fuse chart DATSUN 210 1979 Service Manual
[x] Cancel search | Manufacturer: DATSUN, Model Year: 1979, Model line: 210, Model: DATSUN 210 1979Pages: 548, PDF Size: 28.66 MB
Page 499 of 548
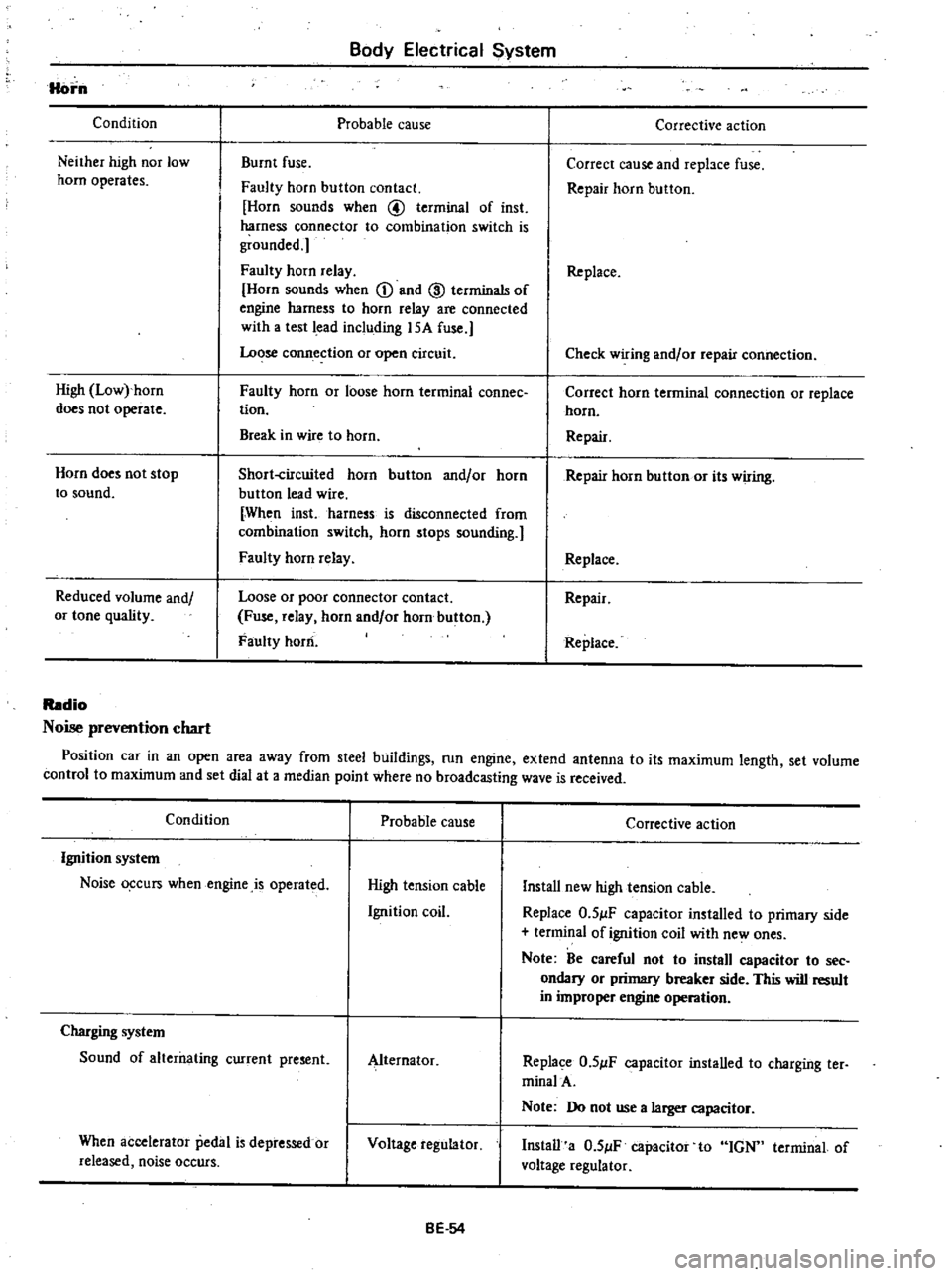
Horn
Condition
Neither
high
nor
low
horn
operates
High
Low
horn
does
not
operate
Horn
does
not
stop
to
sound
Reduced
volume
and
or
tone
quality
Body
Electrical
System
Probable
cause
Burnt
fuse
Faulty
horn
button
contact
Horn
sounds
when
@
terminal
of
inst
harness
connector
to
combination
switch
is
grounded
Faulty
horn
relay
Horn
sounds
when
CD
and
ID
terminals
of
engine
harness
to
horn
relay
are
connected
with
a
test
lead
including
15A
fuse
Lo
se
conn
ection
or
open
circuit
Faulty
horn
or
loose
horn
terminal
connee
tion
Break
in
wire
to
horn
Short
circuited
horn
button
and
or
horn
button
lead
wire
When
inst
harness
is
disconnected
from
combination
switch
horn
stops
sounding
Faulty
horn
relay
Loose
or
poor
connector
contact
Fuse
relay
horn
and
or
horn
button
Faulty
horn
Corrective
action
Correct
cause
and
repbce
fuse
Repair
horn
button
Replace
Check
wiring
and
or
repair
connection
Correct
horn
terminal
connection
or
replace
horn
Repair
Repair
horn
button
or
its
wiring
Replace
Repair
Replace
Radio
Noise
prevention
chart
Position
car
in
an
open
area
away
from
steel
buildings
run
engine
extend
antenna
to
its
maximum
length
set
volume
control
to
maximum
and
set
dial
at
a
median
point
where
no
broadcasting
wave
is
received
Condition
Probable
cause
Ignition
system
Noise
o
curs
when
engine
is
operated
High
tension
cable
Ignition
coil
Charging
system
Sound
of
alterilating
current
present
Alternator
When
accelerator
pedal
is
depressed
or
released
noise
occurs
Voltage
regulator
BE
54
Corrective
action
Install
new
high
tension
cable
Replace
O
5
lF
capacitor
installed
to
primary
side
terminal
of
ignition
coil
with
ne
ones
Note
Be
careful
not
to
install
capacitor
to
see
ondary
or
primary
breaker
side
This
will
result
in
improper
engine
operation
Replace
O
5
lF
capacitor
installed
to
charging
ter
minalA
Note
Do
not
use
a
larger
capacitor
Install
a
O
5
lF
capacitor
to
IGN
terminal
of
voltage
regulator
Page 502 of 548
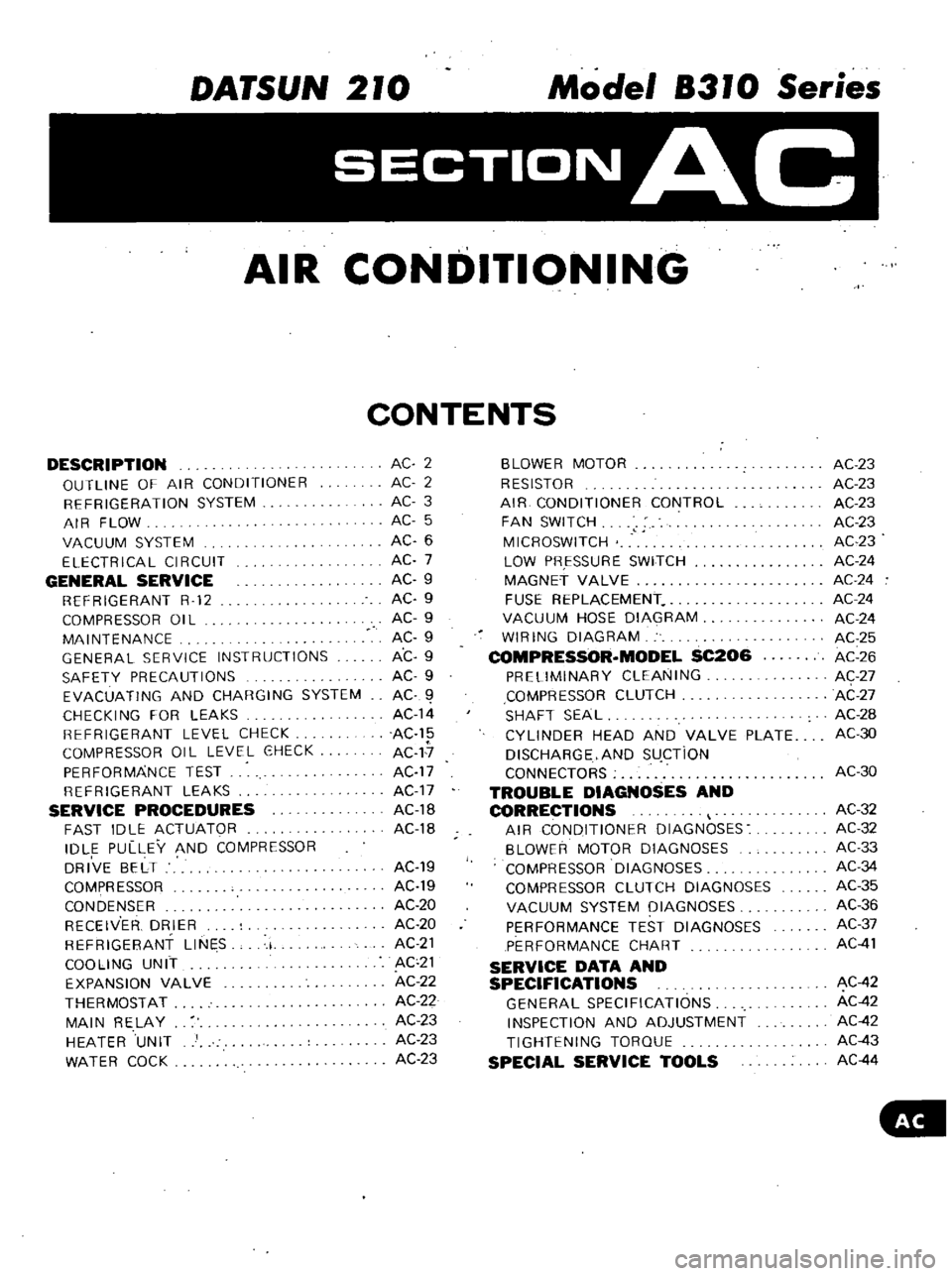
DATSUN
210
Model
8310
Series
SECTIONAC
AIR
CONDITIONING
CONTENTS
DESCRIPTION
OUTLINE
OF
AIR
CONDITIONER
REFRIGERATION
SYSTEM
AIR
FLOW
VACUUM
SYSTEM
ELECTRICAL
CIRCUIT
GENERAL
SERVICE
REFRIGERANT
R
12
COMPRESSOR
OIL
MAINTENANCE
GENERAL
SERVICE
INSTRUCTIONS
SAFETY
PRECAUTIONS
EVACUATING
AND
CHARGING
SYSTEM
CHECKI
NG
FOR
LEAKS
REFRIGERANT
LEVEL
CHECK
COMPRESSOR
OIL
LEVEL
OHECK
PERFORMANCE
TEST
REFRIGERANT
LEAKS
SERVICE
PROCEDURES
FAST
IDLE
ACTUATOR
IDL
E
PULLEY
AND
COMPRESSOR
DRIVE
BELT
COMPR
ESSOR
CONDENSER
RECEIV
ER
DRIER
REFRIGERANT
LINES
I
COOLING
UNIT
EXPANSION
VALVE
THERMOSTAT
MAIN
RELAY
HEATER
UNIT
WATER
COCK
AC
2
AC
2
AC
3
AC
5
AC
6
AC
7
AC
9
AC
9
AC
9
AC
9
AC
9
AC
9
AC
1
AC14
AC15
AC
17
AC17
AC17
AC18
AC1B
AC19
AC19
AC
20
AC
20
AC
21
ACc21
AC
22
AC
22
AC
23
AC
23
AC
23
BLOWER
MOTOR
RESISTOR
AIR
CONDITIONER
CONTROL
FAN
SWITCH
MICROSWITCH
LOW
PRESSURE
SWITCH
MAGNET
VALVE
FUSE
REPLACEMENT
VACUUM
HOSE
DIAGRAM
WIRING
DIAGRAM
COMPRESSOR
MODEL
SC206
PRELIMINARY
CLEANING
COMPRESSOR
CLUTCH
SHAFT
SEAL
CYLINDER
HEAD
AND
VALVE
PLATE
DISCHARGE
AND
sU
CTiON
CONNECTORS
TROUBLE
DIAGNOSES
AND
CORRECTIONS
AIR
CONDITIONER
DIAGNOSES
BLOWER
MOTOR
DIAGNOSES
COMPRESSOR
DIAGNOSES
COMPRESSOR
CLUTCH
DIAGNOSES
VACUUM
SYSTEM
DIAGNOSES
PERFORMANCE
TEST
DIAGNOSES
PERFORMANCE
CHART
SERVICE
DATA
AND
SPECIFICATIONS
GENERAL
SPECIFICATIONS
INSPECTION
AND
ADJUSTMENT
TIGHTENING
TORQUE
SPECIAL
SERVICE
TOOLS
AC
23
AC
23
AC
23
AC
23
AC23
AC
24
AC
24
AC24
AC
24
AC
25
AC
26
AC
27
AC
27
AC
28
AC30
AC30
AC32
AC
32
AC
33
AC34
AC35
AC36
AC37
AC
41
AC
42
AC
42
AC
42
AC
43
AC
44
Page 518 of 548
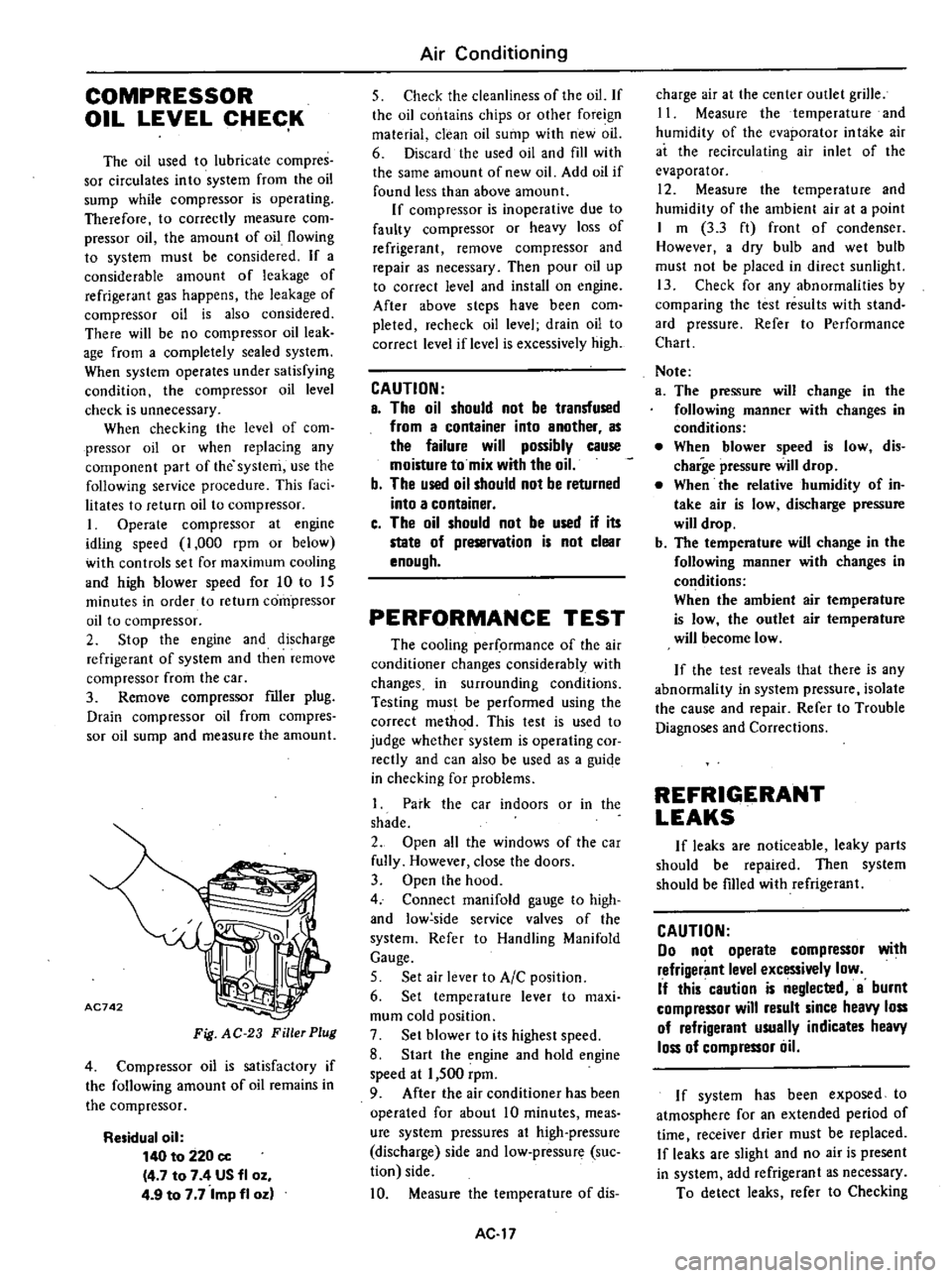
COMPRESSOR
OIL
LEVEL
CHECK
The
oil
used
to
lubricate
compres
sor
circulates
into
system
from
the
oil
sump
while
compressor
is
operating
Therefore
to
correctly
measure
com
pressor
oil
the
amount
of
oil
flowing
to
system
must
be
considered
If
a
considerable
amount
of
leakage
of
refrigerant
gas
happens
the
leakage
of
compressor
oil
is
also
considered
There
will
be
no
compressor
oil
leak
age
from
a
completely
sealed
system
When
system
operates
under
satisfying
condition
the
compressor
oil
level
check
is
unnecessary
When
checking
the
level
of
com
pressor
oil
or
when
replacing
any
component
part
of
the
system
use
the
following
service
procedure
This
facio
litates
to
return
oil
to
compressor
1
Operate
compressor
at
engine
idling
speed
I
OOO
rpm
or
below
with
controls
set
for
maximum
cooling
and
high
blower
speed
for
10
to
15
minutes
in
order
to
return
com
pressor
oil
to
compressor
2
Stop
the
engine
and
discharge
refrigerant
of
system
and
then
remove
compressor
from
the
car
3
Remove
compressor
filler
plug
Drain
compressor
oil
from
compres
sor
oil
sump
and
measure
the
amount
AC742
Fig
AC
23
Filler
Plug
4
Compressor
oil
is
satisfactory
if
the
following
amount
of
oil
remains
in
the
compressor
Residual
oil
140
to
220
cc
4
7
to
7
4
US
fl
oz
4
9
to
7
7
Imp
fl
oz
Air
Conditioning
5
Check
the
cleanliness
of
the
oil
If
the
oil
contains
chips
or
other
foreign
material
clean
oil
sump
with
new
oil
6
Discard
the
used
oil
and
fill
with
the
same
amount
of
new
oil
Add
oil
if
found
less
than
above
amount
If
compressor
is
inoperative
due
to
faulty
compressor
or
heavy
loss
of
refrigerant
remove
compressor
and
repair
as
necessary
Then
pour
oil
up
to
correct
level
and
install
on
engine
After
above
steps
have
been
com
pleted
recheck
oil
level
drain
oil
to
correct
level
if
level
is
excessively
high
CAUTION
a
The
oil
should
not
be
transfused
from
a
container
into
another
as
the
failure
will
possibly
cause
moisture
to
mix
with
the
oil
b
The
used
oil
should
not
be
returned
into
a
container
c
The
oil
should
not
be
used
if
its
state
of
preservation
is
not
clear
enough
PERFORMANCE
TEST
The
cooling
per
ormance
of
the
air
conditioner
changes
considerably
with
changes
in
surrounding
conditions
Testing
must
be
performed
using
the
correct
method
This
test
is
used
to
judge
whether
system
is
operating
cor
rectly
and
can
also
be
used
as
a
guiqe
in
checking
for
problems
1
Park
the
car
indoors
or
in
the
shade
2
Open
all
the
windows
of
the
car
fully
However
close
the
doors
3
Open
the
hood
4
Connect
manifold
gauge
to
high
and
low
side
service
valves
of
the
system
Refer
to
Handling
Manifold
Gauge
5
Set
air
lever
to
AIC
position
6
Set
temperature
lever
to
maxi
mum
cold
position
7
Set
blower
to
its
highest
speed
8
Start
the
engine
and
hold
engine
speed
at
1
500
rpm
9
After
the
air
conditioner
has
been
operated
for
about
10
minutes
meas
ure
system
pressures
at
high
pressure
discharge
side
and
low
pressure
suc
tion
side
10
Measure
the
temperature
of
dis
AC
17
charge
air
at
the
center
outlet
grille
11
Measure
the
temperature
and
humidity
of
the
evaporator
in
take
air
at
the
recirculating
air
inlet
of
the
evaporator
12
Measure
the
temperature
and
humidity
of
the
ambient
air
at
a
point
I
m
3
3
ft
front
of
condenser
However
a
dry
bulb
and
wet
bulb
must
not
be
placed
in
direct
sunlight
13
Check
for
any
abnormalities
by
comparing
the
test
results
with
stand
ard
pressure
Refer
to
Performance
Chart
Note
a
The
pressure
will
change
in
the
following
manner
with
changes
in
conditions
When
blower
speed
is
low
dis
charge
pressure
will
drop
When
the
relative
humidity
of
in
take
air
is
low
discharge
pressure
will
drop
b
The
temperature
will
change
in
the
following
manner
with
changes
in
conditions
When
the
ambient
air
temperature
is
low
the
outlet
air
temperature
will
become
low
If
the
test
reveals
that
there
is
any
abnormality
in
system
pressure
isolate
the
cause
and
repair
Refer
to
Trouble
Diagnoses
and
Corrections
REFRIGERANT
LEAKS
If
leaks
are
noticeable
leaky
parts
should
be
repaired
Then
system
should
be
fIlled
with
refrigerant
CAUTION
00
not
operate
compressor
with
refrigerant
level
excessively
low
If
this
caution
is
neglected
a
burnt
compressor
will
result
since
heavy
loss
of
refrigerant
usually
indicates
heavy
loss
of
compressor
liil
I
f
system
has
been
exposed
to
atmosphere
for
an
extended
period
of
time
I
receiver
drier
must
be
replaced
If
leaks
are
slight
and
no
air
is
present
in
system
add
refrigerant
as
necessary
To
detect
leaks
refer
to
Checking