compression ratio DATSUN 610 1969 User Guide
[x] Cancel search | Manufacturer: DATSUN, Model Year: 1969, Model line: 610, Model: DATSUN 610 1969Pages: 171, PDF Size: 10.63 MB
Page 156 of 171
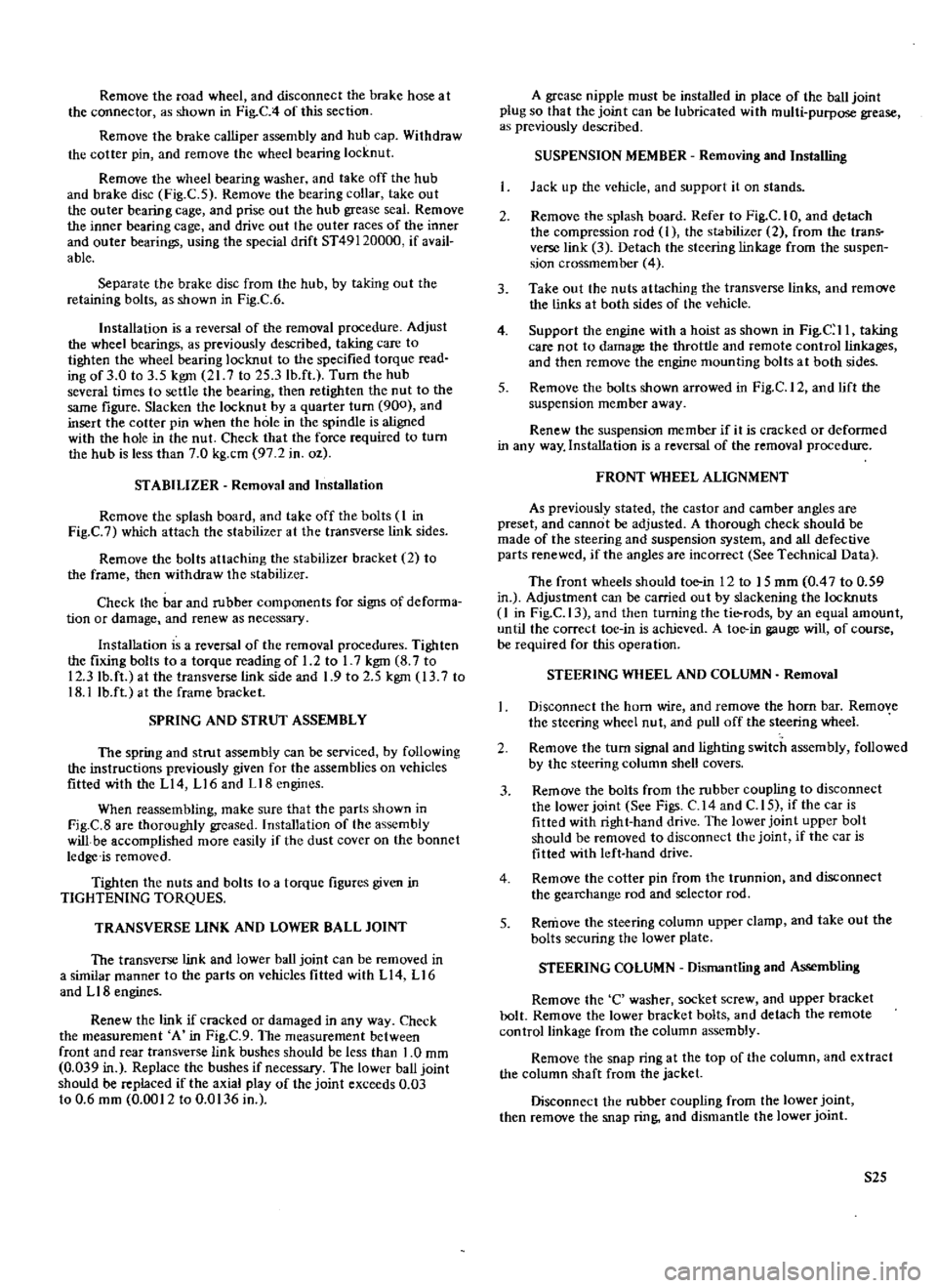
Remove
the
road
wheel
and
disconnect
the
brake
hose
at
the
connector
as
shown
in
Fig
C
4
of
this
section
Remove
the
brake
calliper
assembly
and
hub
cap
Withdraw
the
cotter
pin
and
remove
the
wheel
bearing
locknut
Remove
the
wheel
bearing
washer
and
take
off
the
hub
and
brake
disc
Fig
C
5
Remove
the
bearing
collar
take
out
the
outer
bearing
cage
and
prise
out
the
hub
grease
seal
Remove
the
inner
bearing
cage
and
drive
out
the
outer
races
of
the
inner
and
outer
bearings
using
the
special
drift
ST49120000
if
avail
able
Separate
the
brake
disc
from
the
hub
by
taking
out
the
retaining
bolts
as
shown
in
Fig
C
6
Installation
is
a
reversal
of
the
removal
procedure
Adjust
the
wheel
bearings
as
previously
described
taking
care
to
tighten
the
wheel
bearing
locknut
to
the
specified
torque
read
ing
of
3
0
to
3
5
kgm
21
7
to
25
3lb
ft
Turn
the
hub
several
times
to
settle
the
bearing
then
retighten
the
nut
to
the
same
figure
Slacken
the
locknut
by
a
quarter
turn
900
and
insert
the
cotter
pin
when
the
hole
in
the
spindle
is
aligned
with
the
hole
in
the
nut
Check
that
the
force
required
to
turn
the
hub
is
less
than
7
0
kg
cm
97
2
in
oz
STABILIZER
Removal
and
Installation
Remove
the
splash
board
and
take
off
the
bolts
I
in
Fig
C
7
which
attach
the
stabilizer
at
the
transverse
link
sides
Remove
the
bolts
attaching
the
stabilizer
bracket
2
to
the
frame
then
withdraw
the
stabilizer
Check
the
bar
and
rubber
components
for
signs
of
deforma
tion
or
damage
and
renew
as
necessary
Installation
is
a
reversal
of
the
removal
procedures
Tighten
the
fixing
bolts
to
a
torque
reading
of
1
2
to
I
7
kgm
8
7
to
12
3
lb
ft
at
the
transverse
link
side
and
1
9
to
2
5
kgm
13
7
to
18
llb
ft
at
the
frame
bracket
SPRING
AND
STRUT
ASSEMBLY
The
spring
and
strut
assembly
can
be
serviced
by
following
the
instructions
previously
given
for
the
assemblies
on
vehicles
fitted
with
the
L14
L16
and
Ll8engines
When
reassembling
make
sure
that
the
parts
shown
in
Fig
C
8
are
thomughly
greased
Installation
of
the
assembly
will
be
accomplished
more
easily
if
the
dust
cover
on
the
bonnet
ledge
is
removed
Tighten
the
nuts
and
bolts
to
a
torque
figures
given
in
TIGHTENING
TORQUES
TRANSVERSE
LINK
AND
LOWER
BALL
JOINT
The
transverse
link
and
lower
ball
joint
can
be
removed
in
a
similar
manner
to
the
parts
on
vehicles
fitted
with
L
14
L
16
and
L
18
engines
Renew
the
link
if
cracked
or
damaged
in
any
way
Check
the
measurement
A
in
Fig
C
9
The
measurement
between
front
and
rear
transverse
link
bushes
should
be
less
than
1
0
mm
0
039
in
Replace
the
bushes
if
necessary
The
lower
ball
joint
should
be
replaced
if
the
axial
play
of
the
joint
exceeds
0
03
to
0
6
mm
0
0012
to
0
0136
in
A
grease
nipple
must
be
installed
in
place
of
the
ball
joint
plug
so
that
the
joint
can
be
lubricated
with
multi
purpose
grease
as
previously
described
SUSPENSION
MEMBER
Removing
and
Installing
Jack
up
the
vehicle
and
support
it
on
stands
2
Remove
the
splash
board
Refer
to
Fig
C
I
0
and
detach
the
compression
rod
I
the
stabilizer
2
from
the
trans
verse
link
3
Detach
the
steering
linkage
from
the
suspen
sion
crossmember
4
3
Take
out
the
nuts
attaching
the
transverse
links
and
remove
the
links
at
both
sides
of
the
vehicle
4
Support
the
engine
with
a
hoist
as
shown
in
Fig
C
II
taking
care
not
to
damage
the
throttle
and
remote
control
linkages
and
then
remove
the
engine
mounting
bolts
at
both
sides
5
Remove
the
bolts
shown
arrowed
in
Fig
C
12
and
lift
the
suspension
member
away
Renew
the
suspension
member
if
it
is
cracked
or
deformed
in
any
way
Installation
is
a
reversal
of
the
removal
procedure
FRONT
WHEEL
ALIGNMENT
As
previously
stated
the
castor
and
camber
angles
are
preset
and
cannot
be
adjusted
A
thorough
check
should
be
made
of
the
steering
and
suspension
system
and
all
defective
parts
renewed
if
the
angles
are
incorrect
See
Technical
Data
The
front
wheels
should
toe
in
12
to
15
mm
0
4
7
to
0
59
in
Adjustment
can
be
carried
out
by
slackening
the
locknuts
1
in
Fig
C
13
and
then
turning
the
tie
rods
by
an
equal
amount
until
the
correct
toe
in
is
achieved
A
toe
in
gauge
will
of
course
be
required
for
this
operation
STEERING
WHEEL
AND
COLUMN
Removal
Disconnect
the
horn
wire
and
remove
the
horn
bar
Remove
the
steering
wheel
nut
and
pull
off
the
steering
wheel
2
Remove
the
turn
signal
and
lighting
switch
assembly
followed
by
the
steering
column
shell
covers
3
Remove
the
bolts
from
the
rubber
coupling
to
disconnect
the
lower
joint
See
Figs
C
14
and
C
I
5
if
the
car
is
fitted
with
right
hand
drive
The
lower
joint
upper
bolt
should
be
removed
to
disconnect
the
joint
if
the
car
is
fitted
with
left
hand
drive
4
Remove
the
cotter
pin
from
the
trunnion
and
disconnect
the
gearchange
rod
and
selector
rod
5
Remove
the
steering
column
upper
clamp
and
take
out
the
bolts
securing
the
lower
plate
STEERING
COLUMN
Dismantling
and
Assembling
Remove
the
C
washer
socket
screw
and
upper
bracket
bolt
Remove
the
lower
bracket
bolts
and
detach
the
remote
control
linkage
from
the
column
assembly
Remove
the
snap
ring
at
the
top
of
the
column
and
extract
the
column
shaft
from
the
jacket
Disconnect
the
rubber
coupling
from
the
lower
joint
then
remove
the
snap
ring
and
dismantle
the
lower
joint
S25
Page 160 of 171
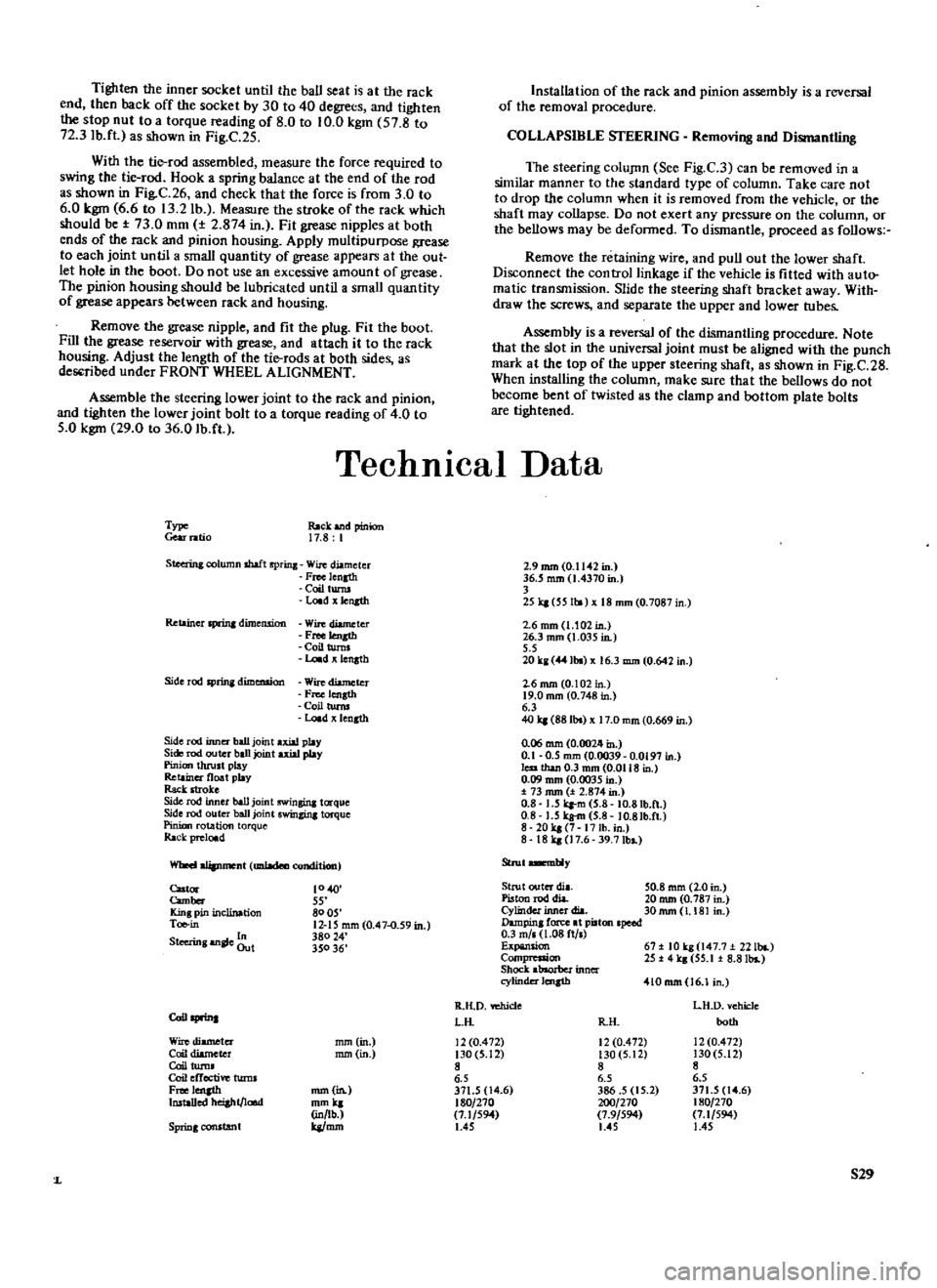
Tighten
the
inner
socket
until
the
ball
seat
is
at
the
rack
end
then
back
off
the
socket
by
30
to
40
degrees
and
tighten
the
stop
nut
to
a
torque
reading
of
8
0
to
10
0
kgm
57
8
to
72
3
Ib
ft
as
shown
in
Fig
C
25
With
the
tie
rod
assembled
measure
the
force
required
to
swing
the
tie
rod
Hook
a
spring
balance
at
the
end
of
the
rod
as
shown
in
Fig
C
26
and
check
that
the
force
is
from
3
0
to
6
0
kgm
6
6
to
13
2
lb
Measure
the
stroke
of
the
rack
which
should
be
73
0
mm
2
874
in
Fit
grease
nipples
at
both
ends
of
the
rack
and
pinion
housing
Apply
multipurpose
ase
to
each
joint
until
a
small
quantity
of
grease
appears
at
the
out
let
hole
in
the
boot
Do
not
use
an
excessive
amount
of
grease
The
pinion
housing
should
be
lubricated
until
a
small
quantity
of
grease
appears
between
rack
and
housing
Remove
the
grease
nipple
and
fit
the
plug
Fit
the
boot
Fill
the
grease
reseIVoir
with
grease
and
attach
it
to
the
rack
housing
Adjust
the
length
of
the
tie
rods
at
both
sides
as
des
ribed
under
FRONT
WHEEL
ALIGNMENT
Assemble
the
steering
lower
joint
to
the
rack
and
pinion
and
tighten
the
lower
joint
bolt
to
a
torque
reading
of
4
0
to
5
0
kgm
29
0
to
36
0
Ib
ft
Installation
of
the
rack
and
pinion
assembly
is
a
reversal
of
the
removal
procedure
COLLAPSIBLE
STEERING
Removi
8
and
Dismantti
8
The
steering
coluJllfl
See
Fig
C
3
can
be
removed
in
a
similar
manner
to
the
standard
type
of
column
Take
care
not
to
drop
the
column
when
it
is
removed
from
the
vehicle
or
the
shaft
may
collapse
Do
not
exert
any
pressure
on
the
column
or
the
bellows
may
be
defonned
To
dismantle
proceed
as
follows
Remove
the
retaining
wire
and
pull
out
the
lower
shaft
Disconnect
the
control
linkage
if
the
vehicle
is
fitted
with
auto
matic
transmission
Slide
the
steering
shaft
bracket
away
With
draw
the
screws
and
separate
the
upper
and
lower
tubes
Assembly
is
a
reversal
of
the
dismantling
procedure
Note
that
the
slot
in
the
universal
joint
must
be
aligned
with
the
punch
mark
at
the
top
of
the
upper
steering
shaft
as
shown
in
Fig
C
28
When
installing
the
column
make
sure
that
the
bellows
do
not
become
bent
of
twisted
as
the
clamp
and
bottom
plate
bolts
are
tightened
TechnICal
Data
TYP
Gear
I1ltio
Rack
and
pinion
17
8
I
Steerin
column
shaft
spring
Wire
diameter
Freelenath
CoiltW
llJ
Load
length
Retainer
sprinJ
dimension
Wire
diameter
F
CoilturnJ
l
oadxlensth
Side
rod
SPrina
dimeruion
Wire
diameter
Fn
elenath
Coil
turns
Load
x
lensth
Side
rod
inner
ball
joint
ax
ia
I
play
Side
rod
outer
ball
joint
uiaJ
play
Pinion
thrultplay
Retainer
float
play
Rack
moke
Side
rod
inner
ball
joint
swinsinl
torque
Side
rod
uter
ball
joint
swingina
torque
Pinion
oration
torque
Rack
pre1
d
Wheel
alipment
1IIl1a
a
ondition
Cut
c
m
Kinl
pin
inclination
Toe
in
S
In
teerinlan
eOut
10
40
8005
12
15
mm
0
47
0
59
in
38024
35036
2
9
mm
0
11
2
in
36
5
mm
1
4370
in
3
25q
551
18mm
0
7087
2
6
mm
1
102in
26
3
mm
1
035
in
5
5
20
kl
lbs
16
3
mm
0
642
in
26
mm
0
102
in
19
0
mm
0
748
in
6
3
40
q
88Ibs
17
0
mm
0
669
in
0
06
mm
0
002
m
0
1
0
5
mm
0
0039
0
0197
in
less
than
0
3
mm
0
0118
in
0
09
mm
0
0035
in
73
mm
t
2
87
in
0
8
1
5
q
m
5
8
10
8Ib
n
0
8
J
S
kg
m
5
8
JO
8Ib
ft
8
20q
7
17
lb
in
8
18
q
l7
6
39
7Ibs
Strut
DlelDbly
Strut
outer
Ilia
50
8
mm
2
0
in
Piston
rod
di
a
20
mm
0
787
in
Cylinder
inner
dia
30mm
I
181
in
Dampinl
force
at
pistonlpeed
0
3
m
I
1
08
ft
I
Expansion
67
IOq
I47
7
221bs
Compression
25
4kl
55
1
8
81bs
Shock
absorber
inner
cylinderlcngth
IOmm
16
1
in
R
IlD
vchicle
LH
D
ehide
CoiIsprina
LIi
IlIi
OOIh
Wire
diameter
mm
in
12
0
472
12
0
472
12
0
472
Coil
diameter
mm
in
130
5
12
130
5
12
130
5
12
Coil
Ium
S
Coil
effective
turnl
6
5
6
5
6
5
Free
lenJth
mm
in
371
5
14
6
386
5
15
2
371
5
14
6
Installed
hei
ht
load
mmq
180
270
200
270
180
270
in
lb
7
1
594
7
9
594
7
1
594
SpriDgCOfl
ltant
ka
mm
1
45
US
1
45
529
1