DATSUN 610 1969 Workshop Manual
Manufacturer: DATSUN, Model Year: 1969, Model line: 610, Model: DATSUN 610 1969Pages: 171, PDF Size: 10.63 MB
Page 101 of 171
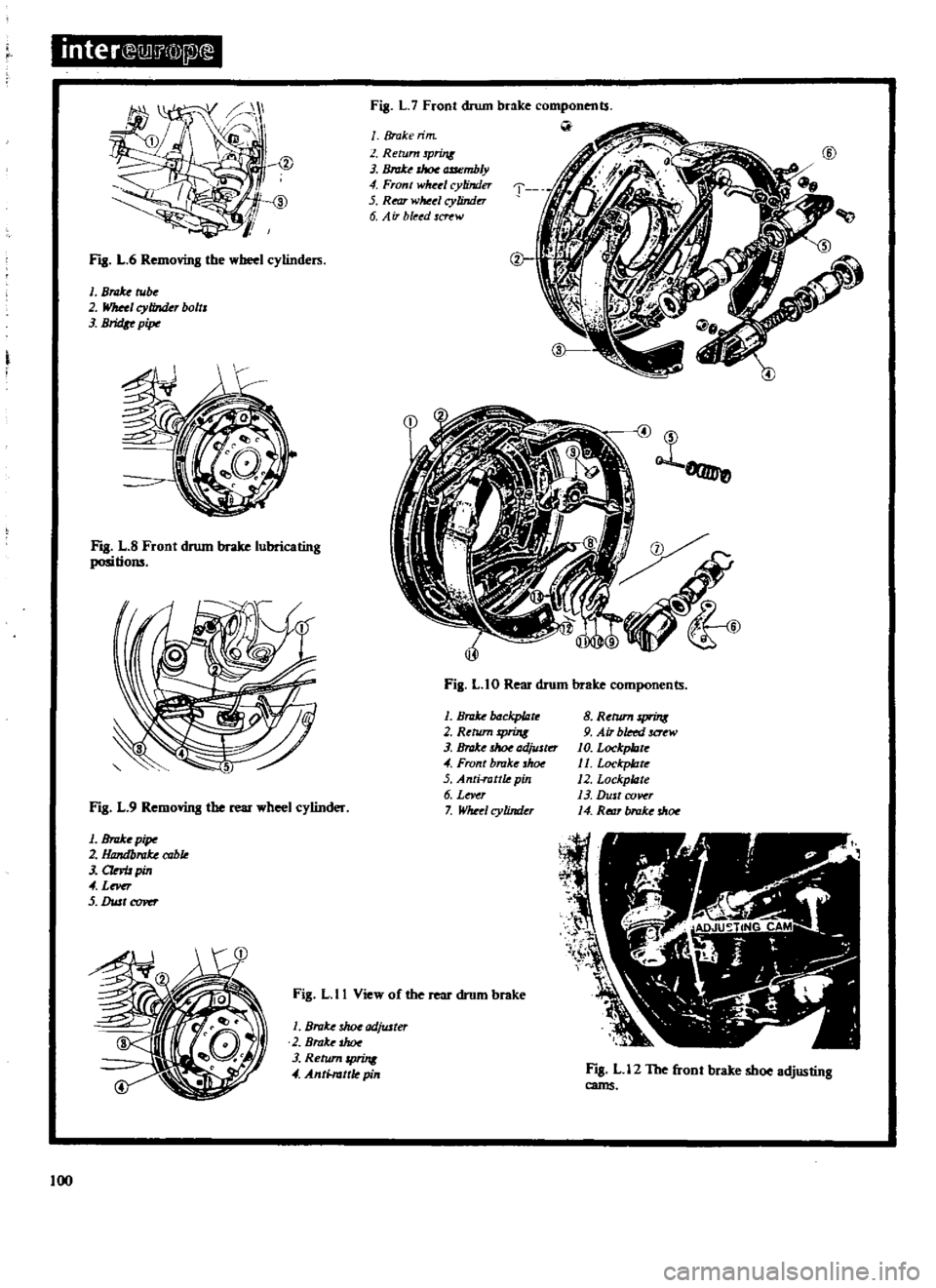
inter
Il
IT
Q
riA
I
I
II
l
11
L
6
Removing
the
wbeel
cylindeIli
1
Brd
be
2
Wllul
cylinder
bolts
J
BridI
pip
I
g
L
8
Front
drum
brake
lubricating
positions
Fig
L
9
Removing
the
rear
wheel
cylinder
1
BnrIce
pip
2
Handblllke
cable
J
CIMJ
pin
4
Lnu
5
DustCI1ft
1
Fig
L
7
Front
drum
brake
components
J
T
Broke
rim
Return
Print
J
rhoe
cmembly
4
Front
wM
1
cylinder
5
Rear
wMtl
cylindu
6
A
iT
bleed
W
o
1
Fig
L
I0
Rear
drum
brake
components
1
BllIke
ckp
tzrc
2
RthUn
spring
3
Brate
ad
JlSkr
4
Front
brake
h
5
Anti
rottk
pin
6
Lever
7
Wheel
cylinder
8
Return
sprins
9
Air
bleed
JCrew
10
Lockp
orc
11
Lockp
tzrc
12
Lockplizte
13
Dust
cover
14
Rt
t1T
brake
dr
oe
Fig
L
II
View
of
the
rear
drum
brake
I
Broke
3Iwe
adjuJter
2
BraJ
e
shot
3
Retum
4
A
ntHuttle
pin
100
11
L
12
The
front
brake
shoe
adjusting
cams
Page 102 of 171
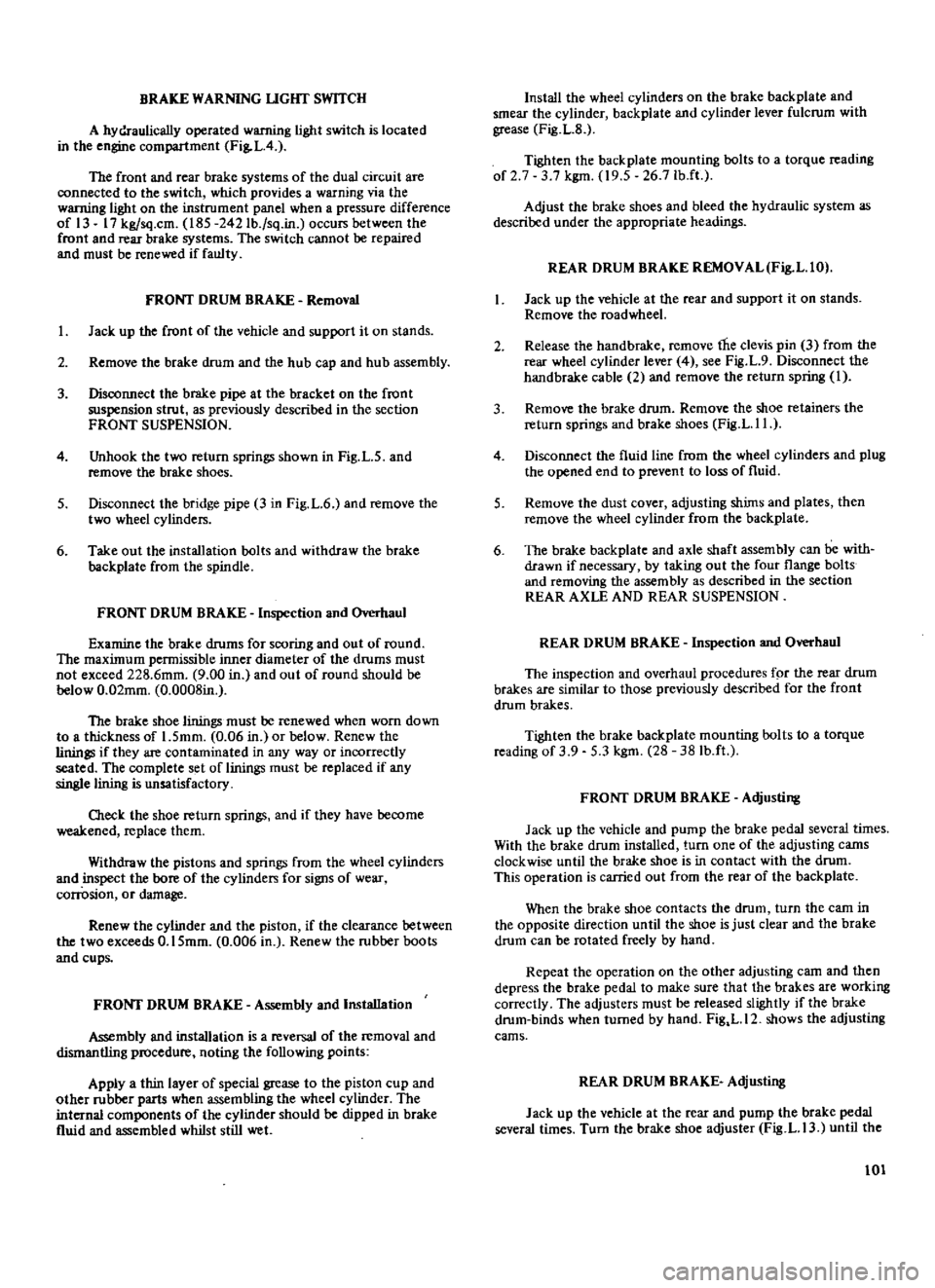
BRAKE
WARNING
UGHT
SWITCH
A
hydraulically
operated
warning
light
switch
is
located
in
the
engine
compartment
Fig
LA
The
front
and
rear
brake
systems
of
the
dual
circuit
are
connected
to
the
switch
which
provides
a
warning
via
the
warning
light
on
the
instrument
panel
when
a
pressure
difference
of
13
17
kg
sq
cm
185
242Ib
sq
in
occurs
between
the
front
and
rear
brake
systems
The
switch
cannot
be
repaired
and
must
be
renewed
if
faulty
FRONT
DRUM
BRAKE
Removal
1
Jack
up
the
front
of
the
vehicle
and
support
it
on
stands
2
Remove
the
brake
drum
and
the
hub
cap
and
hub
assembly
3
Disconnect
the
brake
pipe
at
the
bracket
on
the
front
suspension
strut
as
previously
described
in
the
section
FRONT
SUSPENSION
4
Unhook
the
two
return
springs
shown
in
Fig
L
5
and
remove
the
brake
shoes
5
Disconnect
the
bridge
pipe
3
in
Fig
L
6
and
remove
the
two
wheel
cylinders
6
Take
out
the
installation
bolts
and
withdraw
the
brake
backplate
from
the
spindle
FRONT
DRUM
BRAKE
Inspection
and
Overhaul
Examine
the
brake
drums
for
scoring
and
out
of
round
The
maximum
permissible
inner
diameter
of
the
drums
must
not
exceed
228
6mm
9
00
in
and
out
of
round
should
be
below
0
02mm
0
0008in
The
brake
shoe
linings
must
re
renewed
when
worn
down
to
a
thickness
of
1
5mm
0
06
in
or
below
Renew
the
linings
if
they
are
contaminated
in
any
way
or
incorrectly
seated
The
complete
set
of
linings
must
be
replaced
if
any
single
lining
is
unsatisfactory
O1eck
the
shoe
return
springs
and
if
they
have
become
weakened
replace
them
Withdraw
the
pistons
and
springs
from
the
wheel
cylinders
and
inspect
the
bore
of
the
cylinders
for
signs
of
wear
corrosion
or
damage
Renew
the
cylinder
and
the
piston
if
the
clearance
between
the
two
exceeds
O
15mm
0
006
in
Renew
the
rubber
boots
and
cups
FRONT
DRUM
BRAKE
Assembly
and
Installation
Assembly
and
installation
is
a
reversal
of
the
removal
and
dismantling
procedure
noting
the
fOllowing
points
Apply
a
thin
layer
of
special
grease
to
the
piston
cup
and
other
rubber
parts
when
assembling
the
wheel
cylinder
The
internal
components
of
the
cylinder
should
be
dipped
in
brake
fluid
and
assembled
whilst
still
wet
Install
the
wheel
cylinders
on
the
brake
backplate
and
smear
the
cylinder
backplate
and
cylinder
lever
fulcrum
with
grease
Fig
L
8
Tighten
the
backplate
mounting
bolts
to
a
torque
reading
of
2
7
3
7
kgm
19
5
26
71b
ft
Adjust
the
brake
shoes
and
bleed
the
hydraulic
system
as
described
under
the
appropriate
headings
REAR
DRUM
BRAKE
REMOVAL
Fig
L
IO
Jack
up
the
vehicle
at
the
rear
and
support
it
on
stands
Remove
the
road
wheel
2
Release
the
handbrake
remove
the
clevis
pin
3
from
the
rear
wheel
cylinder
lever
4
see
Fig
L
9
Disconnect
the
handbrake
cable
2
and
remove
the
return
spring
I
3
Remove
the
brake
drum
Remove
the
shoe
retainers
the
return
springs
and
brake
shoes
Fig
L
II
4
Disconnect
the
fluid
line
from
the
wheel
cylinders
and
plug
the
opened
end
to
prevent
to
loss
of
fluid
5
Remove
the
dust
cover
adjusting
shims
and
plates
then
remove
the
wheel
cylinder
from
the
backplate
6
The
brake
backplate
and
axle
shaft
assembly
can
be
with
drawn
if
necessary
by
taking
out
the
four
flange
bolts
and
removing
the
assembly
as
described
in
the
section
REAR
AXLE
AND
REAR
SUSPENSION
REAR
DRUM
BRAKE
Inspection
and
Overhaul
The
inspection
and
overhaul
procedures
fpr
the
rear
drum
brakes
are
similar
to
those
previously
described
for
the
front
drum
brakes
Tighten
the
brake
backplate
mounting
bolts
to
a
torque
reading
of
3
9
5
3
kgm
28
38Ib
ft
FRONT
DRUM
BRAKE
Adjusting
Jack
up
the
vehicle
and
pump
the
brake
pedal
several
times
With
the
brake
drum
installed
turn
one
of
the
adjusting
cams
clockwise
until
the
brake
shoe
is
in
contact
with
the
drum
This
operation
is
carried
out
from
the
rear
of
the
backplate
When
the
brake
shoe
contacts
the
drum
turn
the
cam
in
the
opposite
direction
until
the
shoe
is
just
clear
and
the
brake
drum
can
be
rotated
freely
by
hand
Repeat
the
operation
on
the
other
adjusting
cam
and
then
depress
the
brake
pedal
to
make
sure
that
the
brakes
are
working
correctly
The
adjusters
must
be
released
slightly
if
the
brake
drum
binds
when
turned
by
hand
Fig
L
12
shows
the
adjusting
cams
REAR
DRUM
BRAKE
Adjusting
Jack
up
the
vehicle
at
the
rear
and
pump
the
brake
pedal
several
times
Turn
the
brake
shoe
adjuster
Fig
L
13
until
the
101
Page 103 of 171
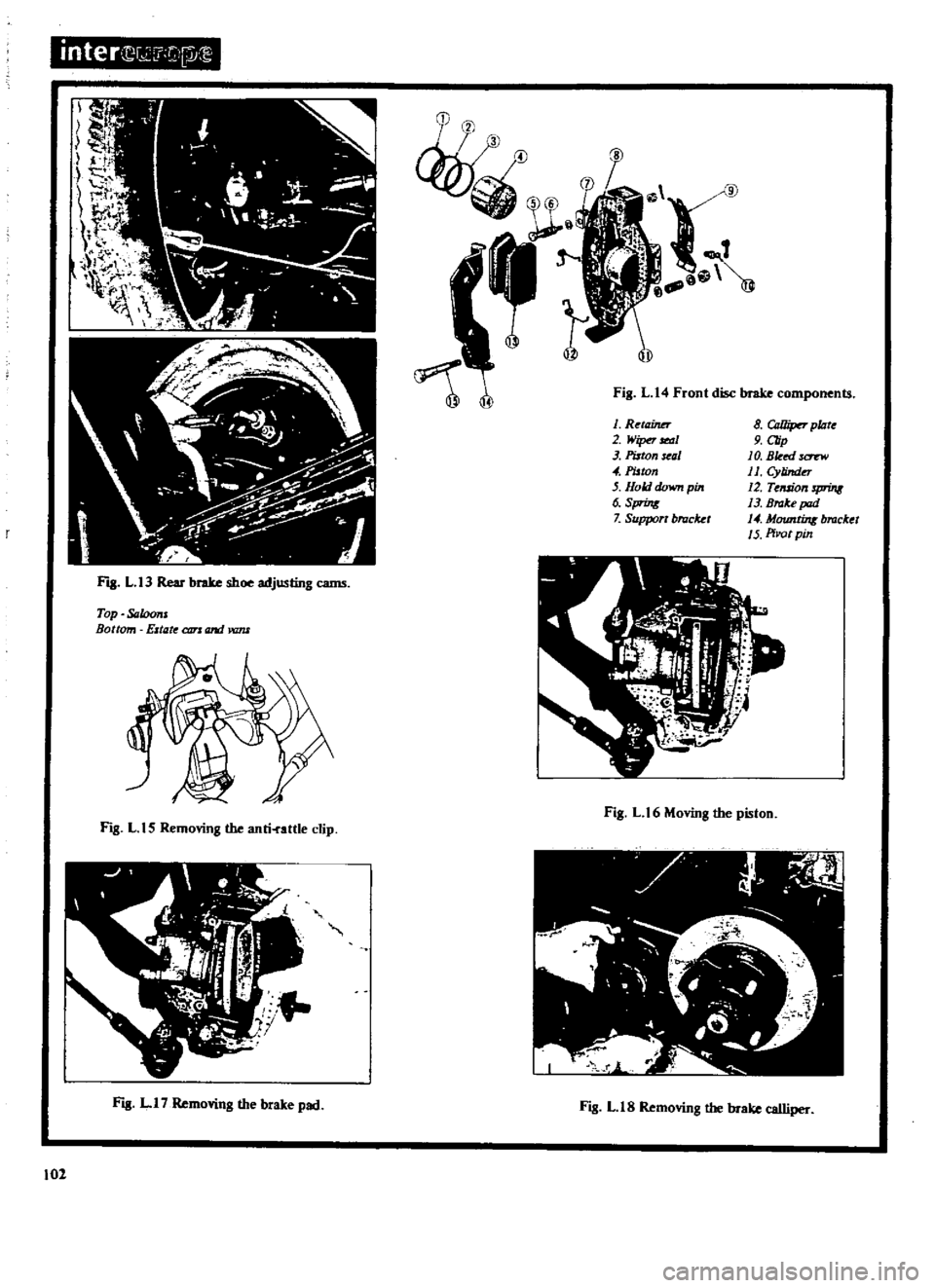
inter
J
i
J
I
E
FJB
L
13
Rear
brake
shoe
adjusling
cams
Top
Saloons
Bottom
Estate
CI1TJ
and
vam
FIg
L
15
Removing
the
anti
attle
clip
I
J
t
h
0
M
FJB
LI7
Removing
the
brake
pad
102
Al
g
b5m
tt
s
t
td
@
Fig
L
14
Front
disc
brake
components
1
Retainer
2
Wiper
It
tZI
J
Paton
seal
4
PiJton
5
Hold
down
pin
6
S
7
Support
bracket
8
Ollliper
plate
9
Clip
10
Bleed
sa
rw
11
Cylinder
12
Tension
spring
13
Brake
pad
14
MountinK
bmcket
1
5
Pi
lOtpin
Fig
L
t
6
Moving
the
piston
Fig
L
IS
Removing
the
brake
calliper
Page 104 of 171
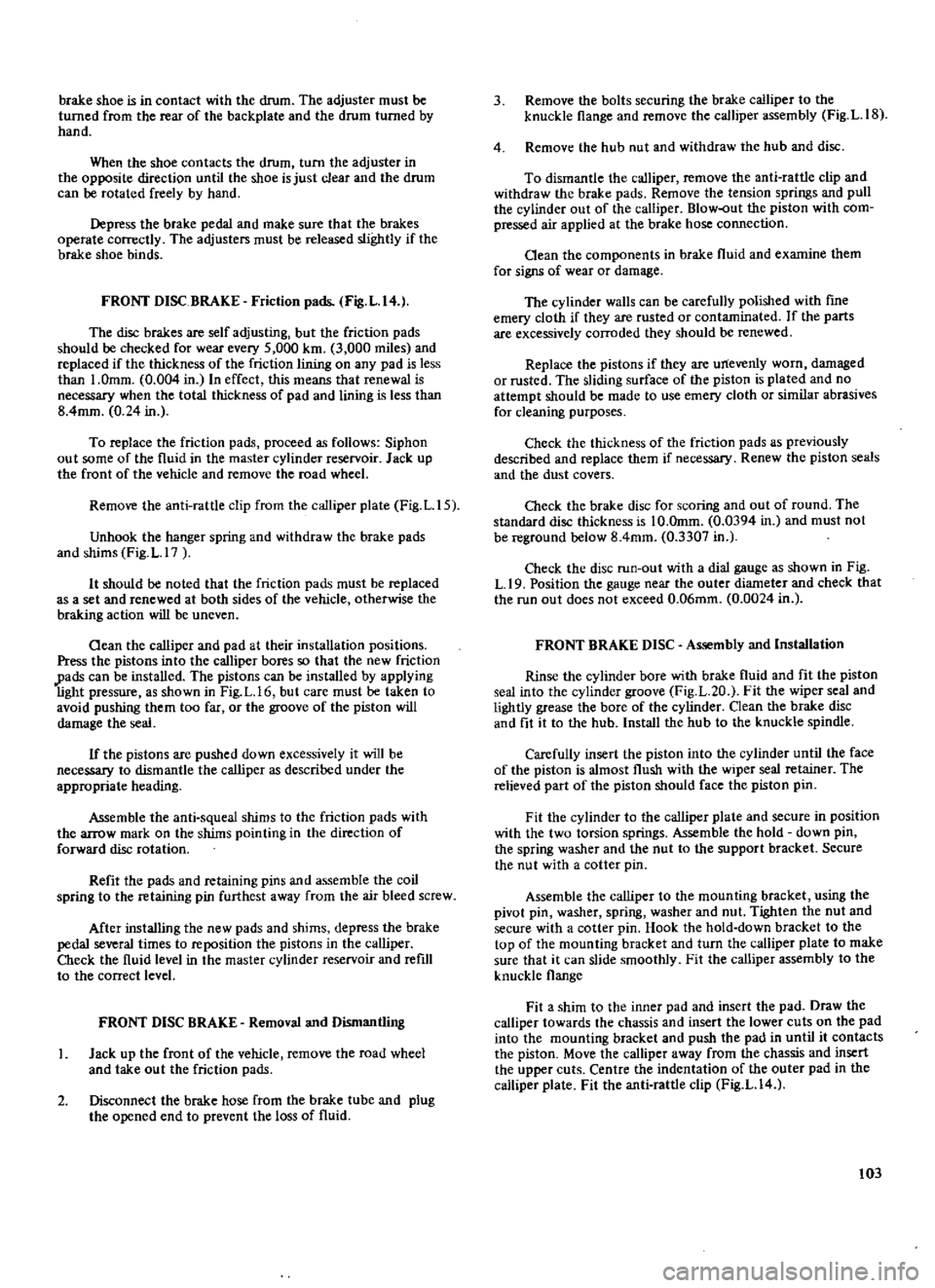
brake
shoe
is
in
contact
with
the
drum
The
adjuster
must
be
turned
from
the
rear
of
the
backplate
and
the
drum
turned
by
hand
When
the
shoe
contacts
the
drum
turn
the
adjuster
in
the
opposite
direction
until
the
shoe
is
just
clear
and
the
drum
can
be
rotated
freely
by
hand
Depress
the
brake
pedal
and
make
sure
that
the
brakes
operate
correctly
The
adjusters
must
be
released
slightly
if
the
brake
shoe
binds
FRONT
DISC
BRAKE
Friction
pads
Fig
L
14
The
disc
brakes
are
self
adjusting
but
the
friction
pads
should
be
checked
for
wear
every
5
000
km
3
000
miles
and
replaced
if
the
thickness
of
the
friction
lining
on
any
pad
is
less
than
1
0mm
0
004
in
In
effect
this
means
that
renewal
is
necessary
when
the
total
thickness
of
pad
and
lining
is
less
than
8
4mm
0
24
in
To
replace
the
friction
pads
proceed
as
follows
Siphon
out
some
of
the
fluid
in
the
master
cylinder
reservoir
Jack
up
the
front
of
the
vehicle
and
remove
the
road
wheel
Remove
the
anti
rattle
clip
from
the
calliper
plate
Fig
L
lS
Unhook
the
hanger
spring
and
withdraw
the
brake
pads
and
shims
Fig
L
17
It
should
be
noted
that
the
friction
pads
must
be
replaced
as
a
set
and
renewed
at
both
sides
of
the
vehicle
otherwise
the
braking
action
will
be
uneven
Oean
the
calliper
and
pad
at
their
installation
positions
Press
the
pistons
into
the
calliper
bores
so
that
the
new
friction
Pads
can
be
installed
The
pistons
can
be
installed
by
applying
light
pressure
as
shown
in
Fig
L
16
but
care
must
be
taken
to
avoid
pushing
them
too
far
or
the
groove
of
the
piston
will
damage
the
seal
If
the
pistons
are
pushed
down
excessively
it
will
be
necessary
to
dismantle
the
calliper
as
described
under
the
appropriate
heading
Assemble
the
anti
squeal
shims
to
the
friction
pads
with
the
arrow
mark
on
the
shims
pointing
in
the
direction
of
forward
disc
rotation
Refit
the
pads
and
retaining
pins
and
assemble
the
coil
spring
to
the
retaining
pin
furthest
away
from
the
air
bleed
screw
After
installing
the
new
pads
and
shims
depress
the
brake
pedal
several
times
to
reposition
the
pistons
in
the
calliper
O1eck
the
fluid
level
in
the
master
cylinder
reservoir
and
refill
to
the
correct
level
FRONT
DISC
BRAKE
Removal
and
Dismantling
1
Jack
up
the
front
of
the
vehicle
remove
the
road
wheel
and
take
out
the
friction
pads
2
Disconnect
the
brake
hose
from
the
brake
tube
and
plug
the
opened
end
to
prevent
the
loss
of
fluid
3
Remove
the
bolts
securing
the
brake
calliper
to
the
knuckle
flange
and
remove
the
calliper
assembly
Fig
L
IS
4
Remove
the
hub
nut
and
withdraw
the
hub
and
disc
To
dismantle
the
calliper
remove
the
anti
rattle
clip
and
withdraw
the
brake
pads
Remove
the
tension
springs
and
pull
the
cylinder
out
of
the
calliper
Blow
out
the
piston
with
com
pressed
air
applied
at
the
brake
hose
connection
Oean
the
components
in
brake
fluid
and
examine
them
for
signs
of
wear
or
damage
The
cylinder
walls
can
be
carefully
polished
with
fine
emery
cloth
if
they
are
rusted
or
contaminated
If
the
parts
are
excessively
corroded
they
should
be
renewed
Replace
the
pistons
if
they
are
unevenly
worn
damaged
or
rusted
The
sliding
surface
of
the
piston
is
plated
and
no
attempt
should
be
made
to
use
emery
cloth
or
similar
abrasives
for
cleaning
purposes
Check
the
thickness
of
the
friction
pads
as
previously
described
and
replace
them
if
necessary
Renew
the
piston
seals
and
the
dust
covers
O1eck
the
brake
disc
for
scoring
and
out
of
round
The
standard
disc
thickness
is
10
Omm
0
0394
in
and
must
not
be
reground
below
8
4mm
0
3307
in
Check
the
disc
run
out
with
a
dial
gauge
as
shown
in
Fig
L
19
Position
the
gauge
near
the
outer
diameter
and
check
that
the
run
out
does
not
exceed
0
06mm
0
0024
in
FRONT
BRAKE
DISC
Assembly
and
Installation
Rinse
the
cylinder
bore
with
brake
fluid
and
fit
the
piston
seal
into
the
cylinder
groove
Fig
L
20
Fit
the
wiper
seal
and
lightly
grease
the
bore
of
the
cylinder
Clean
the
brake
disc
and
fit
it
to
the
hub
Install
the
hub
to
the
knuckle
spindle
Carefully
insert
the
piston
into
the
cylinder
until
the
face
of
the
piston
is
almost
flush
with
the
wiper
seal
retainer
The
relieved
part
of
the
piston
should
face
the
piston
pin
Fit
the
cylinder
to
the
calliper
plate
and
secure
in
position
with
the
two
torsion
springs
Assemble
the
hold
down
pin
the
spring
washer
and
the
nut
to
the
support
bracket
Secure
the
nut
with
a
cotter
pin
Assemble
the
calliper
to
the
mounting
bracket
using
the
pivot
pin
washer
spring
washer
and
nut
Tighten
the
nut
and
secure
with
a
cotter
pin
Hook
the
hold
down
bracket
to
the
top
of
the
mounting
bracket
and
turn
the
calliper
plate
to
make
sure
that
it
can
slide
smoothly
Fit
the
calliper
assembly
to
the
knuckle
flange
Fit
a
shim
to
the
inner
pad
and
insert
the
pad
Draw
the
calliper
towards
the
chassis
and
insert
the
lower
cuts
on
the
pad
into
the
mounting
bracket
and
push
the
pad
in
until
it
contacts
the
piston
Move
the
calliper
away
from
the
chassis
and
insert
the
upper
cuts
Centre
the
indentation
of
the
outer
pad
in
the
calliper
plate
Fit
the
anti
rattle
clip
Fig
L
14
103
Page 105 of 171
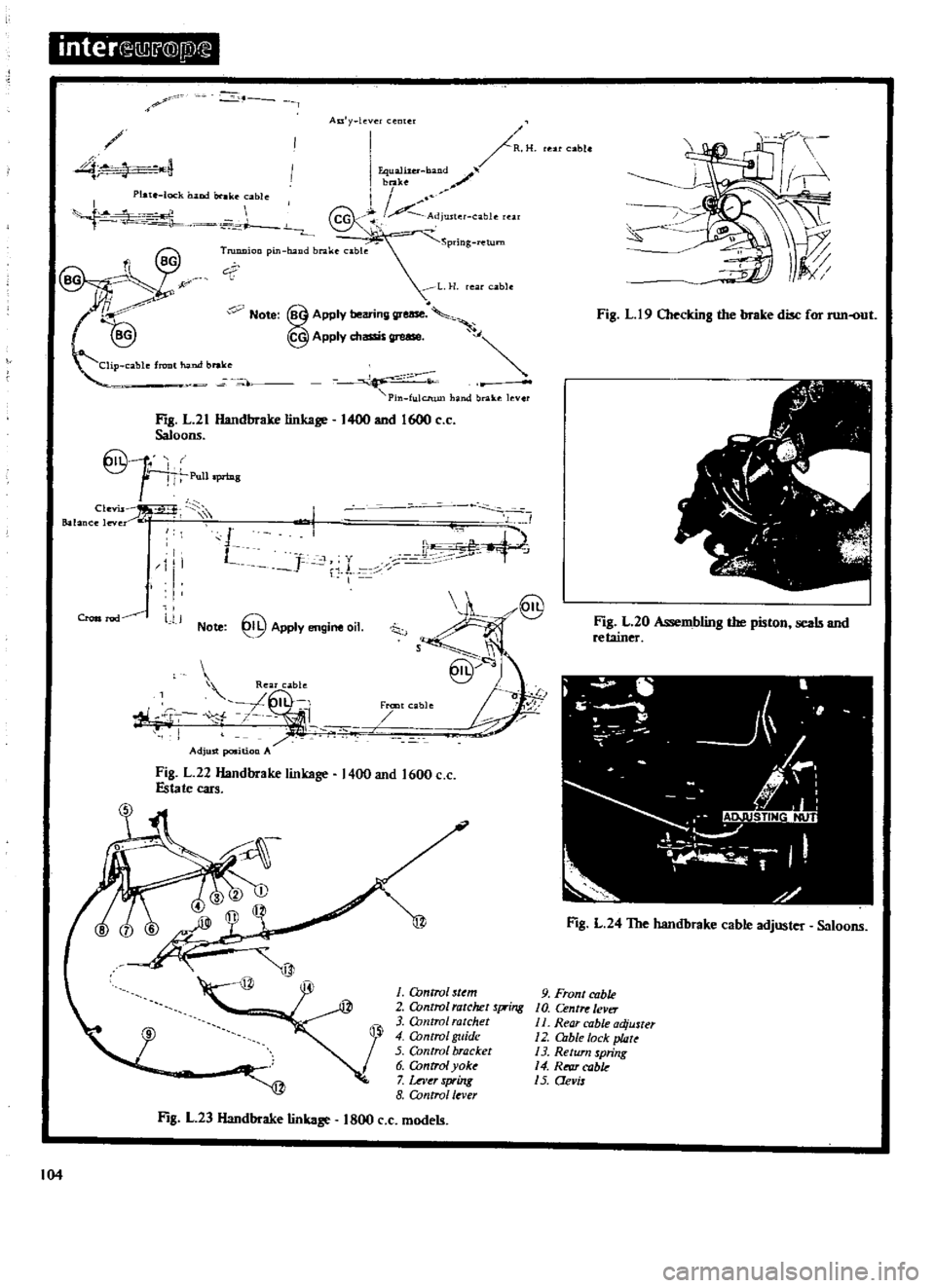
inter
f
illl
@
l
l
Au
y
l
ver
I
R
H
I
Equaliler
b2nd
i
b7ke
Pl
te
Iock
band
buk
able
I
I
I
T
@A
Adjuster
cable
oo
pm
Odb
k
SPd
wm
LH
able
C
Note
@
Apply
bearing
grease
@APPIYch
S
i
Pin
fulcrum
hand
brab
lever
6c
1l
Clip
cable
frout
N
nd
brake
Fill
L21
Handbrake
linkage
1400
and
1600
c
c
Saloons
1
I
J
Pull
priDg
1
Clt
vU
Balance
leve
I
I
J
c
1
1
I
I
1
l
J
L
I
iL
Note
@
Apply
engine
oil
8
S
J
@
I
Aj
Fran
able
Rear
cable
L
I
r
f
7
n
t
i
Adjust
position
A
Fig
L
22
Handbrake
linkage
1400
and
1600
c
c
Estate
cars
1
Control
sUm
2
Control
ratchet
Xing
3
O
mtrol
ratchet
4
O
mtro
guide
5
Control
bracket
6
OJntrol
yoke
7
wer
spring
8
Control
lever
Fig
L
23
Handbrake
linkage
1800
c
c
models
104
able
s
Fig
L
19
Checking
the
brake
disc
for
run
out
1
j
v
fti
r
v
r
Fig
L
20
As
embling
the
piston
seals
and
retainer
ti
J
4
Fill
L
24
The
handbrake
cable
adjuster
Saloons
9
Front
cable
10
Centre
lever
II
Rear
cable
adjuster
12
DIble
lock
plate
13
Return
spring
14
RI
fU
cabk
15
Qevis
Page 106 of 171
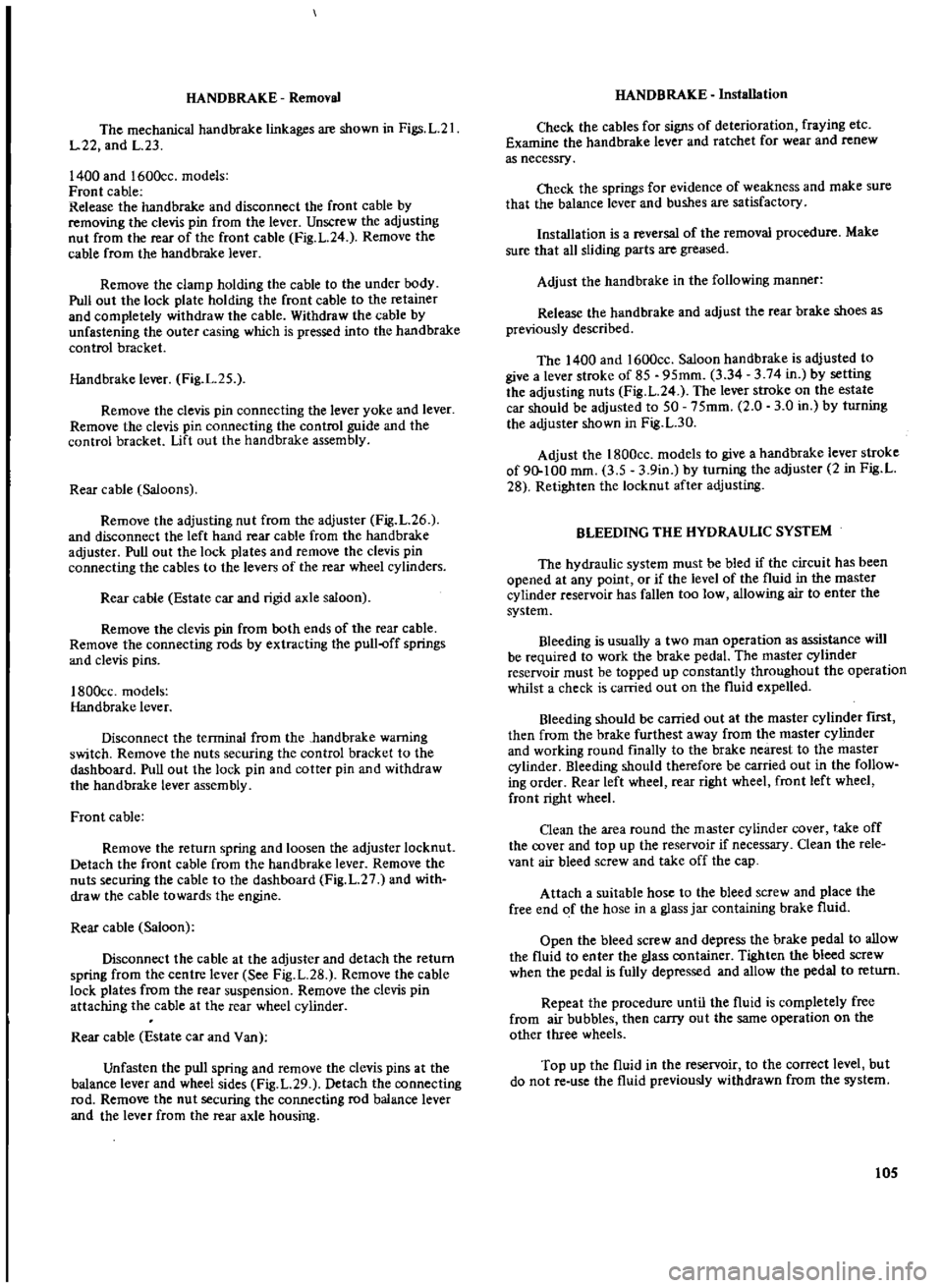
HAND
BRAKE
Removal
The
mechanical
handbrake
linkages
are
shown
in
Figs
L
21
1
22
and
1
23
1400
and
1600cc
models
Front
cable
Release
the
hand
brake
and
disconnect
the
front
cable
by
removing
the
clevis
pin
from
the
lever
Unscrew
the
adjusting
nut
from
the
rear
of
the
front
cable
Fig
L
24
Remove
the
cable
from
the
hand
brake
lever
Remove
the
clamp
holding
the
cable
to
the
under
body
Pull
out
the
lock
plate
holding
the
front
cable
to
the
retainer
and
completely
withdraw
the
cable
Withdraw
the
cable
by
unfastening
the
outer
casing
which
is
pressed
into
the
handbrake
control
bracket
Handbrake
lever
Fig
1
25
Remove
the
clevis
pin
connecting
the
lever
yoke
and
lever
Remove
the
clevis
pin
connecting
the
control
guide
and
the
control
bracket
Lift
out
the
handbrake
assembly
Rear
cable
Saloons
Remove
the
adjusting
nut
from
the
adjuster
Fig
L
26
and
disconnect
the
left
hand
rear
cable
from
the
handbrake
adjuster
Pull
out
the
lock
plates
and
remove
the
clevis
pin
connecting
the
cables
to
the
levers
of
the
rear
wheel
cylinders
Rear
cable
Estate
car
and
rigid
axle
saloon
Remove
the
clevis
pin
from
both
ends
of
the
rear
cable
Remove
the
connecting
rods
by
extracting
the
puU
off
springs
and
clevis
pins
1800cc
models
Handbrake
lever
Disconnect
the
terminal
from
the
hand
brake
warning
switch
Remove
the
nuts
securing
the
control
bracket
to
the
dashboard
Pull
out
the
lock
pin
and
cotter
pin
and
withdraw
the
handbrake
lever
assembly
Front
cable
Remove
the
return
spring
and
loosen
the
adjuster
10cknuL
Detach
the
front
cable
from
the
handbrake
lever
Remove
the
nuts
securing
the
cable
to
the
dashboard
Fig
L
27
and
with
draw
the
cable
towards
the
engine
Rear
cable
Saloon
Disconnect
the
cable
at
the
adjuster
and
detach
the
return
spring
from
the
centre
lever
See
Fig
L
28
Remove
the
cable
lock
plates
from
the
rear
suspension
Remove
the
clevis
pin
attaching
the
cable
at
the
rear
wheel
cylinder
Rear
cable
Estate
car
and
Van
Unfasten
the
pull
spring
and
remove
the
clevis
pins
at
the
balance
lever
and
wheel
sides
Fig
L
29
Detach
the
connecting
rod
Remove
the
nut
securing
the
connecting
rod
balance
lever
and
the
lever
from
the
rear
axle
housing
HANDBRAKE
Installation
Check
the
cables
for
signs
of
deterioration
fraying
etc
Examine
the
handbrake
lever
and
ratchet
for
wear
and
renew
as
necessry
Check
the
springs
for
evidence
of
weakness
and
make
sure
that
the
balance
lever
and
bushes
are
satisfactory
Installation
is
a
reversal
of
the
removal
procedure
Make
sure
that
all
sliding
parts
are
greased
Adjust
the
hand
brake
in
the
following
manner
Release
the
hand
brake
and
adjust
the
rear
brake
shoes
as
previously
described
The
1400
and
1600cc
Saloon
handbrake
is
adjusted
to
give
a
lever
stroke
of
85
95mm
3
34
3
74
in
by
setting
the
adjusting
nuts
Fig
L
24
The
lever
stroke
on
the
estate
car
should
be
adjusted
to
50
75mm
2
0
3
0
in
by
turning
the
adjuster
shown
in
Fig
L
30
Adjust
the
1800cc
models
to
give
a
handbrake
lever
stroke
of
90
100
mm
3
5
3
9in
by
turning
the
adjuster
2
in
Fig
L
28
Retighten
the
locknut
after
adjusting
BLEEDING
THE
HYDRAULIC
SYSTEM
The
hydraulic
system
must
be
bled
if
the
circuit
has
been
opened
at
any
point
or
if
the
level
of
the
fluid
in
the
master
cylinder
reservoir
has
fallen
too
low
allowing
air
to
enter
the
system
Bleeding
is
usually
a
two
man
operation
as
assistance
will
be
required
to
work
the
brake
pedal
The
master
cylinder
reservoir
must
be
topped
up
constantly
throughout
the
operation
whilst
a
check
is
carried
out
on
the
fluid
expelled
Bleeding
should
be
carried
out
at
the
master
cylinder
nrst
then
from
the
brake
furthest
away
from
the
master
cylinder
and
working
round
finally
to
the
brake
nearest
to
the
master
cylinder
Bleeding
should
therefore
be
carried
out
in
the
follow
ing
order
Rear
left
wheel
rear
right
wheel
front
left
wheel
front
right
wheel
Oean
the
area
round
the
master
cylinder
cover
take
off
the
cover
and
top
up
the
reservoir
if
necessary
Clean
the
rele
vant
air
bleed
screw
and
take
off
the
cap
Attach
a
suitable
hose
to
the
bleed
screw
and
place
the
free
end
of
the
hose
in
a
glass
jar
containing
brake
fluid
Open
the
bleed
screw
and
depress
the
brake
pedal
to
allow
the
fluid
to
enter
the
glass
container
Tighten
the
bleed
screw
when
the
pedal
is
fully
depressed
and
allow
the
pedal
to
return
Repeat
the
procedure
until
the
fluid
is
completely
free
from
air
bubbles
then
carry
out
the
same
operation
on
the
other
three
wheels
Top
up
the
fluid
in
the
reservoir
to
the
correct
level
but
do
not
re
use
the
fluid
previously
withdrawn
from
the
system
105
Page 107 of 171
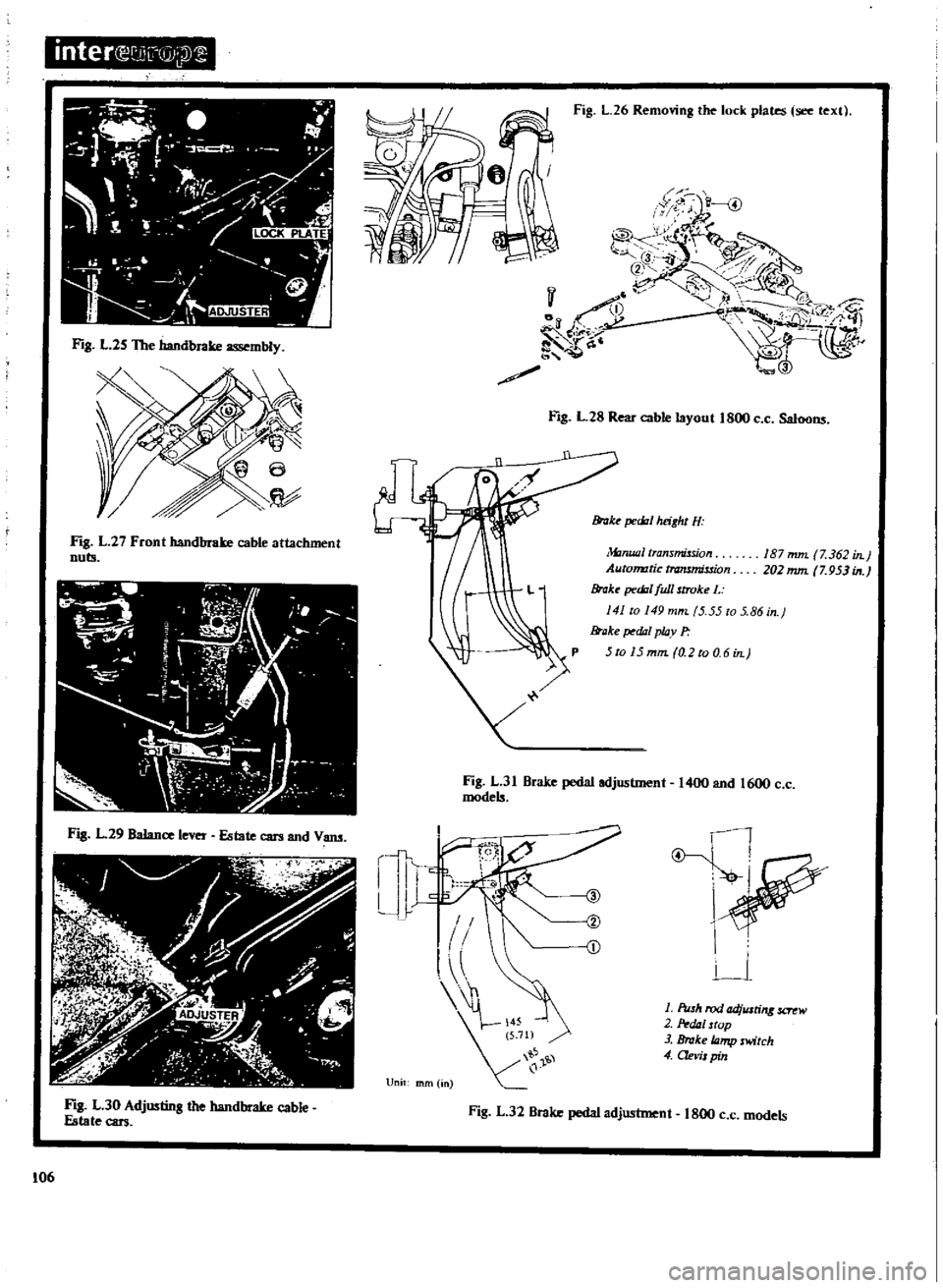
inter
jjiC@
V
6iIiIIlli
I
Ii
r
f
r
7
r
Y
t
I
10
1
L
u
N
c
I
F
ll
L
2S
The
handbrake
mbly
Fig
L
27
Front
handbrake
cable
attachment
nuts
e7
rl
A
I
r
I
r
J
i
I
f
I
I
I
of
II
J
F
F
ll
L29
Balance
lever
Estate
ClU1l
and
Vans
F
ll
L
30
AdjWltins
the
handbrake
cable
Estate
ClU1l
106
J
ei
Fig
L
26
Removing
the
lock
plates
see
text
I
7
I
i
1
@
i
1
0
1
e
V
O
V
I
r
r
if1
1i
cl
t
Ji
Y
a
t
3
F
ll
L
28
Rear
cable
layout
1800
C
c
SatOOWl
ok
pedat
height
H
87
mm
7
362
in
202
mm
7
953
ill
Jltznual
transmission
AutomItic
transmission
y
Brake
pedal
full
stroke
L
141
0149
mm
5
55
to
5
86
in
Brake
pedal
p
tJv
P
5
to
15
mm
0
2
to
0
6
ilL
Fig
L
31
Brake
pedal
adjWltment
1400
and
1600
c
c
models
l
car
Ll
1
f
1
J
111
I
l
j
u
n
l
71
t
i1
Unit
mfll
in
1
Push
rod
adjusting
scrt
W
2
Ptdlz
stop
3
Brake
Iilmp
switch
4
Clevis
pin
Fig
L
32
Brake
pedaladjWltment
800
c
c
models
Page 108 of 171
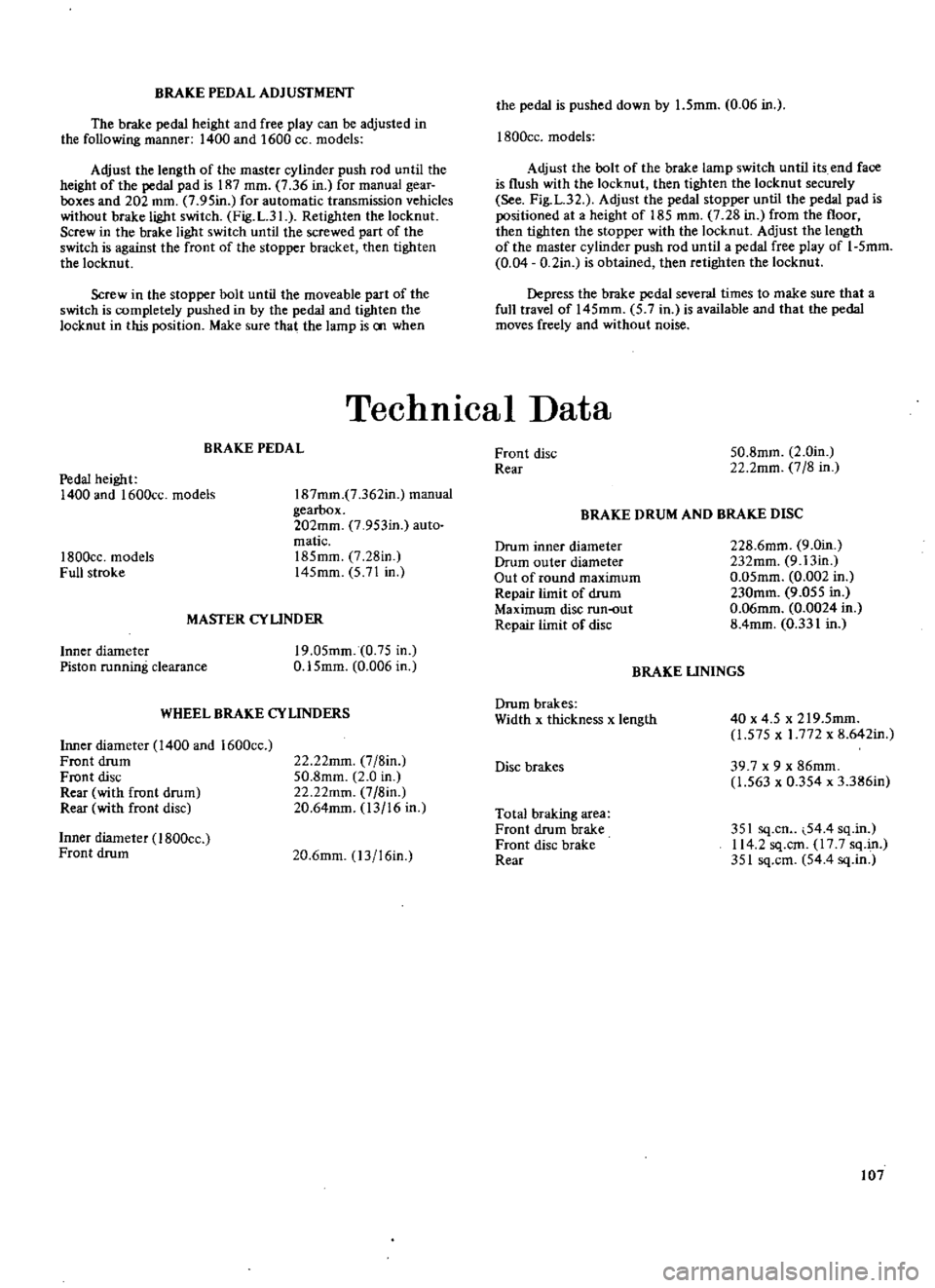
BRAKE
PEDAL
ADJUSTMENT
The
brake
pedal
height
and
free
play
can
be
adjusted
in
the
following
manner
1400
and
1600
CC
models
Adjust
the
length
of
the
master
cylinder
push
rod
until
the
height
of
the
pedal
pad
is
187
mm
7
36
in
for
manual
gear
boxes
and
202
mm
7
95in
for
automatic
transmission
vehicles
without
brake
light
switch
Fig
L
31
Retighten
the
locknut
Screw
in
the
brake
light
switch
until
the
screwed
part
of
the
switch
is
against
the
front
of
the
stopper
bracket
then
tighten
the
locknut
Screw
in
the
stopper
bolt
until
the
moveable
part
of
the
switch
is
completely
pushed
in
by
the
pedal
and
tighten
the
locknut
in
this
position
Make
sure
that
the
lamp
is
00
when
the
pedal
is
pushed
down
by
1
5mm
0
06
in
1800cc
models
Adjust
the
bolt
of
the
brake
lamp
switch
until
its
end
face
is
flush
with
the
locknut
then
tighten
the
locknut
securely
See
Fig
L
32
Adjust
the
pedal
stopper
until
the
pedal
pad
is
positioned
at
a
height
of
185
mrn
7
28
in
from
the
floor
then
tighten
the
stopper
with
the
locknut
Adjust
the
length
of
the
master
cylinder
push
rod
until
a
pedal
free
play
of
I
5mm
0
04
D
2in
is
obtained
then
retighten
the
locknut
Depress
the
brake
pedal
several
times
to
make
sure
that
a
full
travel
of
145mm
5
7
in
is
available
and
that
the
pedal
moves
freely
and
without
noise
Technical
Data
BRAKE
PEDAL
Pedal
height
1400
and
1600cc
models
I
87mm
7
362in
manual
gearbox
202mm
7
953in
auto
matic
185mm
7
28in
145mm
5
71
in
1800cc
models
Full
stroke
MASTER
CYUNDER
Inner
diameter
Piston
running
clearance
19
05mm
0
75
in
0
15mm
0
006
in
WHEEL
BRAKE
CYLINDERS
Inner
diameter
1400
and
1600cc
Front
drum
Front
disc
Rear
with
front
drum
Rear
with
front
disc
22
22mm
7
8in
50
8mm
2
0
in
22
22mm
7
8in
20
64mm
13
16
in
Inner
diameter
I
BOOcc
Front
drum
20
6mm
13
16in
Front
disc
Rear
50
8mm
2
0in
22
2mm
7
8
in
BRAKE
DRUM
AND
BRAKE
DISC
Drum
inner
diameter
Drum
outer
diameter
Out
of
round
maximum
Repair
limit
of
drum
Maximum
disc
run
out
Repair
limit
of
disc
228
6mm
9
0in
232mm
9
13in
0
05mm
0
002
in
230mm
9
055
in
0
06mm
0
0024
in
8
4mm
0
331
in
BRAKE
UNINGS
Drum
brakes
Width
x
thickness
x
length
40
x
4
5
x
219
5mm
1
575
x
1
772
x
8
642in
Disc
brakes
39
7
x
9
x
86mm
1
563
x
0
354
x
3
386in
Total
braking
area
Front
drum
brake
Front
disc
brake
Rear
351
sq
cn
54
4
sq
in
114
2
sq
cm
17
7
sq
in
351
sq
cm
54
4
sq
in
107
Page 109 of 171
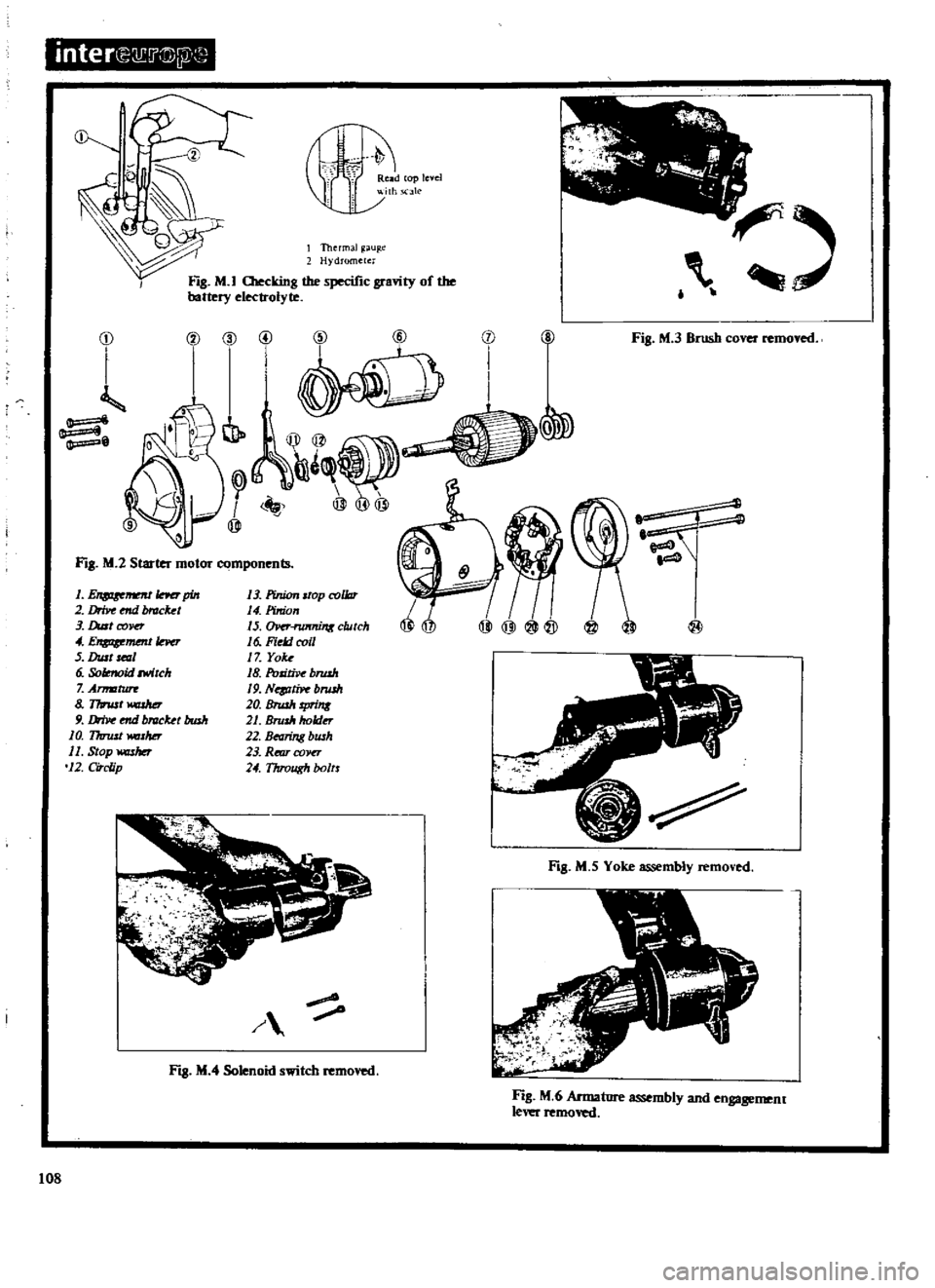
interQ
8
j
@W
2
m
tV
r
ReJld
cop
level
th
elk
FIg
M
I
llIecking
the
specific
gra
ity
of
the
battery
electrolyte
I
Thermal
u
e
Hydrometer
f
j
0
l
Q
I
iJ
Qy@
I
@
@
@
ti
II
@
@
Fig
M
3
Brush
cover
removed
j
i
Fill
M
2
Starter
motor
components
1
L
u
uJIner
pin
2
Drive
mil
Nack
t
3
Dult
COPD
4
E
mmtle
r
5
Aut
mzl
6
Solmoid
mlch
7
Arm
zturr
8
Thnut
9
IJriv
mil
blllck
t
bush
10
17uust
WdSMr
11
Stop
washer
12
CiTc
ip
13
PirUon
srap
collar
14
Pinion
IS
IWfni1l6
clutch
16
Field
coil
17
Yok
18
Politive
brwh
19
N
J1iP
bnuh
20
Bnuh
rprinK
21
Brullr
holder
22
Bearing
bwh
23
Rmr
COJIU
24
Through
botrr
@
FIg
M
5
Yoke
assembly
removed
Fill
M
4
Solenoid
switch
1
108
Fig
M
6
Annatore
assembly
and
engagemenr
lever
removed
Page 110 of 171
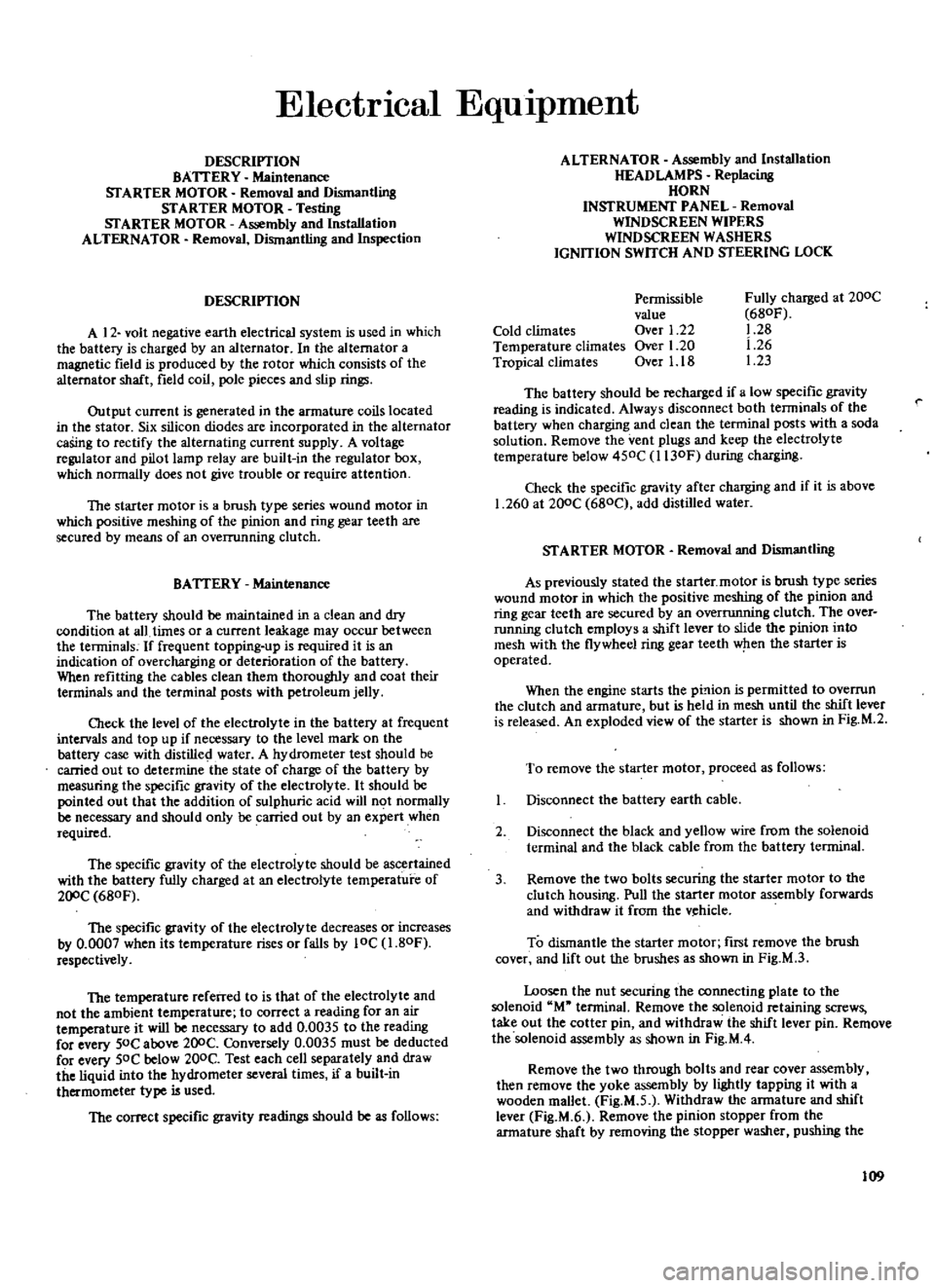
ElectrIcal
EquIpment
DESCRIPTION
BATTERY
Maintenance
STARTER
MOTOR
Removal
and
Dismantling
STARTER
MOTOR
Testing
STARTER
MOTOR
Assembly
and
Installation
ALTERNATOR
Removal
Dismantling
and
Inspection
DESCRIPTION
A
12
volt
negative
earth
electrical
system
is
used
in
which
the
battery
is
charged
by
an
alternator
In
the
alternator
a
magnetic
field
is
produced
by
the
rotor
which
consists
of
the
alternator
shaft
field
coil
p
le
pieces
and
slip
rings
Output
current
is
generated
in
the
armature
coils
located
in
the
stator
Six
silicon
diodes
are
incorporated
in
the
alternator
caSing
to
rectify
the
alternating
current
supply
A
voltage
regulator
and
pilot
lamp
relay
are
built
in
the
regulator
box
which
nonnally
does
not
give
trouble
or
require
attention
The
starter
motor
is
a
brush
type
series
wound
motor
in
which
positive
meshing
of
the
pinion
and
ring
gear
teeth
are
secured
by
means
of
an
overrunning
clutch
BATTERY
Maintenance
The
battery
should
be
maintained
in
a
clean
and
dry
condition
at
all
times
or
a
current
leakage
may
occur
between
the
terminals
If
frequent
topping
up
is
required
it
is
an
indication
of
overcharging
or
deterioration
of
the
battery
When
refitting
the
cables
clean
them
thoroughly
and
coat
their
terminals
and
the
terminal
posts
with
petroleum
jelly
Check
the
level
of
the
electrolyte
in
the
battery
at
frequent
intervals
and
top
up
if
necessary
to
the
level
mark
on
the
battery
case
with
distilled
water
A
hydrometer
test
should
be
carried
out
to
determine
the
state
of
charge
of
the
battery
by
measuring
the
specific
gravity
of
the
electrolyte
It
should
be
pointed
out
that
the
addition
of
sulphuric
acid
will
not
normally
be
necessary
and
should
only
be
carried
out
by
an
expert
when
required
The
specific
gravity
of
the
electrolyte
should
be
ascertained
with
the
battery
fully
charged
at
an
electrolyte
temperature
of
200C
680F
The
specific
gravity
of
the
electrolyte
decreases
or
increases
by
0
0007
when
its
temperature
rises
or
falls
by
10C
1
80F
respectively
The
temperature
referred
to
is
that
of
the
electrolyte
and
not
the
ambient
temperature
to
correct
a
reading
for
an
air
temperature
it
will
be
necessary
to
add
0
0035
to
the
reading
for
every
50C
above
200C
Conversely
0
0035
must
be
deducted
for
every
SOC
below
200C
Test
each
cell
separately
and
draw
the
liquid
into
the
hydrometer
several
times
if
a
built
in
thermometer
type
is
used
The
correct
specific
gravity
readings
should
be
as
follows
ALTERNATOR
Assembly
and
Installation
HEAD
LAMPS
Replacing
HORN
INSTRUMENT
PANEL
Removal
WINDSCREEN
WIPERS
WINDSCREEN
WASHERS
IGNITION
SWITCH
AND
STEERING
LOCK
Cold
climates
Temperature
climates
Tropical
climates
Permissible
value
Over
1
22
Over
1
20
Over
1
18
Fully
charged
at
200C
680F
1
28
1
26
1
23
The
battery
should
be
recharged
if
a
low
specific
gravity
reading
is
indicated
Always
disconnect
both
terminals
of
the
battery
when
charging
and
clean
the
terminal
posts
with
a
soda
solution
Remove
the
vent
plugs
and
keep
the
electrolyte
temperature
below
450C
l130F
during
charging
Check
the
specific
gravity
after
charging
and
if
it
is
above
1
260
at
200C
680C
add
distilled
water
STARTER
MOTOR
Removal
and
Dismantling
As
previously
stated
the
starter
motor
is
brush
type
series
wound
motor
in
which
the
positive
meshing
of
the
pinion
and
ring
gear
teeth
are
secured
by
an
overrunning
clutch
The
over
running
clutch
employs
a
shift
lever
to
slide
the
pinion
into
mesh
with
the
flywheel
ring
gear
teeth
when
the
starter
is
operated
When
the
engine
starts
the
pL
lion
is
permitted
to
overrun
the
clutch
and
armature
but
is
held
in
mesh
until
the
shift
lever
is
released
An
exploded
view
of
the
starter
is
shown
in
Fig
M
2
To
remove
the
starter
motor
proceed
as
follows
Disconnect
the
battery
earth
cable
2
Disconnect
the
black
and
yellow
wire
from
the
solenoid
terminal
and
the
black
cable
from
the
battery
terminal
3
Remove
the
two
bolts
securing
the
starter
motor
to
the
clutch
housing
Pull
the
starter
motor
assembly
forwards
and
withdraw
it
from
the
v
hicle
To
dismantle
the
starter
motor
ftrst
remove
the
brush
cover
and
lift
out
the
brushes
as
shown
in
Fig
M
3
Loosen
the
nut
securing
the
connecting
plate
to
the
solenoid
M
terminal
Remove
the
solenoid
retaining
screws
take
out
the
cotter
pin
and
withdraw
the
shift
lever
pin
Remove
the
solenoid
assembly
as
shown
in
Fig
M
4
Remove
the
two
through
bolts
and
rear
cover
assembly
then
remove
the
yoke
assembly
by
lightly
tapping
it
with
a
wooden
mallet
Fig
M
S
Withdraw
the
armature
and
shift
lever
Fig
M
6
Remove
the
pinion
stopper
from
the
armature
shaft
by
removing
the
stopper
washer
pushing
the
109