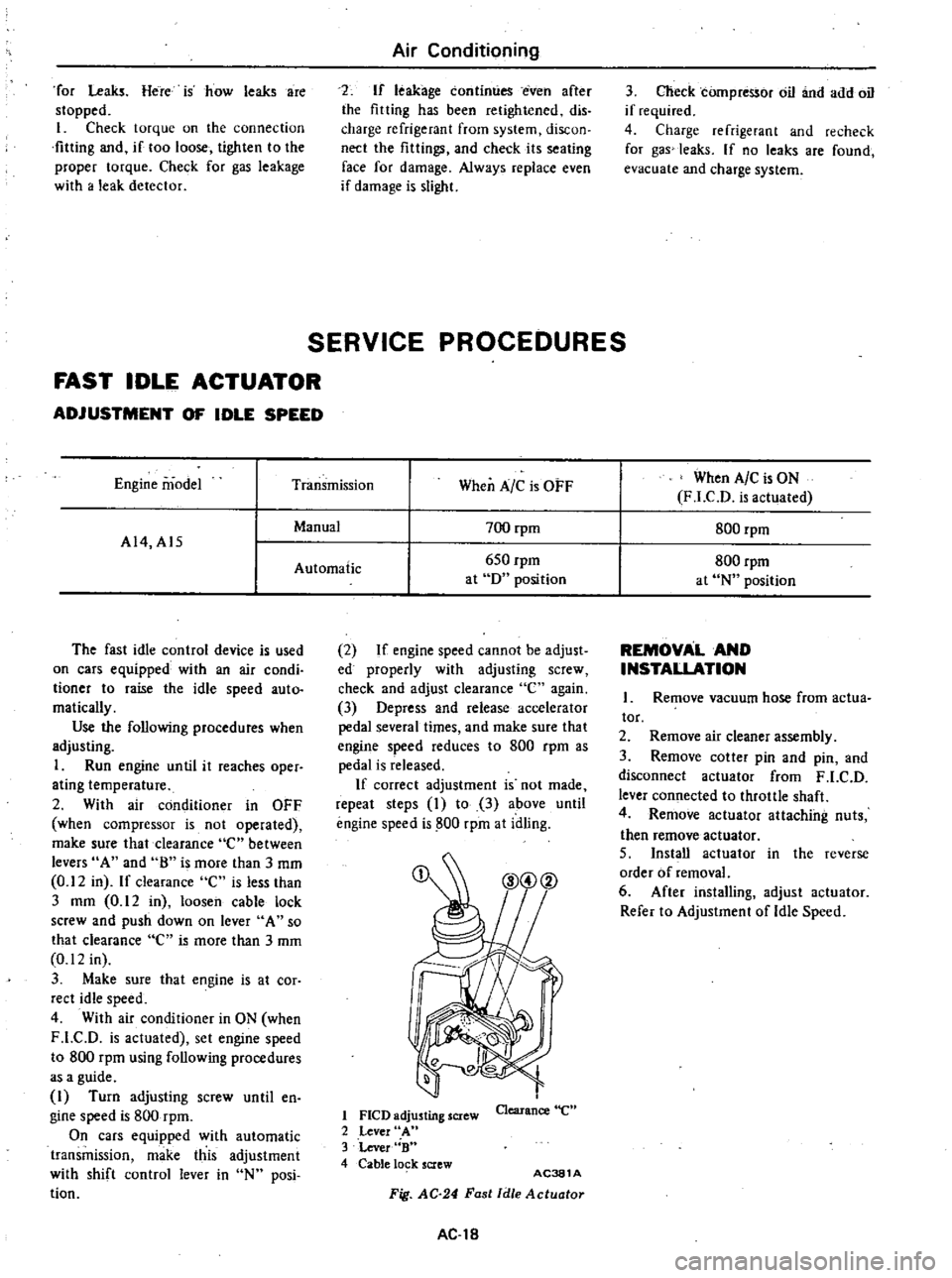
for
Leaks
Here
is
how
leaks
are
stopped
I
Check
torque
on
the
connection
fitting
and
if
too
loose
tighten
to
the
proper
lorque
Check
for
gas
leakage
with
a
leak
detector
Air
Conditioning
2
If
leakage
continues
ven
after
the
fitting
has
been
retightened
dis
charge
refrigerant
from
system
disc
on
net
the
fittings
and
check
its
seating
face
for
damage
Always
replace
even
if
damage
is
slight
J
Check
compressor
6il
and
add
oil
if
required
4
Charge
refrigerant
and
recheck
for
gas
leaks
If
no
leaks
are
found
evacuate
and
charge
system
SERVICE
PROCEDURES
FAST
IDLE
ACTUATOR
ADJUSTMENT
OF
IDLE
SPEED
Engine
model
Transmission
When
A
C
is
OFF
When
A
C
is
ON
F
LCD
is
actuated
Manual
700
rpm
800
rpm
A14
A15
Automatic
650
rpm
800
rpm
at
D
position
at
N
position
The
fast
idle
control
device
is
used
on
cars
equipped
with
an
air
condi
tioner
to
raise
the
idle
speed
auto
matically
Use
the
following
procedures
when
adjusting
1
Run
engine
until
it
reaches
oper
ating
temperature
2
With
air
conditioner
in
OFF
when
compressor
is
not
operated
make
sure
that
clearance
e
between
levers
A
and
8
is
more
than
J
mm
0
12
in
If
clearance
C
is
less
than
J
mm
0
12
in
loosen
cable
lock
screw
and
push
down
on
lever
A
so
that
clearance
C
is
more
than
J
mm
0
12
in
3
Make
sure
that
engine
is
at
cor
rect
idle
speed
4
With
air
conditioner
in
ON
when
F
LC
D
is
actuated
set
engine
speed
to
800
rpm
using
following
procedures
as
a
guide
I
Turn
adjusting
screw
until
en
gine
speed
is
800
rpm
On
cars
equipped
with
automatic
transmission
make
this
adjustment
with
shift
control
lever
in
N
posi
tion
2
If
engine
speed
cannot
be
adjust
ed
properly
with
adjusting
screw
check
and
adjust
clearance
e
again
3
Depress
and
release
accelerator
pedal
several
times
and
make
sure
that
engine
speed
reduces
to
800
rpm
as
pedal
is
released
If
correct
adjustment
is
not
made
repeat
steps
I
to
3
above
until
engine
speed
is
800
rpm
at
idling
1
FlCD
adjusting
screw
2
Lever
A
3
Lever
B
4
Cable
lo
k
screw
Clearance
e
AC381
A
Fig
AC
24
Fast
Idle
Actuotor
AC
18
REMOVAL
AND
INSTALLATION
Remove
vacuum
hose
from
actua
tor
2
Remove
air
cleaner
assembly
3
Remove
cotter
pin
and
pin
and
disconnect
actuator
from
F
LC
D
lever
connected
to
throttle
shaft
4
Remove
actuator
attaching
nuts
then
remove
actuator
5
Install
actuator
in
the
reverse
order
of
removal
6
After
installing
adjust
actuator
Refer
to
Adjustment
of
Idle
Speed